煤化学工程
能源化学工程概论(第二版)2煤化工-2021

现代工业文明对能源的要求
电力 运输燃料 从矿物中提炼金属和化学品(如炼铁) 化工产品,包括塑料、药品、化肥 过程热,即在化学工业及金属加工中用于锅炉、熔化、
退火改型等所需的热能
煤可以满足所有这些需要
发展煤化工
常规煤综合利用技术
用作动力原料 燃烧产生热能、电能;副产品煤渣、煤灰可生产煤渣转、水泥 (能源) 材料、过滤材料等
有一种黑石头,可以燃烧,有时铁匠可用它来代替木 炭, 并把这种可燃烧的石头称anthrax(anthracite)。
摘自Theophrastus(西奥福来斯多斯)在 公元前300年发表的De Lapidus(岩石学)
煤炭的生成
煤炭的生成 植物 泥炭 褐煤 烟煤 无烟煤
煤炭的生成
植物经数千年到数万年复杂的生物化学变化过程形成泥 炭(一种松软有机质的堆积物);
蒸汽机和便宜的铁为各种技术的的发展提供了基础。它也 成为在西方文明史上的一个决定性的转折点-工业革命。
工业革命带来的重要变化
从小规模的以家庭形式的制造业向大工厂的转变 : 蒸汽机为大工厂的生产需要提供可靠的动力源,而蒸汽 机的广泛应用又要求有大量廉价燃料的供给,而当时能满 足这一要求的只有煤炭。 当时具有丰富煤资源的国家是最能适应由工业革命带来 新的经济变化的国家,主要是英国、美国、德国和法国。 19世纪国家的政治力量大小对应于所拥有煤的多少,在 那个时代,煤就意味着power,即动力和权力。
泥炭在不太深的地下经数百万年因压力和温度等作用发 生一系列物理化学变化(成岩作用)转变成褐煤或烟煤;
褐煤或烟煤在地下深处再经数千万年以上因压力、温度 和时间的化学物理作用(变质作用)形成烟煤或无烟煤。
煤炭是一种宝贵的不可再生的资源, 必须加以高效、经济和合理地利用。
煤化工(化工技术)—搜狗百科

煤化工(化工技术)—搜狗百科中国煤化工开始于18世纪后半叶,19世纪形成了完整的煤化工体系。
进入20世纪,许多以农林产品为原料的有机化学品多改为以煤为原料生产,煤化工成为化学工业的重要组成部分。
第二次世界大战以后,石油化工发展迅速,很多化学品的生产又从以煤为原料转移到以石油、天然气为原料,从而削弱了煤化工在化学工业中的地位。
进入二十一世纪后,随着全球石油市场的动荡和石油价格的攀升,煤炭作为储量巨大并且可能替代石油的资源重新受到越来越多的重视。
煤中有机质的化学结构,是以芳香族为主的稠环为单元核心,由桥键互相连接,并带有各种官能团的大分子结构,通过热加工和催化加工,可以使煤转化为各种燃料和化工产品。
世界上生产的煤,主要用作电站和工业锅炉燃料;用于煤化工的占一定比例,其中主要是煤的焦化和气化。
80年代世界焦炭年产量约340Mt,煤焦油年产量约16Mt(从中提炼的萘约1Mt)。
煤焦油加工的产品广泛用于制取塑料、染料、香料、农药、医药、溶剂、防腐剂、胶粘剂、橡胶、碳素制品等。
1981年,世界合成氨总产量95.3Mt,主要来源于石油和天然气。
以煤为原料生产的氨只约占10%;自煤制合成甲醇的比例也很小,仅占甲醇总产量约1%。
美国煤化工1984年美国用煤717.7Mt,其中用于炼焦的占5.5%,达39.5Mt。
炼焦副产的苯占苯总产量的9%,以电石乙炔为原料生产的醋酸乙烯在其总产量中占8%。
1984年美国建成由褐煤气化再甲烷化生产高热值城市煤气的工厂,日加工褐煤22kt,产气3.89Mm。
同时,又在煤气化和液化方面,进行了不少新工艺试验。
联邦德国煤化工1984年联邦德国用煤84.8Mt(不包括褐煤),炼焦用煤占32.6%,为27.6Mt,煤焦油年产量约 1.4Mt。
全国钢铁等企业的焦炉生产的煤焦油集中到五个焦油加工厂进行加工,生产的化学品达500多种。
电石乙炔化工方面曾有很大发展,当前在技术上仍有改进。
在煤的加压气化和直接液化研究方面也有一些新的进展。
煤化工简介6-10
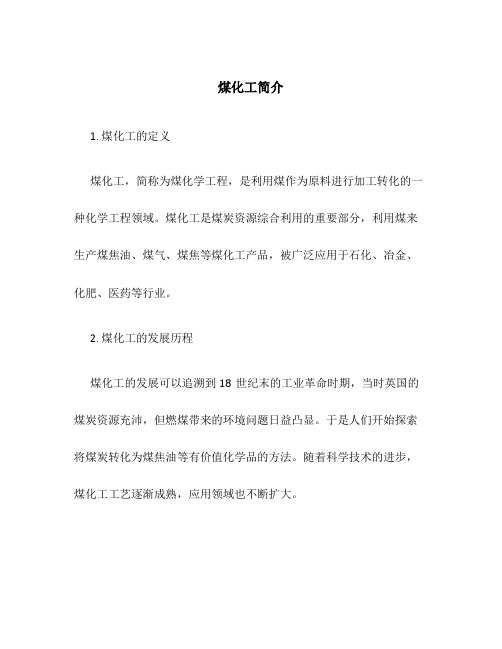
煤化工简介1. 煤化工的定义煤化工,简称为煤化学工程,是利用煤作为原料进行加工转化的一种化学工程领域。
煤化工是煤炭资源综合利用的重要部分,利用煤来生产煤焦油、煤气、煤焦等煤化工产品,被广泛应用于石化、冶金、化肥、医药等行业。
2. 煤化工的发展历程煤化工的发展可以追溯到18世纪末的工业革命时期,当时英国的煤炭资源充沛,但燃煤带来的环境问题日益凸显。
于是人们开始探索将煤炭转化为煤焦油等有价值化学品的方法。
随着科学技术的进步,煤化工工艺逐渐成熟,应用领域也不断扩大。
20世纪70年代以来,中国的煤化工工业得到了迅猛发展。
中国的煤炭资源丰富,煤化工工业的发展不仅可以提高煤炭资源的综合利用率,还能减少对石油等化石能源的依赖。
3. 煤化工的主要产品3.1 煤焦油煤焦油是煤化工的主要产品之一,它是在焦炉中通过干馏煤炭获得的,具有较高的经济和应用价值。
煤焦油可用于生产染料、农药、涂料、橡胶、塑料等多种化工产品,也可以作为燃料使用。
3.2 煤气煤气是煤焦油干馏的副产物,主要由一氧化碳、氢气和少量的甲烷等组成。
煤气可以用作燃料,也可以经过净化处理后用于合成甲醇、乙烯等化工产品。
3.3 煤焦煤焦是在焦炉中将煤炭加热脱除挥发分后得到的固体产物。
煤焦具有较高的热值和机械强度,广泛用于冶金、化肥、铝电解等工业领域。
3.4 其他产品除了煤焦油、煤气和煤焦外,煤化工还可以生产其他化工产品,如苯酚、酚醛树脂、煤脱硫剂等。
这些产品在冶金、化肥、医药等行业有着广泛的应用。
4. 煤化工的发展前景随着能源结构的调整和环境保护意识的增强,煤化工作为煤炭资源的高效利用方式,具有重要的发展前景。
