产品中试管理-从样品到量产PPT教学课件
产品中试管理

精品培训课程课程名称RDM012产品中试管理--从样品到量产Product Piloting-from sample to mass production参加对象企业CEO/总经理、研发总经理/副总、测试部经理、中试/试产部经理、制造部经理、工艺/工程部经理、质量部经理、项目经理/产品经理、高级制造工程师等课程背景我们在为企业提供研发管理咨询服务的过程中发现,很多企业的新产品开发从样机到量产的过程中(产品化过程)存在着共同的问题:1. 新品没有经过中试或中试的时间很短,制造部门戏称研发的新品是“三无”产品,没有生产文件、没有工装、生产现场出了问题没人管;2. 转产没有标准,研发想快点转产,生产对有问题的产品又不愿接收,希望研发把问题都解决了才转过来,而市场又催得急,经常被迫接收,长此以往,导致研发与生产的矛盾激化;3. 有些企业开始成立中试部门,希望在中试阶段把产品质量问题解决掉,但中试的定位与运作也很困惑,发生质量与进度的冲突时,如何取舍与平衡,以前研发与制造的矛盾转化为研发与中试、中试与生产的矛盾,中试成了矛盾集散中心;4. 市场的压力并不因中试的产生而减少,中试需要从哪些方面努力才能满足产品的质量、进度的要求?中试的业务是面向研发还是面向制造,还是兼而有之?5. 量产后才发现产品可制造性差、成品率低、经常返工,影响发货;6. 产品到了生产后还发生大量的设计变更;7. 产品到了客户手中还冒出各种各样的问题以致要研发人员到处去“救火”。
本课程将基于多年的实践、长期的研发咨询积累,总结出一套理论与实践相结合的可操作的方法,配以大量实际案例,以指导研发/试产/制造部门主管如何高效的实现产品从样品走向量产。
培训收益1. 了解业界公司在不同发展阶段的产品中试管理模式与实践2. 掌握面向制造系统的产品设计(DFM)的方法与实施过程3. 掌握面向生产测试的产品设计(DFT)的方法与实施过程4. 掌握面向制造系统的新产品验证的过程与方法5. 掌握在满足质量标准的前提下缩短产品试制周期的方法和技巧6. 了解如何建立从样品到量产的管理机制培训课时2天(12小时)课程大纲一、案例研讨二、从样品到量产概述1. 企业在追求什么:技术?样品?产品?商品?2. 研发与制造的矛盾:1). 制造系统如何面对研发的三无产品?2). 研发如何面对制造系统越来越高的门槛?3. 研发与制造矛盾的激化:中试的产生成为必然4. 中试的定位与发展:1). 研发(RD)、中试(D&P)、生产(P)的关系2). 中试的使命是什么?3). 中试如何定位?4). 中试的发展问题:●大而全?●专业化分工?●产品线划分与共享平台●中试人员的发展定位:广度与深度问题5. 中试的业务范围1). 中试业务:新产品导入(NPI)2). 承上:如何面向产品的研发?3). 启下:如何面向产品的制造?4). 桥梁:中试作为连接研发与制造的桥梁,独木桥还是阳关道?6. 演练与问题讨论1). 根据企业的实际情况,是否需要建立并发展中试的职能?三、新产品导入团队1. 新产品导入团队的构成1). 工艺工程2). 设备工程3). 测试工程4). 工业工程5). 产品验证6). 试生产(计划、生产、质量)2. 新产品导入团队的职责3. 新产品导入团队与产品开发团队的关系1). 开发模式的演变:串行变并行2). 并行工程在产品开发中如何体现?3). 新产品导入团队如何提前介入研发?●为什么要提前介入?●提前到什么时候介入?●提前介入做什么?4). 新产品导入团队的管理●新产品导入团队与产品开发团队、职能部门的沟通●新产品导入团队成员的汇报、考核和管理机制4. 演练与问题讨论1). 根据企业的实际情况,研讨建立新产品导入团队的时机四、面向制造系统的产品设计(DFM)1. 如何在产品设计与开发过程中进行可制造性设计1). 从制造的角度来看产品设计2). 