渗碳层深度不合格的原因与防止方法
渗碳缺陷及质量控制
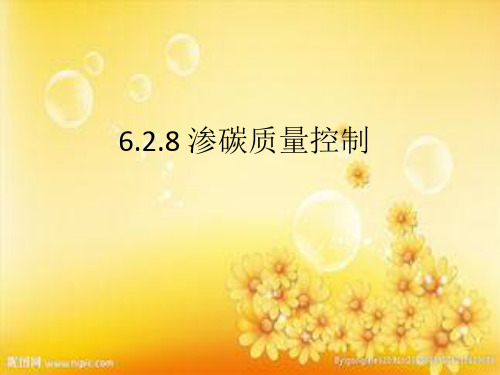
4 过热 渗碳时或渗碳后加热时过热,表现为钢
的晶粒过大。
危害:增加脆性,增加表面碳化物的数量, 并形成粗大碳化物,甚至形成莱氏体,使 零件报废。
消除办法:进行正火后再淬回火。
5 表面氧化和脱碳
原因: 渗碳后期渗碳气氛浓度过低,或渗碳后 冷却及淬火加热时保护不良。
危害:降低了表面硬度和耐磨性,也降低了接触疲 劳强度,淬火时易开裂。
危害:降低表面硬度和接触疲劳、弯曲疲劳 性能,淬火易变形。
消除办法:进行高温回火后,重新加热淬火 或冷处理。
3 黑色组织
所谓黑色组织是指在渗层内的组织中沿晶界出现断续 网状渗碳体及铁素体和黑色的非马氏体组织,其特征颇似 过烧组织。深度约为0.03-0.05毫米左右。 产生原因:出现黑色组织的原因,目前还没有取得一致的看 法。一般认为,可能是由氧化和深层淬透性不足引起的。 危害:降低表面硬度和耐磨性,缩短零件使用寿命。 消除办法:减少氧化性气氛,增加炉子的密封性,排气充分; 同时应加快冷却速度以减少非马氏体体组织的出现。 。
根据分析的数据作出含碳最与离表面距离的分布 曲线,该曲线反映出渗层浓度分布情况。
二、渗碳件常见缺陷
1 渗碳层中有网状或大块状碳化物 2 渗层中有大量的残余奥氏体 3 黑色组织 4 过热 5 表面脱碳 6表面含碳量过低渗层深度不足 7 渗碳层过深 8 渗碳层不均匀 9 表面腐蚀及氧化 10 心部硬度不足 11心部出现过多的铁素体 12反常组织
对严格要求渗层的产品只能报废。
8 渗碳层不均匀
产生原因:零件表面不清洁或积碳,炉温不均,气 氛循环不良或漏气,原材料带状偏析严重。
危害:性能不均,降低使用寿命。 消除办法:补渗 为避免层深增加太多,可适当取低
点的渗碳温度
渗碳件常见的缺陷及防止和补救措施
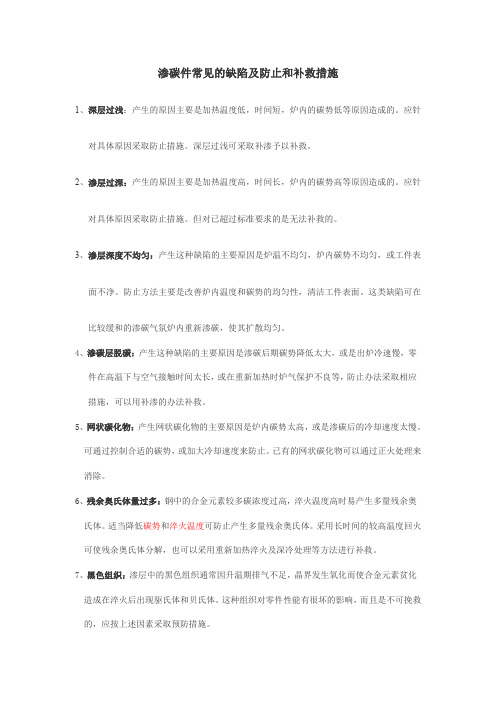
渗碳件常见的缺陷及防止和补救措施1、深层过浅:产生的原因主要是加热温度低,时间短,炉内的碳势低等原因造成的。
应针对具体原因采取防止措施。
深层过浅可采取补渗予以补救。
2、渗层过深:产生的原因主要是加热温度高,时间长,炉内的碳势高等原因造成的。
应针对具体原因采取防止措施。
但对已超过标准要求的是无法补救的。
3、渗层深度不均匀:产生这种缺陷的主要原因是炉温不均匀,炉内碳势不均匀,或工件表面不净。
防止方法主要是改善炉内温度和碳势的均匀性,清洁工件表面。
这类缺陷可在比较缓和的渗碳气氛炉内重新渗碳,使其扩散均匀。
4、渗碳层脱碳:产生这种缺陷的主要原因是渗碳后期碳势降低太大,或是出炉冷速慢,零件在高温下与空气接触时间太长,或在重新加热时炉气保护不良等,防止办法采取相应措施,可以用补渗的办法补救。
5、网状碳化物:产生网状碳化物的主要原因是炉内碳势太高,或是渗碳后的冷却速度太慢。
可通过控制合适的碳势,或加大冷却速度来防止。
已有的网状碳化物可以通过正火处理来消除。
6、残余奥氏体量过多:钢中的合金元素较多碳浓度过高,淬火温度高时易产生多量残余奥氏体。
适当降低碳势和淬火温度可防止产生多量残余奥氏体。
采用长时间的较高温度回火可使残余奥氏体分解,也可以采用重新加热淬火及深冷处理等方法进行补救。
7、黑色组织:渗层中的黑色组织通常因升温期排气不足,晶界发生氧化而使合金元素贫化造成在淬火后出现驱氏体和贝氏体。
这种组织对零件性能有很坏的影响,而且是不可挽救的,应按上述因素采取预防措施。
8、芯部硬度偏高:1.降低淬火温度,但是降低淬火温度后注意可能有铁素体析出。
2.使用冷速慢的油,但有可能表面硬度不均,硬化层不均.3.降低油搅拌的速度,在油冷速慢的油温使用.淬火油甚至不搅拌.4.加大有效尺寸,比如把孔中加实心工装,增大热容量,降低冷速.5. 检测原材料的化学成分,是否有超标。
原始含碳两越高,心部硬度越高。