首先,煤化工可以减少对石油等有限资源的依赖,提高能源供给的可持续性。
其次,煤化工产品的应用领域广泛,可以满足不同行业的需求,推动工业的发展。
最后,煤焦油等产品在低碳环保领域有着巨大的潜力,可以替代某些传统的化工产品,减少二氧化碳等温室气体的排放。
5. 煤化工的挑战与问题尽管煤化工具有广阔的发展前景,但也存在一些挑战与问题。
煤化工工程1
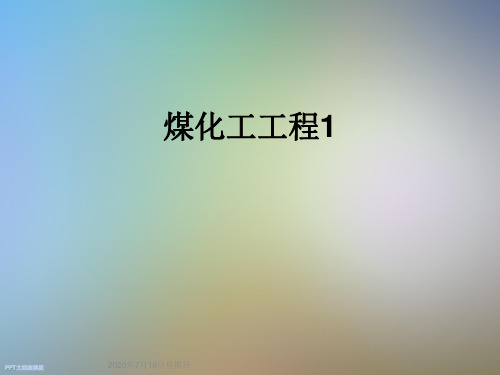
三、 主要成煤期与主要煤田
1、影响成煤期的主要因素 (1)、植物条件
——物质基础;
(2)、气候条件
——影响植物生长,同时影响植物的分解;
(3)、自然地理条件
——植物堆积;
(4)、地壳运动条件
——埋藏条件
2、主要聚煤期和主要煤田
A 主要聚煤期(地质年代:代、纪、世、期、时和地层系统的对应界、系、 统、组、段)
50%—25 %
暗淡型煤
光泽极暗
<25%
▲ ① 煤级和成因类型相同,才能进行光泽强度对比,
新鲜面,不考虑具体光泽;
② 相同煤层中光泽最强的煤岩成分条带(镜煤)
为参考标准,相对光泽;
③ 最小分层厚度为3—10cm,视煤层厚度而定; ④ 每一种光泽类型,据构造、结构再分。
3、煤的显徽组分
煤的显微组分,是指煤在显微镜下能够区分和辨识的基本组成成分。按 其成分和性质又可分为有机显微组分和无机显微组分。有机显微组分是 指在显微镜下能观察到的煤中由植物韧有机质转变而成的组分; 腐殖煤的显微组分分大体可分3类,即凝胶化组分(镜质组)、丝炭化组分 (情质组或丝质组)、稳定组(壳质组)。
我国的煤炭资源和煤的综合利用
我国煤炭资源丰富,探明可采储量为8000多亿t ,居世界之首,约占世界 总储量的46% 。我国也是世界上第一产煤和用煤大国, 中国对煤炭的需 求量约占世界煤炭总产量的30% 。我国煤炭在一次能源中占总消费量的比 重为60%以上。我国2050年的远景规划中,一次能源总消费将增加至每 年40 亿t 标煤, 其中石油占4.28 %,天然气占12.5% .水电占7.75% ,新能源将有较大发展,约占2.5% ,核能将有很大发展,将占12.5% , 但煤炭仍然占有最大比重67.65 %。由上可见,我国在相当长的时间内能 源仍将时煤炭为主。 煤化学是煤炭综合利用技术的理论基础,而煤炭结合利用又是煤化学的服务 对象。煤化学是随着煤炭综合利用的开发、发展而开发和振兴的,煤炭结 合利用的新工艺、新产品的开发充实了煤化学学科的内在,而其中的问题 与不足反过来又促进了煤化学的深入研究与发展。
煤化学工程
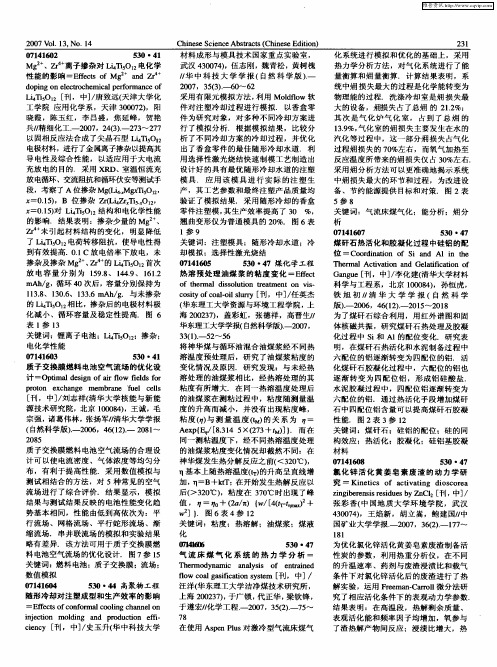
化 系统进 行模拟和优化 的基础 上,采用 热 力 学 分 析 方 法 ,对 气 化 系 统进 行 了 能 量衡算和炯 量衡算.计算结 果表 明,系 统 中炯 损 失最 大 的 过程 是 化 学 能 转 变 为 物 理 能 的过 程 . 洗 涤 冷 却 室 是炯 损 失 最 大 的设 备 ,炯损 失 占 了总 炯 的 2 .%; 1 2 其 次 是 气 化 炉 气 化 室 , 占 到 了 总 炯 的 1.%, 化 室 的炯 损 失 主要 发 生 在水 的 39 气 汽 化 等 过 程 中 ,这 一 部 分 炯 损 失 占气 化 过 程 炯 损 失 的 7 %左 右 ,而 氧 气 加热 至 0 反应温度所带来 的炯损 失仅 占 3 %左 右. 0 采用炯分 析方法可 以更准确地揭示 系统 中炯 损 失最 大 的 环 节 和 过 程 , 为 改进 设 备、节约能源提供 目标和对策. 图 2表
5参 8
关 键 词 :气 流 床 煤 气 化 ; 能 分 析 ;炯 分 析
O 1 1O 7467 5 0・4 3 7
煤 矸 石 热 活 化 和 胶 凝 化 过 程 中硅 铝 的配 位 = C odnt n o iad AIi te o ria o S n h i f n
x . ) =0 1 ,B 位 掺 杂 Z ( i 5 r 4 L 5 1 . 2 ,
x . ) L4 i 2 构 和 电化 学性 能 =01 对 i 5 结 5 T o1 的影 响 . 结 果 表 明 :掺 杂 少 量 的 Mg + 2、 z4 未 引 起 材 料 结 构 的变 化 , 明显 降低 r 了 L4 i 2 i 5 电荷 转 移 阻抗 ,使 导 电性 得 T o1 到有效提高.01 .C放 电倍率下放 电,未 掺 杂 及 掺 杂 Mg+ z4 的 L4 i 2 次 2、 r i 5 首 T 01 放 电 容 量 分 别 为 198 149 1 1 5 .、 4 .、 6 . 2 mA / , h g 循环 4 0次后 , 容量分别保持 为 l3 、 l06 l36mA / . 与 未 掺 杂 l. 3 .、 3 . 8 hg 的 L4 i 2 比 ,掺 杂 后 的 电极 材 料 极 i 5 相 T o1 化 减 小 、循 环 容 量 及 稳 定 性 提 高 . 图 6 表 l l 参 3 关 键 词 :锂 离 子 电 池 ;L4i 2 i 5 :掺 杂 ; T o】 电化 学 性 能
煤化学工程
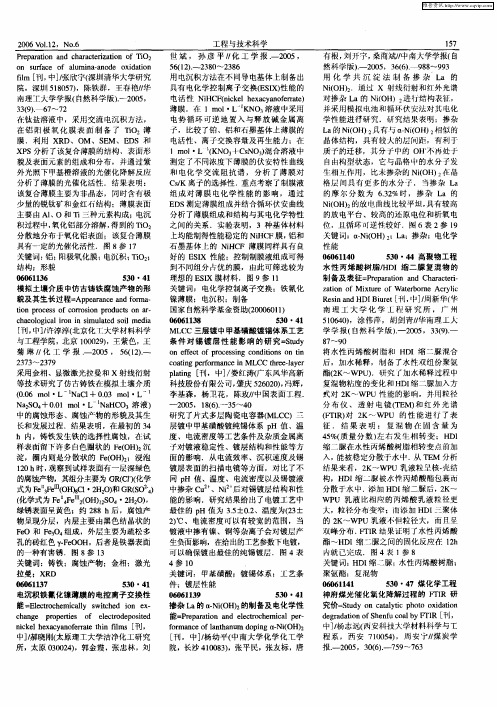
5 0・ 4 高聚物工程 3 4 水 性丙烯 酸树 J / DI缩二脲 复 混物 的 ]H  ̄ 制备 及表 征= e aain ad C aat i r P prt h rc r o n e—
