苎麻、毛丝、化学纤维的前处理
纤维的表面处理方法

纤维的表面处理方法
纤维的表面处理方法主要有以下几种:
1. 蒸汽爆破法:在高温高压情况下,使高压下的蒸汽瞬间进入天然纤维内部,并在短时间内释放压力,使纤维原料分裂成细纤维束。
同时使纤维的结构破坏,纤维分子内氢键被打断。
2. 热处理法:是一种绿色环保的方法,该方法的目的是减少天然植物纤维中的水分。
同时,天然纤维中含有的羟基也会通过热处理减少,从而使天然植物纤维与树脂基体有良好的结合性能。
其方法主要是把纤维置于设定好温度的烘箱内一段时间,从而改变纤维晶体结构的取向与规整度。
3. 拉伸法:通过机械手段改变纤维的分子结构和形态,使纤维表面产生高分子排列或改变排列方向的方法。
这种方法在改善纤维的尺寸稳定性和防止开裂方面具有较好的效果。
但是,拉伸法需要专业的设备和技术,因此成本较高。
4. 筛分法:通过筛分或离心等物理方式分离出具有一定长度和直径范围的纤维段,以减小纤维的粗细不均和结构松散程度。
这种方法比较简单易行,但只能改善部分纤维的性质。
以上是纤维的表面处理方法的相关信息,供您参考。
8.第八章 其他织物及纱线的前处理

H2O2
精练剂 去油剂
7g/L
1 g/L 0.5 g/L
氧漂稳定剂
柔软剂
1 g/L
2 g/L
5、亚氯酸钠漂白 亚氯酸钠的漂白可用浸漂法和汽蒸法。 (四)丝光
棉针织物丝光具有一般织物丝光的优点外,还能防止单 面针织物产生卷边和使织物表面平滑,改进手感等特有的 优点。棉针织物丝光所采用的设备有圆筒状丝光机和开幅 丝光机。 1、丝光工序安排 棉针织物丝光可分为坯布丝光、先漂后丝和先丝后漂。
一种是先经次氯酸钠漂白,然后经水洗后即进行过氧 化氢漂白。这种方法简称氯氧联漂;
另一种工艺为先经次氯酸钠漂白全过程后,再进行过 氧化氢漂白。这种方法简称氯氧双漂。
4、碱—氧一浴练漂法(短流程前处理工艺) 用传统的煮、漂工艺时间长、效率低、设备占地大。 碱—氧一浴 练漂法是将烧碱与双氧水同浴处理棉针织物,使煮练和漂白同时完 成的一种新型练漂工艺。 缩短棉针织物的前处理加工过程,具有减少加工时间和设备,节约 能源,降低劳动强度等优点,因此是练漂加工的发展方向。 工艺处方: NaOH(36°Be) 3g/L
1、过氧化氢漂白
(1)煮布锅漂白法:煮布锅漂白为间歇式漂白法。 漂白液的组成如下: 过氧化氢(100%) 3~4g/L 硅酸钠(密度1.4) 6~8g/L 30%烧碱(36°Bé ) 0~3g/L 润湿剂 0.5~3g/L 漂白的工艺条件如下: pH值 10.5~11 温度 95~100℃ 浴比 1︰5~6 时间 150~180min 漂后将漂液放去,并立即用60~80℃热水洗涤,以 防止硅酸钠残留在织物上,最后用冷水洗净后出锅。
漂白的工艺条件如下: 浸轧液pH值 浸轧温度 轧余率 汽蒸温度 汽蒸时间
10.5~11 80~95℃ 130%~200% 95~100℃ 90~120min
棉、毛、丝、麻纺纱工艺比较
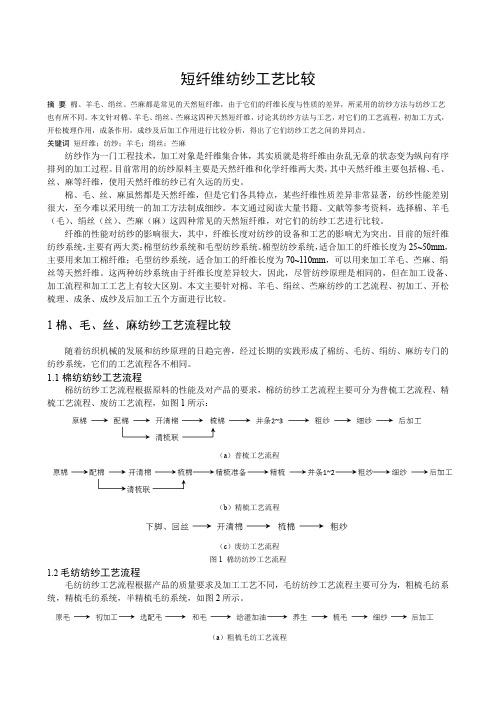
短纤维纺纱工艺比较摘要棉、羊毛、绢丝、苎麻都是常见的天然短纤维,由于它们的纤维长度与性质的差异,所采用的纺纱方法与纺纱工艺也有所不同。
本文针对棉、羊毛、绢丝、苎麻这四种天然短纤维,讨论其纺纱方法与工艺,对它们的工艺流程,初加工方式,开松梳理作用,成条作用,成纱及后加工作用进行比较分析,得出了它们纺纱工艺之间的异同点。
关键词短纤维;纺纱;羊毛;绢丝;苎麻纺纱作为一门工程技术,加工对象是纤维集合体,其实质就是将纤维由杂乱无章的状态变为纵向有序排列的加工过程。
目前常用的纺纱原料主要是天然纤维和化学纤维两大类,其中天然纤维主要包括棉、毛、丝、麻等纤维,使用天然纤维纺纱已有久远的历史。
棉、毛、丝、麻虽然都是天然纤维,但是它们各具特点,某些纤维性质差异非常显著,纺纱性能差别很大,至今难以采用统一的加工方法制成细纱。
本文通过阅读大量书籍、文献等参考资料,选择棉、羊毛(毛)、绢丝(丝)、苎麻(麻)这四种常见的天然短纤维,对它们的纺纱工艺进行比较。
纤维的性能对纺纱的影响很大,其中,纤维长度对纺纱的设备和工艺的影响尤为突出。
目前的短纤维纺纱系统,主要有两大类:棉型纺纱系统和毛型纺纱系统。
棉型纺纱系统,适合加工的纤维长度为25~50mm,主要用来加工棉纤维;毛型纺纱系统,适合加工的纤维长度为70~110mm,可以用来加工羊毛、苎麻、绢丝等天然纤维。
这两种纺纱系统由于纤维长度差异较大,因此,尽管纺纱原理是相同的,但在加工设备、加工流程和加工工艺上有较大区别。
本文主要针对棉、羊毛、绢丝、苎麻纺纱的工艺流程、初加工、开松梳理、成条、成纱及后加工五个方面进行比较。
1棉、毛、丝、麻纺纱工艺流程比较随着纺织机械的发展和纺纱原理的日趋完善,经过长期的实践形成了棉纺、毛纺、绢纺、麻纺专门的纺纱系统,它们的工艺流程各不相同。
