液压传动系统设计与计算 说明书
液压与气压传动课程设计说明书

液压与气压传动课程设计说明书液压与气压传动课程设计说明书一、课程设计目的:本课程设计旨在培养学生对液压与气压传动原理的理解和应用能力,通过实践操作和设计,使学生能够独立完成液压与气压传动系统的设计和优化,提高学生的工程实践能力和综合素质。
二、课程设计内容:1. 液压与气压传动系统的基本原理和工作原理;2. 液压系统的设计方法和步骤;3. 气压系统的设计方法和步骤;4. 液压与气压传动系统的组成和结构设计;5. 液压与气压传动系统的参数优化和调试;6. 液压与气压传动系统的故障分析和排除。
三、课程设计要求:1. 学生需要独立完成一个液压传动系统和一个气压传动系统的设计和优化;2. 设计过程中需要合理选择和搭配液压和气压元件,并进行参数计算和模拟仿真;3. 设计结果需要满足给定的工作要求和性能指标,并经过实践验证和调试;4. 设计过程中需要考虑系统的安全性、可靠性和经济性。
四、课程设计步骤:1. 确定液压传动系统和气压传动系统的工作要求和性能指标;2. 研究液压传动系统和气压传动系统的工作原理和结构组成;3. 选择和搭配液压和气压元件,并进行参数计算和模拟仿真;4. 设计液压传动系统和气压传动系统的结构和布置;5. 进行液压传动系统和气压传动系统的组装和调试;6. 验证设计结果和性能指标,并进行优化和改进;7. 撰写课程设计报告,总结设计过程和结果。
五、课程设计评分标准:1. 设计过程的完整性和合理性(30%);2. 设计结果的准确性和满足性能指标(30%);3. 实践操作和调试的技能和效果(20%);4. 课程设计报告的撰写和总结能力(20%)。
六、参考资料:1. 《液压与气压传动技术手册》;2. 《液压与气压传动系统设计与仿真实例》;3. 《液压与气压传动系统设计与应用》;4. 《液压与气压传动系统故障分析与排除》。
以上是液压与气压传动课程设计的说明书,希望能对你有所帮助。
液压机液压传动与控制系统设计手册
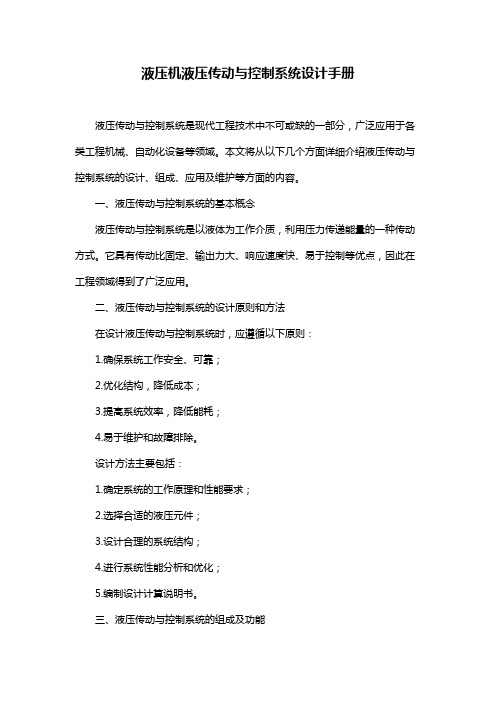
液压机液压传动与控制系统设计手册液压传动与控制系统是现代工程技术中不可或缺的一部分,广泛应用于各类工程机械、自动化设备等领域。
本文将从以下几个方面详细介绍液压传动与控制系统的设计、组成、应用及维护等方面的内容。
一、液压传动与控制系统的基本概念液压传动与控制系统是以液体为工作介质,利用压力传递能量的一种传动方式。
它具有传动比固定、输出力大、响应速度快、易于控制等优点,因此在工程领域得到了广泛应用。
二、液压传动与控制系统的设计原则和方法在设计液压传动与控制系统时,应遵循以下原则:1.确保系统工作安全、可靠;2.优化结构,降低成本;3.提高系统效率,降低能耗;4.易于维护和故障排除。
设计方法主要包括:1.确定系统的工作原理和性能要求;2.选择合适的液压元件;3.设计合理的系统结构;4.进行系统性能分析和优化;5.编制设计计算说明书。
三、液压传动与控制系统的组成及功能液压传动与控制系统主要由以下几部分组成:1.动力元件:如液压泵、电动机等;2.执行元件:如液压缸、液压马达等;3.控制元件:如阀门、压力开关等;4.辅助元件:如油箱、管路、接头等;5.传感器:如压力、流量、温度传感器等。
各部分功能如下:1.动力元件:为系统提供压力油;2.执行元件:将压力油转换为线性或旋转运动;3.控制元件:调节系统油液的流量、压力、流向等;4.辅助元件:保证系统油液的清洁、冷却、密封等;5.传感器:实时监测系统工作状态,为控制系统提供反馈信号。
四、液压传动与控制系统的设计步骤1.确定设计任务和要求;2.选择合适的液压元件;3.设计系统原理图;4.进行系统性能计算和分析;5.编制设计计算说明书;6.绘制设计图纸;7.审核和验收。
五、液压传动与控制系统的应用领域液压传动与控制系统在以下领域得到广泛应用:1.工程机械:如挖掘机、推土机等;2.自动化设备:如机器人、生产线等;3.交通运输:如汽车、船舶等;4.航空航天:如飞行器、卫星等;5.军事领域:如装甲车辆、舰艇等。
液压挖掘机液压系统设计说明书

前言挖掘机作为一种多功能机械产品,目前被广泛应用于水利工程,交通运输,电力工程和矿山采掘等机械施工中。
它能在减轻繁重的体力劳动,保证工程质量,加快工程建设速度以及提高劳动生产率方面起着十分重要的作用。
近年从国内情况来看,我国的挖土机市场90%被外国独资或合资企业垄断,我国挖土机行业整体发展水平较国外缓慢,在挖土机液压系统方面的理论还相对国外比较薄弱。
国内大部分挖土机企业在挖土机液压系统传统技术方面的研究具有一定基础,但由于采用传统液压系统的挖土机产品在性能、质量、作业效率、可靠性等方面均较差,因此采用传统液压系统的挖土机在国内市场上基本失去了竞争力。
液压系统是挖土机的核心部分,通过挖土机液压系统设计计算优化能有效的提高挖土机性能,本挖土机具有工作可靠、结构简单、性能好、成本低、效率高等特点。
我国是一个发展中国家,在辽阔的国土上正在进行大规模的经济建设,这就需要大量的土石方施工机械为其服务,而液压挖掘机是最重要的一类土石方施工机械。
因此,可以肯定液压挖掘机的发展空间很大.可以预见,随着国家经济建设的不断发展,液压挖掘机的需求量将逐年大幅度增长.今后几年我国液压挖掘机行业将会有一个很大的发展,液压挖掘机的年产量将会以高于20%的速度增长。
本设计根据给定的工作要求进行工况分析,以确定系统的主要参数,对液压系统的基本回路的方案进行分析,拟订液压系统原理图;选择液压元件并进行液压系统的性能验算,最后完成工作图,编制技术文件。
希望本设计能为从事液压工作的人员献上微薄之力!摘要液压挖掘机是工程机械的一个重要品种,是一种广泛用于建筑、铁路、公路、水利、采矿等建设工程的土方机械。
液压挖掘机利用液压元件(液压泵、液压马达、液压缸等)带动各种构件动作,具有许多优点。
它对液压系统的设计提出很高的要求,其液压系统也是工程机械液压系统中最为复杂的。
因此,对挖掘机液压系统的分析设计对推动我国挖掘机发展具有十分重要的意义。
在搜集了国内外挖掘机液压系统相关资料的基础上,了解了挖掘机液压系统的发展历史,并对挖掘机液压系统的技术发展动态进行了分析总结.本次毕业设计课题是挖掘机液压系统的设计。
液压传动系统的设计与计算
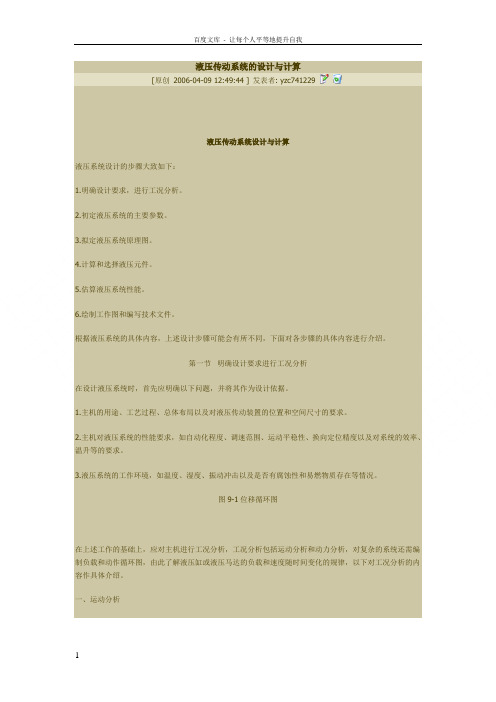
液压传动系统的设计与计算[原创2006-04-09 12:49:44 ] 发表者: yzc741229液压传动系统设计与计算液压系统设计的步骤大致如下:1.明确设计要求,进行工况分析。
2.初定液压系统的主要参数。
3.拟定液压系统原理图。
4.计算和选择液压元件。
