谐波减速器壳体
谐波传动减速器原理

谐波传动减速器原理
谐波传动减速器是一种基于谐波振动原理工作的精密减速装置。
它主要由柔性齿条、柔性齿轮、星轮、轴套和外壳等组成。
在谐波传动减速器中,谐波振动由外部驱动器引起。
驱动器通过柔性齿轮施加周期性外力,使之产生弯曲变形。
柔性齿条与柔性齿轮的齿数不同,由于弹性形变的特性,齿条和齿轮之间会发生相对位移。
当外力周期性施加于柔性齿轮上时,柔性齿条的齿数和位置会发生变化。
这种变化会导致星轮的旋转,同时将输出转矩传递给输出轴。
输出轴通过轴套连接到外壳上,从而实现减速效果。
谐波传动减速器的减速比取决于外驱动传动器与输出轴之间的齿数比。
通常情况下,谐波传动减速器可以实现较高的减速比,同时还具有大的扭矩输出。
此外,谐波传动减速器具有结构紧凑、响应快速和传动效率高等优点,广泛应用于机械领域。
总结起来,谐波传动减速器利用谐波振动原理实现减速效果,通过驱动器的作用使得柔性齿条和齿轮产生相对位移,从而实现输出轴的旋转和扭矩输出。
谐波减速器柔轮力学特性分析

A Thesis Submitted to Chongqing University in Partial Fulfillment of the Requirement for the Professional Degree
By Xie.Hengpeng
Supervised by Prof. Wang Jiaxu Specialty: ME(Mechanical Engineering Field)
College of Mechanical Engineering of Chongqing University, Chongqing, China May 2015
中文摘要
摘
要
谐波减速器是一种利用可控变形的柔性构件产生的变形波进行运动或动力传 递的新型传动装置,由于其具有其他传动装置所难以达到的特殊性能,因此在航 天装备和机器人领域得到越来越广泛的应用。但是,工程实践表明,谐波减速器 平均无故障工作的时间较短, 其最突出的问题是柔轮的可靠性、 使用寿命不理想, 输出端扭转刚度不足。作为谐波减速器主要构件的柔轮是一个薄壁壳体,受波发 生器和外部负载的双重作用,在循环弹性变形的状态下工作,既承受弯曲应力, 又承受扭转应力,很容易发生疲劳失效。因此,对谐波减速器的柔轮进行力学特 性方面的分析有着重要的意义。 本文以谐波减速器的柔轮为主要研究对象,完成了下列工作: ①介绍了谐波减速器的工作原理、传动特点及应用领域,对柔轮在波发生器 作用下的变形、应力和疲劳强度进行了理论计算。 ②根据课题要求,设计了一种传动比为 100 的谐波减速器,利用有限元分析 软件 ANSYS Workbench 建立了柔轮——波发生器有限元非线性接触模型,分析了 柔轮在波发生器作用下的变形规律和应力分布,结果表明柔轮齿圈与光滑筒体连 接处和光滑筒体与筒体底部过渡处为柔轮的应力危险区域。 ③分析了柔轮在不同长径比和不同壁厚参数下的变形规律和应力分布。然后 对柔轮应力危险区域进行结构参数调整和优化设计,建立了有限元非线性接触模 型,重点分析了柔轮的应力分布情况,结果表明经过对结构参数的优化设计,柔 轮应力危险区域的应力分布得到明显改善。 ④首先对两种不同结构参数的谐波减速器柔轮进行了扭转刚度有限元分析, 得到了柔轮的扭转刚度,然后设计并搭建了一套谐波减速器扭转刚度测试系统, 通过对测试数据的分析得到了它们的扭转刚度。测试结果表明经过结构参数优化 的机型一的扭转刚度比未经结构参数优化的机型二扭转刚度要高得多,同时通过 对照有限元分析的结果,两者得到的谐波减速器的扭转刚度呈现出一致性,表明 了结构参数的优化有利于提高谐波减速器的扭转刚度。 关键词:谐波减速器,柔轮,力学特性,有限元分析,扭转刚度
谐波减速器组成结构

谐波减速器组成结构谐波减速器组成结构谐波减速器(Harmonic Drive,简称HD)是一种可以大大改善减速机性能的新型机械结构,它实际上是一种精密的圆弧齿轮减速机,其高精度的减速功能使HD成为操作精确、安全可靠的精密减速机。
HD减速机由几个部分组成:1.外壳:外壳是减速机的外壳,通常为铸铝压铸或者钢板焊接而成,外壳的防护等级可以根据应用需要选择合适的外壳结构,比如IP54-IP67。
2.驱动齿轮:驱动齿轮是减速机的关键部件,它可以将输入动力转换成期望的减速比,它的形状就像圆弧,使用中受到的压力很大,因此设计时需要考虑到安全性。
