齿轮精密锻造的诸多优点.
齿轮件锻造比8.8

齿轮件锻造比8.8全文共四篇示例,供读者参考第一篇示例:齿轮件在现代机械工业中起着至关重要的作用,它们被广泛应用于汽车、航空航天、军工、船舶等领域。
而在齿轮件的生产过程中,锻造是一种常见的制造方法。
锻造是通过将金属加热至一定温度后,施加一定压力将金属进行变形,从而获得所需形状和尺寸的工件。
而对于齿轮件锻造比8.8来说,这是一种特定的材料强度等级,适用于特定的工程要求和应用场景。
让我们来了解一下什么是齿轮件锻造比8.8。
锻造比是指材料在锻造过程中所受的应变比,即工件经过锻造后的形变程度。
比如齿轮件锻造比8.8,表示这种工件在锻造时将受到8.8倍的形变。
这个比例可以影响工件的力学性能,包括硬度、强度、韧性等。
对于齿轮件来说,锻造比的选择对于工件的使用寿命和性能至关重要。
对于齿轮件来说,锻造比8.8通常适用于中等强度和中等应变的情况。
这种锻造比可以保证工件在生产过程中具有良好的韧性和强度,同时也可以满足工程要求。
在实际生产中,选择适合的锻造比可以提高工件的质量和性能,同时也可以降低生产成本。
齿轮件的锻造比选择需要考虑多个因素,包括材料的性质、工件的形状和尺寸、使用环境等。
一般来说,对于高强度和大尺寸的齿轮件,通常会选择较大的锻造比,以确保工件具有足够的强度和硬度。
而对于小尺寸和低强度要求的工件,则可以选择较小的锻造比,以获得更好的韧性性能。
除了锻造比以外,锻造过程中的温度和压力也是影响齿轮件质量的重要因素。
适当的加热温度和施加压力可以确保金属在变形过程中具有良好的流动性和变形性能,从而获得良好的成形效果。
合理控制锻造过程中的温度和压力也可以避免产生裂纹和变形等质量问题。
在齿轮件的锻造过程中,还需要注意选择合适的锻造设备和工艺流程。
现代机械工业中广泛应用的数控锻造设备可以提高生产效率和产品质量,同时也可以实现复杂形状和精度要求的工件生产。
而严格控制生产流程和检测手段也可以保证工件的质量和性能符合要求。
齿轮件锻造比8.8是一种常见的锻造工艺参数,适用于中等强度和应变的齿轮件生产。
齿轮特点及应用

齿轮特点及应用齿轮是一种常见的机械传动元件,具有许多独特的特点和广泛的应用。
下面将详细介绍齿轮的特点及其应用。
一、齿轮的特点1. 传动效率高:齿轮传动的效率通常在95%以上,高于其他传动方式,如皮带传动和链条传动。
这是因为齿轮传动的接触面积大,摩擦损失小,能够有效地传递动力。
2. 传动精度高:齿轮的制造工艺相对较为复杂,但制造出来的齿轮具有较高的精度。
齿轮的齿形准确,齿距均匀,能够保证传动的准确性和稳定性。
3. 传动比可调:通过改变齿轮的齿数,可以实现不同的传动比。
这使得齿轮传动在不同的应用场合中具有灵活性和可调性。
4. 传动平稳:齿轮传动的齿面接触是点对点的,传动过程中没有滑动,因此传动平稳,噪音小。
5. 承载能力强:齿轮的齿面接触面积大,能够承受较大的载荷。
同时,齿轮的齿形设计合理,能够分散载荷,提高承载能力。
6. 传动方向可变:通过组合不同类型的齿轮,可以实现不同的传动方向,如平行轴传动、垂直轴传动、交叉轴传动等。
7. 传动稳定性好:齿轮传动的齿面接触面积大,摩擦力均匀分布,能够保证传动的稳定性和可靠性。
二、齿轮的应用1. 机械传动:齿轮广泛应用于各种机械传动系统中,如汽车变速器、工程机械、船舶、飞机等。
齿轮传动能够实现不同转速和扭矩的传递,满足不同工况下的需求。
2. 机床:齿轮是机床传动系统中的重要组成部分。
例如,齿轮传动用于车床、铣床、磨床等机床上,实现工件的旋转和进给运动。
3. 电动机:齿轮传动常用于电动机的传动系统中,如减速器。
通过减速器的作用,能够将高速低扭矩的电动机输出转换为低速高扭矩的输出。
4. 电梯:齿轮传动是电梯系统中的核心部件。
电梯通过齿轮传动实现升降运动,保证乘客的安全和舒适。
5. 纺织机械:齿轮传动广泛应用于纺织机械中,如纺纱机、织布机等。
齿轮传动能够实现纺织机械的高速运转和精确控制。
6. 机器人:齿轮传动是机器人关节传动的常用方式。
通过齿轮传动,能够实现机器人的精确定位和灵活运动。
齿轮类零件的精密锻造
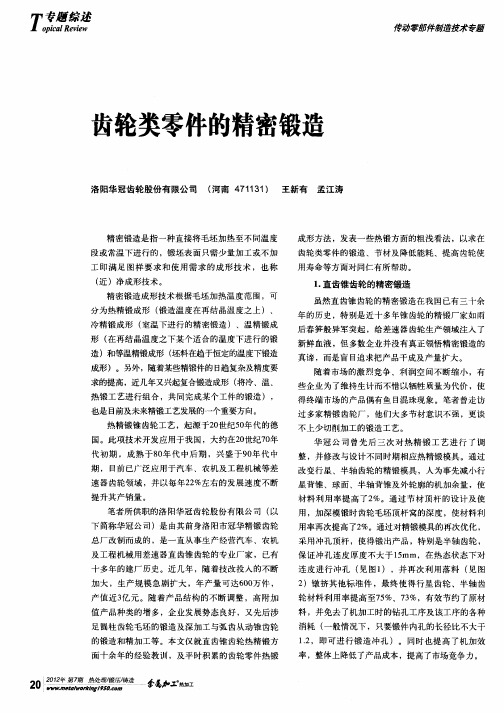
期 , 目前 已广泛 应 用 于 汽车 、农机 及 工 程机 械 等 差
华冠 公司 曾先后 三次对热 精锻工 艺进行 了调 整 ,并修改与设计不同时期相应热精锻模具 。通过 改变行星、半轴齿轮的精锻模具 ,人为事先减小行 星背锥 、球 面、半轴背锥及外轮廓的机加余量 ,使 材料利用率提高 了2 %。通过节材顶杆 的设计及 使 用 ,加深模锻时齿轮毛坯顶杆窝的深度 ,使材料利 用率再次提高了2 %。通过对精锻模具的再次优化 , 采用冲孔顶杆 ,使得锻出产 品,特别是半轴齿轮 ,
成形方法,发表一些热锻方面的粗浅看法 ,以求在 齿轮类零件的锻造 、节材及降低能耗 、提 高齿轮使 用寿命等方面对同仁有所帮助 。
1直齿锥齿轮 的精密 锻造 .
