铝合金腔体高精度内螺纹铣削加工
LY12硬铝异形螺纹的加工

LY12硬铝异形螺纹的加工
LY12硬铝异形螺纹是一种常用于航空航天领域的铝合金材料,具有高强度、耐磨损、耐腐蚀等优点。
加工LY12硬铝异形螺纹需要经过多道工序,包括铣削、钻孔、车削等步骤,下面以1000字进行详细讲解。
铣削是LY12硬铝异形螺纹加工的第一道工序。
铣削是利用铣刀对LY12硬铝异形螺纹
进行切削加工,将其表面切削成所需的形状和尺寸。
在铣削过程中,需要选用适当的铣削
刀具和工艺参数,以确保加工出的异形螺纹的精度和表面质量。
接下来是钻孔工序。
钻孔是在LY12硬铝异形螺纹上钻孔,使其成为一种具有孔的异形螺纹。
钻孔过程中需要选用合适的钻头和冷却液,以提高钻头的切削性能和延长其使用寿命。
在LY12硬铝异形螺纹的加工过程中,还需要进行尺寸检测和表面处理等工序。
尺寸检测是为了保证加工出的异形螺纹的尺寸精度和符合设计要求。
表面处理是为了提高异形螺
纹的表面光洁度和耐腐蚀性能,常用的表面处理方法有阳极氧化、喷砂和喷漆等。
铝合金零部件高速铣削工艺研究

铝合金零部件高速铣削工艺研究摘要:本文研究了铝合金零部件的高速铣削工艺,研究内容涵盖了刀具选择、切削速度、进给量、切削深度以及冷却液的选择等方面。
根据铝合金较低的硬度和加工表面要求,选用了单刃、双刃或多刃实心刀具进行高速铣削,并平衡了切削速度、进给量和切削深度之间的关系。
在冷却液的选择方面,建议使用水溶性切削液或喷雾切削液以降低加工温度和摩擦力,并防止铝屑和必要零件产生热膨胀和变形等问题。
通过实验验证了所提出的高速铣削工艺的可行性和有效性。
关键词:铝合金;零部件;高速铣削工艺引言:铝合金是一种轻质高强度材料,广泛应用于航空、汽车、电子等领域中的零部件制造。
高速铣削是一种有效的铝合金加工方法,可以在保证加工质量的前提下提高生产效率。
本文旨在研究铝合金零部件的高速铣削工艺,包括刀具选择、切削速度、进给量、切削深度以及冷却液的选择等方面。
通过对每个因素的分析,确定了高速铣削的工艺参数,最终实现了对铝合金零部件的高速铣削。
一、合理选择刀具在铝合金高速铣削中,刀具的选择是非常重要的。
由于铝合金是一种相对较软的材料,因此可以选择单刃、双刃或多刃实心刀具。
对于单刃刀具而言,由于只有一个刃口,其切削力较大。
然而,单刃刀具比较容易进行切削力的控制,适用于工件形状复杂的加工。
此外,单刃刀具相对简单,对机床的稳定性要求较低。
双刃刀具则具有两个刃口,能够分摊切削力,因此能够减小每个刃口的切削力。
这样一来,双刃刀具在加工过程中对机床的稳定性要求更高。
双刃刀具适用于需要较高精度和表面质量的加工。
多刃实心刀具是指具有多个刃口的刀具,它能够进一步减小切削力,并提高加工效率。
多刃实心刀具适用于大批量生产和高效率加工的情况下。
然而,多刃实心刀具的设计要求更高,对机床的稳定性和刚性要求也更高[1]。
因此,在选择刀具时,需要根据具体的加工要求、工件形状和尺寸、加工精度要求等因素综合考虑。
单刃刀具适用于复杂形状的加工,双刃刀具适用于高精度和表面质量要求较高的加工,而多刃实心刀具适用于大批量和高效率的加工。
2A12-T4高强度变形铝合金薄壁腔体零件的加工
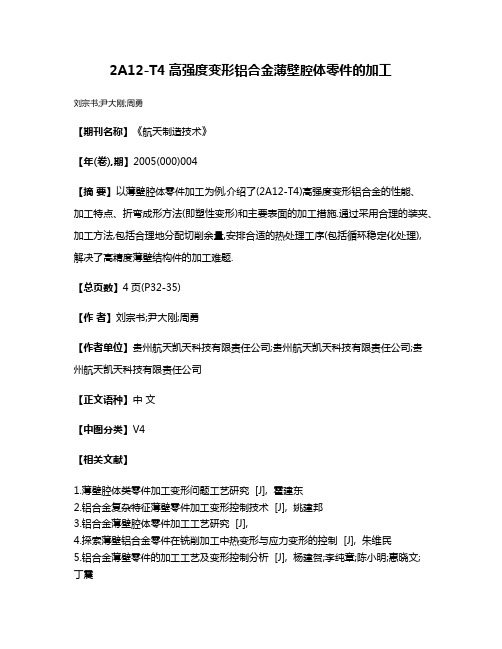
2A12-T4高强度变形铝合金薄壁腔体零件的加工
刘宗书;尹大刚;周勇
【期刊名称】《航天制造技术》
【年(卷),期】2005(000)004
【摘要】以薄壁腔体零件加工为例,介绍了(2A12-T4)高强度变形铝合金的性能、
加工特点、折弯成形方法(即塑性变形)和主要表面的加工措施.通过采用合理的装夹、加工方法,包括合理地分配切削余量,安排合适的热处理工序(包括循环稳定化处理),
解决了高精度薄壁结构件的加工难题.