1.1棉纺纺纱工艺流程棉纺纺纱工艺流程根据原料的性能及对产品的要求,棉纺纺纱工艺流程主要可分为普梳工艺流程、精梳工艺流程、废纺工艺流程,如图1所示:(a)普梳工艺流程(b)精梳工艺流程(c)废纺工艺流程图1 棉纺纺纱工艺流程1.2毛纺纺纱工艺流程毛纺纺纱工艺流程根据产品的质量要求及加工工艺不同,毛纺纺纱工艺流程主要可分为,粗梳毛纺系统,精梳毛纺系统,半精梳毛纺系统,如图2所示。
苎麻织物的酶退煮前处理工艺

印染(2008No.7)删mcdfn.170111.cn苎麻织物的酶退煮前处理工艺朱俊萍(河北科技大学,河北石家庄050018)摘要:分析了酶退煮二浴法和一浴法各工艺因素对处理苎麻织物效果的影响。
测试处理后织物的毛效、自度、断裂强力、强降率、失重率和手感等指标表明,二浴法效果优于一浴法,精练酶301L一浴法退煮工艺较碱退煮强降小,且节能环保。
关键词:退浆;煮练;酶;苎麻织物中图分类号:TSl92.52文献标识码:B文章编号:1000—4017(2008)07—0018—03DesizingandscouringoframiefabricwithenzymesZHUJun・pingIHebeiUniversityofScience&Technology。
Shijiazhuang050018.蕊iM)Abstract:Thedesizingandscouringprocessesoframiefabricwithenzymeswerecarriedoutinonebathandtwobathrespec-tively.Variousfactorsexertinginfluenceswerediscussed.Propertiesofcapillaryeffect.whiteness.breakingstrength.weightlossandsoftnessweretested.Itwasfoundthatramiefabrictreatedwithtwo-bathprocesshadsuperiorresultstothatwithonebathprocess.Onebathprocesswithsouringenzyme301Lcouldimpartramiefabricbetterstrengthretentioncomparedtothatwithconventionalalkalitreatment.Desizingandscouringwithenzymewasbenefitforenvironmentalprotection.Keywords:desizing;scouring;enzyme;ramiefabric目前,苎麻织物的退浆和煮练普遍采用高温强碱前处理工艺,不仅蒸汽消耗量大,而且大量排放强碱性废水,污染生态环境,影响人体健康。
麻纤维

第一节 苎麻脱胶及前处理
一、苎麻化学脱胶工艺
• 苎麻中含有大量杂质,其中以多糖胶状物质为主, 绝大部分要求在纺纱前去除。纺纱前将韧皮中的 胶质去除,并使苎麻的单纤维相互分离,这一过 程就称为脱胶。目的是经过脱胶,除去生麻中含 有的胶质和其他杂质,制成柔软、松散的熟麻纤 维. 脱胶有微生物(细菌)脱胶和化学脱胶两种方法。
麻纤维制品的前处理
麻纤维
• 苎麻与棉同属于纤维 素纤维,但在物理结 构和性质上与棉比较 有较大的差异,同时 两者在含杂方面有很 大的不同。
• 苎麻纤维素含量较棉低,除含有原棉中所 具有的主要杂质如果胶物质、油蜡等外, 还含有少量木质素,同时纤维中杂质的含 量和各种杂质间的比例,随着品种的不同, 有着较大的变动,因此,麻类的前处理较 棉困难,具有独特之处。
• 亚硫酸钠: • ①亚硫酸钠中的SO32-为一个反应性基团, 可与木质素反应生成木质素磺酸而溶于水, 具有去除木质素的作用 • ②亚硫酸钠具有一定的还原性,在煮练液 中加入亚硫酸钠有利于去除煮练液中的氧 气,防止纤维素纤维的氧化 返
• 表面活性剂: • 促进碱液的渗透、扩散和乳化作用。加快 煮练速度,提高纤维脱胶的均匀度和提高 纤维质量。常用的表面活性剂有肥皂、渗 透剂、磷酸三钠、三聚磷酸钠等
返
3.后处理 3.后处理
目的: 目的: a)进一步清除残留杂质,使纤维柔软、松散、 分离,以提高其可纺性 b)改善纤维的色泽及表面性能 工艺: 工艺:打纤、酸洗、水洗、漂白、精练、给油和烘 干等
后处理工艺
1)打纤 1)打纤
打纤又称敲麻(拷麻):它是利用机械的槌击和水的喷洗作用,将 已被碱液破坏的胶质从纤维表面清除掉,使纤维相互分离而变得松散、 柔软
(一)常用的脱胶工艺
第三章_纺织品前处理(第二稿)

第三章纺织品的前处理前处理是纺织品整个染整加工的第一道工序。
前处理的目的是去除纤维上所含的天然杂质以及在纺织加工中所施加的浆料和沾上的油污等,使纤维充分发挥其优良品质,并使织物具有洁白、柔软的性能和良好的渗透性,以满足服用要求,并为染色、印花、整理提供合格的半成品。
