浅谈液相催化加氢反应器的形式
加氢反应器的运行原理和结构组成及结构的作用说明

加氢反应器的运行原理和结构组成及结构的作用说明1.运行原理:加氢反应器的运行原理基于化学反应中的氢气传递和质量传递原理。
当氢气和反应物进入反应器后,经过催化剂的作用,氢气和反应物发生化学反应。
在发生反应的过程中,催化剂的存在可以降低反应的活化能,从而加速反应速率。
2.结构组成:-反应器壳体:反应器壳体是加氢反应器的外部结构,用于包裹并保护内部反应物质。
通常由耐压和耐腐蚀性能良好的钢材制成。
-反应器催化剂:催化剂是加氢反应器中的核心组成部分。
它可以是金属催化剂,如铂、钯等,也可以是非金属催化剂,如硫化钼等。
催化剂通过提供反应表面,降低反应活化能,以促进化学反应的进行。
-反应器填料:反应器填料用于增加内部反应物与催化剂的接触面积,以提高反应效率。
常用的填料包括陶瓷环、金属环、填料包等。
-进料管道:进料管道用于将反应物和氢气引入反应器。
通常包括进料阀门和流量计等部件,以控制反应物的流量和进料速度。
-出料管道:出料管道用于将反应产物从反应器中排出。
通常安装有出料阀门、分析仪器等,以便对产物进行分析和调节。
3.结构的作用:-反应器壳体:反应器壳体起到保护反应物质以及催化剂的作用,同时能够承受反应压力和温度的影响。
-催化剂:催化剂能够提供反应表面,降低反应活化能,促进反应的进行。
不同的催化剂能够选择性地促进特定的反应。
-反应器填料:反应器填料能够增加反应物与催化剂之间的接触面积,改善反应效率。
-进料管道:进料管道用于控制反应物的进料速度和流量,确保反应物质的均匀分布。
进料管道还可以用于引入催化剂和其他辅助物质。
-出料管道:出料管道用于将反应产物从反应器中排出,并进行分析和处理。
出料管道能够控制反应产物的流动速度和排出量。
总之,加氢反应器的运行原理建立在氢气传递和质量传递原理之上,在结构组成方面,反应器壳体起到保护作用,催化剂提供反应表面,反应器填料增加反应物与催化剂的接触面积,进料管道和出料管道分别控制反应物的进料和产物的排出。
加氢反应器

反应器内件结构及作用
6.
催化剂支撑盘
反应器内件结构及作用
7.
催化剂卸料管
固定床反应器每一催化剂床层下部均安装有若干根卸料管,跨过催化剂支撑盘、
加氢反应器的结构特点及各构件的作用
加氢反应器本体结构
加氢反应器是在高温、高压和临氢环境下工作,加氢反应器的筒体,一般采用 铬钼钢作为基体,如2.25Cr-1Mo-0.25V钢锻焊结构筒体,2.25Cr-1Mo钢板焊结构筒 体等。这些材料有较好的抗高温氢腐蚀性,但不能耐高温H2S的腐蚀,必须在反应器 壳体基材上附加不锈钢防腐层。一般情况下,反应器内部均采用堆焊不锈钢作为防 腐层。堆焊层一般为双层,与铬钼钢直接接触的为过渡层,材料为E309L型不锈钢, 在过渡层之上与介质直接接触的为表层,材料为E347型不锈钢。在铬钼钢与E347型 堆焊层之间的E309L型堆焊层是具有较高韧性的过渡层,它可阻止表面裂纹向母材扩 散。E347型堆焊层则是为了能有效的抵抗硫化氢的腐蚀。
加氢反应器的结构特点及各构件的作用
加氢反应器局部详细结构的改进
过去反应器曾有某些脆性损伤常发生在应力集中的高应力区,诸如承受重载荷 的内部支撑圈拐角处和法兰密封槽槽底拐角处以及外部附件连接焊缝部位等。为了 避免或尽可能减少各种损伤的发生,曾对相关局部结构做了改进。
加氢反应器本体结构
1.
催化剂支承结构
设计温度选定
器壁局部 过热现象
反应器有效 容积利用率
材料选用
需选用能抗高温氢腐蚀的材料,若有H2S存在时, 还需要考虑设置不锈钢覆盖层以抵抗H2S的腐蚀
加氢反应器的设计要求和结构分析
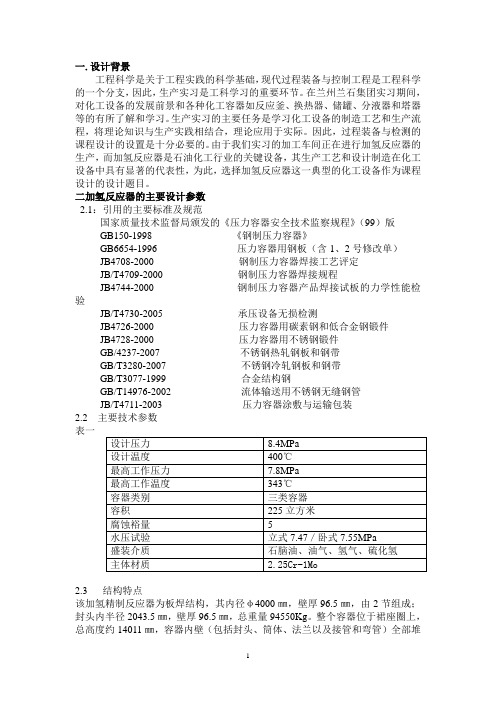
一.设计背景工程科学是关于工程实践的科学基础,现代过程装备与控制工程是工程科学的一个分支,因此,生产实习是工科学习的重要环节。
在兰州兰石集团实习期间,对化工设备的发展前景和各种化工容器如反应釜、换热器、储罐、分液器和塔器等的有所了解和学习。
生产实习的主要任务是学习化工设备的制造工艺和生产流程,将理论知识与生产实践相结合,理论应用于实际。
因此,过程装备与检测的课程设计的设置是十分必要的。
由于我们实习的加工车间正在进行加氢反应器的生产,而加氢反应器是石油化工行业的关键设备,其生产工艺和设计制造在化工设备中具有显著的代表性,为此,选择加氢反应器这一典型的化工设备作为课程设计的设计题目。
二加氢反应器的主要设计参数2.1:引用的主要标准及规范国家质量技术监督局颁发的《压力容器安全技术监察规程》(99)版GB150-1998 《钢制压力容器》GB6654-1996 压力容器用钢板(含1、2号修改单)JB4708-2000 钢制压力容器焊接工艺评定JB/T4709-2000 钢制压力容器焊接规程JB4744-2000 钢制压力容器产品焊接试板的力学性能检验JB/T4730-2005 承压设备无损检测JB4726-2000 压力容器用碳素钢和低合金钢锻件JB4728-2000 压力容器用不锈钢锻件GB/4237-2007 不锈钢热轧钢板和钢带GB/T3280-2007 不锈钢冷轧钢板和钢带GB/T3077-1999 合金结构钢GB/T14976-2002 流体输送用不锈钢无缝钢管JB/T4711-2003 压力容器涂敷与运输包装2.2 主要技术参数表一设计压力8.4MPa设计温度400℃最高工作压力7.8MPa最高工作温度343℃容器类别三类容器容积225立方米腐蚀裕量 5水压试验立式7.47/卧式7.55MPa盛装介质石脑油、油气、氢气、硫化氢主体材质 2.25Cr-1Mo2.3 结构特点该加氢精制反应器为板焊结构,其内径φ4000㎜,壁厚96.5㎜,由2节组成;封头内半径2043.5㎜,壁厚96.5㎜,总重量94550Kg。