z t n o i t r f W ae b r e Ac y i a i f M x u e o tr o n r l o c
:程与技术科 学 [ _
17 5
世 斌 , 孙 彦 平 ,化 工 学 报 . o 5, / 一2 o
5 ( ) 2 8  ̄斌/ / 中南大 学学报( 自
然科 学 版 ) 2 0 ,3 () 9 8 9 . o 5 66. 8  ̄9 3 一 一
0 0 1 3 6 6 18 5 0 ・4 3 1
用 化 学 共 沉 淀 法 制 备 掺 杂 L 的 a Ni , ( OH).通过 x 射线衍射和红外光谱 对掺杂 L a的 N ( H), i O 进行 结构表征 , 并采 用模拟 电池和循环 伏安法对其 电化 学性 能进行研 究.研 究结果表 明:掺 杂 L 的 N ( H) 具有与 cNi ) 相似 的 a i O 2 【 ( 2 一 OH 晶体结构 ,具有较 人的层间距 ,有利 丁 质 子的迁 移,其分 子中的 O 不冉处于 H‘
[ 中]8淳淳( 刊, / 北京化工大学材料科学 与工程学院 , 北京 10 2 ) 0 0 9,王紫色 ,王 菊 琳 /化 工 学 报 . 20 / - 05, 5(2. 61) 一
2 7 ~ 2 7 33 39
模拟土壤介质 中仿古铸铁 腐蚀 产物 的形
貌 及 其 生 长 过 程- p e ac dfr - p a nea ma A r n o
t n p o e s o o r so r d c s o - i r c s f c ro i n p o u t n a o r c a o o i a r n i i l td s i me i h e l g c l o n smu ae ol i da
煤化工考试重点总结范文
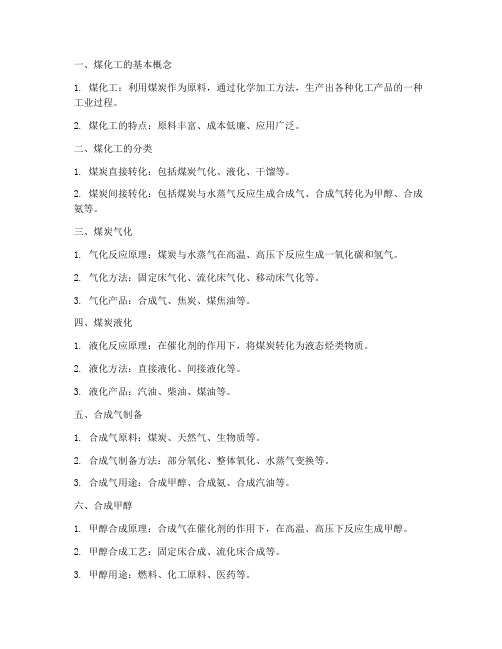
一、煤化工的基本概念1. 煤化工:利用煤炭作为原料,通过化学加工方法,生产出各种化工产品的一种工业过程。
2. 煤化工的特点:原料丰富、成本低廉、应用广泛。
二、煤化工的分类1. 煤炭直接转化:包括煤炭气化、液化、干馏等。
2. 煤炭间接转化:包括煤炭与水蒸气反应生成合成气、合成气转化为甲醇、合成氨等。
三、煤炭气化1. 气化反应原理:煤炭与水蒸气在高温、高压下反应生成一氧化碳和氢气。
2. 气化方法:固定床气化、流化床气化、移动床气化等。
3. 气化产品:合成气、焦炭、煤焦油等。
四、煤炭液化1. 液化反应原理:在催化剂的作用下,将煤炭转化为液态烃类物质。
2. 液化方法:直接液化、间接液化等。
3. 液化产品:汽油、柴油、煤油等。
五、合成气制备1. 合成气原料:煤炭、天然气、生物质等。
2. 合成气制备方法:部分氧化、整体氧化、水蒸气变换等。
3. 合成气用途:合成甲醇、合成氨、合成汽油等。
六、合成甲醇1. 甲醇合成原理:合成气在催化剂的作用下,在高温、高压下反应生成甲醇。
2. 甲醇合成工艺:固定床合成、流化床合成等。
3. 甲醇用途:燃料、化工原料、医药等。
七、合成氨1. 氨合成原理:合成气在催化剂的作用下,在高温、高压下反应生成氨。
2. 氨合成工艺:合成氨装置、合成氨催化剂等。
3. 氨用途:化肥、合成氨水溶液、硝酸等。
八、煤化工的环保与安全1. 环保:减少污染物排放、提高资源利用率、降低能源消耗等。
2. 安全:加强安全管理、防止事故发生、提高应急处理能力等。
九、煤化工发展趋势1. 提高煤炭资源利用率,降低能源消耗。
2. 发展清洁煤化工技术,减少污染物排放。
3. 推广新型煤化工工艺,提高产业竞争力。
通过以上总结,可以看出煤化工考试的重点主要集中在煤炭的转化、合成气制备、合成产品、环保与安全以及发展趋势等方面。
考生在复习时应重点关注这些内容,并结合实际案例进行分析,提高自己的解题能力。
祝广大考生在煤化工考试中取得优异成绩!。
煤化学工程

以管 式 电炉为热解 室,改变热解终温 , 在惰 性气 氛下对无烟 煤与烟煤 的混煤 进 行快速 加热条件下 的热解.采用低温 氮 气 吸附方 法研究 混煤焦 表面形态 的变 化 规律 .通过对吸 附等温 线的分析 ,表 明 煤焦 具有连续 、完整 的孔隙结构 ,无 定 形孔 的存在使得 吸附迪 线存在不 闭合的 状态 .随着热解终温 的升高 ,混煤焦 的 比表 面积 先增加后减 小 ;随着烟煤 掺混 比例 的增加 ,混煤焦 的微孔容积和表 面 积 也先增加后 减小 ,A1 2 混煤焦具 有 B 最大 微孔容积和表 面积 .对煤焦孔 隙的 分形研 究发现煤焦孔 隙分形维数 与微 孔
关键词 :精 细水煤浆 ;表 面分 形;燃烧 特性
7 255 0217 5 0・4 3 7
研究 了用偶联剂 处理玻璃微珠 的方 法及 其对全水发泡硬 质聚氨酯泡沫 的微 观形 貌和压缩性 能的影响.试验结 果表 明, 通过适 当的方法 可以将偶联剂 以氢键 或 化学键 的方 式连 接到玻璃微珠表面 ,经 过偶联 剂处 理的玻璃微珠与硬质聚 氨酯 泡沫基 体具 有较 好的相容性和 界面 强度, 并且用玻璃微珠 K4 ( 6偶联剂 K 5 0处 H5 理 ) 强的聚 氨酯 泡沫 压缩 强度 和压 缩 增 模量有提高. 图 1 0表 1 7 参 关键词 :硬质聚 氨酯泡沫塑料 ;玻璃微 珠 ;偶联剂 ;压缩强度 ;压缩 模量
2 0 ,5 ( ) 1 1 ~ 1 1 0 7 87 . 8 0 8 5 一
旰U ,中] 平传娟( / 浙江大学 能源清洁 利 用 国家重 点实验室 , 杭州 3 0 2 ) 10 7,周俊 虎 ,程 军 ,杨 卫 娟 ,来自 可 法 ∥化 工 学 报 .
