轻型客车车身仿真对比分析及轻量化
客车车身骨架轻量化材料与轻量化设计

客车车身骨架轻量化材料与轻量化设计摘要:现如今,我国汽车制造行业快速发展,制造技术也越来越高。
节能减排是国家能源发展要求和汽车行业的发展方向,轻量化是实现节能减排的有效途径,也是汽车制造企业的核心竞争力。
从车身结构设计、材料、工艺3个方面探讨了汽车车身的轻量化设计方法,并提出了车身产品设计需从多维度多方法综合考虑来合理实现轻量化。
关键词:客车;骨架;轻量化材料;轻量化设计引言目前,汽车轻量化主要通过材料轻量化、结构轻量化、工艺轻量化等途径实现,三者间相互作用相互影响。
相较于结构和工艺的轻量化,材料轻量化带来的效果更为立竿见影。
然而取得材料轻量化的突破并非易事,要兼顾重量轻、强度高,同时还要控制成本。
1车身轻量化内涵及意义在2020年发布的《节能与新能源汽车技术路线图2.0》中确认了全球汽车技术“低碳化、信息化、智能化”的发展方向,节能汽车仍是市场主力,呈现出一体化、轻量化、高压化发展趋势。
由此可见,汽车轻量化作为共性指标,贯穿在国家新能源汽车进步发展的全过程中。
汽车轻量化是一项复杂的系统工程,它是在成本控制与性能改进条件下,通过轻量化结构设计与轻量化材料和制造技术在整车产品上的集成应用而实现的产品减重。
面对日益严峻的油耗法规,世界各国汽车企业都在采取积极的措施以推动汽车产品的节能减排,轻量化是一种有效的手段。
因此,推动汽车轻量化的进步,能够快速提高自主品牌汽车的开发能力。
2车身新材料设计技术2.1镁合金镁合金密度约为钢的1/4,约为1.7g/cm3,比强度和比刚度高,兼有良好的阻尼减震和电磁屏蔽功能,同时易于加工、可回收再利用,逐渐成为轻量化发展的研究应用对象。
镁合金存在耐蚀性差、易燃、室温塑性差的缺点。
汽车上采用镁合金零部件共有60多种,所用的镁合金材料主要是AZ和AM合金,少量采用AE和AS3合金。
目前汽车行业金材料牌号还相对较少,汽车平均用镁量为0.7-1.2kg,个别商用车车型镁合金用量达2.0-3.0kg。
GL6466轻型客车车身结构轻量化优化研究
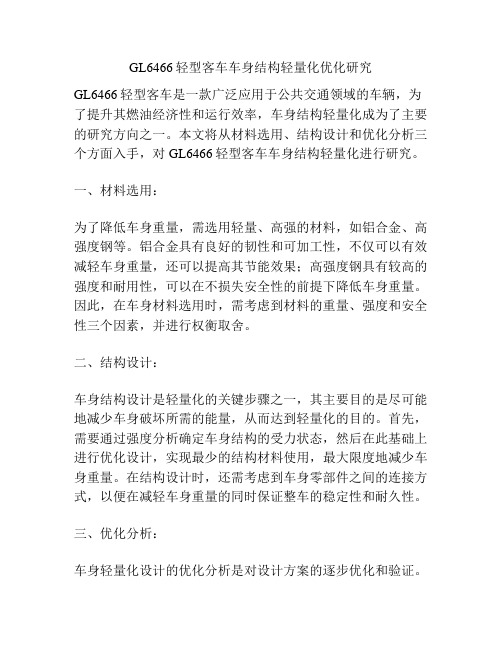
GL6466轻型客车车身结构轻量化优化研究GL6466轻型客车是一款广泛应用于公共交通领域的车辆,为了提升其燃油经济性和运行效率,车身结构轻量化成为了主要的研究方向之一。
本文将从材料选用、结构设计和优化分析三个方面入手,对GL6466轻型客车车身结构轻量化进行研究。
一、材料选用:为了降低车身重量,需选用轻量、高强的材料,如铝合金、高强度钢等。
铝合金具有良好的韧性和可加工性,不仅可以有效减轻车身重量,还可以提高其节能效果;高强度钢具有较高的强度和耐用性,可以在不损失安全性的前提下降低车身重量。
因此,在车身材料选用时,需考虑到材料的重量、强度和安全性三个因素,并进行权衡取舍。
二、结构设计:车身结构设计是轻量化的关键步骤之一,其主要目的是尽可能地减少车身破坏所需的能量,从而达到轻量化的目的。
首先,需要通过强度分析确定车身结构的受力状态,然后在此基础上进行优化设计,实现最少的结构材料使用,最大限度地减少车身重量。
在结构设计时,还需考虑到车身零部件之间的连接方式,以便在减轻车身重量的同时保证整车的稳定性和耐久性。
三、优化分析:车身轻量化设计的优化分析是对设计方案的逐步优化和验证。
可以通过有限元分析等手段对车身结构进行优化分析,评估其强度和稳定性,并确定优化配置。
同时,还可通过仿真实验对设计方案的可行性进行验证,从而避免在实际应用中出现不可预见的安全隐患。
总之,轻量化是目前汽车行业的大趋势,而在GL6466轻型客车的车身结构轻量化研究中,材料选用、结构设计和优化分析是必不可少的关键技术,它们的合理运用将在保证车身安全的前提下提高车身的强度和稳定性,最终实现车身结构的轻量化目标。
随着全球对环保和节能的要求越来越高,汽车设计师们也越来越注重车身结构的轻量化。
对于GL6466轻型客车这类广泛应用在公共交通行业的车型,其车身结构轻量化的研究不仅可以提高燃油经济性和运营效率,还可以降低碳排放量,为环保事业做出贡献。
一、材料选用在材料选用方面,除了铝合金和高强度钢之外,还可以考虑采用纤维增强塑料,这是一种轻量、高耐久的材料。
基于现代设计的客车车身结构分析及其轻量化设计

基于现代设计的客车车身结构分析及其轻量化设计发表时间:2019-06-05T15:23:47.403Z 来源:《中国西部科技》2019年第6期作者:吴准佳[导读] 本文阐述了现代设计客车车身结构的重要性,对现代设计的客车车身结构进行分析,制定出现代设计的客车车身轻量化方案,希望对我国客车车身结构设计有所帮助。
中兴智能汽车有限公司随着经济社会的不断发展,交通事业得到迅猛提高,客车也需要随着科技发展不断进行技术结构革新。
现代设计客车是我国公共交通行业的组成部分之一。
现代设计客车车身结构进行重新的优化设计对于我国客车行业发展具有重要的现实意义。
现代设计客车车身结构优化和轻量化设计有助于我国控制车辆计算机技术,实现制动和操作的功能性要求,可以符合现代化市场需求,选择合适的材料,逐步实现现代设计客车车身结构设计升级和优化改造。
我国国产客车在加工制造环节具备优先的设备和工艺方法,可以实现优质的管理经验和营销网络系统,在研发也逐步向着完善的方向发展,研制出合理的技术操作流程。
国产客车在生产中需要采用先进的设备、优质生产加工制造工艺,逐步完善管理验收流程,采用合适的加工制造流程,逐步对客车车身技术进行稳步提升,促使国内客车车身制造水平得到持续稳固提升,提高客车整体水平,缩小与国外先进客车的差距。
一、现代设计客车车身结构的重要性随着经济社会的不断发展和进步,我国客车现代化设计起步较晚,与国际先进客车工艺相比仍存在差异。
现代设计客车车身结构优化有助于开发国产的全承载式的车身结构,增强零件的研发水平和生产力,促进零部件企业在现代社会中得到迅猛发展。
现代设计的客车车身结构对于客车而言就是车身结构制造加工,零部件在制造加工中受到轻量化结构的限制,因此需要对车辆的自重情况和合理结构进行调整。
底架车身组合才能搭建出客车设计结构,车身主要可以分担车辆的荷载,在底架基础上可以减少荷载,对车辆车身和车架的结构进行辅助。
现代设计的客车车身需要选择全部承载式的车身结构,增强零部件的自主研发和生产力模式,促使零部件发展与车辆发展水平相统一,提高客车车辆工艺设计水平,提高客车工业数字化设计和制造水平,促使其结构设计摆脱传统设计技术的方向前进,提高我国现代设计客车车身细分领域的整体水平。
