标准铝型材机箱与PCB技术
pcb与金属压合 标准
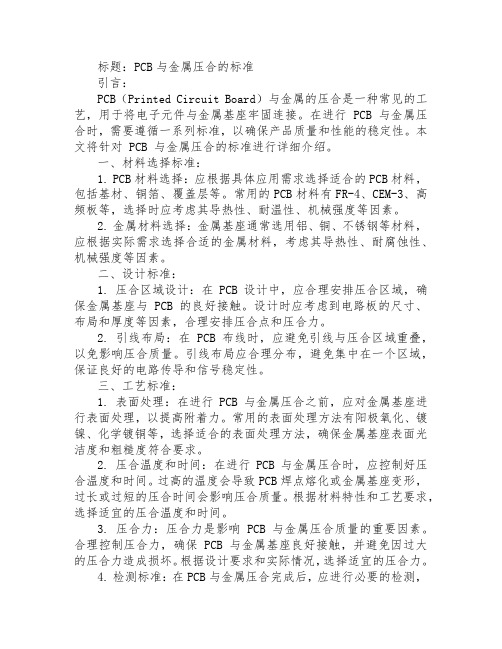
标题:PCB与金属压合的标准引言:PCB(Printed Circuit Board)与金属的压合是一种常见的工艺,用于将电子元件与金属基座牢固连接。
在进行 PCB 与金属压合时,需要遵循一系列标准,以确保产品质量和性能的稳定性。
本文将针对 PCB 与金属压合的标准进行详细介绍。
一、材料选择标准:1. PCB 材料选择:应根据具体应用需求选择适合的PCB 材料,包括基材、铜箔、覆盖层等。
常用的PCB 材料有FR-4、CEM-3、高频板等,选择时应考虑其导热性、耐温性、机械强度等因素。
2. 金属材料选择:金属基座通常选用铝、铜、不锈钢等材料,应根据实际需求选择合适的金属材料,考虑其导热性、耐腐蚀性、机械强度等因素。
二、设计标准:1. 压合区域设计:在 PCB 设计中,应合理安排压合区域,确保金属基座与 PCB 的良好接触。
设计时应考虑到电路板的尺寸、布局和厚度等因素,合理安排压合点和压合力。
2. 引线布局:在 PCB 布线时,应避免引线与压合区域重叠,以免影响压合质量。
引线布局应合理分布,避免集中在一个区域,保证良好的电路传导和信号稳定性。
三、工艺标准:1. 表面处理:在进行 PCB 与金属压合之前,应对金属基座进行表面处理,以提高附着力。
常用的表面处理方法有阳极氧化、镀镍、化学镀铜等,选择适合的表面处理方法,确保金属基座表面光洁度和粗糙度符合要求。
2. 压合温度和时间:在进行 PCB 与金属压合时,应控制好压合温度和时间。
过高的温度会导致PCB 焊点熔化或金属基座变形,过长或过短的压合时间会影响压合质量。
根据材料特性和工艺要求,选择适宜的压合温度和时间。
3. 压合力:压合力是影响 PCB 与金属压合质量的重要因素。
合理控制压合力,确保 PCB 与金属基座良好接触,并避免因过大的压合力造成损坏。
根据设计要求和实际情况,选择适宜的压合力。
4. 检测标准:在PCB 与金属压合完成后,应进行必要的检测,以确保压合质量符合要求。
PCB技术要求及标准

PCB技术要求及作业指导一、目的根据公司现有的设备加工能力并结合IPC标准,规范生产用印刷电路板(PCB)的工艺制作,增加基板定位方式的通用性,更好地提高生产效率及生产灵活性。
二、适用范围适用于公司电力自动化事业部硬件设计管理和PCB基板的工艺设计指导。
三、具体内容主要对PCB命名标识和硬件文档设计;以PCB的外形、元件区域设计、基准点(Mark)、定位孔及PCB重要线宽、器件间的间距等方面提出PCB设计的技术要求。
(注:本PCB技术要求及作业指导仅供PCB设审核流程使用)1.硬件设计文档命名规定将同一组件的硬件设计文档分为以下三种:(1)研发原始文档(2)PCB加工文档(3)生产文档命名规则如下:ST6006BHMI __ D __ 080514日期:6位数08年05月14日单下画线(半角)文档类型:D—研发原始文档M--PCB加工文档P--生产文档单下画线(半角)文件名(英文数字)2.硬件设计文档内容2.1研发文档研发文档除了设计的PCB和SCH目录外,还应有以下4个目录:2.2 PCB加工文档PCB加工文档含有两个目录(1)PCB目录:存放需要加工的PCB文件(2)加工说明目录:存放PCB的开孔、外型等说明2.3 生产文档生产文档只含存放元件的BOM和在PCB上的元件布置图的生产说明。
3.硬件设计文档细则3.1 SCH及其PCB在以文件名命名的目录中含有两个目录,它们分别是SCH目录和PCB目录,其中SCH目录只能存放SCH文件和与SCH相关的文件;PCB目录只能存放PCB文件及其PCB相关的文件。
SCH文件采用A4篇幅,如果SCH文件超过一张,则采用Project进行管理。
3.2设计说明设计说明含版本历史和设计说明3.3加工说明加工说明采用16色BMP或GIF图形格式,采用PROTEL SE中的import进行输入存档。
3.4生产说明生产说明中含有BOM和PCB上的元件布置图,其中PCB上的元件布置图为PDF格式,如果是两面安装的元件,在其文件名后用下画线标识出TOP戓BOTTOM。
铝合金 壳体 技术要求

铝合金壳体技术要求
1. 铝合金壳体的材质要求高纯度、良好的机械性能和热稳定性,满足工艺要求。
2. 壳体表面要求平整、光滑、无气泡,不得有缺陷,如裂纹、气孔、凸起、细槽等。
3. 壳体的尺寸公差要符合图纸要求,不得超出规定范围。
4. 壳体表面应进行表面处理,如阳极氧化、喷漆或电镀等,以提高其防腐性和耐磨性。
5. 壳体内部要求光滑平整,不得有锐角和毛刺,以避免损坏零部件和影响外观。
6. 壳体的制造要求严格控制加工工艺和数控加工设备的精度,以确保壳体加工精度高、尺寸准确。
7. 壳体的装配要求精度高、无松动,各组件之间的间隙要符合设定值,以确保整体性能稳定、耐用。
8. 壳体的温度和湿度要求受制造和使用环境的限制,应在正常范围内,以确保壳体和内部元件的正常工作。
pcb板设计工艺标准

pcb板设计工艺标准PCB板设计工艺标准。
PCB板(Printed Circuit Board)是电子产品中不可或缺的部分,它承载着电子元器件并连接它们,是电子产品的“大脑”。
因此,PCB板的设计工艺标准对于电子产品的性能和稳定性至关重要。
本文将就PCB板设计工艺标准进行详细介绍,以帮助大家更好地了解和掌握PCB板的设计工艺。
首先,PCB板设计工艺标准需要考虑的第一点是材料选择。
在PCB板的设计中,选择合适的基板材料对于电路的性能至关重要。
常见的基板材料有FR-4、铝基板、陶瓷基板等,不同的材料具有不同的性能特点,例如导热性能、介电常数等,因此在设计PCB板时需要根据具体的应用场景选择合适的基板材料。
其次,PCB板设计工艺标准需要考虑的是布线规则。
良好的布线规则可以有效地减小信号传输的损耗和干扰,提高电路的稳定性和可靠性。
在布线规则的设计中,需要考虑信号线和电源线的走向、长度匹配、阻抗控制等因素,以确保电路在工作时能够稳定可靠地传输信号和供电。
另外,PCB板设计工艺标准还需要考虑的是元器件布局。
良好的元器件布局可以有效地减小元器件之间的干扰,提高电路的抗干扰能力。
在元器件布局的设计中,需要考虑元器件之间的间距、走线的合理性、散热器件的位置等因素,以确保电路在工作时能够稳定可靠地工作。
此外,PCB板设计工艺标准还需要考虑的是工艺要求。
在PCB板的设计中,需要考虑到工艺要求对于电路的影响,例如焊接工艺、阻焊工艺、喷镀工艺等。
良好的工艺要求可以有效地提高PCB板的制造质量,降低制造成本,提高生产效率。
最后,PCB板设计工艺标准需要考虑的是设计文件的输出。
在PCB板的设计过程中,需要输出相应的设计文件,包括原理图、布局图、元器件清单、工艺文件等。
这些设计文件对于PCB板的制造和生产至关重要,因此设计文件的准确性和完整性对于PCB板的质量和性能有着直接的影响。