【总页数】4页(P32-35)
【作者】刘宗书;尹大刚;周勇
【作者单位】贵州航天凯天科技有限责任公司;贵州航天凯天科技有限责任公司;贵
州航天凯天科技有限责任公司
【正文语种】中文
【中图分类】V4
【相关文献】
1.薄壁腔体类零件加工变形问题工艺研究 [J], 霍建东
2.铝合金复杂特征薄壁零件加工变形控制技术 [J], 姚建邦
3.铝合金薄壁腔体零件加工工艺研究 [J],
4.探索薄壁铝合金零件在铣削加工中热变形与应力变形的控制 [J], 朱维民
5.铝合金薄壁零件的加工工艺及变形控制分析 [J], 杨建贺;李纯章;陈小明;惠晓文;
丁震
因版权原因,仅展示原文概要,查看原文内容请购买。
铝合金型腔粗加工加工方法
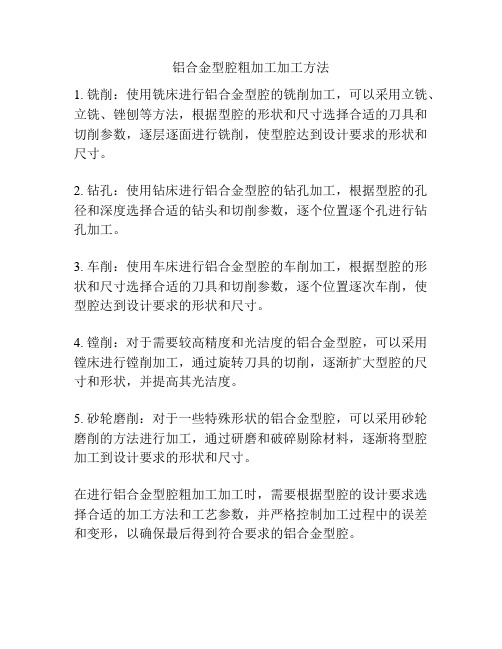
铝合金型腔粗加工加工方法
1. 铣削:使用铣床进行铝合金型腔的铣削加工,可以采用立铣、立铣、锉刨等方法,根据型腔的形状和尺寸选择合适的刀具和切削参数,逐层逐面进行铣削,使型腔达到设计要求的形状和尺寸。
2. 钻孔:使用钻床进行铝合金型腔的钻孔加工,根据型腔的孔径和深度选择合适的钻头和切削参数,逐个位置逐个孔进行钻孔加工。
3. 车削:使用车床进行铝合金型腔的车削加工,根据型腔的形状和尺寸选择合适的刀具和切削参数,逐个位置逐次车削,使型腔达到设计要求的形状和尺寸。
4. 镗削:对于需要较高精度和光洁度的铝合金型腔,可以采用镗床进行镗削加工,通过旋转刀具的切削,逐渐扩大型腔的尺寸和形状,并提高其光洁度。
5. 砂轮磨削:对于一些特殊形状的铝合金型腔,可以采用砂轮磨削的方法进行加工,通过研磨和破碎剔除材料,逐渐将型腔加工到设计要求的形状和尺寸。
在进行铝合金型腔粗加工加工时,需要根据型腔的设计要求选择合适的加工方法和工艺参数,并严格控制加工过程中的误差和变形,以确保最后得到符合要求的铝合金型腔。
铝合金薄壁深腔的数控加工
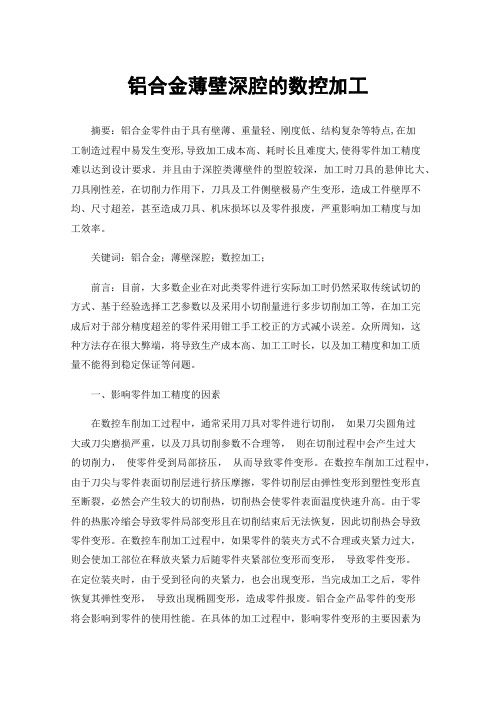
铝合金薄壁深腔的数控加工摘要:铝合金零件由于具有壁薄、重量轻、刚度低、结构复杂等特点,在加工制造过程中易发生变形,导致加工成本高、耗时长且难度大,使得零件加工精度难以达到设计要求。
并且由于深腔类薄壁件的型腔较深,加工时刀具的悬伸比大、刀具刚性差,在切削力作用下,刀具及工件侧壁极易产生变形,造成工件壁厚不均、尺寸超差,甚至造成刀具、机床损坏以及零件报废,严重影响加工精度与加工效率。
关键词:铝合金;薄壁深腔;数控加工;前言:目前,大多数企业在对此类零件进行实际加工时仍然采取传统试切的方式、基于经验选择工艺参数以及采用小切削量进行多步切削加工等,在加工完成后对于部分精度超差的零件采用钳工手工校正的方式减小误差。
