简述螺旋压力机的发展历程
螺杆式空压机发展史

螺杆式空压机发展史一、螺杆式空压机发展史螺杆式空压机在工业界使用时间已超过40年。
早在1878年德国工程师Krigar即有用螺旋形齿沟压缩的构想。
最初阴阳转子各有两个齿,此为螺旋压缩机的雏形。
1934年,瑞典SRM公司工程师A.Lysholm提出了设定压缩比的概念,将排气压力控制缘口直接铸于机壳上而获得专利,至此,螺杆式发展才获得突破。
1934年。
瑞典SRM公司完成了全世界第一台螺杆式压缩机,其阳转子四齿,阴转子六齿,转子外径分别为φ500mm和φ450mm。
1947年SRM工程师H.R.Nilson将螺杆转子的齿形确定为对称圆弧形试制成功并获得专利。
1950年,英国Horoyd公司开发完成螺杆加工铣床,可以用成形铣刀一次完成转子加工。
1964年,SRM对称圆弧齿形的螺杆式压缩机才真正步入商业实用阶段,70年代开始大量生产。
1965年我国开始研制螺杆式空压机,1970年上海压缩机厂研制成功了螺杆加工铣床,加工的螺杆直径在世界领先。
80年代中期我国开始制造螺杆空压机。
二.双螺杆式空压机基本结构和工作原理1.基本结构通常所称的螺杆压缩机即指双螺杆压缩机。
与活塞压缩机相比,螺杆压缩机的发展历程较短,是一种比较新颖的压缩机。
螺杆压缩机的基本结构是在一“∞”形的腔体内,平行地配置着一对互相啮合的螺旋形转子。
通常对节圆外有凸齿的转子,称为阳转子或阳螺杆。
在节圆内具有凹齿的转子,称为阴转子或阴螺杆。
一般阳转子与原动机连接,阳转子带动阴转子转动。
因此,阳转子又称为主动转子,阴转子又称为从动转子。
在压缩机机体的两端,分别开设一定形状和大小的孔口。
一个供吸气用,称作吸气口;另一个供排气用,称作排气口。
2.工作原理螺杆式空压机的工作循环可分为吸气、压缩和排气三个过程。
随着转子旋转,每对相互啮合的齿相继完成相同的工作循环。
图(一)吸气过程压缩与喷油过程排气过程1)吸气过程——当转子转动时,阴阳转子的齿沟空间在转至进气端壁开口时,其空间最大,此时转子的齿沟空间与进气口的自由空气相通,外界空气即被吸入由阴阳转子及壳体组成的封闭腔内。
第四章-螺旋压力机
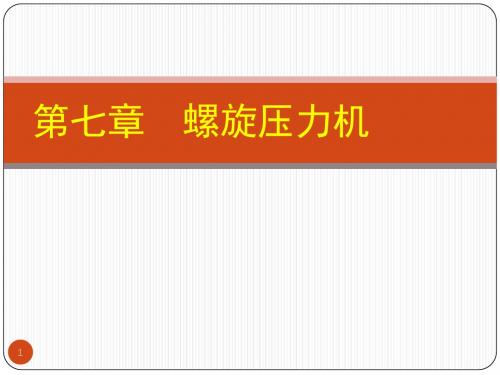
31
副螺母固定在液压缸支座上
胶木副螺母能 储存微量润滑油, 自润滑性能好,传 动效率95%以上。
上下腔停止供油,滑块静止
19
四、离合器式高能螺旋压力机 高能螺旋压力机采用复合传动形式,利用 液压缸回程。高能螺旋压力机和惯性螺旋压力 机的区别:飞轮的工作方式完全不同。 1、 工作过程
飞轮由电动机通过皮带驱动,总朝一向个方 向旋转;
7.1 螺旋压力机的工作原理及工作特性
目前螺旋压力机是我国应 用最为广泛的模锻设备, 占全部模锻设备的37%。
螺旋压力机是采用螺旋副 作为工作机构的锻压机械。
5
一、工作原理:螺旋副(以惯性螺旋压力机为例进行
说明)
1) 惯性螺旋压力机的共同特征是采用一个惯性飞轮; 2) 打击前传动系统输送的能量以动能形式暂时存放在打击部 分(包括飞轮和直线运动质量),飞轮处于惯性运动状态; 3) 打击过程中,飞轮的惯性力矩经螺旋副转化成打击力使毛 坯产生变形,对毛坯作变形功;
20
液压→2→螺杆/飞轮通过从动盘结合 螺杆旋转运动
固定在滑块上的螺母旋转 滑块向下运动/锻击
21
离合器接合后,飞轮转速逐渐下降,当飞轮 转速降到一定数值时离合器脱开,飞轮继续沿 原方向旋转,并逐渐恢复速度; 打击完成后,液压回程缸推动滑块上行,完 成一个工作循环。
22
2、 打击力的控制 高能螺旋压力机一次打击能量不是飞轮的 全部动能,通常设计为飞轮转速降12.5%时所 释放的能量。该种螺旋压力机属于压力限定型 设备,当出现下列情况时打击过程将结束:
16
三、液压螺旋压力机
采用液压传动,相对于摩擦和电动螺旋压 力机,液压螺旋压力机具有高效节能的优点。 易于实现工作能力大型化,公称压力4000 14000吨。
螺杆压缩机发展史
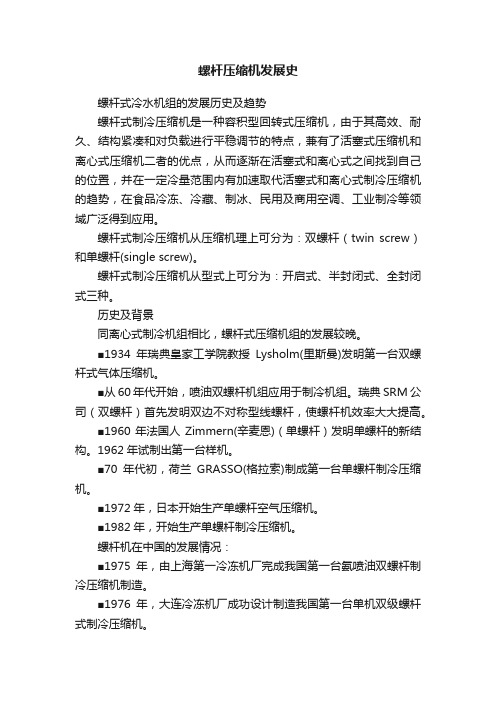
螺杆压缩机发展史螺杆式冷水机组的发展历史及趋势螺杆式制冷压缩机是一种容积型回转式压缩机,由于其高效、耐久、结构紧凑和对负载进行平稳调节的特点,兼有了活塞式压缩机和离心式压缩机二者的优点,从而逐渐在活塞式和离心式之间找到自己的位置,并在一定冷量范围内有加速取代活塞式和离心式制冷压缩机的趋势,在食品冷冻、冷藏、制冰、民用及商用空调、工业制冷等领域广泛得到应用。
螺杆式制冷压缩机从压缩机理上可分为:双螺杆(twin screw)和单螺杆(single screw)。
螺杆式制冷压缩机从型式上可分为:开启式、半封闭式、全封闭式三种。
历史及背景同离心式制冷机组相比,螺杆式压缩机组的发展较晚。
■1934年瑞典皇家工学院教授Lysholm(里斯曼)发明第一台双螺杆式气体压缩机。
■从60年代开始,喷油双螺杆机组应用于制冷机组。
瑞典SRM公司(双螺杆)首先发明双边不对称型线螺杆,使螺杆机效率大大提高。
■1960年法国人Zimmern(辛麦恩)(单螺杆)发明单螺杆的新结构。
1962年试制出第一台样机。
■70年代初,荷兰GRASSO(格拉索)制成第一台单螺杆制冷压缩机。
■1972年,日本开始生产单螺杆空气压缩机。
■1982年,开始生产单螺杆制冷压缩机。
螺杆机在中国的发展情况:■1975年,由上海第一冷冻机厂完成我国第一台氨喷油双螺杆制冷压缩机制造。
■1976年,大连冷冻机厂成功设计制造我国第一台单机双级螺杆式制冷压缩机。
■1986年,武汉冷冻机厂开发了XBY齿型的新型单边不对称圆弧齿型。
