在电泳涂装过程中会出现形形色色的问题,我们来介绍及解决问题
电泳常见问题及处理方法
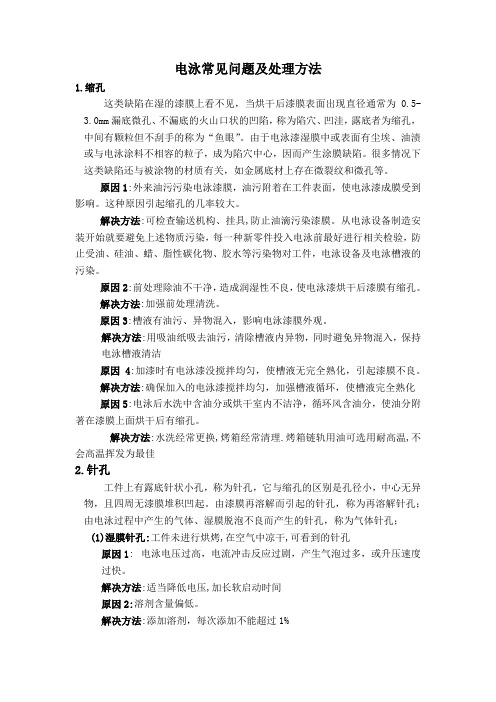
电泳常见问题及处理方法1.缩孔这类缺陷在湿的漆膜上看不见,当烘干后漆膜表面出现直径通常为0.5-3.0mm漏底微孔、不漏底的火山口状的凹陷,称为陷穴、凹洼,露底者为缩孔,中间有颗粒但不刮手的称为“鱼眼”。
由于电泳漆湿膜中或表面有尘埃、油渍或与电泳涂料不相容的粒子,成为陷穴中心,因而产生涂膜缺陷。
很多情况下这类缺陷还与被涂物的材质有关,如金属底材上存在微裂纹和微孔等。
原因1:外来油污污染电泳漆膜,油污附着在工件表面,使电泳漆成膜受到影响。
这种原因引起缩孔的几率较大。
解决方法:可检查输送机构、挂具,防止油滴污染漆膜。
从电泳设备制造安装开始就要避免上述物质污染,每一种新零件投入电泳前最好进行相关检验,防止受油、硅油、蜡、脂性碳化物、胶水等污染物对工件,电泳设备及电泳槽液的污染。
原因2:前处理除油不干净,造成润湿性不良,使电泳漆烘干后漆膜有缩孔。
解决方法:加强前处理清洗。
原因3:槽液有油污、异物混入,影响电泳漆膜外观。
解决方法:用吸油纸吸去油污,清除槽液内异物,同时避免异物混入,保持电泳槽液清洁原因4:加漆时有电泳漆没搅拌均匀,使槽液无完全熟化,引起漆膜不良。
解决方法:确保加入的电泳漆搅拌均匀,加强槽液循环,使槽液完全熟化原因5:电泳后水洗中含油分或烘干室内不洁净,循环风含油分,使油分附著在漆膜上面烘干后有缩孔。
解决方法:水洗经常更换,烤箱经常清理.烤箱链轨用油可选用耐高温,不会高温挥发为最佳2.针孔工件上有露底针状小孔,称为针孔,它与缩孔的区别是孔径小,中心无异物,且四周无漆膜堆积凹起。
由漆膜再溶解而引起的针孔,称为再溶解针孔;由电泳过程中产生的气体、湿膜脱泡不良而产生的针孔,称为气体针孔;(1)湿膜针孔:工件未进行烘烤,在空气中凉干,可看到的针孔原因1: 电泳电压过高,电流冲击反应过剧,产生气泡过多,或升压速度过快。
解决方法:适当降低电压,加长软启动时间原因2:溶剂含量偏低。
解决方法:添加溶剂,每次添加不能超过1%原因3:槽液温度过低。
电泳过程中的不正常现象和对策

辉骏生物电泳过程中的不正常现象和对策如果电源上没有显示电压,则说明电源没有输入电压,保险丝断了或电源故障。
如果没有电流或电流很小,则说明凝胶,缓冲液凝胶条(或缓冲液滤纸条)及电极三者之间有气泡,接触不好,甚至没有接触。
如果前沿指示剂向相反方向移动(如阳极电泳中溴酚蓝向阴极移动或阴极电泳中焦宁向阳极移动),则说明电源连接的正、负错置或缓冲液选择错误。
如果指示剂前沿呈现两边向上的曲线形,即常称的“微笑”现象。
则说明凝胶的不均匀冷却,中间部分冷却不好,所以导致凝胶中的分子有不同的迁移率所致。
这种情况在用较厚的凝胶以及垂直电泳时常常发生。
如果指示剂前沿呈现两边向下的曲线形,即常称的“皱眉”现象。
则常常是由于垂直电泳时电泳槽的装置不合适引起的,特别是当凝胶和玻璃板组成的“三明治”底部有气泡或靠近隔片的凝胶聚合不完全便会产生这种现象。
图示1,电泳时,前沿指示剂的(1)“微笑”现象和(2)“皱眉”现象如果电泳时间比正常要长,则可能是由于凝胶缓冲系统和电极缓冲系统的pH选择错误。
即缓冲系统的pH和被分离物质的等电点差别太小或缓冲系统的离子强度太高。
电泳时电流产生的热是大部分电泳方法的主要问题。
即使使用冷却装置,也仍然会正在凝胶中产生温度差异。
这种温度差异导致相同分子在凝胶的不同部位会有不同的迁移速度,而使蛋白带产生弯曲畸变。
特别在使用柱胶和较厚的凝胶时这种现象更为常见。
凝胶厚度、冷却温度、电参数和电泳时间4者之间在电泳时存在着依赖关系。
电压应根据加在凝胶上电极之间的距离(即凝胶宽度)而定。
电流则与凝胶的长度(加样数和加样量)有关。
一般来说,常规聚丙烯酰胺凝胶电泳不需要太高的电压,所以对薄层胶来说,温度要求也不高。
如果加双倍的电压,从理论上来说,电泳时间可缩短一倍。
但实际上由于高电压产生的副作用,并不能达到预期的目的。
所以有时采用伏/小时作为电泳时间参数可能更具有实际应用价值。
电泳过程中如果电泳盖上出现冷凝水,则表示加的电压和功率过高。
电泳涂装常见问题汇总
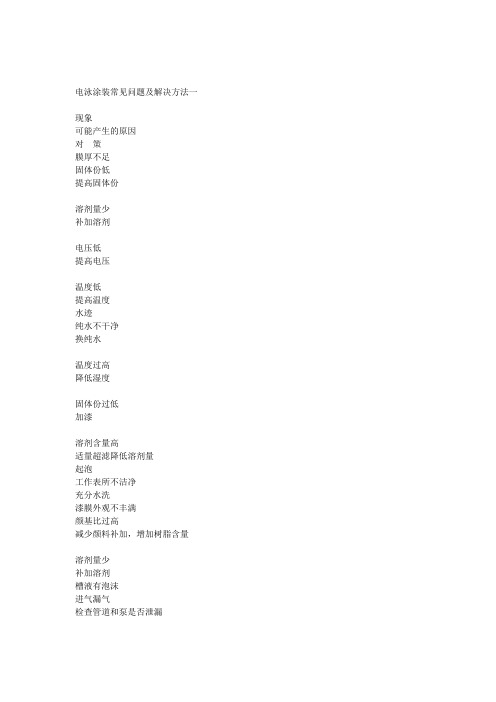
电泳涂装常见问题及解决方法一现象可能产生的原因对策膜厚不足固体份低提高固体份溶剂量少补加溶剂电压低提高电压温度低提高温度水迹纯水不干净换纯水温度过高降低湿度固体份过低加漆溶剂含量高适量超滤降低溶剂量起泡工作表所不洁净充分水洗漆膜外观不丰满颜基比过高减少颜料补加,增加树脂含量溶剂量少补加溶剂槽液有泡沫进气漏气检查管道和泵是否泄漏溢流槽液体过低提出高液体高度固体份过高,槽液粘度太大降低固体份涂膜粗糙颜料份高减少色浆,增加树脂电导率高超滤,降低电导率针孔槽液温度低升高槽液温度电导率过高超滤降低电导率漆膜不均匀,破裂槽液温度高降低温度电压高降低电压电导率高超滤降低电导率斑纹地图斑痕基材表面污染检查金属表面漆迹清洗不够增加清洗凹孔,缩孔杂质污染清除工件上杂质颜料份低补加色浆硬度烘烤时间延长烘烤时间烘烤温度低升高温度不够流平加溶剂麻点液温低升温溶剂少加溶剂浓度低加漆条纹表面外观不佳电压升高快溶剂含量低槽液固含量低??????? 电泳漆膜常见故障及其纠正方法故障产生原因纠正方法桔皮或表面粗糙电压过高降低电压溶液温度高降低温度固体分过高加水稀释槽液极距太近加大极距烘烤加温太快压缩空气吹干后再烘烤PH 值过高用醋酸或乳酸调整针孔或麻点固体分过低调整至工艺范围PH 值过低降低溶液酸度清洗水不干净换清洗水溶液电导率太高超滤去掉杂质离子膜厚太薄增加电泳电压或时间电镀表面针孔压缩空气吹干后再烘烤火山口或油点工件上附有油加强除油工序槽液面有油渍防止槽液被油污染颗粒污染加强循环过滤和超滤电压高膜层厚降低电泳电压和时间彩虹膜层太薄增加电泳电压提高膜厚颜色不符膜层太厚或太薄选择合适的工作电压和时间调配涂料时,颜色比例错严格按工艺配方配制电泳漆溶剂太多,渗透能力差,膜层厚薄不均调整溶剂含量,使其符合工艺规范不规则图形前处理不彻底加强前处理工序硬度不够烤烘时间短或温度低严格按工艺规范进行涂装面点状或片状颜色差异零件有针孔或砂眼杜绝不合格工件下槽色料乳化搅拌不匀加强电泳漆搅拌表面有水液用压缩空气吹干水滴未干即烘烤用压缩空气吹干电泳前水洗不彻底加强入槽产零件的清洗工件漆膜局部堆积PH太高用冰醋酸或乳酸调整然后超滤工件表面带碱性增加中和槽处理工件油污未除尽加强除油工艺漆膜附着力差工件表面带碱性增加中和槽处理工件油污未除尽加强除油工艺烘烤温度不够或时间太短提高烘烤温度,增加烘烤时间???????电泳槽液常规问题处理操作规范流程1.离子杂质处理测量电导率一般采用电导率仪进行测量,目前较为普遍采用的超滤处理法,在超滤以后,必须补加2-5%的溶剂(视槽液内溶剂量而定),否则会因为槽液内溶剂量缺失而造成电泳工件不良。
