铝合金金属型铸造气孔如何解决
铸造铝合金的常见缺陷及应对方法【标准版】
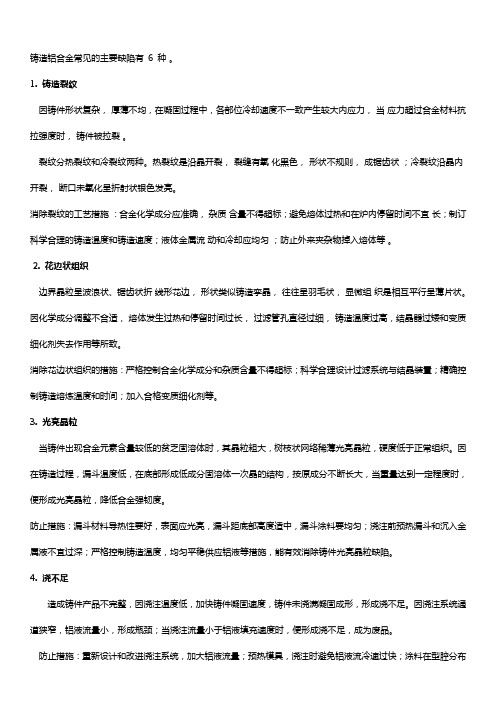
铸造铝合金常见的主要缺陷有6 种。
1. 铸造裂纹因铸件形状复杂,厚薄不均,在凝固过程中,各部位冷却速度不一致产生较大内应力,当应力超过合金材料抗拉强度时,铸件被拉裂。
裂纹分热裂纹和冷裂纹两种。
热裂纹是沿晶开裂,裂缝有氧化黑色,形状不规则,成锯齿状;冷裂纹沿晶内开裂,断口未氧化呈折射状银色发亮。
消除裂纹的工艺措施:合金化学成分应准确,杂质含量不得超标;避免熔体过热和在炉内停留时间不宜长;制订科学合理的铸造温度和铸造速度;液体金属流动和冷却应均匀;防止外来夹杂物掉入熔体等。
2. 花边状组织边界晶粒呈波浪状、锯齿状折线形花边,形状类似铸造孪晶,往往呈羽毛状,显微组织是相互平行呈薄片状。
因化学成分调整不合适,熔体发生过热和停留时间过长,过滤管孔直径过细,铸造温度过高,结晶器过矮和变质细化剂失去作用等所致。
消除花边状组织的措施:严格控制合金化学成分和杂质含量不得超标;科学合理设计过滤系统与结晶装置;精确控制铸造熔炼温度和时间;加入合格变质细化剂等。
3. 光亮晶粒当铸件出现合金元素含量较低的贫乏固溶体时,其晶粒粗大,树枝状网络稀薄光亮晶粒,硬度低于正常组织。
因在铸造过程,漏斗温度低,在底部形成低成分固溶体一次晶的结构,按原成分不断长大,当重量达到一定程度时,便形成光亮晶粒,降低合金强韧度。
防止措施:漏斗材料导热性要好,表面应光亮,漏斗距底部高度适中,漏斗涂料要均匀;浇注前预热漏斗和沉入金属液不宜过深;严格控制铸造温度,均匀平稳供应铝液等措施,能有效消除铸件光亮晶粒缺陷。
4. 浇不足造成铸件产品不完整,因浇注温度低,加快铸件凝固速度,铸件未浇满凝固成形,形成浇不足。
因浇注系统通道狭窄,铝液流量小,形成瓶颈;当浇注流量小于铝液填充速度时,便形成浇不足,成为废品。
防止措施:重新设计和改进浇注系统,加大铝液流量;预热模具,浇注时避免铝液流冷速过快;涂料在型腔分布应合理,厚度适中均匀,涂料不宜太薄;确保模具排气顺畅等措施,可有效消除浇不足形成的废品。
铸造铝合金中的针孔及其防止
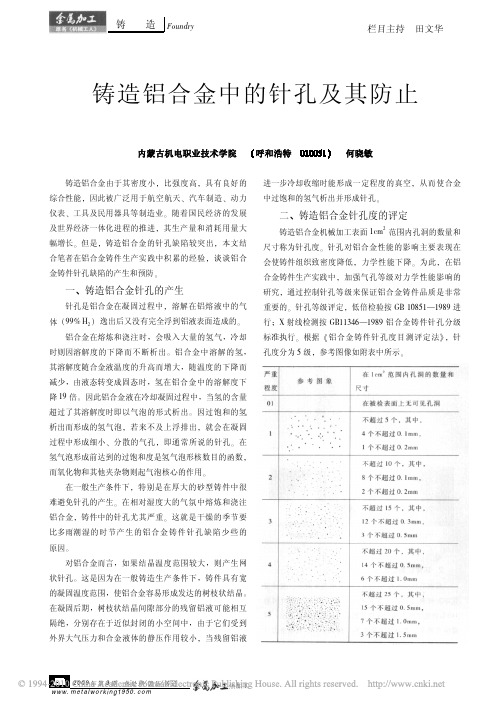
一# 铸造铝合金针孔的产生
针孔是铝合金在凝固过程中! 溶解在铝熔液中的气 体 % ==69 $ & 逸出后又没有完全浮到铝液表面造成的 $ 铝合金在熔炼和浇注时! 会吸入大量的氢气! 冷却 时则因溶解度的下降而不断析出$ 铝合金中溶解的氢! 其溶解度随合金液温度的升高而增大! 随温度的下降而 减少! 由液态转变成固态时! 氢在铝合金中的溶解度下 降 #= 倍$ 因此铝合金液在冷却凝固过程中! 当氢的含量 超过了其溶解度时即以气泡的形式析出$ 因过饱和的氢 析出而形成的氢气泡! 若来不及上浮排出! 就会在凝固 过程中形成细小# 分散的气孔! 即通常所说的针孔$ 在 氢气泡形成前达到的过饱和度是氢气泡形核数目的函数! 而氧化物和其他夹杂物则起气泡核心的作用$ 在一般生产条件下! 特别是在厚大的砂型铸件中很 难避免针孔的产生$ 在相对湿度大的气氛中熔炼和浇注 铝合金! 铸件中的针孔尤其严重$ 这就是干燥的季节要 比多雨潮湿的时节产生的铝 合 金 铸 件 针 孔 缺 陷 少 些 的 原因$ 对铝合金而言! 如果结晶温度范围较大! 则产生网 状针孔$ 这是因为在一般铸造生产条件下! 铸件具有宽 的凝固温度范围! 使铝合金容易形成发达的树枝状结晶$ 在凝固后期! 树枝状结晶间隙部分的残留铝液可能相互 隔绝! 分别存在于近似封闭的小空间中! 由于它们受到 外界大气压力和合金液体的静压作用较小! 当残留铝液
, 溶- 三方面的工艺措施时! 必须遵循 , 以防为主! 以 排为辅- 的工艺原则! 但着眼点应仍放在 , 防- 字上$ ! % $))%)=#= &
! ( # " # # $年 第 %期! 热 处 理 " 锻 压" 铸造 !!!" #$ % & ’ !( ) *+ , . / 0 1 " 2( #
铝压铸件产生气孔的可能原因精选版

铝压铸件产生气孔的可能原因Document serial number【KKGB-LBS98YT-BS8CB-BSUT-BST108】铝压铸件产生气孔的可能原因(供参考)一.人的因素:1.脱模剂是否喷得太多因脱模济发气量大,用量过多时,浇注前未燃尽,使挥发气体被包在铸件表层。
所以在同一条件下,某些工人操作时会产生较多的气孔的原因之一。
选用发气量小的脱模济,用量薄而均匀,燃净后合模。
2未经常清理溢流槽和排气道3开模是否过早是否对模具进行了预热各部位是否慢慢均匀升温,使型腔、型芯表面温度为150℃~200℃。
4刚开始模温低时生产的产品有无隔离5如果无预热装置时是否使用铝合金料慢速推入型腔预热或用其它方法加热6是否取干净的铝液,有无将氧化层注入压室7倒料时,是否将勺子靠近压室注入口,避免飞溅、氧化或卷入空气降温等。
8金属液一倒入压室,是否即进行压射,温度有无降低了。
9冷却与开模,是否根据不同的产品选择开模时间10有无因怕铝液飞出(飞水),不敢采用正常压铸压力更不敢偿试适当增加比压。
11操作员有无严格遵守压铸工艺12有无采用定量浇注如何确定浇注量二.机(设备、模具、工装)的因素:主要是指模具质量、设备性能。
1压铸模具设计是否合理,会否导致有气孔压铸模具方面的原因:1.浇口位置的选择和导流形状是否不当,导致金属液进入型腔产生正面撞击和产生旋涡。
(降低压射速度,避免涡流包气)2.浇道形状有无设计不良3.内浇口速度有无太高,产生湍流4.排气是否不畅5.模具型腔位置是否太深6.机械加工余量是否太大穿透了表面致密层,露出皮下气孔压铸件的机械切削加工余量应取得小一些,一般在左右,既可减轻铸件重量、减少切削加工量以降低成本,又可避免皮下气孔露出。
余量最好不要大于,这样加工出来的面基本看不到气孔的,因为有硬质层的保护。
2排气孔是否被堵死,气排不出来3?冲头润滑剂是否太多,或被烧焦这也是产生气体的来源之一。