众所周知,这种方法存在很大弊端,将导致生产成本高、加工工时长,以及加工精度和加工质量不能得到稳定保证等问题。
一、影响零件加工精度的因素在数控车削加工过程中,通常采用刀具对零件进行切削,如果刀尖圆角过大或刀尖磨损严重,以及刀具切削参数不合理等,则在切削过程中会产生过大的切削力,使零件受到局部挤压,从而导致零件变形。
在数控车削加工过程中,由于刀尖与零件表面切削层进行挤压摩擦,零件切削层由弹性变形到塑性变形直至断裂,必然会产生较大的切削热,切削热会使零件表面温度快速升高。
由于零件的热胀冷缩会导致零件局部变形且在切削结束后无法恢复,因此切削热会导致零件变形。
在数控车削加工过程中,如果零件的装夹方式不合理或夹紧力过大,则会使加工部位在释放夹紧力后随零件夹紧部位变形而变形,导致零件变形。
在定位装夹时,由于受到径向的夹紧力,也会出现变形,当完成加工之后,零件恢复其弹性变形,导致出现椭圆变形,造成零件报废。
铝合金产品零件的变形将会影响到零件的使用性能。
在具体的加工过程中,影响零件变形的主要因素为切削力、切削热和夹紧力。
切削过程中,产生的切削力大小直接影响到切削热和夹紧力,切削热引起铝合金材料的热变形;施加在零件上的夹紧力引起薄壁零件的冷变形;从而容易产生切削力下的振动变形。
内螺纹的铣削加工程序
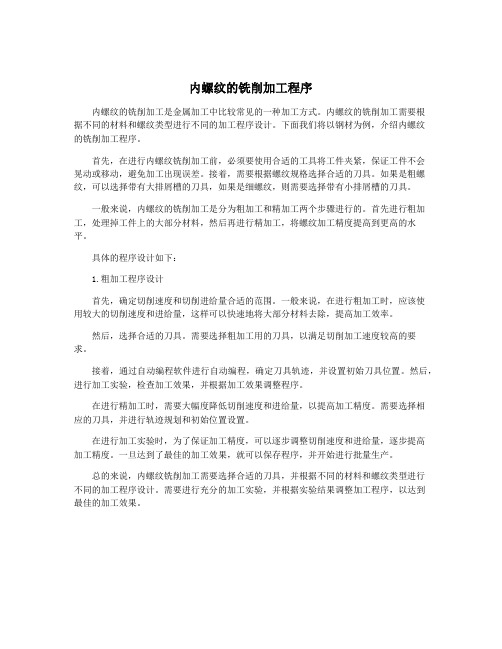
内螺纹的铣削加工程序内螺纹的铣削加工是金属加工中比较常见的一种加工方式。
内螺纹的铣削加工需要根据不同的材料和螺纹类型进行不同的加工程序设计。
下面我们将以钢材为例,介绍内螺纹的铣削加工程序。
首先,在进行内螺纹铣削加工前,必须要使用合适的工具将工件夹紧,保证工件不会晃动或移动,避免加工出现误差。
接着,需要根据螺纹规格选择合适的刀具。
如果是粗螺纹,可以选择带有大排屑槽的刀具,如果是细螺纹,则需要选择带有小排屑槽的刀具。
一般来说,内螺纹的铣削加工是分为粗加工和精加工两个步骤进行的。
首先进行粗加工,处理掉工件上的大部分材料,然后再进行精加工,将螺纹加工精度提高到更高的水平。
具体的程序设计如下:1.粗加工程序设计首先,确定切削速度和切削进给量合适的范围。
一般来说,在进行粗加工时,应该使用较大的切削速度和进给量,这样可以快速地将大部分材料去除,提高加工效率。
然后,选择合适的刀具。
需要选择粗加工用的刀具,以满足切削加工速度较高的要求。
接着,通过自动编程软件进行自动编程,确定刀具轨迹,并设置初始刀具位置。
然后,进行加工实验,检查加工效果,并根据加工效果调整程序。
在进行精加工时,需要大幅度降低切削速度和进给量,以提高加工精度。
需要选择相应的刀具,并进行轨迹规划和初始位置设置。
