齿轮接触疲劳强度计算方法的探讨
齿面接触强度

齿面接触强度齿面接触强度是指齿轮或齿条在啮合过程中齿面的接触力大小。
齿面接触强度的大小直接影响着齿轮传动的可靠性和工作性能。
本文将从齿面接触强度的定义与计算、影响齿面接触强度的因素以及提高齿面接触强度的方法等方面进行探讨。
一、齿面接触强度的定义与计算齿面接触强度是指单位接触长度齿面所承受的力大小。
在齿轮传动中,齿面接触强度的计算一般采用接触力分析法或应力分析法。
接触力分析法通过计算齿轮啮合过程中齿面的接触力来确定齿面接触强度;应力分析法则是根据材料力学性能参数和齿轮几何参数来计算齿面的接触应力,进而确定齿面接触强度。
1. 齿轮的材料性能:齿轮材料的强度和硬度对齿面接触强度有着重要影响。
一般来说,齿轮材料的强度越高,齿面接触强度就越大。
2. 齿轮的几何参数:齿轮的模数、齿数、齿面宽度等几何参数也会影响齿面接触强度。
通常情况下,齿轮的模数越大,齿面接触强度越大;齿数越多,齿面接触强度越小。
3. 齿轮的啮合角:啮合角是指齿轮啮合时齿面接触线与齿轮轴线的夹角。
啮合角的大小会直接影响齿面接触强度,一般来说,啮合角越小,齿面接触强度越大。
4. 齿轮的润滑条件:润滑条件对齿面接触强度也有着重要影响。
良好的润滑条件可以降低齿轮的摩擦系数,从而提高齿面接触强度。
5. 齿轮的加工精度:齿轮的加工精度也会对齿面接触强度产生影响。
高精度的齿轮加工可以减小齿面接触强度的波动,提高齿轮传动的可靠性。
三、提高齿面接触强度的方法1. 选择合适的齿轮材料:根据具体工况要求选择合适的齿轮材料,提高齿轮的强度和硬度,从而提高齿面接触强度。
2. 优化齿轮的几何参数:根据传动要求合理选择齿轮的模数、齿数和齿面宽度等几何参数,使齿面接触强度达到最大。
3. 控制齿轮的啮合角:通过调整齿轮的啮合角,使其保持在合适的范围内,以提高齿面接触强度。
4. 保证良好的润滑条件:在齿轮传动中,确保良好的润滑条件,选择适当的润滑剂和润滑方式,以减小齿面摩擦,提高齿面接触强度。
齿面接触疲劳强度计算

齿面接触疲劳强度计算由齿面接触疲劳强度计算公式:d≥1、材料弹性系数ZE根据参考文献《机械设计》表8.5查取,材料都为铸铁。
查取ZE =188.0。
2、节点区域系数ZH根据参考文献《机械设计》图8.14查取,此系数反映了节点齿廓形状对接触应力的影响。
查取ZH=2.5。
3、重合度系数Zε根据参考文献《机械设计》图8.15查取,次系数是考虑重合度对齿面接触应力影响的系数。
查处Zε=0.975。
4、齿宽系数dφ,根据参考文献《机械设计》表8.6查取,dφ=0.6。
5、齿宽b根据计算公式b=dφ*d= 0.6×30=18mm。
6、齿轮传递的转矩T1根据计算公式T1= 2F1d1=2×1.2×9.8×50=1176N·mm ZN接触强度计算的寿命系数根据参考文献《机械设计》图8.29查取,ZN=1.15齿面接触疲劳极限minHσ根据参考文献《机械设计》图8.28查取,minHσ=750MPa9接触强度计算的安全系数SH根据参考文献《机械设计》表8.7查取,一般选取SH=1.0。
10许用接触应力[]H σ根据参考文献《机械设计》公式8.26min []/H H N H Z S σσ=代入数据[]H σ=862.5MPa 。
11、设计计算根据公式 其中数据由上可知,带入数据:d=30≥ =11.4所求得满足齿面接触疲劳强度要求。
则可取齿轮的标准分度圆直径d=30。
起重机用中硬齿面减速器的接触疲劳强度计算

其 中 ,F为 每 小 时 应 力循 环 次 数 ;z 为 零 件 总设 计
寿命 :载荷系数 由公式
k m = ∑ ( )
计算得出 ,也可根据材料 、机构载荷状态和计算指 数 查 取 ;齿 轮分 度 圆基本 切 向力 ‰ 由公 式
F t ] l l t  ̄ -
都 比较大 ,后几级齿轮模数基本都在 1 2 m m以上 ,
应 用 技
载能力计算方法强度校核 ,一般情况接触强度安全 系数 大 于 0 . 8即为 通 过 。而 实 际 上 ,针对 起 重 机 减
速 器 强 度 校 核 ,需 要 采 用 结 合 G B / T 3 8 1 1起 重 机 设 计规范和 G B / T 3 4 8 0 渐 开线 圆 柱 齿 轮 承 载 能 力 计 算 方 法 。与 一 般 的 G B / T 3 4 8 0 渐 开 线 圆 柱 齿 轮
4 与 起 重 机 中硬 齿 面 减 速 器 标 准 的 b 匕 较
承载能力计算方法相 比,该方法结合起重机 的工作
特 点对 G B / T 3 4 8 0 渐 开 线 圆 柱 齿 轮 承 载 能力 计 算
方法 中的使用系数和寿命 系数等做 了适 当的调整 ,
并 与 起重 机 工作 级 别相 结 合 ,确 定 了起 重机 用 渐 开
~
度都 比较低 , 所 以保证其齿面硬度对提高整体设备
的运 行 质量 有很 大 影 响 中硬 齿 面齿 轮 是 通过 调 质 处理 来 提 高齿 面硬 度 ,但 是 大模 数齿 轮 如 果采 用 整
V
‘
