GM整车开发流程简述
超简明通用汽车GM供应商开发阶段节点要求

开发阶段(节点)要求
五、 PPAP(生产件批准) 10、零件和包装箱标识要求: 正式包装 11、包装运输要求: 正式量产时包装运输 12、过程能力(CPK)要求:CPK统计分析≥1.33(符合SOR要求) 13、检具(MSA)要求: MSA≤10%,GM检具制造认可 14、设计记录/工程变更记录要求:提交最新设计记录,汇总工程变更记录 15、客户工程认可要求:3660表GM签署认可 16、资料认可要求:PFMEA、控制计划、过程流程图(SQE认可)
开发阶段(节点)要求
三、 MC2(匹配装车2) 1、尺寸要求: 100% 2、材料要求: 材料认可,IMDS通过 3、生产工装要求 :量产工装 4、生产设备要求:量产设备 5、生产场地要求:量产场地 6、性能要求 :PV实验开始 7、文件资料要求:①需提交:全尺寸检验报告、测点图、性能检验报告、PSW、 1411(零件状态说明及未达到FULL PPAP要求事项的对策)、材质报告、设计记录 ②需完成:作业人员上岗培训计划、设备能力分析、正式BOM表、控制计划 GATE REVIEW-3资料、GP12规划及控制文件。 8、表面处理和颜色要求 :AAR零件提交认可 9、零件标记要求 :N/A(纸质标不需要) 10、零件和包装箱标识要求: N/A 包装设计认可 11、包装运输要求:IVER(手工验证) 1、尺寸要求: 70% 2、材料要求: N/A 3、生产工装要求 :N/A 4、生产设备要求: N/A 5、生产场地要求: N/A 6、性能要求 :DV试验 7、文件资料要求:GP11 8、表面处理和颜色要求 :N/A 9、零件标记要求 :N/A 10、零件和包装箱标识要求: PROTOTYPE GM 1827/1828 11、包装运输要求: N/A 12、过程能力(CPK)要求: N/A 13、检具(MSA)要求: N/A 14、设计记录/工程变更要求: N/A 15、客户工程认可要求:N/A
GM整车开发流程简述

GM整车开发流程简述首先,GM整车开发流程的第一步是市场调研和需求分析。
通用汽车公司通过调查市场的需求和趋势,了解消费者的喜好和需求,确定新车型的市场定位和开发目标。
在此阶段,公司还会与其它部门和合作伙伴进行合作,例如,在设计和工程方面与供应商和工程公司进行合作。
第二步是概念设计和评估。
在这一阶段,公司会开展设计研究和创意概念阶段,以确定新车型的外观和内饰设计。
公司还会进行车辆的动力学和性能评估,以确保新车型符合安全和法规要求。
第三步是工程开发和验证。
在这个阶段,公司会进行车辆的工程和零部件设计,制定详细的车辆规格和技术要求。
公司会进行多种测试和验证,包括在试验室和公路上进行的测试,以验证新车型的性能和安全性。
在此阶段,公司还会与合作伙伴和供应商进行协商和合作,以确保零部件的供应和质量。
第四步是产品生产和试制。
在这一阶段,公司会建立生产线,生产新车型的试制车辆。
试制车辆将进行各种测试和评估,以验证生产工艺和确保新车型的质量。
公司也会与合作伙伴和供应商进行合作,以确保零部件的供应和质量。
第五步是市场推广和销售。
在这个阶段,公司会进行市场推广活动,包括新车型的广告宣传和销售推广。
公司还会与经销商和合作伙伴合作,确保新车型在市场上得到良好的推广和销售。
最后一步是售后服务和客户满意度管理。
在这一阶段,公司会提供售后服务和维修保养支持,以确保客户对新车型的满意度。
公司会收集客户的反馈和建议,并根据客户需求做出相应的改进和调整。
总的来说,GM整车开发流程是一个系统而复杂的过程,包括市场调研、概念设计、工程开发、产品生产和试制、市场推广和销售以及售后服务和客户满意度管理等多个环节。
通过这个流程,通用汽车公司能够设计、开发和推出符合市场需求的新车型,并提供满足客户需求的售后服务,从而提高公司的竞争力和市场份额。
整车产品开发流程浅析

通用汽车 ( GM ) 的 GVDP、大众汽车 ( VW ) 的 PEP、丰田 ( Toyota) 的精益产品开发流程都是一些 正向开发流程。虽然各国汽车企业对产品开发项 目各有侧重, 但是其项 目管理的思想和方法却基 本一致。这些共同点都与门径管理系统和集成产 品开发思想体系相符, 并且在 IT 行业的新产品开 发中得到证明, 值得我 国自主研发企业在研发流 程制定和流程建设中全面学习和借鉴。一套完整
非增值的活动不均衡和超负荷2均衡的精益研发流程丰田在流程形成行过程追求均衡其个性特征主要表现在以下几个方面在概念开发阶段利用研讨尽可能多预测和解决下游技术问题从而在价值流早期降低变异性错开一个功能部门到下一个功能部门的数据发布有利于掌控开发工作节奏使用检查清单标准化的工作流程和分零件开发计划排除任务变异性形成的防错系统有力支持开发流种流程的对比上海汽车46201008过度生产批量不同步进行工作等待等待决定信息的发布运输信息过度发布过度加工走走停停的任务缺乏标准化库存物料或信息的堆积移动长距离出差无用的审查返工通过检验发现质量问题制造返工以管理为中心的流程以质量为中心的流程精益流程用户诉求追求尚产品追求高技术质产品追求高性价产品管理导向管理导向质量技术导向成本导向研发组织多技术中心主兼矩阵管理按市场需求研发式管理评审指标交付物评审技术评审强项要求管理能力高技术能力高管理能力较高管理和技术均衡知识传递知识数