一
2 0 ,5 ( ) 1 9 ~ 1 0 0 7 87 . 7 8 8 4 一
大唐煤化工项目工艺概况
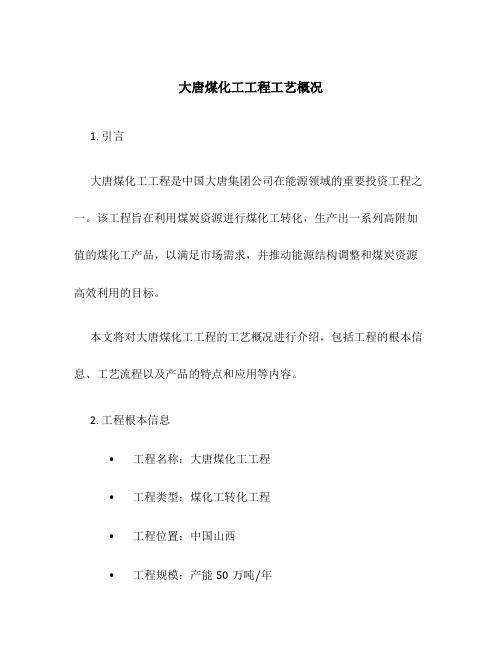
大唐煤化工工程工艺概况1. 引言大唐煤化工工程是中国大唐集团公司在能源领域的重要投资工程之一。
该工程旨在利用煤炭资源进行煤化工转化,生产出一系列高附加值的煤化工产品,以满足市场需求,并推动能源结构调整和煤炭资源高效利用的目标。
本文将对大唐煤化工工程的工艺概况进行介绍,包括工程的根本信息、工艺流程以及产品的特点和应用等内容。
2. 工程根本信息•工程名称:大唐煤化工工程•工程类型:煤化工转化工程•工程位置:中国山西•工程规模:产能50万吨/年3. 工艺流程大唐煤化工工程采用了煤气化技术和合成气体转化技术,通过将煤炭进行气化处理,生成合成气,再将合成气通过一系列化学反响,制造出多种煤化工产品。
工程的工艺流程主要包括以下几个步骤:3.1 煤气化煤气化是将煤炭在高温和缺氧条件下进行气化反响,生成合成气的过程。
在大唐煤化工工程中,采用了常压煤气化技术,主要包括煤炭的破碎、枯燥、预处理、气化反响和炉渣处理等步骤。
3.2 合成气体转化合成气体转化是将合成气中的一氧化碳和氢气进行化学反响,生成各种煤化工产品的过程。
在大唐煤化工工程中,采用了催化剂和适当的温度、压力和反响时间等条件,将合成气转化为甲醇、液化石油气、氨等产品。
3.3 产品别离和纯化在合成气体转化反响后,产生的混合气体中含有多种煤化工产品和副产物。
为了得到纯洁的煤化工产品,需要进行产品的别离和纯化。
在大唐煤化工工程中,采用了适当的别离技术,如蒸汽吸附和洗涤,以获得高纯度的煤化工产品。
4. 产品特点和应用大唐煤化工工程所生产的产品具有以下特点:•高纯度:通过优化的工艺流程和纯化技术,产品的纯度到达了行业标准要求。
•多样性:工程生产的产品种类丰富,包括甲醇、液化石油气、氨等多种煤化工产品。
•高附加值:煤化工产品是高附加值的化工原料,可以用于制造化学品、燃料和材料等。
这些产品可以应用于以下领域:•化学工业:作为根底化学品和有机合成中间体,用于生产塑料、纤维、橡胶、涂料等化学品。
现代煤化工知识点总结
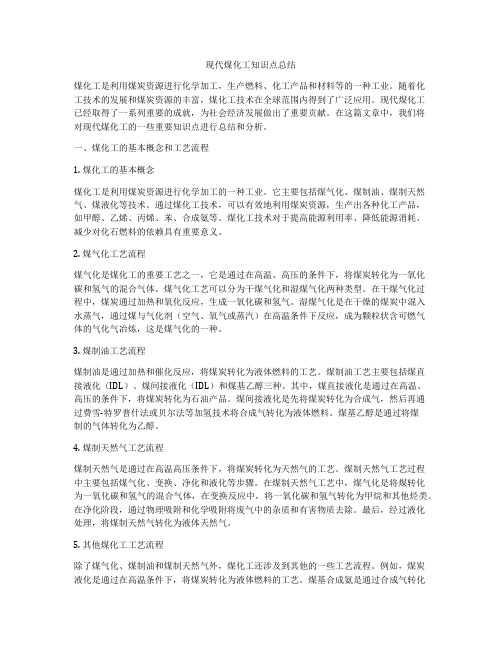
现代煤化工知识点总结煤化工是利用煤炭资源进行化学加工,生产燃料、化工产品和材料等的一种工业。
随着化工技术的发展和煤炭资源的丰富,煤化工技术在全球范围内得到了广泛应用。
现代煤化工已经取得了一系列重要的成就,为社会经济发展做出了重要贡献。
在这篇文章中,我们将对现代煤化工的一些重要知识点进行总结和分析。
一、煤化工的基本概念和工艺流程1. 煤化工的基本概念煤化工是利用煤炭资源进行化学加工的一种工业。
它主要包括煤气化、煤制油、煤制天然气、煤液化等技术。
通过煤化工技术,可以有效地利用煤炭资源,生产出各种化工产品,如甲醇、乙烯、丙烯、苯、合成氨等。
煤化工技术对于提高能源利用率、降低能源消耗、减少对化石燃料的依赖具有重要意义。
2. 煤气化工艺流程煤气化是煤化工的重要工艺之一,它是通过在高温、高压的条件下,将煤炭转化为一氧化碳和氢气的混合气体。
煤气化工艺可以分为干煤气化和湿煤气化两种类型。
在干煤气化过程中,煤炭通过加热和氧化反应,生成一氧化碳和氢气。
湿煤气化是在干燥的煤炭中混入水蒸气,通过煤与气化剂(空气、氧气或蒸汽)在高温条件下反应,成为颗粒状含可燃气体的气化气冶炼,这是煤气化的一种。
3. 煤制油工艺流程煤制油是通过加热和催化反应,将煤炭转化为液体燃料的工艺。
煤制油工艺主要包括煤直接液化(IDL)、煤间接液化(IDL)和煤基乙醇三种。
其中,煤直接液化是通过在高温、高压的条件下,将煤炭转化为石油产品。
煤间接液化是先将煤炭转化为合成气,然后再通过费雪-特罗普什法或贝尔法等加氢技术将合成气转化为液体燃料。
煤基乙醇是通过将煤制的气体转化为乙醇。
4. 煤制天然气工艺流程煤制天然气是通过在高温高压条件下,将煤炭转化为天然气的工艺。
煤制天然气工艺过程中主要包括煤气化、变换、净化和液化等步骤。
在煤制天然气工艺中,煤气化是将煤转化为一氧化碳和氢气的混合气体,在变换反应中,将一氧化碳和氢气转化为甲烷和其他烃类。
在净化阶段,通过物理吸附和化学吸附将废气中的杂质和有害物质去除。
煤化工工程2
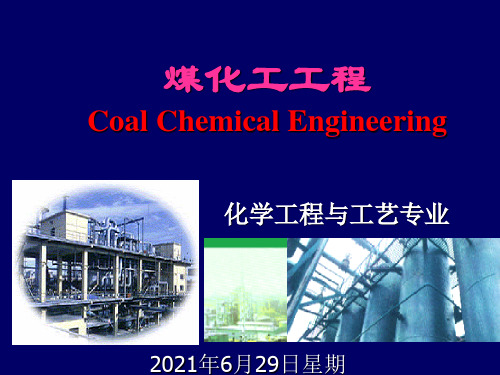
七、化学方法研究煤
1、煤中的官能团分析
(1)含氧官能团 1)主要含氧官能团的测定方法 ➢羟基(-OH)
➢羧基(-COOH) ➢羰基(C=O)
➢甲氧基(-OCH3)
➢非活性氧(-O-)
2)煤中含氧官能团随煤化度的变化
煤中含氧官能团随煤化度增加 而急剧降低, 其中以羟基降低最多,其次是羰基和羧基。
结果的计算
空气干燥煤样的灰分按下式计算:
式中Aad——空气干燥煤样的灰分产率,%; m1——残留物的质量,g; m——煤样的质量,g。
煤中灰分的组成:
我国煤炭的平均灰分含量为25% 灰分的存在降低了煤的热值,也增加了烟尘污染和出渣量
煤中矿物质来源:
原生矿物质——存在于成煤植物中的矿物质。 次生矿物质——成煤过程中,由外界混入煤层
3)干燥基(dry):指绝对干燥的煤的组成。这种基准不受煤在开采、 运输和贮存过程中水分变动的影响,能比较稳定地反映成批贮存煤 的真实组成,在各组成的右下角以“d”表示。
Vd+FCd+Ad=100%
4)干燥无灰基(dry ash free):指假想的无水无灰的煤的组成,由 于煤的灰分在开采、运输或洗煤过程中要发生变化,故除去灰分和 水分后的煤组成,可排除外界条件的影响。该基准在各组成的右下 角以“daf”表示。