工艺人员介入产品开发过程的切入点:从立项就开始3). 工艺管理的三个阶段:工艺设计、工艺调制与验证、工艺管制4). 工艺设计:●如何提出可制造性需求?●需要哪些典型的工艺规范?●可制造性需求如何落实到产品设计方案中?●工艺设计与产品设计如何并行?●产品工艺流程设计●电装、整装、包装与物流的可制造性设计分析●如何确保可制造性需求在产品开发中已被实现?●工艺评审如何操作?●什么时候考虑工装?●如何在开发过程中同步输出工艺文件与生产操作指导文件5). 工艺调制与验证●工艺验证的时机●工艺验证方案包括哪些内容?●如何实施工艺验证?●工艺验证报告的内容●如何推动工艺验证的问题解决?●研发人员如何配合新产品的工艺验证?●制造外包模式下的工艺如何验证?6). 工艺管制●工艺管制的困惑:救火何时是尽头?●工艺转产评审(标准、流程、责任)●量产过程中的例行监控与异常管理2. 演练与问题讨论1). 分析学员企业的工艺管理工作做到什么程度?存在哪些差距?3. 工艺管理平台建设1). 谁负责工艺平台的建设?2). 工艺委员会的产生:责任与运作模式3). 如何进行工艺规划?4). 基础工艺研究与应用5). 支撑工艺管理平台的四大规范:●品质规范●设备规范●工艺规范。
从样品到量产(学员版)教学教材

创新驱动发展
鼓励创新思维,通过研发和技 术创新,不断推出具有差异化 竞争优势的新产品。
04
生产计划与调度
生产计划制定
01
02
03
确定生产目标
根据市场需求、订单和产 品特点,制定合理的生产 目标,包括产量、质量和 交货期等。
目的与意义
目的
通过本教材的学习,学员将掌握 从样品到量产的整个流程、关键 技术和注意事项,为未来的产品 开发工作打下坚实的基础。
意义
本教材旨在提高学员对从样品到 量产阶段的重视,培养学员在实 际工作中解决相关问题的能力, 为企业创造更大的价值。
02
从样品到量产的流程
样品阶段
样品制作
根据设计图纸或技术要求,制作出符合规格的样品 。
在生产过程中,定期进行质量检 查,及时发现并处理问题,防止 不合格品的产生。
80%
建立质量追溯体系
建立完善的质量追溯体系,对每 个批次的产品进行质量追溯,以 便快速定位问题并采取措施。
产品优化与改进
收集用户反馈
通过市场调查、客户反馈等方 式,收集用户对产品的意见和 建议,为产品优化提供依据。
进行持续改进
根据实际生产进度,适时 调整生产计划,确保按时 完成生产任务,避免 及时发现和解决生产过程 中的问题,确保生产顺利 进行。
生产进度监控
收集生产数据
通过各种手段收集生产过程中的 数据,包括产量、质量、设备运
行状况等。
分析生产数据
对收集到的生产数据进行整理和分 析,找出问题点和改进点。
样品测试
对样品进行性能、可靠性等方面的测试,确保满足 设计要求。
产品中试管理-从样品到量产

产品中试管理-从样品到量产主讲:Charles(研发管理咨询资深顾问、国家发改委创新管理培训中心特邀讲师、清华大学国际工程项目管理研究院特邀讲师)课程对象:企业CEO/总经理、研发总经理/副总、测试部经理、中试/试产部经理、制造部经理、工艺/工程部经理、质量部经理、项目经理/产品经理、高级制造工程师等授课方式:讲师讲授 + 视频演绎 + 案例研讨 +角色扮演 + 讲师点评【课程背景】我们在为企业提供研发管理咨询服务的过程中发现,很多企业的新产品开发从样机到量产的过程中(产品化过程)存在着共同的问题:1、新品没有经过中试或中试的时间很短,制造部门戏称研发的新品是“三无”产品,没有生产文件、没有工装、生产现场出了问题没人管;2、转产没有标准,研发想快点转产,生产对有问题的产品又不愿接收,希望研发把问题都解决了才转过来,而市场又催得急,经常被迫接收,长此以往,导致研发与生产的矛盾激化;3、有些企业开始成立中试部门,希望在中试阶段把产品质量问题解决掉,但中试的定位与运作也很困惑,发生质量与进度的冲突时,如何取舍与平衡,以前研发与制造的矛盾转化为研发与中试、中试与生产的矛盾,中试成了矛盾集散中心;4、市场的压力并不因中试的产生而减少,中试需要从哪些方面努力才能满足产品的质量、进度的要求?中试的业务是面向研发还是面向制造,还是兼而有之?5、量产后才发现产品可制造性差、成品率低、经常返工,影响发货;6、产品到了生产后还发生大量的设计变更;7、产品到了客户手中还冒出各种各样的问题以致要研发人员到处去“救火”。
