工序质量分析表
工序能力指数Cpk计算表

工序能力指数Cpk计算表1234567891011121314151617181964109154199计算表1#2#Cp 1.09918634CpCpU0.719800509CpUCpL-0.719800509CpLCpk0.719800509CPKT 6.6Tε 1.139ε标准正态累积分0.999512354标准正态累积分CP的P值0.0975292%CP的P值标准正态累积分0.984590485标准正态累积分CPU的P值 1.5409515%CPU的P值标准正态累积分0.015409515标准正态累积分CPL的P值98.4590485%CPL的P值CPK的P值 1.5414103%CPK的P值判断上公差是否FALSE判断上公差是否为空判断下公差是否FALSE判断下公差是否为空结果0.719800509结果P显示结果 1.5414103%P显示结果Cpk Cpk>1.67过程能力非常充分,为>1.67过程能>1.33过程能力充分,当不是>1.33过程能>1过程能力尚可,必须用控>1过程能力>0.67过程能力不充分,分析>0.67过程能过程能力不足,一般应停止继过程能力不足1.67≥ 1.67≥1.33≥ 1.33≥1≥1≥0.67>0.67>1≥Cpk>0.67过程能力不充分0.67>Cp过程频次3#4#0.666666667Cp0Cp0.0721687840.666666667CpU-0.96225045CpU 2.838638824-0.666666667CpL0.962250449CpL-2.694301260.666666667CPK-0.96225045CPK-2.694301260.2T0T0.050ε 1.666666667ε0.9583333330.977249868标准正态累积分0.5标准正态累积分0.5857034624.5500264%CP的P值###########CP的P值82.8593075%0.977249868标准正态累积分0.001946209标准正态累积分12.2750132%CPU的P值99.8053791%CPU的P值0.0000000%0.022750132标准正态累积分0.998053791标准正态累积分3.16213E-1697.7249868%CPL的P值0.1946209%CPL的P值###########4.5500264%CPK的P值###########CPK的P值###########FALSE判断上公差是否为空TRUE判断上公差是否为空FALSEFALSE判断下公差是否为空FALSE判断下公差是否为空TRUE0.666666667结果0.962250449结果 2.8386388244.5500264%P显示结果0.1946209%P显示结果0.0000000%CpL CpU>1.67过程能力非常充分,为提高产品质量,对过程能力非常充分,为>1.67过程能力非常充分,>1.33过程能力充分,当不是关键或主要项目时>1.33过程能力充分,当不过程能力充分,当不是>1过程能力尚可,必须用>1过程能力尚可,必须用控制图或其它方法对程能力尚可,必须用控>0.67过程能力不充分,分析分散程度大的原因>0.67过程能力不充分,分过程能力不充分,分析过程能力不足,一般应停止继续加工,找出原因力不足,一般应停止继过程能力不足,一般应停止1.67≥ 1.67≥1.33≥ 1.33≥1≥1≥0.67>0.67>CpU>1.67过程能力非常充分,为提高产品质量Cp过程能力不足,一般1≥CpL>0.67过程能力不充高产品质量,对关键或主要项目可缩小公差范围;或为提高效率、降低成本而放宽波动幅度,降低设备精度等级;或键或主要项目时,放宽流动幅度;降低对原材料的要求;简化质量检验,采用抽样检验或减少检验频次或其它方法对过程进行控制和监督,以便及时发现异常波动;对产品按正常规定进行检验散程度大的原因,制订措施加以改进,在不影响产品质量的情况下,放宽公差范围,加强质量检验,进行全数检验或加工,找出原因,改进工艺,提高Cp值,否则全检,挑出不合格品提高产品质量,对关键或主要项目可缩小公差范围;或为提高效率、降低成本而放宽波动幅度,降低设备精度等级降低设备精度等级;或将精度要求特别高的零件调至该工序进行加工等检验,进行全数检验或增加检验频次度,降低设备精度等级;或将精度要求特别高的零件调至该工序进行加工等。
关键工序质量控制的措施分析
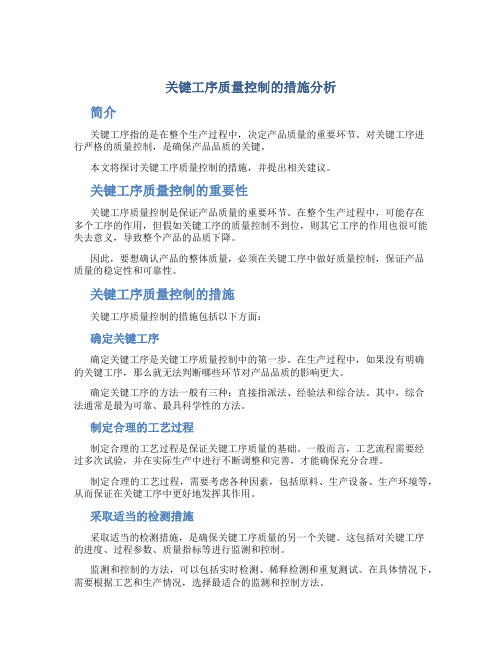
关键工序质量控制的措施分析简介关键工序指的是在整个生产过程中,决定产品质量的重要环节。
对关键工序进行严格的质量控制,是确保产品品质的关键。
本文将探讨关键工序质量控制的措施,并提出相关建议。
关键工序质量控制的重要性关键工序质量控制是保证产品质量的重要环节。