进一步提高了国产螺杆制冷压缩机水平。
■90年开始,国外著名厂商进入我国,在螺杆机方面进行多家合资生产。
其中有:中美合资:上海一冷-开利 23XL系列空调用螺杆冷水机组中日合资:烟台荏原螺杆模块式冷(热)水机组中美合资:烟台顿汉布什空调用全封闭螺杆冷水机组中美合资:武汉麦克维尔WHS系列R22,R134a单螺杆冷水机组中美合资:江阴特灵 RTHB系列螺杆冷水机组中美合资:无锡约克 YS、YCWS系列螺杆冷水机组中日合资:1998年大冷-前川单机双级双螺杆压缩机组中日合资:1998年大金-三石 CUW系列单螺杆冷水机组中国台湾地区的复盛在上海设厂生产双螺杆制冷压缩机。
电动螺旋压力机的发展概况--中英文翻译
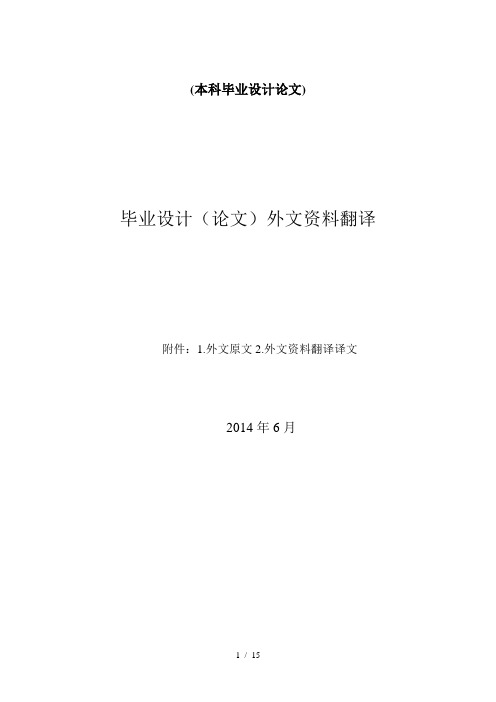
(本科毕业设计论文)毕业设计(论文)外文资料翻译附件:1.外文原文2.外文资料翻译译文2014年6月电动螺旋压力机的发展概况1 概述螺旋压力机是一种历史悠久的锻压设备,具有较人的能容量,结构简单、调整和维护简便、没有固定的下死点,能保证模锻件精度的稳定性。
广泛应用于金属模锻、精压、冲压工艺以及耐火材料、陶瓷等非金属材料的压力加工。
螺旋压力机的设备投资、模具和锻件成本比模锻锤和热模锻压力机便宜一半,加工余量小、锻件精度高。
现代螺旋压力机相继采用了超载保护、力能显示、能量预选及先进的计算机控制系统和自动送料、模具更换等辅助装置。
理论和实践都证明螺旋压力机工艺适应性广、生产率适中、劳动条件好,己成为现代锻压生产优选设备之一。
国内外相关企业都十分重视螺旋压力机的开发与应用。
青岛青锻锻压机械有限公司开发研制了80MN摩擦螺旋压力机,经查证为目前国内外最大规格的同类设备。
由于摩擦压力机传动效率低、功率损耗较大和结构上的限制,规格发展受到了影响。
随着科学水平的不断提高,螺旋压力机的结构形式及传动形式己经有了很大的改进。
除了机械式摩擦传动以外,又采用了新的传动形式,如离合器式螺旋压力机、液压螺旋压力机和电动螺旋压力机等。
这不仅提高了螺旋压力机的实用性、工作速度、生产率和可靠性,打击力和能量也得到了很大的发展。
如电动螺旋压力机打击力己达到320MN,能量达到5000kJ 以上。
电动螺旋压力机自上世纪40年代研制成功以来,在国内外得到了广泛响应。
我国上世纪80年代由青岛青锻锻压机械有限公司与山东工业人学成功研制生产出了J58- 160型1.6MN电机直驱式电动螺旋压力机,但因当时电力条件和控制技术的限制而中断了进一步的研发工作,十分可惜。
近年来,随着科技发展,变频技术和电子数控技术的不断提高,电动螺旋压力机的开发创新、生产制造己全面展开,华中科技人学、青岛青锻锻压机械有限公司等,都相继拥有了自己的技术和产品并迅速地推向市场。
螺旋压力机的智能化改造与发展趋势
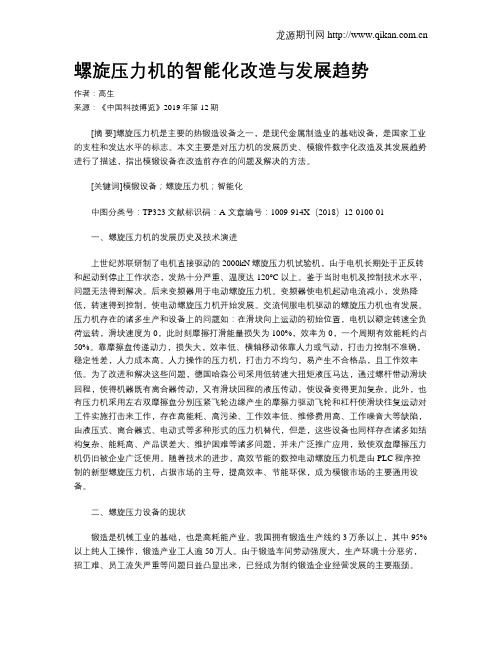
螺旋压力机的智能化改造与发展趋势作者:高生来源:《中国科技博览》2019年第12期[摘要]螺旋压力机是主要的热锻造设备之一,是现代金属制造业的基础设备,是国家工业的支柱和发达水平的标志。
本文主要是对压力机的发展历史、模锻件数字化改造及其发展趋势进行了描述,指出模锻设备在改造前存在的问题及解决的方法。
[关键词]模锻设备;螺旋压力机;智能化中图分类号:TP323 文献标识码:A 文章编号:1009-914X(2018)12-0100-01一、螺旋压力机的发展历史及技术演进上世纪苏联研制了电机直接驱动的2000kN螺旋压力机试验机,由于电机长期处于正反转和起动到停止工作状态,发热十分严重、温度达120°C以上。
鉴于当时电机及控制技术水平,问题无法得到解决。
后来变频器用于电动螺旋压力机。
变频器使电机起动电流减小,发热降低,转速得到控制,使电动螺旋压力机开始发展。
交流伺服电机驱动的螺旋压力机也有发展。
压力机存在的诸多生产和设备上的问题如:在滑块向上运动的初始位置,电机以额定转速全负荷运转,滑块速度为0,此时刻摩擦打滑能量损失为100%,效率为0,一个周期有效能耗约占50%。
靠摩擦盘传递动力,损失大,效率低、横轴移动依靠人力或气动,打击力控制不准确,稳定性差,人力成本高。
人力操作的压力机,打击力不均匀,易产生不合格品,且工作效率低。
为了改进和解决这些问题,德国哈森公司采用低转速大扭矩液压马达,通过螺杆带动滑块回程,使得机器既有离合器传动,又有滑块回程的液压传动,使设备变得更加复杂。
此外,也有压力机采用左右双摩擦盘分别压紧飞轮边缘产生的摩擦力驱动飞轮和杠杆使滑块往复运动对工件实施打击来工作,存在高能耗、高污染、工作效率低、维修费用高、工作噪音大等缺陷,由液压式、离合器式、电动式等多种形式的压力机替代,但是,这些设备也同样存在诸多如结构复杂、能耗高、产品误差大、维护困难等诸多问题,并未广泛推广应用,致使双盘摩擦压力机仍旧被企业广泛使用。
公元前5000年至今的机械发展史,你有必要了解下

公元前5000年⾄今的机械发展史,你有必要了解下远古时代简单机械:杠杆、车轮、滑轮、斜⾯、螺旋等。
公元前3000年,在修建⾦字塔的过程中,就使⽤了滚⽊来搬运巨⽯。
阿基⽶德⽤螺旋将⽔提升⾄⾼处,那就是今天的螺旋式输送机的始祖。
古代中国公元⼀世纪东汉“⽔排”⽤⽔⼒⿎风炼铁,其中应⽤了齿轮和连杆机构。
晋代(公元266年-420年)“连磨”⽤⼀头⽜驱动⼋台磨盘,其中应⽤了齿轮系。
中世纪欧洲(约公元476年—公元1453年)(⽤脚踏板驱动的加⼯⽊棒的车床)(利⽤曲轴的研磨机)13世纪以后,机械钟表在欧洲发展起来。