在进行加工实验时,为了保证加工精度,可以逐步调整切削速度和进给量,逐步提高加工精度。
一旦达到了最佳的加工效果,就可以保存程序,并开始进行批量生产。
总的来说,内螺纹铣削加工需要选择合适的刀具,并根据不同的材料和螺纹类型进行不同的加工程序设计。
需要进行充分的加工实验,并根据实验结果调整加工程序,以达到最佳的加工效果。
一种内螺纹孔的数控铣削工艺

Mechanical & Chemical Engineering242《华东科技》一种内螺纹孔的数控铣削工艺张华珍(中国航发成都发动机有限公司,四川 成都 610503)摘要:某种壳体零件的两处M14×1.5-5H6H 螺纹孔采用车削和手攻螺纹相结合的方法加工,螺纹孔表面粗糙度不合格,加工效率低。
针对加工难点进行技术改进,采用在加工中心上铣螺纹加工工艺,选用合金多刃可换刀片的螺纹铣刀,匹配合理的切削用量及程序,保证了螺纹孔的粗糙度要求。
利用加工中心的特点,工序集中,减少了单件的装夹、找正时间,提高了加工效率;两套夹具减少为一套,相比丝锥、车螺纹刀片螺纹铣刀更耐用,降低了工装的制造成本。
关键词:表面粗糙度;加工中心;铣螺纹;可换刀片的螺纹铣刀传统的螺纹孔加工方法主要采用螺纹车刀车削螺纹或采用丝锥、板牙手工攻丝。
对于有位置度等形位公差及粗糙度要求高的的小直径的螺纹孔,钻孔后手工攻丝难保证,特别对不允许有过度扣或退刀槽结构的螺纹孔,采用传统的车削方法或丝锥、板牙很难加工。
因此,传统的螺纹加工工艺在很多场合有一定的局限性[1]。
某种壳体零件的内螺纹孔结构见图1,因端面M 对螺纹孔的垂直度要求0.05mm。
采用传统的车削和丝锥攻螺纹结合的方法加工,加工一直存在的难点是两处M14×1.5-5H6H 螺纹孔表面易起皮,粗糙度达不到“”。
随着数控加工技术的发展,尤其是三轴联动数控加工系统的出现,使更先进的螺纹加工方式---螺纹的数控铣削得以实现,考虑从数控加工中心上铣螺纹进行尝试来解决螺纹孔的加工问题[2]。
1 加工难点分析 1.1 材料的加工特点 材料38CrA,毛料模锻件,热处理硬度HB269~321,材料易粘刀,内螺纹牙型面易起皮,属难加工材料,零件加工及周转中容易锈蚀。
1.2 加工方法分析 两处M14×1.5-5H6H 螺纹孔因端面M 对螺纹孔的垂直度要求0.05mm,螺纹孔、倒角、M 端面在数控车床上一次装夹加工,两处螺纹孔分两道工序加工,车床夹具需用两套。
铝管内螺纹加工方法
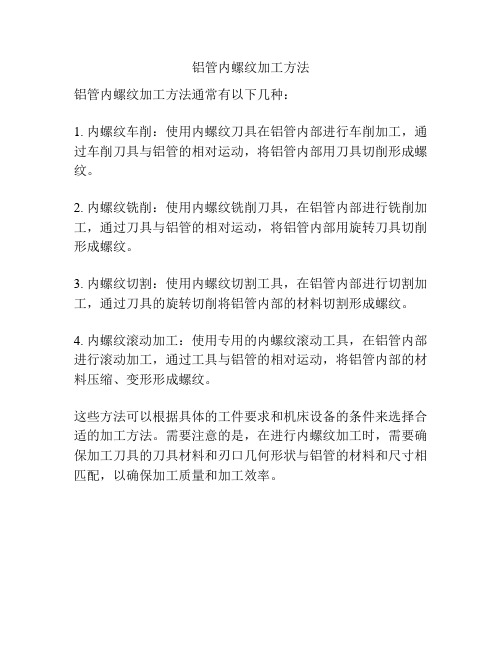
铝管内螺纹加工方法
铝管内螺纹加工方法通常有以下几种:
1. 内螺纹车削:使用内螺纹刀具在铝管内部进行车削加工,通过车削刀具与铝管的相对运动,将铝管内部用刀具切削形成螺纹。