4?浇口位置和导流形状,有无金属液先封闭分型面上的排溢系统5内浇口位置是否不合理,通过内浇口后的金属立即撞击型壁、产生涡流,气体被卷入金属流中6?排气道位置不对,造成排气条件不良5?溢气道面积是否够大,是否被阻塞,位置是否位於最后充填的地方模具排气部位是否经常清理避免因脱模剂堵塞而失去排气作用。
铸造铝合金缺陷及分析

铸造铝合金缺陷及分析一氧化夹渣缺陷特征:氧化夹渣多分布在铸件的上表面,在铸型不通气的转角部位;断口多呈灰白色或黄色,经x光透视或在机械加工时发现,也可在碱洗、酸洗或阳极化时发现产生原因:1.炉料不清洁,回炉料使用量过多2.浇注系统设计不良3.合金液中的熔渣未清除干净4.浇注操作不当,带入夹渣5.精炼变质处理后静置时间不够防止方法:1.炉料应经过吹砂,回炉料的使用量适当降低2.改进浇注系统设计,提高其挡渣能力3.采用适当的熔剂去渣4.浇注时应当平稳并应注意挡渣5.精炼后浇注前合金液应静置一定时间二气孔气泡缺陷特征:三铸件壁内气孔一般呈圆形或椭圆形,具有光滑的表面,一般是发亮的氧化皮,有时呈油黄色;表面气孔、气泡可通过喷砂发现,内部气孔气泡可通过X光透视或机械加工发现气孔气泡在X光底片上呈黑色产生原因:1.浇注合金不平稳,卷入气体2.型芯砂中混入有机杂质如煤屑、草根马粪等3.铸型和砂芯通气不良4.冷铁表面有缩孔5.浇注系统设计不良防止方法:1.正确掌握浇注速度,避免卷入气体;2.型芯砂中不得混入有机杂质以减少造型材料的发气量3.改善芯砂的排气能力4.正确选用及处理冷铁5.改进浇注系统设计三缩松缺陷特征:铝铸件缩松一般产生在内浇道附近飞冒口根部厚大部位、壁的厚薄转接处和具有大平面的薄壁处;在铸态时断口为灰色,浅黄色经热处理后为灰白浅黄或灰黑色在x光底片上呈云雾状严重的呈丝状缩松可通过X光、荧光低倍断口等检查方法发现<br>产生原因:1.冒口补缩作用差2.炉料含气量太多3.内浇道附近过热4.砂型水分过多,砂芯未烘干5.合金晶粒粗大6.铸件在铸型中的位置不当7.浇注温度过高,浇注速度太快防止方法:1.从冒口补浇金属液,改进冒口设计2.炉料应清洁无腐蚀3.铸件缩松处设置冒口,安放冷铁或冷铁与冒口联用4.控制型砂水分,和砂芯干燥5.采取细化品粒的措施6.改进铸件在铸型中的位置降低浇注温度和浇注速度四裂纹缺陷特征:1.铸造裂纹;沿晶界发展,常伴有偏析,是一种在较高温度下形成的裂纹在体积收缩较大的合金和形状较复杂的铸件容易出现2.热处理裂纹:由于热处理过烧或过热引起,常呈穿晶裂纹;常在产生应力和热膨张系数较大的合金冷却过剧;或存在其他冶金缺陷时产生产生原因:1.铸件结构设计不合理,有尖角,壁的厚薄变化过于悬殊2.砂型芯退让性不良3.铸型局部过热4.浇注温度过高5.自铸型中取出铸件过早6.热处理过热或过烧,冷却速度过激防止方法:1.改进铸件结构设计,避免尖角,壁厚力求均匀,圆滑过渡2.采取增大砂型芯退让性的措施3.保证铸件各部分同时凝固或顺序凝固,改进浇注系统设计4.适当降低浇注温度5.控制铸型冷却出型时间6.铸件变形时采用热校正法7.正确控制热处理温度,降低淬火冷却速度气孔分析压铸件缺陷中,出现最多的是气孔;气孔特征;有光滑的表面,形状是圆形或椭圆形;表现形式可以在铸件表面、或皮下针孔、也可能在铸件内部;1气体来源1 合金液析出气体—a与原材料有关b与熔炼工艺有关2 压铸过程中卷入气体¬—a与压铸工艺参数有关b与模具结构有关3 脱模剂分解产生气体¬—a与涂料本身特性有关b与喷涂工艺有关2原材料及熔炼过程产生气体分析铝液中的气体主要是氢,约占了气体总量的85%;熔炼温度越高,氢在铝液中溶解度越高,但在固态铝中溶解度非常低,因此在凝固过程中,氢析出形成气孔;氢的来源:1 大气中水蒸气,金属液从潮湿空气中吸氢;2 原材料本身含氢量,合金锭表面潮湿,回炉料脏,油污;3 工具、熔剂潮湿;3压铸过程产生气体分析由于压室、浇注系统、型腔均与大气相通,而金属液是以高压、高速充填,如果不能实现有序、平稳的流动状态,金属液产生涡流,会把气体卷进去;压铸工艺制定需考虑以下问题:1 金属液在浇注系统内能否干净、平稳地流动,不会产生分离和涡流;2 有没有尖角区或死亡区存在3 浇注系统是否有截面积的变化4 排气槽、溢流槽位置是否正确是否够大是否会被堵住气体能否有效、顺畅排出应用计算机模拟充填过程,就是为了分析以上现象,以作判断来选择合理的工艺参数;4涂料产生气体分析涂料性能:如发气量大对铸件气孔率有直接影响;喷涂工艺:使用量过多,造成气体挥发量大,冲头润滑剂太多,或被烧焦,都是气体的来源;5解决压铸件气孔的办法先分析出是什么原因导致的气孔,再来取相应的措施;1 干燥、干净的合金料;2 控制熔炼温度,避免过热,进行除气处理;3 合理选择压铸工艺参数,特别是压射速度;调整高速切换起点;4 顺序填充有利于型腔气体排出,直浇道和横浇道有足够的长度>50mm,以利于合金液平稳流动和气体有机会排出;可改变浇口厚度、浇口方向、在形成气孔的位置设置溢流槽、排气槽;溢流品截面积总和不能小于内浇口截面积总和的60%,否则排渣效果差;5 选择性能好的涂料及控制喷涂量;解决缺陷的思路由于每一种缺陷的产生原因来自多个不同的影响因素,因此在实际生产中要解决问题,面对众多原因到底是非功过先调机还是先换料或先修改模具建议按难易程度,先简后复杂去处理,其次序:1 清理分型面,清理型腔,清理顶杆;改善涂料、改善喷涂工艺;增大锁模力,增加浇注金属量;这些靠简单操作即可实施的措施;2 调整工艺参数、压射力、压射速度、充型时间、开模时间,浇注温度、模具温度等;3 换料,选择质优的铝合金锭,改变新料与回炉料的比例,改进熔炼工艺;4 修改模具,修改浇注系统,增加内浇口,增设溢流槽、排气槽等;例如压铸件产生飞边的原因有:1 压铸机问题:锁模力调整不对;2 工艺问题:压射速度过高,形成压力冲击峰过高;。
解决铸件气孔修补的方法
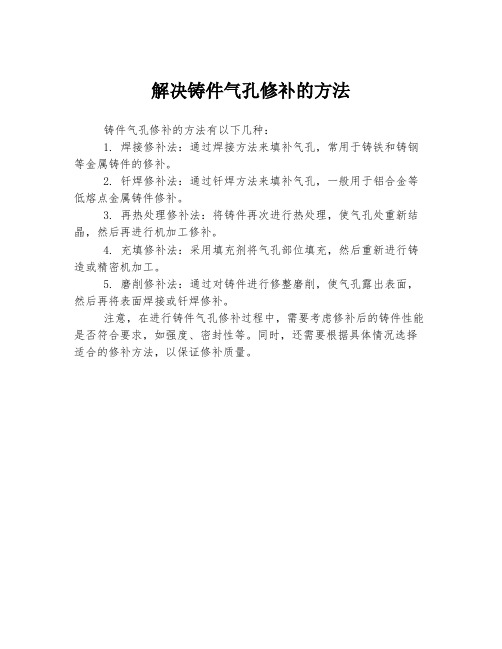
解决铸件气孔修补的方法
铸件气孔修补的方法有以下几种:
1. 焊接修补法:通过焊接方法来填补气孔,常用于铸铁和铸钢等金属铸件的修补。
