产品中试管理-从样品到量产
产品中试管理

精品培训课程课程名称RDM012产品中试管理--从样品到量产Product Piloting-from sample to mass production参加对象企业CEO/总经理、研发总经理/副总、测试部经理、中试/试产部经理、制造部经理、工艺/工程部经理、质量部经理、项目经理/产品经理、高级制造工程师等课程背景我们在为企业提供研发管理咨询服务的过程中发现,很多企业的新产品开发从样机到量产的过程中(产品化过程)存在着共同的问题:1. 新品没有经过中试或中试的时间很短,制造部门戏称研发的新品是“三无”产品,没有生产文件、没有工装、生产现场出了问题没人管;2. 转产没有标准,研发想快点转产,生产对有问题的产品又不愿接收,希望研发把问题都解决了才转过来,而市场又催得急,经常被迫接收,长此以往,导致研发与生产的矛盾激化;3. 有些企业开始成立中试部门,希望在中试阶段把产品质量问题解决掉,但中试的定位与运作也很困惑,发生质量与进度的冲突时,如何取舍与平衡,以前研发与制造的矛盾转化为研发与中试、中试与生产的矛盾,中试成了矛盾集散中心;4. 市场的压力并不因中试的产生而减少,中试需要从哪些方面努力才能满足产品的质量、进度的要求?中试的业务是面向研发还是面向制造,还是兼而有之?5. 量产后才发现产品可制造性差、成品率低、经常返工,影响发货;6. 产品到了生产后还发生大量的设计变更;7. 产品到了客户手中还冒出各种各样的问题以致要研发人员到处去“救火”。
本课程将基于多年的实践、长期的研发咨询积累,总结出一套理论与实践相结合的可操作的方法,配以大量实际案例,以指导研发/试产/制造部门主管如何高效的实现产品从样品走向量产。
培训收益1. 了解业界公司在不同发展阶段的产品中试管理模式与实践2. 掌握面向制造系统的产品设计(DFM)的方法与实施过程3. 掌握面向生产测试的产品设计(DFT)的方法与实施过程4. 掌握面向制造系统的新产品验证的过程与方法5. 掌握在满足质量标准的前提下缩短产品试制周期的方法和技巧6. 了解如何建立从样品到量产的管理机制培训课时2天(12小时)课程大纲一、案例研讨二、从样品到量产概述1. 企业在追求什么:技术?样品?产品?商品?2. 研发与制造的矛盾:1). 制造系统如何面对研发的三无产品?2). 研发如何面对制造系统越来越高的门槛?3. 研发与制造矛盾的激化:中试的产生成为必然4. 中试的定位与发展:1). 研发(RD)、中试(D&P)、生产(P)的关系2). 中试的使命是什么?3). 中试如何定位?4). 中试的发展问题:●大而全?●专业化分工?●产品线划分与共享平台●中试人员的发展定位:广度与深度问题5. 中试的业务范围1). 中试业务:新产品导入(NPI)2). 承上:如何面向产品的研发?3). 启下:如何面向产品的制造?4). 桥梁:中试作为连接研发与制造的桥梁,独木桥还是阳关道?6. 演练与问题讨论1). 根据企业的实际情况,是否需要建立并发展中试的职能?三、新产品导入团队1. 新产品导入团队的构成1). 工艺工程2). 设备工程3). 测试工程4). 工业工程5). 产品验证6). 试生产(计划、生产、质量)2. 新产品导入团队的职责3. 新产品导入团队与产品开发团队的关系1). 开发模式的演变:串行变并行2). 并行工程在产品开发中如何体现?3). 新产品导入团队如何提前介入研发?●为什么要提前介入?●提前到什么时候介入?●提前介入做什么?4). 新产品导入团队的管理●新产品导入团队与产品开发团队、职能部门的沟通●新产品导入团队成员的汇报、考核和管理机制4. 演练与问题讨论1). 根据企业的实际情况,研讨建立新产品导入团队的时机四、面向制造系统的产品设计(DFM)1. 如何在产品设计与开发过程中进行可制造性设计1). 从制造的角度来看产品设计2). 工艺人员介入产品开发过程的切入点:从立项就开始3). 工艺管理的三个阶段:工艺设计、工艺调制与验证、工艺管制4). 工艺设计:●如何提出可制造性需求?●需要哪些典型的工艺规范?●可制造性需求如何落实到产品设计方案中?●工艺设计与产品设计如何并行?●产品工艺流程设计●电装、整装、包装与物流的可制造性设计分析●如何确保可制造性需求在产品开发中已被实现?●工艺评审如何操作?●什么时候考虑工装?●如何在开发过程中同步输出工艺文件与生产操作指导文件5). 工艺调制与验证●工艺验证的时机●工艺验证方案包括哪些内容?●如何实施工艺验证?●工艺验证报告的内容●如何推动工艺验证的问题解决?●研发人员如何配合新产品的工艺验证?●制造外包模式下的工艺如何验证?6). 工艺管制●工艺管制的困惑:救火何时是尽头?●工艺转产评审(标准、流程、责任)●量产过程中的例行监控与异常管理2. 演练与问题讨论1). 分析学员企业的工艺管理工作做到什么程度?存在哪些差距?3. 工艺管理平台建设1). 谁负责工艺平台的建设?2). 工艺委员会的产生:责任与运作模式3). 如何进行工艺规划?4). 基础工艺研究与应用5). 支撑工艺管理平台的四大规范:●品质规范●设备规范●工艺规范。
从样机走向量产-中试规划与管理
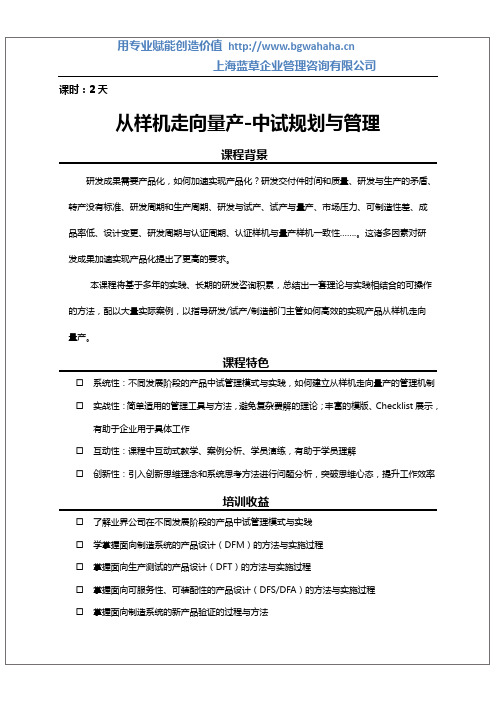
产品试制验证管理
11.面向制造系统的产品验证活动和策略
12.产品试制准备
13.影响产品试制周期的因素分析
14.研发人员对试制准备提供的支持
15.试制人员介入产品开发过程的时机
16.面向制造系统的验证方案及验证内容
17.制造系统验证的基本假设
18.工艺验证的内容
19.文档验证的内容
企业在不同的发展阶段如何开展测试的相关工作(短平快的项目测试工作如何开展)
10.面向生产测试业务的产品设计与开发
生产测试业务流程分析
典型的部品测试、整机测试方法介绍
开发专门的生产测试工装的条件分析
生产测试工装的开发管理
在产品开发过程中如何实施面向生产测试的产品设计
如何推动可测试性设计(DFT)业务的发展
本课程将基于多年的实践、长期的研发咨询积累,总结出一套理论与实践相结合的可操作
的方法,配以大量实际案例,以指导研发/试产/制造部门主管如何高效的实现产品从样机走向
量产。
课程特色
系统性:不同发展阶段的产品中试管理模式与实践,如何建立从样机走向量产的管理机制
实战性:简单适用的管理工具与方法,避免复杂费解的理论;丰富的模版、Checklist展示,有助于企业用于具体工作
工程设计的关键要素;
中试如何利用工程设计的关键要素进行前期导入;
中试与可制造性设计(DFM)
5.如何在产品设计与开发过程中进行可制造性设计(DFM)
从制造的角度来看产品设计
工艺人员介入产品开发过程的切入点:从立项就开始
工艺管理的三个阶段:工艺设计、工艺调制与验证、工艺管制
工艺设计
工艺调制与验证
工艺管制
课程大纲
样品到量产的管理机制

课程背景:我们在为企业提供研发管理咨询服务的过程中发现,很多企业的新产品开发从样机到量产的过程中(产品化过程)存在着共同的问题:1.新品没有经过中试或中试的时间很短,制造部门戏称研发的新品是“三无”产品,没有生产文件、没有工装、生产现场出了问题没人管;2.转产没有标准,研发想快点转产,生产对有问题的产品又不愿接收,希望研发把问题都解决了才转过来,而市场又催得急,经常被迫接收,长此以往,导致研发与生产的矛盾激化;3.有些企业开始成立中试部门,希望在中试阶段把产品质量问题解决掉,但中试的定位与运作也很困惑,发生质量与进度的冲突时,如何取舍与平衡,以前研发与制造的矛盾转化为研发与中试、中试与生产的矛盾,中试成了矛盾集散中心;4.市场的压力并不因中试的产生而减少,中试需要从哪些方面努力才能满足产品的质量、进度的要求?中试的业务是面向研发还是面向制造,还是兼而有之?5.量产后才发现产品可制造性差、成品率低、经常返工,影响发货;6.产品到了生产后还发生大量的设计变更;7.产品到了客户手中还冒出各种各样的问题以致要研发人员到处去“救火”。
本课程将基于多年的实践、长期的研发咨询积累,总结出一套理论与实践相结合的可操作的方法,配以大量实际案例,以指导研发/试产/制造部门主管如何高效的实现产品从样品走向量产。