2. 内螺纹铣削:使用内螺纹铣削刀具,在铝管内部进行铣削加工,通过刀具与铝管的相对运动,将铝管内部用旋转刀具切削形成螺纹。
3. 内螺纹切割:使用内螺纹切割工具,在铝管内部进行切割加工,通过刀具的旋转切削将铝管内部的材料切割形成螺纹。
4. 内螺纹滚动加工:使用专用的内螺纹滚动工具,在铝管内部进行滚动加工,通过工具与铝管的相对运动,将铝管内部的材料压缩、变形形成螺纹。
这些方法可以根据具体的工件要求和机床设备的条件来选择合适的加工方法。
需要注意的是,在进行内螺纹加工时,需要确保加工刀具的刀具材料和刃口几何形状与铝管的材料和尺寸相匹配,以确保加工质量和加工效率。
6000系铝合金腔体铣削加工工艺的优化
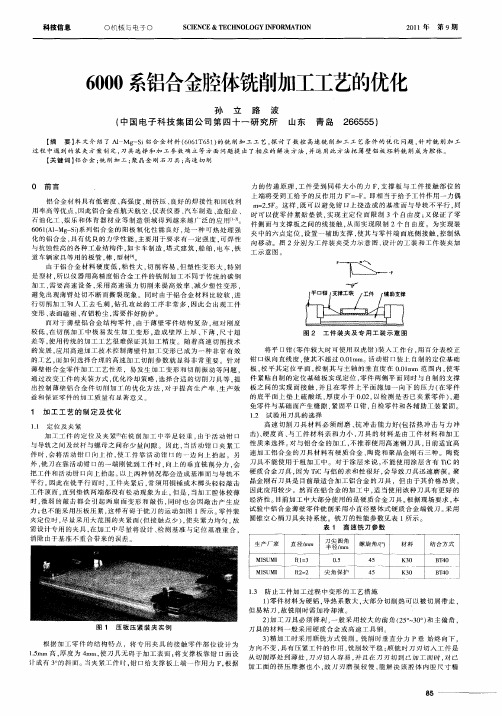
~
将 平 口钳 ( 件 较 大 时 可 使 用 双 虎 钳 ) 人 工 作 台 , 百 分 表 校 正 零 装 用 使 .1 m。活 动 钳 口装 上 自制 的定 位 基 础 工艺 , 如 何 选 择合 理 的 高速 加 工 切 削参 数 就 显 得 非 常 重 要 。针 对 钳 口纵 向 直 线 度 , 其 不 超过 00 m 而 校 控 .1 使 羹铝 合 金 零 件 加 工 工艺 性 差 , 易发 生 加 工 变 形 和 切 削 振 动 等 问题 , 板 , 平 其 定 位 平 面 , 制 其 与 主 轴 的 垂 直 度 在 00 mm 范 围 内 , 零 吐改 变 工 件 的 夹 装 方式 , 化 冷却 策 略 , 优 选择 合 适 的 切 削 刀 具 等 , 提 件 紧 贴 自制 的 定位 基 础板 实 现定 位 , 件 两 侧 平 面 同时 与 自制 的支 撑 零 并 在 陉制 薄 壁 铝 合 金 件 切 削 加 二 的 优 化 方 法 , 于 提 高 生 产 率 、 产 效 板 之 间 的 实 现 面 接 触 , 且 在 零 件 上 平 面 施 加 一 向下 的压 力 ( 零 件 [ 对 生 阳保 证 零 件 的加 工 质 量有 显 著 意 义 的底 平 面 上 垫 上 硫 酸 纸 , 度 小 于 00 , 厚 .2 以检 测 是 否 已夹 紧 零 件 )避 . 免 零 件 与基 础 面产 生 缝 隙 , 固平 口钳 , 紧 自检 零 件 和 各 辅 助 工 装 紧 固 。
IN E&T C NO O CE C E H L GYI F MA I N N OR T O
21 0 1年
第 9期
60 系铝合金腔体铣削加工工艺的优化 00
关于铝合金材料的螺纹加工的毛刺及铝屑的原理及解决方案