加氢反应器结构设计与优化现状分析

加氢反应器结构设计与优化现状分析加氢反应器是一种常见的化工设备,用于加氢反应,将有机物质中的多个双键或多个三键加氢饱和成单键。
在石油化工、化肥、食品、医药等行业中都有着广泛的应用。
加氢反应器的结构设计与优化对于提高反应效率、降低能耗、延长设备寿命具有重要意义。
本文将对加氢反应器结构设计与优化现状进行分析。
一、加氢反应器的结构设计1. 反应器类型目前常见的加氢反应器类型有固定床反应器、流化床反应器和搅拌式反应器等。
固定床反应器是将催化剂填充在固定的反应器内,通过氢气的通入来进行反应。
流化床反应器是将催化剂悬浮在气体或液体流动介质中进行反应。
搅拌式反应器则是将催化剂悬浮在液态的原料中,通过机械搅拌来进行反应。
不同类型的反应器在结构设计上存在着差异,需要根据具体的反应条件和要求来选择合适的类型。
2. 反应器材质加氢反应器所选用的材质需要具有良好的耐高温、耐腐蚀性能,一般选择优质的合金钢材料。
在材质选择上,需要考虑到反应器内部的高温、高压和腐蚀性气体对设备的影响,确保设备可以长期稳定运行。
3. 反应器密封加氢反应器在高温高压条件下进行反应,密封性能对于设备的安全运行至关重要。
合理设计和选择适合的密封结构可以有效防止气体泄漏,保证反应器内部的高压环境。
4. 催化剂的选用对于加氢反应器而言,催化剂是非常重要的一环。
合理选择催化剂对反应效率和产品质量有着直接的影响。
因此在反应器的设计中需要考虑到催化剂的填充方式、更换方式以及对催化剂的保护等方面。
5. 反应器的热平衡设计加氢反应过程是一个吸热反应过程,因此需要合理设计反应器的热平衡系统。
通过加入冷却系统和加热系统,有效控制反应温度,保证反应器的稳定运行。
1. 反应器流体动力学分析通过对反应器内部流体动力学特性进行分析,可以优化反应器的内部结构,改善流态化性能和传质传热性能。
合理设计反应器的进料口、出料口、填料结构等,可以提高反应器的传质传热效率,减少反应物的局部堆积,提高反应器的利用率。
液相加氢技术的应用现状

C-NUM 液相加氢技术的应用对象也是航煤原料,这种原 料本身的性质和状态比常规的柴油等油料更好,加氢效果更 佳,整个精制过程的对循环系统、反应环境的要求比较小。在面 对航煤原料时,C-NUM 技术应用装置取消了循环油系统,有效 降低了循环泵可能带来的安全风险和成本、动力消耗;反应温 度为 245 ℃,压力为 3.5 MPa,氢油比在 12~13 范围内,属于较 为理想的反应过程。但如果面对的是原料性质、状态更差一些 的焦化柴油等柴油种类时,C-NUM 技术装置能否顺利加氢,能 否顺利完成精制反应获得符合标准的产品油,还需要进一步的 实践和验证分析。
目前来看,液相加氢技术始终存在氢气消耗量高、循环加 氢能耗较高、循环泵安全风险较高、催化剂使用寿命较低等问 题。想要改善这些问题需要通过特殊的设备装置,提高氢气与 原料油的混合程度,实现原料油中的氢气饱和状态[3]。想要达 到氢气饱和的理想状态,可能需要超重力、微米气泡等类型的 装置,使原料油中的氢气溶解量远超于实际需求量。如果能够 解决溶氢过程中的氢气饱和问题,就能够真正节约掉循环加氢 的装置和能耗,并且规避掉循环泵可能带来的安全风险和泄露 风险。这是液相加氢技术未来发展的主要方向,突破这一难题 就能够促进液相加氢技术的有效发展,扩大液相加氢技术的应 用范围。目前的液相加氢技术还不能代替气相滴流等技术的应 用,在原料油精制反应中还不能占据更大的主动性[4]。
LI Nong, LI Hai-feng, ZHAO Xin-quan, LI Guo-qi (Sinochem Changhe Technology Co., Ltd., Dongying 257335, China)
Abstract: Liquid phase hydrogenation technology is a process to maintain high hydrogen-oil ratio, which can effectively improve the heat transfer effect between phases, can improve the reaction eff iciency of oil, reduce the power consumption in the application process of diesel oil, kerosene and other feedstock oils, and produce more environmentally friendly clean oil. In the process of liquid phase hydrogenation, the amount of hydrogen dissolved in oil is the key problem, which affects the energy consumption and production eff iciency of the technology. This paper mainly analyzes the application status and application prospect of this technology.
