防错管理技术七步法
防错技术与防错管理

做对的效益的三倍 ➢ 低错误率的保证—防错机制的建立
第三部分 防错技术开发
防错技法的理解与实现
防错案例
产品设计开发中的防错应用
36
互动
➢你的答案正确吗? 为什么出错了?
人为错误方式的分析
人为错误的种类 自以为是
敷衍、马虎 拖沓、松散
健忘 误解 判断(识别)失误 工作疏忽 故意
错误的场景 自认为了解 小事、不重要
无所谓 压力、精力不集中时 面对新的工作环境、自认为了解 环境、速度、经验主义 心不在焉、重复性工作 忽略标准或规则、情绪或利益
例1:在零件上预防缺陷 过程描述:用螺定紧固塑料外观件 问题:螺丝刀划伤塑料件表面
改进前:
解决方案:改变螺钉槽形状 关键改进措施:
改进后:
例2:在零件上预防缺陷 过程描述:轴的装配 问题:轴两端头装配错误
改进前:
不正确
正确
解决方案:轴的两端可互 换
关键改进措施:改变零件 的形状
改进后:
思考: 解决方案二:
案、拟达到的作用级别 步骤5 实施改善方案: 步骤6 确认防错效果:活动后必须查核能否按照目标获
得成果。 步骤7 维持防错:将防错方法规范化、标准化
分析问题的金字塔原理
问题
一级因素
二级 因素
原 因
解决问题的九个控制要素
5W
➢ Why ➢ What ➢ Where ➢ Who ➢ When
3H
➢ How ➢ How much ➢ How much cost
(完整版)七步管理法
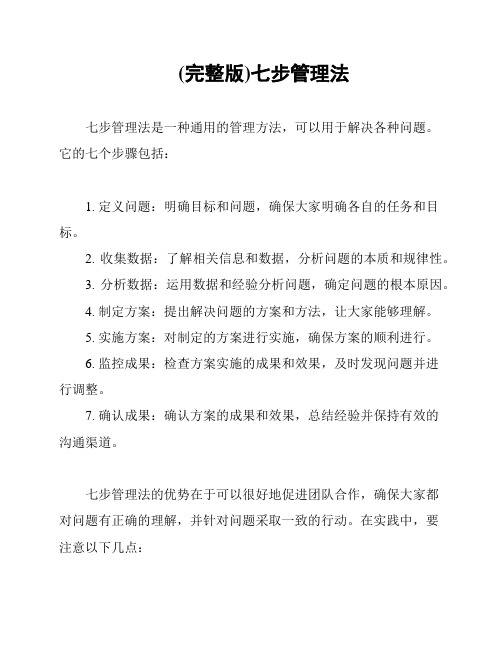
(完整版)七步管理法
七步管理法是一种通用的管理方法,可以用于解决各种问题。
它的七个步骤包括:
1. 定义问题:明确目标和问题,确保大家明确各自的任务和目标。
2. 收集数据:了解相关信息和数据,分析问题的本质和规律性。
3. 分析数据:运用数据和经验分析问题,确定问题的根本原因。
4. 制定方案:提出解决问题的方案和方法,让大家能够理解。
5. 实施方案:对制定的方案进行实施,确保方案的顺利进行。
6. 监控成果:检查方案实施的成果和效果,及时发现问题并进
行调整。
7. 确认成果:确认方案的成果和效果,总结经验并保持有效的
沟通渠道。
七步管理法的优势在于可以很好地促进团队合作,确保大家都
对问题有正确的理解,并针对问题采取一致的行动。
在实践中,要
注意以下几点:
1. 不要把所有问题都用七步管理法解决,根据情况灵活运用。
2. 在方案制定时,要充分考虑各种因素,包括人力、物力、财
务等。
3. 在实施方案时,要找到适当的平衡点,既不能东拼西凑、不
切实际,也不能过于保守。
4. 在监控成果时,要及时发现问题,及时总结和调整,避免错
失机会。
5. 在确认成果时,要保持有效的沟通,避免因为信息不畅通而
产生新的问题。
总之,七步管理法是一种非常实用的工具,可以帮助团队更好
地解决各种问题,在规划、执行和监控过程中不断改进和优化方案。
防错法(质量管理类工具)ppt课件

