氧氯化锆工艺介绍
沸腾氯化法制备氧氯化锆的工艺研究

沸腾氯化法制备氧氯化锆的工艺研究摘要:采用沸腾氯化法制备氧氯化锆的技术工艺是目前最先进的工艺技术路线,利用沸腾氯化炉进行水解、加热、结晶生产出高纯氧氯化锆和高附加值的四氯化硅产品。
它具有低成本、低消耗、产品纯度高等优势。
关键词:沸腾氯化法,氯化炉,加热系统,蒸发,结晶,氧氯化锆,四氯化硅氧氯化锆是一种制备锆系列材料的重要中间产品,重要用途之一是用来制备含锆化学制品,如碳酸锆、硫酸锆、硝酸锆、醋酸锆等。
锆英砂直接沸腾氯化法,是我国参考国外技术自行开发的一项技术,先将原料锆英砂,还原剂石油焦经过磨细混匀后进入料仓,由螺旋送料器送入沸腾氯化炉进行氯化,由工频电炉加热沸腾氯化炉内的石墨管对沸腾氯化炉内的锆英砂和石油焦进行加热使锆英砂氯化为ZrCl4和SiCl4,ZrCl4分别收集在三个冷凝器中,SiCl4由于沸点较低,进入经过冷冻控制的列管冷凝器和收集器中收集。
然后将ZrCl4水解制得氧氯化锆。
相关的化学反应方程式:ZrSiO4 + 4C + 4Cl2 = ZrCl4 + SiCl4 + 4COZrCl4 + H2O = ZrOCl2 +2HCl综上所述氯化法制取氧氯化锆,分为两个步骤:先将含锆物料如锆英砂、二氧化锆、碳化锆氯化制得四氯化锆,再将四氯化锆水解结晶即可值得氧氯化锆。
由于氧氯化锆或由此制得的硫酸锆是萃取分离锆铪时的中间物料,氯化水解法制取氧氯化锆较碱熔法具有流程紧凑、“三废”较易处理,环保投资少等优点。
一、氧氯化锆工艺的研究背景由于资源消耗、环境污染等方面的原因,美国、欧洲、日本等发达经济体已经相继减少或停止氧氯化锆的生产,除了南非、印度等少数国家还有少量的氧氯化锆生产外,其余氧氯化锆产能几乎全部集中在我国占世界总产量95%以上;目前,我国已经成为世界上最大的氧氯化锆生产国、消费国和出口国。
氧氯化锆行业产能过剩,利润大幅下滑;面对如此严峻形势,要发展、增加收益,出路之一就是节约能源、降低消耗,用最少的投入去获取最大的经济效益。
氧氯化锆生产技术中酸解与絮凝脱硅过程的研究

氧氯化锆生产技术中酸解与絮凝脱硅过程的研究氧氯化锆是一种重要的锆化合物,广泛应用于陶瓷、化工、电子等领域。
酸解与絮凝脱硅过程是氧氯化锆生产技术中的关键环节,本文将对这两个过程进行研究。
下面是本店铺为大家精心编写的4篇《氧氯化锆生产技术中酸解与絮凝脱硅过程的研究》,供大家借鉴与参考,希望对大家有所帮助。
《氧氯化锆生产技术中酸解与絮凝脱硅过程的研究》篇1引言氧氯化锆(ZrOCl2)是一种重要的锆化合物,具有较高的熔点和良好的耐腐蚀性,广泛应用于陶瓷、化工、电子等领域。
在氧氯化锆的生产过程中,酸解与絮凝脱硅过程是关键环节,直接影响到产品的质量和产量。
因此,对这两个过程进行深入研究,对于提高氧氯化锆的生产技术和产品质量具有重要意义。
酸解过程的研究酸解是指利用酸将锆矿石中的锆化合物转化为可溶性的锆盐的过程。
在氧氯化锆生产中,通常采用硫酸或盐酸作为酸解剂。
本文以硫酸为例,研究酸解过程中的影响因素。
1. 酸解温度的影响酸解温度对酸解率的影响较大。
实验结果表明,随着酸解温度的升高,酸解率逐渐增加。
这是因为温度升高,硫酸分子的热运动增强,与锆矿石中的锆化合物反应的速率增加,从而导致酸解率提高。
2. 酸解时间的影响酸解时间对酸解率也有一定的影响。
实验结果表明,随着酸解时间的延长,酸解率逐渐增加。
这是因为酸解时间延长,硫酸与锆矿石中的锆化合物的反应时间增加,从而使反应更加充分,酸解率提高。
3. 酸解剂浓度的影响酸解剂浓度对酸解率也有一定的影响。
实验结果表明,随着酸解剂浓度的增加,酸解率逐渐增加。
这是因为酸解剂浓度增加,硫酸与锆矿石中的锆化合物的反应物浓度增加,从而使反应更加充分,酸解率提高。
絮凝脱硅过程的研究絮凝脱硅是指将酸解后的锆矿石浆液进行絮凝处理,使硅酸盐形成絮凝体,从而实现脱硅的过程。
本文对絮凝脱硅过程中的影响因素进行了研究。
1. 絮凝剂的选择絮凝剂的选择对絮凝脱硅效果具有重要意义。
实验结果表明,使用聚丙烯酰胺作为絮凝剂,可以有效提高絮凝脱硅效果。
氧氯化锆湿法生产工艺及其废渣处理研究进展

氧氯化锆湿法生产工艺及其废渣处理研究进展罗六保;温盛红;谢志鹏【摘要】介绍了我国氧氯化锆的生产概况,对氧氯化锆湿法生产工艺特别是目前我国大多数企业所采用的“一酸一碱法”生产工艺及其废渣处理研究进展进行了评述。
指出当前我国氧氯化锆生产技术相对落后,能耗、污染较大,国内氧氯化锆生产企业要想取得更大的发展,必须不断的进行工艺改进和技术革新,尤其是要解决好锆硅渣的处理问题。
%This paper introduces briefly the production of zirconium chloride in China,and re-views the progress of the wet process of zirconium oxychloride production,especially for the widely used process of “one acid-one alkali method”in China and the waste residue treatment. The current production technology of zirconium oxychloride in China is relatively backward for high-energy-consumption and heavy-pollution.In order to achieve greater development,the process improvement and technological innovation should be continued,especially to solve the problem of zirconium silicon residue treatment.【期刊名称】《化学研究》【年(卷),期】2016(027)006【总页数】6页(P791-796)【关键词】氧氯化锆;湿法生产工艺;硅渣;三废处理【作者】罗六保;温盛红;谢志鹏【作者单位】江西应用技术职业学院材料工程学院,江西赣州 341000;江西赣州技师学院,江西赣州 341000;江西理工大学冶金与化学工程学院,江西赣州341000【正文语种】中文【中图分类】TQ134.1;X705氧氯化锆又名二氯氧化锆、氯氧化锆或氯化锆酰[1],其工业产品一般以八水合氧氯化锆(ZrOC12·8H2O)的形式存在.