制动摩擦材料高速摩擦学性能的主要影响因素.
影响汽车制动性能的主要因素分析

影响汽车制动性能的主要因素分析发表时间:2019-03-20T09:39:47.543Z 来源:《电力设备》2018年第28期作者:高建李根[导读] 摘要:随着国民经济的不断增长,人们生活水平也得到了全面提高,越来越多的家庭都使用汽车出行。
(长城汽车股份有限公司技术中心河北省汽车工程技术研究中心保定 071000) 摘要:随着国民经济的不断增长,人们生活水平也得到了全面提高,越来越多的家庭都使用汽车出行。
对于汽车交通而言,出行安全是第一位。
其中,汽车的制动功能首当其冲。
要想更好地对汽车制动进行维护,就要了解影响汽车制动系统性能的关键因素,这也是对我国汽车行业的进一步发展创新的准备。
关键词:影响;汽车制动性能;主要因素 1汽车制动性能的三个评价指标 1.1制动效能制动效能通常是指汽车在匀速行驶或高速行驶过程中,遇到障碍物或突发情况出现时,驾驶员紧急踩下制动,车辆能迅速降低行驶速度,直至停车时的能力。
制动效能主要包括制动距离、制动力、制动减速度和制动时间四个方面。
制动距离,在测试实验中一般是指汽车在2.5m宽的试车道上,以每小时50Km的速度行驶,驾驶员紧急制动,踩下制动踏板等车辆完全停下时,车辆所经过的距离。
制动距离与车辆空载、满载、车型有关,不同的车型在空载、满载情况下制动距离标准不一样。
同时与制动初速度、制动最大减速度和制动系统协调时间因素有密切的关系。
在实际车辆行驶当中,制动协调时间和制动距离越短的车辆,它的制动性能效果就越好。
制动力变化的特性间接地反映了制动距离的变化。
制动力使汽车强制减速度到车辆完全停车的本质因素。
在测试过程中通常用制动检测仪对制动踏板力进行检测,制动力过大超出标准范围,驾驶强度增大,驾驶员容易疲劳,直接影响车辆行车安全。
制动力越大,制动减速度也越大。
在制动过程中,制动减速度越大,则制动效果越好。
制动减速度是评价制动性能的重要参数之一。
1.2制动效能的恒定性制动效能的恒定性通常是指制动器具有抗水衰退和热衰退的能力。
C_C刹车材料的摩擦磨损性能与机理

C C刹车材料的摩擦磨损性能与机理F ricti on and W ear P rop erties and M echan is mof Carbon2Carbon Com po sites谈竞霜,张保法,姜 海,李东生(北京百慕航材高科技股份有限公司,北京100095)TAN J ing2shuang,ZHAN G B ao2fa,J I AN G H ai,L I Dong2sheng(B ai m tec M aterial Co1,L td1,B eijing100095,Ch ina)摘要:简要介绍了C C复合材料在刹车领域的应用,综述了几十年来人们对C C刹车材料摩擦磨损性能与机理的研究结果,对C C复合材料的摩擦磨损特征和影响摩擦磨损性能的一些因素作了介绍。
关键词:C C复合材料;摩擦磨损;性能;机理中图分类号:TB332 文献标识码:A 文章编号:100124381(2001)1020021204Abstract:T he p ap er in troduced b riefly the app licati on s of carbon2carbon com po sites in the field of b rak ing and overview ed the research resu lts over the p ast several decades on fricti on and w ear p rop2 erties and m echan is m of carbon2carbon com po sites1T he facto rs influenced the fricti on and w ear characteristics w ere also discu ssed1Key words:carbon2carbon com po site;fricti on and w ear;p roperty;m echan is m1 C C复合材料在刹车领域的应用 1973年C C复合材料第一次用于飞机刹车。
高速列车车辆制动系统的热力学性能分析与优化设计

高速列车车辆制动系统的热力学性能分析与优化设计随着高速列车的快速发展,车辆制动系统的热力学性能分析与优化设计变得日益重要。
这不仅涉及到列车的安全性和稳定性,还关乎乘客的舒适度和行车效率。
因此,研究和改进高速列车车辆制动系统的热力学性能至关重要。
一、热力学性能分析1. 系统组成高速列车车辆制动系统主要由制动器、刹车盘、刹车片、气动设备和控制系统组成。
其中,制动器是实现制动操作的核心组件,刹车盘和刹车片则负责实现制动力的传递。
气动设备负责控制制动系统的气动效能,而控制系统则用于对制动系统进行监控和控制。
2. 制动机理制动器通过施加在刹车盘上的摩擦力来减速和停车列车。
刹车片与刹车盘之间的接触会产生摩擦热量,而制动器的冷却系统则负责散热。
刹车片材料的选择对于制动器的性能至关重要,需要考虑其摩擦系数、耐磨性和热膨胀系数等因素。
3. 热力学性能指标分析高速列车车辆制动系统的热力学性能主要关注以下指标:制动力、制动距离、制动效率和制动温度。
制动力是制动器产生的力量,需要足够强大以确保列车的安全性。
制动距离是列车从开始制动到完全停车所需的距离,需要尽量缩短以提高行车效率。
制动效率是制动力与列车质量的比值,需要最大化以确保制动系统的有效性。
制动温度是制动过程中产生的热量所引起的温度增加,需要控制在合理范围内以避免制动片热衰减。
二、热力学性能优化设计1. 刹车盘材料优化刹车盘作为传递制动力的重要部件,其材料选择对于热力学性能的优化至关重要。
优化设计的目标是降低刹车盘的质量和降低其热膨胀系数,以减少制动过程中由于摩擦所引起的热量。
采用先进的纳米材料技术和复合材料技术,可以实现刹车盘材料的强度提升和热膨胀系数的降低。
2. 刹车片材料优化刹车片材料对于制动效果和制动温度有重要影响。
传统的刹车片材料如金属材料存在制动效率不高、热衰减严重等问题。
优化设计的目标是提高刹车片的摩擦系数和耐磨性,同时降低其热膨胀系数,以减少制动过程中的热衰减和提高制动效果。
摩擦速度对铜基摩擦材料摩擦磨损性能影响