棉织物的前处理,包括原布准备、烧毛、退浆、煮练、漂白、开幅、轧水、烘干和丝光工序,以去除纤维中的果胶、蜡质、棉籽壳和浆料等杂质,提高织物的外观和内在质量。
苎麻织物的前处理,包括苎麻纤维的脱胶和苎麻织物的煮练、漂白,以去除果胶等杂质。
羊毛的前处理,包括选毛、洗毛和炭化工序,以去除羊毛纤维中的羊脂、羊汗、尘土和植物性杂质。
丝织物前处理,以脱胶为主,去除生丝中的大部分丝胶、色素和其它杂质。
化学纤维织物不含有天然杂质,只有浆料、油污等,因此前处理工艺较简单。
对于混纺和交织织物的前处理,要满足各自前处理加工的要求。
绒类织物、色织物和针织物的前处理主要去除杂质,其工艺与一般棉织物前处理既有相似之处,又有其各自的特殊要求。
第一节棉织物的前处理一、原布准备纺织厂织好的布称原布或坯布,原布准备是染整加工的第一道工序。
原布准备包括原布检验、翻布(分批、分箱、打印)和缝头。
(一)原布检验原布在进行前处理加工之前,都要经过检验,发现问题及时采取措施,以保证成品的质量和避免不必要的损失。
由于原布的数量很大,通常只抽查10%左右,也可根据品种要求和原布的一贯质量情况适当增减。
检验内容包括物理指标和外观疵点两方面,前者包括原布的长度、幅宽、重量、经纬纱细度和密度、强力等指标;后者主要是指纺织过程中所形成的疵病,如缺经、断纬、跳纱、油污纱、色纱、棉结、斑渍、筘条、稀弄、破洞等。
一般对漂布的油污,色布的棉结、筘条和密路要求较严,而对花布,由于其花纹能遮盖某些疵病,因此外观疵病要求相对低一些。
(二)翻布(分批、分箱、打印)为了便于管理,常把同规格、同工艺原布划为一类加以分批分箱。
生化物化组合工艺处理苎麻脱胶废水
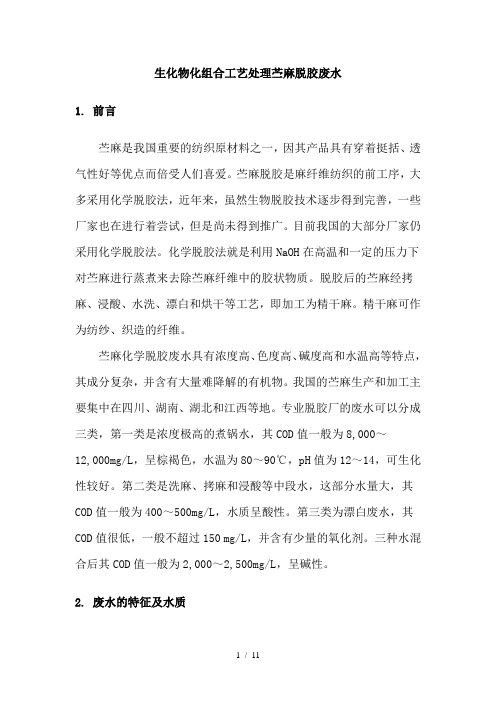
生化物化组合工艺处理苎麻脱胶废水1. 前言苎麻是我国重要的纺织原材料之一,因其产品具有穿着挺括、透气性好等优点而倍受人们喜爱。
苎麻脱胶是麻纤维纺织的前工序,大多采用化学脱胶法,近年来,虽然生物脱胶技术逐步得到完善,一些厂家也在进行着尝试,但是尚未得到推广。
目前我国的大部分厂家仍采用化学脱胶法。
化学脱胶法就是利用NaOH在高温和一定的压力下对苎麻进行蒸煮来去除苎麻纤维中的胶状物质。
脱胶后的苎麻经拷麻、浸酸、水洗、漂白和烘干等工艺,即加工为精干麻。
精干麻可作为纺纱、织造的纤维。
苎麻化学脱胶废水具有浓度高、色度高、碱度高和水温高等特点,其成分复杂,并含有大量难降解的有机物。
我国的苎麻生产和加工主要集中在四川、湖南、湖北和江西等地。
专业脱胶厂的废水可以分成三类,第一类是浓度极高的煮锅水,其COD值一般为8,000~12,000mg/L,呈棕褐色,水温为80~90℃,pH值为12~14,可生化性较好。
第二类是洗麻、拷麻和浸酸等中段水,这部分水量大,其COD值一般为400~500mg/L,水质呈酸性。
第三类为漂白废水,其COD值很低,一般不超过150 mg/L,并含有少量的氧化剂。
三种水混合后其COD值一般为2,000~2,500mg/L,呈碱性。
2. 废水的特征及水质该苎麻纺织厂排放的水质情况见表1和表2。
处理后水质要求达到GB8978-1996《污水综合排放标准》的二级标准,具体参数见表3。
3. 工艺工艺的选择处理苎麻脱胶废水的典型工艺有厌氧-好氧(活性污泥)工艺、生物转盘工艺和氧化沟工艺等,上述处理工艺虽然有一定的效果,但是随着人们对周围水体的环境质量要求越来越高,排放污染物质的控制指标(如COD、BOD)也越来越严,这种处理远远达不到目前的环境要求。
我们经过研究和多次试验得出结论:单纯的生化或物化工艺处理脱胶废水均有一定的效果,但是不能达标排放,而且处理效果不稳定,运行费用也居高不下,因此我们在一家苎麻纺织厂的废水设施改造中采用了“生化-物化”组合工艺,该工艺具有耐冲击负荷、运行稳定、易于管理和运行费用低等优点。
纤维处理

麻纤维短麻纤维表面处理:KH550处理:将KH550和无水乙醇按1:1比例配成溶液,将短亚麻纤维浸入混合溶液处理30 min,取出,在80℃烘箱中干燥至恒重备用。
NaOH处理:将NaOH配成2%水溶液,将短亚麻纤维浸入NaOH水溶液处理30 min,取出,在80℃烘箱中干燥至恒重,备用。
短亚麻纤维/PLA复合材料制备:将PLA、短亚麻纤维(将长亚麻纤维剪为长度≤5 mm)在80℃烘箱中干燥6 h后,取出,按一定配比加入高速混合机混合,然后用双螺杆挤出机挤出造粒,挤出温度140~160℃。
将切好的粒子在80℃烘箱中干燥8 h后,注塑成标准样条以备测试。
为了消除加工过程对实验结果的影响,将纯PLA用相同条件挤出加工。
剑麻纤维用质量分数为18%的常温NaOH对剑麻浸泡处理3h1.将梳理整齐的长剑麻纤维用纤维切割机切成10mm长的短纤维。
