硝基苯液相催化加氢制苯胺技术进展
硝基苯加氢制备苯胺的催化体系研究进展
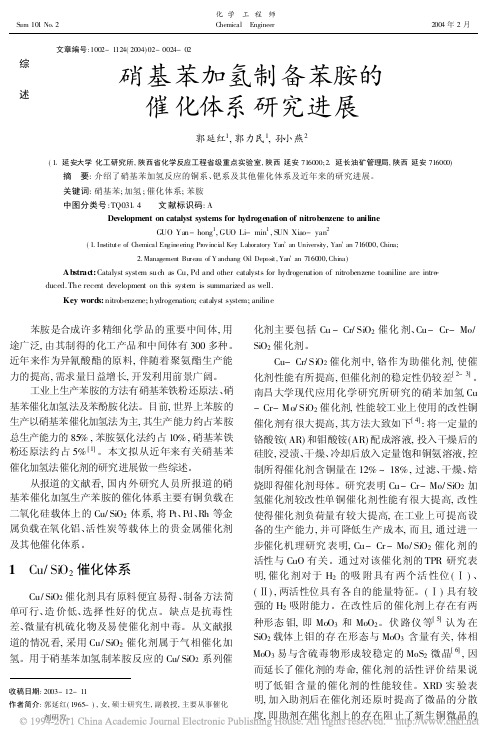
综述文章编号:1002-1124(2004)02-0024-02硝基苯加氢制备苯胺的催化体系研究进展郭延红1,郭力民1,孙小燕2(1 延安大学化工研究所,陕西省化学反应工程省级重点实验室,陕西延安716000;2 延长油矿管理局,陕西延安716000)摘 要:介绍了硝基苯加氢反应的铜系、钯系及其他催化体系及近年来的研究进展。
关键词:硝基苯;加氢;催化体系;苯胺中图分类号:TQ031 4 文献标识码:ADevelopment on catalyst systems for hydrogenation of nitrobenzene to anilineGUO Yan-hong 1,GUO Li-min 1,S UN Xiao-yan 2(1.Institute of Chemical Engineering Provinci al Key Laboratory Yan an Universi ty,Yan an 716000,China;2.Management Bureau of Yanc hang Oil Depos it,Yan an 716000,Chi na)Abstract:Catalyst system such as Cu,Pd and other catalysts for hydrogenation of nitrobenzene toaniline are intro -duced.The recent development on thi s sys tem is summarized as well.Key words:nitrobenzene;hydrogenation;catalyst system;aniline收稿日期:2003-12-11作者简介:郭延红(1965-),女,硕士研究生,副教授,主要从事催化剂研究。
苯胺是合成许多精细化学品的重要中间体,用途广泛,由其制得的化工产品和中间体有300多种。
硝基苯催化加氢制苯胺的安全技术分析
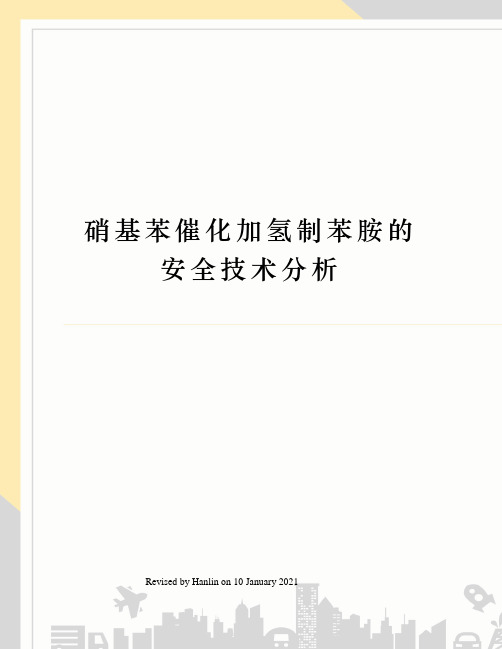
硝基苯催化加氢制苯胺的安全技术分析Revised by Hanlin on 10 January 2021硝基苯催化加氢制苯胺的安全技术分析苯胺是重要的有机化工中间体,广泛地应用于橡胶助剂、染料、感光化学品、医药、农药、炸药及聚氨酯等行业。
由于市场需求较大,近几年改建、扩建及新建一批苯胺生产装置。
但在苯胺及配套装置生产过程中使用大量易燃易爆、有毒有害的危险化学品,加之生产工艺条件苛刻,装置及控制技术要求严格,使其生产过程事故具有突发性、灾害性的特点。
因此,有必要对苯胺的安全生产问题进行认真剖析并提出具体的对策。
1?苯胺生产工艺流程简介以目前国内先进的35000t/a硝基苯催化加氢制苯胺生产装置为例。
苯胺生产中的原料氢与系统中的循环氢混合经氢压机增压至0.2MPa后,与来自流化床顶的高温混合气在热交换器中进行热交换,被预热到约180oC 进入硝基苯汽化器,硝基苯经预热后在汽化器中汽化,与过量的氢气合并过热至180oC~200oC,进入流化床反应器,与催化剂接触。
硝基苯被还原,生成苯胺和水并放出大量热,利用流化床反应器中的余热锅炉中的软水汽化产生蒸气带走反应热来控制反应温度在250oC~270℃。
反应后的混合气与催化剂分离,进热交换器与混合氢进行热交换,用水冷却,粗苯胺及水被冷凝,与过量的氢分离,过量氢循环使用,粗苯胺与饱和苯胺水进入连续分离器,粗苯胺进入脱水塔脱水,然后进精馏塔精馏得到成品苯胺。
苯胺水进共沸塔回收苯胺,废水中含苯胺≤500mg/L,去污水车间进行二级生化处理。
2?苯胺生产中的主要危险介质分析苯胺生产中的危险介质主要是硝基苯、氢气和苯胺。
2.1?硝基苯硝基苯的分子式为C6H5NO2,相对分子质量为123.11,淡黄色透明油状液体,有苦杏仁味,能溶于苯、乙醇及乙醚,难溶于水。
有毒,多量吸人蒸气或经皮肤吸收都会引起中毒,在车间空气中的最高容许浓度为5mg /m3。
常用的理化数据:相对密度1.205(25℃),熔点5.7℃,沸点210.9℃,闪点87.8℃(闭杯),爆炸下限1.8%(93.3℃),自燃点482℃,蒸气密度4.25g/L。
[课外阅读]苯胺制备技术进展概述
![[课外阅读]苯胺制备技术进展概述](https://img.taocdn.com/s3/m/1a95be0631126edb6f1a10d4.png)
[课外阅读]苯胺制备技术进展概述目前苯胺生产工艺路线主要有硝基苯铁粉还原法、苯酚氨化法和硝基苯催化加氢法,分别占苯胺总生产能力的5%、10%和85%,开发的新工艺路线中以苯直接胺化法较有前途,但与实现工业化还有一定距离。
1.硝基苯铁粉还原法该法是最早的苯胺工业生产方法,其污染环境,设备腐蚀严重,操作维护费用高,难以连续化生产,现已基本淘汰,目前只有拜尔在西维吉尼亚洲的新马丁斯维勒的装置采用此工艺。