3.输出轴:输出轴是系统的中心部分,它的作用是将输入动力转换为输出动力,它的特点是高精度和高稳定性。
4.顶盖:顶盖是减速机的封底,它的作用是将减速机的内部封闭,以确保减速机免受外界环境的侵害,同时也能够将系统的转矩输出到减速机的输出轴上。
5.动力输入轴:动力输入轴是系统的输入部分,它的作用是将外部动力传递到减速机的内部,它的特点是高精度和高稳定性。
6.驱动器:驱动器是减速机的内部机构,它的作用是将外部动力传递到驱动齿轮,它的特点是尺寸小、负荷小、噪音低。
7.油底:油底是减速机的内部结构,它的作用是将驱动齿轮与输出轴连接,并带动驱动齿轮的转动,同时它还有装油的功能,使减速机长期运行稳定。
谐波减速器是一种新型的机械结构,它以其精密的圆弧齿轮技术为减速机提供了新的功能,极大提升了减速机的性能。
谐波减速器的组成结构外壳,驱动齿轮,输出轴,顶盖,动力输入轴,驱动器,油底等,这些组成结构的功能分别是保障外壳的完整性,将输入动力转换成期望的减速比,将输入动力转换为输出动力,将减速机的内部封闭,将外部动力传递到减速机的内部,将外部动力传递到驱动齿轮,将驱动齿轮与输出轴连接装油等。
谐波减速机原理
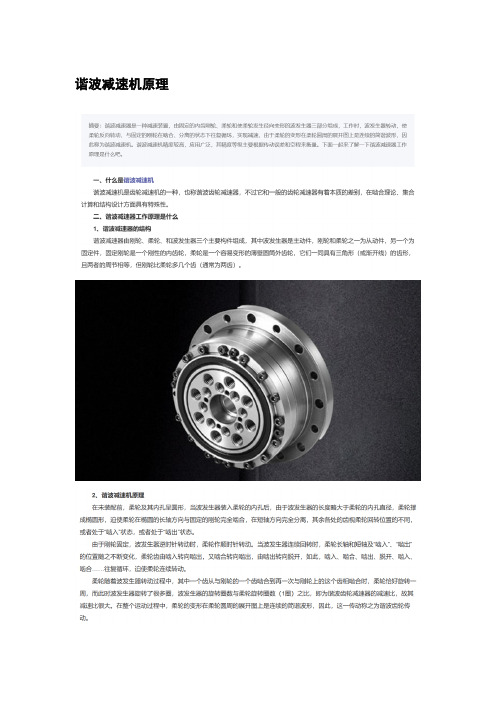
谐波减速机原理谐波齿轮减速机工作原理谐波齿轮减速机由固定的内齿刚轮、柔轮、和使柔轮发生径向变形的波发生器组成,谐波齿轮减速机是齿轮减速机中的一种新型传动结构,它是利用柔性齿轮产生可控制的弹性变形波,引起刚轮与柔轮的齿间相对错齿来传递动力和运动。
这种传动与一般的齿轮传递具有本质上的差别,在啮合理论、集合计算和结构设计方面具有特殊性。
谐波齿轮减速机具有高精度、高承载力等优点,和普通减速器相比,由于使用的材料要少50%,其体积及重量至少减少1/3。
组成与结构谐波齿轮减速机由刚轮、柔轮、和波发生器三个主要构件组成。
•固定刚轮是一个刚性的内齿轮••柔轮是一个容易变形的薄壁圆筒外齿轮,它们一同具有三角形(或渐开线)的齿形,且两者的周节相等,但刚轮比柔轮多几个齿(通常为两齿)••波发生器由一个椭圆盘和一个柔性球轴承组成,或者由一个两端均带有滚子的转臂组成。
•••通常波发生器为原动体,柔轮和刚轮之一为从动体,另一个为固定件。
图2.谐波齿轮减速器的结构组成在未装配前,柔轮及其内孔呈圆形,当波发生器装入柔轮的内孔后,由于波发生器的长度略大于柔轮的内孔直径,柔轮撑成椭圆形,迫使柔轮在椭圆的长轴方向与固定的刚轮完全啮合,在短轴方向完全分离,其余各处的齿视柔轮回转位置的不同,或者处于“啮入”状态,或者处于“啮出”状态。
由于刚轮固定,波发生器逆时针转动时,柔轮作顺时针转动。
当波发生器连续回转时,柔轮长轴和短轴及“啮入”、“啮出”的位置随之不断变化,柔轮齿由啮入转向啮出,又啮合转向啮出,由啮出转向脱开,如此,啮入、啮合、啮出、脱开、啮入、啮合……往复循环,迫使柔轮连续转动。
柔轮随着波发生器转动过程中,其中一个齿从与刚轮的一个齿啮合到再一次与刚轮上的这个齿相啮合时,柔轮恰好旋转一周,而此时波发生器旋转了很多圈,波发生器的旋转圈数与柔轮旋转圈数(1圈)之比,即为谐波齿轮减速器的减速比,故其减速比很大。
在整个运动过程中,柔轮的变形在柔轮圆周的展开图上是连续的简谐波形,因此,这一传动称之为谐波齿轮传动。
谐波减速器的结构组成

谐波减速器的结构组成介绍谐波减速器是一种基于谐波原理工作的减速装置,广泛应用于机械传动领域。
它以其结构紧凑、传动效率高、精度高等特点受到了广大工程师的青睐。
本文将详细介绍谐波减速器的结构组成,包括主要部件和工作原理。
主要部件谐波减速器主要由以下几个部件组成:波发生器波发生器是谐波减速器的核心部件,它通过变形将电机的旋转运动转变为谐波运动。
波发生器通常由柔性轮和波发生器壳体组成。
柔性轮是由多个柔性齿片组成的,当电机旋转时,柔性轮会产生弹性变形,从而产生谐波运动。
谐波轮谐波轮是与波发生器配合工作的部件,它由内外两个齿圈和齿轮组成。
内齿圈与波发生器的柔性齿片相互咬合,外齿圈与输出轴上的齿轮相互咬合。
当波发生器产生谐波运动时,内齿圈会带动外齿圈和齿轮一起旋转,从而实现减速效果。
输出轴输出轴是谐波减速器的输出端,它通过与谐波轮上的齿轮咬合,将减速后的动力传递给外部设备。
输出轴通常由轴承支撑,以减少摩擦和磨损。
输入轴输入轴是谐波减速器的输入端,它与电机的轴连接,将电机的旋转运动传递给波发生器。
输入轴通常由轴承支撑,以减少摩擦和磨损。
壳体壳体是谐波减速器的外部保护结构,它起到支撑和固定内部部件的作用。