2. 钎焊修补法:通过钎焊方法来填补气孔,一般用于铝合金等低熔点金属铸件修补。
3. 再热处理修补法:将铸件再次进行热处理,使气孔处重新结晶,然后再进行机加工修补。
4. 充填修补法:采用填充剂将气孔部位填充,然后重新进行铸造或精密机加工。
5. 磨削修补法:通过对铸件进行修整磨削,使气孔露出表面,然后再将表面焊接或钎焊修补。
注意,在进行铸件气孔修补过程中,需要考虑修补后的铸件性能是否符合要求,如强度、密封性等。
同时,还需要根据具体情况选择适合的修补方法,以保证修补质量。
铸件气孔类缺陷的特征及预防措施
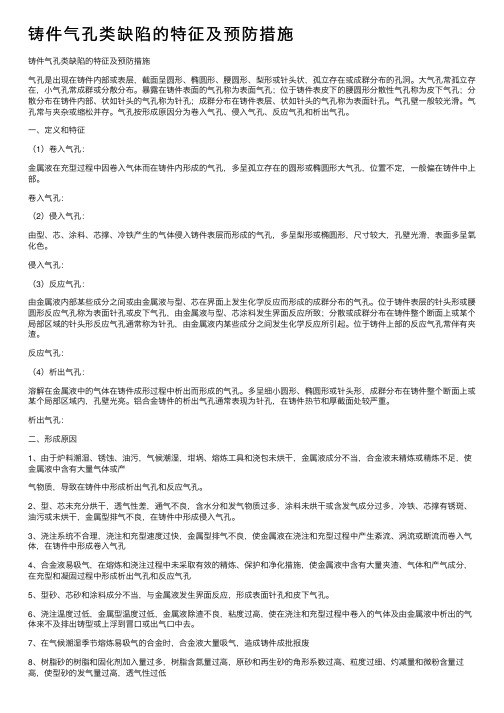
铸件⽓孔类缺陷的特征及预防措施铸件⽓孔类缺陷的特征及预防措施⽓孔是出现在铸件内部或表层,截⾯呈圆形、椭圆形、腰圆形、梨形或针头状,孤⽴存在或成群分布的孔洞。
⼤⽓孔常孤⽴存在,⼩⽓孔常成群或分散分布。
暴露在铸件表⾯的⽓孔称为表⾯⽓孔;位于铸件表⽪下的腰圆形分散性⽓孔称为⽪下⽓孔;分散分布在铸件内部、状如针头的⽓孔称为针孔;成群分布在铸件表层、状如针头的⽓孔称为表⾯针孔。
⽓孔壁⼀般较光滑。
⽓孔常与夹杂或缩松并存。
⽓孔按形成原因分为卷⼊⽓孔、侵⼊⽓孔、反应⽓孔和析出⽓孔。
⼀、定义和特征(1)卷⼊⽓孔:⾦属液在充型过程中因卷⼊⽓体⽽在铸件内形成的⽓孔,多呈孤⽴存在的圆形或椭圆形⼤⽓孔,位置不定,⼀般偏在铸件中上部。
卷⼊⽓孔:(2)侵⼊⽓孔:由型、芯、涂料、芯撑、冷铁产⽣的⽓体侵⼊铸件表层⽽形成的⽓孔,多呈梨形或椭圆形,尺⼨较⼤,孔壁光滑,表⾯多呈氧化⾊。
侵⼊⽓孔:(3)反应⽓孔:由⾦属液内部某些成分之间或由⾦属液与型、芯在界⾯上发⽣化学反应⽽形成的成群分布的⽓孔。
位于铸件表层的针头形或腰圆形反应⽓孔称为表⾯针孔或⽪下⽓孔,由⾦属液与型、芯涂料发⽣界⾯反应所致;分散或成群分布在铸件整个断⾯上或某个局部区域的针头形反应⽓孔通常称为针孔,由⾦属液内某些成分之间发⽣化学反应所引起。
位于铸件上部的反应⽓孔常伴有夹渣。
反应⽓孔:(4)析出⽓孔:溶解在⾦属液中的⽓体在铸件成形过程中析出⽽形成的⽓孔。
多呈细⼩圆形、椭圆形或针头形,成群分布在铸件整个断⾯上或某个局部区域内,孔壁光亮。
铝合⾦铸件的析出⽓孔通常表现为针孔,在铸件热节和厚截⾯处较严重。
析出⽓孔:⼆、形成原因1、由于炉料潮湿、锈蚀、油污,⽓候潮湿,坩埚、熔炼⼯具和浇包未烘⼲,⾦属液成分不当,合⾦液未精炼或精炼不⾜,使⾦属液中含有⼤量⽓体或产⽓物质,导致在铸件中形成析出⽓孔和反应⽓孔。
2、型、芯未充分烘⼲,透⽓性差,通⽓不良,含⽔分和发⽓物质过多,涂料未烘⼲或含发⽓成分过多,冷铁、芯撑有锈斑、油污或未烘⼲,⾦属型排⽓不良,在铸件中形成侵⼊⽓孔。
铸造气孔解决方法
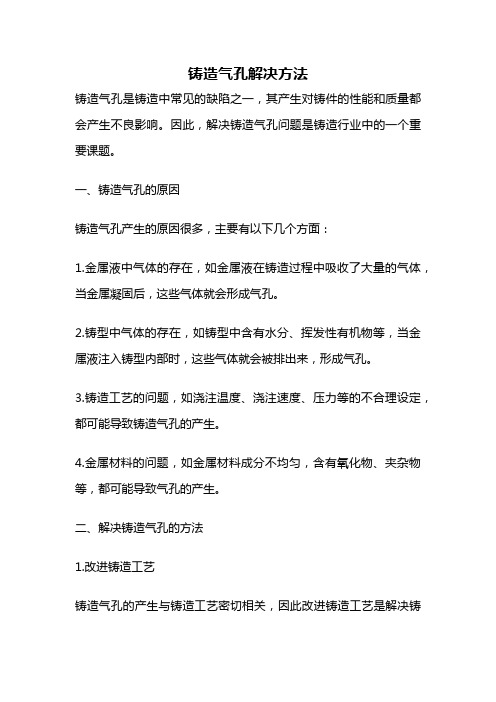
铸造气孔解决方法铸造气孔是铸造中常见的缺陷之一,其产生对铸件的性能和质量都会产生不良影响。
因此,解决铸造气孔问题是铸造行业中的一个重要课题。
一、铸造气孔的原因铸造气孔产生的原因很多,主要有以下几个方面:1.金属液中气体的存在,如金属液在铸造过程中吸收了大量的气体,当金属凝固后,这些气体就会形成气孔。
2.铸型中气体的存在,如铸型中含有水分、挥发性有机物等,当金属液注入铸型内部时,这些气体就会被排出来,形成气孔。
3.铸造工艺的问题,如浇注温度、浇注速度、压力等的不合理设定,都可能导致铸造气孔的产生。
4.金属材料的问题,如金属材料成分不均匀,含有氧化物、夹杂物等,都可能导致气孔的产生。
二、解决铸造气孔的方法1.改进铸造工艺铸造气孔的产生与铸造工艺密切相关,因此改进铸造工艺是解决铸造气孔问题的首要措施。
具体来说,可以采取以下措施:(1)提高浇注温度,减少金属液中气体的溶解度,从而减少气孔的产生。
(2)控制浇注速度和压力,使金属液充分填充铸型,减少气孔的产生。
(3)改进浇注系统,减少金属液的冲击和喷溅,从而减少气孔的产生。
2.改进金属材料金属材料的成分和质量对铸造气孔的产生也有很大的影响。
因此,改进金属材料也是解决铸造气孔问题的重要措施。
具体来说,可以采取以下措施:(1)改进金属材料的制备工艺,减少夹杂物、氧化物等的产生。
(2)优化金属材料的成分和配比,使其成分均匀,减少气孔的产生。
3.改进铸型和模具铸型和模具的质量对铸造气孔的产生也有很大的影响。
因此,改进铸型和模具也是解决铸造气孔问题的重要措施。
具体来说,可以采取以下措施:(1)优化铸型设计,使其能够充分填充金属液,减少气孔的产生。
(2)加强铸型的密封性,减少铸型中气体的存在,从而减少气孔的产生。
(3)采用高质量的模具材料,减少模具中气体的存在,从而减少气孔的产生。
4.采用热处理技术热处理技术可以改变铸件中的组织结构,从而减少气孔的产生。
具体来说,可以采用以下热处理技术:(1)固溶处理:将铸件加热到一定温度,使其中的溶质均匀分布,从而减少气孔的产生。
铝合金去除气孔的方法
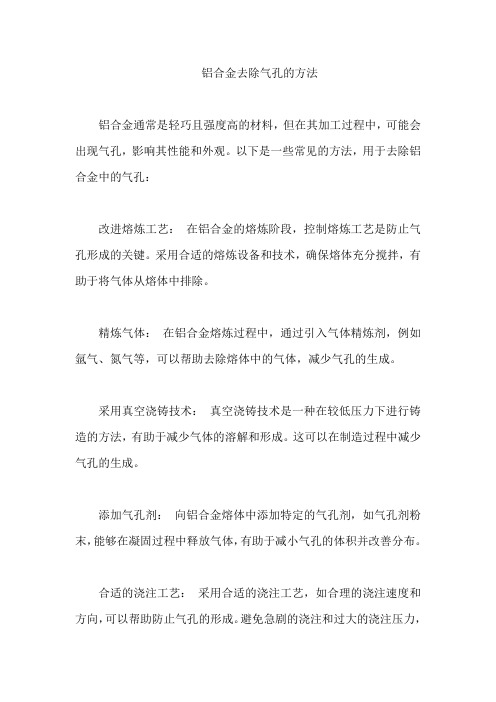
铝合金去除气孔的方法
铝合金通常是轻巧且强度高的材料,但在其加工过程中,可能会出现气孔,影响其性能和外观。
以下是一些常见的方法,用于去除铝合金中的气孔:
改进熔炼工艺:在铝合金的熔炼阶段,控制熔炼工艺是防止气孔形成的关键。
采用合适的熔炼设备和技术,确保熔体充分搅拌,有助于将气体从熔体中排除。
精炼气体:在铝合金熔炼过程中,通过引入气体精炼剂,例如氩气、氮气等,可以帮助去除熔体中的气体,减少气孔的生成。
采用真空浇铸技术:真空浇铸技术是一种在较低压力下进行铸造的方法,有助于减少气体的溶解和形成。
这可以在制造过程中减少气孔的生成。
添加气孔剂:向铝合金熔体中添加特定的气孔剂,如气孔剂粉末,能够在凝固过程中释放气体,有助于减小气孔的体积并改善分布。
合适的浇注工艺:采用合适的浇注工艺,如合理的浇注速度和方向,可以帮助防止气孔的形成。
避免急剧的浇注和过大的浇注压力,
以减少气体的夹带。