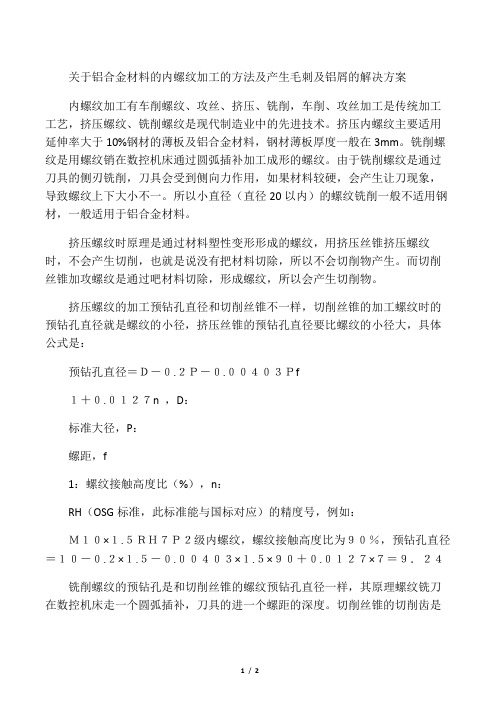
关于铝合金材料的内螺纹加工的方法及产生毛刺及铝屑的解决方案内螺纹加工有车削螺纹、攻丝、挤压、铣削,车削、攻丝加工是传统加工工艺,挤压螺纹、铣削螺纹是现代制造业中的先进技术。
挤压内螺纹主要适用延伸率大于10%钢材的薄板及铝合金材料,钢材薄板厚度一般在3mm。
铣削螺纹是用螺纹销在数控机床通过圆弧插补加工成形的螺纹。
由于铣削螺纹是通过刀具的侧刃铣削,刀具会受到侧向力作用,如果材料较硬,会产生让刀现象,导致螺纹上下大小不一。
所以小直径(直径20以内)的螺纹铣削一般不适用钢材,一般适用于铝合金材料。
挤压螺纹时原理是通过材料塑性变形形成的螺纹,用挤压丝锥挤压螺纹时,不会产生切削,也就是说没有把材料切除,所以不会切削物产生。
而切削丝锥加攻螺纹是通过吧材料切除,形成螺纹,所以会产生切削物。
挤压螺纹的加工预钻孔直径和切削丝锥不一样,切削丝锥的加工螺纹时的预钻孔直径就是螺纹的小径,挤压丝锥的预钻孔直径要比螺纹的小径大,具体公式是:预钻孔直径=D-0.2P-0.00403Pf1+0.0127n ,D:标准大径,P:螺距,f1:螺纹接触高度比(%),n:RH(OSG标准,此标准能与国标对应)的精度号,例如:M10×1.5RH7P2级内螺纹,螺纹接触高度比为90%,预钻孔直径=10-0.2×1.5-0.00403×1.5×90+0.0127×7=9.24铣削螺纹的预钻孔是和切削丝锥的螺纹预钻孔直径一样,其原理螺纹铣刀在数控机床走一个圆弧插补,刀具的进一个螺距的深度。
切削丝锥的切削齿是按照螺距螺旋的,在丝锥的每个截面圆上是按照一个螺距在上升的。
螺纹铣刀的切削齿刃不是按照螺距螺旋的,每个齿形在刀具的一个截面圆上的。
金属切削时,由于材料有延伸性,所以被切削材料容易在被切处的棱边、孔等的相交线处形成毛刺。
铝合金材料的延伸性好,所以在加工铝合金材料是更容易产生毛刺,特别是在加工铝合金材料的内螺纹时,会在螺纹的牙尖形成毛刺和铝屑。
- 1、下载文档前请自行甄别文档内容的完整性,平台不提供额外的编辑、内容补充、找答案等附加服务。
- 2、"仅部分预览"的文档,不可在线预览部分如存在完整性等问题,可反馈申请退款(可完整预览的文档不适用该条件!)。
- 3、如文档侵犯您的权益,请联系客服反馈,我们会尽快为您处理(人工客服工作时间:9:00-18:30)。
铝合金腔体高精度内螺纹铣削加工
摘要:随着电子产品结构件的加工精度逐步提高,用传统的丝锥手工攻丝加工的螺纹孔很难达到设计精度要求。
本文研究了铝合金腔体高精度内螺纹铣削加工中的工艺方法,包括加工原理、刀具选择以及编程方式。
在MIKRON数控机床上进行了螺纹铣削的加工试验,并对铣削的螺纹进行了加工精度检测评估。