据库人员知识库技术经济应该对企业的内外部环境进行深入分明确企业的优势和今后的发展方向以此为基础进行流程建设才能获得成功42遵循开发流程发展三阶段的规律不能逾越发展无论是哪个流程随企业的诞生和发展都要经过流程建设阶段流程优化阶段和流程管理1流程建设阶段内应保持流程稳定流程建设阶段是流程发展的第一阶段这一阶段初期是新流程的导入新流程需要经过一定时间的认同1998年引入ipd产品开发模关注发明试点导入期需要有一套结构化的标准流程大部分的产品研发活动本质上需要大量循环资源和活动标准化的流程能使产品研发流程在变幻莫流程标准化的过程就是让所有流程参与者都理解他们在流程工作分解的作用明确流程所界定的每项工作的输入和输出2流程优化阶段应关注流程在非结构化与过于结构化之间的平衡学习丰田的通过在流程中设置总结节点流程发展过程中要把握非结构化随意性与结构强化标准之间的平衡关系如已有的流程需要对其按变化进行细分3流程管理阶段应有相对侧重的调整发展方向流程的成熟时期整车的开发流程不应只限于整车企业内部的工作流还需考虑将研发体系中的零件供应商和开发供应商也纳入到流提高研发效率让整车企业通过研发流程引领使其担负起整个汽车产业链的引领作用自主汽车产品研发流程在模式上的关注点探讨从三大汽车公司的研发流程分析不难看到代表其产品特点
GM汽车供应商一般开发程序-14页word资料

##汽车公司供应商开发一般程序##汽车公司关于前期样件及样件材料供应商程序GP11本程序适用于提供新的前期样件和样件材料的所有供应商(包括分支机构供应商、联合供应商以及外部供应商)。
所有材料均应满足本程序规定的要求。
术语“供应商”表示通用公司采购部初期承包商。
做前期样件和样件工作的目的就是集中检测生产零件、总装系统和整车设计及装配工艺的有效性。
在前期样件和样件阶段对零件的审批能够保证零件所存在的问题能够在这个阶段被发现并得到改正以便最大限度地减少零件在设计评估、制造和安装时的变化。
本程序对前期样件和样件供应商提出了要求,包括材料直接装运到接收地以及需要供应商存档的证明文件。
同时也对供应商在装运材料前制备零件和准备供采购部评估的文件提出了统一的最低要求。
本程序包括对GP-11 A/D/V 的要求。
GP-11A/D/V是GP-11要求的子系统。
GP-11A/D/V代表GP-11的分析/开发/认证。
只有在SOR中有说明时,才需要GP-11 A/D/V。
本程序包括以下内容:1-0前期样件和样件及其文件要求2-0提交要求3-0装运方法4-0档案保存要求5-0 附件/样本前期样件和样件的要求GP-111-0前期样件和样件及其文件要求零件应按照通用公司授权的图纸、样板、模型和/或其它设计文件所规定的材料制做。
若与设计有偏差,请与采购部联系以获得正式的授权。
所有的前期样件及样件供应商均需要具有下文所列的完整的、成文的、有效的文件以供评审。
规定年型的样件的存档应保存到该样件开始正常生产后的两个月。
1.通用公司前期样件及样件材料供应商保证书(样本A)2.设计档案3.检查结果和检查和/或检测工具4.材料证明5.零件重量(质量)6.排序信息7.生产材料及工艺8.分析/开发/认证(若需要的话)1-1.通用公司前期样件及样件材料供应商保证书通用公司前期样件及样件材料供应商保证书应由负责制备和装运零件的供应商授权的官员完成并签字。
主机厂配套产品开发流程

主机厂配套产品开发流程
主机厂配套产品开发流程众所周知的项目开发三架马车:时间,成本,质量。
今天我们先来简单的看看流程:
戴姆勒-奔驰的流程比较简单,每个里程碑的目标安排合理,概念冻结、需求冻结、然后1:1模型确认,最后设计冻结,这一套流程简介不繁琐,目标性很强,效率高。
通用汽车(GM)是贯彻先期质量策划的先驱,其流程和体系(QSB)被广为效仿,甚至很多零部件供应商直接照搬通用的流程体系,这个流程对于文件、订单方式、造车区域有了明确的定义,正式物流订单分为小批量、中批量、大批量。
日产的流程是分为从Phase1~Phase5,
VC lot代表试装样件,主机厂试验和实车试装;
PT1预批量生产,需要完成量产流程和产品尺寸过程能力验证;
PT2预批量生产,需要完成制造过程能力审核;
日产每个阶段中有小的任务和里程碑,只有将所有任务验证完成并且合格,才能进入到下一个大阶段,一环扣一环,比较可靠。
沃尔沃的节点名称和描述比较详细,造车理念也是贯彻了欧洲人的精细,沃尔沃在MP1批量投产后,会进行为期6个月的量产全检,用通用体系的术语叫GP12,GP12全检对新项目刚投产的质量不稳定现象能够有效防范和隔离。
大众集团整个项目节点划分非常细,其QPN里具有更详细描述。
其中最关键点分别是:PF项目确认、B认可、0S零批量以及SOP量产。
0S交样也是大众非常关键,大众质保部门会全力介入,比如产线试装、各路况路试、供应商首批样件检验和认可,供应商产能评审2TP等。
整车开发流程第六章-整车开发管理

整车开发流程第六章-整车开发管理“ 从整车开发概览到各个开发阶段介绍,相信之前的⽂章或多或少有不少读者在读⽂章之前或许了解⼀些内容;或者⾃⼰亲⾝经历过的项⽬。
但本章整车开发管理将串联各个阶段的逻辑,不但介绍整车开发管理的⼯具,更揭⽰整车开发管理背后的逻辑思维。
⾮常值得管理⼈员⼀读”摘要:为了全⾯管控整车开发项⽬以及最优掌握产品开发过程中涉及的各⽅资源,整车项⽬开发采⽤了多种⽅法和流程。