摩擦速度对铜基摩擦材料摩擦磨损性能影响摩擦速度是影响铜基摩擦材料摩擦磨损性能的重要因素之一。
在摩擦过程中,摩擦速度会对材料表面的磨损、摩擦热和摩擦学性能产生影响。
本文将对铜基摩擦材料在不同摩擦速度下的摩擦磨损性能进行分析研究。
一、铜基摩擦材料的基本性能铜基摩擦材料是一种新型的高性能摩擦材料,具有优良的摩擦学性能、高温稳定性和抗磨损性能。
其主要成分为铜基合金,常用的铜基材料有铜-锡合金、铜-锌合金、铜-镍合金等。
二、摩擦速度对铜基摩擦材料摩擦磨损性能的影响1. 磨损率变化摩擦速度对铜基摩擦材料的磨损率有一定的影响。
当摩擦速度增加时,材料表面受力变化,摩擦热和磨擦力增大,容易产生热膨胀和磨损现象,从而加剧材料的磨损。
而当摩擦速度较低时,材料表面的温度和应力较小,磨损率相对较低。
2. 摩擦学性能变化随着摩擦速度的增加,铜基摩擦材料的摩擦系数也会随之增加,摩擦学性能也会发生相应变化。
对于一些要求高速摩擦的工况,如高速铁路、航空等领域,需要选择抗磨损、摩擦系数稳定的铜基摩擦材料。
3. 磨损形态变化在摩擦过程中,材料表面的磨损形态也会发生变化。
随着摩擦速度的增加,磨损形态会由点状磨损、区域性磨损逐渐转变为大面积磨损,甚至产生严重的表面磨损与裂纹。
三、总结综上所述,摩擦速度是影响铜基摩擦材料摩擦磨损性能的重要因素,受摩擦速度影响的性能包括磨损率、摩擦学性能和磨损形态等。
在实际应用中,需要根据工况的不同选择不同的铜基摩擦材料以获得最佳的摩擦磨损性能。
针对铜基摩擦材料的摩擦磨损性能影响因素之一的摩擦速度,需要进一步研究其具体影响机理,以便更好地指导其实际应用。
首先,随着摩擦速度的增加,材料表面的温度升高,摩擦热增大,从而加速了材料表面的磨损。
此外,在高速摩擦过程中,摩擦力也随之增大,这对于材料表面的磨损、剥落等现象也有较大的促进作用。
其次,不同的铜基材料对于摩擦速度的敏感程度可能也有所不同,因此需要对不同的材料进行具体实验验证。
刹车速度对C/C复合材料制动摩擦性能的影响

刹车速度对C/C复合材料制动摩擦性能的影响近年来,随着车辆运行速度的提高以及对安全性需求的不断增强,制动系统作为车辆行驶的重要保障系统之一,对制动摩擦性能的要求也越来越高。
而汽车制动系统的实现离不开制动材料的性能。
其中,C/C复合材料因其低密度、高强度和优异的耐高温性能而被广泛运用于车辆制动系统中。
然而,制动时的刹车速度会对C/C复合材料制动摩擦性能产生影响,我们将在本文中进行探讨。
首先,我们需要了解C/C复合材料的制动机理。
C/C复合材料由碳纤维和碳基材料构成,摩擦时,摩擦面的高温会导致碳基材料氧化,因此在高温下具有较高的热稳定性和抗氧化性。
同时,C/C复合材料具有较低的热膨胀系数和较好的自润滑性,能够保证制动时稳定的摩擦性能。
其次,刹车速度的不同会对C/C复合材料的制动摩擦性能产生影响。
当刹车速度较慢时,摩擦面温度较低,氧化反应比较微弱,此时C/C复合材料的制动性能较为稳定。
但当刹车速度加快,摩擦面温度升高,氧化反应加剧,C/C复合材料产生更多的气体和灰尘,影响了制动性能。
因此,刹车速度越快,C/C复合材料的制动性能就越容易产生不稳定现象。
最后,针对上述问题,我们可以采取一些技术手段来改善制动性能。
例如,在制动系统中增加冷却装置,能够有效地降低摩擦面的温度,避免高温引起的氧化反应。
同时,也可以通过优化制动材料的成分及工艺,提高其耐高温性能和抗氧化性能。
总之,刹车速度对C/C复合材料制动摩擦性能产生着重要的影响。
对于车辆制动系统的设计和制造,我们需要充分考虑这一因素,采取适当的措施来提高C/C复合材料制动性能,保障驾驶安全。
此外,C/C复合材料的摩擦性能除了受刹车速度的影响外,还受到其他外界因素的影响。
例如,制动过程中的油温、制动器的磨损状态、路面湿度等都会对C/C复合材料的制动性能产生影响。
因此,在制动系统设计和制造中,需要考虑到这些因素,并通过精密测量、实验研究等方法来探究其对制动性能的影响,从而进行优化设计。
制动速度对铜基粉末冶金闸片材料摩擦学性能的影响

制动速度对铜基粉末冶金闸片材料摩擦学性能的影响王毅;刘铁军;朱军;马强【摘要】以Sn+SiO2+Al2O3+CaF2作为摩擦组元,石墨+Pb作为润滑组元,制备铜基粉末冶金列车闸片材料,在MM-1000Ⅱ型摩擦试验机上进行摩擦试验,测定制动速度在120~200 km/h范围内材料的摩擦因数、磨损量与表面温度,并观察摩擦表面形貌,研究制动速度对该材料摩擦学性能的影响.结果表明:在制动速度<180 km/h时,随制动速度增加,闸片材料的摩擦因数在0.41~0.46之间波动,但制动速度达到200 km/h时,摩擦因数显著减小至0.32,摩擦因数稳定性总体较好.材料的磨损量随制动速度增大而增加,但在制动速度达到180 km/h时磨损量趋于稳定,为119 mg.低速制动下材料的磨损机理主要为疲劳磨损,高速制动时主要为磨粒磨损和氧化磨损.【期刊名称】《粉末冶金材料科学与工程》【年(卷),期】2017(022)003【总页数】6页(P366-371)【关键词】铜基闸片材料;粉末冶金;制动速度;摩擦;磨损;显微组织【作者】王毅;刘铁军;朱军;马强【作者单位】郑州航空工业管理学院,郑州 450046;郑州航空工业管理学院,郑州450046;西北工业大学力学与土木建筑学院,西安 710129;西北工业大学力学与土木建筑学院,西安 710129【正文语种】中文【中图分类】TG46.2铁路车辆的制动器由制动盘和闸片构成,制动效果与闸片材料的性能密切相关。
我国高速列车常用的制动闸片主要有粉末冶金闸片和合成闸片[1−3]。
合成闸片称为三元复合物,是将树脂或橡胶粘结基体、各种增强纤维和摩擦性能调节剂等混合后加压加热固化而制得的材料。
合成闸片材料在制动时,由于温度升高和热负荷增大,制动功率低,造成制动性能稳定性差,难以满足列车高速运行的要求。
随着列车的不断提速,对制动器性能的要求更加苛刻。
粉末冶金闸片性能稳定,具有良好的耐磨性、导热性、抗粘性和多孔性等优点[4−5]。
影响摩擦系数的主要因素