5.估算液压系统性能。
6.绘制工作图和编写技术文件。
根据液压系统的具体内容,上述设计步骤可能会有所不同,下面对各步骤的具体内容进行介绍。
第一节明确设计要求进行工况分析在设计液压系统时,首先应明确以下问题,并将其作为设计依据。
1.主机的用途、工艺过程、总体布局以及对液压传动装置的位置和空间尺寸的要求。
2.主机对液压系统的性能要求,如自动化程度、调速范围、运动平稳性、换向定位精度以及对系统的效率、温升等的要求。
3.液压系统的工作环境,如温度、湿度、振动冲击以及是否有腐蚀性和易燃物质存在等情况。
图9-1位移循环图在上述工作的基础上,应对主机进行工况分析,工况分析包括运动分析和动力分析,对复杂的系统还需编制负载和动作循环图,由此了解液压缸或液压马达的负载和速度随时间变化的规律,以下对工况分析的内容作具体介绍。
一、运动分析主机的执行元件按工艺要求的运动情况,可以用位移循环图(L—t),速度循环图(v—t),或速度与位移循环图表示,由此对运动规律进行分析。
1.位移循环图L—t图9-1为液压机的液压缸位移循环图,纵坐标L表示活塞位移,横坐标t表示从活塞启动到返回原位的时间,曲线斜率表示活塞移动速度。
该图清楚地表明液压机的工作循环分别由快速下行、减速下行、压制、保压、泄压慢回和快速回程六个阶段组成。
2.速度循环图v—t(或v—L)工程中液压缸的运动特点可归纳为三种类型。
图9-2为三种类型液压缸的v—t图,第一种如图9-2中实线所示,液压缸开始作匀加速运动,然后匀速运动,图9-2 速度循环图最后匀减速运动到终点;第二种,液压缸在总行程的前一半作匀加速运动,在另一半作匀减速运动,且加速度的数值相等;第三种,液压缸在总行程的一大半以上以较小的加速度作匀加速运动,然后匀减速至行程终点。
液压传动设计手册煤炭工业部
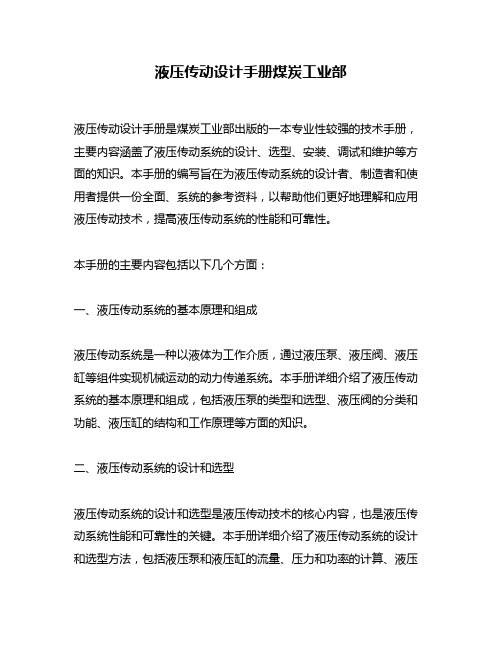
液压传动设计手册煤炭工业部液压传动设计手册是煤炭工业部出版的一本专业性较强的技术手册,主要内容涵盖了液压传动系统的设计、选型、安装、调试和维护等方面的知识。
本手册的编写旨在为液压传动系统的设计者、制造者和使用者提供一份全面、系统的参考资料,以帮助他们更好地理解和应用液压传动技术,提高液压传动系统的性能和可靠性。
本手册的主要内容包括以下几个方面:一、液压传动系统的基本原理和组成液压传动系统是一种以液体为工作介质,通过液压泵、液压阀、液压缸等组件实现机械运动的动力传递系统。
本手册详细介绍了液压传动系统的基本原理和组成,包括液压泵的类型和选型、液压阀的分类和功能、液压缸的结构和工作原理等方面的知识。
二、液压传动系统的设计和选型液压传动系统的设计和选型是液压传动技术的核心内容,也是液压传动系统性能和可靠性的关键。
本手册详细介绍了液压传动系统的设计和选型方法,包括液压泵和液压缸的流量、压力和功率的计算、液压阀的选型和配置、液压管路的设计和布置等方面的知识。
三、液压传动系统的安装和调试液压传动系统的安装和调试是液压传动技术的重要环节,也是液压传动系统性能和可靠性的保证。
本手册详细介绍了液压传动系统的安装和调试方法,包括液压系统的安装和布置、液压元件的连接和调试、液压系统的启动和运行等方面的知识。
四、液压传动系统的维护和保养液压传动系统的维护和保养是液压传动技术的重要环节,也是液压传动系统性能和可靠性的保证。
本手册详细介绍了液压传动系统的维护和保养方法,包括液压系统的清洗和检修、液压元件的更换和维修、液压油的更换和保养等方面的知识。
总之,液压传动设计手册是一本涵盖了液压传动系统设计、选型、安装、调试和维护等方面知识的专业性较强的技术手册,对于液压传动技术的研究和应用具有重要的参考价值。
液压传动系统设计与计算-说明书
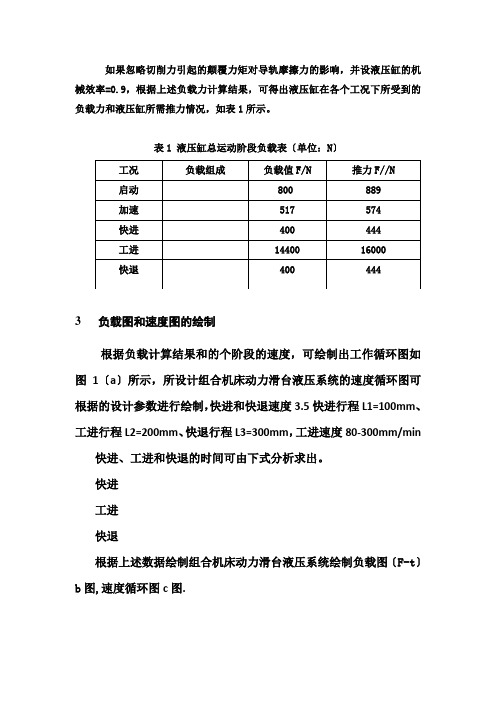
如果忽略切削力引起的颠覆力矩对导轨摩擦力的影响,并设液压缸的机械效率=0.9,根据上述负载力计算结果,可得出液压缸在各个工况下所受到的负载力和液压缸所需推力情况,如表1所示。
表1 液压缸总运动阶段负载表〔单位:N〕3 负载图和速度图的绘制根据负载计算结果和的个阶段的速度,可绘制出工作循环图如图1〔a〕所示,所设计组合机床动力滑台液压系统的速度循环图可根据的设计参数进行绘制,快进和快退速度3.5快进行程L1=100mm、工进行程L2=200mm、快退行程L3=300mm,工进速度80-300mm/min 快进、工进和快退的时间可由下式分析求出。
快进工进快退根据上述数据绘制组合机床动力滑台液压系统绘制负载图〔F-t〕b图,速度循环图c图.ab c在此处键入公式。
4 确定液压系统主要参数4.1确定液压缸工作压力由表2和表3可知,组合机床液压系统在最大负载约为16000时宜取3MPa。
表2按负载选择工作压力表3 各种机械常用的系统工作压力4.2计算液压缸主要结构参数根据参数,液压缸无杆腔的有效作用面积可计算为A1=Fmas/P1-0.5P2=16000/3X10^6那么活塞直径为mm根据经验公式,因此活塞杆直径为d=58.3mm,根据GB/T2348—1993对液压缸缸筒内径尺寸和液压缸活塞杆外径尺寸的规定,圆整后取液压缸缸筒直径为D=80mm,活塞杆直径为d=56mm。
此时液压缸两腔的实际有效面积分别为:根据计算出的液压缸的尺寸,进一步计算液压缸在各个工作阶段中的压力、流量和功率值,如表4所示。
表4 各工况下的主要参数值5 液压系统方案设计根据组合机床液压系统的设计任务和工况分析,所设计机床对调速范围、低速稳定性有一定要求,因此速度控制是该机床要解决的主要问题。
速度的换接、稳定性和调节是该机床液压系统设计的核心。
此外,与所有液压系统的设计要求一样,该组合机床液压系统应尽可能结构简单,本钱低,节约能源,工作可靠5.1确定调速方式及供油形式由表4可知,该组合机床工作时,要求低速运动平稳行性好,速度负载特性好。
液压传动课程设计

【液压传动课程设计说明书设计题目:半自动液压专用铣床液压系统[工程技术系机械设计制造及其自动化4班。
设计者指导教师2016 年 12 月 1 日摘要、液压系统设计计算是液压传动课程设计的主要内容,包括明确设计要求进行工况分析、确定液压系统主要参数、拟定液压系统原理图、计算和选择液压件以及验算液压系统性能等。
现以半自动液压专用铣床液压系统为例,介绍液压系统的设计计算方法。
设计一台多用途大台面液压机液压系统,适用于可塑材料的压制工艺,如冲压、弯曲翻边、落板拉伸等。
要求该机的控制方式:用按钮集中控制,可实现调整,手动和半自动,自动控制。
要求该机的工作压力、压制速度、空载快速下行和减速的行程范围均可根据工艺要求进行调整。
主缸工作循环为:快降、工作行程、保压、回程、空悬。