课程收益:1.了解业界公司在不同发展阶段的产品中试管理模式与实践2.掌握面向制造系统的产品设计(DFM)的方法与实施过程3.掌握面向生产测试的产品设计(DFT)的方法与实施过程4.掌握面向制造系统的新产品验证的过程与方法5.掌握在满足质量标准的前提下缩短产品试制周期的方法和技巧6.了解如何建立从样品到量产的管理机制导师简介:[Charles] 研发咨询品牌资深顾问 INCOSE 国际系统工程师联合会会员 16年的高科技企业从业背景,具有丰富的产品研发、新产品导入、工艺工程、售前与售后等领域的实践与管理经验。
曾在多家高科技企业中担任产品开发工程师(电子)、工艺工程师、售后服务工程师、项目经理、产品经理、设计工程部经理、工艺工程部经理、新产品导入部经理、技术管理部经理、企业管理顾问等职务; 在某著名通信公司工作7年(97~03),期间长期与国际顶尖咨询顾问一起工作,全程参与推动该公司研发管理体系的变革工作,并成功主导了新产品导入平台的建设工作,作为产品经理主导了某产品线多个大型项目的产品研发工作。
产品中试管理—从样品到量产的方法

DFA(可装配性设计)
将装配准则集成到产品设计过程中;
将•产D品 FA设 :D计e和 sig工 n F艺 or 设 Ass计em集bl成 y 到同一个过程中
目的: 提高产品的可装配性 降低产品成本
DFA的层次
零件级 组件级 产品级
最重要的DFA原则
简化设计,减少零件数量和种类 标准化设计,采用通用件和材料 方便运输 方便安装(避免调整和错误安装) 尽可能使零件对称 适合目前的工艺
概念
•产品需求 •关键技术 •产品概念
计划
开发 验证 发布
生命 周期
•设计需求 •总体方案 •概要设计
•详细设计 •构建原型 (功能样机) •性能样机
•试生产 •制造验证 •BETA
•产品发布 •开始销售
•向量产切 换
•维护改进
•产品生命周 期管理
单元二、工艺管理
课程目录
1、概述
2 、工艺管理
3、测试管理
TR3
可制造性需求的分解与分配
• DFM需求分解与分配样例 • 形成产品规格
工艺总体设计
• 产品特点 • 工艺难点(设计、验证) • 工艺流程、工艺路线 • 返修策略(备件计划、停产器件、报废/呆滞、财务部负
责仓库)
• 品质保证(工装) • 制造效率(更多是测试效率/DFT) • 制造成本
半成品加工流程(电子产品)
(热处理要求)
(压接件选用防误插、导向装置的器件)
(尽量少用插装器件,)
6.3.2
(器件种类要尽量少) PCB可加工性要求
(PCB材料选用) (PCB尺寸、厚度要求) (尺寸厚度与板材的关系) (板厚与孔径比要求) (曲翘度要求)
制造需求列表示例(4)
样品到量产的管理机制

课程背景:我们在为企业提供研发管理咨询服务的过程中发现,很多企业的新产品开发从样机到量产的过程中(产品化过程)存在着共同的问题:1.新品没有经过中试或中试的时间很短,制造部门戏称研发的新品是“三无”产品,没有生产文件、没有工装、生产现场出了问题没人管;2.转产没有标准,研发想快点转产,生产对有问题的产品又不愿接收,希望研发把问题都解决了才转过来,而市场又催得急,经常被迫接收,长此以往,导致研发与生产的矛盾激化;3.有些企业开始成立中试部门,希望在中试阶段把产品质量问题解决掉,但中试的定位与运作也很困惑,发生质量与进度的冲突时,如何取舍与平衡,以前研发与制造的矛盾转化为研发与中试、中试与生产的矛盾,中试成了矛盾集散中心;4.市场的压力并不因中试的产生而减少,中试需要从哪些方面努力才能满足产品的质量、进度的要求?中试的业务是面向研发还是面向制造,还是兼而有之?5.量产后才发现产品可制造性差、成品率低、经常返工,影响发货;6.产品到了生产后还发生大量的设计变更;7.产品到了客户手中还冒出各种各样的问题以致要研发人员到处去“救火”。
本课程将基于多年的实践、长期的研发咨询积累,总结出一套理论与实践相结合的可操作的方法,配以大量实际案例,以指导研发/试产/制造部门主管如何高效的实现产品从样品走向量产。
课程收益:1.了解业界公司在不同发展阶段的产品中试管理模式与实践2.掌握面向制造系统的产品设计(DFM)的方法与实施过程3.掌握面向生产测试的产品设计(DFT)的方法与实施过程4.掌握面向制造系统的新产品验证的过程与方法5.掌握在满足质量标准的前提下缩短产品试制周期的方法和技巧6.了解如何建立从样品到量产的管理机制导师简介:[Charles] 研发咨询品牌资深顾问 INCOSE 国际系统工程师联合会会员 16年的高科技企业从业背景,具有丰富的产品研发、新产品导入、工艺工程、售前与售后等领域的实践与管理经验。
曾在多家高科技企业中担任产品开发工程师(电子)、工艺工程师、售后服务工程师、项目经理、产品经理、设计工程部经理、工艺工程部经理、新产品导入部经理、技术管理部经理、企业管理顾问等职务; 在某著名通信公司工作7年(97~03),期间长期与国际顶尖咨询顾问一起工作,全程参与推动该公司研发管理体系的变革工作,并成功主导了新产品导入平台的建设工作,作为产品经理主导了某产品线多个大型项目的产品研发工作。
从样品到量产中试培训1讲课文档

第一页,共一百二十一页。
问题讨论
▪ 请各小组讨论从样品到量产过程中存在的主要问 题(10分钟)
第二页,共一百二十一页。
制造的烦恼
制造部门为什么抵触新产品? • 烦(效率/质量/市场投诉/考核压力) 制造部门的对策: • 推(提高门槛/提条件) • 拖(新产品排在夜班生产) • 拉(要研发人员现场跟线)
低
中
高
项目管理难度
第十七页,共一百二十一页。
最佳的产品开发团队(PDT)
测试 结构
手册
硬件 知识产权
投入产出分析
系统工程
软件 标准 渠道支持
成本核算 定价 客户调研
开发
财务
项目 项目经经理理
市场
渠道服务
技术 支持
培训
制造
试制工程
竞争对手分析 渠道管理
采购
工艺工程 生产测试
行销策划
供应商优选 供应商管理
第三十六页,共一百二十一页。
半成品加工流程(电子产品)
原材料
PCB
印刷
点胶
贴片
回流
AOI
AXI
压接
器件预加工(成型)
补焊
波峰焊
插件
铆接
ICT
装配
FT
老化
FT
PCBA
第三十七页,共一百二十一页。
整机加工流程(电子产品)
PCBA 结构件
装配
检验
调测
老化
检验
入库
客户
发运
检验
包装
理货
第三十八页,共一百二十一页。
• 组织制造工艺和装备的验证
• 监控产品开发的制造准备度 • 监控关键时间点
从样品走向量产-DFM和DFT

从样品走向量产–DFM和DFT参加对象企业CEO/总经理、研发总经理/副总、测试部经理、中试/试产部经理、制造部经理、工艺/工程部经理、质量部经理、项目经理/产品经理、高级制造工程师等。
课程背景我们在为企业提供研发管理咨询服务的过程中发现,很多企业的新产品开发从样机到量产的过程中(产品化过程)存在着共同的问题:1. 新品没有经过中试或中试的时间很短,制造部门戏称研发的新品是“三无”产品,没有生产文件、没有工装、生产现场出了问题没人管;2. 转产没有标准,研发想快点转产,生产对有问题的产品又不愿接收,希望研发把问题都解决了才转过来,而市场又催得急,经常被迫接收,长此以往,导致研发与生产的矛盾激化;3. 有些企业开始成立中试部门,希望在中试阶段把产品质量问题解决掉,但中试的定位与运作也很困惑,发生质量与进度的冲突时,如何取舍与平衡,以前研发与制造的矛盾转化为研发与中试、中试与生产的矛盾,中试成了矛盾集散中心;4. 市场的压力并不因中试的产生而减少,中试需要从哪些方面努力才能满足产品的质量、进度的要求?中试的业务是面向研发还是面向制造,还是兼而有之?5. 量产后才发现产品可制造性差、成品率低、经常返工,影响发货;6. 产品到了生产后还发生大量的设计变更;7. 产品到了客户手中还冒出各种各样的问题以致要研发人员到处去“救火”……本课程将基于多年的实践、长期的研发咨询积累,总结出一套理论与实践相结合的可操作的方法,配以大量实际案例,以指导研发/试产/制造部门主管如何高效的实现产品从样品走向量产。