本课程将基于多年的实践、长期的研发咨询积累,总结出一套理论与实践相结合的可操作的方法,配以大量实际案例,以指导研发/试产/制造部门主管如何高效的实现产品从样品走向量产。
【课程价值】1.了解业界公司在不同发展阶段的产品中试管理模式与实践2.掌握面向制造系统的产品设计(DFM)的方法与实施过程3.掌握面向生产测试的产品设计(DFT)的方法与实施过程4.掌握面向制造系统的新产品验证的过程与方法5.掌握在满足质量标准的前提下缩短产品试制周期的方法和技巧6.了解如何建立从样品到量产的管理机制【培训内容】一、案例研讨二、从样品到量产概述1、企业在追求什么:技术?样品?产品?商品?2、研发与制造的矛盾:1)制造系统如何面对研发的三无产品?2)研发如何面对制造系统越来越高的门槛?3、研发与制造矛盾的激化:中试的产生成为必然4、中试的定位与发展:1)研发(RD)、中试(D&P)、生产(P)的关系2)中试的使命是什么?3)中试如何定位?4)中试的发展问题:大而全?专业化分工?产品线划分与共享平台中试人员的发展定位:广度与深度问题5、中试的业务范围1)中试业务:新产品导入(NPI)2)承上:如何面向产品的研发?3)启下:如何面向产品的制造?4)桥梁:中试作为连接研发与制造的桥梁,独木桥还是阳关道?6、演练与问题讨论1)根据企业的实际情况,是否需要建立并发展中试的职能?三、新产品导入团队1、新产品导入团队的构成1)工艺工程2)设备工程3)测试工程4)工业工程5)产品验证6)试生产(计划、生产、质量)2、新产品导入团队的职责3、新产品导入团队与产品开发团队的关系1)开发模式的演变:串行变并行2)并行工程在产品开发中如何体现?3)新产品导入团队如何提前介入研发?为什么要提前介入?提前到什么时候介入?提前介入做什么?4)新产品导入团队的管理新产品导入团队与产品开发团队、职能部门的沟通新产品导入团队成员的汇报、考核和管理机制4、演练与问题讨论1)根据企业的实际情况,研讨建立新产品导入团队的时机四、面向制造系统的产品设计(DFM)1、如何在产品设计与开发过程中进行可制造性设计1)从制造的角度来看产品设计2)工艺人员介入产品开发过程的切入点:从立项就开始3)工艺管理的三个阶段:工艺设计、工艺调制与验证、工艺管制4)工艺设计:如何提出可制造性需求?需要哪些典型的工艺规范?可制造性需求如何落实到产品设计方案中?工艺设计与产品设计如何并行?产品工艺流程设计电装、整装、包装与物流的可制造性设计分析如何确保可制造性需求在产品开发中已被实现?工艺评审如何操作?什么时候考虑工装?如何在开发过程中同步输出工艺文件与生产操作指导文件5)工艺调制与验证工艺验证的时机工艺验证方案包括哪些内容?如何实施工艺验证?工艺验证报告的内容如何推动工艺验证的问题解决?研发人员如何配合新产品的工艺验证?制造外包模式下的工艺如何验证?6)工艺管制工艺管制的困惑:救火何时是尽头?工艺转产评审(标准、流程、责任)量产过程中的例行监控与异常管理2、演练与问题讨论1)分析学员企业的工艺管理工作做到什么程度?存在哪些差距?3、工艺管理平台建设1)谁负责工艺平台的建设?2)工艺委员会的产生:责任与运作模式3)如何进行工艺规划?4)基础工艺研究与应用5)支撑工艺管理平台的四大规范:品质规范设备规范工艺规范设计规划6)工艺管理部门如何推动DFM业务的开展?7)工艺体系的组织构成、发展与演变8)工艺人员的培养与技能提升4、演练与问题讨论1)分析学员企业的工艺平台建设工作做到什么程度?