客车车身结构轻量化分析

客车车身结构轻量化分析摘要:对于大客车车身结构轻量化设计要给予更多重视与关注,在实际轻量化设计中,工作人员对于各方面问题要进行全面分析与了解。
可以通过材料轻量化以及工艺轻量化等措施,减轻大客车车身重量,使得大客车在行驶过程中能够达到节能减排效果。
关键词:大客车;车身结构;轻量化在如今社会发展背景下,环保成为汽车产业发展中的重点与关键,尤其对于大客车来说,车身骨架在承受车辆行驶过程中全部载荷的同时,重量占据客车总重量的2/5左右,由此可以看出,大客车的车身结构轻量化对整体节能减排的影响。
为了达到节能减排的目的,要实现大客车车身结构的轻量化发展,使得大客车在行驶过程中能够减少污染物的排放,在环境保护中将自身作用发挥出来。
1材料轻量化从目前大客车生产中可以看出,客车材料主要以钢铁材料为主,并且在整体材料中占据65%以上,钢铁材料密度相对较大,这也是大客车整车较为笨重的一个主要原因。
在材料制造加工技术的不断发展背景下,使得钢铁材料在客车中的使用比例逐渐减少,同时,高强钢、铝镁合金材料以及碳纤维材料,在客车材料中得到更好应用。
例如,蜀都客车与中铝集团合作研发的新能源客车,就是全铝车身。
全铝车身的出现,相较于刚结构车身而言,12米客车能够减重500kg左右。
而且此类轻型材料具备强度高、耐腐蚀性好等特点。
基于此,在实际大客车的材料轻量化设计中,要对不同材料进行合理应用。
具体几种材料的实际情况,如图一所示。
2结构轻量化尽管汽车材料轻量化的研究占据大多数,也使得客车轻量化设计得到一定进步与完善,但是轻型材料在具体使用中,会存在不少缺陷与问题,在此背景下,要加强结构轻量化设计。
结构轻量化根据其形式与用途的不同,还可将其细化分类,比如,拓扑优化,拓扑优化是要确保材料布置的科学性与合理性;形貌优化,形貌优化要明确肋板位置与加强筋位置;自有尺寸优化,自有尺寸优化需要对壳单元厚度分布进行明确;尺寸优化,尺寸优化需要明确单元的宽尺寸与截面长;形状优化,形状优需要明确开发单元对象的有限元模型当中的几何形状;自由形状优化,自由形状优化需要明确研究区域内最为适合的形状。
基于碰撞模拟仿真的车身结构轻量化设计与优化研究

基于碰撞模拟仿真的车身结构轻量化设计与优化研究车身结构是汽车产品中至关重要的部分之一,它承担着保护车内乘员安全的重要任务。
然而,随着环保意识的提高以及对汽车性能要求的不断增加,轻量化成为了汽车设计的重要方向。
本文将基于碰撞模拟仿真的方法,研究车身结构的轻量化设计与优化。
1. 引言随着全球经济的发展和人们生活水平的提高,汽车已经成为人们生活中不可或缺的一部分。
然而,汽车对资源和能源的消耗也给环境带来了压力。
因此,研究车身结构的轻量化设计与优化变得尤为重要。
2. 碰撞模拟仿真技术介绍碰撞模拟仿真技术是一种通过计算机模拟车辆在碰撞事故中的受力情况的方法。
它基于有限元分析原理,可以准确地模拟车身结构在碰撞过程中的变形和受力情况。
通过这种技术,我们可以更好地了解车身结构在碰撞事故中的表现,以及如何优化车身结构来提高乘员的安全性。
3. 车身结构轻量化设计的意义车身结构的轻量化设计可以带来多方面的好处。
首先,它可以减少车辆的整体重量,提高燃油经济性和减少尾气排放。
其次,轻量化设计还可以降低碰撞事故中乘员的伤害风险,并提高整车的安全性能。
此外,轻量化设计还可以提高车辆的加速性能和操控性,提升用户的驾驶体验。
4. 车身结构轻量化设计与优化的方法在进行车身结构的轻量化设计与优化时,我们可以采用以下几种方法。
首先,通过使用轻量材料,如高强度钢、铝合金和复合材料等,来替代传统材料,可以有效地降低车辆的整体重量。
其次,通过优化车身结构的形状和布局,例如使用设计优化软件对车身结构进行拓扑优化,可以进一步降低车辆的重量,同时确保车身的刚度和强度符合设计要求。
最后,通过碰撞模拟仿真技术对车辆的碰撞性能进行评估和优化,可以提高车辆的安全性能。
5. 案例分析与结果讨论本文以某车型为例,进行了车身结构的轻量化设计与优化研究。
首先,使用碰撞模拟仿真技术对车辆在不同碰撞情况下的受力情况进行了分析。
然后,通过改变车身结构的材料和形状,对车辆的整体重量进行了优化。
纯电动客车车身有限元分析与轻量化研究

分析客车在运行过程中的水平弯曲工况、极限扭转工况、紧急 制动工况和紧急转弯工况,在以上四种典型工况下对客车进行静 态分析,计算了车身骨架结构的应力值与位移值。对客车车身结 构进行模态分析,获得了车身前10阶的自由振动频率及相应的振 型,结果均满足要求,为后续车身骨架轻量化设计提供依据。
然后,基于OptiStruct结构优化方法对车身进行轻量化研究,运 用多种方案对车身骨架进行拓扑优化分析,对比分析结果,获得 车身结构最佳的质量分布。根据拓扑优化分析结果、车身骨架 的设计要求和制造工艺要求,设计出拓扑优化后的车身骨架结构。
纯电动客车车身有限元分析与轻量化 研究
目前,节能、环保、安全成为汽车工业可持续发展所面临的主要 问题,汽车轻量化是实现节能减排的主要途径之一。客车车身骨 架作为主要承载结构,其重量约占客车总重量的30%~40%,因此车 身骨架的轻量化对减轻整车的质量有着非常重要的意义。
Hale Waihona Puke 本文对某纯电动客车车身结构进行有限元分析并采用拓扑优化 方法对车身结构进行了轻量化研究。首先,建立客车骨架结构的 有限元模型,对其进行有限元分析。
最后,对优化设计后的车身骨架进行静态、模态分析,并与原车 身骨架进行对比,结果表明,新车身骨架性能有所上升,质量减少 6.96%,取得了较好的轻量化效果。本文所作研究在丰富车身结 构优化设计的分析结果和相关数据方面做出了一定的贡献。
基于CAE技术的某轻型客车车身轻量化设计

基于CAE技术的某轻型客车车身轻量化设计第一章绪论随着人们对环保和节能意识的提高,轻量化已成为汽车工业的热门话题。
而轻型客车作为城市和旅游交通中的重要存在,其轻量化设计显得尤为重要。
本文将采用计算机辅助工程(CAE)技术,针对某轻型客车进行车身轻量化设计的研究。
第二章参考文献综述本章主要介绍了车身轻量化设计相关技术和理论。
首先介绍了减重材料的种类和使用情况,如高强度钢、铝合金、碳纤维等;然后介绍了CAE技术在车身轻量化中的应用,包括有限元分析、优化算法等。
最后还列举了一些车身轻量化的案例研究,说明了轻量化设计的重要性和实际应用效果。
第三章仿真分析本章将应用CAE技术进行车身轻量化仿真分析。
