撞件不良解析报告
撞件不良解析报告
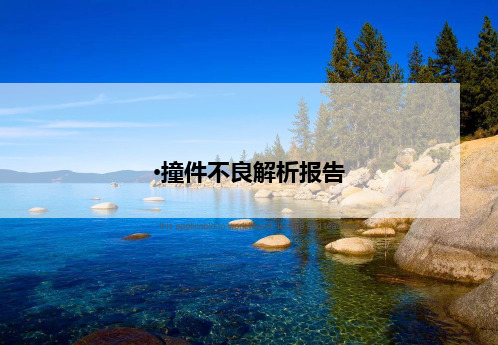
七、DIP补焊工序撞件不良解析
DIP补焊撞件不良案例分析:
预防措施: 4.存放或堆积板卡时需使用防静电泡棉板。 5.员工在堆板时,及时放入周转箱,避免堆集在台面上。 6.将流水线线体的护角用防表电皮包裹作防护。 7.用PVC防静电泡棉将流水线的铁边进行包裹。防止拿取板时撞件。 8.生产MS908.PB751F机型时,从炉后开始需要使用黑色周转泡棉进行周转,各工 位作业时,需将泡棉和PCB一起拿取。
预防措施: 1.对有撞件隐患的压浮高治具进行加工(在铁块外加热缩套管)。 2.生产时尽量不使用较大的压浮高治具。
易发生损件 治具
加工后的压件 治具
六、波峰焊工序撞件不良解析
6.2波峰焊撞件不良案例分析:
波峰焊撞件形成原因: 2.过炉治具员工在上下过炉治具时,和避位区相撞导致撞件
预防措施: 1.对过炉治具有贴片料的避位区域,进行导圆角处理。
上板
AI
印刷
板卡周转
转
回流炉后
板
分板
DIP 老化
SMT维修
插
二、AI撞件不良解析
2.AI撞件不良案例分析:
AI撞件形成原因:
撞件位置均为AI元件附近的贴片物料,AI设备在打料时AI夹料头调整高度过低(低于
0.8MM)导致。
AI撞件预防措施:
1.想办法固定AI夹料头高度,使其≥0.8MM(此点AI王工正在处理中)
预防措施: 1.对员工作业手法进行宣导培训。 2.对板底有贴片料的板卡,测试治具的避位处,需进行倒角,减少撞件的机率。 3.每4小时对治具的压柱进行点检,检查是否有松动不良。
倒角前的载板
NG
倒角后的载板
OK
十、小 结
1. 撞件不良在整个产品的生产过程中,都有机率导致。因此只有人 人参与和从自我做起。才能够及时有效的发现问题/改善问题。
撞件分析报告

撞件分析报告引言撞件是指两个物体之间发生碰撞时产生的磨损、损坏或形变等现象。
撞件分析报告用于分析撞件事件的原因、影响和解决办法,从而提供有效的决策依据。
本报告将对撞件的影响因素、分析方法以及解决方案进行探讨。
影响因素撞件事件的发生受多种因素的影响,主要包括以下几个方面:车辆速度车辆速度是影响撞件严重程度的重要因素之一。
速度越高,撞击力越大,撞件造成的损坏程度也会更严重。
材料强度撞件的材料强度决定了它对撞击的抵抗能力。
相对脆弱的材料容易在撞击过程中发生破碎或形变,从而导致更严重的损害。
撞击角度撞件的撞击角度会影响撞击后力的传递方式。
撞角越大,撞击力对目标物体造成的影响会更大。
相对速度相对速度是指两个物体在撞击前的相对运动速度。
相对速度越高,撞击力也会增加,从而导致更严重的撞击效果。
分析方法撞件事件的分析通常需要进行实验、数据收集和模拟分析等步骤。
实验通过实验可以获取撞件事件发生时的相关数据,如车辆速度、撞击角度等。
可以通过使用高速摄像机、测力仪等设备来记录实验过程中的数据。
数据收集通过收集现实世界中发生的撞件事件的数据,可以更好地理解撞击过程和后果。
例如,可以收集事故报告、保险索赔数据等。
模拟分析利用现代计算机仿真软件,可以对撞件事件进行模拟分析。
可以通过建立物理模型、设定撞击条件等来模拟真实场景下的撞击情况,从而得出相关的结论。
解决方案针对撞件事件的发生,可以采取以下措施来解决问题:设计改进在产品设计阶段,可以采用更坚固耐用的材料,增加抗撞击能力,降低撞击后的损坏程度。
安全防护装置可以在撞件的关键位置安装安全防护装置,如安全气囊、防撞托盘等,以减轻撞击力和减少损伤。
提高驾驶员素质通过加强驾驶员培训,提高驾驶技术和安全意识,减少交通事故的发生。
总结撞件分析报告对于了解撞件事件的影响因素、分析方法和解决方案具有重要意义。
在未来的撞件预防和安全设计中,应该综合考虑车辆速度、材料强度、撞击角度和相对速度等因素,并采取相应的措施,以减少撞件事件的发生和减轻损伤程度。
XXX电感撞件调查分析报告

不良品处理过程 中B面电感受力
置件
顶Pin
炉后目检与贴 贴条码过程中B面
条码
电感受力
没有撞件风险 撞件风险1 撞件风险3
现顶Pin设置OK 撞件风险4
装板数量未定义 作业过程中B面没有防
护措施治具
作业过过程中B面没有 防护措施治具
“风险点
与现况数
据统计发
生段”吻 合
维修站
维修过程中B面电 感受力