2,配制一定质量分数为18%的氢氧化钠溶液。
由于氢氧化钠的溶解属于放热过程,因此需要等溶液的温度降至室温后,再将短切后的纤维浸泡在氢氧化钠溶液中,处理时间为3h,;3.将经碱处理的剑麻纤维用蒸馏水洗至中性,散开风干后备用。
复合材料的制备1.原料的干燥。
分别将未改性处理的剑麻纤维,碱处理剑麻纤维在50度温度下的恒温鼓风干燥箱中干燥5h,聚乳酸粒料在50度温度下干燥8h2.开炼共混。
开炼机双辊温度设置为180度,预热1h,按照纤维质量分数为10wt%、20wt%、30wt%和40wt%分别称取上述干燥后的改性剑麻纤维和聚乳酸粒料。
调整开炼机转速5r/min,将称取的聚乳酸粒料在开炼机上完全熔融后,均匀加入相应的剑麻纤维,调整转速为25r/min,然后翻料共混5-6min,使剑麻和聚乳酸基体充分混合均匀。
3.预压。
将开炼后的共混物趁热预压成5-6mm厚的片材,备用。
4.热压成型。
将上述预压共混物在平板硫化机上经预热2-3min,反复泄压加压放气1min,除去复合材料熔体中的气泡,保压5-6min,后冷却成型,分别制得尺寸为160mm*80mm*4mm和160mm*80mm*1mm的复合板材,成型温度为185度,压力为10Mpa5.竹纤维本试验共制作了竹纤维体积分数分别为30%、40%、50%、60% 和70% 的五种竹原纤维/PLA 复合材料。
苎麻脱胶实验报告

苎麻脱胶实验报告苎麻脱胶实验报告一、引言苎麻是一种具有悠久历史的植物,其纤维被广泛用于纺织、造纸等领域。
然而,在利用苎麻纤维之前,需要对其进行脱胶处理,以去除纤维表面的胶质物质,从而提高纤维的质量和可用性。
本实验旨在探究苎麻脱胶的最佳方法和条件,并对脱胶后的苎麻纤维进行分析。
二、实验方法1. 原料准备:收集新鲜的苎麻植株,并将其晾干至含水量在10%左右。
2. 脱胶方法:采用热水脱胶法和化学脱胶法进行对比实验。
a) 热水脱胶法:将苎麻纤维与适量的水放入容器中,加热至沸腾,保持一段时间后取出。
b) 化学脱胶法:将苎麻纤维与适量的碱性溶液(如氢氧化钠溶液)浸泡,保持一段时间后取出。
3. 纤维分析:对脱胶后的苎麻纤维进行形态学和物理性能的分析。
a) 形态学分析:使用显微镜观察纤维的形态特征,如长度、直径等。
b) 物理性能分析:测量纤维的强度、断裂伸长率等指标。
三、实验结果与讨论1. 脱胶效果比较:a) 热水脱胶法:经过热水脱胶处理后,苎麻纤维表面的胶质物质明显减少,纤维变得更加清洁,但纤维长度有所缩短。
b) 化学脱胶法:化学脱胶法能够更彻底地去除苎麻纤维表面的胶质物质,纤维长度相对保持较好,但可能会对纤维的物理性能产生一定影响。
2. 形态学分析:a) 热水脱胶法:显微镜观察显示,经过热水脱胶处理后的苎麻纤维表面光滑,纤维断面呈圆形或椭圆形,直径较均匀。
b) 化学脱胶法:化学脱胶法处理后的苎麻纤维表面更加光滑,纤维断面呈圆形,直径较均匀。
3. 物理性能分析:a) 热水脱胶法:经过热水脱胶处理后的苎麻纤维强度略有下降,断裂伸长率也有所降低。
b) 化学脱胶法:化学脱胶法处理后的苎麻纤维强度和断裂伸长率相对较好,但仍略有下降。
四、结论通过对苎麻脱胶实验的研究,可以得出以下结论:1. 热水脱胶法和化学脱胶法都能有效去除苎麻纤维表面的胶质物质,但化学脱胶法效果更好。
2. 脱胶后的苎麻纤维在形态学和物理性能上都有一定的变化,但整体质量仍然较好。
麻织物前处理—麻纤维脱胶
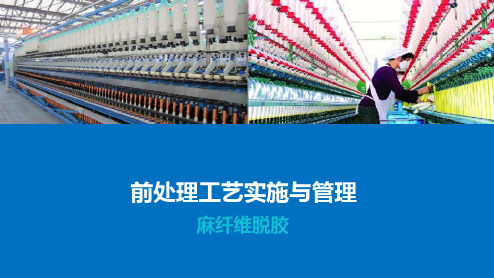
麻纤维脱胶
请在此处插入小标题
苎麻的韧皮中有纤维素、胶质、木质素、蜡 状物质等物质。其中,胶质大都包围在纤维的 表面,把纤维素的单纤维胶合在一起而形成原 麻。所以原麻纤维比较粗硬,不适合纺纱,纺 纱前必须将韧皮中的胶质去除,使苎麻的单纤 维相互分离,这一过程就称为脱胶。苎麻的脱 胶一般可采用化学脱胶方法。
(2)碱液煮练。与棉纤维相比,由于苎麻原麻中杂质含量高,所以煮练时耗碱 量较大。而且,为了降低杂质在煮练液中的浓度,提高煮练效果,煮练时的浴比 也较大。采用烧碱去除原麻中的绝大部分胶质这是苎麻化学脱胶中的残留杂质,使纤维柔软、 松散、相互分离,以提高其可纺性,还可改善纤维的色泽及表 面性能,包括:1)打纤;2)酸洗:1~2g/L的稀硫酸,室温; 3)水洗;4)漂白:有效氯浓度为1~1.5g/L,室温,时间30 ~45min,pH值为9~11;脱氯:酸1.5~2.5g/L,常温,时间 为3~5min;5)精练:肥皂、合成洗涤剂等煮2~6h;6)给油 :少量;(7)脱水、烘干:要均匀,不要急烘。
纺中、高特(中、低支)纱,但这种纱不能用作高档产品。具体流程 如下:原麻拆包、扎把→预浸(水浸、浸酸、预氯)→水洗→一次煮 练→水洗→二次煮练→打纤及水洗→酸洗—→水洗→脱水—→给油— →脱水—→烘干。