首先构建了某轻型客车的三维模型,并建立了包括载荷和约束条件在内的有限元模型。
然后进行了静态和动态分析,获得了车身在不同工况下的受力和变形情况。
最后应用优化算法对车身进行了优化设计,得到了轻量化方案。
第四章结果分析本章将对仿真分析的结果进行分析。
通过对优化后的车身进行静态和动态分析,验证了轻量化方案的可行性。
并将轻量化前后的车身质量和性能指标进行对比,得出了轻量化设计带来的质量降低和性能提升情况。
第五章结论和展望本章将对轻量化设计的效果进行总结和评价,并对未来的研究方向进行展望。
本文采用CAE技术对某轻型客车进行了车身轻量化设计的研究。
通过仿真分析和优化算法,得出了轻量化方案,并在验证可行性的基础上进行了质量和性能对比。
结果表明,轻量化设计能够有效降低车身质量,并提高车辆的性能和节能效果。
未来的研究方向应该进一步深入探究轻量化材料的性能和应用范围,开发更为先进的CAE技术进行轻量化设计研究。
客车车身轻量化分析

客车车身轻量化分析作者:沈浩陈昌明姚晓冬周正飞赵吉文摘要:以某车型为例,分别从优化流程、优化分析模型、分析工况等方面研究车身轻量化方法,提出一套切实可行的技术路线。
关键词:车身;结构;轻量化;优化技术轻量化设计是当今汽车设计中的主题之一,它可以提高车辆的动力性,降低成本,减少能源消耗并相应降低污染。
然而,轻量化结构是一双刃剑,不仅对车辆强度和刚度将产生影响,也对结构寿命有影响,这两方面需要协调处理。
目前关于这方面研究大多集中于采用轻型材料,但由于成本、加工工艺、环保等方面的问题[ 1,2 ] ,这些材料还很难用于一般车辆,而从结构角度方向优化却更具有实际意义。
结构轻量化本质上是一优化问题,现有优化技术已大规模应用于工程设计领域,但客车结构的特殊性使现有优化方法必须加以改进才具有可行性,其中优化流程、控制工况、约束条件、优化模型等均是非常关键的技术问题,在现有可参考的文献中,关于这方面的系统研究很少。
1 优化流程确定优化分析模型一般由目标函数、约束方程、优化设计变量三个方面组成。
如果能将这三个方面以解析数学函数的形式书写,在现有计算机技术和优化理论的条件下可以借助相关软件,能比较简单地完成,但由于客车结构轻量化设计的许多特殊条件,这种方法不适用。
首先,在轻量化分析过程中,一般选取目标函数为车身总质量最小。
对于现有的分析软件可以实现此目标函数的定义,前提是在分析环境中建立参数化几何模型,但是现有分析用几何模型大多来自于CAD软件,其通过一定格式进入分析软件中,丧失了一些特征参数,从而无法实现优化。
若在分析软件中进行几何建模,对于梁单元尚可,对于板壳单元则不现实。
所以,基于车身近似建模的梁单元模型是这种优化方法的唯一模型。
其次,约束条件主要包括合理的车身动刚度(主要指前几阶振型对应的固有频率控制在一定范围之内)、各工况下车身结构件应力不大于屈服极限、在扭转工况下各车窗的变形控制在一定范围之内等,这些方程在软件中可以定义。
客车车身轻量化研究-周俊杰
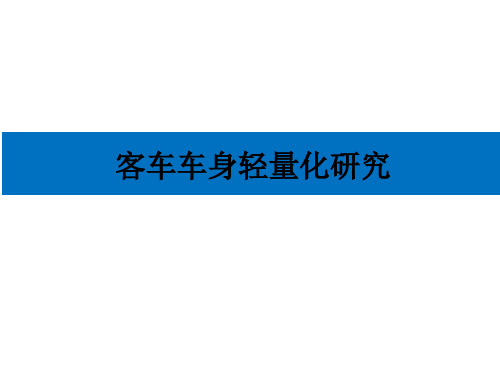
3
计算结果——静态分析(强度、刚度分析)
结果分析,扭转工况
3
计算结果——静态分析(强度、刚度分析)
壳单元有限元模型 弯曲工况应力 /MPa 车顶 车底 左侧围 右侧围 前围 后围 55.114 107.75 87.838 104.82 27.613 45.496 扭转工况应 /MPa 89.274 142.13 159.34 123.16 63.728 73.327 梁单元有限元模型 弯曲工况 应力/MPa 24.287 71.188 34.29 45.373 18.073 21.829 扭转工况应力/MPa 43.169 111.39 142.98 66.814 29.126 27.2
4
构件名称
轻量化设计
变量名 t1 t2 t3 t4 t5 t6 初始值(mm) 2 2 2 2 2 2 下限(mm) 1.5 1.5 1.5 1.5 1.5 1.5 上限(mm) 3 3 3 3 3 4
车顶纵、横梁 后围骨架 前围骨架 地板骨架
左右侧围立柱 、斜撑梁
上下门立柱
具体优化过程中使其值弯曲、扭转工况下分别不超过130MPa、 180MPa(按经验值安全系数取1.3~1.8,Q235屈服极限为 235MPa),低于所选材料的屈服极限,使形变值满足该车在两种 工况下的最大变形量均小于《客车定型试验规程》(GB/T130432006)中所规定的10mm和12mm的限值。
1.5 1.5 1.75 1.5 1.75 3
圆整后整个车身骨架的质量降低了约为167kg,占原车 身骨架的5.6%,基本达到预期减重目标。将圆整后的数 据重新计算,得到其静、动态数值。
4
轻量化设计—轻量化后车型分析
轻量化后该车车身骨架在弯曲、扭转工况下的最大应力值分别为 86.725MPa、166.97MPa,最大变形值为3.7921mm、13.223mm,强 度、刚度均满足要求。
基于汽车碰撞模拟仿真的车辆车身轻量化设计与优化

基于汽车碰撞模拟仿真的车辆车身轻量化设计与优化随着汽车行业的快速发展,车辆碰撞模拟仿真技术在车身轻量化设计与优化中扮演着重要角色。
本文将基于汽车碰撞模拟仿真,探讨车辆车身轻量化设计与优化的相关内容。
1. 引言汽车碰撞模拟仿真技术是指通过计算机仿真,模拟出车辆在碰撞事故中的运动轨迹、变形情况和受力状况。
利用该技术,可以有效评估车身结构的强度和刚度,进而优化车辆的设计方案。
2. 车辆碰撞模拟仿真的原理与方法2.1 车辆碰撞模拟仿真的原理汽车碰撞模拟仿真主要基于有限元法,即将车身结构分割为许多小的有限元单元,通过数学计算和力学分析,模拟车辆在碰撞过程中的受力和变形情况。
2.2 车辆碰撞模拟仿真的方法车辆碰撞模拟仿真方法主要分为前期数据准备、建模、加载条件设定、计算及分析、结果评价等步骤。
其中,前期数据准备包括车辆结构参数和材料参数的获取;建模则是将车身结构用有限元模型表示;加载条件设定是指在仿真中设置碰撞的速度、角度等条件;计算及分析阶段是通过数值计算求解模型的变形情况;结果评价是根据仿真数据对车辆结构进行评估和优化。
3. 车辆车身轻量化设计的意义车辆车身轻量化设计的意义在于降低车辆整体重量,提高燃油经济性和减少碳排放,同时有效提升车辆的性能和安全性。
轻量化设计可以通过优化材料使用、结构设计和制造工艺来实现。
4. 车辆车身轻量化设计与优化的方法4.1 材料选择与优化选择适合的轻量化材料(如高强度钢、铝合金、复合材料等)可以减轻车辆自重,提升整车刚度,但也需考虑材料成本和制造工艺等因素。