电泳涂装漆膜的若干问题及其防治措施

专题I实用经验Special Practical Experiences电泳涂装漆膜的若干问题及其防治措施董素芳(山东淄博职业学院化学工程系)0引言金属表面电泳涂装工艺在我国涂装行业中已经得到普遍采用,尤其在汽车行业中应用最为广泛。
电泳涂装是利用外加电场使悬浮于电泳液中的颜料和树脂等微粒定向迁移并沉积于电极之一的基底表面的涂装方法,是对水性涂料最具有实际意义的施工工艺,其主要功能是防腐蚀。
1电泳涂装的工艺流程和工艺特点1.1电泳涂装的工艺流程汽车金属表面的电泳涂装,其工艺流程为:预清理一>■上线一除油一水洗一除锈一水洗一中和一水洗—>■磷化一水洗一钝化一电泳涂装一槽上清洗一超滤水洗T烘干T下线等。
工艺流程见图lo1.2电泳涂装的工艺特点电泳漆膜具有涂层丰满、均匀、平整、光滑的优点,电泳漆膜的硬度、附着力、耐腐蚀、冲击性能、渗透性能明显优于其它涂装工艺。
主要有以下特点:①电沉积涂漆获得的漆膜质量与通电量成正比,472019年第4~5期•总第108期[W1-4预处理慕统底漆系统底漆装配生产线叢配十UK力水清谶总憑凋试A—*1馳砸诵--m密磁喊图1金属表面电泳涂装的工艺流程所以可借助增减通电量来调整涂膜沉积量。
②工件各部位都可获得比较均匀的漆膜,如内层、凹陷、焊缝、箱形体的内外表面等,解决了其它涂装方法对复杂形状工件的涂装难题,防腐性能获得显著改善。
③电沉积漆膜含水率低,它不溶于水,不流动,不易产生垂滴、流痕、滞痕等漆膜缺陷,也不会在烘干过程中产生像浸涂漆膜烘干时经常发生的溶剂气洗现象。
④由于带负电的高分子粒子在电场作用下定向沉积,因而电沉积漆膜的耐水性能很好,附着力也比其它施工方法好。
⑤电沉积涂漆所用漆液浓度低、黏度小,因而浸渍作用黏附于被涂物而带出的漆较少,特别是超实用经验丨专题Practical Experiences Special滤技术应用于电沉积涂漆后,涂料的利用率可达95%以上。
电泳常见问题分析

防治措施:改进工件的入槽条件,入槽后停留一段时间再通电电泳,使附着在工件上的气体尽量排除;检查循环系统和阴极掩蔽情况,对不合要求的地方进行调整;加大循环量,使槽内流速均匀,防止气泡在槽内滞留;适当调整电泳电压及槽液参数,使之符合工艺要求。
(12)氧化膜破裂。透过电泳漆膜,可以看到型材表面有无规则的裂纹。
(4)雾斑。与正常部位相比,局部出现无光亮斑点,侧光观察更为明显。容易出现在型材的大面和水平面上。
产生原因:酸雾、碱雾或有机溶剂气雾飞入电泳涂装工序的气氛中,附着在烘烤前的漆膜表面引起局部凝固、交联反应而产生的;漆液的中和度偏离控制范围;热水洗槽的温度、pH 值控制不好;电泳后水洗槽的pH 值太低。
(16)水平表面粗糙。亦称L效果差。被涂物电泳后水平表面粗糙,无光泽而垂直表面正常。
产生原因:槽液固体分低,有细小的凝聚物、不溶颗粒;槽液溶剂含量过低;槽液电导率太高,杂质离子含量太高;pH值太低,溶解性差;槽衬里破损,腐蚀。
防治措施:提高槽液固体分,加强过滤;适当补加电泳漆配套溶剂;加强槽液精制或排掉部分RO透过液,补加去离子水;倒槽检修槽衬里。
(2)麻点。亦称颗粒状异物,灰尘附着等。尘埃等附着在漆膜表面或漆膜下形成有手感的凹凸物。
产生原因:电泳槽前的水洗水太脏;电泳槽液中存在较粗大的机械杂质;车间空气中含有尘埃等漂浮物飘落到放在沥干区的工件上;烘烤炉内存在尘灰等杂物。
防治措施:更换电泳前水洗水;检查电泳槽过滤装置并过滤电泳槽液;搞好车间环境卫生,控制沥干区风向,防止灰尘飘浮;清理烘烤炉内卫生,清洁或更换热风循环过滤网。
(6)涂料滴痕。亦称漆斑或漆流痕。漆膜表面有略为凸起的漆斑或朝下的漆流痕迹,有手感。
产生原因:电泳出槽后停留时间过长;涂料的浓度不适当;电泳后水洗不足;RO2水洗槽固体分过高;未滴干的导电梁从正在沥干的料挂上方跨过。
电泳常见问题及处理方法
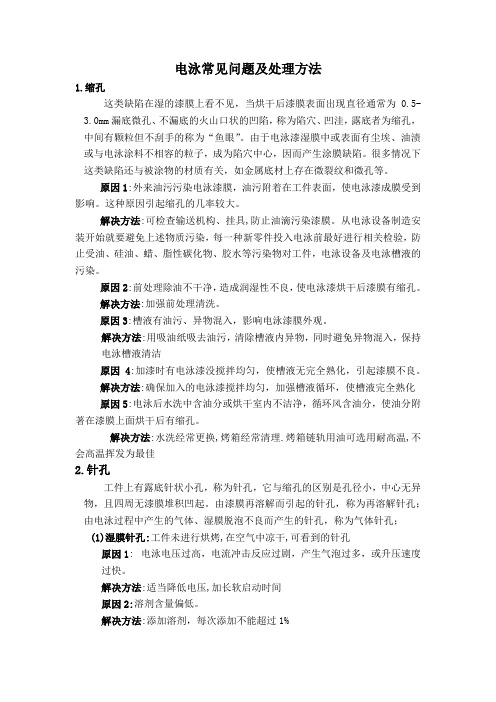
电泳常见问题及处理方法1.缩孔这类缺陷在湿的漆膜上看不见,当烘干后漆膜表面出现直径通常为0.5-3.0mm漏底微孔、不漏底的火山口状的凹陷,称为陷穴、凹洼,露底者为缩孔,中间有颗粒但不刮手的称为“鱼眼”。
由于电泳漆湿膜中或表面有尘埃、油渍或与电泳涂料不相容的粒子,成为陷穴中心,因而产生涂膜缺陷。
很多情况下这类缺陷还与被涂物的材质有关,如金属底材上存在微裂纹和微孔等。
原因1:外来油污污染电泳漆膜,油污附着在工件表面,使电泳漆成膜受到影响。
这种原因引起缩孔的几率较大。
解决方法:可检查输送机构、挂具,防止油滴污染漆膜。
从电泳设备制造安装开始就要避免上述物质污染,每一种新零件投入电泳前最好进行相关检验,防止受油、硅油、蜡、脂性碳化物、胶水等污染物对工件,电泳设备及电泳槽液的污染。
原因2:前处理除油不干净,造成润湿性不良,使电泳漆烘干后漆膜有缩孔。
解决方法:加强前处理清洗。
原因3:槽液有油污、异物混入,影响电泳漆膜外观。
解决方法:用吸油纸吸去油污,清除槽液内异物,同时避免异物混入,保持电泳槽液清洁原因4:加漆时有电泳漆没搅拌均匀,使槽液无完全熟化,引起漆膜不良。