氧氯化锆是锆英砂的初步加工产品,是重要的锆盐基础化工产品,也是制备氧化锆、硫酸锆、碳酸锆等锆化学制品的主要原料,广泛应用于冶金、化工、陶瓷、珠宝、电子和医疗等行业[2].例如,以氧氯化锆为原料生产的立方氧化锆晶体被广泛用作钻石的替代品.此外,氧氯化锆也是采用湿法锆铪分离工艺制备原子能级金属锆的重要原材料[3-5].随着我国国民经济的发展,特别是卫生陶瓷、电子、核电、汽车制造等行业的高速发展,我国各行各业对锆化学制品的需求日益增大.目前,我国已经成为世界上氧氯化锆最大的生产国、消费国和出口国.据有关部门统计,我国氧氯化锆产量己超过20万吨,居世界第一位[6].表1是我国主要氧氯化锆生产企业[7].氧氯化锆的生产方法有很多种,归纳起来可以分为湿法工艺和火法工艺两大类.顾名思义,湿法工艺生产过程以湿法为主,即先采用碱熔烧结的方法分解锆英石,然后采用湿法工艺制得氧氯化锆;火法工艺则是先采取火法以锆英砂制取ZrCl4,然后再由ZrCl4水解得到氧氯化锆.具体的生产工艺主要有氢氧化钠碱熔法、碳酸钠烧结法、碳酸钙(石灰)烧结法、氟硅酸钾烧结法、碳化氯化法、沸腾氯化法等.目前,我国的氧氯化锆生产企业大多采用湿法工艺中的氢氧化钠碱熔法来制备氧氯化锆.因为这种生产方法的原材料中除了锆英砂外,还大量使用了氢氧化钠和盐酸,所以也称作“一酸一碱法”.1.1 一酸一碱法工艺及其进展1.1.1 一酸一碱法工艺一酸一碱法是国内外普遍采用的一种方法[8].一酸一碱法的主要生产过程为:先把氢氧化钠加入反应锅中加热熔融,待温度上升到700 ℃左右后,将锆英砂加入反应锅反应得到Na2ZrO3和Na4SiO4,经锆硅分离、酸化、结晶得氧氯化锆.生产涉及的主要化学反应式如下:用氢氧化钠分解锆英砂的主要工艺参数为:氢氧化钠和锆英砂的物质的量之比为6∶1(质量比约为1.3∶1),反应温度为600~750 ℃,反应时间为30~60 min.在此工艺条件下,锆英砂的分解率在98%左右[7].一酸一碱法工艺流程如图1所示,主要工序有:碱烧(高温碱熔)、水洗(一次除硅)、转型(除钠)、酸化(酸分解)、水溶过滤(二次除硅)、浓缩、结晶等.1.1.2 一酸一碱法研究进展由于一酸一碱法为我国氧氯化锆的主要生产工艺,所以近年来我国广大科技工作者对此工艺进行了比较多的研究,在工艺和设备方面均取得了一些进展.在工艺方面的研究主要集中在两次除硅和一次除钠.如邓淑华和郑文裕[9]在二次除硅工艺中,通过控制多元体系的温度、酸度及锆盐和硅的浓度,使硅杂质以三维网状的硅酸凝胶形式存在,然后筛选合适的絮凝剂令凝胶粒子絮凝,可以迅速地将硅杂质过滤分离,除硅率在99%左右,产品中硅杂质含量≤ 0.000 5%;吴江[10]针对“一酸一碱”法中二次脱硅过程流程复杂,操作周期长,设备量大等问题,提出一种高浓度锆液制备及絮凝脱硅新工艺.在其提出的工艺和条件下,水溶液中硅含量可降至35~50 mg/L,锆浓度与传统工艺相比较可以提高20%.曲景奎等[11]则提出采用聚丙酰胺类絮凝剂与聚乙二醇进行复配絮凝方法深度脱除其中的锆液中的硅酸,从而得到高纯度高浓度氧氯化锆溶液.与传统工艺相比较,可以省去一次冷却结晶等步骤,简化了生产流程,提高生产效率,降低了能耗与设备投入.陈仲丛[12]、吴锦鹏[13]等则对水洗、转型工艺(水洗为一次除硅工艺,转型则为除钠工艺)进行了一些技术改造性的研究.在氧氯化锆生产设备方面,罗方承等[14]对碱熔工序的锆英砂投料装置进行了改进,降低了工人操作的危险性,改善了操作环境;孙亚光等[15]针对原氧氯化锆工艺中自然结晶耗时长、受气候影响大、结晶破碎困难等缺点,开发出了一种新的结晶装置.何绍敏[16]、陈勇兵[17]、许园春[18]等就氧氯化锆浓缩生产工艺的蒸发浓缩设备和控制系统进行了研究探讨.何航军等[19]则根据同离子效应,提出在锆母液中加入氯化钙以提高氯离子的浓度来缩短氧氯化锆结晶时间,提高氧氯化锆的结晶率.1.2 其他湿法工艺研究进展最近,张建东[7]针对锆英砂碱熔法产氧氯化锆生存在的烧碱消耗大、碱性废水和废硅渣容易造成环境污染等问题,提出了用氧化钙来替代部分氢氧化钠,即采用混合氢氧钠和氧化钙两种碱来分解锆英砂生产氧氯化锆的工艺.童吉灶等[20]针对铌钽矿常伴有丰富的锆钍的情况,提出了以生石灰为主要原料,以少量的固体氢氧化钠作为反应助剂来分解富锆尾矿制备氧氯化锆.李中军等[21]进行了用碳化锆碱熔制备氧氯化锆的研究,其研究采用氢氧化钠在高温下分解碳化锆,然后通过水洗、盐酸浸出和蒸发结晶等工序制备氧氯化锆,为以碳化锆为原料制备氧氯化锆提供了一条新途径.目前国内氧氯化锆生产采用的湿法工艺具有产品质量稳定、生产装置规模较大的特点[22],但其不足之处是生产过程有大量的废渣——锆硅渣产生,如果对废渣处理不当将严重污染和破坏厂区及其周边的生态环境.据估算,每生产1吨氧氯化锆成品则会产生约1吨的锆硅渣[23-24].2.1 废渣的主要成份及其来源2.1.1 废渣的主要成份锆硅渣外观呈浅黄色,为松软的酸性团聚状凝胶体,主要化学组成为具有较高活性的二氧化硅[25].锆硅渣的固体含量为20%左右,二氧化硅含量为16%左右,可溶性锆(以ZrO2计)含量为1%~2%,另外还含有未分解的锆英砂约为1.5%,含有少量Fe3+、Na+等杂质离子及机械杂质[7].2.1.2 废渣的来源锆硅渣中的二氧化硅来源于原料中的锆英砂.锆英砂(ZrSiO4)经与碱烧结反应生成锆酸钠(Na2ZrO3)、硅酸钠(Na2SiO3),原硅酸钠(Na4SiO4)及少量锆硅酸钠(Na2ZrSiO5)[26].其中硅酸钠、原硅酸钠溶于水,称为水溶性硅,而锆硅酸钠则不溶于水称为不溶性硅.水溶性硅因溶于水,在水洗工序中可以直接漂洗除去;而不溶性硅,则随不溶于水的锆酸钠一起沉淀下来成为水转料的主要成份.在后续酸化工序中,水转料中的锆硅酸钠及锆酸钠与盐酸反应,生成溶于水的氧氯化锆.物料经水溶后进行压滤实现锆硅分离,得到滤渣和锆母液.锆母液经浓缩结晶、破碎、酸洗除杂后可得氧氯化锆产品;而压滤剩下的滤渣即为锆硅渣.2.2 废渣处理研究进展目前,国内氧氯化锆生产厂家对锆硅渣主要采用堆积、填埋和制浆排放等方式处理,不仅会对水体和土壤造成污染,也会恶化厂区及其周边生态环境,并造成SiO2及锆元素的流失[27].而且随着我国氧氯化锆生产规模的不断扩大,锆硅渣的处理问题显得日益突出[28-29].为了解决锆硅渣的处理问题,近年来国内很多科技工作者对锆硅渣的无害化处理、综合回收利用进行了大量的研究.2.2.1 制备白炭黑白炭黑主要成份为二氧化硅,是一种十分重要的化工产品,它具有耐高温、高的表面活性和多孔结构等特点,在塑料、橡胶、制药、油漆、造纸等行业应用广泛[30-31].以废弃的锆硅渣为原料来制备白炭黑,是一条“变废为宝”回收利锆硅渣的新途径[32].