化学脱胶工艺中各工序的作用(1)预处理工序1)拆包、扎把:逐包解开,检验 ,扎束;2)预浸:包括水浸、浸酸、预氯等几种方法,去除原麻中的部分胶质,减 轻煮练负担,降低碱液消耗,提高煮练效果,并改善精干麻的质量。
常用的脱胶工艺举例(1)一煮法。该法工艺简单,生产的产品适
合于纺制低支纱,以用于生产麻线。具体流程如下: 原麻拆包、 扎把→预浸(水浸、浸酸、预氯)→水洗→碱液煮练→水洗→打纤及 水洗→酸洗→水洗→脱水→给油→脱水→烘干。(2)二煮法。该工 艺的特点是工艺比较简单,精干麻的质量比一煮法有所提高,适用于
苎麻面料的洗涤方法

苎麻面料的洗涤方法
苎麻面料的洗涤方法如下:
1. 在洗涤苎麻面料之前,先检查衣物上是否有任何特殊标志或标签。
遵循洗涤说明。
2. 最好是手洗苎麻面料。
在温水中加入适量的温和洗涤剂,搅拌均匀。
3. 将苎麻衣物放入洗涤液中,轻轻搓洗。
避免强烈的搓揉或扭转面料,以免损坏纤维。
4. 如果面料上有顽固的污渍,可以在洗涤液中加入适量的氧化剂或漂白剂进行浸泡。
注意遵循产品说明,避免过度浸泡。
5. 冲洗衣物时,避免使用过热的水,以免影响面料的质地。
最好使用温水彻底冲洗,直到水清澈为止。
6. 轻轻挤去多余的水分,避免扭转或搓揉。
7. 将苎麻面料平放在阴凉通风的地方自然晾干。
8. 如果需要熨烫苎麻面料,应将其翻面熨烫,适量使用低温。
第四章 麻纤维制品前处理
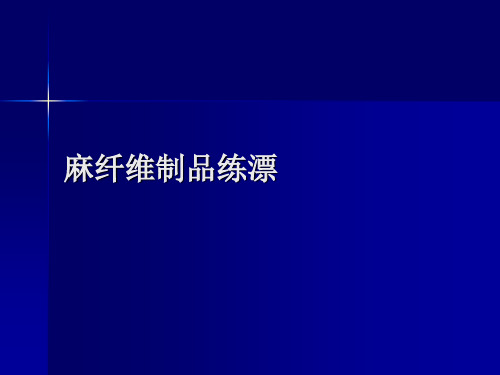
工艺:
轧碱NaOH 轧碱温度 轧余率 热碱冲洗温度 去碱箱温度 平洗温度
150~160g/L 室温 85%
70℃以上 90~95℃
80℃
三、亚麻脱胶
亚麻的初步加工:从亚麻茎中获取亚麻纤维的过程
利用微生物将亚麻中的胶质部分分解
沤麻
将亚麻原茎在一定的温度 条件下浸渍一定的时间
亚麻脱胶方法: 粗纱煮漂
机械
化学脱胶
1.除杂(机械脱胶)
目的:除去纤维中的麻屑,使纤维的整齐度提高, 以利于达到纺纱的要求
2.化学脱胶
硫酸:1.5~3g/L 时间:10~15min 浴比:1:15
亚麻粗纺 漂白
酸洗 水洗
水洗 脱水
煮练 烘干
水洗
氯—氧漂
脱胶原则:部分脱胶,降低纤维的线密度、保持纤维的长度
五、亚麻织物的前处理
烧毛
去除织物上的麻屑、无机盐、重金属离子
退浆 煮练 酸洗 漂白 丝光
重煮轻漂
氯—氧漂
亚麻纱脱胶只是部分脱胶, 剩余胶质很难煮透
轻漂减少纤维损伤
提高织物吸附性能和染色性能 碱浓度:140~220g/ L 作用较棉缓和
2.加工原理
根据纤维素与杂质化学性能的不同,在高温、高压条件下, 利用化学药品使纤维中的杂质去除,同时使纤维的白度提高
3.粗纱煮漂的设备
粗纱煮漂需高温条件下进行
高温高压设备
4.粗纱煮漂工艺
煮漂工艺: 碱煮—亚氧漂工艺
(1)煮练
煮练用剂:氢氧化钠、纯碱、水玻璃、亚硫酸钠、渗透剂
(2)亚氯酸钠漂白
(二)精干麻的变性处理
苎麻纤维结晶度高,纤维刚硬,易折皱,不易染深色
需变性处理
碱法 磺化法 碳烷基化法
染整专业《麻》

煮练
主要助剂:氢氧化钠,用量为3~5g/L,助练剂有硅酸钠2g/L、亚硫酸钠1~2g/L、 渗透剂1g/L、净洗剂0.5~1g/L、软水剂0~1g/L。 煮练时一般采用高温高压设备进行,温度可达130℃,但一般实际温度110℃左右, 时间60min。 煮练之后要进行充分的水洗,以利于纤的漂白。
漂白
前处理主要工序:烧毛、退浆、煮练、漂白、丝光
烧毛
由于亚麻/棉织物坯布表面的麻屑、麻皮等杂质很多,影响织物外观及使用性能,所以在烧毛前需经过刮刀和金刚砂辊,使麻屑、 麻皮等杂质部分脱落,再经过二正二反烧毛。煮漂等工艺对浮在织物表面的麻皮等杂质有一定的去除作用,但由于亚麻纤维的抱 合力差,煮漂后又会有粗硬的麻皮和纤毛,在布面浆料退除后,在不断受到的机械作用下,又重新露出布面。从而影响织物的外观 效果,所以在丝光前再进行第二次烧毛,可以得到理想的布面光洁度。
麻纤维制品的前处理
10染整一班
李庭伟 101503020
麻
麻是草本植物,种类很多,有“大麻”、“苎麻”、“苘 麻”、“亚麻”等。茎皮纤维通常亦称“麻”,可制绳索、织 布:麻布。麻衣。麻袋。麻绳。麻纺。
苎麻脱胶及前处理
苎麻与棉同属于纤维素纤维,但在物理结构和性质上与棉比较有较大的差异, 同时两者在含杂方面有很大的不同。苎麻纤维素含量较棉低,除含有原棉中所具有 的主要杂质如果胶物质、油蜡等外,还含有少量木素,同时纤维中杂质的含量和各 种杂质间的比例,随着品种的不同,有着较大的变动,因此,麻类的前处理较棉困 难,具有独特之处。苎麻收割后,从麻茎上剥取麻皮,并从麻皮上刮去青皮,而得 到苎麻的韧皮,经晒干后成为苎麻纺织厂的原料,称为原麻。原麻不能用来纺织, 必须经过脱胶,制取苎麻单纤维,才能用来进行纺织加工。
凉爽羊毛/苎麻复合纱的前处理工艺研究

1 原 理
11羊 毛 改 性 的原 理 .