影响摩擦系数的主要因素两个物体之间的摩擦力与其法向压力之比值为摩擦系数,有静摩擦系数和动摩擦系数之分。
同一摩擦副在相同条件下,静摩擦系数大于动摩擦系数。
摩擦系数的大小取决于摩擦种类、材料种类、摩擦面的粗糙度等条件,不同种类的摩擦系数大致如下:干摩擦系数为0.1—0.8,边界摩擦系数为0.05一0.1;液体摩擦系数为0.001一0.1;滚珠摩擦系数为0.001—0.03,滚柱摩擦系数为0.002一0.07 影响摩擦系数的主要因素有:1:材料的性质相同金属或互溶性加大的金属摩擦副容易发生粘着现象,使摩擦系数增大。
不同金属由于互溶性差,不易发生粘着,摩擦系数一般比较低。
2:表面膜的存在基建在空气中总有一层氧化膜,可以使摩擦系数降低。
3:速度和温度的影响4:载荷的影响对大多数物质来说,载荷的变化会直接影响到摩擦系数。
5:振动的影响6:光洁度的影响材料的摩擦系数与温度摘要:本文介绍了温度变化对材料摩擦系数的影响,并分析了实际应用中对薄膜摩擦系数的实际检测要求。
关键词:摩擦系数,温度,粘滑1、摩擦系数摩擦系数是对两表面摩擦力的一种量度,它表征了材料的摩擦行为。
薄膜表面的摩擦系数取决于薄膜表面的粘着性(表面张力和结晶度)、添加剂(爽滑剂、颜料等)、以及表面抛光。
在进行以下操作工序时需要严格控制材料的摩擦系数,如当薄膜越过自由转辊、袋成型、产品缠绕膜、以及包装袋及其它容器的堆放。
除了材料的内部可变因素能够影响材料的摩擦系数,环境因素(如机器运转的速度、温度、静电积累、以及湿度)也能影响摩擦系数的试验结果。
2、温度对摩擦系数的影响高分子材料分子运动状态的改变按照动力学的观点称作松弛。
温度升高时,一方面可提高各运动单元的热运动能力,另一方面由于热膨胀,分子间距离增加,即高聚物内部的自由体积增加,这就增大了各运动单元活动空间,有利于分子运动,使松弛时间缩短,松弛过程加快。
伴随着高聚物的松弛,它的热力学性质、粘弹性能和其它物理性质会发生急剧地改变。
影响摩擦系数的主要因素

影响摩擦系数的主要因素两个物体之间的摩擦力与其法向压力之比值为摩擦系数,有静摩擦系数和动摩擦系数之分。
同一摩擦副在相同条件下,静摩擦系数大于动摩擦系数。
摩擦系数的大小取决于摩擦种类、材料种类、摩擦面的粗糙度等条件,不同种类的摩擦系数大致如下:干摩擦系数为0.1—0.8,边界摩擦系数为0.05一0。
1;液体摩擦系数为0.001一0。
1;滚珠摩擦系数为0。
001—0.03,滚柱摩擦系数为0.002一0.07影响摩擦系数的主要因素有:1:材料的性质相同金属或互溶性加大的金属摩擦副容易发生粘着现象,使摩擦系数增大。
不同金属由于互溶性差,不易发生粘着,摩擦系数一般比较低。
2:表面膜的存在基建在空气中总有一层氧化膜,可以使摩擦系数降低。
3:速度和温度的影响4:载荷的影响对大多数物质来说,载荷的变化会直接影响到摩擦系数。
5:振动的影响6:光洁度的影响材料的摩擦系数与温度摘要:本文介绍了温度变化对材料摩擦系数的影响,并分析了实际应用中对薄膜摩擦系数的实际检测要求.关键词:摩擦系数,温度,粘滑1、摩擦系数摩擦系数是对两表面摩擦力的一种量度,它表征了材料的摩擦行为。
薄膜表面的摩擦系数取决于薄膜表面的粘着性(表面张力和结晶度)、添加剂(爽滑剂、颜料等)、以及表面抛光。
在进行以下操作工序时需要严格控制材料的摩擦系数,如当薄膜越过自由转辊、袋成型、产品缠绕膜、以及包装袋及其它容器的堆放.除了材料的内部可变因素能够影响材料的摩擦系数,环境因素(如机器运转的速度、温度、静电积累、以及湿度)也能影响摩擦系数的试验结果。
2、温度对摩擦系数的影响高分子材料分子运动状态的改变按照动力学的观点称作松弛。
温度升高时,一方面可提高各运动单元的热运动能力,另一方面由于热膨胀,分子间距离增加,即高聚物内部的自由体积增加,这就增大了各运动单元活动空间,有利于分子运动,使松弛时间缩短,松弛过程加快.伴随着高聚物的松弛,它的热力学性质、粘弹性能和其它物理性质会发生急剧地改变。
树脂基复合制动材料摩擦学性能的影响因素分析

树脂基复合制动材料摩擦学性能的影响因素分析唐明;林有希【摘要】汽车制动材料是汽车制动器中的关键材料,其性能直接关系到制动系统运行的可靠性和稳定性。
分析了影响树脂基复合制动材料摩擦学性能的一些因素,讨论了基体改性与增强纤维对材料摩擦磨损性能的影响,并总结了复合制动材料以后的研究方向。
%Automobile brake material is the key material for automobile brake. Its performance is directly related to the reliability and stability of the braking system. This paper analyzes the impact factors on tribology performance of resin-based compound brake,dis-cusses the effect of compound modification and enhancement fiber on friction and wear properties of materials,and summarizes the research direction of brake materials in future.【期刊名称】《机械制造与自动化》【年(卷),期】2014(000)006【总页数】4页(P59-62)【关键词】树脂;摩擦磨损;制动;机理【作者】唐明;林有希【作者单位】福州大学机械工程及自动化学院,福建福州350108;福州大学机械工程及自动化学院,福建福州350108【正文语种】中文【中图分类】TH117.10 引言自从20世纪60年代提出摩擦学这个概念,这门学科就一直备受关注,也使其成为发展最快的学科之一。
制动摩擦学作为摩擦学研究领域里的重要分支,其发展也极其迅速[1]。
制动器制动摩擦性能机理及其影响因素分析