2.苯酚胺化法苯酚胺化的理论产率为99%,优点是原料易得、生产方法简单、催化剂廉价、产品质量好、“三废”少,适于大规模连续生产,并可根据需要联产二苯胺,但比硝基苯催化加氢工艺成本高,目前只有美国阿里斯特克化学公司和日本三井石油化学公司采用此工艺。
3.硝基苯催化加氢法该法以硝基苯为原料,氢气为还原剂,铜/硅、镍或铂/钯为催化剂,以氢为还原剂,将硝基苯还原生成苯胺,理论产率为99%,我国全部采用该法生产。
该法的硝化环节很关键,设备投资占总固定投资的50%以上。
硝基苯催化加氢生产主要采用混酸硝化法,可采用等温或绝热硝化工艺,等温硝化能耗大,反应时间长,副产物多,收率低,产品质量差;绝热硝化工艺突破了反应必须在低温下恒温操作的传统观念,物料停留时间短,副反应少,是当前最有前途的一种硝化技术。
国外采用绝热硝化工艺的公司较多,而国内的主流技术为等温硝化工艺。
胺化过程包括固定床气相加氢、流化床气相加氢以及硝基苯液相催化加氢工艺。
除德国巴斯夫公司采用流化床外,其他公司多采用固定床反应器。
我国除山东烟台万华聚氨酯集团有限公司采用固定床反应器外,其他公司均采用流化床反应器。
硝基苯催化加氢技术进展硝基苯催化加氢技术不断改进:气相催化加氢改为液相催化加氢;开发活性高、负荷大、稳定性好、机械强度高、寿命长而价廉的催化剂;苯绝热硝化代替苯等温硝化等。
莫贝公司研制出由金、银、铂或钯等贵金属制成的网状、波纹状或蜂窝状催化剂,以甲醇为溶剂,于131~150℃、6.4MPa压力下硝基苯加氢反应63min,苯胺收率98.1%以上。
硝基苯液相催化加氢制备苯胺的研究进展
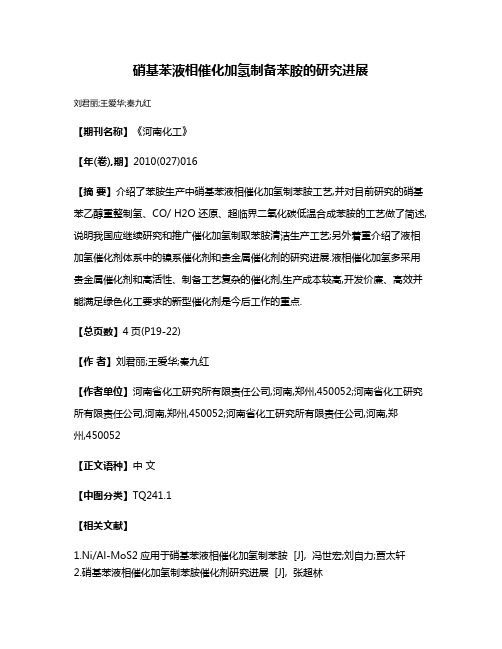
硝基苯液相催化加氢制备苯胺的研究进展
刘君丽;王爱华;秦九红
【期刊名称】《河南化工》
【年(卷),期】2010(027)016
【摘要】介绍了苯胺生产中硝基苯液相催化加氢制苯胺工艺,并对目前研究的硝基苯乙醇重整制氢、CO/ H2O 还原、超临界二氧化碳低温合成苯胺的工艺做了简述,说明我国应继续研究和推广催化加氢制取苯胺清洁生产工艺;另外着重介绍了液相加氢催化剂体系中的镍系催化剂和贵金属催化剂的研究进展.液相催化加氢多采用贵金属催化剂和高活性、制备工艺复杂的催化剂,生产成本较高,开发价廉、高效并能满足绿色化工要求的新型催化剂是今后工作的重点.
【总页数】4页(P19-22)
【作者】刘君丽;王爱华;秦九红
【作者单位】河南省化工研究所有限责任公司,河南,郑州,450052;河南省化工研究所有限责任公司,河南,郑州,450052;河南省化工研究所有限责任公司,河南,郑
州,450052
【正文语种】中文
【中图分类】TQ241.1
【相关文献】
1.Ni/Al-MoS2应用于硝基苯液相催化加氢制苯胺 [J], 冯世宏;刘自力;贾太轩
2.硝基苯液相催化加氢制苯胺催化剂研究进展 [J], 张超林
3.4-甲基-2-硝基苯胺常压液相漆原镍催化加氢制备4-甲基邻苯二胺 [J], 陈金芳;贾涛;黄筱玲
4.硝基苯液相催化加氢制苯胺催化剂研究进展 [J], 张飞宁;仵静;李飞
5.硝基苯液相催化加氢制苯胺技术进展 [J], 张超林
因版权原因,仅展示原文概要,查看原文内容请购买。
硝基苯加氢制苯胺工艺技术

硝基苯加氢制苯胺工艺技术硝基苯加氢制苯胺工艺技术是一种用于合成苯胺的重要工艺技术。
苯胺是一种重要的有机化工原料,广泛用于染料、医药、塑料、橡胶等行业。
硝基苯加氢制苯胺是一种环保、高效的合成方法,下面将介绍其工艺流程和反应原理。
硝基苯加氢制苯胺工艺流程主要包括预处理、催化氢化反应和后处理三个步骤。
预处理主要是将硝基苯原料进行净化,去除杂质。
硝基苯主要存在于硝基苯的混合物中,其中常见的杂质有对硝基苯、间硝基苯等。
预处理的方法可以采用蒸馏、结晶、吸附等工艺,使得硝基苯的纯度达到要求。
催化氢化反应是整个工艺中的核心步骤。
反应的条件一般为高温高压下进行,催化剂一般选择贵金属催化剂。
在反应过程中,硝基苯首先与氢气发生加氢反应,生成亚硝基苯。
亚硝基苯继续与氢气发生加氢反应,生成苯胺。
整个加氢反应的过程具有较高的选择性,可以有效地将硝基苯转化为苯胺。
后处理主要是对反应产物进行分离和纯化。
由于反应产物中还包含有机溶剂、催化剂残留等杂质,需要通过蒸馏、结晶、洗涤等工艺对产物进行纯化,得到纯度较高的苯胺产品。
硝基苯加氢制苯胺的反应原理是通过氢气进行加氢反应,将硝基苯中的硝基基团还原为氨基基团,从而合成苯胺。
反应过程中需要使用催化剂来提高反应速率和选择性。
常用的催化剂有钯、镍等贵金属催化剂,它们具有较高的催化活性和稳定性。
催化剂活性的提高可以通过调整催化剂的结构和制备方法来实现。
此外,反应的条件(温度、压力、物质的摩尔比等)也会对反应的选择性和产率有一定的影响,需要通过合理地选择和控制反应条件来达到最优化的反应结果。
硝基苯加氢制苯胺工艺技术具有高效、环保等特点,能够实现较高的转化率和选择性。
随着环保要求的提高和技术水平的发展,硝基苯加氢制苯胺技术将会得到更广泛的应用和推广。
硝基苯加氢制备苯胺的催化体系研究进展
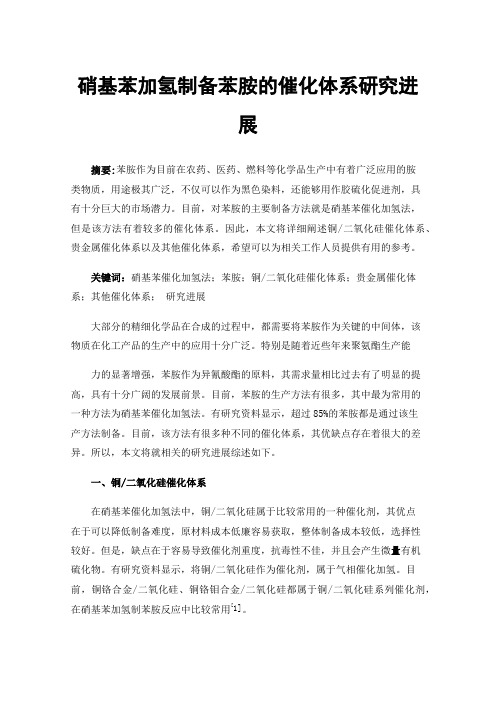