体 毛皮 调质 ,由于 受到 淬 透性 的限制 ,往 往在 齿 根 不 能获得 要求 的调质 组 织 和硬 度 ,因此 。当齿 轮模 数较 大 ( 模数大于 1 2 m m )时 ,应 采 用先 开 齿 再 调 质 的工艺 ,基本 的工 艺路 线 为 :毛 坯锻 造一 退 火一 粗 车~ 精 车一 粗 铣 齿 ( 开 齿 )一调 质 一精 铣 齿 。铸 造 起重 机 中一 般 的 中硬 齿 面起 升减 速 器 .承 载 能力
齿轮接触疲劳强度试验方法

齿轮接触疲劳强度试验方法(GB/T14229-93)1主题内容与适用范围本标准规定了测定渐开线圆柱齿轮接触疲劳强度的试验方法,以确定齿轮接触承载能力所需的基础数据。
本标准适用于钢、铸铁制造的渐开线圆柱齿轮由齿面点蚀损伤而失效的试验。
其它金属齿轮的接触疲劳强度试验可参照使用。
4试验方法确定齿轮接触疲劳强度应在齿轮试验机上进行试验齿轮的负荷运转试验。
当齿面出现接触疲劳失效或齿面应力循环次数达到规定的循环基数N。
而未失效时(以下简称“越出”),试验终止并获得齿面在试验应力下的一个寿命数据。
当试验齿轮及试验过程均无异常时,通常将该数据称为“试验点”。
根据不同的试验目的,选择小列不同的试验点的组合,经试验数据的统计处理,确定试验齿轮的接触疲劳特性曲线及接触疲劳极限应力。
4.1常规成组法常规成组法用于测定试验齿轮的可靠度-应力-寿命曲线(即R-S-N曲线),求出试验齿轮的接触疲劳极限应力。
试验时取4~5个应力级,每个应力级不少于5个试验点(不包括越出点)。
最高应力有中的各试验点的齿面应力循环次数不少于1×106。
最高应力级与次高应力级的应力间隔为总试验应力范围的40%~50%,随着应力的降低,应力间隔逐渐减少。
最低应力级至少有一个试验点越出。
4.2少试验点组合法少试验点组合法通常用于测定S-N曲线或仅测定极限应力。
试验时试验点总数为7~16个。
测定S-N曲线时,应力级为4~10个,每个应力级取1~4个试验点。
测定极限应力时可采用升降法。
采用正交法进行对比试验时,每个对比因素至少有3个试验点。
5试验条件及试验齿轮5.1齿轮接触疲劳强度试验按下述规定的试验条件和试验齿轮进行(对比试验的研究对象除外),上此可确定试验齿轮的接触疲劳极限应力σHlim。
5.1.1试验条件5.1.1.1试验机试验应使用功率流封闭式结构的齿轮试验机,试验机的性能校核见表A(补充件)。
试验机的中心距一般为90~150mm,试验齿轮线速度为8~16m/s。
齿轮接触疲劳强度计算方法的探讨
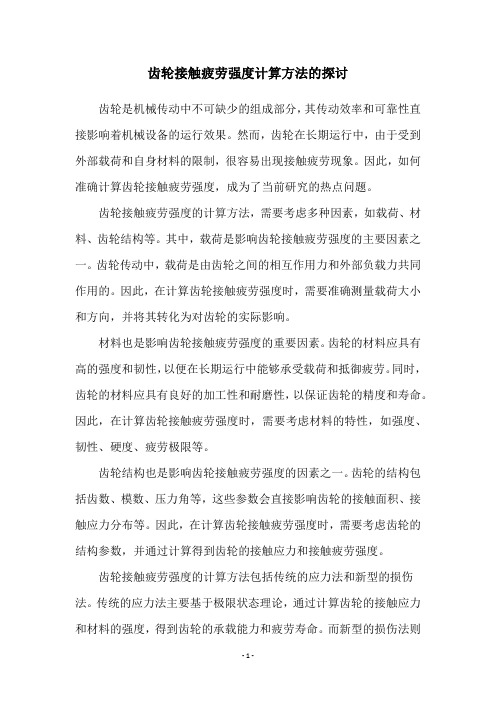
齿轮接触疲劳强度计算方法的探讨齿轮是机械传动中不可缺少的组成部分,其传动效率和可靠性直接影响着机械设备的运行效果。
然而,齿轮在长期运行中,由于受到外部载荷和自身材料的限制,很容易出现接触疲劳现象。
因此,如何准确计算齿轮接触疲劳强度,成为了当前研究的热点问题。
齿轮接触疲劳强度的计算方法,需要考虑多种因素,如载荷、材料、齿轮结构等。
其中,载荷是影响齿轮接触疲劳强度的主要因素之一。
齿轮传动中,载荷是由齿轮之间的相互作用力和外部负载力共同作用的。
因此,在计算齿轮接触疲劳强度时,需要准确测量载荷大小和方向,并将其转化为对齿轮的实际影响。
材料也是影响齿轮接触疲劳强度的重要因素。
齿轮的材料应具有高的强度和韧性,以便在长期运行中能够承受载荷和抵御疲劳。
同时,齿轮的材料应具有良好的加工性和耐磨性,以保证齿轮的精度和寿命。
因此,在计算齿轮接触疲劳强度时,需要考虑材料的特性,如强度、韧性、硬度、疲劳极限等。
齿轮结构也是影响齿轮接触疲劳强度的因素之一。
齿轮的结构包括齿数、模数、压力角等,这些参数会直接影响齿轮的接触面积、接触应力分布等。
因此,在计算齿轮接触疲劳强度时,需要考虑齿轮的结构参数,并通过计算得到齿轮的接触应力和接触疲劳强度。
齿轮接触疲劳强度的计算方法包括传统的应力法和新型的损伤法。
传统的应力法主要基于极限状态理论,通过计算齿轮的接触应力和材料的强度,得到齿轮的承载能力和疲劳寿命。
而新型的损伤法则是基于损伤力学理论,通过计算齿轮表面的损伤量和材料的损伤极限,得到齿轮的疲劳寿命。
相比传统的应力法,新型的损伤法可以更准确地预测齿轮的疲劳寿命,特别是在高速、高载荷和复杂工况下。
总之,齿轮接触疲劳强度的计算方法是一个复杂而又关键的问题。
在实际工程中,应根据具体情况选择合适的计算方法,并结合实验验证,以确保齿轮的可靠性和寿命。
齿面接触疲劳强度计算

齿面接触疲劳强度计算齿面接触疲劳强度计算一、轮齿受力分析一对直齿圆锥齿轮啮合传动时,如果不考虑摩擦力的影响,轮齿间的作用力可以近似简化为作用于齿宽中点节线的集中载荷f n,其方向垂直于工作齿面。
如图6-14所示主动锥齿轮的受力情况,轮齿间的法向作用力f n可分解为三个互相垂直的分力:圆周力f t1、径向力f r1和轴向力f a1。
各力的大小为:=(6-15)式中:d m1为主动锥齿轮分度圆锥上齿宽中点处的直径,也称分度圆锥的平均直径,可根据锥距r、齿宽b和分度圆直径d1确定,即:d m1=(1-0.5)d1(6-16)式中:称齿宽系数,通常取=0.25~0.35圆周力的方向在主动轮上与回转方向相反,在从动轮上与回转方向相同;径向力的方向分别指向各自的轮心;轴向力的方向分别指向大端。