解决方法:确保加入的电泳漆搅拌均匀,加强槽液循环,使槽液完全熟化原因5:电泳后水洗中含油分或烘干室内不洁净,循环风含油分,使油分附著在漆膜上面烘干后有缩孔。
解决方法:水洗经常更换,烤箱经常清理.烤箱链轨用油可选用耐高温,不会高温挥发为最佳2.针孔工件上有露底针状小孔,称为针孔,它与缩孔的区别是孔径小,中心无异物,且四周无漆膜堆积凹起。
由漆膜再溶解而引起的针孔,称为再溶解针孔;由电泳过程中产生的气体、湿膜脱泡不良而产生的针孔,称为气体针孔;(1)湿膜针孔:工件未进行烘烤,在空气中凉干,可看到的针孔原因1: 电泳电压过高,电流冲击反应过剧,产生气泡过多,或升压速度过快。
解决方法:适当降低电压,加长软启动时间原因2:溶剂含量偏低。
解决方法:添加溶剂,每次添加不能超过1%原因3:槽液温度过低。
电泳涂装常见问题汇总
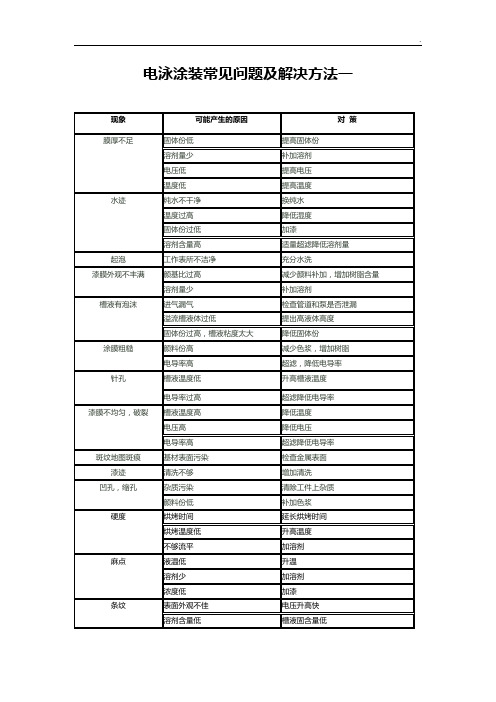
电泳涂装常见问题及解决方法一电泳漆膜常见故障及其纠正方法故障产生原因纠正方法桔皮或表面粗糙电压过高降低电压溶液温度高降低温度固体分过高加水稀释槽液极距太近加大极距烘烤加温太快压缩空气吹干后再烘烤PH 值过高用醋酸或乳酸调整针孔或麻点固体分过低调整至工艺范围PH 值过低降低溶液酸度清洗水不干净换清洗水溶液电导率太高超滤去掉杂质离子膜厚太薄增加电泳电压或时间电镀表面针孔压缩空气吹干后再烘烤火山口或油点工件上附有油加强除油工序槽液面有油渍防止槽液被油污染颗粒污染加强循环过滤和超滤电压高膜层厚降低电泳电压和时间彩虹膜层太薄增加电泳电压提高膜厚颜色不符膜层太厚或太薄选择合适的工作电压和时间调配涂料时,颜色比例错严格按工艺配方配制电泳漆溶剂太多,渗透能力差,膜层厚薄不均调整溶剂含量,使其符合工艺规范不规则图形前处理不彻底加强前处理工序硬度不够烤烘时间短或温度低严格按工艺规范进行涂装面点状或片状颜色差异零件有针孔或砂眼杜绝不合格工件下槽色料乳化搅拌不匀加强电泳漆搅拌表面有水液用压缩空气吹干水滴未干即烘烤用压缩空气吹干电泳前水洗不彻底加强入槽产零件的清洗工件漆膜局部堆积PH太高用冰醋酸或乳酸调整然后超滤工件表面带碱性增加中和槽处理工件油污未除尽加强除油工艺漆膜附着力差工件表面带碱性增加中和槽处理工件油污未除尽加强除油工艺烘烤温度不够或时间太短提高烘烤温度,增加烘烤时间电泳槽液常规问题处理操作规范流程1.离子杂质处理测量电导率一般采用电导率仪进行测量,目前较为普遍采用的超滤处理法,在超滤以后,必须补加2-5%的溶剂(视槽液内溶剂量而定),否则会因为槽液内溶剂量缺失而造成电泳工件不良。
2.溶剂含量处理溶剂含量过高处理:正确判断是否溶剂含量偏高,溶剂含量偏高容易出现水痕、伴随上膜快、同样电压下电泳膜偏厚、湿膜粘性大、湿膜蓬松等现象;如果确定是溶剂含量高,可以采用超滤方式进行超滤处理,处理完后须测量电导率,要是电导率偏低的情况下需适量补加冰醋酸或乳酸调整(一般电导率控制在400μs/cm以上即可,PH低于4.5以下的慎用)溶剂含量过低处理方法:正确判断槽液溶剂含量是否过低,一般在长时间循环下新漆补加量少,槽液温度高,频繁超滤等情况下容易出现溶剂含量较低的情况,溶剂较低的现象表现为同样电压下漆膜较薄,湿膜干燥粘性小,膜厚不均匀(彩色电泳较为明显,工件颜色不均匀现象),工件烘烤后流平较差等现象;3.槽液PH值控制槽液PH偏高的处理:一般电泳槽液较难容忍PH偏高,PH值偏高容易带来很多负面影响,常见现象较为普遍的是漆膜容易出现局部漆膜堆积现象,电泳槽液发白,明显水溶性不好,如果长时间PH偏高将造成电泳槽液沉淀,严重影响槽液稳定性,出现颗粒等现象,直至无法调整;出现PH值偏高现象可以采用补加冰醋酸或乳酸调整。
电泳涂装工艺与常见的缺陷和防治措施
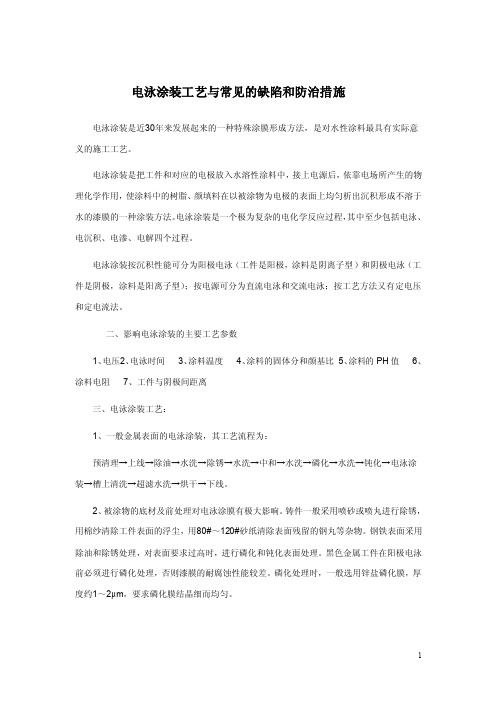
电泳涂装工艺与常见的缺陷和防治措施电泳涂装是近30年来发展起来的一种特殊涂膜形成方法,是对水性涂料最具有实际意义的施工工艺。
电泳涂装是把工件和对应的电极放入水溶性涂料中,接上电源后,依靠电场所产生的物理化学作用,使涂料中的树脂、颜填料在以被涂物为电极的表面上均匀析出沉积形成不溶于水的漆膜的一种涂装方法。
电泳涂装是一个极为复杂的电化学反应过程,其中至少包括电泳、电沉积、电渗、电解四个过程。
电泳涂装按沉积性能可分为阳极电泳(工件是阳极,涂料是阴离子型)和阴极电泳(工件是阴极,涂料是阳离子型);按电源可分为直流电泳和交流电泳;按工艺方法又有定电压和定电流法。
二、影响电泳涂装的主要工艺参数1、电压2、电泳时间3、涂料温度4、涂料的固体分和颜基比5、涂料的PH值6、涂料电阻7、工件与阴极间距离三、电泳涂装工艺:1、一般金属表面的电泳涂装,其工艺流程为:预清理→上线→除油→水洗→除锈→水洗→中和→水洗→磷化→水洗→钝化→电泳涂装→槽上清洗→超滤水洗→烘干→下线。
2、被涂物的底材及前处理对电泳涂膜有极大影响。
铸件一般采用喷砂或喷丸进行除锈,用棉纱清除工件表面的浮尘,用80#~120#砂纸清除表面残留的钢丸等杂物。
钢铁表面采用除油和除锈处理,对表面要求过高时,进行磷化和钝化表面处理。
黑色金属工件在阳极电泳前必须进行磷化处理,否则漆膜的耐腐蚀性能较差。
磷化处理时,一般选用锌盐磷化膜,厚度约1~2μm,要求磷化膜结晶细而均匀。
电泳涂装与其他涂装方法相比较,具有下述特点:(1)采用水溶性涂料,以水为溶解介质,节省了大量有机溶剂,大大降低了大气污染和环境危害,安全卫生,同时避免了火灾的隐患;(2)涂装效率高,涂料损失小,涂料的利用率可达90%~95%;(3)涂膜厚度均匀,附着力强,涂装质量好,工件各个部位如内层、凹陷、焊缝等处都能获得均匀、平滑的漆膜,解决了其他涂装方法对复杂形状工件的涂装难题;(4)生产效率高,施工可实现自动化连续生产,大大提高劳动效率;(5)设备复杂,投资费用高,耗电量大,其烘干固化要求的温度较高,涂料、涂装的管理复杂,施工条件严格,并需进行废水处理;(6)只能采用水溶性涂料,在涂装过程中不能改变颜色,涂料贮存过久稳定性不易控制。
电泳漆操作问题及解决方法
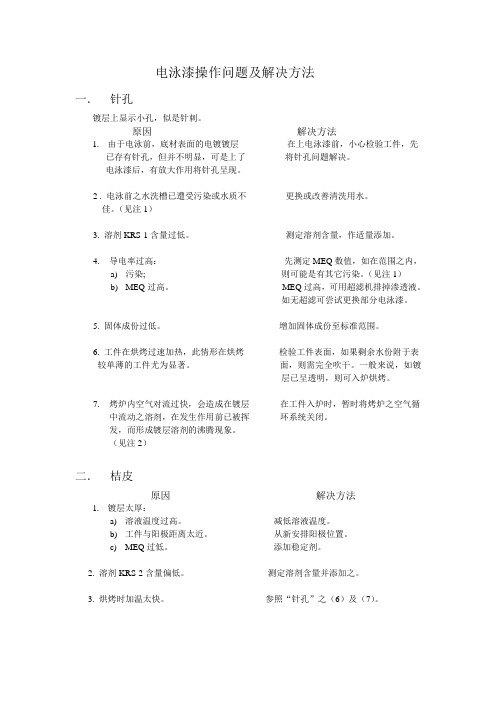