煤的可选性曲线
中国表示煤炭可选性特征的方法是:先 做原煤的筛分试验,然后进行各粒度 级煤样的浮沉试验( GB478) 并绘制出 煤的可选性曲线。
煤炭气化的工艺性质及气化用煤的质量指标
1、煤的反应性 煤的反应性又称煤的化学活性,指在一定温度条件下 煤与不同气体介质(如二氧化碳、氧、水蒸气等) 发 生化学反应的能力。 2、煤的机械强度 煤的机械强度指煤对外力作用时的抵抗能力,包括煤 的抗碎强度、耐磨强度和抗压强度等物理性质
煤化工技术专业介绍

煤化工技术专业介绍煤化工技术是利用煤炭作为原料开发生产化工产品的一门技术。
煤化工技术是继石油化工、天然气化工之后发展的第三大化工领域。
它是将煤炭中的有机物质通过物理、化学或生化反应转化为有用的化工产品,包括煤制燃料、煤制气、煤制石油化工、合成氨、合成甲醇、合成乙烯、合成乙二醇、有机酸、聚碳酸酯、聚苯乙烯、聚酯纤维等。
煤化工技术是现代化工技术中的重要领域之一,具有以下特点:1. 原料广泛:煤炭资源丰富,不仅在国内广泛分布,而且在世界范围内也具有重要地位。
且热值高、不易受季节和天气等自然因素影响,具有比较稳定的供应和价格。
2. 改善环境:传统化工生产中,石油、天然气等化石能源的开采和加工对环境污染较大。
而煤炭的开采和利用方式相对较简单,采用煤化工技术可以使煤的利用率提高,减少对环境的污染,且更为节能。
3. 开发前景广:随着世界经济的发展,对能源需求越来越大,而且越来越看重资源的多元化。
在石油、天然气等化石能源的供应紧张的情况下,煤炭得到了更多的重视。
因此,煤化工技术具有很好的发展前景。
煤化工技术专业主要涉及煤化学、有机化学、化工原理和反应工程等方面的知识。
主要课程包括:1. 煤种分类与煤化学基础2. 煤制气工艺学3. 煤制油与煤制燃料加工学4. 煤液化原理与工艺5. 合成氨与合成甲醇技术6. 合成乙烯工艺学7. 聚合物制备工艺学8. 煤化工过程控制与优化职业发展前景煤化工技术专业毕业生可在煤炭企业、化工企业、能源研究机构等单位从事煤化工技术相关的研究、设计、生产等工作。
未来,随着煤炭资源的逐渐减少和环保要求的提高,煤化工技术将面临更多的挑战和机遇。
为适应这种趋势,煤化工专业的学生需要具备良好的计算机技术、英语阅读与写作能力、创新思维、团队协作能力以及环境保护意识等。
未来,煤化工技术专业毕业生的就业市场将更加广阔。
煤化工教学大纲

煤化工教学大纲煤化工教学大纲煤化工作为一门重要的工程学科,涵盖了煤炭资源的开发利用、煤炭转化为化工产品的过程以及相关的环境保护和安全管理等方面的内容。
为了保证煤化工专业的教学质量和培养学生的综合能力,制定一份科学合理的煤化工教学大纲至关重要。
一、绪论煤化工教学大纲的绪论部分应该包括对煤化工学科的概述,介绍煤炭资源的重要性以及煤化工技术的发展现状和前景。
同时,还应该明确煤化工教学的目标和任务,以及培养学生的核心素养和职业能力的要求。
二、课程设置煤化工教学大纲的课程设置部分应该明确各门课程的名称、学时、学分和内容。
煤化工专业的核心课程包括煤化学、煤炭资源与利用、煤炭转化工程、煤化工过程与设备、煤化工产品制备与应用等。
此外,还应该设置一些选修课程,以满足学生的个性化需求和专业发展方向。
三、教学目标煤化工教学大纲的教学目标部分应该明确学生在学习过程中需要达到的知识、能力和素养。
对于煤化工专业的学生来说,他们需要具备扎实的专业基础知识,掌握煤化工的基本理论和技术,具备煤炭资源开发利用和煤化工产品制备的能力,同时还需要具备科学研究和工程实践的能力。
四、教学内容煤化工教学大纲的教学内容部分应该具体明确各门课程的内容和重点。
例如,在煤化学课程中,应该包括煤的组成与结构、煤的物理性质和化学性质、煤的热解和气化过程等内容。
在煤炭转化工程课程中,应该包括煤的洗选和煤的干燥技术、煤的气化和煤的液化工艺等内容。
通过明确教学内容,可以保证教学的系统性和完整性,提高学生的学习效果。
五、教学方法煤化工教学大纲的教学方法部分应该明确教师在教学过程中应采用的教学方法和手段。
煤化工教学应该注重理论与实践相结合,通过实验室实践、工程实习和科研训练等方式,培养学生的实际操作能力和问题解决能力。
此外,还应该鼓励学生参与科研项目和工程实践,提高他们的创新能力和团队合作精神。
六、教学评价煤化工教学大纲的教学评价部分应该明确教学评价的目的、内容和方法。
煤化学工程在煤炭加工中的应用与研究进展
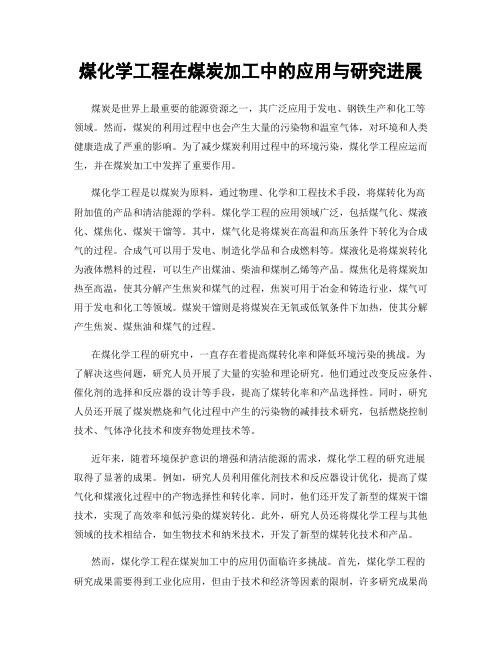
煤化学工程在煤炭加工中的应用与研究进展煤炭是世界上最重要的能源资源之一,其广泛应用于发电、钢铁生产和化工等领域。
然而,煤炭的利用过程中也会产生大量的污染物和温室气体,对环境和人类健康造成了严重的影响。
为了减少煤炭利用过程中的环境污染,煤化学工程应运而生,并在煤炭加工中发挥了重要作用。
煤化学工程是以煤炭为原料,通过物理、化学和工程技术手段,将煤转化为高附加值的产品和清洁能源的学科。
煤化学工程的应用领域广泛,包括煤气化、煤液化、煤焦化、煤炭干馏等。
其中,煤气化是将煤炭在高温和高压条件下转化为合成气的过程。
合成气可以用于发电、制造化学品和合成燃料等。
煤液化是将煤炭转化为液体燃料的过程,可以生产出煤油、柴油和煤制乙烯等产品。
煤焦化是将煤炭加热至高温,使其分解产生焦炭和煤气的过程,焦炭可用于冶金和铸造行业,煤气可用于发电和化工等领域。
煤炭干馏则是将煤炭在无氧或低氧条件下加热,使其分解产生焦炭、煤焦油和煤气的过程。