根据作用力与反作用力的原理得主、从动轮上三个分力之间的关系:f t1 =-f t2、f r1=-f a2、f a1= -f r2,负号表示方向相反。
二、齿面接触疲劳强度计算直齿圆锥齿轮的失效形式及强度计算的依据与直齿圆柱齿轮基本相同,可近似按齿宽中点的一对当量直齿圆柱齿轮来考虑。
将当量齿轮有关参数代入直齿圆柱齿轮齿面接触疲劳强度计算公式,则得圆锥齿轮齿面接触疲劳强度的计算公式分别为≤(6-17)d1 ≥(6-18)式中:z e为齿轮材料弹性系数,见表6-5;z h为节点啮合系数,标准齿轮正确安装时z h =2 .5;为许用应力,确定方法与直齿圆柱齿轮相同。
三、齿根弯曲疲劳强度计算将当量齿轮有关参数代入直齿圆柱齿轮齿根弯曲疲劳强度计算公式,则得圆锥齿轮齿根弯曲疲劳强度的计算公式为≤(6-19)m ≥ (6-20)式中:为齿形系数,应根据当量齿数z v(z v=z/cosδ)由图6-8查得;[]为许用弯曲应力,确定方法与直齿圆柱齿轮相同。
20CrMoH齿轮接触疲劳强度研究
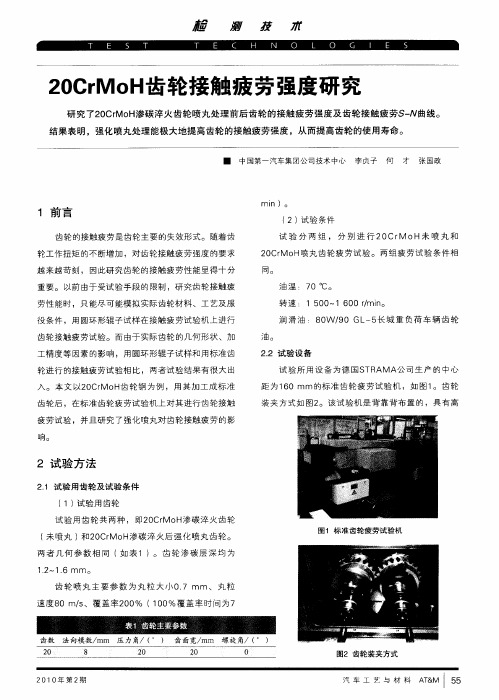
由表 3 可知 , 当齿 轮 工作 扭 矩 增 加 到 2 3 0 Nm 0
时齿 轮 断齿 ,即在高 应 力 区没等 发生 齿轮 接触 疲 劳 失 效 就 先发 生齿 轮弯 曲疲 劳 。用升 降法 求 出齿 轮接 触疲 用 升 降 法 求 出喷 丸 齿 轮 接 触 疲 劳 强 度 为2 0 9 6
获 得在试验 应 力下 的1 个寿命 数据 ,即1 个试 验点 。完
成一 条齿 轮 接触 疲劳S一 ~曲线 ,至 少应 选择3 应 力 个 水平 ,最高 应力 级中应 力循环 次数 不少于 1×1 。 , O次 应力增量 一般取 5 %~1 % ,每个应 力水平 取2 4 0 ~ 个试
H C 残余压应=为9 0MP。2 cM H R, ! 8 a 0 r o 齿轮材料 ]
( 试 验 用齿 轮 1)
试 验 用齿 轮共 两 种 ,即2 Cr H渗碳 淬 火 齿 轮 0 Mo
( 喷丸 ) D 0 H 未  ̄ 2 C Mo 渗碳 淬 火 后 强 化 喷丸 齿 轮 。 r
两 者 几 何 参 数 相 同 ( 表 1)。 齿 轮 渗 碳 层 深 均 为 如
12-1 6 m m 。 .
■
中 国第一 汽车 集 团公 司技术 中 心 李 贞子 何 才 张 国政
mi n)。
1 前 言
齿 轮 的接触 疲劳 是齿 轮主 要 的失 效形 式。 随着 齿 轮工作 扭矩 的不断 增加 ,对齿 轮接 触疲 劳 强度 的要 求 越 来越 苛 刻 ,因此研 究 齿 轮的 接触 疲劳 性 能显 得十 分
裣
渤 技 7 l t
2 C Mo 0 r H齿轮接触 疲劳 强度研究
研 究 了2 Cr H 碳淬 火齿 轮喷 丸处理 前后 齿轮 的接触疲 劳 强度及齿 轮接触 疲 劳S一\ 0 Mo 渗 /曲线。 / 结果表 明 ,强化喷丸处理 能极大 地提高齿轮 的接触疲劳 强度 ,从 而提高齿轮 的使用寿命 。
齿轮接触疲劳强度计算方法的探讨
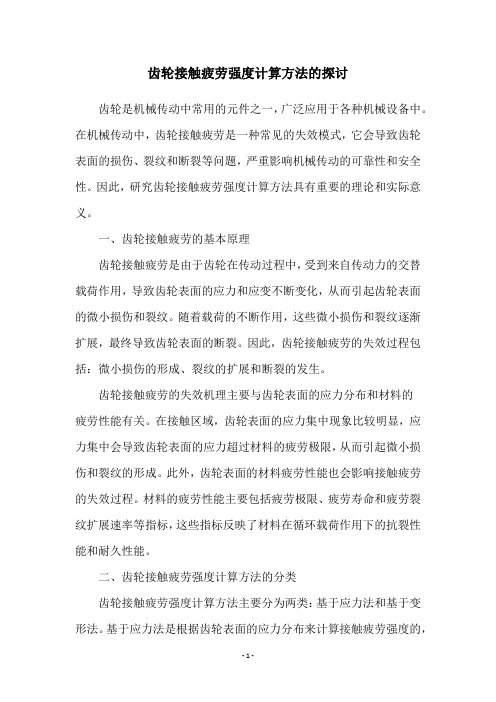
齿轮接触疲劳强度计算方法的探讨齿轮是机械传动中常用的元件之一,广泛应用于各种机械设备中。
在机械传动中,齿轮接触疲劳是一种常见的失效模式,它会导致齿轮表面的损伤、裂纹和断裂等问题,严重影响机械传动的可靠性和安全性。
因此,研究齿轮接触疲劳强度计算方法具有重要的理论和实际意义。
一、齿轮接触疲劳的基本原理齿轮接触疲劳是由于齿轮在传动过程中,受到来自传动力的交替载荷作用,导致齿轮表面的应力和应变不断变化,从而引起齿轮表面的微小损伤和裂纹。
随着载荷的不断作用,这些微小损伤和裂纹逐渐扩展,最终导致齿轮表面的断裂。
因此,齿轮接触疲劳的失效过程包括:微小损伤的形成、裂纹的扩展和断裂的发生。
齿轮接触疲劳的失效机理主要与齿轮表面的应力分布和材料的疲劳性能有关。
在接触区域,齿轮表面的应力集中现象比较明显,应力集中会导致齿轮表面的应力超过材料的疲劳极限,从而引起微小损伤和裂纹的形成。
此外,齿轮表面的材料疲劳性能也会影响接触疲劳的失效过程。
材料的疲劳性能主要包括疲劳极限、疲劳寿命和疲劳裂纹扩展速率等指标,这些指标反映了材料在循环载荷作用下的抗裂性能和耐久性能。
二、齿轮接触疲劳强度计算方法的分类齿轮接触疲劳强度计算方法主要分为两类:基于应力法和基于变形法。
基于应力法是根据齿轮表面的应力分布来计算接触疲劳强度的,该方法一般采用极限应力理论或弹性应力集中理论来计算齿轮表面的应力分布。
基于变形法是根据齿轮表面的变形分布来计算接触疲劳强度的,该方法一般采用极限变形理论或弹性变形集中理论来计算齿轮表面的变形分布。
基于应力法的齿轮接触疲劳强度计算方法主要包括极限应力法、应力集中法和有限元法等。
其中,极限应力法是一种经典的计算方法,它基于极限应力理论,将齿轮表面的应力与材料的疲劳极限进行比较,从而确定齿轮的疲劳寿命。
应力集中法是一种基于弹性应力集中理论的计算方法,它通过计算齿轮表面的应力集中系数,来确定齿轮表面的应力分布和疲劳寿命。
有限元法是一种基于数值模拟的计算方法,它通过建立齿轮的有限元模型,计算齿轮表面的应力分布和疲劳寿命。
一、齿面接触疲劳强度计算.