电泳漆操作问题及解决方法一.针孔镀层上显示小孔,似是针刺。
原因解决方法1.由于电泳前,底材表面的电镀镀层在上电泳漆前,小心检验工件,先已存有针孔,但并不明显,可是上了将针孔问题解决。
电泳漆后,有放大作用将针孔呈现。
2 . 电泳前之水洗槽已遭受污染或水质不更换或改善清洗用水。
佳。
(见注1)3. 溶剂KRS-1含量过低。
测定溶剂含量,作适量添加。
4.导电率过高:先测定MEQ数值,如在范围之内,a)污染; 则可能是有其它污染。
(见注1)b)MEQ过高。
MEQ过高,可用超滤机排掉渗透液。
如无超滤可尝试更换部分电泳漆。
5. 固体成份过低。
增加固体成份至标准范围。
6. 工件在烘烤过速加热,此情形在烘烤检验工件表面,如果剩余水份附于表较单薄的工件尤为显著。
面,则需完全吹干。
一般来说,如镀层已呈透明,则可入炉烘烤。
7.烤炉内空气对流过快,会造成在镀层在工件入炉时,暂时将烤炉之空气循中流动之溶剂,在发生作用前已被挥环系统关闭。
发,而形成镀层溶剂的沸腾现象。
(见注2)二.桔皮原因解决方法1.镀层太厚:a)溶液温度过高。
减低溶液温度。
b)工件与阳极距离太近。
从新安排阳极位置。
c)MEQ过低。
添加稳定剂。
2. 溶剂KRS-2含量偏低。
测定溶剂含量并添加之。
3. 烘烤时加温太快。
参照“针孔”之(6)及(7)。
三.“火山口”(Crater)现象火小点,山口形之或者为极小之气泡,但在视觉幻象下认为是火山口小点。
原因解决方法1. 打磨腊渍遗留于在工件表面。
可用除油方法,最好是用超声波,再用阴极电解清洗。
2. 工件上附有油质。
除油清洗。
3. a)于电泳漆槽水面呈有不溶解关闭循环系统,再视察水面,如有油质浮之油质。
于液面,可用干净之面巾纸将油除或用特别的除油过滤器亦可。
b)颗粒污染。
增加过滤率,或改用较小孔之滤蕊进行过滤。
4. 进入电泳槽前之污染,于水洗时槽清理水洗槽,使用溢流式槽,并加置过滤面的尘埃附于镀层上泵会较为理想。
5. 固体成份过低。
【工艺技术】汽车电泳漆膜外观不良的产生原因及其解决方法

【工艺技术】汽车电泳漆膜外观不良的产生原因及其解决方法
汽车电泳漆膜外观不良的产生原因及其解决方法
汽车电泳漆是目前进行汽车涂装中,必须要使用到的一种水性电泳漆产品,用于各种各样的汽车零件涂装。
但是由于在涂装过程中,存在着很多的不确定性,因此有时候会导致汽车电泳漆膜出现外观不良的现象。
这次就来介绍一下汽车电泳漆膜外观不良的常见原因及其解决方法。
外观不良:
汽车电泳漆膜的外观不良,主要是指电泳漆膜出现有砂粒,阴阳面,光泽、光滑度等不匀,失光,外观不丰满,漆面粗糙,手感不好等现象。
因为,优质的汽车电泳漆膜外观应是光滑、平整、丰满的。
常见原因:
1、槽液过滤不良;
2、槽液温度过低;
3、槽液固体分过低;
4、槽液颜料含量过高;
5、槽液有机溶剂含量过低 ;
6、槽液中杂质离子含量过高;
7、被涂物周围的槽液流速过低或不流动;
8、磷化膜不均匀。
解决方法:
1、及时更换过滤袋,并确保循环状况的正常。
2、严格控控槽液温度在28~32℃范围内。
3、及时补加新漆。
4、加大乳液的补加量,将灰份控制在指标要求范围内。
5、适量添加相应的有机溶剂。
6、适当地排放超滤液,补回合格纯水。
7、适时倒槽检查循环管路与喷嘴状况,确保正常。
8、加强脱脂与磷化管理,确保磷化膜均一、完整、致密。
电泳常见问题分析和解决方案
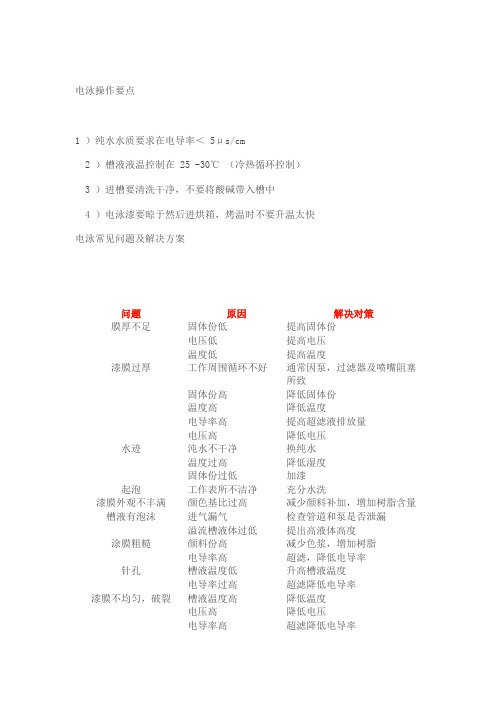
电泳操作要点1 )纯水水质要求在电导率< 5μs/cm2 )槽液液温控制在 25 -30℃ (冷热循环控制)3 )进槽要清洗干净,不要将酸碱带入槽中4 )电泳漆要晾于然后进烘箱,烤温时不要升温太快电泳常见问题及解决方案问题原因解决对策膜厚不足固体份低提高固体份电压低提高电压温度低提高温度漆膜过厚工作周围循环不好通常因泵,过滤器及喷嘴阻塞所致固体份高降低固体份温度高降低温度电导率高提高超滤液排放量电压高降低电压水迹沌水不干净换纯水温度过高降低湿度固体份过低加漆起泡工作表所不洁净充分水洗漆膜外观不丰满颜色基比过高减少颜料补加,增加树脂含量槽液有泡沫进气漏气检查管道和泵是否泄漏溢流槽液体过低提出高液体高度涂膜粗糙颜料份高减少色浆,增加树脂电导率高超滤,降低电导率针孔槽液温度低升高槽液温度电导率过高超滤降低电导率漆膜不均匀,破裂槽液温度高降低温度电压高降低电压电导率高超滤降低电导率斑纹地图斑痕底材表面污染检查金属表面漆迹清洗不够增加清洗凹孔,缩孔杂质污染清除工件上杂质颜料份低补加色浆硬度烘烤时间延长,严格按工艺操作烘烤温度升温不够流平加溶剂麻点液温低升温溶剂少加溶剂浓度低加漆条纹表面外观不佳电压升高快溶剂含量低槽液固含量低常见故障及其纠正方法故障产生原因纠正方法桔皮或表面粗糙电压过高降低电压溶液温度高降低温度固体分过高稀释溶液极距太近加大极距烘烤加温太快压缩空气吹干后再烘烤PH 值过高用有机酸调整针孔或麻点固体分过低调整至工艺范围PH 值过低降低溶液酸度清洗水不干净换清洗水溶液电导率太高超滤去掉杂质离子膜厚太薄增加电泳电压或时间电镀表面针孔压缩空气吹干后再烘烤火山口或油点工件上附有油加强除油工序槽液面有油渍防止槽液被油污染颗粒污染加强循环过滤和超滤电压高膜层厚降低电泳电压和时间彩虹膜层太薄增加电泳电压颜色不符膜层太厚或太薄选择合适的工作电压和时间调配涂料时,颜色比例错严格按工艺配方配制电泳漆溶剂太多,渗透能力差,膜层厚薄不均调整溶剂含量,使其符合工艺规范不规则图形前处理不彻底加强前处理工序硬度不够烤烘时间短或温度低严格按工艺规范进行涂装面点状或片状颜色差异零件有针孔或砂眼杜绝不合格工件下槽色料乳化搅拌不匀加强电泳漆搅拌表面有水液用压缩空气吹干水滴未干即烘烤用压缩空气吹干电泳前水洗不彻底加强入槽产零件的清洗。
汽车电泳涂装常见问题及其解决措施

汽车电泳涂装常见问题及其解决措施汽车电泳涂装常见问题及其解决措施摘要:介绍了汽车车身电泳涂装工艺流程,主要包括预清理、脱脂、表调、磷化、沥干、阴极电泳、烘干和冷却。
分析了汽车电泳涂装中常见的一些问题,如缩孔、气泡、漏底。