45制动器制动摩擦性能机理及其影响因素分析苏 辉 (中检西部检测有限公司)制动器俗称刹车,它是依靠制动摩擦副之间的相互摩擦作用实现速度调节,从而达到减速停车等目的的一种装置,一般也称为摩擦制动器或机械制动器。
在汽车、摩托车等交通运输设施中,无一例外都要为其配备制动器来实现速度调节、制动停车的功能。
制动过程中,制动装置是将机械系统的运动动能通过摩擦作用转化为热能和其它形式的能量消耗掉,因此制动过程的本质是一个能量转换的过程,它通过制动器摩擦副之间的机械摩擦作用,将车辆行驶或设备运转时产生的动能转换成热能消耗掉,从而使其减速或停止。
制动器根据摩擦副结构形式的不同,主要可分为鼓式制动器和盘式制动器两大类,本文主要介绍盘式制动器的制动摩擦性能机理及其影响因素。
1 盘式制动器的简介及分类盘式制动器又称为碟式制动器,它有液压驱动和气压驱动两种形式,通常为液压驱动。
其主要零部件有:制动盘、制动分泵、制动钳、制动油管等。
制动盘用合金钢制造并固定在车轮上,随车轮转动,按照其摩擦副中固定元件结构的不同,又可分为全盘式制动器和钳盘式制动器两大类。
在全盘式制动器中摩擦副的旋转元件及固定原件均为圈型盘,制动时各盘摩擦表面全部接触,其作用原理与摩擦式离合器相同。
由于此类制动器的制动盘散热不好,所以其实际应用没有钳盘式制动器广泛。
钳盘式制动器的固定摩擦原件是制动块,它安装在与车轴相连接但不能绕车轴轴线旋转的制动钳中,在此类盘式制动器中,制动块与制动盘的接触面积很小。
Su Hui (CCIC WEST Testing Co., Ltd.)Analysis Onbrake Friction Performance Mechanismand its Influencing Factors按照制动钳结构形式的不同,钳盘式制动器又可分为:定钳式盘式制动器和浮钳式盘式制动器两大类,其结构示意图如图1所示。
定钳式盘式制动器:制动钳固定不动,制动盘与车轮(a )定钳式盘式制动器(b )浮钳式盘式制动器进油口制动盘制动盘摩擦块摩擦块活塞轮毂制动卡钳制动卡钳活塞进油口导向销轮毂图1 钳盘式制动器结构示意图46 相连并能在制动钳的开口槽中旋转。
增强纤维含量对汽车摩擦材料性能的影响

增强纤维含量对汽车摩擦材料性能的影响随着汽车行业的发展,对汽车摩擦材料的性能要求也越来越高。
其中,纤维含量作为影响材料性能的重要因素之一,其对摩擦材料性能的影响备受关注。
本文将从纤维含量对摩擦材料的摩擦性能、磨损性能以及力学性能等方面进行探讨。
1.纤维含量对摩擦性能的影响纤维含量的增加能够显著提高摩擦材料的摩擦性能。
这是因为纤维能够增加材料的接触面积和摩擦力。
同时,纤维能够防止材料表面的高温烧结现象,有效提高摩擦材料的摩擦性能。
同时,纤维含量的增加也能够增强材料的耐热性能。
在高温环境下,纤维可以起到隔热作用,减少材料表面的温度升高,从而提高材料的摩擦性能。
2.纤维含量对磨损性能的影响纤维含量的增加也能够显著提高摩擦材料的磨损性能。
这是因为纤维可以形成一种类似于交织的结构,防止材料表面的磨损现象。
同时,纤维还能够增加材料的硬度,从而减缓材料的磨损速度。
3.纤维含量对力学性能的影响纤维含量的增加能够显著提高摩擦材料的力学性能。
这是因为纤维可以增加材料的韧性和强度,提高摩擦材料的抗拉强度和抗压强度。
同时,纤维也能够提高材料的抗疲劳性能,减少材料的断裂率。
总之,纤维含量作为影响摩擦材料性能的重要因素之一,能够显著影响摩擦材料的摩擦性能、磨损性能以及力学性能等方面。
因此,为了提高摩擦材料的性能,应该适当增加纤维含量。
然而,纤维含量不是越高越好,纤维含量增加到一定程度后,摩擦材料性能反而会受到负面影响。
这是因为过高的纤维含量会导致材料的刚度增加,形变能力降低,导致材料的断裂率和疲劳寿命降低。
因此,具体的纤维含量和性能之间的关系,需要在实践中进行深入研究和实验验证。
在具体应用中,应根据不同的需求和要求,选择适当的纤维含量,平衡不同性能指标之间的矛盾,以实现最佳性能。
另外,加入纤维的摩擦材料也需要合适的制备工艺。
例如,采用注塑、压制等传统工艺生产的摩擦材料含纤率较低;而高纤维含量的摩擦材料往往采用注射成型等尖端加工技术进行生产。
浅析气压盘式制动器磨擦片磨损过快的原因

盘式制动作为制动方式的一种,以其制动间隙小、制动响应快、制动强度大、制动距离短、水稳定性强、散热性能好、热衰退少、安全性高、结构紧凑,维修简便等优点而受到推崇。
盘式制动器在客车上的应用,还处于起步阶段,离普及还有相当长的一段距离。
作为一项较新的技术,欧美国家自20世纪90年代初开始将盘式制动器用于公交客车。
至2000年左右,前、后制动均采用盘式制动器已经成为欧美国家城市公交客车的标准配置。
一、盘式制动摩擦片磨损过快问题提出盘式制动技术随着国外的一些车辆带入我国后,在与国内城市道路状况和运载负荷的结合方面还存在着不少问题,制动摩擦片磨损过快的问题是困扰城市客车持续使用这一技术的一大原因。
所谓客车盘式制动器摩擦片磨损过快,是指与前、后桥都采用鼓式制动器而车辆其他配置完全相同的城市客车相比较而言的。
采用盘式制动器的车辆平均行驶25000~27000km就需要更换制动摩擦片,少数车辆甚至在行驶不足2万km的时候,就需要更换制动摩擦片。
盘式制动器的这种表现根本无法满足相关标准中关于公交车辆制动摩擦片使用寿命不得低于3万km的要求。
而前、后桥都采用鼓式制动器的同种类型的城市客车,其制动摩擦片的使用寿命平均为6万km。
经过调查表明,国内几个著名客车生产企业生产的前、后桥全部采用盘式制动器的客车,也不同程度地存在的摩擦片磨损过快的问题。
尤其是在北京、上海等大城市公交市场运行的客车,这种情况表现得更为突出。
二、磨损量与车辆行驶里程之间的关系由摩擦学可知,正常工作期内摩擦片的表面磨损量与车辆行驶里程之间的关系服从一元线性规律,即W=ωL式中:W-总摩损量:ω-单位行程磨损量:L-车辆行驶里程就显得特别重要。
随着车辆的行驶里程的不断增加,盘式制动器摩擦片的磨损越来越大,当厚度接近磨损极限时,对客车的行驶安全来说,就构成一种严重的威胁。
此时,如果驾驶员或技术管理人员稍有疏忽,不认真监控摩擦片的厚度、不及时更换摩擦片,就会致使车辆面临摩擦片被磨光、制动盘被磨坏,进而导致制动功能失效、造成车毁人亡的严重后果。
汽车制动系统摩擦片材料基本知识