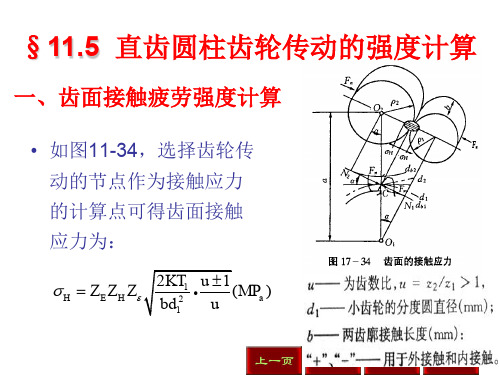
将 d
b d1
,d1=mZ1代入上式,得弯曲疲劳强度设寸公式
设计公式为:m
3
2KT1YFSY
d z12 F
mm
YFS-复合齿形系数,值可由图11-9 查取,Yε下
式计算
0.75
Y 0.25
对于长期工作的齿轮[σF] 可按下式 计算:
F
Y F lim x
§11.5 直齿圆柱齿轮传动的强度计算
一、齿面接触疲劳强度计算
• 如图11-34,选择齿轮传 动的节点作为接触应力 的计算点可得齿面接触 应力为:
H ZEZH Z
2KT1 bd12
u
u
1
(MPa
)
其中: ZE——材料弹性系数见表11-5
表11-5 材料弹性系数ZE
ZH—— 节点区域系数,见图11-8
SF
MPa
•σFlim---齿根弯曲疲劳极限应力,其值按图1137查取,若轮齿的工作条件是双向受载,则应将 图值σFlim乘以0.7
• SFmin---齿面弯曲强度的最小安全系数,一 般取SFmin =1,齿轮损坏会引起严重后果的 取SFmin =1.5,也可查表11-6
Yx——尺寸系数,考虑齿轮尺寸对材料强度的影响而 引人的系数。其值由图11-12查取;
表11-7 圆柱齿轮的齿宽系数
注:1. 大﹑小齿轮均为硬齿面时ψ d取表中偏下限的数值;均为软齿面时或仅大齿轮为软 齿面时,ψd取表中偏上限数值;
2. 直齿园柱齿轮宜选较小值,斜齿可取较大值; 3. 载荷稳定﹑轴刚性较大时取大值,否则取小值。
标准圆柱齿轮ZH=2.5
图11-8 节点区域系数ZH(an=20°)
齿面接触疲劳强度计算

齿面接触疲劳强度计算
1.确定载荷:首先需要确定齿轮所承受的载荷。
这包括齿轮的扭矩或
力矢量、运动速度、传动比等。
这些参数将决定齿轮齿面的接触压力和接
触应力。
2.计算接触应力:接触应力是齿轮齿面接触区域的应力状态,是齿轮
疲劳强度计算的基础。
接触应力可以通过使用赛德勒公式或哈密顿公式进
行计算。
这些公式基于齿轮几何参数和载荷数据来计算接触应力分布。
3.确定表面强化系数:齿轮表面强化是提高齿轮疲劳寿命的一种方法。
通过对齿轮进行渗碳、淬火、磨削等工艺来改善其表面性能,并增加其疲
劳寿命。
表面强化系数是指表面强化对齿轮疲劳寿命的贡献程度,一般通
过实验得出。
4.计算齿面接触疲劳强度:在确定了接触应力和表面强化系数后,可
以使用维克托法则或SN曲线法进行齿面接触疲劳强度计算。
维克托法则
是通过将接触应力和齿轮材料的疲劳极限强度相比较来判断齿轮的寿命。
SN曲线法则是通过实验获得的SN曲线数据来计算疲劳强度。
5.寿命评估:根据齿面接触疲劳强度计算的结果,可以评估齿轮的寿命。
如果计算的疲劳强度大于齿轮的设计要求,那么齿轮在设计条件下应
具备较长的寿命。
如果计算的疲劳强度小于齿轮的设计要求,那么需要重
新调节设计参数,或者选择具有更高疲劳强度的齿轮材料。
综上所述,齿面接触疲劳强度计算是一项复杂的工程任务,需要综合
考虑齿轮的载荷、接触应力、材料性能等因素。
在实际工程中,通常需要
使用专业的有限元分析软件来进行计算,以获得准确的结果,并确保齿轮
的寿命和可靠性。
齿轮接触疲劳强度计算方法的探讨
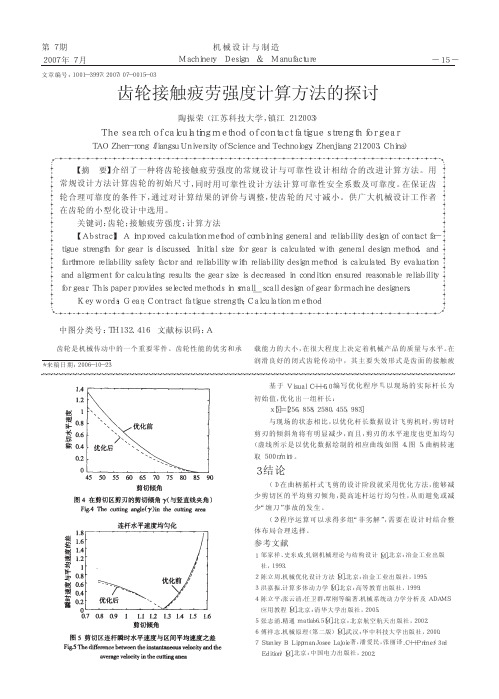
1( 见文献 ) [1]、[4] 选定。
对照标准正态分布函数表, 查得齿轮接触疲劳强度的计算
表 1 可靠度及最小安全系数 SHmin Ta b.1 Re lia blity a nd minimum s a fe ty fa ctor SHmin
可靠性要求
可靠度
SHmin
≥0.9999
1.50
高可靠性
247b10133mm32齿轮的可靠性计算安全系数shc等有关数据代入5式得齿轮可靠性计算安全系数的值即33齿轮可靠度计算等数据代入6式得齿轮可靠度系数的数值即对照标准正态分布函数表查得齿轮接触疲劳强度的计算可靠度998634计算评估341计算安全系数与可靠度的许用值根据使用要求该齿轮传动无特殊要求为一般可靠性要求故对照表1选取r9986shmin10342可靠度及安全系数的验算由计算值与许用值进行比较则上述计算结果偏于安全
( 6)
式中: $r、$s — ——分别为齿轮接触疲劳强度和应力的均值 !r、!s — ——分别为齿轮接触疲劳强度和应力的标准差 齿轮接触疲劳强度的均值 $r 用下式计算, 即
( 2)
齿轮接触疲劳强度计算式, 即小齿轮分度圆直径 d1 的计算 式, 由条件式 !Hmax![!]H 推导求得。将( 2) 式等号右侧计算式代 入不等式, 并经整理得
( 3) 通 过 常 规 计 算 , 分 别 求 出 齿 轮 中 心 距 ", 齿 数 Z1、Z2, 模 数 mn, 螺旋角 #, 齿宽 b1、b2 及分度圆直径 d1、d2 等。在此基础上, 再