培训收益1、业界公司在不同发展阶段的产品中试管理模式与实践2、面向制造系统的产品设计(DFM)的方法与实施过程3、面向生产测试的产品设计(DFT)的方法与实施过程4、面向制造系统的新产品验证的过程与方法5、在满足质量标准的前提下缩短产品试制周期的方法和技巧6、如何建立从样品到量产的管理机制课程内容一、案例研讨二、从样品到量产概述1. 企业在追求什么:技术?样品?产品?商品?2. 研发与制造的矛盾:1)制造系统如何面对研发的三无产品?2)研发如何面对制造系统越来越高的门槛?3. 研发与制造矛盾的激化:中试的产生成为必然4. 中试的定位与发展:1)研发(RD)、中试(D&P)、生产(P)的关系2)中试的使命是什么?3)中试如何定位?4)中试的发展问题:* 大而全?* 专业化分工?* 产品线划分与共享平台* 中试人员的发展定位:广度与深度问题5. 中试的业务范围1)中试业务:新产品导入(NPI)2)承上:如何面向产品的研发?3)启下:如何面向产品的制造?4)桥梁:中试作为连接研发与制造的桥梁,独木桥还是阳关道?6. 演练与问题讨论根据企业的实际情况,是否需要建立并发展中试的职能?三、新产品导入团队1. 新产品导入团队的构成1)工艺工程2)设备工程3)测试工程4)工业工程5)产品验证6)试生产(计划、生产、质量)2. 新产品导入团队的职责3. 新产品导入团队与产品开发团队的关系1)开发模式的演变:串行变并行2)并行工程在产品开发中如何体现?3)新产品导入团队如何提前介入研发?* 为什么要提前介入?* 提前到什么时候介入?* 提前介入做什么?4)新产品导入团队的管理* 新产品导入团队与产品开发团队、职能部门的沟通* 新产品导入团队成员的汇报、考核和管理机制4. 演练与问题讨论根据企业的实际情况,研讨建立新产品导入团队的时机四、面向制造系统的产品设计(DFM)1. 如何在产品设计与开发过程中进行可制造性设计1)从制造的角度来看产品设计2)工艺人员介入产品开发过程的切入点:从立项就开始3)工艺管理的三个阶段:工艺设计、工艺调制与验证、工艺管制4)工艺设计:* 如何提出可制造性需求?* 需要哪些典型的工艺规范?* 可制造性需求如何落实到产品设计方案中?* 工艺设计与产品设计如何并行?* 产品工艺流程设计* 电装、整装、包装与物流的可制造性设计分析* 如何确保可制造性需求在产品开发中已被实现?* 工艺评审如何操作?* 什么时候考虑工装?* 如何在开发过程中同步输出工艺文件与生产操作指导文件5)工艺调制与验证* 工艺验证的时机* 工艺验证方案包括哪些内容?* 如何实施工艺验证?* 工艺验证报告的内容* 如何推动工艺验证的问题解决?* 研发人员如何配合新产品的工艺验证?* 制造外包模式下的工艺如何验证?6)工艺管制* 工艺管制的困惑:救火何时是尽头?* 工艺转产评审(标准、流程、责任)* 量产过程中的例行监控与异常管理2. 演练与问题讨论分析学员企业的工艺管理工作做到什么程度?存在哪些差距?3. 工艺管理平台建设1)谁负责工艺平台的建设?2)工艺委员会的产生:责任与运作模式3)如何进行工艺规划?4)基础工艺研究与应用5)支撑工艺管理平台的四大规范:* 品质规范* 设备规范* 工艺规范* 设计规划6)工艺管理部门如何推动DFM业务的开展?7)工艺体系的组织构成、发展与演变8)工艺人员的培养与技能提升4. 演练与问题讨论分析学员企业的工艺平台建设工作做到什么程度?存在哪些差距?如何改进?五、面向生产测试的产品设计(DFT)1. 基于产品生命周期全流程的测试策略1)研发测试(Alpha)、试验局测试(Beta)、生产测试2. 研发测试(Alpha)与BETA测试1)测试人员介入产品开发过程的时机(提可测试性需求的时机)2)可测试性需求需要考虑的内容(示例)3)单元测试、模块测试、系统集成测试、专业化测试、BETA测试的重点分析4)产品开发过程中测试业务流程分析5)企业在不同的发展阶段如何开展测试的相关工作(短平快的项目测试工作如何开展)3. 面向生产测试业务的产品设计与开发1)生产测试业务流程分析2)典型的部品测试、整机测试方法介绍3)开发专门的生产测试工装的条件分析4)生产测试工装的开发管理5)在产品开发过程中如何实施面向生产测试的产品设计?* 如何提出可测试性需求?* 可测试性需求如何落实到产品设计方案中?* 研发面对众多的需求如何取舍?可测试性需求的优先级分析* 如何在产品开发过程中同步开发生产测试工装?* 如何在产品开发过程中同步输出生产测试所需的操作指导文件?* 如何进行测试工装的验证?* 如何推动测试验证问题的解决?6)如何推动可测试性设计(DFT)业务的开展7)如何进行测试平台的建设?4. 演练与问题讨论分析学员企业的DFT工作做到什么程度?存在哪些差距?如何改进?六、产品试制验证管理1. 影响产品试制周期的因素分析2. 研发人员对试制准备提供的支持3. 试制团队的构成、职责与定位(设置试制部门的时机与优缺点分析)4. 试制人员介入产品开发过程的时机1)如何进行试制准备(准备要素示例)5. 面向制造系统的验证1)研发人员如何在试制过程中进行产品设计的优化2)制造系统的验证策略与计划3)制造系统的验证方案4)如何实施制造系统的验证:* 工艺验证(工艺流程、工艺路线、单板工艺、整机工艺、包装工艺、物流工艺)* 工装验证(装配工装、测试工装、生产设备)* 结构验证* 产品数据验证(BOM验证、制造文档验证)* 产品试制验证(质量、效率、成本)5)批次验证报告,验证多少批才合适?6)如何推动验证问题的解决?6. 转产评审1)研发人员如何支持新产品的转产工作2)转产评审的评审组织如何构成?* 评审标准是什么?* 如何判定是否转产?* 评审流程与运作机制7. 产品转产后的管理1)新产品的试制效果评价2)新产品的质量目标达成情况3)工程变更管理4)缺陷与问题管理5)质量审计8. 演练与问题讨论分析学员企业的产品试制验证过程,分析差距,提出改进建议讲师资质Charles 资深顾问专业背景十几年高科技行业从业背景,丰富的研发管理咨询经验,在国内某大型知名企业工作近10年,主持和参与过多个大型产品的研发工作,先后担任过开发工程师、项目经理、产品经理、新产品导入部总监、研发项目管理部总监等职位。
从样品走向量产工艺管理
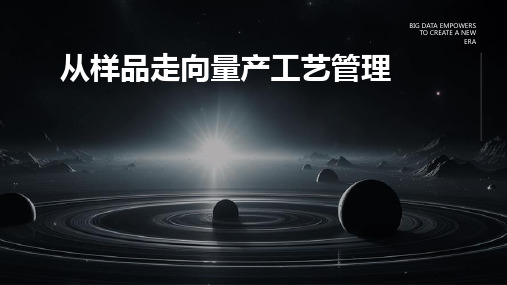
BIG DATA EMPOWERS TO CREATE A NEWERA
目录
CONTENTS
引言样品阶段工艺管理量产阶段工艺管理工艺转移过程中的问题与对策持续改进与优化总结与展望
BIG DATA EMPOWERS TO CREATE A NEWERA
引言
03
降低生产成本和风险
标准化操作
在样品阶段,操作可能较为灵活和多样化。但在量产阶段,为了确保稳定性和可重复性,必须实现标准化操作。这包括制定详细的操作规程、培训员工以及确保设备维护和校准。
质量保证
在从样品到量产的过渡中,质量保证至关重要。建立严格的质量控制体系,确保产品的一致性和可靠性,是满足客户需求和赢得市场认可的关键。
制定改进计划
根据改进需求,制定详细的改进计划,包括改进目标、方法、时间表和责任人。
BIG DATA EMPOWERS TO CREATE A NEWERA
总结与展望
工艺流程优化
在从样品走向量产的过程中,对工艺流程进行优化是关键。通过对生产流程的仔细分析和改进,可以提高生产效率、降低成本并确保产品质量。
01
确保产品从样品阶段到量产阶段的稳定性和一致性
02
提高生产效率和产品质量
BIG DATA EMPOWERS TO CREATE A NEWERA
样品阶段工艺管理
验证产品设计
通过制作样品,验证产品设计的可行性和正确性,确保产品满足设计要求。
评估工艺可行性
在样品阶段评估制造工艺的可行性,确定工艺流程、工艺参数和设备要求。
BIG DATA EMPOWERS TO CREATE A NEWERA
工艺转移过程中的问题与对策
新产品从样品到量产-产品中试管理129页PPT

35、不要以为自己成功一次就可以了 ,也不 要以为 过去的 光荣可 以被永 远肯定 。
新产品从样品到量产-产品中 试管理
31、别人笑我太疯癫,我笑他人看不 穿。(名 言网) 32、我不想听失意者的哭泣,抱怨者 的牢骚 ,这是 羊群中 的瘟疫 ,我不 能被它 传染。 我要尽 量避免 绝望, 辛勤耕 耘,忍 受苦楚 。我一 试再试 ,争取 每天的 成功, 避免以 失败收 常在别 人停滞 不前时 ,我继 续拼搏 。
23、一切节省,归根到底都归结为时间的节省。——马克思 24、意志命运往往背道而驰,决心到最后会全部推倒。——莎士比亚
25、学习是劳动,是充满思想的劳动。——乌申斯基
谢谢!