汽车制动系统摩擦片材料根本知识摩擦材料一、概论摩擦材料是一种应用在动力机械上,依靠摩擦作用来执行制动和传动功能的部件材料。
它主要包括制动器衬片〔刹车片〕和离合器面片〔离合器片〕。
刹车片用于制动,离合器片用于传动。
任何机械设备及运动的各种车辆都必须要有制动或传动装置。
摩擦材料是这种制动或传动装置上的关键性部件。
它最主要的功能是通过摩擦来吸收或传递动力。
如离合器片传递动力,制动片吸收动能。
它们使机械设备及各种机动车辆能够平安可靠地工作。
所以说摩擦材料是一种应用广泛又甚关键地材料。
摩擦材料是一种高分子三元复合材料,是物理及化学复合体。
它是由高分子粘结剂〔树脂及橡胶〕、增强纤维和摩擦性能调节剂三大类组成及其它配合剂构成,经一系列生产加工而制成的制品。
摩擦材料的特点是具有良好的摩擦系数和耐磨损性能,同时具有一定的耐热性和机械强度,能满足车辆或机械的传动及制动的性能要求。
它们被广泛应用在汽车、火车、飞机、石油钻机等各类工程机械设备上。
民用品如自行车、洗衣机等作为动力的传递或制动减速用不可缺少的材料。
二、摩擦材料开展简史自世界上出现动力机械和机动车辆后,在其传动和制动机构中就使用摩擦片。
初期的摩擦片系用棉花、棉布、皮革等作为基材,如:将棉花纤维或其织品浸渍橡胶浆液后,进展加工成型制成刹车片或刹车带。
其缺点:耐热性较差,当摩擦面温度超过120℃后,棉花和棉布会逐渐焦化甚至燃烧。
随着车辆速度和载重的增加,其制动温度也相应提高,这类摩擦材料已经不能满足使用要求。
人们开场寻求耐热性好的、新的摩擦材料类型,石棉摩擦材料由此诞生。
石棉是一种天然的矿物纤维,它具有较高的耐热性和机械强度,还具有较长的纤维长度、很好的散热性,柔软性和浸渍性也很好,可以进展纺织加工制成石棉布或石棉带并浸渍粘结剂。
石棉短纤维和其布、带织品都可以作为摩擦材料的基材。
更由于其具有较低的价格〔性价比〕,所以很快就取代了棉花及棉布而成为摩擦材料中的主要基材料。
机动车制动摩擦片磨损机理与磨损特征分析

机动车制动摩擦片磨损机理与磨损特征分析随着机动车数量不断增长,制动系统的安全性和性能变得尤为重要。
在机动车的制动系统中,摩擦片是一个关键组件,它在车辆行驶时起到制动的重要作用。
然而,由于长时间的使用和各种外在因素的影响,摩擦片会产生磨损,从而影响制动性能。
因此,了解机动车制动摩擦片的磨损机理和磨损特征对于维护制动系统的安全性和性能至关重要。
一、机动车制动摩擦片磨损机理机动车制动摩擦片的磨损机理可以分为几个方面。
1.摩擦磨损摩擦磨损是机动车制动摩擦片磨损最常见的机理之一。
在摩擦制动过程中,摩擦片与制动盘之间产生的摩擦力使得摩擦片表面产生摩擦磨损现象。
长时间的使用和剧烈的制动行为会导致摩擦片表面逐渐磨损,减少了摩擦片与制动盘之间的接触面积,从而降低了制动性能。
2.热磨损在高速制动时,摩擦片产生的摩擦力会导致摩擦片表面温度上升,从而引发热磨损。
热磨损是机动车制动摩擦片磨损的一种重要机理。
高温下,摩擦片的摩擦系数会变化,表面温度过高还可能导致摩擦片材料的结构发生变化,进而引发更严重的磨损。
3.疲劳磨损长时间的使用和频繁的制动行为会导致摩擦片材料发生疲劳现象,从而引发疲劳磨损。
疲劳磨损是机动车制动摩擦片磨损的一种常见机制。
在疲劳磨损过程中,摩擦片表面会产生微小裂纹,随着使用时间的增长,这些裂纹会扩展并最终导致摩擦片的磨损。
二、机动车制动摩擦片磨损特征分析磨损特征是研究机动车制动摩擦片磨损的重要内容,通过分析摩擦片的磨损特征可以更好地了解制动系统的工作状态和寿命。
1.磨屑堆积磨屑堆积是机动车制动摩擦片磨损的一个主要特征。
在摩擦片磨损过程中,摩擦片会产生大量磨屑。
这些磨屑会随着制动时产生的热气流被带走,同时也会在制动系统内部堆积。
磨屑堆积的程度可以用来评估摩擦片的磨损程度和制动系统的工作状态。
2.颜色变化摩擦片的颜色变化也是研究磨损特征的一个重要方面。
在制动过程中,摩擦片表面会发生摩擦磨损现象,从而导致表面温度的上升和材料结构的变化。
高速列车粉末冶金制动闸片的制备与摩擦磨损性能研究
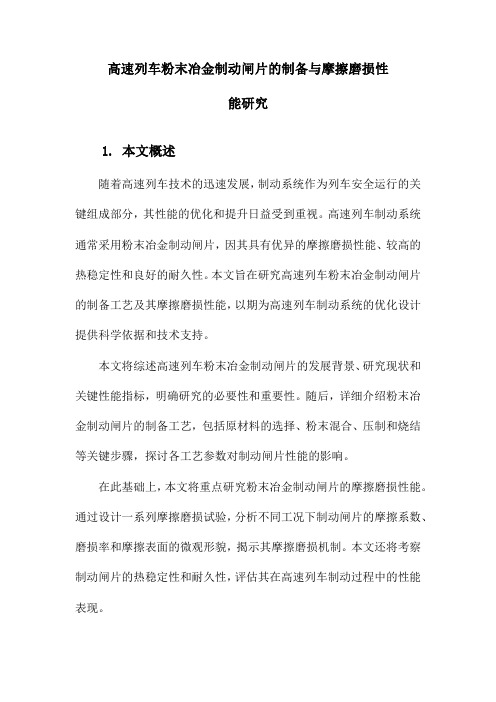
高速列车粉末冶金制动闸片的制备与摩擦磨损性能研究1. 本文概述随着高速列车技术的迅速发展,制动系统作为列车安全运行的关键组成部分,其性能的优化和提升日益受到重视。
高速列车制动系统通常采用粉末冶金制动闸片,因其具有优异的摩擦磨损性能、较高的热稳定性和良好的耐久性。
本文旨在研究高速列车粉末冶金制动闸片的制备工艺及其摩擦磨损性能,以期为高速列车制动系统的优化设计提供科学依据和技术支持。
本文将综述高速列车粉末冶金制动闸片的发展背景、研究现状和关键性能指标,明确研究的必要性和重要性。
随后,详细介绍粉末冶金制动闸片的制备工艺,包括原材料的选择、粉末混合、压制和烧结等关键步骤,探讨各工艺参数对制动闸片性能的影响。
在此基础上,本文将重点研究粉末冶金制动闸片的摩擦磨损性能。
通过设计一系列摩擦磨损试验,分析不同工况下制动闸片的摩擦系数、磨损率和摩擦表面的微观形貌,揭示其摩擦磨损机制。
本文还将考察制动闸片的热稳定性和耐久性,评估其在高速列车制动过程中的性能表现。
最终,本文将综合实验结果,提出优化高速列车粉末冶金制动闸片性能的方案和建议,为高速列车制动系统的安全、高效运行提供科学依据和技术支持。
通过本研究,期望能够推动高速列车制动技术的发展,为我国高速列车制动系统的自主研发和性能提升贡献力量。
2. 制动闸片材料的选择与制备制动闸片作为高速列车的重要安全部件,其材料的选择与制备工艺对列车的运行安全和制动性能具有决定性的影响。
本研究中,我们经过深入调研和试验,最终选择粉末冶金工艺制备制动闸片。
粉末冶金工艺能够制备出具有优良机械性能和摩擦磨损性能的复合材料,且易于实现材料的均匀分布和微观组织的优化。
在材料选择上,我们主要考虑了材料的硬度、耐磨性、抗热衰退性和热稳定性等因素。
通过对比分析,我们选择了以铁基粉末为基体,添加适量的铜、石墨、二硫化钼等润滑剂,以及稀土元素进行强化的复合材料。
这种材料组合既保证了制动闸片具有较高的硬度和耐磨性,又能够减少制动过程中的摩擦热,防止制动热衰退。
摩擦机理及的影响因素分析Word版