存在哪些差距?如何改进?五、面向生产测试的产品设计(DFT)1、基于产品生命周期全流程的测试策略1)研发测试(Alpha)、试验局测试(Beta)、生产测试2.研发测试(Alpha)与BETA测试1)测试人员介入产品开发过程的时机(提可测试性需求的时机)2)可测试性需求需要考虑的内容(示例)3)单元测试、模块测试、系统集成测试、专业化测试、BETA测试的重点分析4)产品开发过程中测试业务流程分析5)企业在不同的发展阶段如何开展测试的相关工作(短平快的项目测试工作如何开展)3、面向生产测试业务的产品设计与开发1)生产测试业务流程分析2)典型的部品测试、整机测试方法介绍3)开发专门的生产测试工装的条件分析4)生产测试工装的开发管理5)在产品开发过程中如何实施面向生产测试的产品设计?如何提出可测试性需求?可测试性需求如何落实到产品设计方案中?研发面对众多的需求如何取舍?可测试性需求的优先级分析如何在产品开发过程中同步开发生产测试工装?如何在产品开发过程中同步输出生产测试所需的操作指导文件?如何进行测试工装的验证?如何推动测试验证问题的解决?6)如何推动可测试性设计(DFT)业务的开展7)如何进行测试平台的建设?4、演练与问题讨论1)分析学员企业的DFT工作做到什么程度?存在哪些差距?如何改进?六、产品试制验证管理1、影响产品试制周期的因素分析2、研发人员对试制准备提供的支持3、试制团队的构成、职责与定位(设置试制部门的时机与优缺点分析)4、试制人员介入产品开发过程的时机1)如何进行试制准备(准备要素示例)5、面向制造系统的验证1)研发人员如何在试制过程中进行产品设计的优化2)制造系统的验证策略与计划3)制造系统的验证方案4)如何实施制造系统的验证:工艺验证(工艺流程、工艺路线、单板工艺、整机工艺、包装工艺、物流工艺)工装验证(装配工装、测试工装、生产设备)结构验证产品数据验证(BOM验证、制造文档验证)产品试制验证(质量、效率、成本)5)批次验证报告,验证多少批才合适?6)如何推动验证问题的解决?6、转产评审1)研发人员如何支持新产品的转产工作2)转产评审的评审组织如何构成?3)评审标准是什么?4)如何判定是否转产?5)评审流程与运作机制7、产品转产后的管理1)新产品的试制效果评价2)新产品的质量目标达成情况3)工程变更管理4)缺陷与问题管理5)质量审计8、演练与问题讨论1)分析学员企业的产品试制验证过程,分析差距,提出改进建议。
产品中试管理-从样品到量产
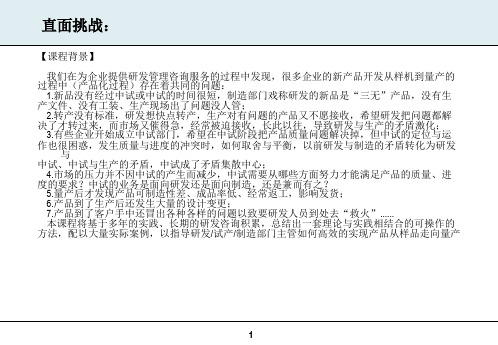
d 产品数据验证(BOM验证、制造文档验证) e 产品试制验证(质量、效率、成本) 5).批次验证报告,验证多少批才合适? 6).如何推动验证问题的解决?
6.转产评审 1).研发人员如何支持新产品的转产工作 2).转产评审的评审组织如何构成? 3).评审标准是什么? 4).如何判定是否转产? 5).评审流程与运作机制 7.产品转产后的管理 1).新产品的试制效果评价 2).新产品的质量目标达成情况 3).工程变更管理 4).缺陷与问题管理 5).质量审计 8.演练与问题讨论 1).分析学员企业的产品试制验证过程,分析差距,提出改进建议。
直面挑战:
【课程背景】 我们在为企业提供研发管理咨询服务的过程中发现,很多企业的新产品开发从样机到量产的
过程中(产品化过程)存在着共同的问题: 1.新品没有经过中试或中试的时间很短,制造部门戏称研发的新品是“三无”产品,没有生
产文件、没有工装、生产现场出了问题没人管; 2.转产没有标准,研发想快点转产,生产对有问题的产品又不愿接收,希望研发把问题都解