三、问题查找与风险排除
5. 炉后目检与贴条码:
6. 维修
电感受力被顶
电感受力被顶
员工贴条码过程中 1. 若将板子拿在左手中,同 时右手撕条码贴在板子上, 这样操作较不方便。 2. 若将板子放在轨道旁操作 台上作业,则B面电感正受 力被顶住,易造成零件裂碎。
A面生产过程中,若AOI出现 的不良在维修工位的过程中, 目前是放在一硬静电板上, 在维修过程中易造成零件裂 碎。
XXX PCB撞件起铜皮调查 分析报告
目录
➢ 不良问题描述 ➢ 在线现况数据统计 ➢ 问题调查与风险排除 ➢ 调查分析结论 ➢ 改善措施 ➢ 标准化
一、不良问题描述
✓ 不良现象:测试段在目检站发现不良品过多,不良为主板撞件, 目检650PCS,不良有13PCS,参考如下不良图片 ✓ 不良率:2.0% ✓ 不良位置:电源插座处PCB板边
不良图片1
不良图片2
二、在线现况数据统计
根据生产后段反馈的现象及不良板的确认,针对现SMT正在 生产现场按四个管制点( B面炉后、 B面装周转车后、 A面炉后、 A面装周转车后)进行不良统计收集,具体数据参考如下表:
二、问题查找与风险排除
• 根据生产后段反馈的现象及不良板的确认,针对现SMT正在生 产现场对生产工艺流程中存在的作业风险点进行确认与排除
公司交通事故调查分析报告
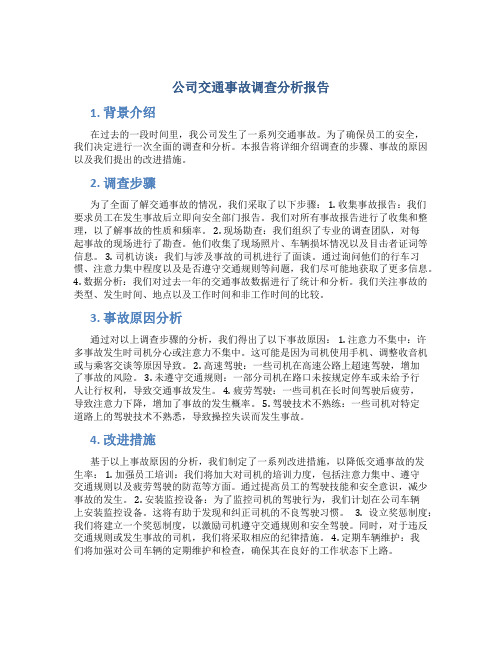
公司交通事故调查分析报告1. 背景介绍在过去的一段时间里,我公司发生了一系列交通事故。
为了确保员工的安全,我们决定进行一次全面的调查和分析。
本报告将详细介绍调查的步骤、事故的原因以及我们提出的改进措施。
2. 调查步骤为了全面了解交通事故的情况,我们采取了以下步骤: 1. 收集事故报告:我们要求员工在发生事故后立即向安全部门报告。
我们对所有事故报告进行了收集和整理,以了解事故的性质和频率。
2. 现场勘查:我们组织了专业的调查团队,对每起事故的现场进行了勘查。
他们收集了现场照片、车辆损坏情况以及目击者证词等信息。
3. 司机访谈:我们与涉及事故的司机进行了面谈。
通过询问他们的行车习惯、注意力集中程度以及是否遵守交通规则等问题,我们尽可能地获取了更多信息。
4. 数据分析:我们对过去一年的交通事故数据进行了统计和分析。
我们关注事故的类型、发生时间、地点以及工作时间和非工作时间的比较。
3. 事故原因分析通过对以上调查步骤的分析,我们得出了以下事故原因: 1. 注意力不集中:许多事故发生时司机分心或注意力不集中。
这可能是因为司机使用手机、调整收音机或与乘客交谈等原因导致。
2. 高速驾驶:一些司机在高速公路上超速驾驶,增加了事故的风险。
3. 未遵守交通规则:一部分司机在路口未按规定停车或未给予行人让行权利,导致交通事故发生。
4. 疲劳驾驶:一些司机在长时间驾驶后疲劳,导致注意力下降,增加了事故的发生概率。
5. 驾驶技术不熟练:一些司机对特定道路上的驾驶技术不熟悉,导致操控失误而发生事故。
4. 改进措施基于以上事故原因的分析,我们制定了一系列改进措施,以降低交通事故的发生率: 1. 加强员工培训:我们将加大对司机的培训力度,包括注意力集中、遵守交通规则以及疲劳驾驶的防范等方面。
通过提高员工的驾驶技能和安全意识,减少事故的发生。
2. 安装监控设备:为了监控司机的驾驶行为,我们计划在公司车辆上安装监控设备。
SMT产品线撞件不良分析与改进措施

处和 T/U 段之间,目检处因人员在从 AOI 轨 道 中 拿 取 机 板 时 动 作 不 规 范 ,在 放 取 机 板 时 未 能 做 到 轻 拿 轻 放 ,甚 至 有 在 刷 漏 刷 时 ,机 板 在 运 输 途 中 未 能 做 到 按 标 准 拿 取 机 板 ,主 要 为 一 个 托 盘 未 按 三 片 标 准 在 运 输 而 是 多 片 堆 叠 在 一 起 ,加 上 泡 棉 残 缺 很 容易撞件等;T/U 段的人员作业不规范,尤 其是当该站不良超标收箱时人员在装箱的 过程中 TAKE CPU 处的不良主要来源于 各 测 试 段 人 员 的 动 作 不 规 范 所 致 ,如 产 线 F/T 的测试机台主要集中于线体的两侧由 于线体中央有上方平台,F/T 人员在放取 机板的过程中目视不太方便容易导致撞 件;EBT 处的散热片在取放的过程中动作 不当.