连杆机构、齿轮机构和凸轮机构等在古代机械中即已经有所应⽤。
在达·芬奇时代,现在最常⽤的⼀些机构型式即已基本知晓。
近代(18世纪中叶- 20世纪中叶)因动⼒、材料、加⼯⼿段、⽣产模式、机构与传动等的变⾰,加上机械理论和设计⽅法的建⽴,机械的推动发展带来了质的飞跃。
古代机械的动⼒:⼈⼒、畜⼒和⽔⼒。
动⼒制约了机械的发展。
⾸先是动⼒的变⾰推动了机械的飞速发展和⼴泛应⽤。
1765年,⽡特(Watt)发明了蒸汽机。
揭开了第⼀次⼯业⾰命的序幕。
蒸汽机给⼈类带来了强⼤的动⼒,各种由动⼒驱动的产业机械 — 纺织机、车床等,如⾬后春笋般出现。
(蒸汽时代的纺织⼯⼚)19世纪,第⼆次⼯业⾰命电动机和内燃机发明电⼒代替了蒸汽。
集中驱动被抛弃了,每台机器都安装了独⽴的电动机。
为汽车、飞机的出现提供了可能性。
1886年,本茨发明的汽油发动机为动⼒的三轮车被授予专利。
与此同时,戴姆勒也发明出了他的第⼀辆四轮汽车。
18世纪中叶,发明了炼钢法,从那时⼀直到现在,钢铁始终是制造机械最主要的材料。
(最开始的⼟法炼钢)18世纪末,现代车床的雏形在英国问世19世纪中叶,通⽤机床的各种类型已⼤体齐备19世纪末,⾃动机床、⼤型机床出现社会需求⽇益增长。
20世纪初叶,机械制造进⼊了⼤批量⽣产模式的时代。
标志:美国福特汽车的⽣产18世纪欧拉(Euler)⾸次提出采⽤渐开线作为齿轮的齿廓,从⽽使⾼速、⼤功率的机械传动成为可能。
《螺旋压力机》课件

分析某型号螺旋压力机的优化 过程和效果,展示优化策略的
实际应用。
04
螺旋压力机的操作与维护
安全操作规程
操作前检查
确保螺旋压力机在操作前已经进 行了全面检查,包括设备状态、 安全装置、润滑系统等。
遵守操作步骤
严格按照螺旋压力机的操作步骤 进行操作,不得擅自更改或跳过 任何步骤。
穿戴
技术创新与改进方向
高效能驱动技术
01
研发更高效、更稳定的驱动系统,提高压力机的运行效率和稳
定性。
智能化控制技术
02
引入先进的传感器和控制系统,实现压力机的智能化控制和远
程监控。
环保与节能技术
03
采用新型的环保材料和节能技术,降低压力机的能耗和排放。
市场发展前景与趋势
未来,随着环保意识的提高和能源消 耗的增加,螺旋压力机将更加注重节 能减排和绿色制造,采用新型传动系 统和优化结构设计,提高能源利用效 率和加工过程的环保性能。同时,随 着智能制造技术的深入应用,螺旋压 力机将进一步实现自动化、柔性化和 智能化,以适应未来制造业的发展需 求。
03
螺旋压力机的设计与优化
结构简单、操作方便、压力稳定 、适用于多种材料的加工和成型 。
工作原理
工作原理
螺旋压力机通过电机或液压驱动,使 螺旋轴转动,从而将旋转运动转化为 压力作用于材料上,实现加工或成型 。
工作过程
螺旋轴旋转,带动螺母移动,螺母与 工作台固定,从而实现对材料的加压 。
分类与应用
分类
根据传动方式的不同,螺旋压力机可分为机械式和液压式两 类。
维护与保养建议
定期润滑
按照设备要求定期对螺旋压力机进行润滑,保持 设备良好运行状态。
电动螺旋压力机的自动化与智能化发展趋势
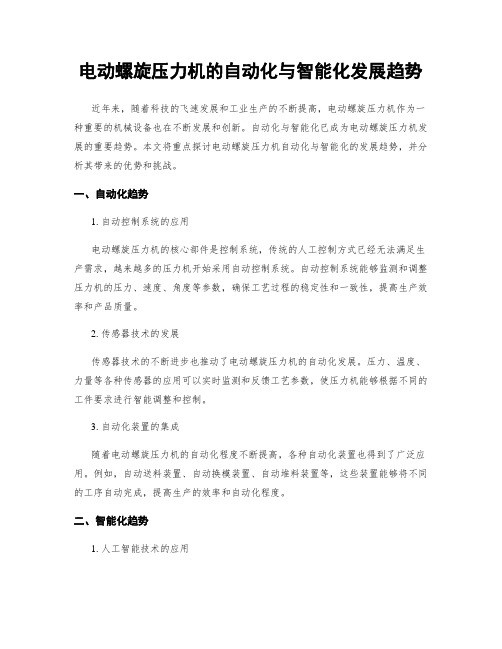
电动螺旋压力机的自动化与智能化发展趋势近年来,随着科技的飞速发展和工业生产的不断提高,电动螺旋压力机作为一种重要的机械设备也在不断发展和创新。
自动化与智能化已成为电动螺旋压力机发展的重要趋势。
本文将重点探讨电动螺旋压力机自动化与智能化的发展趋势,并分析其带来的优势和挑战。
一、自动化趋势1. 自动控制系统的应用电动螺旋压力机的核心部件是控制系统,传统的人工控制方式已经无法满足生产需求,越来越多的压力机开始采用自动控制系统。
自动控制系统能够监测和调整压力机的压力、速度、角度等参数,确保工艺过程的稳定性和一致性,提高生产效率和产品质量。
2. 传感器技术的发展传感器技术的不断进步也推动了电动螺旋压力机的自动化发展。
压力、温度、力量等各种传感器的应用可以实时监测和反馈工艺参数,使压力机能够根据不同的工件要求进行智能调整和控制。
3. 自动化装置的集成随着电动螺旋压力机的自动化程度不断提高,各种自动化装置也得到了广泛应用。
例如,自动送料装置、自动换模装置、自动堆料装置等,这些装置能够将不同的工序自动完成,提高生产的效率和自动化程度。
二、智能化趋势1. 人工智能技术的应用随着人工智能技术的不断进步,电动螺旋压力机开始逐渐具备智能化的功能。
通过学习和分析大量的数据,电动螺旋压力机可以实现自主学习和决策,提高生产过程的灵活性和智能化水平。
例如,电动螺旋压力机可以根据不同的产品要求自动调整压力和速度,实现个性化生产。
2. 远程监控和操作智能化技术还可以实现电动螺旋压力机的远程监控和操作。
通过云平台,操作人员可以随时随地监测和控制电动螺旋压力机的状态,并及时进行故障诊断和维修。
这种远程监控和操作不仅提高了生产的效率,还降低了人力成本和维修成本。
3. 数据共享和分析智能化技术可以实现电动螺旋压力机数据的共享和分析,提供更准确的生产预测和决策支持。
通过大数据分析,可以发现生产过程中的潜在问题,并采取相应的措施进行优化和改进。
螺旋压力机

山东威力重工
2.历史