总之,PCB板设计工艺标准是保证电子产品性能和稳定性的重要保障。
精美铝型材机箱面板丝印工艺
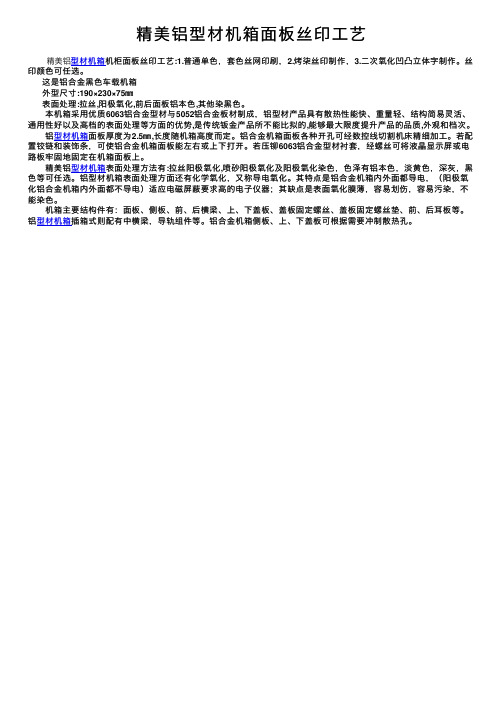
精美铝型材机箱⾯板丝印⼯艺
精美铝型材机箱机柜⾯板丝印⼯艺:1.普通单⾊,套⾊丝⽹印刷,2.烤柒丝印制作,3.⼆次氧化凹凸⽴体字制作。
丝印颜⾊可任选。
这是铝合⾦⿊⾊车载机箱
外型尺⼨:190×230×75㎜
表⾯处理:拉丝,阳极氧化,前后⾯板铝本⾊,其他染⿊⾊。
本机箱采⽤优质6063铝合⾦型材与5052铝合⾦板材制成,铝型材产品具有散热性能快、重量轻、结构简易灵活、通⽤性好以及⾼档的表⾯处理等⽅⾯的优势,是传统钣⾦产品所不能⽐拟的,能够最⼤限度提升产品的品质,外观和档次。
铝型材机箱⾯板厚度为2.5㎜,长度随机箱⾼度⽽定。
铝合⾦机箱⾯板各种开孔可经数控线切割机床精细加⼯。
若配置铰链和装饰条,可使铝合⾦机箱⾯板能左右或上下打开。
若压铆6063铝合⾦型材衬套,经螺丝可将液晶显⽰屏或电路板牢固地固定在机箱⾯板上。
精美铝型材机箱表⾯处理⽅法有:拉丝阳极氧化,喷砂阳极氧化及阳极氧化染⾊,⾊泽有铝本⾊,淡黄⾊,深灰,⿊⾊等可任选。
铝型材机箱表⾯处理⽅⾯还有化学氧化,⼜称导电氧化。
其特点是铝合⾦机箱内外⾯都导电,(阳极氧化铝合⾦机箱内外⾯都不导电)适应电磁屏蔽要求⾼的电⼦仪器;其缺点是表⾯氧化膜薄,容易划伤,容易污染,不能染⾊。
机箱主要结构件有:⾯板、侧板、前、后横梁、上、下盖板、盖板固定螺丝、盖板固定螺丝垫、前、后⽿板等。
铝型材机箱插箱式则配有中横梁,导轨组件等。
铝合⾦机箱侧板、上、下盖板可根据需要冲制散热孔。
PCB技术标准

PCB技术标准在当今的电子制造行业中,PCB技术一直扮演着重要的角色。
PCB技术的发展不仅带动了电子设备制造业的发展,而且还对全球经济发展做出了巨大的贡献。
作为关键的制造流程之一,PCB 技术的标准化已经成为了电子制造工业发展的重要问题,下面将对PCB技术标准的重要性、标准的现状以及未来的发展进行探讨。
一、PCB技术标准的重要性在电子制造行业中,PCB技术标准的重要性是不言而喻的。
每个PCB厂商都应该遵循相关国际标准,这有助于确保其生产出的成品符合国际标准并且可以在全球市场中获得广泛的应用。
标准化可以提高生产的一致性和可重复性,从而可以降低设备故障率、提高生产效率。
另外,标准化还可以帮助促进各个PCB制造商之间的信息交流和协作,以达到最优的生产规划。
标准化还可以确保制造出的产品符合相关的安全标准,因为电子设备中存在着高电压、电磁干扰等风险,标准化可以降低相关风险,提高产品的质量和稳定性。
二、PCB技术标准的现状在目前,电子制造行业中还没有一个全球性的PCB技术标准。
虽然有很多标准可以用作参考,包括IPC、IEC、ISO等国际标准组织制定的标准,但这些标准的适用范围可能会有所不同,并且这些标准也可能存在一些不足之处。
IPC是美国电子行业联合会所制定的标准,它是美国和欧洲PCB技术的主要标准之一。
IPC通过ICO的合作发布了很多PCB 设计和制造方面的标准。
IEC是国际电工委员会所制定的标准,它主要涉及电子设备的安全性和可靠性。
ISO是国际标准化组织所制定的标准,它是全球范围内制定标准的主要机构。
ISO所制定的标准广泛应用于PCB制造中的环境管理、质量管理、工艺管理等方面。
虽然PCB标准存在,但是制定标准的机构之间存在竞争关系,标准之间存在冲突和重复。
标准的制定、审批和发布也需要时间,所以PCB标准仍然面临着一些的问题和挑战。
三、PCB技术标准的未来发展面对如今PCB技术标准存在的问题,我们需要寻求行之有效的解决方法。
pcb加工工艺标准
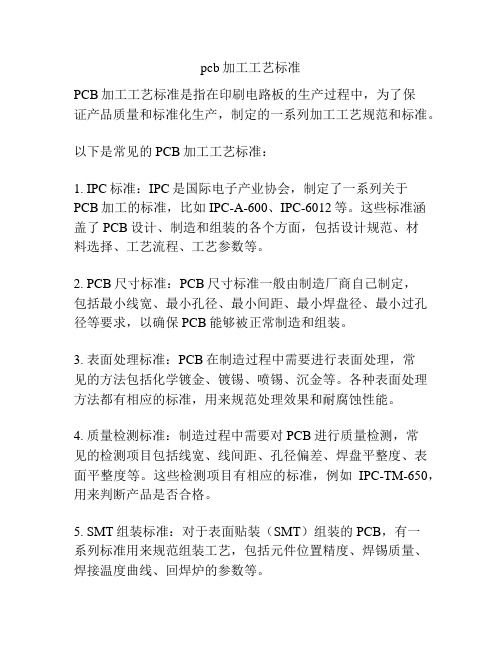
pcb加工工艺标准
PCB加工工艺标准是指在印刷电路板的生产过程中,为了保
证产品质量和标准化生产,制定的一系列加工工艺规范和标准。
以下是常见的PCB加工工艺标准:
1. IPC标准:IPC是国际电子产业协会,制定了一系列关于PCB加工的标准,比如IPC-A-600、IPC-6012等。
这些标准涵
盖了PCB设计、制造和组装的各个方面,包括设计规范、材
料选择、工艺流程、工艺参数等。
2. PCB尺寸标准:PCB尺寸标准一般由制造厂商自己制定,
包括最小线宽、最小孔径、最小间距、最小焊盘径、最小过孔径等要求,以确保PCB能够被正常制造和组装。
3. 表面处理标准:PCB在制造过程中需要进行表面处理,常
见的方法包括化学镀金、镀锡、喷锡、沉金等。
各种表面处理方法都有相应的标准,用来规范处理效果和耐腐蚀性能。
4. 质量检测标准:制造过程中需要对PCB进行质量检测,常
见的检测项目包括线宽、线间距、孔径偏差、焊盘平整度、表面平整度等。
这些检测项目有相应的标准,例如IPC-TM-650,用来判断产品是否合格。
5. SMT组装标准:对于表面贴装(SMT)组装的PCB,有一
系列标准用来规范组装工艺,包括元件位置精度、焊锡质量、焊接温度曲线、回焊炉的参数等。
以上是一些常见的PCB加工工艺标准,不同的厂商和行业可能会有一些特定的标准要求,需要根据具体情况进行制定和执行。
机箱结构设计技术规范标准[详]
![机箱结构设计技术规范标准[详]](https://img.taocdn.com/s3/m/24fbe39e4128915f804d2b160b4e767f5bcf804f.png)
机箱结构设计技术规范标准[详]一、设计原则1. 安全性:机箱结构设计应确保设备在正常使用及意外情况下,对人体及设备本身不造成伤害。
2. 实用性:机箱设计需满足设备功能需求,布局合理,便于操作和维护。
3. 美观性:机箱外观应简洁大方,符合现代审美观念,体现产品特色。
5. 经济性:在满足性能要求的前提下,尽量降低成本,提高产品竞争力。
二、材料选择1. 材料种类:机箱材料可分为金属和非金属两大类。
金属材料主要包括铝合金、冷轧钢板、不锈钢等;非金属材料主要包括工程塑料、ABS等。
3. 材料厚度:根据机箱尺寸、承重要求及成本等因素,合理选择材料厚度。
三、结构设计1. 尺寸与形状:机箱尺寸应根据设备内部元器件及散热需求进行设计,形状应简洁、便于加工。
2. 壁厚:机箱壁厚应均匀,避免因壁厚不均导致强度不足或变形。
3. 固定方式:机箱内部元器件固定方式应牢固可靠,便于拆装和维护。
4. 接口设计:机箱接口应满足设备连接需求,布局合理,便于操作。
5. 散热设计:根据设备发热量,合理设计散热孔、风扇等散热部件,确保设备运行温度在合理范围内。
四、防护措施1. 防尘:机箱应具备一定的防尘功能,避免灰尘进入影响设备性能。
2. 防水:机箱应具备一定的防水能力,防止因意外进水导致设备损坏。
3. 防震:机箱结构设计应考虑抗震性能,确保设备在运输和运行过程中不受损害。
五、加工工艺1. 冲压:金属机箱采用冲压工艺,提高生产效率,降低成本。
2. 折弯:根据机箱结构需求,对板材进行折弯处理,确保机箱强度。