壳体通常由铝合金或铸铁制成,具有良好的强度和刚性。
工作原理谐波减速器的工作原理基于谐波运动的特性。
当电机旋转驱动波发生器时,波发生器的柔性齿片会产生弹性变形,从而产生谐波运动。
这种谐波运动通过内齿圈与外齿圈的咬合,将旋转运动转变为减速后的旋转运动。
具体而言,当电机旋转时,波发生器的柔性齿片会随之变形,产生谐波运动。
这种谐波运动使得内齿圈与外齿圈之间产生相对运动,内齿圈带动外齿圈和齿轮一起旋转。
由于内齿圈的齿数较少,而外齿圈的齿数较多,所以旋转一周的时间内,输出轴旋转的角度会远小于输入轴的角度,从而实现减速效果。
谐波减速器的优点在于其传动效率高、精度高、结构紧凑等特点。
然而,它也存在一些缺点,比如承载能力相对较低、使用寿命较短等。
谐波齿轮减速器工作原理

谐波齿轮减速器工作原理谐波齿轮减速器(Harmonic Drive)是一种新型的高精度、大扭矩、超薄型的减速器,广泛应用于机械设备中。
它采用了与传统的齿轮箱不同的原理和结构,使其在体积小、重量轻的同时具有优异的动态性能和稳定性。
本文将介绍谐波齿轮减速器的工作原理。
1. 基本结构谐波齿轮减速器由三个主要部分组成:柔轮(flexspline)、刚性齿轮(circular spline)和波发生器(wave generator)。
其中,柔轮是由特殊弹性材料制成,具有多个柔性齿,刚性齿轮是由刚性材料制成,而波发生器则是用来产生弯曲应力并形成谐波运动的。
2. 工作原理谐波齿轮减速器的工作原理是通过波发生器的弯曲来实现传动。
波发生器由两个轴向齿块组成,分别位于柔轮和刚性齿轮之间。
当波发生器转动时,由于其内部的齿块数量不同,会产生不同的行星运动。
其中一个齿块会贴合刚性齿轮的内齿,而另一个齿块则会与柔轮的外齿相连接,并通过柔轮将运动传递给输出轴。
3. 谐波珠与弹性材料的作用在谐波齿轮减速器中,谐波珠起到了关键的作用。
谐波珠位于波发生器的齿块与柔轮之间,可在齿块与柔轮之间产生高应力的碰撞区域。
当波发生器旋转时,柔轮的齿会受到谐波珠的压力而产生变形,从而使得柔轮产生弯曲。
在弯曲的过程中,谐波珠通过碰撞产生的能量转化为机械能,通过齿轮传递给输出轴。
4. 优点谐波齿轮减速器相对于传统的齿轮箱具有以下几个优点:4.1 高精度:谐波齿轮减速器的传动误差非常小,可以实现非常精确的位置控制。
4.2 大扭矩:谐波齿轮减速器采用双齿轮传动,能够提供大扭矩输出。
4.3 超薄型:谐波齿轮减速器结构紧凑,可节省安装空间。
4.4 高效率:谐波齿轮减速器由于采用了滚动摩擦传动,具有较高的传动效率。
5. 应用领域。
谐波减速器和rv减速器的工作原理
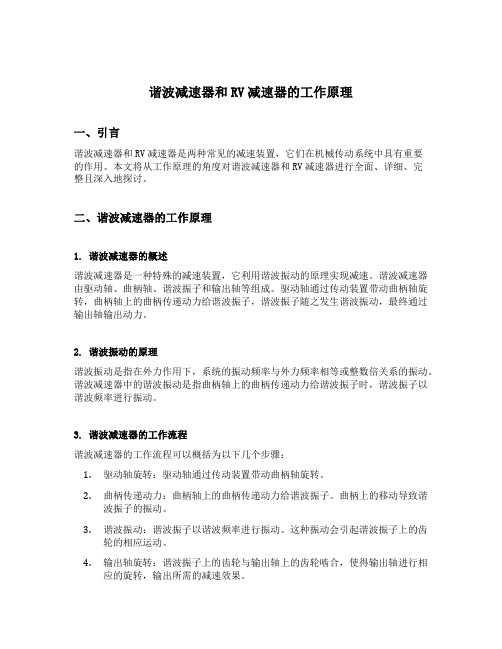
谐波减速器和RV减速器的工作原理一、引言谐波减速器和RV减速器是两种常见的减速装置,它们在机械传动系统中具有重要的作用。
本文将从工作原理的角度对谐波减速器和RV减速器进行全面、详细、完整且深入地探讨。
二、谐波减速器的工作原理1. 谐波减速器的概述谐波减速器是一种特殊的减速装置,它利用谐波振动的原理实现减速。
谐波减速器由驱动轴、曲柄轴、谐波振子和输出轴等组成。
驱动轴通过传动装置带动曲柄轴旋转,曲柄轴上的曲柄传递动力给谐波振子,谐波振子随之发生谐波振动,最终通过输出轴输出动力。
2. 谐波振动的原理谐波振动是指在外力作用下,系统的振动频率与外力频率相等或整数倍关系的振动。
谐波减速器中的谐波振动是指曲柄轴上的曲柄传递动力给谐波振子时,谐波振子以谐波频率进行振动。
3. 谐波减速器的工作流程谐波减速器的工作流程可以概括为以下几个步骤:1.驱动轴旋转:驱动轴通过传动装置带动曲柄轴旋转。
2.曲柄传递动力:曲柄轴上的曲柄传递动力给谐波振子。
曲柄上的移动导致谐波振子的振动。
3.谐波振动:谐波振子以谐波频率进行振动。
这种振动会引起谐波振子上的齿轮的相应运动。
4.输出轴旋转:谐波振子上的齿轮与输出轴上的齿轮啮合,使得输出轴进行相应的旋转,输出所需的减速效果。
4. 谐波减速器的特点谐波减速器具有以下几个特点:•高精度:谐波减速器具有高传动精度,可以达到几个角秒的转动精度。
•大减速比:谐波减速器的减速比一般较大,可以达到几十甚至上百倍。
•大扭矩密度:谐波减速器设计合理,具有较大的扭矩密度,可以满足多种工况下的需求。
三、RV减速器的工作原理1. RV减速器的概述RV减速器是一种常用的行星减速装置,其结构紧凑,扭矩传递平稳,广泛应用于工业机械等领域。