在整个生产过程中,可能存在多个工序的作用,但假如关键工序的质量控制不到位,则其它工序的作用也很可能失去意义,导致整个产品的品质下降。
因此,要想确认产品的整体质量,必须在关键工序中做好质量控制,保证产品质量的稳定性和可靠性。
关键工序质量控制的措施关键工序质量控制的措施包括以下方面:确定关键工序确定关键工序是关键工序质量控制中的第一步。
在生产过程中,如果没有明确的关键工序,那么就无法判断哪些环节对产品品质的影响更大。
确定关键工序的方法一般有三种:直接指派法、经验法和综合法。
其中,综合法通常是最为可靠、最具科学性的方法。
制定合理的工艺过程制定合理的工艺过程是保证关键工序质量的基础。
一般而言,工艺流程需要经过多次试验,并在实际生产中进行不断调整和完善,才能确保充分合理。
制定合理的工艺过程,需要考虑各种因素,包括原料、生产设备、生产环境等,从而保证在关键工序中更好地发挥其作用。
采取适当的检测措施采取适当的检测措施,是确保关键工序质量的另一个关键。
这包括对关键工序的进度、过程参数、质量指标等进行监测和控制。
监测和控制的方法,可以包括实时检测、稀释检测和重复测试。
在具体情况下,需要根据工艺和生产情况,选择最适合的监测和控制方法。
建立质量保障体系建立质量保障体系,是确保产品质量的可靠保证。
质量保障体系包括质量计划、设计管理、生产管理、检测验证等多方面内容,是关键工序质量控制中的重要一环。
建立质量保障体系,需要有完善的管理体系和强大的技术支持,以确保每一个关键工序都得到了充分的质量保障。
后记通过以上措施,可以对关键工序质量进行有效的控制和保障。
在具体操作过程中,需要根据不同生产环境和工艺流程,制定相应的措施,并根据实际情况进行不断的调整和完善。
职业技能鉴定国家题库机修钳工高级技师理论知识试题及答案五
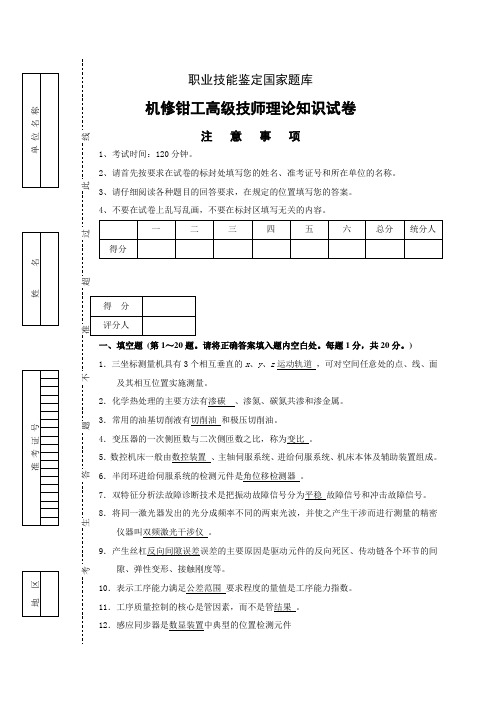
职业技能鉴定国家题库机修钳工高级技师理论知识试卷 注 意 事 项 1、考试时间:120分钟。
2、请首先按要求在试卷的标封处填写您的姓名、准考证号和所在单位的名称。
3、请仔细阅读各种题目的回答要求,在规定的位置填写您的答案。
4、不要在试卷上乱写乱画,不要在标封区填写无关的内容。
一、填空题 (第1~20题。
请将正确答案填入题内空白处。
每题1分,共20分。
) 1.三坐标测量机具有3个相互垂直的x 、y 、z 运动轨道 ,可对空间任意处的点、线、面及其相互位置实施测量。
2.化学热处理的主要方法有渗碳 、渗氮、碳氮共渗和渗金属。
3.常用的油基切削液有切削油 和极压切削油。
4.变压器的一次侧匝数与二次侧匝数之比,称为变比 。
5.数控机床一般由数控装置 、主轴伺服系统、进给伺服系统、机床本体及辅助装置组成。
6.半闭环进给伺服系统的检测元件是角位移检测器 。
7.双特征分析法故障诊断技术是把振动故障信号分为平稳 故障信号和冲击故障信号。
8.将同一激光器发出的光分成频率不同的两束光波,并使之产生干涉而进行测量的精密仪器叫双频激光干涉仪 。
9.产生丝杠反向间隙误差误差的主要原因是驱动元件的反向死区、传动链各个环节的间隙、弹性变形、接触刚度等。
10.表示工序能力满足公差范围 要求程度的量值是工序能力指数。
11.工序质量控制的核心是管因素,而不是管结果 。
12.感应同步器是数显装置中典型的位置检测元件 考生答题 不超 过 此 线13.对设备的某个部件或某项精度的修理,称为项目性修理(或项修。
14.数控机床位置精度的三项评定项目有轴线的重复定位精度、定位精度和反向差值。
15.桥式起重机主梁的下挠变形常伴随主梁侧弯和腹板呈波浪形,统称为主梁架的变形。
16.铸石材料具有良好的耐磨性和耐化学腐蚀性。
17.对振动的控制需对振源、振动传播途径和振动影响的地点三个环节进行治理。
18.可编程控制器和变频调速系统用于设备改造时,基本上不改变机械结构的正常传动,只从电控系统给于改进,比较简单可行。
机修钳工技师题库

1. 7k-15-8型透平压缩机修复滑动轴承,因轴瓦间隙较大,还必须(用仪器测量)。
2.项修是对设备部件因突发性事故所造成的损坏或(精度)的丧失的恢复。
3.项修工艺是设备(大修工艺)的一部分。
4.高速设备联轴器的调整,应采用(专用的检具)。
5. 7k-15-8型透平压缩机主机的组装重点是(转子轴)装配。
6.为了提高传动链的精度,在设计齿轮机床时,尽量增加传动链中传动元件的数量,已减少误差的来源。
(X)7.坐标镗床几何精度检查,检查项目G11是垂直于主轴线对工作台面的垂直度,G11超差往往是主轴旋转精度不高造成的。
(,)8.坐标镗床几何精度检查前先要调整机床安装水平,将工作台置于行程中间位置,在工作台中央位置放置水平仪,水平仪在(纵向和横向)的读书均不得超过0.02mm/1000mm。
9.坐标镗床几何精度检查,检查项目G1是工作台面的(平面度)。
