汽车制动摩擦材料的性能要求及影响因素分析
陶瓷制动摩擦材料的分析及性能探究

陶瓷制动摩擦材料的分析及性能探究汽车产业快速发展,对汽车的制动系统要求越来越高,作为汽车刹车片的摩擦材料要具有良好的热传递性和耐磨损性,同时摩擦系数要适度,而且还要具备优良的隔热性能,本文对摩擦材料的组成和性能进行了分析和探究,得出陶瓷制动摩擦材料热稳定性和热传导率的性能优异,并且还具有良好的硬度大、污染少、安全性、耐磨性、使用寿命长、轻量化等优点。
前言目前,汽车产业、汽车制造环境的快速发展,使汽车制造过程向高速化、安全化、稳定和可靠的方向发展,同时对汽车的制动系统要求越来越高。
由于汽车刹车过程都是靠摩擦产生的,而且都需要一种耐磨的材料铸成的摩擦片,与汽车的旋转部分紧密贴合,致使摩擦力快速增大,让旋转部位快速停止转动,车辆就停止下来,在此过程中伴随着温度的变化和能量的传递,会使局部温度急剧升高,从而影响摩擦性能。
因此,作为汽车刹车片的摩擦材料要具有良好的热传递性和耐磨损性,同时摩擦系数要适度,不能过大或过小,而且还要具备优良的隔热性能[1]。
传统刹车片制动时起主要作用的材料是金属,而陶瓷刹车片起主要作用的是陶瓷,因此具备噪声小的优点。
与此同时,陶瓷刹车片摩擦材料热稳定性和热传导率的性能优异,并且还具有良好的硬度大、污染少、安全性、耐磨性、使用寿命长、轻量化等优点[2]。
一、摩擦材料的组成刹车片作为汽车制动体系中最重要的部位,性能优异的刹车片的,是通过多种摩擦材料的混合压制而成的,每种摩擦材料的含量对刹车片摩擦性能有很大的影响,所以我们应该控制每种摩擦材料的含量,使其刹车性能达到最优化。
其中,长纤维、粘合剂、填料和摩擦改性剂对刹车片的性能影响最大。
刹车片的摩擦材料一般包括三部分,粘合剂、纤维增强材料和填料,每一种材料所起的作用都不同,通过对这三种材料和其他材料的混合、热处理等工艺,在经过一系制作工艺生产出的成品。
1.粘合剂作为刹车片材料中的粘合剂,不只是树脂和橡胶,现在已经展到使用在高温下具有特殊性能的金属粉末或金属硫化物,是为了减少摩擦材料中树脂的含量,填补高温条件下树脂和橡胶的不足,从而改善高温条件下摩擦材料的不足之处,使在性能上更加优化。
刹车片新材料摩擦磨损机理实验解析

刹车片新材料摩擦磨损机理实验解析刹车片是汽车安全行驶过程中至关重要的部件之一。
为了提高刹车片的性能和耐久性,制造商们一直在寻求新的材料和制造技术。
其中,研究刹车片新材料的摩擦磨损机理是非常重要的一环,它可以帮助我们更好地了解刹车片在使用过程中的摩擦磨损特性,并为新材料的研发提供指导。
摩擦磨损是指两个物体相对运动时表面之间的相互作用所导致的材料剥离、磨损和变形现象。
在刹车片的使用中,摩擦磨损机理主要包括热磨损、表面摩擦、车轮截面磨损等。
首先,热磨损是刹车片磨损的主要机理之一。
当刹车片与刹车盘之间的接触摩擦产生高温时,刹车片表面的材料会发生相变和加热,形成热软化层。
这种热软化层的存在会使刹车片表面的摩擦系数降低,增加刹车片和刹车盘的接触面积,从而增加了磨损。
此外,刹车片磨损生成的高温还会导致刹车片内部材料的结构改变,进一步加剧磨损。
其次,表面摩擦是刹车片磨损的另一个重要机理。
刹车片与刹车盘之间的高速接触会产生大量的摩擦热,使刹车片表面的温度升高。
随着温度升高,刹车片表面的材料会剥离、氧化和软化,从而导致表面磨损。
除了温度的影响,表面粗糙度、材料硬度、润滑剂的使用等也会影响刹车片的表面摩擦特性。
最后,车轮截面磨损也是刹车片磨损的一个重要机理。
车轮截面磨损指的是刹车片表面与车轮之间的相互作用磨损。
当刹车片与车轮之间的接触面积增大时,摩擦力也会相应增加,从而导致刹车片的磨损。
车轮截面磨损的程度取决于刹车片和车轮的材料特性、接触面积和接触压力等因素。
针对以上磨损机理,科学家们已经采取了一系列的实验手段来进一步研究和解析刹车片的摩擦磨损特性。
其中,摩擦副试验是一个常用的手段之一。
在这样的实验中,科学家们通过模拟刹车片与刹车盘之间的接触摩擦过程,对刹车片表面的摩擦磨损进行定量分析。
实验数据的收集和分析可以帮助科学家们了解不同材料在不同条件下的磨损特性,为刹车片的研发提供指导。
除了摩擦副试验,还有一些其他的实验手段也被应用于刹车片新材料的摩擦磨损机理研究中。
汽车制动摩擦系数影响因素浅谈
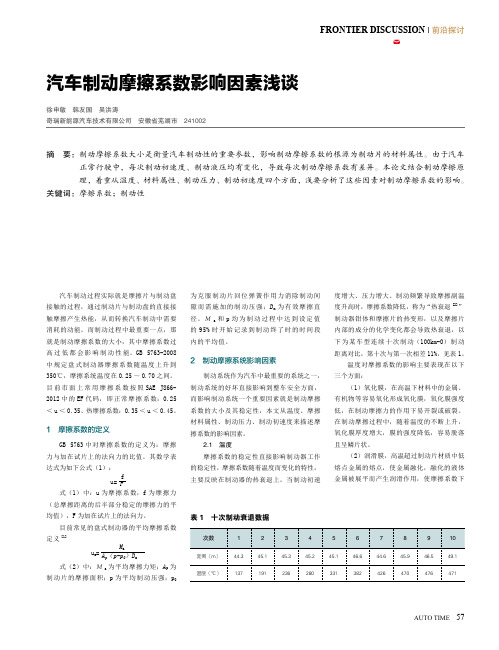
FRONTIER DISCUSSION | 前沿探讨 时代汽车 www.cnautotime.com汽车制动摩擦系数影响因素浅谈徐申敏 韩友国 吴洪涛奇瑞新能源汽车技术有限公司 安徽省芜湖市 241002摘 要: 制动摩擦系数大小是衡量汽车制动性的重要参数,影响制动摩擦系数的根源为制动片的材料属性。
由于汽车正常行驶中,每次制动初速度、制动液压均有变化,导致每次制动摩擦系数有差异。
本论文结合制动摩擦原理,着重从温度、材料属性、制动压力、制动初速度四个方面,浅要分析了这些因素对制动摩擦系数的影响。
关键词:摩擦系数;制动性汽车制动过程实际就是摩擦片与制动盘接触的过程,通过制动片与制动盘的直接接触摩擦产生热能,从而转换汽车制动中需要消耗的动能。
而制动过程中最重要一点,那就是制动摩擦系数的大小,其中摩擦系数过高过低都会影响制动性能。
GB 5763-2008中规定盘式制动器摩擦系数随温度上升到350℃,摩擦系统温度在0.25~0.70之间。
目前市面上常用摩擦系数按照SAE J866-2012中的EF代码,即正常摩擦系数:0.25<u<0.35、热摩擦系数:0.35<u<0.45。
1 摩擦系数的定义GB 5763中对摩擦系数的定义为:摩擦力与加在试片上的法向力的比值。
其数学表达式为如下公式(1):u=f F式(1)中:u为摩擦系数,f为摩擦力(总摩擦距离的后半部分稳定的摩擦力的平均值),F为加在试片上的法向力。
目前常见的盘式制动器的平均摩擦系数定义[1]u a =MaAp(p-p)Dm式(2)中:Ma 为平均摩擦力矩;AP为制动片的摩擦面积;p为平均制动压强;p0为克服制动片回位弹簧作用力消除制动间隙而需施加的制动压强;Dm为有效摩擦直径。
Ma和p均为制动过程中达到设定值的95%时开始记录到制动终了时的时间段内的平均值。
2 制动摩擦系统影响因素制动系统作为汽车中最重要的系统之一,制动系统的好坏直接影响到整车安全方面,而影响制动系统一个重要因素就是制动摩擦系数的大小及其稳定性,本文从温度、摩擦材料属性、制动压力、制动初速度来描述摩擦系数的影响因素。
影响汽车制动性能的主要因素分析