例如⽬标管理,包括⽬标推导,协调,更新;问题管理,登记和管理整车集成当中检测到的车辆设计问题;设计发布以及变更管理,包括部件发布的明确标记和设计更改的评估;质量管理,确保整车开发和量产活动的项⽬或者产品达到既定⽬标。
6.1—⽬标管理Target Management6.1.1整车开发要求产品开发的⼀个重要环节就是开发结果要符合要求。
完整的车辆要求(⽐较。
5.2.3)是指允许车辆在预定市场出售和上牌登记所必须满⾜的法律要求和消费者要求的总和,这些要求表明了单个⽤户对车辆功能和性能特性的直接感知。
虽然法律要求通常由政府指令和法规(如美国安全标准的FMVS,中国的CCC和GB)明确定义,但消费者要求是相当主观的。
消费者寻求满⾜其个⼈要求的车辆功能和性能特性-当然,除了所有法律要求。
成功的整车开发的⼀个先决条件是需求(客户想要或需要的)和技术功能(⼯程师寻求解决客户需求带来的问题的⽅法)之间的必要区别。
客户的相关问题定义了客户域。
以空调舒适性为例,驾驶员和乘客只希望车内有⼀个舒适的⽓候,例如:头部/⾝体/脚感知温度车辆内部表⾯特别是座椅表⾯的感知温度感知温度的稳定性感知⽓流窗户除霜除雾所需时间调节⽓温和⽓流的容易程度由于使⽤空调系统(加热,通风,制冷)产⽣的额外油耗然⽽,零部件⼯程师通过功能需求在功能域中形式化这些需求,并通过发布的零部件的设计参数在物理域中进⼀步形式化这些需求,这两者都是客户不感兴趣的部分。
在上述空调舒适性⽰例中,设计参数如下:左/右出⼝测得的空⽓温度通过左/右风道测得的流量暖通空调压缩机功率座椅加热器功率当以上三个域(客户域,功能域,物理域)被混淆时,可能会导致糟糕的解决⽅案。
整车开发流程(上)

整车开发流程(上)导读:面向应用工程师的商业软件咨询、自研软件定制开发服务的仿真公众号,点击关注进入菜单,查看更多精彩内容。
一、关键开发阶段一件产品(一辆汽车)的诞生,需要经历以下几个Main Stages:在以上原则的基础上,整车开发共定义了15个里程碑,分别是A4-A1、G9-G1、产品上市(G0)和项目关闭(GC)。
为更清晰的表明各里程碑之间的关系,整车开发过程可以归纳形成五个阶段,如下表更清晰的如下图,从图中可以看出单是架构阶段就需要2年时间,当然战略、概念阶段与架构可以同步进行,就算这样,一个完整的整车开发,从架构阶段开始到产品成熟需要56个月的时间(2012年的研发生产制造水平),就算近年研发能力及生产制造能力相对提高了一些,但最起码的一个完整的整车开发也是需要3年左右时间的。
二、里程碑架构阶段、战略阶段及概念阶段这三个阶段的主要参与者有市场部、技术总监、财务部等公司高层领导,这块作为工程师来说顶多会参与一些与平台选型相关的讨论会议,其它基本还参与不了。
在此阶段笔者也就被叫去参与了平台选型会议中与自己当时负责的系统有关的问题讨论,总之这几个阶段讨论的东西都是很宏观的东西,主要是领导层进行品牌战略的决策。
到了G8就是工程师开始参与进来的里程碑了。
G8:项目启动(PC-Program Commencement) 即之前架构、战略及概念阶段已经有了初始的项目周期及开发范围,在G8需通过前期可行性研究分析确定项目的边界条件,平台架构方案批准、整车性能等主要技术规范确定等。
G7:方案批准(CA-Concept Approval),此阀目的对重要的产品方案,包括动力总成方案,整车的性能、造型主题模型,制造地方案、关键产品配置和新技术的开发方案等,进行评审决策,确定可以实现G8 设定的竞争性目标。
G6:项目批准(PA-Program Approval),此阀目的为在产品项目架构开发基本完成,造型开发和同步工作结束的情况下,全面平衡产品项目的边界条件是否达到设定的目标,对是否终止或继续项目的开发做出决策。
整车开发流程概述

整车开发流程概述产品保证策划是一种系统的、以预防为中心的战略,把与质量相关的活动统一到产品开发过程中,保证开发世界一流产品。
一个产品保证计划是跨功能的产品保证团队制订的一个特定项目或方案的特定工作计划。
团队确定用以开发一种产品和制造过程的任务、责任和时间进度。
一个产品保证团队是一个平台内的跨功能的小组,它分为整车、系统、分系统、或部件级,它的职责是完成产品保证策划。
产品保证策划要求从各个组织来的人员很好地参与和交流,这些组织包括: - 车辆工程平台 - 车辆工程运作 - 科学实验室和试验场 -先期制造工程- 装配 - 冲压 - 财务-质量和可靠性计划- 概念设计部门- 产品计划- 销售和市场- 动力总成部门- 零部件部门- 采购供应- 供应商- 维修工程在产品保证策划阶段的结束点的主要里程碑是;●主题选择和工程概念选择●项目批准●第一辆项目样车(F1)制造的开始●第一辆试装样车(P0)制造的开始●第一辆产品车制造的开始主题选择和工程设计概念选择——概念选择阶段的结束主题和工程设计概念选择是考虑和评估多种主题和设计概念的可行性,并在概念选择阶段它们被合并为一种概念的里程碑。
产品设计和造型主题被选定。
同时,底盘、动力及传动、内部和电器部件的工程设计概念也被选定,以支持主题和其他项目目标的选择。
在作出这些选择前,团队工作研究多个主题和产品工程的设计和制造可行性。
项目批准——批准阶段的结束项目批准是高层管理部门和平台团队之间的继续执行项目的合同。
根据完成项目所要求的详细的目标、目的和活动,以及对项目能够在可获得的资源和条件下满足这些要求的高度的自信心,项目将被批准。