Байду номын сангаас
21、要知道对好事的称颂过于夸大,也会招来人们的反感轻蔑和嫉妒。——培根 22、业精于勤,荒于嬉;行成于思,毁于随。——韩愈
从样品到量产产品中试管理课件

•100
•从样品到量产产品中试管理
•101
•从样品到量产产品中试管理
•102
•从样品到量产产品中试管理
•103
•从样品到量产产品中试管理
•104
•从样品到量产产品中试管理
•105
•从样品到量产产品中试管理
•106
•从样品到量产产品中试管理
•107
•从样品到量产产品中试管理
•108
•从样品到量产产品中试管理
•46
•从样品到量产产品中试管理
•47
ቤተ መጻሕፍቲ ባይዱ
•从样品到量产产品中试管理
•48
•从样品到量产产品中试管理
•49
•从样品到量产产品中试管理
•50
•从样品到量产产品中试管理
•51
•从样品到量产产品中试管理
•52
•从样品到量产产品中试管理
•53
•从样品到量产产品中试管理
•54
•从样品到量产产品中试管理
•37
•从样品到量产产品中试管理
•38
•从样品到量产产品中试管理
•39
•从样品到量产产品中试管理
•40
•从样品到量产产品中试管理
•41
•从样品到量产产品中试管理
•42
•从样品到量产产品中试管理
•43
•从样品到量产产品中试管理
•44
•从样品到量产产品中试管理
•45
•从样品到量产产品中试管理
•从样品到量产产品中试管理
•1
•从样品到量产产品中试管理
•2
•从样品到量产产品中试管理
•3
•从样品到量产产品中试管理
•4
•从样品到量产产品中试管理
从样品走向量产-产品中试规划管理
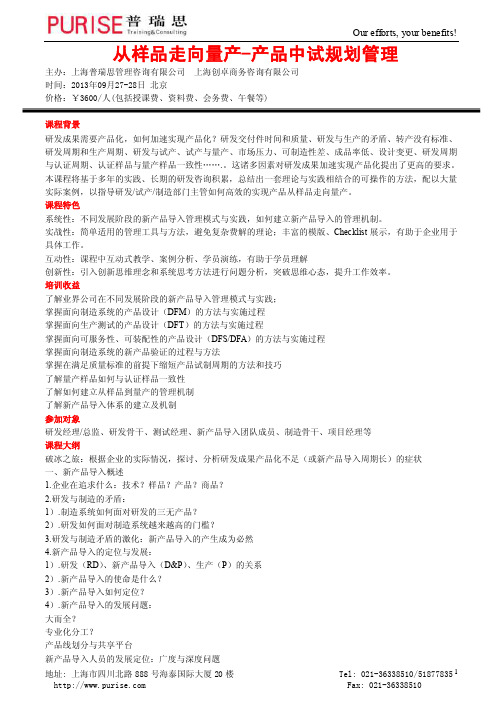
从样品走向量产-产品中试规划管理主办:上海普瑞思管理咨询有限公司上海创卓商务咨询有限公司时间:2013年09月27-28日北京价格:¥3600/人(包括授课费、资料费、会务费、午餐等)课程背景研发成果需要产品化,如何加速实现产品化?研发交付件时间和质量、研发与生产的矛盾、转产没有标准、研发周期和生产周期、研发与试产、试产与量产、市场压力、可制造性差、成品率低、设计变更、研发周期与认证周期、认证样品与量产样品一致性…….。
这诸多因素对研发成果加速实现产品化提出了更高的要求。
本课程将基于多年的实践、长期的研发咨询积累,总结出一套理论与实践相结合的可操作的方法,配以大量实际案例,以指导研发/试产/制造部门主管如何高效的实现产品从样品走向量产。
课程特色系统性:不同发展阶段的新产品导入管理模式与实践,如何建立新产品导入的管理机制。
实战性:简单适用的管理工具与方法,避免复杂费解的理论;丰富的模版、Checklist展示,有助于企业用于具体工作。
互动性:课程中互动式教学、案例分析、学员演练,有助于学员理解创新性:引入创新思维理念和系统思考方法进行问题分析,突破思维心态,提升工作效率。
培训收益了解业界公司在不同发展阶段的新产品导入管理模式与实践;掌握面向制造系统的产品设计(DFM)的方法与实施过程掌握面向生产测试的产品设计(DFT)的方法与实施过程掌握面向可服务性、可装配性的产品设计(DFS/DFA)的方法与实施过程掌握面向制造系统的新产品验证的过程与方法掌握在满足质量标准的前提下缩短产品试制周期的方法和技巧了解量产样品如何与认证样品一致性了解如何建立从样品到量产的管理机制了解新产品导入体系的建立及机制参加对象研发经理/总监、研发骨干、测试经理、新产品导入团队成员、制造骨干、项目经理等课程大纲破冰之旅:根据企业的实际情况,探讨、分析研发成果产品化不足(或新产品导入周期长)的症状一、新产品导入概述1.企业在追求什么:技术?样品?产品?商品?2.研发与制造的矛盾:1).制造系统如何面对研发的三无产品?2).研发如何面对制造系统越来越高的门槛?3.研发与制造矛盾的激化:新产品导入的产生成为必然4.新产品导入的定位与发展:1).研发(RD)、新产品导入(D&P)、生产(P)的关系2).新产品导入的使命是什么?3).新产品导入如何定位?4).新产品导入的发展问题:大而全?专业化分工?产品线划分与共享平台新产品导入人员的发展定位:广度与深度问题5.新产品导入的业务范围1).新产品导入业务:新产品导入(NPI)2).承上:如何面向产品的研发?3).启下:如何面向产品的制造?4).桥梁:新产品导入作为连接研发与制造的桥梁,独木桥还是阳关道?6.演练与问题讨论根据企业的实际情况,是否需要建立并发展新产品导入的职能?二、新产品导入(NPI)团队1.新产品导入团队的构成1).工艺工程2).设备工程3).测试工程4).工业工程5).产品验证6).试生产(计划、生产、质量)2.新产品导入团队的职责3.新产品导入团队与产品开发团队的关系1).开发模式的演变:串行变并行2).并行工程在产品开发中如何体现?3).新产品导入团队如何提前介入研发?为什么要提前介入?提前到什么时候介入?提前介入做什么?4).新产品导入团队的管理新产品导入团队与产品开发团队、职能部门的沟通新产品导入团队成员的汇报、考核和管理机制教学片分享:利益不同的双方如何沟通?4.演练与问题讨论根据企业的实际情况,研讨建立新产品导入团队的时机三、面向制造系统的产品设计(DFM)1.如何在产品设计与开发过程中进行可制造性设计1).从制造的角度来看产品设计2).工艺人员介入产品开发过程的切入点:从立项就开始产品立项阶段,需要考虑未来制造车间或制造厂的工艺、设备、人员因素产品立项阶段,需要考虑新产品导入的可复制性(A工厂成功模式切换到B工厂)3).工艺管理的三个阶段:工艺设计、工艺调制与验证、工艺管制4).工艺设计:如何提出可制造性需求?需要哪些典型的工艺规范?可制造性需求如何落实到产品设计方案中?工艺设计与产品设计如何并行?产品工艺流程设计电装、整装、包装与物流的可制造性设计分析如何确保可制造性需求在产品开发中已被实现?工艺评审如何操作?什么时候考虑工装?如何在开发过程中同步输出工艺文件与生产操作指导文件5).工艺调制与验证工艺验证的时机工艺验证方案包括哪些内容?如何实施工艺验证?工艺验证报告的内容如何推动工艺验证的问题解决?研发人员如何配合新产品的工艺验证?制造外包模式下的工艺如何验证?6).工艺管制工艺管制的困惑:救火何时是尽头?工艺转产评审(标准、流程、责任)量产过程中的例行监控与异常管理2.工艺管理平台建设1).谁负责工艺平台的建设?2).工艺委员会的产生:责任与运作模式3).如何进行工艺规划?4).基础工艺研究与应用5).支撑工艺管理平台的四大规范:品质规范设备规范工艺规范设计规划6).工艺管理部门如何推动DFM业务的开展?7).工艺体系的组织构成、发展与演变8).工艺人员的培养与技能提升四、面向生产测试的产品设计(DFT)1.基于产品生命周期全流程的测试策略1).研发测试(Alpha)、试验局测试(Beta)、生产测试2.研发测试(Alpha)与BETA测试1).测试人员介入产品开发过程的时机(可测试性需求的时机)2).可测试性需求需要考虑的内容(示例)3).单元测试、模块测试、系统集成测试、专业化测试、BETA测试的重点分析(可选择)4).产品开发过程中测试业务流程分析5).企业在不同的发展阶段如何开展测试的相关工作(短平快的项目测试工作如何开展)3.面向生产测试业务的产品设计与开发1).生产测试业务流程分析2).典型的部品测试、整机测试方法介绍3).开发专门的生产测试工装的条件分析4).生产测试工装的开发管理5).在产品开发过程中如何实施面向生产测试的产品设计?如何提出可测试性需求?可测试性需求如何落实到产品设计方案中?研发面对众多的需求如何取舍?可测试性需求的优先级分析如何在产品开发过程中同步开发生产测试工装?如何在产品开发过程中同步输出生产测试所需的操作指导文件?如何进行测试工装的验证?如何推动测试验证问题的解决?6).如何推动可测试性设计(DFT)业务的开展7).如何进行测试平台的建设?五、产品试制验证管理1.影响产品试制周期的因素分析2.研发人员对试制准备提供的支持3.试制团队的构成、职责与定位(设置试制部门的时机与优缺点分析)4.试制人员介入产品开发过程的时机1).如何进行试制准备(准备要素示例)5.面向制造系统的验证1).研发人员如何在试制过程中进行产品设计的优化2).制造系统的验证策略与计划3).制造系统的验证方案4).如何实施制造系统的验证:工艺验证(工艺流程、工艺路线、部件工艺、整件工艺、包装工艺、物流工艺)工装验证(装配工装、测试工装、生产设备)结构验证产品数据验证(BOM验证、制造文档验证)产品试制验证(质量、效率、成本)5).批次验证报告,验证多少批才合适?6).如何推动验证问题的解决?6.转产评审1).研发人员如何支持新产品的转产工作?2).转产评审的评审组织如何构成?3).评审标准是什么?4).如何判定是否转产?5).评审流程与运作机制7.产品转产后的管理1).新产品的试制效果评价2).新产品的质量目标达成情况3).工程变更管理4).缺陷与问题管理5).质量审计8.演练与问题讨论1).分析企业的产品试制验证过程,分析差距,提出改进建议六、新产品导入体系建设规划1.新产品导入体系建设策略1).系统规划2).先易后难3).。
从样品到量产中试培训[可修改版ppt]
![从样品到量产中试培训[可修改版ppt]](https://img.taocdn.com/s3/m/e89d3e4fbd64783e09122ba0.png)
TR2 TR3 TR4 TR4A TR5 TR6
参与可制造 性需求分解
与分配
工艺总体方 案设计 参与并评估可 制造性设计
制造工艺 详细设计
工艺开发
参与制造 系统验证 并优化工
艺
工艺复制
工艺管制
概念阶段DFM的关键活动
概念
计划
开发 验证 发布
生命 周期
提出可制造性需求 TR1
什么是可制造性需求?