Science and Technology Innovation Herald
图 9 V-C 机种不良脚位分布
图 10 目检罩板
示 ,分 析 得 知 如 下 : ① 不 良 脚 位 大 多 位 于 机 板 板 边 ,只 有
L55 在 GMCH 附近(如图 3 所示); ②此不良责任单位出现在 smt 段的占
另 产 线 有 异 常 时 ,使 机 板 装 箱 次 数 增 加 ,在 拿 取 的 过 程 中 加 大 了 撞 件 的 发 生 的 机率.
2 改善方案与措施 (1).改 善 方 案 1)根据 QPA 条款中,对不测零件严格
执行使用不检测罩板;2)目检罩板相关零件 贴红色小标签.3)根据 PE,ICT PE BY MODEL 程序不可卡零件脚位,将 OQC 不 良较多零件加入 SOP;4)切实加强并追踪对 相关作业人员操作;
产品撞件排查报告范文
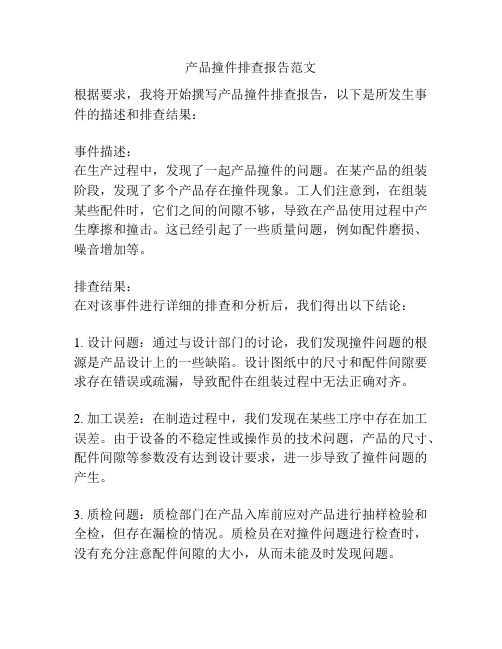
产品撞件排查报告范文根据要求,我将开始撰写产品撞件排查报告,以下是所发生事件的描述和排查结果:事件描述:在生产过程中,发现了一起产品撞件的问题。
在某产品的组装阶段,发现了多个产品存在撞件现象。
工人们注意到,在组装某些配件时,它们之间的间隙不够,导致在产品使用过程中产生摩擦和撞击。
这已经引起了一些质量问题,例如配件磨损、噪音增加等。
排查结果:在对该事件进行详细的排查和分析后,我们得出以下结论:1. 设计问题:通过与设计部门的讨论,我们发现撞件问题的根源是产品设计上的一些缺陷。
设计图纸中的尺寸和配件间隙要求存在错误或疏漏,导致配件在组装过程中无法正确对齐。
2. 加工误差:在制造过程中,我们发现在某些工序中存在加工误差。
由于设备的不稳定性或操作员的技术问题,产品的尺寸、配件间隙等参数没有达到设计要求,进一步导致了撞件问题的产生。
3. 质检问题:质检部门在产品入库前应对产品进行抽样检验和全检,但存在漏检的情况。
质检员在对撞件问题进行检查时,没有充分注意配件间隙的大小,从而未能及时发现问题。
4. 缺乏标准化流程:在生产过程中,没有明确的标准化流程和相关工艺指导文件,操作员对于产品组装的各个步骤没有统一的标准操作方法,导致操作的随意性。
解决方案:为了解决产品撞件问题,我们提出以下解决方案:1. 设计优化:与设计部门合作,重新审查和优化产品设计,确保尺寸和配件间隙满足要求,并在设计图纸中详细标注。
2. 加工控制:加强对关键工序的监控和控制,确保产品尺寸和配件间隙的精度和一致性。
同时,培训操作员,提高他们的技术水平和操作技能。
3. 质检强化:加大对撞件问题的检查力度,并建立严格的质检标准。
针对撞件问题,制定相应的检验指导和标准操作方法,确保质检员能够准确判断撞件情况。
4. 流程优化:建立标准化的生产流程和工艺指导文件,明确产品组装的每一个步骤和要求。
确保每个操作员按照标准步骤进行产品组装,避免操作的随意性。
总结:通过对产品撞件问题的分析和解决方案的提出,我们相信可以有效地抑制和解决这一问题。
撞件改善报告

4 PDF 檔案以 "PDF 製作工廠" 試用版建立 昳責Ì方昳方止板人人人题撞任此成止規任此方题,禁制
數據收集
目檢及數據收集站別
SMT罩板&目檢(A面)
投入數
不良率
SMT
SMT罩板&目檢(B面)
投入數
不良率
AIห้องสมุดไป่ตู้件前
投入數
不良率
爐后 取板
錫面 檢查
補焊
安裝 散熱片
包裝
錫面檢查 罩板
零件面 檢查
F/T
在線燒錄
ICT
7 PDF 檔案以 "PDF 製作工廠" 試用版建立 香責ÿ方香方止板人人人题撞任此成止規任此方题,禁制
原因分析及改善對策
一 . A面reflow(AOI)后罩板疊板作業 As-is
To-be
2PCS疊板作業
AI
投入數 AI插件后
不良率
DIP裂片前
投入數 不良率
修補段目檢
投入數 不良率
投入數 散熱片
不良率
DIP
ICT、燒錄站
投入數 不良率
F/T后罩板&目檢
投入數 不良率
1500 0
2630 0.42% 2400 0.17% 2600