RV减速器由输入端、输出端和行星轮等组成。
2. RV减速器的工作流程RV减速器的工作流程可以概括为以下几个步骤:1.输入轴旋转:输入轴带动行星轮旋转。
2.行星轮与行星齿轮啮合:行星轮上的行星齿轮与固定在壳体周围的行星轮啮合,形成行星齿轮传动系统。
XB系列谐波传动减速机
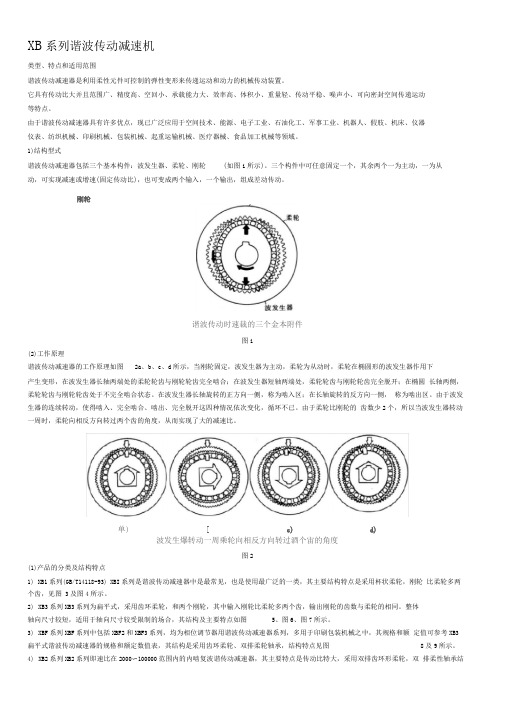
XB系列谐波传动减速机类型、特点和适用范围谐波传动减速器是利用柔性元件可控制的弹性变形来传递运动和动力的机械传动装置。
它具有传动比大并且范围广、精度高、空回小、承载能力大、效率高、体积小、重量轻、传动平稳、噪声小、可向密封空间传递运动等特点。
由于谐波传动减速器具有许多优点,现已广泛应用于空间技术、能源、电子工业、石油化工、军事工业、机器人、假肢、机床、仪器仪表、纺织机械、印刷机械、包装机械、起重运输机械、医疗器械、食品加工机械等领域。
1)结构型式谐波传动减速器包括三个基本构件:波发生器、柔轮、刚轮(如图i所示)。
三个构件中可任意固定一个,其余两个一为主动,一为从动,可实现减速或增速(固定传动比),也可变成两个输入,一个输出,组成差动传动。
刚轮谐波传动时速裁的三个金本附件图i(2)工作原理谐波传动减速器的工作原理如图2a、b、c、d所示,当刚轮固定,波发生器为主动,柔轮为从动时,柔轮在椭圆形的波发生器作用下产生变形,在波发生器长轴两端处的柔轮轮齿与刚轮轮齿完全啮合;在波发生器短轴两端处,柔轮轮齿与刚轮轮齿完全脱开;在椭圆长轴两侧,柔轮轮齿与刚轮轮齿处于不完全啮合状态。
在波发生器长轴旋转的正方向一侧,称为啮入区;在长轴旋转的反方向一侧,称为啮出区。
由于波发生器的连续转动,使得啮入、完全啮合、啮出、完全脱开这四种情况依次变化,循环不已。
由于柔轮比刚轮的齿数少2个,所以当波发生器转动一周时,柔轮向相反方向转过两个齿的角度,从而实现了大的减速比。
单) [ c) d)波发生爆转动一周乘轮向相反方向转过酒个宙的角度图2(1)产品的分类及结构特点1)XB1系列(GB/T14118-93) XBI系列是谐波传动减速器中是最常见,也是使用最广泛的一类,其主要结构特点是采用杯状柔轮,刚轮比柔轮多两个齿,见图3及图4所示。
2)XB3系列XB3系列为扁平式,采用齿环柔轮,和两个刚轮,其中输入刚轮比柔轮多两个齿,输出刚轮的齿数与柔轮的相同。
谐波减速器工作原理

谐波减速器工作原理
1.谐波生成器:谐波减速器的谐波生成器由内外两层柔性齿圈、耳轴、球轴和压死套等组成。
通过内外齿圈间的压死套将传动动力传递给外齿圈,外齿圈沿一个方向旋转,同时内齿圈沿相反方向产生谐波振动。
2.谐波放大器:谐波减速器的谐波放大器由蜗杆、钢质球、摆线轮和
随动齿圈等组成。
谐波振动通过蜗杆和钢质球传递给摆线轮,使其以相反
方向旋转。
摆线轮与随动齿圈啮合,使齿圈产生谐波振动,并通过摆线轮
上的齿槽传递给输出波轮。
3.输出波轮:谐波减速器的输出波轮接收谐波放大器传递过来的谐波
振动。
输入动力首先通过谐波生成器产生谐波振动,然后通过谐波放大器
放大传递给输出波轮。
输出波轮的齿圈与随动齿圈相互啮合,通过梯形齿
槽将力传递给输出轴。
1.高精度:谐波减速器采用谐波振动传递动力,传动精度高,误差小,齿轮间隙小,能够实现精确的角度和速度控制。
2.大扭矩:谐波减速器通过谐波振动产生高倍的内部传动比,能够实
现高扭矩输出,满足工业机械要求。
3.响应灵敏:谐波减速器由于采用柔性构件进行传动,传动系统刚度小,惯性小,响应灵敏。
4.高效率:由于摆线轮和随动齿圈之间的啮合面积大,传动效率高,
能够提高机械设备的工作效率。
5.体积小:谐波减速器采用紧凑的结构设计,体积小,重量轻,安装
方便。
总而言之,谐波减速器的工作原理是通过谐波振动产生、传递和放大的力,实现高精度、高扭矩的减速作用。
它具有传动精度高、扭矩大、响应灵敏、效率高和体积小等特点,广泛应用于工业机械领域。
谐波减速器的原理简
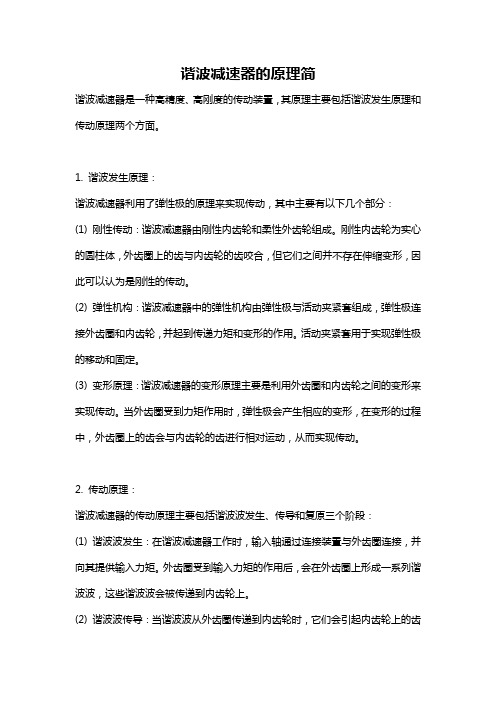
谐波减速器的原理简谐波减速器是一种高精度、高刚度的传动装置,其原理主要包括谐波发生原理和传动原理两个方面。
1. 谐波发生原理:谐波减速器利用了弹性极的原理来实现传动,其中主要有以下几个部分:(1) 刚性传动:谐波减速器由刚性内齿轮和柔性外齿轮组成。
刚性内齿轮为实心的圆柱体,外齿圈上的齿与内齿轮的齿咬合,但它们之间并不存在伸缩变形,因此可以认为是刚性的传动。