技术难题与解决方案
管理问题与改进措施
问题一
管理层对防错法的重视程度不足
改进措施
通过培训、宣传等方式,提高管理层对防错法的认识和重视程度,使其成为企业文化的一部分。
问题二
缺乏完善的防错法实施流程和规范
改进措施
建立完善的防错法实施流程和规范,明确各部门的职责和权限,确保防错法的顺利实施。
问题三
缺乏有效的监督和考核机制
THANKS
防错法(质量管理类工具)ppt课件
目录
CONTENTS
防错法概述 防错法原理与核心思想 防错法实施步骤与方法 常见防错技术及应用案例 防错法在质量管理中的应用价值 实施防错法面临的挑战与解决方案 总结与展望
01
防错法概述
定义:防错法,又称为“愚巧法”,是一种预防错误发生的方法,通过设计、装置、程序等手段,使操作变得简单、直观,减少或避免人为错误。
条形码/二维码识别
利用OCR技术对产品上的文字、数字等进行识别,确保信息的准确性和一致性。
字符识别
视觉识别防错技术
数据挖掘与分析
利用数据挖掘和分析技术,对历史数据进行分析和挖掘,找出潜在的问题和改进点,为质量改进提供决策支持。
质量追溯系统
建立质量追溯系统,对产品的生产、检验、销售等全过程进行记录和追踪,便于问题的查找和原因分析。
难题一
如何准确识别潜在错误
解决方案
借鉴行业内的最佳实践,结合自身的生产流程和设备特点,定制化设计防错装置,确保其与生产线的完美融合。
解决方案
采用先进的数据分析技术,对历史数据进行深入挖掘,找出可能引发错误的模式和趋势。
难题三
如何确保防错装置的可靠性
难题二
如何设计有效的防错装置
最新防错技术精品文档
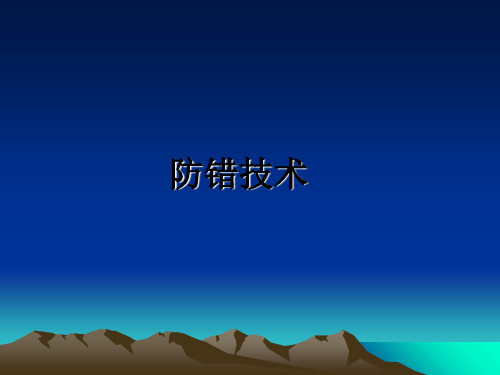
改变或增添工具、工装 改变加工步骤 增加使用清单、模板或测量仪 执行控制图表
三、防错的基本原则
基本原则: 使作业的动作轻松:难于观察、难拿、难动等作业即变得易做。区分颜 色使得容易看,或放大标示,或加上把手使得容易拿,或使用搬运器具 使动作轻松; 使作业不要技能与直觉:需要高度技能与直觉的作业,容易发生失 误.考虑治具及工具,进行机械化,使新进人员或支持人员也能做不出 错的作业; 使作业不会有危险:因不安全或不安定而会给人或产品带来危险时,加 以改善使之不会有危险.马虎行之或勉强行之而发生危险时,设法装设 无法马虎或无法勉强的装置; 使作业不依赖感官:依赖像眼睛、耳朵、感触等感官进行作业时,容易 发生失误。制作治具或使之机械化,减少用人的感官来判断的作业。又 一定要依赖感官的作业,譬如,当信号一红即同时有声音出现,设法使
之能做二重三重的判断。
四、防错的五大基本思路
基本思路
目标
方法
事例说明
评价
排除 消除可能的错误
通过产品及制造过程的重 新设计, 加入防错方法
XXX倒角的设 计
最好
替代
用更可靠的过程代替 目前的过程以降低失 误
运用机器技术或自动化 生产技术
游隙检测:机器 替代人工
较好
容易/简 化
使作业更容易完成
合并生产步骤/流程, 实 施工业工程改善
六、防错十大原理
10.缓和原理:以各种方法来减少错误发生后所造成的损害,虽然 不能完全排除错误的发生,但是可以降低其损害的程度。 例1:新车间四线三道游隙检测,两道称重,两道测振; 例2:磨工工具上刻上字,便于追溯回; 例3:汽车之安全带,骑机车戴安全帽。 例4:鸡蛋之隔层装运盒减少搬运途中的损伤。 例5:自动消防洒水系统,火灾发生了开始自动洒水减火。 例6:加纸板以减少轴承在搬运中之碰伤。
利用七步法解决质量管理中的问题

利用七步法解决质量管理中的问题在现代企业管理中,质量管理一直是重中之重。
如何有效地解决质量管理中的问题,提高产品和服务的质量,已经成为企业发展的关键因素之一。
利用七步法进行质量管理,可以帮助企业识别问题、分析原因、制定解决方案,从而提高工作效率、降低成本,实现持续改进。
下面将介绍如何利用七步法解决质量管理中的问题。
第一步:确定问题范围在质量管理中,首先要确定问题的范围。
了解问题的具体情况,明确问题的性质和影响范围,才能有针对性地进行改进。
通过调查和分析,找出质量管理中存在的问题,比如产品质量不达标、客户投诉率高等,从而确定解决问题的重点。
第二步:收集数据收集数据是分析问题的重要一环。
企业可以通过调查问卷、数据统计等方式,获取相关数据,用于分析问题的根本原因。
数据的准确性和完整性对问题的解决至关重要,只有有了足够的数据支持,才能做出准确的判断。
第三步:进行分析在收集到足够的数据后,企业需要进行深入分析。
通过比较、统计和图表展示等方式,找出问题的主要原因。
分析问题的根源,有助于从根本上解决问题,而不是仅仅处理表面现象。
只有找到问题的真正原因,才能采取有针对性的措施。
第四步:制定解决方案在分析问题的基础上,企业需要制定详细的解决方案。
根据问题的性质和原因,制定可行的解决方案,确保解决方案的有效性和可操作性。
解决方案应该具体、可执行,包括目标、步骤、责任人等,方便实施和监控。
第五步:实施方案将制定好的解决方案付诸实施是解决问题的关键环节。
企业需要明确实施计划、组织资源、指定责任人,确保每个步骤都得到有效执行。
在实施过程中,及时调整和优化方案,保证问题的解决效果。
第六步:监控效果实施方案后,企业需要对效果进行监控。
通过数据统计、质量检测等方式,及时了解问题解决的效果。
监控可以帮助企业发现问题,及时调整方案,避免问题再次发生。
只有持续监控,才能保证质量管理的稳定和提升。
第七步:总结经验最后一步是总结经验。
企业在解决问题的过程中,应该及时总结经验教训,吸取经验,不断完善质量管理体系。
IE七大手法之防错法(经典作品)(共43张PPT)