虽 然直 齿 锥 齿轮 的 精 密锻 造 在 我 国 已 有三 十 余
分为热精锻成形 ( 锻造温度在再结晶温度之上 )、 冷精锻成形 ( 室温下进行的精密锻造)、温精锻成 形 ( 在再结晶温度之下某个适合的温度下进行的锻 造)和等温精锻成形 ( 坯料在趋于恒定的温度下锻造
原 材 料 ,同时 因热 锻造 时 闭式 正 向挤 压 ,使得 热 态 金 属 按 照齿 模 型 腔 流动 充满 各 部位 ,在 切 削齿 形 时
2 直齿 圆柱齿轮 的精密锻造 .
直 齿 圆柱 齿 轮 一 般 都 是 按 常 规 机 加 工 艺 生 产 的 ,最 近 几 年 也有 部 分 企 业和 科 研 院 所 ,力 图通 过
Z 2 U 0
.
参 … 磊
,‘而— j加工 ,‘ 蜀 ’ ; ! I
齿 形 两 侧面 仅 留03 . m的精 切 余量 ,其 他机 加 _ ~04 a r
滚齿机在齿轮加工中的优势和不足
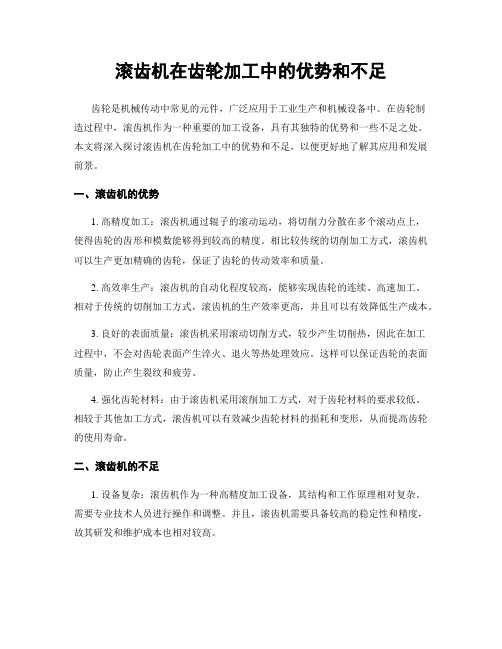
滚齿机在齿轮加工中的优势和不足齿轮是机械传动中常见的元件,广泛应用于工业生产和机械设备中。
在齿轮制造过程中,滚齿机作为一种重要的加工设备,具有其独特的优势和一些不足之处。
本文将深入探讨滚齿机在齿轮加工中的优势和不足,以便更好地了解其应用和发展前景。
一、滚齿机的优势1. 高精度加工:滚齿机通过辊子的滚动运动,将切削力分散在多个滚动点上,使得齿轮的齿形和模数能够得到较高的精度。
相比较传统的切削加工方式,滚齿机可以生产更加精确的齿轮,保证了齿轮的传动效率和质量。
2. 高效率生产:滚齿机的自动化程度较高,能够实现齿轮的连续、高速加工。
相对于传统的切削加工方式,滚齿机的生产效率更高,并且可以有效降低生产成本。
3. 良好的表面质量:滚齿机采用滚动切削方式,较少产生切削热,因此在加工过程中,不会对齿轮表面产生淬火、退火等热处理效应。
这样可以保证齿轮的表面质量,防止产生裂纹和疲劳。
4. 强化齿轮材料:由于滚齿机采用滚削加工方式,对于齿轮材料的要求较低。
相较于其他加工方式,滚齿机可以有效减少齿轮材料的损耗和变形,从而提高齿轮的使用寿命。
二、滚齿机的不足1. 设备复杂:滚齿机作为一种高精度加工设备,其结构和工作原理相对复杂。
需要专业技术人员进行操作和调整。
并且,滚齿机需要具备较高的稳定性和精度,故其研发和维护成本也相对较高。
2. 加工范围有限:滚齿机适用于一些特定齿轮的生产,例如直齿轮、斜齿轮等。
但是对于特殊的齿轮结构,如曲线齿轮、螺旋齿轮等,滚齿机的应用存在一定的局限性。
3. 非标准化加工难度大:针对某些非标准齿轮的加工,滚齿机可能无法满足生产要求,需要进行后续的手工加工和修整,增加了生产的工时和复杂度。
4. 能耗较高:滚齿机在高速加工时,由于需要驱动滚轮的运动,并且对工作台的定位和调整有严格要求,因此消耗的能量较大。
这也会导致生产成本的增加。
结论:滚齿机作为齿轮加工中的重要设备,在许多行业中得到了广泛应用。
它具有高精度加工、高效率生产、良好的表面质量和强化齿轮材料等许多优势。
滚齿机在高精度齿轮加工中的优势
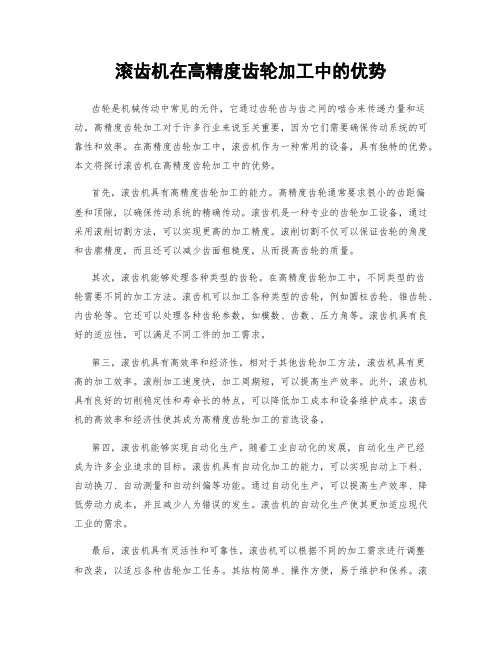
滚齿机在高精度齿轮加工中的优势齿轮是机械传动中常见的元件,它通过齿轮齿与齿之间的啮合来传递力量和运动。
高精度齿轮加工对于许多行业来说至关重要,因为它们需要确保传动系统的可靠性和效率。
在高精度齿轮加工中,滚齿机作为一种常用的设备,具有独特的优势。
本文将探讨滚齿机在高精度齿轮加工中的优势。
首先,滚齿机具有高精度齿轮加工的能力。
高精度齿轮通常要求很小的齿距偏差和顶隙,以确保传动系统的精确传动。
滚齿机是一种专业的齿轮加工设备,通过采用滚削切割方法,可以实现更高的加工精度。
滚削切割不仅可以保证齿轮的角度和齿廓精度,而且还可以减少齿面粗糙度,从而提高齿轮的质量。
其次,滚齿机能够处理各种类型的齿轮。
在高精度齿轮加工中,不同类型的齿轮需要不同的加工方法。
滚齿机可以加工各种类型的齿轮,例如圆柱齿轮、锥齿轮、内齿轮等。
它还可以处理各种齿轮参数,如模数、齿数、压力角等。
滚齿机具有良好的适应性,可以满足不同工件的加工需求。
第三,滚齿机具有高效率和经济性。
相对于其他齿轮加工方法,滚齿机具有更高的加工效率。
滚削加工速度快,加工周期短,可以提高生产效率。
此外,滚齿机具有良好的切削稳定性和寿命长的特点,可以降低加工成本和设备维护成本。
滚齿机的高效率和经济性使其成为高精度齿轮加工的首选设备。
第四,滚齿机能够实现自动化生产。
随着工业自动化的发展,自动化生产已经成为许多企业追求的目标。
滚齿机具有自动化加工的能力,可以实现自动上下料、自动换刀、自动测量和自动纠偏等功能。
通过自动化生产,可以提高生产效率、降低劳动力成本,并且减少人为错误的发生。
滚齿机的自动化生产使其更加适应现代工业的需求。
最后,滚齿机具有灵活性和可靠性。
滚齿机可以根据不同的加工需求进行调整和改装,以适应各种齿轮加工任务。
其结构简单、操作方便,易于维护和保养。