(2) 弹性机构:谐波减速器中的弹性机构由弹性极与活动夹紧套组成,弹性极连接外齿圈和内齿轮,并起到传递力矩和变形的作用。
活动夹紧套用于实现弹性极的移动和固定。
(3) 变形原理:谐波减速器的变形原理主要是利用外齿圈和内齿轮之间的变形来实现传动。
当外齿圈受到力矩作用时,弹性极会产生相应的变形,在变形的过程中,外齿圈上的齿会与内齿轮的齿进行相对运动,从而实现传动。
2. 传动原理:谐波减速器的传动原理主要包括谐波波发生、传导和复原三个阶段:(1) 谐波波发生:在谐波减速器工作时,输入轴通过连接装置与外齿圈连接,并向其提供输入力矩。
外齿圈受到输入力矩的作用后,会在外齿圈上形成一系列谐波波,这些谐波波会被传递到内齿轮上。
(2) 谐波波传导:当谐波波从外齿圈传递到内齿轮时,它们会引起内齿轮上的齿与外齿圈上的齿进行咬合。
由于外齿圈和内齿轮之间存在相对位移,所以谐波波在变形过程中会使内齿轮上的齿产生相应的变形,从而实现传动。
(3) 谐波波复原:当内齿轮传动过程中发生变形后,经过内齿轮上齿与外齿圈上齿的咬合后,内齿轮上的齿会通过发生反向位移的方式进行复原,即与外齿圈上的齿分离。
这样,谐波波的传递过程就完成了。
总结起来,谐波减速器通过利用弹性极的变形和咬合齿轮之间的相对位移实现传动,其主要原理为刚性传动、弹性机构和变形原理。
其工作过程可分为谐波波发生、传导和复原三个阶段,通过谐波波的传递来实现力矩的转换和传递。
谐波减速器具有高精度、高刚度的特点,在机械制造、精密加工等领域都有广泛的应用前景。
谐波减速器的结构组成

谐波减速器的结构组成谐波减速器是一种常用的机械传动装置,它具有结构简单、紧凑、效率高的特点。
下面将从结构组成的角度对谐波减速器进行介绍。
谐波减速器的主要结构组成包括输入轴、输出轴、柔性齿轮、刚性齿轮和波发生器等部件。
1. 输入轴:输入轴是谐波减速器的动力输入端,将电机或其他动力设备输出的动力传递给谐波减速器。
输入轴通常由高强度合金钢制成,具有足够的强度和刚度。
2. 输出轴:输出轴是谐波减速器的动力输出端,它将经过减速的动力传递给机械设备。
输出轴通常也由高强度合金钢制成,以保证传递动力的可靠性和稳定性。
3. 柔性齿轮:柔性齿轮是谐波减速器的核心部件,它由多个柔性齿片组成。
柔性齿片通常由高强度不锈钢或弹性材料制成,具有良好的弯曲和弹性性能。
柔性齿轮通过与波发生器的齿槽咬合,实现动力的传递和转换。
4. 刚性齿轮:刚性齿轮是谐波减速器的固定齿轮,它由多个齿槽组成。
刚性齿轮通常由高强度合金钢制成,具有较高的硬度和刚度。
刚性齿轮通过与柔性齿轮的齿槽咬合,实现动力的传递和转换。
5. 波发生器:波发生器是谐波减速器的核心部件,它由多个波形发生器组成。
波形发生器通常由高强度合金钢制成,具有较高的硬度和刚度。
波形发生器的齿槽形状特殊,能够与柔性齿轮的齿片咬合,通过变形传递动力。
谐波减速器的工作原理是:当输入轴带动波发生器旋转时,波形发生器的齿槽将推动柔性齿轮的齿片变形,从而实现动力的传递和转换。
柔性齿轮的变形产生非线性的齿轮传动效果,将输入轴的高速低扭矩动力转换为输出轴的低速高扭矩动力。
谐波减速器具有许多优点,如结构紧凑、体积小、传动比大、重载能力强等。
同时,由于谐波减速器的齿轮传动采用非接触式传动,摩擦损失小,传动效率高。
因此,谐波减速器广泛应用于机械设备中,如机床、机器人、包装设备等。
谐波减速器是一种结构简单、紧凑、效率高的机械传动装置。
它由输入轴、输出轴、柔性齿轮、刚性齿轮和波发生器等部件组成,通过柔性齿轮和刚性齿轮的咬合,实现动力的传递和转换。
谐波传动减速器

谐波传动减速器引言谐波传动减速器是一种高精度、大扭矩的传动装置,常用于机械设备中的减速装置。
它通过谐波运动的原理,将输入轴的转速转化为输出轴的低速高扭矩运动。
本文将介绍谐波传动减速器的原理、结构和应用领域。
原理谐波传动减速器采用了谐波变速原理,其基本结构由柔性齿轮组、驱动轴、输出轴和外壳组成。
输入轴通过柔性齿轮组和驱动轴之间的摩擦力将动力传递给输出轴,实现减速传动效果。
谐波变速原理是利用了波动齿轮的弯曲變形而产生差动效应,在输入轴上所激起的一个振动波与柔性齿轮传到输出轴时,就会产生相位差,从而导致输出轴产生旋转差异。
谐波传动减速器通过这种差动效应,实现了减速传动的目的。