3. 表面处理:机箱表面处理方式有喷漆、阳极氧化、拉丝等,提高机箱美观性和耐腐蚀性。
4. 装配:机箱零部件装配应牢固可靠,确保机箱整体性能。
六、检验标准1. 外观检查:机箱表面应光滑平整,无划痕、凹陷、锈蚀等缺陷。
2. 尺寸测量:机箱尺寸应符合设计要求,误差在允许范围内。
3. 功能测试:机箱组装完成后,进行功能测试,确保各项性能指标达到设计要求。
PCB板材FR-4和铝基技术参数

super-current,
Super-power circuit.
特點:用途:
●良好得散熱性●LED照明電路
●優良的尺寸穩定性●厚膜混合集成電路
●良好的機械加工性●電源電路
●電磁波的屏蔽性●固态繼電器
●優良的性價比
Features: Applications:
No-blistering
S
150S
150S
120S
10min
150S
表面電阻
Surface
Resistance
C-96/35/90
E-24/125
MΩ
體積電阻率
Volume
Resistance
C-96/35/90
E-24/125
MΩ.cm
電氣強度
Electrical
Strength
A
KV/mm
30
AL-H-5
熱傳導率
Thermal
Conductivity
A
W/m.k
≤1.0
3
2
2.5
2
剝離強度
Peel Strength
A
熱應力後
After thermal
stress
N/mm
1.5
1.0
0.9
1.3
1.5
1.5
1.0
0.9
1.3
1.5
熱應力
Thermal
Stress
288℃
不分層、不起泡
No-delimitation,
solidrelayhighcostperformance性能指标性能指标performance項目iten熱傳導率thermalconductivity剝離強度aa熱應力後peelstrengthafterthermalstress熱應力thermalstress表面電阻surfaceresistance體積電阻率volumeresistance電氣強度electricalstrength燃燒性flameabilitytg吸水率moisturabsorptionct1ul94ad2423iec6012vv0v0v0130003600v0130003600v0130003600akvmm3030303030288不分層不起泡nodelimitationnoblisteringc963590e24125c963590e24125nmmwmk101515310102090925131321515實驗條件testcondition單位units典型值alm01alh02ahh3alh4alh5s150s150s120s10min150sm?m?cm13017010501200003250fr4技术参数12层数最大加工面积112层449599mm18244层040mm16mil3最小板厚6层100mm40mil8层120mm48mil10层160mm60mil456789最小板厚最小间距最小孔径孔壁铜厚金属化孔径公差非金属化也径公差010mm4mil010mm4mil030mm12mil0025mm1mil010mm4mil005mm2mil005mm2mil015mm6mil01mm4mil151012常态300常态13kvmm10a15nmm4h28820秒94v050300v10孔位公差11外型尺寸公差12最小阻焊桥13扭曲和弯曲14绝缘电阻15孔电阻16抗电强度17耐电流18抗剥离强度19阻焊剂硬度20热冲击21自熄性22通断测试电压
关于PCB板制作的规范与技巧

关于PCB板制作的规范与技巧PCB板制作是电子产品制造过程中的一项重要环节,对于电路性能和稳定性起着至关重要的作用。
本文将介绍PCB板制作的规范与技巧,帮助读者更好地理解和掌握这一过程。
首先,PCB板制作的规范是保证电路质量的基础,其包括以下几个方面:1.尺寸规范:PCB板的尺寸应符合设计要求,尤其是与外部设备或机箱的安装接口要匹配,避免出现尺寸不符合的问题。
2.材料规范:PCB板的材料应符合相关标准,如使用高质量的玻璃纤维和铜箔,以保证PCB板的稳定性和电气性能。
3.线路布局规范:在PCB板上进行线路布局时,需要注意避免线路的交叉干扰以及与其他元件的冲突。
合理布局有助于减小电磁干扰,提高信号传输的质量。
4.连接规范:PCB板上的焊接点或连接点应严格按照设计要求进行焊接或连接,确保连接的牢固性和电气接触的可靠性。
5.标记规范:PCB板上应标明元件的位置、型号、方向等信息,同时在PCB板边缘标明板名、版本号和制造日期以便追溯和维护。
在PCB板制作过程中,还有一些技巧可以提高制作质量和效率:1.设计前的准备工作:在进行PCB板设计之前,需要对电路进行充分的分析和测试,确保设计的正确性和可行性。
2.选用合适的CAD软件:选择适合自己的CAD软件,学习和掌握其使用方法,以便快速而准确地完成PCB板的设计。
3.合理安排元件布局:在PCB板上合理安排元件的布局,使得线路布局更加紧凑、美观,并且便于后续的焊接和维修。
4.优化线路走向:在进行线路布局时,应该尽量缩短线路长度,减小电磁干扰,并且避免线路交叉等情况,以提高信号传输的质量。
5.制作PCB板前的预备工作:在制作PCB板之前,需要准备好所需的材料和工具,如铜箔、玻璃纤维板、化学溶液、刷子等,以便顺利进行制作过程。
6.注意工艺细节:在进行PCB板制作的每一个步骤中,都要注意一些细节,如化学液体的浓度和温度控制、刻蚀时间的控制、曝光光源的选择等等。
7.严格按照制作流程进行操作:在进行PCB板制作时,要严格按照制作流程进行操作,避免操作失误或遗漏,以保证制作质量和效率。
铝基板PCB制作规范

1、前言:鋁基板製作規範隨著電子技術的發展和進步,電子產品向輕、小、個體化、高可靠性、多功能化已成為必然趨勢。
鋁基板順應此趨勢應運而生,該產品以優異的散熱性、機械加工性、尺寸穩定性及電氣性能在混合積體電路、汽車、辦公自動化、大功率電氣設備、電源設備等領域近年更得到LED載板廣泛的應用。
鋁基覆銅板1969 年由日本三洋公司首先發明,中國於1988 年開始研製和生產,為了適應量產化穩定生產,各公司制定製作規範。
2、範圍:本製作規範針對鋁基覆銅板的製作全過程進行介紹和說明,以保證順利生產。
3、工藝流程:開料鑽孔圖形轉移(D/F)檢板蝕刻蝕檢綠油字元包裝綠檢出貨噴錫鋁基面處理沖板終檢4、注意事項:4.1 鋁基板料昂貴,生產過程中應特別注意操作的規範性,杜絕因不規範操作而導致報廢現象的產生。
4.2 生工序操作人員操作時必須輕拿輕放,以免板面及鋁基面擦花。
4.3 各工序操作人員,應儘量避免用手接觸鋁基板的有效面積內,噴錫及以後工序持板時只准持板邊,嚴禁以手指觸鋁基板內。
4.4 鋁基板屬特種板,其生產應引起各工序高度重視,各工序必須保證此板的順利生產,板到各工序必須由領班或主管級以上人員操作。