在煤化学工程的研究中,一直存在着提高煤转化率和降低环境污染的挑战。
为了解决这些问题,研究人员开展了大量的实验和理论研究。
他们通过改变反应条件、催化剂的选择和反应器的设计等手段,提高了煤转化率和产品选择性。
同时,研究人员还开展了煤炭燃烧和气化过程中产生的污染物的减排技术研究,包括燃烧控制技术、气体净化技术和废弃物处理技术等。
近年来,随着环境保护意识的增强和清洁能源的需求,煤化学工程的研究进展取得了显著的成果。
例如,研究人员利用催化剂技术和反应器设计优化,提高了煤气化和煤液化过程中的产物选择性和转化率。
同时,他们还开发了新型的煤炭干馏技术,实现了高效率和低污染的煤炭转化。
此外,研究人员还将煤化学工程与其他领域的技术相结合,如生物技术和纳米技术,开发了新型的煤转化技术和产品。
然而,煤化学工程在煤炭加工中的应用仍面临许多挑战。
首先,煤化学工程的研究成果需要得到工业化应用,但由于技术和经济等因素的限制,许多研究成果尚未得到广泛应用。
煤化学工程
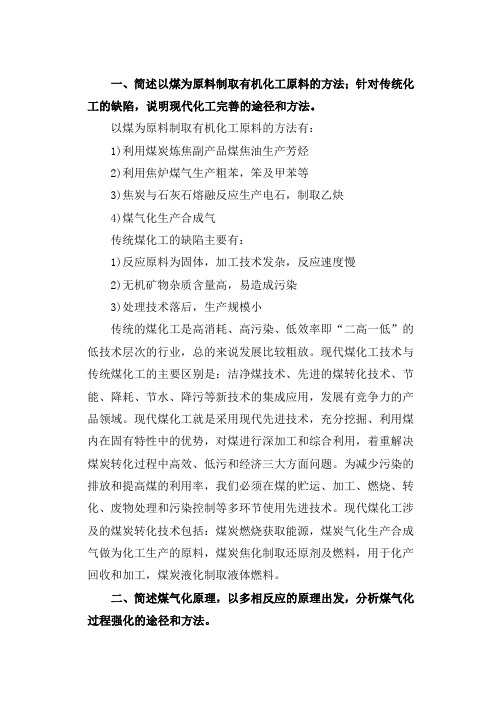
一、简述以煤为原料制取有机化工原料的方法;针对传统化工的缺陷,说明现代化工完善的途径和方法。
以煤为原料制取有机化工原料的方法有:1)利用煤炭炼焦副产品煤焦油生产芳烃2)利用焦炉煤气生产粗苯,笨及甲苯等3)焦炭与石灰石熔融反应生产电石,制取乙炔4)煤气化生产合成气传统煤化工的缺陷主要有:1)反应原料为固体,加工技术发杂,反应速度慢2)无机矿物杂质含量高,易造成污染3)处理技术落后,生产规模小传统的煤化工是高消耗、高污染、低效率即“二高一低”的低技术层次的行业,总的来说发展比较粗放。
现代煤化工技术与传统煤化工的主要区别是:洁净煤技术、先进的煤转化技术、节能、降耗、节水、降污等新技术的集成应用,发展有竞争力的产品领域。
现代煤化工就是采用现代先进技术,充分挖掘、利用煤内在固有特性中的优势,对煤进行深加工和综合利用,着重解决煤炭转化过程中高效、低污和经济三大方面问题。
为减少污染的排放和提高煤的利用率,我们必须在煤的贮运、加工、燃烧、转化、废物处理和污染控制等多环节使用先进技术。
现代煤化工涉及的煤炭转化技术包括:煤炭燃烧获取能源,煤炭气化生产合成气做为化工生产的原料,煤炭焦化制取还原剂及燃料,用于化产回收和加工,煤炭液化制取液体燃料。
二、简述煤气化原理,以多相反应的原理出发,分析煤气化过程强化的途径和方法。
将煤炭转化为气态产物的工艺过程。
通过煤与空气、氢气、氧气、水蒸气中的一种或几种的混合物的化学反应得出气态产物,即煤气,这种过程称为煤的气化。
煤气主要由二氧化碳、一氧化碳、氢气、甲烷等气体组成,煤气化过程包括10个基本反应,化学方程式如下CO+O2=CO2-393.8KJ/mol2C+O2=2CO-231.4KJ/molC+CO2=2CO+162.4 KJ/molC+H2O(g)=CO+H2+131.5 KJ/molC+2H2O(g)=CO2+H2+90.0 KJ/molCO+H2O=CO2+H2-41.5 KJ/molC+2H2=CH4-74.9 KJ/molCO+3H2=CH4+H2O-206.4 KJ/mol2CO+2H2=CH4+CO2+247.3 KJ/molCO2+4H2=CH4+2H2O+253.7 KJ/mol煤炭的气化属于固气两相之间的反应,提高气化过程强度可采取以下方法:1)提高气化反应温度2)减小原料煤粒度(增大原料煤的比表面积,增加气固接触面积)3)增强气化剂和煤粒间的相对运动4)提高气化剂中的氧含量5)增大气相压力(提高单位体积内气体物质的分子数)6)使用催化剂(改变反应的路径)三、结合煤分子结构的现代认识,说明烟煤炼焦的原理;讨论炼焦工艺参数对结焦过程的影响,并分析改善炼焦过程,提高焦炭质量的途径。
煤化学教学大纲
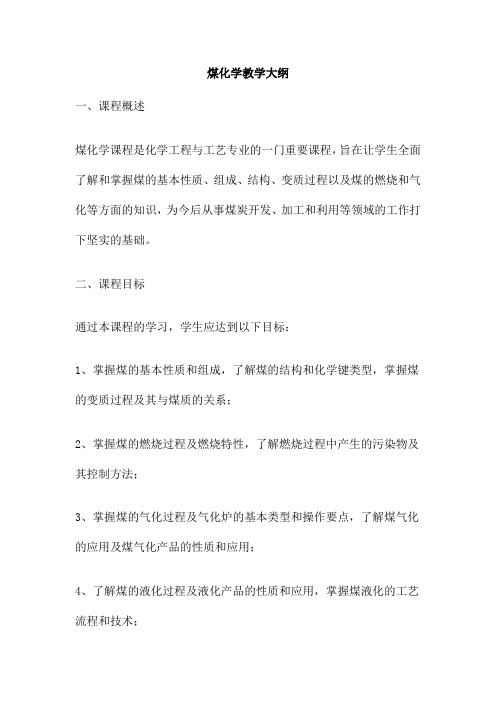
煤化学教学大纲一、课程概述煤化学课程是化学工程与工艺专业的一门重要课程,旨在让学生全面了解和掌握煤的基本性质、组成、结构、变质过程以及煤的燃烧和气化等方面的知识,为今后从事煤炭开发、加工和利用等领域的工作打下坚实的基础。
二、课程目标通过本课程的学习,学生应达到以下目标:1、掌握煤的基本性质和组成,了解煤的结构和化学键类型,掌握煤的变质过程及其与煤质的关系;2、掌握煤的燃烧过程及燃烧特性,了解燃烧过程中产生的污染物及其控制方法;3、掌握煤的气化过程及气化炉的基本类型和操作要点,了解煤气化的应用及煤气化产品的性质和应用;4、了解煤的液化过程及液化产品的性质和应用,掌握煤液化的工艺流程和技术;5、掌握煤的分析方法和煤质评价,了解煤的分类和分级及其与煤质的关系。
三、课程内容本课程主要包括以下内容:1、煤的基本性质和组成:包括煤的物理性质、化学组成、结构、矿物质和有害元素等;2、煤的变质过程:介绍煤的变质规律及与煤质的关系,包括地质变质、高温变质和化学变质等;3、煤的燃烧过程:介绍煤燃烧的基本原理和燃烧特性,包括燃烧反应动力学、燃烧过程污染物的产生与控制等;4、煤的气化过程:介绍煤气化的基本原理和气化炉的类型,包括固定床气化炉、流化床气化炉和气流床气化炉等;5、煤的液化过程:介绍煤液化的基本原理和工艺流程,包括直接液化和间接液化等;6、煤的分析方法和煤质评价:介绍煤的分析方法和指标,包括工业分析、元素分析和热值等,同时介绍煤质的评价方法和指标。
四、教学安排本课程为3学分,总学时数为54学时,其中理论授课36学时,实验18学时。
教学内容应结合实际案例和实践操作进行讲解,注重培养学生的实际操作能力和解决问题的能力。