硝基苯加氢制备苯胺的催化体系研究进展摘要:苯胺作为目前在农药、医药、燃料等化学品生产中有着广泛应用的胺类物质,用途极其广泛,不仅可以作为黑色染料,还能够用作胶硫化促进剂,具有十分巨大的市场潜力。
目前,对苯胺的主要制备方法就是硝基苯催化加氢法,但是该方法有着较多的催化体系。
因此,本文将详细阐述铜/二氧化硅催化体系、贵金属催化体系以及其他催化体系,希望可以为相关工作人员提供有用的参考。
关键词:硝基苯催化加氢法;苯胺;铜/二氧化硅催化体系;贵金属催化体系;其他催化体系;研究进展大部分的精细化学品在合成的过程中,都需要将苯胺作为关键的中间体,该物质在化工产品的生产中的应用十分广泛。
特别是随着近些年来聚氨酯生产能力的显著增强,苯胺作为异氰酸酯的原料,其需求量相比过去有了明显的提高,具有十分广阔的发展前景。
目前,苯胺的生产方法有很多,其中最为常用的一种方法为硝基苯催化加氢法。
有研究资料显示,超过85%的苯胺都是通过该生产方法制备。
目前,该方法有很多种不同的催化体系,其优缺点存在着很大的差异。
所以,本文将就相关的研究进展综述如下。
一、铜/二氧化硅催化体系在硝基苯催化加氢法中,铜/二氧化硅属于比较常用的一种催化剂,其优点在于可以降低制备难度,原材料成本低廉容易获取,整体制备成本较低,选择性较好。
但是,缺点在于容易导致催化剂重度,抗毒性不佳,并且会产生微量有机硫化物。
有研究资料显示,将铜/二氧化硅作为催化剂,属于气相催化加氢。
目前,铜铬合金/二氧化硅、铜铬钼合金/二氧化硅都属于铜/二氧化硅系列催化剂,在硝基苯加氢制苯胺反应中比较常用[1]。
在铜铬合金/二氧化硅催化剂中,铬虽然可以起到催化剂的作用,并提高催化剂的性能,然而却无法保证催化剂的稳定性。
我国南昌大学在开展相关的化学研究后发现,使用铜铬钼合金/二氧化硅作为催化剂,相比传统的改性铜催化剂在性能方面有着明显的优势,能够有效提高催化剂的使用性能,并使其生产能力大幅提高,从而减少对苯胺的生产成本。
硝基苯催化加氢制苯胺化工生产安全

硝基苯催化加氢制苯胺化工生产安全一平安生产的重要性和必要性平安生产是指在生产经营活动中,为了避开造成人员损害和财产损失的事故而实行相应的事故预防和掌握措施,使生产过程在符合规定的条件下进行,以保证从业人员的人身平安与健康,设备和设施免受损坏,环境免遭破坏,保证生产经营活动得以顺当进行的相关活动。
平安生产是平安与生产的统一,平安促进生产,生产必需平安。
平安生产关系人民群众的生命财产平安,关系改革进展和社会稳定大局。
搞好平安生产工作,切实保障人民群众的生命财产平安,体现了最广阔人民群众的根本利益,反映了先进生产力的进展要求和先进文化的前进方向。
做好平安生产工作是全面建设小康社会、统筹经济社会全面进展的重要内容,是实施可持续进展战略的组成部分。
二硝基苯催化加氢制苯胺工艺硝基苯催化加氢制苯胺生产方法主要是相应硝基化合物的还原,包括铁粉还原法、硫化碱还原法和催化加氢法等。
其中,催化加氢制备芳胺具有污染少和产品质量高等特点,是环境友好的生产工艺。
硝基苯催化加氢法是目前工业上生产苯胺的主要方法。
它又包括固定床气相催化加氢、流化床气相催化加氢以及硝基苯液相催化加氢三种工艺。
(1)硝基苯催化加氢为放热反应C6H5NO2+3H2=======C6H5NH2+2H2O+544kj/mol固定床气相催化加氢固定床气相催化加氢工艺是在200~300℃、1~3MPa条件下,经预热的氢和硝基苯发生加氢反应生成粗苯胺,粗苯胺经脱水、精馏后得成品,苯胺的选择性大于99%。
固定床气相催化加氢工艺具有技术成熟,优点:反应温度较低,设备及操作简洁,修理费用低,建设投资少,不需分别催化剂,产品质量好等;缺点:是反应压力较高,易发生局部过热而引起副反应和催化剂失活,必需定期更换催化剂。
目前,国外大多数苯胺生产厂家采纳固定床气相加氢工艺,我国山东烟台万华聚氨酯集团有限公司采纳该法进行生产。
(2)流化床气相催化加氢流化床气相催化加氢法是原料硝基苯加热汽化后,与理论量约三倍的氢气混合,进入装有铜—硅胶催化剂的流化床反应器中,在260~280℃条件下进行加氢还原反应生成苯胺和水蒸气,再经冷凝、分别、脱水、精馏得到苯胺产品。
杜邦硝基苯液相加氢技术副产物研究
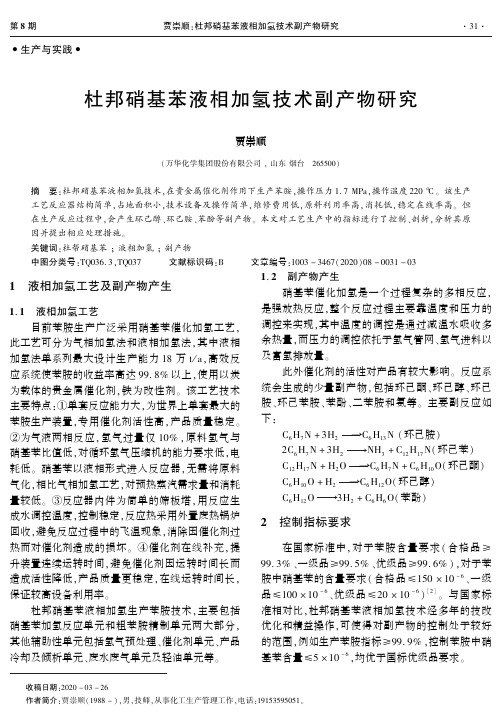
•生产与实践•杜邦硝基苯液相加氢技术副产物研究贾崇顺(万华化学集团股份有限公司ꎬ山东烟台㊀265500)摘㊀要:杜邦硝基苯液相加氢技术ꎬ在贵金属催化剂作用下生产苯胺ꎬ操作压力1.7MPaꎬ操作温度220ħꎮ该生产工艺反应器结构简单ꎬ占地面积小ꎬ技术设备及操作简单ꎬ维修费用低ꎬ原料利用率高ꎬ消耗低ꎬ稳定在线率高ꎮ但在生产反应过程中ꎬ会产生环己醇㊁环己胺㊁苯酚等副产物ꎮ本文对工艺生产中的指标进行了控制㊁剖析ꎬ分析其原因并提出相应处理措施ꎮ关键词:杜帮硝基苯ꎻ液相加氢ꎻ副产物中图分类号:TQ036.3ꎬTQ037㊀㊀㊀文献标识码:B㊀㊀㊀文章编号:1003-3467(2020)08-0031-031㊀液相加氢工艺及副产物产生1.1㊀液相加氢工艺目前苯胺生产广泛采用硝基苯催化加氢工艺ꎬ此工艺可分为气相加氢法和液相加氢法ꎬ其中液相加氢法单系列