给出了其解决措施。
关键词:汽车;涂装;电泳;缩孔1 前言电泳涂装是汽车车身涂装的第一道环节,也可以说是整个车身涂装的基础,其质量的好坏直接影响车身的抗腐蚀性能及漆膜的装饰效果。
本文根据生产实际,对电泳涂装中出现的一些问题进行分析,介绍了解决的措施,希望对读者能有所启迪和帮助。
2 汽车车身电泳涂装工艺流程手工预清理─(60 ± 5) °C 洪流冲洗─(60 ± 5) °C 预脱脂─(60 ± 5) °C 脱脂─水洗2 次─表调─(43 ± 2) °C磷化─水洗2 次─去离子水洗─沥干─(28 ± 1) °C 阴极电泳─超滤洗2 次─去离子水洗─沥干─电泳烘干─强冷─电泳后存放。
3 常见问题分析及其解决措施上述电泳涂装工艺流程中,车身冲洗采用全浸式喷浸结合的处理方式,而车身运输系统采用自行葫芦和滑橇地面输送机相结合的方式。
受工艺条件、设备、车身结构的限制,在车身电泳涂装生产过程中出现了一些问题。
以下为常见问题及其解决方法。
3. 1 滑橇底部油泥污染导致电泳缩孔及其解决办法在车身经手工预清理完后,进行洪流冲洗前,需要将车身承载在滑橇上并锁紧,再装挂在自行葫芦系统的吊架上,然后依次通过电泳涂装各工艺槽。
当滑橇第一次通过电泳槽时,滑橇表面会泳涂上一层电泳漆膜,形成绝缘层。
而当滑橇承载车身再一次通过电泳槽时,滑橇表面因有绝缘层的存在而不会泳涂上新的电泳漆膜,但会一次次附上一层新的电泳浮漆。
由于电泳后的水洗工艺主要是针对车身,而位于车身底部的滑橇不可能被冲洗干净。
因此,当附有电泳浮漆的滑橇在电泳后工位(如电泳烤房、电泳烤后存放)的输送链上前行时,滑橇底部的电泳浮漆和已泳涂上的电泳漆膜与输送链上的滚子不断接触、摩擦,就会粘附滚子上的润滑油,形成油泥。
电泳漆外观不良的产生原因和整改措施

电泳漆外观不良的产生原因和整改措施电泳漆外观不良的产生原因和整改措施产生原因•电泳漆质量不过关•涂装工艺不合理•漆膜表面处理不到位•设备设施存在问题•人为操作失误整改措施提高电泳漆质量•定期检测原材料质量,确保电泳漆质量符合标准要求•引进高质量的电泳漆品牌,提高涂装质量优化涂装工艺•对涂装工艺进行全面评估和改进,确保其科学合理•采用先进的涂装设备,提高涂装效率和质量加强漆膜表面处理•对待涂物体进行必要的去油、除锈处理,确保漆膜附着力•增加表面处理工序,如喷砂、磨光等,提高表面质量维护设备设施•定期维护和检修涂装设备,确保其正常工作•更新老旧设备,提高设备性能和稳定性加强员工培训与管理•定期组织员工参加培训课程,提高操作技术水平•加强对员工的日常管理,规范操作流程,减少人为操作失误的发生结语针对电泳漆外观不良问题,我们应从电泳漆质量、涂装工艺、漆膜表面处理、设备设施和员工培训与管理等方面进行整改措施的制定和落实。
只有全面加强管理,优化工艺,提高质量,才能确保电泳漆外观良好,满足客户的要求和期望。
经过对电泳漆外观不良产生原因的分析,我们可以制定以下更具体的整改措施:提高电泳漆质量•定期对电泳漆进行抽样检测,确保其颜色、附着力、耐磨性等性能符合要求•与供应商建立稳定的合作关系,确保供应的电泳漆质量稳定可靠•定期参加行业技术交流会议,了解最新的电泳漆技术和质量管理方法优化涂装工艺•加强工艺流程的规范化管理,确保每一道工序的操作规范和标准化•优化涂装参数,如电压、电流、涂装时间等,确保漆膜均匀、平整•使用适当的涂装模板和工装夹具,提高产品涂装一致性和效率加强漆膜表面处理•确保表面处理工序的配套设备和工艺操作符合要求,保持一致性•使用合适的表面处理剂和材料,如去油剂、除锈剂等,保证处理效果•对处理后的表面进行检查,确保去污彻底、除锈彻底维护设备设施•建立设备设施定期检修和保养的计划和制度,确保设备长期稳定运行•对设备设施进行定期维护和检修,及时发现和处理潜在问题•更新老旧设备,引进新型涂装设备,提高自动化程度和涂装效果加强员工培训与管理•建立员工技能培训和考核制度,提高员工的涂装技术和质量意识•指定专人负责员工培训工作,确保培训内容全面、系统•建立纪律制度,对涂装操作规范进行严格管理,防止人为操作失误通过采取以上整改措施,能够解决电泳漆外观不良问题,提高产品质量,满足客户的需求和期望。
电泳弊病及解决方法

电泳施工中常见的漆膜缺陷及预防办法虽然电泳涂装是大量操作变量的动态平衡,操作人员不时地对电泳涂装工艺的控制参数进行监控和调整,就可以获得良好的外观、膜厚和物理特性。
因此,当检测出漆膜缺陷时,就应对它进行一系列准确、可靠的分析,然后及时提出解决办法。
电泳施工中最常见的漆膜缺陷有涂膜粗糙、缩孔、针孔、花斑、涂膜过薄、涂膜过厚、水痕、工件内表面涂膜过薄等,造成这些缺陷的原因不是单一的因素,下面简单介绍一下漆膜缺陷的原因及防止办法。
(一)漆膜粗糙(肉眼可见小颗粒)1.产生原因①槽液颜基比过高。
②进入电泳槽的被涂工件及挂具不干净。
③电泳槽由于过滤不良,使槽液杂质离子过多,电导率偏高。
④槽液中助溶剂含量偏低。
2.防治方法①与供应商协商,提供低颜基比涂料,以便调整槽液。
②加强前处理液的过滤,降低磷化液的残渣含量,严格控制磷化后冲洗的水质,以及浮在工件表面上的磷化残渣;定时清洗挂具疏松污垢等。
③加强电泳槽液的过滤。
定期清洗、更换过滤装置,严格控制槽液的PH值和碱性物质的带入,防止树脂析出。
④定期检测槽液溶剂的含量,若偏低应及时补加溶剂。
以确保槽液的稳定。
(二)缩孔、陷穴1.产生原因①槽液颜基比失调,颜料含量低。
②被涂工件前处理不良或清洗后磷化膜上面落上油污、尘埃等。
③槽液中混入油污、尘埃、油飘浮在槽液面或乳化在槽液中。
④电泳后冲洗液混入油污。
⑤外来油污污染电泳涂膜。
⑥烘干室内不干净、循环风内含油。
2.防止方法①调整槽液的颜基比,补加色浆提高颜料含量。
②加强被涂工件脱脂工序的管理,确保磷化膜不被二次污染。
③在槽液循环系统安装除油过滤装,同时检查油污染来源,以便彻底清除油法。
④加强后冲洗液水质的检测,定期清洗更换过滤袋,以确保后冲洗水过滤质量。