影响汽车制动性能的主要因素分析发表时间:2019-03-20T09:39:47.543Z 来源:《电力设备》2018年第28期作者:高建李根[导读] 摘要:随着国民经济的不断增长,人们生活水平也得到了全面提高,越来越多的家庭都使用汽车出行。
(长城汽车股份有限公司技术中心河北省汽车工程技术研究中心保定 071000) 摘要:随着国民经济的不断增长,人们生活水平也得到了全面提高,越来越多的家庭都使用汽车出行。
对于汽车交通而言,出行安全是第一位。
其中,汽车的制动功能首当其冲。
要想更好地对汽车制动进行维护,就要了解影响汽车制动系统性能的关键因素,这也是对我国汽车行业的进一步发展创新的准备。
关键词:影响;汽车制动性能;主要因素 1汽车制动性能的三个评价指标 1.1制动效能制动效能通常是指汽车在匀速行驶或高速行驶过程中,遇到障碍物或突发情况出现时,驾驶员紧急踩下制动,车辆能迅速降低行驶速度,直至停车时的能力。
制动效能主要包括制动距离、制动力、制动减速度和制动时间四个方面。
制动距离,在测试实验中一般是指汽车在2.5m宽的试车道上,以每小时50Km的速度行驶,驾驶员紧急制动,踩下制动踏板等车辆完全停下时,车辆所经过的距离。
制动距离与车辆空载、满载、车型有关,不同的车型在空载、满载情况下制动距离标准不一样。
同时与制动初速度、制动最大减速度和制动系统协调时间因素有密切的关系。
在实际车辆行驶当中,制动协调时间和制动距离越短的车辆,它的制动性能效果就越好。
制动力变化的特性间接地反映了制动距离的变化。
制动力使汽车强制减速度到车辆完全停车的本质因素。
在测试过程中通常用制动检测仪对制动踏板力进行检测,制动力过大超出标准范围,驾驶强度增大,驾驶员容易疲劳,直接影响车辆行车安全。
制动力越大,制动减速度也越大。
在制动过程中,制动减速度越大,则制动效果越好。
制动减速度是评价制动性能的重要参数之一。
1.2制动效能的恒定性制动效能的恒定性通常是指制动器具有抗水衰退和热衰退的能力。
影响汽车制动性能的主要因素

制动初速度高时,需要通过制动消耗的运动能量也大,故制动距离会延长。制动初速度愈高,通过制动器转化产生的热量也愈多,制动器的温度也愈高。制动蹄片的摩擦性能会随温度的升高而降低,导致制动力衰减,制动距离增长。
六、利用发动机制动
发动机的内摩擦力矩和泵气损耗可用来作为制动时的阻力矩,而且发动机的散热能力要
影名称
汽车使用性能与检测技术
第9讲
章节
第五章汽车制动性能
课题
影响汽车制动性能的主要因素
学时
2
本讲主要内容
汽车汽车制动性能的影响因素
本讲教学目的
知识点:
了解影响汽车制动性能的因素
能力点:
学会分析汽车制动性能好坏的原因
教学重点
理解汽车制动性能的指标及影响行车安全性的因素
三、汽车载质量的影响
对于载质量较大的汽车。因前、后轮的制动器设计,一般不能保证在任何道路条件下都使其制动力同时达到附着极限,所以汽车的制动距离就会由于载质量的不同而发生差异。实践证明,对于载质量为3t以上的汽车,大约载质量每增加lt,其制动距离平均要增加1.0m。即使是同一辆汽车,在装载质量和方式不同时,由于重心位置变动,也会影响汽车的制动距离。
四、车轮制动器的影响
车轮制动器的摩擦副、制动鼓的构造和材料,对于制动器的摩擦力矩和制动效能的热衰退都有很大影响。在设计制造中应选用好的结构型式及材料,在使用维修中也应注意摩擦片的选用。
制动器的结构型式不同,其制动器效率不同。制动器效能因数大,则在制动鼓半径和制动器张力相同的条件下,制动器所能产生的制动力矩也大。但当制动器摩擦副的摩擦系数下降时,其制动力矩将显着下降,制动性能的稳定性较差。
发动机的制动效果对汽车制动性的影响很大。它不仅能在较长的时间内发挥制动作用,
制动摩擦材料高速摩擦学性能的主要影响因素.