10.坐标镗床精度检查是在机床空运转试验后进行,在负荷试验前均应检查几何精度,而坐标定位精度只有在(负荷试验后)进行检验。
11.坐标镗床几何精度检查,当实测长度与检验标准规定的长度不同时,允差可按能测量的长度折算,折算结果小于0.001mm时,按(等于0.001mm)计。
12.滚出机属于(展成)运动的齿轮加工机床,不但要求有一定的几何精度,而且还应具有一定的传动链精度。
13.滚出机床加工齿轮的齿距相邻误差、累计误差和展成的齿形误差主要取决于机床(传动链精度)。
14.角位移测量仪是用来检验(主轴回转传动链精度)的检验工具。
15.镗孔时,锁紧螺母端面与螺纹中心线不垂直,造成孔的圆度超差,可通过修复螺母顶面解决。
(X)16.磨削齿轮工作台回转控制器过松或导轨磨损,应调整制动器,修刮圆形导轨。
(V)17.螺纹磨床砂轮主轴与轴承间隙过大或轴向窜动超差。
应调整或修复主轴。
(V)18.在经济型数控改造中,往往是进步点动机和滚球丝杠副的进给量很微小,精度很高。
(V)19.磨削齿轮,工件与定位孔中心线不垂直,压紧螺母端面不垂直,心轴端面不垂直等,是造成(工件出句误差)超差的原因之一。
装配钳工技师理论考试练习(三)

一.单项选择(第1题~第20题。
选择一个正确的答案,将相应的字母填入题内的括号中。
每题1分,满分20分。
)1.检验吊钩的载荷值时,吊钩应可靠地支持()倍的检验载荷而不脱落。
A、1B、2C、3D、42.数控机床普通闭环控制系统要求测量元件能测量的最小位移为( )mm。
A、0.001~0.01B、0.001~0.02C、0.001~0.05D、0.001~0.13.能保证瞬时传动比恒定的传动是( )。
A、带传动B、链传动C、齿轮传动D、摩擦轮传动4.切削液的作用是()。
A、缓冲作用B、减震作用C、密封作用D、洗涤和排屑作用5.制定箱体零件的工艺过程应遵循( )原则。
A、先孔后平面B、先平面后孔C、先键槽后外圆D、先内后外6.违反安全文明生产要求的是( )。
A、遵守劳动纪律B、贯彻操作规程C、遵守生产纪律D、使用不知悉的机床和工具7.行程开关的作用是( )。
A、限制机械运动的位置或行程B、过载保护C、频繁地接通或断开交直流主电路D、短路保护8.在振动的三个基本量中,由振动频率或振动值的变化来判定的振动基本量称为( )。
A、相位差B、振动值C、频率D、振幅9.由机床运动精度及工艺系统变形等因素引起误差,属于( )误差。
A、定位B、安装.调整C、加工D、测量10.()属于抗氧化钢。
A、15CrMoB、1CriMoVC、1Cr25Ni20Si2D、CrWMn11.职业道德基本规范不包括( )。
A、搞好与他人的关系B、服务群众奉献社会C、遵纪守法廉洁奉公D、爱岗敬业忠于职守12.三视图中,左视图和俯视图应( )。
A、长对正B、高平齐C、宽相等D、宽对齐13.对龙门刨床等大型机床的蜗杆.蜗条齿面进行刮研修复,齿面接触率在齿高上应达到( )以上即为合格。
A、50B、60C、70D、8014.对机床床身的测量和修刮最好用( )点支承。
A、3B、4C、5D、615.潜水泵入水深度不宜超过5m,距水底的距离应在()mm以上。
关键工序质量分析表

第 单位名称 资产编 号 部门名称 工序质量分析表 工序名 称 质量问题原因 (展开原因分 析) 管 理 一 二 方 式 次 次 三 次 四 次 产品型号 零件名称 页 共 零件号 页
Hale Waihona Puke 设备型号工序号材料 牌号 检测要求 检测 允差 极限 方法 值 频数 检测
材料规格 及硬度 纳入 标准 编号 名称 标准 操 作 者 班 组 长
工人等级
序 工序名称及 号 加工内容
质量管理点 质 量 质 检查类别 等 量 级 项 自 首 巡 抽 全 目 检 检 检 检 检
责任者 工 段 长 检 验 员 设 备 员 工 艺 员
备注
标志
数量
文件号
签名
日期
拟订 校对 审核
单位会签
压铸工序质量审核表

压铸工序质量审核表表号:QR-8.2.3-01NO:序号审核项目涉及部门审核内容对照标准质量特性分级审核结果不符合项记录工艺因素管理因素一质量控制计划1质量控制点流程图生产部查(2-3个)管理文件,看是否有管理点流程图,质量控制点选择是否合适质量点控制程序2控制文件生产部文件是否齐全;压铸件工艺卡,工序质量表,作业指导书质量点控制程序生产部压铸机“日检维修卡”,“设备定检卡”品控室检查作业指导书二工序因素(一)人1熔化工压铸车间办公室持证上岗,查有无操作合格证人员培训控制程序压铸车间到生产部查(3个月)“工艺纪律检查表”看该岗贯彻率工艺纪律检查控制程序生产部询问熔化工:工艺规程是否便于操作工艺技术文件控制程序压铸车间询问熔化工:工艺规程是否便于操作工艺技术文件控制程序询问熔化工:该合金的最高熔化温度,出炉温度合金熔化工艺流程询问熔化工:炉控柜仪表(电压表、电流表、功率因素表、温度表)的作用及控制范围,查当月合金成份记录图表的记录情况,查(半个月)“熔化工艺日记录”是否认真填写设备操作规程;压铸合金及炉料管理2压铸工办公室压铸车间持证上岗,查有无操作合格证人员培训控制程序压铸车间查控制点压铸工,是否由专人生产到生产部查(3个月)“工艺纪律检查表”看该岗位贯彻率工艺纪律检查控制程序;质量控制点控制程序查“控制点”文件是否齐全(压铸工艺卡,作业指导书)质量控制点控制程序生产部询问压铸工:按工艺卡及作业指导书操作有无困难,工艺参数的选择是否正确、完善工艺技术文件控制程序压铸车间询问压铸工:所生产的铸件应控制的主要工艺参数值,压射压力、慢压射行程、余料饼厚、留模时间、浇注温度压铸工艺卡;作业指导书压铸车间抽查(1份)质量控制点的“压铸工艺参数记录表”,看记录状况是否在控制范围作业指导书压铸车间抽查(2个)质量控制点压铸工,讲述“压铸机日检维修卡”几项内容设备日检点控制程序压铸车间抽查(2名)压铸工询问“压铸模巡检记录卡”的部份内容压铸模控制程序(三)设备1压铸模压铸模库(模具车间)看(3份)“压铸模调试传票”,查是否有相应的“产品鉴定表”压铸模控制程序查(2份)模具使用工作传票的填写情况看(2份)“质量问题通知单”,并查“模具传票”上相应的处理意见模具车间查(2套)库存现生产模具,看是否带“尾件”及“尾件检查表”模具车间维修工询问(2个)维修工“压铸模巡检记录卡”上的部份内容压铸模控制程序看库存模具状况:是否有合金、涂料等杂物及锈钝现象看现场模具使用状况、各活动部分是否活动自如压铸车间压铸工查模具使用维护状况;分型面、溢流槽、排气槽、滑块槽有无合金、夹杂物等压铸模控制程序查“导柱、导套”,斜杆、孔及“滑块、滑块槽”接合面的润滑状况2压铸机生产部查(2份)压铸机“日检维修卡”档案,看“日检”是否认真设备使用与维护管理查(2份)压铸机“定检表”,看是否按期定检查(3份)近期“日检维修卡”的停机工时,看设备能力压铸车间压铸工查(3台)压铸机的液压系统是否漏油,看维修状况设备日点检管理机电维修工看(3台)压铸机压射系统的建压时间是否正确,查维修状况设备日点检管理看(3台)压铸机的压射系统的持压状况,查设备维护效果压铸车间压铸工查(3台)压铸机储能器压力是否合适,看设备工作状况设备日点检管理查(3台)压铸机活塞是否发卡,看设备点检状况品控室查(3台)压铸机各压力表是否完好,查这些压力表是否有合格证计量器具使用维护和保养管理(三)材料1原材料(金属炉料)(1)采购单供销部查铝锭、锌锭、电解铜的采购单各1份,看其规格是否与规定相符金属炉料消耗定额汇总表查(2-3种)原材料供方名单,看是否有质量保证能力认可采购物资控制程序(2)材质证明书品控室查(2种)炉料(铝、锌锭)近半年的材质证明书,看是否有检查员签字认可进货检验与试验控制程序品控室及保管员查(2种)批炉号的锌(或铝)锭,看是否有材质证明书或化验报告单原材料质量检验管理供销部查(2-3种)材料代用单(炉料),看审批手续是否齐全原材料质量检验管理(3)原材料储存炉料库看库房原材料是否分类堆放,有无明显标识,是否防潮原材料质量检验管理2回炉料压铸车间回炉料库到库房看回炉料是否分类堆放,有无标识,是否防潮,看回炉料中是否有混料现象及其他杂物压铸合金及炉料管理压铸车间查压铸机旁回炉料箱内是否有混料现象压铸车间带镶件回炉料是否单独存放品控室看合金检查员“保温炉”抽查“化验报告单”所查不合格料是否签署了“处理意见”3合金铸锭压铸车间炉料库询问保管员,合金锭入库的依据,并查看近2天的铝(或铜)合金的“化验报告单”再核定实物合金熔化工艺规程查库房合金锭是否按炉号分类存放压铸车间熔化工段看合金锭箱上是否有明显的合金炉号标识合金熔化工艺规程4镶件品控室看车间内存放镶件是否有检查员确认的合格单配套件质量检查管理品控室看车间内存放镶件是否有锈钝现象5辅助材料(1)精炼剂供销部、车间查熔化炉台上精炼覆盖剂是否过期,受潮变质合金熔化工艺规程(2)型腔涂料(脱模剂)供销部看现场使用的型腔涂料是否有沉淀现象型腔涂料配制工艺规程(四)工艺方法1熔化过程炉料准备压铸车间查(2-3种)炉料的破碎粒粒度是否符合要求(Si,Cu),查破碎或炉料剪切现场是否有混料现象。
山积表(工序平衡分析)

类型Ⅱ山积表
生产节拍T.T=37s
B型车
C型车
加权平均 作业时间 33.52秒
加权
13
2、山积表的编制
标准作业类型Ⅲ山积表
表示可用工作时间
堆积柱状图:用以表示对应人员的作业内容、作业时间 。
14
2、山积表的编制
标准作业类型Ⅲ
作业时间调查表1—调查总表
定义:生产线外的作业,算不出生产节 拍,不是反复作业的工序;其目的就是根据 全厂的效率核算,将生产线外的人的作业标 准化、量化到每个人每班。
步行 安放缸盖 螺栓与缸盖结合面涂油 螺栓涂油安装
步行 放车扫描
合计
时间/秒 14 22 8 12 8 20 14 4 24 14 64 4 24 232
232 148
32
谢谢大家!