5、具體工藝流程及特殊製作參數:第1 頁共5 頁5.1 開料鋁基板製作規範5.1.1 加強來料檢查(必須使用鋁面有保護膜的板料)。
5.1.2 開料後無需烤板。
5.1.3 輕拿輕放,注意鋁基面(保護膜)的保護。
5.2 鑽孔5.2.1 鑽孔參數與FR-4 板材鑽孔參數相同。
5.2.2 孔徑公差特嚴,1OZ 含以上CU 注意控制披峰的產生。
5.2.3 銅皮朝上進行鑽孔。
5.3 乾膜5.3.1 來料檢查:磨板前須對鋁基面保護膜進行檢查,若有破損,必須用藍膠貼牢後再進行前處理。
5.3.2 磨板:僅對銅面進行處理。
5.3.3 貼膜:銅面、鋁基面均需貼膜,控制磨板與貼膜間隔時間不超過 1 分鐘,確保貼膜溫度穩定。
5.3.4 拍板:注意拍板精度。
金属制品技术规范—机柜装配技术要求
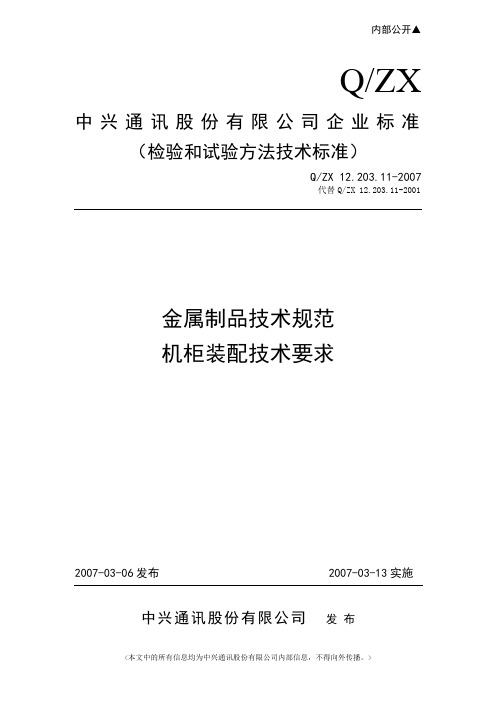
内部公开▲Q/ZX 中兴通讯股份有限公司企业标准(检验和试验方法技术标准)Q/ZX 12.203.11-2007代替Q/ZX 12.203.11-2001金属制品技术规范机柜装配技术要求2007-03-06发布 2007-03-13实施中兴通讯股份有限公司发布前言为了提高金属结构件生产制造质量,加强对金属制品生产流程相关环节的监督检验和质量控制,保证结构件设计要求的完全贯彻和实施,特编写本系列标准。
《金属制品技术规范》为系列标准:Q/ZX 12.203.1《金属制品技术规范-钣金冷冲压件技术要求和检验规则》Q/ZX 12.203.2《金属制品技术规范-机械切削加工件》Q/ZX 12.203.3《金属制品技术规范-铸造加工件》Q/ZX 12.203.4《金属制品技术规范-铝及铝型材技术要求》Q/ZX 12.203.5《金属制品技术规范-焊接加工》Q/ZX 12.203.6《金属制品检验规范-镀覆零件检验》Q/ZX 12.203.7《金属制品检验规范-化学处理层的质量检验》Q/ZX 12.203.8《金属制品技术规范-涂覆层技术条件》Q/ZX 12.203.9《金属制品检验规范-丝印加工检验》Q/ZX 12.203.10《金属制品技术规范-紧固件》Q/ZX 12.203.11《金属制品技术规范-机柜装配技术要求》Q/ZX 12.203.12《金属制品技术规范-汇流排技术要求与试验方法》本标准是《金属制品技术规范》第11部分。
本标准由Q/ZX 12.203.11-2001修订而成,主要修订内容如下:a)规范名称更改及文档结构调整;b)增加机柜机箱防护检验要求;本标准自实施之日起代替 Q/ZX 12.203.11-2001。
本标准由中兴通讯股份有限公司康讯结构系统部提出,总部直属机构质量部归口。
本标准起草部门:质企中心工艺部。
本标准起草人:万东霞。
本标准修订部门(第一次修订):康讯结构系统部。
本标准修订人(第一次修订):崔文斌、曹水春、彭永辉。
解读铝基板pcb制作规范及设计规则
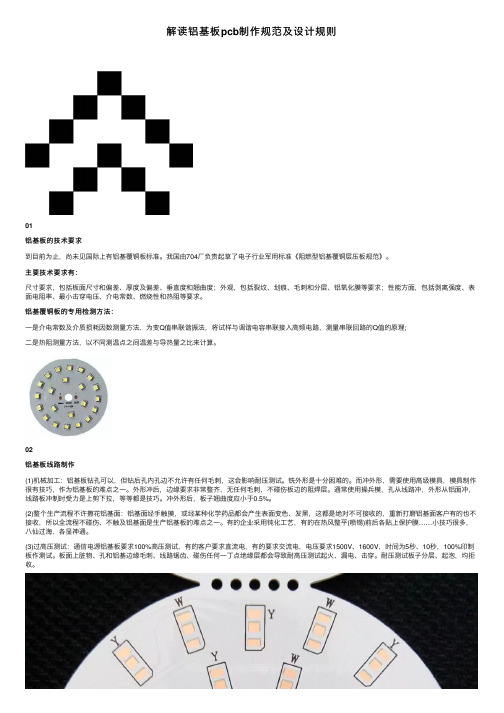
解读铝基板pcb制作规范及设计规则01铝基板的技术要求到⽬前为⽌,尚未见国际上有铝基覆铜板标准。
我国由704⼚负责起草了电⼦⾏业军⽤标准《阻燃型铝基覆铜层压板规范》。
主要技术要求有:尺⼨要求,包括板⾯尺⼨和偏差、厚度及偏差、垂直度和翘曲度;外观,包括裂纹、划痕、⽑刺和分层、铝氧化膜等要求;性能⽅⾯,包括剥离强度、表⾯电阻率、最⼩击穿电压、介电常数、燃烧性和热阻等要求。
铝基覆铜板的专⽤检测⽅法:⼀是介电常数及介质损耗因数测量⽅法,为变Q值串联谐振法,将试样与调谐电容串联接⼊⾼频电路,测量串联回路的Q值的原理;⼆是热阻测量⽅法,以不同测温点之间温差与导热量之⽐来计算。
02铝基板线路制作(1)机械加⼯:铝基板钻孔可以,但钻后孔内孔边不允许有任何⽑刺,这会影响耐压测试。
铣外形是⼗分困难的。
⽽冲外形,需要使⽤⾼级模具,模具制作很有技巧,作为铝基板的难点之⼀。
外形冲后,边缘要求⾮常整齐,⽆任何⽑刺,不碰伤板边的阻焊层。
通常使⽤操兵模,孔从线路冲,外形从铝⾯冲,线路板冲制时受⼒是上剪下拉,等等都是技巧。
冲外形后,板⼦翘曲度应⼩于0.5%。
(2)整个⽣产流程不许擦花铝基⾯:铝基⾯经⼿触摸,或经某种化学药品都会产⽣表⾯变⾊、发⿊,这都是绝对不可接收的,重新打磨铝基⾯客户有的也不接收,所以全流程不碰伤、不触及铝基⾯是⽣产铝基板的难点之⼀。
有的企业采⽤钝化⼯艺,有的在热风整平(喷锡)前后各贴上保护膜……⼩技巧很多,⼋仙过海,各显神通。
(3)过⾼压测试:通信电源铝基板要求100%⾼压测试,有的客户要求直流电,有的要求交流电,电压要求1500V、1600V,时间为5秒、10秒,100%印制板作测试。
板⾯上脏物、孔和铝基边缘⽑刺、线路锯齿、碰伤任何⼀丁点绝缘层都会导致耐⾼压测试起⽕、漏电、击穿。
耐压测试板⼦分层、起泡,均拒收。
03铝基板pcb制作规范1.铝基板往往应⽤于功率器件,功率密度⼤,所以铜箔⽐较厚。
如果使⽤到3oz以上的铜箔,厚铜箔的蚀刻加⼯需要⼯程设计线宽补偿,否则,蚀刻後线宽就会超差。
pcb工艺标准

PCB工艺标准一、PCB尺寸与层数1.PCB尺寸:PCB(Printed Circuit Board)板的尺寸根据实际应用需求而确定。
一般来说,PCB板的最大尺寸为400mm x 400mm,最小尺寸为1mm x 1mm。
2.PCB层数:PCB板的层数根据信号的复杂性和电源分布的需求来确定。
常见的PCB层数从2层到8层不等。
二、PCB材料选择1.基材:PCB板常用的基材包括FR4、CEM-1、铝基板等。
FR4是一种较为常用的材料,具有高绝缘、耐高温、耐化学腐蚀等优点。
CEM-1具有较高的机械强度和刚性,适用于高密度和多层PCB。
铝基板具有高导热、轻量化等特点,适用于大功率电子器件。
2.铜箔:PCB板上的导电层是由铜箔构成,铜箔的厚度和材料质量对PCB的性能有重要影响。
一般来说,厚度为18μm的普通铜箔应用较为广泛。
三、表面处理标准1.镀金处理:镀金层可以提高PCB板的耐腐蚀性和导电性能。
常见的镀金处理包括镀镍金和镀锡金。
2.化学镍金处理:化学镍金是一种环保且性能优良的表面处理方式,可以提高PCB板的可焊性和耐腐蚀性。
3.有机可焊性涂覆:在PCB板的表面涂覆一层有机可焊性涂层,可以提高PCB板的可焊性和耐腐蚀性。
四、IPC标准IPC(International Electrical Manufacturers Association)标准是美国电子电路与互联技术制造商协会制定的标准,旨在确保PCB制造的质量和可靠性。
IPC标准包括IPC-6012(印制板通用规范)、IPC-6013(印制板组装通用规范)等。
五、PCB尺寸标准1.标准尺寸:PCB板的尺寸标准根据实际应用需求而确定,常见的标准尺寸包括50mm x 50mm、100mm x 100mm、200mm x 200mm等。