上式中的齿轮接触疲劳强度变异系数一般取 Cr =0.06。 齿轮接触疲劳强度标准差按 !r = Cr $r 公式计算之。齿轮接 触疲劳应力的标准差 !s 的计算见文献[2]。 齿 轮 接 触 疲 劳 强 度 可 靠 度 RH 数 值 由( 6) 式 求 得 的 可 靠 度 系数 Z 值, 在文献[3]的标准正态分布函数表中查得。 按可靠性设计准则, 齿轮接触疲劳强度的计算可靠度应大 于或等于许用可靠度, 即 RH =[R]H
齿面接触强度计算
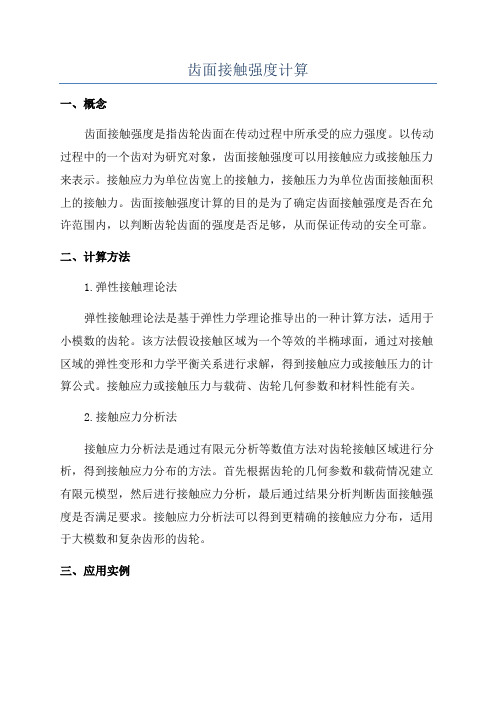
齿面接触强度计算一、概念齿面接触强度是指齿轮齿面在传动过程中所承受的应力强度。
以传动过程中的一个齿对为研究对象,齿面接触强度可以用接触应力或接触压力来表示。
接触应力为单位齿宽上的接触力,接触压力为单位齿面接触面积上的接触力。
齿面接触强度计算的目的是为了确定齿面接触强度是否在允许范围内,以判断齿轮齿面的强度是否足够,从而保证传动的安全可靠。
二、计算方法1.弹性接触理论法弹性接触理论法是基于弹性力学理论推导出的一种计算方法,适用于小模数的齿轮。
该方法假设接触区域为一个等效的半椭球面,通过对接触区域的弹性变形和力学平衡关系进行求解,得到接触应力或接触压力的计算公式。
接触应力或接触压力与载荷、齿轮几何参数和材料性能有关。
2.接触应力分析法接触应力分析法是通过有限元分析等数值方法对齿轮接触区域进行分析,得到接触应力分布的方法。
首先根据齿轮的几何参数和载荷情况建立有限元模型,然后进行接触应力分析,最后通过结果分析判断齿面接触强度是否满足要求。
接触应力分析法可以得到更精确的接触应力分布,适用于大模数和复杂齿形的齿轮。
三、应用实例以一对调整齿轮为例,齿轮参数如下:模数m=2mm,齿数z1=20,z2=30,齿轮宽度b=40mm,法向载荷Ft=1000N,转速n=1000r/min。
根据给定参数,可以采用弹性接触理论法或接触应力分析法计算齿面接触强度。
采用弹性接触理论法,根据经验公式得到接触应力σt=1.2√(Ft/(m·b))=48MPa。
根据齿面接触强度的规定,该齿轮的接触应力在允许范围内,齿面接触强度满足要求。
采用接触应力分析法,建立有限元模型,进行接触应力分析,得到齿面接触应力分布。
通过结果分析,判断齿轮齿面的接触强度是否满足要求。
综上所述,齿面接触强度的计算是齿轮传动设计中的重要环节。
齿面接触强度的计算方法有弹性接触理论法和接触应力分析法。
通过合适的计算方法和实例分析,可以判断齿面接触强度是否满足要求,保证齿轮传动的安全可靠运行。
齿轮传动系统设计中的疲劳强度分析

齿轮传动系统设计中的疲劳强度分析齿轮传动系统是机械运动控制系统中的重要组成部分,广泛应用于汽车、航空、船舶、军工等领域。
在设计齿轮传动系统时,疲劳强度分析是至关重要的一步,因为齿轮在长期使用过程中会承受不同程度的疲劳损伤,从而导致传动系统失效。
本文将从齿轮材料选用、载荷分析、疲劳寿命预估等多个方面探讨齿轮传动系统设计中的疲劳强度分析。
一、齿轮材料选用在齿轮传动系统设计中,首先要确定齿轮的材料。
尤其对于高负荷、高速传动的齿轮来说,材料的选用更显得至关重要。
传统齿轮材料包括低碳钢、中碳钢、铸铁等,但这些材料在高负载、高速传动的情况下容易产生疲劳裂纹,进而导致齿轮失效。
针对这一问题,现代齿轮传动系统常采用效应材料,如合金钢、超高强钢等。
这类材料不仅具有高拉伸强度和高硬度,而且还能够增加齿轮的韧性和耐久性,从而提高齿轮的疲劳强度。
此外,在选用材料时,也需要结合实际应用场景和经济成本综合考虑。
二、载荷分析在考虑齿轮的疲劳强度时,载荷分析是一个关键的环节。
不同的载荷会对齿轮的疲劳强度造成不同影响,因此需要根据具体应用情况设计不同的载荷条件。
一般而言,载荷分为静载荷和动载荷两种,其中静载荷是指传动系统在静止状态下的承载能力,而动载荷则是指传动系统在运动状态下受到的载荷。
在实际应用中,载荷往往是非常复杂的。
对于齿轮传动系统来说,载荷来源多种多样,如机器本身的振动、不同部件之间的相互作用、外部环境的影响等。
因此,需要对多种载荷进行分析,确保齿轮的设计满足最糟糕的载荷情况下的强度要求。
三、疲劳寿命预估齿轮的疲劳寿命是指在一定载荷条件下,齿轮出现第一个裂纹的时间。
疲劳寿命的长短直接影响齿轮传动系统的可靠性和安全性。
因此,在齿轮传动系统设计中,预估疲劳寿命非常重要。
常用的疲劳寿命预估方法包括双应力范围法、极限载荷法、等效应力法等。
这些方法分别通过不同的方式计算疲劳寿命,具有各自的优缺点。
其中,等效应力法是目前应用最广泛的方法,它将不同载荷情况下的应力转化为等效应力,进而推导出疲劳寿命。
齿轮传动的强度设计方案计算)
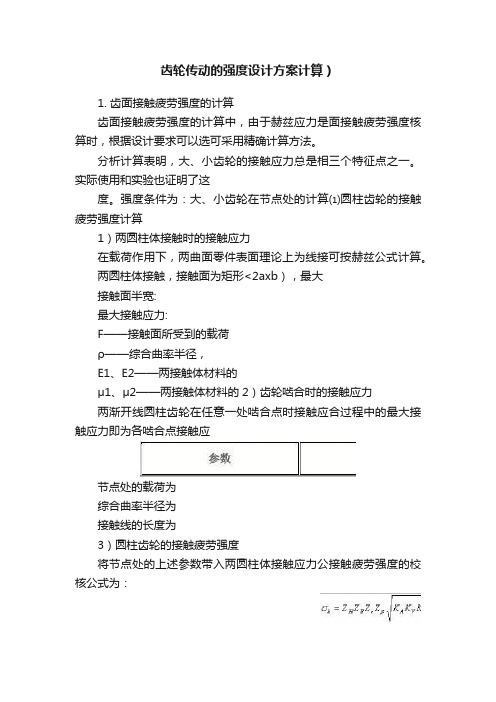
齿轮传动的强度设计方案计算)1. 齿面接触疲劳强度的计算齿面接触疲劳强度的计算中,由于赫兹应力是面接触疲劳强度核算时,根据设计要求可以选可采用精确计算方法。
分析计算表明,大、小齿轮的接触应力总是相三个特征点之一。