用锆硅渣制备白炭黑采用工艺有直接中和法、沉淀法和离子交换法等.如陈文利等[33]以锆硅渣为主要原料,采用直接中和的方法制备白炭黑,其主要工艺为:在废硅渣中加入去离子水进行强力搅拌,静置后去除机械杂质;然后用氢氧化钠调节溶液pH为8;升温至80~90 ℃,加入分散剂使之充分胶溶;水洗至无氯离子检出后过滤;固体产物水于110~120 ℃烘干,经过粉碎即得产品白炭黑.该工艺具有流程短、操作简单等特点,其缺点是:废硅渣中Zr4+、Fe3+、Na+等离子杂质不能有效除去,导致白炭黑产品的品质偏低.古映莹等[34]以废弃的锆硅渣为原料,利用沉淀法成功制得白炭黑.该研究采用正交实验法考察了水玻璃浓度、硅溶胶浓度、氯化钠的加入量、陈化pH、反应温度值等因素对白炭黑质量的影响,总结得到了制备白炭黑的最佳工艺条件.潘群雄等[35]提出离子交换法制备白炭黑新工艺,工艺的除杂机理为:用倾析法除去硅溶胶液中机械混合物;在酸性条件下水洗去除物理吸附的Zr4+离子;用离子交换法除去进入硅溶胶中的Ti4+、Fe3+、Na+等离子.此外,吉娜[36]对化学沉淀法和直接中和法等白炭黑制备工艺进行了深入研究,最后找到了制备符合国家白炭黑产品标准的工艺方法,并确定了其最佳工艺条件.最近,杨得鑫等[27]以锆硅渣为原料,研究了采用锆煅烧—酸洗方法制备白炭黑的工艺技术.研究发现,通过煅烧—酸洗方法可以提高产品中无定型二氧化硅的含量.张晓静等[37]采用锆硅渣制浆—研磨—水洗—固液分离流程,通过优化工艺参数,得到了利用锆硅渣回收白炭黑的最佳工艺条件,并实现了无定形SiO2与锆组分的分离.通过此法生产的白炭黑产品其质量达到了HG/T 3061-2009和ISO 5794-1-2005标准要求.2.2.2 制备硅酸钠、层状硅酸钠硅酸钠是硅化合物的基本原料,用以生产硅胶、白炭黑、沸石分子筛等产品,在化工、陶瓷、造纸、建材和皮革加工等工业领域具有重要用途.卢艳龙等[38]利用锆硅渣及氧氯化锆生产排放的废碱液为原料,通过水热—碱化反应合成硅酸钠.具体方法是:先用废碱液将酸性硅渣中和,然后经水洗得到中性二氧化硅凝胶,再在反应锅中与计量的氢氧化钠溶液进行化合反应,待反应完成后进行固液分离,最后将所得溶液进行浓缩即可获得产物.层状结晶二硅酸钠(简称层硅),其分子式为Na2Si2O5,它是一种排列规则的二维层状硅酸盐,有α、β、γ、δ 几种晶体结构形式[39].其中δ-层硅是公认的一种替代三聚磷酸钠制备无磷洗涤剂的助剂.δ-层硅与洗涤剂其他组分配伍使用时具有加工工艺简单、洗涤性能好、价格适中、污染小等特点.孙亚光、李国昌等[40-41]等利用氧氯化锆生产排放的锆硅渣和稀碱液为主要原料,以石英砂作为辅料,成功制备出层状结晶二硅酸钠,所得产品完全满足洗涤助剂的基本要求,并可达到GB/T 19421-2003标准.2.2.3 制备五水偏硅酸钠、水玻璃五水偏硅酸钠俗称速溶水玻璃,它和水玻璃都是常用的化工原料,大量应用于精细化工领域.文献[42]用氧氯化锆生产排放的锆硅渣和碱液制备五水偏硅酸钠.其采用的工艺路线为:先将氧氯化锆生产排放的稀碱液经澄清,控制悬浮物质量分数≤ 0.3% 、w(Na2O) ≥ 10%、溶液密度≥ 1.1335 g/cm3;再用稀碱液洗涤酸性锆硅渣,回收部分硅,然后经分离、热压溶解、过滤得到高硅钠比的稀水玻璃,稀水玻璃与澄清处理后的稀碱液经硅钠比调整、蒸发浓缩、结晶等步骤可制得五水偏硅酸钠;而直接蒸发浓缩稀水玻璃便可制取常规浓度的水玻璃.2.2.4 锆硅渣的其他利用除了用于制备白炭黑、硅酸钠、层状硅酸钠、五水偏硅酸钠、水玻璃外,锆硅渣还可以在其他领域进行回收利用.例如苏振等[43]以锆硅渣为主要原料,采用动态水热法合成了硬硅钙石;廖雯丽[25]利用锆硅渣采用一次反应法制备出了密度较低的硅酸钙绝热材料;宋海燕[44]和李玉寿等[45]将锆硅渣掺入混凝土,发现其可以提高混凝土的强度,且特别适宜于蒸养、蒸压养护混凝土.锆化学品因其独特的物理和化学性能在很多领域特别是在现代高科技领域得到了广泛的应用,被有关专家誉为“21世纪最有发展前途的材料之一”.但是氧氯化锆作为锆英石的初级加工产品,其附加值并不是很高.从总体上来说,当前我国氧氯化锆生产技术相对落后,能耗、污染较大,国内的氧氯化锆生产企业如果要想取得更大的发展,就必须不断的进行工艺改进和技术革新、搞好氧氯化锆下游产品的开发,尤其需要解决好氧氯化锆生产过程中锆硅渣的处理问题.。
氧氯化锆工艺

氧氯化锆工艺一、概述氧氯化锆是一种重要的陶瓷材料,具有高硬度、高强度、高耐磨性和耐腐蚀等优良性能,被广泛应用于机械制造、电子通讯、医疗器械和航空航天等领域。
本文将介绍氧氯化锆的制备工艺。
二、原材料准备1. 氧化锆:选择纯度高、粒度均匀的氧化锆作为原材料。
2. 氯化铝:选择纯度高的氯化铝作为助剂。
三、工艺流程1. 氧气预处理:将空气经过压缩机压缩后进入预处理器进行除尘和除湿处理,再通过加热器升温至300-400℃,使其中的水分和杂质得以去除。
2. 氧化锆还原:将经过预处理的氧气与粉末状的氧化锆混合后送入还原反应器中,在1000-1200℃下进行还原反应,生成粉末状的金属锆。
3. 锆粉球形化:将金属锆粉放入球形化设备中,在500-800℃下进行球形化处理,得到粒度均匀的锆粉球。
4. 氯化锆:将锆粉球放入氯化反应器中,在750-900℃下与氯化铝反应生成氧氯化锆。
5. 氧氯化锆还原:将氧氯化锆与碳混合后在高温下还原,得到纯度高的氧化锆。
四、详细工艺步骤1. 原材料准备:将选择好的氧化锆和助剂氯化铝按照一定比例混合均匀备用。
2. 氧气预处理:将空气经过压缩机压缩后进入预处理器进行除尘和除湿处理,再通过加热器升温至300-400℃,使其中的水分和杂质得以去除。
3. 氧化锆还原:将经过预处理的氧气与粉末状的氧化锆混合后送入还原反应器中,在1000-1200℃下进行还原反应,生成粉末状的金属锆。
反应条件为:H2/O2=1/1,反应时间为3-4小时。
4. 锆粉球形化:将金属锆粉放入球形化设备中,在500-800℃下进行球形化处理,得到粒度均匀的锆粉球。
球形化条件为:温度500-800℃,时间1-2小时。
5. 氯化锆:将锆粉球放入氯化反应器中,在750-900℃下与氯化铝反应生成氧氯化锆。
反应条件为:Cl2/Zr=1/1,Al/Zr=0.05/1,反应时间为6-8小时。
6. 氧氯化锆还原:将氧氯化锆与碳混合后在高温下还原,得到纯度高的氧化锆。
氯化氧锆粉晶

氧氯化锆晶体介绍
1、氧氯化锆简介
氧氯化锆是一种无机化工产品,其分子式为Cl2OZr,分子量为178.1294。