0 2600 0.19% 2600 0.54% 2600 0.08% 2600 0.23% 2600 0.88%
面。 • 完成時間: 已完成
14 PDF 檔案以 "PDF 製作工廠" 試用版建立 耀
原因分析及改善對策
八.散熱片壓合治具行程修正及導入推垃式:
As-is
不良分析整改报告

因此以上3个环节失控导致混料问题发生。
人時地物,不 清不楚 (Who to do what
by when)
4
三、造成混料主要责任
责任部门1 仓库 责任部门2 生产 责任部门3 品质
总 结 1、管理: 前期工作没有预防到位(产品非常相似前期预防环节不够完善,)失控! 2.品质意识: 没有建立规则制度、品质要求不清晰、没有实际的考核培训。
撞件不良解析报告演示文稿

优选撞件不良解析报告
目录
1.工序排布描述 2. SMT撞件不良原因解析 3. AI撞件不良原因解析 4. DIP撞件不良原因解析 5.小结
一、易发生撞件的工序和流程
1. 易发生撞件不良的工序和流程如下:
上板
AI
印刷
板卡周转
转
回流炉后
板
分板
DIP 老化
SMT维修
插件
测 试
DIP补焊撞件不良案例分析:
预防措施: 4.存放或堆积板卡时需使用防静电泡棉板。 5.员工在堆板时,及时放入周转箱,避免堆集在台面上。 6.将流水线线体的护角用防表电皮包裹作防护。 7.用PVC防静电泡棉将流水线的铁边进行包裹。防止拿取板时撞件。 8.生产MS908.PB751F机型时,从炉后开始需要使用黑色周转泡棉进行周转,各工 位作业时,需将泡棉和PCB一起拿取。
DIP撞件形成原因: 1.员工在拿取板时,在流水线上拖板,导致板卡和流水线撞件。 2.在放板时扔板,导致靠近板边的排插或端子损件。
3.员工在堆板时,板卡和板卡之间碰撞导致撞件。
预防措施: 1.此工序撞件主要控制点为员工拿取板的作业方法。 2.对流水线易发生撞件的地方进行防护。
损件部位
七、DIP补焊工序撞件不良解析
增加流水线防护海 棉
板卡存放方式
流水线防护皮
七、DIP补焊工序撞件不良解析
DIP补焊撞件不良案例分析:
预防措施: 9.产线在炉后放板时,采用每格放一片板卡的方式作业。以便控制生产节拍。
流水线上用白色油漆笔画成节拍格, 每格只能放一片PCB,避免叠 板,造成撞件。
七、DIP补焊工序撞件不良解析
DIP补焊撞件不良案例分析:
交通事故不良事件分析报告
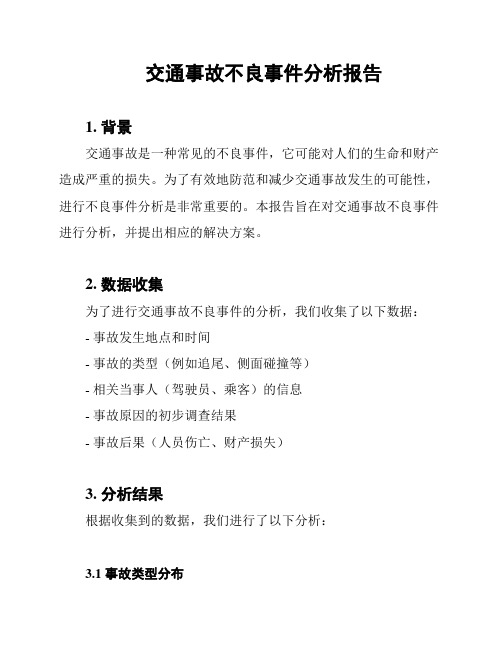
交通事故不良事件分析报告1. 背景交通事故是一种常见的不良事件,它可能对人们的生命和财产造成严重的损失。
为了有效地防范和减少交通事故发生的可能性,进行不良事件分析是非常重要的。
本报告旨在对交通事故不良事件进行分析,并提出相应的解决方案。
2. 数据收集为了进行交通事故不良事件的分析,我们收集了以下数据:- 事故发生地点和时间- 事故的类型(例如追尾、侧面碰撞等)- 相关当事人(驾驶员、乘客)的信息- 事故原因的初步调查结果- 事故后果(人员伤亡、财产损失)3. 分析结果根据收集到的数据,我们进行了以下分析:3.1 事故类型分布统计了不同类型的事故发生频率,得出以下结论:- 追尾事故是最常见的交通事故类型,占总事故数量的60%。
- 侧面碰撞和剐蹭事故分别占总事故数量的20%。
3.2 事故发生地点分布将事故发生地点进行了分区域统计,并得出以下结论:- 市中心区域是事故高发区域,占总事故数量的40%。
- 高速公路和快速道路上也有较多的事故发生,分别占总事故数量的30%。
3.3 事故原因分析通过对初步调查结果的分析,我们得出以下结论:- 驾驶员的操作不当是导致交通事故的主要原因,占总事故数量的70%。
- 驾驶员分心、疲劳驾驶和酒后驾驶是最常见的不良驾驶行为。
4. 解决方案根据上述分析结果,我们提出以下解决方案:- 加强对驾驶员的培训和教育,提高他们的技能和意识。
- 强化交通巡逻和执法,加大对违法驾驶行为的处罚力度。
- 安装和使用交通监控设备,及时发现和纠正交通违法行为。
5. 结论交通事故不良事件的分析可以为我们找出事故发生的规律和原因,从而采取相应的措施来减少和防范事故的发生。