对于薄壁件,心部硬度降不下来,厚大的件,心部硬度提不上来.因此针对某种产品选择原材料的含碳量是最重要的.热处理只能在很小的范围内调节.。
渗碳件常见缺陷及防止措施

淬火温度低,或重新加热淬火保温时间不够
渗层浓度不够
炉温低,渗层活性低,炉子漏气或渗碳盐浴成分不正常加强炉温校验,及炉气成分或盐浴成分的监测
渗层深度不均匀
炉温不均匀:炉内气氛循环不良;升温过程中工件表面氧化;碳黑在工件表面沉积;工件表面氧化皮等没有清理干净;固体渗碳时渗碳箱内温差大及催渗剂拌和不均匀
渗碳件常见缺陷及防止措施
缺陷形式
形成原因及防止措施
表层粗大块状或网状碳化物
渗碳剂活性太高或渗碳保温时间过长
降低渗剂活性当渗层要求较深时,保温后期适当降低渗剂活性
表层大量残余奥氏体
淬火温度过高,奥氏体中碳及合金元素含量高
降低渗剂活性,降低直接淬火或重新加热淬火的温度
表面脱碳
渗碳后期渗剂活性过分降低,气体渗碳炉漏气.液体渗碳时碳酸盐含量过高,在冷却罐中及淬火加热时保护不当,出炉时高温状态在空气中停留时间过长
渗碳后慢冷时组织转变不均匀所致,如18CrMnMo钢渗碳后空冷时,在表层托氏体下面保留了一层未转变的奥氏体,后者在随后的冷却过程中或室温停留过程中转变为马氏体,使表面产生拉应力而出现裂纹
减速慢冷却速度,使渗层完成共析转变,或加快冷却速度,使渗层全部转变马氏体加残余奥氏体
表面非马氏体组织
渗碳介质中的氧向钢中扩散,在晶界上形Cr,Mn等元素的氧化物,致使该处合金元系贫化,淬透性降低,淬火后出理黑色网状组织(托氏体)控制炉内介质成分,降低氧的含量,提高淬火速度,合理选择钢材
反常组织
当钢中含氧量较高(沸腾钢),固体渗碳时渗碳后冷却速度过慢,在渗碳层中出现先共析渗碳体网周围有铁素体层,淬火后余奥氏体量过多,或表面形成托氏体网
表面腐蚀和氧化
渗剂中含有硫或硫酸盐,催渗剂在工件表面熔化;液体渗碳后工件表面粘有残盐有氧化皮工件涂硼砂重新加热淬火等均引起腐蚀
渗碳常见的五种缺陷和相应的防止方法

书山有路勤为径,学海无涯苦作舟
渗碳常见的五种缺陷和相应的防止方法
一、碳浓度过高
1、产生原因及危害:假如渗碳时急剧加热,温度又过高或固体渗碳时用全新渗碳剂,或用强烈的催渗剂过多都会引起渗碳浓度过高的现象。
随着碳浓度过高,工件表面出现块状粗大的碳化物或网状碳化物。
由于这种硬脆组织产生,使渗碳层的韧性急剧下降。
并且淬火时形成高碳马氏体,在磨削时容易出现磨削裂纹。
⒉防止的方法
①不能急剧加热,需采用适当的加热温度,不使钢的晶粒长大为好。
假如渗碳时晶粒粗大,则应在渗碳后正火或两次淬火处理来细化晶粒。
②严格控制炉温均匀性,不能波动过大,在反射炉中固体渗碳时需特别注意。
③固体渗碳时,渗碳剂要新、旧配比使用。
催渗剂最好采用47%的BaCO3,不使用Na2CO3 作催渗剂。
二、碳浓度过低
⒈产生的原因及危害:温度波动很大或催渗剂过少都会引起表面的碳浓度不足。
最理想的碳浓度为0.91.0%之间,低于0.8%C,零件容易磨损。
⒉防止的方法:
①渗碳温度通常采用920940℃,渗碳温度过低就会引起碳浓度过低,且延长渗碳时间;渗碳温度过高会引起晶粒粗大。
②催渗剂(BaCO3)的用量不应低于4%。
三、渗碳后表面局部贫碳:。
渗碳件的缺陷有哪些及防止措施

渗碳件的缺陷有哪些?如何防止渗碳缺陷?(1)渗碳层中网状或大块花碳化物产生的原因是渗碳碳势太高,使表面渗层含碳量太高合渗碳后冷却速度过慢。
网状碳化物增加了表面脆性,渗层容易剥落,降低使用寿命,容易使零件表面在淬火或磨削加工中产生裂纹。
消除的办法是进行Acm以上的高温淬火或正火。
预防办法是减低炉内碳势,延长扩散时间。
(2)渗碳层中大量残余奥氏体产生的原因是渗碳剂浓度太高使表面含碳量过高、淬火温度太高。
消除的办法是进行高温回火后重新加热淬火+回火或冷处理+回火。
预防措施:降低炉内碳势,选择较低的淬火温度。
淬火剂温度偏高也是原因之一。