加氢反应器介绍2015

n
其主要作用为: 一是将进入的介质扩散
到反应器的整个截面上; 二是消除气 、液介
质对顶分配盘的垂直冲击 , 为分配盘的稳定
工作创造条件; 三是通过扰动 , 促使气液两
相混合
2. 分配盘
n
目前 , 国内加氢反应器所使用的反应物流分配器 , 按其作用原理大致可分为
溢流式和抽吸喷射式两类; 反应物流分配盘应不漏液 , 安装后须进行测漏试验,
n
·2 .氢脆
n 所谓氢脆 , 就是由于氢残留在钢中所引起的脆化现象 。产生了氢 脆的钢材 , 其延伸率和断面收缩率显著下降 。这是由于侵人钢中的原 子氢 , 使结晶的原子结合力变弱 , 或者作为分子状在晶界或夹杂物周 边上析出的结果 。但是 , 在一定条件下 , 若能使氢较彻底地释放出来, 钢材的力学性能仍可得到恢复 。这一特性与前面介绍的氢腐蚀截然不 同 , 所以氢脆是可逆的 , 也称作一次脆化现象。
开有数个缺口 ,供停工时排液用。
8. 热电偶
为监视加氢放热反应引起床层温度升高及床层截面温度分布状况 而对操作温度进行监控。
·加氢反应器常见损伤与对策
1.高温氢腐蚀
2. 高温氢腐蚀是在高温高压条件下扩散侵入钢中的氢与不稳定 的碳化物发生化学反应 , 生成甲烷气泡(它包含甲烷的成核过程和成长 即FeC+2H2一CH4+3Fe ,并在晶间空穴和非金属夹杂部位聚集 , 引起钢 的强度 、延性和韧性下降与劣化 , 同时发生晶间断裂 。 由于这种脆化 现象是发生化学反应的结果 , 所以它具有不可逆的性质 , 也称永久脆 化现象。
加氢反应器及催化裂化反应器介绍

反应条件控制
利用新型合金和高性能陶瓷等材料,提高反应器的耐腐蚀性能和使用寿命。
高强度耐腐蚀材料
研发新型高温和高压材料,满足加氢反应器和催化裂化反应器在高温高压下的操作需求。
耐高温和高压材料
探索具有特殊功能的材料,如光催化材料、电催化材料等,为加氢和催化裂化过程提供新的解决方案。
功能材料
THANKS
石油化工
煤化工
环保领域
在煤化工领域,加氢反应器可用于煤焦油加氢、煤液化等过程,生产清洁燃料和化学品。
加氢反应器还可用于处理含硫、氮、氧等杂质的废弃物,实现环保减排。
03
02
01
优点
加氢反应器能够脱除原料油中的硫、氮、氧等杂质以及重金属元素,提高油品质量;能够生产高清洁油品,满足环保要求;具有较高的处理能力和较低的投资成本。
缺点
催化裂化反应器需要使用催化剂,且催化剂容易失活和中毒,需要定期更换或再生。此外,催化裂化技术还需要消耗大量的能量和原料,生产成本较高。
加氢反应器与催化裂化反应器的比较
CATALOGUE
03
加氢反应器的工作原理是通过加氢反应将原料中的有害物质转化为无害物质,而催化裂化反应器则是通过催化剂的作用将重质油转化为轻质油。
总结词
加氢反应器主要用于石油化工和煤化工领域,如煤制油、柴油加氢精制、润滑油加氢精制等。而催化裂化反应器则广泛应用于炼油工业,将重质油转化为轻质油、气体和焦炭等,是炼油工业中最重要的加工方法之一。
详细描述
总结词:加氢反应器的优点在于能够提高产品质量、减少环境污染,缺点是工艺复杂、投资成本高。催化裂化反应器的优点在于能够将重质油转化为轻质油,缺点是会产生较多的副产品和废弃物。
加氢反应器和催化裂化反应器的未来发展
第七章化学反应工程学----反应器基本原理
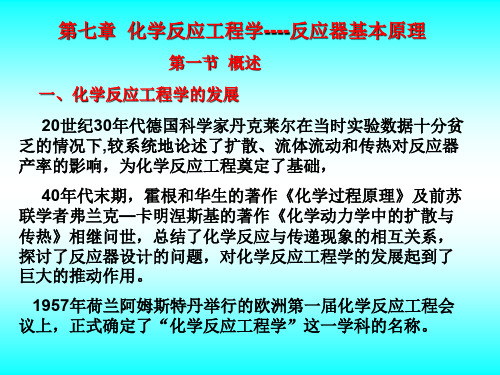
三、化学反应工程学与相关学科的关系
传递工程
反应器中流体 流动与传热
化学反应工程 反 测
化 学
化化
应量
学 学 反应器的设计 系 与
动热
统控
工 程 控
力力
中制
制
学学
催化
反应工艺流
最
剂与
程与设备
佳
反应
3)、反应器内形成的死角也会导致逆向混合。
二、非理想流动模型
凡是流动状况偏离活塞流和全混流这两种理想情况的流动 统称为非理想流动。 造成非理想流动的原因有: ①、设备内各处速度的不均匀所致
层流
湍流
平推流
②、由于反应器中物料粒子 的运动(如搅拌、分子扩散 等)导致与主体流动方向相 反的运动,导致偏离全混流 的特性。
反应器的种类反应类型设备的结构形式反应特性均相气相液相燃烧裂解中和硫化水解管式釜式无相界面反应速率只与温度或浓度有关非均相气气液相液液液相气气固相液液固相固固固相气气液固相氧化氯化加氢磺化硝化烷基化燃烧还原固相催化还原离子交换水泥制造加氢裂解加氢硫化釜式塔式釜式塔式固定床流化床釜式塔式回转筒式固定床流化床在相界面实际反应速率与相界面大小及相间扩散速率有关??2按反应器的结构型式分类结构型式适用的相态应用举例反应釜液相气液相液液液相液固相药物的合成染料中间体合成树脂合成管式气相液相轻质油裂解高压聚乙烯鼓泡塔气气液相气液固相变换气的碳化苯的烷基化二甲苯的氧化固定床气气固相so2氧化乙苯脱氢半水煤气的产生流化床气气固相硫铁矿焙烧萘氧化制苯酐回转筒式气气固相固固相水泥生产喷嘴式气相高速反应的液相氯化氢的合成天然气裂解制乙炔?3按操作方式分类?1间歇操作?2连续操作?3半连续半间歇操作??五理想均相反应器?1理想间歇反应器?反应器理想化的条件
液相加氢技术

学习资料1、杜邦公司Iso Therming 加氢技术杜邦公司Iso Therming 加氢技术特点是不使用喷淋床反应器,而采用液相填充床反应器。