⑤保持涂装环境洁净,清除对涂装有害的物质,尤其是含有机硅物质源(如电缆、拉延油、防锈油、防焊渣粘结剂、密封胶等),涂装车间及相关车间的设备及工艺介质所使用的原材料和辅助材料都不能含有酯酮。
铝合金电泳外观异常现象原因及对策

变黄(乳白)
变黄(铝材之端部容易发生)
a-阳极氧化皮膜太厚;
b-阳极氧化后水洗不足;
c-热水洗不足(时间);
d-热水洗温太低;
e-热水洗水质变(如:电导率上升,pH值降);
f-电泳涂膜太厚(15μ以上)。
a-控制氧化皮膜于规格内;
b-加强阳极氧化后水洗:增加水量,加空气搅拌;
c-延长热水洗时间;
聚云状斑痕
雪状、波状条痕状、麒云状
a-碱浸蚀不足;
b-碱浸蚀中铝含量过多。
a1-上升碱蚀浓度;
a2-延长碱蚀时间;
b-减少铝含量。
聚痕状斑痕
铝材表面全面,聚当痕状斑痕
a-电泳后被溶解;
b-放置RO水洗水中时间太长(电泳液,水洗液pH也会影响再溶解)。
a-不要长时间(15分钟以上)放置于电泳液中;
b-不要长时间(25分钟以上)放置于水洗中(管理电泳液,水洗液pH)。
铝材已干燥
a-缩短滴水时间;
b-延长浸渍时间;
c-提高循环量;
d-检查入槽速度。
泡沫附着
(泡斑痕,气泡),
铝材侧面,下面易发生
a-电泳表面含极小气泡;
b-阴极气体分散于电泳槽液中;
c-由循环系统吸入空气;
d-铝材入槽所带入气泡。
a1-以溢流除去;
a2-增加循环量;
a3-液体流向要均匀;
a4-用空气吹去;
铝合金电泳外观异常现象原因及对策
深圳雷邦磷化液工程部编辑
摘要:本文对目前铝合金电泳漆出问题最多的种类及相应的处理对策进行了归纳总结。
异常现象
原因
处理对策
接点烧焦
变黄
a-接点不良。
a-接点要充分接触。
电泳掉漆纠正预防措施

电泳掉漆纠正预防措施1. 引言电泳是一种常用的金属表面涂装工艺,它可以有效地提高金属制品的耐腐蚀性和美观性。
然而,在电泳过程中,有时会出现掉漆的问题,影响涂装质量。
因此,有必要采取一些纠正和预防措施来解决这个问题。
2. 掉漆原因分析2.1 涂装质量不合格电泳掉漆问题的一个常见原因是涂装质量不合格。
涂料的选择、稀释比例、喷涂工艺等因素都会影响涂装质量。
如果使用的涂料质量不佳或者稀释比例不正确,就会导致涂料附着力差,容易掉漆。
2.2 电泳液质量问题电泳液的质量也是导致掉漆问题的原因之一。
电泳液的配方、浓度、PH值等因素都会影响涂装效果。
如果电泳液的配方不合适或者浓度、PH值不稳定,就会导致涂料附着力不足,容易出现掉漆现象。
2.3 电泳工艺参数不当电泳工艺参数的设定也是掉漆问题的重要原因。
电泳槽的温度、电流密度、电泳时间等参数都需要合理设定,才能确保涂料均匀附着在金属表面。
如果这些参数设定不当,就会导致涂料附着不良,容易掉漆。
3. 纠正措施针对以上分析的掉漆原因,我们可以采取以下纠正措施来解决电泳掉漆问题。
3.1 提高涂装质量首先,选择优质的涂料,并按照厂家的建议稀释,确保涂料的质量和稀释比例正确。
其次,严格控制喷涂工艺,确保涂料均匀喷涂在金属表面,附着力良好。
3.2 优化电泳液配方调整电泳液的配方,确保液体稳定,成分均匀。
合理控制电泳液的浓度和PH 值,确保液体对金属表面的附着力适宜,避免掉漆问题的发生。
3.3 合理设定工艺参数根据具体情况,合理设定电泳槽的温度、电流密度和电泳时间等参数。
温度应在涂料的固化温度范围内,电流密度应适中,电泳时间要足够长,以确保涂料均匀附着在金属表面,提高涂装质量,减少掉漆风险。
4. 预防措施除了纠正措施之外,我们还可以采取一些预防措施,减少电泳掉漆的发生。
4.1 加强质量管理加强对涂料和电泳液的质量管理,确保其符合标准要求。
定期检测涂料的质量、稀释比例、PH值等指标,并进行调整。
某电泳涂装线出现的异常附着问题及解决对策
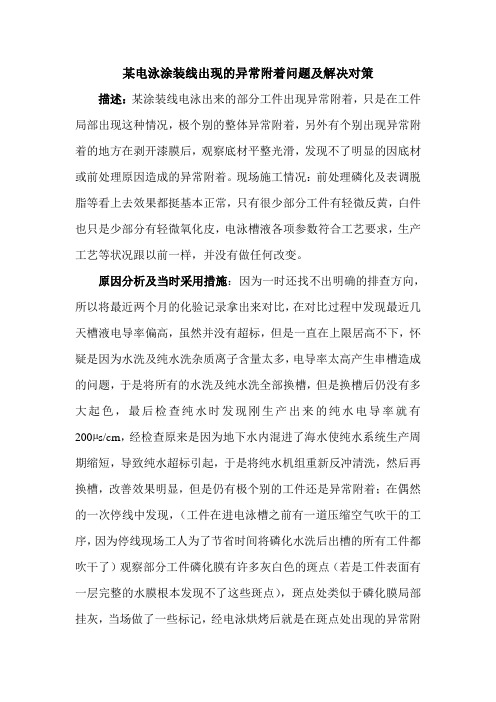
某电泳涂装线出现的异常附着问题及解决对策描述:某涂装线电泳出来的部分工件出现异常附着,只是在工件局部出现这种情况,极个别的整体异常附着,另外有个别出现异常附着的地方在剥开漆膜后,观察底材平整光滑,发现不了明显的因底材或前处理原因造成的异常附着。
现场施工情况:前处理磷化及表调脱脂等看上去效果都挺基本正常,只有很少部分工件有轻微反黄,白件也只是少部分有轻微氧化皮,电泳槽液各项参数符合工艺要求,生产工艺等状况跟以前一样,并没有做任何改变。
原因分析及当时采用措施:因为一时还找不出明确的排查方向,所以将最近两个月的化验记录拿出来对比,在对比过程中发现最近几天槽液电导率偏高,虽然并没有超标,但是一直在上限居高不下,怀疑是因为水洗及纯水洗杂质离子含量太多,电导率太高产生串槽造成的问题,于是将所有的水洗及纯水洗全部换槽,但是换槽后仍没有多大起色,最后检查纯水时发现刚生产出来的纯水电导率就有200µs/cm,经检查原来是因为地下水内混进了海水使纯水系统生产周期缩短,导致纯水超标引起,于是将纯水机组重新反冲清洗,然后再换槽,改善效果明显,但是仍有极个别的工件还是异常附着;在偶然的一次停线中发现,(工件在进电泳槽之前有一道压缩空气吹干的工序,因为停线现场工人为了节省时间将磷化水洗后出槽的所有工件都吹干了)观察部分工件磷化膜有许多灰白色的斑点(若是工件表面有一层完整的水膜根本发现不了这些斑点),斑点处类似于磷化膜局部挂灰,当场做了一些标记,经电泳烘烤后就是在斑点处出现的异常附着,但斑点处也是有的好有的坏,但是可以认定就跟这些斑点有关,于是开始排查磷化及表调效果,最后发现原来是因为表调使用周期太久,检测参数虽然正常但是效果并不能达到理想要求,于是将表调更换重新配槽,为了更安全起见排放了部分超滤,降低了入槽电压采用了较为缓和的电泳涂装条件,情况完全解决。
案例总结:出现这种情况以我个人来看应该是一个综合的因素引起的,并不是因为某一个环节所造成的。
电泳涂装异常发生的原因和对策(精)

溶剂少(BC过少、二甲苯过少)
干燥温度下降,改善环境条件
涂膜过厚
涂料温度、电压、时间在正确的条件下进行
溶剂量过剩(膜厚)
分析溶剂量、超滤离子交换处理
预干燥不良、有水份
预干燥延长时间
涂料被污染、气泡过多
阳离子交换处理
涂膜过低
