同步带的设计计算
3轴同步带轮设计计算

3轴同步带轮设计计算随着机械制造技术的不断发展,同步带轮的应用越来越广泛。
在机械传动中,同步带轮是一种重要的传动元件,它能够实现高效、精准的传动效果。
而在同步带轮的设计中,3轴同步带轮设计计算是一项非常重要的工作。
一、3轴同步带轮的概念3轴同步带轮是指在机械传动中,通过三个轴之间的同步带轮来实现传动的一种方式。
其中,同步带轮是一种带齿轮,它通过齿与同步带的齿槽相咬合,从而实现传动的目的。
3轴同步带轮的设计计算是指在设计过程中,通过计算来确定同步带轮的尺寸、齿数、齿距等参数,以确保传动的精度和可靠性。
二、3轴同步带轮的设计计算1.同步带轮的齿数计算同步带轮的齿数是决定传动比的重要参数之一。
在3轴同步带轮的设计中,需要根据传动比的要求来确定同步带轮的齿数。
一般来说,同步带轮的齿数应该尽量多,以提高传动的精度和可靠性。
同时,还需要考虑同步带轮的尺寸和齿距等因素,以确保同步带轮的齿数符合实际应用的要求。
2.同步带轮的齿距计算同步带轮的齿距是指同步带轮上相邻两个齿之间的距离。
在3轴同步带轮的设计中,需要根据传动比和同步带的齿距来确定同步带轮的齿距。
一般来说,同步带轮的齿距应该尽量小,以提高传动的精度和可靠性。
同时,还需要考虑同步带轮的齿数和尺寸等因素,以确保同步带轮的齿距符合实际应用的要求。
3.同步带轮的尺寸计算同步带轮的尺寸是指同步带轮的直径、宽度等参数。
在3轴同步带轮的设计中,需要根据传动比、齿数和齿距等因素来确定同步带轮的尺寸。
一般来说,同步带轮的直径应该尽量大,以提高传动的精度和可靠性。
同时,还需要考虑同步带轮的齿数和齿距等因素,以确保同步带轮的尺寸符合实际应用的要求。
三、3轴同步带轮的应用3轴同步带轮广泛应用于各种机械传动中,如机床、印刷机、包装机、纺织机等。
它具有传动精度高、传动效率高、噪音小、寿命长等优点,能够满足各种复杂的传动要求。
同时,3轴同步带轮的设计计算也是机械制造中的重要工作之一,它能够保证同步带轮的传动效果和可靠性。
同步带长度计算方法

同步带长度计算方法
同步带长度(节线)计算方法是用于计算两个轴之间同步带的长度,
以确保同步带的尺寸适合于两个轴的距离。
同步带是一种用于传递动力的
特殊带形式,通常由橡胶或聚氨酯材料制成,可以用于连接两个轮子或齿轮,使它们以相同的速度旋转。
在进行同步带长度计算之前,需要先确认以下几个参数:
1.中心距离(C):指两个轴心之间的水平距离,通常以毫米为单位。
2.大轮直径(D1):指驱动侧轮子的直径大小,通常以毫米为单位。
3.小轮直径(D2):指被驱动侧轮子的直径大小,通常以毫米为单位。
4.两轮之间的垂直距离(H)(可选):指两个轮子之间的垂直间距,通常以毫米为单位。
计算同步带长度的方法如下:
1.计算有效中心距离(Ce):有效中心距离等于实际中心距离减去两
轮直径之和的一半。
即Ce=(C-(D1+D2))/2
2.计算节线长度(L):节线长度是同步带需要的长度,可通过以下
公式计算:L=2Ce+π√[(D1/2+D2/2)²-H²]。
需要注意的是,使用上述公式时,要确保所使用的单位保持一致,通
常以毫米为单位。
同步带传动类型及及设计计算标准

同步带传动类型及及设计计算标准(GB-T10414¸2-2002同步带轮设计标准) 圆弧齿同步带轮轮齿ArctoothTimingtooth直边齿廓尺寸Dimensionoflineartypepulley1、同步带轮的型式2、齿型尺寸、公差及技术参数3、各种型号同步带轮齿面宽度尺寸表4、订购须知圆弧齿轮传动类型:1)圆弧圆柱齿轮分单圆弧齿轮和双圆弧齿轮。
2)单圆弧齿轮的接触线强度比同等条件下渐开线齿轮高,但弯曲强度比渐开线低。
3)圆弧齿轮主要采用软齿面或中硬齿面,采用硬齿面时一般用矮形齿。
圆弧齿轮传动设计步骤:1)简化设计:根据齿轮传动的传动功率、输入转速、传动比等条件,确定中心距、模数等主要参数。
如果中心距、模数已知,可跳过这一步。
2)几何设计计算:设计和计算齿轮的基本参数,并进行几何尺寸计算。
3)强度校核:在基本参数确定后,进行精确的齿面接触强度和齿根弯曲强度校核。
4)如果校核不满足强度要求,可以返回圆弧齿轮传动的特点:1)圆弧齿轮传动试点啮合传动,值适用于斜齿轮,不能用于直齿轮。
2)相对曲率半径比渐开线大,接触强度比渐开线高。
3)对中心距变动的敏感性比渐开线大。
加工时,对切齿深度要求较高,不允许径向变位切削,并严格控制装配误差。
单圆弧齿轮传动小齿轮的凸齿工作齿廓在节圆以外,齿廓圆心在节圆上;大齿轮的凹齿工作齿廓在节圆内,齿廓圆心略偏於节圆以外(图2单圆弧齿轮传动的嚙合情况)。
由於大齿轮的齿廓圆弧半径p2略大於小齿轮的齿廓半径p1,故当两齿廓转到K点,其公法线通过节点c时,齿便接触,旋即分离,但与它相邻的另一端面的齿廓随即接触,即两轮齿K1﹑K'1、K2﹑K'2﹑K3﹑K'3……各点依次沿嚙合线接触。
因此,圆弧齿轮任一端面上凹﹑凸齿廓仅作瞬时嚙合。
一对新圆弧齿轮在理论上是瞬时点嚙合,故圆弧齿轮传动又常称为圆弧点嚙合齿轮传动。
轮齿经过磨合后,实际上齿廓能沿齿高有相当长的一段线接触。
同步带的设计计算