反应中使用的氢溶解在液体中,而不是作为气体进行循环。
(见下图)液相反应器在杜邦公司内的商业运行时间已有几十年的时间。
液相反应器设计中的一项技术要求为溶解在反应器进料中的氢的量应该高于反应所需氢的量。
在大多数炼油厂中,氢的数量只是高于新鲜原料中氢的溶解度。
在Iso Therming 加氢技术中,产品液体进行再循环,以便溶解在混合原料中的氢量远高于反应所需的氢量。
正确的再循环率通过中试装置使用实际进料及反应工程模型进行测试来确定。
装置中不需要设置价格昂贵的氢气循环压缩机。
补充氢压缩机与喷淋床反应器相比,液相填充床反应器在设计及提高产能方面更加简单。
在喷淋床反应器中,气体及液体的最佳分布状态非常关键,并且再分布格栅需要仔细设计以防止分布状态不佳,与此相比,填充床反应器中液体流量的分布并不是一个关键设计问题。
在反应器设计中未考虑与多相流相关的其它问题,如压力降及流动状态。
在Iso Therming 加氢技术中,催化剂是全湿的。
这一点与喷淋床反应器形成对比,在该反应器中充满大量气体,而液体向下喷淋到催化剂床上。
在催化剂中以及催化剂周围存在液体可以尽可能降低减少催化剂活性部位的热点。
由于溶解于液体中氢的量远远超过反应中所需氢的量,催化剂活性部位即有氢的存在。
这些因素可以将结焦造成的催化剂减活作用降至最低程度。
Iso Therming反应器中的绝热温度远低于喷淋反应器中的温度,因为充满液体的反应器中的热质量较高。
这种低温升的特点可以在工艺设计中降低对中间冷却的依赖。
Iso Therming反应器的最大温升受到溶解于液体中氢的数量限制。
而在Iso Therming反应器中没有大量的热偏移或者温度超出控制范围的现象,这一点与喷淋反应器不同,在喷淋床反应器气体持续流动,且气体循环流率比反应所需的流率高几倍。
加氢反应器及催化裂化反应器介绍

煤化工
在煤化工领域,加氢反应 器用于煤制油、煤制气等 过程中,提高产品质量和 产量。
精细化工
加氢反应器在精细化工领 域也有应用,如合成香料 、医药中间体等。
催化裂化反应器的应用
重油轻质化
催化裂化反应器可将重质 油转化为轻质油,提高油 品的使用价值。
ห้องสมุดไป่ตู้生产高辛烷值汽油
通过催化裂化反应,可以 生产出高辛烷值的汽油, 满足日益严格的环保要求 。
反应过程
原料油和空气在催化剂床层中发生催化裂化反应,生成轻 质油和裂化气。反应过程中产生的热量通过取热装置移走 。
催化剂再生
催化剂在反应过程中会逐渐失活,需要进行再生处理。再 生过程通常包括烧焦、氧化等步骤,使催化剂恢复活性并 循环使用。
04
CHAPTER
加氢反应器和催化裂化反应 器的比较
原理比较
加氢反应器及催化裂化反应器 介绍
汇报人:XX
目录
CONTENTS
• 引言 • 加氢反应器概述 • 催化裂化反应器概述 • 加氢反应器和催化裂化反应器的比较 • 加氢反应器和催化裂化反应器的应用 • 加氢反应器和催化裂化反应器的发展趋势 • 结论与建议
01
CHAPTER
引言
目的和背景
介绍加氢反应器和催 化裂化反应器的基本 概念、原理、特点及 应用。
THANKS
谢谢
催化裂化反应器
优点包括原料适应性强、轻质油 收率高、操作灵活等;缺点包括 产品质量相对较差、催化剂消耗 量大、设备磨损严重等。
05
CHAPTER
加氢反应器和催化裂化反应 器的应用
加氢反应器的应用
01
02
03
石油加工
加氢反应器在石油加工中 广泛应用,主要用于提高 油品质量、降低硫含量、 改善颜色等。
催化加氢原理
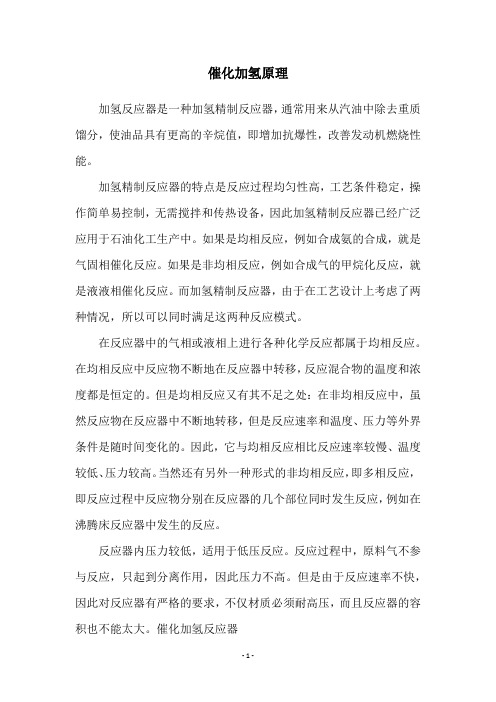
催化加氢原理加氢反应器是一种加氢精制反应器,通常用来从汽油中除去重质馏分,使油品具有更高的辛烷值,即增加抗爆性,改善发动机燃烧性能。
加氢精制反应器的特点是反应过程均匀性高,工艺条件稳定,操作简单易控制,无需搅拌和传热设备,因此加氢精制反应器已经广泛应用于石油化工生产中。
如果是均相反应,例如合成氨的合成,就是气固相催化反应。
如果是非均相反应,例如合成气的甲烷化反应,就是液液相催化反应。
而加氢精制反应器,由于在工艺设计上考虑了两种情况,所以可以同时满足这两种反应模式。
在反应器中的气相或液相上进行各种化学反应都属于均相反应。
在均相反应中反应物不断地在反应器中转移,反应混合物的温度和浓度都是恒定的。
但是均相反应又有其不足之处:在非均相反应中,虽然反应物在反应器中不断地转移,但是反应速率和温度、压力等外界条件是随时间变化的。
因此,它与均相反应相比反应速率较慢、温度较低、压力较高。
当然还有另外一种形式的非均相反应,即多相反应,即反应过程中反应物分别在反应器的几个部位同时发生反应,例如在沸腾床反应器中发生的反应。
反应器内压力较低,适用于低压反应。
反应过程中,原料气不参与反应,只起到分离作用,因此压力不高。
但是由于反应速率不快,因此对反应器有严格的要求,不仅材质必须耐高压,而且反应器的容积也不能太大。
催化加氢反应器其实在设计催化加氢反应器时,大家都知道应该采用合理的设计方案,合理的设计方案可以避免催化剂过早失活,也可以避免活性较高的脱氢催化剂氧化分解;也可以保证较高的净化效率。
但是有很多工厂为了降低能耗,所以会把反应器设计得非常大。