PDT角色 • 制定制造策略和计划 • 提供产品可制造性需求 • 组织制造工艺和装备的开发 • 组织制造工艺和装备的验证 • 监控产品开发的制造准备度 • 监控关键时间点
制造代表
FUNTION角色 • 输入制造策略和计划 • 组织验证制造系统 • 监控制造系统的准备度 • 监控物料计划 • 组织量产前的产品生产 • 跟踪和解决供货问题
DCP TR
NPD流程/NPI流程
项目管理
协调和沟通
制造系统流程/NPI流程
执行
NPI团队介入产品开发过程的时机
概念
•产品需求 •关键技术 •产品概念
计划
•设计需求 •总体方案 •概要设计
开发 验证
发布
生命 周期
•详细设计 •构建原型 (功能样机)
•性能样机
•试生产 •制造验证
•BETA
•产品发布 •开始销售
▪ 可制造性设计(DFM) 的核心在于工艺设计。
什么是工艺?
▪ 什么是工艺?
▪ 工艺人员在做什么?
➢ 救火 ➢ 防火
▪ 怎么防火?
➢ 正本清源,提前介入
工艺管理的三段论
工艺设计 工艺调制与验证
工艺管制
产品开发过程中面向制造系统的设计
从样品走向量产工艺管理

【解决措施】
1、 由 于 更 改 方 案 困 难 , 涉 及 面 广 , 硬 件 方 案 不 好 更 改 ;
2、 盒 体 和 上 盖 的 表 面 处 理 方 面 , 从 最 开 始 设 计 为 表 面 氧 化 更 改 为 表 面 发 黑 , 同 时在盒体表面贴保护膜,待调测完后撕去保护膜。
DFA(可装配性设计)
▪ DFA:Design For Assembly ➢将装配准则集成到产品设计过程中; ➢将产品设计和工艺设计集成到同一个过程中
▪ 目的: ➢提高产品的可装配性 ➢降低产品成本
零件级 组件级 产品级
DFA的层次
最 重 要 的 DFA原 则
简化设计,减少零件数量和种类 标准化设计,采用通用件和材料 方便运输 方便安装(避免调整和错误安装) 尽可能使零件对称 适合目前的工艺
(新型电缆的制造需求)
计划阶段DFM的关键活动
概念
计划
开发 验证 发布
生命 周期
工艺仿真 工艺总体设计
跟进可制造性需求已被落实
到规格/总体方案/概要设计中
(需求的分解与分配)
TR2
可制造性需求的分解与分配
▪ DFM需求分解与分配样例 ▪ 形成产品规格
工艺总体设计
▪ 产品特点 ▪ 工艺难点(设计、验证) ▪ 工艺流程、工艺路线 ▪ 返修策略(备件计划、停产器件) ▪ 品质保证(工装) ▪ 制造效率 ▪ 制造成本
NPI团队的角色和职责定位
PDT角色 • 制定制造策略和计划 • 提供产品可制造性需求 • 组织制造工艺和装备的开发 • 组织制造工艺和装备的验证 • 监控产品开发的制造准备度 • 监控关键时间点
产品中试管理从样品到量产

产品中试管理——从样品到量产●课程背景我们在为企业提供研发管理咨询服务的过程中发现,很多企业的新产品开发从样机到量产的过程中(产品化过程)存在着共同的问题:1、新品没有经过中试或中试的时间很短,制造部门戏称研发的新品是“三无”产品,没有生产文件、没有工装、生产现场出了问题没人管;2、转产没有标准,研发想快点转产,生产对有问题的产品又不愿接收,希望研发把问题都解决了才转过来,而市场又催得急,经常被迫接收,长此以往,导致研发与生产的矛盾激化;3、有些企业开始成立中试部门,希望在中试阶段把产品质量问题解决掉,但中试的定位与运作也很困惑,发生质量与进度的冲突时,如何取舍与平衡,以前研发与制造的矛盾转化为研发与中试、中试与生产的矛盾,中试成了矛盾集散中心;4、市场的压力并不因中试的产生而减少,中试需要从哪些方面努力才能满足产品的质量、进度的要求?中试的业务是面向研发还是面向制造,还是兼而有之?5、量产后才发现产品可制造性差、成品率低、经常返工,影响发货;6、产品到了生产后还发生大量的设计变更;7、产品到了客户手中还冒出各种各样的问题以致要研发人员到处去“救火”。
本课程将基于多年的实践、长期的研发咨询积累,总结出一套理论与实践相结合的可操作的方法,配以大量实际案例,以指导研发/试产/制造部门主管如何高效的实现产品从样品走向量产。
●培训方式:案例分享、实务分析、互动讨论、项目模拟、培训游戏●培训收益1、了解业界公司在不同发展阶段的产品中试管理模式与实践2、掌握面向制造系统的产品设计(DFM)的方法与实施过程3、掌握面向生产测试的产品设计(DFT)的方法与实施过程4、掌握面向制造系统的新产品验证的过程与方法5、掌握在满足质量标准的前提下缩短产品试制周期的方法和技巧6、了解如何建立从样品到量产的管理机制●课程内容一、案例研讨二、从样品到量产概述1、企业在追求什么:技术?样品?产品?商品?2、研发与制造的矛盾:1)制造系统如何面对研发的三无产品?2)研发如何面对制造系统越来越高的门槛?3、研发与制造矛盾的激化:中试的产生成为必然4、中试的定位与发展:1)研发(RD)中试(D&P)生产(P)的关系2)中试的使命是什么?3)中试如何定位?4)中试的发展问题:◇大而全?◇专业化分工?◇产品线划分与共享平台◇中试人员的发展定位:广度与深度问题5、中试的业务范围1)中试业务:新产品导入(NPI)2)承上:如何面向产品的研发?3)启下:如何面向产品的制造?4)桥梁:中试作为连接研发与制造的桥梁,独木桥还是阳关道?6、演练与问题讨论1)根据企业的实际情况,是否需要建立并发展中试的职能?三、新产品导入团队1、新产品导入团队的构成1)工艺工程2)设备工程3)测试工程4)工业工程5)产品验证6)试生产(计划、生产、质量)2、新产品导入团队的职责3、新产品导入团队与产品开发团队的关系1)开发模式的演变:串行变并行2)并行工程在产品开发中如何体现?3)新产品导入团队如何提前介入研发?◇为什么要提前介入?◇提前到什么时候介入?◇提前介入做什么?4)新产品导入团队的管理◇新产品导入团队与产品开发团队、职能部门的沟通◇新产品导入团队成员的汇报、考核和管理机制4、演练与问题讨论1)根据企业的实际情况,研讨建立新产品导入团队的时机四、面向制造系统的产品设计(DFM)1、如何在产品设计与开发过程中进行可制造性设计1)从制造的角度来看产品设计2)工艺人员介入产品开发过程的切入点:从立项就开始3)工艺管理的三个阶段:工艺设计、工艺调制与验证、工艺管制4)工艺设计:◇如何提出可制造性需求?◇需要哪些典型的工艺规范?◇可制造性需求如何落实到产品设计方案中?◇工艺设计与产品设计如何并行?◇产品工艺流程设计◇电装、整装、包装与物流的可制造性设计分析◇如何确保可制造性需求在产品开发中已被实现?◇工艺评审如何操作?◇什么时候考虑工装?◇如何在开发过程中同步输出工艺文件与生产操作指导文件5)工艺调制与验证◇工艺验证的时机◇工艺验证方案包括哪些内容?◇如何实施工艺验证?◇工艺验证报告的内容◇如何推动工艺验证的问题解决?◇研发人员如何配合新产品的工艺验证?◇制造外包模式下的工艺如何验证?6)工艺管制◇工艺管制的困惑:救火何时是尽头?◇工艺转产评审(标准、流程、责任)◇量产过程中的例行监控与异常管理2、演练与问题讨论1)分析学员企业的工艺管理工作做到什么程度?存在哪些差距?3、工艺管理平台建设1)谁负责工艺平台的建设?2)工艺委员会的产生:责任与运作模式3)如何进行工艺规划?4)基础工艺研究与应用5)支撑工艺管理平台的四大规范:◇品质规范◇设备规范◇工艺规范◇设计规划6)工艺管理部门如何推动DFM业务的开展?7)工艺体系的组织构成、发展与演变8)工艺人员的培养与技能提升4、演练与问题讨论1)分析学员企业的工艺平台建设工作做到什么程度?存在哪些差距?如何改进?