同步带的设计计算同步带是一种用于传动动力的重要机械元件,广泛应用于机械设备、汽车、航空航天等领域。
其设计计算包括带长、带速、传动比、带宽、转动惯量等方面,下面详细介绍同步带的设计计算。
首先是带长的设计计算。
带长是指同步带在传动过程中所需的长度。
计算带长的步骤如下:1.确定传动轴之间的距离,即轴距。
2.计算滚动圆弧长度,即传动轮的齿数乘以齿距。
3.计算两个滚动圆弧之间的带长,即传动轴之间的距离减去两个滚动圆弧的长度。
4.根据实际使用情况,考虑带的松紧度及连接方式,计算出最终的带长。
接下来是带速的设计计算。
带速是指同步带传动时带子与齿轮之间的线速度。
计算带速的步骤如下:1.确定传动轴之间的距离,即轴距。
2.根据传动比和齿轮参数,计算出齿轮的转速。
3.确定齿轮的直径,根据直径和转速计算出齿轮的线速度。
4.通过判断带速是否符合使用要求,确定同步带的规格和材质。
然后是传动比的设计计算。
传动比是指驱动轮与被驱动轮之间的转速比。
计算传动比的步骤如下:1.确定驱动轮和被驱动轮的参数,包括齿数、模数等。
2.根据齿轮参数,计算出驱动轮和被驱动轮的转速比。
3.通过判断传动比是否满足设计要求,确定同步带的规格和材质。
此外,还需要考虑带宽的设计计算。
带宽是指同步带的宽度,也称为带槽数。
带宽的计算根据传动功率、转速和带的材料强度等参数来进行。
一般来说,带宽的设计应该根据传动功率和转速来选择合适的带宽,同时要考虑带的强度和材料特性。
最后是转动惯量的设计计算。
转动惯量是指同步带在传动过程中所具有的惯性。
转动惯量的计算一般根据同步带和传动轮的几何参数,通过积分计算的方法进行。
转动惯量的设计计算主要是为了优化传动系统的动态特性和传动精度,减少振动和噪音。
综上所述,同步带的设计计算涉及带长、带速、传动比、带宽和转动惯量等方面。
在进行设计计算时,需要考虑传动要求、传动功率、轴距、齿轮参数、带材料强度等因素,以便选择合适的同步带规格和材质,并确保传动系统的可靠性和效率。
同步带选型、计算资料
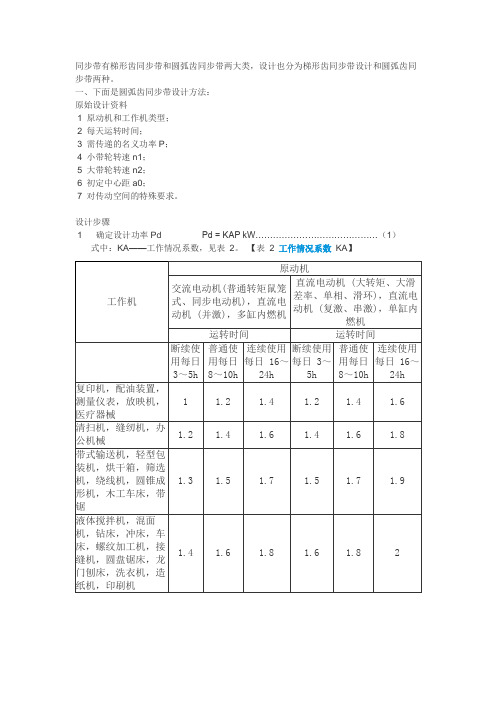
同步带有梯形齿同步带和圆弧齿同步带两大类,设计也分为梯形齿同步带设计和圆弧齿同步带两种。
一、下面是圆弧齿同步带设计方法:原始设计资料1 原动机和工作机类型;2 每天运转时间;3 需传递的名义功率P;4 小带轮转速n1;5 大带轮转速n2;6 初定中心距a0;7 对传动空间的特殊要求。
设计步骤1 确定设计功率Pd Pd = KAP kW (1)式中:KA——工作情况系数,见表2。
【表2 工作情况系数KA】2 选择带型按n1 和Pd,由图1 选择带型。
【参考同步带选型网页】3 计算传动比ii = n1 / n2 (2)4 确定带轮直径4.1 确定带轮齿数Z1、Z2小带轮齿数按Z1≥Zmin 原则确定,Zmin见表3 【参考带轮最小齿数网页】圆弧齿同步带传动小带轮最少齿数zmin可得。
【查看各种同步带轮参数计算公式】5选择带的节线长度LP和确定实际中心距a。
5. 1 计算带的初定节线长度L0L0=2a0+1.57(d2+d1)+ (d2 –d1)2 /4a0 mm (3)式中:a0——初定中心距,mm,由设计任务给定。
5. 2 选择带的标准节线长度LPLP根据L0从同步带现有模具表中查询【3M同步带5M同步带8M同步带14M同步带】5. 3确定实际中心距a中心距近似计算公式为: (4)M=4LP–6.28(d2+d1)mm (5)中心距精确计算公式见同步带节线长计算【参考同步带节线长计算网页】6 确定中心距调整下限I和调整上限S中心距范围为:(a—I)~(a+S)mm。
I和S值见表4。
表4 中心距安装量I 和调整量S7 确定带长系数KL带长系数KL由表5查取。
表5 带长系数K L0.85 0.958 确定啮合齿数系数KZ啮啮合齿数Zm由式(6)计算:Zm =ent(0.5–(d2 −d1 )/6a )Z1 (6)啮合齿数系数KZ 由式(7)确定:Zm≥6,KZ=1Zm<6,KZ=1–0.2(6–Zm) (7)9 确定带的基本额定功率P0各带型的最小宽度推荐用基本额定功率P0圆弧齿3M同步带基准带宽6mm的基本额定功率P0圆弧齿5M同步带基准带宽9mm的基本额定功率P0圆弧齿8M同步带基准带宽20mm的基本额定功率P0圆弧齿14M同步带基准带宽40mm的基本额定功率P0圆弧齿20M同步带基准带宽115mm的基本额定功率P010 带的额定功率Pr带的额定功率按式(3)计算: Pr=KLKZKWP0 kW (8)式中:KW—带宽系数KW=( bs/ bs0 )1.14 (9)11 确定带和带轮的宽度按Pd≤Pr 原则选择带的宽度bs,则 (10)式中:b s0 见下表bs0 6 9 20 40 115 按计算结果选择相对应的常见宽度【同步带常见宽度表】,并确定带轮的齿面宽度及总宽度。
同步带传动设计计算