4.2 结构设计与拓扑优化通过优化车身结构的设计,如更合理的构架布置、强化重点部位等,可以达到减轻车身重量的目的。
拓扑优化方法则可以帮助确定充分利用材料强度的结构形态。
4.3 碰撞模拟与仿真利用碰撞模拟仿真技术,评估车身结构在碰撞事故中的受力状况,进而优化设计方案,提高车身的碰撞性能和安全性。
5. 车辆车身轻量化设计与优化案例分析以某款城市SUV为例,结合碰撞模拟仿真技术,进行车身轻量化设计与优化。
客车车身结构轻量化设计

客车车身结构轻量化设计客车车身不仅起到覆盖件的作用,而且还承载了客车一部分载荷,因此在概念设计阶段,对其进行拓扑优化就显得非常有必要。
文章首先通过Hypermesh 建立以某客车车身结构为基础的有限元模型,之后根据拓扑理论构建其拓扑优化模型,确定合适的优化三要素,选取最为常见的四种极限工况,再通过有限元软件OptiStruct的优化计算,最终得到其优化结果。
以拓扑优化结果来指导客车车身的设计,在确保满足车身各项性能要求达标的同时,能够提高材料利用率,减少冗余,达到车身结构的轻量化。
标签:有限元;拓扑优化;轻量化引言节能、环保和安全是汽车工业发展中所面临着的三大主要问题,油耗和排放是影响这些的重要因素。
大量数据研究表明,整车质量的大小与油耗密切相关,因此在满足整车各项性能指标的基础上对其进行轻量化是十分有必要的。
就客车来说,车身质量占整个客车质量的比重很大,通常为了满足其强度的要求车身骨架强度会出现局部富余的情况,这将进一步导致车身质量的偏大。
而我们国家的客车车身往往存在质量偏大的情况,甚至于存在有些结构刚度强度富余的情况。
大量研究表明,汽车质量每降低10%,油耗降低6-8%,排放降低4-10%。
而车身是客车三大总成之一,占整个客车总质量的40%-60%,由此可见影响整车轻量化的主要因素是对车身的轻量化。
目前,汽车轻量化的主要途径有以下两种,一是采用轻量化材料,例如采用高强度钢,铝镁合金等新材料,在满足刚度强度的情况下,使得质量更轻;二是利用CAE技术进行客车结构的优化,使得材料分布和各零部件布局更加合理,在满足要求的情况下,最大限度的减重。
文章就是基于拓扑优化的某客车车身结构设计,从而到达优化减重的目的。
1 拓扑理论简介与拓扑模型的建立1.1 拓扑理论简介拓扑优化(Topology)作为一种概念性的数学方法,是将一定设计空间内的连续体离散成有限单元网格,为每个离散单元附上合适的材料属性,给定合适的约束条件,利用OptiStruct自身的近似优化算法-根据结构自身的传力路径对材料分布进行重新布置,来完成设计人员给定的设计目标。
客车车身骨架轻量化设计分析
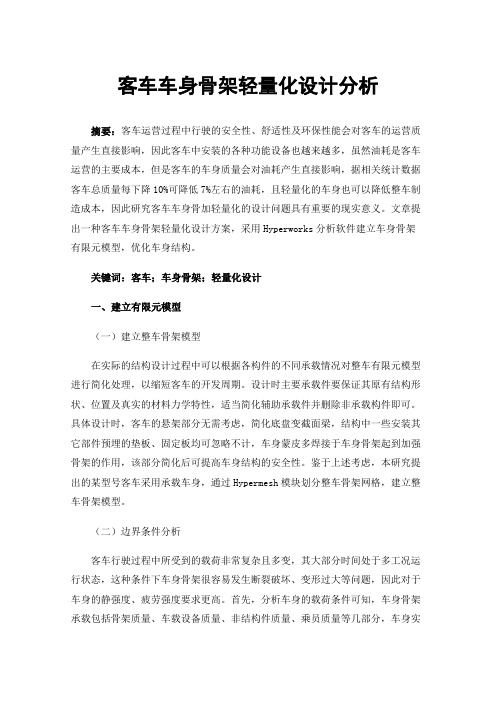
客车车身骨架轻量化设计分析摘要:客车运营过程中行驶的安全性、舒适性及环保性能会对客车的运营质量产生直接影响,因此客车中安装的各种功能设备也越来越多,虽然油耗是客车运营的主要成本,但是客车的车身质量会对油耗产生直接影响,据相关统计数据客车总质量每下降10%可降低7%左右的油耗,且轻量化的车身也可以降低整车制造成本,因此研究客车车身骨加轻量化的设计问题具有重要的现实意义。
文章提出一种客车车身骨架轻量化设计方案,采用Hyperworks分析软件建立车身骨架有限元模型,优化车身结构。
关键词:客车;车身骨架;轻量化设计一、建立有限元模型(一)建立整车骨架模型在实际的结构设计过程中可以根据各构件的不同承载情况对整车有限元模型进行简化处理,以缩短客车的开发周期。
设计时主要承载件要保证其原有结构形状、位置及真实的材料力学特性,适当简化辅助承载件并删除非承载构件即可。
具体设计时,客车的悬架部分无需考虑,简化底盘变截面梁,结构中一些安装其它部件预埋的垫板、固定板均可忽略不计,车身蒙皮多焊接于车身骨架起到加强骨架的作用,该部分简化后可提高车身结构的安全性。
鉴于上述考虑,本研究提出的某型号客车采用承载车身,通过Hypermesh模块划分整车骨架网格,建立整车骨架模型。
(二)边界条件分析客车行驶过程中所受到的载荷非常复杂且多变,其大部分时间处于多工况运行状态,这种条件下车身骨架很容易发生断裂破坏、变形过大等问题,因此对于车身的静强度、疲劳强度要求更高。
首先,分析车身的载荷条件可知,车身骨架承载包括骨架质量、车载设备质量、非结构件质量、乘员质量等几部分,车身实际质量即为车身骨架质量,并根据车辆中相关辅助结构的质量确定质心H的位置,并在对应节点上均匀设置行李架、乘客行李、备胎、车内地板等构件的质量。
其次,确定客车动载系数。
车辆行驶过程中,不平整的路面会对车身产生瞬态冲击载荷,在这种条件下车身骨架、零部件极易出现疲劳缺隐,因此需要考虑动载荷系数。
客车车身骨架强度分析及轻量化设计

中国储运网H t t p ://w w w .c h i n a c h u y u n .c o mD I S C U S S I O N A N D RE S E A R C H 探讨与研究摘要:本文以某客车车身骨架为例,建立有限元模型,以四种典型工况下车身骨架强度为基础,以质量最小为目标,在满足车身强度的前提下,通过降低车身零件厚度,实现轻量化设计。
轻量化后车身骨架减轻276.3k g ,通过对比轻量化前后模型应力,验证方法了可行性。
关键词:车身骨架;有限元模型;轻量化设计0引言汽车轻量化、电动化和智能化是汽车工业的发展方向[1]。
大量研究表明,采用新材料、新工艺外,车身轻量化是汽车实现节能减排的重要途径之一。
在车身轻量化的设计过程中,车身结构必须满足强度特性要求。
目前车身轻量化设计主要采用有限元的方法[2-3],因此本文利用H y p e r Me s h 软件对客车车身骨架进行强度分析和轻量化研究。
1.有限元分析1.1有限元模型的建立由于车身骨架以钣金和管材为主,厚度大多在2mm 左右,因此采用s h e l l 单元划分网格比较合适。
网格尺寸为10mm,零件之间缝焊采用s e a m w e l d 单元模拟,车身骨架单元总数为1024506,其中三角形网格为24503,占比2.39%,车身有限元模型如图1所示。
图1客车车身骨架有限元模型1.2材料属性客车骨架材料主要采用Q 235、Q 195和T 52,其密度、弹性模量和泊松比均为7800K g /m 3,2.1×105MP a 和0.3,许用应力为160MP a ,135MP a 和270MP a 。