螺旋压力机起源于公元15世纪的德国,有个叫约翰·唐地贝格的人发明了一种活字印刷机,涂上油 墨的活字板通过螺旋装置被压摁在纸上。这种机器被当作榨葡萄和橄榄油的木制螺栓压榨机来使用, 可以说是所有压力机械的起源。它采用的是逐步花时间压缩的施加静压方式。 在欧洲的博物馆中,同样陈列有通过静压进行热锻造的螺旋压力机。据推测是在中世纪,用于制造 城市及教会的钢制门窗及五金部件的。 后来的锻造用螺旋压力机,发展到可在外螺栓轴上端安装转轮,采用飞轮方式蓄积能量进行驱动。 最初是人力操作旋转飞轮,后来因为这样效率低、人工工作强度大,人们在机械上部安装了2片可 以持续运转的摩擦盘,成功地通过连杆将牛皮缠绕在飞轮上,使其相互接触运转产生动力。这便是 摩擦螺旋压力机,采用的是摩擦驱动方式。 摩擦螺旋压力机在早期是操作工人用手动方向盘操纵连杆控制的,滑块上下移动和加压力的强弱程 度完全依赖于操作工人的熟练程度。 后来连杆方式消失,取而代之的是通过油压或空压气缸与继电器控制的按键开关和脚踏板来操作的 方式。
山东威力重工
5.功能
螺旋压力机无固定下死点,对较大的模锻件,可以多次 打击成形,可以进行单打、连打和寸动。打击力与工件 的变形量有关,变形大时打击力小,变形小(如冷击) 时打击力大。在这些方面,它与锻锤相似。但它的滑块 速度低(约0.5米/秒,仅为锻锤的1/10),打击力通过 机架封闭,故工作平稳,振动比锻锤小得多,不需要很 大的基础。螺旋压力机装有打滑保险机构,将最大打击 力限制在公称压力的2倍以内,以保护设备安全。
螺旋压力机
螺旋压力机(Screw Press),是指通过使一 组以上的外螺栓与内螺栓在框架内旋转产生加 压力形式的压力机械的总称
螺杆式空压机发展史
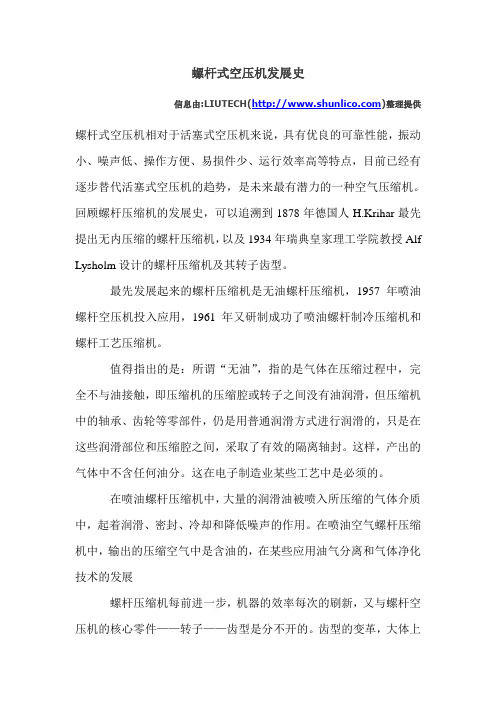
螺杆式空压机发展史信息由:LIUTECH()整理提供螺杆式空压机相对于活塞式空压机来说,具有优良的可靠性能,振动小、噪声低、操作方便、易损件少、运行效率高等特点,目前已经有逐步替代活塞式空压机的趋势,是未来最有潜力的一种空气压缩机。
回顾螺杆压缩机的发展史,可以追溯到1878年德国人H.Krihar最先提出无内压缩的螺杆压缩机,以及1934年瑞典皇家理工学院教授Alf Lysholm设计的螺杆压缩机及其转子齿型。
最先发展起来的螺杆压缩机是无油螺杆压缩机,1957年喷油螺杆空压机投入应用,1961年又研制成功了喷油螺杆制冷压缩机和螺杆工艺压缩机。
值得指出的是:所谓“无油”,指的是气体在压缩过程中,完全不与油接触,即压缩机的压缩腔或转子之间没有油润滑,但压缩机中的轴承、齿轮等零部件,仍是用普通润滑方式进行润滑的,只是在这些润滑部位和压缩腔之间,采取了有效的隔离轴封。
这样,产出的气体中不含任何油分。
这在电子制造业某些工艺中是必须的。
在喷油螺杆压缩机中,大量的润滑油被喷入所压缩的气体介质中,起着润滑、密封、冷却和降低噪声的作用。
在喷油空气螺杆压缩机中,输出的压缩空气中是含油的,在某些应用油气分离和气体净化技术的发展螺杆压缩机每前进一步,机器的效率每次的刷新,又与螺杆空压机的核心零件——转子——齿型是分不开的。
齿型的变革,大体上是这样的,四十到六十年代后期是瑞典的SRM技术——Lysholm齿型的螺杆机时代,而七十、八十年代将是Sigma-X-G.H.H的螺杆时代。
螺杆式压缩机,由于结构简单,易损件少,排气温度低,压比大,尤其不怕气体中带液、带尘压缩,喷油螺杆式压缩机的出现,动力工艺和制冷用的螺杆式压缩机(包括螺杆式空压机、螺杆式制冷机等),在国内外得到了飞速的发展。
离心式压缩机属于透平式压缩机。
在早期,离心式压缩机是用来压缩空气的,并且只适用于低、中压力及气量很大的场合。
但自离心式压缩机开始用于化工流程后,情况有了很大的变化。
塑性成形设备之螺旋压力机

塑性成形设备之螺旋压力机概述螺旋压力机是一种常见的塑性成形设备,广泛应用于金属加工、汽车制造、航空航天、机械制造等领域。
它通过螺杆和螺纹套的转动,将金属材料进行塑性变形,从而制造出各种形状和尺寸的零部件。
工作原理螺旋压力机主要由电机、螺杆、螺纹套、工作台等组件组成。
工作时,通过电机驱动螺杆旋转,螺杆与螺纹套之间形成螺旋压力。
将待加工的金属材料放置在工作台上,并通过调整工作台的高度和位置,将材料与螺杆螺纹套的进给口对准。
当螺杆旋转时,金属材料被螺纹套的进给口推动,沿着螺旋路径受到挤压和塑性变形。
设备结构螺旋压力机的主要部件包括: - 电机:用于驱动螺杆的旋转,通常采用变频调速,可以根据需要调整压力机的工作速度。
- 螺杆:是螺旋压力机的核心组件,通过旋转实现金属材料的进给和挤压。
- 螺纹套:与螺杆配合工作,负责对金属材料施加压力,使其发生塑性变形。
- 工作台:用于放置待加工的金属材料,通过调整工作台的高度和位置,实现材料与螺纹套的对准。
- 控制系统:用于控制螺旋压力机的运行,包括电机速度控制、工作台位置控制等。
运行过程1.调整工作台:根据加工要求,调整工作台的高度和位置,使金属材料与螺纹套的进给口对准。
2.准备金属材料:将待加工的金属材料放置在工作台上,并固定好。
3.启动电机:按下启动按钮,电机开始旋转。
4.压力施加:螺杆和螺纹套之间的螺旋运动产生挤压力,将金属材料从进给口推入螺纹套,并沿着螺旋路径发生塑性变形。
5.压制结束:根据加工要求设定的压制时间和速度,控制系统自动停止电机的运转。
6.取出成品:打开螺纹套,将成品从螺旋压力机中取出,并进行检查和整理。
优势和应用螺旋压力机具有以下优势: - 塑性变形能力强:螺旋压力机通过螺纹套的旋转推动金属材料发生塑性变形,能够对各种金属材料进行加工,形成复杂形状和尺寸精确的零部件。
- 生产效率高:螺旋压力机具有较高的工作速度和较大的加工能力,能够满足大批量生产的需求。
螺旋压力机资料
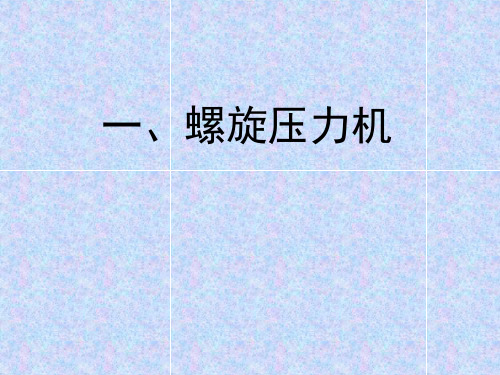
• 四、多点成形设备
• 1.多点成形主机
• 目前已开发出十余个品种YAM 与SM 两 个系列的多点成形设备,若用户需要其 他规格与参数的设备,可以根据