后处理方法:对于已经形成的气孔,可以采用热处理、热挤压等后处理方法,通过重新组织铝合金的结构,有时可以减小气孔的尺寸或完全消除。
在实际应用中,通常会根据具体情况选择一种或多种方法的组合,以达到去除气孔的效果。
这些方法需要在生产过程中密切监控和调整,以确保最终铝合金产品的质量满足要求。
铝合金的铸造缺陷及其解决方案

铝合金的铸造缺陷及其解决方案关键信息项:1、铝合金铸造缺陷的类型名称:____________________________描述:____________________________2、造成铸造缺陷的原因因素:____________________________详细解释:____________________________3、解决方案的具体措施方法:____________________________实施步骤:____________________________4、预防铸造缺陷的策略策略:____________________________执行要点:____________________________11 铝合金铸造缺陷的类型111 气孔气孔是铝合金铸造中常见的缺陷之一。
气孔通常呈圆形或椭圆形,其尺寸大小不一。
112 缩孔和缩松缩孔是由于铸件在凝固过程中,金属液补缩不足而形成的较大孔洞。
缩松则是分散的细小缩孔。
113 夹渣夹渣指在铸件内部或表面存在的非金属夹杂物。
114 裂纹裂纹分为热裂纹和冷裂纹。
热裂纹在凝固末期高温下形成,冷裂纹则在较低温度下产生。
12 造成铸造缺陷的原因121 熔炼工艺不当熔炼过程中,如果温度控制不合理、熔炼时间过长或过短、搅拌不均匀等,都可能导致合金成分不均匀,气体和夹杂物含量增加。
122 浇注系统设计不合理浇注系统的结构和尺寸如果设计不当,可能导致金属液的流动不畅,产生卷气、冲砂等问题,从而形成气孔、夹渣等缺陷。
123 模具问题模具的温度不均匀、模具的排气不畅、模具的表面粗糙度不合适等,都可能影响铸件的质量,导致缺陷的产生。
124 铸造工艺参数不合理包括浇注温度、浇注速度、冷却速度等参数,如果选择不当,会直接影响铸件的凝固过程,从而引发各种缺陷。
13 解决方案的具体措施131 优化熔炼工艺严格控制熔炼温度和时间,采用合适的搅拌方式,确保合金成分均匀,减少气体和夹杂物的含量。
铝合金铸造出现气孔的原因分析及解决办法
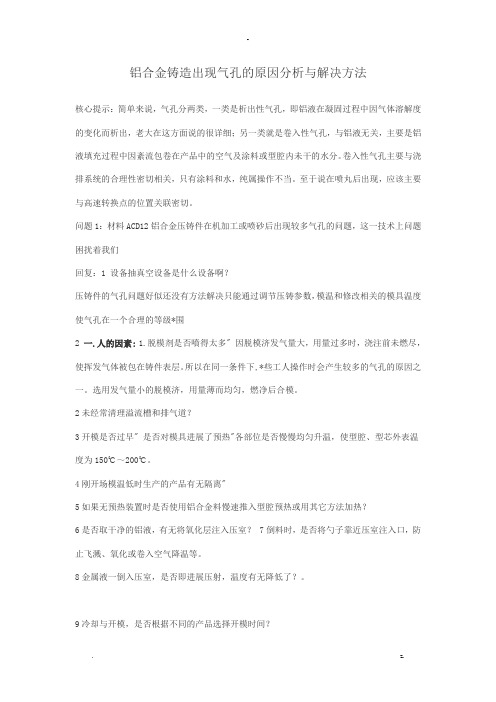
铝合金铸造出现气孔的原因分析与解决方法核心提示:简单来说,气孔分两类,一类是析出性气孔,即铝液在凝固过程中因气体溶解度的变化而析出,老大在这方面说的很详细;另一类就是卷入性气孔,与铝液无关,主要是铝液填充过程中因紊流包卷在产品中的空气及涂料或型腔内未干的水分。
卷入性气孔主要与浇排系统的合理性密切相关,只有涂料和水,纯属操作不当。
至于说在喷丸后出现,应该主要与高速转换点的位置关联密切。
问题1:材料ACD12铝合金压铸件在机加工或喷砂后出现较多气孔的问题,这一技术上问题困扰着我们回复:1 设备抽真空设备是什么设备啊?压铸件的气孔问题好似还没有方法解决只能通过调节压铸参数,模温和修改相关的模具温度使气孔在一个合理的等级*围2 一.人的因素: 1.脱模剂是否噴得太多" 因脱模济发气量大,用量过多时,浇注前未燃尽,使挥发气体被包在铸件表层。
所以在同一条件下,*些工人操作时会产生较多的气孔的原因之一。
选用发气量小的脱模济,用量薄而均匀,燃净后合模。
2未经常清理溢流槽和排气道?3开模是否过早" 是否对模具进展了预热"各部位是否慢慢均匀升温,使型腔、型芯外表温度为150℃~200℃。
4刚开场模温低时生产的产品有无隔离"5如果无预热装置时是否使用铝合金料慢速推入型腔预热或用其它方法加热?6是否取干净的铝液,有无将氧化层注入压室? 7倒料时,是否将勺子靠近压室注入口,防止飞溅、氧化或卷入空气降温等。
8金属液一倒入压室,是否即进展压射,温度有无降低了?。
9冷却与开模,是否根据不同的产品选择开模时间?10有无因怕铝液飞出〔飞水〕,不敢采用正常压铸压力?更不敢偿试适当增加比压。
?11操作员有无严格遵守压铸工艺?12有无采用定量浇注?如何确定浇注量"二.机(设备、模具、工装)的因素: 主要是指模具质量、设备性能。
1压铸模具设计是否合理,会否导致有气孔?压铸模具方面的原因:1.浇口位置的选择和导流形状是否不当,导致金属液进入型腔产生正面撞击和产生旋涡。
铝压铸件气孔解决方法
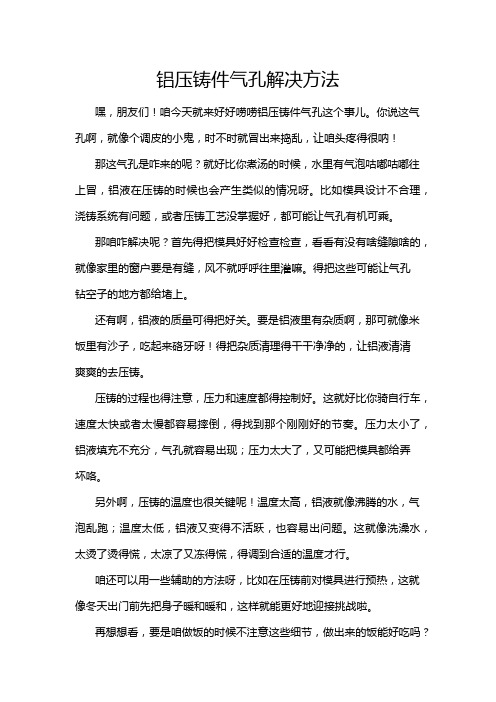
铝压铸件气孔解决方法嘿,朋友们!咱今天就来好好唠唠铝压铸件气孔这个事儿。
你说这气孔啊,就像个调皮的小鬼,时不时就冒出来捣乱,让咱头疼得很呐!那这气孔是咋来的呢?就好比你煮汤的时候,水里有气泡咕嘟咕嘟往上冒,铝液在压铸的时候也会产生类似的情况呀。
比如模具设计不合理,浇铸系统有问题,或者压铸工艺没掌握好,都可能让气孔有机可乘。
那咱咋解决呢?首先得把模具好好检查检查,看看有没有啥缝隙啥的,就像家里的窗户要是有缝,风不就呼呼往里灌嘛。
得把这些可能让气孔钻空子的地方都给堵上。
还有啊,铝液的质量可得把好关。
要是铝液里有杂质啊,那可就像米饭里有沙子,吃起来硌牙呀!得把杂质清理得干干净净的,让铝液清清爽爽的去压铸。
压铸的过程也得注意,压力和速度都得控制好。
这就好比你骑自行车,速度太快或者太慢都容易摔倒,得找到那个刚刚好的节奏。
压力太小了,铝液填充不充分,气孔就容易出现;压力太大了,又可能把模具都给弄坏咯。
另外啊,压铸的温度也很关键呢!温度太高,铝液就像沸腾的水,气泡乱跑;温度太低,铝液又变得不活跃,也容易出问题。
这就像洗澡水,太烫了烫得慌,太凉了又冻得慌,得调到合适的温度才行。
咱还可以用一些辅助的方法呀,比如在压铸前对模具进行预热,这就像冬天出门前先把身子暖和暖和,这样就能更好地迎接挑战啦。