1.3边界条件1.3.1载荷条件客车车身骨架载荷由骨架质量、非结构质量、设备质量及乘客质量。
根据材料的密度,可以通过有限元软件计算出车身骨架质量;非结构件质量可以采用质量单元以均布在车身结构相应的位置;设备质量在其质心处施加质量单元,然后施加于车身骨架连接节点上;乘客质量均布在车身底盘车架上。
电动客车车身有限元分析及其轻量化设计

电动客车车身有限元分析及其轻量化设计作者:北京理工大学代红军林程摘要:以某电动客车为例,对其车身强度进行ANSYS有限元分析,并对其进行轻量化设计。
关键词:电动客车;客车车身;轻量化;有限元分析8 m电动客车是国家“863”重点项目。
作为电动客车,其动力总成为电池组。
电动客车车架承载也与一般客车不同,一般后置式发动机客车安装发动机的位置,现放置电池,行李舱位置也放置电池,要求车身结构强度和刚度必须足够。
而车身轻量化对提高客车的动力性,降低成本,延长行驶里程,提高经济性都有重要意义[ 1 ] 。
因此,如何优化车身结构,在保证强度和刚度满足使用要求的情况下使其轻量化非常重要,而且也是该车设计中一个关键的问题。
1 车身模型的建立(1) 首先,通过在三维设计软件PROE上建立电动大客车的整车结构几何模型。
然后,利用ANSYS软件[ 2 ]建立该车整车的详细有限元模型。
如图1所示。
(2) 电动客车的骨架采用标准的矩型管型材组焊而成,因此,在用有限元进行车身结构计算时,采用梁单元模型,其优点是划分的单元数目和节点数目少,计算速度快,而且模型的前处理工作量不大。
(3) 采用梁单元时,做了以下一些简化:①略去蒙皮和某些非承载构件,如面板、窗玻璃等。
②将车身中的各微曲梁直化处理,对侧围和顶盖中一些曲率较小的构件近似地看作由直梁单元分段组成。
③对两个靠得很近但并不重合的交叉连接点简化为一个节点处理。
④对两个并联焊在一起的梁当作一根梁,相应横截面积加大。
⑤取约束、载荷作用点处为梁单元节点。
模型中载荷、约束模拟真实的精确程度对整体结构的位移、应力影响很大。
因而载荷的类型、作用点、大小,约束的类型、作用点应尽量逼近实际情况。
图1车身骨架有限元模型图由于采用了简化处理,会使结果出现误差,但从简化措施来看,相当于降低了整车的强度和刚度,会使应力结果偏大,是一种偏安全的分析,因此是比较可靠的。
2 载荷和约束处理电动客车使用情况不是很复杂,基本上是在城市普通公路上行驶,因此选取弯曲、扭转、紧急制动和急转弯四种工况[ 3 ]对车身结构进行计算分析。
汽车碰撞模拟仿真在车身结构优化设计与轻量化中的应用研究
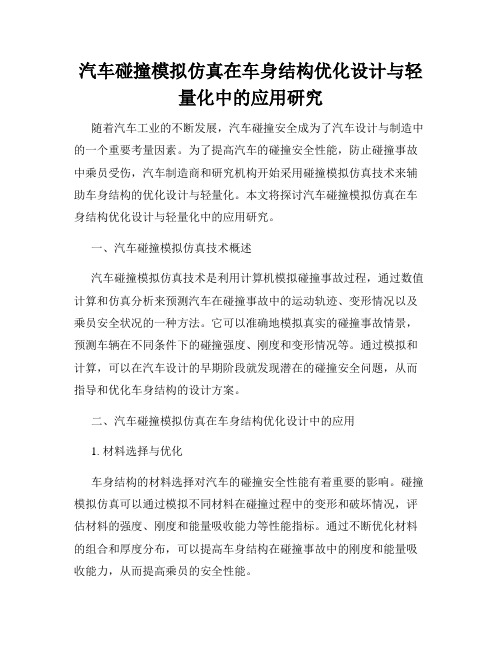
汽车碰撞模拟仿真在车身结构优化设计与轻量化中的应用研究随着汽车工业的不断发展,汽车碰撞安全成为了汽车设计与制造中的一个重要考量因素。
为了提高汽车的碰撞安全性能,防止碰撞事故中乘员受伤,汽车制造商和研究机构开始采用碰撞模拟仿真技术来辅助车身结构的优化设计与轻量化。
本文将探讨汽车碰撞模拟仿真在车身结构优化设计与轻量化中的应用研究。
一、汽车碰撞模拟仿真技术概述汽车碰撞模拟仿真技术是利用计算机模拟碰撞事故过程,通过数值计算和仿真分析来预测汽车在碰撞事故中的运动轨迹、变形情况以及乘员安全状况的一种方法。
它可以准确地模拟真实的碰撞事故情景,预测车辆在不同条件下的碰撞强度、刚度和变形情况等。
通过模拟和计算,可以在汽车设计的早期阶段就发现潜在的碰撞安全问题,从而指导和优化车身结构的设计方案。
二、汽车碰撞模拟仿真在车身结构优化设计中的应用1. 材料选择与优化车身结构的材料选择对汽车的碰撞安全性能有着重要的影响。
碰撞模拟仿真可以通过模拟不同材料在碰撞过程中的变形和破坏情况,评估材料的强度、刚度和能量吸收能力等性能指标。
通过不断优化材料的组合和厚度分布,可以提高车身结构在碰撞事故中的刚度和能量吸收能力,从而提高乘员的安全性能。
2. 结构设计与优化汽车碰撞模拟仿真可以帮助设计师评估和优化车身结构的刚度、刚性分布和变形情况等。
通过改变车身结构的设计,如加强A、B、C柱的设计,增加承载板的数量和位置,优化车身的撞击能量分散路径等,可以提高车身的刚度和刚性分布,减轻乘员在碰撞事故中的受力情况,从而提高碰撞安全性能。
3. 碰撞事故模拟与仿真碰撞事故模拟与仿真是碰撞模拟仿真技术中的核心内容。
通过对不同碰撞事故情景的模拟与仿真,可以预测汽车在复杂碰撞条件下的运动轨迹、变形情况和乘员受力情况。
通过模拟不同角度、不同速度和不同碰撞方式下的碰撞事故,可以评估车身结构在不同碰撞条件下的安全性能,指导车身结构的优化设计。
三、汽车碰撞模拟仿真在车身轻量化中的应用1. 材料轻量化设计碰撞模拟仿真可以帮助设计师评估不同材料的轻量化效果以及在碰撞过程中的性能表现。
单层软座客车的车身结构优化与轻量化设计

单层软座客车的车身结构优化与轻量化设计随着人们生活水平的提高,旅游、出行需求逐渐增加,单层软座客车成为了现代出行的重要交通工具之一。
为了提高客车的性能和燃油效率,减轻车身重量是一项非常重要的任务。
本文将介绍单层软座客车车身结构优化与轻量化设计的相关内容,以期提供一些优化和改进的思路。
1. 常用的轻量化材料轻量化设计的关键是采用适当的材料来替代传统材料,以降低车身重量。
常见的轻量化材料包括高强度钢材、铝合金、碳纤维复合材料等。
高强度钢材具有强度高、韧性好的特点,可用于车身主要结构件。
铝合金具有较低的密度和优异的成形性能,可应用于车身非主要结构件。
碳纤维材料具有极高的强度和刚度,重量轻且耐腐蚀,可用于车身部分增强件。
2. 车身结构优化车身结构的优化设计可以通过有限元分析等方法进行。
首先,可以通过对原始设计进行模拟和分析,了解车身在不同载荷和条件下的应力和变形情况。
然后,结合材料力学性能,对车身结构进行优化设计,以降低应力集中和减少材料使用量。
此外,合理设置加强筋和支撑结构,可以提高整个车身的刚度和抗扭性能,从而提升车辆的安全性和操控性。
3. 软座设计与轻量化软座是客车舒适性的重要组成部分,也是乘客选择客车的关键因素之一。
为了在保证舒适性的前提下实现轻量化,可以采用一些创新的软座设计。
例如,采用轻质材料制造软座椅架,选择高分子材料制造软座垫和背靠,同时保证座椅的结构牢固性。
此外,通过合理的减震和隔音设计,可以提高软座的舒适性,为乘客提供更好的旅行体验。
4. 空气动力学优化设计空气阻力是影响客车能耗的关键因素之一。
为了降低客车的空气阻力,可以通过优化外形设计和减小车身尺寸来实现。