制动摩擦材料高速摩擦学性能的主要影响因素Ξ马东辉张永振陈跃官宝(河南科技大学材料科学与工程学院河南洛阳 471039摘要 :综述了高速条件下速度、温度、压力对制动材料摩擦学性能的影响。
重点讨论了摩擦表面的相对滑动速度对摩擦学性能的影响。
关键词 :相对滑动速度压力温度The Main Influencing F actor of H igh 2speed FrictionMa Donghui Zhang Y ongzhen Chen Y ue Shangguan Bao(Department of Materials Science , Henan University of Science &T echn ology , Lu oyang 471039, ChinaAbstract :The in fluence of friction under different pressure , temperature and slide velocity condition introduced , and the in fluence of relative slide velocity on the frictional interfaces was discussed.K eyw ords :R elative Slide V elocity Pressure T emperature高速摩擦学 , 是研究摩擦副处在相对高的滑动速度时 , 两个表面之间相互作用、践的学科。
, 对制动装置及制动材料的性能也提出了更高的要求。
例如制动材料要有足够而稳定的摩擦系数 , 动、静摩擦系数之差小 ; 良好的导热性、较大的热容量和一定的高温机械强度 ; 良好的耐磨性和抗粘着性 , 不易擦伤对偶件 , 无噪声 ; 低成本 , 对环境无污染等。
传统的制动材料已不能满足高速条件下的需要 , 这就必须开发新的摩擦制动材料 , 研究高速摩擦条件下各种因素对材料摩擦学性能的影响。
刹车速度对C/C复合材料制动摩擦性能的影响

刹车速度对C/C复合材料制动摩擦性能的影响近年来,随着车辆运行速度的提高以及对安全性需求的不断增强,制动系统作为车辆行驶的重要保障系统之一,对制动摩擦性能的要求也越来越高。
而汽车制动系统的实现离不开制动材料的性能。
其中,C/C复合材料因其低密度、高强度和优异的耐高温性能而被广泛运用于车辆制动系统中。
然而,制动时的刹车速度会对C/C复合材料制动摩擦性能产生影响,我们将在本文中进行探讨。
首先,我们需要了解C/C复合材料的制动机理。
C/C复合材料由碳纤维和碳基材料构成,摩擦时,摩擦面的高温会导致碳基材料氧化,因此在高温下具有较高的热稳定性和抗氧化性。
同时,C/C复合材料具有较低的热膨胀系数和较好的自润滑性,能够保证制动时稳定的摩擦性能。
其次,刹车速度的不同会对C/C复合材料的制动摩擦性能产生影响。
当刹车速度较慢时,摩擦面温度较低,氧化反应比较微弱,此时C/C复合材料的制动性能较为稳定。
但当刹车速度加快,摩擦面温度升高,氧化反应加剧,C/C复合材料产生更多的气体和灰尘,影响了制动性能。
因此,刹车速度越快,C/C复合材料的制动性能就越容易产生不稳定现象。
最后,针对上述问题,我们可以采取一些技术手段来改善制动性能。
例如,在制动系统中增加冷却装置,能够有效地降低摩擦面的温度,避免高温引起的氧化反应。
同时,也可以通过优化制动材料的成分及工艺,提高其耐高温性能和抗氧化性能。
总之,刹车速度对C/C复合材料制动摩擦性能产生着重要的影响。
对于车辆制动系统的设计和制造,我们需要充分考虑这一因素,采取适当的措施来提高C/C复合材料制动性能,保障驾驶安全。
此外,C/C复合材料的摩擦性能除了受刹车速度的影响外,还受到其他外界因素的影响。
例如,制动过程中的油温、制动器的磨损状态、路面湿度等都会对C/C复合材料的制动性能产生影响。
因此,在制动系统设计和制造中,需要考虑到这些因素,并通过精密测量、实验研究等方法来探究其对制动性能的影响,从而进行优化设计。
摩擦材料

填料
摩擦材料组分中的填料,主要是由摩擦性能调节剂和配合剂组成。使用填料的目的,主要有以下几个方面: (1)调节和改善制品的摩擦性能、物理性能与机械强度。 (2)控制制品热膨胀系数、导热性、收缩率,增加产品尺寸的稳定性。 (3)改善制品的制动噪音。 (4)提高制品的制造工艺性能与加工性能。 (5)改善制品外观质量及密度。 (6)降低生产成本。 在摩擦材料的配方设计时,选用填料必须要了解填料的性能以及在摩擦材料的各种特性中所起到的作用。正 确使用填料决定摩擦材料的性能,在制造工艺上也是非常重要的。 根据摩擦性能调节剂在摩擦材料中的作用,可将其分为“增磨填料”与“减磨填料”两类。摩擦材料本身属 于摩阻材料,为能执行制动和传动功能要求具有较高的摩擦系数,因此增摩填料是摩擦性能调节剂的主要成分。 数
物理性能
摩擦系数
摩擦系数是评价任何一种摩擦材料的一个最重要的性能指标,关系着摩擦片执行传动和制动功能的好坏。它 不是一个常数,而是受温度、压力、摩擦速度或表面状态及周围介质因素等影响而发生变化的一个数。理想的摩 擦系数应具有理想的冷摩擦系数和可以控制的温度衰退。由于摩擦产生热量,增高了工作温度,导致了摩擦材料 的摩擦系数发生变化。
介绍
介绍
摩擦材料是一种高分子三元复合材料,是物理与化学复合体。它是由高分子粘结剂(树脂与橡胶)、增强纤 维和摩擦性能调节剂三大类组成及其它配合剂构成,经一系列生产加工而制成的制品。
摩擦材料的特点是具有良好的摩擦系数和耐磨损性能,同时具有一定的耐热性和机械强度,能满足车辆或机 械的传动与制动的性能要求。它们被广泛应用在汽车、火车、飞机、石油钻机等各类工程机械设备上。民用品如 自行车、洗衣机等作为动力的传递或制动减速用不可缺少的材料。
发动机制动工况下汽车制动器摩擦性能分析

发动机制动工况下汽车制动器摩擦性能分析汽车制动器是汽车安全性的重要组成部分之一。
汽车制动器的使用可以让车辆在行驶过程中便捷地停止。
在制动时,摩擦片会与制动盘或制动鼓摩擦,形成摩擦力,从而停止车辆的运动。
但是,在一些特殊的情况下,制动器的摩擦性能可能会受到一定的影响。
本文将针对发动机制动工况下的汽车制动器摩擦性能进行分析。
一、发动机制动工况下汽车制动器的摩擦性能特点发动机制动指的是通过发动机的压缩式刹车方式来减速。
这种刹车方式对汽车制动器的要求更高,因为在制动的同时,发动机也产生了强大的负载。
这种负载会影响到汽车制动器的摩擦性能,表现在以下几个方面:1. 摩擦噪音:发动机制动时汽车制动器产生过多的热量,会导致制动器上的摩擦材料变形。
这种变形会导致制动器产生噪音。
2. 摩擦副磨损:发动机制动的过程中,制动材料的磨损速度与常规刹车时相比会更快。
这种磨损会导致摩擦片变薄,从而降低制动器的性能。
3. 制动力变化:发动机制动的特殊工况下,制动器的制动力也会受到影响。
这种影响可能表现为制动器制动力的不稳定或降低。
二、如何提高发动机制动工况下汽车制动器的摩擦性能为了提高发动机制动工况下汽车制动器的摩擦性能,我们可以从以下几个方面进行改进:1. 选择适当的制动材料:为了适应发动机制动的特殊工况,我们可以选择一些耐高温、摩擦系数稳定的制动材料。
例如一些高峰值摩擦系数和良好稳定性的有机复合材料,如金属陶瓷制动材料等。
2. 加强制动器的散热系统:制动时会产生很多热能,而散热系统的缺陷会导致制动器的性能下降。
因此,为了保证制动器的性能,在设计制动器时需要考虑合理的散热系统。
3. 提高制动器的硬度:摩擦片的硬度与其摩擦性能有着密切的关系。
因此,我们可以通过选用硬度更高的摩擦片或添加更多的填料来提高制动器的硬度,从而提高其摩擦性能和耐磨性能。
4. 优化制动系统的设计:制动器的性能不仅受到制动器本身的影响,还与整个制动系统的设计有着关系。
制动器制动摩擦性能机理及其影响因素分析