33
换刀频率
换刀时间(分钟) 时间(分钟)/台
1
铰刀DX246-C1-60701
1000
2
丝锥M12-H2
300
3
丝锥M12-H2进口
1000
4
丝锥M16-H2侧面国产
300
5
丝锥M16-H2上平面全用进口
1000
6
丝锥M18×1.5-H2
300
7
丝锥M30×1.5
200
8
螺旋丝锥M8-H2国产
300
9
20
3、山积表的运用及改善案例
什么是生产线平衡?
生产线平衡是指构成生产线各道工序所需的时间处于平衡状态,作业人员的作业时间尽可能 的保持一致,从而消除各道工序间的各种等待的浪费,进而取得生产线平衡,达到生产效率的最 大化。
生产线平衡的计算
各工序常见质量问题的分析、解决

盒
接入接线盒端子内的尺 寸过窄、过短
电阻增大、过流、发热
接线盒安装在背板后不允许有位移 接线盒底部补胶、注意打胶量与安装方式 叠层处胶带使用不当,使用无殘留胶渍、耐高温的胶 带 硅胶密封引出线根部
接入接线端子内的尺寸:宽4.5~5mm、长10mm
接入接线端子后剩余的 汇流条过紧
无热胀冷缩的余地,反复如此电阻变大, 长期使用可能会断
裸手接触原材料
戴手套、指套
烙铁头不良容易造成虚焊或不光滑
烙铁头在细砂纸上抹平,加锡保养或更换烙铁头
烙铁温差大
选择质量好的烙铁
3
焊接不良(包括虚焊、过焊 员工手势不当,容易造成虚焊、侧焊
正确的方法多加练习,找到烙铁头平面
、侧焊、不光滑)
电池片可焊性不好,容易造成虚焊或过焊
不同厂家不同批次的电池片先试焊,找到相对合适的 工艺再批量焊接
*功率衰减过大 (1)串联电阻增大
--电池 --焊带疲劳 --焊接不良 --接线盒接触不良 (2)并联电阻减小 --电池 --微短路 --二极管反流 (3)脱层 --EVA过期或污染
--玻璃污染 --环境污染 (4)EVA GEL ---工艺 -一材料
(5)接线盒 --二极管性能
--接触
--密封
(6)功率不足 --测试问题 根据不良原因采取相应对策。
焊接收尾处打折太深或离电池片太近
电池片自身隐裂
叠层在灯光下仔细检查
焊接时打折过重导致电池片隐裂
层压前,操作人员抬组件时压倒电池片, 进料不注意
抬组件时护住四角,不要压到TPT上
8
层压后破片
异物、锡渣、堆锡再电池片上导致层压后 破片
保持工作台面整洁,各工序自检、互检
工序质量控制点管理制度(4篇)

工序质量控制点管理制度第一章总则第一条为了加强工序质量控制,提高产品质量,确保工序质量,制定本管理制度。
第二条本制度适用于所有涉及工序质量控制的部门和岗位。
第三条工序质量控制点是指工序中需要严格把关的节点,对工序质量起决定性作用的环节。
第四条工序质量控制点的设立应基于工序流程的特点和质量要求,经过充分的论证和协商确定。
第五条各部门应根据自身的工序特点和质量要求,制定相应的工序质量控制点管理办法。
第二章工序质量控制点的设立第六条工序质量控制点的设立应遵循以下原则:(一)必要性原则:工序质量控制点的设立必须符合工序质量管理的需要,能够确保工序质量的稳定性和可控性。
(二)关键性原则:工序质量控制点的设立应针对工序中的关键环节,对工序的整体质量起决定性作用的环节。
(三)规范化原则:工序质量控制点的设立应符合相关的质量管理规范和标准。
第七条工序质量控制点的设立要经过充分的论证和协商,并报经质量管理部门批准。
第八条工序质量控制点应具备以下特点:(一)明确性:要明确该控制点的具体位置和表现形式。
(二)可操作性:要能够根据相关规范和标准,对该控制点进行有效的检测和判定。
(三)追溯性:要能够追溯到具体的操作人员和时间。
第九条工序质量控制点的设立应综合考虑以下因素:(一)产品质量要求(二)工序特点(三)工序流程(四)技术规范和标准第三章工序质量控制点的管理第十条工序质量控制点的管理应遵循以下原则:(一)全员参与原则:所有操作人员在工序中都应主动参与工序质量控制点的管理工作。
(二)标准化操作原则:所有操作人员在工序中都应按照相关规范和标准进行操作。
(三)主动预防原则:所有操作人员在工序中都应主动发现和预防工序中潜在的质量问题。
(四)及时反馈原则:所有操作人员在工序中都应及时将发现的质量问题反馈给质量管理部门。