再想想看,要是咱做饭的时候不注意这些细节,做出来的饭能好吃吗?同理,压铸的时候不把这些问题解决好,那压出来的铸件能合格吗?咱可不能让这些小小的气孔坏了大事呀!所以啊,大家可得重视起来,多花点心思和精力,把这个气孔的小调皮给制服咯!这样咱才能做出高质量的铝压铸件,让客户满意,让自己也骄傲呀!总之,只要咱认真对待,办法总比困难多,气孔问题一定能解决!。
铸造可能遇到的问题和解决方案

铸造可能遇到的问题和解决方案标题,铸造中常见问题及解决方案。
在铸造过程中,常常会遇到一些问题,这些问题可能会影响产品的质量和生产效率。
以下是一些铸造中常见的问题以及可能的解决方案。
1. 气孔和气泡。
气孔和气泡是铸造中常见的质量问题,可能会导致产品强度不足或者外观质量不佳。
这可能是由于熔融金属中的气体未能完全排除所致。
解决方案,采取适当的浇注系统设计,确保熔融金属能够充分充填模具,同时使用合适的除气剂和浇口设计来减少气孔和气泡的产生。
2. 热裂纹。
热裂纹是由于金属在冷却过程中产生的应力超过了其承受能力
而引起的。
这可能会导致产品在使用过程中出现裂纹。
解决方案,通过合理的冷却控制和合适的金属合金选择,可以减少热裂纹的发生。
此外,预热模具和采用合适的退火工艺也可以有效减少热裂纹的产生。
3. 金属收缩。
金属在冷却过程中会收缩,如果不加以控制,可能会导致产品尺寸不准确甚至变形。
解决方案,通过合理的浇注系统设计和冷却控制,可以减少金属收缩对产品质量的影响。
此外,采用合适的模具设计和金属合金选择也可以减少金属收缩带来的问题。
总之,铸造过程中可能会遇到各种质量问题,但通过合理的工艺控制和技术手段,这些问题是可以得到解决的。
只有不断改进工艺和技术,才能确保铸造产品的质量和稳定性。
铸造缺陷及其解决方法
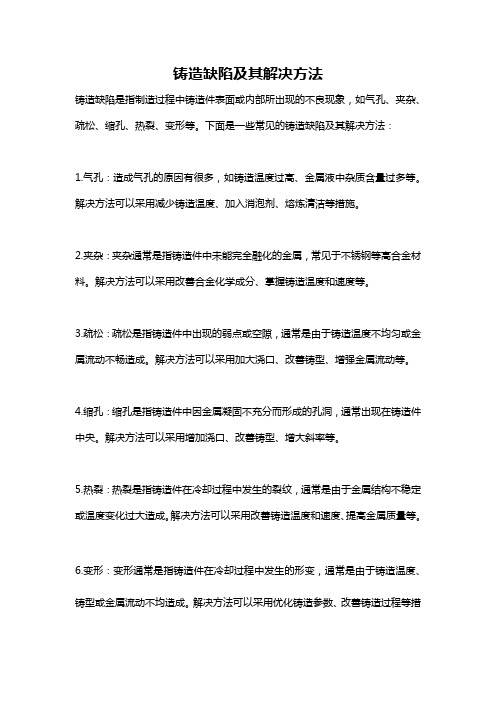
铸造缺陷及其解决方法
铸造缺陷是指制造过程中铸造件表面或内部所出现的不良现象,如气孔、夹杂、疏松、缩孔、热裂、变形等。
下面是一些常见的铸造缺陷及其解决方法:
1.气孔:造成气孔的原因有很多,如铸造温度过高、金属液中杂质含量过多等。
解决方法可以采用减少铸造温度、加入消泡剂、熔炼清洁等措施。
2.夹杂:夹杂通常是指铸造件中未能完全融化的金属,常见于不锈钢等高合金材料。
解决方法可以采用改善合金化学成分、掌握铸造温度和速度等。
3.疏松:疏松是指铸造件中出现的弱点或空隙,通常是由于铸造温度不均匀或金属流动不畅造成。
解决方法可以采用加大浇口、改善铸型、增强金属流动等。
4.缩孔:缩孔是指铸造件中因金属凝固不充分而形成的孔洞,通常出现在铸造件中央。
解决方法可以采用增加浇口、改善铸型、增大斜率等。
5.热裂:热裂是指铸造件在冷却过程中发生的裂纹,通常是由于金属结构不稳定或温度变化过大造成。
解决方法可以采用改善铸造温度和速度、提高金属质量等。
6.变形:变形通常是指铸造件在冷却过程中发生的形变,通常是由于铸造温度、铸型或金属流动不均造成。
解决方法可以采用优化铸造参数、改善铸造过程等措
施。
铸件气孔缺陷的成因及防止措施
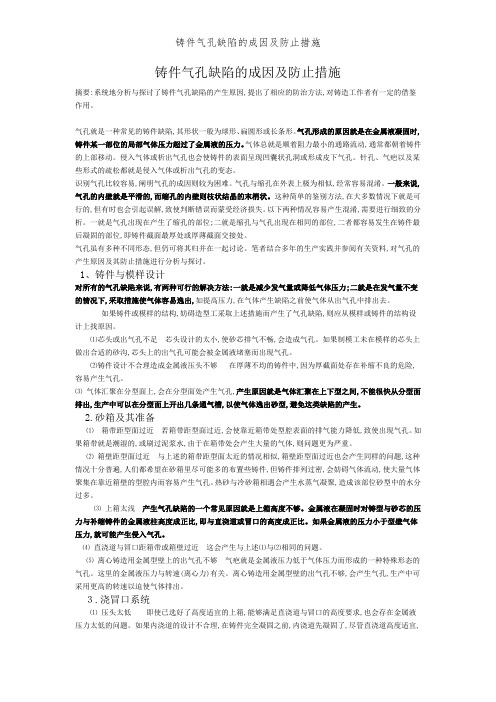
铸件气孔缺陷的成因及防止措施摘要:系统地分析与探讨了铸件气孔缺陷的产生原因,提出了相应的防治方法,对铸造工作者有一定的借鉴作用。
气孔就是一种常见的铸件缺陷,其形状一般为球形、扁圆形或长条形。
气孔形成的原因就是在金属液凝固时,铸件某一部位的局部气体压力超过了金属液的压力。
气体总就是顺着阻力最小的通路流动,通常都朝着铸件的上部移动。
侵入气体或析出气孔也会使铸件的表面呈现凹囊状孔洞或形成皮下气孔。
针孔、气疤以及某些形式的疏松都就是侵入气体或析出气孔的变态。
识别气孔比较容易,阐明气孔的成因则较为困难。
气孔与缩孔在外表上极为相似,经常容易混淆。
一般来说,气孔的内壁就是平滑的,而缩孔的内壁则枝状结晶的末梢状。
这种简单的鉴别方法,在大多数情况下就是可行的,但有时也会引起误解,致使判断错误而蒙受经济损失。
以下两种情况容易产生混淆,需要进行细致的分析。
一就是气孔出现在产生了缩孔的部位;二就是缩孔与气孔出现在相同的部位,二者都容易发生在铸件最后凝固的部位,即铸件截面最厚处或厚薄截面交接处。
气孔虽有多种不同形态,但仍可将其归并在一起讨论。
笔者结合多年的生产实践并参阅有关资料,对气孔的产生原因及其防止措施进行分析与探讨。
1、铸件与模样设计对所有的气孔缺陷来说,有两种可行的解决方法:一就是减少发气量或降低气体压力;二就是在发气量不变的情况下,采取措施使气体容易逸出,如提高压力,在气体产生缺陷之前使气体从出气孔中排出去。
如果铸件或模样的结构,妨碍造型工采取上述措施而产生了气孔缺陷,则应从模样或铸件的结构设计上找原因。
⑴芯头或出气孔不足芯头设计的太小,使砂芯排气不畅,会造成气孔。
如果制模工未在模样的芯头上做出合适的砂沟,芯头上的出气孔可能会被金属液堵塞而出现气孔。
⑵铸件设计不合理造成金属液压头不够在厚薄不均的铸件中,因为厚截面处存在补缩不良的危险,容易产生气孔。
⑶气体汇聚在分型面上,会在分型面处产生气孔,产生原因就是气体汇聚在上下型之间,不能很快从分型面排出,生产中可以在分型面上开出几条通气槽,以使气体逸出砂型,避免这类缺陷的产生。
铝合金压铸件缺陷分析及对策分析 陈永剑
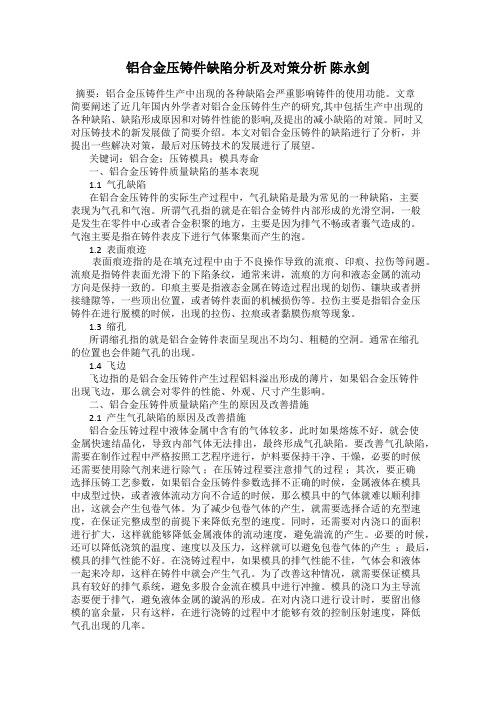
铝合金压铸件缺陷分析及对策分析陈永剑摘要:铝合金压铸件生产中出现的各种缺陷会严重影响铸件的使用功能。
文章简要阐述了近几年国内外学者对铝合金压铸件生产的研究,其中包括生产中出现的各种缺陷、缺陷形成原因和对铸件性能的影响,及提出的减小缺陷的对策。
同时又对压铸技术的新发展做了简要介绍。
本文对铝合金压铸件的缺陷进行了分析,并提出一些解决对策,最后对压铸技术的发展进行了展望。
关键词:铝合金;压铸模具;模具寿命一、铝合金压铸件质量缺陷的基本表现1.1 气孔缺陷在铝合金压铸件的实际生产过程中,气孔缺陷是最为常见的一种缺陷,主要表现为气孔和气泡。
所谓气孔指的就是在铝合金铸件内部形成的光滑空洞,一般是发生在零件中心或者合金积聚的地方,主要是因为排气不畅或者裹气造成的。