2.非标尺寸:对于一些非标尺寸的PCB板,需要根据具体应用需求进行定制化生产。
非标尺寸的PCB板需要在生产前进行图纸设计和审核,以确保满足实际应用的要求。
pcb板工艺标准
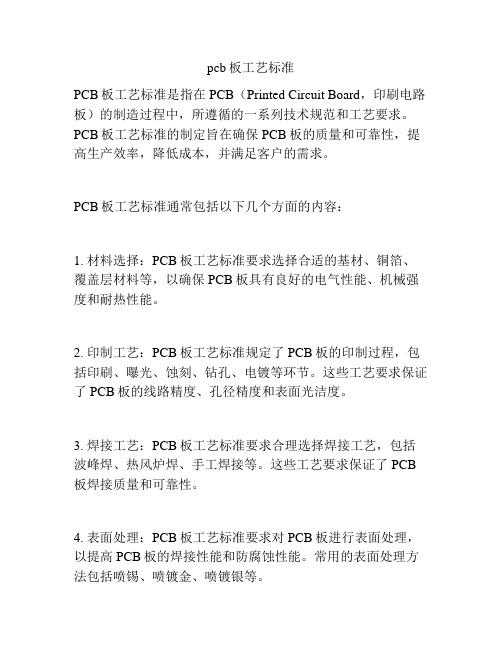
pcb板工艺标准PCB板工艺标准是指在PCB(Printed Circuit Board,印刷电路板)的制造过程中,所遵循的一系列技术规范和工艺要求。
PCB板工艺标准的制定旨在确保PCB板的质量和可靠性,提高生产效率,降低成本,并满足客户的需求。
PCB板工艺标准通常包括以下几个方面的内容:1. 材料选择:PCB板工艺标准要求选择合适的基材、铜箔、覆盖层材料等,以确保PCB板具有良好的电气性能、机械强度和耐热性能。
2. 印制工艺:PCB板工艺标准规定了PCB板的印制过程,包括印刷、曝光、蚀刻、钻孔、电镀等环节。
这些工艺要求保证了PCB板的线路精度、孔径精度和表面光洁度。
3. 焊接工艺:PCB板工艺标准要求合理选择焊接工艺,包括波峰焊、热风炉焊、手工焊接等。
这些工艺要求保证了PCB 板焊接质量和可靠性。
4. 表面处理:PCB板工艺标准要求对PCB板进行表面处理,以提高PCB板的焊接性能和防腐蚀性能。
常用的表面处理方法包括喷锡、喷镀金、喷镀银等。
5. 检测要求:PCB板工艺标准规定了对PCB板进行各种检测和测试的要求,以确保PCB板的质量和可靠性。
常用的检测方法包括X射线检测、AOI(自动光学检测)、ICT(针床测试)等。
6. 封装要求:PCB板工艺标准要求合理选择适当的封装方式,以满足产品的尺寸、功耗和散热要求。
常用的封装方式包括贴片封装、插件封装等。
7. 标志和包装:PCB板工艺标准规定了对PCB板进行标志和包装的要求,以便于产品的追溯和运输。
除了以上内容,PCB板工艺标准还可以根据不同行业和应用领域的需求进行定制。
例如,在航空航天领域,对PCB板的可靠性和抗干扰能力有更高的要求;在医疗设备领域,对PCB板的生物相容性有更高的要求。
总之,PCB板工艺标准是保证PCB板质量和可靠性的重要依据。
通过遵循PCB板工艺标准,可以提高生产效率,降低成本,并满足客户的需求。
在实际生产中,应根据具体情况选择合适的PCB板工艺标准,并严格执行,以确保PCB板的质量和可靠性。
PCB技术标准

PCB技术标准PCB(Printed Circuit Board)技术标准是指制定和规范PCB设计和制造过程中必须遵循的技术要求和规范。
这些标准旨在确保PCB的质量和可靠性,并提供通用的设计和制造指导,以便不同的制造商和设计者能够互通有无。
1.PCB设计标准:PCB设计标准是指PCB布图和布线的相关规定,包括PCB尺寸、布局、线宽与间距、层间间隔、引脚分配等。
这些标准有利于提高电路的可靠性和稳定性,减少电磁干扰和串扰。
2.材料选择标准:PCB材料的选择直接关系到电路板的性能和可靠性,因此需要遵循一定的标准。
例如,标准要求使用高耐温、低介电常数和稳定的材料,以确保电路板在高温和湿度环境下的可靠性。
3.焊接标准:PCB制造过程中的焊接工艺对于电路板的质量和可靠性起着至关重要的作用。
焊接标准包括焊接参数、焊接剂选择、焊接工艺等内容,以确保焊接质量符合要求。
4.线路板层间绝缘标准:PCB多层板的层间绝缘水平对于电路板的可靠性和安全性至关重要。
标准规定了层间绝缘材料的性能要求和测试方法,以确保电路板在高温和高湿度环境下具有良好的层间绝缘性能。
5.表面处理标准:PCB表面处理是为了提供良好的焊接性能和防止氧化腐蚀。
标准规定了表面处理的种类、工艺和要求,例如有机锡、化学镀金和喷锡等,以确保焊接质量和电路板的可靠性。
6.工艺检测标准:在PCB制造过程中,需要进行工艺检测以确保产品质量。
标准规定了各项工艺检测的方法、流程和要求,例如PCB外观检测、线宽测量、阻焊检测、电性能测试等。
PCB技术标准的制定和遵循,对于保证产品质量和生产效率具有重要的意义。
标准化的PCB制造过程可以提高生产效率,降低生产成本,并确保产品质量和可靠性。
同时,标准化还有利于不同厂家之间的互通性和协作,促进行业的发展和进步。
因此,制定和遵守PCB技术标准是PCB设计和制造过程中不可或缺的一部分。
铝基板技术参数要求

铝基板技术参数要求铝基板是一种用于电子设备的重要材料,广泛应用于LED照明、电源模块、通信设备等领域。
铝基板具有优异的导热性能、机械强度和电磁屏蔽性能,因此在选取铝基板时需要考虑一些重要的技术参数要求。
1. 板材厚度:铝基板的厚度通常在0.5mm至3.0mm之间,根据具体应用需求进行选择。
较薄的板材适用于轻薄型设备,而较厚的板材适用于高功率电子设备。
2.铜箔厚度:铜箔是铝基板的导热层,一般厚度为35μm至140μm。
较薄的铜箔能够提供更好的导热性能,但也会降低铝基板的机械强度。
3.热导率:铝基板的热导率决定了其散热性能,一般要求达到1.0W/mK以上,通常铝基板的热导率为1.0W/mK至5.0W/mK。
4.绝缘层:铝基板的绝缘层是由聚酰亚胺(PI)或环氧树脂形成的,能够提供良好的绝缘性能。
绝缘层的厚度通常为75μm至125μm。
5.表面处理:铝基板的表面通常需要经过化学处理,以提供更好的连接性能。
通常的表面处理方式有化学镀镍、金属化和喷锡等。
铝基板的表面处理应符合IPC标准。
6. 尺寸和孔径:铝基板的尺寸和孔径应根据具体设计要求进行制定。
常见的尺寸有400mm x 500mm、500mm x 600mm等,孔径的基准值通常为0.8mm。
7.焊盘:铝基板上的焊盘要求良好的焊接性能和机械强度,通常采用HASL(热气呢锡焊)或ENIG(电镀金)等方式进行处理。
8.焊膏:焊膏是连接元件和铝基板的重要材料,需要具有良好的粘接性、可焊性和可修正性。
9.表面平整度:铝基板的表面平整度直接影响到元件的安装和连接性能,因此要求板材表面平整度高,不得有凸起、凹陷或不平整现象。
10.过孔设计:铝基板上的过孔设计要考虑到吸波层和绝缘层的要求,确保过孔的稳定性和连接性能。
总之,铝基板在不同的领域和应用中有着不同的技术参数要求。
以上列举的参数只是一些常见的要求,具体选择合适的铝基板应根据具体需求进行评估和测试。
常用PCB工艺技术参数

常用PCB工艺技术参数PCB(Printed Circuit Board,印刷电路板)是一种用于支持和连接电子元器件的基板。
PCB工艺技术参数对于保证电路板质量和可靠性至关重要。
下面是一些常用的PCB工艺技术参数:1. 板材厚度:PCB的材料通常是由玻璃纤维和树脂组成的复合材料。
板材厚度通常在0.2mm至6.0mm之间,取决于应用需求。
较薄的板材适用于高密度电路板,而较厚的板材可提供更好的耐用性。
2. 线宽/线距:线宽和线距是指PCB上导线(铜线)的宽度和相邻导线之间的最小距离。
常见的线宽/线距值为0.1mm至0.2mm,取决于PCB的复杂程度和电路要求。
3. 最小孔径:PCB上的孔用于安装元器件、连接电路以及提供通过PCB层之间的电气连接。