45制动器制动摩擦性能机理及其影响因素分析苏 辉 (中检西部检测有限公司)制动器俗称刹车,它是依靠制动摩擦副之间的相互摩擦作用实现速度调节,从而达到减速停车等目的的一种装置,一般也称为摩擦制动器或机械制动器。
在汽车、摩托车等交通运输设施中,无一例外都要为其配备制动器来实现速度调节、制动停车的功能。
制动过程中,制动装置是将机械系统的运动动能通过摩擦作用转化为热能和其它形式的能量消耗掉,因此制动过程的本质是一个能量转换的过程,它通过制动器摩擦副之间的机械摩擦作用,将车辆行驶或设备运转时产生的动能转换成热能消耗掉,从而使其减速或停止。
制动器根据摩擦副结构形式的不同,主要可分为鼓式制动器和盘式制动器两大类,本文主要介绍盘式制动器的制动摩擦性能机理及其影响因素。
1 盘式制动器的简介及分类盘式制动器又称为碟式制动器,它有液压驱动和气压驱动两种形式,通常为液压驱动。
其主要零部件有:制动盘、制动分泵、制动钳、制动油管等。
制动盘用合金钢制造并固定在车轮上,随车轮转动,按照其摩擦副中固定元件结构的不同,又可分为全盘式制动器和钳盘式制动器两大类。
在全盘式制动器中摩擦副的旋转元件及固定原件均为圈型盘,制动时各盘摩擦表面全部接触,其作用原理与摩擦式离合器相同。
由于此类制动器的制动盘散热不好,所以其实际应用没有钳盘式制动器广泛。
钳盘式制动器的固定摩擦原件是制动块,它安装在与车轴相连接但不能绕车轴轴线旋转的制动钳中,在此类盘式制动器中,制动块与制动盘的接触面积很小。
Su Hui (CCIC WEST Testing Co., Ltd.)Analysis Onbrake Friction Performance Mechanismand its Influencing Factors按照制动钳结构形式的不同,钳盘式制动器又可分为:定钳式盘式制动器和浮钳式盘式制动器两大类,其结构示意图如图1所示。
定钳式盘式制动器:制动钳固定不动,制动盘与车轮(a )定钳式盘式制动器(b )浮钳式盘式制动器进油口制动盘制动盘摩擦块摩擦块活塞轮毂制动卡钳制动卡钳活塞进油口导向销轮毂图1 钳盘式制动器结构示意图46 相连并能在制动钳的开口槽中旋转。
制动器常用几种摩擦材料介绍

制动器常用几种摩擦材料介绍制动器是一种常见的汽车零部件,用于控制车辆的速度和停车。
制动器的核心部件是摩擦材料,它能产生摩擦力,使车轮减速并最终停止运动。
下面将介绍几种常用的制动器摩擦材料。
1.有机摩擦材料:有机摩擦材料由有机树脂、填充剂和增强剂等组成。
有机树脂起到与摩擦面接触并转化为热能的作用,填充剂用于增加材料的强度和刚度,增强剂用于提高材料的耐热性和耐磨性。
有机摩擦材料具有良好的摩擦性能、热稳定性和耐磨性,同时具备制造成本低、噪音小和环保等优点。
因此,有机摩擦材料广泛应用于制动器和离合器等摩擦传动装置中。
2.无机摩擦材料:无机摩擦材料是指由无机材料制成的摩擦材料,如金属材料和无机复合材料等。
金属材料通常由铸铁、铝合金、铜合金等制成,具有良好的导热性和抗高温性能,适用于高速和高温的制动工况。
无机复合材料由金属颗粒、陶瓷颗粒和有机树脂复合而成,具有高强度、高硬度和耐磨性等特点,适用于高负荷和高温的制动条件。
3.纤维增强复合材料:纤维增强复合材料由纤维和基体材料构成,纤维通常采用碳纤维、玻璃纤维和有机纤维等,基体材料通常采用有机树脂、金属、陶瓷等。
纤维增强复合材料具有高强度、高刚度和低密度的特点,能在高温和高速条件下保持较好的摩擦性能。
在制动器中应用纤维增强复合材料可以减轻重量、减少摩擦噪音,并且提高制动效果和制动寿命。
4.碳化硅摩擦材料:碳化硅摩擦材料是一种新型的摩擦材料,由碳化硅粉末和有机粘结剂混合而成。
碳化硅材料具有高硬度、高热导率和高耐热性,能够在高速和高温条件下保持较好的摩擦性能。
碳化硅摩擦材料广泛应用于高速列车、机车和飞机等制动系统中,具有良好的制动稳定性和寿命。
除了以上几种常用的制动器摩擦材料,还有一些其他材料也被应用于特定的制动器中,如陶瓷摩擦材料和聚合物摩擦材料等。
陶瓷摩擦材料具有高硬度和高耐磨性,适用于高速和高温的制动条件。
聚合物摩擦材料具有低噪音和低摩擦系数的特点,适用于要求低噪音和平稳制动的车辆。
汽车制动器常用几种摩擦材料性能简介

尘、 通风、 光线等都有一定要求。 试验前试样的调节过程、成雾冷凝结束后玻璃 板或铝箔的平衡, 都要求环境温度在 !& 45! 4 , 否 则将会对试验结果造成直接影响。试验过程的其它 环节一般要求环境温度在 &" 4以下。 冷凝结束后的玻璃板要求在相对空气湿度为
#"!5,!的环境中平衡。
空气中的小颗粒如灰尘,对试验结果的影响是 显而易见的, 在玻璃板或铝箔的表面上, 一旦有灰尘 附着, 将直接导致错误的试验结果。 所以雾化试验室 应配备相应的除尘设备,试验人员应经常用湿布擦 拭桌面、 设备、 附件。 为了避免灰尘进入试验室, 试验 人员进入试验室应穿隔离服装、 换专用拖鞋, 并要求 无关人员不要随便进入试验室内。 在用一些有机溶剂清洗试验器件、 玻璃器皿时, 会产生刺激性的气味。 此外, 用于对照试验的试剂邻 苯二甲酸二异葵酯 ( /0/6) 和 邻 苯 二 甲 酸 二 辛 酯 ( 都有轻微毒性, 所以要求试验室应有良好的 /76) 通风条件。但是当冷凝结束后的玻璃板放在空气中
汽车工艺与材料
・ 经验交流 ・
!"#$%$&’() #)*+,$($-. / %!#)0’!(
%##"&’’%$( (##)) %(&##"’&#( 文章编号:
汽车制动器常用几种摩擦材料性能简介
陈汉汛, 朱
*!+",)%,#! 中图分类号 : 文献标识码 :
攀
( 武汉理工大学 汽车工程学院, 湖北 武汉 !"##$#)
0 %2 0
汽车工艺与材料
・ 经验交流 ・
!"#$%$&’() #)*+,$($-. / %!#)0’!(
制动摩擦片常见问题分析