最大设计生产能力18万t/aꎬ高效反应系统使苯胺的收益率高达99.8%以上ꎬ使用以炭为载体的贵金属催化剂ꎬ铁为改性剂ꎮ该工艺技术主要特点:①单套反应能力大ꎬ为世界上单套最大的苯胺生产装置ꎬ专用催化剂活性高ꎬ产品质量稳定ꎮ②为气液两相反应ꎬ氢气过量仅10%ꎬ原料氢气与硝基苯比值低ꎬ对循环氢气压缩机的能力要求低ꎬ电耗低ꎮ硝基苯以液相形式进入反应器ꎬ无需将原料气化ꎬ相比气相加氢工艺ꎬ对预热蒸汽需求量和消耗量较低ꎮ③反应器内件为简单的筛板塔ꎬ用反应生成水调控温度ꎬ控制稳定ꎬ反应热采用外置废热锅炉回收ꎬ避免反应过程中的飞温现象ꎬ消除因催化剂过热而对催化剂造成的损坏ꎮ④催化剂在线补充ꎬ提升装置连续运转时间ꎬ避免催化剂因运转时间长而造成活性降低ꎬ产品质量更稳定ꎬ在线运转时间长ꎬ保证较高设备利用率ꎮ杜邦硝基苯液相加氢生产苯胺技术ꎬ主要包括硝基苯加氢反应单元和粗苯胺精制单元两大部分ꎬ其他辅助性单元包括氢气预处理㊁催化剂单元㊁产品冷却及倾析单元㊁废水废气单元及轻油单元等ꎮ1.2㊀副产物产生硝基苯催化加氢是一个过程复杂的多相反应ꎬ是强放热反应ꎬ整个反应过程主要靠温度和压力的调控来实现ꎬ其中温度的调控是通过减温水吸收多余热量ꎬ而压力的调控依托于氢气管网㊁氢气进料以及富氢排放量ꎮ此外催化剂的活性对产品有较大影响ꎮ反应系统会生成的少量副产物ꎬ包括环己酮㊁环己醇㊁环己胺㊁环己苯胺㊁苯酚㊁二苯胺和氨等ꎮ主要副反应如下:C6H7N+3H2ңC6H13N(环己胺)2C6H7N+3H2ңNH3+C12H17N(环己苯)C12H17N+H2OңC6H7N+C6H10O(环己酮)C6H10O+H2ңC6H12O(环己醇)C6H12Oң3H2+C6H6O(苯酚)2㊀控制指标要求在国家标准中ꎬ对于苯胺含量要求(合格品ȡ99.3%㊁一级品ȡ99.5%㊁优级品ȡ99.6%)ꎬ对于苯胺中硝基苯的含量要求(合格品ɤ150ˑ10-6㊁一级品ɤ100ˑ10-6㊁优级品ɤ20ˑ10-6)[2]ꎮ与国家标准相对比ꎬ杜邦硝基苯液相加氢技术经多年的技改优化和精益操作ꎬ可使得对副产物的控制处于较好的范围ꎬ例如生产苯胺指标ȡ99.9%ꎬ控制苯胺中硝基苯含量ɤ5ˑ10-6ꎬ均优于国标优级品要求ꎮ㊀㊀收稿日期:2020-03-26㊀㊀作者简介:贾崇顺(1988-)ꎬ男ꎬ技师ꎬ从事化工生产管理工作ꎬ电话:19153595051ꎮ 13第8期㊀㊀㊀㊀㊀㊀㊀㊀㊀㊀㊀㊀㊀㊀贾崇顺:杜邦硝基苯液相加氢技术副产物研究3㊀产品指标分析调控及解决方案当精苯胺产品中分析指标出现异常超标时ꎬ即硝基苯㊁环己胺㊁环己酮㊁苯酚㊁环己醇超标以及各指标异常富集等ꎬ应立即将产品采出切循环操作ꎬ并组织排查原因ꎮ①确认反应单元出现异常ꎬ粗苯胺与精苯胺产品均不合格ꎬ则需根据不合格指标ꎬ开展相对应调整ꎬ即通过反应单元新鲜催化剂㊁氢油比(原料氢气与硝基苯比值)㊁激冷水以及精制单元回流比㊁焦油采出㊁蒸汽用量等手段调控ꎮ②确认反应单元正常ꎬ反应粗苯胺产品合格ꎬ只是单纯的精苯胺产品不合格ꎬ可通过精制单元回流比㊁焦油采出㊁蒸汽用量等手段调控ꎮ3.1㊀硝基苯异常分析调控反应单元温度控制偏低ꎬ导致粗苯胺产品和精产品中硝基苯超标ꎮ反应器内通过减温水来吸收多余热量ꎬ达到调控温度目的ꎬ当温度偏低反应不充分ꎬ硝基苯转化率低ꎬ从而导致反应器顶部粗苯胺产品和侧线循环催化剂采出中硝基苯超标ꎮ解决方案:首先将粗苯胺产品切至不合格罐ꎬ避免影响精制单元ꎬ然后依据反应单元生产情况ꎬ微调激冷水ꎬ将反应核心温度调高ꎬ氢油比调高ꎬ新鲜催化剂和循环催化剂调高等手段ꎮ反应单元催化剂活性降低或失活ꎬ导致粗苯胺产品和精产品中硝基苯超标ꎮ催化剂直接参与反应进行ꎬ加快反应速率ꎬ其活性直接影响主反应和副反应的进程ꎬ当催化剂活性低时ꎬ主副反应均减弱ꎬ反应不完全ꎬ硝基苯转化率低ꎬ从而导致反应器顶部粗苯胺产品和侧线循环催化剂中硝基苯超标ꎮ解决方案:当发生催化剂活性降低时ꎬ第一时间确定原因ꎮ①循环催化剂中焦油含量高ꎬ会堵塞催化剂表面积以及内部通道ꎬ造成催化剂活性被抑制ꎬ影响催化剂和反应物的接触ꎬ严重时造成失活ꎮ解决方案是定期检测焦油含量ꎬ并对焦油净化过滤分离ꎬ使其维持在较低的浓度(1%~2%)ꎮ②原料硝基苯中杂质(长链烷烃)含量高ꎬ使催化剂中毒失活ꎬ同时也会延长粗苯胺的分层时间(1min延长至13min)ꎬ造成苯胺泛白乳化和生产系统紊乱ꎮ解决方案是控制原料中长链烷烃的含量(<400ˑ10-6)ꎬ当含量较高时需调和后使用ꎮ③原料氢气中杂质(CO/CO2/S)含量高ꎬ会对催化剂造成不可恢复性中毒而失活ꎮ解决方案是加强氢气指标的监控ꎬ并对原料氢气及循环氢气进行甲烷化预处理ꎮ④新鲜催化剂添加量持续偏少ꎬ反应单元内催化剂浓度不足ꎬ导致硝基苯转化率低ꎬ解决方案是在线补充损失的催化剂ꎮ3.2㊀环己胺异常分析调控反应过程氢气过量10%ꎬ且在液相苯胺中会溶解氢气7ˑ10-6~12ˑ10-6ꎬ在反应器温度过高时ꎬ会导致苯胺氢化生成环己胺ꎬ造成氢气单耗的增加和副产物环己胺的超标ꎮ解决方案:控制在反应器内生成是重点ꎬ根据反应器各项运行参数㊁微调激冷水㊁新鲜催化剂和循环催化剂㊁控制反应核心温度以及调整氢油比等手段ꎬ严重时可将精致单元脱水塔填料层温度调高(145ħ)ꎬ加大塔顶轻组分采出ꎬ储存富集的轻油ꎬ启用轻油单元脱除环己胺ꎮ3.3㊀环己酮异常分析调控苯胺反应单元高负荷运行中ꎬ若氢油比控制持续较高ꎬ反应器逐步偏离正常调控ꎬ导致粗苯胺产品环己酮异常超标ꎬ而超出后续精制单元处理能力ꎬ最终也会使精产品中苯酚超标ꎮ解决方案:首先将反应单元氢油比控制降低ꎬ微调反应各项参数ꎬ核心是要控制环己酮在反应单元的生成ꎮ其次确认后续精致单元处理环己酮是否异常ꎬ环己酮与苯胺在真空㊁高温㊁干燥特定条件下ꎬ会转化为重组分席夫碱和水ꎬ该反应为可逆反应ꎻ排查精制单元换热器/水冷器是否存在列管泄漏ꎬ使水分进入ꎬ导致席夫碱水解(水分300ˑ10-6ꎬ环己酮转化率96.5%ꎻ水分600ˑ10-6ꎬ环己酮转化率94.7%ꎻ水分1000ˑ10-6ꎬ环己酮转化率93.1%)ꎬ致使环己酮超标ꎻ排查精制单元物料温度㊁压力㊁停留时间等运行参数是否异常ꎬ导致环己酮的转化受抑制ꎮ最后排查其他单元泥浆型屏蔽泵外漏情况ꎬ使不合格苯胺通过泵补苯胺管线反窜补苯胺储罐ꎬ然后经精致单元的泥浆型屏蔽泵内漏至系统内部ꎬ严重时可检修泵ꎬ并将泵补苯胺储罐排液置换清洗ꎮ3.4㊀苯酚异常分析调控粗苯胺产品中苯酚超标ꎬ导致精产品中苯酚超标ꎮ苯胺反应单元持续长时间高负荷运行ꎬ若氢油比控制持续较低ꎬ则导致氢气过量相对不足ꎬ此时添加催化剂量过多ꎬ会使催化剂活性偏高ꎬ副产物苯酚的含量将会升高ꎬ导致粗苯胺产品苯酚异常超标ꎮ解决方案:根据反应单元的不同负荷ꎬ合理控制反应器的氢油比ꎬ通过对反应器的微调ꎬ从源头上控制减少苯酚含量ꎮ反应单元负荷频繁调整ꎬ导致苯酚超标ꎮ若频繁的调整反应负荷ꎬ会影响苯胺生产的优化运行ꎬ导23 河南化工HENANCHEMICALINDUSTRY㊀㊀㊀㊀㊀㊀㊀㊀㊀㊀㊀㊀㊀2020年㊀第37卷致氢气单耗增加(影响成本节约指标)ꎬ能耗变高ꎮ副产物含量增加ꎬ影响苯胺产品指标质量ꎬ主要体现在精制单元苯酚㊁环己胺㊁环己酮的波动超标ꎮ解决方案:减少反应单元㊁精制单元负荷的频繁调整ꎬ保证 安稳长满优 运行ꎮ精制单元升降负荷操作速度过快ꎬ导致底部温度波动ꎮ精制单元升降负荷速度较快ꎬ塔底蒸汽流量调节不同步ꎬ造成塔底温度升高ꎬ部分苯酚随苯胺至塔顶采出ꎬ此外塔釜液位出现大幅度降低时ꎬ也会造成底部物料浓缩ꎬ焦油浓度和苯酚浓度快速增长ꎬ苯酚也会被大量蒸出ꎮ精制塔控制参数有温度㊁压力㊁液位㊁流量ꎬ压力对塔的影响也比较大ꎬ正常情况下ꎬ由于精制塔体积大ꎬ压力变化缓慢ꎬ不会出现突增突减的情况ꎬ压力变动往往发生在改变负荷的情况下ꎮ在精制单元提升高负荷时ꎬ精制塔压力上涨ꎬ塔压增高ꎬ塔内物料沸点高于设定值ꎬ塔间及塔底蒸汽使用量增加ꎬ导致底部温度升高ꎬ从而造成苯酚上蒸量增大ꎬ进入精馏段随顶部产品一起采出ꎬ导致精苯胺产品中苯酚超标ꎮ解决方案:精制单元调整负荷过程中ꎬ严格按照操作规程ꎬ精细升降负荷ꎬ注意脱水塔填料层平均温度ꎬ同步调节精制塔回流比及塔底蒸汽用量ꎬ严密监视温度参数的变化ꎬ焦油采出可适当高于正常负荷匹配值ꎬ待负荷稳定后再根据样品指标ꎬ焦油采出逐步与负荷匹配ꎬ避免塔器出现波动ꎬ保证产品合格ꎮ此外当产品指标异常时ꎬ塔回流比可适当增加ꎬ提高精馏效果ꎬ但会使蒸汽用量增大㊁单耗升高ꎬ不宜长时间维持ꎮ精制单元焦油采出量持续偏少ꎮ在精制单元正常稳定运行时ꎬ焦油采出量长时间低于正常负荷采出量ꎬ会造成精制塔塔底温度持续缓慢升高ꎬ底部物料被浓缩ꎬ苯酚持续累积ꎬ部分苯酚随苯胺蒸出至塔顶采出ꎮ解决方案:在精制单元平稳运行期间ꎬ焦油采出量不易长时间偏低ꎬ保持正常负荷采出量ꎬ对于精制单元不同的负荷ꎬ应合理控制焦油采出ꎮ精制单元精制塔蒸汽量控制偏离正常值ꎬ导致苯酚上蒸至产品中ꎮ若精制塔塔间及塔底再沸器蒸汽分配不均ꎬ底部蒸汽量过高ꎬ塔间蒸汽量偏少ꎬ会导致底部温度偏高ꎬ底部物料被浓缩ꎬ焦油浓度和苯酚浓度持续增长ꎬ部分苯酚随苯胺蒸出至塔顶采出ꎮ解决方案:对于精制塔控制ꎬ在落实回流比和蒸汽分配优化的基础上ꎬ要结合粗苯胺和精苯胺指标中苯酚含量ꎬ调节平衡塔间和塔底的蒸汽量及回流比ꎮ精制单元脱水塔和精制塔内填料损坏ꎬ导致苯酚脱出效果差ꎮ精制单元操作不当或者塔内填料质量问题ꎬ存在脱水塔和精制塔内填料损坏问题ꎬ会使苯酚脱出效果不佳ꎬ导致精苯胺产品中苯酚超标ꎮ解决方案:工艺人员要操作平稳ꎬ持续关注塔内压差变化ꎬ若确定为塔内填料损坏ꎬ则将装置停车处理ꎬ对塔清洗㊁置换㊁隔离ꎬ联系设备专业人员拆开人孔ꎬ进一步检查㊁检修或更换ꎮ3.5㊀环己醇异常分析调控苯胺反应单元持续长时间高负荷运行中ꎬ若氢油比控制持续较低ꎬ则导致氢气过量相对不足ꎬ此时添加催化剂量过多ꎬ会使反应器内催化剂的活性偏高ꎬ副产物苯酚升高ꎮ苯酚在催化剂的作用下ꎬ与氢气反应生成环己醇(可逆)ꎬ致使环己醇含量随之升高ꎮ而后续又无法除去环己醇ꎬ环己醇在系统内持续累积ꎬ最终导致精苯胺产品中环己醇超标ꎮ解决方案:在本工艺的选择中ꎬ环己醇的生成量很少ꎬ可根据反应单元的不同负荷ꎬ合理控制氢油比ꎬ通过对反应器的微调ꎬ从反应源头上控制减少环己醇生成ꎮ3.6㊀产品各指标超标富集处理在装置生产运行中ꎬ若通过各控制手段调节后ꎬ产品指标持续异常且有恶化现象ꎬ说明苯胺生产各单元内富集较多的副产物ꎬ造成生产紊乱ꎬ威胁装置的正常生产和产品指标ꎬ可采取积极妥善的应对措施ꎬ从精制单元脱水塔塔顶采出富集的轻组分ꎬ启用轻油单元处理ꎬ用来分离含有苯胺㊁水㊁环己胺㊁环己醇㊁苯等ꎬ以回收其中的重组分苯胺ꎬ降低不必要的苯胺浪费ꎬ外排环己胺㊁环己醇㊁苯等轻组分ꎬ维持工艺平稳运转ꎮ4㊀结论目前世界上最先进杜邦液相加氢技术ꎬ在运行生产中ꎬ会出现产品指标异常超控现象ꎬ要综合考虑ꎬ统筹调控ꎬ兼顾粗苯胺中副产物和硝基苯异常的相应措施ꎮ任何一个运行参数都不能单独进行分析调整ꎬ特别注意反应单元氢油比的控制ꎬ存在过加氢和转化率的矛盾点ꎮ只有反应单元控制稳定ꎬ调控关联所有的运行参数ꎬ才能从根源上消除隐患ꎬ保证精苯胺产品的合格稳定ꎮ本文研究硝基苯液相加氢技术副产物ꎬ分析异常情况及相应调控措施ꎬ使得产品更稳定㊁高质量和低成本ꎬ保证了生产 