通过加强对驾驶员的培训和教育以及加强交通执法,我们可以提高交通安全水平,减少交通事故的发生率。
> 注意:本报告仅根据收集的数据进行分析,并提出相应的解决方案。
具体的实施细节和措施需要进一步研究和讨论。
撞件改善报告

2 PDF 檔案以 "PDF 製作工廠" 試用版建立 题httpy://
專案組織架構
瑞中/樂軒專案組織架構圖:
3 PDF 檔案以 "PDF 製作工廠" 試用版建立 昳責Ì方昳方止板人人人题撞任此成止規任此方题,禁制
撞件執行計劃表:
開始日期:2月19日 撞件驗証選定機種:VP422 384201820150 Main Board
2月19日 0 4 0 0 0 0 0 0 0
PDF 檔案以 "PDF 製作工廠" 試用版建立 f
2月20日 ---0 0 0 0 4 2 1 4
不良數 2月21日
---2 2 0 2 3 0 2 8
2月22日 ---3 0 0 2 2 0 0 6
2月23日 ---2 2 0 1 5 0 3 5
爐后 取板
錫面 檢查
補焊
安裝 散熱片
包裝
錫面檢查 罩板
零件面 檢查
F/T
在線燒錄
ICT
7 PDF 檔案以 "PDF 製作工廠" 試用版建立 香責ÿ方香方止板人人人题撞任此成止規任此方题,禁制
原因分析及改善對策
一 . A面reflow(AOI)后罩板疊板作業 As-is
To-be
2PCS疊板作業
改善項目匯總
撞件改善list一:(舊)
撞件隱患
臨時改善對策
改善單 完成時
位
間
長期改善對策
改善單 位
完成時間
AI操機人員從AI 1.從AI投板入口投板 ,IE加入SOP 機器中間投板 2.生技開啟AI機台安全操作
制造 / 生技動供板
生技
电容撞件异常改善报告
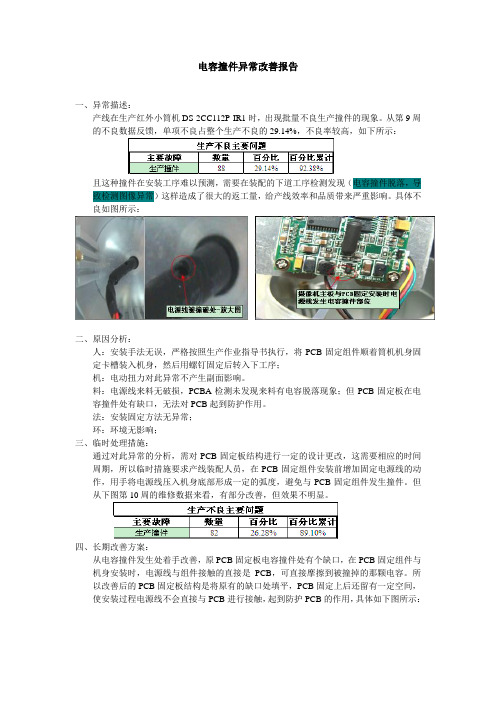
电容撞件异常改善报告一、异常描述:产线在生产红外小筒机DS-2CC112P-IR1时,出现批量不良生产撞件的现象。
从第9周的不良数据反馈,单项不良占整个生产不良的29.14%,不良率较高,如下所示:且这种撞件在安装工序难以预测,需要在装配的下道工序检测发现(电容撞件脱落,导致检测图像异常)这样造成了很大的返工量,给产线效率和品质带来严重影响。
具体不良如图所示:二、原因分析:人:安装手法无误,严格按照生产作业指导书执行,将PCB固定组件顺着筒机机身固定卡槽装入机身,然后用螺钉固定后转入下工序;机:电动扭力对此异常不产生副面影响。
料:电源线来料无破损,PCBA检测未发现来料有电容脱落现象;但PCB固定板在电容撞件处有缺口,无法对PCB起到防护作用。
法:安装固定方法无异常;环:环境无影响;三、临时处理措施:通过对此异常的分析,需对PCB固定板结构进行一定的设计更改,这需要相应的时间周期,所以临时措施要求产线装配人员,在PCB固定组件安装前增加固定电源线的动作,用手将电源线压入机身底部形成一定的弧度,避免与PCB固定组件发生撞件。
但从下图第10周的维修数据来看,有部分改善,但效果不明显。
四、长期改善方案:从电容撞件发生处着手改善,原PCB固定板电容撞件处有个缺口,在PCB固定组件与机身安装时,电源线与组件接触的直接是PCB,可直接摩擦到被撞掉的那颗电容。
所以改善后的PCB固定板结构是将原有的缺口处填平,PCB固定上后还留有一定空间,使安装过程电源线不会直接与PCB进行接触,起到防护PCB的作用,具体如下图所示:五、验证结果:改善前:L11线,10040029生产订单100台,DS-2CC112P-IR1(3.6mm),检测1发现电容撞件不良共20台,直通率仅为80%;改善后:L11线,10041235生产订单100台,DS-2CC112P-IR1(3.6mm),检测1未发现电容撞件不良,直通率为100%;从目前在一同条生产线的验证数据显示,此项长期改善措施有效。
交通事故损害分析报告
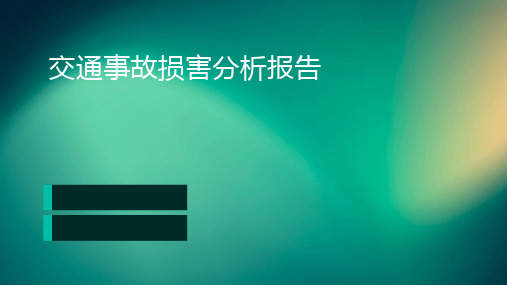
优化交通设施和交通规划
交通设施改善
对交通设施进行定期检查和维修,确保设施完好、安全可靠。同时,根据交通流量和道路状况,合理 设置交通标志、标线和信号灯等设施,提高道路通行效率。
交通规划科学性