二、锻锤
• 锻锤 • 科技名词定义 • 中文名称: • 锻锤 • 英文名称:
• forging hammer • 定义: • 利用工作部分(落下部分或是活动部分)所积蓄
的动能在下行程时对锻件进行打击,使锻件获 得塑性变形的锻压机械。
• 利用气压或液压等传动机构使落下部分(活塞、 锤杆、锤头、上砧(或上模块),产生运动并积 累动能,在极短的时间施加给锻件,使之获得塑 性变形能,完成各种锻压工艺的锻压机械称为锻 锤。锤头打击固定砧座的为有砧座锤;上下锤头 对击的对击锤为无砧座锤。
。
(二)高能螺旋压力机工作原理
l)打击力增大到给定数值时结 束打击。这时摩擦离合器发生打 滑,螺杆很快停止运动。打击力 通过控制离合器缸压强给定;
2) 滑块行程达到给定值时结束 打击。由位移传感器发出信号控 制杠杆系统使离合器脱开。给定 行程相当给定毛坯变形量。
从动件惯性较小,打滑时间很短,向下空程速度很快, 打击过程以飞轮同步速度快速完成。换向速度快,闷模时 间为10一20ms。
的制成并投入使用,在国际上尚属首创,是具有我国自主 知识产权的产品。性能更优的快速液压模锻锤我国已有系 列产品投放市场,利用纯液压原理制成的液压动力头来改 造蒸—空锤的产品也已投入市场。
三、多点成形压力机
• 一、多点成形技术简介
• 多点成形是金属板材三维曲面成形的全新技术,是对传统 板料生产方式的重大变革。其原理是将传统的整体模具离 散成一系列规则排列、高度可调的基本体(或称冲头)。 在整体模具成形中,板材由模具曲面来成形,而多点成形 中则由基本体群冲头的包络面(或称成形曲面)来完成, 如图1-1 所示。
第6章 螺旋压力机

6.1 螺旋压力机概论
6.1.4 螺旋压力机的应用范围
广泛的工艺实用性:
(1)螺旋压力机既能用来完成锻锤能完成的工艺,又能用来完成压 力机能完成的工艺,如各种热模锻、板料冲压和切边等工艺; (2)由于螺旋压力机一般都设臵有下顶料装臵,因而又适宜于顶镦、 挤压 、闭式模锻等工艺。 (3)螺旋压力机还具有一个很大的特点,即滑块行程不固定,因而 也没有固定的下死点,因此特别适合于精整、精压、压印、校正、粉末 冶金锻造等工艺。同样由于行程不固定,模锻精度不受压力机弹性变形 的影响,所以螺旋压力机被公认为是进行叶片、齿轮等零件精密模锻的 最佳锻压设备。
西安交通大学机械工程学院模具与塑性加工研究所
6.1 螺旋压力机概论
6.1.3 螺旋压力机的优缺点
锻造时的成型速度极快,最适用于热锻,温锻加工:
螺旋压力机接近下死点时的滑动速度极快(通常为800mm/ 秒左右), 可见模具挤压材料的时间非常短。因此可以趁加热的材料冷却前瞬间完 成加工。一般用曲柄式压力机或者肘杆式压力机进行热锻造时,因在下 死点附近滑块的运动速度很低,造成了模具与被加工的热态材料接触时 间长,模具温度过高而须采取水冷却措施。一般来说加热锻造时,与模 具接触时间越短,模具温度变化不大,则模具寿命越长。 螺旋压力机所产生的锻冲力作用于机身的框架之上,基础振动相对 较小。结构简单零件较少,购入价格与维修成本低廉,可提高生产效率。 伺服马达驱动机无离合器机构。制动器在停电等紧急时刻亦无消耗,维 修成本极其节约。加压能量可简单准确地预先设定,每个行程反复实施 无出入的加压。因伺服驱动机没有导致变动的摩擦离合器,每次都可以 产生相同的成形能量,实施精准的加压。可组入全自动化生产线,伺服 驱动压力机与传统的摩擦驱动机相比,可节能30%至50%。 西安交通大学机械工程学院模具与塑性加工研究所
电动螺旋压力机课件

高效传动系统
优化电动螺旋压力机的传动系统,降低能耗,提高传动效率。
绿色化发展
节能环保设计
电动螺旋压力机将采用 节能环保设计,降低能 耗和减少对环境的影响 。
可再生能源利用
利用可再生能源如太阳 能、风能等为电动螺旋 压力机提供动力,实现 绿色生产。
停机操作
完成工作后,应按照规定的操作步骤停机,并关闭电源,确保设备处 于安全状态。
维护保养
1 2
定期检查
定期对电动螺旋压力机进行检查,包括电机、传 动系统、压力装置等关键部件,确保设备正常运 行。
润滑保养
按照规定对电动螺旋压力机进行润滑保养,保证 设备正常运转,延长设备使用寿命。
3
清洁保养
定期对电动螺旋压力机进行清洁保养,保持设备 整洁,防止因灰尘、污垢等引起的故障。
应用案例二:航空航天领域应用
总结词
高强度、高刚度、高稳定性
详细描述
电动螺旋压力机在航空航天领域应用中表现出高强度、高刚度和高稳定性的特点 。它能够满足航空航天领域对设备高强度、高刚度和高稳定性的要求,提高生产 效率和安全性。
应用案例三:模具行业应用
总结词
高效率、高精度、高寿命
详细描述
电动螺旋压力机在模具行业应用中具有高效率、高精度和高寿命的特点。它能够满足模具行业对加工设备高效率 、高精度和高寿命的要求,提高生产效率和产品质量。
02
电动螺旋压力机结构
主机结构
主机框架
采用高强度钢材焊接而成 ,具有足够的刚性和稳定 性,能够承受高强度的工 作负载。
螺杆部件
由高强度合金钢制成,经 过精密加工和热处理,具 有高耐磨性和抗拉强度。
螺旋压力机简介
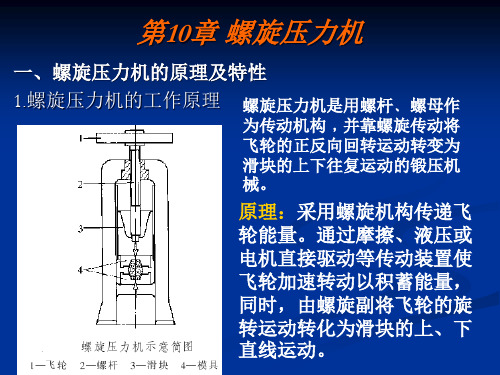
1、 工作过程
1)飞轮由电动机通过皮带驱动,总朝一向个方 向旋转;
2)向下行程时,由液压推动离合器接合,带动螺 杆转动,通过固定在滑块上的螺母使滑块向下运动, 进行打击;
3) 离合器接合后,飞轮转速逐渐下降,当飞轮 转速降到一定数值时离合器脱开,飞轮继续沿原方向 旋转,并逐渐恢复速度;