滚齿机的可靠性也是其优势之一,它可以保持较长时间的高精度运行,减少加工误差和故障的发生。
综上所述,滚齿机在高精度齿轮加工中具有明显的优势。
高精度齿轮传动系统申报材料

高精度齿轮传动系统申报材料摘要:1.高精度齿轮传动系统概述2.高精度齿轮传动系统的优势3.高精度齿轮传动系统的应用领域4.高精度齿轮传动系统的发展前景正文:一、高精度齿轮传动系统概述高精度齿轮传动系统,顾名思义,是一种具有高精度、高效率、高承载能力的齿轮传动装置。
它是通过精确的设计、制造和装配,实现齿轮之间的精确啮合,从而达到传递扭矩、转速等动力参数的目的。
在现代工业生产中,高精度齿轮传动系统被广泛应用于各种机械设备和传动系统中,以满足不同场合的高精度传动需求。
二、高精度齿轮传动系统的优势高精度齿轮传动系统具有以下几个显著优势:1.高精度:高精度齿轮传动系统采用精密加工和装配技术,使得齿轮之间的啮合误差尽可能小,从而保证了传动的精度。
2.高效率:高精度齿轮传动系统采用优化的齿轮设计,降低了摩擦和磨损,提高了传动效率。
3.高承载能力:高精度齿轮传动系统采用高强度、耐磨损的材料,使得齿轮具有较高的承载能力,可以满足各种工况下的传动需求。
4.稳定性能:高精度齿轮传动系统采用先进的润滑和密封技术,有效防止了润滑油泄漏和杂质进入,保证了传动系统的稳定性能。
三、高精度齿轮传动系统的应用领域高精度齿轮传动系统在以下领域有着广泛的应用:1.航空航天:在航空航天领域,高精度齿轮传动系统应用于飞行器、卫星等设备中,以满足其对高精度、高效率传动的需求。
2.精密机床:在精密机床领域,高精度齿轮传动系统可以提供高精度的轴向和径向定位,保证机床的加工精度。
3.机器人:在机器人领域,高精度齿轮传动系统可以实现关节部位的精确传动,提高机器人的运动精度和性能。
4.汽车:在汽车领域,高精度齿轮传动系统可以应用于变速器、驱动轴等部件,以提高汽车的传动性能和燃油经济性。
四、高精度齿轮传动系统的发展前景随着科学技术的不断进步,高精度齿轮传动系统在各个领域的应用将越来越广泛,发展前景十分广阔。
锻造齿轮

锻造齿轮、齿轮调质、齿轮淬火锻造齿轮属于锻件的一种,形状为车轮状,通常使用在起重机、矿车、火车、汽轮机、输送机等大型机械设备。
锻件质量高,密度好,使用寿命增长,大型机械设备的安全生得到了更好的保证。
是金属被施加压力,这种力量典型的通过使用铁锤或压力来实现。
锻件过程建造了精致的颗粒结构,并改进了金属的物理属性。
优质的车轮锻件可保证磁粉、UT超声波、机械性能、原材料化学成分合格。
山西永鑫生锻造有限公司提供。
中文名外文名生产商锻件forging 山西永鑫生锻造有限公司热处理车轮锻件在80年代,一般采用的是铸钢件,在生产过程中由于铸件处在气孔、夹杂,质量不稳定,安全有隐患。
在不断改进中,在逐渐的改为锻件,锻件再经过热处理组织细化,表面淬火,硬度加强,耐磨损。
热处理技术也不断改进,硬度层深度也可以达到20mm以上。
齿轮热踏面热处理硬度:HB320-380重点项目+出口要求高的硬度:HRC40以上、HRC50以上。
热处理开始是整体调质到HB240-280左右,然后再表面高频感应加热,使车轮锻件接触面硬度提高,耐磨损。
慢慢工艺改进,现在可以直接调质到HB320-380,一是成本节约、二是硬度深度提高,质量保证。
现在山西永鑫生锻造有限公司可以整体调质+表面喷水,使内孔腹板硬度保持在HB300以下,踏面硬度最高可达到HRC50以上,深度在20MM、。
常用材质:40Cr、42CrMo、50SiMn出口材质:4140、SSW-Q1R、CL60、C60齿轮锻件产品介绍:齿轮锻件山西永鑫生锻造可按图纸尺寸、化学成分、技术要求锻造、机加工、热处理、同步完成。
出口车轮锻件材质可咨询定制。
齿轮精锻工艺及模具探讨

齿轮精锻工艺及模具探讨摘要:本文介绍了一种新的齿轮精锻工艺和模具结构,对所得齿轮的精度、材料消耗、表面缺陷等与常规的铣齿、滚齿、插齿等常规切削加工方法进行了对比,精锻工艺具有明显的技术经济效益。
关键词:铣齿;剃齿;滚齿;插齿; 齿轮精锻1 引言生产实践中绝大部分齿轮的加工仍然采用切削加工,其机加工工作量是整个制造工作量的40~60%,其材料的利用率不超过35%,还占用大量的齿轮加工机床,在生产中造成大量的人力和金属材料的消耗。
运用塑性成形方法制造齿轮与切削加工相比,具有很多优点,如减少了金属消耗量,提高了劳动生产率,由于塑性成形加工可以最大限度地利用材料的纤维方向性,获得更加合理的金属内部组织分布,从而增强了齿轮的机械性能等等,能取得明显的技术经济效益和社会效益。
目前采用塑性成形制造齿轮的方法很多,如精锻、精冲、挤压、滚辗、轧制等。
用这些成型加工方法取代常规切削加工需要解决的关键问题是如何提高成形精度,减小齿廓精修加工量及减少金属的消耗量。
本课题设计了一种不带毛边槽的齿轮精锻模具。
凹模采用可分式结构,在机械压力机上,能进行批量生产。
该模具价格不高,结构简单,但如何更换模具的易磨损件,是提高经济效益的关键因素。