設計系統和程序來消除缺陷產生機會
消除浪费
5
二、失誤與缺陷
失误与 缺陷
由於作
業果
二、失誤與缺陷
失誤 漏加錫 漏檢 漏裝螺絲 漏關煤氣
缺陷 元件半焊 外觀凹痕 産品少螺帽 燒裂水壺
三、産生失誤的一般原因
1、忘記
2、對過程/作業不熟悉
失
误
3、识別錯誤
原
因
4、缺乏工作经验
失误原因分析表
失誤原因
忘記 對過程/作業不熟悉 缺乏工作經驗 故意失誤 疏忽 行動遲緩 缺乏適當的作業指導 突發事件
原因歸類
人 人 人 人 人 人 方法 設備
所占比例 77.8%
11.1% 11.1%
一、對待失誤的兩種出發點
失误防止的两种出发点
传统观点
POKA-
YOKE 的观点
培训教育
惩罚处理
事前预防
一、防錯法的作用
■第一次就把事情
03、確認缺陷產生工序的作業指導書. 第四篇 防错法应用例
做好
2、常見檢測項目及檢測裝置 。
當未被壓下時, 開關斷開, 當被運動部件壓下時, 開關導通, 接通控制電路.
三、防錯法應用例
(2)在照相機上加裝自動過卷馬達, 只要拍攝者按下快門, 則過卷馬達自動過卷.
使每個人都參與缺陷預防
31 是否在调整中
36 是否作业量不足
2 工具/设备变更 否
3 规格/参数/作业标准 变否
4 部品相混或堆放過 多否
5 操作步骤是否太多.
7 作业标准是否够
38
作业是否平衡
9 作业环境如何
10 作业节拍是否快
二、防錯法實施的一般步驟 。
06、分析缺陷原因.
防错技术的应用课件

防错管理流程
设计 修改
设计 防错
防错输出
顾客需求
设计 FMEA
过程 FMEA
控制计划
作业SOP
过程 修改
过程 防错
防错运行
防错的2个途径
the Design 重新设计产品
– 消除犯错误的条件 – 重新进行对称或不对称设计 – 改变材料 – 改变组件的类型、特征或供应商
the Process 制造过程
防错的基本思路
基本思路
目标
排除 消除可能的错误
替代
用更可靠的过程代替目 前的过程以降低失误
容易/简化 使作业更容易完成
异常检出 缓和影响
在缺陷流入下工序前对 其进行检测并剔除
将错误影响降至最低
方法
通过产品及制造过程的重新 设计, 加入防错方法
运用机器人技术或自动化生 产技术
合并生产步骤, 实施工业工 程改善
防错的等级
根据防错的效果,防错技术可分为如下三个等级:
– 不制造缺陷的防错,即不可能制造出坏零件,可能损 坏的零件数为零;
– 不传递缺陷的防错,即不可能将坏零件传递到下一工 位;
– 不接受缺陷的防错,即后续工位不接受坏零件。
防错的等级
防错技术的理想状态是不制造缺陷的防错,这是最主动、最经济、 可预见并防止错误的控制技术。如加工前的探头探测、导向限位、 传感器感应等的防错就能达到不制造缺陷的目标。
防错7步法
第7步:标准化和推广
– 对防错过程进行评审,前面的过程和结果进行总结、归档并补充 数据库,探讨方案能否复制、推广其它类似设备或和生产厂。
– 特别要强调的是改进工作的标准化,它包括: 为新的系统/装置建立文档、图纸; 更新现有文档,清理无用的文档; 重新评估现有的工作程序(包括操作、维护、检查等)并进行 必要的修定; 对相关人员进行培训。
精益管理的技巧——防呆防错