同步带传动设计计算一、同步带基础知识:同步带传动是一种特殊的带传动,带的工作表面做成齿形与带轮的齿形相吻合,带和带轮主要靠啮合进行传动。
1)同步带分类:(1)按齿形分:同步带分为梯形齿和圆弧齿两大类。
目前梯形齿同步带应用较广,圆弧齿同步带因其承载能力和疲劳寿命高于梯形齿而应用日趋广泛。
(2)按结构分:同步带分为单面和双面同步带两种形式。
双面同步带按齿的排列不同又分为对称齿双面同步带(DA型)和交错齿双面同步带(DB型)两种。
2)常用的梯形齿同步带齿形有周节制和模数制两种。
我国规定梯形齿同步带采用周节制,周节制梯形齿同步带称为标准同步带。
周节制同步带的主要参数是节距Pb。
节距Pb是在规定的张紧力下,同步带纵向截面上相邻两齿在节线上的对称距离。
(注:同步带节线长度Lp=Pb*z)标准同步带(梯形齿)按节距大小又分为七类:MXL(2.032)一最轻型;XXL(3.175)一超轻型;XL(5.080)一特轻型;L(9.525)一轻型;H(12.700)一重型;XH(22.225)一特重型;XXH(31.750)一超重型。
同步带的标记方法:如梯形齿同步带的标记有带长代号、带型、带宽代号和标准号组成,举例:450 H100 GB/T 10414 表示:带长代号450,节线长1143mm;带型H(重型),节距为12.7mm;带宽代号100,带宽为25.4mm; GB/T10414为标准号。
模数制梯形齿同步带以模数m为基本参数(模数m=Pb/π),模数系列为1.5、2.5、3、4、5、7、10,齿形角2β=40°,其标记为:模数x齿数x宽度。
例如:橡胶同步带2x45x25表示模数为2、齿数z=45、带宽bs=25mm。
同步带属于标准件,同步带的材料主要有橡胶和聚氨酯(TTBU)两种。
设计选用时参考相关产品样本从从同步带长度系列中选择标准长度尺寸,带宽的选择经计算后从宽度系列中选用或按使用要求进行裁剪。
同步带长度节线计算方法

同步带长度节线计算方法
1.确定带长计算方式:根据传动装置类型和实际工作条件,选择适合
的带长计算方式。
主要有以下几种方法:
-最小中心距法:根据最小中心距、传动比和齿数计算带长。
-链轮法:根据链轮的齿数和实际中心距计算带长。
-综合法:结合实际工作条件,综合考虑中心距、弹性调整量等因素
计算带长。
2.确定最小中心距:根据传动装置的型号、带轮的齿数和模数等参数,计算最小中心距。
最小中心距是指同步带两个相邻齿轮之间的最小距离。
3.确定传动比:根据实际工作条件,计算传动比。
传动比是指两个相
邻齿轮的齿数比值。
4.计算带长:选择合适的带长计算方法,根据最小中心距和传动比计
算同步带的带长。
带长一般采用没有张紧装置时,绕两个齿轮的围长。
5.计算转速比:根据传动比计算转速比。
转速比是指驱动轴和被动轴
的转速之比。
6.确定多带速比:根据实际工作条件和带轮的齿数,计算多带速比。
多带速比是指同步带上多个带轮之间的转速比。
7.校核带轮和带长:根据计算结果校核带轮的选型和带长的选择是否
符合工作要求。
以上就是同步带长度节线的计算方法,通过计算可以确定同步带的带长、传动比、转速比和多带速比等参数,从而保证传动装置的正常工作。
同步带设计计算

1、
确定设计时的必
要条件
1.1机械种类
1.2传递动力
1.3负载变动情况1.4日工作时间
1.5小带轮的转速1.6旋转比
1.7暂定轴间距
1.8带轮直径上限1.9其他使用条件
2.1、计
算设计动
力
MXL/XL/H
/H/S*M/M
设计动力
Pd=传动
动力Pt*M
M为过负
载系数
过负载系
数
Ks=Ko+Kr
+KiKo
Ko:负载
补偿系数
Kr:旋转
比补偿系
数
Ki:惰轮
补偿系数
2.2、计
算设计动
力 P*M系
过负载系
数
Ks=Ko+Ki
+Kr+Kh
Kh:运转
时间的补
偿系数
3、查表
选型
4、大小
带轮的齿
数、节线
长、轴间
旋转比
确定同步带选型的步骤
传动比i小带轮齿数大带轮齿数
1.6666671220 Lp'C'大带轮直径Dp
20013020
C Lp Dp
84.7856422020
的步骤
3.15
1.5
1.5
0.1
4.1
1
小带轮直径dp
12
dp b
12339.52。
同步带的长度计算方法

同步带的长度计算方法
方法一:使用带轮直径和中心距计算同步带长度。
步骤1:确定带轮直径,通常使用两个带轮的直径之和作为计算的参考值。
步骤2:确定中心距,即两个带轮之间的距离。
步骤3:计算同步带的长度,可以根据下面的公式进行计算:
同步带长度=(π/2)×(带轮1直径+带轮2直径)+2×中心距
例如,带轮1的直径为200mm,带轮2的直径为300mm,中心距为500mm,则同步带长度为:
方法二:使用带的类型和中心距计算同步带长度。
步骤1:确定带的类型,例如HTD型、STD型等。
步骤2:确定中心距。
步骤3:根据带的类型和中心距查找相应的同步带长度计算表,表中会提供不同类型和不同中心距下的同步带长度。
例如,HTD型同步带,中心距为500mm,在HTD型同步带长度计算表中查找,找到中心距为500mm下的同步带长度为1802mm。
需要注意的是,同步带的长度计算方法可能会有一定的误差,因为同步带的伸长和收缩以及带材的松紧度等因素都会对长度产生影响。
因此,在实际应用中,可能需要根据具体情况进行适当的修正和调整。
另外,还可以使用CAD软件或专业的同步带设计软件进行计算和绘制。
同步带及带轮设计计算