淬火剂的温度越低,淬火冷却的终止温度距离马氏体转变终止点Mf也就越近,马氏体转变进行越充分,残余奥氏体就越少。
反之,淬火剂温度高了,则残余奥氏体量也就多了。
(3)反常组织一般在含氧量较高的钢(如沸腾钢)固体渗碳时出现,其特征是网状碳化物和珠光体之间被一层铁素体所分离。
这种组织淬火后易出现软点。
消除的办法是适当提高淬火温度或适当延长淬火加热的保温时间,以便使组织均匀化,并选用更为剧烈的冷却剂淬火。
(4)渗碳零件中形成魏氏组织在高温下进行长时间渗碳后,奥氏体晶粒会急剧长大,碳浓度也大大增加,在随后的缓慢冷却中,二次渗碳体很易于沿奥氏体晶粒的一定晶面析出,形成穿插在晶粒内部的白亮色的粗针,这种组织称为过共析魏氏组织。
产生的原因是长时间过热渗碳和渗碳后冷却太缓慢。
这种组织可通过渗碳后的两次家人淬火予以改善或完全消除。
在渗碳件的心部出现魏氏组织,这种魏氏组织的针状物是先共析铁素体。
形成的原因是:①原材料为本质粗晶粒钢或原始组织中已有魏氏体组织,通过高温长时间渗碳,晶粒会更加粗大,在随后的缓慢冷却中,先共析铁素体以针状自晶界向晶内析出或在晶粒内部单独呈针状析出而形成白亮针状的魏氏组织。
②渗碳工艺不当。
渗碳温度过高,保温时间太长,奥氏体晶粒特别粗大,导致冷却后出现魏氏组织,这种组织具有明显的过热特征。
钢件渗碳处理的质量检验以及缺陷补偿

钢件渗碳处理的质量检验以及缺陷补偿钢件渗碳处理的质量检验以及缺陷补偿在生产加工中,无论是哪种加工工艺都会出现缺陷,缺陷的产生也是每个生产者所苦恼的问题。
因为一旦产生缺陷,不仅无法保证产品质量,对于资源也造成了浪费。
所以,质量检验与缺陷补偿就显得十分重要。
一、渗碳件的检验对于渗碳件来说,进行质量检验是不能忽视的问题。
神探见必须要按照技术要求进行质量检验,主要的检查项目有以下几个方面:1、硬度:渗碳件的硬度检查应在工件淬火并回火后进行。
渗层心部和防渗部位均需要进行硬度检查,所测出的硬度值应符合技术要求。
2、渗碳层深度:渗碳层深应保证传递到心部的应力小于心部的强度。
此外,为保证工件有足够的耐磨性,在整个磨损层内的碳含量不应低于共析成分,并据此来选择要求的层深。
检查渗层深度的试样是在试棒或工件上截取的。
试棒或工件应缓慢冷却,若不是缓冷,则应经过适当的退火之后再截取试样。
渗碳层深度的确定目前还没有统一的标准,一般,合金渗碳钢的渗层深度是从表面测到出现原始组织位置,并要求过共析层加上共析层的厚度应该不少于所测定的50%到75%。
另一种方法是将通过共析层、共析层和亚共析层的一半作为渗层深度。
这种方法对碳素渗碳钢和合金渗碳钢均适用。
3、渗碳层及心部的金相组织:这个检查项目应该用工件来做。
对渗碳层组织的检查主要看淬火后渗层中马氏体的粗细、未熔碳化物数量和分布情况以及残余奥氏体量等是否正常。
对心部组织的检查主要是看铁素体数量,大小以及分布情况是否正常。
二、渗碳件的常见缺陷1、过渗碳渗碳表面出现粗大块状碳化物以及网状碳化物,主要是由于渗碳剂活性太高,或渗碳保温时间过长。
气体渗碳时适当减少渗碳剂滴量或固体渗碳时适当降低催渗剂含量,可防止发生过渗碳。
对于已经出现过渗碳的工件,可以通过高温加热扩散或提高淬火加热温度,延长保温时间重新淬火的办法进行补救。
2、晶界氧化在含有水和二氧化碳的气氛中进行气体渗碳时,因这两种物质与钢发生反应而在晶界形成氧化物的现象,叫做晶界氧化。
渗碳零件的质量检验及缺陷预防

渗碳零件的质量检验及缺陷预防渗碳化学热处理工艺是通过改变零件表面化学成分及显微组织,使得零件表面具有高硬度、高耐磨性、高接触疲劳强度,心部应具有良好的综合力学性能。
文章结合渗碳零件宏观质量检验及微观质量检验的基本内容,论述了渗碳零件的热处理缺陷产生的原因及不同缺陷的解决措施。
标签:渗碳零件;质量检验;解决措施1 概述在现代工业中,齿轮、凸轮及其他磨损件承受了一定的摩擦力、交变弯曲应力、接触疲劳应力、一定的冲击力。
失效形式有过量磨损,表面剥落、断裂等。