2 毛坯的制备和加热2.1毛坯重量的确定为了保证精锻时材料完全充满模膛,获得较高精度的锻件,并尽量减少材料流动阻力和流动距离,防止发生齿廓折断,合理确定毛坯下料重量十分重要,相关资料及工艺实践表明,对精锻后采用铣齿、插齿时毛坯重量偏差控制在5%以内,可保证所得齿轮精度在公差范围之内,且不会引起模具折断;若要采用剃齿、滚齿加工,则毛坯的重量偏差应超过1~1.5%,否则零件尺寸就可能超出规定的公差范围。
2.2 毛坯下料方法可由热轧圆钢在压力机上利用剪刃剪切下料;也可采用经光整加工的轧制毛坯,用全封闭的剪切模具下料。
2.3 毛坯预热可利用室式工频感应炉,对于是18CrMnTi的齿轮材料,加热温度在900~1100℃范围内。
齿轮精密锻造技术

汽车齿轮的精密锻造技术摘要:本文介绍了精密锻造成形在汽车齿轮制造中的应用,总结了各种齿形精密锻造的关键技术,特别提到分流锻造在齿形成形方面的应用。
关键词:齿轮锻造;精密锻造前言:齿轮精密锻造成形是一种优质、高效、低消耗的先进制造技术,被广泛地用于汽车齿形零件的大批量生产中。
随着精密锻造工艺和精密模具制造技术的进步,汽车齿轮和齿形类零件的生产已越来越多地采用精密锻造成形。
当前国外一台普通轿车采用的精锻件总质量已达到(40—45)Kg,其中齿形类零件总质量达10Kg以上。
精锻成形的齿轮单件质量可达1Kg以上、齿形精度达到(DIN) 7级。
随着汽车的轻量化要求和人们环保意识的增强,汽车齿轮制造业将更多地应用精锻成形技术。
一.伞齿轮的精锻成形1. 伞齿轮(锥齿轮)的热精锻成形(1)早期的伞齿轮精密锻造伞齿轮的精密锻造最早见于50年代德国的拜尔工厂,并在蒂森等公司得到广泛的应用(1)。
我国上海汽车齿轮厂等在70年代采用热精锻技术,成功进行了伞齿轮的精密锻造生产。
在当时社会主义大协作的环境下,伞齿轮的精锻技术很快在齿轮行业得到推广应用。
该技术的应用和发展得益于2项当时先进的技术:模具的放电加工技术和毛坯感应加热技术。
先淬火后加工的放电加工避免了模具淬火变形带来的齿廓误差;快速加热的中频感应加热解决了齿轮毛坯在加热过程中的氧化和脱碳问题,以上2项技术的应用使锻造成形的伞齿轮齿面达到无切削加工要求(图1、图2)。
图1.精锻成形的行星和半轴齿轮图2.精锻成形的汽车行星齿轮(2)锻造设备伞齿轮的锻造设备在国外一般使用热模锻压力机。
但在60-70年代的中国,热模锻压力机是非常昂贵的设备。
因此,国内企业普遍使用的锻造设备是双盘摩擦压力机(图3)。
该设备结构简单,价格便宜,很快成为齿轮精锻的主力设备。
但摩擦压力机技术陈旧、难以控制打击精度、而且能源利用率较低。
随着高能螺旋压力机和电动螺旋压力机的出现(图4),落后的摩擦压力机有被取代的趋势。
直齿锥齿轮精密锻造生产技术(上)
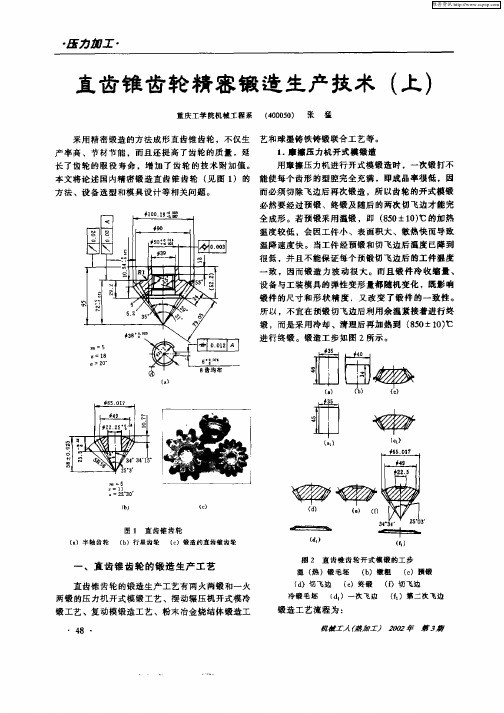
痫商
珂
(_ ]
—
c1 c)
/ ' ¥ 5 01' 6
. — — —
—
—
—
_
= :
11 3 2z- o—
r) b
( d
苎苎苎
《 ( I e £ )
:: I ::
J
。 ,
图 1 直 齿 锥 齿 轮
()半 轴 齿 轮 ( )行 星 齿 轮 () 锻 造 的 直 齿 雉 齿 轮 a b c
冷锻毛坯 ( 1 d)一改飞边 ( 毛)第二改飞边
锻造 工艺 流程 为 :
巍糖I凡( 热抽I ) 2 0 0 2年 第 3荨 9
维普资讯
下料一 加热 ( 5 8 0±1 ) 0 ℃一 镦粗 一预 锻一 切飞 锻之前 均需 要退火 软 化 ,连同热处 理正 火共 有三 次 边 一空冷 、喷砂清 理一 加 热到 ( 5 8 0±1 ) 0 ℃一 终锻 加热。瑞士摆动辗压机价格昂贵 ,总的设备投资额
维普资讯
直齿锥齿轮精密锻造生产技术 ( 上)
重 庆工学院机械工程系 (0O0 张 猛 4 O5 )
采 用精 密锻 造 的方 法 成形 直齿锥 齿 轮 ,不仅生 艺 和球 墨铸 铁铸锻 联合 工 艺等 。
产 率高 、节 材节 能 ,而且 还提 高 了齿 轮 的质 量 ,延
切 飞边后 的余 热 ,所 以初始 加热 温度 高 于两火 两锻 化 工件 的力 学性能 ,以粉末 称重 而严格 控 制预制坯 工 艺初 始加热 温 度 10 .而终 锻温度 定在 8 0 。 的质 量 ,压 制 出高 精 度的烧 结体 预制坯 ,进 行封 闭 0℃ 0℃ 10 的 温 度 问 隔 能够 满 足 前后 工 步 的 温 降 需 要 。 模 无飞 边模锻 ,节 约 材料 ,实现 最大程 度 的近似 净 5℃ 预 锻前 的镦粗 有 两个作 用 :一是 去除 加热 过程 中形 形 加工 。工艺 流程 为 : 成 的氧化 皮 ;二是 获 得预锻 时对 中放 置所 需要 的尺
汽车齿轮加工总结范文

随着汽车工业的不断发展,汽车齿轮作为汽车传动系统中的核心部件,其加工质量直接影响到汽车的传动性能、安全性和可靠性。
本文将对汽车齿轮加工技术进行总结,分析其加工工艺、加工方法及注意事项。
一、汽车齿轮加工工艺1. 锻造:锻造是汽车齿轮加工的第一道工序,通过锻造,可以使齿轮的内部组织形成纤维流,提高齿轮的承载能力。