最小孔径取决于所用的钻头尺寸,通常在0.2mm至0.4mm之间。
4.阻焊和喷锡工艺:阻焊是一种涂覆在PCB表面的保护层,用于防止短路、防潮和保护焊盘。
阻焊通常有不同的颜色,例如绿色、红色和蓝色。
喷锡是一种在焊盘上涂覆一层锡防止氧化的工艺。
5.焊盘:焊盘是在PCB上用于焊接元器件的金属圆形区域。
焊盘的直径和形状取决于元器件的引脚尺寸和形状。
6.表面处理:常见的PCB表面处理工艺包括有:热浸镀金(HASL)、电镀金(ENIG)、喷锡、喷银等。
不同的表面处理工艺可提供不同的电阻和尺寸特性。
7.贴片工艺:贴片工艺是一种将SMT(表面贴装技术)元器件安装在PCB上的工艺。
此工艺考虑到元器件尺寸、引脚布局、封装类型以及自动贴片设备能力。
8.最小线宽间距:这是导线之间的最小间距,也是制约导线粗细的最小限制。
9.控制阻焊剂的多少:控制阻焊的多少来提高制造的品质。
10.第一网格的大小:第一网格是指PCB上的最小间距,通常表示为X/Y规格。
11.最小过孔量:指从板表面到板底面的最小孔径。
12.最小钻孔量:指在PCB内部内层产生孔的最小尺寸。
13. via孔:用于将信号传输到不同PCB层的孔。
标准铝型材机箱与PCB技术

19″系统的尺寸和定义安装法兰外侧宽度尺寸(包括安装支架在内)是482.6mm(19″),所以将其定义为19″系统。
插箱插箱是电子设备的重要组成部分。
一般由横梁、上下盖板、前后面板、左右侧板组成。
使用空间以多少个槽位计算。
一个槽位通常是由几个水平TE 构成,或由设计者给定。
内部插件主要分板式插件和盒式插件。
一个板式插件有前面板和带有连接器的电路板组成。
一个盒式插件一般是将大量的元器件或几个电路板安装在内的盒子。
宽度W安装法兰后面(包括螺钉)的全部宽度应该小于449mm。
插箱内的宽度以TE 作为单位。
1 TE = 5.08mm(0.2″)内间距≥84 ×5.08 = 426.72mm。
高度插箱的高度以U作为单位,1U=44.45mm(1.75″)通常:高度H = (n ×U-0.8)±0.4RX 是H = (n ×U -1.35″)见表1.深度插箱深度无明确规定,具体由插件的深度及后连接器的尾针后输入输出插件的大小决定插箱安装尺寸插箱水平安装间距是465.1±1.6mm插箱垂直安装孔间距见(说明书29页中图)及(表1)法兰安装孔尺寸见(29页上图)表1单位:mm高度(U)H-0.3(mm)RX 高度el e2h2HS143.1031.7533.6023.10287.6076.2078.0567.553132.0057.15122.50156.454176.50101.6166.95112.005221.00146.10211.40201.006265.40190.50255.85245.356(!)265.4076.20255.85289.807309.80120.60300.30289.808354.20165.10344.75334.259398.70120.60389.20378.7010443.20165.10433.65423.1511487.60146.10478.10467.6012532.10190.60522.55512.05插箱PCB板卡标准尺寸插箱PCB板卡标准尺寸PCB插板对应面板安装位置:(配合II 型拉手)导轨导槽宽度可容纳1.6±0.2mm厚的印制板,这种印制板符合IEC 249-2标准导轨A符合IEC 60 297- 3- 101 标准导轨B配有编码销插孔和导向针孔,符合IEC 60 297 - 3 -103标准导轨C是导轨B向右偏移2.54mm . 用于印制板背面有元器件的情况插箱深度尺寸校验注释:DC:插箱前侧的校验尺寸(从前面板背面到背板连接器末端的间距)RDC:插箱后侧的校验尺寸(从后面板背面到背板连接器末端的间距)Dt2:前插卡检验尺寸(从前面板背面到活动连接器末端的间距)RDt2:后插卡检验尺寸(从后面板背面到活动连接器末端的间距)插箱印刷电路板设计机箱的基本概念19英寸机箱设计一、前言:1-何谓19”机箱?19”机箱泛指装设在19”机柜(Cabinet or Rack)内的机器设备,其中Cabinet和Rack的差异为Cabinet四周有外壳和上下盖保謢,而Rack则无,Rack为和Cabinet有所区别常被称为”机架”,此二者外形均为长方体,19”机箱(Chassis)为了能装在机柜内,其外形多设计成长方体,并遵守特定之高度限制让不同制造者所生产之机箱能放入依规格设计之机柜.2-19”机箱和机柜的由来19”机箱和机柜原本是美国军方电子控制仪器的一种规格,其设定的目的在于统一仪器的外形尺寸和方便快速组装抽换和维护,最后随着军方技术转移民间,此一规格亦广泛的被企业界所采用.2-19”机箱产品的种类.2-1-机柜的优点在于提供机箱安全保护和扩充的便利性,早期常用于工业控制机台,近几年由于网络的发展,网络通讯设备也开始大量使用;因此其产品的种类大致可区分成办公室用和工业用产品两大类:2-2-办公室用产品2-2-1-Server.2-2-2-Telcom产品2-2-3-Internet/Intranet产品2-2-4-其它计算机周边相关产品2-3-工业用产品2-3-1-IPC(Industrial PC)2-3-2-Control Panel2-3-3-其它机器辅助相关产品二、19”机箱外部和机柜的规格1-机柜之规格.机柜不单如字面上的解释一般像个柜子,其外形有很多种,如下列三图所示,图中的机柜均为HP公司产品,但用于不同操作环境时,机柜之外形和尺寸亦会有所差异,所有机柜都依相关规格制造,机柜之宽度,高度与深度有一定之规格,在IEC-60297系列和EIA-310系列中均有详细规格,此二规格明定高度单位为U(1U=1.75”=44.45mm),宽度为19”(尚有其它之宽度规格,但以19”规格最为常用),深度虽亦有规定,但其变化却比较多,机柜之规格可分成高度,宽度和深度三项.1-1-高度单位U之定义: 1U=1.75英吋=44.45mm.