顶出缸工作循环为:顶出、顶出回程(或浮动压边)。
关键字:液压; 快进; 工进; 快退{前言本课程是机械设计制造及其自动化专业的主要专业基础课和必修课,是在完成《液压与气压传动》课程理论教学以后所进行的重要实践教学环节。
本课程的学习目的在于使学生综合运用《液压与气压传动》课程及其它先修课程的理论知识和生产实际知识,进行液压传动的设计实践,使理论知识和生产实际知识紧密结合起来,从而使这些知识得到进一步的巩固、加深和扩展。
通过设计实际训练,为后续专业课的学习、毕业设计及解决工程问题打下良好的基础。
,(1) 液压传动课程设计是一项全面的设计训练,它不仅可以巩固所学的理论知识,也可以为以后的设计工作打好基础。
在设计过程中必须严肃认真,刻苦钻研,一丝不苟,精益求精。
(2) 液压传动课程设计应在教师指导下独立完成。
教师的指导作用是指明设计思路,启发学生独立思考,解答疑难问题,按设计进度进行阶段审查,学生必须发挥主观能动性,积极思考问题,而不应被动地依赖教师查资料、给数据、定方案。
(3) 设计中要正确处理参考已有资料与创新的关系。
任何设计都不能凭空想象出来,利用已有资料可以避免许多重复工作,加快设计进程,同时也是提高设计质量的保证。
液压系统的设计计算步骤和内容

• 最大负载值是初步确定执行元件工作压力和结构尺寸的依据。 • 液压马达的负载力矩分析与液压缸的负载分析相同,只需将上述负载
设计计算
步骤和内容
4~5
>5~7
18
系统工作压力的确定
表9-3 按主机类型选择系统工作压力
设备 类型
磨床
机床
组合机床 牛头刨床
插床 齿轮加工
机床
车床 铣床 镗床
珩磨 拉床 机 龙门 床 刨床
农业机械 汽车工业 小型工程 机械及辅 助机械
工程机械 重型机械 锻压设备 液压支架
船用 系统
压力 /MPa
摆动缸
单叶片缸转角小于300°,双叶片缸转角小于150°
往复摆动运动
齿轮、叶片马达 轴向柱塞马达 径向柱塞马达
结构简单、体积小、惯性小 运动平稳、转大、转速范围宽 结构复杂、转大、转速低
设计计算
步骤和内容
高速小转矩回转运动 大转矩回转运动 低速大转矩回转运动
7
负载分析
• 负载分析就是通过计算确定各液压执行元件的负载大小和方向,并分 析各执行元件运动过程中的振动、冲击及过载能力等情况。
设计计算
步骤和内容
2
1.1 液压系统的设计依据和工况分析
液压系统的设计依据
• 设计要求是进行工程设计的主要依据。设计前必须把主机对液压系统 的设计要求和与设计相关的情况了解清楚,一般要明确下列主要问题:
液压传动课程设计指导书-新

液压传动课程设计任务书指导书学生班级学生姓名指导教师设计日期扬州大学机械工程学院液压传动课程设计任务书一、设计课题1.设计一台专用卧式铣床液压系统,要求实现“夹紧→快进→工进→快退→原位停止→松开” 的自动工作循环。
夹紧力为3500N ,工作缸的最大有效行程为400mm 工作行程为200mm ,工作台自重3000N ,工件及液压夹具最大重量为1000N ,取静摩擦系数0.25s f =,动摩擦系数0.1d f =,缸的机械效率0.9m η=,启动或制动时间0.25t s ∆=,夹紧行程20mm ,夹紧时间1s ,其余参数见表1。
表12.设计一台卧式专用钻床液压系统,此系统应能完成“夹紧→快进→工进→死挡铁停留→快退→原位停止→松开”的自动工作循环。
快速进给行程200mm ,工作进给行程50mm ,夹紧力为4000N ,工作台自重2000N ,工件及液压夹具最大重量为1500N 静摩擦系数0.25s f =,动摩擦系数0.1d f =,取缸的机械效率0.9m η=,启动或制动时间0.25t s ∆=,夹紧行程20mm ,夹紧时间1s ,其余参数见表2。
表23.设计一台卧式专用镗床液压系统,工作循环是“夹紧→快进→一工进→二工进→快退→原位停止→松开”的自动工作循环。
快进快退速度均为4.5/min m ,快进行程为200mm ,一工进行程为40mm ,二工进行程为40mm ,夹紧力为5000N ,工作台自重2000N ,工件及液压夹具最大重量为1000N 取静摩擦系数0.25s f =,动摩擦系数0.1d f =,取缸的机械效率0.9m η=,启动或制动时间0.25t s ∆=,夹紧行程20mm ,夹紧时间1s ,其余参数见表3。
表3二、设计计算内容1.设计计算液压系统包括液压系统的拟定,液压缸的设计,液压元件及电机的选择;液压站的设计。
2.编写设计计算说明书包括设计任务,设计计算过程,液压系统原理图,液压元件一览表。
300T液压机液压系统设计说明书
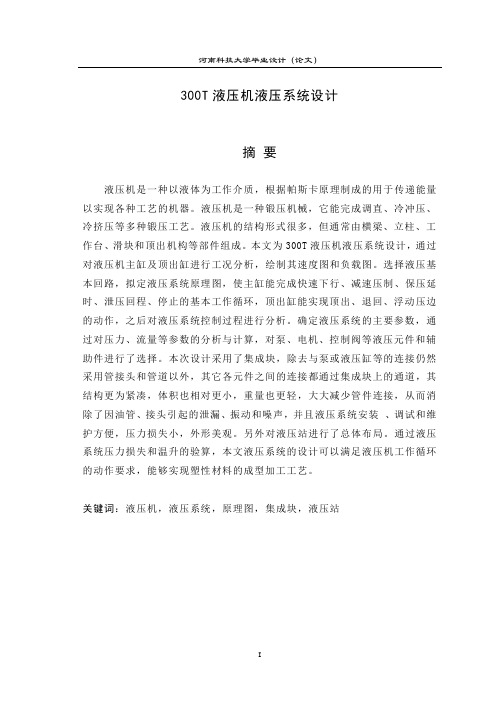
300T液压机液压系统设计摘要液压机是一种以液体为工作介质,根据帕斯卡原理制成的用于传递能量以实现各种工艺的机器。
液压机是一种锻压机械,它能完成调直、冷冲压、冷挤压等多种锻压工艺。
液压机的结构形式很多,但通常由横梁、立柱、工作台、滑块和顶出机构等部件组成。
本文为300T液压机液压系统设计,通过对液压机主缸及顶出缸进行工况分析,绘制其速度图和负载图。
选择液压基本回路,拟定液压系统原理图,使主缸能完成快速下行、减速压制、保压延时、泄压回程、停止的基本工作循环,顶出缸能实现顶出、退回、浮动压边的动作,之后对液压系统控制过程进行分析。
确定液压系统的主要参数,通过对压力、流量等参数的分析与计算,对泵、电机、控制阀等液压元件和辅助件进行了选择。
本次设计采用了集成块,除去与泵或液压缸等的连接仍然采用管接头和管道以外,其它各元件之间的连接都通过集成块上的通道,其结构更为紧凑,体积也相对更小,重量也更轻,大大减少管件连接,从而消除了因油管、接头引起的泄漏、振动和噪声,并且液压系统安装、调试和维护方便,压力损失小,外形美观。
另外对液压站进行了总体布局。
通过液压系统压力损失和温升的验算,本文液压系统的设计可以满足液压机工作循环的动作要求,能够实现塑性材料的成型加工工艺。