4.演练与问题讨论 1).分析学员企业的DFT工作做到什么程度?存在哪些差距?如何改进? 六、产品试制验证管理 1.影响产品试制周期的因素分析 2.研发人员对试制准备提供的支持 3.试制团队的构成、职责与定位(设置试制部门的时机与优缺点分析) 4.试制人员介入产品开发过程的时机 1).如何进行试制准备(准备要素示例) 5.面向制造系统的验证 1).研发人员如何在试制过程中进行产品设计的优化 2).制造系统的验证策略与计划 3).制造系统的验证方案 4).如何实施制造系统的验证: a 工艺验证(工艺流程、工艺路线、单板工艺、整机工艺、包装工艺、物流工艺) b 工装验证(装配工装、测试工装、生产设备) c 结构验证
产品中试管理--从样品到量产
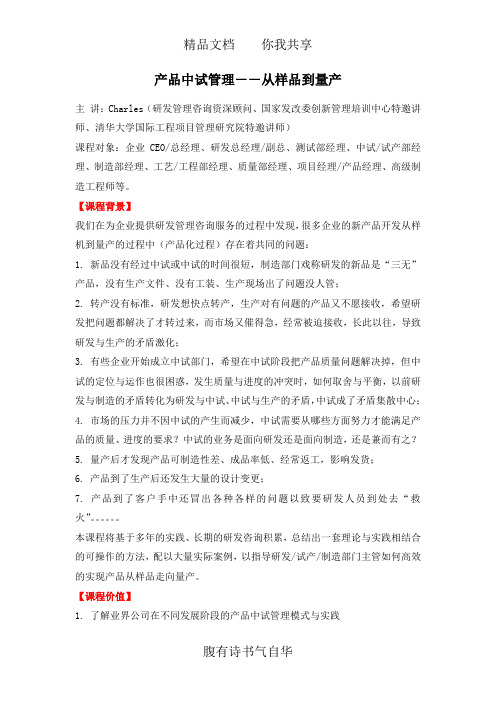
产品中试管理--从样品到量产主讲:Charles(研发管理咨询资深顾问、国家发改委创新管理培训中心特邀讲师、清华大学国际工程项目管理研究院特邀讲师)课程对象:企业CEO/总经理、研发总经理/副总、测试部经理、中试/试产部经理、制造部经理、工艺/工程部经理、质量部经理、项目经理/产品经理、高级制造工程师等。
【课程背景】我们在为企业提供研发管理咨询服务的过程中发现,很多企业的新产品开发从样机到量产的过程中(产品化过程)存在着共同的问题:1. 新品没有经过中试或中试的时间很短,制造部门戏称研发的新品是“三无”产品,没有生产文件、没有工装、生产现场出了问题没人管;2. 转产没有标准,研发想快点转产,生产对有问题的产品又不愿接收,希望研发把问题都解决了才转过来,而市场又催得急,经常被迫接收,长此以往,导致研发与生产的矛盾激化;3. 有些企业开始成立中试部门,希望在中试阶段把产品质量问题解决掉,但中试的定位与运作也很困惑,发生质量与进度的冲突时,如何取舍与平衡,以前研发与制造的矛盾转化为研发与中试、中试与生产的矛盾,中试成了矛盾集散中心;4. 市场的压力并不因中试的产生而减少,中试需要从哪些方面努力才能满足产品的质量、进度的要求?中试的业务是面向研发还是面向制造,还是兼而有之?5. 量产后才发现产品可制造性差、成品率低、经常返工,影响发货;6. 产品到了生产后还发生大量的设计变更;7. 产品到了客户手中还冒出各种各样的问题以致要研发人员到处去“救火”。
本课程将基于多年的实践、长期的研发咨询积累,总结出一套理论与实践相结合的可操作的方法,配以大量实际案例,以指导研发/试产/制造部门主管如何高效的实现产品从样品走向量产。
【课程价值】1. 了解业界公司在不同发展阶段的产品中试管理模式与实践2. 掌握面向制造系统的产品设计(DFM)的方法与实施过程3. 掌握面向生产测试的产品设计(DFT)的方法与实施过程4. 掌握面向制造系统的新产品验证的过程与方法5. 掌握在满足质量标准的前提下缩短产品试制周期的方法和技巧6. 了解如何建立从样品到量产的管理机制【培训内容】一、案例研讨二、从样品到量产概述1.企业在追求什么:技术?样品?产品?商品?2.研发与制造的矛盾:1).制造系统如何面对研发的三无产品?2).研发如何面对制造系统越来越高的门槛?3.研发与制造矛盾的激化:中试的产生成为必然4.中试的定位与发展:1).研发(RD)、中试(D&P)、生产(P)的关系2).中试的使命是什么?3).中试如何定位?4).中试的发展问题:5.中试的业务范围1).中试业务:新产品导入(NPI)2).承上:如何面向产品的研发?3).启下:如何面向产品的制造?4).桥梁:中试作为连接研发与制造的桥梁,独木桥还是阳关道?6.演练与问题讨论1).根据企业的实际情况,是否需要建立并发展中试的职能?三、新产品导入团队1.新产品导入团队的构成1).工艺工程2).设备工程3).测试工程4).工业工程5).产品验证6).试生产(计划、生产、质量)2.新产品导入团队的职责3.新产品导入团队与产品开发团队的关系1).开发模式的演变:串行变并行2).并行工程在产品开发中如何体现?3).新产品导入团队如何提前介入研发?4).新产品导入团队的管理、考核和管理机制4.演练与问题讨论1).