采用流线型的车身设计可以减少空气阻力系数,提高车辆速度和燃油效率。
此外,合理布置车身上的空气导流板、下护板和尾部扩散器等附件,进一步优化车辆的空气动力学性能,减少空气阻力。
5. 新技术的应用随着科技的不断进步,新材料和新技术的应用为车身设计提供了更多可能性。
汽车碰撞模拟仿真对车辆结构轻量化的优化研究
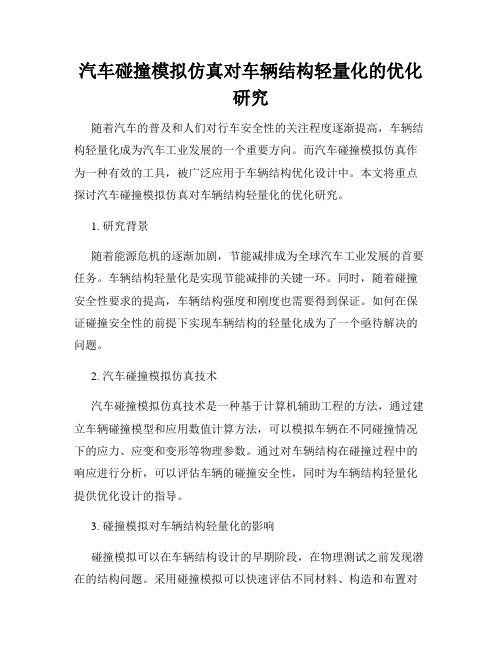
汽车碰撞模拟仿真对车辆结构轻量化的优化研究随着汽车的普及和人们对行车安全性的关注程度逐渐提高,车辆结构轻量化成为汽车工业发展的一个重要方向。
而汽车碰撞模拟仿真作为一种有效的工具,被广泛应用于车辆结构优化设计中。
本文将重点探讨汽车碰撞模拟仿真对车辆结构轻量化的优化研究。
1. 研究背景随着能源危机的逐渐加剧,节能减排成为全球汽车工业发展的首要任务。
车辆结构轻量化是实现节能减排的关键一环。
同时,随着碰撞安全性要求的提高,车辆结构强度和刚度也需要得到保证。
如何在保证碰撞安全性的前提下实现车辆结构的轻量化成为了一个亟待解决的问题。
2. 汽车碰撞模拟仿真技术汽车碰撞模拟仿真技术是一种基于计算机辅助工程的方法,通过建立车辆碰撞模型和应用数值计算方法,可以模拟车辆在不同碰撞情况下的应力、应变和变形等物理参数。
通过对车辆结构在碰撞过程中的响应进行分析,可以评估车辆的碰撞安全性,同时为车辆结构轻量化提供优化设计的指导。
3. 碰撞模拟对车辆结构轻量化的影响碰撞模拟可以在车辆结构设计的早期阶段,在物理测试之前发现潜在的结构问题。
采用碰撞模拟可以快速评估不同材料、构造和布置对结构强度和刚度的影响,从而优化车辆的结构设计。
通过模拟多种碰撞情况,可以选取最佳的结构方案,实现车辆结构的轻量化。
4. 优化方法及案例分析为了进一步提高轻量化效果,通常采用以下优化方法:材料优化、结构优化、形状优化和拓扑优化等。
以材料优化为例,通过选择具有较高强度重力比的新型材料,可以在不牺牲碰撞安全性的前提下降低车辆重量。
此外,结构优化可以通过调整零件的尺寸和形状来提高结构的强度和刚度,以适应不同碰撞情况的要求。
案例分析可以选择一款现有车型,对其进行碰撞模拟仿真并进行结构优化设计。
通过对比分析不同方案的轻量化效果和碰撞安全性,可以得出最佳的结构设计方案。
5. 挑战与未来展望尽管汽车碰撞模拟仿真对车辆结构轻量化的优化研究有着显著的优势,但目前仍存在一些挑战。
利用碰撞模拟仿真优化汽车车身轻量化设计
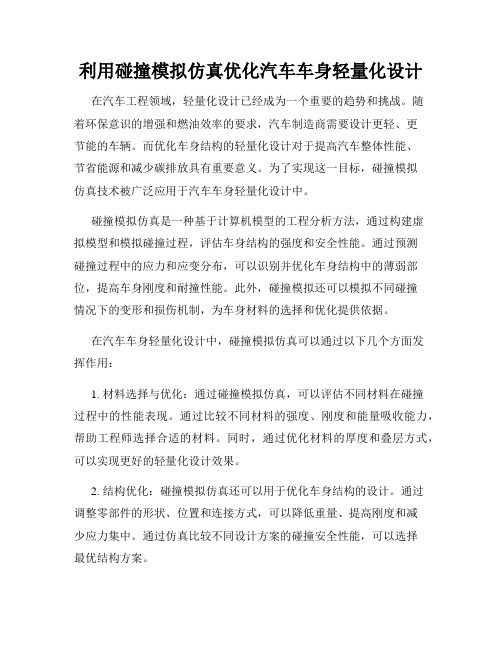
利用碰撞模拟仿真优化汽车车身轻量化设计在汽车工程领域,轻量化设计已经成为一个重要的趋势和挑战。
随着环保意识的增强和燃油效率的要求,汽车制造商需要设计更轻、更节能的车辆。
而优化车身结构的轻量化设计对于提高汽车整体性能、节省能源和减少碳排放具有重要意义。
为了实现这一目标,碰撞模拟仿真技术被广泛应用于汽车车身轻量化设计中。
碰撞模拟仿真是一种基于计算机模型的工程分析方法,通过构建虚拟模型和模拟碰撞过程,评估车身结构的强度和安全性能。
通过预测碰撞过程中的应力和应变分布,可以识别并优化车身结构中的薄弱部位,提高车身刚度和耐撞性能。
此外,碰撞模拟还可以模拟不同碰撞情况下的变形和损伤机制,为车身材料的选择和优化提供依据。
在汽车车身轻量化设计中,碰撞模拟仿真可以通过以下几个方面发挥作用:1. 材料选择与优化:通过碰撞模拟仿真,可以评估不同材料在碰撞过程中的性能表现。
通过比较不同材料的强度、刚度和能量吸收能力,帮助工程师选择合适的材料。
同时,通过优化材料的厚度和叠层方式,可以实现更好的轻量化设计效果。
2. 结构优化:碰撞模拟仿真还可以用于优化车身结构的设计。
通过调整零部件的形状、位置和连接方式,可以降低重量、提高刚度和减少应力集中。
通过仿真比较不同设计方案的碰撞安全性能,可以选择最优结构方案。
3. 碰撞安全性评估:碰撞模拟仿真可以评估车身在不同碰撞情况下的安全性能。
通过模拟正面碰撞、侧面碰撞和倒车碰撞等不同碰撞情况,可以预测车身在碰撞过程中受到的应力和变形情况。
根据仿真结果,可以选择合适的安全装置和加强措施,提高车辆的碰撞安全性。
4. 耐久性评估:碰撞模拟仿真还可以评估车身在长期使用过程中的耐久性能。
通过模拟车辆在不同工况下的动态应力加载,可以预测车身的疲劳寿命和损伤累积情况。
根据仿真结果,可以针对性地进行结构加固和零部件更换,延长车身的使用寿命。
综上所述,利用碰撞模拟仿真优化汽车车身轻量化设计具有重要意义。
通过模拟碰撞过程,可以评估车身结构的强度、安全性能和耐久性能,为轻量化设计提供科学依据。
某轻型客车侧翻仿真分析

2 0 1 5 ( 5 / 6)
技 术纵横
2 1
某轻型客车侧翻仿真分析
张遵智 袁刘 凯
( 南 京依 维柯汽 车 有 限公 司)
摘
要: 本文运 用 L S — DYNA软 件 , 以 某轻 型客 车 为研 究对 象 , 建 立 了整 车侧
翻模型 , 依 据 法规 GB 1 7 5 7 8 - 2 0 1 3进 行客 车动 态仿 真分 析 , 该 车生 存 空 间符 合 法
此 试验前 期 必须做 充 分 的准备 工作 ,试 验要 点 如
下。
人数达到 2 . 8 亿。 具统计数据显示 , 2 0 1 2 年全国涉
及 人员 伤亡 的交 通事 故 4 . 6 万起 , 造成 1 . 1 万 人 死 亡, 5万 人受 伤 。交通 事 故 居高 不 下 , 严重 影 响 了 人 们 的生活 和生产 , 带来 了一 系列 的社 会 问题 。 因 此, 开 展客 车上 部结 构强 度分析 , 研 究汽 车被 动 安
于1 9 9 8年 1 1 月 制订 了 G B / T 1 7 5 7 8 -1 9 9 8 ,规 定
主题 , 具有重要的社会 、 经济意义 , 得到了政府部 门的高度重视 ,汽车安全性已成为消费者购车时
考虑 的重 要 因素 。汽车安 全性 分 为主 动安全 和被 动安 全 ,其 中主动 安全是 汽 车避免 发生 事故 的能 力 ;被 动 安全是 发 生事故 时对 乘员 进行 有效 保 护 的能力 [ 1 】 。随着汽 车工业 的快速 发展 , 我 国汽 车数 量 日益增 多 , 根 据公 安 部 门数 据显 示 , 截止到 2 0 1 3 年 底, 我 国机动 车保有量 2 . 5亿余 辆, 驾驶机 动车 的
轻型客车车身仿真对比分析及轻量化
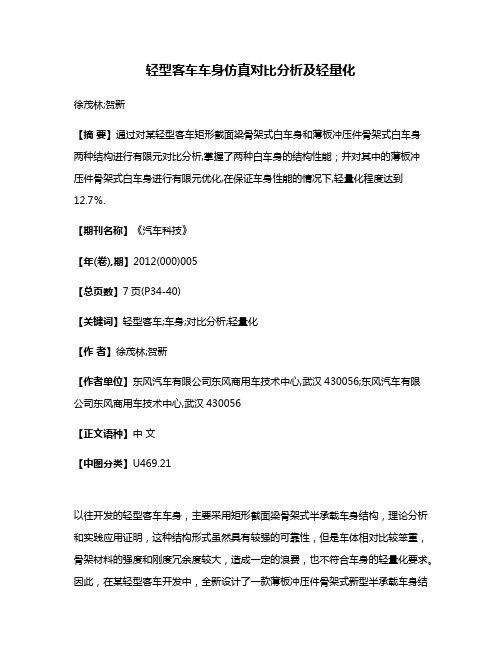