关键词:液压机,液压系统,原理图,集成块,液压站THE DESIGN OF 300T HYDRAULIC PRESS' HYDRAULICSYSTEMABSTRACTHydraulic presses are machines that use liquid as working medium and are made according to the principle of PASCAL to deliver energy to achieve various processes. Hydraulic presses are metal forming machines which can complete various forging technology such as alignment, cold forging, cold extruding and so on. Hydraulic presses have many structural forms but more often than not they are composed of crossbeam, vertical post, work table, slide block and ejector parts. This paper is about the design of 300T hydraulic press's hydraulic system, though the condition analysis of the hydraulic press's main cylinder and ejection cylinder, we can draw their velocity diagrams and load diagrams. Then we choose basic hydraulic circuit to form the hydraulic system schematics. We must make sure the main cylinder can complete the basic working cycle of fast descending, deceleration repression, time delay of press forming, relinef-pressure return and stop, and on the other hand, ejection cylinder can realize the action of ejection, return and floating side pressing. After that, we must analyse the control process of the hydraulic system. Hydraulic system's main parameters are determined and through the analysis and calculation of pressure, flow and other parameters, and then we can go on the choose hydraulic components and auxiliary parts such as pump , motor, filters, control valves. This design adopted the manifold block, and except that the connection of pump and hydraulic cylinder still uses the pipes and pipe joints, the connection of other components all through the channel of the manifold block. Its structure is more compact, volume is relatively smaller, its weight is lighter without pipe connection. What's more, it can eliminate leakage of tubing, connectors,vibration and noise, also, the installation, commissioning and maintenance of hydraulic systrem are convenient, low pressure drop, and it looks more beautiful.The paper has also designed the overall layout of the hydraulic station.what is more this paper have three-dimensional graph of integrated block, hydraulic pressure station, which make it more beautiful and accessible to reader. The hydraulic system can meet the press order cycle action requires and realize the plastic material forging press, stamping cold extrusion, straightening, bending forming process and other contour machining technic through check calculation of hydraulic system pressure loss and the temperature of the hydraulic system.KEYWORDS:hydraulic press, hydraulic system, system diagram,manifold block, hydraulic station目录前言 ................................................................. 错误!未定义书签。
液压传动课程设计说明书