氢氧化锆盐酸法采用锆英石与烧碱熔融,漂洗、除硅之后与硫酸作用,在加入氨水,得到氢氧化锆沉淀,用盐酸溶解沉淀物,得到氯氧化锆,经蒸发浓缩、冷却结晶、晶体粉碎,制得二氯氧化锆成品。
氧氯化锆为白色针状或丝状结晶。
水溶性良好,也溶于甲醇、乙醇和醚,微溶于盐酸,不溶于其他有机溶剂。
是生产其它锆制品如二氧化锆、碳酸锆、硫酸锆、复合氧化锆以及锆铪分离制备金属锆铪的主要原料。
2、氧氯化锆理化性质
氧氯化锆名称
中文名氧氯化锆
英文名zirconyl chloride
中文别名锆ICP | 二氯氧锆
CAS号7699-43-6
密度 1.344 g/mL at 25 °C
熔点−15 °C
分子式Cl2OZr
分子量178.129
精确质量175.837
PSA 17.07
LogP 1.2602
外观性状白色潮湿晶体
储存条件阴凉通风处保存
稳定性避免强氧化剂
3、氧氯化锆生产工艺
4、氧氯化锆应用
氧氯化锆的用途广泛,除可以用作媒介染料的原料和媒染剂、定色剂、除臭剂、助燃剂等产品的添加剂,也可以用作油田底层泥土的稳定剂、工业废水的凝结处理剂等。
氧氯化锆的重要用途是作为深加工的中间原料。
用氧氯化锆直接煅烧可得工业级和高纯氧化锆、纳米超细氧化锆;添加稳定剂后可制取稳定、半稳
定氧化锆,用氧氯化锆也可以制取碳酸锆、硫酸锆、硝酸锆、氢氧化锆等含锆化学品,这些含锆化学品用途广泛。
氧氯化锆_二氧化锆_的生产及在电池中的应用前景_罗方承

2001年增刊 矿产与地质第15卷2001年10月M IN ERA L RESO U RCES A ND GEO LO GY增刊氧氯化锆(二氧化锆)的生产及在电池中的应用前景¹罗方承,吕文广,陈忠锡,黄朝辉(江西晶安高科技股份有限公司,江西安义330029)摘 要:介绍了氧氯化锆(氧化锆)的生产原理和生产工艺,阐述了该产品在镍氢动力电池负极材料(贮氢材料A B2)和燃料电池中的应用前景。
关键词:氧氯化锆;二氧化锆;贮氢材料A B2;燃料电池;应用前景;晶安高科中图分类号:T Q134.12 文献标识码:B 文章编号:1001-5663(2001)增刊-0559-041 概述锆及其化合物在国防、民品中应用越来越广[1]。
特别是在结构陶瓷和功能陶瓷方面,涉及到机械、电子、能源等领域[2][3][4][5]。
锆及其化合物的生产在我国发展不是很快,主要原因可能是原料(锆精矿主要产于南非和澳大利亚)所限制。
国内生产规模太小,20000吨/年产量的企业尚无,晶安高科15000~18000吨/年产量算是国内最大企业。
据国家“星火计划”‘“九五、十五”、“863”等攻关项目及“二十一世纪新材料丛书(宋健题)”公布:镍氢动力电池负极材料(贮氢材料AB2)和燃料电池给锆及其化合物的应用提供了一片光明前景。
高容量的AB2合金(比AB5合金容量高30%~40%)中锆的研究[6][7]应用表明,如生产3000吨AB2合金(以Ti0.5Zr0.5Ni1.3V0.7Cr0.2合金作为基准进行计算)则需要锆575吨[4]。
燃料电池中的第三代高温固体氧化物燃料电池(SOFC),最适宜的应用在大型工业电站,用稳定ZrO2做为固体电解质(加Y2O3的ZrO2),是锆化合物的一个重要用途。
是今后电能的重要发展方向[4][5]。
“零”排放的燃料电池被美国列为21世纪十大高新技术之首。
加拿大政府已决定将燃料电池产业作为国家知识经济的支柱产业之一加以发展。
氧氯化锆生产工艺

氧氯化锆生产工艺
氧氯化锆生产工艺是指将氧氯化锆合成成品氧氯化锆的一系列生产过程。
其主要步骤包括原料制备、氧氯化锆反应、沉淀和制品加工等。
首先是原料制备。
氧氯化锆的原料主要是氯化锆和氢氧化锆。
首先将氯化锆经过蒸馏、冷却等工艺步骤进行纯化。
然后将纯化后的氯化锆与氢氧化锆按一定比例混合。
接下来是氧氯化锆反应。
将混合好的氯化锆和氢氧化锆加入反应釜中,在高温高压条件下进行反应。
反应过程主要是氧化锆的氯化反应,生成氧氯化锆。
然后是沉淀。
将反应釜中得到的氧氯化锆溶液从反应釜中排出,经过沉淀处理。
通常使用饱和盐酸溶液进行沉淀,通过调节盐酸浓度和温度来实现氧氯化锆的沉淀。
最后是制品加工。
经过沉淀处理得到的氧氯化锆沉淀物经过过滤、干燥等工艺步骤,得到成品氧氯化锆。
然后按照客户需求将氧氯化锆进行加工,制成不同形状和规格的产品,如颗粒状、粉末状或块状。
总的来说,氧氯化锆生产工艺包括原料制备、反应、沉淀和制品加工等步骤。
通过这些步骤可以将氯化锆和氢氧化锆合成成品氧氯化锆,为相关行业提供优质的原料。
氧氯化锆制备工艺与应用
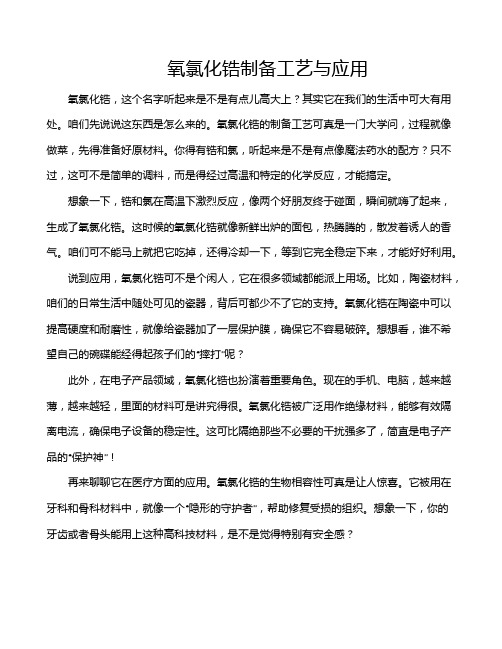
氧氯化锆制备工艺与应用氧氯化锆,这个名字听起来是不是有点儿高大上?其实它在我们的生活中可大有用处。
咱们先说说这东西是怎么来的。
氧氯化锆的制备工艺可真是一门大学问,过程就像做菜,先得准备好原材料。
你得有锆和氯,听起来是不是有点像魔法药水的配方?只不过,这可不是简单的调料,而是得经过高温和特定的化学反应,才能搞定。
想象一下,锆和氯在高温下激烈反应,像两个好朋友终于碰面,瞬间就嗨了起来,生成了氧氯化锆。
这时候的氧氯化锆就像新鲜出炉的面包,热腾腾的,散发着诱人的香气。
咱们可不能马上就把它吃掉,还得冷却一下,等到它完全稳定下来,才能好好利用。
说到应用,氧氯化锆可不是个闲人,它在很多领域都能派上用场。
比如,陶瓷材料,咱们的日常生活中随处可见的瓷器,背后可都少不了它的支持。
氧氯化锆在陶瓷中可以提高硬度和耐磨性,就像给瓷器加了一层保护膜,确保它不容易破碎。
想想看,谁不希望自己的碗碟能经得起孩子们的“摔打”呢?此外,在电子产品领域,氧氯化锆也扮演着重要角色。
现在的手机、电脑,越来越薄,越来越轻,里面的材料可是讲究得很。
氧氯化锆被广泛用作绝缘材料,能够有效隔离电流,确保电子设备的稳定性。
这可比隔绝那些不必要的干扰强多了,简直是电子产品的“保护神”!再来聊聊它在医疗方面的应用。
氧氯化锆的生物相容性可真是让人惊喜。
它被用在牙科和骨科材料中,就像一个“隐形的守护者”,帮助修复受损的组织。
想象一下,你的牙齿或者骨头能用上这种高科技材料,是不是觉得特别有安全感?氧氯化锆的魅力不仅仅局限于这些,咱们还可以在化妆品中见到它的身影。
许多护肤品中会加入氧氯化锆,起到增稠和改善肤感的效果。
用在妆容上,让妆面看起来更细腻、自然,简直是化妆品界的小秘密。
不过,制作氧氯化锆可不是随便的事儿。
工艺流程中有很多细节,比如温度、压力和时间的掌控,稍有不慎就可能前功尽弃。
就像煮面条,水开得太久,面条就会变得软绵绵的,不好吃。
而这也是氧氯化锆的制备工艺需要特别讲究的地方。
氧氯化锆的煅烧过程