(干涉膜的发生或
色泽太淡)
固体份太低
经常补充并保持涂料适当浓度
涂料温度太低
控制涂料温度在正常状态
电压低
提高电压
3、使用阳极袋
涂料中溶剂过少
补充BC或二甲苯
杂质的混入和涂料的污染导致电导度
上升
实施离子交换树脂处理或超滤处理
涂料温度的过高
将温度控制在适当的温度范围内
电镀层不活化
除去氧化膜
涂料的PH过低
炉内有油(如硅油,含氯气体)
用UV处理或阳离子交换处理
净化干燥炉
电泳涂装异常发生的原因和对策(2)
发布时间:10-06-10关注次数:46
搅拌太强
正确控制搅拌速度
涂料被污染
离子交换树脂处理
涂料老化
分析补充或涂料一部分更新
溶剂量太少
补充BC溶剂或二甲苯
光泽不好
(注意粗糙、块状物、
橘皮同时发生的场合)
钝化促进处理过度
采用浸渍或不用钝化促进处理
涂料的污染
离子交换树脂处理
电泳后水洗不良
检查水洗槽是否污染或水的流量
涂料中有微粒状物
用硅藻土或精密滤芯过滤
保持干燥炉内和作业场内清洁
涂膜外观粗糙
部分的异常电泳
(颜色不均匀)
涂料的污染(杂质或老化)
1、离子交换树脂处理、UF处理
- 1、下载文档前请自行甄别文档内容的完整性,平台不提供额外的编辑、内容补充、找答案等附加服务。
- 2、"仅部分预览"的文档,不可在线预览部分如存在完整性等问题,可反馈申请退款(可完整预览的文档不适用该条件!)。
- 3、如文档侵犯您的权益,请联系客服反馈,我们会尽快为您处理(人工客服工作时间:9:00-18:30)。
二、阴极电泳工艺流程简介:超滤有卷式和管式两种。
超滤设备是电堆积涂装的首要辅佐设备,选用合适的超滤设备,它将供给满足的超滤液,供涂装后工件的后冲刷,一起也能够挑选性地铲除槽液中某些低分子物质或电解质等,抵达槽液净化的意图。
当超滤液电导过高,可排放部分超滤液,替换去离子水,添加部分助溶剂和有机酸加以调整。
5、过滤设备为及时铲除电堆积涂料作业液的杂质粒子,体系应设有过滤设备,一般有过滤筒和过滤袋二种。
6、烘烤设备烘烤设备须考虑对被涂材料的耐热及厚薄加以归纳考虑。
为保证涂膜质量,可选用对流办法以行进热传导的效果,抵达涂层色彩均匀的意图。
7、直流电源直流电源是供给电堆积进程的动力设备,其波纹系数一般小于5%,最高运用电压尽或许与电泳漆的作业电压接近。
涂装时所需电流密度应为20安/米2,电源电压应挑选可调式,直流电源设备能够选用可控硅或硅管及调压整流办法。
起动可选用软起动。
8、热交换设备、水洗设备、电堆积液的装备设备(略)四、阴极电泳建槽及涂装1、配比(分量比)称谓黑浆基料去离子水亮光双组份 145~10哑光双组份 134~82、进程:(1)清洗电泳槽循环管道A.清洗电泳槽中的可见杂质粒子、尘土和油污。
B.再将适量乳化剂、有机酸、溶剂投入电泳槽内,并灌满自来水,循环3-5小时,清洗电泳槽和循环管道内的油污,中和槽中碱性杂质,然后排放用于清洗水洗槽和阳极罩。
C.别离再用去离子水清洗电泳槽、循环管道及泵内的杂质离子。
(2)电泳液的配比:依据电泳槽的规范核算出所需原漆量,按要求用去离子水将原漆稀释至规则漆液固含量。
并经280-350目过滤网过滤入槽,让电泳漆循环熟化24小时。
(1)电泳温度:一般操控在30-35℃之间,漆膜厚度随温度升高而添加。
(2)施工电压:依据不同型材,极板之间不同的距离,施工电压一般操控在80-180V。
(3)电泳时刻:依据漆膜厚度,一般操控在40—90秒。
(4)烘烤:烘烤温度在180℃,时刻操控在30分钟左右。
留神事项:A.配漆时所用去离子水导电率不得高于5µs/cm。
B.配完漆液后,要求主副槽液位差在5-250px之间,以保证槽液的正常循环。
C.工件电泳好后,在槽内停放时刻不能过长,不然漆膜将被溶解。
D.如工件在操作进程中落入电泳槽内,应及时取出。
E.前处理是要害,它将直接影响电泳涂装质量和漆液的安稳,以及电泳漆的防腐性功用。
F.不允许将油污、碱性物质带入漆槽内。
五、保护阴极电泳涂装的若干重要事项1、漆液固含量漆液固体份一般操控在12-18%(依据颜基比的不同),因为不断地电泳,漆液固含量不断下降,所以有必要依据加工量(加工面积)算出一个作业周期所需用漆量,添加漆时以槽液或去离子水作为稀释液,稀释后通过滤入槽,选用少数屡次参加法为好,尽或许坚持漆液的固含量在必定规划之内,一起坚持主副槽的落差。
假定固含量偏低,简略发生槽液安稳性差,电泳膜偏薄,泳透率下降等害处。
2、漆液PH值漆液PH值一般操控在6.3+0.3以内,假定PH值偏低,可加速阳极液的更新或用超滤液加以调整。
有必要常常盯梢查验。
3、关于电导率电导率是电泳槽液的根柢政策之一,一般操控在1100—1700µs/cm,它首要用于衡量槽液的导电性,具有较高电导率的电泳涂料可得到满足高的泳透率,因而,电导率越高,泳透率越高,但高的电导率有必要是因为电泳涂料自身的电导率而得到的,在另一种状况下,因为电泳施工进程中的槽液污染而导致槽液中的金属盐类杂离子的浓度过高,然后引起槽液的电导率升高,此刻会构成涂料的泳透率下降,咱们常见到电泳槽液在作业一段时刻往后泳透率相对下降就有这一类的原因,这种状况,可通过加强前处理清洗和超滤等办法进行槽液的保护。
4、助溶剂添加电泳涂料槽液中含有少数的助溶剂,它有助于电泳涂膜在堆积时聚结,然后构成均一的涂膜,因而,助溶剂的含量有必要坚持在一个正常的规划之内,过低的溶剂含量会构成堆积涂膜的黏度过大,不易聚结,易构成成膜过薄,流平差等现象,过高的溶剂含量,会大大下降涂膜的黏度,湿膜发粘,电导率增大,然后引起泳透率大大下降,漆膜疏松,功用下降。
假定正常的操作,而且槽液的更新期不太长的状况下,一般不需求添加助溶剂,假定槽液温度长时刻过高、或接连多日不电泳、漆液溶剂含量将会下降,坚持必定的溶剂含量是槽液安稳的一个重要政策,所以需恰当补加助溶剂。
5、循环体系循环体系首要效果有:防止颜填料堆积,使槽液温度均匀,消泡效果(消除电泳时工件外表发生的气泡,并将气泡移至副槽)。
循环体系需常常查看,以保证漆槽处于正常的作业状况。
6、漆液的立异需常常翻开电泳槽的过滤体系,以保证正常的漆膜外观。