大家想一想,既然采用非均相催化反应,那么我们采用的催化剂的粒径应该是非常小的,大概只有纳米级甚至亚微米级。
大家可能感觉这样的催化剂怎么可能存在呢?其实现在科技水平越来越先进,人类利用光电子技术将催化剂颗粒做得极小,并将表面包覆,从而达到提升催化活性的目的。
气相加氢和液相加氢
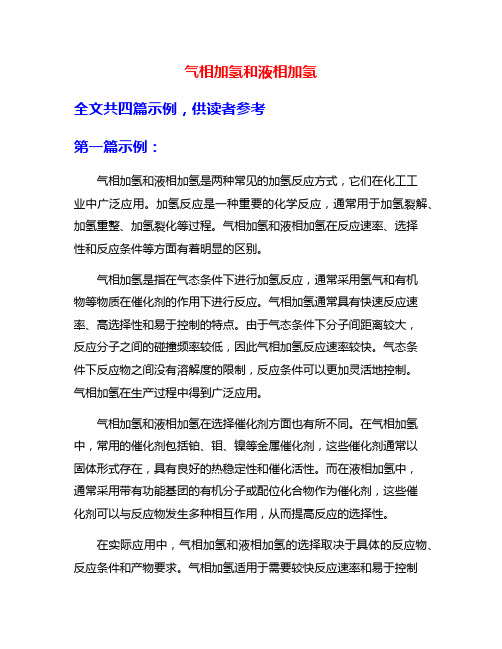
气相加氢和液相加氢全文共四篇示例,供读者参考第一篇示例:气相加氢和液相加氢是两种常见的加氢反应方式,它们在化工工业中广泛应用。
加氢反应是一种重要的化学反应,通常用于加氢裂解、加氢重整、加氢裂化等过程。
气相加氢和液相加氢在反应速率、选择性和反应条件等方面有着明显的区别。
气相加氢是指在气态条件下进行加氢反应,通常采用氢气和有机物等物质在催化剂的作用下进行反应。
气相加氢通常具有快速反应速率、高选择性和易于控制的特点。
由于气态条件下分子间距离较大,反应分子之间的碰撞频率较低,因此气相加氢反应速率较快。
气态条件下反应物之间没有溶解度的限制,反应条件可以更加灵活地控制。
气相加氢在生产过程中得到广泛应用。
气相加氢和液相加氢在选择催化剂方面也有所不同。
在气相加氢中,常用的催化剂包括铂、钼、镍等金属催化剂,这些催化剂通常以固体形式存在,具有良好的热稳定性和催化活性。
而在液相加氢中,通常采用带有功能基团的有机分子或配位化合物作为催化剂,这些催化剂可以与反应物发生多种相互作用,从而提高反应的选择性。
在实际应用中,气相加氢和液相加氢的选择取决于具体的反应物、反应条件和产物要求。
气相加氢适用于需要较快反应速率和易于控制的生产过程,而液相加氢适用于需要提高反应选择性和增加反应条件的情况。
在某些情况下,可以将气相加氢和液相加氢进行组合应用,以充分发挥两种反应方式的优势。
气相加氢和液相加氢是两种重要的加氢反应方式,它们在化工工业中扮演着重要角色。
通过深入研究和比较两种反应方式的特点和应用,可以更好地指导实际生产中的加氢反应设计和优化,为化工产业的发展做出贡献。
【已达到2000字要求,如有需要可继续添加内容】。
第二篇示例:气相加氢和液相加氢是两种常见的加氢反应方式,广泛应用于化工工业中。
气相加氢指的是将氢气与其他物质在气相条件下反应生成加氢产物,液相加氢则是指在液相条件下进行加氢反应。
两种加氢方式各有优缺点,本文将就气相加氢和液相加氢进行详细的介绍。
液相加氢催化技术研究进展探析

液相加氢催化技术研究进展探析祝传奇,毛金亮摘㊀要:加氢催化技术是通过加氢催化反应来生产目标分子的方法㊂其可降低生产成本,提高产品生产效率及产品质量,减少对环境的污染,提升产品竞争力,可实现近乎零排放的清洁生产㊂关键词:液相;加氢催化;催化剂一㊁技术现状液相加氢技术按照反应压力强度分为高压加氢催化㊁中压加氢催化及低压加氢催化㊂高压加氢催化用于含COOH㊁COOR㊁苯环等不容易还原的化合物,主要用于脂肪醇㊁胺㊁饱和环化合物等原料㊁中间体的生产㊂中压㊁低压加氢催化技术用于含醛㊁酮及部分杂环化合物加氢催化,主要用在芳胺类中间体的生产㊂20世纪中期时,加氢催化技术在国外被发展应用,其多应用在石油化工㊁化工中间体领域㊂20世纪80年代,我国才开始对加氢催化技术进行研究,由于研究起步晚,且研究较为分散,故在加氢催化剂及相关设备开发上较为薄弱,发展较慢,应用上受到了较大影响㊂近几年,我国成为化工中间体生产与出口的大国,一些发达国家化工中间体产业向我国转移,这使我国的化工行业得到了长足发展㊂新型催化技术目前已成为重要研究方向,加氢催化技术也随之得到了发展㊂目前,中低压加氢催化技术在国内的部分芳胺类产品生产中替代了铁粉还原㊁锌粉还原㊁硫化碱还原等技术㊂其取得了良好的经济效益㊁环境效益㊂高压催化技术在国内发展缓慢,应用极少㊂二㊁催化剂的特性及制产方法(一)催化剂的特性加氢反应中,催化物起到三个作用:其一,可提高反应的速度;其二,可选择反应路径;其三,可降低反应中的温度㊁压力等环境条件㊂从其作用可见,催化剂的选用十分重要㊂催化剂的性能主要是由其化学成分㊁结构构成等因素所决定的㊂另外,催化剂的性能也随其制产方法的不同而存在差异㊂所以在制产方法的选取上应加以重视㊂不同的制产方法可获取不同形态的催化剂,其催化活性也有所不同㊂例如,铂在催化反应中,其按如下形态顺序进行增长:块状㊁丝状㊁粉状㊁铂黑㊁胶状㊂单位质量催化剂的活性会随着分散程度㊁表面积的增大而增强㊂好的催化剂应具有如下特性:第一,需要具备足够的氢化活性;第二,在反应过程中需状态稳定;第三,对反应物及条件不敏感;第四,具备一定的强度;第五,要有较好的选择性;第六,制产简单,价格低,且可回收循环使用㊂(二)催化剂的制产方法1.固相反应法固相反应法是通过热稳定性的盐或其混合物,在300-400度高温下加热,从而将其变成分散且均匀的氧化物或者氧化混合物㊂然后直接将这些氧化物为催化剂,或者把通过氢气把这些氧化物或混合物还原到纯金属㊂氧化物或纯金属均为微细粒子,其结构㊁形状与原料的种类㊁纯度㊁处理时间㊁周围气体及加热温度等因素均有关系㊂故固相反应法制产催化剂在原料选取㊁制产条件均有严格要求㊂2.湿法湿法是将金属离子转化成氢氧化物㊁碳酸物或者碱式碳酸物形式㊂通常为以硝酸盐或者有机酸盐的水溶液为基料,用强碱㊁氨或碳酸盐的水溶液为沉淀剂,将沉淀物洗涤去掉氢氧根㊁硝酸根或盐酸根等阴离子,然后过滤㊁干燥㊁高温煅烧制产,最后把沉淀物放到反应器皿中还原,这样即可获得到具有催化活性的催化剂㊂3.