(4)确定带轮的节圆直径 d1, d2
小带轮节圆直径: d1 Pb z1 / 9.52512 / 3.14 36.38mm 大带轮节圆直径: d2 Pb z2 / 9.525 31/ 3.14 93.99mm
(5)验证带速 v
同步带轮: z1 12 , d1 36.38mm , z2 31 , d2 93.99mm
传动中心距 a:精确计算 a 83.07mm
订购图纸如下图 2 所示:
图 2 带轮订购图纸
表 1 载荷修正系数 K0 表 2 梯形同步带选型图
表 3 带轮最小许用齿数 表 4 同步带允许最大线速度 表 5 L 型号梯形齿同步带规格、型号、尺寸表
设计任务:
设计一同步带及同步带轮,其传动比为 i 2.6 ,传递功率为:50 ~ 100w 。小带轮的转 速为 n1 1000RPM ,中心距:80mm 左右。设计确定带及带轮的订购型号。(小带轮有一
个5mm 的孔)
设计计算如下所示:
(1)确定同步带传动的设计功率 Pd
Pd K0 Pm
K ④宽度系数
w
:
Kw
( bs bso
)1.14
⑤额定功率: Pr
K z KwP0
K
z
P0
bs bso
1.14
1.14
P 根据设计要求, d
Pr
。故带宽 bs
bs 0
Pd K z P0
8.20mm 。
根据表 7 可已选择 bs 12.7mm 的同步带,其宽度代号为:050。
同步带的长度计算公式及出现损坏的解决办法

同步带的长度计算公式如下:
lb= ((df+ dm) 1.5708 ) + (2 lfm)
其中lb是同步带的长度,df是大同步带轮的直径,dm是小同步带轮的直径,lfm是大同步带轮的中心和小同步带轮中心的距离。
从上述同步带长度的计算公式可以看出同步带轮的直径对于同步带的长度有一定的影响。
而同步带轮的直径和同步带轮的型号还有尺寸有关。
所以同步带轮的型号会对同步带的长度有一定的影响。
同步带出现损坏的解决方案
1、同步带在使用的过程中不可以扭结同步带,当安装宽同步带或者是大同步带轮的时候,增加同步带轮的直径或者是宽同步带,需要去除存在的异物,并且进行正确的张紧。
2、同步带在使用的过程中需要进行正确的张紧,当安装宽度更大,动力传输更高的同步带的时候,应该增加同步带的尺寸或者是同步带轮的尺寸。
需要检查一下同步带的型号,并且在必要的时候进行及时的更换。
3、如果同步带轮出现严重的磨损的话则需要将同步带轮及时进行更换。
4、如果同步带轮没有办法进行轴的对齐,就需要更换同步带轮的法兰,并且加固轴承或者
是机箱。
5、同步带如果出现纵向的裂开就需要立即更换法兰同步带轮,并且重新对齐同步带轮还有轮轴,并且更正同步带传动系统的张紧力,去除表面的异物,安装防护罩。
重新检查一下切割装置还有同步带的导向装置。
同步带选型计算公式

同步带选型计算公式1.速比计算公式:速比是指同步带驱动轴的转速之比。
同步带选型时,首先需要确定所需的速比。
速比计算公式如下:速比=高速轴转速/低速轴转速2.传动比计算公式:传动比是指同步带传动装置中从输入轴到输出轴的转速比。
传动比计算公式如下:传动比=高速轴转速/低速轴转速3.中心距计算公式:中心距是指同步带驱动轮轴与从动轮轴之间的轴心距离。
中心距计算公式如下:中心距=√((最小中心距)^2+(节圆直径之和/2)^2)4.节圆直径计算公式:节圆直径是指同步带的实际外径。
节圆直径计算公式如下:节圆直径=节圆直径计算参数×模数5.给定转速下的带速计算公式:带速是指同步带在工作状态下的线速度。
给定转速下的带速计算公式如下:带速=π×节圆直径×转速/606.理论节圆直径计算公式:理论节圆直径是指同步带理论上的外径。
理论节圆直径计算公式如下:理论节圆直径=最小中心距×2+节圆直径之和7.弯曲张力计算公式:弯曲张力是指同步带在传动区域受到的张力。
弯曲张力计算公式如下:弯曲张力=(Cf+Ct)/28.载荷系数计算公式:载荷系数是指同步带所能承受的最大载荷。
载荷系数计算公式如下:载荷系数=弯曲张力/拉伸伸长力9.接触角计算公式:接触角是指同步带与驱动轮接触时的沿圆周方向的角度大小。
接触角计算公式如下:接触角=180°-α10.张紧力计算公式:张紧力是指用于保证同步带与传动装置正常工作所需的松紧程度的力量。
张紧力计算公式如下:张紧力=(拉紧力系数×动力(马力))/(带速×功率因数)以上是同步带选型计算中常用的公式,通过这些公式,可以根据不同传动系统的要求和参数进行合理的同步带选型和设计。
同步皮带计算方式

同步皮帶計算方式(原创实用版)目录1.概述同步皮带的概念和作用2.介绍同步皮带的计算方法3.同步皮带的选用和安装注意事项4.总结同步皮带的计算方式正文一、同步皮带的概念和作用同步皮带,又称同步带或传动带,是一种用于传递动力和同步运动的工业用皮带。
它由橡胶带体、尼龙布层和钢丝芯组成,具有较高的承载能力和良好的传动性能。
同步皮带广泛应用于各种机械设备的传动系统,如机床、汽车、纺织机械等。
二、同步皮带的计算方法1.确定传动比:根据传动系统的设计要求,确定主动轮和从动轮的转速比。
2.计算最大传动功率:根据机械设备的动力需求,计算同步皮带的最大传动功率。
公式为:Pmax = (2π× n1 × n2 × T) / η,其中 Pmax 为最大传动功率,n1 为主动轮转速,n2 为从动轮转速,T 为同步皮带的张力,η为传动效率。
3.选择合适的皮带宽度和长度:根据最大传动功率和传动比,选择合适的同步皮带宽度和长度。
一般皮带宽度的选取要考虑承载能力、弯曲疲劳和离心力等因素;皮带长度的选取要考虑传动系统的安装空间和工作环境。
4.校核皮带的弯曲疲劳强度:根据皮带的宽度、长度和最大传动功率,校核皮带的弯曲疲劳强度是否满足设计要求。
公式为:σ = Pmax / (w ×L),其中σ为弯曲疲劳强度,w 为皮带宽度,L 为皮带长度。
三、同步皮带的选用和安装注意事项1.选用高质量的同步皮带:选择具有良好承载能力、高传动效率和较长使用寿命的同步皮带。
2.安装时注意皮带的张紧力:同步皮带在安装过程中,要保持适当的张紧力,以保证传动精度和减少皮带的磨损。
3.避免皮带在安装过程中受到损伤:在安装同步皮带时,要避免皮带受到切割、折弯等损伤,以免影响传动性能。
四、总结同步皮带的计算方式同步皮带的计算方式主要包括确定传动比、计算最大传动功率、选择合适的皮带宽度和长度以及校核皮带的弯曲疲劳强度等步骤。
林——同步带传动设计计算