摩擦机理及的影响因素分析摘要:阐述了轮胎与路面的摩擦机理,即路面与轮胎间的分子引力作用、轮胎与路面间黏着作用以及轮胎胎面橡胶弹性变形。
通过分析三种因素,得出路面、轮胎、行车速度及交通荷载、环境以及施工技术对摩擦系数的影响程度。
关键字:摩擦机理;影响因素;弹性变形前言随着科技的不断发展,对摩擦学研究也逐步深入,学者们渐渐认识到摩擦系数不仅仅是特定物品的一项固有参数,而是对于一个特定的摩擦对象,很多因素都会影响着摩擦系数。
1摩擦机理摩擦可定义为两个物体接触面间的阻力及对应的能量损耗。
顾名思义,轮胎摩擦学主要研究轮胎与道路间相互作用时的力学特征及材料性质。
轮胎中主要组成部分橡胶属于黏弹性材料,荷载、实际接触面积、滑移速率及温度等都会影响其摩擦性能。
根据以上理论,轮胎与路面的摩擦机理主要由以下几个因素构成。
1.1路面与轮胎间的分子引力作用汽车运行时,轮胎与路面间距离非常小,此时轮胎分子及路面分子间的分子力不可忽视,并成为轮胎与路面间摩擦力的组成部分。
这种摩擦力取决于路面材料和轮胎类型,同时也受实际接触面积的大小、水膜、路面污染、湿度、尘埃等因素的影响。
1.2轮胎与路面间黏着作用研究指出,路面材料与轮胎胎面间也会产生黏着作用。
对橡胶轮胎进行长期磨耗试验后,可在胎面上发现路面材料的微小颗粒;同时在路面面层上也附着有微小橡胶粒状物。
与此同时,轮胎与路面材料间的静电引力作用也可证明轮胎与路面产生的相互黏着作用,而此时的摩擦力的黏着分力为剪断轮胎与路面间粘着点所需的力。
橡胶轮胎性能、路面材料类型、实际接触面积、相互的作用力都对由黏着作用产生的摩擦力有显著的影响。
1.3轮胎胎面橡胶弹性变形橡胶轮胎属于高弹性黏弹性材料,在与路面较大微凸体挤压、碰撞时,橡胶材料会反复发生弹性形变。
当轮胎相对于路面处于无滑移条件下,由胎面橡胶形变产生的应力在水平方向合力为零,并不会导致摩擦力的产生。
但对于属于高弹性黏弹性材料的橡胶轮胎,橡胶内部分子链由于变形而发生相互扭动及摩擦作用,使变形滞后于应力,进而损失部分能量,而这一现象有助于提高轮胎的抗滑能力。
汽车制动摩擦系数影响因素浅谈

汽车制动摩擦系数影响因素浅谈作者:徐申敏韩友国吴洪涛来源:《时代汽车》2019年第03期摘要:制动摩擦系数大小是衡量汽车制动性的重要参数,影响制动摩擦系数的根源为制动片的材料属性。
由于汽车正常行驶中,每次制动初速度、制动液压均有变化,导致每次制动摩擦系数有差异。
本论文结合制动摩擦原理,着重从温度、材料属性、制动压力、制动初速度四个方面,浅要分析了这些因素对制动摩擦系数的影响。
关键词:摩擦系数;制动性汽车制动过程实际就是摩擦片与制动盘接触的过程,通过制动片与制动盘的直接接触摩擦产生热能,从而转换汽车制动中需要消耗的动能。
而制动过程中最重要一点,那就是制动摩擦系数的大小,其中摩擦系数过高过低都会影响制动性能。
GB 5763-2008中规定盘式制动器摩擦系数随温度上升到350℃,摩擦系统温度在0.25~0.70之间。
目前市面上常用摩擦系数按照SAE J866-2012中的EF代码,即正常摩擦系数:0.251 摩擦系数的定义GB 5763中对摩擦系数的定义为:摩擦力与加在试片上的法向力的比值。
其数学表达式为如下公式(1):u=式(1)中:u为摩擦系数,f为摩擦力(总摩擦距离的后半部分稳定的摩擦力的平均值),F为加在试片上的法向力。
目前常见的盘式制动器的平均摩擦系数定义[1]ua=式(2)中:Ma为平均摩擦力矩;AP为制动片的摩擦面积;p为平均制动压强;p0为克服制动片回位弹簧作用力消除制动间隙而需施加的制动压强;Dm为有效摩擦直径。
Ma和p 均为制动过程中达到设定值的95%时开始记录到制动终了时的时间段内的平均值。
2 制动摩擦系统影响因素制动系统作为汽车中最重要的系统之一,制动系统的好坏直接影响到整车安全方面,而影响制动系统一个重要因素就是制动摩擦系数的大小及其稳定性,本文从温度、摩擦材料属性、制动压力、制动初速度来描述摩擦系数的影响因素。
2.1 温度摩擦系数的稳定性直接影响制动器工作的稳定性,摩擦系数随着温度而变化的特性,主要反映在制动器的热衰退上。
影响摩擦系数的主要因素