制动摩擦片常见问题分析制动摩擦片摩擦系数高低对制动的影响?制动摩擦片的摩擦系数过高或过低都会影响汽车的制动性能。
尤其是汽车在高速行驶中需紧急制动时,摩擦系数过低就会出现制动不灵敏,而摩擦系数过高就会出现轮胎抱死现象,进而造成车辆甩尾和打滑,对行车安全构成严重威胁。
按照国家标准,制动摩擦片的适宜工作温度为100~350 ℃。
但许多劣质制动摩擦片在温度达到250 ℃时,其摩擦系数就会急剧下降,而此时制动就会完全失灵。
一般来说,按照SAE标准,制动摩擦片生产厂商都会选用FF级额定系数,即摩擦额定系数为0.35~0.45。
制动摩擦片的寿命与硬度的关系是怎样的?制动摩擦片的寿命与表面硬度并没有一定的关系。
但如果表面硬度高时,制动摩擦片与制动盘的实际接触面积小,往往会影响使用寿命。
而影响制动摩擦片寿命的主要因素包括硬度、强度、摩擦材料的磨损性等。
一般情况下,前制动摩擦片的寿命为3万km,后制动摩擦片的使用寿命为12万km。
制动时为什么会产生抖动现象?往往是由于制动摩擦片或制动盘的变形造成的,这与制动摩擦片和制动盘的材质、加工精度及使用受热变形有关,其主要原因有制动盘厚薄不匀、制动鼓的圆度差、制动摩擦片的不均匀磨损,以及热变形和热斑等。
除此之外,制动卡钳的变形或安装不当,以及制动摩擦片的摩擦系数不稳定也会引起制动时抖动。
另外,如果制动摩擦片在制动时产生的振动频率与悬挂系统产生共振时,也会产生抖动现象。
涉水后对制动性能的影响?由于涉水后制动摩擦片/蹄与制动盘/鼓之间有一层水膜,减小了摩擦力,会影响制动效果,而且制动鼓内的水也不容易散出。
对于盘式制动器来说,这种涉水对于制动效果带来的影响会低一些,因为盘式制动器的制动摩擦片接触面积小,而且是暴露在外,不会存留水滴。
在车轮转动时由于离心力的作用,制动盘片上的水滴会很快散失,只要涉水后猛踩几脚制动就会去除残留的水层。
但对于鼓式制动器来说,在涉水后必须要边走边踩制动,即边踩油门边踩制动,连续几次后可将制动蹄与制动鼓之间的水份蒸发掉,进而恢复制动效果。
汽车对制动摩擦片的性能要求

制 动摩擦片 的摩 擦系数过 高或过 低都会影 响汽 车的制动 性 表面的湿摩擦材料沾水时 , 摩擦系数会 降低 , 水膜 消除时 , 回 到干燥状态后 , 摩擦系数会恢 复正常 , 叫做涉水恢复 。 能。特别是在 汽车紧急制动时 , 低摩擦 系数 会出现刹车不 敏感 现 象, 而摩擦 系数太高会 出现轮胎抱死现象 , 造成车辆 甩尾和打滑 , 3 良好的耐磨性 适用 于 1 0 0 — 3 5 o  ̄ c N动 耐磨性是摩擦材料寿命 的体 系 , 而且 是衡量摩擦材料一个 重 这对 安全造成严重 的威胁。根据国家标准 , 要 的技术经济指标。 耐久性越好 , 表明其使用寿命长 。 但该摩擦材 器的工作温度 。 但许多劣质 的制动摩擦 片在 温度达到 2 5 0  ̄ C, 摩擦 料 的磨损在工作 的过程 中 , 主要 由剪 应力造成的接触面上 的摩 擦 系数 急剧下降 , 而制动将彻底失败 。一般来说 , 按照 S A E标 准 , 制 动摩擦片制造商可 以选择 F F额定系数 , 摩擦系数为 0 . 3 5 ~ 0 . 4 5 。 所产生 的。
说, 制动噪声是一个重要 的性能要求 。有关部 门提 出的标准 , 一般 2 适 当 的抗 热 衰 退 - 眭及 核 复性 的汽车制动噪声不应超过 8 5 d B 。 温度是 影响摩擦 系数的最重要 因素 。在摩擦 过程 中, 摩擦材 制动噪声是相互干扰 的共振相关零件及悬挂系统造成。 但也有 料由于温 度上升 , 一般 当温度达到 2 0 0 %, 摩擦系数减 小 , 当温度 因使用不 当或变形制动盘材料 , 制动摩擦 片的硬度 、 孔隙率和可压 达到树脂 和橡胶 的温度范 围后 , 突然降低 的摩擦 系数 , 这种 现象 缩性不合格 , 生锈 的制动摩擦片和制动盘的受潮 , 金属丝太硬 , 制动 称为热衰退 , 严重的热衰退将导致制动效能的变化和恶化 。 摩擦 片磨损程度报警, 机械制动盘 的原因引起噪音或尖叫。 随着高温摩擦改进剂填料在摩擦 材料 中的减少 , 是克服热衰 6 新装的制动摩擦片有制动偏软的现象
汽车制动系统摩擦片材料基本知识