关键词:螺纹铣削内螺纹加工精度
正文:
1.引言
电子产品中使用螺纹连接的铝合金材料的结构件,其螺纹孔加工的典型工艺流程为:数铣点出中心孔——钳工打螺纹底孔——钳工用丝锥攻丝加工内螺纹。
此方法加工内螺纹存在以下问题:(1)很难控制攻丝深度和垂直度,螺纹精度不高;(2)丝锥加工螺纹毛刺较多,去除困难。
随着数控技术的发展,螺纹铣削加工开始应用到螺纹加工当中。
螺纹铣削具有以下优势:⑴螺纹垂直度较好,毛刺少,尺寸精度高,无需退刀槽就能靠近底部加工出精确深度的螺纹;(2)不受螺纹结构和旋向的限制,用同一把螺纹铣刀可以加工不同结构、旋向的螺纹;(3)螺纹铣刀耐用度高,能降低加工成本。
随电子产品的发展,其铝合金结构件上螺纹孔的加工精度提出了更高的要求,丝锥攻丝加工内螺纹的方法已经很难满足精度要求,研究数控加工是实现高精度内螺纹铣削加工成为必须。
2.高精度内螺纹加工存在问题分析
电子产品中一个典型的铝合金腔体结构内螺纹结构如下图:(单位:mm,下同)
图中螺纹孔大小为M5×0.5,要求此螺纹孔最小深度为3.3,且不允许深度为3.5的平面有毛刺。
使用手工攻丝加工很难实现,面对此类工艺瓶颈,急需寻找一种新的精度更高的内螺纹加工方法。
3.内螺纹铣削加工工艺研究
3.1加工原理
考虑到螺纹铣削法在加工精度上的优势,采用以下工艺流程进行加工:数铣点出螺纹孔中心孔——数铣加工出螺纹孔底孔——数铣铣削出螺纹孔内螺纹。
通过工件一次装夹和定位,就可加工出一个完整的螺纹孔。
螺纹孔内螺纹铣削中,利用数控铣床的螺旋插补功能,刀具在XY方向上做圆周运动,同时沿Z轴做直线运动,从而走出螺旋线轨迹的方法形成螺纹。
加工示意图如下:
从图2可以看出,螺纹铣刀在XY平面内每旋转一周,在Z方向上就移动一个螺距。
3.2铣削刀具选择
螺纹铣刀分为三种:单齿式、机夹式和整体式,各螺纹铣刀的结构见下图。
单齿式机夹式整体式
其中单齿式螺纹铣刀结构简单,可以利用折断报废的铣刀刃磨而成,成本较低,在铣削螺纹时与工件接触面积小,切削力较小,不会出现让刀现象,能较好的保证螺纹的精度。
因此从加工成本和加工安全性的角度综合考虑,优先选用单齿式螺纹铣刀进行腔体螺纹孔内螺纹的铣削实验。
3.3加工机床选择和程序编制
只要是三轴联动数控机床都可实现螺纹铣削加工。
选择了MIKRON数控机床进行腔体的内螺纹铣削试验,螺纹铣削过程为:
3.3.1.刀具以快速进给的方式沿着刀具轴向定位在工件表面上方的装夹间隙中。
3.3.2.刀具按预定的进给速度移动到螺纹孔起始面。
3.3.3.刀具首先以相切的方式切入螺纹公称直径,在进行螺旋线切入之前,进行刀具轴的补偿运动,以便使螺纹路径编程从螺纹孔起始面处开始。
3.3.