安稳长满优 的运行ꎮ33第8期㊀㊀㊀㊀㊀㊀㊀㊀㊀㊀㊀㊀㊀㊀贾崇顺:杜邦硝基苯液相加氢技术副产物研究。
硝基苯加氢制备苯胺的最新研究进展
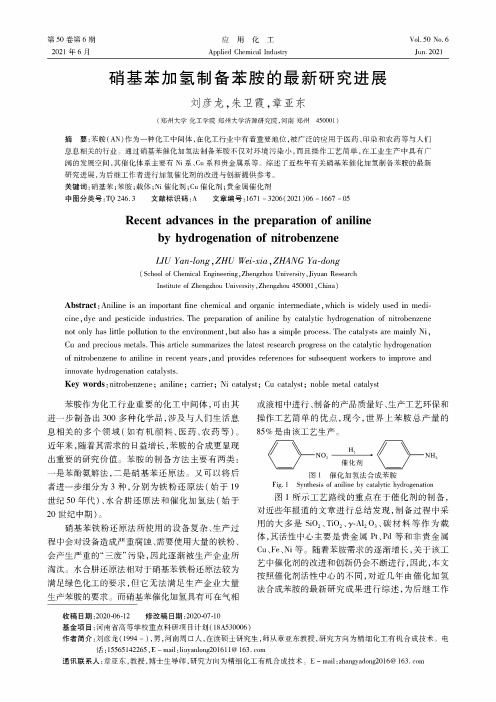
F do Souza等74合成出Cx纳米颗粒,使用壳聚糖/
烯醇 对其
载, • 的催化
为CPCx催化剂,以NaBH作为氢源,将102 my催
化剂、2 mL的硝基苯溶液(5 mmol/E)、1 mL新鲜制
备的NaBH水溶液(56 mmol/E)加入到反应器内,
反应温度保持在室温下,2 min后86%的硝基苯被
Keywoodt: dnioobedeede; adninde; aaoneo; Nnaaiaissi; Cuaaiaissi; dobiemeiaiaaiaissi
苯胺作为化工行业重要的化工中间体,可由其
进一步制备出300多种化学品,涉及与人们生活息
相关的 4
(
、 、 等 )。
近年来,随着其需求的日益增长,苯胺的合成更显现
转化,并使用CPOx再连续进行2次该反应,其催化
l
%,作-将其 {出,的高
重复性归因于壳聚糖/聚乙烯醇薄膜对Cx纳米颗 粒的 5 稳 作用。
Diao Shipang等制备出了 Cx/yiO0,采用了气相
催化加氢的不同反应方式,反应装置为单级、两级流
化} 应器776] , 实验
在
化} 应器
, 硝基苯的 化率 苯 的
可达95.21%,实验完成取出NO/:催化剂,用其继 '作 <实验的催化 , '9< ,苯 的收率
只 了 4295%。
非晶 金 具0+ O 特;,
b
有较多的不饱和中心,二是可调变的电子性质,三是 均一的化学和结构环境,从而使其蕴藏了巨大催化 潜力。赵卿飞等⑷第一步制出了 Ni0 + /2iOo,其制备
出重要的研究价值。苯胺的制备方法主要有两0:
硝基苯液相催化加氢制苯胺技术进展

硝基苯液相催化加氢制苯胺技术进展相关专题:催化剂时间:2008-11-27 13:50苯胺是一种用途十分广泛的有机化工中间体,广泛应用于聚氨酯原料二苯基甲烷二异氰酸酯(MDI)、燃料、医药、橡胶助剂、农药及精细化工中间体的生产。
尤其是作为MDI的生产原料,具有很大的市场潜力。
近年来,随着MDI 生产的不断发展,苯胺生产能力不断扩大,生产装置趋向大型化。
目前苯胺生产工艺路线主要有硝基苯铁粉还原法、苯酚氨化法和硝基苯催化加氢法,分别占苯胺总生产能力的5%、10%和85%,其中硝基苯催化加氢法又分为固定床气相催化加氢、流化床气相催化加氢和液相催化加氢法。
目前我国除山东烟台万华聚氨酯集团公司采用固定床工艺、山西天脊集团公司采用液相加氢工艺外,全部采用流化床气相催化加氢法。
虽然气相加氢取得了流化床和固定床的混合床技术、催化剂体外再生等一些科技成果,使加氢装置有了很大的改进;但是当年产量达到10万t以上时,就遇到了设备体积以及产品质量的巨大挑战。
而国外应运而生的液相法加氢制苯胺技术则成功地解决了这一问题,使苯胺的生产技术有了质的飞跃。
由于液相加氢具有反应温度低、副反应少、催化负荷高、设备生产能力大、总投资低等优点,近年来已引起人们的关注。
本文介绍了硝基苯液相催化加氢技术研究进展,为我国硝基苯催化加氢制苯胺技术提供参考建议。
1 传统硝基苯液相加氢制苯胺工艺为了解决硝基苯气相加氢制苯胺反应温度高等问题,英国IC I、日本三井东亚(Mitsui Toatsu)、美国杜邦(DuPont)公司等相继开发出硝基苯液相催化加氢工艺。
1.1 ICI公司硝基苯液相加氢制苯胺工艺ICI公司在1939年成功开发硝基苯液相加氢制苯胺工艺,采用苯胺作为溶剂,以硅藻土为载体的活性镍为催化剂,载体的粒径为200目,在反应时要及时移走反应中产生的水,防止水浸湿催化剂。
当硝基苯浓度较低时,如当苯胺的摩尔分数大于还原的摩尔分数时,该催化剂具有很好的活性。
- 1、下载文档前请自行甄别文档内容的完整性,平台不提供额外的编辑、内容补充、找答案等附加服务。
- 2、"仅部分预览"的文档,不可在线预览部分如存在完整性等问题,可反馈申请退款(可完整预览的文档不适用该条件!)。
- 3、如文档侵犯您的权益,请联系客服反馈,我们会尽快为您处理(人工客服工作时间:9:00-18:30)。
硝基苯液相催化加氢制苯胺技术进展苯胺是一种用途十分广泛的有机化工中间体,广泛应用于聚氨酯原料二苯基甲烷二异氰酸酯(MDI)、燃料、医药、橡胶助剂、农药及精细化工中间体的生产。
尤其是作为MDI的生产原料,具有很大的市场潜力。