实验 中 ,对羊毛粗纱采用 的是高锰酸钾一 蛋 白酶改性处理 。羊毛 的改性 的 目的主要是去处羊 毛的鳞 片以消
除羊毛织 物对人体 的刺痒感 。采用适 当浓度 的高锰酸钾进行预处理, 与羊毛 的鳞片层发生氧化反应 ,使鳞 片得 它 到适度的降解 , 从而 降低 了纤维 的定 向摩擦效应及纤维的细度 等 , 如果浓度控制的好 , 皮质层将不会被破坏, 加上
处理后粗纱纤维 的 2 0 倍 S M 图。从 图中对 比可以看到工艺 1 00 E 处理后 的羊毛纤维表 面剥鳞效果不 明显 ,工艺 4处理后的羊毛纤维可以明显看 出由于高锰酸钾 的过量 , 使得处理过程 中伤 害到 了皮质层 , 工艺 3改性 后的羊 毛 纤维表面因去除了大部 分鳞 片而显得 比较光滑 ,有少部分鳞片的根部没 有去除依 旧留在羊毛 的表面 ,证 明羊 毛
Fe . 0 7 b 2 0
凉爽羊毛/ 苎麻复合纱的前处理工艺研究
邹 桦 ,张尚勇
( 武汉科技挚院 纺织与材料学院,湖北 武汉 407 ) 303
摘 要 :介绍 了羊毛与苎麻两种粗纱的前处理工艺。实验证 明,高锰酸钾一蛋 白酶改性处理后的羊毛 纤维素酶改性处理后的苎麻纤维不仅对伸长率、结晶度、取向度与刚度等各方面性能都有较大改善 , 而且对其后道成纱工艺及服用性能也有一定作用,为夏季用羊毛, 苎麻复合纱的开发奠定基础。
蛋 白酶的处理后, 白酶在碱性 的条件下不仅去除 了类脂层, 蛋 而且 会被 Mn 所激活, 从而加快了鳞片层 的蛋 白质肽
键 的水 解 , 到 剥 鳞 的 效 果 口。 达 】
1 . 2苎麻 改性的原理 通过 Na H与 苎麻纤维素相作用生成碱纤维素 ,使纤 维素大分子产生膨化 、溶胀 的物理化学变化 。削弱苎 O 麻 纤维素 大分子 内部结构横 向连接, 分子链定向破坏, 使无定形 区的密度下降, 晶度下 降。又 由于酶的作用 ,苎 结
纺织品前处理的正确办法
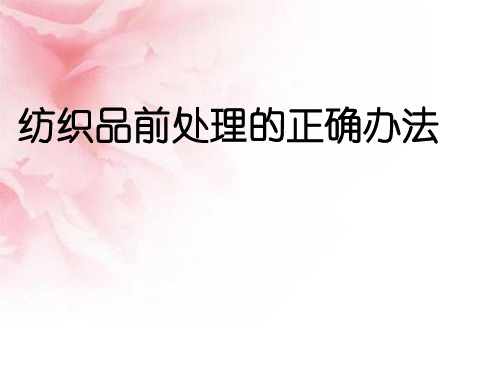
(一)烧毛 腈纶的混纺制品或其中长化纤织物在穿着过程中 易起毛,所以烧毛显得更为重要。烧毛可使织物布面光 洁,改善织物的起毛起球现象,提高产品的风格。 烧毛采用气体烧毛机,中长化纤织物烧毛应适度,采用 少火口、强火焰、快车速的烧毛工艺,一正一反。
2021/8/12
(二)退浆 腈纶中长化纤织物不仅可去除织物上的浆料,更 重要的是使织物在松弛、湿热加工中充分收缩, 获得仿毛风格; 腈纶多以PVA浆为主,可采用碱、氧化剂(亚溴 酸钠、双氧水)和洗涤剂(209洗涤剂或平平加 O)退浆;在松式退浆联合机上退浆。
2021/8/12
2021/8/12
二、腈纶及其混纺制品的前处理
腈纶及其混纺制品或中长化纤织物练漂工艺比 较简单,只需要烧毛、退浆、定型加工即可。 对特殊要求的产品还可进行增白处理;
整个练漂加工保持松弛状态,以消除纺织加工 过程中形成的内应力,使织物充分松弛、回缩 ,提高织物的仿毛风格。
2021/8/12
2021/8/12
2.涤纶碱减量加工设备
(1)间歇式碱减量设备 精练槽:成本低、张力小,减量率易控制,适于 小批量多品种生产,但重现性差。 NaOH:3-10g/L,促进剂:; 坯绸准备→精练→预热定型→浸渍碱→9598℃→80℃水洗→60℃水洗→冷水洗→酸中和→ 水洗→脱水→烘干。
2021/8/12
2021/8/12
(2)促进剂 提高碱对涤纶的水解效率,加快碱对涤纶分子的水
解反应,提高碱利用率; 常用阳离子表面活性剂,可促进碱对涤纶的反应。
将它加到涤纶碱减量浴中会被迅速吸附到纤维表面 ,使浴液中OH-转移并富集在纤维表面,更容易进 攻涤纶分子中带部分正电荷的羰基中的碳原子,造 成涤纶分子断裂,从而完成水解反应。
4.第四章_麻纤维制品的前处理

麻纤维制品的前处理
染整技术
碱液煮练
(3)煮练温度和时间
苎麻煮练分常压和高压煮练两种方法
目前多数工厂采用的是高压二煮法工艺。煮练的
压力一般为1.96×105Pa(2kgf/cm2左右),此时的
温度在120℃左右 煮练的时间:头煮为1~2h,二煮为4~5h
麻纤维制品的前处理
染整技术
碱液煮练
(4)煮练浴比
• 苎麻与涤纶混纺的织物挺括,滑爽,不易起皱,吸湿性和 透气性较好,易洗快干,也是夏季理想的服装面料
麻纤维制品的前处理
染整技术
一、苎麻化学脱胶工艺
• 在苎麻的韧皮中,主要成分是纤维素,还含有较多的胶质、木质素、蜡 状物质等杂质。其中胶质大都包围在纤维的表面,把纤维素的单纤维胶 合在一起而形成原麻 • 苎麻的原麻纤维比较粗硬,不适合纺纱,纺纱前必须将韧皮中的胶质去 除,使苎麻的单纤维相互分离,这一过程就称为脱胶 • 由于苎麻的单纤维细长,强度高,一般都是单纤维形态进行纺纱,所以 苎麻脱胶可采用化学全脱胶方法
(2)预浸:包括水浸、酸浸、预氯等几种方法。其工艺目的是为了去除原 麻中的部分胶质,减轻煮练负担,降低碱液消耗,提高煮练效果,并 改善精干麻的质量 ①水浸:将生苎麻浸于90℃以上的热水中,煮30~60min,去除部分 水溶性胶质,并使不溶于水的胶质膨化。其优点是预处理条件缓和, 纤维损伤小。但脱胶效果较差