第十一条工序质量控制点的管理工作主要包括:(一)质量检测和判定:对工序质量控制点进行定期的检测和判定,确保工序质量符合要求。
质量管理工具-调查表.ppt
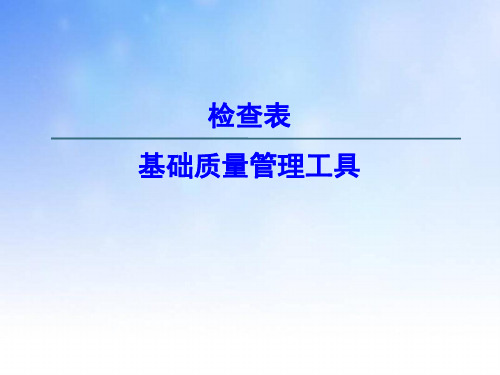
特别提示:
调查表的种类很多,也没有 固定的格式。常用的调查表有不 合格项目调查表、不合格原因调 查表、缺陷位置调查表、工序质量 调查表、废品分类统计表等,具 体使用时应针对所要调查的具体 问题进行设计表格。
4、查看表—格局举例
表4—1
制品抽样查验及外观不合格品项目查询表
批 产品 成品量 抽样数 次 型号 (箱) (支)
2、检查表--使用目的
用于记录(记录原始数据,便于报告)。 用于调查(用于原因调查、纠正措施有效性的调查)。 用于日常管理(如首件检查、设备检查、安全检查)。
3、查看表--运用的程序
第1步 确定对观察事件/情况的定义; 第2步 计划数据收集:
-谁, 收集期限,来源; -资料收集者应有必要的时间和知识; -要用足够的时间收集资料; 第3步 设计检查表:清楚,完整,易于使用; 第4步 收集数据:连续性,准确性。 必要时,评审并修订表格。
外观不合格项目
不合格品 批不合格
数(支)
率(%)
切 贴口 口
空松 短 烟
过紧 钢 油点 软
印
腰
表 面
1 烤烟型
10
500
3
2 烤烟型
10
500
8
3 烤烟型
10
500
4
4 烤烟型
10
500
3
5 烤烟型
10
500
5
… …
……
250 烤烟型
合计
…… 10
2500
…… 500 125000
…… 6 990
调查者:王XX 日期: ** 年 **
项目
插头槽径大 插头假焊 插头焊化
插头内有焊锡 绝缘不良 芯线未露 其他
工序统计分析七种工具

排列图
• 用 MINITAB 作 Pareto图
9
排列图
• 用 MINITAB 作 Pareto图 报废情况统计
100
4000 80
3000
60
2000
40
Count Percent
1000
20
0
Defect
Count Percent Cum %
铸 欠
1746 36.8 36.8
隔 冷
1537 32.4 69.2
4. 对于主要的、关键的要因,分别用显著符号标记出来,以示突出和重要。
• 2、3、4找出的关键因素(要因,以3-5个为宜),用圆圈“○”或方框“□” 框 起来,作为制订质量改进措施的重点考虑对象。
5. 注明画图者,参加讨论分析人员、时间等可供参考的事项。
15
因果图
• 绘图注意事项:
1. 因果图只能用于单一目的研究分析。一个主要质量问题只画一张因果图。 2. 集思广益,一般以召开各种质量分析会共同分析,整理出因果分析图。讨论
7. 在图上注明累计频数,累计百分数;注明排列图的名称、收集数据的时间, 以及绘图者可供参考的其他事项。
8. 利用排列图确定对质量改进最为重要的项目。
6
排列图
• 排列图的观察分析
– 首先观察柱形条高的前2~3项,一般说来这几项是影响质量的重要因素。 – 一般把因素分成A、B、C三类
• A类因素:主要因素。累积频率在0%~80%的那些因素是影响产品报废的主要者, 一般情况下,A类因素不多于3个。
3
排列图
排列图示例
项目
50欠00铸
45冷00隔
小400砂0 眼
废 35粘00砂 品 30其00他 数 25合00计
质量分析报告 表格 XLS格式
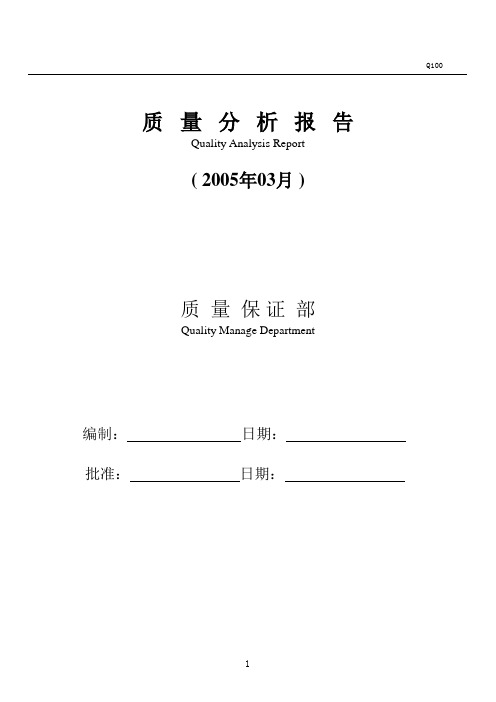