五、面向生产测试的产品设计(DFT)1、基于产品生命周期全流程的测试策略1)研发测试(Alpha)试验局测试(Beta)生产测试2、研发测试(Alpha)与BETA测试1)测试人员介入产品开发过程的时机(提可测试性需求的时机)2)可测试性需求需要考虑的内容(示例)3)单元测试、模块测试、系统集成测试、专业化测试、BETA测试的重点分析4)产品开发过程中测试业务流程分析5)企业在不同的发展阶段如何开展测试的相关工作(短平快的项目测试工作如何开展)3、面向生产测试业务的产品设计与开发1)生产测试业务流程分析2)典型的部品测试、整机测试方法介绍3)开发专门的生产测试工装的条件分析4)生产测试工装的开发管理5)在产品开发过程中如何实施面向生产测试的产品设计?◇如何提出可测试性需求?◇可测试性需求如何落实到产品设计方案中?◇研发面对众多的需求如何取舍?可测试性需求的优先级分析◇如何在产品开发过程中同步开发生产测试工装?◇如何在产品开发过程中同步输出生产测试所需的操作指导文件?◇如何进行测试工装的验证?◇如何推动测试验证问题的解决?6)如何推动可测试性设计(DFT)业务的开展7)如何进行测试平台的建设?4、演练与问题讨论1)分析学员企业的DFT工作做到什么程度?存在哪些差距?如何改进?六、产品试制验证管理1、影响产品试制周期的因素分析2、研发人员对试制准备提供的支持3、试制团队的构成、职责与定位(设置试制部门的时机与优缺点分析)4、试制人员介入产品开发过程的时机1)如何进行试制准备(准备要素示例)5、面向制造系统的验证1)研发人员如何在试制过程中进行产品设计的优化2)制造系统的验证策略与计划3)制造系统的验证方案4)如何实施制造系统的验证:◇工艺验证(工艺流程、工艺路线、单板工艺、整机工艺、包装工艺、物流工艺)◇工装验证(装配工装、测试工装、生产设备)◇结构验证◇产品数据验证(BOM验证、制造文档验证)◇产品试制验证(质量、效率、成本)5)批次验证报告,验证多少批才合适?6)如何推动验证问题的解决?6、转产评审1)研发人员如何支持新产品的转产工作2)转产评审的评审组织如何构成?3)评审标准是什么?4)如何判定是否转产?5)评审流程与运作机制7、产品转产后的管理1)新产品的试制效果评价2)新产品的质量目标达成情况3)工程变更管理4)缺陷与问题管理5)质量审计8、演练与问题讨论1)分析学员企业的产品试制验证过程,分析差距,提出改进建议。
企业内训:从样机走向量产-中试规划与管理

企业内训:从样机走向量产-中试规划与管理明阳天下拓展培训主题:从样机到量产产品中试管理体系 IPD集成产品开发天数:2 天课程目标:了解业界公司在不同发展阶段的产品中试管理模式与实践学掌握面向制造系统的产品设计(DFM)的方法与实施过程掌握面向生产测试的产品设计(DFT)的方法与实施过程掌握面向可服务性、可装配性的产品设计(DFS/DFA)的方法与实施过程掌握面向制造系统的新产品验证的过程与方法掌握在满足质量标准的前提下缩短产品试制周期的方法和技巧了解量产样机如何与认证样机一致性了解如何建立从样机到量产的管理机制了解中试体系的建立及机制课程大纲:一、从样机到量产概述1.制造的烦恼?研发的困惑?2.企业在追求什么:技术?样品?产品?商品?3.研发成果产品化不足的症状?4.演练与讨论:根据企业的实际情况,分析研发成果产品化不足的症状5.研发成果产品化不足症状表现(总结)缺乏中试体系测试物料工艺装备产品数据试制验证6.新产品投产后的问题:设计问题原材料质量问题输出工艺问题产品认证周期延期7.综合性的解决方案:建设新产品中试体系8.中试体系的定义9.新产品中试体系的产生背景10.案例分析:某公司中试发展历程分享11.中试是研发工作的组成部分12.中试概念的由来13.中试的意义中试空白现象别让“中试”成短板政府的重视与扶持案例分享14.讨论:根据企业实际情况,研讨是否需要建立并发展中试职能?二、中试业务体系及工作目标1.产品商品的关键要素;2.样机产品化的关键要素;3.研发样机商品化—如何实现?4.中试工作分解目标:提高产品质量;制造系统设计;提高产品可销售性5.中试业务体系图详解;6.中试的定位与发展;7.构建中试体系成为必然;8.提高质量,加快新产品上市进程;9.中试工作目标:“从样机走向量产,加速实现开发成果商品化”;10.研发模式的演变说明;11.IPD整体框架介绍;12.集成产品开发简介-研发阶段;讨论:根据企业实际情况:讨论如何建立中试体系?三、中试团队(NPI团队)组织介绍1.中试团队(NPI团队)的构成;2.中试团队(NPI团队)的职责;3.新产品导入团队与产品开发团队的关系;4.中试团队的优点;5.中试各业务部门管理特点;6.中试业务主管的任职要求;7.中试KPI指标及分解;8.中试骨干人员素质要求9.演练与问题讨论根据企业的实际情况,研讨建立中试团队(NPI团队)的时机四、中试与工程设计(DFX)中试与工程设计概论1.工程设计的定义:为了满足除了用户功能需求之外的其它需求而做的产品设计;2.工程设计切入点—从立项阶段开始、实施并行开发;3.工程设计(DFX:DesignForeXcellence);DFM:可制造性设计;DFA:可装配性设计;DFT:可测试性设计;DFS:可服务性设计;工程设计(DFX:DesignForeXcellence);4.中试与工程设计关系阐述中试业务的核心要素;工程设计的关键要素;中试如何利用工程设计的关键要素进行前期导入;中试与可制造性设计(DFM)5.如何在产品设计与开发过程中进行可制造性设计(DFM)从制造的角度来看产品设计工艺人员介入产品开发过程的切入点:从立项就开始工艺管理的三个阶段:工艺设计、工艺调制与验证、工艺管制工艺设计工艺调制与验证工艺管制6.工艺管理平台建设谁负责工艺平台的建设工艺委员会的产生:责任与运作模式如何进行工艺规划?基础工艺研究与应用支撑工艺管理平台的四大规范工艺管理部门如何推动DFM业务的开展?工艺体系的组织构成、发展与演变工艺人员的培养与技能提升中试与可服务性设计(DFS)7.产品可服务性(DFS)示例、模式及方法业界公司可服务性模式分享提高可服务性的常见方法中试与可测试性设计(DFT)8.基于产品生命周期全流程的测试策略(DFT)9.研发测试(α)与β测试测试人员介入产品开发过程的时机(提可测试性需求的时机)可测试性需求需要考虑的内容(示例)单元测试、模块测试、系统集成测试、专业化测试、β测试的重点分析产品开发过程中测试业务流程分析企业在不同的发展阶段如何开展测试的相关工作(短平快的项目测试工作如何开展)10.面向生产测试业务的产品设计与开发生产测试业务流程分析典型的部品测试、整机测试方法介绍开发专门的生产测试工装的条件分析生产测试工装的开发管理在产品开发过程中如何实施面向生产测试的产品设计如何推动可测试性设计(DFT)业务的发展如何进行测试平台的建设?产品试制验证管理11.面向制造系统的产品验证活动和策略12.产品试制准备13.影响产品试制周期的因素分析14.研发人员对试制准备提供的支持15.试制人员介入产品开发过程的时机16.面向制造系统的验证方案及验证内容17.制造系统验证的基本假设18.工艺验证的内容19.文档验证的内容20.BOM验证的内容21.制造系统验证报告格式及内容22.验证阶段的关键活动分析23.试制验证KPI分解转产评审24.转产评审25.发布、生命周期阶段的关键活动分析26.产品转产后的管理并行化中试介绍27.并行化中试业务流程说明工程设计是中试应提前开展的主要工作产品测试流程示意图及分析工艺设计流程示意图及分析装备开发流程示意图及分析物料品质流程示意图及分析产品数据流程示意图及分析批量流程示意图及分析28.演练与问题讨论本企业在产品中试六个专业领域方面的问题和改进措施29.中试部职责总体描述五、中试体系建设规划1.中试体系建设策略a)系统规划b)先易后难c)。
产品中试管理——从样品到量产(Charles--曹修洪)
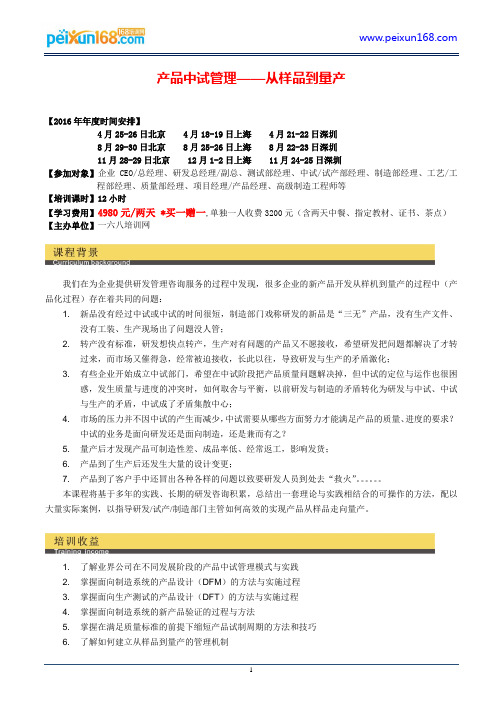