在项目批准时,高层管理部门承诺提供所要求的用以满足顾客的期望和项目目标的必要资源,平台或方案团队则同意执行该项目。
第一辆项目样车(F1)制造的开始——项目样车阶段的结束项目样车(F1)要达到生产设计意图,以评估部件、系统、整车的制造和装配生产过程。
GM产品开发流程

GVDP v5_Upd_trg.ppt/Don Smith/5/22/2006/version 6.0
Pre-VPI GVDP Overview
No Architecture Modifications
(outside of bandwidth)
(e.g. GMX211,GMX272, GMX386)
VPI
Lead Program Derivative Program(s)
(e.g. GMX 353, GMX 354)
Program Framing
Program Developme nt
Once printed this document is UNCONTROLLED, please refer to /gvdp
(for more information go to: / gvdp/asiapacific/index.html)
Once printed this document is UNCONTROLLED, please refer to /gvdp
INDEX
7
GVDP v5_Upd_trg.ppt/Don Smith/5/22/2006/version 6.0
Program Framing
The purpose of Program Framing:
• Develop common program vision and objectives with Leadership • Translate customer and corporate requirements into technical requirements • Understand the engineering solutions within the existing architecture Modifications as required within existing bandwidths • Develop the compatible boundary conditions captured in the DSI
gm开发流程

gm开发流程Developing a game as a gm involves a complex process that requires careful planning and execution. It starts with conceptualizing the game idea and creating a detailed design document outlining all aspects of the game, from storyline to gameplay mechanics. As a gm, you need to work closely with the development team to ensure that the vision for the game is realized and that all elements come together seamlessly.作为一名gm开发一款游戏涉及到一个复杂的过程,需要仔细的规划和执行。
它始于构思游戏理念,创建一个详细的设计文档,概述游戏的所有方面,从故事情节到游戏机制。
作为一名gm,你需要与开发团队密切合作,确保游戏的愿景得以实现,所有要素无缝地融合在一起。
Communication is key in the gm development process. Clear and effective communication ensures that everyone is on the same page and working towards the same goal. Regular meetings, brainstorming sessions, and updates are essential to keep everyone informed and engaged throughout the development process. As a gm, it is your responsibility to foster a collaborative and openenvironment where ideas can be shared and feedback can be given freely.沟通在gm开发过程中至关重要。
整车开发流程详解
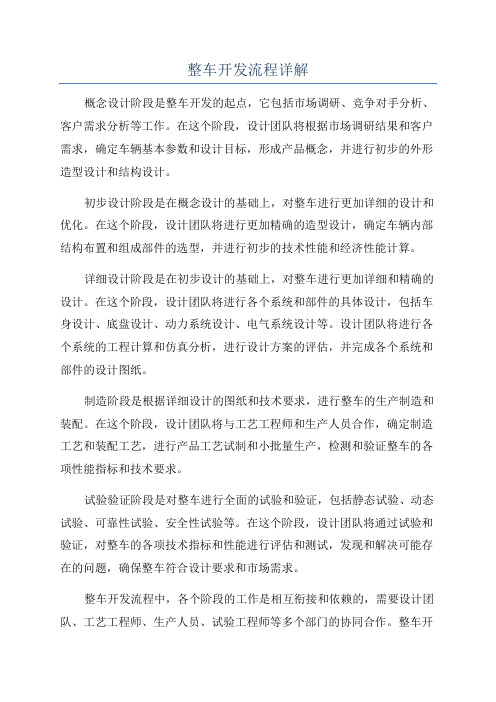
整车开发流程详解概念设计阶段是整车开发的起点,它包括市场调研、竞争对手分析、客户需求分析等工作。
在这个阶段,设计团队将根据市场调研结果和客户需求,确定车辆基本参数和设计目标,形成产品概念,并进行初步的外形造型设计和结构设计。
初步设计阶段是在概念设计的基础上,对整车进行更加详细的设计和优化。