防错法是一门技术,有一系列技术和工具用于各类过程的错误防止.一、防错思路下表列明了不同的防错思路及其策略从上表可看出, 防错的思路有减少失误、检测失误、简化作业, 替代、削除等, 从其目标及采用的方法来看:1、消除失误削除失误是最好的防错方法。
因为其从设计角度即考虑到可能出现的作业等失误并用防错方法进行预防。
这是从源头防止失误和缺陷的方法,符合质量的经济性原则, 是防错法的发展方向。
2、替代法替代法是对硬件设施进行更新和改善,使过程不过多依赖于作业人员,从而降低由于人为原因造成的失误(占失误的部分)。
这种防错方法可以大大失误率,为一种较好的防错方法,缺点在于投入过大,另外由于设备问题导致的失误无法防止。
3、简化简化是通过合并、削减等方法对作业流程进行简化,流程越简单、出现操作失误的概率越低。
因此,简化流程为较好的防错方法之一,但流程简化并不能完全防止人为缺陷的产生。
4、检测检测是在作业失误时自动提示的防错方法, 大都通过计算器软件实现, 为目前广泛使用的防错方法.5、减少从减少由于失误所造成的损失的角度出发, 即发生失误后, 将损失降至最低或可接受范围, 目前许多智能设备均或多或少具备该功能。
二、防错法则以下是几个基本的防错法则, 遵循这些法则, 可有效防止作业失误.1、只生产所需的产品。
有两层意思, 一为只生产所需数量的产品, 生产量超过需要量, 不仅是一大浪费, 而且在生产、运输、存储各环节增加了出现失误的机会. 二为生产时需牢记客户对产品的质量需求, 使作业符合要求, 背离客户需求, 无从谈到质量, 当然失误频频.2、削减、简化、合并作业步骤作业步骤越多, 出现失误的机会越多。
削减、简化和合并作业步骤, 等于为减少失误创造条件, 在新产品开发阶段, 生产过程设计时遵守该原则可大大降低后续生产中的不良. 对现有过程的分析和改善时运用该原则同样会降低失误机会.3、使每个人都参与缺陷预防质量是全员参与才可成就的, 这早已成为共误, 但人人树产预防失误、防止缺陷的观念, 并参与缺陷预防才是最重要的. 人人参与预防了, 零失误、零缺陷可有望实现.4、追求完美在质量、成本、交期、技术和服务几个方面持续追求。
防错技术管理规定
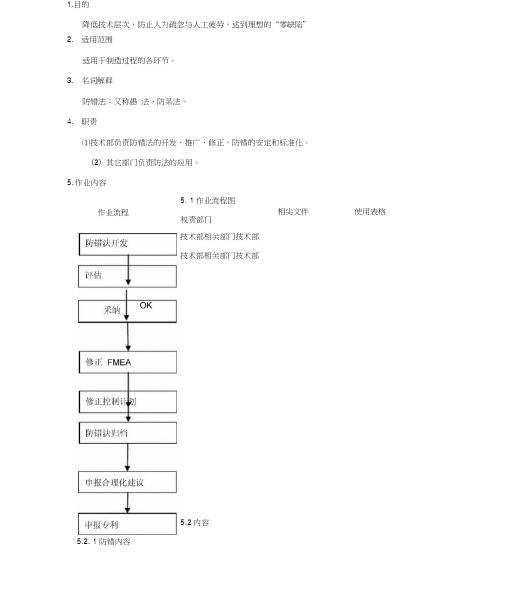
1.目的降低技术层次,防止人为疏忽与人工疲劳,达到理想的“零缺陷”2.适用范围适用于制造过程的各环节。
3.名词解释防错法:又称愚法、防呆法。
4.职责⑴技术部负责防错法的开发、推广、修正,防错的安定和标准化。
(2)其它部门负责防法的应用。
5.作业内容作业流程5. 1作业流程图权责部门相尖文件使用表格5.2. 1防错内容技术部相关部门技术部技术部相关部门技术部5.2内容(1)防止加工不良(组装失误、加工失误)(2)防止不同类品的混入(M6螺母、M8螺母混装等)(3)防止欠品(防止遗漏零件及少工序)5.2.2 防错方法(1)颜色的防错法(2)标线防错法(3)看板(4)警示声音(5)警示灯号(6)治具、夹具(7)限制失误(8)半自动化、自动化(9)定数防错法5.2.3 防错步骤(1)结合日常管理,发掘问题项目(2)分析问题项目所具备的机能(3)找出现状缺点(4)问题点要点分析(5)提出改善问题点的防错构想(6)防错的开发、试行、修正(7)防错的安定与标准化(8)防错的试用与教育5.2.4 防错要领(1)实施公司人员防止疏忽法的教育(2)纳入公司的标准制度(3)实施自主管理,推行提案改善制度、品管圈活动、5S活动等(4)从管理上提升员工工作士气,促进提出防错的意愿5.2.5 防错技巧(1)防错装置技术(2)物料防错(3)人工防错(4)安全防错(1)使其具有一旦发生错误,物品无法在治具、设备上进行组装的功能。
(2)使其具有如果作业错误有不良品产生时,机械加工作业就无法开始的功能。
(3)使其具有一旦忘了作业的话,不让不良品流入下工程的功能。
(4)使其具有一旦物品有不合适之处,机械就无法加工的功能。
(5)使其具有不良、异品的混入等情形发生时,不让不良品下工程的功能。
(6)使其具有不良时,能在原工程被检查出事,使不良品被拦截下来的功能。
527防错原理(1)断根原理(2)保险原理(3)自动原理(4)机符原理(5)顺序原理(6)隔离原理(7)复制原理(8)层别原理(9)警告原理(10缓和原理5. 2. 8防错模式(1)有形防错(2)有序防错(3)计数防错(4)信息加强防错5 2 9产生错误一般原因(1)忘记(2)对过程/作业不熟悉(3)识别错误(4)缺乏工作经验(5)疏忽(6)行动迟缓(7)缺乏适当的指导书(8)故意失误(9)突发事件(10制造过程常见的失误5.3防错法开发(1)根据《FEMA提出防错法的开发计划(2)根据纠正、预防信息提出防错法的开发计划(3)客户提出的质量信息反馈,提出防错法的开发计划5.4防错法的归案、标准化(1 )防错方案一定采纳,纳入《控制计划》,并修改FEMA(2)申报合理化建议6.附则(1)本程序由技术部负责控制及管理。
七步管理法-七步管理法

七步管理法-七步管理法介绍七步管理法是一种简单而实用的管理方法,它由七个基本步骤组成,可以帮助管理者有效地处理问题和决策。
本文档将详细介绍七步管理法的每个步骤及其应用方法。
步骤一:明确问题在开始解决任何问题之前,第一步是明确问题的本质和范围。
这意味着要准确地定义问题,了解其背景和影响,并明确问题所需的解决方案。
步骤二:收集信息在第一步明确问题后,需要收集相关的信息和数据,以便更好地了解问题的各个方面。
这可以通过调查、研究、采访等方式来获取必要的信息。
步骤三:分析信息在收集了足够的信息后,需要对其进行分析和评估。
这一步骤的目标是理解信息的含义,发现问题的根本原因和可能的解决方案。
步骤四:制定解决方案基于对问题和信息的分析,制定可行的解决方案是第四步。
在制定解决方案时,需要考虑各种因素,如成本、风险、时间等,以确保解决方案的可行性和有效性。
步骤五:实施解决方案在确定了解决方案后,需要将其付诸实施。
这可以涉及指派任务、制定计划、分配资源等活动,以确保解决方案得到有效地执行。
步骤六:监控进展一旦解决方案开始实施,需要定期监控和评估其进展情况。
这可以通过收集反馈、进行评估和调整计划等方式来完成。
步骤七:总结和反思最后一步是总结和反思整个过程。
这包括评估解决方案的效果,记录经验教训,并为以后类似问题的解决提供指导和建议。
总结七步管理法是一个简单而实用的问题解决和决策工具。
通过明确问题、收集信息、分析信息、制定解决方案、实施解决方案、监控进展和总结反思,管理者可以更加有效地处理问题和做出决策。
防错技术(防)