目录1 课程设计的目的和基本要求 .................................................................... - 1 -(1)课程设计的目的................................................................................. - 1 -(2) 课程设计的基本要求......................................................................... - 1 - 2 课程设计的主要内容 ................................................................................ - 1 -(1) 课程设计题目..................................................................................... - 1 -(2) 课程设计要完成的主要内容............................................................. - 1 -3 液压系统设计方法 .................................................................................... - 2 -3.1 明确设计依据,进行工况分析....................................................... - 2 -3.1.1设计依据........................................................................................ - 2 -3.1.2工况分析........................................................................................ - 2 -3.2 确定系统方案,拟定液压系统图................................................... - 4 -3.2.1 确定系统方案............................................................................... - 4 -3.2.2 拟定液压系统图........................................................................... - 6 -3.3 液压元件的计算和选择................................................................... - 8 -3.3.1 执行元件主要参数的计算......................................................... - 8 -3.3.2 执行元件所需流量..................................................................... - 11 -3.3.3 作出执行元件工况循环图......................................................... - 11 -3.3.4 选定油泵和确定电动机功率................................................... - 12 -3.3.5 选择控制元件........................................................................... - 13 -3.3.6 选择辅助元件............................................................................. - 14 -3.4 液压系统验算及质术文件的编制................................................. - 17 -(1) 压力损失验算和压力阀的调整压力............................................ - 17 -(2) 油箱容量的验算............................................................................ - 19 -(3) 绘制工作图,编制技术文件........................................................ - 20 -4 课程设计参考题目 .................................................................................. - 21 -液压传动与控制课程设计指导书1 课程设计的目的和基本要求(1)课程设计的目的:《液压传动与控制》课程设计是机械设计制造及其自动化专业学生在学完《流体力学与液压传动》课程之后进行的一个重要的实践性教学环节。
液压系统设计与计算
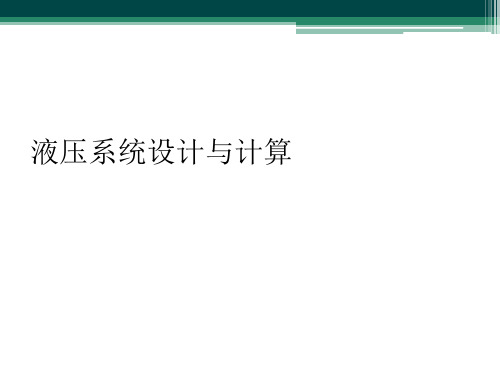
(2)确定执行元件的主要结构参数
以缸为例,主要结构尺寸指缸的内径D和活塞杆的直 径d,计算后按系列标准值确定D和d。
对有低速运动要求的系统,尚需对液压缸有效工作面 积进行验算,即应保证:
式中
A q min v min
(10.8)
:A—液压缸工作腔的有效工作面积;
v m in—控制执行元件速度的流量阀最小稳定流量;
17
1.3.2 选择液压泵
先根据设计要求和系统工况确定泵的类型, 然后根据液压泵的最大供油量和系统工作压力来 选择液压泵的规格。
(1) 液压泵的最高供油压力
ppp pl (10.11)
式中: p—执行元件的最高工作压力;
pl —进油路上总的压力损失。
18
(2)确定液压泵的最大供油量 液压泵的最大供油量为:
khAt (10.15)
式中: A—油箱的散热面积;
t —液压系统的温升;
k h —油箱的散热系数,其值可查阅液压设计手册。
系统的温升为 t kh A
(10.16)
计算温升值如果超过允许值,应采取适当的冷却措施。
27
1.5 绘制正式工作图和编制技术文件
10.1.5.1 绘制正式工作图 正式工作图包括液压系统原理图、液压系统装配图、
30
机床的外形示意图。
1-左主轴头;2-夹具;3-右主轴头;4-床身;5-工件
31
2.1 确定对液压系统的工作要求
根据加工要求,刀具旋转由机械传动来实现;主轴头 沿导轨中心线方向的“快进一工进—快退—停止”工作循环 拟采用液压传动方式来实现。故拟选定液压缸作执行机构。
考虑到车削进给系统传动功率不大,且要求低速稳定 性好,粗加工时负载有较大变化,故拟选用调速阀、变量 泵组成的容积节流调速方式。
液压传动系统设计计算

液压系统的设计步骤与设计要求液压传动系统是液压机械的一个组成部分,液压传动系统的设计要同主机的总体设计同时进行。
着手设计时,必须从实际情况出发,有机地结合各种传动形式,充分发挥液压传动的优点,力求设计出结构简单、工作可靠、成本低、效率高、操作简单、维修方便的液压传动系统。