汽车制动系统摩擦片材料根本知识摩擦材料一、概论摩擦材料是一种应用在动力机械上,依靠摩擦作用来执行制动和传动功能的部件材料。
它主要包括制动器衬片〔刹车片〕和离合器面片〔离合器片〕。
刹车片用于制动,离合器片用于传动。
任何机械设备及运动的各种车辆都必须要有制动或传动装置。
摩擦材料是这种制动或传动装置上的关键性部件。
它最主要的功能是通过摩擦来吸收或传递动力。
如离合器片传递动力,制动片吸收动能。
它们使机械设备及各种机动车辆能够平安可靠地工作。
所以说摩擦材料是一种应用广泛又甚关键地材料。
摩擦材料是一种高分子三元复合材料,是物理及化学复合体。
它是由高分子粘结剂〔树脂及橡胶〕、增强纤维和摩擦性能调节剂三大类组成及其它配合剂构成,经一系列生产加工而制成的制品。
摩擦材料的特点是具有良好的摩擦系数和耐磨损性能,同时具有一定的耐热性和机械强度,能满足车辆或机械的传动及制动的性能要求。
它们被广泛应用在汽车、火车、飞机、石油钻机等各类工程机械设备上。
民用品如自行车、洗衣机等作为动力的传递或制动减速用不可缺少的材料。
二、摩擦材料开展简史自世界上出现动力机械和机动车辆后,在其传动和制动机构中就使用摩擦片。
初期的摩擦片系用棉花、棉布、皮革等作为基材,如:将棉花纤维或其织品浸渍橡胶浆液后,进展加工成型制成刹车片或刹车带。
其缺点:耐热性较差,当摩擦面温度超过120℃后,棉花和棉布会逐渐焦化甚至燃烧。
随着车辆速度和载重的增加,其制动温度也相应提高,这类摩擦材料已经不能满足使用要求。
人们开场寻求耐热性好的、新的摩擦材料类型,石棉摩擦材料由此诞生。
石棉是一种天然的矿物纤维,它具有较高的耐热性和机械强度,还具有较长的纤维长度、很好的散热性,柔软性和浸渍性也很好,可以进展纺织加工制成石棉布或石棉带并浸渍粘结剂。
石棉短纤维和其布、带织品都可以作为摩擦材料的基材。
更由于其具有较低的价格〔性价比〕,所以很快就取代了棉花及棉布而成为摩擦材料中的主要基材料。
汽车制动摩擦材料的性能要求及影响因素分析
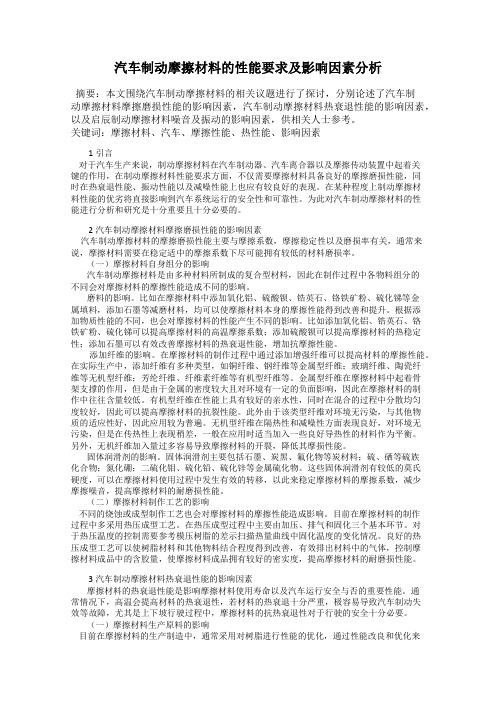
汽车制动摩擦材料的性能要求及影响因素分析摘要:本文围绕汽车制动摩擦材料的相关议题进行了探讨,分别论述了汽车制动摩擦材料摩擦磨损性能的影响因素,汽车制动摩擦材料热衰退性能的影响因素,以及启辰制动摩擦材料噪音及振动的影响因素,供相关人士参考。
关键词:摩擦材料、汽车、摩擦性能、热性能、影响因素1引言对于汽车生产来说,制动摩擦材料在汽车制动器、汽车离合器以及摩擦传动装置中起着关键的作用,在制动摩擦材料性能要求方面,不仅需要摩擦材料具备良好的摩擦磨损性能,同时在热衰退性能、振动性能以及减噪性能上也应有较良好的表现。
在某种程度上制动摩擦材料性能的优劣将直接影响到汽车系统运行的安全性和可靠性。
为此对汽车制动摩擦材料的性能进行分析和研究是十分重要且十分必要的。
2汽车制动摩擦材料摩擦磨损性能的影响因素汽车制动摩擦材料的摩擦磨损性能主要与摩擦系数,摩擦稳定性以及磨损率有关,通常来说,摩擦材料需要在稳定适中的摩擦系数下尽可能拥有较低的材料磨损率。
(一)摩擦材料自身组分的影响汽车制动摩擦材料是由多种材料所制成的复合型材料,因此在制作过程中各物料组分的不同会对摩擦材料的摩擦性能造成不同的影响。
磨料的影响。
比如在摩擦材料中添加氧化铝、硫酸钡、锆英石、铬铁矿粉、硫化锑等金属填料,添加石墨等减磨材料,均可以使摩擦材料本身的摩擦性能得到改善和提升。
根据添加物质性能的不同,也会对摩擦材料的性能产生不同的影响。
比如添加氧化铝、锆英石、铬铁矿粉、硫化锑可以提高摩擦材料的高温摩擦系数;添加硫酸钡可以提高摩擦材料的热稳定性;添加石墨可以有效改善摩擦材料的热衰退性能,增加抗摩擦性能。
添加纤维的影响。
在摩擦材料的制作过程中通过添加增强纤维可以提高材料的摩擦性能。
在实际生产中,添加纤维有多种类型,如铜纤维、钢纤维等金属型纤维;玻璃纤维、陶瓷纤维等无机型纤维;芳纶纤维、纤维素纤维等有机型纤维等。
金属型纤维在摩擦材料中起着骨架支撑的作用,但是由于金属的密度较大且对环境有一定的负面影响,因此在摩擦材料的制作中往往含量较低。
钳式制动器摩擦材料的粘结力

钳式制动器摩擦材料的粘结力钳式制动器是一种常见的制动装置,广泛应用于汽车、电梯、起重机等机械设备中。
而摩擦材料的粘结力是决定钳式制动器性能的重要因素之一。
摩擦材料的粘结力直接影响了制动器的制动效果和使用寿命。
本文将从摩擦材料的组成、制备工艺和粘结力的影响因素等方面进行探讨。
钳式制动器的摩擦材料通常由摩擦片和摩擦盘组成。
摩擦片一般由金属基体和摩擦剂两部分组成。
金属基体主要起到机械支撑和导热传导的作用,而摩擦剂则负责提供摩擦力和热耐磨性。
常见的摩擦剂有有机物质(如石棉、树脂等)和无机物质(如石墨、金属氧化物等)。
摩擦盘则是钳式制动器中起到摩擦的部分,通常由钢材制成。
摩擦材料的粘结力是指摩擦片与金属基体之间的粘结强度。
粘结力的好坏直接影响了摩擦片的使用寿命和制动效果。
一般来说,粘结力越强,摩擦片与金属基体的粘结越牢固,制动器的性能越好。
摩擦材料的粘结力受多种因素的影响。
首先是摩擦材料的组成和制备工艺。
不同的摩擦剂和金属基体在制备过程中的配比和工艺条件会影响到粘结力的大小。
合适的配比和优良的工艺条件能够提高摩擦材料的粘结力。
其次是工作条件的影响。
钳式制动器在使用过程中会受到摩擦片与摩擦盘之间的压力、温度和速度等因素的影响。
这些因素会对摩擦材料的粘结力产生一定的影响。
例如,高温和高速度下,摩擦材料容易发生热膨胀和热变形,从而影响粘结力。
摩擦材料的表面状态也会对粘结力产生影响。
表面的粗糙度和清洁度会影响到摩擦材料与金属基体之间的接触面积和接触强度,从而影响粘结力。
为了提高钳式制动器摩擦材料的粘结力,可以从以下几个方面进行考虑。
首先,选择合适的摩擦剂和金属基体,确保它们的相容性和亲和力。
其次,优化制备工艺,控制好温度、压力和时间等参数,确保摩擦材料的组成和结构符合要求。
同时,注意保持摩擦材料和金属基体的表面清洁和光滑,以提高粘结力。
钳式制动器摩擦材料的粘结力是影响制动器性能的重要因素之一。
通过合理的组成和制备工艺,以及注意工作条件和表面状态的影响,可以提高摩擦材料的粘结力,从而提高钳式制动器的制动效果和使用寿命。
制动盘 材料成分 石墨 摩擦系数