影响摩擦系数的主要因素两个物体之间的摩擦力与其法向压力之比值为摩擦系数,有静摩擦系数和动摩擦系数之分。
同一摩擦副在相同条件下,静摩擦系数大于动摩擦系数。
摩擦系数的大小取决于摩擦种类、材料种类、摩擦面的粗糙度等条件,不同种类的摩擦系数大致如下:干摩擦系数为0.1—0.8,边界摩擦系数为0.05一0。
1;液体摩擦系数为0.001一0。
1;滚珠摩擦系数为0。
001—0.03,滚柱摩擦系数为0.002一0.07影响摩擦系数的主要因素有:1:材料的性质相同金属或互溶性加大的金属摩擦副容易发生粘着现象,使摩擦系数增大。
不同金属由于互溶性差,不易发生粘着,摩擦系数一般比较低。
2:表面膜的存在基建在空气中总有一层氧化膜,可以使摩擦系数降低。
3:速度和温度的影响4:载荷的影响对大多数物质来说,载荷的变化会直接影响到摩擦系数。
5:振动的影响6:光洁度的影响材料的摩擦系数与温度摘要:本文介绍了温度变化对材料摩擦系数的影响,并分析了实际应用中对薄膜摩擦系数的实际检测要求.关键词:摩擦系数,温度,粘滑1、摩擦系数摩擦系数是对两表面摩擦力的一种量度,它表征了材料的摩擦行为。
薄膜表面的摩擦系数取决于薄膜表面的粘着性(表面张力和结晶度)、添加剂(爽滑剂、颜料等)、以及表面抛光。
在进行以下操作工序时需要严格控制材料的摩擦系数,如当薄膜越过自由转辊、袋成型、产品缠绕膜、以及包装袋及其它容器的堆放.除了材料的内部可变因素能够影响材料的摩擦系数,环境因素(如机器运转的速度、温度、静电积累、以及湿度)也能影响摩擦系数的试验结果。
2、温度对摩擦系数的影响高分子材料分子运动状态的改变按照动力学的观点称作松弛。
温度升高时,一方面可提高各运动单元的热运动能力,另一方面由于热膨胀,分子间距离增加,即高聚物内部的自由体积增加,这就增大了各运动单元活动空间,有利于分子运动,使松弛时间缩短,松弛过程加快.伴随着高聚物的松弛,它的热力学性质、粘弹性能和其它物理性质会发生急剧地改变。
- 1、下载文档前请自行甄别文档内容的完整性,平台不提供额外的编辑、内容补充、找答案等附加服务。
- 2、"仅部分预览"的文档,不可在线预览部分如存在完整性等问题,可反馈申请退款(可完整预览的文档不适用该条件!)。
- 3、如文档侵犯您的权益,请联系客服反馈,我们会尽快为您处理(人工客服工作时间:9:00-18:30)。
制动摩擦材料高速摩擦学性能的主要影响因素Ξ马东辉张永振陈跃官宝(河南科技大学材料科学与工程学院河南洛阳 471039摘要 :综述了高速条件下速度、温度、压力对制动材料摩擦学性能的影响。
重点讨论了摩擦表面的相对滑动速度对摩擦学性能的影响。
关键词 :相对滑动速度压力温度The Main Influencing F actor of H igh 2speed FrictionMa Donghui Zhang Y ongzhen Chen Y ue Shangguan Bao(Department of Materials Science , Henan University of Science &T echn ology , Lu oyang 471039, ChinaAbstract :The in fluence of friction under different pressure , temperature and slide velocity condition introduced , and the in fluence of relative slide velocity on the frictional interfaces was discussed.K eyw ords :R elative Slide V elocity Pressure T emperature高速摩擦学 , 是研究摩擦副处在相对高的滑动速度时 , 两个表面之间相互作用、践的学科。
, 对制动装置及制动材料的性能也提出了更高的要求。
例如制动材料要有足够而稳定的摩擦系数 , 动、静摩擦系数之差小 ; 良好的导热性、较大的热容量和一定的高温机械强度 ; 良好的耐磨性和抗粘着性 , 不易擦伤对偶件 , 无噪声 ; 低成本 , 对环境无污染等。
传统的制动材料已不能满足高速条件下的需要 , 这就必须开发新的摩擦制动材料 , 研究高速摩擦条件下各种因素对材料摩擦学性能的影响。
但这方面前人的研究工作不多 , 本文综述了这方面的研究进展 , 着重讨论了高速条件下速度、温度、正压力对材料摩擦学性能的影响。
1速度对材料摩擦学性能的影响(1 相对滑动速度 v 对摩擦系数μ的影响一般情况下 , 相对滑动速度 v 越大 , 摩擦系数μ越小。
具体减小的程度 , 不同的学者根据各自的实验条件得出的结论也不一致。
如法国人 Boehet 通过机车车辆的制动试验得出了摩擦系数与滑动速度的关系表达式为 [1]μ=k/(1+0173v(1式中 :k 为系数 , 对于干燥钢轨 k =0145, 潮湿钢轨0v (m/s 。
Frank G 提出了摩擦系数与速度的经验公式μ=μ0+e -cv(2 式中:μ0———静摩擦系数 ; C ———常数。
对铁基烧结闸片在速度 10~32m/s 和压力01005~1MPa 范围内进行的摩擦试验得出 :图 1摩擦系数与滑动速度的关系 [2]1 当速度增大时摩擦系数随着减小 (图 1 。
2 当压力增大时摩擦系数增大 ; 但在较高压力下 , 随速度增大摩擦系数减小更快。
对摩擦系数的影响主要是由于摩擦发热升温引起的 , 如果配偶材料的导热率较高及温升较小 , 那么影响不大。
对于 Pb 、 Sn 等导热率和熔点都较低的金属 , 高速下 , 由于表面层熔化或软化 , 滑动摩擦系数随着相对速度增加会出现最小值。
μ值最小时 , 摩擦表面开始形成熔化膜 , 摩擦系数回升的快慢取决于熔化膜的粘度、厚度、速度、接触面积等因素 [3]。
在低的和中等的滑动速度时 , 摩擦主要是由于接触区的局部粘着和剪切引起的 , 摩擦阻力表现为表44《润滑与密封》Ξ基金项目 :河南科技大学基金项目 (20020003 1作者简介 :马东辉 , 男 , 1976年生 , 硕士研究生 1E -mail :mdh760509@1631com 1面发热 , 可以认为这种发热效应对总的摩擦机理不会有大的影响 , 但在很高滑动速度下 , 金属表面产生极为强烈的摩擦热 , 它将从本质上改变滑动的表面状态。