要求条件符号单位传动及负载重量m kg移动速度V0m/min 初选带轮直径d0m转速n0rpm piπ重力加速度g N/kg 摩擦系数ɳ摩擦力f N传递功率P kw载荷修正系数K0设计功率P d kw带型号节距P b mm传动比i同步带轮1主,齿数Z1同步带轮2从,齿数Z2初步轴间距a0mm带长(节线长度)L0mm3M型号带节线长度L p mm带齿数ZM mm实际中心距a mm安装量I mm调整量S mm带长系数K L啮合齿数Z m啮合齿数系数K Z带的基本额定功率P0kw带的基本宽度b s0mm要求带宽b s mm标准宽带b f mm带速度V1m/s 紧边张力F1N松边张力F2N矢量相加修正量K F压轴力F Q N综上:同步带型号选择为日本公式及数据来源数值10.000由原定400mm/s转24m/min 24.000由原定19.10mm转0.019m 0.019n 0=V 0/(π*d 0)399.9713.1429.8000.500f=ɳmg 49.000P=fV 00.020表14.1-55 1.400P d =K 0P0.027图14.1-16,带型取3M3.0001.000表14.1-69a,Z 1≥Z min ,取Z 1=20,d 1=19.10mm 20.000Z 2=Z 1*i,d 2=19.10mm 20.0000.7(d 1+d 2)≦a 0≦2(d 1+d 2)范围27~76L 0=2a 0+π(d 1+d 2)/2+(d 2-d 1)²/(4a 0)937.099表14.1-66,取L p =936936.000Z=L 0/P b312.000M=4L p -2π(d 2+d 1)3504.000a=[M+√(M²-32(d 2-d 1)²)]/16438.000a min =a-I,表14.1-74,I=1.02 1.020a max =a-S,表14.1-74,S=0.760.760表14.1-73,取K L =1.201.200Z m =ent(0.5-(d2-d1)/6a)Z 1,ent指取整10.000Z m ≥6时,K z =1,Z m <6时,K z =1-0.2(6-Z m ) 1.000由转速n 0和主动轮齿数Z 1,在表14.1-69a选取0.030由表14.1-70,3M带型取b s0=66.0005.140表14.1-65,且b f ≥b s ,取b f =1010.000V 1=(π*d 1*n 1)/(60*1000)0.400F 1=1250P d /V 185.756P 14.10ds 0s b b P K K Z LF2=250P d/V117.151图14.1-17,KF=0.990.990F Q=K F(F1+F2)101.879为日本三星100S3M936,同步带轮选择米思米型号:HTPB20S3M100-A-H4齿数带轮形状材质表面处理轴孔规格。
圆弧齿同步带设计计算

计算项目单位公式及数据K A按表选取传递的功率PKW 设计功率P dkw P d =K A P 带型:节距p b 或模数mmm 根据功率和转速选取小带轮齿数z 1z 1≥z min 大带轮齿数z 2z 2小带轮直径d 1mm 小带轮转速n 1r/min 带速v m/s 传动比i大带轮直径d 2mm minmax 选取:初定带的节线长度L 0p 及其齿数z b mm 初定节线长L p mm 按表选取小带轮包角α1:°9.275178311中心距可调内侧调整量i 1外侧调整量s 中心距范围中心距不可调小带轮啮合齿数z m 初定中心距a 0mm 实际中心距a mmd _1=(p _b ×z _1)/πv =(〖π×d 〗_1×n i =z _2/z _1 ≤10d _2=(p _b ×z _2)/π=i ×z0.7(d _1+d _2)<a _0<2(d _1+L _0p ≈2a _0+π/2 (d _1+d _2 )+〖(d _2−d_1)〗^2/(4a _0 )inv α_1/2=(L _p −πd a ≈a _0+(L _p −L _0P )/a=a _0+(d _2−d _1)/((a −i _1)~(a +s )z _m =ent [z _1/2−(p _b z _1)/(2π^2基准额定功率P 0KW 按表选取基准宽度b s0mm 小带轮啮合齿数系数K z 按表选取圆弧齿带长系数K L根据表选定值mm 计算值根据表选定值矢量相加修正系数K F右图选择作用在轴上的力F r N 带宽b sb _s ≥b _s 0 √(1.14&P _dF _r =K _F p _d /v ×1500当K _A ≥1.3 时F _r =K _F p _d /v ×1155值说明1.4按表选取0.10.143为使传动平稳,尽量选取最小值。
同步带传动的设计计算和使用

同步带传动的设计计算和使用同步带传动是一种新型的机械传动(见图 i).由于它是一种啮合传动因而带和带轮之间i殳有相对滑动,从而使主从轮间的传动达到同步。
同步带传动和 y 带、平带相比具有: (i)传动准确,无滑动,能达到同步传动的目的; (2)传动效率高·一般可达驰蓐;(3)速比范围大允许线速度也高;(1)传递功率范围大。
从几十瓦到几百千瓦;(5)结构紧凑,还适用于乡轴传动等优点。
因此,同步带传动已日益弓『起各方面的注意和重视,并把这种传动应用到各种机械设备上。
相应地设计者要求有一种设计方法来台理地选择同步带传动的各项参数。
笔者根据参加制订同步带传动国家标准讨论和学术活动的体会,提出了同步带传动的设计方法及应注意的问题,以供同步带传动设计者参考直用。
同步带传动的设计准则同步带传动是以带齿与轮齿依敬啮合来传递动力。
达到同步传动的目的。
因此。
在同步带传递扭矩时,带将受拉力作用。
带齿承受剪切,而带齿的工作表面在进八和退出与轮齿啮合的过程中将被磨损。
因此同步带的主要失效形式有如下三种:(1)同步带承载绳 (又称骨架蝇,的疲劳断裂;(2)带齿的剪切破裂:(3)带齿工作表面磨损。
失去原来的形乇I}。
根据试验分析,当同步带绕于带轮时,在所包圆弧内带齿与带轮齿的啮合齿数 z.大于 6时带齿的剪切强度将大干带的抗拉强度。
同时,随着粘附于带齿工作表面上的尼龙包雍层的设置.使带齿的耐磨性有了报大的提高。
因此在同步带正常工作条件下,同步带的主要失效形式是带在变拉力作用下的疲劳断裂所以同步带传动是根据带的抗拉强度作为设计准则来进行设计的。
在 ISb5295 t同步带额定功率与传动中心距的计算,标准中,就是以此为依据提出了带宽为基准宽度的基准额定功率计算公式:Pd (T 一mv')v/100o(kw )式中:Po——某一型号同步带在基准宽度下所能抟递的基准额定功率 ( W )某一型号同步带在基准宽度下的许用工作拉力 (见表1) (Ⅳ)m——某一型号同步带在基准宽度下舳单位长度质量 g/m} v——同步带线速度 (m/s,由公式可知:L为带的许用工作拉力,m 为带在运转过程中由离心力产生的拉力。
同步带齿数计算公式