在这个阶段,设计团队将进行更加精确的造型设计,确定车辆内部结构布置和组成部件的选型,并进行初步的技术性能和经济性能计算。
详细设计阶段是在初步设计的基础上,对整车进行更加详细和精确的设计。
在这个阶段,设计团队将进行各个系统和部件的具体设计,包括车身设计、底盘设计、动力系统设计、电气系统设计等。
设计团队将进行各个系统的工程计算和仿真分析,进行设计方案的评估,并完成各个系统和部件的设计图纸。
制造阶段是根据详细设计的图纸和技术要求,进行整车的生产制造和装配。
在这个阶段,设计团队将与工艺工程师和生产人员合作,确定制造工艺和装配工艺,进行产品工艺试制和小批量生产,检测和验证整车的各项性能指标和技术要求。
试验验证阶段是对整车进行全面的试验和验证,包括静态试验、动态试验、可靠性试验、安全性试验等。
在这个阶段,设计团队将通过试验和验证,对整车的各项技术指标和性能进行评估和测试,发现和解决可能存在的问题,确保整车符合设计要求和市场需求。
整车开发流程中,各个阶段的工作是相互衔接和依赖的,需要设计团队、工艺工程师、生产人员、试验工程师等多个部门的协同合作。
整车开发流程一般需要经历多次迭代和优化,以确保最终产品达到设计要求和市场需求的目标。
总之,整车开发流程是一个复杂而系统的过程,包括概念设计、初步设计、详细设计、制造和试验验证等阶段。
每个阶段都有各自的任务和目标,需要设计团队和相关部门的协同努力,才能最终实现一个满足市场需求和技术要求的整车产品。
整车开发作业流程

1.骡子车(Mule Car)在项目开始早期利用现有生产车辆, 经过改装等方法安装新发动机支撑, 功效性发动机冷却、进气系统和整个发动机总成。
目标: 在项目早期(G7方案同意前)支持动力总成初始验证和标定工作(开发Mule车标定)。
比如: 整车载重分析、底盘操纵和控制系统开发、空调和发动机冷却系统开发、噪声和振动分析、动力总成集成系统开发、电气系统开发等等。
2.模拟样车(Simu Car)利用代表设计结构件经过拼装和改装而成样车(软模、简易工装、手工工艺等)。
目标: 为支持整车、系统深入设计和验证, 完成架构件设计和公布。
3.工程样车(EP Car)依据工程设计公布信息, 采取对应工程样件制造工艺制造出满足设计要求零件在技术中心试制车间装配车。
目标: 整车集成开发、验证和整车相关SSTS(子系统技术规范)要求、零件调试、开发动力总成标定、公告法规早期验证和验证总装次序等。
1、铸造同意和铣削同意由产品和制造在同时工程基础上共同同意!2、制造验证造车(MCB)制造验证造车( Manufacturing confirmation Build )是在生产线正式造车(PPV )前准备工作, 检验车辆工艺可行性, 在工厂里完成制造, 以识别工厂问题并为正式造车做好职员培训。
造车会经过全部工艺系统, 为工厂职员展示产品和工艺过程学习机会。
造车所用零部件能够采取EP 车零部件, 运输到工厂。
在PPV 前1 个月完成首辆车制造。
2.生产验证车(PPV Car)用正式生产工装模具和制造工艺制造样件并根据生产线工艺装配而成样车。
目标: 100% 动力总成标定、底盘操控性验证、动力加速性验证和VTS 认证, 同时对制造工艺进行验证和生产工人培训。
PPV造车职责分工:1)采购负责PPV 零部件采购到位2)PPV 批量零部件入库许可-SQE3)物流负责PPV 零部件上线准备4)工程负责零部件技术状态控制, 零部件工程认可5)质保负责零部件MB2 80%合格6)制造工程负责生产线就绪, 工厂负责制造3.预试生产造车(PP Car)Pre-Pilot 造车关键考评工艺装备、检验步骤和检验装置过程能力。
GM 项目开发培训

PPQP
PPQP Part Identification Label
PPQP Part Identification for fully inspected parts (M Suffix)
Parts ordered for Pre-Production/Prototype builds that are in the PPAP approval process but HAVE NOT successfully achieved full PPAP approval: A) A Quality Warrant and Corrective Action Plan shall be submitted. B) The PPAP Part Submission Warrant (CGF-1001), PPAP Interim Recovery Worksheet (GM1411) and copies of all associated test reports shall also be submitted with the shipment.
2. Conforming Non-Critical parts do NOT require GM approval prior to shipment to the PPO build site.
3. NON-CONFORMNG Non-Critical Parts---Suppliers must submit each NON-Conforming Part Quality Warrant, Corrective Action Plan and supporting documentation.