2. 正火处理:正火处理可以使齿轮心部具有良好的韧性,为后续的机械加工提供良好的加工性能。
3. 表面淬火:表面淬火可以使齿轮的轮齿硬度高、耐磨性好,提高齿轮的使用寿命。
4. 低温回火:低温回火可以消除齿轮加工过程中的残余应力,提高齿轮的疲劳强度。
5. 机械加工:机械加工是汽车齿轮加工的关键工序,主要包括粗加工、半精加工和精加工。
6. 热处理:热处理是提高齿轮性能的重要手段,主要包括渗碳、淬火和回火等工艺。
7. 磨削:磨削是汽车齿轮加工的最后一道工序,可以提高齿轮的尺寸精度和表面粗糙度。
二、汽车齿轮加工方法1. 仿形法:仿形法是通过模拟齿轮齿形曲线,加工出与齿形曲线相吻合的齿轮。
2. 范成法:范成法是利用展成原理,通过展成机构加工出齿轮。
3. 数控加工:数控加工是利用计算机编程控制机床,实现齿轮的高精度加工。
4. 超精密加工:超精密加工是利用特殊加工设备,实现齿轮的超高精度加工。
三、汽车齿轮加工注意事项1. 严格控制加工精度:汽车齿轮加工精度直接影响到汽车的传动性能和可靠性,因此在加工过程中要严格控制精度。
2. 选择合适的加工方法:根据齿轮的材料、形状和精度要求,选择合适的加工方法。
3. 注意热处理工艺:热处理工艺对齿轮的性能有很大影响,要严格控制热处理工艺参数。
4. 保证加工表面质量:加工表面质量直接影响到齿轮的耐磨性和使用寿命,要保证加工表面质量。
5. 优化加工工艺参数:根据齿轮的材料、形状和精度要求,优化加工工艺参数,提高加工效率。
总之,汽车齿轮加工技术在汽车工业中占有重要地位。
通过不断优化加工工艺、改进加工方法,提高汽车齿轮的加工质量,为汽车行业的发展提供有力保障。
滚齿机在齿轮精密加工中的应用
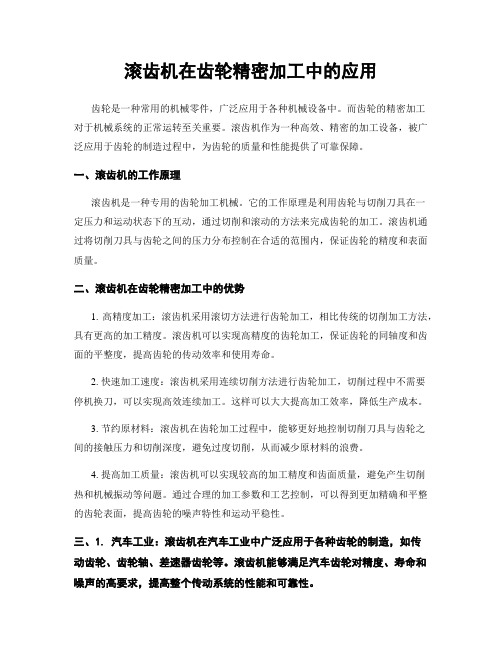
滚齿机在齿轮精密加工中的应用齿轮是一种常用的机械零件,广泛应用于各种机械设备中。
而齿轮的精密加工对于机械系统的正常运转至关重要。
滚齿机作为一种高效、精密的加工设备,被广泛应用于齿轮的制造过程中,为齿轮的质量和性能提供了可靠保障。
一、滚齿机的工作原理滚齿机是一种专用的齿轮加工机械。
它的工作原理是利用齿轮与切削刀具在一定压力和运动状态下的互动,通过切削和滚动的方法来完成齿轮的加工。
滚齿机通过将切削刀具与齿轮之间的压力分布控制在合适的范围内,保证齿轮的精度和表面质量。
二、滚齿机在齿轮精密加工中的优势1. 高精度加工:滚齿机采用滚切方法进行齿轮加工,相比传统的切削加工方法,具有更高的加工精度。
滚齿机可以实现高精度的齿轮加工,保证齿轮的同轴度和齿面的平整度,提高齿轮的传动效率和使用寿命。
2. 快速加工速度:滚齿机采用连续切削方法进行齿轮加工,切削过程中不需要停机换刀,可以实现高效连续加工。
这样可以大大提高加工效率,降低生产成本。
3. 节约原材料:滚齿机在齿轮加工过程中,能够更好地控制切削刀具与齿轮之间的接触压力和切削深度,避免过度切削,从而减少原材料的浪费。
4. 提高加工质量:滚齿机可以实现较高的加工精度和齿面质量,避免产生切削热和机械振动等问题。
通过合理的加工参数和工艺控制,可以得到更加精确和平整的齿轮表面,提高齿轮的噪声特性和运动平稳性。
三、1. 汽车工业:滚齿机在汽车工业中广泛应用于各种齿轮的制造,如传动齿轮、齿轮轴、差速器齿轮等。
滚齿机能够满足汽车齿轮对精度、寿命和噪声的高要求,提高整个传动系统的性能和可靠性。
2. 航空航天工业:航空航天工业对于齿轮的精度和可靠性要求更高。
滚齿机作为一种高精密加工设备,在航空航天齿轮的制造过程中,能够提供高强度和高耐磨的齿轮产品,确保飞机、火箭等空中器械的稳定飞行。
3. 燃气轮机工业:燃气轮机是一种重要的能源转换设备,其中的齿轮系统承担着关键任务。
滚齿机在燃气轮机齿轮的制造过程中,能够提供精确、高效的加工方法,保证齿轮的匹配精度和传动效率,提高整个燃气轮机的性能。
简述齿轮传动的优点、缺点

简述齿轮传动的优点、缺点
齿轮传动的优点有以下几点:
1. 结构紧凑、重量轻:由于齿轮和轴承的几何尺寸相对较小,因此齿轮箱的体积可以做得更小,重量也更轻,这使得整个机械系统的重量大大减轻,方便运输和操作。
2. 高效:齿轮传动可以以很高的速度传递动力,同时也可以承受较大的载荷,因此可以有效地提高机械系统的效率和输出。
3. 稳定性好:齿轮传动过程中不会出现滑动和冲击,因此可以保证机械系统的稳定性和精度。
4. 可靠性高:齿轮传动具有较高的可靠性和耐久性,因为齿轮和轴承的材料和制造工艺都经过精心设计和严格控制,可以保证在长时间使用中不出现故障。
5. 适用范围广:齿轮传动可以适用于各种不同的机械系统,如汽车、航空、工业、建筑等各个领域,用途十分广泛。
齿轮传动的缺点有以下几点:
1. 制造复杂、成本高:齿轮和轴承的制造需要经过多道工序和复杂的加工过程,因此制造成本较高。
2. 需要维护和保养:齿轮传动需要定期维护和保养,如更换润滑油、清洗轴承等,以确保其正常运转和延长使用寿命。
3. 对环境要求高:齿轮传动对环境的要求较高,如温度、湿度、灰尘等都会对其产生影响,因此需要在良好的环境下使用。