骨架催化剂制产法骨架催化剂制产法是将具有催化活性的金属与铝或者硅按照一定比例熔融做成脆性合金,再将其粉碎成带有一定粒度范围的粉末㊂然后再用氢氧化钠融掉不需要的铝或硅,这样就获得了具有骨架结构的金属㊂催化剂即制产㊂4.氢气还原法氢气还原法即是用氢气将金属氧化物或金属盐还原制成金属粉末做催化剂的方法㊂例如铂金类催化剂,即将含有铂金的盐类通过氢气还原获得催化剂㊂目前液相加氢还原的催化剂最多的是骨架镍㊁钯炭两种催化剂㊂要获得高活性的催化剂,需要严格控制其性状㊁还原温度等条件㊂另外,氢气还原的催化剂冷却后会吸附大量氢,会在空气中自燃,为防止此情况发生,需将催化剂保存在充有惰性气体(氮气或CO2)的密闭容器中㊂三㊁加氢催化的特点加氢还原催化技术相较于其他还原技术具有许多优势,其一,加氢催化技术获取催化剂的收率高,质量高㊂加氢催化反应后收获的只有产物与水,其他副产物较少,产收率可高达80%以上㊂同时,产品容易分离㊂其与传统技术相比,产收率高,质量好㊂其二,产制的工艺流程短㊂使用加氢催化技术可以简化制产工艺,同时,原料也简单,辅助的原料为氢气与催化剂,操作简易㊂而传统的制产工艺则较为复杂,辅助原料较多,且完成制产后均转化成废物排放㊂其三,加氢催化的反应器通用性较好㊂加氢催化的反应器几乎均可通用,只是调节不同的压力条件即可㊂同一反应器可制产多种产物㊂其四,加氢催化利用资源较为合理㊂其可利用合成氨生产的弛放气来回收氢气,也可用氯碱厂的副产物氢气㊂使原副产物有效再利用,提高经济效益㊂其五,加氢催化技术为清洁工艺㊂传统的催化技术生产将造成较为严重的环境污染,据统计,每生产1吨产品,就需要排放数吨以至数十吨的高浓度废水㊂而加氢催化技术基本不产生相应的废水,清洁环境㊂四㊁结论在我国高速发展的经济环境下,化工产业也会得到长足的发展㊂化工的中间体也会随之得到很好的发展㊂液相加氢催化技术具有制产率高,工艺简单,工艺清洁无污染等特点,其与我国发展环境保护㊁提高经济效益㊁提高生产效率的大化境高度吻合㊂相信定能长远发展㊂参考文献:[1]刘建军;FCC汽油选择加氢脱除二烯烃技术进展[J].广州化工,2011(11).[2]梁长海,赵安琪,张晓菲,等.类贵金属催化新材料催化芳烃加氢研究[A],第六届全国环境催化与环境材料学术会议论文集[C],2009年.作者简介:祝传奇,毛金亮,南京诚志清洁能源有限公司㊂291。
精细有机合成技术:催化加氢工艺方法
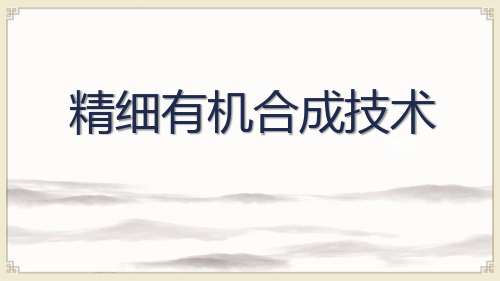
(2)液相催化加氢工艺实例 液相催化加氢常用于 芳香族硝基化合物的催化加氢。采用钯、铑、铂或骨架 镍作催化剂。如2,4-二氨基甲苯的制备:它是由2,4-二 硝基甲苯通过液相催化加氢还原而制得。甲苯经过二硝 化得到混合的二硝基甲苯,其中2,4与2,6-异构体的比 例是80:20,其反应式及工艺过程如下:
2.气相催化加氢 气相催化加氢是指反应物在气态下进行的加氢反应。
适用于易气化的有机化合物(如苯、硝基苯、苯酚等) 的加氢,气相催化加氢实际上是气-固相反应。含铜催化 剂是普遍使用的一类,最常用的是铜-硅胶载体型催化剂 及铜-浮石、Cu-Al2O3。
气相催化加氢主要用于由硝基苯生产苯胺。苯胺是 一种很重要的精细化工产品,它的产量很大,大量用于 聚氨酯、橡胶助剂、染料、颜料等领域。图8-1是一种比 较常见的流化床气相加氢法制苯胺的工艺流程,反应器2 是流化床反应器。
中压催化反应器多用不锈钢或不锈钢衬套来制备。常用的催化
剂为钯、铂等贵金属或高活性的骨架镍,所以中压催化反应器应用 范围广,效率也较高。
高压催化反应器多为高压釜。它由厚壁不锈钢或不锈钢衬套来 制备,具有耐高强度及良好的耐腐蚀性能。但使用时必须注意安全。
催化加氢反应器按催化剂状态不同,可分为三类:泥浆型反应器、 固定床反应器、流化床反应器。
精细有机合成技术 邹静
目
录
Contents
催化加氢
1 2 3
催化加氢的基本原理 催化加氢反应类型 催化加氢工艺方法
三、催化加氢工艺方法
1.液相催化加氢 (1)液相催化加氢反应器 液相加氢反应系统中有三个 相态,氢气为气相、反应物料为液相、催化剂为固相,反 应发生在催化剂的表面。反应过程为:氢气溶解于液相反 应物料中,然后扩散到催化剂表面进行反应,增加氢气压 力和增强扩散效率可加速反应。因此,提高氢压和强化搅 拌是加速反应的最有效的措施。对于加氢反应器,应尽可 能满足上述条件和反应传热要求,其分类如下。
加氢反应器的设计

加氢反应器的设计一、反应器类型的选择一般来说,加氢反应器可以分为两种类型:固定床反应器和搅拌槽式反应器。
固定床反应器适用于多相反应体系,具有较高的传质效率和产率,但操作较为复杂。
搅拌槽式反应器则适用于液相反应体系,操作相对简单,但传质效率较低。
在选择反应器类型时,需根据实际情况综合考虑反应物性质、反应条件以及生产要求等因素。
二、反应物选择1.反应物的稳定性:选择具有较高稳定性的反应物,以保证反应的连续性和产量稳定性。
2.反应物的溶解性:选择溶解度较高的反应物,有利于提高反应速率和传质效率。
3.反应物的纯度:选择纯度较高的反应物,减少杂质对反应的干扰。