4) 打击完成后,液压回程缸推动滑块上行,完 成一个工作循环。
图4-11 液压马达-齿轮式液压螺 旋压力机示意图
1、拉杆 2、滑块 3、主螺杆 4、主螺母 5、大齿轮 6、小齿轮 7、液压马达
2、螺旋液压缸式液压螺旋压 力机:
飞轮7的上方与主螺杆8同 轴串联着副螺旋副,其导程 和旋向与主螺旋副相同,副 螺母4在支座上固定不动。副 螺杆2(即为活塞杆)下端与飞 轮7连接,上端为活塞1。高 压油进入液压缸3上腔作用在 活塞上时,活塞与副螺杆便 相对副螺母下行并作螺旋运 动,带动飞轮与主螺杆同步 运动,同时飞轮加速积蓄能 量。当液压缸上腔排油、下 腔进油时,推动主、副螺杆 反向做螺旋运动,于是滑块 被提升回程。
二、主要技术参数
1、公称压力Fg:在此压力下螺旋压力机工作时 能提供较多的有效能量。不是压力机的最大压力。 最大打击能量: ET=½Iωmax
2、许用力Fa:螺旋压力机连续打击时所允许的最大载荷,为公 称压力的1.6倍,是螺旋压力机最有实用意义的力参数。 3、最大打击ET:螺旋压力机所能提供的最大打击能量,是螺旋 压力机的最主要的技术参数。反映了设备的最大工作能力。 4、滑块最大行程S:滑块从设计规定的上止点到下极限位置之 间的距离。行程较大,能加工变形程度较大、高度较高的工件, 通用性强。 5、滑块行程次数n0:螺旋压力机每分钟能完成的全行程的次数。 n0=60/t。
数控电动螺旋压力机简介
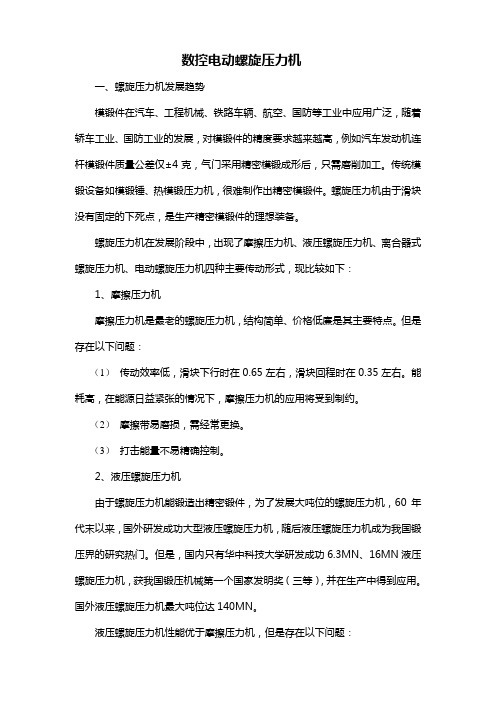
数控电动螺旋压力机一、螺旋压力机发展趋势模锻件在汽车、工程机械、铁路车辆、航空、国防等工业中应用广泛,随着轿车工业、国防工业的发展,对模锻件的精度要求越来越高,例如汽车发动机连杆模锻件质量公差仅±4克,气门采用精密模锻成形后,只需磨削加工。
传统模锻设备如模锻锤、热模锻压力机,很难制作出精密模锻件。
螺旋压力机由于滑块没有固定的下死点,是生产精密模锻件的理想装备。
螺旋压力机在发展阶段中,出现了摩擦压力机、液压螺旋压力机、离合器式螺旋压力机、电动螺旋压力机四种主要传动形式,现比较如下:1、摩擦压力机摩擦压力机是最老的螺旋压力机,结构简单、价格低廉是其主要特点。
但是存在以下问题:(1)传动效率低,滑块下行时在0.65左右,滑块回程时在0.35左右。
能耗高,在能源日益紧张的情况下,摩擦压力机的应用将受到制约。
(2)摩擦带易磨损,需经常更换。
(3)打击能量不易精确控制。
2、液压螺旋压力机由于螺旋压力机能锻造出精密锻件,为了发展大吨位的螺旋压力机,60年代末以来,国外研发成功大型液压螺旋压力机,随后液压螺旋压力机成为我国锻压界的研究热门。
但是,国内只有华中科技大学研发成功6.3MN、16MN液压螺旋压力机,获我国锻压机械第一个国家发明奖(三等),并在生产中得到应用。
国外液压螺旋压力机最大吨位达140MN。
液压螺旋压力机性能优于摩擦压力机,但是存在以下问题:(1)液压系统复杂,管道敷设工作量大,液压泄漏对环境有污染。
(2)维修技术水平要求高,一般锻造工厂维修困难。
(3)价格远高于摩擦压力机。
3、离合器式螺旋压力机上世纪70年代末推出,又称高能螺旋压力机。
其特点是具有高的打击能量,滑块在小行程能输出额定能量值和达到最大锻击力;最大吨位为112MN。
但是存在以下问题:(1)机器结构十分复杂,既有机械离合器传动,又有用于滑块回程的液压传动。
(2)常用的滑块回程方式是采用液压缸推动滑块,同时使螺杆作反向运动。
第4章-螺旋压力机

图4-3 螺旋压力机的传 动类型
1、机架 2、滑块 3、电动机 4、螺 杆 5、螺母 6、带 7、摩擦盘 8、飞轮 9、操纵气缸 10、大齿轮(飞轮) 11、小齿轮 12、液压马达 13、液压缸 14、电动机定子 15、电动机转子 (飞轮) 16、回程缸 17、离合器
4.1 摩擦压力机
工作原理:
图4-16 数控电动螺旋机
4.4 离合器式螺旋压力机
优点:
打击能量高 闷模时间短,模具使用寿命长 抗偏载能力强 生产效率高、节省能源。
缺点:
机器结构十分复杂,既有机械离合器传动,又有用于 滑块回程的液压传动。 在锻击和回程时,主螺杆和螺母的螺牙为同一受力面, 润滑液不易补充,导致螺母螺牙容易磨损。
2、螺旋液压缸式液压螺旋压力机:
飞轮7的上方与主螺杆8同轴串联着副螺旋副,其导 程和旋向与主螺旋副相同,副螺母4在支座上固定不动。 副螺杆2(即为活塞杆)下端与飞轮7连接,上端为活塞1。 高压油进入液压缸3上腔作用在活塞上时,活塞与副螺杆 便相对副螺母下行并作螺旋运动,带动飞轮与主螺杆同 步运动,同时飞轮加速积蓄能量。当液压缸上腔排油、 下腔进油时,推动主、副螺杆反向做螺旋运动,于是滑 块被提升回程。
机身两侧装有两个液压缸
3,其活塞杆与滑块铰接。当
高压油进入液压缸上腔,作用
在活塞上时,便推动滑块向下
运动,带动主螺旋副运动,使
飞轮旋转并积蓄能量。当高压
油进入液压缸下腔,而上腔排
油时,滑块便被提升回程。直
动液压缸式螺旋压力机结构简
单,制造容易,动作可靠,但
主螺旋副在工作中磨损较严重,
设备的传动效率也较低。
第4章 螺旋压力机
学习摩擦式、电动式、液压式和离合器式螺旋压 力机的结构和工作原理。 学习螺旋压力机的工艺特性。
简述输送机的发展历史
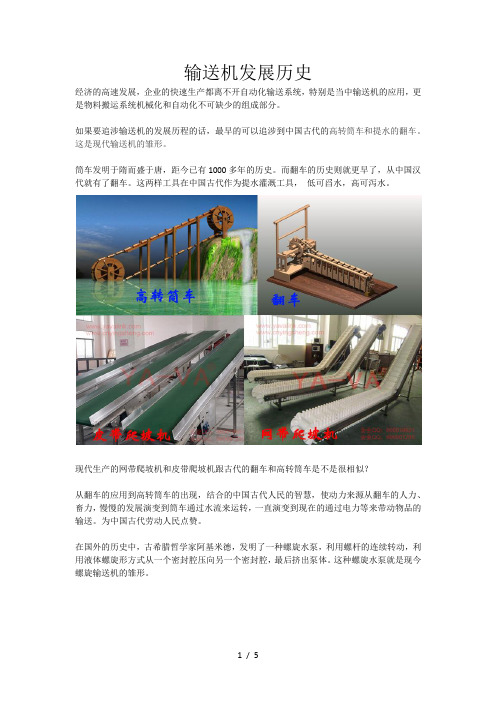
输送机发展历史经济的高速发展,企业的快速生产都离不开自动化输送系统,特别是当中输送机的应用,更是物料搬运系统机械化和自动化不可缺少的组成部分。
如果要追涉输送机的发展历程的话,最早的可以追涉到中国古代的高转筒车和提水的翻车。