对待错误的两种方式
传统的错误防止方式:
生产中人为错误是主因,这是很多质量学者和公司管理 层很早就认识到的,长期以来,一直被各大公司沿用的防止 人为错误的主要措施是“培训与惩罚”,即对作业者进行大 量培训,管理人员每每劝戒作业者工作要更加认真和努力, 确实,通过培训,可以避免相当一部分人为错误,比如由对过 程/作业不熟悉,缺乏工作经验、缺乏适当的作业指导所导 致的错误。但由于人为疏忽、忘记等所造成的错误却很难防 止。经长期以来的大量实践及质量学者研究发现:惩罚与教 育相结合的防错方式并不怎么成功。
生“错误”。 (6)紧急事态时的对策。
人因“错误”的预防:
(二)设备方面的对策 (1)要根据人体特性来设计设备或系统。 (2)设备或系统设计,要贯彻“简单”的设计原则,以
便减少和防止差错和事故。 (3)合理安排显示器、控制器。 (4)对于重要的设备或系统.可以使用联锁装置、故障
安全装置、自动安全装置等安全性设计的方法,确保安全。 (5)通过设置防护装置把人与生产中危险部分隔离。 (6)科学设计信号装置。 (7)有缺陷的设备、工具及时修理或更换。
0.9831570 0.9666010
98.31570% 96.66010%
不良数ppm 3.40000 67.99780
169.98584 339.94278 679.77001 1698.55870 3394.23231 6773.56683 16842.97291 33398.97364
一辆汽车有多少零部件?
对待错误的两种方式
• 防错的观点。 – 随着技术的发展和客户要求的提高,质量标准也越来越高,很 明显仅靠“培训和惩罚”的传统防错方法所取得的改鄯效果与 新的质量标准相去甚远。为了适应新的质量标准,企业管理人 员须杜绝错误,而要杜绝错误,须首先弄清楚产生错误的根本 原因,然后针对原因采取对策。传统方法可以防止产生错误的 人为原因中的一部分,而因为人为疏忽、忘记等原因所造成的 错误无法靠培训和惩罚来消除。新的防错模式——POKA-YOKE, 其基本原理为:用一套设备或方法使作业者在作业时直接可以 明显发现缺陷或使操作错误后不产生缺陷。作业人员通过 POKA-YOKE完成自我检查,错误会得明白易见,同时,POKAYOKE也保证了必须满足其设定要求,操作才可完成。
防错法的技术与管理原理课件

详细描述
在生产线环境中,防错法可以通过自动化检测、传感器和控制系统等技术手段实现。例 如,通过安装光学传感器检测产品尺寸和外观,当发现异常时自动剔除不合格品,确保 产品质量。此外,还可以采用条形码或RFID技术追踪产品批次和生产过程,及时发现
定制化
针对不同行业和企业的特点, 防错法将更加定制化,以满足 企业的个性化需求。
可持续性
未来的防错法将更加注重可持 续发展,不仅关注生产效率, 还将考虑环境保护和社会责任
。
如何应对防错法的挑战与机遇
持续研发与创新
企业应加大在防错技术研发和创新方 面的投入,不断更新技术和系统,以 应对新的挑战。
提高员工素质
案例三:医疗设备中的防错法应用
要点一
总结词
要点二
详细描述
医疗设备中防错法的应用对于保障患者安全至关重要,通 过智能化监测、报警系统等技术手段降低医疗差错。
在医疗设备领域,防错法可以通过智能化监测、报警系统 等技术手段实现。例如,在医疗影像设备中,采用图像识 别技术自动识别异常病变,提高诊断准确率。同时,在手 术室中采用智能化的手术器械和导航系统,确保手术部位 和操作过程的准确性。此外,还可以通过患者识别和药品 管理等手段防止用药错误和输血不当等医疗差错。
效果评估与改进
对防错措施的实施效果进 行评估,不断改进和完善 防错方案和技术。
设计防错方案
根据错误原因分析结果, 制定相应的防错方案。
选择防错技术
实施防错措施
将防错方案和技术应用到 实际生产过程中。
根据实际情况选择合适的 防错技术。
Part
七步法ppT课件

保证职责和责任人得到了确定和落实
注:实施一项改进/解决问题/防错说到底是一种变化,如果 不能妥善处理将会导致其自身问题的出现
23
第六
计况下采用防错措施
实施计划
• 确定表示改进成功与否的指标 • 持续足够长的时间以消除缺陷
核实现有库存合格可以交付 访问用户以挑选/返工现有的或急需的物料 注意与第三步的关系
3
为何要用七步工作法?
数据
没有确切的事实和数据我们无法解 决问题。没有数据我们只能猜想产 生问题的原因。
工具
质量工具有助于我们组织、理解数 据和事实。
结构
在工作中做到持续突破就需要有逻 辑、有结构的方法。七步工作法为 我们提供了这种结构。
控制计划
确保控制计划得到及时更新 确保控制计划的内容与FMEA一致 确保更改得到交流并得到正确的展开
改进的标志性指标
在第一步确认的故障模式根除了吗? 工作的“质量”提高了吗? 客户满意度提高了吗? 改进过程中有统计证据吗?
28
第七 评估项目以持续改进、表彰团队
步
目的:
通过量化的方法评估消除问题根源的效果,并验证防 止问题重复发生所需的控制方法已经到位,如:
通过验证因果关系的存在确定出起作用和不起作用的项目
整理数据
运用合适的工具来整理数据
柱状图
控制图 能力研究
运行图
排列图 衰退分析
21
第五 进行试验,分析数据,选择解决方案
步
分析数据
哪些模式再现了周期、趋势或轮换变化的出现 差错(故障)的出现与你确定的可能原因一致吗? 数据明确地证实了你对原因的设想吗? 数据向你提出了哪些问题?
(防)防呆法防错法(IE七大手法)