同时应安排适当的复习和预习时间,帮助学生巩固所学知识。
一、指导思想坚持以《幼儿园教育指导纲要》为指导,进一步深入学习《3-6岁儿童学习与发展指南》,深刻领会指南的精神,转变教师观念,为幼儿今后的发展打下扎实的基础。
- 1、下载文档前请自行甄别文档内容的完整性,平台不提供额外的编辑、内容补充、找答案等附加服务。
- 2、"仅部分预览"的文档,不可在线预览部分如存在完整性等问题,可反馈申请退款(可完整预览的文档不适用该条件!)。
- 3、如文档侵犯您的权益,请联系客服反馈,我们会尽快为您处理(人工客服工作时间:9:00-18:30)。
一、简述以煤为原料制取基本有机化工原料的方法;针对传统煤化工的缺陷,说明现代煤化工完善的途径和方法。
答:以煤为原料制取有机化工原料的方法有:1)利用煤炭炼焦副产品煤焦油生产芳烃2)利用焦炉煤气生产粗苯,笨及甲苯等3)焦炭与石灰石熔融反应生产电石,制取乙炔4)煤气化生产合成气具体工艺方法及流程见下图传统煤化工的缺陷主要有:1)反应原料为固体,加工技术发杂,反应速度慢2)无机矿物杂质含量高,易造成污染3)处理技术落后,生产规模小现代煤化工完善的途径和方法:发展和完善现代煤化工需要扩大原料煤的适应性。
我国高硫、高灰的劣质煤比重较高,有大量的褐煤,如何利用这些煤作为原料煤进行煤炭气化、液化等化工过程具有重大的意义。
大型化、多联产、一体化是煤化工未来发展的方向。
现代煤气化工程采用先进的气化炉和气化工艺,极大的扩大了原料煤的种类,使煤炭资源得到了更加合理的利用。
配煤炼焦技术通过原料煤性质的不同,按一定的比例进行掺杂,来获得较高的成焦效果,扩大了我国炼焦煤资源。
大型化能够提高整体的运行效率,降低生产成本。
多联产、一体化对于化工过程中产生的各种副产物进行综合有效的利用,减少产品运输过程中的花费。
以建设大型企业及大的产业集群为主,根据煤种、煤制特点及目标产品不同,采用不同煤转化技术,有效利用煤化工过程中产生的各种副产品进行综合利用,并且与化工产品形成一体化产业,发挥资源与价格优势,资源优化配置,使资源、能源得到高效合理利用,降低生产成本、提高综合经济效益。
二、简述煤气化原理,以多相反应的原理出发,分析煤气化过程强化的途径和方法。
煤炭气化是指以煤或煤焦为原料,以氧气(空气、富氧或纯氧)、水蒸气或氢气等作气化剂,在一定温度和压力下通过化学反应将固体煤或煤焦中的可燃部分转化为气体燃料的热化学过程。
其反应过程主要为:碳的氧化反应 CO+O2=CO2-393.8KJ/mol碳的部分氧化反应2C+O2=2CO-231.4KJ/mol二氧化碳还原反应 C+CO2=2CO+162.4 KJ/mol水蒸气分解反应 C+H2O(g)=CO+H2+131.5 KJ/mol水蒸气分解反应 C+2H2O(g)=CO2+H2+90.0 KJ/mol一氧化碳变换反应 CO+H2O=CO2+H2-41.5 KJ/mol碳的加氢反应 C+2H2=CH4-74.9 KJ/mol甲烷化反应 CO+3H2=CH4+H2O-206.4 KJ/mol甲烷化反应 2CO+2H2=CH4+CO2+247.3 KJ/mol甲烷化反应 CO2+4H2=CH4+2H2O+253.7 KJ/mol其中在气化过程中,煤炭主要经历干燥、干馏、气化、燃烧几个过程。
碳的燃烧反应主要为气化提供热量,气化过程的核心反应为二氧化碳的还原和水蒸气分解反应。
煤炭的气化属于固气两相之间的反应,提高气化过程强度可采取以下方法:(1)提高气化反应温度:高温使得气体的热运动剧烈,扩散速率加快,从而提高反应速率;(2)减小原料煤粒度:不仅可以缩短气化剂或产物煤气的内扩散的路程,减少了扩散所需时间,而且增大了煤粒的比表面积,从而提高反应速率(3)增强气化剂和煤粒间的相对运动(气流床气化>流化床气化>固定床气化,强化了气固两相之间的混合)(4)提高气化剂中的氧含量(使燃烧充分,提高气化炉内温度)(5)增大气相压力(提高单位体积内气体物质的分子数,强化了气化剂的扩散过程,使反应速率加快)(6)使用催化剂(改变反应的路径)三、结合煤分子结构的现代认识,说明烟煤炼焦的原理;讨论炼焦工艺参数对结焦过程的影响,并分析改善炼焦过程,提高焦炭质量的途径。
煤的有机质是由大量相对分子质量不同、分子结构相似但不完全相同的“相似化合物”组成的混合物。
根据实验研究,煤的有机质可以大体分为两部分:一部分是以方向结构为主的环状化合物,称为大分子化合物,另一部分是以链状结构为主的化合物,称为低分子化合物。
煤的大分子是由多个结构相似的“基本结构单元”通过桥键连接而成的。
这种基本结构单元类似于聚合物的聚合单体,它可分为规则部分和不规则部分。
规则部分由几个或几十个苯环、脂环、氢化芳香环及杂环(含氮、氧、硫等元素)缩聚而成,称为基本结构单元或芳香核;不规则部分则是连接在核周围的烷基侧链和各种官能团;桥键则是连接相邻基本结构单元的原子或原子团。
煤在炼焦的过程中,随温度的升高,连在核上的侧链不断脱落分解。
芳核本身则缩合合并稠环化,反应最终形成煤气、化学产品和焦炭。
在化学反应的同时,伴有煤软化形成胶质体,胶质体固化黏结,以及膨胀、收缩和裂纹等现象产生。
反应过程中,当温度逐渐上升,在室温-300℃,煤料先后经历干燥阶段和脱吸阶段;当煤受热温度在300~450℃左右时,煤、发生激烈的分解、解聚反应,产生热解的一次气体(主要是CH4、不饱和烃等焦油蒸汽),同时形成胶质体,由于胶质体透气性H2不好,气体析出不易,产生了对炉墙的膨胀压力。
450~550℃胶质体加速分解,当超过胶质体固化温度时,则发生黏结现象,产生半焦。