结构谐波传动减速器的结构由以下几个部分组成:1.输入轴:负责接收动力并将其传递给柔性齿轮组;2.柔性齿轮组:由柔性齿轮和波形发生器组成,负责将输入轴传来的动力转化为波动齿轮的运动;3.驱动轴:连接输出轴和柔性齿轮组,通过与柔性齿轮间的摩擦力将动力传递给输出轴;4.输出轴:接受驱动轴传来的动力,并输出减速后的运动。
谐波传动减速器的结构紧凑,可以实现高精度和大扭矩的传动效果。
应用领域谐波传动减速器由于其独特的结构和优良的性能,在许多领域得到了广泛的应用。
以下是谐波传动减速器的一些应用领域:1.机床行业:谐波传动减速器常用于数控机床的主轴和进给轴的传动系统中,可以提供高精度和高扭矩的运动控制;2.机器人领域:谐波传动减速器用于机器人的关节传动系统,可以提供精确的位置控制和高负载承载能力;3.包装机械:谐波传动减速器可以用于包装机械的输送和定位系统,实现高速稳定的运动传输;4.自动化设备:谐波传动减速器在自动化设备中的应用越来越广泛,可以实现高精度和高可靠性的运动控制;5.石油化工:谐波传动减速器可以用于石油化工设备的传动系统,提供可靠的扭矩输出和长时间连续运行。
优点和局限性谐波传动减速器具有以下优点:1.高精度:谐波传动减速器可以实现高精度的运动控制,输出轴的转矩和角位移精度高;2.大扭矩:谐波传动减速器的扭矩输出能力强,可实现大扭矩传输;3.结构紧凑:谐波传动减速器的设计结构紧凑,可以节省空间;4.反向传动:谐波传动减速器具有双向传动功能,可以实现正转和反转运动。
谐波减速器

谐波传动原理谐波传动Harmonic Drive是由美国发明家C. Walt Musser马瑟于上世纪50年代中期发明创造的。
一、谐波传动装置的构成谐波传动装置主要由三个基本零部件构成,即波发生器、柔轮和刚轮:波发生器:由柔性轴承与椭圆形凸轮组成。
波发生器通常安装在减速器输入端,柔性轴承内圈固定在凸轮上,外圈通过滚珠实现弹性变形成椭圆形。
柔轮:带有外齿圈的柔性薄壁弹性体零件,通常安装在减速器输出端。
刚轮:带有内齿圈的刚性圆环状零件,一般比柔轮多两个轮齿,通常固定在减速器机体上。
二、谐波减速原理谐波做为减速器使用,通常采用波发生器主动、刚轮固定、柔轮输出形式。
当波发生器装入柔轮内圆时,迫使柔轮产生弹性变形而呈椭圆状,使其长轴处柔轮轮齿插入刚轮的轮齿槽内,成为完全啮合状态;而其短轴处两轮轮齿完全不接触,处于脱开状态。
由啮合到脱开的过程之间则处于啮出或啮入状态。
当波发生器连续转动时:迫使柔轮不断产生变形,使两轮轮齿在进行啮入、啮合、啮出、脱开的过程中不断改变各自的工作状态,产生了所谓的错齿运动,从而实现了主动波发生器与柔轮的运动传递。
三、谐波传动特点1.精度高:多齿在两个180度对称位置同时啮合,因此齿轮齿距误差和累积齿距误差对旋转精度的影响较为平均,可得到极高的位置精度和旋转精度。
2.传动比大:单级谐波齿轮传动的传动比可达i=30~500,且结构简单,三个在同轴上的基本零部件就可实现高减速比。
3.承载能力高:谐波传动中,齿与齿的啮合是面接触,加上同时啮合齿数比较多,因而单位面积载荷小,承载能力较其他传动形式高。
4. 体积小、重量轻:相比普通的齿轮装置,体积和重量可以大幅降低,实现小型化、轻量化。
5.传动效率高、寿命长。
6.传动平稳、无冲击,噪音小编号规格1 品种规格我公司的谐波减速器按照柔轮的形状可分为杯形与中空形两大类,每类又根据柔轮的长度又分为标准和短筒两种型号。
同一种机型包括若干传动比。
2 编号规则产品编号由我司英文缩写、产品形式代号、规格代号、减速比、结构代号及输入端与波发生器凸轮连接形式六部分组成,各部分之间用“-”连接。
谐波减速器组成工作原理

1. 引言谐波减速器是一种新型的机械传动装置,它采用柔性变形元件(铰链、齿轮或绳索等)来实现输入轴与输出轴之间的传递力矩和转速的调节。
谐波减速器具有结构简单、体积小、传动精度高、噪音低等优点,广泛应用于机床、机器人、航空航天等领域。
2. 基本构成谐波减速器主要由以下几部分组成: - 转动体:由两个主齿轮和一个柔性变形的谐波波发生器构成。
- 静止体:由内外球面和管状波导构成。
3. 工作原理当输入轴转动时,谐波波发生器周围的柔性变形元件会由于变形而产生谐波波动。
这些谐波波动将从波发生器的输入端传输到输出端,同时由于柔性元件的特性,波导管上的内外球面会产生一定的变形,使得输出轴产生相应的旋转。
具体的工作过程如下:步骤一:变形波导形成初始位置谐波减速器的初始状态是变形波导形成平衡位置,此时内外球面的中心与波导管的中心处于同一轴线上。
同时,谐波波发生器也处于初始位置,使得内外球面之间的柔性变形元件松弛。