同步带齿数计算公式
同步带齿数计算公式是用来计算同步带的齿数的公式。
同步带是一种传动方式,通过带子和齿轮传递动力。
在计算同步带齿数时,需要考虑带子的长度、齿距和齿数等因素。
同步带齿数计算公式通常是根据带子长度和齿距来计算的,公式为:齿数=(带子长度/齿距)+1。
这个公式可以用来计算同步带的齿数,从而确定传动比和传动方式。
同时,还可以根据带子长度和齿数来计算齿距,从而确定同步带的参数。
因此,同步带齿数计算公式是同步带传动设计中非常重要的工具。
- 1 -。
同步带长度计算方法
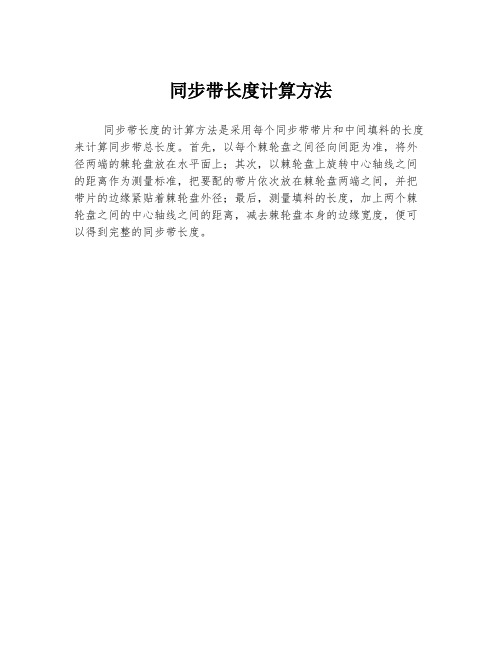
同步带长度计算方法
同步带长度的计算方法是采用每个同步带带片和中间填料的长度来计算同步带总长度。
首先,以每个棘轮盘之间径向间距为准,将外径两端的棘轮盘放在水平面上;其次,以棘轮盘上旋转中心轴线之间的距离作为测量标准,把要配的带片依次放在棘轮盘两端之间,并把带片的边缘紧贴着棘轮盘外径;最后,测量填料的长度,加上两个棘轮盘之间的中心轴线之间的距离,减去棘轮盘本身的边缘宽度,便可以得到完整的同步带长度。
同步带的设计计算
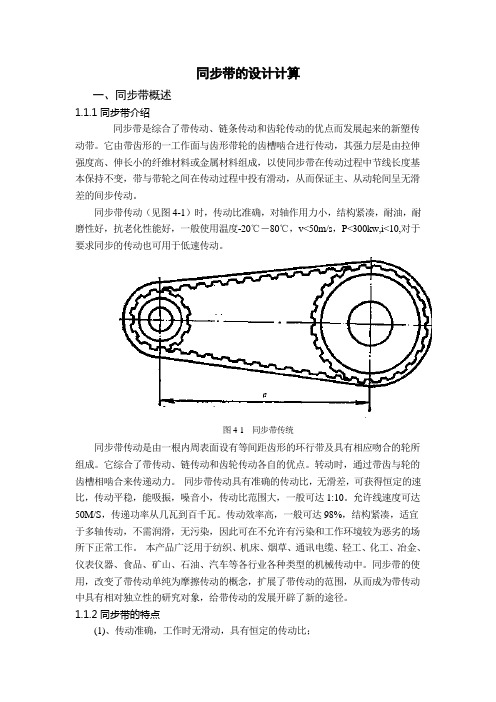
同步带的设计计算一、同步带概述1.1.1同步带介绍同步带是综合了带传动、链条传动和齿轮传动的优点而发展起来的新塑传动带。
它由带齿形的一工作面与齿形带轮的齿槽啮合进行传动,其强力层是由拉伸强度高、伸长小的纤维材料或金属材料组成,以使同步带在传动过程中节线长度基本保持不变,带与带轮之间在传动过程中投有滑动,从而保证主、从动轮间呈无滑差的间步传动。
同步带传动(见图4-1)时,传动比准确,对轴作用力小,结构紧凑,耐油,耐磨性好,抗老化性能好,一般使用温度-20℃―80℃,v<50m/s,P<300kw,i<10,对于要求同步的传动也可用于低速传动。
图4-1 同步带传统同步带传动是由一根内周表面设有等间距齿形的环行带及具有相应吻合的轮所组成。
它综合了带传动、链传动和齿轮传动各自的优点。
转动时,通过带齿与轮的齿槽相啮合来传递动力。
同步带传动具有准确的传动比,无滑差,可获得恒定的速比,传动平稳,能吸振,噪音小,传动比范围大,一般可达1:10。
允许线速度可达50M/S,传递功率从几瓦到百千瓦。
传动效率高,一般可达98%,结构紧凑,适宜于多轴传动,不需润滑,无污染,因此可在不允许有污染和工作环境较为恶劣的场所下正常工作。
本产品广泛用于纺织、机床、烟草、通讯电缆、轻工、化工、冶金、仪表仪器、食品、矿山、石油、汽车等各行业各种类型的机械传动中。
同步带的使用,改变了带传动单纯为摩擦传动的概念,扩展了带传动的范围,从而成为带传动中具有相对独立性的研究对象,给带传动的发展开辟了新的途径。
1.1.2同步带的特点(1)、传动准确,工作时无滑动,具有恒定的传动比;(2)、传动平稳,具有缓冲、减振能力,噪声低;(3)、传动效率高,可达0.98,节能效果明显;(4)、维护保养方便,不需润滑,维护费用低;(5)、速比范围大,一般可达10,线速度可达50m/s,具有较大的功率传递范围,可达几瓦到几百千瓦;(6)、可用于长距离传动,中心距可达10m以上。
- 1、下载文档前请自行甄别文档内容的完整性,平台不提供额外的编辑、内容补充、找答案等附加服务。
- 2、"仅部分预览"的文档,不可在线预览部分如存在完整性等问题,可反馈申请退款(可完整预览的文档不适用该条件!)。
- 3、如文档侵犯您的权益,请联系客服反馈,我们会尽快为您处理(人工客服工作时间:9:00-18:30)。
一、同步带概述同步带介绍同步带是综合了带传动、链条传动和齿轮传动的优点而发展起来的新塑传动带。
它由带齿形的一工作面与齿形带轮的齿槽啮合进行传动,其强力层是由拉伸强度高、伸长小的纤维材料或金属材料组成,以使同步带在传动过程中节线长度基本保持不变,带与带轮之间在传动过程中投有滑动,从而保证主、从动轮间呈无滑差的间步传动。
同步带传动(见图4-1)时,传动比准确,对轴作用力小,结构紧凑,耐油,耐磨性好,抗老化性能好,一般使用温度-20℃―80℃,v<50m/s,P<300kw,i<10,对于要求同步的传动也可用于低速传动。
图4-1 同步带传统同步带传动是由一根内周表面设有等间距齿形的环行带及具有相应吻合的轮所组成。
它综合了带传动、链传动和齿轮传动各自的优点。
转动时,通过带齿与轮的齿槽相啮合来传递动力。
同步带传动具有准确的传动比,无滑差,可获得恒定的速比,传动平稳,能吸振,噪音小,传动比范围大,一般可达1:10。
允许线速度可达50M/S,传递功率从几瓦到百千瓦。