机柜均以U为基本单位,如35U高度之机柜,是指此一机柜中可装入总共35U高之机箱,而非机柜由上到下的高度是35U.1-2-19英吋(482.6mm) 宽度之定义为机箱由正前方观察可视之最宽距离,通常是机箱两侧之mounting flange宽度,而非机柜本体之宽度,19”机柜之宽度受限于机箱尺寸,几乎全都大于500mm(因19”机箱宽度为483mm左右),目前市面上之机柜宽度由500mm~800mm都有,甚至有超过1000mm之特殊规格,但最常用的为600mm宽之机柜.1-3-在机柜深度方面,虽然有规定但却很少被提及,因其不像高度和宽度一般限制机箱设计,即使短机箱卜亦可用长机柜,只要其设计规格完全符合规格设计,而机柜制造商不泛各种不同深度规格之机柜,其中又以600mm,700mm和800mm深度的机柜最常被使用(深度系指机柜外观不含把手的深度):2-机箱设计时外观和机柜的关系.2-1-外观尺寸:机箱受限于机柜的尺寸限制,因此设计时需考虑下列几点:2-1-1-在高度方面;由于高度以U为单位,1U为1.75”或44.45mm,因此如果1U机箱的高度不可超出44.45mm,为了堆栈和拆装方便,通常设计成44mm以下,以此类推即使不同U之机箱其实际高度亦比该U少0.8—1.35MM,让机柜内每一台机箱之箱有间隙而不会影响组装和拆卸.2-1-2-在宽度方面;19”机柜在内部四个角落都有钣金件(或铝矩形)支柱用以支撑机柜和固定机箱,因此其内部宽度只有450mm(约17.7”左右)可装机箱,而非有19”宽度可装机箱,且机箱在设计上为要考量组装性,不可能宽度设定成450mm,通常不会超过449mm,左右会各留少许间隙,若有考虑在两侧装设滑轨(装滑轨的机箱高度都比较低,大都不会超过4U高度)以方便机箱拆装和保养时,机箱还要再缩小宽度,常用的滑轨厚度有10~20mm不等,双边都要装滑轨,扣除两倍的厚度,如此机箱宽度就更窄了.2-1-3-在深度方面;深度要考虑的就是机箱在机柜内必需有空间散热,跑线和其它机构的安排,由于左右两侧空间不大,只好利用前后方的空间了,通常前后各有75mm以上的空间(和固定架位置有关),因此600mm的机柜其机箱深度最好设计在450mm以下.2-2-机柜固定孔:机箱放入机柜时必需由两侧固定,其固定孔通常在mounting flange上,其位置尺寸如下图所示(数据来源:EIA-310-D),图中尺寸在宽度标示上有3个,每个尺寸又各有三个数字,其中最上层的尺寸为19英吋机柜的标准尺寸(即450,465,483.4三个尺寸),三个尺寸所代表的意义如下:450mmà机箱可放入机柜内之最宽距离.465mmà机箱和机柜之固定孔的间距.483.4mmà机箱上mounting flange两侧可容许之最宽距离.31.8mmà1U高度内之两个固定孔距离,若1U高度内有三个固定孔时,其固定孔之间距为31.8mm的一半15.9mm.12.7mmà两个U之间最近的固定孔距离,即上面U的最下方固定孔和下面U的最上方固定孔距离,因此1U和1U之相接合位置在12.7mm距离的正中间.6.75à机箱在最上方(或最下方)的固定孔和机柜内侧上端(或下端)之间的距离.2-3-正面把手:机箱放入机柜时是由前方推入,拉出时自然是由前方操作,为了方便机箱能由前方推入和拉出,在机箱前方两侧经常会设计有把手固定在机箱上,方便使用者的操作,在设计把手时要特别注意不可干涉到机箱和机柜组装的螺丝固定孔,因其位置正好也在机箱两侧.2-4-脚垫:有些机箱设计成在机柜外侧仍能独立作业,因此其下方大多装有脚垫,如此放于桌上时便不会括伤桌面,但如要装入机柜时就会迼成脚垫和下方机箱干涉的情形,因此脚垫最好能设计成可拆装的较好.1.EIA-310-D (电子工业协会)规格2.IEC 20697-1~20697-4 (国际电子委员会)规格PCB设计时抗EMC的改进PCB设计时抗ESD的方法来自人体、环境甚至电子设备内部的静电对于精密的半导体芯片会造成各种损伤,例如穿透元器件内部薄的绝缘层;损毁MOSFET和CMOS元器件的栅极;CMOS器件中的触发器锁死;短路反偏的PN结;短路正向偏置的PN结;熔化有源器件内部的焊接线或铝线。
- 1、下载文档前请自行甄别文档内容的完整性,平台不提供额外的编辑、内容补充、找答案等附加服务。
- 2、"仅部分预览"的文档,不可在线预览部分如存在完整性等问题,可反馈申请退款(可完整预览的文档不适用该条件!)。
- 3、如文档侵犯您的权益,请联系客服反馈,我们会尽快为您处理(人工客服工作时间:9:00-18:30)。
19″系统的尺寸和定义安装法兰外侧宽度尺寸(包括安装支架在内)是482.6mm(19″),所以将其定义为19″系统。
插箱插箱是电子设备的重要组成部分。
一般由横梁、上下盖板、前后面板、左右侧板组成。
使用空间以多少个槽位计算。
一个槽位通常是由几个水平TE 构成,或由设计者给定。
内部插件主要分板式插件和盒式插件。
一个板式插件有前面板和带有连接器的电路板组成。
一个盒式插件一般是将大量的元器件或几个电路板安装在内的盒子。
宽度W安装法兰后面(包括螺钉)的全部宽度应该小于449mm。
插箱内的宽度以TE 作为单位。
1 TE = 5.08mm(0.2″)内间距≥84 ×5.08 = 426.72mm。
高度插箱的高度以U作为单位,1U=44.45mm(1.75″)通常:高度H = (n ×U-0.8)±0.4RX 是H = (n ×U -1.35″)见表1.深度插箱深度无明确规定,具体由插件的深度及后连接器的尾针后输入输出插件的大小决定插箱安装尺寸插箱水平安装间距是465.1±1.6mm插箱垂直安装孔间距见(说明书29页中图)及(表1)法兰安装孔尺寸见(29页上图)表1单位:mm高度(U)H-0.3(mm)RX 高度el e2h2HS143.1031.7533.6023.10287.6076.2078.0567.553132.0057.15122.50156.454176.50101.6166.95112.005221.00146.10211.40201.006265.40190.50255.85245.356(!)265.4076.20255.85289.807309.80120.60300.30289.808354.20165.10344.75334.259398.70120.60389.20378.7010443.20165.10433.65423.1511487.60146.10478.10467.6012532.10190.60522.55512.05插箱PCB板卡标准尺寸插箱PCB板卡标准尺寸PCB插板对应面板安装位置:(配合II 型拉手)导轨导槽宽度可容纳1.6±0.2mm厚的印制板,这种印制板符合IEC 249-2标准导轨A符合IEC 60 297- 3- 101 标准导轨B配有编码销插孔和导向针孔,符合IEC 60 297 - 3 -103标准导轨C是导轨B向右偏移2.54mm . 用于印制板背面有元器件的情况插箱深度尺寸校验注释:DC:插箱前侧的校验尺寸(从前面板背面到背板连接器末端的间距)RDC:插箱后侧的校验尺寸(从后面板背面到背板连接器末端的间距)Dt2:前插卡检验尺寸(从前面板背面到活动连接器末端的间距)RDt2:后插卡检验尺寸(从后面板背面到活动连接器末端的间距)插箱印刷电路板设计机箱的基本概念19英寸机箱设计一、前言:1-何谓19”机箱?19”机箱泛指装设在19”机柜(Cabinet or Rack)内的机器设备,其中Cabinet和Rack的差异为Cabinet四周有外壳和上下盖保謢,而Rack则无,Rack为和Cabinet有所区别常被称为”机架”,此二者外形均为长方体,19”机箱(Chassis)为了能装在机柜内,其外形多设计成长方体,并遵守特定之高度限制让不同制造者所生产之机箱能放入依规格设计之机柜.2-19”机箱和机柜的由来19”机箱和机柜原本是美国军方电子控制仪器的一种规格,其设定的目的在于统一仪器的外形尺寸和方便快速组装抽换和维护,最后随着军方技术转移民间,此一规格亦广泛的被企业界所采用.2-19”机箱产品的种类.2-1-机柜的优点在于提供机箱安全保护和扩充的便利性,早期常用于工业控制机台,近几年由于网络的发展,网络通讯设备也开始大量使用;因此其产品的种类大致可区分成办公室用和工业用产品两大类:2-2-办公室用产品2-2-1-Server.2-2-2-Telcom产品2-2-3-Internet/Intranet产品2-2-4-其它计算机周边相关产品2-3-工业用产品2-3-1-IPC(Industrial PC)2-3-2-Control Panel2-3-3-其它机器辅助相关产品二、19”机箱外部和机柜的规格1-机柜之规格.