近年来,随着MDI生产的不断发展,苯胺生产能力不断扩大,生产装置趋向大型化。
目前苯胺生产工艺路线主要有硝基苯铁粉还原法、苯酚氨化法和硝基苯催化加氢法,分别占苯胺总生产能力的5%、10%和85%,其中硝基苯催化加氢法又分为固定床气相催化加氢、流化床气相催化加氢和液相催化加氢法。
目前我国除山东烟台万华聚氨酯集团公司采用固定床工艺、山西天脊集团公司采用液相加氢工艺外,全部采用流化床气相催化加氢法。
虽然气相加氢取得了流化床和固定床的混合床技术、催化剂体外再生等一些科技成果,使加氢装置有了很大的改进;但是当年产量达到10万t 以上时,就遇到了设备体积以及产品质量的巨大挑战。
而国外应运而生的液相法加氢制苯胺技术则成功地解决了这一问题,使苯胺的生产技术有了质的飞跃。
由于液相加氢具有反应温度低、副反应少、催化负荷高、设备生产能力大、总投资低等优点,近年来已引起人们的关注。
本文介绍了硝基苯液相催化加氢技术研究进展,为我国硝基苯催化加氢制苯胺技术提供参考建议。
1 传统硝基苯液相加氢制苯胺工艺为了解决硝基苯气相加氢制苯胺反应温度高等问题,英国ICI、日本三井东亚(Mitsui Toatsu)、美国杜邦(DuPont)公司等相继开发出硝基苯液相催化加氢工艺。
1.1 ICI公司硝基苯液相加氢制苯胺工艺ICI公司在1939年成功开发硝基苯液相加氢制苯胺工艺,采用苯胺作为溶剂,以硅藻土为载体的活性镍为催化剂,载体的粒径为200目,在反应时要及时移走反应中产生的水,防止水浸湿催化剂。
当硝基苯浓度较低时,如当苯胺的摩尔分数大于还原的摩尔分数时,该催化剂具有很好的活性。
一般在100℃、3MPa压力下反应。
采用浆态床反应器或流化床反应器,通过反应压力将反应物混合进行浓缩,从而去除反应热。
该技术的先进性在于氢气不必为高纯气,可以是摩尔比为3:1的H2与N2的混合气体,而且混合气体可以循环使用。
从加氢反应器出来的气体冷却分离水汽后,再补充一部分氢气重新进入反应段反应,该工艺中必须具有大量的循环气,确保快速移走反应中产生的水蒸气,并且确保催化剂悬浮在反应段中。
图1(略)为ICI 公司硝基苯液相加氢制苯胺工艺流程图。
在ICI工艺中,溶剂苯胺在液相中的质量分数维持在84%左右,而且反应温度在100℃,此时制备的苯胺中含有质量分数丸0.6%的硝基苯,并含有其他具有氢化核的杂质,需经过精馏装置对其精馏,才能得到高纯度苯胺。
1.2 日本三井东亚化学株式会社硝基苯液相加氢制苯胺工艺为了克服ICI公司硝基苯反应体系中杂质较多的缺点,日本三井东亚化学株式会社提出改进型硝基苯液相加氢技术,通过降低硝基苯在反应物中的浓度来提高苯胺的纯度,采用贵金属催化剂,包括将沉积在吸油性至少为100的亲油性炭上的钯或钯-铂催化剂悬浮于苯胺溶剂中,向反应体系加入锌化合物和碱金属碳酸盐(碳酸钠)或碱金属碳酸氢盐(碳酸氢钠)作为助催化剂,以及在基本无水情况下在温度150-250℃、压力0.3-0.7 MPa下进行反应,并将硝基苯在反应物中的质量分数维持在0.01%或更低,同时以蒸汽形式连续蒸出产物苯胺和水。
在该技术中所用的催化剂是粒径为20-60μm、比表面积为50-100m2/g、负载Pd质量分数为0.5%-1.0%的Pd/C、Pd-Pt/C催化剂,载体还可以含有少量的铁或镍的氧化物或氢氧化物,反应混合物中催化剂的质量分数通常为0.2%-2.0%。
该技术的采用可更有效地抑制含氢化核物质的产生,并且可以得到基本上不含未反应的硝基苯的苯胺,制得的苯胺不需任何特殊的附加纯化就可作为生产亚甲基二苯胺(MDA)的原料,不使未反应的硝基苯在生产MDA方法的体系中聚集便可生产高质量的MDA,而且大量溶剂的添加可以通过溶剂的潜热来控制反应温度。
1.3 DuPont硝基苯液相加氢制苯胺工艺一般制备的粗硝基苯中通常含有聚硝基苯酚(PNP),以前人们通常在加氢前先通过碱性溶液抽提分离PNP,这种方法虽然效果很好,但由于PNP具有很大的毒性,完全分离是非常困难的,而且分离费用很高。
为了避免该分离工序,美国DuPont公司在1983年提出通过含有聚硝基苯酚杂质的硝基苯液相催化加氢制苯胺工艺,反应后杂质聚硝基苯酚被转化为焦油,以焚烧的方式达到分离除去的目的。
在该工艺中,含有PNP杂质的粗硝基苯进行液相催化加氢生成苯胺,在反应中PNP可以转化为聚合焦油,其可从苯胺产品中轻易分离出来,然后进行焚烧除去。
这种方法的先进性在于粗硝基苯转化为苯胺工艺中本身副产焦油,而产生的焦油必须从苯胺产品中分离,因此2种焦油可以混合除去。
DuPont公司的液相加氢技术使用以炭为载体的铂/4E催化剂,以铁为改性剂,使用改性剂可以延长催化剂使用寿命,提高活性,并使之不受芳环的加氢反应引起的损害,反应在一个活塞式流动床反应器内进行。
该工艺采用贵金属催化剂在无水条件下,通常反应在温度150-250℃、压力0.15-1.00MPa,催化剂为Pd(4.50%)-Pt(0.54%)-Fe(5.00%)/C。
所得苯胺经精馏后硝基苯质量分数小于0.001%,苯胺产品中只有5μg/g的PNP,PNP转化为焦油的转化率大于99%,苯胺收率大于99%。