一、设计步骤液压系统的设计步骤并无严格的顺序,各步骤间往往要相互穿插进行。
一般来说,在明确设计要求之后,大致按如下步骤进行。
1〕确定液压执行元件的形式;2〕进行工况分析,确定系统的主要参数;3〕制定基本方案,拟定液压系统原理图;4〕选择液压元件;5〕液压系统的性能验算;6〕绘制工作图,编制技术文件。
1.1 明确设计要求设计要求是进行每项工程设计的依据。
在制定基本方案并进一步着手液压系统各部分设计之前,必须把设计要求以及与该设计内容有关的其他方面了解清楚。
1〕主机的概况:用途、性能、工艺流程、作业环境、总体布局等;2〕液压系统要完成哪些动作,动作顺序及彼此联锁关系如何;3〕液压驱动机构的运动形式,运动速度;4〕各动作机构的载荷大小及其性质;5〕对调速范围、运动平稳性、转换精度等性能方面的要求;6〕自动化程序、操作控制方式的要求;7〕对防尘、防爆、防寒、噪声、安全可靠性的要求;8〕对效率、成本等方面的要求。
进行工况分析、确定液压系统的主要参数通过工况分析,可以看出液压执行元件在工作过程中速度和载荷变化情况,为确定系统及各执行元件的参数提供依据。
液压系统的主要参数是压力和流量,它们是设计液压系统,选择液压元件的主要依据。
压力决定于外载荷。
流量取决于液压执行元件的运动速度和结构尺寸。
制定基本方案和绘制液压系统图〔1〕制定调速方案液压执行元件确定之后,其运动方向和运动速度的控制是拟定液压回路的核心问题。
方向控制用换向阀或逻辑控制单元来实现。
对于一般中小流量的液压系统,大多通过换向阀的有机组合实现所要求的动作。
对高压大流量的液压系统,现多采用插装阀与先导控制阀的逻辑组合来实现。
液压系统的课程设计说明书
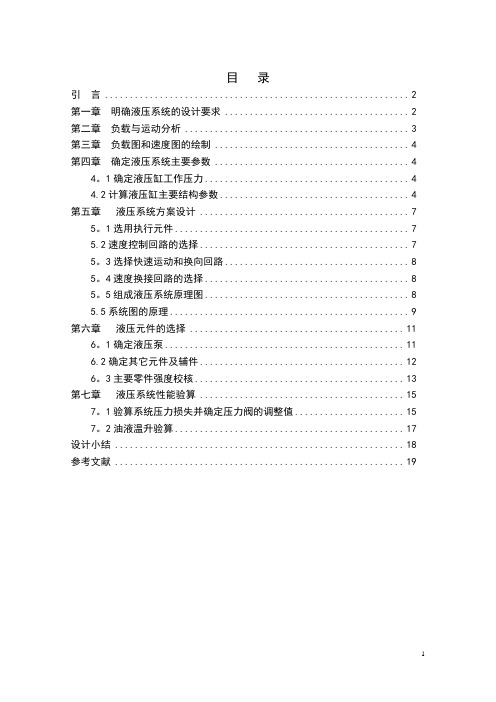
目录引言 (2)第一章明确液压系统的设计要求 (2)第二章负载与运动分析 (3)第三章负载图和速度图的绘制 (4)第四章确定液压系统主要参数 (4)4。
1确定液压缸工作压力 (4)4.2计算液压缸主要结构参数 (4)第五章液压系统方案设计 (7)5。
1选用执行元件 (7)5.2速度控制回路的选择 (7)5。
3选择快速运动和换向回路 (8)5。
4速度换接回路的选择 (8)5。
5组成液压系统原理图 (8)5.5系统图的原理 (9)第六章液压元件的选择 (11)6。
1确定液压泵 (11)6.2确定其它元件及辅件 (12)6。
3主要零件强度校核 (13)第七章液压系统性能验算 (15)7。
1验算系统压力损失并确定压力阀的调整值 (15)7。
2油液温升验算 (17)设计小结 (18)参考文献 (19)引言液压系统已经在各个部门得到越来越广泛的应用,而且越先进的设备,其应用液压系统的部门就越多.液压传动是用液体作为来传递能量的,液压传动有以下优点:易于获得较大的力或力矩,功率重量比大,易于实现往复运动,易于实现较大范围的无级变速,传递运动平稳,可实现快速而且无冲击,与机械传动相比易于布局和操纵,易于防止过载事故,自动润滑、元件寿命较长,易于实现标准化、系列化。
液压传动的基本目的就是用液压介质来传递能量,而液压介质的能量是由其所具有的压力及力流量来表现的。
而所有的基本回路的作用就是控制液压介质的压力和流量,因此液压基本回路的作用就是三个方面:控制压力、控制流量的大小、控制流动的方向。
所以基本回路可以按照这三方面的作用而分成三大类:压力控制回路、流量控制回路、方向控制回路。
第一章明确液压系统的设计要求要求设计一台卧式单面多轴钻孔组合机床动力滑台的液压系统.要求实现的动作顺序为:启动→快进→工进→快退→停止。
液压系统的主要参数与性能要求如下:轴向切削力Ft =20000N,移动部件总质量G=10000N;快进行程l1=100mm,工进行程l2=50mm。
液压传动说明书
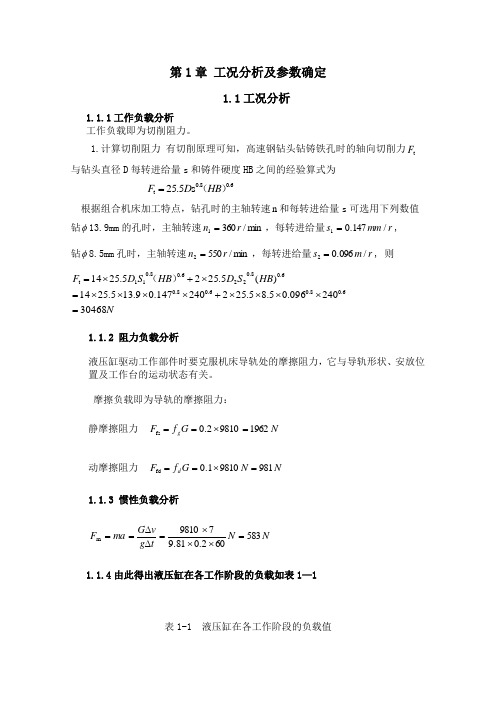
第1章 工况分析及参数确定1.1工况分析1.1.1工作负载分析工作负载即为切削阻力。
1.计算切削阻力 有切削原理可知,高速钢钻头钻铸铁孔时的轴向切削力t F 与钻头直径D 每转进给量s 和铸件硬度HB 之间的经验算式为6.08.0t s 5.25)(HB D F =根据组合机床加工特点,钻孔时的主轴转速n 和每转进给量s 可选用下列数值 钻φ13.9mm 的孔时,主轴转速min /3601r n =,每转进给量r mm s /147.01=,钻φ8.5mm 孔时,主轴转速min /5502r n =,每转进给量r m s /096.02=, 则NHB S D HB S D F 30468240096.05.85.252240147.09.135.2514)(5.2525.25146.08.06.08.06.08.0226.08.011t =⨯⨯⨯⨯+⨯⨯⨯⨯=⨯+⨯=)( 1.1.2 阻力负载分析液压缸驱动工作部件时要克服机床导轨处的摩擦阻力,它与导轨形状、安放位置及工作台的运动状态有关。
摩擦负载即为导轨的摩擦阻力:静摩擦阻力 N G f F g 196298102.0fs =⨯==动摩擦阻力 N N G f F d 98198101.0fd =⨯== 1.1.3 惯性负载分析N N t g v G ma F 583602.081.979810m =⨯⨯⨯=∆∆== 1.1.4由此得出液压缸在各工作阶段的负载如表1—1表1-1 液压缸在各工作阶段的负载值工况 负载组成负载值F (N )推力m F η/(N )启动 fs F F =1962 2180 加速 m fd F F F += 1564 1738 快进 fd F F =981 1090 工进 t fd F F F += 31449 34943 快退 fd F F =9811090注:1.液压缸的机械效率取9.0m =η。
2.不考虑动力滑台上颠覆力矩的作用。
第9章液压系统设计与计算-

• 快进时:
差动系统
p F A1 A2
qv快 (A1A2)
非差动系统
p1
F A1
A2 A1
p2
q v快A1
P pq
•工进时:
p1
A2 A1
F pb A1
q v工A1
P p工q工
• 快退
p1
A2 A1
pb
F A1
qv快退A2
P pq
图9-2 组合机床执行元件工况图
Ff f FN
(9-2)
式中 FN——运动部件及外负载对支撑面的正压力; f——摩擦系数,分 静摩擦系数( fS≤0.2~0.3)和动摩擦系数(fd ≤0.05~0.1)。
(3)惯性负载 Fa 惯性负载是运动部件的速度变化时,由其惯性而产生的负
载,可用牛顿第二定律计算:
Fa
ma Gv g t
液压缸推力F(N)