整车开发流程
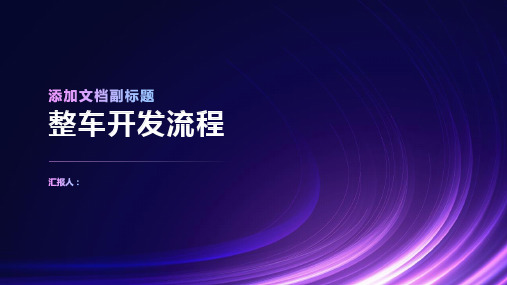
设计方案的评审与优化
评审内容:设计方 案的技术可行性、 经济性、市场竞争 力等
优化方向:根据评 审结果,对设计方 案进行针对性优化
评审流程:初步评 审、详细评审、综 合评审
优化流程:方案调 整、技术评估、再 次评审
试制阶段的流程和任务
试制准备:确定试制方案、准备物 料和工装设备
过程问题解决:针对试制过程中出 现的问题进行改进和优化
添加标题
添加标题
添加标题
添加标题
试制生产:按照试制方案进行小批 量生产,验证产品可行性
试验验证:对试制产品进行各项性 能试验,确保产品符合设计要求
试验阶段的流程和任务
试验准备:根据开发要求和目标, 制定试验计划和方案,准备试验设 备和器材。
试验总结:对试验过程和结果进行 总结,编写试验报告,提出改进意 见和建议。
车身结构设计
确定车身结构形式 设计车身骨架和覆盖件 确定车身材料和工艺 完成车身结构详细设计
零部件设计与选型
零部件设计:根据整车需求和规格,进行零部件的结构设计、性能分析和优化。
选型标准:基于设计要求、性能参数、制造成本等因素,对零部件进行选型和匹配。
供应商评估:对供应商的技术能力、产品质量、交货期等进行评估,确保零部件的供应和质量。 详细设计审查:对零部件设计的可行性和合理性进行审查,确保满足整车性能和安全要求。
添加标题
添加标题
添加标题
添加标题
试验执行:按照试验计划和方案进 行各项试验,记录试验数据和结果, 分析试验数据,评估试验效果。
试验评估:对试验效果进行评估, 确定是否达到开发要求和目标,为 后续开发提供依据。
试制与试验的结果评估与改进
试制与试验的目的是为了评估产品的性能和安全性,以及发现潜在的问题和改进空间。
GMAPQP开发流程(PPAP初期流动品管理)XXXX
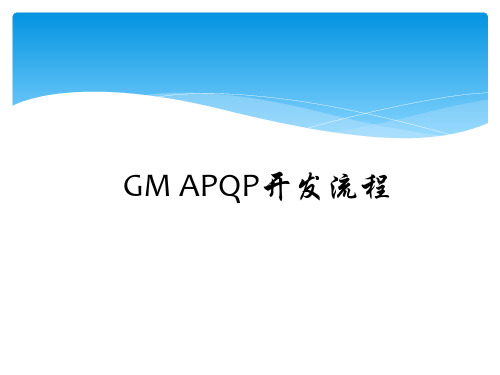
全球采购供应商质量改进程序
APQP 17个任务 / 可交付的内容
- 产品定点策略会议 -技术评审 -风险评估/定点 -供应商项目评审 - 时 间 进 度 表 / 问题清单 - 可 行 性 评估 -流程图 - 设 计 FMEA -设计评审
- 检具 / 工 装 / 设 备 审 核 - GP-11 - 过 程 FMEA
任务责任人:产品工程师 任务时间:初始评审Beta样件前
持续进行后续评审
பைடு நூலகம்
检具、工装与设备评审
任务号 : 10 任务描述 :
目的在于确保制造过程按最新图纸更改水平设计、制造和验证,从而生产出 符合SGM质量要求的零件
任务的关键输出:
对检具、工装和设备的设计概念的初始评审于APQP启动会议时进行,概
念批准在Beta样件前进行;持续进行后续评审,直至PPAP
样件批准—GP11
认可流程:
发布OTS零件清单 向选定的供应商订购OTS 样品
工程标准及要求 提交寄清单,图纸,电子数据,标准
供应商应识别任何有关的更改并与SQE沟通 满足推出标准时,退出GP-12 所有分供方应遵守GP-12程序,并提前节点以保证一级供应商的GP-12进度
任务责任人:供应商 任务时间:PPAP时评审控制计划
SGM指定时间段实施
生产件批准PPAP
任 务 号 : 15 任务描述:
目的在于确认供应商是否完全理解所有的顾客工程设计记录和规范要求,通过按报 价生产速率进行的正式生产,以验证其过程有能力生产出符合以上要求的产品。
启动会议时,SQE和供应商共同评审经验教训,将相关未关闭问题列入APQP 问题清单
供应商在开发DFMEA、PFMEA期间应使用经验教训信息 在PR#2,3,4中,供应商应评审APQP问题清单中的新问题解决方案,并更新
GVDP-整车开发流程2.0介绍
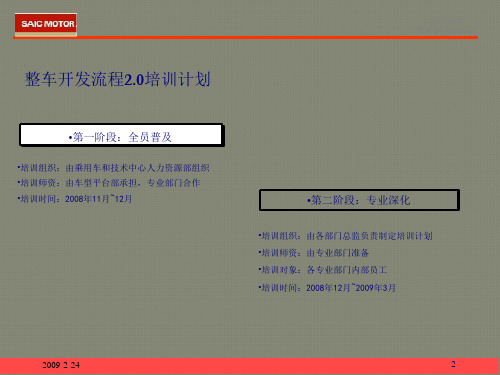
Pilot 试生产
G3
G2
ESO 工程签署
Pilot build reivew
试生产评审
G1
Production Signoff 制造签署
Change to Engineering Release工程发布 Change to Product & Process Validation-产品和制造验证
造型冻结 硬模设计
模型冻结
硬模面板 仪表板
量产模具 EMS 主要标定
M/MV/M 最终EMS标定
S.O.P
概念开发
产品开发
产品认证
准备量产
可行性研究
目标材料成本建立 成本细分评审
目标材料确定 成本细分运作
CDM
初始版汇聚了中英韩三方的经验和智慧,建立了整车开发流程的框架,为GVDP 1.0的发布奠定了 坚实的基础
Simulators
D02
D1
TRM
TG0
TG1
TG2
C
Maturation QP, M
DE
Volume
2009-2-24
6
整车产品开发模式简单对比 SYMC
车型平台部 VLE Department
Gate8
M-18
Concept Initiation
Pre-Planning Approval • Concept Approved • VOC Analysis • Product Mix
项目任务书Review Produt Program Content :VTS/FFL
G6 PA
项目批准 Programe Approval
项目任务书冻结 Produt Program content