这是现代输送机的雏形。
筒车发明于隋而盛于唐,距今已有1000多年的历史。
而翻车的历史则就更早了,从中国汉代就有了翻车。
这两样工具在中国古代作为提水灌溉工具,低可舀水,高可泻水。
现代生产的网带爬坡机和皮带爬坡机跟古代的翻车和高转筒车是不是很相似?从翻车的应用到高转筒车的出现,结合的中国古代人民的智慧,使动力来源从翻车的人力、畜力,慢慢的发展演变到筒车通过水流来运转,一直演变到现在的通过电力等来带动物品的输送。
为中国古代劳动人民点赞。
在国外的历史中,古希腊哲学家阿基米德,发明了一种螺旋水泵,利用螺杆的连续转动,利用液体螺旋形方式从一个密封腔压向另一个密封腔,最后挤出泵体。
这种螺旋水泵就是现今螺旋输送机的雏形。
另外小编再透露下,我们上海YA-VA输送机械总经理万晓光在螺旋输送机系统上还有发明专利的哦!!17世纪中起,人们就开始应用架空索道输送散状物料,这一点就类似中国西南地区至今还存在的滑索一样,在两山之间架设绳索,方便交通。
第一次工业革命开创了以机器代替手工劳动的时代,使工厂制代替了手工工场,用机器代替了手工劳动。
1795年,美国费城的一本杂志上,将输送带描述为“在一框或槽里的2个滚筒上旋转的宽环皮带或帆布带”,这是历史上对于输送机描述最早的文献。
第二次工业革命时期,发电机、电动机的发明,使得世界从“蒸汽时代”进入“电气时代”,工业重心由轻纺业转向重工业,输送机在时期进入了大跨越的发展。
1868年,在英国出现了带式输送机;1887年,在美国出现了螺旋输送机;1892年,美国人汤麦斯·罗宾斯(Thomas Robins)发明了槽形结构,输送机才开始在矿业工业中使用,确定了当代输送机的基本形式。
螺旋压力机发展现状及未来趋势分析

螺旋压力机发展现状及未来趋势分析螺旋压力机是一种常见的机械设备,用于材料的加工和成形。
由于其高效、节能和易于控制的特点,螺旋压力机在各个行业中得到广泛应用。
本文将对螺旋压力机的发展现状及未来趋势进行分析。
首先,我们来看螺旋压力机的发展现状。
目前,螺旋压力机的技术已经相对成熟,压力机的结构和工作原理基本上保持不变。
螺旋压力机具有压力大、速度快、操作简单等优势,可以满足大部分材料加工的需求。
特别是在金属、塑料和橡胶等行业,螺旋压力机已经成为必备的生产设备。
然而,随着科技的不断进步和市场需求的变化,螺旋压力机也在不断发展和改进。
一方面,新的材料和工艺要求对螺旋压力机的性能提出了更高的要求。
另一方面,数字化技术的兴起使得螺旋压力机的智能化和自动化成为可能。
因此,螺旋压力机的未来发展趋势将体现在以下几个方面:首先,螺旋压力机将更加智能化。
随着人工智能和机器学习技术的发展,螺旋压力机可以通过自主学习和自适应控制来优化操作和加工过程。
智能化的螺旋压力机可以根据不同的材料和产品要求进行自动调整,提高生产效率和产品质量。
其次,螺旋压力机将更加数字化。
传感器和数据采集技术的应用可以实时监测和记录螺旋压力机的工作状态和性能参数。
通过数据分析和挖掘,生产厂家可以及时发现潜在问题,并采取相应措施进行优化和改进。
数字化的螺旋压力机还可以实现远程监控和远程操作,提高生产过程的灵活性和安全性。
另外,螺旋压力机将更加注重环保和节能。
随着环境保护意识的增强和能源成本的上涨,螺旋压力机需要不断优化设计和改进工艺,以减少能源消耗和环境污染。
例如,采用节能电机、优化液压系统和减少废气排放等措施,可以降低螺旋压力机的能耗和对环境的影响。
此外,螺旋压力机还将更加多样化。
不同行业对螺旋压力机的需求各有不同,生产厂家需要开发和设计不同规格和功能的螺旋压力机来适应不同的工艺要求。
例如,低压、高压、小型、大型和专用功能等各种型号的螺旋压力机将会得到更广泛的应用。
- 1、下载文档前请自行甄别文档内容的完整性,平台不提供额外的编辑、内容补充、找答案等附加服务。
- 2、"仅部分预览"的文档,不可在线预览部分如存在完整性等问题,可反馈申请退款(可完整预览的文档不适用该条件!)。
- 3、如文档侵犯您的权益,请联系客服反馈,我们会尽快为您处理(人工客服工作时间:9:00-18:30)。
简述螺旋压力机的发展历程
对于压力机的发展,各类螺旋压力机在发展特性以及工作的现状和动向上面都各有不同。
文章主要通过对螺旋压力机的整个发展的趋向做出了分析,通过比较和论证提出大吨位的螺旋压力机在发展上应当适当的受到限制,而离合器压力机以及新型的伺服驱动的螺旋压力机则应当得到相应的发展。
标签:螺旋压力机;特点;发展;趋向
1 发展
压力机的发展由来已久,从很早很早以前的欧洲就开始使用木质的螺旋压力机了,这种古老的设备是机械设备成型较早的一种,历史悠久。
早期的螺旋压力机主要被用作压制葡萄汁或者是橄榄油。
十五世纪的德国人根据螺旋压力机的原理,在此基础上进行改进和发挥造出了螺旋印刷机,这两种机械就成为了后来的各种压力机的原型。
所以,在欧洲的语言中,印刷以及压力这两个词语在词根上也是彼此相同的。
后来,意大利人在十六世纪使用压力机开始制作金属制品,诸如艺术品以及硬币。
一直到了十九世纪中期,蒸汽机的出现才有了以蒸汽为动力的机械压力机。
在工业生产中最早使用的就是通过摩擦盘传递的动力,这种摩擦压力机是于十九世纪初被广泛使用的,首个有关摩擦压力机的专利是得过于1877年公布的。
在工作性能上摩擦压力机较为可靠,且在结构上也简单便捷,所以到今天,这种机械设备还是受到人们的青睐。
但是缺点就是效率太低,在摩擦传动的过程中会损失掉很多的能量,总的动能利用率大约只有一半,而总效率则最多只能达到总能量的四分之一。