所以要求表面具有高硬度、高的接触疲劳抗力和良好的耐磨性,而心部有一定的塑韧性[1]。
通过改变这些零件表面化学成分及显微组织的渗碳、渗氮、渗硼等化学热处理工艺,使得零件表面具有高硬度、高耐磨性、高接触疲劳,心部应具有良好的综合力学性能[2]。
渗碳钢碳含量为0.12%~0.25%(质量),锰、铬、镍的作用是提高渗碳钢的淬透性,淬火时心部能获得大量的板条马氏体组织。
钛、钒、钨、钼等能细化晶粒。
锰、铬、镍等元素还能改善渗碳层性能。
渗碳层性能有表层含碳量、表层浓度梯度和渗碳层深度。
表层含碳量0.80%~1.05%(质量分数),碳的浓度梯度宜平缓过渡,以免性能变化太大,增大内应力。
铬、锰、钼有利于渗碳层增厚,而钛、钒减小渗碳层厚度。
镍、硅等元素不利于渗碳层增厚,一般渗碳钢中不用硅合金化。
钢中碳化物形成元素含量过高,在渗碳层中产生块状碳化物,造成表面脆性,所以碳化物和非碳化物形成元素含量要适当。
渗碳零件由于表面化学成分及显微组织都发生变化,加之要进行淬火及回火热处理工艺,所以常产生热处理缺陷,降低零件的弯曲强度、疲劳强度及耐磨性能。
因此,加强渗碳零件的质量检验及缺陷预防,对于提高力学性能、延长产品寿命、节约材料、促进可持续发展具有实际意义[3]。
2 渗碳零件的质量检验内容2.1 渗碳零件的外观及硬度检验渗碳零件的外观检验属于宏观检验方法,主要有渗碳零件表面的无氧化检验、锈蚀检验、剥落检验、机械碰伤检验、表面裂纹检验等。
渗碳齿轮热处理常见缺陷及预防措施

保持热处理过程中温度和冷却速度的稳定性、加强齿轮结构 设计等。
02
预防措施
选用高质量渗碳剂
确保渗碳剂质量
选用由正规厂家生产、质量稳定的渗 碳剂,避免因渗碳剂质量问题导致热 处理缺陷。
查验成分含量
避免混用不同牌号渗碳剂
不同牌号的渗碳剂成分和性能有所差 异,避免混用以免影响热处理效果。
对渗碳剂的成分含量进行严格检验, 确保其符合工艺要求。
渗碳剂的选用和调整
选用
根据齿轮的材质和热处理需求,选择合适的渗碳剂。
调整
根据实际操作情况,对渗碳剂的成分和比例进行适当调整,以确保齿轮能够获得理想的 渗碳效果。
渗碳过程的控制
温度控制
保持渗碳炉内的温度稳定 ,以避免齿轮在渗碳过程 中出现不均匀的温度分布 。
时间控制
渗碳过程应控制在适当的 温度和时间下进行,以确 保齿轮能够充分吸收碳元 素。
淬火过程的控制
温度控制
保持淬火炉内的温度稳定,以避 免齿轮在淬火过程中出现不均匀 的温度分布。
时间控制
淬火过程应控制在适当的温度和 时间下进行,以确保齿轮能够获 得理想的硬度和耐磨性。
冷却控制
淬火后的冷却过程也需严格控制 ,以避免齿轮出现裂纹或其他淬 火缺陷。
04
渗碳齿轮热处理质量检测方法
渗碳层深度检测
预防措施
提高渗碳温度、延长渗碳时间、优化 炉内气氛等。
渗碳层碳浓度不均匀
原因
渗碳层碳浓度不均匀可能是由于渗碳过程中温度波动大、炉内气氛不稳定、渗碳剂分布不均匀等原因引起的。
预防措施
保持渗碳过程中温度稳定、优化炉内气氛、均匀分布渗碳剂等。
齿轮表面粗糙
原因
齿轮表面粗糙可能是由于渗碳后表面残渣未清理干净、热处理过程中氧化脱碳严重等原因引起的。
渗碳件常见缺陷与对策

渗碳件常见缺陷与对策一、渗碳层出现大块状或网状碳化物缺陷产生原因:1、表面碳浓度过高;2、滴注式渗碳,滴量过大;3、控制气氛渗碳,富化气太多;4、液体渗碳,盐浴氰根含量过高;5、渗碳层出炉空冷,冷速太慢;对策:1、降低表面碳浓度,扩散期内减少滴量和适当提高扩散期湿度,也可适当减少渗碳期滴量;2、减少固体渗碳的催碳剂;3、减少液体渗碳的氰根含量;4、夏天室温太高,渗后空冷件可吹风助冷;5、提高淬火加热温度50~80ºC并适当延长保温时间;6、两次淬火或正火+淬火,也可正火+高温回火,然后淬火回火;二、渗层出现大量残余奥氏体缺陷产生原因:1、奥氏体较稳定,奥氏体中碳与合金元素的含量较高;2、回火不与时,奥氏体热稳定化;