- 1、下载文档前请自行甄别文档内容的完整性,平台不提供额外的编辑、内容补充、找答案等附加服务。
- 2、"仅部分预览"的文档,不可在线预览部分如存在完整性等问题,可反馈申请退款(可完整预览的文档不适用该条件!)。
- 3、如文档侵犯您的权益,请联系客服反馈,我们会尽快为您处理(人工客服工作时间:9:00-18:30)。
• 三、SOR概述 • 四、PDT概述
一、通用整车开发流程概述
新车型的开发是一个相当复杂的系统工程,它需要几百号人花费3至4年的时间才 能完成,不同的汽车企业其汽车的研发流程有所不同。下面以通用的开发流程为例, 粗略的讲解一下整车的开发流程。通用的整车开发流程从大的节点可分为8个重要 的项目节点。对应为G8~G1. 后面的内容将会对各节点中各部门所要进行的基本工作以及条件输出加以描述, 让大家更清楚的明白在项目的各个阶段,各负责人所需要完成的具体工作。
4.设计数据: 4.1、工程图纸:图纸是报价的依据 SOR技术条件所包含的主要内容: 4.2、技术条件:若SOR中没有提供的技术规范, 则供应商应自己负责获得。供应商有责
任把原 图纸或技术规范翻译成相应要求的语言 。 4.3、CAD数据/数模:规定了供应商提交数据的软件种类、版本以及对数模质量要求 的详细定义。 定义了二维图所需要的元素,如界面、尺寸公差、图纸具体规范等。 4.4、零部件数据的命名应符合公司规范。 4.5、设计在制造过程中的符合程度 :整车厂将指导供应商进行设计在制造过程失效 模式分析(DFM/A). 设计在制造过程中的符合程度理论方法,包括那些在主要车间的跨 功能件拼装过程的分析进一步提高设计. 4.6、设计潜在失效模式及后果分析 :对于供应商设计的零件,供应商应提交DFMEA 文 件给整车厂 批准,同时负责更新数据 。对于整车厂设计的零件,要求供应商积极支持设 计发布工程师开始和更新 。 5.进度要求: 整车公司提供该项目主控制计划,供应商必须按最新的项目主计划进行开发。供应 商列出的详细计划,检测要求、工装、材料、生产件 批准程序(PPAP)等时间进度 必须符合整车公司最新主控制计划的要求 。 . 6.样品需求: 填写所有造车中要求供应商送样的次数和零件数量,项目包括功能评估、工装样件 及其它送样项目,按照时间节点填写详细的供样时间。要求交样和供货时间以项目 组或主管工程师或采购员通知为准。
GM整车开发流程简述
———学习总结稿
• 一、通用整车开发流程概述 • 二、整车流程开发的阶段工作
2.1-PM在整车开发的具体内容 2.2-PE在整车开发的具体内容
2.2.1-造型设计 2.2.2-工程数据发布 2.2.3- (骡子)样车试制、试验 2.2.4-工程样车试制至SOP
2.3-ME在整车开发的具体内容
2.2.2.工程数据发布: 在项目开发初期阶段总布置工程师开始介入进 行整车布置工作。 为整车总成系统提供边界条件、参与组织数据 的整车评审并规定数据开发、设计的时间节点。 底盘、动力、电器、车身系统各工程师在唯一 造型确定后开始具体的结构设计。 在G5节点完成 工程样车数据的发布。 主要经历概念车数据发布、结构车数据发布以 及最终的集成车数据发布。
二、整车流程开发的阶段工作
2.1-PM在整车开发的具体内容 2.2-PE在整车开发的具体内容
2.2.1-造型设计
2.2.2-工程数据发布 2.2.3- (骡子)样车试制、试验 2.2.4-工程样车试制至SOP
2.3-ME在整车开发的具体内容
2.1、PM在整车开发的具体内容
在项目前期(G8)发布立项 建议书: ①.提出项目目标: SOP目标、 目标生产场地 、宏观市场、 价格范围、预计生产纲领、竞 争产品、边际利润 等。 ②.Dev Veh BOM 整车开发物 料清单.初步确定在整车开发 项目中的沿用系统、新开发系 统、匹配修改系统。 ③.Dev VTS: 发布整车技术条件。 ④在项目进行阶段参与项目文 件编制、进行设计评审、协调 各部门工作、控制节点进度等。 项目后期制定初步的维修服务 信息以及协调完成PPAP工作。
G8 (DSI):发布立项建议书,确定整车开发的边界条件、开发的主体方向(SOP 目标、目标生产基地、宏观市场、价格范围、预生产能力、竞争产品、边界利 各节点主要介入人员及主要工作: 润、初步质量策略、质量目标等)。 G7(VPI) :通过对造型主题的评审,确定唯一造型主题,结合立项建议书,方案 正式批准启动。同时开始骡子车的试制工作。 G6(CSO) :此节点前需完成内外饰造型数据的冻结,并完成批量制造模具和生 产设备等投资批准 。 进行骡子车的关键试验及标定工作。 G5(VDR) :发布A面数据、发布所有内外饰表面数。在G5~G4间实现工程样车数 据发布,实现首辆工程样车的试制工作,并开始相关试验标定工作 G4(PPV) :完成产品及工艺的验证。完成焊装、涂装、冲压、总装的工艺验证。 G3(MVB/ns) :预、试生产阶段。对整车质量、性能进行评估;生产线设备预验 收。