传动效率高,一般可达98%,结构紧凑,适宜于多轴传动,不需润滑,无污染,因此可在不允许有污染和工作环境较为恶劣的场所下正常工作。
本产品广泛用于纺织、机床、烟草、通讯电缆、轻工、化工、冶金、仪表仪器、食品、矿山、石油、汽车等各行业各种类型的机械传动中。
同步带的使用,改变了带传动单纯为摩擦传动的概念,扩展了带传动的范围,从而成为带传动中具有相对独立性的研究对象,给带传动的发展开辟了新的途径。
同步带的特点(1)、传动准确,工作时无滑动,具有恒定的传动比;(2)、传动平稳,具有缓冲、减振能力,噪声低;(3)、传动效率高,可达,节能效果明显;(4)、维护保养方便,不需润滑,维护费用低;(5)、速比范围大,一般可达10,线速度可达50m/s,具有较大的功率传递范围,可达几瓦到几百千瓦;(6)、可用于长距离传动,中心距可达10m以上。
同步带传动的主要失效形式在同步带传动中常见的失效形式有如下几种:(1)、同步带的承载绳断裂破坏同步带在运转过程中承载绳断裂损坏是常见的失效形式。
失效原因是带在传递动力过程中,在承载绳作用有过大的拉力,而使承载绳被拉断。
此外当选用的主动捞轮直径过小,使承载绳在进入和退出带抡中承受较大的周期性的弯曲疲劳应力作用,也会产生弯曲疲劳折断(见图4-2)。
图4-2 同步带承载绳断裂损坏(2)、同步带的爬齿和跳齿根据对带爬齿和跳齿现象的分析,带的爬齿和眺齿是由于几何和力学两种因素所引起。
因此为避免产生爬齿和跳齿,可采用以下一些措施:1、控制同步带所传递的圆周力,使它小于或等于由带型号所决定的许用圆周力。
2、控制带与带轮间的节距差值,使它位于允许的节距误差范围内。
3、适当增大带安装时的初拉力开。
,使带齿不易从轮齿槽中滑出。
4、提高同步带基体材料的硬度,减少带的弹性变形,可以减少爬齿现象的产生。
(3)、带齿的剪切破坏带齿在与带轮齿啮合传力过程中,在剪切和挤压应力作用下带齿表面产生裂纹此裂纹逐渐向齿根部扩展,并沿承线绳表面延件,直至整个带齿与带基体脱离,这就是带齿的剪切脱落(见图4-3)。
造成带齿剪切脱落的原因大致有如下几个:1、同步带与带轮问有较大的节距差,使带齿无法完全进入轮齿槽,从而产生不完全啮合状态,而使带齿在较小的接触面积上承受过大的载荷,从而产生应力集中,导致带齿剪切损坏。
2、带与带轮在围齿区内的啮合齿数过少,使啮合带齿承受过大的载荷,而产生剪切破坏。
3、同步带的基体材料强度差。
为减少带齿被剪切,首先应严格控制带与带轮间的节距误差,保证带齿与轮齿能正确啮合;其次应使带与带轮在围齿区内的啮合齿数等于或大于6,此外在选材上应采用有较高勿切韧挤压强度的材料作为带的基体材料。
图4-3 带齿的剪切破坏(4)、带齿的磨损带齿的磨损(见图4-4)包括带齿工作面及带齿齿顶因角处和齿谷底部的廓损。
造成磨损的原因是过大的张紧力和忻齿和轮齿间的啮合干涉。
因此减少带齿的磨损,应在安装时合理的调整带的张紧力;在带齿齿形设计时,选用较大的带齿齿顶圆角半径,以减少啮合时轮齿的挤压和刮削;此外应提高同步带带齿材料的耐磨性。
图4-4 带齿磨损(5)、同步带带背的龟裂(图4—5)同步带在运转一段时期后,有时在带背会产生龟裂现象,而使带失效。
同步带带背产生龟裂的原因如下,1、带基体材料的老化所引起;2、带长期工作在道低的温度下,使带背基体材料产生龟裂。
图4-5 同步带带背龟裂防止带背龟裂的方法是改进带基体材料的材质,提向材料的耐寒、耐热性和抗老化性能,此外尽量避免同步带在低温和高温条件下工作。
同步带传动的设计准则据对同步带传动失效形式的分析,可知如同步带与带轮材料有较高的机械性能,制造工艺合理,带、轮的尺寸控制严格,安装调试也正确,那么许多失效形式均可避免。
因此,在正常工作条件下,同步带传动的主要失效形式为如下三种;(1)同步带的承载绳疲劳拉断;(2同步带的打滑和跳齿;(3)同步带带齿的磨损。
因此,同步带传动的设计淮则是同步带在不打滑情况下,具有较高的抗拉强度,保证承线绳不被拉断。
此外,在灰尘、杂质较多的工作条件下应对带齿进行耐磨性计算。
同步带分类同步带齿有梯形齿和弧齿两类,弧齿又有三种系列:圆弧齿(H系列又称HTD带)、平顶圆弧齿(S系列又称为STPD带)和凹顶抛物线齿(R系列)。
梯形齿同步带梯形齿同步带分单面有齿和双面有齿两种,简称为单面带和双面带。
双面带又按齿的排列方式分为对称齿型(代号DA)和交错齿型(代号DB〕。
梯形齿同步带有两种尺寸制:节距制和模数制。
我国采用节距制,并根据ISO 5296制订了同步带传动相应标准GB/T 11361~11362-1989和GB/T 11616-1989。
弧齿同步带弧齿同步带除了齿形为曲线形外,其结构与梯形齿同步带基本相同,带的节距相当,其齿高、齿根厚和齿根圆角半径等均比梯形齿大。