如没有过滤体系,须守时翻槽,行将漆液悉数打出,清洗电泳槽,并将漆液从头过滤入槽。
7、极板和挂具的清洗在挂具运用进程中有必要保证其超卓的导电性,特别要留神常常查看阳极板(不锈钢板),并常常铲除其外表的污染物。
8、电泳漆的更新周期更新周期是电泳槽液的重要政策之一,它标明的是槽液中添加的涂料固含抵达槽液华夏有固含量时,所需求的时刻,阴极电泳涂料常常推荐槽液的更新时刻为2-8周,在此刻刻内,按正常的施工工艺运用,涂料作业正常,即便需求调整,也仅须较小的调整即可,而抵达8周以上,则需求对槽液进行较大的调整方可保证槽液正常的运用,这首要是因为槽液更新太慢,涂料长时刻在低固含下循环,有机物的老化,助溶剂的许多蒸发而引起,因而,在涂装线规划和涂装作业中,应尽或许的缩短更新周期。
六、阴极电泳漆膜的若干害处及其防治1、颗粒(疙瘩)在烘干后的电泳漆膜外表,存在有手感粗糙的(或肉眼可见的)较硬的粒子,称为颗粒。
发生原因:(1)槽液过滤不良,电泳槽液有堆积物、凝集物或其它异物。
(2)电泳后冲刷液脏或冲刷水中含漆浓度过高。
(3)烘干炉脏。
(4)磷化后的水洗不净,进入电泳槽的被涂物不洁净。
(5)涂装环境脏,磷化后和电泳后湿膜,晒干时受污染。
(6)后道冲刷水的碱性过高,使得冲刷不掉的漆液在水中溶解性差。
(7)槽液外表漆液活动不良,槽液外表的气泡过多。
(8)前处理未将金属外表的氧化颗粒铲除。
(9)漆膜低于必定厚度。
(10)漆槽中杂质离子浓度高,或有碱性杂质带入槽中,使得电泳树脂从水中分出。
防治办法:(1)尽或许防止尘土带入漆槽,加强电泳槽液的过滤。
悉数循环的漆液应悉数通过过滤设备,漆槽规划时,尽或许防止有“死角”,防止颜填料堆积。
(2)勤替换后道清洗液,清洗液最好有过滤,一起做个溢流口,削减清洗液外表的泡沫。
(3)守时拾掇烘干室和空气过滤器,查看平衡体系和漏气状况。
(4)加强磷化后的冲刷,要洗净浮在工件外表上的磷化残渣。
查看去离子水循环洗槽的过滤器是否阻塞,防止被涂物外表的二次污染。
(5)涂装环境应坚持清洁,磷化至电泳槽之间和电泳后沥干(进入烘干室前),应设间壁查看并消除周围空气的尘土源。
(6)后道清洗水的PH操控在中性。
(7)添加槽液外表流速。
(8)用打磨的办法铲除工件外表的氧化颗粒。
(9)漆膜厚度操控在要求规划之内。
(10)防止将碱性杂质和其它杂质离子带入电泳槽。
常常排放超滤液,去除槽中杂质离子。
2、陷穴(缩孔)由外界构成被涂物外表、磷化膜或电泳湿膜上附有尘土、油分等,或在漆膜中混有与电泳涂料不相溶的异物,它们成为陷穴中心,并构成烘干初期的流展才华不均衡而发生火山口状的凹坑,直径一般为0.5-3.0mm,不露底的称为陷穴、凹坑,露底的称为缩孔。
发生原因:(1)槽液中混入异物(油分、灰分),油漂浮在电泳槽液外表或乳化在槽液中。
(2)被涂物被异物污染(如尘土、运送链上坠落的润滑油、油性铁粉、与电泳漆不相溶油漆的尘土、吹干用的压缩空气中有油污,湿膜晒干时受环境污染)。
(3)前处理脱脂不良,磷化膜上有油污。
、(4)电泳后冲刷时清洗液中混入异物(油分、尘土)。
(5)烘干炉内不净或循环风内含油分。
(6)去离了水的水质欠好,使得补给涂料在水中溶解不良。
防治办法:(1)在槽液循环体系应设除油过滤袋,以除掉污物,及时去除滞于副槽液面的油污。
(2)坚持涂装环境洁净,运送链(规划要防止润滑油滴落)、挂具要清洁,所用压缩空气应无油,防止尘土、其它漆雾和油污落到被涂工件上。
不允许带油污和灰土的被涂工件进入电泳槽,工件在电泳前后与环境触摸段设置间壁。
(3)加强前处理的脱脂工序,保证磷化膜上无污染。
(4)坚持电泳后冲刷的水质,加强清洗液的过滤。
在冲刷后至烘干之间要设防通廊。
(5)坚持烘干室和循环热风的清洁。
(6)严峻操控稀释用的去离子质量,保证电泳漆溶解于水中,并通过滤入槽。
3、针孔在漆膜上发生针状小凹坑现象称为针孔,它与陷穴(麻坑)的区别是后者有凹坑,中心部一般有成为中心的异物,凹坑的周围是漆膜堆积凹起。
依据发生的原因,针孔有以下几种:(1)再溶解性针孔:泳涂的湿漆膜在电泳后冲刷不及时,涂膜再溶解而发生针孔。
(2)气体针孔:在电泳进程中,因为电解反响剧烈,发生气泡过多脱泡不良;槽液温度偏低或拌和不充沛,电泳时附在工件外表的气泡被漆膜包裹,在烘干进程中气泡割裂而呈现针孔。
(3)带电入槽阶梯式针孔:因为工件刚入槽时,槽液对工件外表湿润不良,此刻的电流又特别大,电解反响剧烈,使得槽液外表的气泡和作业外表发生的气泡被关闭在漆膜内,漆膜烘干后构成气泡针孔,易发生在被涂工件的下部。
(4)水洗针孔:湿膜电渗不行或冲刷水压过大。
(5)漆膜太薄。
(6)颜基比过高,漆膜烘干时活动性差,无法加添电泳时发生的针孔。
(7)被涂材料外表太疏松,烘干时露出孔隙。
(8)湿膜的溶剂含量过低,使得漆膜烘干时活动性差。
防冶办法:(1)工件经泳涂成膜后,离开槽液应立即用UF液(或纯水)冲刷,以消除再溶解性针孔。
(2)在电泳涂装时,应操控漆液中杂质离子的浓度,如超滤液电导过高,要排放超滤液,由此尽或许削减水的电解反响。
阳极罩除酸要正常,使得漆液PH值操控在必定规划之内。
磷化膜孔隙率高也易含气泡,磷化膜应尽或许细些。
此外还需保证漆液上下的流速,及在工艺规则的温度下电泳。
(3)为消除带电入槽的阶梯式针孔,要求槽液外表大于0.2m/s,以消除堆积泡沫,在带电入槽的通电办法出产时,防止运送链速度过低。
选用分段升压的办法,使得初步电压低,缓解初步水的电解反响。
(4)为消除水洗针孔,要保证满足的电泳时刻,湿膜溶剂含量不宜过高,使得漆膜的电渗性好,以取得细密的漆膜。
后冲刷的水压不行高于0.15mpa。
(5)保证漆膜的厚度。
(6)槽液的颜基比操控在正常规划内,颜基比高的电泳漆,漆膜尽或许做厚些。
(7)较疏松的材料电泳时,最好在电泳槽中预先湿润,烘干时,升温不宜过急。
(8)漆液的溶剂含量操控在必定的规划之内,保证电泳树脂在水中的溶解,一起行进烘干漆膜的活动性。
4、涂膜太薄泳涂后工件外表的单调漆膜厚度低于所选用电泳涂料技能条件或工艺规则的膜厚。