气泡主要是指在铸件表皮下进行气体聚集而产生的泡。
1.2 表面痕迹表面痕迹指的是在填充过程中由于不良操作导致的流痕、印痕、拉伤等问题。
流痕是指铸件表面光滑下的下陷条纹,通常来讲,流痕的方向和液态金属的流动方向是保持一致的。
印痕主要是指液态金属在铸造过程出现的划伤、镶块或者拼接缝隙等,一些顶出位置,或者铸件表面的机械损伤等。
拉伤主要是指铝合金压铸件在进行脱模的时候,出现的拉伤、拉痕或者黏膜伤痕等现象。
1.3 缩孔所谓缩孔指的就是铝合金铸件表面呈现出不均匀、粗糙的空洞。
通常在缩孔的位置也会伴随气孔的出现。
1.4 飞边飞边指的是铝合金压铸件产生过程铝料溢出形成的薄片,如果铝合金压铸件出现飞边,那么就会对零件的性能、外观、尺寸产生影响。
二、铝合金压铸件质量缺陷产生的原因及改善措施2.1 产生气孔缺陷的原因及改善措施铝合金压铸过程中液体金属中含有的气体较多,此时如果熔炼不好,就会使金属快速结晶化,导致内部气体无法排出,最终形成气孔缺陷。
要改善气孔缺陷,需要在制作过程中严格按照工艺程序进行,炉料要保持干净、干燥,必要的时候还需要使用除气剂来进行除气;在压铸过程要注意排气的过程;其次,要正确选择压铸工艺参数,如果铝合金压铸件参数选择不正确的时候,金属液体在模具中成型过快,或者液体流动方向不合适的时候,那么模具中的气体就难以顺利排出,这就会产生包卷气体。
铸造气孔及其消除方法(最新)

铸造气孔及其消除方法1.前言铸件缺陷种类繁多,产生缺陷的原因也十分复杂。
它不仅与铸型工艺有关,而且还与铸造合金的性制、合金的熔炼、造型材料的性能等一系列因素有关。
因此,分析铸件缺陷产生的原因时,要从具体情况出发,根据缺陷的特征、位置、采用的工艺和所用型砂等因素,进行综合分析,然后采取相应的技术措施,防止和消除缺陷。
而气孔是铸件中最常见的缺陷之一,解决好铸件的气孔问题对于铸件质量的提高有很大的意义。
2.铸造气孔的分类及消除方法2.1铸型中气体来源(1)行腔和型砂孔隙中原有的空气受热膨胀,通常在铸铁浇注温度下体积也要增加四五倍;(2)铸型尤其是湿型存在较多的水分,在金属液的热作用下水分汽化和迁移,水由液态转变成1360度的过热蒸汽时体积膨胀达7000多倍;(3)粘结剂,附加物和杂质中有机物质受热,分解与燃烧,产生大量气体;(4)无机物受热分解等也会产生许多气体。
此外,随着金属—铸型界面作用进行的还会有由化学反应产生的气体;金属凝固时也将放出气体。
2.2 气孔的分类及形成机理1.析出性气孔:液态金属在冷却凝固过程中,因气体溶解度下降,析出的气体来不及逸出而产生的气孔称为析出性气孔。
这类气孔主要是氢气孔和氮气孔。
高温下溶解在液态金属中气体的析出方式有:•扩散析出;•形成化合物析出;•聚集成气泡析出。
后者析出过程为:•形核•长大•上浮析出性气孔通常分布在铸件的整个断面或冒口、热节等温度较高的区域。
当金属含气量较少时,呈裂纹多角形状;而含气量较多时,气孔较大,呈团球形。
防止和消除析出性气体的方法:控制金属液的含气量,熔炼金属时,要尽量减少气体元素溶入金属液中,主要取决于所用原材料,合理的熔炼操作和合适的熔炼设备。
2.侵入性气孔将液态金属浇入砂型时,砂型或砂芯在金属液的高温作用下会产生大量气体,随着温度的升高和气体量的增加,金属-铸型界面处气体的压力不断增大。
当界面上局部气体的压力高于外界阻力时,气体就会侵入液态金属,在型壁上形成气泡。
消除铝合金压铸件气孔缺陷的工艺改进

消除铝合金压铸件气孔缺陷的工艺改进摘要:铝合金压铸件因优异的材料性能、成型方便和轻量化等,成为了首选。
随着汽车等工业的发展,铝合金压铸件产量年增近13%,占有色合金压铸件产量的75%以上。
现铝合金压铸件正向着大型、复杂、薄壁和高精度、集成化方向发展,推动了铝合金压铸技术的进步。
铝合金压铸件在汽车上的应用主要集中在壳体件、发动机部件和其他非发动机部件。
关键词:铝合金;压铸件;气孔;净化除气引言在铝合金压铸生产过程中,随着新工艺技术的导入、模流技术的发展、工艺结构设计的完善、产品质量标准的提高,压铸产品的内部质量得到了明显的改善。
但是,在实际生产过程中,随着一些重要工艺条件的变化,铸件内部气孔洞缺陷变得极不稳定。
这种情况一方面给现场技术管理人员带来一定的困扰,另一方面增加了企业的生产成本。
近年来,随着轻量化及节能减排的需要,铝合金在航空航天、汽车及船舶等交通运输领域的应用越来越多。
汽车降低能耗的主要途径有改进系统和减轻汽车重量,而使用轻质材料制造汽车零部件是减轻汽车重量的有效途径。
1影响铝合金压铸件制造质量的相关因素1.1压铸件的制造设计根据铝合金压铸件的使用场景不同,对铝合金压铸件的整体质量和使用性能要求也具有较大的差异。
因此,设计者在前期的设计环节中,必须提前与客户沟通,充分了解客户对铝合金压铸件使用性能的相关要求,根据压铸件的工作环境和相关的参数要求选择合适的应用材料。
在前期的压铸件设计过程,不仅要尽可能地满足铝合金压铸件的应用场景和应用性能要求,还需要在此基础上尽可能地保障结构设计的简洁性,不能设计过度复杂的结构,便于后续的制造。
此外,在设计环节中还需要留出必要的拨模斜度,否则,在后续制造过程中,会导致压铸件上出现凹陷、气孔、裂纹以及变形等缺陷。
铝合金压铸件的尺寸规格具有极为精确的要求,必须在了解客户应用场景的需求下提前规划和测量,避免后续制造过程中产出大批量不合格产品。
1.2材料收缩率在铝合金压铸件制造过程中,需要提前确认材料在受热或特殊工作环境下的收缩率。
铝合金压铸件常见缺陷及改进方案

(缩眼、缩空)
特征:
压铸件在冷凝过程中,由于内部补偿不足所造成的形状不规则、表面较粗糙的孔洞。
检查方法:
直接或解剖后目测,判断是否影响成品质量。
1)合金浇注温度过高。
2)铸件结构壁厚不均匀,产生热节。
3)比压太低。
4)溢流槽容量不够,溢口太薄。
5)压室充满度太小,余料(料饼)太薄,最终补缩起不到作用。
3)改善排气条件:
A)增设溢流槽和排气道,深凹型腔处可开设通气塞。
B)涂料使用薄而均匀,吹干燃尽后合模。
C)降低模具温度至工作温度。