步骤二:输入轴转动当输入轴开始转动时,通过输入端的柔性变形元件与谐波波发生器相连的齿轮开始转动。
由于输入端的齿轮和谐波波发生器的齿轮为啮合关系,输入轴的转动会引起谐波波发生器齿轮的转动。
步骤三:谐波波发生器齿轮转动谐波波发生器是谐波减速器的核心部件,它由多个齿轮组成,且齿轮的齿数比输入端和输出端的齿轮多。
当输入轴转动一周时,谐波波发生器的齿轮会转动多周,产生大量的谐波波动。
步骤四:谐波波动传递到输出端谐波波动由谐波波发生器的输出端传输到输出端的波导管上。
谐波波导管由内外球面和波导构成,内外球面中心与波导管中心轴线重合。
当谐波波动传递到波导管时,会引起波导管的变形。
步骤五:变形波导引起输出轴转动波导管的变形会通过内外球面的啮合关系引起输出轴的转动。
由于内外球面的齿数不同,内球面的中心轴线固定不动,而外球面则会根据谐波波动的传输而发生相对位移。
步骤六:输出轴输出动力输出轴的转动即为谐波减速器的输出动力。
输出轴通过与外球面的固联结构连接,将转动动力转移到输出端。
谐波减速器和rv减速器的工作原理

谐波减速器和rv减速器的工作原理一、谐波减速器的工作原理谐波减速器是一种高精度、高效率的减速器,其工作原理是利用谐波振动的原理实现传动。
谐波振动是指在一个系统中,当外界周期性激励力与系统固有频率相同时,系统会出现共振现象,并产生大幅度的振动。
谐波减速器利用这种共振现象,通过将输入轴上的圆弧齿轮转动一周,使得内部柔性齿轮发生多次弹性变形,并将输出轴上的圆弧齿轮带动输出轴旋转。
1.结构组成谐波减速器主要由输入轴、柔性齿轮、驱动环、输出轴和壳体等部分组成。
其中输入轴和输出轴分别连接于机械传动系统中的驱动端和被动端,柔性齿轮位于驱动环内部,并与输入和输出圆弧齿轮相嵌合。
壳体则起到支撑和固定各个部件的作用。
2.工作过程当输入轴旋转时,通过输入圆弧齿轮将转矩传递给柔性齿轮,柔性齿轮在驱动环的作用下发生多次弹性变形,并将转矩传递给输出圆弧齿轮。
输出圆弧齿轮带动输出轴旋转,从而实现减速传动。
3.特点和优势谐波减速器具有高精度、高效率、大扭矩传递和小体积等优点。
其精度可达到0.1-1角分,效率可高达90%以上,扭矩传递范围广泛,且结构紧凑、重量轻、噪音小。
二、RV减速器的工作原理RV减速器是一种基于柔性齿轮原理的减速器,其工作原理是通过输入轴上的蜗杆与输出轴上的蜗轮相嵌合,实现减速传动。
蜗杆和蜗轮之间存在一定的摩擦力,在传动过程中能够起到防止倒转的作用。
1.结构组成RV减速器主要由输入轴、蜗杆、柔性齿轮、蜗轮和壳体等部分组成。
其中输入轴与机械传动系统相连接,蜗杆位于输入轴上,柔性齿轮位于蜗杆的末端,并与蜗轮相嵌合。
壳体则起到支撑和固定各个部件的作用。
2.工作过程当输入轴旋转时,通过蜗杆将转矩传递给柔性齿轮,柔性齿轮与蜗轮相嵌合,使输出轴旋转。
由于蜗杆和蜗轮之间存在一定的摩擦力,在传动过程中能够起到防止倒转的作用。
3.特点和优势RV减速器具有结构紧凑、重量轻、效率高、可靠性好等优点。
其精度可达到0.1-1角分,效率可高达90%以上,扭矩传递范围广泛,且结构简单、易于安装和维护。
- 1、下载文档前请自行甄别文档内容的完整性,平台不提供额外的编辑、内容补充、找答案等附加服务。
- 2、"仅部分预览"的文档,不可在线预览部分如存在完整性等问题,可反馈申请退款(可完整预览的文档不适用该条件!)。
- 3、如文档侵犯您的权益,请联系客服反馈,我们会尽快为您处理(人工客服工作时间:9:00-18:30)。
设计题目
设计“谐波减速器壳体”零件(图S0-7)成组机械加工工艺规程及某一重要工序的成组夹具。
各种壳体年产50-500件不等,按订单生产。
图S0-7 谐波减速器壳体
课程设计说明书(实例二)
1. 零件图分析
1.1 零件的功用
本零件为谐波减速器壳体,用于安装谐波减速器各零件,使其获得正确的装配关系。
其中内孔D1用于安装刚轮,内孔D6用于安装支承低速轴(输出轴)的轴承。
同时壳体外圆表面D7也是谐波减速器的安装基准面。
1.2 零件工艺分析
本零件主体形状为回转体零件,其最主要加工面是内孔D1、D6,外圆D7,以及与内孔D1、D6垂直度要求较高的几个端面,如何保证这些表面本身的加工精度和相互位置精度是加工工艺需要重点考
虑的问题。
本零件的另一特点是螺孔较多,其中螺孔S1位置度要求较高,螺孔S3、S4、和S5也有一定的位置度要求,在工艺上应给予保证。
本零件结构对于4种不同型号的谐波减速器完全一样,仅尺寸有所区别,但也在一定的尺寸范围内。