轻型客车车身仿真对比分析及轻量化徐茂林;贺新【摘要】通过对某轻型客车矩形截面梁骨架式白车身和薄板冲压件骨架式白车身两种结构进行有限元对比分析,掌握了两种白车身的结构性能;并对其中的薄板冲压件骨架式白车身进行有限元优化,在保证车身性能的情况下,轻量化程度达到12.7%.【期刊名称】《汽车科技》【年(卷),期】2012(000)005【总页数】7页(P34-40)【关键词】轻型客车;车身;对比分析;轻量化【作者】徐茂林;贺新【作者单位】东风汽车有限公司东风商用车技术中心,武汉430056;东风汽车有限公司东风商用车技术中心,武汉430056【正文语种】中文【中图分类】U469.21以往开发的轻型客车车身,主要采用矩形截面梁骨架式半承载车身结构,理论分析和实践应用证明,这种结构形式虽然具有较强的可靠性,但是车体相对比较笨重,骨架材料的强度和刚度冗余度较大,造成一定的浪费,也不符合车身的轻量化要求。
因此,在某轻型客车开发中,全新设计了一款薄板冲压件骨架式新型半承载车身结构,经初步分析判断,这种车身重量比传统矩形截面梁骨架式车身要轻,能实现一定程度的轻量化设计要求。
但是,这款车身结构能否满足整车的安全性能要求,需要与传统矩形截面梁骨架式车身结构进行仿真对比分析验证;是否还有轻量化的空间,需要进行仿真优化分析。
基于此,本文通过对轻型客车两种白车身结构——矩形截面梁骨架式白车身(传统结构)和薄板冲压件骨架式白车身(新型结构)进行有限元仿真对比计算分析,验证薄板冲压件骨架式白车身的各项性能。
并且,在保证白车身满足结构强度、刚度以及振动特性的情况下,对薄板冲压件骨架式车身结构进行轻量化分析。
本文所用软件为Altair HyperWorks 7.0有限元分析软件。
1 矩形截面梁与薄板冲压件骨架式白车身仿真对比分析1.1 结构仿真对比分析方法概述1.1.1 分析对象及分析流程以某轻型客车为目标车型进行,外廓尺寸为:长6 090 mm×宽2 040 mm×高 2 620 mm,“骨架+蒙皮”的结构形式,半承载式车身。
- 1、下载文档前请自行甄别文档内容的完整性,平台不提供额外的编辑、内容补充、找答案等附加服务。
- 2、"仅部分预览"的文档,不可在线预览部分如存在完整性等问题,可反馈申请退款(可完整预览的文档不适用该条件!)。
- 3、如文档侵犯您的权益,请联系客服反馈,我们会尽快为您处理(人工客服工作时间:9:00-18:30)。
的结构形 式 , 承载 式车身 。 半 分析 对象 包括该 客车 的
两 种 结构 : 形截 面梁 骨架式 白车 身 ( 矩 以下 简 称 “ 车 身 1 , 图 1所 示 ) 薄板 冲压件 骨 架式 白车 身 ( ”如 和 以
下 简 称 “ 身 2 图 2所 示 ) 车 ”如 。
截面 梁 骨 架式 车 身结 构进 行 仿 真对 比分析 验 证 ; 是
Ab t a t B n t e e n to r c a g l rb a s e eo o y i i n h e tlsa ig s eeo o y i sr c : y f i l me tmeh d, t n u a e m k lt n b d n wh t a d s e tmea t mp n k ltn b d n i e e e w i f o e l h u e e a ay ie .o t e sr cu a e o ma c ft e t o y i i a r s e T e h e h t o n i t b s w r n l ss d S h t t r lp r r n e o h wo b d n wh t w s ga p d; h n s e t e g u f e me a tmp n k lt n b d n w i a p i z d b n t lme t to n t e c s fa s rn o y p r r a c , t l a i g s eeo o y i h t w s o t s e mi y f i ee n h d i h a e o s u i g b d e o e i e me f m n e t e b d ’ ih weg t e e r a h d 27 . h o y Sl t i h v l e c e 1 .% g l Ke r s l h u ; o y;o a a ie a ay i ;ih w ih n l ss y wo d : g t s b d c mp r t n lss l t eg t ay i i b v g a
否还 有轻 量化 的空 间 , 需要进行 仿真优 化 分析 。 基 于 此 .本 文 通 过 对 轻 型 客 车 两 种 白车 身 结
构 — — 矩 形 截 面 梁 骨 架 式 白 车 身 ( 统 结 构 ) 薄 板 传 和
对 比分析流程 包括 有 限元模 型建 立、 力对 比、 应 模 态 对 比等 , 图 3所 示。 如
轻量 化 的 目标 是使 材 料 分布 于合 适 的位 置 , 但 是充 分考虑 轻型 客车 制造工 艺特 点 ,车 身各部 分 内 部 的厚度 基本保 持一 致。 结合前 面 的应力 分析结 果
和 灵 敏 度 分 析 结 果 ,有 针 对 性 的 确 定 了轻 量 化 各 部
件 集合 , 以及具 体 的轻量 化对 象 , 并对 车身质 量 变化
62 1 .1 06 9 .2 O
O 97 4 .9
1 侧 窗 纵 梁 0 1 l 上车 门框
1 . 0 1 . 5
09 . 1 l 2
-.6 75 7 29 0 .3
75 6 . 7 39 6 .0
根据 图 l 1各 部 位 频 率 灵 敏 度 的 分 析 结 果 可
Co pa a i e Ana y i nd Li ht i htAna y i fLi htBu d m r tv l ssa g weg l sso g s Bo y
XU Ma — i HE Xi ol n, n
( n fn o Do ge gC mmeca Ve il e h ia C ne f L, u a 4 0 5 C ia ril hceT c nc l e tro DF W h n 3 0 6, hn )
知 , 身 各 部件 变化 对 车 身 模 态 的 变 化 关 系 , 利 车 有 于 更好 的通 过 材 料厚 度 变 化来 控 制 车 身模 态 。 车
门 总 成 、 围 竖 梁 、 盖 骨 架 接 头 及 蒙 皮 等 截 面 厚 侧 顶
/H/ 州 趟 z . .