3、回火后冷却太慢;对策:1、表面碳浓度不宜太高;2、降低直接淬火或重新加热淬火温度,控制心部铁素体的级别≤3级;3、低温回火后快冷;4、可以重新加热淬火,冷处理,也可高温回火后重新淬火;三、表面脱碳缺陷产生原因:1、气体渗碳后期,炉气碳势低;2、固体渗碳后,冷却速度过慢;3、渗碳后空冷时间过长;4、在冷却井中无保护冷却;5、空气炉加热淬火无保护气体;6、盐浴炉加热淬火,盐浴脱氧不彻底;对策:1、在碳势适宜的介质中补渗;2、淬火后作喷丸处理;3、磨削余量,较大件允许有一定脱碳层(≤0.02mm);四、渗碳层淬火后出现屈氏体组织(黑色组织)缺陷产生原因:渗碳介质中含氧量较高:氧扩散到晶界形成Cr、Mn、Si的氧化物,使合金元素贫化,使淬透性降低。
对策:1、控制炉气介质成分,降低含氧量;2、用喷丸可以进行补救;3、提高淬火介质冷却能力;五、心部铁素体过多,使硬度不足缺陷产生原因:1、淬火温度低;2、重新加热淬火保温时间不足,淬火冷速不够;3、心部有未溶铁素体;4、心部有奥氏体分解产物;对策:1、按正常工艺重新加热淬火;2、适当提高淬火温度延长保温时间;六、渗碳层深度不足缺陷产生原因:1、炉温低、保温时间短;2、渗剂浓度低;3、炉子漏气;4、盐浴渗碳成分不正常;5、装炉量过多;6、工件表面有氧化皮或积炭;对策:1、针对原因,调整渗碳温度、时间、滴量与炉子的密封性;2、加强新盐鉴定与工作状况的检查;3、零件应该清理干净;4、渗层过薄,可以补渗,补渗的速度是正常渗碳的1/2,约为0.1mm/h 左右;七、渗层深度不均匀缺陷产生原因:1、炉温不均匀;2、炉内气氛循环不良;3、炭黑在表面沉积;4、固体渗碳箱内温差大与催渗剂不均匀;5、零件表面有锈斑、油污等;6、零件表面粗糙度不一致;7、零件吊挂疏密不均;8、原材料有带状组织;对策:1、渗碳前严格清洗零件;2、清理炉内积炭;3、零件装夹时应均匀分布间隙大小相等;4、经常检查炉温均匀性;5、原材料不得有带状组织;6、经常检查炉温、炉气与装炉情况;八、表面硬度低缺陷产生原因:1、表面碳浓度低;2、表面残余奥氏体多;3、表面形成屈氏体组织;4、淬火温度高,溶入奥氏体碳量多,淬火后形成大量残余奥氏体;5、淬火加热温度低,溶入奥氏体的碳量不够,淬火马氏体含碳低;6、回火温度过高;对策:1、碳浓度低,可以补渗;2、残余奥氏体多,可高温回火后再加热淬火;3、有托氏体组织,可以重新加热淬火;4、严格热处理工艺纪律;九、表面腐蚀和氧化缺陷产生原因:1、渗剂不纯有水、硫和硫酸盐;2、气体渗碳炉漏气固体渗碳时催渗剂在工件表面融化,液体渗碳后,工件表面粘有残盐;3、高温出炉,空冷保护不够;4、盐炉校正不彻底,空气炉无保护气氛加热,淬火后不与时清洗;5、零件表面不清洁;对策:1、严格控制渗碳剂与盐浴成分;2、经常检查设备密封情况;3、对零件表面与时清理和清洗;4、严格执行工艺纪律;十、渗碳件开裂缺陷产生原因:1、冷却速度过慢,组织转变不均匀;2、合金钢渗后空冷,在表层托氏体下面保留一层未转变奥氏体在随后冷却或室温放置时,转变成马氏体,比容加大,出现拉应力;3、第一次淬火时,冷却速度太快或工件形状复杂;4、材质含提高淬透性的微量元素(Mo、B)太多等;对策:1、渗后减慢冷却速度,使渗层在冷却过程中完全共析转变;2、渗后加快冷却速度,得到马氏体+残余奥氏体。
浅谈渗碳工艺缺陷及预防措施

浅谈渗碳工艺缺陷及预防措施张曙灵 吴 镝(焦作大学,河南焦作 454000)摘要:以煤矿机械广泛使用的渗碳齿轮为例,详细分析热处理过程中的各种缺陷,指出产生缺陷的原因,提出了预防措施及各种工艺方法,对提高制造渗碳齿轮的质量有一定的指导作用。
关键词:渗碳 硬化层 淬火 预防措施Ξ中图分类号:TH162 文献标识码:A 文章编号:1008Ο7257(2001)04Ο0053Ο04渗碳齿轮在煤矿机械中有着广泛应用。
采煤机、运输机、提升机中都有许多渗碳齿轮,现场使用表明,齿轮的失效多数与渗碳齿轮在热处理过程中的许多缺陷有关。