4. 噪音和振动:齿轮传动过程中可能会出现噪音和振动,这可能会对机械系统的稳定性和精度产生影响,因此需要进行相应的减噪和减震设计。
5. 适用范围受限:虽然齿轮传动在许多领域都有应用,但在某些特殊情况下,如需要大范围改变传动比的情况下,可能会受到限制。
总的来说,齿轮传动具有许多优点,但也存在一些缺点。
在实际应用中,需要根据具体的使用场景和需求来选择是否使用齿轮传动。
汽车用齿轮类零件的精密锻造技术
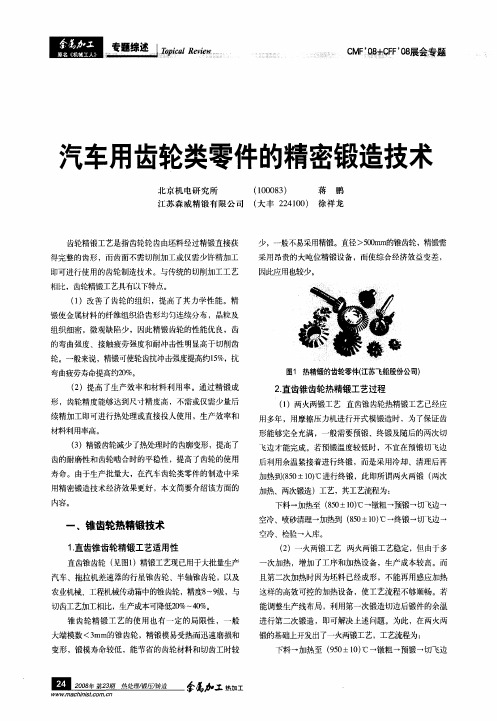
一
\
闭塞锻造的基本动作包括合模并锁紧模腔 、单个或
多个冲头进 出模具型腔 、开模及 卸料 杆顶件 出模等5 类
动作 。实质是 冲头挤 压封 闭型腔的坯件使之变形为预 先
设定 的形状 。其特 点是一次锻 造成 尺寸形状 精度高的工 件 ,实现近净形锻造 。它要求预制坯体 积误 差小 、接 触 工件的模具型 面能承受较 高的单位压 力 , 锻造工艺 力较 大 。所以对设备能力 、设备与工装模具 的刚度及工况状
。
—■●●oaew ■堡■ i v ■■ —TcRi 曼■ x l e ■■ ● ■ 苎 p ■上
CF8 F0 会 题 M Qc’展 专 士 F8
汽车用齿轮类零件的精密锻造技术
北京机 电研究所 (0 0 3 10 8 ) 蒋 鹏
江苏森威精锻有限公司 ( 大丰 2 4 0 ) 徐祥龙 2 10
下料一加热至 (5 ±1) 90 0 ℃一镦粗 一预锻 一切飞边
目 堡 塑 垫 _ 丝 竺
' 们 m aCh nl . Om . l StC 鲫
参 加 磊 工热工
C ’ C’ 会 题 M0 F0 专 F8 F8 + 展
一
, I竺 苎 堡
二 锥齿轮的冷精锻技术
1 . 锥齿轮的闭塞冷锻成形技术
o
一
态下的强度等提出了更高的要求。 闭塞锻造直 齿锥 齿轮 的锻造工步仅有制坯和成形两 步 ,工艺流程短,成形精度高。
2冷摆辗工艺 .
除 闭塞成形外 ,冷摆辗技术也可应用于汽车伞齿轮
的精密成形 , 并用于钢质同步器齿环的齿形成形。
瑞士T ( rt o o i r s 摆动辗压机是 型 Ob aC lFr n P s il d m g e )
精密锻造知识点归纳总结
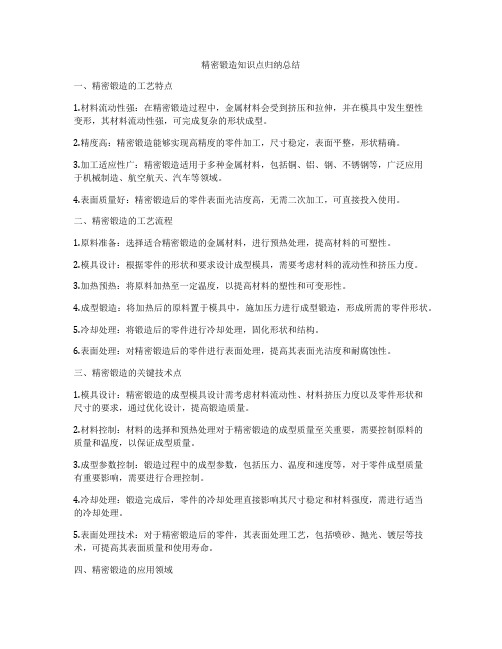
精密锻造知识点归纳总结一、精密锻造的工艺特点1.材料流动性强:在精密锻造过程中,金属材料会受到挤压和拉伸,并在模具中发生塑性变形,其材料流动性强,可完成复杂的形状成型。
2.精度高:精密锻造能够实现高精度的零件加工,尺寸稳定,表面平整,形状精确。
3.加工适应性广:精密锻造适用于多种金属材料,包括铜、铝、钢、不锈钢等,广泛应用于机械制造、航空航天、汽车等领域。
4.表面质量好:精密锻造后的零件表面光洁度高,无需二次加工,可直接投入使用。
二、精密锻造的工艺流程1.原料准备:选择适合精密锻造的金属材料,进行预热处理,提高材料的可塑性。
2.模具设计:根据零件的形状和要求设计成型模具,需要考虑材料的流动性和挤压力度。
3.加热预热:将原料加热至一定温度,以提高材料的塑性和可变形性。
4.成型锻造:将加热后的原料置于模具中,施加压力进行成型锻造,形成所需的零件形状。
5.冷却处理:将锻造后的零件进行冷却处理,固化形状和结构。
6.表面处理:对精密锻造后的零件进行表面处理,提高其表面光洁度和耐腐蚀性。
三、精密锻造的关键技术点1.模具设计:精密锻造的成型模具设计需考虑材料流动性、材料挤压力度以及零件形状和尺寸的要求,通过优化设计,提高锻造质量。
2.材料控制:材料的选择和预热处理对于精密锻造的成型质量至关重要,需要控制原料的质量和温度,以保证成型质量。
3.成型参数控制:锻造过程中的成型参数,包括压力、温度和速度等,对于零件成型质量有重要影响,需要进行合理控制。
4.冷却处理:锻造完成后,零件的冷却处理直接影响其尺寸稳定和材料强度,需进行适当的冷却处理。
5.表面处理技术:对于精密锻造后的零件,其表面处理工艺,包括喷砂、抛光、镀层等技术,可提高其表面质量和使用寿命。
四、精密锻造的应用领域1.航空航天:精密锻造在航空航天领域应用广泛,可用于制造各种飞机发动机零件、轴承等高精度工程零部件。
2.汽车制造:汽车发动机、传动系统以及底盘和车身零部件等,都可采用精密锻造工艺,提高零件的精度和性能。
- 1、下载文档前请自行甄别文档内容的完整性,平台不提供额外的编辑、内容补充、找答案等附加服务。
- 2、"仅部分预览"的文档,不可在线预览部分如存在完整性等问题,可反馈申请退款(可完整预览的文档不适用该条件!)。
- 3、如文档侵犯您的权益,请联系客服反馈,我们会尽快为您处理(人工客服工作时间:9:00-18:30)。
齿轮精密锻造的诸多优点齿轮精密锻造在近几十年来有很大的发展,越来越多的制造厂家和用户重视用锻造的方法制造齿轮。
普遍认为,用锻造的方法,可以提高材料的利用率,提高生产率,提高齿轮的机械性能,降低成本和增强市场竞争力。
尤其对用于汽车工业的大规模生产,齿轮精密锻造具有更大的效益和潜力。