加
m
O
减 少低 频 共 振 。
变载荷 而减 少车 体 变形 、减 轻疲 劳破 坏有 较大 的好 处: 车身 的应 力水平 较高 , 分发挥 了车 身材料 的利 充 用率 。
24 轻量 化仿 真优化 分析 结论 .
通 过 利 用 灵 敏 度 轻 量 化 优 化 方 法 , 薄 板 冲 压 件
以往开 发 的轻 型客 车车 身 ,主要 采用矩 形截 面 梁骨 架式半 承载 车身 结构 ,理论 分析 和实践 应用 证 明, 这种结 构形 式虽 然具有较 强的可靠 性 , 是 车体 但 相 对 比较 笨重 , 骨架 材料 的强度 和 刚度 冗 余度较 大 , 造成 一定 的浪 费 ,也 不符 合车 身 的轻量化 要 求。 因 此, 在某 轻型 客车开 发 中 , 全新 设计 了一 款薄板 冲压 件 骨架 式新 型半承 载车 身结构 , 初步 分析 判断 , 经 这 种 车 身重 量 比传 统矩 形 截 面梁 骨 架 式车 身 要轻 , 能 实现 一定程 度 的轻量 化设计 要 求。 但是 , 款车 身结 这 构能 否满 足整 车的安 全性 能要 求 ,需 要与传 统矩 形
图 1 各 部位 频 率 灵 敏 度 柱 状 图 1
3 ・ 8
白车身综 合性 能 ,还 需 要对轻 量化 后 的 白车身进 行
・
风[ AE学会专栏
从 弯扭 工况 下 的计 算 分析可 以得 出 ,轻量化 后
汽 车科技第5 02 月 期21 年9
85 H , 小 处 于 8 1Hz之 间 , 性 较 好 , 利 .9 z 大 ~0 刚 有
汽车科技第5 02 月 期21 年9
如 加m∞
修 改部 位 轻 量 化 前 厚 度/ m a r 轻 量 化 后 厚 度/ m a r 一 阶灵 敏度 二 阶灵 敏 度
车 门 内板
1
1 . 0
15 . 1 . 5 1 . O O8 .
O8 .
2 39 0.4 1 20 3 2 .9
的车身 的满 足设计 要 求。 车身所 受 的应力 分布 比较
均 匀 , 时 应 力 区 间 的 波 动 范 围较 小 , 车 身 抵 抗 交 同 对
于 避 开 低 频 激 振 频 率 ; 量 化 后 车 身 结 构 刚度 分 轻
布 均 匀 合 理 , 率 间 隔较 大 , 布 较 均 匀 , 利 于 频 分 有
车 门外 板 2 3 4 侧 围竖 梁 顶盖 骨 架 纵 梁 顶盖 骨 架 横 梁
1 . 2 l _ 2 08 . 07 . 1. 2 98 0 - .9 90 1 3 3 .6 2 88 1 .0 - .9 90 1 - .3 32 6
5 6 7
冲压 件 骨架 式 白车身 ( 新型结 构 ) 行有 限 元仿真 对 进 比计 算分析 ,验 证薄板 冲压 件骨 架式 白车 身的各 项 性能 。并且 , 保证 白车身 满足 结构 强度 、 在 刚度 以及
振 动特 性 的情 况下 对 薄 析。
本 文所 用软 件 为 A ti H p r rs . l r y eWok 0有 限元 a 7
收 稿 日期 :0 2 0 — 6 2 1— 7 1
图 1 矩 形 截 面 梁 骨架 式 白车 身
・
3 ・ 4
东风 I S AE学会专
表 4 车 身 各 部分 材料 厚 度 变 化 的 灵敏 度
m
度 的减 小 均 可 使 模 态 频 率 增 加 : 盖 骨 架 纵 、 梁 顶 横 等 材 料厚 度 的增 加 均 可 使 模 态 频 率 下 降 ;地 板 骨 架厚 度 变化 对模 态 频 率 影 响 很 小 :一 二 阶 灵 敏 度
度 正 负 方 向 不 一致 说 明零 件 截 面 厚 度 改 变对 前 两 阶模 态 频 率 影 Ⅱ 向不相 同 , 同 时提 高 它们 有一 定 困
分析软 件 。
1 矩 形 截 面 梁 与 薄 板 冲 压 件 骨 架 式 白 车 身
仿 真 对 比分 析
11 结 构 仿 真 对 比 分 析 方 法 概 述 .
111 分析 对 象及 分析 流程 . .
以 某 轻 型 客 车 为 目标 车 型 进 行 , 廓 尺 寸 为 : 外 长 60 0mm 宽 20 0m X 26 0E ,骨 架 + 皮 ” 9 X 4 B 高 2 l “ m 蒙
8 9
顶 盖 骨架 接 头 车 身 蒙 皮 地 板 骨 架方 形 管
地 板 骨 架 呈方 形 围梁 外 边 轮 包
1 . 5 1 . O 1 . 5
2O . 1 . 0
1 _ 2 O8 . 1 . 2
15 _ 08 .
O 37 4 .7 O
0 97 4 .9
摘 要 : 过 对 某 轻 型 客 车 矩 形截 面 梁 骨 架 式 白车 身和 薄板 ; 件 骨 架 式 白车 身两 种 结 构 进 行 有 限元 对 比分 析 , 握 通 中压 掌 了 两种 白车 身 的结 构 性 能 : 对 其 中 的 薄 板 冲压 件 骨 架 式 白车 身 进 行 有 限 元优 化 , 保 证 车 身性 能 的 情 况 下 , 量 并 在 轻
化 程 度 达 到 1 .%。 27
关键 词 : 型 客车 : 身 ; 比 分 析 量 化 轻 车 对 轻
中 图分 类 号 : 6 .1 U4 92 文 献 标 志码 : A 文 章编 号 : 0 5 2 5 2 2) 5 0 3 — 7 1 0 — 5 0(01 0 — 0 4 0
难。
图1 2 各 部 位 一 阶 灵 敏 度 从 小 到 大 柱 形 图