F =( Ffs + FL ± Fg) /ηm F =( Ffd + FL +Fa± Fg) /ηm F =( Ffd + FL± Fg) /ηm F =( Ffd + FL — Fa± Fg) /ηm F =( Ffd + FL ± Fg) /ηm F =( Ffd + FL — Fa± Fg) /ηm F =( Ffs + Fa ± Fg) /ηm
来验பைடு நூலகம்,即
A q min v min
(9-5)
qmin—流量阀最小稳定流量。
液压马达:排量的计算式为
2T
V
p Mm
(9-6)
式中 T—液压马达的总负载转矩,N.m; ηMm—液压马达的机械效率; p—液压马达的工作压力,pa; V—所求液压马达的排量,m3/r。
液压传动课程设计指导书

液压传动课程设计指导书1.选题液压传动是工程机械的重要部件,具有功率传递稳定、传动效率高、响应速度快以及可靠性高等特点。
在课程设计中,可选择液压传动系统中的一个构件或液压系统进行设计,如液压缸、油泵、液压阀、液压管路等,也可以做一个完整的液压传动系统。
2.设计要求对于设计的液压传动系统或部件,需要满足以下要求:(1)满足所需的工作效率和负载要求(2)满足工作条件下的可靠性和安全要求(3)设计成本合理,尽可能降低制造和运行成本(4)满足环保要求,减少液压系统对环境的污染(5)结构简单,易于制造和维修3.设计步骤(1)确定液压传动系统或部件的工作条件,包括负载大小、工作环境、工作压力等参数。
(2)选择适合的液压元件,如液压泵、液压缸、液压阀门等,并制定相应的选型标准。
(3)进行系统或部件的设计计算,包括流量计算、功率计算、力学分析等。
(4)进行系统或部件的结构设计,包括选取适合的材料、制定加工流程、进行装配设计等。
(5)进行系统的调试和测试,对设计性能进行评估和改进。
(6)编写设计报告,包括设计原理、设计计算、设计结果以及实验数据等。
4.注意事项在液压传动的课程设计中需要注意以下事项:(1)充分了解液压传动的基本原理和各类液压元件的工作原理和特点。
(2)设计时需要考虑液压系统的安全运行,减少故障发生的概率。
(3)设计时需要合理控制设计成本,同时保证设计效果。
(4)在设计过程中进行交流,以理解师生之间的设计思路和设计思维方式。
(5)设计报告需要清楚、详细,表达方式应该正确,规范化,流畅易懂。
(6)尽可能利用实验室设备和知识资源,充分发挥实验室的优势,提高设计水平和质量。
- 1、下载文档前请自行甄别文档内容的完整性,平台不提供额外的编辑、内容补充、找答案等附加服务。
- 2、"仅部分预览"的文档,不可在线预览部分如存在完整性等问题,可反馈申请退款(可完整预览的文档不适用该条件!)。
- 3、如文档侵犯您的权益,请联系客服反馈,我们会尽快为您处理(人工客服工作时间:9:00-18:30)。
1明确液压系统的设计要求设计卧式双面铣削组合机床的液压系统。
机床的加工对象为铸铁变速箱箱体,动作顺序为夹紧缸夹紧——工作台快速趋近工件——工作台进给——工作台快退——夹紧缸松开——原位停止。
工作台移动部件的总质量为400kg ,工作台快进行程为 100mm ,快进、快退速度为 3.5m /min ,工进行程为 200mm ,工进速度为 80~300mm /min ,轴向工作负载为14000N ,加、减速时间为0.2s 。
采用平导轨,静摩擦系数为0.2,动摩擦系数为0.1,夹紧缸行程为30mm ,夹紧力为 800N ,夹紧时间为1s 。
要求工作台运动平稳,夹紧力可调并保压。
2 负载与运动分析负载分析中,暂不考虑回油腔的背压力,液压缸的密封装置产生的摩擦阻力在机械效率中加以考虑。
因工作部件是卧式放置,重力的水平分力为零,这样需要考虑的力有:夹紧力,导轨摩擦力,惯性力。
在对液压系统进行工况分析时,本设计实例只考虑组合机床动力滑台所受到的工作负载、惯性负载和机械摩擦阻力负载,其他负载可忽略。
(1)工作负载F WFw=14000(2)阻力负载f F阻力负载主要是工作台的机械摩擦阻力,分为静摩擦阻力和动摩擦阻力两部分。
导轨的正压力等于动力部件的重力,设导轨的静摩擦力为f F ,则 静摩擦阻力N G fs F 800fs =⨯=(G=1000N)动摩擦阻力 N N G fd F 400040001.0fd =⨯=⨯=(3)惯性负载最大惯性负载取决于移动部件的质量和最大加速度,其中最大加速度可通过工作台最大移动速度和加速时间进行计算。
已知加速减速时间为0.2s ,工作台最大移动速度,即快进、快退速度为3.5m/min ,因此惯性负载可表示为Na F 67.116m m =⨯=如果忽略切削力引起的颠覆力矩对导轨摩擦力的影响,并设液压缸的机械效率w η=0.9,根据上述负载力计算结果,可得出液压缸在各个工况下所受到的负载力和液压缸所需推力情况,如表1所示。
表1 液压缸总运动阶段负载表(单位:N )3 负载图和速度图的绘制根据负载计算结果和已知的个阶段的速度,可绘制出工作循环图如图1(a )所示,所设计组合机床动力滑台液压系统的速度循环图可根据已知的设计参数进行绘制,已知快进和快退速度==31v v 3.5快进行程L1=100mm 、工进行程L2=200mm 、快退行程L3=300mm ,工进速度=2v 80-300mm/min快进、工进和快退的时间可由下式分析求出。
快进 ssv L t 7.1605.3101003111=⨯==-工进 s v L t 150~4060300~80200222===快退 ss v l t 1.5605.3103003331=⨯==-根据上述已知数据绘制组合机床动力滑台液压系统绘制负载图(F-t )b 图,速度循环图c 图.ab c在此处键入公式。
4 确定液压系统主要参数4.1确定液压缸工作压力由表2和表3可知,组合机床液压系统在最大负载约为16000时宜取3MPa。
表2按负载选择工作压力表3 各种机械常用的系统工作压力4.2计算液压缸主要结构参数根据已知参数,液压缸无杆腔的有效作用面积可计算为A1=Fmas/P1-0.5P2=16000/3X10^6则活塞直径为4.8241==πA D mm根据经验公式D d 2=,因此活塞杆直径为d=58.3mm ,根据GB/T2348—1993对液压缸缸筒内径尺寸和液压缸活塞杆外径尺寸的规定,圆整后取液压缸缸筒直径为D =80mm ,活塞杆直径为d =56mm 。
此时液压缸两腔的实际有效面积分别为:242211024.506^10804m D A -⨯=-⨯⨯==ππ()242221062.254m d D A -⨯=-=π根据计算出的液压缸的尺寸,进一步计算液压缸在各个工作阶段中的压力、流量和功率值,如表4所示。