尽管齿轮精密锻造有诸多优点,并已用于锥齿轮的规模生产,但距应用于一定尺寸的圆柱直齿轮和斜齿轮的规模生产还有一段距离。
特别是应用于汽车动力传动的齿轮,还需要建立一套实用和可靠的生产工艺流程,才能为厂家所接受。
齿轮精密锻造技术源于德国。
早在50年代,由于缺乏足够的齿轮加工机床德国人开始用闭式热模锻的方法试制锥齿轮。
其中的主要特征是使用了当时很新的电火花加工工艺来制造锻模的型腔。
另外还对锻造工艺过程进行了严格地控制。
此基础上,齿轮锻造技术进一步应用到螺旋锥齿轮和圆柱齿轮的生产。
但是圆柱齿轮锻造中,由于金属材料的塑性流动方向与其受力方向垂直,所以其齿形比锥齿轮更难形成。
60年代开始圆柱齿轮的锻造研究,70年代有较大的发展,这主要是受到来自汽车工业降低成本的压力。
80年代,锻造技术更加成熟,能达到更高的精度和一致性,使锻造生产齿轮能在流水生产线上准确定位,适合于批量生产。
齿轮精密锻造的目的直接生产出不需要后续切削加工的齿轮。
如果能在室温下进行锻造,则齿轮的形状和尺寸较易控制,也可避免高温带来的误差。
目前已有较多的锥齿轮和小尺寸的圆柱齿轮用这种方法制成。
当整体尺寸适合时,还可以用冷挤压的工艺来制造圆柱直、斜齿轮。
但大部分用于汽车传动的齿轮,其直径、高度比较大,不适合采用挤压工艺。
如用闭式模锻,则需要很高的压力才能使金属材料流动并充满模具型腔,因而此类齿轮需要采用热锻或温锻工艺。
而高温将带来材料的氧化,模具畸变,影响锻件的精度和表面质量。
用附加的切削加工来修正这些误差难度较大,还要增加成本。
特别是当使用后续磨削工艺来修正齿形上的误差,除增加成本和延长工时外,还存在磨削工艺中齿轮的定位问题。
目前,比较一致认同的工艺途径为热锻、温锻和冷锻的结合。
热锻、温锻可实现高效能和材料的高利用率,冷锻过程则修正热、温锻过程的误差和提高表面质量。
同时,冷处理工艺还能使轮齿表面获得残余压应力,提高齿轮的寿命。
机械工程学院完成了一项由英国工程科学研究协会(EPSRC资助),与英国的7家企业(齿轮制造,模具制造,齿轮用户,锻造厂以及钢铁公司)合作的3年研究课题:圆柱直齿轮和斜齿轮精密锻造。
该项目在多年研究和实践的基础上,进一步探讨齿轮锻造的机理,利用现代的分析手段,如计算机模拟和设计技术,旨在开发一种生产和经济上可行的锻造加工技术,制造出在齿形上不再需要后续加工的精密齿轮。
该项目研究和试验了圆柱直齿轮、圆柱斜齿轮和同步齿轮等3种齿轮。
考虑到整个过程的经济性,精密锻造只限于轮廓部分,而齿端和内孔等部分,则采用切削加工。
制造工艺为温锻加冷处理,由温锻获得满足形状要求的齿轮,并在轮廓部分留有011mm左右的余量。
冷处理过程中,把温锻后的齿轮挤压通过一精密设计和制造的模具,从而修正轮廓部分的误差,获得高精度的齿形表面。
研究过程中,有限元方法被用来分析锻造过程,设计模具,从而保证齿轮的精度。
经过3年的研究,已经掌握其基本技术,下一步将进行工厂现场试验。
同时正在准备申报该项目的第二阶段研究。
2温锻工艺由于项目要求寻求一适合工厂实用的生产途径,该研究选用一高速率、单动单曲柄机械压机。
由于锻件被加热,必须考虑材料的热膨胀和冷收缩以及模具的变形,为此采用有限元作精确计算。
此外还用有限元对锻造过程模拟,以保证锻件精度。
实验表明,850℃~950℃之间锻造钢齿轮,误差可控制在0105mm范围内。
锻造过程中保持静止,锻造后把齿轮顶出型腔。
芯棒此处与冲头连成一体,用来帮助毛坯的定位。
由于型腔在锻造过程中与锻件一起运动,型腔与锻件之间的摩擦力将有助于金属流动,所需载荷也比型腔固定时低。
|齿轮加工机床用齿轮加工工具加工齿轮齿面或齿条齿面的机床。
齿轮加工机床齿轮加工机床是加工各种圆柱齿轮、锥齿轮和其他带齿零件齿部的机床。
齿轮加工机床的品种规格繁多,有加工几毫米直径齿轮的小型机床,加工十几米直径齿轮的大型机床,还有大量生产用的高效机床和加工精密齿轮的高精度机床。
齿轮加工机床广泛应用在汽车、拖拉机、机床、工程机械、矿山机械、冶金机械、石油、仪表、飞机和航天器等各种机械制造业中。
发展沿革古代的齿轮是用手工修锉成形的。
1540年,意大利的托里亚诺在制造钟表时,制成一台使用旋转锉刀的切齿装置;1783年,法国的勒内制成了使用铣刀的齿轮加工机床,并有切削齿条和内齿轮的附件;1820年前后,英国的怀特制造出第一台既能加工圆柱齿轮又能加工圆锥齿轮的机床。
具有这一性能的机床到19世纪后半叶又有发展。
齿轮加工机床1835年,英国的惠特沃思获得蜗轮滚齿机的专利;1858年,席勒取得圆柱齿轮滚齿机的专利;以后经多次改进,至1897年德国的普福特制成带差动机构的滚齿机,才圆满解决了加工斜齿轮的问题。
在制成齿轮形插齿刀后,美国的费洛斯于1897年制成了插齿机。
二十世纪初,由于汽车工业的需要,各种磨齿机相继问世。
1930年左右在美国制成剃齿机;1956年制成珩齿机。
60年代以后,现代技术在一些先进的圆柱齿轮加工机床上获得应用,比如在大型机床上采用数字显示指示移动量和切齿深度;在滚齿机、插齿机和磨齿机上采用电子伺服系统和数控系统代替机械传动链和交换齿轮;用设有故障诊断功能的可编程序控制器,控制工作循环和变换切削参数;发展了数字控制非圆齿轮插齿机和适应控制滚齿机;在滚齿机上用电子传感器检测传动链运动误差,并自动反馈补偿误差等。