该工艺优点是反应温度低,催化剂负荷高,副反应少,催化剂寿命长,设备生产能力大;缺点是所需压力高,反应物与催化剂及溶剂必须进行分离,设备操作费用高。
现在DuPont公司已建成12.5万t/a液相法装置。
我国山西天脊集团公司现采用DuPont技术建成13万t/a液相法装置,目前装置运行良好。
图2(略)为DuPont公司硝基苯液相催化加氢制苯胺工艺流程图。
2 硝基苯液相加氢制苯胺工艺研究进展除上述介绍的3种生产工艺外,为了降低生产成本,解决反应温度和压力较高的情况,国内外还对其他工艺路线进行研究与开发,不过目前均处于实验室研究阶段。
2.1 乙醇重整制氢进行硝基苯原位液相加氢合成苯胺工艺硝基苯催化加氢合成苯胺是先进的生产工艺,但是催化加氢法要使用氢气,由于氢气是易燃气体,在生产中危险性很大,储存、运输困难,且大多数中小企业无氢源,直接影响到催化加氢生产工艺的推广应用。
浙江工业大学严新焕等提出硝基苯在乙醇溶剂中液相加氢制苯胺工艺,该工艺采用直接从溶剂中获得氢用于硝基苯催化加氢反应,减少了反应步骤,降低了生产成本,简化了生产工艺。
在该反应体系中,溶剂具有双重作用,既是溶剂,也是氢供体,而催化剂既能催化液相重整制氢,又能催化液相加氢反应,液相制氢与加氢还原反应合二为一,突破了外加氢气的限制,因而具有重要的实际应用价值。
该工艺是一种反应系统自供氢源的苯胺制备方法。
硝基苯在醇溶液及催化剂存在下,在190-230℃下进行还原反应,反应时间5-6h,产品处理后得到苯胺。
催化剂可选用Pt/Al2O3、NiB、Renay-Ni,催化剂用量为原料质量的10%-20%,其中乙醇溶液中乙醇的质量分数为92%-97%,反应从醇催化裂解直接获得氢,该氢可直接用于硝基苯催化加氢反应,苯胺收率在99%以上,催化剂表现出较高的加氢活性和选择性。
2.2 CO/H2O还原硝基苯制苯胺工艺国外专利曾报道采用水和一氧化碳还原硝基苯制备苯胺,如在甲醇、乙醇存在下,将水、钯、三氯化铁、三氧化二铁和吡啶在高压釜中加热并通入一氧化碳,温度为180℃,压力为6.9MPa,硝基苯转化率为98%,苯胺选择性为100%,其优点是原料价廉,但是需要高温、高压条件,反应技术难度比较大。
英国Skupinska 等研究了还原硝基苯制备苯胺在CO和水存在下,使用PdCl2/Fe/I2催化剂体系。
在180℃、2.5-4.0MPa下反应2h,硝基苯转化率大于98%,苯胺的选择性为100%。
中国科学院大连化学物理研究所的彭爱东等提出硒催化下CO/H2O还原硝基苯制苯胺工艺,采用价廉易得的Se作催化剂,利用一氧化碳和水反应作为氢源,用于硝基苯催化加氢制苯胺,发现在较高的温度下,不使用任何助催化剂也可以得到苯胺,这使得反应体系得以简化,有利于产物的分离。
将硝基苯、四氢呋喃和一定量的硒粉及水加入到反应釜中,密封,用CO气体置换釜中的空气,数次后充至所需压力,升温到160℃,反应3 h,硝基苯转化率为98.2%,苯胺选择性为100%。
2.3 超临界二氧化碳低温硝基苯加氢工艺中国科学院长春应用化学研究所赵风玉等提出一种低温硝基苯加氢一步获得高品质的苯胺的方法,该工艺中硝基苯在负载型过渡金属钯存在下,在超临界二氧化碳中在温和的反应条件下与氢气接触,发生催化还原反应。
该工艺具有反应条件温和、反应过程清洁、没有副产物和废弃物产生等优点,避免大量有机溶剂及添加剂使用时所带来的后续分离过程,并可一步获得高品质的苯胺。
该工艺的反应温度从已有技术的200℃以上降到30-100℃,极大地节省能源,而且不添加任何有机溶剂和添加剂,反应过程不产生任何副产物,有利于环境保护。
反应物硝基苯和钯为活性组分的负载型催化剂的投料质量比为(200-500):1,在高压反应釜中加入配比量的硝基苯和钯催化剂,密闭反应釜,用氮气吹扫,排净釜内空气,把高压釜加热到30-100℃,向反应釜中充入氢气,其压力为1-5 MPa,然后通过二氧化碳液泵充入二氧化碳,压力为2-16MPa,开启磁力搅拌器,反应时间为10-50min,得到低温硝基苯合成的苯胺。
其催化剂为Pd/C、Pd/Al2O3、Pd/TiO2、Pd/SiO2,温度为35-50℃。
苯胺的选择性为100%,苯胺收率大于99.9%。
超临界二氧化碳中硝基苯加氢反应与现有的硝基苯反应工艺如流化床硝基苯气相加氢的传统方法相比,具有反应条件温和、产品纯度高和反应过程清洁等优点,该发明的反应温度从已有技术的200℃以上降到30-100℃,极大地节省了能源,并且不添加任何有机溶剂和添加剂,反应过程不生成任何副产物,有利于环境保护。
2.4 微波辐射水相法还原硝基苯制苯胺的研究饶美香等研究了微波水相法还原硝基苯制备苯胺的方法。
选择锌粉为催化剂、乙酸乙酯为萃取剂,在硝基苯、氯化铵及锌粉摩尔比为1:1:4、微波功率50%的最佳条件下,苯胺产率达90%以上。
其合成方法如下:在乎底烧瓶中加入6.15mL(0.06mol)硝基苯、3.21 g(0.06 mol)氯化铵、15.6 g(0.24mol)锌粉以及100mL 水,混合均匀,装上回流冷凝管,微波辐射(薄层色谱法检测),直至反应完全。
冷却,反应物用乙酸乙酯萃取,过滤,水层用旋转蒸发除去水;再用乙酸乙酯萃取,分离有机层,用无水MgSO4干燥后。