麻纤维制品的前处理
染整技术
(2)酸洗 酸洗是用1~2g/L的稀硫酸中和纤维上残余的碱液, 并去除纤维上吸附的残胶等有色物质,使纤维松散,手 感柔软,洁白。 (3)水洗 水洗是为了洗去纤维上的酸液,还可继续去除纤维 上残留的胶质,使纤维表面清洁、柔软。
麻纤维制品的前处理
- 1、下载文档前请自行甄别文档内容的完整性,平台不提供额外的编辑、内容补充、找答案等附加服务。
- 2、"仅部分预览"的文档,不可在线预览部分如存在完整性等问题,可反馈申请退款(可完整预览的文档不适用该条件!)。
- 3、如文档侵犯您的权益,请联系客服反馈,我们会尽快为您处理(人工客服工作时间:9:00-18:30)。
◆棉针织物的前处理工艺流程:漂白汗布品种:坯布-碱缩-煮练-漂白-增白染色(印花)汗布品种:坯布-碱缩-煮练-漂白-(丝光)染色(印花)棉毛品种:坯布-煮练-漂白-(丝光)工艺条件:碱缩:干缩、湿缩煮练:比机织物缓和,织物上保留较多蜡质,避免造成缝纫破洞漂白:丝光:◆苎麻织物的练漂麻纤维的特点:属纤维素:但在物理结构和性质上与棉有很大差异,含杂方面有着很大差异纤维素含量较低,主要杂质:除果胶物,油蜡外,还含有木质素,半纤维素等。
且杂质的含量和各种杂质间的比例,随品种不同有着很大的变动。
麻类的练漂较棉困难,具有其独特之处。
一、苎麻纤维的脱胶麻皮--(剥皮)原麻苎麻原麻中含有大量多糖胶状物质(25-30%),--麻胶,绝大部分要求在纺纱前除去,故称“脱胶”使剩余含胶量的2%。
(原麻脱胶得到精干麻)为什么要除去麻胶?脱胶方法:土法脱胶、化学脱胶、物理机械脱胶、微生物脱胶脱胶工艺流程:预处理(拆包、扎把、预浸)—碱液煮练(温度、时间、浴比)—后处理(打纤、酸洗、水洗、漂白、精练、给油、脱水、烘干)H2SO4浸堆置净洗煮布锅煮练洗净第二次煮练出锅杵击冲洗NaC1O漂白二、麻织物的练漂基本上与棉织物练漂相似,其特点:1、烧毛:可多次烧毛,加强烧毛工艺,因毛刺多。
2、退浆、煮练:煮布锅或常压松式绳状机。
厚重织物练液:18g/L NaOH 浴比:1:107g/L Na2CO3时间:5h120-130℃稀薄织物:5g/L NaOH 浴比:1:105g/L Na2CO3时间:2h3g/L 肥皂 95-100℃3、漂白:例:NaC10绳状漂白,轧漂,有效氯1.8g,堆置1h宜采用平幅加工,减少折痕和漂斑4、半丝光:提高对染料的吸附率为什么进行半丝光?◆羊毛的前处理原毛含有大量杂质:天然杂质:羊脂羊汗附加杂质:植物性杂质、尘土、色素原毛纺织前经洗毛、炭化、漂白等工序毛条、纱线或织物在染色前,洗呢一、洗毛(精练):洗毛的目的?1、杂质特点:羊脂:高级脂肪酸和胆固醇结合而成的酯及少量游离醇脂肪酸。
羊汗:脂肪酸的钾盐、砂土2、羊毛特点:不耐碱、特别在高温下,会发生严重损伤。
3、洗毛:弱碱条件下:中温,乳化法方法:皂碱法:肥皂+Na2CO3 用量肥皂 2-4%Na2CO3 2%(对原毛重)温度50℃ pH=8-9时间10-20min洗涤质量衡量:含脂率 1.2%设备:耙式洗毛机四槽第一槽第二槽第三槽第四槽单用Na2CO3液碱皂液水洗水洗羊脂可回收利用二、炭化炭化的目的?1、植物性杂质的去除原理:强无机酸:纤维素水解羊毛不受显著损害2、方法: 散毛炭化毛条炭化匹条炭化3、散毛炭化工艺浸水脱水浸酸脱酸烘干轧炭(散毛)机械除尘清水洗,中和烘干三、漂白对白度要求较高的白色织物等加以漂白一般染色用可直染色不必漂白流程:浸H2O2漂液清洗漂毛粉漂白清洗◆丝的前处理一、坯绸练漂目的:坯绸:生蚕丝丝朊:丝素丝胶:其中含有少量脂蜡,无机物,色素附加杂质去除脱胶原理:丝胶蛋白中极性氨基酸含量比丝素高得多,而且分子间的排列远不如丝素整齐,结晶度低无取向,因此二者化学活泼性显著不同,采用适当方法和工艺条件,去除丝胶少损伤丝素来达到脱胶目的。
丝胶的化学性质:在水中溶解度很小,强酸,强碱溶解度较高,但易造成丝素损伤。
因此,用皂碱法脱胶,pH=9.5-10.5 弱碱性。
二、桑蚕丝的精练(脱胶):1、皂碱法工艺流程(传统方法):练前准备初练复练练后处理(水洗→脱水)初练:Na2CO3,肥皂对丝重35-45%,50-60℃,30min复练:肥皂对丝重15-25%,浴比:1:40,98-100℃,1-1.5h练后处理(水洗→脱水):逐步降温水洗丝鸣?(醋酸室温处理10-20min,改善手感,产生丝鸣2、设备,间歇式:方形槽连续式:松式平幅松式绳状三、丝织物漂白:漂白(氧化性漂白、还原性漂白)→热水洗→温水洗→冷水洗H2O2Na2SiO3或多聚磷酸钠pH=8-8.5 70℃ 2-3h◆化学纤维织物的前处理化学纤维本身比较洁白,制成织物后练漂的目的,去杂,织造上的油污,浆料。
一、人造纤维的练漂①粘胶纤维织物的前处理粘胶:化学敏感性大,湿强力差,易变形,应避免过分强烈的化学和机械作用。