2.2.3.(骡子)样车试制、试验: 所谓骡子车,是属于试制样车的一种,一 般是在全新平台的车型开发中实施。 在整车开发的早期阶段,完成了动力总成、 底盘等机械部件的基本开发之后,为了测 试其性能而制作的一辆可以行驶的整车样 车。骡子可以是在某一辆参考车型上修改, 将新开发部分的待测试样件安装上去;也 可以是基于已开发的车身结构做部分样件, 将待测试样件安装上去,并借用部分参考 车型上的零件拼装而成。 此阶段的样车不代表未来产品的外观,并且拼凑了不同车型上的零件.制作该车的目的主要是,在完成一 个结构平台的研究后,需要对多辆样车进行系列分析、试验和验证,从而确保下一阶段开发的顺利进展 . 一般在G5节点前完成了骡子车的试制、试验、标定工作。
• 三、SOR概述
SOR,可以理解为技术条件。在工程过程、任务、事项、交付方式对潜在供应商的要 求. 商务协议及合同作具体要求,如:价格、购货合同、交货日期、零件数量和质量、 关键标准事项等等. SOR技术条件所包含的主要内容如下: 1.项目信息: 简述项目的基本信息及开发件的基本情况。 2.法规要求: 供应商生产的零部件必须满足现行的法规要求(强制标准要求),在 进行OTS 时,供应商必须提供认证证书或合格的检验报告。 3.产品要求: ①概要:说明零件或子系统总要求,内容包括整体质量水平、功能、造型、主要结 构、新技术、新材料、法规项等。 ②系统要求:填写在功能系统中对待开发零部件的要求 。 ③统一性要求:零部件除应符合图样及各项技术规范的要求外,还应符合本SOR的 要求。图样、技术规范及SOR的任何一项有更改时,零件应符合更改后的要求。 ④材料:所有的材料必须符合企业/国家工程材料的技术要求,材料的选择由供应商 根据设计、耐久性和性能要求(见图纸和技术规范),供应商有责任提供每个零部 件的详细的材料目录并标识,塑料件应标识是否可回收利用。 ⑤装饰、外观、灯光、颜色的要求 ⑥标识和可追溯 ⑦噪声和异响
工程样车的试制数量的需求:主要包括 用于ABS标定、电喷系统标定、公告样车 需求、安全气囊验收等。
2.3-ME在整车开发的具体内容
1.项目前期制定新产品开发所需的制造成本投资预算 2.制定整车生产四大工艺的制造策略 3.确定制造工艺策略 4.在概念车数据发布过程中同时进行概念车工艺数据的发布,概念车工艺数据发布后进 行概念车模具设计阶段。 5.在结构车数据发布过程中同时进行结构车工艺数据的发布,结构车工艺数据发布后进 行结构车模具设计阶段。 6.在集成车数据发布过程中同时进行集成车工艺数据的发布,集成车工艺数据发布后进 行集成车模具设计阶段。 7.在G2节点前,完成所有模具的调试及试模工作。 8.在G4节点,完成首台PPV白车身,以及首台PPV整车,以实现在G4节点验证生产的工艺 性。
SOR技术条件所包含的主要内容如下: 1.项目信息: 简述项目的基本信息及开发件的基本情况。 2.法规要求: 供应商生产的零部件必须满足现行的法规要求(强制标准要 求),在进行OTS 时,供应商必须提供认证证书或合格的检验报告。 3.产品需求: 3.1概要:说明零件或子系统总要求,内容包括整体质量水平、功能、造型、 主要结构、新技术、新材料、法规项等。 3.2系统要求:填写在功能系统中对待开发零部件的要求 。 3.3统一性要求:零部件除应符合图样及各项技术规范的要求外,还应符合 本SOR的要 求。图样、技术规范及SOR的任何一项有更改时,零件应符 合更改后的要求。 3.4材料:所有的材料必须符合企业/国家工程材料的技术要求,材料的选择 由供应商根据设计、耐久性和性能要求(见图纸和技术规范),供应商有 责任提供每个零部件的详细的材料目录并标识,塑料件应标识是否可回收 利用。 3.5装饰、外观、灯光、颜色的要求 3.6标识和可追溯 3.7噪声和异响
SOR技术条件所包含的主要内容:
7、试验认证: 7.1、认证工作由供应商完成具有代表性的零部件实验室耐久性试验,试验指标应满足整车公司提 出的潜在顾客使用要求和极端环境测试.所有的零部件都应符合这些要求,并在原型车制造前完 成。 7.2、整车公司 有责任进行整车集成系统性认证. 在整车平台设计认证进行的过程中零部件供应 商有责任及时响应所有的问题. 所有问题引起的改变供应商都要通过PPAP批准流程.。 7.3、零部件的集成和认证是供应商的责任, 供应商必须完成零部件在图纸中的特殊性能测试和/ 或附加的测试 。 7.4、零部件供应商应提供零部件测试计划给整车公司相关工程师批准.计划必须包括:最小的测 试样品数,测试顺序,测试地点,时间. 8、工装要求: 关于工装的设计,供应商可以与整车公司PE和ME以及其他供应商讨论以获得更好的方案。 8.1、提交模具、检具、夹具清单 8.2、供应商的工装在生产前需得到整车公司技术人员的评审与批准。 8.3、模具痕迹:会影响零件质量的浇口、顶杆和分模线位置,必须在开始制造前得到整车厂技 术人员的批准。 8.4、模具验证:新投产的模具必需进行生产验证阶段,以保证零部件与整车的配合精度。为解 决整车配合问题而进行的模具调整,不属于工程更改,供应商应按要求,控制样件的生产数量, 积极配合,并承担相应的模具调整费用。 8.5、产能要求:产能必须符合整车厂的要求,具体需与整车厂采购部门联系。
2.2.4.工程样车试制至SOP 1.P2数据的发布 2.签订商务、技术协议 3.正式商务定点 4.监督供应商模具、夹具、检具完成情况 5.监督供应商关键试验进行情况 6.跟踪搭载件的送样时间 7.OTS样件装车验证 8.工程试验车路试验证 9.整合相关OTS件性能、尺寸、材料报告 以及路试报告,完成零部件OTS认可。 10.提交OTS认可资料,由采购部完成 PPAP流程