表4 各工况下的主要参数值5 液压系统方案设计根据组合机床液压系统的设计任务和工况分析,所设计机床对调速范围、低速稳定性有一定要求,因此速度控制是该机床要解决的主要问题。
速度的换接、稳定性和调节是该机床液压系统设计的核心。
此外,与所有液压系统的设计要求一样,该组合机床液压系统应尽可能结构简单,成本低,节约能源,工作可靠5.1确定调速方式及供油形式由表4可知,该组合机床工作时,要求低速运动平稳行性好,速度负载特性好。
由工况图可知,液压缸快进和工进时功率都较小,负载变化也较小,故宜采用调速阀的进油节流调速方式及开式循环系统。
为解决钻孔通时滑台突然前冲的问题,回油路上要设置背压阀。
由表4可知,液压系统的工作循环主要由低压大流量和高压小流量两个阶段组成,采用单个定量液压泵作为油源显然是合适的,因此可采用单泵来供油。
单泵泵因结构简单、噪声小、寿命长、成本低、故被采用。
如图2图25.2 组成液压系统原理图3图31双联叶片泵2二位二通电磁阀3背压阀4溢流阀5调速阀6单向阀8压力继电器9三位五通电液换向阀10滤油器表55.3系统图的原理1.快进快进如图3所示,按下启动按钮,电磁铁1YA通电,3YA接通。
这时的主油路为:进油路:泵→→三位五通换向阀(1YA得电)→经过行程阀→液压缸左腔。
回油路:液压缸右腔→三位五通换向阀(1YA得电→油箱2.工进快进终了时,二位二通电磁阀通电(3YA得电),这时的主油路为:进油路:泵1 →三位五通换向阀(1YA得电)→调速阀→液压缸左腔。
回油路:液压缸右腔→三位五通换向阀(1YA 得电→油箱。
3.快退工进到达终点时,时间继电器发出信号,使三位五通换向阀6的右侧2YA 得电 ,形成换向油路,这时的主油路为:进油路:泵1→ 三位五通换向阀6(2YA 得电)→液压缸右腔。
回油路:液压缸左腔→二位二通换向阀(右侧)→三位五通换向阀6→油箱。
4.停止当滑台退回到原位时,使三位五通换向阀右侧2YA 断电,换向阀处于中位,泵输出的油液被三位五通换向阀堵住,液压缸停止运动。
液压缸左侧的油液经单向阀7回到油箱,做到卸荷的作用。
6 液压元件的选择6.1确定液压泵的规格和电动机功率本设计所使用液压元件均为标准液压元件,因此只需确定各液压元件的主要参数和规格,然后根据现有的液压元件产品进行选择即可。
(1)计算液压泵的最大工作压力由表4可知,液压缸在整个工作循环中的最大工作压力为1.15Mpa,本系统采用调速阀进油节流调速,选取进油路压力损失为MPa 5.0P1=∆∑。
考虑到压力 继电器的动作可靠要求压差为MPa 5.0P e =∆,故泵的最高工作压力为:()MPaMPa P p 5.45.05.05.31=++=此压力即为小流量泵的最高工作压力,也即溢流阀的调整压力。
大流量泵仅在快进和快退时向液压缸供油,图4表明可知,液压缸快退时的工作压力比快进时大,考虑到快退时进油不通过调速阀,故其进油路上的压力损失比工进时小,现取进油路损失为MPa 3.0P 1=∆∑,则大流量泵的最高压力估算为:()MPa MPa P p 45.13.015.12=+=(2)计算总流量由表4可知,快进时需要最大供油量,其值为17.6L/min 。
计算液压泵的最大流量,取回路泄漏修正系数K=1.15,则泵的总流量为:min24.20min 6.1715.1max L L q K q p =⨯==∑最小流量在工进时,其值为0.4L/min 。
为保证工进时系统压力稳定,应考虑溢流阀有一定的最小溢流量,取其额定流量的10%,约为2.0L/min 。
故小流量泵的流量最小应为2.4L/min 。
根据以上压力和流量的数值查阅产品样本,最后确定选取PV2T12-6/33型双联叶片泵,其小流量泵和大流量泵的排量分别为 6mL/r 和33mL/r ,当液压泵的转速n p =940r/min 时,该液压泵的理论流量为 36.66L/min ,若取液压泵的容积效率率v η=0.9,则双泵供油时,液压泵的实际输出流量为:()[]m in33m in 10009.0940336L L q p =⨯⨯+=小流量泵单独供油时:()min08.5min 1000/9.094061L L q p =⨯⨯=(3)计算总流量由于液压缸在工进时输入功率最大,其值为0.08KW ,若取泵的总效率为0.75p η=,则液压泵驱动电动机所需的功率为:W kW q p P ppp 33..2931075.0601033104.0336=⨯⨯⨯⨯⨯==-η 根据上述功率计算数据,此系统选取Y100L-6型电动机,其额定功率kW P n 5.1=,额定转速min 940r n n =。
6.2确定其它元件及辅件(1) 确定阀类元件及辅件根据阀类及辅助元件所在油路的最大工作压力和通过该元件的最大实际流量,查阅产品样本,选出的阀类元件和辅件的型号及规格见表6。
表中序号与图4元件标号相同。
表6 液压元件规格及型号*注:此为电动机额定转速为940r/min时的流量。
(2) 确定油管在选定了液压泵后,液压缸在实际快进、工进和快退运动阶段的运动速度、时间以及进入和流出液压缸的流量,与原定数值不同,重新计算的结果如表7所列。
表7各工况实际运动速度和流量由表可以看出,液压缸在各阶段的实际运动速度符合设计要求。
根据选定的液压阀的连接尺寸确定油管尺寸,也可接管路中允许流速计算。
设管道内允许流速V=4m/s 。
根据表7中的数值,可算得与液压缸无杆腔和有杆腔相连的油管内径分别为:()()()mm mm v q d 9.18604103.6722311=⨯⨯⨯⨯==-ππ取标准值20mm ;()()()mm mm v q d 5.18604107.6422322=⨯⨯⨯⨯==-ππ由于本系统液压缸快进时,油管内通油量最大,其实际流量为约泵额定流量的两倍,则液压缸进、出油管直径d 按产品样本,选用内经20mm 、外径为28mm 的10号冷拔钢管。
(3)油箱的设计油箱的主要用途是贮存油液,同时也起到散热的作用,参考相关文献及设计资料,油箱的设计可先根据液压泵的额定流量按照经验计算方法计算油箱的体积,然后再根据散热要求对油箱的容积进行校核。
油箱中能够容纳的油液容积按JB/T7938—1999标准估算,取7=ζ时,求得其容积为L L q V p 230337≈⨯==ζ6.3主要零件强度校核① 缸筒壁厚δ=8㎜ 因为方案是低压系统,校核公式, 式中:——缸筒壁厚()——实验压力 ,其中是液压缸的额定工作压力D ——缸筒内径 D=0.08M——缸筒材料的许用应力。
n b /][σσ=,b σ为材料抗拉强度(MPa ),n 为安全系数,取n=5。
对于P 1<16MPa.材料选45号调质钢,对于低压系统mm D P e 2.710100208.01045.4][266=⨯⨯⨯⨯⨯=≥σδ 因此满足要求。