工序:烧毛,退浆,(精练)漂白(一般不丝光)轻度精炼工艺:纯碱1g/LNa2SiO30.3g/l净洗剂5g/l温度100℃ 60-90min设备:绳状松式浸染机②天丝织物的前处理③Modal纤维织物的前处理二、合纤练漂:轻微的洗练,去除浆料及油剂油污涤纶织物的前处理工艺:退浆精练—松弛—碱减量—热定形热定形一、热定形目的和机理:(一)热定形:将织物保持一定的尺寸,经高温加热一定时间,然后以适当速度冷却的过程。
(二)目的有三:消除已有皱痕针对合成纤维:防止织物在温热条件下产生难以去除的皱痕提高织物热稳定性(高温条件下的不收缩性)(三)机理:第一阶段:在一定张力作用下纤维分子链段热运动加剧,从而分子重排。
第二阶段:非晶区在新的位置上相邻分子链段建立起新的关系,结晶区完整性↑。
第三阶段:非晶区冷却后新状态固定下来。
二、热定形机温热定形:锦纶及其混坊干热定形:涤纶及其混坊设备:热风针铗(板)链式,卧式热定形应用最为广泛组成:进布架整纬起喂针板拉幅喷风冷却出布热风房:防热区、定形区◆混纺和交织物的前处理一、涤棉混纺和交织物的前处理烧毛-退浆-煮练-漂白-丝光-热定形二、含氨纶弹性机织物的前处理坯布检验-酶退浆(平幅松弛处理)-水洗烘干-预定形-冷轧堆(煮漂)-水洗烘干-烧毛-(复漂)-水洗烘干-丝光第三章 染色 第一节 概述一、染色1、染色:通过染料(或颜料)和纺织材料发生物理的、化学的或物理化学的结合,使纺织材料获得鲜艳、均匀和坚牢色泽的加工过程。
2、染色产品的要求:1)色泽均匀 2)鲜艳及良好的染色牢度3、按纺织品形态不同: 织物染色 应用最广染色种类 纱线染色 色织、针织、纱线制品 散纤维染色 混纺交织厚密织物4、染色方法:浸染:散纤维,纱线,小批量织物染色混染:大批量机织物5、染色牢度:染品在使用或在染色以后的加工过程中,染料或颜料在各种外界因素影响下,能保持染色产品原来染色状态的程度。
包括项目:日晒、气候、皂洗、汗渍、干、湿摩擦牢度 耐海水牢度、耐漂牢度、 耐酸、耐碱、熨烫、烟气牢度等 耐日晒牢度 (8级,一级最差,八级最好) 摩擦牢度(5级,一级最差,五级最好) 皂洗牢度(5级,一级最差,五级最好)与染料染色牢度相关因素:由它的化学结构决定 染料在纤维上的状态 染色方法和工艺条件 二、染料的基本知识染料分类染料:有色的有机化合物,大都溶于水,或通过一定化学处理,转变为可以溶解于水。
它能和纤维发生物理或物理化学的结合,而染着在纤维上,且具有一定牢度的颜色。
颜料:有色无机物质,不溶于水 ,不能染着在纤维上,依靠粘着剂的作用,机械地附着在纤维材料的表面或内部。
1、染料概述颜色的形成:各种物质对入射光所引起的反射,折射及吸收等作用不同,肉眼的感觉也不同,而形成不同的颜色。
作为染料的四个条件A 色度 必须能染得一定浓度的颜色B 上色的能力 与纺织材料有一定的结合力,即亲和力或直接性C 溶解性D 染色牢度2、染料的分类:一般(除分散染料)都是电解质阴离子染料DSO 3Na3Na阳离子染料 DXD X (ClSO 3)12(1)直接染料:染色方法简单(家庭使用NaCl 、沸煮)色谱齐全,成本低廉,但水洗日晒牢度差。
(2)不溶性偶氮染料:在织物上偶合成不溶于水的颜料。
(3)活性染料:分子中有活性基团,适用范围广。
(4)还原染料:在强碱溶液中借助还原剂还原溶解进行染色,再氧化重新转变成不溶于性染料而固着纤维上。
(5)可溶性还原染料纤维素(6)硫化染料纤维素(7)分散染料涤纶牢度较高(8)酸性染料羊毛,蚕丝,锦纶(9)酸性媒染及酸性含媒染料:羊毛(10)碱性及阳离子染料腈纶(11)氧化染料黑色棉织物3染料的选择:环保性能选择根据纤维性质选择根据纺织品用途选择根据染料成本选择根据拼色用染料性能选择根据染色设备选择根据印染的后续加工方式选择4染料的命名活性艳红M-8B150%活性—冠称,表示染料的类别艳红—色称,表示其颜色是鲜艳的红色M-8B150%--尾注M--M型活性染料B—染料的色光偏蓝8B—比B蓝很多,是支蓝光很重的红色染料150%--表示染料的强度或力分三、上染过程中一些基本问题的分析:不同纤维不同染料共同点:上染过程不同染色方法1、上染过程:将纤维投入染浴中,染料选择性地转移到纤维上,被纤维吸附,并逐渐扩散入纤维内部,这种染料从染浴向纤维转移的过程。
称为三个阶段:1)染料在纤维上的吸附:染液中染料分子迅速被纤维表面分子吸附。
2)染料向纤维内部扩散:由于纤维表面与内部形成的染料浓度差,吸附在表面的染料转移到内部3)染料在纤维上的固着:通过染料与纤维之间的作用力而固着在纤维上。
2、固着方式纯粹化学固着物理化学固着四、染色机械设备1常用染色方法浸染(竭染)轧染2常用染色设备染色机织物平幅卷染机常温常压高温高压连续轧染机高温常压热溶常温常压轧染(经轴染色机)绳状绳状染色机常温常压溢流染色机常温常压溢喷染色机高温高压纱线筒子纱绞纱经轴散纤维常压高压对染色设备要求:符合工艺,染品匀适,坚牢,不损伤织物纤维,降低成本★散纤维染色机:用途:混纺织物,交织物用纤维。
吊筐式染色机:吊筐,染槽,循环泵,中心管,槽盖★纱线染色机用途:纱线,经纱。
色织物经纱。
130℃涤纶经纱★织物染色机1、绳状染色机:2、卷染机种类:普通卷染机:棉高温高压卷染机:涤纶3、连续轧染机:根据染料不同设备组成也不同。
4、高温高压,溢流染色机涤纶高温高压,喷射染色机。