4.反应物的可再生性:选择可再生的反应物,有利于提高资源利用效率。
三、反应条件的优化加氢反应器的反应条件包括反应温度、压力、反应物浓度以及催化剂种类和用量等。
反应温度和压力是影响反应速率和产物选择性的重要因素,应根据反应物的性质进行优化。
一般来说,较高的反应温度和压力有利于提高反应速率和产物选择性,但也会增加能耗和设备成本。
反应物浓度的选择应考虑到溶解度和传质效果的影响。
催化剂的选择和用量应综合考虑活性、稳定性以及成本等因素。
四、安全性考虑在加氢反应器的设计中,安全性是一个不可忽视的重要因素。
应加强对高温、高压反应的控制,采取合适的措施确保设备的密封性和抗腐蚀性。
同时,应配备完善的安全措施,如搭建防爆设备、配置气体泄漏探测器和应急处理方案等。
五、其他考虑因素除了上述因素外,加氢反应器的设计还需考虑以下几个因素:1.反应器的尺寸和形状:应根据反应物的性质选择合适的反应器尺寸和形状,以提高传质效率和反应均匀性。
2.搅拌方式和速度:在搅拌槽式反应器中,搅拌方式和速度对反应速率和传质效果有着重要影响。
3.回收制约:在反应过程中产生的副产物、废气和废液的回收处理问题也需要考虑。
总之,加氢反应器的设计需要充分考虑反应器类型选择、反应物选择、反应条件优化以及安全性等因素,并根据实际情况进行综合考虑和优化,以提高反应效果和产量,确保生产的安全和可持续性。
加氢反应器介绍

பைடு நூலகம் 1、加氢反应器分类
2、典型加氢反应器结构
目录 3、加氢反应器内部催化剂装填
4、典型的加氢反应过程
5、影响加氢反应深度的条件
一、加氢反应器分类 1、(按照工艺流程及结构分类) 1. 固定床反应器 2. 移动床反应
器 3. 流化床反应器 4.鼓泡床 反应器 固定床反应器使用最为广泛(气液 并流下流式)
2、 加氢脱氮反应:含氮化合物对产品质量的稳定性有较大危害, 并且在燃烧时会排放出NOX污染环境,同时会使油品变色。石油馏 分中的含氮化合物主要是杂环化合物,非杂环化合物较少。杂环氮 化物又可分为非碱性杂环化合物(如吡咯)和碱性杂环化合物(如吡 啶)。
(1)非杂环化合物
非杂环氮化合物加氢反应时脱氮比较容易,如脂族胺类 (RNH2):
固定床反应器每一催化剂床层下部均安装有若干根卸料管,跨过催化剂支撑盘、 物料分配盘及冷氢箱,通向下一床层,作为在反应器停工卸除催化剂的卸剂通道。
5. 冷氢管
烃类加氢反应属于放热反应,对多床层的加氢反应器来说, 油气和氢气在上一床层反应后温度将升高,为了下一床层继续 有效反应的需要,必须在两床层间引入冷氢气来控制温度。将 冷氢气引入反应器内部并加以散布的管子被称为冷氢管。
二、加氢反应器结构 加氢过程由于存在有气、液、固三 相的放热反应,欲使反应进料(气、 液两相)与催化剂(固相)充分、 均匀、有效地接触,加氢反应器设 计有多个催化剂床层,在每个床层 的顶部都设置有分配盘,并在两个 床层之间设有温控结构(冷氢箱), 以确保加氢装置的安全平稳生产和 延长催化剂的使用寿命。
反应器内设置有入口扩散器、 积垢篮、卸料管、催化剂支撑盘、 出口捕集器、气液反应物流分配盘、 冷氢箱、熱电偶保护管和出口收集 器等反应器内构件。
加氢反应器介绍 ppt课件

(3)装置停工时冷却速度不应过快,且停工过程中应有使钢中吸藏的 氢能尽量释放出去的工艺过程,以减少器壁中的残留氢含量。
加氢反应器
一.加氢反应器
加氢反应器是各类加氢工艺(Hydrogen Cracking Unit)的关键设备 加氢是在催化剂存在的条件下从外界补入氢气以提高油品的氢碳比。 加氢裂化实质上是加氢和催化裂化过程的有机结合,一方面能使重 质油品通过裂化反应转化为汽油、煤油和柴油等轻质油品,另一方 面又可防止像催化裂化那样生成大量焦炭,而且还可将原料中的硫、 氯、氧化合物杂质通过加氢除去,使烯烃饱和。 因此,加氢裂化具有轻质油收率高、产品质量好的突出优点。
影响高温氢腐蚀的主要因素
1)温度、压力和暴露时间的影响
温度和压力对氢腐蚀的影响很大,温度越高或者压力越大发生高 温腐蚀的起始时间就越早。
2)合金元素和杂质元素的影响
在钢中凡是添加能形成很稳定碳化物的元素(如铬、钼、钒、钛、 钨等),就可使碳的活性降低,从而提高钢材抗高温氢腐蚀的能力。
在合金元素对抗氢腐蚀性能的影响中,元素的复合添加和各自添 加的效果不同。例如铬、钼的复合添加比两个儿素单独添加时可使抗 氢腐蚀性能进一步提高。在加氢高压设备中广泛地使用着铬-钼钢系, 其原因之一也在于此。
床层的下沉。
4. 催化剂支撑盘
催化剂支撑盘由T形大梁、格栅和丝网组成。大梁的两边搭在反应器 器壁的凸台上,而格栅则放在大梁和凸台上。格栅上平铺一层粗不锈钢丝 网,和一层细不锈钢丝网,上面就可以装填磁球和催化剂了。
- 1、下载文档前请自行甄别文档内容的完整性,平台不提供额外的编辑、内容补充、找答案等附加服务。
- 2、"仅部分预览"的文档,不可在线预览部分如存在完整性等问题,可反馈申请退款(可完整预览的文档不适用该条件!)。
- 3、如文档侵犯您的权益,请联系客服反馈,我们会尽快为您处理(人工客服工作时间:9:00-18:30)。
出的热量 , 又可 以 克服 高压下 搅拌 器 密封性 能 差 应速 率很快 , 可连续化 生产 , 热 传
方便等 , 缺点是能 耗大 , 对循 环泵 的要求 十分 苛刻 , 因为金属 催