如表层和心部硬度不够,表层过度渗碳与硬化层偏浅,渗碳层深度不均匀,表层内氧化等。
这些缺陷在生产和应用中危害极大,严重地影响齿轮的寿命,更有甚者影响到整个机器的寿命。
因此探讨渗碳齿轮热处理缺陷及预防措施,对于提高煤矿机械的性能、使用可靠性有着重大意义。
本文根据渗碳齿轮制造及使用中出现的问题,分析并提出一些具体的工艺措施。
1.渗碳齿轮热处理缺陷及工艺措施111 齿轮表层过度渗碳渗碳齿轮由于处理不当过度渗碳后,表层将会出现块状、网状碳化物,使用时齿轮塑性变形能力降低,耐冲击性减弱,轮齿根部弯曲疲劳性能下降,齿尖角变脆,易于崩裂,淬火后渗碳齿轮在磨削加工时易于开裂。
11111 齿轮过度渗碳的原因(1)齿轮在固体介质中渗碳时渗碳箱内碳势过高,又不能任意调整碳势,因此渗碳温度越高,时间越长,表层过共析程度就越大。
特别对含有强碳化合物形成元素Cr、M o的渗碳钢,碳的扩散较慢,齿轮渗碳层表面碳浓度更高,达到过共析成份的渗碳层,在冷却时,从奥氏体晶界析出渗碳体形成网状分布。
(2)在气体介质中渗碳时,若渗碳炉内碳势过高,强渗时间过长,也会出现齿轮表层渗碳过度。
11112 预防措施(1)固体渗碳时,为了防止碳势过高造成过度渗碳,可以采用较低的渗碳温度或使用较弱的渗碳剂(新渗碳剂和旧渗碳剂混合使用)。
(2)气体渗碳时,为了防止表层过度渗碳,在渗碳后期安排扩散阶段。
气体渗碳的常见缺陷和预防措施

櫡櫡櫡櫡櫡櫡櫡櫡~现场经验櫡櫡櫡櫡櫡櫡櫡櫡~收稿日期:2020 01 14作者简介:赵步青(1943—),男,江苏阜宁人,高级工程师,研究方向为工模具热处理工艺,已发表论文和实用性文章共270余篇,出版热处理专著5部,协编图书两部。
联系电话:15067596339;E mail:zsg4272@163.com气体渗碳的常见缺陷和预防措施赵步青,朱 敏,高旭华,徐利建(浙江省金华市华南汽配有限公司,浙江金华321000)中图分类号:TG157 文献标志码:B 文章编号:1008 1690(2020)02 0048 03CommonDefectsforGasCarburizingandPreventiveMeasuresZHAOBuqing,ZHUMin,GAOXuhua,XULijian(ZhejiangJinhuaHuananAutomobiveFittingsCo.,Ltd.,Jinhua321000,ZhejiangChina)0 引言气体渗碳是制造业应用最广泛的化学热处理工艺。
渗碳并淬火和低温回火的低碳钢工件表面硬度和疲劳强度高、耐磨性好,且心部具有足够的强度和韧性。
华南汽配公司是生产汽车防滑链的民营企业,大部分产品都要进行气体渗碳。
渗碳炉有网带炉、井式炉和滚筒炉,产品质量稳定。
本文为生产实践经验的总结,介绍30多年来遇到的以及同行提供的常见的12种气体渗碳缺陷,供参考。
1 粗大针状马氏体通常,设计人员对渗碳件淬火后渗层的马氏体都会提出级别要求。
对于汽车防滑链,要求其渗碳层马氏体针≤4级。
图1为由于渗碳温度过高和炉气氛碳势较高造成的渗层粗大马氏体组织。
为了防止产生这种缺陷,必须调整渗碳气氛的碳势,降低渗碳温度,加强炉前的抽样检查。
2 网状碳化物根据经验,碳化物的形态、数量、大小及分布对渗碳件的性能有很大影响。
图2为渗碳层中严重的网状碳化物。
其产生的原因有3点:①滴注式渗碳时,煤油或其他渗剂滴量太大;②控制气氛渗碳的富化气用量太大;③渗碳后直接淬火的温度过高且冷却较慢。
20cr2ni2mo渗碳淬火抗拉不合格

20cr2ni2mo渗碳淬火抗拉不合格
20Cr2Ni2Mo渗碳淬火抗拉不合格可能是由多个因素导致的。
以下是一些可能的原因和相应的解决方案:
碳含量控制不佳:渗碳淬火过程中,碳含量的控制至关重要。
碳含量过低会导致渗碳效果不佳,碳含量过高则可能导致淬火开裂。
因此,要确保渗碳过程中碳含量的控制精度,并采用适当的淬火工艺。