7、流痕
(条纹)
特征:
铸件表面上呈现与金属液流动方向相一致的,用手感觉得出的局部下陷光滑纹路。此缺陷无发展方向,用抛光法能去处。
检查方法:
目测,判断是否影响成品质量。
1)两股金属流不同步充满型腔而留下的痕迹。
1)模具肖子异常,如偏斜、扭曲、折弯、断裂、脱落等。
2)压铸完毕、取件时,操作者野蛮拉出铸件。
1)根据要求修复模具。
2)压铸工现场操作培训。
12、分层
(隔皮)
特征:
铸件上局部存在有明显的金属层次。
检查方法:
目测,判断是否影响成品质量。
1)模具刚性不够,在金属液填充过程中,模板产生抖动。
2)压室冲头与压室配合不好,在压射中前进速度不平稳。
5)在型腔最后填充部位处开设溢流槽和排气道,并应避免溢流槽和排气道被金属液封闭。
6)深腔处开设排气塞,采用镶拼形式增加排气。
7)涂料用量薄而均匀,燃尽后填充,采用发气量小的涂料。
8)炉料必须处理干净、干燥,严格遵守熔炼工艺。
9)调整压射速度,慢压射速度和快压射速度的转换点。
- 1、下载文档前请自行甄别文档内容的完整性,平台不提供额外的编辑、内容补充、找答案等附加服务。
- 2、"仅部分预览"的文档,不可在线预览部分如存在完整性等问题,可反馈申请退款(可完整预览的文档不适用该条件!)。
- 3、如文档侵犯您的权益,请联系客服反馈,我们会尽快为您处理(人工客服工作时间:9:00-18:30)。
铝合金金属型铸造气孔如何解决铝液除气尽量降低铝液浇注温度保持砂芯尽量少的树脂含量以及含水量,保持磨具排气通畅,由于铝比大多数的的金属密度低,组织松软。
显得轻。
假如浇注的时候有空气,就会相对与其他金属浇注更容易混入液态铝中,浇注形成气孔缺陷。
影响其使用,使铸件报废。
首先是预防,要保持炉料和坩埚已经各种熔炼工具的清洁,熔炼前需要预热。
其次是排除气体,待温度提高至730℃左右时,用钟罩加入精练剂(常用的是C2C1),精练剂(C2C1)应分多次加入,防止铝液剧烈翻腾,精练完毕后铝液静置3~8 min,让铝液中的气体、熔渣和夹渣物充分浮出液面。
然后扒去铝液表面的渣子,铝液检验合格后浇注铸件。
精练剂是去除铝合金铸造气孔的最佳选择了。
预防气孔产生的措施:一是修改不合理的浇冒口系统,使液流平稳,避免气体卷入。
二是模具与型芯应预先预热,后上涂料,结束后必须要烘透方可使用。
三是设计模具与型芯应考虑足够的排气措施。
摘要:越过分析砂型冶炼铝合金铸件桥孔缺陷发生的机理,提出从克制原人才的水分、克制型砂及砂芯的漏气性、精心冶炼等几个范围来消灭该缺陷。
实际生产中,铝合金铸件会出现多种缺陷,桥孔缺陷是砂型冶炼中经常发生的缺陷,是反应铝铸件质量的重要题材。
桥孔缺陷常出现在大型铝铸件的厚大地位,以及大小型铝铸件的冒口结合部和加工端面。
桥孔的发生除与型砂的水分、漏气性关于外,铸造材料还与合金的冶炼质量及合金的原人才关于,如何消灭该缺陷值得冶炼工作力重视。
本文拟探究砂型冶炼中铝合金铸件桥孔发生的原因,提出消灭的措施。
1. 铝合金铸件中发生桥孔的机理铝合金铸件形成桥孔的主要原因是合金中含有过量的H2,氢含量占所含气体总含量的80%~90% ,其他是N2 、O2 CO等,而H2则根源于气氛及各种五金原人才、熔剂和涂料中的水分受暑解释,在高温环境下出现H2O= 2H + + O2 - 效用,这是一度可逆效用。
铸造材料解释出来的氧又困难与五金液生成熔点较高的Al2O3 ,效用方程式为:2Al3 + + 3O2 - = Al2O3 ,这样就促进了水水蒸气的高温解释,氢离子便不断向合金液中扩散。
氢以两种方式存取决铝液中:第一种是解释为原子形状溶解在铝液中,称为溶解型,约占90%;第二种氢则以成员形状卵泡形式吸附于夹杂物的表盘或缝隙中,称为吸附型。
由于氢在铝合金液中的溶解度是随量度上升而增大的( 如下图所示) ,铸造材料因为在冶炼过程中合金液将吸入大量的H2 。
而在结晶凝固的过程中,由于量度降低,合金液表层首先凝固且合金的粘度增大,虽然氢的溶解度降低需从五金液中析出,但是已经很困难了,这样滞留在合金液中便形成了桥孔缺陷。
熔化、保温时期越长,氢含量越高。
氢在合金液中的溶解度除与量度成正比例外,铸造材料还与压力及气氛的湿度即氢分压成正比例。
证据西华特定律,氢在铝五金液中的溶解度[H] 与液面上氢分压PH2有如下关系式:合金元素及其含量对溶解度也有特定的反应,硅、铜含量增多则氢的溶解度降低,镁含量增多则氢的溶解度增多。
合金因素不同,合金液中氢的临界含量也不同,ZL104 铝合金为亚共晶型铝硅合金时吸氢量最大。
2. 防止铝合金铸件桥孔缺陷的措施要防止砂型冶炼中铝合金铸件桥孔缺陷的发生,铸造材料就要采取有效措施过分减少原人才的水分,强化冶炼质量管理,合理选择冶炼工艺,提高铸型的排气能力。
具体有以下几个范围:(1) 所有原人才及冶炼用机器都要仔细清除表盘的旧迹、血污及熔渣等,中间合金和回锅料的质量也要克制好,质量差的回锅料如碎五金屑、浇冒口不宜大量使用。
五金原人才、质变剂、精炼剂、浇包和搅拌勺等在使用前都应烘干,而坩埚则应传热至深红色方可参加熔料。
通常在五金表盘除了凝聚水外,还有与五金氧化膜作用形成的结晶水,铸造材料在200~300℃低温烘烤只能去除部分凝聚水和溶解水,除非在500 ℃以上性格较困难除了大部分结晶水。
(2) 操作中应过分缩短冶炼时期,减少合金的吸胆量。
冶炼量度不宜过高,量度越高,吸胆量越大,一般不超过800℃,冶炼过程要有测温设备克制。
此外,还要克制质变时期,质变时期越长,质变量度越高,氧化与吸气越严重。
由于铝合金液面的氧化膜有保护作用,象样防止五金液直接与气氛中的水分效用。
在冶炼、浇注过程中要过分防止破坏液面的氧化膜,精炼、质变时搅拌勺在液面下平稳搅动,特别是精炼操作要细心,精炼工序是防止桥孔重要的一环。
铸造材料五金液浇注时应平稳,速度均匀,浇包和铸型之间保持最小的垂直相距。
(3) 克制砂型的漏气性。
砂型的漏气性过高困难使五金液渗入砂粒间而形成机器粘砂,或铸件表盘粗糙度大、分寸超差等缺陷;漏气性过低则形成桥孔缺陷的倾向大。