带齿受载后,应力分布状态较好,平缓了齿根的应力集中,提高了齿的承载能力。
故弧齿同步带比梯形齿同步带传递功率大,且能防止啮合过程中齿的干涉。
弧齿同步带耐磨性能好,工作时噪声小,不需润滑,可用于有粉尘的恶劣环境。
已在食品、汽车、纺织、制药、印刷、造纸等行业得到广泛应用。
同步带传动设计计算1.电机额定输出功率估算=2、确定计算功率电动机每天使用24小时左右,查表4-1得到工作情况系数=。
则计算功率为:3、小带轮转速计算4、选定同步带带型和节距由同步带选型图可以看出,由于在这次设计中功率转速都比较小,所以带的型号可以任意选取,现在选取H型带,节距表4-1 工作情况系数看图同步带选型图5、选取主动轮齿数查表4-2知道小带轮最小齿数为14,现在选取小带轮齿数为41。
6小带轮节圆直径确定=表4-2 小带轮最小齿数表7、大带轮相关数据确定由于系统传动比为,所以大带轮相关参数数据与小带轮完全相同。
齿数,节距8、带速v的确定9、初定周间间距根据公式得现在选取轴间间距为600mm。
10、同步带带长及其齿数确定=()==11、带轮啮合齿数计算有在本次设计中传动比为一,所以啮合齿数为带轮齿数的一半,即=20。
12、基本额定功率的计算查基准同步带的许用工作压力和单位长度的质量表4-3可以知道=,m=m。
所以同步带的基准额定功率为==表4-3 基准宽度同步带的许用工作压力和单位长度的质量13、计算作用在轴上力==同步带的主要参数1、同步带的节线长度同步带工作时,其承载绳中心线长度应保持不变,因此称此中心线为同步带的节线,并以节线周长作为带的公称长皮,称为节线长度。
在同步带传动中,带节线长度是一个重要参数。
当传动的中心距已定时,带的节线长度过大过小,都会影响带齿与轮齿的正常啮合,因此在同步带标准中,对梯形齿同步带的各种哨线长度已规定公差值,要求所生产的同步带节线长度应在规定的极限偏差范围之内(见表4-4)。
表4-4 带节线长度表2、带的节距Pb如图4-2所示,同步带相邻两齿对应点沿节线量度所得约长度称为同步带的节距。
带节距大小决定着同步带和带轮齿各部分尺寸的大小,节距越大,带的各部分尺寸越大,承载能力也随之越高。
因此带节距是同步带最主要参数.在节距制同步带系列中以不同节距来区分同步带的型号。
在制造时,带节距通过铸造模具来加以控制。
梯形齿标准同步带的齿形尺寸见表4-5。
3、带的齿根宽度一个带齿两侧齿廓线与齿根底部廓线交点之间的距离称为带的齿根宽度,以s表示。
带的齿根宽度大,则使带齿抗剪切、抗弯曲能力增强,相应就能传送较大的裁荷。
图4-2 带的标准尺寸表4-5 梯形齿标准同步带的齿形尺寸4、带的齿根圆角带齿齿根回角半径r的大小与带齿工作时齿根应力集中程度有关t齿根圆角半径大,可减少r齿的应力集中,带的承载能力得到提高。
但是齿根回角半径也不宜过大,过大则使带齿与轮齿啮合时的有效接触面积城小,所以设计时应选适当的数值。
5、带齿齿顶圆角半径八带齿齿项圆角半径八的大小将影响到带齿与轮齿啮合时会否产生于沙。
由于在同步带传动中,带齿与带轮齿的啮合是用于非共扼齿廓的一种嵌合。
因此在带齿进入或退出啮合时,带齿齿顶和轮齿的顶部拐角必然会超于重叠,而产生干涉,从而引起带齿的磨损。
因此为使带齿能顺利地进入和退出啮合,减少带齿顶部的磨损,宜采用较大的齿顶圆角半径。
但与齿根圆角半径一样,齿顶圆角半径也不宜过大,否则亦会减少带齿与轮齿问的有效接触面积。
6、齿形角梯形带齿齿形角日的大小对带齿与轮齿的啮合也有较大影响。
如齿形角霹过小,带齿纵向截面形状近似矩形,则在传动时带齿将不能顺利地嵌入带轮齿槽内,易产生干涉。
但齿形角度过大,又会使带齿易从轮齿槽中滑出,产生带齿在轮齿顶部跳跃现象。
同步带的设计在这里,我们选用梯形带。
带的尺寸如表4-6。
带的图形如图4-3。
表4-6 同步带尺寸图4-3 同步带同步带轮的设计同步带轮的设计的基本要求1、保证带齿能顺利地啮入与啮出由于轮齿与带齿的啮合同非共规齿廓啮合传动,因此在少带齿顶部与轮齿顶部拐角处的干涉,并便于带齿滑入或滑出轮齿槽。
2、轮齿的齿廊曲线应能减少啮合变形,能获得大的接触面积,提高带齿的承载能力即在选探轮齿齿廓曲线时,应使带齿啮入或啮出时变形小,磨擦损耗小,并保证与带齿均匀接触,有较大的接触面积,使带齿能承受更大的载荷。
3、有良好的加了工艺性加工工艺性好的带轮齿形可以减少刀具数量与切齿了作员,从而可提高生产率,降低制造成本。
4、具有合理的齿形角齿形角是决定带轮齿形的重要的力学和几何参数,大的齿形角有利于带齿的顺利啮入和啮出,但易使带齿产生爬齿和跳齿现象;而齿形角过小,则会造成带齿与轮齿的啮合干涉,因此轮齿必须选用合理的齿形角。
同步带轮的设计结果同步带轮用梯形齿,其图形如图4-4。
图4-4 同步带轮结构。