1884年,美国的比尔格拉姆发明了采用单刨刀按展成法加工的直齿锥齿轮刨齿机;1900年,美国的比尔设计了双刀盘铣削直齿锥齿轮的机床。
40年代,为适应航空工业的需要,发展了弧齿锥齿轮磨齿机。
1944年,瑞士厄利康公司制成延长外摆线齿锥齿轮铣齿机;从50年代起,又发展了用双刀体组合式端面铣刀盘,加工延长外摆线齿锥齿轮的铣齿机。
齿轮加工机床主要分为圆柱齿轮加工机床和锥齿轮加工机床两大类。
圆柱齿轮加工机床主要用于加工各种圆柱齿轮、齿条、蜗轮。
常用的有滚齿机,插齿机、铣齿机、剃齿机等。
工作原理齿轮加工机床的种类繁多,构造各异:成形法范成法成形法要求:刀具的切削刃形状与被切齿轮的齿槽形状相吻合。
优点:机床较简单,可利用通用机床加工。
缺点:1.对于同一模数的齿轮,只要齿数不同,齿廓形状就不相同,需采用不同的成形刀具;2.加工出来的齿形是近似的,加工精度较低;3.每加工完一个齿槽后,工件需要周期地分度一次,生产率也较低。
1)滚齿法母线(渐开线):采用成形法,机床不需要表面成形运动。
形成导线(直线):相切法。
机床需要两个成形运动。
一个是铣刀的旋转B1,一个铣刀沿齿坯的轴向移动A。
两个都是简单运动。
铣完一个齿后,铣刀返回原位,齿坯作分度运动——转过360º/z(z是被加工齿轮的齿数),然后再铣下一个齿槽,直至全部齿被铣削完毕。
用单齿廓成形刀具加工齿轮——用于修配行业中加工精度要求不高的齿轮;用于重型机器制造业中,以解决缺乏大型齿轮加工机床的问题。
2)铣齿法采用多齿廓成形刀具时,在一个工作循环中即可加工出全部齿槽,生产率很高,但刀具制造复杂,仅用于大量生产中。
范成法范成法: 利用齿轮的啮合原理把齿轮啮合副(齿条——齿轮、齿轮——齿轮)中的一个转化为刀具;另一个转化为工件,并强制刀具和工件作严格的啮合运动而范成切出齿廓。
范成法切齿所用刀具切削刃的形状相当于齿条或齿轮的齿廓,它与被切齿轮的齿数无关。
每一种模数,只需用一把刀具就可以加工各种不同齿数的齿轮;加工时能连续分度,加工精度和生产率一般比较高,应用广泛。
此法必须在专门的齿轮机床上加工,而且机床的调整、刀具的制造和刃磨都比较复杂,一般用于成批大量生产类型按照被加工齿轮种类不同,齿轮加工机床可分为两大类:圆柱齿轮加工机床—滚齿机、插齿机、车齿机等锥齿轮加工机床——加工直齿锥齿轮:刨齿机、铣齿机、拉齿机。
加工弧齿锥齿轮:铣齿机。
加工齿线形状为延伸渐开线:锥齿轮铣齿机。
精加工齿轮齿面:珩齿机、剃齿机和磨齿机。
滚齿机是用滚刀按展成法粗、精加工直齿、斜齿、人字齿轮和蜗轮等,加工范围广,可达到高精度或高生产率;插齿机是用插齿刀按展成法加工直齿、斜齿齿轮和其他齿形件,主要用于加工多联齿轮和内齿轮;铣齿机是用成形铣刀按分度法加工,主要用于加工特殊齿形的仪表齿轮;剃齿机是用齿轮式剃齿刀精加工齿轮的一种高效机床;磨齿机是用砂轮,精加工淬硬圆柱齿轮或齿轮刀具齿面的高精度机床;珩齿机是利用珩轮与被加工齿轮的自由啮合,消除淬硬齿轮毛刺和其他齿面缺陷的机床;挤齿机是利用高硬度无切削刃的挤轮与工件的自由啮合,将齿面上的微小不平碾光,以提高精度和光洁程度的机床;齿轮倒角机是对内外啮合的滑移齿轮的齿端部倒圆的机床,是生产齿轮变速箱和其他齿轮移换机构不可缺少的加工设备。
圆柱齿轮加工机床还包括齿轮热轧机和齿轮冷轧机等。
锥齿加工机床主要用于加工直齿、斜齿、弧齿和延长外摆线齿等锥齿轮的齿部。
直齿锥齿轮刨齿机是以成对刨齿刀按展成法粗、精加工直齿锥齿轮的机床,有的机床还能刨制斜齿锥齿轮,在中小批量生产中应用最广。
双刀盘直齿锥齿轮铣齿机使用两把刀齿交错的铣刀盘,按展成法铣削同一齿槽中的左右两齿面,生产效率较高,适用于成批生产。
由于铣刀盘与工件无齿长方向的相对运动,铣出的齿槽底部呈圆弧形,加工模数和齿宽均受到限制。
这种机床也可配以自动上下料装置,实现单机自动化。
直齿锥齿轮拉铣机是在一把大直径的拉铣刀盘的一转中,从实体轮坯上用成形法切出一个齿槽的机床。
它是锥齿轮切削加工机床中生产率最高的机床,由于刀具复杂,价格昂贵,而且每种工件都需要专用刀盘,只适用于大批大量生产。
机床一般都带有自动上下料装置。
弧齿锥齿轮铣齿机以弧齿锥齿轮铣刀盘,按展成法粗、精加工弧齿锥齿轮和准双曲面齿轮的机床,有精切机、粗切机和拉齿机等变型。
弧齿锥齿轮磨齿机是用于磨削淬硬的弧齿锥齿轮,以提高精度和光洁程度的机床,其结构与弧齿锥齿轮铣齿机相似,但以砂轮代替铣刀盘,并装有砂轮修整器,也可磨削准双曲面齿轮。
延长外摆线齿锥齿轮铣齿机利用延长外摆线齿锥齿轮铣刀盘,或双刀体组合式端面铣刀盘,按展成法连续分度切齿的机床。
切齿时,摇台铣刀盘和工件均作连续旋转运动,同时摇台作进给运动加工一个工件摇台往复一次。
铣刀盘和工件的连续旋转使工件获得一定齿数的连续分度,并形成齿长曲线。
摇台的旋转和工件的附加运动结合起来,产生展成运动,使工件获得齿形曲线。
准渐开线齿锥齿轮铣齿机用锥度滚刀,按展成法连续分度切齿的机床。