实际使用和实验也证明了这度。
强度条件为:大、小齿轮在节点处的计算⑴圆柱齿轮的接触疲劳强度计算1)两圆柱体接触时的接触应力在载荷作用下,两曲面零件表面理论上为线接可按赫兹公式计算。
两圆柱体接触,接触面为矩形<2axb),最大接触面半宽:最大接触应力:F——接触面所受到的载荷ρ——综合曲率半径,E1、E2——两接触体材料的μ1、μ2——两接触体材料的2)齿轮啮合时的接触应力两渐开线圆柱齿轮在任意一处啮合点时接触应合过程中的最大接触应力即为各啮合点接触应节点处的载荷为综合曲率半径为接触线的长度为3)圆柱齿轮的接触疲劳强度将节点处的上述参数带入两圆柱体接触应力公接触疲劳强度的校核公式为:KA——使用系数KV——动载荷系数KHβ——接触强度计算的齿KHα——接触强度计算的齿Ft——端面内分度圆上的名T1——端面内分度圆上的名d1——小齿轮分度圆直径,b ——工作齿宽,mm,指u ——齿数比;ψd——齿宽系数,指齿宽构尺寸,降低圆周速度,但ZH——节点区域系数,用于ZE——弹性系数,用于修正Zε——重合度系数,用于考Zε可按下式计算:直齿轮:斜齿轮:当式中:——端面重合度;——纵向重Zβ——螺旋角系数,用于考σHp——许用接触应力,N(2> 直齿锥齿轮的接触疲劳强度计算公式将相互啮合的一对直齿锥齿轮转化为相应的当对于轴交角为90°的直齿锥齿轮传动,将齿宽Zk——接触强度计算的锥齿Fmt——齿宽中点分度圆上dm1——小轮齿宽中点分度beH——接触强度计算的有将当量直齿轮的参数转化为锥齿轮的大端参数直齿锥齿轮接触强度校核公式:设计公式:d1——小齿轮大端分度圆直KHβ——接触强度计算的齿2. 齿根弯曲疲劳强度的计算齿根弯曲疲劳强度的计算中,作为判据的齿根量)来确定。
解决设计齿轮传动时齿面接触疲劳强度不够的问题

解决方案
• 具体解决办法: • 使用弹性系数较低材料的齿轮,比如说灰铸铁齿 轮 • 增大主动轮分度圆直径,使用直径更大的齿轮来 设计该齿轮传动
直齿面接触强度的计算
• 参数取值说明
影接直齿轮齿面接触强度的因素分析
• 从赫兹接触应力公式的校核式中可以得出影响齿 面接触强度的因素主要有: • ZE---弹性系数 • d1---主动轮分度圆直径 • µ---大齿轮齿数Z2与小齿轮齿数Z1之比。
解决方案
• 齿面接触疲劳强度不够则表示许用接触应力过小, 这时必须降低接触应力,具体易于改变的变量可 以是: • 降低弹性系数ZE • 增大主动轮分度圆直径d1
解决设计齿轮传动时齿面接 触疲劳强度不够的问题
原因
• ቤተ መጻሕፍቲ ባይዱ面接触疲劳强度不够造成齿轮失效
具体分析
• 直齿轮齿面接触强度的计算 • 影接直齿轮齿面接触强度的因素分析 • 解决方案
直齿面接触强度的计算
• 赫兹接触应力公式
H
1 Fn L 1 12 1 2 2 E E 1 2
H
直齿面接触强度的计算
整理得:
校核式: P
H Z E Z H Z
设计式:
2 KT1 1 bd12
H
H
2 KT1 1 Z E Z H Z d1 d H
3
2
硬齿面齿轮层深接触疲劳强度计算

硬齿面齿轮层深接触疲劳强度计算
硬齿面齿轮层深接触疲劳强度是指齿面经受疲劳载荷下的承载能力。
在齿轮传动中,由于工作负荷的不均匀和齿面的微小缺陷,容易产生接触疲劳。
计算硬齿面齿轮层深接触疲劳强度的关键是确定应力循环,然后应用疲劳强度理论进行计算。
1. 接触应力计算:首先需要计算齿轮的接触应力,根据齿轮传动的几何参数和工作条件,可以使用Hertz接触理论来计算接触应力。
接触应力是计算接触疲劳强度的基础。
2.疲劳强度计算:根据齿轮材料的疲劳特性,可以使用疲劳强度公式来计算齿轮的疲劳强度。
常用的疲劳强度公式有极限弯曲应力法、维豪勒法、褶皱理论等。
选择合适的疲劳强度公式时需要考虑齿轮的几何结构、材料特性和工作条件。
3.接触疲劳强度计算:接触疲劳是由于齿面微小缺陷引起的,其计算需要考虑齿形误差、齿面粗糙度等因素。
根据疲劳强度理论,可以建立接触疲劳强度公式,计算齿轮的接触疲劳强度。
常用的接触疲劳强度公式有等效应力法、极限曲率法等。
4.安全系数确定:在计算齿轮的层深接触疲劳强度时,需要确定安全系数。
安全系数一般取决于齿轮传动的可靠性要求、工作条件、齿轮材料等因素。
较大的安全系数可以提高齿轮的可靠性,但也会增加成本。
总之,硬齿面齿轮层深接触疲劳强度的计算是一个复杂的过程,需要综合考虑齿轮的几何结构、材料特性和工作条件等因素。
通过合理的计算和设计,可以提高齿轮的疲劳强度,保证齿轮传动的可靠性和寿命。
齿轮接触疲劳强度计算中的节点区域系数

齿轮接触疲劳强度计算中的节点区域系数【齿轮接触疲劳强度计算中的节点区域系数】【作者:你的文章写手】一、引言在齿轮机械设计中,齿轮接触疲劳强度是一个至关重要的参数。
节点区域系数,作为齿轮接触疲劳强度计算的重要指标之一,对于齿轮传动的性能及寿命具有重要影响。
本文将深入探讨节点区域系数的计算方法、影响因素和应用场景,并分享对该主题的个人观点和理解。