制动盘的材料成分一直是制动性能的重要因素之一,而石墨是制动盘中常见的材料之一,具有较高的摩擦系数。
下面将从制动盘的材料成分和石墨的摩擦系数两个方面进行探讨。
一、制动盘的材料成分1.金属材料制动盘的主要材料一般包括铸铁、铝合金和钢铁等金属材料。
这些金属材料具有一定的强度和耐磨性,能够满足制动盘在高速运转时的使用要求。
2.陶瓷材料除了金属材料,制动盘还常采用陶瓷材料,如碳化硅陶瓷和氧化铝陶瓷等。
这些材料具有高硬度、高温稳定性和耐磨性等优良性能,能够有效提升制动盘的耐用性和制动性能。
3.石墨在制动盘的材料成分中,石墨也是常见的一种材料。
石墨具有良好的自润滑性和热稳定性,能够有效减少制动盘与制动衬片之间的摩擦损耗,改善制动性能。
二、石墨的摩擦系数1.自润滑性石墨具有良好的自润滑性,能够减少摩擦时的磨损和能量损失,提高制动盘的稳定性和制动效果。
2.热稳定性石墨具有良好的热稳定性,能够在高温条件下保持稳定的摩擦性能,不易发生摩擦衰减和失效。
3.摩擦系数石墨的摩擦系数一般在0.1-0.3之间,具有较高的摩擦性能,能够满足制动盘在不同工况下的制动需求。
总结:制动盘的材料成分和石墨的摩擦系数是制动性能的重要影响因素,合理选用材料和提高石墨的摩擦性能能够有效提升制动盘的性能和使用寿命。
随着科技的不断进步,制动盘的材料研发和石墨的摩擦性能也将不断得到提升,为汽车和机械设备的安全运行提供更加可靠的保障。
在制动盘的材料成分中,石墨作为一种常见的材料,具有很多优异的性能,特别是在提高制动盘的摩擦性能方面发挥着重要的作用。
石墨具有多层片状结构,这种特殊的结构使其具有良好的自润滑性和热稳定性,能够在高温和高速摩擦环境下保持稳定的摩擦系数。
石墨还具有较低的摩擦系数和耐磨性,能够减少制动盘和制动衬片之间的摩擦损耗,延长制动盘的使用寿命。
在制动盘的制动过程中,石墨作为摩擦材料,能够有效地抵抗高温、高速下的摩擦磨损,保持稳定的摩擦系数,确保制动盘有良好的制动效果。
机动车制动摩擦片磨损特征与制动性能关联性研究