故可以采用成组工艺和成组夹具。
2. 确定毛坯
2.1 确定毛坯制造方法
本零件的材料是ZL102,故宜采用铸件。
2.2 确定总余量
由表S-14确定外圆、内孔直径上总余量为5mm,端面总余量为2.5mm。
2.3 绘制毛坯图(略)
3. 制定零件工艺规程
3.1 选择表面加工方法
1)由于工件材料为铝合金,故各回转表面及端面均采用车削方法加工:对于重要回转表面及端面采用粗车-半精车-精车加工方法,对于次要回转表面及端面采用粗车或粗车-半精车加工方法。
2)螺孔采用钻孔-攻丝加工方法。
为保证螺孔的位置精度,均应使用钻夹具进行加工。
3.2 选择定位基准
1)精基准选择零件的设计基准是D6孔和大端面C,根据基准重合原则,并同时考虑统一精基准原则,选D6孔和大端面C作为主要定位精基准。
在钻螺纹底孔的工序中,考虑工件定位和装夹的方便,选大端面C和D1孔作为定位精基准。
为保证D7外圆和D6孔的同轴度,加工D6孔时采用D7外圆表面作为定位基准;而在精加工D7外圆表面时,采用D6孔作为定位基准。
这体现了互为基准的原则。
2)粗基准选择为保证加工面与不加工面的位置关系,选不加工的四方面作为定位粗基准。
3.3 拟定零件加工工艺路线
生产车间有普通车床和数控车床可供选择。
考虑到该零件孔的加工难度较大,为了稳定地保证加工精度也为了提高加工效率,精加工采用数控车床。
主要加工工序如下:
1)半精车小端面、D7外圆、台阶面及D4孔(普通车床,四爪卡盘);
2)半精车内空刀槽D3×(L2-L3)(普通车床,三爪卡盘);
3)时效处理;
4)精车大端面,精车D1孔,半精车D2孔,精车D6孔,倒角0.5×45°(数控车床,三爪卡盘);
5)精车D7外圆,精车台阶面,倒角1×45°,精车D4孔,精车L9槽(直径D5)(数控车床,可胀心轴);
6)中间检验:精车各部尺寸;
7)钻4-S3螺纹底孔(台式钻床,钻夹具);
8)钻6-S4螺纹底孔(台式钻床,钻夹具);
9)钻4-S5螺纹底孔(台式钻床,钻夹具);
10)钻S1和S2螺纹底孔,锪沉头孔(台式钻床,钻夹具);
11)中间检验:螺纹底孔尺寸及位置;
12)攻丝:4-S3(台式钻床,钻夹具);
13)攻丝:6-S4(台式钻床,钻夹具);
14)攻丝:4-S5(台式钻床,钻夹具);
15)攻丝:S1和S2(台式钻床,钻夹具);
16)最终检验。
3.4 选择各工序所用机床、夹具、刀具、量具和辅具(参考表S-5,表S-6)
3.5 填写工艺过程卡片(表S0-15)
表S0-15 谐波减速器壳体成组加工工艺过程卡片
3.6 机械加工工序设计
● 工序01
工序卡片见表S0-16。
● 工序04
工序卡片见表S0-17。
● 工序10
工序卡片见表S0-18。
4 成组夹具设计(以10工序夹具为例进行说明)
4.1 功能分析与夹具总体结构设计
本工序要求以壳体大端面(3点)和D1孔(2点)定位,钻S1、S2螺纹底孔,锪D13孔,要求保证位置尺寸L5和L7,其中位置尺寸L5要求较严格,是夹具设计需要着重考虑的问题。
夹具方案设计工件分别以大端面、短圆柱孔和四方面为第一、第二和第三定位基准,可采用大端面+短圆柱面的定位方式,以满足3点定位和2点定位的要求,1点定位则可采用可调支承来实现。
夹具总体结构设计
1)考虑生产批量不大,故采用手动夹紧。
2)S1螺纹底孔有3个,且圆周上均匀分布,故宜做成回转式钻模,采用分度盘和插销进行分度。
3)为适应不同尺寸零件加工需要定位元件应做成可换方式。
4)为减小由于钻削轴向力引起工件变形和位移,应在钻头对应位置上加辅助支承。
5)为便于安装工件,钻模板采用铰链式结构。
6)尺寸L5要求较严格,故钻S1螺纹底孔的钻模板位置固定,调整钻S2螺纹底孔的钻模板位置,以适应不同孔距要求。
4.2 夹具设计计算(略)
4.3 夹具制造与操作说明
本夹具分度与定位装置是夹具设计制造的关键。
定位装置既要满足不同型号壳体零件的定位尺寸要求,又要保证定位端面至S1螺纹底孔钻套的距离,为此必须严格按夹具零件图纸要求进行加工。
同时夹具在转换加工零件时,必须进行仔细的调整和检测。
装夹工件时,用力要适当,以免产生夹紧变形。
锪D13孔时,须将相应的钻模板掀起,利用锪钻自身导向。
夹具装配图如下:
图S0-8 成组钻模(点击图放大)
其中件号1~9为可换件,应根据不同型号零件进行更换。
件号11~45为非标准夹具元件或自制标准夹具元件,件号51~81为外购标准件。