四、 本月份三月月份三月3月份装配车间的主要报废产品是滑板95件,烟灰缸(盖)64件,支架40件,后立柱饰板(右)26件,这四种产品累计报废率达到了86.54%;销售数量(千件)索赔量(千件)百分比(%)实际达成PPM 目标PPM36000.00%0463.371目标PPM27324.870.0060.00%080销售数量(千件)索赔量(千件)百分比(%)实际达成PPM 9564402624541136.54%61.15%0.00%10.00%20.00%30.00%40.00%50.00%60.00%050100150200累计百分比(%N =260报废数量(件)累计百分比(%)0200400360三月份0公里内外装饰件PPM 达成情况统计图实际达成PPM 目标PPM3月份0公里内外装饰件PPM 实际达成为0,未超出目标值,希望能继续保持;50100080三月份0公里紧固件\冲压件PPM 达成情况统计图3月份0公里紧固件/冲压件PPM 实际达成值为0,未超出目标值,希望能继续保持;50发货数量索赔数量百分比(%)目标PPM PPM ###0.312报废数量(千件)2.65600.024 4.3830.0010.2721.7014.17341.82%表面生馏/缺料项目表面锈蚀状态更改开裂累计报废数量(千件)7.4931.620.00%0.24%尺寸超差变形0.01%牙纹破损/烂牙 2.1051.3761.5722.7926.87%29.60%46.64%88.46%累计报废率(%)26.62%26.62%26.86%五、 产品缺陷排列图:2.73%17.05%报废率(%)26.62%0实际达成PPM 目标PPM3月份安全件未发生索赔,所以0公里安全件PPM 值为0,要继续保持;5050三月份0公里安全件PPM 达成情况统计图实际达成PPM 目标PPM51015012 三月份售后PPM 达成情况统计图目标PPM 实际达成PPM3月份售后PPM 实际达成值为12,主要是风神公司售后索赔0.32千件;注:以上四项PPM 达成情况统计都是以当月收到的索赔发票为依据;。
生产工序管理
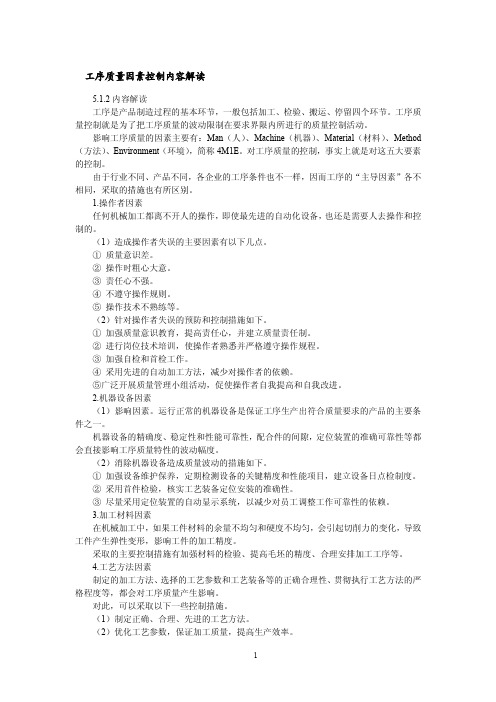
工序质量因素控制内容解读5.1.2内容解读工序是产品制造过程的基本环节,一般包括加工、检验、搬运、停留四个环节。
工序质量控制就是为了把工序质量的波动限制在要求界限内所进行的质量控制活动。
影响工序质量的因素主要有:Man(人)、Machine(机器)、Material(材料)、Method (方法)、Environment(环境),简称4M1E。
对工序质量的控制,事实上就是对这五大要素的控制。
由于行业不同、产品不同,各企业的工序条件也不一样,因而工序的“主导因素”各不相同,采取的措施也有所区别。
1.操作者因素任何机械加工都离不开人的操作,即使最先进的自动化设备,也还是需要人去操作和控制的。
(1)造成操作者失误的主要因素有以下几点。
①质量意识差。
②操作时粗心大意。
③责任心不强。
④不遵守操作规则。
⑤操作技术不熟练等。
(2)针对操作者失误的预防和控制措施如下。
①加强质量意识教育,提高责任心,并建立质量责任制。
②进行岗位技术培训,使操作者熟悉并严格遵守操作规程。
③加强自检和首检工作。
④采用先进的自动加工方法,减少对操作者的依赖。
⑤广泛开展质量管理小组活动,促使操作者自我提高和自我改进。
2.机器设备因素(1)影响因素。
运行正常的机器设备是保证工序生产出符合质量要求的产品的主要条件之一。
机器设备的精确度、稳定性和性能可靠性,配合件的间隙,定位装置的准确可靠性等都会直接影响工序质量特性的波动幅度。
(2)消除机器设备造成质量波动的措施如下。
①加强设备维护保养,定期检测设备的关键精度和性能项目,建立设备日点检制度。
②采用首件检验,核实工艺装备定位安装的准确性。
③尽量采用定位装置的自动显示系统,以减少对员工调整工作可靠性的依赖。
3.加工材料因素在机械加工中,如果工件材料的余量不均匀和硬度不均匀,会引起切削力的变化,导致工件产生弹性变形,影响工件的加工精度。
采取的主要控制措施有加强材料的检验、提高毛坯的精度、合理安排加工工序等。
产品质量分析报告

产品质量分析报告篇一:产品质量分析报告篇二:产品质量分析报告质量分析报告一、采购原材料质量检验情况从入库抽检情况下看,材料外观数量、性能指标符合产品自身要求,指标见质保书。
二、产品过程检验情况在生产过程中,操作者按产品工艺进行生产并进行自检,质检员进行过程抽检,过程检验中发现的问题统计如下:三成品无不合格品出现说明:表1、中的不良品是指可以重新加工的产品。
表3中标注“*”的不良品是让步接收的产品。