机动车制动摩擦片磨损特征与制动性能关联性研究随着汽车保有量的不断增加,机动车的制动系统也成为了汽车安全的重要组成部分。
而摩擦片作为制动系统中的核心部件,其磨损特征对于整个制动性能起着至关重要的作用。
因此,研究机动车制动摩擦片的磨损特征及其与制动性能之间的关联性,对于提升汽车的制动性能和安全性具有重要意义。
1. 引言机动车的制动系统是保障驾驶安全的重要组成部分,其性能直接关系到车辆的制动效果。
而摩擦片作为制动系统中的核心部件,其性能和特征对制动性能起着至关重要的作用。
2. 机动车制动摩擦片的磨损特征机动车制动摩擦片的磨损特征主要包括以下几个方面:2.1 厚度磨损摩擦片在制动过程中会不可避免地发生磨损,表现为其厚度的逐渐减小。
磨损量的增加会导致摩擦片的厚度降低,从而影响制动性能。
2.2 粉尘生成摩擦片在与制动盘接触时,会发生摩擦磨损,产生大量的摩擦粉尘。
这些粉尘会影响制动器的摩擦效果,从而降低制动性能。
2.3 表面温度升高摩擦片在制动过程中会不断受到摩擦的作用,导致其表面温度升高。
过高的温度会使摩擦片材料发生退火、氧化等现象,进而降低制动性能。
3. 机动车制动摩擦片磨损特征与制动性能的关联性制动摩擦片的磨损特征与制动性能之间存在着密切的关联性。
磨损特征的变化会直接影响摩擦片与制动盘之间的摩擦系数,从而影响制动效果。
3.1 磨损特征对摩擦系数的影响随着摩擦片的磨损,材料表面会发生纹理的变化,导致摩擦系数的变化。
一般来说,摩擦片磨损后的表面粗糙度会增加,摩擦系数也会随之降低。
3.2 磨损特征对制动距离的影响制动距离是衡量制动性能的一个重要指标。
摩擦片的磨损特征会对制动距离产生影响。
当摩擦片磨损到一定程度时,制动距离会逐渐增加,从而减少车辆的制动效果。
4. 提高机动车制动摩擦片的磨损特征和制动性能为了提高机动车制动摩擦片的磨损特征和制动性能,可以采取以下措施:4.1 优化摩擦材料的选择选择合适的摩擦材料对提高摩擦片的磨损特征和制动性能至关重要。
- 1、下载文档前请自行甄别文档内容的完整性,平台不提供额外的编辑、内容补充、找答案等附加服务。
- 2、"仅部分预览"的文档,不可在线预览部分如存在完整性等问题,可反馈申请退款(可完整预览的文档不适用该条件!)。
- 3、如文档侵犯您的权益,请联系客服反馈,我们会尽快为您处理(人工客服工作时间:9:00-18:30)。
汽车制动摩擦材料的性能要求及影响因素分析
发表时间:2018-09-12T14:20:56.057Z 来源:《科技新时代》2018年7期作者:张国华
[导读] 本文围绕汽车制动摩擦材料的相关议题进行了探讨,分别论述了汽车制动摩擦材料摩擦磨损性能的影响因素。
杭州优纳摩擦材料有限公司浙江省杭州市 311404
摘要:本文围绕汽车制动摩擦材料的相关议题进行了探讨,分别论述了汽车制动摩擦材料摩擦磨损性能的影响因素,汽车制动摩擦材料热衰退性能的影响因素,以及启辰制动摩擦材料噪音及振动的影响因素,供相关人士参考。
关键词:摩擦材料、汽车、摩擦性能、热性能、影响因素
1引言
对于汽车生产来说,制动摩擦材料在汽车制动器、汽车离合器以及摩擦传动装置中起着关键的作用,在制动摩擦材料性能要求方面,不仅需要摩擦材料具备良好的摩擦磨损性能,同时在热衰退性能、振动性能以及减噪性能上也应有较良好的表现。
在某种程度上制动摩擦材料性能的优劣将直接影响到汽车系统运行的安全性和可靠性。
为此对汽车制动摩擦材料的性能进行分析和研究是十分重要且十分必要的。
2汽车制动摩擦材料摩擦磨损性能的影响因素
汽车制动摩擦材料的摩擦磨损性能主要与摩擦系数,摩擦稳定性以及磨损率有关,通常来说,摩擦材料需要在稳定适中的摩擦系数下尽可能拥有较低的材料磨损率。
(一)摩擦材料自身组分的影响
汽车制动摩擦材料是由多种材料所制成的复合型材料,因此在制作过程中各物料组分的不同会对摩擦材料的摩擦性能造成不同的影响。
磨料的影响。
比如在摩擦材料中添加氧化铝、硫酸钡、锆英石、铬铁矿粉、硫化锑等金属填料,添加石墨等减磨材料,均可以使摩擦材料本身的摩擦性能得到改善和提升。
根据添加物质性能的不同,也会对摩擦材料的性能产生不同的影响。
比如添加氧化铝、锆英石、铬铁矿粉、硫化锑可以提高摩擦材料的高温摩擦系数;添加硫酸钡可以提高摩擦材料的热稳定性;添加石墨可以有效改善摩擦材料的热衰退性能,增加抗摩擦性能。
添加纤维的影响。
在摩擦材料的制作过程中通过添加增强纤维可以提高材料的摩擦性能。
在实际生产中,添加纤维有多种类型,如铜纤维、钢纤维等金属型纤维;玻璃纤维、陶瓷纤维等无机型纤维;芳纶纤维、纤维素纤维等有机型纤维等。
金属型纤维在摩擦材料中起着骨架支撑的作用,但是由于金属的密度较大且对环境有一定的负面影响,因此在摩擦材料的制作中往往含量较低。
有机型纤维在性能上具有较好的亲水性,同时在混合的过程中分散均匀度较好,因此可以提高摩擦材料的抗裂性能。
此外由于该类型纤维对环境无污染,与其他物质的适应性好,因此应用较为普遍。
无机型纤维在隔热性和减噪性方面表现良好,对环境无污染,但是在传热性上表现稍差,一般在应用时适当加入一些良好导热性的材料作为平衡。
另外,无机纤维加入量过多容易导致摩擦材料的开裂,降低其摩损性能。
固体润滑剂的影响。
固体润滑剂主要包括石墨、炭黑、氟化物等炭材料;硫、硒等硫族化合物;氮化硼;二硫化钼、硫化铅、硫化锌等金属硫化物。
这些固体润滑剂有较低的莫氏硬度,可以在摩擦材料使用过程中发生有效的转移,以此来稳定摩擦材料的摩擦系数,减少摩擦噪音,提高摩擦材料的耐磨损性能。
(二)摩擦材料制作工艺的影响
不同的烧蚀或成型制作工艺也会对摩擦材料的摩擦性能造成影响。
目前在摩擦材料的制作过程中多采用热压成型工艺。
在热压成型过程中主要由加压、排气和固化三个基本环节。
对于热压温度的控制需要参考模压树脂的差示扫描热量曲线中固化温度的变化情况。
良好的热压成型工艺可以使树脂材料和其他物料结合程度得到改善,有效排出材料中的气体,控制摩擦材料成品中的含胶量,使摩擦材料成品拥有较好的密实度,提高摩擦材料的耐磨损性能。
3汽车制动摩擦材料热衰退性能的影响因素
摩擦材料的热衰退性能是影响摩擦材料使用寿命以及汽车运行安全与否的重要性能。
通常情况下,高温会提高材料的热衰退性,若材料的热衰退十分严重,极容易导致汽车制动失效等故障,尤其是上下坡行驶过程中,摩擦材料的抗热衰退性对于行驶的安全十分必要。
(一)摩擦材料生产原料的影响
目前在摩擦材料的生产制造中,通常采用对树脂进行性能的优化,通过性能改良和优化来提高树脂的热分解温度,使摩擦材料能够在较高的温度条件下摩擦系数更加稳定,提高摩擦材料的抗热衰退性能。
比如利用纳米金属材料对树脂进行导热性能的改良,纳米金属材料本身导热性能优异,与树脂原料结合后可以将摩擦表面产生的热量迅速地传递到材料内部,减少摩擦材料自身的温度差,减少树脂的热分解反应,提高摩擦材料的稳定性。
另外,基于硫化锑在高温条件下容易生产硬度更高的氧化物,因此在原料中加入硫化锑不仅能够提高材料的耐磨损性,同时也起到了抗热衰退性的作用。
(二)摩擦材料制作工艺的影响
烧蚀技术涉及到摩擦材料的炭化,因此可以通过对烧蚀工艺优化来改善摩擦材料的抗热衰退性。
为避免摩擦材料在高温过程中剧烈炭化,可以在烧蚀工艺前线对摩擦材料进行高温预处理,使材料在经过高温烧蚀过程中能够降低炭化的速率,提高摩擦材料的抗热衰退性。
4汽车制动摩擦材料噪音及振动的影响因素
随着汽车行业的不断发展,汽车制造技术也越来越贴合消费者的需求,从过去的功能性,美观性逐渐走向功能性、美观性、舒适性、环保性。
对于汽车制动摩擦材料而言,越来越注重材料的降噪性能和抗振动性能。
在降噪性能方面,可从摩擦材料的生产配方入手,通过降低原料中金属的含量来提高降噪性能。
另外,由于摩擦材料中的孔隙率对降噪性能有着十分重要的影响,因此,可采用较高的显气孔率来
实现良好的阻尼功能,减少制动过程中的噪音。
摩擦材料的压缩性也是一个影响因素,压缩率不仅与汽车的舒适性有密切关系,同时也与制动系统的振动性以及降噪性有关。
当增加摩擦材料的压缩率时,可以减少低频振动现象,提高汽车的舒适度,减小噪音。
5结语
随着汽车制造业的不断发展,对于汽车制动摩擦材料的性能也有了更高的要求,不仅要满足基本的功能,同时在摩擦磨损性能、热衰退性能、降噪性能、防振动性能等方面也应具有更加优良的表现,以此来更好地满足消费者的使用需求和汽车行业的发展需求。
参考文献
[1]盘式制动器摩擦材料摩擦性能试验研究,李兵,王庆波,杨圣岽,等,《工程与试验》,2012,52(10)
[2]NAO与低金属摩擦材料制动性能的对比研究,黎军,李义顺,《工艺材料》,2013(8)
[3]MM-1000膜材磨损实验机在汽车制动材料研发中的应用,王秀飞,韩娟,尹彩流,等,《广西民族大学学报》,2013,19(4)
[4]碳纤维长度与取向对纸基膜材材料热负荷及摩擦学性能影响,宋晓东,杨方,齐乐华,《摩擦学学报》,2014,34(1)。