氧氯化锆的煅烧过程氧氯化锆是一种常用于高温反应和材料制备的重要材料。
煅烧是氧氯化锆制备过程中的关键步骤,它能够通过改变温度、时间和煅烧气氛来调控氧氯化锆的物理和化学性质。
本文将深入探讨氧氯化锆的煅烧过程,并分享对其的理解与观点。
1. 煅烧过程的基本概念和原理在氧氯化锆的制备中,煅烧是将原料进行高温处理以形成所需氧氯化锆颗粒的过程。
通过控制煅烧温度、时间和气氛,可以影响氧氯化锆的晶体结构、晶粒尺寸、表面形貌和化学组成等性质。
煅烧过程中,原料中的杂质会被消除或转变成稳定的化合物,同时晶粒会长大并形成规整的结构。
2. 煅烧温度对氧氯化锆的影响煅烧温度是影响氧氯化锆性质的关键因素之一。
在低温下进行煅烧,氧氯化锆的晶粒会较小且分散,晶粒的表面积较大,利于提高材料的催化活性和表面反应性能。
而高温煅烧则会导致晶粒的尺寸增大和晶界结构重排,从而提高氧氯化锆的力学性能和稳定性。
3. 煅烧时间对氧氯化锆的影响煅烧时间是煅烧过程中另一个重要的影响因素。
较短的煅烧时间可能导致氧氯化锆晶粒的未充分生长,使其性能不稳定。
而过长的煅烧时间则可能导致氧氯化锆晶粒的尺寸增大过多,反而降低了材料的催化活性和表面反应性能。
选择适宜的煅烧时间是保证氧氯化锆材料性能优良的关键之一。
4. 煅烧气氛对氧氯化锆的影响煅烧气氛是指煅烧过程中环境气氛的组成,它对氧氯化锆的形成和性质也起着重要的影响。
常用的煅烧气氛有氩气、空气和氧气等。
不同气氛下的煅烧会导致氧氯化锆材料晶格中氧位的变化,从而影响其导电性、催化性能以及稳定性。
选择适宜的煅烧气氛可以实现对氧氯化锆性能的有针对性调节。
氧氯化锆的煅烧过程是制备高质量氧氯化锆材料的重要步骤。
通过调控煅烧温度、时间和气氛,可以控制氧氯化锆的物理和化学性质,进而实现对其性能的优化。
在实际应用中,熟悉氧氯化锆煅烧过程的基本原理和影响因素,对于制备出具有良好性能的氧氯化锆材料具有重要意义。
(观点和理解)在我看来,氧氯化锆的煅烧过程不仅仅是一种简单的高温处理过程,更是一门科学和艺术的结合。
氧氯化锆直接热分解制备三维有序大孑L氧化锆

氧氯化锆直接热分解制备三维有序大孑L氧化锆物理化学(WuliHuaxueXuebao)SeptemberActaPhys.一Chim.Sin.,2006,22(9):1121-1125112l[Article].ca氧氯化锆直接热分解制备三维有序大孔氧化锆沈勇邬泉周李玉光(中山大学化学与化学_T程学院,广州510275)摘要以聚苯乙烯微球胶品为模板,氧氯化锆的甲醇溶液为前驱物,通过直接热分解的方法制备了三维有序大孔氧化锆(3DOM—ZrO.);利用SEM,TEM,EDS和BET等技术对其进行了表征,并探讨了实验条件对大孔结构与形态的影响.结果表明,过低或过高的氧氯化锆浓度都不利于形成长程有序的三维大孔结构;增加填充次数只有在较高的氧氯化锆浓度下才能有效增加填充量;合适的焙烧温度在600—700℃之间;BET分析表明3DOM—ZrO孔壁具有非多孔结构,与TEM观察结果非常一致.关键词:氧化锆,聚苯乙烯微球(Ps),三维有序大孑L,胶晶中图分类号:0643ThreeDimensionalOrderedMacroporousZrO2PreparedbyDirectly CalciningZrOClzSHEN,Y ongWU,Quan—ZhouLI,Yu—Guang (SchoolofChemistryandChemicalEngineering,SunY at—senUniversity,Guangzhou510275,P.R.China) AbstractThmedimensionalorderedmacroporous(3DOM)zirconiumdioxideswithporedia metersofabout500amalesuccessfullypreparedviaadirectcalciningstep,usingamethanolsolutionofZrOCl2.81-1 20asfillingprecursorandpolystyrenesphereff,s)colloidcrystalsastemplates.Themethodofsynthesisissimple,quick erthanothersynthesis,andbasedonreadilyavailableprecursors.Precursorconcentrationandasecondfillingofthe3Dp ackedpolystyrene spheresageimportantpagametersinfinetuningthemechanicalpropertiesofthewallsandach ievinglongrangeorderedmaterials.Lowcalcinationtemperature(≤500℃)introducesimpuritiesinthewallstructureofzirconiaand crystallitephasetransformationinthecrystalstructure.Excesshighcalcinationtemperature(≥800℃)leadsthe3Dwallstructuredestroyedandcollapse.TheBETbehaviourof3DOM—ZrO2showsthatporewallhasanon—porousstructure, whichagreeswiththeTEMresults.Keywords:ZrO2,Polystyrenesphere,3DOM,Colloidcrystal维有序大~L(3DOM)材料在光子晶体,载体,催化剂,分离材料和电极材料等方面有着广泛的应用前景,引起了人们极大的关注【l-51.寻找简单易行的3DOM材料的制备方法是目前3DOM研究的热点之一.胶晶模板法工艺简单,操作容易,目前较常用,但其缺点是原料价格昂贵.Y an等人嘲以醋酸盐的乙醇或醋酸溶液为前驱物,用盐沉积及化学转化法制备了一系列三维有序大孑L材料.该方法虽然降低了原料成本,但制备过程多了一道沉淀转化步骤,操作较复杂.ZrO是工业上常用的催化剂和载体,特别是在低温下具有催化活性高的特点,有利于直链烷烃的异构化1.通常方法制备的ZrO具有微孔结构,对小分子的气相反应具有很高的催化活性.但这种微孔催化剂并不适合大分子的液相反应.虽然采用模板技术可以得到中孔ZrO,但孑L壁只是部分晶化fl】1.Received:March9,2006;Revised:May17,2006.