“不良品”:指表面有些小缺陷,顾客同意可按合格品接受的产品,所以仍可以进行生产或可以让步接收,让步接收的产品单独包装并标识。
四、质量过程检验分析表1:R-28多功能缓蚀剂①返工2件由于操作工在整形过程中对工艺要求认识不清,搅拌时间未达到要求,需要重新加工,加工后全数检验,合格后流入下道工序;Z-18催化分子筛抗焦活化剂①1件返工是由于操作工在整形过程中对工艺要求认识不清,搅拌时间未达到要求,需要重新加工,加工后全数检验,合格后流入下道工序表2:上述分析统计后用因果图表示如下:表2不良品、返工品、工废品因果分析图五、质量改进与纠正措施1、从表2中可以看出造成不良品、返工、工废品的原因,关键在于人,所以加强员工的质量意识教育,对员工操作技能进行培训,提高其操作技能。
2、统一工艺标准,建议强化各种工件工序指导书的学习,有利于员工按工序指导书操作。
3、加强现场管理,对不良品、工废品、返工品标识要尽快建立并实施;产品按“先进先出、定置定量”的原则实施,有利于产品质量可追溯性的顺利进行。
质量部 2021.4.8篇三:产品质量分析报告模板产品质量分析及节能降耗报告一、传感器产品质量概况(一)监督抽查情况1、国家监督质量抽查情况(1)国家监督抽查合格率格率数据。
附图:将本地区国抽合格率以柱状图的形式与上季度或往年同期排列比较。
(2)国家监督抽查合格率分布情况说明:本节需采集本地区本季度按产品分类的国抽合格率,并以合格率的8个区间(分别是合格率为100%、90~99%、80~90%、70~80%、60~70%、50~60%、30~50%、 30%)来统计抽查产品的比率。
工序分析法
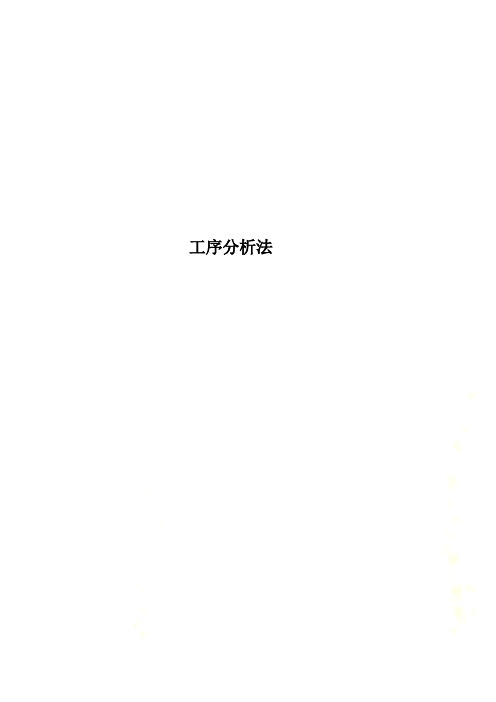
工序分析法工序分析法教育实践资料产品工序分析法深圳3A企业管理顾问有限公司编制:苏迎斌工序分析法1.工序分析法a)定义:在工厂里,原材料按照一定的顺序进行各种加工,最终形成产品上市。
在各个过程中,包括加工、搬运、验货、甚至待工、搁置等作业。
这种产品生产过程称之为“工序”。
对一系列的工序进行调查、分析的手法称之为“工序分析法”工序分析法是生产现场IE管理的基本方法之一b)目的:消除工序流程中存在的浪费、勉强、不均的流程和作业现象。
使作业变得更加舒适、快捷、低成本,生产高质量的产品。
c)种类:1)产品工序分析法(以产品为主要对象)2)作业工序分析法(以作业者为主要对象)3)联合分析析法(以人机共同作业、多台设备同时作业、多人共同作业为分析对象)4)事务工序分析法(以办公流程、手续流程、信息流程为主要对象)2.工序图记号在工序分析中,工序流程使用规定的记号来表示,其方便之处在于人人很容易学会看懂,一目了然,能够非常清楚表达和进行统计说明。
序号工序记号名称记号解释备注1 加工加工○使原材料、零部件或者产品的形状、基本记号性质进行改变的过程基本记号2 搬运搬运♉使原材料、零部件或者产品的位置进行改变的过程3 停滞贮藏▽将原材料、零部件或者产品按计划贮基本记号藏的过程基本记号4 滞留 D 原材料、零部件或者产品未能按计划进行而处于滞留状态5 检查数量检查□对原材料、零部件或者产品的数量进基本记号行核算,将结果与标准要求相比较,判别差异的过程基本记号6 质量检查 检验原材料、零部件或者产品的品质特性,并将结果和标准要求相比较,判定批量的合格率和单个体的优劣7 数量检查□◇数量检查为主,同时检查质量混合记号8 质量检查◇□质量检查为主,同时检查数量混合记号9 加工加工/数量检查○□加工为主,同时检查数量混合记号10 加工/质量检查○◇加工为主,同时检查质量混合记号11 加工/搬运♋加工为主,同时进行搬运混合记号12 流程流程线—表示主要工序的顺序关系辅助记号13 区分﹋表示在工序流程中的管理上的区分辅助记号14 省略═表示工序流程的某一部分省略辅助记号产品工序分析法a)目的:以原材料、零部件或者产品为对象,着眼于物流,分析各工序如何进行,达到设计和改善下列内容的目的:1)是否有不必要的停滞:2)搬运的次数是否太多;3)搬运的距离是否太长;4)搬运的方法是否存在问题;5)检查和加工是否可以同时进行;并研究下列个项目是否适当,以寻求更好的作业方法:6)设备配置;7)作业顺序;8)作业分配。