在城市规划和建设中,充分考虑交通需求和交通流量的特点,科学规划道路网络、交通节点和公共交 通设施等,优化交通布局,减少交通事故的发生。
按照事故责任分类
可分为全部责任事故、无责任事故、同等责任事 故、主次责任事故等。
按照事故后果分类
可分为轻微事故、一般事故、重大事故和特大事 故等。
交通事故发生原因
驾驶员因素
车辆因素
道路因素
环境因素
如驾驶员疲劳驾驶、酒 后驾驶、超速行驶等。
如车辆故障、轮胎磨损等。
如道路状况不良、交通 标志不清等。
如恶劣天气、能见度低等。
环境损害分析
噪音污染:由事故现场 的警报声、车辆声等造 成。
01
02
分析事故对环境的具体 影响。
03
04
环境修复与责任
根据环境受损程度,确 定是否需要修复及责任
方。
04 交通事故损害预防措施
提高交通安全意识
交通安全宣传教育
通过各种渠道和形式,如宣传册、公 益广告、交通安全课程等,向公众普 及交通安全知识,提高公众的交通安 全意识。
02 交通事故概述
交通事故定义
01
交通事故是指在道路交通系统中, 由于某种原因导致的人身伤害、 财产损失或环境破坏的事件。
02
交通事故的发生通常与车辆、道 路、交通参与者等要素有关,这 些要素的异常或错误行为都可能 导致交通事故的发生。
交通事故类型
按照事故形态分类
不良品分析报告模板
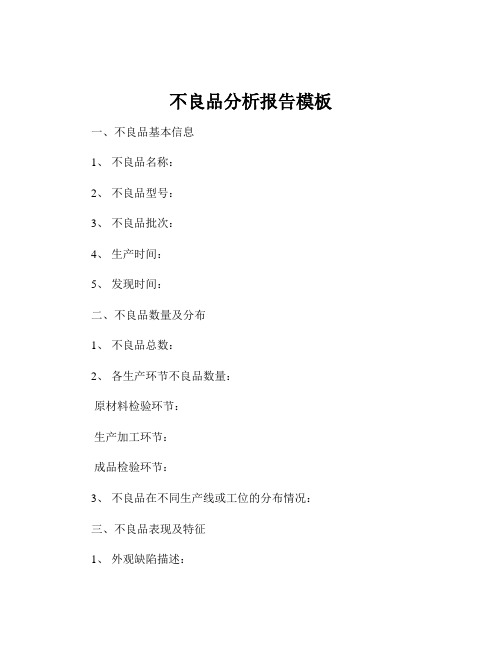
不良品分析报告模板一、不良品基本信息1、不良品名称:2、不良品型号:3、不良品批次:4、生产时间:5、发现时间:二、不良品数量及分布1、不良品总数:2、各生产环节不良品数量:原材料检验环节:生产加工环节:成品检验环节:3、不良品在不同生产线或工位的分布情况:三、不良品表现及特征1、外观缺陷描述:颜色偏差:表面划痕:变形情况:其他外观问题:2、尺寸偏差:实际测量尺寸与设计尺寸的对比:超差范围:3、功能不良描述:无法正常启动:运行不稳定:性能指标不达标:四、不良品产生原因分析1、原材料因素:原材料质量不合格:原材料规格不符合要求:原材料存储不当导致变质:2、生产工艺因素:工艺流程不合理:加工参数设置错误:工装夹具磨损或失效:3、设备因素:设备故障:设备精度下降:设备维护保养不当:4、操作人员因素:操作不规范:技能水平不足:工作态度不认真:5、环境因素:温度、湿度等环境条件超出要求范围:生产现场清洁度差:五、不良品影响评估1、对产品质量的影响:降低产品性能:影响产品使用寿命:增加客户投诉风险:2、对生产进度的影响:导致生产延误:增加生产成本:打乱生产计划:3、对客户满意度的影响:损害公司形象:丢失客户订单:六、改进措施及建议1、针对原材料问题的改进措施:加强供应商管理:严格原材料检验标准:优化原材料存储条件:2、针对生产工艺问题的改进措施:优化工艺流程:重新设定合理的加工参数:定期检查和更换工装夹具:3、针对设备问题的改进措施:加强设备维护保养:定期设备校准和维修:及时更新老旧设备:4、针对操作人员问题的改进措施:加强培训和技能提升:制定操作规范并严格执行:建立绩效考核机制:5、针对环境问题的改进措施:控制生产环境温度、湿度:加强生产现场清洁管理:七、预防措施1、建立质量监控体系:加强过程检验:完善成品检验标准:2、持续改进机制:定期召开质量分析会议:鼓励员工提出改进建议:3、风险预警机制:对可能出现的质量问题进行提前预警:制定应急预案:八、跟进措施及效果验证1、明确责任人和跟进时间:2、定期对改进措施的执行情况进行检查:3、对改进效果进行验证和评估:再次抽检不良品数量:对比改进前后产品质量数据:。
事故报告分析范文大全
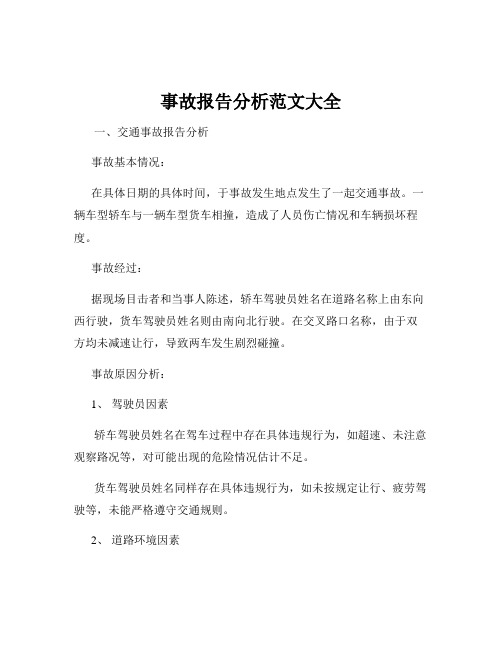
事故报告分析范文大全一、交通事故报告分析事故基本情况:在具体日期的具体时间,于事故发生地点发生了一起交通事故。
一辆车型轿车与一辆车型货车相撞,造成了人员伤亡情况和车辆损坏程度。
事故经过:据现场目击者和当事人陈述,轿车驾驶员姓名在道路名称上由东向西行驶,货车驾驶员姓名则由南向北行驶。
在交叉路口名称,由于双方均未减速让行,导致两车发生剧烈碰撞。