二、节点区域系数的计算方法节点区域系数是描述齿轮接触疲劳强度的重要参数之一。
计算节点区域系数需要考虑多个因素,包括齿轮的几何形状、材料力学性能以及工作条件等。
一般情况下,节点区域系数可以通过有限元分析、模拟计算或经验公式来获得。
1. 有限元分析方法有限元分析方法是一种常用的计算节点区域系数的手段。
通过将齿轮模型建立为有限元模型,利用计算机仿真软件对齿轮在工作条件下的应力分布进行分析,可以获得节点区域的应力集中情况。
进一步,通过分析应力集中较为严重的节点区域,可以得到节点区域系数的数值。
2. 模拟计算方法模拟计算方法是通过对齿轮接触问题进行数值模拟,结合实验验证,对节点区域系数进行计算。
该方法需要建立详细的数学模型,考虑齿轮的几何形状、材料力学性能以及工作条件等因素,通过求解接触区域的应力、应变分布,进而计算节点区域系数。
3. 经验公式经验公式是对节点区域系数进行近似计算的方法,可作为快速估算的依据。
经验公式通常基于大量实验数据和理论分析,考虑了齿轮的几何形状、材料性能以及工作条件等因素,通过简化计算方法,得到节点区域系数的估算值。
三、影响节点区域系数的因素节点区域系数的计算值不仅受到计算方法的选择和精度的影响,还受到多个因素的综合影响。
以下是一些影响节点区域系数的重要因素:1. 齿轮的几何形状齿轮的齿形、齿数、齿宽等几何参数对节点区域系数的计算具有重要影响。
较小的齿数和大的齿宽通常会导致较大的节点区域系数,从而影响齿轮的接触疲劳强度。
2. 齿轮材料的力学性能齿轮材料的硬度、弹性模量和延展性等力学性能对节点区域系数的计算也具有重要影响。
机械设计基础-第五版直齿圆柱齿轮齿面接触疲劳强度计算
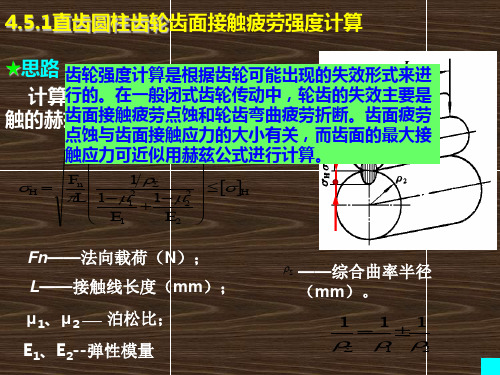
★思路:齿轮强度计算是根据齿轮可能出现的失效形式来L 进
计算行模的型。:在两一平般行闭式圆齿柱轮体传相动接中,轮齿的失效主要是
触的赫兹齿面(接18触8疲1劳年点提蚀出和)轮公齿式弯曲:疲劳折断。齿面疲劳
点蚀与齿面接触应力的大小有关,而齿面的最大接
H
触应 力可近似用赫兹公式进行计算。
2K1T u1 b1 2 d u
ZE
1
(112 122 )
E1
E2
ZH
2
sincos
ZE-弹性影响系数, 表4-6
ZH-区域系数,图4-14(标准直齿轮时α=20°, ZH =2.5)
校核计算 式为:
HZEZHZ 2bK1 d 21T uu 1H
令ψd=b/d1代入校核计算式,并整理得设计计算式:
Fn
1
L
1
12
1 22
H
E1
E2
Fn——法向载荷(N); L——接触线长度(mm); μ1、μ2 —— 泊松比; E1、E2--弹性模量
——综合曲率半径 (mm)。
1 11
1 2
实◆应验用表到明齿:轮齿中根(1部90分8年靠
设计计算 式为:
d13
2 Kd1Tuu 1ZE ZH H Z
2
几点说明:
① H1H2
② 设计式中代入的是min{[σH]1,[σH]2}, 计算偏于安全。
③齿轮传动的接触疲劳强度取决于中心距或齿轮分度 圆直径。 ④ Φd 。 当Φd过大时,会使轮齿受力不均。为便于装 配和调整,b1=b2+5~10mm。
若设计新的齿轮传动时,尺寸均未知,分度圆直径 的初步计算公式:
- 1、下载文档前请自行甄别文档内容的完整性,平台不提供额外的编辑、内容补充、找答案等附加服务。
- 2、"仅部分预览"的文档,不可在线预览部分如存在完整性等问题,可反馈申请退款(可完整预览的文档不适用该条件!)。
- 3、如文档侵犯您的权益,请联系客服反馈,我们会尽快为您处理(人工客服工作时间:9:00-18:30)。
1.1 齿面形成点蚀的原因及其对策
点蚀是一种在节线附近靠近齿根部分齿面上出现的小块剥 落而形成的麻点现象。齿面点蚀后会影响齿轮传动的平稳性, 引 起振动和噪音, 甚至会失去正常的工作。
很多学者研究表明, 形成点蚀有许多原因。其中主要原因 是, 其交变接触应力的最大值超过齿轮材料的接触疲劳极限而 形成的点蚀。其次是齿面润滑油渗入裂纹的胀挤作用, 加速了裂 纹的扩展而形成点蚀。油的粘度愈小, 愈易渗入裂纹, 点蚀扩展 愈快。此外, 点蚀还与轮齿的工艺表面状态有关。由于表面出现 裂纹, 裂缝和粗糙度等应力集中源, 使接触应力增大, 也易引起 点蚀的发生。
2.1 齿轮可靠性计算安全系数的计算式
在这里, 我们将齿轮可靠性计算安全系数定义为齿轮材料 失效概率为 0.01 的接触疲劳极限 r0.01 与齿轮失效 概 率 为 0.5 的 接触应力的平均值( 均值 $s) 之比, 即
( 4)
考虑到齿轮接触寿命系数 ZN 对接触疲劳强度的影响, 则 r0.01 = !Hlim·ZN 式中: !Hlim — ——齿轮材料失效概率为 0.01 的接触疲劳极限。 常规计算接触疲劳应力的失效概率为 0.50, 可视为平均接 触应力, 即
!!!!!!!!!!!!!!!!"
!!!!!!!!!!!!!!!!"