机柜不单如字面上的解释一般像个柜子,其外形有很多种,如下列三图所示,图中的机柜均为HP公司产品,但用于不同操作环境时,机柜之外形和尺寸亦会有所差异,所有机柜都依相关规格制造,机柜之宽度,高度与深度有一定之规格,在IEC-60297系列和EIA-310系列中均有详细规格,此二规格明定高度单位为U(1U=1.75”=44.45mm),宽度为19”(尚有其它之宽度规格,但以19”规格最为常用),深度虽亦有规定,但其变化却比较多,机柜之规格可分成高度,宽度和深度三项.1-1-高度单位U之定义: 1U=1.75英吋=44.45mm.机柜均以U为基本单位,如35U高度之机柜,是指此一机柜中可装入总共35U高之机箱,而非机柜由上到下的高度是35U.1-2-19英吋(482.6mm) 宽度之定义为机箱由正前方观察可视之最宽距离,通常是机箱两侧之mounting flange宽度,而非机柜本体之宽度,19”机柜之宽度受限于机箱尺寸,几乎全都大于500mm(因19”机箱宽度为483mm左右),目前市面上之机柜宽度由500mm~800mm都有,甚至有超过1000mm之特殊规格,但最常用的为600mm宽之机柜.1-3-在机柜深度方面,虽然有规定但却很少被提及,因其不像高度和宽度一般限制机箱设计,即使短机箱卜亦可用长机柜,只要其设计规格完全符合规格设计,而机柜制造商不泛各种不同深度规格之机柜,其中又以600mm,700mm和800mm深度的机柜最常被使用(深度系指机柜外观不含把手的深度):2-机箱设计时外观和机柜的关系.2-1-外观尺寸:机箱受限于机柜的尺寸限制,因此设计时需考虑下列几点:2-1-1-在高度方面;由于高度以U为单位,1U为1.75”或44.45mm,因此如果1U机箱的高度不可超出44.45mm,为了堆栈和拆装方便,通常设计成44mm以下,以此类推即使不同U之机箱其实际高度亦比该U少0.8—1.35MM,让机柜内每一台机箱之箱有间隙而不会影响组装和拆卸.2-1-2-在宽度方面;19”机柜在内部四个角落都有钣金件(或铝矩形)支柱用以支撑机柜和固定机箱,因此其内部宽度只有450mm(约17.7”左右)可装机箱,而非有19”宽度可装机箱,且机箱在设计上为要考量组装性,不可能宽度设定成450mm,通常不会超过449mm,左右会各留少许间隙,若有考虑在两侧装设滑轨(装滑轨的机箱高度都比较低,大都不会超过4U高度)以方便机箱拆装和保养时,机箱还要再缩小宽度,常用的滑轨厚度有10~20mm不等,双边都要装滑轨,扣除两倍的厚度,如此机箱宽度就更窄了.2-1-3-在深度方面;深度要考虑的就是机箱在机柜内必需有空间散热,跑线和其它机构的安排,由于左右两侧空间不大,只好利用前后方的空间了,通常前后各有75mm以上的空间(和固定架位置有关),因此600mm的机柜其机箱深度最好设计在450mm以下.2-2-机柜固定孔:机箱放入机柜时必需由两侧固定,其固定孔通常在mounting flange上,其位置尺寸如下图所示(数据来源:EIA-310-D),图中尺寸在宽度标示上有3个,每个尺寸又各有三个数字,其中最上层的尺寸为19英吋机柜的标准尺寸(即450,465,483.4三个尺寸),三个尺寸所代表的意义如下:450mmà机箱可放入机柜内之最宽距离.465mmà机箱和机柜之固定孔的间距.483.4mmà机箱上mounting flange两侧可容许之最宽距离.31.8mmà1U高度内之两个固定孔距离,若1U高度内有三个固定孔时,其固定孔之间距为31.8mm的一半15.9mm.12.7mmà两个U之间最近的固定孔距离,即上面U的最下方固定孔和下面U的最上方固定孔距离,因此1U和1U之相接合位置在12.7mm距离的正中间.6.75à机箱在最上方(或最下方)的固定孔和机柜内侧上端(或下端)之间的距离.2-3-正面把手:机箱放入机柜时是由前方推入,拉出时自然是由前方操作,为了方便机箱能由前方推入和拉出,在机箱前方两侧经常会设计有把手固定在机箱上,方便使用者的操作,在设计把手时要特别注意不可干涉到机箱和机柜组装的螺丝固定孔,因其位置正好也在机箱两侧.2-4-脚垫:有些机箱设计成在机柜外侧仍能独立作业,因此其下方大多装有脚垫,如此放于桌上时便不会括伤桌面,但如要装入机柜时就会迼成脚垫和下方机箱干涉的情形,因此脚垫最好能设计成可拆装的较好.1.EIA-310-D (电子工业协会)规格2.IEC 20697-1~20697-4 (国际电子委员会)规格PCB设计时抗EMC的改进PCB设计时抗ESD的方法来自人体、环境甚至电子设备内部的静电对于精密的半导体芯片会造成各种损伤,例如穿透元器件内部薄的绝缘层;损毁MOSFET和CMOS元器件的栅极;CMOS器件中的触发器锁死;短路反偏的PN结;短路正向偏置的PN结;熔化有源器件内部的焊接线或铝线。
为了消除静电释放(ESD)对电子设备的干扰和破坏,需要采取多种技术手段进行防范。
在PCB板的设计当中,可以通过分层、恰当的布局布线和安装实现PCB的抗ESD设计。
在设计过程中,通过预测可以将绝大多数设计修改仅限于增减元器件。
通过调整PCB布局布线,能够很好地防范ESD。
以下是一些常见的防范措施。
*尽可能使用多层PCB,相对于双面PCB而言,地平面和电源平面,以及排列紧密的信号线-地线间距能够减小共模阻抗和感性耦合,使之达到双面PCB的1/10到1/100。
尽量地将每一个信号层都紧靠一个电源层或地线层。
对于顶层和底层表面都有元器件、具有很短连接线以及许多填充地的高密度PCB,可以考虑使用内层线。
*对于双面PCB来说,要采用紧密交织的电源和地栅格。
电源线紧靠地线,在垂直和水平线或填充区之间,要尽可能多地连接。
一面的栅格尺寸小于等于60mm,如果可能,栅格尺寸应小于13mm。
*确保每一个电路尽可能紧凑。
*尽可能将所有连接器都放在一边。
*如果可能,将电源线从卡的中央引入,并远离容易直接遭受ESD影响的区域。
*在引向机箱外的连接器(容易直接被ESD击中)下方的所有PCB层上,要放置宽的机箱地或者多边形填充地,并每隔大约13mm的距离用过孔将它们连接在一起。
*在卡的边缘上放置安装孔,安装孔周围用无阻焊剂的顶层和底层焊盘连接到机箱地上。