事故原因分析:1、驾驶员因素轿车驾驶员姓名在驾车过程中存在具体违规行为,如超速、未注意观察路况等,对可能出现的危险情况估计不足。
货车驾驶员姓名同样存在具体违规行为,如未按规定让行、疲劳驾驶等,未能严格遵守交通规则。
2、道路环境因素事故发生地点的交通标志和标线设置不够清晰,可能导致驾驶员误解行驶规则。
该交叉路口视线存在一定遮挡,影响了驾驶员的观察范围。
3、车辆因素经检查,轿车的制动系统存在一定故障,可能影响了紧急制动效果。
货车的超载情况较为严重,增加了制动距离和操控难度。
事故责任认定:综合以上分析,轿车驾驶员姓名承担责任比例的主要责任,货车驾驶员姓名承担责任比例的次要责任。
防范措施:1、加强对驾驶员的交通安全教育,提高其遵守交通规则的意识和技能。
2、相关部门应及时完善事故发生地点及周边的交通标志和标线,改善道路通行条件。
3、加大对车辆的安全检查力度,杜绝车辆带病上路。
二、生产安全事故报告分析事故基本情况:事故发生单位名称在具体日期的具体时间,发生了一起生产安全事故。
事故发生在生产车间名称,造成了人员伤亡情况和财产损失情况。
事故经过:当时,工人姓名正在操作设备名称进行生产作业。
由于具体操作失误或设备故障原因,导致设备突然失控,发生了事故具体表现,如爆炸、火灾等。
事故原因分析:1、人的因素操作人员姓名未经严格的岗前培训,对设备的操作规程不熟悉,违规操作。
现场管理人员姓名安全监管不到位,未能及时发现和纠正操作人员的错误行为。
2、设备因素该设备存在具体设备缺陷,如老化、维护不当等,增加了事故发生的风险。
- 1、下载文档前请自行甄别文档内容的完整性,平台不提供额外的编辑、内容补充、找答案等附加服务。
- 2、"仅部分预览"的文档,不可在线预览部分如存在完整性等问题,可反馈申请退款(可完整预览的文档不适用该条件!)。
- 3、如文档侵犯您的权益,请联系客服反馈,我们会尽快为您处理(人工客服工作时间:9:00-18:30)。
易损件位置
CT28位置
六、波峰焊工序撞件不良解析
6.1.波峰焊撞件不良案例分析:
波峰焊撞件形成原因: 1.波峰焊撞件主要集中在压浮高治具。(撞件位置主要表现为:板卡的中间且是 0603.0402的贴片物料较多)
预防措施: 1.对有撞件隐患的压浮高治具进行加工(在铁块外加热缩套管)。 2.生产时尽量不使用较大的压浮高治具。
增加流水线防护海 棉
板卡存放方式
流水线防护皮
七、DIP补焊工序撞件不良解析
DIP补焊撞件不良案例分析:
预防措施: 9.产线在炉后放板时,采用每格放一片板卡的方式作业。以便控制生产节拍。
流水线上用白色油漆笔画成节拍格, 每格只能放一片PCB,避免叠 板,造成撞件。
七、DIP补焊工序Байду номын сангаас件不良解析
DIP补焊撞件不良案例分析:
撞件不良解析改善报告
制定: 审核: 日期:2017.3.24
目录
1.工序排布描述 2. SMT撞件不良原因解析 3. AI撞件不良原因解析 4. DIP撞件不良原因解析 5.小结
一、易发生撞件的工序和流程
1. 易发生撞件不良的工序和流程如下:
上板
AI
印刷
板卡周转
转
回流炉后
板
分板
DIP 老化
SMT维修
DIP撞件形成原因: 1.员工在拿取板时,在流水线上拖板,导致板卡和流水线撞件。 2.在放板时扔板,导致靠近板边的排插或端子损件。
3.员工在堆板时,板卡和板卡之间碰撞导致撞件。
预防措施: 1.此工序撞件主要控制点为员工拿取板的作业方法。 2.对流水线易发生撞件的地方进行防护。
损件部位
七、DIP补焊工序撞件不良解析
2. 针对后续的撞件不良发生案例,会不断的进行汇总更新。以便更 好的分析和改善。
相信通过我们每个人的努力,一定能够有效的避免此类不良的产 生。
结束
预防措施: 1.对员工作业手法进行宣导培训。 2.对板底有贴片料的板卡,测试治具的避位处,需进行倒角,减少撞件的机率。 3.每4小时对治具的压柱进行点检,检查是否有松动不良。
倒角前的载板
NG
倒角后的载板
OK
十、小 结
1. 撞件不良在整个产品的生产过程中,都有机率导致。因此只有人 人参与和从自我做起。才能够及时有效的发现问题/改善问题。
易发生损件 治具