当温度超过550~750℃左右时,半焦分解析出热解二次气体,半焦体积收缩产生裂纹;当温度超过750~1050℃阶段,半焦进一步分解、缩聚,最后转化为焦炭。
工艺参数对炼焦过程的影响—(1)煤料的散密度。
散密度提高,煤粒间的间隙减小,在炼焦过程中胶质体易于填满孔隙,气体不易析出,胶质体的膨胀性和流动性都增加,使煤粒间的接触更加紧密,形成结构坚实的焦炭。
另外,散密度高,炼焦过程中半焦收缩小,因而焦炭裂纹少,提高了焦炭的强度。
(2)加热速度。
炼焦过程分为低温阶段和高温阶段。
低温阶段主要是胶质体形成阶段。
高温阶段主要是半焦形成焦炭。
在炼焦过程中希望低温阶段能够快速加热,能使煤料的胶质体温度范围变宽。
高温阶段则希望有较低的升温速度,因为半焦中不稳定部分受热后,不断裂解,形成气态产物。
残留部分不断地缔合增谈。
由于半焦失重紧密化,产生了体积收缩。
因为半焦受热不均,存在收缩梯度,而且相邻层又不能自由移动,固有收缩应力产生。
当收缩应力大于焦饼强度时,则出现裂纹。
降低升温速度,有助于半焦受热均匀,减小收缩应力,防止焦炭开裂。
对煤进行预热,可以有效地改善。
预热煤装炉炼焦能够提高装煤量,提高焦炭质量。
在低温阶段可以迅速的提高温度。
(3)煤料的细度。
当细度过大,配合煤混合不均匀,焦炭内部结构不均一,强度降低;当细度国小,煤料表面积升高,固体颗粒对胶质体液相吸附作用增强,胶质体粘度增加,流动相下降,不利于粘结。
(4)配添加物。
必要时可以添加粘结剂如沥青等物质增加结焦过程中的液相物质,此外还有瘦化剂,能够降低炉煤挥发分,减少气体析出量,降低焦炭气孔率,增大块度和抗碎强度。
改善焦炭质量的途径除了调节上述提到的工艺参数,是之达到适合炼焦的途径外,还可以考虑:(1)捣固炼焦。
煤料捣固后,一般堆比重可提高40%左右,因而煤粒间接触致密,使结焦过程中胶质体充满程度大,并减小气体的析出速度,从而提高膨胀压力和粘结性,使焦炭结构变得致密。
(2)煤干燥炼焦。
干煤炼焦可以提高炉煤堆密度,改善焦炭质量。
(3)预热煤炼焦。
预热煤炼焦有利于改善煤料的粘结性和提高焦炭质量。
(4)优化配煤所谓优化配煤就是运用焦炭质量预测方程,在多种煤参加配比炼焦且满足一定的焦炭质量的前提下,筛选出一组成本最低的炼焦用煤及配比。
显而易见,采用优化配煤技术可以在焦炭质量一定的条件下降低炼焦用煤成本,或者在炼焦煤成本一定的条件下,提高焦炭质量。
四、简述煤间接液化的工艺构成,讨论一下F-T 合成原理。
煤气化产生合成气(CO+H 2),再以合成气为原料合成液体燃料或化学产品,此过程称为煤的间接液化,已工业化的煤炭间接液化的工艺有费托(Fischer-Tropsch )合成和甲醇转化制汽油(MTG )的Mobil 工艺。
F-T 合成的原理F-T 合成的基本化学反应是由一氧化碳加氢生成饱和烃和不饱和烃,反应式如下:O nH H C 1)H (2n nCO 222n n 2+→+++当催化剂、反应条件和气体组成不同时,还进行下述平行反应:O H CH 2H CO 222+--⇔+O H CH 3H CO 242+⇔+222CO CH H 2CO +--⇔+222CO 2CH O H 3CO +--⇔+2CO C 2CO +⇔根据热力学平衡计算,上述平行反应,在50~350℃有利于甲烷生成,温度越高越有利。
生成产物的概率顺序为CH 4>烷烃>烯烃>含氧化合物。
反应产物中主要为烷烃和烯烃。
产物中正构烷烃的生成概率随链的长度而减小,正构烯烃则相反。
产物中异构甲基化合物很少。
增大压力,导致反应向容积减少的相对分子质量增大的方向进行,因而长链产物的数量增加。
合成气富含氢时,有利于形成烷烃,如果不出现催化剂积炭,一氧化碳含量高将导致烯烃和醛的增多。
合成反应也能生成含氧化合物,如醇类、醛、酮、酸和酯等。
其化学反应式如下:O H n OH H C n n 2122)1(2nH nCO -+⇔++O nH 1)(2n 1)CO (n 2122+⇔++++CHO H C H n n在F-T 合成中,含氧化合物是作为副产物,其含量已控制到尽可能低的程度。
长期以来,对于合成醇类很感兴趣,用含碱的铁催化剂生成含氧化合物的趋势较大,采用低温、高压和大空速条件进行反应,有利于醇类合成,一般主要产物为乙醇。
当增加反应温度时,例如在气流床方法中,也发现合成产物中有脂环族和芳香族化合物,他们是继续反应的二次产物。
F-T合成的第一步是CO和H2在催化剂上同时进行化学吸附,CO的C原子和催化剂金属结合,形成活化的C-O-键,与活化的氢反应,构成一次复合物,进一步形成链状烃。
链状烃由于表面化合物的加碳作用,使碳链增长。
此增长碳链因脱吸附,加氢或因与合成产物反应而终止。
此反应的主要产物是烷烃和烯烃,副产物是醇、醛和酮。
F-T合成催化剂F-T合成用的催化剂,主要有铁、钴、镍和钌。
其中用于工业生产主要是铁。
这些金属有加氢活性,能形成金属羰基复合物;它们对硫敏感,易中毒。
铁催化剂具有很好的活性,用在固定床反应器的中压合成时,反应温度较低,为220~240℃。
铁催化剂加钾活化,具有比表面积高和热稳定性好的结构,并可载于载体上。
可用的载体为Al2O3、CaO、MgO和SiO2。
铁催化剂由铁盐水溶液,经过沉淀、干燥和氢气还原制成。
当合成低分子产品时,可在较高温度(320~340℃)下进行反应。
用于流化床反应工艺的催化剂为熔铁催化剂,熔铁催化剂是先将磁铁矿与助燃剂融化,然后用氢气还原制成,强度较高但活性较小。
五.简述下列煤化工技术进展(任选一)煤制甲醇煤制天然气煤制烯烃煤制乙二醇煤制甲醇甲醇是重要的化工产品和原料。