*Correspondent,E—mail:***************:Tel:+8620-84110696⑥EditorialofficeofActaPhysico-ChimicaSinicaII22ActaP}tYs—ChimSintWtdiHuaxueXuebao).2006VOIl22如果能制备孔壁具有晶体特性的大孔ZrO则大分子反应物容易进入大孔,接触到催化活性中心,吲而大LZrO是潜在的长链直链烷烃异构化反应催化剂.目前制备大孔ZrO所用的前驱物一般是错的醇盐(如il!丙醇锆),成本比较高,不利于工业化生产.氧氯化锆是常用来制备zr的原材料,价格便宜,而H.有较高的熔点,焙烧后能分解成金属氧化物.ZrOCI?8H20在溶液中具有【z(OH)B(H/O)I的单元结构1,在甲醇或乙醇中具有极高的溶解度,有利于形成坚固的:维骨架.因而ZrOCI-8HO足制备3DOM—ZrO十分合适的前驱物.本研究以氧氯化锆的甲醇溶液为前驱物,聚苯乙烯微球胶晶为模板,通过直接热分解的方法制备了■维有序大孔氧化锆,利用SEM,TEM,EDS和BET等技术对其进行了表征+弼:探讨了实验条件对大孔结构与形态的影响.1实验部分1.1三维有序大孔Zr0:的制备聚苯乙烯微球(Ps)按文献[5]方法合成,平均直径在600nm左右.将制得的含聚苯乙烯微球的母液通过玻璃纤维过滤,除去较大的团聚体.取一定量的母液装入离心管中,在1000f?vain转速下离心l2~24h.然后去掉面的清液,置于空气中干燥2~3天即制得胶晶(colloidcrysta1)模板.将一定量的ZrOCI~.8H(AR,上海化学试剂一厂)溶解在甲醇(AR,广州化学试剂二厂)溶剂中,配制成浓度为0.67,1,0,1.2,1.6及1.8tool?L的一系列溶液,分别记为Z-I,Z.2,Z一3,Z.4及Z.5.将制好的溶液滴加到已制成的胶品模板中,浸泡3—10min,抽滤除去多余的溶液,在6(J~70℃干燥60min.然后再进行一次浸泡,抽滤,干燥过程.干燥后的样品用焙烧法除去胶晶模板.采用程序升温控制焙烧过程.在通空气的条件下,首先以2℃?min速率缓慢升温至300℃.恒温5h,再以5℃?min速率升温至4OO一800℃,恒温5h,即制得3DOM.ZrO.样品.1.23DOn-ZrO2表征大孔的形貌与结构特征用日本电子JeolJSM一6330F型场发射扫描电镜和日本Hitachi公司S-520扫描电镜(SEM)表征;L壁结构用JeolJEM2000FX(瑞典Lund大学)透射电镜(TEM)表征;晶相分析用甘本RigakuD/Max.3Ax射线粉末衍射仪(XRD)测定;BET比表面积与L径分布采用MicromeriticsASAP2400V306(瑞典Lund大学)测定.2结果与讨论2.1前驱物浓度对大孔结构的影响I虱l是不同ZrOCI!浓度((a),fb):c(ZrOCl)=0.67tool-L;(c),(d):c(ZrOCI2)=1.6mol?L)所得3DOM一图1不同ZrOCl2浓度所得3DOM-ZrO2样品的SEM图Fig.1SEMimagesof3DOM-ZrO2atdifferentZrOChconcentrationsfa),(h):c(ZrOCl267rhr,I?L.:{c),(d):c{ZrOCI):I_6tool?L;7)【w】℃:la)xSO00.(b)xl5【x]O.【c】~300~,(山xStX)0No.9沈勇等:氧氯化锆直接热分解制备三维有序大孔氧化锆1123 ZrO样品的SEM图.x8000倍的图l(a)显示三维大孔结构已经形成,但裂缝较多,致使大孔有序排列的范围不大.在~15000倍的图l(b)中,可观察到孔壁较薄,破损较多.其原因可能是前驱物浓度低,微球间隙填充量不高,焙烧时孔壁收缩引起孑L壁的破损.x3000倍的图l(c)显示,三维大孔排列有序,几乎观察不到裂缝.与图l(a)相比,大孔有序排列范围大大增加.在x8000倍的图l(d)中可观察到孔与孑L之间紧密连接,大孔完好,几乎没有破损,平均孑L径在500nm左右.右上角的单孔放大图显示孔壁较厚而且非常致密,表明微球空隙间的残留量随ZrOC1浓度的增加有了较大的提高.另外,孔下面有三个清晰可见小孔窗,分别对应下一层的三个大孔,这种结构反映了模板中微球之间的密堆积排列方式.表l列出了制备过程中各个阶段样品的质量,焙烧后残留量与胶晶的质量比()以及残留量与焙烧前干基的质量比().表中数据显示,第一次和第二次浸泡后ZrOC1在微球间隙的填充量(w1,)都随浓度的增加而增加,而且第一次浸泡的填充量()比第二次(一)的高.当浓度低于1.0mol?L时,第二次浸泡后增加的量很小,表明在较低的浓度下,增加浸泡的次数并不能有效增加填充量.当浓度达到1.8tool?L时,填充量反而减小.这可能是由于浓度较高时,粘性增加,流动性降低,使得胶晶中心部分区域得不到有效填充.相对残留量o),随ZrOC1浓度变化的趋势与填充量相似.当ZrOC1浓度在1.6mol?L左右时,残留量达到最大,o/Wps达到21.9,为l5.7,高于以正丙醇锆为前驱物时的值(13.5)ts1.这可能缘于[Zr4(OH).(H0)61脚与微球表面有较强的亲和作用.聚苯乙烯微球表面带有磺酸基,羟基及羰基, 而ZrOC1?8HO在溶液中具有[Zr4(OH)8(H2O)6]脚的单元结构,含有大量的羟基及水分子,能与微球表面上的基团以氢键的形式相作用,从而使ZrOC12?8HO容易吸附在微球表面.由此可见,以ZrOC12?8HO为前驱物,能得到较大的相对残留量,有利于形成比较致密的孔壁,因而是正丙醇锆十分合适的替代品.2.2孔壁结构与形态分析图2是在600oC下焙烧的样品z.4的透射电镜图.图2(a)显示孑L呈规则的密堆积排列,孔壁致密性好,没有缺陷.三角形区域的大小相当于边长为60 nm的等边三角形,孔壁最薄处约20llm左右.图2(b)显示,在孑L壁较厚的地方有单颗晶粒出现,其大小从10nm到50nm(见图中的圆形标记处).而在较薄的孔壁处,很少见到单独颗粒状晶粒.图2(c)显示了较薄孔壁的结构.其整齐排列的原子影像表明,较薄的孔壁由扁平状的晶体构成.晶体之间有一条明显的分界线,从原子线的排列方向可看出,分界线的两边属于不同的晶体.另外在较薄的孔壁处可观察到许多小孔,其尺寸不等,最大的可达7rim,最小的只有l~2rim.这些孔可能是由于聚苯乙烯微球表面含有一些基团导致表面不均匀而造成的.目前文献上报道的3DOM材料中具有晶体特征的孔壁一般由纳米粒子组成,其形状有颗粒状或棒状,而且当晶粒尺寸过大时难以形成大孔结构.本研究中孔壁是由平板状的晶体构成,目前未见文献报道.据文献[131报道,醇盐法和化学沉积转化法制备的3DOM.Zr02孔壁是由大小不等的纳米粒子组成,其粒径分别为28ilm及l~2ilm.