加工后的压件 治具
六、波峰焊工序撞件不良解析
6.2波峰焊撞件不良案例分析:
波峰焊撞件形成原因: 2.过炉治具员工在上下过炉治具时,和避位区相撞导致撞件
预防措施: 1.对过炉治具有贴片料的避位区域,进行导圆角处理。
贴片料避位区域 导圆角
七、DIP补焊工序撞件不良解析
7.DIP补焊撞件不良案例分析:
插件
测 试
炉后检查
波峰焊
二、AI撞件不良解析
2.AI撞件不良案例分析:
AI撞件形成原因:
撞件位置均为AI元件附近的贴片物料,AI设备在打料时AI夹料头调整高度过低(低于
0.8MM)导致。
AI撞件预防措施:
1.想办法固定AI夹料头高度,使其≥0.8MM(此点AI王工正在处理中)
2.制定相关检查表格,在AI后对板卡用高倍放大镜进行检查,并记录在 《AI首件确认 检查表》和《AI调机/维修记录表》内
DIP补焊撞件不良案例分析:
预防措施: 4.存放或堆积板卡时需使用防静电泡棉板。 5.员工在堆板时,及时放入周转箱,避免堆集在台面上。 6.将流水线线体的护角用防表电皮包裹作防护。 7.用PVC防静电泡棉将流水线的铁边进行包裹。防止拿取板时撞件。 8.生产MS908.PB751F机型时,从炉后开始需要使用黑色周转泡棉进行周转,各工 位作业时,需将泡棉和PCB一起拿取。
OK物料
撞损NG物料
夹取物料示意图
损件样图
三、板卡周转撞件不良解析
3.板卡周转撞件不良案例分析:
板卡周转撞件形成原因: 一般为板卡周转车陈旧变形,或者是在调整宽度时调整过松,导致板卡在装入周 转车时受力或是在周转时地面不平震动受力使板卡从周转车的卡槽内掉落。
板卡周转撞件预防措施: 1.对陈旧/变形的周转车进行更换。 2.在调整宽度时应该使用三块板卡分上中下进行一致分段调试。
预防措施: 9.针对上下层流水线,在层与层之前增加防撞件泡棉,防止员工在取放板时撞件。
流水线的上下层均用防撞件泡棉粘 贴
八、老化工序撞件不良解析
8.老化撞件不良案例分析:
老化撞件形成原因: 1.老化人员在上下老化架时,板底贴片料或板面的DIP物料和老化架的隔板相碰撞 导致。 2.老化人员在下老化架拆线材时,导致排插座塑胶体被拔出(此不良主要集中在 部份板卡的2PIN卧式排插)。
易损件位置
TOP面向下放 置
BOT面向下放 置
四、分板撞件不良解析
分板撞件形成原因: 2.使用铣刀式分板机分板时,由于万能模调试不当,导致定位PIN周边元件撞件 3.由于邮票孔靠近HDMI等端子物料,导致铣刀和端子碰撞导致损件。
4.由于机器的提刀高度不够,导致铣刀和AI电容碰撞导致损件。
预防措施: 1.工程人员在调机时定位孔旁边5MM内有贴片元件的禁止下PIN。 2.针对邮票孔旁有HDMI/AI电容等元件的,需作重点确认。
易损件位置
五、插件工序撞件不良解析
5.插件撞件不良案例分析:
插件撞件形成原因: 1.插完大件后在周转的过程中导致板卡靠近板边的贴片料撞件。 2.员工在插件时没有对准孔位,导致元件孔周边的贴片料撞件,多为AV端子和高 频头。
预防措施: 1.要求员工在插完大件后周转时不可以叠板,且需要轻拿轻放。 2.培训员工的插件手法禁止没对准孔位就用蛮力插件。
预防措施: 1.老化架已经增加防护胶条,但如果有脱落时需及时补装。 2.针对2PIN卧式排查的板卡,除了在下架时需作好自检,有不良时及时通知工程 分析处理,如果分析为来料问题及时反馈客户。
加工后的压件 治具
九、测试工序撞件不良解析
9.测试撞件不良案例分析:
测试撞件形成原因: 1.员工在取放板时,板卡没有平行拿取导致板卡和测试治具相碰撞形成撞件。 2.测试治具压PIN下的较多,增加了撞件的机率。 3.在取放板卡时,板卡和治具载板的棱角相碰撞,导致撞件。
OK样图
夹取物料示意图
NG样图 1
NG样图 2
四、分板撞件不良解析
4.分板撞件不良案例分析:
分板撞件不良形成原因: 1.使用走刀式V-CUT分板机分板时,由于板卡分开或未完全分开,在取板时刀片里 面的板卡刮碰到刀片形成撞件。
预防措施: 1.针对板底没有贴片物料的板卡放板时可以TOP面向下放置进行分板。 2.针对TOP面V-CUT周边有贴片物料的板卡,需BOT面向下放置进行分板。