产品中试管理——从样品到量产【2016年年度时间安排】4月25-26日北京 4月18-19日上海 4月21-22日深圳8月29-30日北京 8月25-26日上海 8月22-23日深圳11月28-29日北京 12月1-2日上海 11月24-25日深圳【参加对象】企业CEO/总经理、研发总经理/副总、测试部经理、中试/试产部经理、制造部经理、工艺/工程部经理、质量部经理、项目经理/产品经理、高级制造工程师等【培训课时】12小时【学习费用】4980元/两天 *买一赠一,单独一人收费3200元(含两天中餐、指定教材、证书、茶点)【主办单位】一六八培训网我们在为企业提供研发管理咨询服务的过程中发现,很多企业的新产品开发从样机到量产的过程中(产品化过程)存在着共同的问题:1. 新品没有经过中试或中试的时间很短,制造部门戏称研发的新品是“三无”产品,没有生产文件、没有工装、生产现场出了问题没人管;2. 转产没有标准,研发想快点转产,生产对有问题的产品又不愿接收,希望研发把问题都解决了才转过来,而市场又催得急,经常被迫接收,长此以往,导致研发与生产的矛盾激化;3. 有些企业开始成立中试部门,希望在中试阶段把产品质量问题解决掉,但中试的定位与运作也很困惑,发生质量与进度的冲突时,如何取舍与平衡,以前研发与制造的矛盾转化为研发与中试、中试与生产的矛盾,中试成了矛盾集散中心;4. 市场的压力并不因中试的产生而减少,中试需要从哪些方面努力才能满足产品的质量、进度的要求?中试的业务是面向研发还是面向制造,还是兼而有之?5. 量产后才发现产品可制造性差、成品率低、经常返工,影响发货;6. 产品到了生产后还发生大量的设计变更;7. 产品到了客户手中还冒出各种各样的问题以致要研发人员到处去“救火”。
本课程将基于多年的实践、长期的研发咨询积累,总结出一套理论与实践相结合的可操作的方法,配以大量实际案例,以指导研发/试产/制造部门主管如何高效的实现产品从样品走向量产。
- 1、下载文档前请自行甄别文档内容的完整性,平台不提供额外的编辑、内容补充、找答案等附加服务。
- 2、"仅部分预览"的文档,不可在线预览部分如存在完整性等问题,可反馈申请退款(可完整预览的文档不适用该条件!)。
- 3、如文档侵犯您的权益,请联系客服反馈,我们会尽快为您处理(人工客服工作时间:9:00-18:30)。
产品中试管理-从样品到量产主讲:Charles(研发管理咨询资深顾问、国家发改委创新管理培训中心特邀讲师、清华大学国际工程项目管理研究院特邀讲师)课程对象:企业CEO/总经理、研发总经理/副总、测试部经理、中试/试产部经理、制造部经理、工艺/工程部经理、质量部经理、项目经理/产品经理、高级制造工程师等授课方式:讲师讲授 + 视频演绎 + 案例研讨 +角色扮演 + 讲师点评【课程背景】我们在为企业提供研发管理咨询服务的过程中发现,很多企业的新产品开发从样机到量产的过程中(产品化过程)存在着共同的问题:1、新品没有经过中试或中试的时间很短,制造部门戏称研发的新品是“三无”产品,没有生产文件、没有工装、生产现场出了问题没人管;2、转产没有标准,研发想快点转产,生产对有问题的产品又不愿接收,希望研发把问题都解决了才转过来,而市场又催得急,经常被迫接收,长此以往,导致研发与生产的矛盾激化;3、有些企业开始成立中试部门,希望在中试阶段把产品质量问题解决掉,但中试的定位与运作也很困惑,发生质量与进度的冲突时,如何取舍与平衡,以前研发与制造的矛盾转化为研发与中试、中试与生产的矛盾,中试成了矛盾集散中心;4、市场的压力并不因中试的产生而减少,中试需要从哪些方面努力才能满足产品的质量、进度的要求?中试的业务是面向研发还是面向制造,还是兼而有之?5、量产后才发现产品可制造性差、成品率低、经常返工,影响发货;6、产品到了生产后还发生大量的设计变更;7、产品到了客户手中还冒出各种各样的问题以致要研发人员到处去“救火”。
本课程将基于多年的实践、长期的研发咨询积累,总结出一套理论与实践相结合的可操作的方法,配以大量实际案例,以指导研发/试产/制造部门主管如何高效的实现产品从样品走向量产。
【课程价值】1.了解业界公司在不同发展阶段的产品中试管理模式与实践2.掌握面向制造系统的产品设计(DFM)的方法与实施过程3.掌握面向生产测试的产品设计(DFT)的方法与实施过程4.掌握面向制造系统的新产品验证的过程与方法5.掌握在满足质量标准的前提下缩短产品试制周期的方法和技巧6.了解如何建立从样品到量产的管理机制【培训内容】一、案例研讨二、从样品到量产概述1、企业在追求什么:技术?样品?产品?商品?2、研发与制造的矛盾:1)制造系统如何面对研发的三无产品?2)研发如何面对制造系统越来越高的门槛?3、研发与制造矛盾的激化:中试的产生成为必然4、中试的定位与发展:1)研发(RD)、中试(D&P)、生产(P)的关系2)中试的使命是什么?3)中试如何定位?4)中试的发展问题:大而全?专业化分工?产品线划分与共享平台中试人员的发展定位:广度与深度问题5、中试的业务范围1)中试业务:新产品导入(NPI)2)承上:如何面向产品的研发?3)启下:如何面向产品的制造?4)桥梁:中试作为连接研发与制造的桥梁,独木桥还是阳关道?6、演练与问题讨论1)根据企业的实际情况,是否需要建立并发展中试的职能?三、新产品导入团队1、新产品导入团队的构成1)工艺工程2)设备工程3)测试工程4)工业工程5)产品验证6)试生产(计划、生产、质量)2、新产品导入团队的职责3、新产品导入团队与产品开发团队的关系1)开发模式的演变:串行变并行2)并行工程在产品开发中如何体现?3)新产品导入团队如何提前介入研发?为什么要提前介入?提前到什么时候介入?提前介入做什么?4)新产品导入团队的管理新产品导入团队与产品开发团队、职能部门的沟通新产品导入团队成员的汇报、考核和管理机制4、演练与问题讨论1)根据企业的实际情况,研讨建立新产品导入团队的时机四、面向制造系统的产品设计(DFM)1、如何在产品设计与开发过程中进行可制造性设计1)从制造的角度来看产品设计2)工艺人员介入产品开发过程的切入点:从立项就开始3)工艺管理的三个阶段:工艺设计、工艺调制与验证、工艺管制4)工艺设计:如何提出可制造性需求?需要哪些典型的工艺规范?可制造性需求如何落实到产品设计方案中?工艺设计与产品设计如何并行?产品工艺流程设计电装、整装、包装与物流的可制造性设计分析如何确保可制造性需求在产品开发中已被实现?工艺评审如何操作?什么时候考虑工装?如何在开发过程中同步输出工艺文件与生产操作指导文件5)工艺调制与验证工艺验证的时机工艺验证方案包括哪些内容?如何实施工艺验证?工艺验证报告的内容如何推动工艺验证的问题解决?研发人员如何配合新产品的工艺验证?制造外包模式下的工艺如何验证?6)工艺管制工艺管制的困惑:救火何时是尽头?工艺转产评审(标准、流程、责任)量产过程中的例行监控与异常管理2、演练与问题讨论1)分析学员企业的工艺管理工作做到什么程度?存在哪些差距?3、工艺管理平台建设1)谁负责工艺平台的建设?2)工艺委员会的产生:责任与运作模式3)如何进行工艺规划?4)基础工艺研究与应用5)支撑工艺管理平台的四大规范:品质规范设备规范工艺规范设计规划6)工艺管理部门如何推动DFM业务的开展?7)工艺体系的组织构成、发展与演变8)工艺人员的培养与技能提升4、演练与问题讨论1)分析学员企业的工艺平台建设工作做到什么程度?存在哪些差距?如何改进?五、面向生产测试的产品设计(DFT)1、基于产品生命周期全流程的测试策略1)研发测试(Alpha)、试验局测试(Beta)、生产测试2.研发测试(Alpha)与BETA测试1)测试人员介入产品开发过程的时机(提可测试性需求的时机)2)可测试性需求需要考虑的内容(示例)3)单元测试、模块测试、系统集成测试、专业化测试、BETA测试的重点分析4)产品开发过程中测试业务流程分析5)企业在不同的发展阶段如何开展测试的相关工作(短平快的项目测试工作如何开展)3、面向生产测试业务的产品设计与开发1)生产测试业务流程分析2)典型的部品测试、整机测试方法介绍3)开发专门的生产测试工装的条件分析4)生产测试工装的开发管理5)在产品开发过程中如何实施面向生产测试的产品设计?