淬火温度过高或过低:淬火温度过高可能导致材料过烧,淬火温度过低则可能使材料得不到充分的淬火。
因此,要选择适当的淬火温度,并保持温度的均匀性和稳定性。
冷却速度不当:淬火过程中,冷却速度过快可能导致淬火开裂,冷却速度过慢则可能使材料得不到充分的淬火。
因此,要选择适当的冷却速度,并保持冷却的均匀性和稳定性。
渗碳层深度不足:渗碳层深度不足可能导致抗拉强度不合格。
因此,要确保渗碳层深度的控制精度,并选择适当的渗碳工艺参数。
原材料质量不佳:原材料质量不佳可能导致抗拉强度不合格。
因此,要选择质量可靠的原材料,并进行质量检测和控制。
针对以上可能的原因,可以采取相应的措施进行改进和优化,以提高20Cr2Ni2Mo
渗碳淬火抗拉强度。
同时,建议在生产过程中加强质量控制和检测,及时发现并解决问题,确保产品的质量和稳定性。
渗碳层深度不合格的原因与防止方法

渗碳层深度不合格的原因与防止方法1、渗层太浅(1)原因●炉温偏低,渗碳时间短。
●装炉量过多或新工装没有补渗,没有增加煤油滴量。
●排气不充分就进入强渗期。
●炉子密封不严,炉气压力过低。
●工件表面被炭黑或覆盖影响活性碳原子被钢件吸收。
●操作者判断渗层试样失误。
(2)被救方法:重新入炉进行被渗处理,将原试样同炉被渗。
2、渗层过深(1)原因●渗碳温度偏高,渗入时间过长。
●碳势太高,加快了渗碳速度。
●仪表失灵跑温。
●操作者判断出炉试样失误。
(2)处理意见:一般应报废或打不合格品让步接收报告。
3、渗层不均原因●装炉量过多,工件之间未留间隔,互相接触。
●工件表面有油污和锈斑。
●炉内气氛不均匀,局部有死角。
●炉罐长期不清理。
●炉内没安装导风板或已损坏。
4、过共析+共析层过深(1)原因●强渗期炉内碳势太高。
●强渗时间太长,扩散时间太短。
(2)补救方法:如渗层总深度偏下限,可在渗碳炉内进行扩散处理,加以补救。
5、过共析+共析层过深(1)原因●强渗期炉内碳势太低。
●强渗时间短,扩散时间长。
(2)补救方法:如在总渗层深度范围内,可在高碳势气氛中补渗。
6、防止方法(1)渗碳温度渗碳温度对渗碳速度影响很大。
一旦工艺温度确定以后,必须保持渗碳温度的稳定性,不能过高或过低,过高容易使渗层太深,过低容易使渗层太浅。
(2)渗碳时间碳在钢中的扩散及扩散层深度是温度和时间的函数,因此在渗碳温度稳定的情况下,要正确地掌握渗碳时间,不能过长和过短,过长容易使渗层太深,过短容易使渗层太浅。
(3)炉气压力炉气压力的大小明显地影响炉内各种化学反应速度,当炉压过小时,不利于排除废气并使氧化性气体进入炉内,过高的压力不利于有机渗剂的进一步分解,因而影响碳势的提高。
在强渗期炉气压力控制在198~392Pa,扩散期炉压控制在49~198Pa。
所以,一般使炉气压力维持正压,有利于渗碳过程的顺序进行。
(4)渗剂滴量●排气阶段———由于工件刚装炉带入大量空气和微量水份,使炉内出现氧化气氛,应迅速将氧化气氛排出,甲醇裂化分解温度比煤油低,又不产生炭黑,且产气量比煤油大一倍,所以排气前期用甲醇比用煤油效果好。
渗碳层不均匀 -回复

渗碳层不均匀-回复什么是渗碳层?渗碳层是指通过渗碳工艺将碳元素渗入金属表面形成的一层碳化物层。
渗碳层可以有效提高金属材料的表面硬度、耐磨性和耐蚀性,增强材料的强度和韧性。
为什么出现渗碳层不均匀的问题?渗碳层不均匀是指在渗碳过程中,金属材料的表面硬度和碳化物层厚度不一致。
这可能是由于渗碳工艺参数设置不当、材料表面准备不足、渗碳剂质量不合格、工艺设备问题等原因导致的。
如何解决渗碳层不均匀的问题?1. 工艺参数的优化:对于渗碳工艺,温度、时间、渗碳剂浓度和渗碳剂中的抑制剂含量等参数都需要严格控制。
在渗碳过程中,可以对温度和时间进行调整,以确保渗碳层均匀分布。
2. 表面准备的改进:在进行渗碳之前,需要对金属材料的表面进行充分的准备工作,确保表面干净、光滑且无氧化物。
采用机械抛光、除锈等方法可以有效提高渗碳层的均匀性。