平板状晶体的产生可能与前驱物ZrOC1?8HO的结构有密切关系.ZrOC|2~8H2O在溶液中具有[Zr4(OH)8(H0)6]脚的单元结构,四个锆原子在同一平面上,整个结构呈平板状.当进入到微球间隙时,特别在微球接触较紧密处,由于空间位阻效应及氢键作用,这些平板状单元表1ZrOClz-8HzO浓度与残留量的关系Table1TheeffectoftheconcentrationofZrOC12?8H20ontheresidueamountPS:polystyrenesphere;W~:theweightofPSafterthefirstfilling,W2:theweightofPSafterth esecondf'dling,Wz~z:theweightofresidueamountaftercalcinationl124AcmPhv.ChimSin(WuliHuaxueXue&w).2006图23DOM-ZrO样品(z-4)的TEM囤Fig.2TEMimagesof3DOM-ZrO2(Z-4)£fZrOCI!J=lnmill?L.丁=舢cl℃与微球表面以平行的方式附着在微球的表面.表面填满后.后续单元又会以同样方式附着在前一层的}'面.在晶化前,错原子以这种方式排列有序,因而在焙烧晶化过程中,原子的位移很小,从而形成较大的扁平状晶体.而当用醇盐法和化学沉积转化法制备时,前驱物为单体,原子在微球间隙内随机排列,品化时,形成众多品化点(或晶核),随着晶体生【∈,形成的是颗粒状晶体.2.3焙烧温度对孔壁结构与组成的影响图3足在小同焙烧温度下所得3DOM.ZrOL擘的XRD图.由图中可看到:在m℃下,孔壁晶型属于四方ZrO.SEM分析显示大孔排列有序;在500℃下焙烧所得的样品含有两种晶型(四方及单斜ZrO),表明在该温度下开始发生品型转变,SEM分析显示大tL~Ptl仍然有序;从600℃到800℃,孔壁晶型均是单斜ZrO,晶型比较稳定,没有晶相转变. SEM及TEM显示600℃及700oC焙烧的3DOM. 圈3不同焙烧温度下孔壁的xRD谱Fig.3XRDpatternsof3DOM-ZrO2calcinedat differenttemperaturesV ol22ZrO孔壁收缩不大,L道排列十分整齐.但8【)I】℃下焙烧的样品有序范围不大.出现较大的孔洞,L径在400~450nm之间,孔壁收缩较大说明过高的温度会导致孔道的过度收缩,从而使得L壁崩溃,破坏了大孔的长程有序排列.电子能谱分析表明,在400,500和600℃下焙烧所得样品中氯的摩尔分数分别为13.86%,6.00%和310%.表明在低于500oC 的温度F焙烧,ZrOCI分解不完全,所得3DOM. ZrO中氯的摩尔分数高当焙烧温度高于600oC时, 分解基本完成,氯的摩尔分数也有了大幅度降低,由此可见.较适宜的焙烧温度应该在600~70(3℃. 2.4样品的比表面及孔径分布图4是3DOM.Zro2孔壁的BET吸附等温线,为典删的lv型.从图中可以看到,在很低P.值下曲线出现拐点,而且在很大的p慨值范嗣,吸附体积缓慢增加,这些表明3DOM.ZrOL壁中孔径较小.实验测得的3DOM—ZrO.的比表面积仅为图43DOM-ZrO2N2吸附等温线Fig.4Nitrogenadsorptionisothermsof3DOM-ZrO2NO.9沈勇等:氧氯化锆直接热分解制备三维有序大孔氧化锆1125 图5孔面积(a)和体积(b)与孔径关系图Fig.5Plotsofporearea(a)andvolume(b)105porediameterof3DOM-Zr02 23mz?g~,说明3DOM—ZrO孔壁为非多孔性.这些结果与在TEM下观察到的具有平板状晶体的孑L壁结构非常吻合.另外,在图4中还可看到脱附曲线与吸附曲线不一致,出现了滞后回线,说明孔壁中有一定的中孔存在.从孔面积一孔径关系图(图5(a))中看到,孔径在2—4nm范围孔贡献较大的表面积,表明这一范围的孔有较大的分布.这些孔可能属于孔壁中平板状晶体上的小孔.从TEM图(图2c)上观察,晶体上小孔尺寸在l一7nm之间,与BET测定的结果相一致.吸附过程的孔体积一孔径分布曲线(图5(b))显示,孔径在6—20nm的孔占有较大体积,这部分孔可能是孔壁中较大晶粒堆积所形成.100—300nm之间的孔可能属于大孔之间的小孔窗.3结论本研究以氧氯化锆的甲醇溶液代替常用的醇锆作为前驱物,以聚苯乙烯微球胶晶为模板,通过直接热分解的方法制备了三维有序大孑L氧化锆.与传统方法相比,该方法具有原料价格低廉,方法简单等特点,容易规模化生产.而且焙烧后ZrO残留量与用丙醇锆为前驱物时的残留量相当,说明氧氯化锆是丙醇锆十分合适的替代品.探讨了实验条件对三维大孑L结构与形态的影响,得到了制备3DOM.ZrO适宜前驱物浓度,填充次数及焙烧的温度范围,并对3DOM—ZrO孔壁的孔道特性进行了BET表征.这些实验结果为大规模生产3DOM.ZrO提供了有意义的基础数据.ReferenceslImhof,A.;Pine,D..,-Nature,1997,389:9482V elev,0.D.;Jede,T.A.;Lobo,R.F.;Lenhoff,A.M.Nature, 1997,389:4473Zakhidov,A.A.;Baughman,R.H.;Iqbal,Z.;Cui,C.X.; Khayrullin,I.;Dantas,S.0.;Marti,I.;Ralchenko,V.G.Science, 1998,282:8974Holland,B.T.;Blanford,C.F.;Stein,A.Science,1998,281:5385Holland,B.T.;Blanford,C.F.;Do,T.;Stein,A.Chem.Mater., 1999,11:7956Y an,H.;Blanford,C.F.;Holland,B.T.;Smyrl,W.H.;Stein,A. Chem.Mater.,2000,12:l1347Bell,A.T.;Manzer,L.E.;Chen,N.Y.;Weekman,V.W.;Hegedus, L.L.;Pereira,C.J.Chem.Eng.Prog.,199S,91:268Song,X.;Sayari,A.Cata1.Rev.-Sci.Eng.,1996,38:3299Arata,K.Adv.Cata1.,1990,37:16510Mercera,P.D.L.;vanOmmen,J.G.;Doesburg,E.B.M.; Burggraaf,A.J.;Ross,J.R.H.App1.Cata1.,1990,57:127 llHuang,Y.Y.;McCarthy,T.J.;Sachtler,W.M.H.App1.Cata1.A, 1996,148:13512Cong,Y.;Liang,D.B.;Lin,P.Z.;Lin,L.W.FuelChem.Tech.. 1998,26:230[丛昱,梁东白,林培滋,林励吾.燃料化学学报(RanliaoHuaxueXuebao),1998,26:23013Schroden,R.C.;AI-Daous,M.;Blandford,C.F.;Stein,A.Chemo Mater.,2002,14:3305。