如何提出可测试性需求?可测试性需求如何落实到产品设计方案中?研发面对众多的需求如何取舍?可测试性需求的优先级分析如何在产品开发过程中同步开发生产测试工装?如何在产品开发过程中同步输出生产测试所需的操作指导文件?如何进行测试工装的验证?如何推动测试验证问题的解决?6)如何推动可测试性设计(DFT)业务的开展7)如何进行测试平台的建设?4、演练与问题讨论1)分析学员企业的DFT工作做到什么程度?存在哪些差距?如何改进?六、产品试制验证管理1、影响产品试制周期的因素分析2、研发人员对试制准备提供的支持3、试制团队的构成、职责与定位(设置试制部门的时机与优缺点分析)4、试制人员介入产品开发过程的时机1)如何进行试制准备(准备要素示例)5、面向制造系统的验证1)研发人员如何在试制过程中进行产品设计的优化2)制造系统的验证策略与计划3)制造系统的验证方案4)如何实施制造系统的验证:工艺验证(工艺流程、工艺路线、单板工艺、整机工艺、包装工艺、物流工艺)工装验证(装配工装、测试工装、生产设备)结构验证产品数据验证(BOM验证、制造文档验证)产品试制验证(质量、效率、成本)5)批次验证报告,验证多少批才合适?6)如何推动验证问题的解决?6、转产评审1)研发人员如何支持新产品的转产工作2)转产评审的评审组织如何构成?3)评审标准是什么?4)如何判定是否转产?5)评审流程与运作机制7、产品转产后的管理1)新产品的试制效果评价2)新产品的质量目标达成情况3)工程变更管理4)缺陷与问题管理5)质量审计8、演练与问题讨论1)分析学员企业的产品试制验证过程,分析差距,提出改进建议。
七、总结【讲师介绍】Charles研发管理咨询资深顾问、国家发改委创新管理培训中心特邀讲师、清华大学国际工程项目管理研究院特邀讲师专业背景16年的高科技企业从业背景,具有丰富的产品策划、产品研发、产品中试、产品服务等领域的实践与管理经验。
从事过产品设计与开发、NPI、项目经理、产品经理、研发管理部经理、企业管理顾问等职务;曾在国内某著名通信设备公司工作过7年(97~04),期间与国际顶尖咨询顾问一起工作,作为核心成员全程参与推动该公司研发管理体系的变革工作,并作为产品经理主导了某产品线多个大型项目的产品设计、开发、中试、转产与上市工作。
研发管理咨询经验7年的研发管理咨询经验,主导了20多个研发管理咨询项目,项目范围涉及到市场需求、产品规划、产品开发、产品决策、技术评审、技术开发、研发组织、研发绩效、技术任职资格、项目管理、变更管理、知识管理、研发IT规划等领域。
典型客户如下:1)科达通信2)OPPO3)TCL家网事业部4)苏州金龙5)宇通重工6)京信集团7)福建敏讯8)中电集团某军品研究所研发管理培训经验曾为中国空间技术研究院、南瑞科技、TCL集团、长虹集团、OPPO、同方威视、宝钢集团、中国移动、大唐电信、上海电信、陕鼓集团、科达通信、中电集团、威创科技、和记奥普泰、国人通信、京信科技、天碁科技、格林威尔、兴大豪科技、星星集团、山特电子、富港电子、宇龙通信、聚光科技、绿盟科技、天津内燃机研究所、中集集团、高斯贝尔、星网锐捷、特变电工、思源电器、美的集团、海尔集团、海信集团、普天集团、福建敏讯、国光电子、苏州金龙、宇通重工、雷沃重汽、上汽五凌、东风汽车、威科姆、同洲电子、科立讯、新北洋、光迅科技、沈阳机床、瑞斯康达、佳讯飞鸿、浪潮集团、威胜电子、京城控股、联想集团、迈瑞医疗、华大电子、上海华虹、联芯科技、旋极科技、畅通科技、长城软件、九院、天地奔牛、阳天电子、清华机械、方正集团、研祥智能、烟台万华、东方电子、东方通信、美菱、科大讯飞、万峰石材、万家乐、泛仕达、远光软件、优特等近500家企业提供了专业的研发管理培训。
部分培训和咨询客户本咨询公司自成立以来,已经为近2000家企业提供了专业的研发管理培训,同时也为近80家大中型企业提供了研发管理咨询服务,帮助这些企业建立研发管理体系并实现研发模式的转型。
咨询的客户主要为知名的大中型企业、细分行业的龙头企业和快速增长的高科技公司,部分客户名单如下:通信类企业:诺基亚-西门子、摩托罗拉、大唐移动、普天研究院、康佳移动、神州数码、海信通信、信威通信、TCL移动通信、德信无线、威盛电子、格林威尔、经纬科技、东方通信、星网锐捷、鑫诺通讯、京信通信、广东普泰、金鹏通信、TCL网络、冠日通讯、佳讯飞鸿、和记澳普泰、飞通光电、东进通讯、海天天线、PBI国际、海格通信、阿尔西、福建敏讯、无限立通、瑞斯康达、全亚通讯、虹信科技、国人通讯、杰赛科技、冠日通讯、实达网络……软件及互联网类企业:阿里巴巴、支付宝、淘宝网、中软国际、用友、东软、金蝶、网易、新浪、搜狐、盛大网络、腾讯、格尔软件、天融信、网御神州、广联达、北大方正、方正阿帕比、华胜天成、绿盟、超图、灵图、卫士通、亚信、亿阳信通、思特奇、神州数码软件集团、广州新太、金证科技、中国工商银行软件开发中心、卓望科技、黎明网络、新粤交通投资、中太数据、华友世纪、今朝科技、联友科技、穗彩科技、龙江风采、华友世纪、高阳金信、杭州虹软、中国银联、雁联……计算机类企业:联想集团、清华同方、华硕电脑、方正科技、TCL电脑、朗科科技、记忆科技、华旗资讯、研祥智能、国微电子、升腾资讯、普瑞尔电子、长城电脑、穗彩科技、冠捷电子、南京富士通计算机、三诺电子、多彩科技、伟创力、顶星数码、顶星科技、大将科技、清华比威、太极计算机……家电电子类:海尔集团、康佳集团、夏新电子、格力电器、美的电饭煲、美的空调、荣事达、TCL王牌、创维集团、海信集团、威创集团、同洲电子、赛科世纪、信利半导体、北洋电气、步步高、万家乐电器、苏泊尔、达实智能、卓力电器、美欧电子、豪恩科技、四达时代等……电信运营商:中国网通、中国电信北京研究院/广州研究院、北京移动、广东移动、深圳移动、吉林移动、上海电信、武汉电信、广东联通、深圳联通、东莞联通、新乡联通、深大电话、湛江移动、惠州移动、深圳市邮政局、天威视讯……机械及交通运输:北京奔驰、上汽通用泛亚研发中心、上海通用、上汽通用五菱、长城汽车、中兴汽车、北汽福田汽车、一汽轿车、一汽解放、一汽夏利、长安汽车、天津内燃机研究所、黄海汽车、徐工集团、中联重工、东风汽车、神龙汽车、江铃汽车、南汽汽车、南车集团、北京吉普、成都飞机制造厂、东风标致、江淮汽车、宇通客车、元征科技、西子OTIS、西子孚信、顺德震德、鹰牌控股、青岛英派斯、浙大中控等……集成电路(芯片):华大电子、上海华虹、天碁科技、上海展讯、珠海炬力、凯明、上海贝岭、复旦微电子、博奥生物、北方微电子、威睿电通等……电源及其他电子类企业:爱默生网络能源、比亚迪、山特电子、雄韬电源、皇源电子、伊博电源、核达中远通、斯比泰、珠海金电电源、泰坦科技、华德电子、福建科华、信瑞电子、湖南瑞翔、中达电通、天津中环电子、天津光电集团、天仪集团、中电集团第7研究所、中电集团第43研究所、中电集团第29研究所、公安部第一研究所、东进电子、威科姆电子、上海精伦等……电力及自动化类企业:国电南自、四方继保、南瑞继保、深圳南瑞、科陆电子、上海海得、华力特设备、上海思源、泰豪科技、汇港科技、金智科技、申瑞电力、如高高压、浪拜迪等……医疗器械类:迈瑞医疗、安科高技术、和佳医疗、宝莱特医用科技、金科威电子、三瑞医疗、广州白云蓝天科技、理邦精密、邦健电子、万东医疗、泰杰磁电研究所等……医药化工类:太太药业、先声药业、康缘药业、浙江现代中药与天然药研究所、石药集团、汇仁集团、华南药业、双鹤药业、威高集团、烟台万华、乐凯集团等……航空航天及军工企业:……(行业特殊要求,客户名单保密)Ctrl+鼠标左键【点击访问诺达名师官方网站】出师表两汉:诸葛亮精品文档你我共享先帝创业未半而中道崩殂,今天下三分,益州疲弊,此诚危急存亡之秋也。