(2 相对滑动速度对材料磨损率的影响通常情况下 , 磨损率随相对滑动速度的增大而减小 , 达到一定程度 , 开始随速度的增大而增大。
在这个过程中 , 磨损机理可能发生了变化。
居毅 [4]对碳钢表面 C 2N 共渗层在高速干摩擦状态下进行了研究 , 得出其磨损率随载荷和滑动速度变化的关系如图 2。
可见在不同载荷下 , 随着滑动速度的增加 , 磨损率逐渐降低 , 当滑动速度达到 35m/s 时 , 随着滑动速度的增加 , 磨损率明显增大。
由此可以推测 , 当滑动速度在 35m/s 左右 , 磨损机理可能发生了转变。
2与磨损率的关系 [1]通过 SE M 观察可以发现 , 当滑动速度在 25~35m/s 之间变化时 , 试样磨损表面的“ 凹坑” 尺寸随着滑动速度的增加而减小 , 减小。
35m/s 时随着滑动速度的进一步提高 , 试样磨损表面出现了“流线”特征 , 这是因为随着滑动速度的提高 , 试样磨损表面温度提高 , 试样表层和亚表层软化 , 产生塑性变形。
磨损表面的微突体在高速摩擦状态的“ 闪点”温度可能接近熔点 , 而在宏观观察时 , 其磨损表面很平整。
当滑动速度达到 45m/s , 此时试样磨损表面出现了大量的微裂纹和熔斑 , 大量的微裂纹对应于较高的磨屑剥落几率 , 亦意味着磨损率增大。
通过磨损表面的 XPS 分析表明 :当滑动速度为 25m/s 时 , 试样磨损表面形成的氧化膜主要由 Fe 2O 3组成。
当滑动速度增大至 45m/s 时 , 试样磨损表面的氧化膜主要由 FeO 组成。
另一方面 , 从摩擦副接触表面温度的变化也可以推测试样表面的氧化物类型。
当摩擦表面平均温度大于 500℃时才可能形成 FeO , 而摩擦表面平均温度大于 200℃ , 即可以形成 Fe 2O 3。
由此可以得出结论 :当滑动速度为25m/s 时 , 试样磨损表面主要含有 Fe 2O 3; 45m/s 时 , , , 20#钢 , 当滑动速度达到, 磨损率最小 ; 此后随着速度的进一步提高 , 磨损率显著提高 , 共渗层经历从轻微磨损向严重磨损的转变。
(3 制动初速度对磨损率、摩擦系数的影响对于不同的材料 , 制动初速度对磨损率、摩擦系数的影响不同。
例如 C/C 复合材料与特种铸铁。
杨勇 , 吴洁君等人研究了制动初速度对 C/C 复合材料摩擦学性能影响 [5~7], 结果表明(表 1 :表 1不同制动速度下 C/C 复合材料的摩擦性能 [5]制动速度 v (m/s 平均摩擦系数μcp 单位面积能量 W S (J/cm 2平均功率 P S (W/m 2 稳定系数 S 尺寸损失(μm 磨损质量损失 (mg50118163124116017501090157100129684171501201781124514915013519871428 713015711065104200140279512405130167618240147250140436116499150176161251 1210628013545011049514016636100163127300135401510505110166391041861301 随着制动初速度的增大 , C/C 复合材料制动盘的摩擦系数逐渐增大 , 当制动初速度在 20~25m/s 范围内时摩擦系数出现峰值。
此后随着制动初速度的继续增大 , 摩擦系数仍维持较高值。
2 当制动初速度小于 15m/s 时 , 线性磨损和磨损质量损失均较小 , 当制动初速度大于 15m/s 时 , 磨损质量损失明显增大 , 当制动初速度达到 30m/s 时制动盘的磨损质量损失最大。
3 低速时 C/C 复合材料制动盘磨损表面由较薄的磨屑层所覆盖 , 磨损较轻微 ; 随着制动速度的增加(大于 15m/s , 磨屑不断增多并形成较厚的表面膜层。
在高速 (28~30m/s 下 , 由于剧烈的氧化和剪切作用 , 大量的基质炭发生氧化剥落 , 同时碳纤维被磨断和拔出 , 因此磨损剧烈。
钱坤才等人对高速列车特种铸铁制动盘进行了研究 [8], 用特种铸铁制动盘和半金属合成闸片进行台架试验。
结果表明 , 随着制动初速度的提高 , 平均摩擦系数降低。
制动初速度从 120km/h 提高到 250km/h , 平均摩擦系数μ从 01331降到 01303。
2温度对材料摩擦学性能的影响542003年第 6期摩擦制动过程是将物体的运动动能转化为热能和其他形式的能量 , 从而达到制动的目的 , 其中约有 90%使物质内部的分子动能增加 , 表现为温度的升高。
由于摩擦热效应产生的温升和接触应力 , 它们对摩擦副表层的结构与性能会产生一定的影响。
(1 对表面膜的影响从物理吸附膜和化学吸附膜看 [3], 摩擦使被吸附分子的热运动加快 , 随温升发生失向、散乱、脱附 , 而失去作用。
从反应膜看 , 摩擦热补给化学反应所需的活化能 , 不仅提高反应速率 , 增加反应膜的厚度 ; 还可能在超过反应温度之后 , 出现新的化学反应物。
例如铁的氧化 , 温升加快了氧离子向里扩散和铁离子向外扩散 , Fe 2O 3减少而 Fe 3O 4增多 ; 并且氧化膜在超过 750℃时出现 FeO 层 , 相应的显微硬度由 4900N/mm 2降低到2940N/mm 2。
(2 对基体表层的影响温升活化基体表层 ,属 , ,六方在 417℃由 03增到 017。
对于固熔体 , , 例如淬火钢中 , 体心立方的马氏体在750~800℃很快通过共格转变的方式转为面心立方的奥氏体 ; 温升还可能使有序转变为无序 ; 使摩擦副之间易于相互扩散 , 发生粘着。
鲍登 (Bowdon 等人的试验表明 [3]:大多数金属摩擦系数对应于环境 700-800℃出现最小值。
高聚物是弹性材料 , 对温度很敏感。
随着温度升温由玻璃相转变为橡胶相 , 因粘着作用加强而使μ增大 ; 温度进一步升高 , 因力学性能下降而使μ下降。
此外温度对材料表面变形性能和表层应力也有一定的影响。
刘佐民在对 M 50高速钢进行高温摩擦试验表明 [9]:当试验温度处于100~300℃范围时 , 材料的磨损率随着温度的上升而明显增大 , 而摩擦因数的增大甚微 , 基本保持在 0164左右 ; 当温度高于 400℃时 , M 50高速钢的摩擦和磨损都明显减小 , 主要原因是界面微接触点处材料发生软化融熔而在摩擦面上形成了一层金属膜 , 使材料的磨损由微切削向金属膜间对摩转变。
在这种情况下 , 材料的磨损率主要取决于表面膜的承载能力。