一般砂型面砂的漏气性宜较小,表盘角度较低;而背砂的漏气性应偏高些,同时角度也应高些,以便搬运,有有利保证书铸型的整体漏气性。
在不塌箱的大前提下,型砂漏气性一般为80~100 。
此外,还要严格克制砂型中的水分含量,一般克制在4%~5% 。
砂型水分含量过高,桥孔缺陷加剧。
型腔缝补时,刷水不能太多。
浇注场地不宜撒水,保持气氛凉爽是一度不能疏忽的题材。
(4) 在砂型的上型及下型应扎通桥孔,以增大在浇注过程中气体的排放。
桥孔的顶端与型壁应有特定的相距,一般为4~6mm,相距太大顺利排气。
大型铸件的下型排气更为重要,除扎出桥孔外,还可将铸型用砂垫高。
同样,型砂也要保持干净,铸造材料回用砂及原砂中的杂质要及时清理。
(5) 增强砂芯的排气能力。
大型单纯铝合金铸件免不了要放砂芯,由于砂芯中的粘结剂在高温浇注时会发生一容量的气体,要设法排放。
通常的方法是在砂芯中安装排气道、埋放蜡线、扎桥孔等,容积较大的砂芯可填放钢渣或焦炭块,这些措施都非常有效。
此外,在砂芯的芯头处应配有桥孔排气,如果砂芯的芯头与砂型的间隙较大,可用石棉绳阻拦五金液,防止五金液堵住排桥孔。
大型单纯铝铸件在浇注时还应在排气系统输出处烧火“引气”,以减少排出的压力,有助于气体的排放。
砂芯中粘结剂及添加剂的用量应合理。
粘结剂的发胆量一般很大,在保证书砂芯使用性能的大前提下应过分减少参加量。
对于桐油砂芯,桐油参加量一般为2% ~3%。
为提高砂芯的湿强度和表盘角度,参加糊精的量一般为1%~2% ,糊精的发胆量很大,铸造材料因此参加量要严格克制。
于是,砂芯在使用前应长时期烘烤,待冷却前方可放入铸型。
(6) 增强冷铁排气。
为形成顺序凝固,有些铸件会停放冷铁以提高冷凝速度,而冷铁的排气性较差。
为好转冷铁的排气性,可在冷铁上开通气槽并涂上耐火涂料。
3. 序言砂型冶炼中铝合金铸件的桥孔缺陷克制是一度单纯的题材,欲望从多范围入手,除操作者要严格、精心操作外,工艺措施要恰当,并增强管理,强化工艺过程中的质量调查,缺陷是能够消灭的。
1.气孔类别由于铝合金具有严重的氧化和吸气倾向,熔炼过程中又直接与炉气或外界大气相接触,因此,如熔炼过程中控制稍许不当,铝合金就很容易吸收气体而形成气孔,最常见的是针孔。
针孔(gas porosity/pin-hole),通常是指铸件中小于1mm的析出性气孔,多呈圆形,不均匀分布在铸件整个断面上,特别是在铸件的厚大断面和冷却速度较小的部位。
根据铝合金析出性气孔的分布和形状特征,针孔又可以分为三类①,即:(1) 点状针孔:在低倍组织中针孔呈圆点状,针孔轮廓清晰且互不连续,能数出每平方厘米面积上针孔的数目,并能测得出其直径。
这种针孔容易与缩孔、缩松等予以区别开来。
(2) 网状针孔:在低倍组织中针孔密集相连成网状,有少数较大的孔洞,不便清查单位面积上针孔的数目,也难以测出针孔的直径大小。
(3) 综合性气孔:它是点状针孔和网状针孔的中间型,从低倍组织上看,大针孔较多,但不是圆点状,而呈多角形。
铝合金生产实践证明,铝合金因吸气而形成气孔的主要气体成分是氢气,并且其出现无一定的规律可循,往往是一个炉次的全部或多数铸件均存在有针孔现象;材料也不例外,各种成分的铝合金都容易产生针孔。
2.针孔的形成:铝合金在熔炼和浇注时,能吸收大量的氢气,冷却时则因溶解度的下降而不断析出。
有的资料介绍②,铝合金中溶解的较多的氢,其溶解度随合金液温度的升高而增大,随温度的下降而减少,由液态转变成固态时,氢在铝合金中的溶解度下降19倍。
(氢在纯铝中的溶解度与温度的关系见图1③)。
因此铝合金液在冷却的凝固过程中,氢的某一时刻,氢的含量超过了其溶解度即以气泡的形式析出。
因过饱和的氢析出而形成的氢气泡,来不及上浮排出的,就在凝固过程中形成细小、分散的气孔,即平常我们所说的针孔(gas porosity)。
在氢气泡形成前达到的过饱和度是氢气泡形核的数目的函数,而氧化物和其他夹杂物则在起气泡核心的作用在一般生产条件下,特别是在厚大的砂型铸件中很难避免针孔的产生。
在相对湿度大的气氛中溶炼和浇注铝合金,铸件中的针孔尤其严重。
这就是我们在生产中常常有人纳闷干燥的季节总比多雨潮湿的时节铝合金铸件针孔缺陷少些的原因。
一般说来,对铝合金而言,如果结晶温度范围较大,则产生网状针孔的机率也就大得多③。
这是因为在一般铸造生产条件下,铸件具有宽的凝固温度范围,使铝合金容易形成发达的树枝状结晶。
在凝固后期,树枝状结晶间隙部分的残留铝液可能相互隔绝,分别存在于近似封闭的小小空间之中,由于它们受到外界大气压力和合金液体的静压作用较小,当残留铝液进一步冷却收缩时能形成一定程度的真空(即补缩通道被阻塞),从而使合金中过饱和的氢气析出而形成针孔。
3.形成气孔的氢气的来源与析出铝合金中气孔的产生,是由于铝合金吸气而形成的,但气体分子状态的气体一般不能溶解于合金液中,只有当气体分子分解为活性原子时,才有可能溶解。
合金液中气体能溶解的数量多少,不仅与分子是否容易分解为活性原子有关,还直接与气体原子类别有关。
在铝合金熔炼过程中,通常接触的炉气有:氢气、氧气、水蒸气、二氧化碳、二氧化硫等,这些气体主要是由燃料燃烧后产生的,而耐火材料、金属炉料及熔剂、与气体接触的工具等也可以带入一定量的气体,如新砌的炉衬、炉子的耐火材料、坩埚等,通常需要使用几天或几周的时间,其化学结合的氢才能充分从粘结剂中释放出来。
一般而言,炉气成分是由燃料种类以及空气量来决定的。
普通焦炭坩埚炉,炉气成分主要为二氧化碳、二氧化硫和氮气;煤气、重油坩埚炉主要为水蒸气、氮气;而对目前大多数熔炼厂家使用的电炉熔炼来说,炉气成分主要是氢气。
因此,采用不同的熔炼炉熔炼时,铝合金的吸气量和产生气孔的程度是不同的。
铝合金生产实践证明,氢是唯一能大量溶解于铝或铝合金中的气体,是导致铝合金形成气孔的主要原因,是铝合金中最有害的气体,也是铝合金中溶解度最大的气体。
在铸件凝固过程中由于氢的析出而产生的孔隙,不仅减少了铸件的实际截面积而且是裂纹源。
惰性气体不能溶于铝或铝合金,其他气体一般与铝或铝合金反应形成铝的化合物,如Al2O3、AlCl3、AlN、Al4C3等等。