2 液 体 外 循 环 反 应 器
液体外循环反应器是 目前液相催化 加氢反应效 果最理想 的
反应器 , 叫管式反应 器 , 也 是瑞士 B S U S公司最 早研究 开发用 于
应, 因为这类加氢反应所用 的贵金属催 化剂便 于分离 回收套用 ,
工业上应用 非常广泛 。例 如硝 基芳烃 、 脂肪腈 、 烯烃 、 炔烃 、 酮 醛
a r cpe,p r r n ea dtec aa tr t eea ay e n o r e eal.I p itdt a tesl —id cn lp n il ef ma c n h h rce si w r n zd a d c mp sd i d ti i o i c l i n s t one t h ef n u ig h
( aghuY a h n h mcl ni e n ehooyadE up e t o , t. Z e agH n zo 0 2 C i ) H nzo unZ egC e ia E g er gT cnl n q im n C . Ld , hj agh u30 1 , h a n i g i n 1 n
等的液相催 化加 氢反应 , 共 同特点是 反应 速率受 气液 传质 的 其 控制 , 而气液传质涉 及到气 体分 散 、 体循 环 、 气 以及 固体 催化 剂
悬浮等过程 , 而且 , 催化 加氢反 应一般 是强 放热 反应 , 以反 应 所 体系显得比较复杂。 由于气 液的不相 容性 , 且密度差别非 常大 , 气液反 应器 中未
Ke r s i u d—p a e c tl t y r g n t n;i e lr ef n u i g i elr y wo d :l i q h s aay i h d o e ai c o mp l ;s l —i d c n mp l e e
在精细化工行业 中 , 我们经常会 遇到液相催 化加氢 反应 , 尤 其是催 化剂以 固态形 式 存在 于 反应 体 系的 非均 相催 化 加氢 反
析和互相对 比 , 指出 自吸式反应器是最适合应用于液相催化加氢反应场合 , 中杭 州原正 化学工程技 术装备有 限公 司是 国内较早 从 其 事研究开发 自吸式搅拌装置 的单位 , 设计和生产制造的 自吸式搅拌装置性能 比较优越 , 术在国内处于领先水平 。 技
关 键词 : 液相催化加氢; 反应器; 形式; 吸式反应器 自
泡, 大幅度提高气液相接触 面积 和反应速 率。而且 , 该反应 系统 在外循 环管路上可设 置无 限大 的换热 面积 , 时移走氢 化 时放 及
反应的气体 聚积在反应 器 内的上 部空 间 , 重影 响反应 速率 和 严
效率。同时 , 催 化剂 悬浮 的不均 匀 也 约束 了反 应 的 速率 。 固体
Diiu so n t e f r o q i —p a e Ca a y i d 0 e a in I elr sc s i n o h o m fLi u d h s t l t Hy r g n tO mp l c e
S O n HA Ho g—g n,Z O Ja e HA in—mig n
i el rg a ual e a r fre h ie f rlq i mp l r d l b c me a p e e r d c o c i u d—p a e c tl t y r g n to e y o h s aay i h d o e a in.Ha g h u Yua e g Ch mia c n zo n Zh n e c l En i e rn c n l g n u p n ., d g n e i g Te h oo y a d Eq i me tCo Lt .wa h o e n e o R & D,a d l a h e i n a d ma u a t rn f s te f r r n rt u n e d t e d sg n n f cu go i sl ef—idu i g mii g e u p n . n cn x n q i me t
21 年 3 00 8卷第 3期
广州化工
・6 ・ l1
浅 谈 液 相 催化 加 氢 反应 器 的 形式
邵洪根 , 赵建 明
( 州原正化 学工程技术装备有限公 司, 杭 浙江 杭州 30 1 ) 10 2
摘 要 : 介绍了目前液相催化加氢反应中遇到的主要几种反应器的形式, 并对各种反应器的结构、 工作原理及优缺点进行了分
双键 、 三键 、 脂肪族 等化合 物 的加 氢 反应 中。它 主要 由反应釜 、 文丘里管 、 循环泵等组成 , 是用循环泵将 反应混合 物从反应 器底
部抽出 , 通过文丘里管抽 吸反应 器气相空 间内的反应 气体 , 在文
丘里管 内进行高强度 的湍 流混合 与分 散 , 可得 到十分 细小 的气
Absr t:S me tp so mp l rfrl i tac o y e fi e l o i d—ph s aay i y r g nain we e d s u s d,t e sr cu e,o e a in e qu a e c t ltc h d o e to r ic se h tu t r p rt - o