4.根据螺纹铣刀的不同种类和设置的螺纹切削参数,刀具通过连续的螺旋线运动铣削螺纹。
3.3.5.切削完成后,刀具在切线方向切出轮廓并返回加工平面的起始点处。
MIKRON五轴加工中心为海德汉控制系统,本身提供了螺纹铣削指令262,只需短短几条指令便可完成内螺纹的切削,主要程序段如下:
CYCLE DEF 262 螺纹铣削
Q335=5;螺纹公称直径
Q239=0.5;螺纹螺距
Q201=-3.3;螺纹高度
Q355=1;刀具为单齿铣刀
Q351=+1;铣削方式为顺铣
Q200=10;安全间隙
Q203=30;工件表面坐标
Q204=50;第二个安全间隙
Q204=1000;铣削进给速度
3.4铣削精度对比
分别用铣削加工和传统手工攻丝加工图1所示的M5×0.5深3.3的内螺纹,试验样件如图4。
两种工艺方法加工的内螺纹剖开形貌如图5和图6所示。
加工试验后,进行了螺纹检测,其中螺纹径向尺寸采用M5×0.5的标准螺纹通规和止规进行检测,而螺纹深度尺寸采用螺纹深度规进行检测,结果如下:
铣削加工的螺纹径向尺寸:通规通,止规止;深度尺寸:3.2—3.4;螺纹表面质量:毛刺少,深3.5平面光洁无划痕,螺纹尾部无积屑现象。
攻丝的螺纹的径向尺寸:通规旋入较困难,止规止;深度尺寸:3.0—3.5;螺纹表面质量:毛刺较多,深3.5平面有划痕,螺纹尾部有明显积屑现象。
可以看出,数控铣削加工的内螺纹尺寸精度均能很好的满足设计要求。
通过数控程序控制,既精确保证了内螺纹最小深度尺寸,又避免了刀具触伤3.5深的平面,完美地解决了传统手工攻丝无法解决的难题。
4.结语与展望
本文研究了螺纹铣削技术在高精度内螺纹加工中的应用。
分析了螺纹铣削的工作原理,介绍了内螺纹铣削刀具的选择、数控机床的选择以及程序的编制方法,对腔体螺纹孔拟制了铣削工艺路线并进行了实验。
实验结果表明,螺纹铣削工艺可以较好的提高螺纹加工的尺寸精度。
参考文献:
[1]才卫国,张悦,高利民,单刃螺纹铣刀加工加工螺纹[J],煤矿机械,2010,31(04):108-110.
[2]蔺小军,单晨伟,史耀耀,螺纹数控铣削加工技术研究[J],制造业自动化,
2010,32(1):54-56.
[3] 丁玎,螺纹铣削加工刀具技术[J],工具技术,2007,41(10):105-107.
[4] 代勇韬,汪建军,小孔螺纹铣削在超高
强度钢加工中的应用[J],工艺与检测,2005,2010,32(1):54-56
[5] 梁兵,螺纹铣削法在机械加工中的运用[J],新技术新工艺,2009(10):119-120.
作者简介:
周广晏,男,山东郓城,1980年12月西南电子设备研究所,工程师电子产品制造。