25
防错法简介
交易过程常见失误: 交易过程常见失误有以下几类: 文件中漏掉重要信息; 文件中存在错误信息; 文件中存在与该交易无关的重要信息。
26
防错法简介
三类检测方法和区别:
检测是进行质量控制的有效手段,根据检测的性质及进行检
测的阶段,可将其分为三类:
1、判断型检测:
判断型检测是指在通过对产品的检测和挑选,以将不合
参加试验的人最终的结果显而易见......!
5
前言
墨菲定律: 如果坏事有可能发生,不管这种可能性多么小,它总会发 生,并引起最大可能的损失。 错误在有可能出现时,就一定会出现。 问题总是出现在最坏的时候。
6
前言
99.9%的正确率意味着什么? 每天北京机场有一次飞机着陆是不安全的! 每年发生两万起药物处方错误! 每天发生50起新生婴儿掉在地上的事件! 每小时发生两万起支票帐户的错误! 一个人一生出现三万二千次心跳异常! 代表我们每月最少报废100台冰箱!
19
防错法简介
产生失误的一般原因:
5、故意失误:
出于某种原因,作业者有意造成的失误,如被组长骂了,
心里很不爽,故意不打螺丝、不放垫片等。
6、疏忽:
这类失误是由于作业者不小心所造成,失误的很大一部
分是由此类原因造成,如晚上没有休息好,精神状态差。
7、行动迟缓:
由于作业人员判断或决策能力过慢而导致的失误,如锡
17
防错法简介
产生失误的一般原因: 2、对过程/作业不熟悉: 由于不熟悉作业过程或步骤,产生失误就很难避免,如 让一个刚经过培训的新手去做焊接工序,产生失误的概率比 熟手肯定大得多。
18
防错法简介
(防)防呆法防错法(IE七大手法)

防错法的原理
Poka-Yoke的特点:
(1)全检产品,但不增加作业者负担; (2)必须满足防错/防呆规定操作要求,方可成功; (3)低成本/低投入; (4)实时发现失误,实时反馈。
比较可知,传统防错方式通过培训和惩 罚解决了部分失误,而防错/防呆可以从根 本上解决失误问题。
36
防错法的原理
Poka-Yoke的四种模式: 在防错针对不同的过程和失误类别,分别采用不同的防错模 式,分别是:
防错IE防法七呆(大P手法o法ka-Yoke)
IE七大手法
演讲者:
1
目录
IE七大手法:
(1)防呆法/防错法(Fool-Proof) (2)动作改善法(动作经济原则) (3)流程程序法
防呆法
动改法
流程法
(4)5 × 5W1H(5X5何法) (5)人机配合法(多动作法) (6)双手操作法 (7)工作抽查法
槽焊接时间为3秒之内,而作业员5秒后才将漆包线从锡槽内
拿出,而导致绝缘不良。
20
防错法简介
产生失误的一般原因:
8、缺乏适当的作业指导: 由于缺乏作业指导或作业指导不当,发生失误的概率是
相当大的。如装配机壳,假设正确的装配方法是先预装一颗 螺丝,后预装对角螺丝,第三步预装其余螺丝中的一个,如 作业指导为随机装配螺丝,则可能发生装配间隙等失误。 9、突发事件:
7
前言
0.1%的错误率又意味着什么?
8
前言
防错法的精髓: 一个世界500强的日用品生产商,在制造香皂的生产线上
发现会有没有香皂的空盒子从流水线上流入包装箱,造成客 户投诉,于是工厂立即为此成立一个课题来解决这个问题, 问题最终获得解决!
在最后一段流水线增加了一个称重装置,并能自动将重 量超出设定公差的包装盒剥离流水线,经过一段时间的监视 使用,最后成功关闭了该问题,并做了创意课题在整个集团 中分享。
产品设计和制造过程的差错预防

防错技术应用:
员工在生产操作过程中,每天对同一个动作进行论百上千遍的操作,一年下来就有几十万遍的记录,大量的重复操作没有一次产生错误简直就是“奇迹”,但客户不会因为我们出现一次或几次质量问题而原谅我们,而是没有回旋的余地,我们如何保证员工在长久的操作过程中不出现问题呢?愚巧化管理,就是所谓的防错技术管理,通过防错技术的应用,保证企业员工在任何情况下也不会犯错误,防错技术有很强的工程技术特色,也包含有管理的思想和理念在里面,是一项系统的工程。
防錯法的应用
防错法:——防愚法
防止愚笨的人做错事,也就是说,连愚笨的人也不会做错的设计方案。
狹义:如何设计一个东西(一套方法),使错误绝不会发生.
广义:如何设计一个东西(一套方法),而使错误发生的机会减至最低的程度.
因此,更具体的说”防错法”是:
1>. 具有即使有人为疏忽也不会发生错误的构造—不需要注意力
2>. 具有外行人来做也不会做错的构造—不需要经验与直觉
3>. 具有不管是谁或在何时工作都能不出差错的构造—不需要专门知识与高度的技能2.作用
1>. 使任何的错误绝不会发生。
2>. 使错误发生的机會减至最低程度。
根据重量根据尺寸根据形状
加工过程程序化方法:
工序到工序的程序方法(顺序方法):
用计数器零散零件剔出方法临界条件的检测。
36.防呆法防错法(IE七大手法)