3. 渗碳剂质量的把控:渗碳剂作为渗碳过程中的重要组成部分,需要确保其质量符合要求。
检测渗碳剂中的杂质含量、成分浓度等,并根据检测结果进行调整,保证渗碳剂的质量稳定。
4. 设备检修和维护:渗碳过程中使用的设备需要定期检修和维护,确保设备的工作状态正常。
如果设备存在问题,可能导致渗碳剂分布不均匀,进而影响渗碳层的均匀性。
5. 渗碳工艺的监控和控制:引入实时监测和控制系统,在渗碳过程中对关键参数进行监控和记录。
通过对数据的分析和比对,可以及时发现渗碳不均匀的问题,并采取相应的调整措施。
总结:渗碳层不均匀的问题对金属材料的性能产生很大的影响。
通过优化工艺参数、改进表面准备、控制渗碳剂质量、维护设备和引入监控系统等措施,可以有效解决渗碳层不均匀的问题,提高金属材料的性能。
渗碳层深度

渗碳层深度(Carburized case depth)是由渗碳工件表面向内至碳含量为规定值处(一般为0.4%C)的垂直距离。
渗碳层(Carburized case)是指渗碳工件含碳量高于原材料的表层。
某渗碳层深度的测量有维氏硬度法、断口法和金相法。
维氏硬度法直接反映了零件的力学性能(硬度),是国家标准指定的唯一仲裁方法,但因操作复杂效率低而较少被采用,生产中一般用断口法和金相法。
断口法常用于零件炉前检查,便于控制零件出炉时间;金相法则是渗碳后对零件进行相应热处理,通过分析热处理后的组织来判定渗碳层的深度,是生产中常用的测试零件渗碳层深度的方法。
中文名渗碳层深度外文名Carburized case depth学科冶金工程领域冶炼释义渗碳工件表面向内至碳含量的距离应用18Cr2Ni4WA钢目录1. 1 简介2. 2 渗碳后热处理工艺与组织3. ▪渗碳后淬火及组织4. ▪渗碳后退火及组织5. ▪渗碳后正火及组织1. ▪渗碳后等温淬火及组织2. 3 渗碳层深度的测定与分析3. ▪试样打磨与腐蚀4. ▪界限判定1. ▪光学显微镜下的组织特征2. ▪退火、正火、普通淬火下深度测定3. ▪在等温淬火下的深度测定4. ▪渗碳层深度测定误差分析1. ▪补渗及渗碳层深度的再次测定2. ▪维氏硬度测定法简介3. 4 总结简介编辑低碳钢与合金钢渗碳时的主要区别在于低碳钢比合金钢渗层中的碳浓度要低,其组织和硬度略有不同,但对渗碳层深度测量无影响。
由于渗碳层具有变化的碳浓度,其由表及里逐渐减小,退火状态的渗碳层由表及里由以下三个区域组成:①过共析层组织为珠光体+二次渗碳体;②共析层组织为珠光体;③亚共析渗碳层过渡层,组织为珠光体+铁素体。
珠光体逐渐减少,铁素体逐渐增加,直到心部原始组织(珠光体+铁素体),渗碳缓冷试样渗碳层界限为出现铁素体组织,较容易区分。
飞机防扭臂销棒材料为18Cr2Ni4WA钢,要求在外径φ38.5mm的两端各40mm内渗碳,渗碳层深度为1.0~1.4mm。
渗碳层深度不合格的原因与防止方法

渗碳层深度不合格的原因与防止方法
吕永顺
【期刊名称】《机械工人:热加工》
【年(卷),期】1999(000)012
【摘要】从多年的热处理实践中体会到齿轮在渗碳过程中。
由于设备、材料、工艺和操作者等诸多方面的原因,会出现各种各样的缺陷。
如渗碳层深度不合格会影响产品质量和生产效率。
因此,有必要弄清楚缺陷产生的原因与防止方法。
【总页数】1页(P44)
【作者】吕永顺
【作者单位】山东省莱西市青岛第一齿轮厂
【正文语种】中文
【中图分类】TG156.81
【相关文献】
1.非切割破坏法渗碳层深度在线检测设备及应用 [J], 厉晓航
2.基于巴克豪森噪声的渗碳层深度检测方法 [J], 屈辰鸣;孙俊杰;李廷超;王启龙;刘星;李阳
3.基于有限数据的电磁检测仪渗碳层深度检测灵敏度预测 [J], 贾健明
4.基于EXCEL模板及宏的全渗碳层深度求解应用研究 [J], 蒋明;王维新;袁进
5.渗碳层深度和有效硬化层深度的控制 [J], 赵振东
因版权原因,仅展示原文概要,查看原文内容请购买。