第7期 2007 年 7 月
机械设计与制造 Machinery Design & Manufacture
文章编号: 1001- 3997( 2007) 07- 0015- 03
Hale Waihona Puke 齿轮接触疲劳强度计算方法的探讨
- 15 -
陶振荣( 江苏科技大学, 镇江 212003)
剪切倾角
图 5 剪切区连杆瞬时水平速度与区间平均速度之差 Fig.5 The difference between the instantaneous velocity and the
average velocity in the cutting anea
( 2) 程序运算可以求得多组“非劣解”, 需要在设计时结合整 体布局合理选择。 参考文献 1 邹家祥、史东成.轧钢机械理论与结构设计[M].北京: 冶金工业出版
1( 见文献 ) [1]、[4] 选定。
对照标准正态分布函数表, 查得齿轮接触疲劳强度的计算
表 1 可靠度及最小安全系数 SHmin Ta b.1 Re lia blity a nd minimum s a fe ty fa ctor SHmin
可靠性要求
可靠度
SHmin
≥0.9999
1.50
高可靠性
2.3 齿轮接触疲劳强度计算的评估与设计调整
通过齿轮接触疲劳强度计算, 确定了齿轮的尺寸与参数, 求
No. 7 Jul.2007
机械设计与制造
- 17 -
得了齿轮可靠性计算安全系数及可靠度数值后, 要对其设计的 安全系数的值, 即
可靠性与合理性作一评估, 以确保齿轮在满足其可靠度的条件
下具有合理的齿轮尺寸, 使其做到恰到好处以及达到进一步减
2 齿轮接触疲劳强度的可靠性计算
在可靠性设计中, 我们将齿轮的强度、应力和几何尺寸等均 作为服从正态分布的随机变量来处理。
在这里, 我们列出齿轮可靠性计算安全系数和可靠度的计 算式, 并将可靠性计算安全系数与可靠度作为齿轮接触疲劳强 度计算的设计指标。用这两个指标来设计齿轮, 更符合与接近实 际情况。
≥0.999
1.25
一般可靠性
≥0.99
1.00
低可靠性
≥0.90
0.85
可靠度 RH =99.86%
3.4 计算评估 3.4.1 计算安全系数与可靠度的许用值
根据使用要求, 该齿轮传动无特殊要求, 为一般可靠性要 求, 故对照表 1, 选取[R]H =99.86%, SHmin =1.0。
3.4.2 可靠度及安全系数的验算
( 6)
式中: $r、$s — ——分别为齿轮接触疲劳强度和应力的均值 !r、!s — ——分别为齿轮接触疲劳强度和应力的标准差 齿轮接触疲劳强度的均值 $r 用下式计算, 即
( 2)
齿轮接触疲劳强度计算式, 即小齿轮分度圆直径 d1 的计算 式, 由条件式 !Hmax![!]H 推导求得。将( 2) 式等号右侧计算式代 入不等式, 并经整理得
The s e a rch of ca lcula ting me thod of conta ct fa tigue s tre ngth for ge a r
TAO Zhen- rong (Jiangsu University of Science and Technology, Zhenjiang 212003, China) !!!!!!!!!!!!!!!!!!!!!!!!!!!!!!!!!!!!!!!!!!!"
将 r0.01 及 $s 等号右边的计算式代入( 4) 式, 得可靠性计算安 全系数计算式
( 5)
根据可靠性设计准则, 要求可靠性计算安全系数应大于或 等于最小安全系数, 即
SHC = SHmin
2.2 齿轮接触疲劳强度可靠度计算式
齿轮接触疲劳强度可靠度计算, 可借助正态分布可靠性联 结方程来进行计算。
########################################################################################
基 于 Visual C++6.0 编 写 优 化 程 序[7], 以 现 场 的 实 际 杆 长 为
初始值, 优化出一组杆长:
!!!!!!!!!!!!!!!!!!!!!!!!!!!!!!!!!!!!!!!!!!!"
中图分类号: TH132、416 文献标识码: A
齿轮是机械传动中的一个重要零件。齿轮性能的优劣和承 载能力的大小, 在很大程度上决定着机械产品的质量与水平。在
* 来稿日期: 2006- 10- 23
润滑良好的闭式齿轮传动中, 其主要失效形式是齿面的接触疲
【摘 要】介绍了一种将齿轮接触疲劳强度的常规设计与可靠性设计相结合的改进计算方法。用 常规设计方法计算齿轮的初始尺寸, 同时用可靠性设计方法计算可靠性安全系数及可靠度。在保证齿 轮合理可靠度的条件下, 通过对计算结果的评价与调整, 使齿轮的尺寸减小。供广大机械设计工作者 在齿轮的小型化设计中选用。
关键词: 齿轮; 接触疲劳强度; 计算方法 【Abstr act】 A improved calculation method of combining general and reliability design of contact fa- tigue strength for gear is discussed. Initial size for gear is calculated with general design method, and furthmore reliability safety factor and reliability with reliability design method is calculated. By evaluation and alignment for calculating results the gear size is decreased in condition ensured reasonable reliability for gear. This paper provides selected methods in small_ scall design of gear for machine designers. Key wor ds: Gear ; Contr act fatigue str ength; Calculation method
1.2 齿轮接触疲劳强度计算的常规计算式
齿面最大接触应力的计算式是从赫芝公式转换而来的。我 们将两个平行的圆柱体转化为两个渐开线齿轮的齿廓, 并以相 应的参数与尺寸替代, 并以交变接触应力代替静接触应力, 用齿 面节点作为计算点, 其齿面最大接触应力的计算式见文献[1]。
进行齿轮的接触疲劳强度的可靠性计算。
( 3) 通 过 常 规 计 算 , 分 别 求 出 齿 轮 中 心 距 ", 齿 数 Z1、Z2, 模 数 mn, 螺旋角 #, 齿宽 b1、b2 及分度圆直径 d1、d2 等。在此基础上, 再
上式中的齿轮接触疲劳强度变异系数一般取 Cr =0.06。 齿轮接触疲劳强度标准差按 !r = Cr $r 公式计算之。齿轮接 触疲劳应力的标准差 !s 的计算见文献[2]。 齿 轮 接 触 疲 劳 强 度 可 靠 度 RH 数 值 由( 6) 式 求 得 的 可 靠 度 系数 Z 值, 在文献[3]的标准正态分布函数表中查得。 按可靠性设计准则, 齿轮接触疲劳强度的计算可靠度应大 于或等于许用可靠度, 即 RH =[R]H
小齿轮尺寸的目的。对齿轮接触疲劳强度计算的评估方法作如
下说明。
2.3.1 评价指标的选择
评价指标是指齿轮接触疲劳强度的许用可靠度[R]H 及最小 安全系数 SHmin。这两个指标主要是根据设计者的经验和机械部 门的行业标准来确定。当缺乏设计经验或无行业标准时, 可在表
3.3 齿轮可靠度计算
将 # r、$ s、"r 及 "s 等 数 据 代 入( 6) 式 , 得 齿 轮 可 靠 度 系 数 的数值, 即
社, 1993. 2 陈立周.机械优化设计方法[M].北京: 冶金工业出版社, 1995. 3 洪嘉振.计算多体动力学[M].北京: 高等教育出版社, 1999. 4 陈立平,张云清,任卫群,覃刚等编著.机械系统动力学分析及 ADAMS
应用教程[M].北京: 清华大学出版社, 2005. 5 张志涌.精通 matlab6.5[M].北京: 北京航空航天出版社, 2002. 6 傅祥志.机械原理( 第二版) [M].武汉: 华中科技大学出版社, 2000. 7 Stanley B Lippman,Josee Lajoie 著, 潘爱民, 张丽译.C++Primer( 3rd