7
前言
0.1%的错误率又意味着什么?
8
前言
防错法的精髓: 一个世界500强的日用品生产商,在制造香皂的生产线上
发现会有没有香皂的空盒子从流水线上流入包装箱,造成客
户投诉,于是工厂立即为此成立一个team来解决这个问题, 问题最终获得解决! 在最后一段流水线增加了一个称重装置,并能自动将重 量超出设定公差的包装盒剥离流水线,经过一段时间的监视 使用,最后成功关闭了该问题,并做了Success story在整个 集团中分享。
18
防错法简介
产生失误的一般原因: 3、识别错误:
识别错误是对工作指令或程序判断或理解错误所致。如
作业指导书说明烧焊时必须预热到铜管变成鲜红色,但焊工 却误以为预热一下就可以了。 4、缺乏工作经验: 由于缺乏工作经验,很容易产生失误,如,让一个从未 在企业中做过的人去进行制造过程管理,就比较容易产生失 误。
3
前言
4
前言
在1949年美国空军的一项火箭发射计划中,需要做一个
人体试验,试验的内容是测验一个人的身体对速度增加能有
多大容限。测验之一,是用一套16个“加速表”装在被验者 身体的各部分。这些仪器有对与不对两种装法,果不其然, 负责装配的那位员工,把16件仪器统统都装错了。 参加试验的人最终的结果显而易见......!
物质属性,采用的一种硬件防错模式。 如,电饭煲中的感应开关即为一种有形Poka-Yoke防错模式。
如果电饭煲中未加入水,加热开关就无法设定至加热位置,只有加
水,加热开关方可打至加热位置。
42
防错法的原理
Poka-Yoke的四种模式: 2、有序Poka-Yoke防错:
有序Poka-Yoke防错模式是针对过程操作步骤,对其顺序进行
企业推行精益管理做好这10步防错
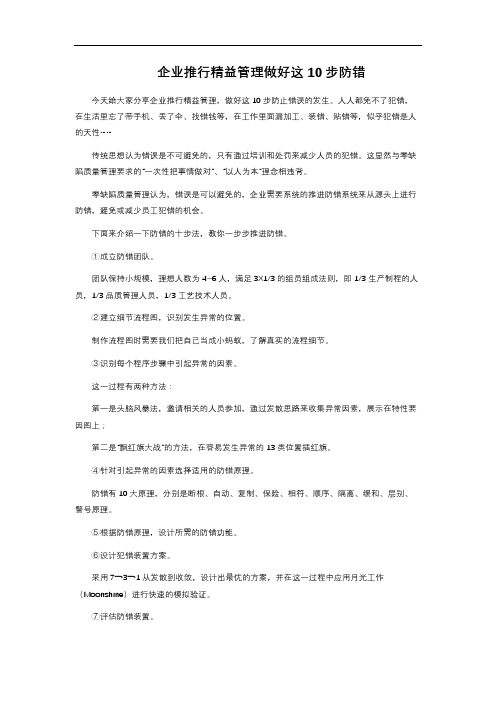
企业推行精益管理做好这10步防错今天给大家分享企业推行精益管理,做好这10步防止错误的发生。
人人都免不了犯错,在生活里忘了带手机、丢了伞、找错钱等,在工作里面漏加工、装错、贴错等,似乎犯错是人的天性……传统思想认为错误是不可避免的,只有通过培训和处罚来减少人员的犯错。
这显然与零缺陷质量管理要求的“一次性把事情做对”、“以人为本”理念相违背。
零缺陷质量管理认为,错误是可以避免的,企业需要系统的推进防错系统来从源头上进行防错,避免或减少员工犯错的机会。
下面来介绍一下防错的十步法,教你一步步推进防错。
①成立防错团队。
团队保持小规模,理想人数为4~6人,满足3X1/3的组员组成法则,即1/3生产制程的人员,1/3品质管理人员,1/3工艺技术人员。
②建立细节流程图,识别发生异常的位置。
制作流程图时需要我们把自己当成小蚂蚁,了解真实的流程细节。
③识别每个程序步骤中引起异常的因素。
这一过程有两种方法:第一是头脑风暴法,邀请相关的人员参加,通过发散思路来收集异常因素,展示在特性要因图上;第二是“飘红旗大战”的方法,在容易发生异常的13类位置插红旗。
④针对引起异常的因素选择适用的防错原理。
防错有10大原理,分别是断根、自动、复制、保险、相符、顺序、隔离、缓和、层别、警号原理。
⑤根据防错原理,设计所需的防错功能。
⑥设计犯错装置方案。
采用7→3→1从发散到收敛,设计出最优的方案,并在这一过程中应用月光工作(Moonshine)进行快速的模拟验证。
⑦评估防错装置。
通过10项评估法则来评估防错装置,这一过程需要进行“恶心试验”,来评估它可以防止错误重复发生么?靠近发生点么?减轻员工负荷么?成本够低么?是经过团队思考过的解决方案么?易于使用么?安全么?能简单实施么?容易维护么?耐用么?⑧制作使用防错装置,并把它添加到质量控制计划中去。
⑨通过验证岗位测量其效力。
新增或修改的防错装置,需要在其制程后面增加验证岗位,连续验证是否满足防错的要求。
防呆法防错法(IE七大手法)