所以人们一直以来都是努力的对其进行改进想要寻求一个可以提高工作效率的办法,改进的主要目标就是首先要对传动效率进行改进,降低不必要的耗能;其次,则是对设备的吨位进行提高,这是对其工作能力的改进;最后,则是对机械控制打击能量上的精度以及自动化的操作程度上。
螺旋压力机总体开始快速发展是在二十世纪,整个二十世纪的初期,液压式的螺旋压力机开始得到研制,人们致力于将其投入工业的生产中,三十年代,电动式的螺旋压力机开始被前苏联研制出来;到了四十年代末期螺旋式的压力机被投入到工业中使用;五十年代末期,德国也开始生產电动压力机;到了七十年代的末期,德国已经研制出了离合器式的螺旋压力机,这种设备是由新佩坎公司研发出的。
而到了二十世纪的末期,伺服驱动的电动压力机也由日本问世。
即便是进入到了新世纪,螺旋压力机仍旧生机盎然,蓬勃发展,并且还在向着更多地品种和更齐全的规格以及自动化程度更高的方向发展。
其发展必然会继续为人类社会的进步作出更多。
2 几种典型的螺旋压力机
2.1 摩擦压力机
螺旋压力机在现代工业中的应用非常广泛,主要就是以其简单的结构以及低廉的价格作为主要的优势,其使用历史由来已久,可以追溯到二百年前。
并且其应用行业也很广泛,除了在锻压领域中应用广泛之外,还能够应用到建材行业。
摩擦压力机在使用中的主要问题就在于电动机在带动摩擦盘进行告诉的转动后,飞轮会和摩擦盘之间出现打滑现象,这种现象是由于飞轮需要在循环中改变旋转的方向。
这样在传动效率上就会受到影响,并且摩擦带也会由于打滑而出现磨损。
这一问题的改进从上个世纪就开始被人们关注,先后出现了双电机驱动的压力机,以及三盘式的压力机。
并且在工作以及回程上,摩擦盘的速度特性不同,所以,飞轮以及摩擦盘的滑动速度就得到了控制,设备在性能的稳定性上有了一定的提高。
但是,在结构以及操作上就会相对的增加了复杂性,所以,制造以及维修费用也有了一定的提高,因此应用并未推广。
摩擦压力机的吨位不大,并且效率不高打击力度的控制无法做到很精确,但是在造价上具有着别的设备无法达到的优势,所以,一般在中小吨位的机械应用中十分受到人们的青睐,目前中小吨位的压力机仍是摩擦压力机压力机作为主导。
2.2 液压螺旋压力机
与摩擦传动相比,液压传动有更高的效率。
油泵的总效率在70%~80%左右,而柱塞泵更可达到90%(以上,还可利用蓄能器储存减速制动时的能量。
人们在上世纪20年代就开始研制液压螺旋压力机,以求发展更大吨位的设备。
1984年美国公司研制成功6300KN样机,1972年德国公司制造了当时世界最大的6300KN压力机,设计吨位则达到250000KN。
液压螺旋压力机按驱动方式有两种-液压缸驱动(推缸式)和液压马达驱动(副螺杆式)。
液压螺旋压力机的效率大大提高,其加速传动效率可达60%~70%。
此外,系统工作寿命大大提高,据德国公司40000KN压力机连续工作6年,没换过油泵和马达,没出现过故障。
但与摩擦压力机相比,结构复杂,维修成本也更高些。
2.3 电动螺旋压力机
直接用电动机转子来代替飞轮,或通过齿轮或皮带带动飞轮旋转,去除了低效率的摩擦传动,具有最短的传动链和较高的效率。
前苏联学者基于这一想法,在1933年研制了电动机直接驱动的2000KN螺旋压力机试验机。
但由于电机长期处于正-反转和启动-停止工作状态,发热十分严重,温升达120度。
2.4 离合器式螺旋压力机
具有很大惯性飞轮的频繁正反转是螺旋压力机效率不高的主要原因,因为在加速减速及制动过程中会消耗大量能量。
如果能像曲柄压力机一样,飞轮无需换向,效率就可以大大提高了。
基于这一思想,德国辛佩坎公司在1979年研制成功离合器式螺旋压力机,在飞轮与螺杆之间靠离合器来连接,与曲柄压力机相似。
飞轮在工作过程中始终向一个方向旋转,无须停止和反向,其尺寸和转动惯量可远大于普通摩擦压力机。
3 螺旋压力机的新进展
交流伺服驱动电动螺旋压力机
近20多年来,交流伺服驱动技术步入了工业应用阶段,与直流伺服驱动相比,表现出极大的优越性。
上世纪末,发达工业国家开始将这一技术应用于成形设备。
日本公司在不久前声称在世界上首次开发成功交流伺服电机驱动的螺旋压力机。
它有两种传动方式,一种是将扁平型伺服电机直接安装在螺杆上;另一种则是通过皮带带动飞轮旋转。
由于采用交流伺服驱动,它具有更加优越的工作性能:(1)节能可达50%;(2)可获得更高的控制和锻造精度;(3)适应性广,一种设备可完成从小到大的多种锻件的压制,更适应小批量多品种的柔性化生产。
该产品获得2001,年日本第31届新机械技术奖,目前的最大吨位为16000KN,安装有两台100KW的伺服电机。
4 结束语
高能耗的摩擦式压力机虽然在控制上精度不算很高,但是由于其造价低并且结构简单,所以在我国的机械制造业中还是应用十分广泛的,并且市场前景仍旧很好。
但是同目前提倡的节能口号有些不相适应,所以对其发展应当给予相应的控制,尤其是对于吨位较大的摩擦压力机,由于吨位的原因,其能耗会更高。
离合器式的螺旋压力机在目前来说能够解决一些摩擦压力机能耗高一级吨位的问题,在效率上较高,并且打击力度较大,且精度也较容易控制等等,这些优点是目前市场上所使用的大吨位的压力机所要发展的一个趋势。
并且目前来说,电子电气以及计算机和电机科技的发展,使得螺旋压力机的结构也有了很大的改变,并且发展的空间更大,不但可以更加精确的对其精度予以控制,更能在离合器以及制动器的能耗上有所突破,因为这些部件的去除使得能耗进一步的减少。
所以其发展的前景很好,会得到社会的关注。
并且在螺旋压力的自动化发展上会进一步,使得在更加精准的前提先,提高打击的的力度、速度以及位置。
使得设备的使用更加的方便,这就是螺旋压力机在今后的方向。