10000 吨氧氯化锆生产工艺的改进研究和经济效益分析

10000 吨氧氯化锆生产工艺的改进研究和经济效益分析摘要: 通过对晶安高科万吨氧氯化锆生产工艺的研究改进, 在生产中取得较好的经济效益, (1) 洗渣中二氧化锆回收率提高; (2) 用于洗涤硅渣的工业盐酸的加入量减少, 减少了酸雾对环境的污染; (3) 水转料中二氧化硅含量降低了, 氧氯化锆的使回收率提高了; (4)水转料中氧化钠含量降低了, 产品质量得到提高; 二次废酸的使用周期延长。
关键词: 生产工艺; 氧氯化锆工艺; 研究; 经济效益1概述氧氯化锆是制备锆化合物的一种重要中间产品, 其锆化合物已被广泛用于实际生活中, 锆英砂制备氧氯化锆有四种方法: 两酸两碱法、一酸一碱法、石灰法、氯化法。
其中两酸两碱法已不被企业采用, 一酸一碱法成为生产的主流。
我公司在吸收XX大学和有色金属研究总院二单位工艺优点的基础上加以改进, 先后进行了从实验室、生产中试到产业化生产一系列攻关研究。
对生产工艺中一些重要工序进行进一步完善和改进, 经数月的中试和生产验证, 取得较满意效果。
回收率提高到82%(其他企业为74% ); 杂质降低(Fe2O3 10×10-6、Na2O 15×10-6以下, 其他企业为: Fe2O3 30×10-6、Na2O 50×10- 6) ; 盐酸单耗较其他企业少0.8吨左右; 生产效率高; 废碱液、硅渣、挥发氯化氢得到合理利用并取得一定经济效益, 成为国内同行业中最佳生产工艺流程。
2氧氯化锆生产工艺简介一酸一碱法工艺流程如下图1。
3重点改进的工序简介经对工艺多次、多因素试验, 结果表明, 最有突破的且能取得很好经济效益的是“水洗转型”工序和“硅渣洗涤”工序(即逆流洗涤工艺)。
其他试验已有验证, 不再重复。
本研究重点对以上两工序作了大量工作。
水转工序其主要目的是除硅、钠, 是整个工艺的主要工序, 关系到锆的回收率和二次废酸的循环利用, 因为每公斤二氧化硅产生十公斤的硅渣, 且吸附大量的锆,在弃置的硅渣中流失。
氧氯化锆的生产、应用和贸易

43
锆英石
烧碱
废碱水
滤饼
酸性废硅渣
锆母液
—r
氧氯化锆
图2.碱熔法生产氧氯化锆工艺流程图
ZrSi04+6NaOH—Na2Zr03+Na4Si04+3H20 (3)
Na2Zr03+4HCl一ZrOCl2+2NaCI+2H20
(4)
3.贸易
氯氧化锆是重要的锆盐基础化工产品,也是锆行业主要的出口产品,主要出口到美国、日本、 欧洲等国家和地区。2007年我国氧氯化锆出口量已经超过了5万吨,并且出口量量逐年增加。表1为 近三年我国氧氯化锆的出口情况。
(2)
洗出可溶性杂质,得水洗料,用行水洗料的盐酸进酸浸、浓缩、结晶、重结晶得成品八水氧氯 化锆。由于石灰的纯度较低,使得氧氯化锆中杂质含量偏高,限制了氧氯化锆使用范围。目前,石 灰法生产氧氯化锆工艺已经被淘汰。
2.2氯化法 氯化法分为固定床氯化法和沸腾氯化法。固定床氯化法在我国只有一家采用,沸腾氯化法是国
2008年错行业大会论文集
氧氯化锆的生产、应用和贸易
蒋东民1,张建东2 浙江产华拜克生物股份有限公司,2北京有色金属研究总院)
摘要:氯氧化锆是制备锆化学制品和金属锆锆的重要中间产品,本文介绍了氯氧化锆在复合材 料、锆英石基陶瓷色料新能源材料、原子能级锫铪等方面的应用、生产和贸易情况。
- 1、下载文档前请自行甄别文档内容的完整性,平台不提供额外的编辑、内容补充、找答案等附加服务。
- 2、"仅部分预览"的文档,不可在线预览部分如存在完整性等问题,可反馈申请退款(可完整预览的文档不适用该条件!)。
- 3、如文档侵犯您的权益,请联系客服反馈,我们会尽快为您处理(人工客服工作时间:9:00-18:30)。
氧氯化锆工艺介绍
氧氯化锆工艺介绍
引言:
在当今科技发展迅猛的时代,氧氯化锆(ZrOCl2)作为一种重要的无机化合物,在各种工业领域中具有广泛的应用。
本文将深入探讨氧氯化锆的工艺过程,包括制备方法、反应机理、应用领域等多个方面。
1. 氧氯化锆的制备方法:
(1)氧化锆和氯化铵反应法:将氧化锆和氯化铵按一定比例混合,加热至一定温度,反应生成氧氯化锆,并通过加水蒸氨处理获得纯净的氧氯化锆。
(2)氯化锆和氧气反应法:将氧化锆和氯化锆按一定比例混合,通入氧气,在高温条件下反应生成氧氯化锆。
(3)还原法:将氯化锆和还原剂如氢气或金属锌按一定比例混合,进行还原反应生成氧氯化锆。
2. 氧氯化锆的反应机理:
氧氯化锆的反应机理主要是氯化锆分子与氧气、水蒸氨等反应生成氧氯化锆。
在氯化锆和氧气反应中,氧气会被氯化锆分子氧化成氧氯化锆,而氯化锆会发生还原反应生成氧气。
氧氯化锆的反应机理还与温度、压力、反应物浓度等因素密切相关。
3. 氧氯化锆的应用领域:
(1)催化剂:氧氯化锆可作为高效的氧化催化剂,广泛应用于有机合成反应中。
它可催化醇的氧化反应、烯烃环氧化反应等。
(2)陶瓷工业:氧氯化锆作为陶瓷材料的添加剂,能够提高材料的机械性能、化学稳定性和热稳定性,广泛应用于陶瓷制品生产中。
(3)电子材料:氧氯化锆具有优良的电介质性能和特殊的储能特性,因此可用于制备电容器、电子陶瓷材料等。
(4)生物医学领域:氧氯化锆在生物医学领域中具有重要应用,可以作为成骨材料、人工关节材料等。
4. 对氧氯化锆的观点和理解:
氧氯化锆的制备方法多样,可以选择适合不同需求的方法进行制备。
氧氯化锆在催化剂、陶瓷工业、电子材料和生物医学领域的应用广泛,体现了它的多功能性和优越性能。
然而,要进一步提高氧氯化锆的制
备方法和应用性能,仍需要进行更深入的研究和探索。
总结:
氧氯化锆是一种重要的无机化合物,在各个领域中具有广泛的应用。
本文深入探讨了氧氯化锆的制备方法、反应机理和应用领域,对于从
简到繁、由浅入深地理解氧氯化锆发挥了重要作用。
透过对氧氯化锆
的研究,我们可以更全面、深入地认识它在催化剂、陶瓷工业、电子
材料和生物医学领域的应用潜力,并为进一步开发和改进氧氯化锆的
制备方法和应用提供了思路和借鉴。