防呆法防错法(IE七大手法)
17 17
防错法简介
产生失误的一般原因: 2、对过程/作业不熟悉:
由于不熟悉作业过程或步骤,产生失误就很难避免,如 让一个刚经过培训的新手去做焊接工序,产生失误的概率比 熟手肯定大得多。
防呆法防错法(IE七大手法)
18 18
防错法简介
产生失误的一般原因:
3、识别错误: 识别错误是对工作指令或程序判断或理解错误所致。如
防错IE防法七呆(大P手法o法ka-Yoke)
IE七大手法
防呆法防错法(IE七大手法)
演讲者:
11
目录
IE七大手法:
(1)防呆法/防错法(Fool-Proof)
防呆法
(2)动作改善法(动作经济原则) (3)流程程序法
动改法
流程法
(4)5 × 5W1H(5X5何法) (5)人机配合法(多动作法)
五五法 人机法
防呆法防错法(IE七大手法)
88
前言
防错法的精髓:
一个世界500强的日用品生产商,在制造香皂的生产线上 发现会有没有香皂的空盒子从流水线上流入包装箱,造成客 户投诉,于是工厂立即为此成立一个课题来解决这个问题, 问题最终获得解决!
在最后一段流水线增加了一个称重装置,并能自动将重 量超出设定公差的包装盒剥离流水线,经过一段时间的监视 使用,最后成功关闭了该问题,并做了创意课题在整个集团 中分享。
失误 漏打减震胶 漏检 漏打螺丝 漏贴铭牌
缺陷 整车异响 外观凹花伤等 顶盖松动、卡条松脱 少铭牌,客户投诉
防呆法防错法(IE七大手法)
因为失误是造成缺陷的 原因,故可通过消除或 控制失误来消除缺陷。
16 16
防错法简介
产生失误的一般原因: 产生失误的基本原因有以下九个: 1、忘记: 即忘记了作业或检查步骤,比如忘记在打中门铰螺丝之 前先装上垫片。
- 1、下载文档前请自行甄别文档内容的完整性,平台不提供额外的编辑、内容补充、找答案等附加服务。
- 2、"仅部分预览"的文档,不可在线预览部分如存在完整性等问题,可反馈申请退款(可完整预览的文档不适用该条件!)。
- 3、如文档侵犯您的权益,请联系客服反馈,我们会尽快为您处理(人工客服工作时间:9:00-18:30)。
防错管理技术七步法
防错技术是实践性很强的改进方法,主要依靠现场工作人员的经验来发现和实施。
这在很大程度上妨碍了防错技术的技术的推广实施。
第0步:心理准备
1. 通过持续过程改善和防错,零缺陷是可以实现的;
2. 防错并不需要大量的资源投入或很高的技术水平;
3. 所有发生错误的场所和过程都可以使用防错;
第1步:识别和描述
1. 详细识别和描述缺陷/红牌条件。
出现缺陷后,考察缺陷的历史。
为明确责任,指派一位团队队员跟踪缺陷/红牌条件;
2. 用FEMA (潜在失效模式分析)的方法对过程进行分析,找出可能发生失误的地方;
3. SPC数据、客户投诉、日常生产问题;
4. 确定产品/ 服务缺陷并收集数据;
5. 追溯缺陷的发现工序和产生工序;
6. 确认缺陷产生工序的作业指导书;
7. 确认实际作业过程与作业指导书之间的差异;
8. 确认工序是否存在问题:
第2步:缺陷分析,确定根本原因
进行因果图分析以评估根本原因。
确定根本原因对应用防错技术以消除缺陷/红旗是至关重要的。
找出缺陷发生的源头,用质量管理七工具和“五个为什么”方法找出根本原因,找出失误和缺陷之间的联系。
第3步:提出防错方案
1. 脑力风暴是一种可以激发小组成员产生大量的有创意的点子的方法。
2. 利用防错装置数据库检索相关的防错装置。
3. 用四种防错方法(信息加强法、接触法、计数法和动作顺序控制法)确定所需用到的防错技术、标准及装置。
第4步:评估选择可行方案
对方案进行成本/ 效益分析,评审行动方案,选择最优方案,在此基础上提出实施计划。
然后确定工序上的更改,选择合适的防错装置,制定责任及时间表,分配所需的资源。
需特别注意的是改进团队要与每一位相关的人员进行交流,使他们了解项目的目的。
第5步:方案实施
尽可能快地实施防错计划。
不要苛求防错方案可以100% 的解决问题,如果有50%的有效性就值得尝试。
第6步:运行和评估
1. 收集数据并与实施前相比较:
2. 操作工是距生产线最近的人,最适合观察记录的工作。
3. 工业工程师进行实地评测
4. 质量工程师跟踪产品质量的变化。
5. 不要急于结束改进小组的工作,改进小组还要定时召开会议,将收集数据并与实施前相比较,检查缺陷是否已经消除并没有新的问题产生。
6. 防错装置的验证:使用新的防错装置时,必须进行功能准确率的验证,预防差错率。
只有通过PPAP(生产件批准程序)方式的验证,方可使用。
第7步:标准化和推广
对防错过程进行评审,前面的过程和结果进行总结、归档并补充数据库,探讨方案能否复制、推广其它类似设备或和生产厂。
特别要强调的是改进工作的标准化。
为了更好地普及防错技术,一方面需要不断积累已有的应用案例,另外一方面还要考虑提供一个一般性的改进实施流程,帮助大家发现和解决问题,避免走弯路。