根据企业的实际情况,研讨建立新产品导入团队的时机四、面向制造系统的产品设计(DFM)1.如何在产品设计与开发过程中进行可制造性设计1).从制造的角度来看产品设计2).工艺人员介入产品开发过程的切入点:从立项就开始3).工艺管理的三个阶段:工艺设计、工艺调制与验证、工艺管制4).工艺设计:与物流的可制造性设计分析5).工艺调制与验证6).工艺管制2.演练与问题讨论1).分析学员企业的工艺管理工作做到什么程度?存在哪些差距?3.工艺管理平台建设1).谁负责工艺平台的建设?2).工艺委员会的产生:责任与运作模式3).如何进行工艺规划?4).基础工艺研究与应用5).支撑工艺管理平台的四大规范:6).工艺管理部门如何推动DFM业务的开展?7).工艺体系的组织构成、发展与演变8).工艺人员的培养与技能提升4.演练与问题讨论1).分析学员企业的工艺平台建设工作做到什么程度?存在哪些差距?如何改进?五、面向生产测试的产品设计(DFT)1.基于产品生命周期全流程的测试策略1).研发测试(Alpha)、试验局测试(Beta)、生产测试2.研发测试(Alpha)与BETA测试1).测试人员介入产品开发过程的时机(提可测试性需求的时机)2).可测试性需求需要考虑的内容(示例)3).单元测试、模块测试、系统集成测试、专业化测试、BETA测试的重点分析4).产品开发过程中测试业务流程分析5).企业在不同的发展阶段如何开展测试的相关工作(短平快的项目测试工作如何开展)3.面向生产测试业务的产品设计与开发1).生产测试业务流程分析2).典型的部品测试、整机测试方法介绍3).开发专门的生产测试工装的条件分析4).生产测试工装的开发管理5).在产品开发过程中如何实施面向生产测试的产品设计?6).如何推动可测试性设计(DFT)业务的开展7).如何进行测试平台的建设?4.演练与问题讨论1).分析学员企业的DFT工作做到什么程度?存在哪些差距?如何改进?六、产品试制验证管理1.影响产品试制周期的因素分析2.研发人员对试制准备提供的支持3.试制团队的构成、职责与定位(设置试制部门的时机与优缺点分析)4.试制人员介入产品开发过程的时机1).如何进行试制准备(准备要素示例)5.面向制造系统的验证1).研发人员如何在试制过程中进行产品设计的优化2).制造系统的验证策略与计划3).制造系统的验证方案4).如何实施制造系统的验证:BOM验证、制造文档验证)5).批次验证报告,验证多少批才合适?6).如何推动验证问题的解决?6.转产评审1).研发人员如何支持新产品的转产工作2).转产评审的评审组织如何构成?3).评审标准是什么?4).如何判定是否转产?5).评审流程与运作机制7.产品转产后的管理1).新产品的试制效果评价2).新产品的质量目标达成情况3).工程变更管理4).缺陷与问题管理5).质量审计8.演练与问题讨论1).分析学员企业的产品试制验证过程,分析差距,提出改进建议。
产品中试管理-从样品到量产

产品中试管理-从样品到量产主讲:Charles(研发管理咨询资深顾问、国家发改委创新管理培训中心特邀讲师、清华大学国际工程项目管理研究院特邀讲师)课程对象:企业CEO/总经理、研发总经理/副总、测试部经理、中试/试产部经理、制造部经理、工艺/工程部经理、质量部经理、项目经理/产品经理、高级制造工程师等授课方式:讲师讲授 + 视频演绎 + 案例研讨 +角色扮演 + 讲师点评【课程背景】我们在为企业提供研发管理咨询服务的过程中发现,很多企业的新产品开发从样机到量产的过程中(产品化过程)存在着共同的问题:1、新品没有经过中试或中试的时间很短,制造部门戏称研发的新品是“三无”产品,没有生产文件、没有工装、生产现场出了问题没人管;2、转产没有标准,研发想快点转产,生产对有问题的产品又不愿接收,希望研发把问题都解决了才转过来,而市场又催得急,经常被迫接收,长此以往,导致研发与生产的矛盾激化;3、有些企业开始成立中试部门,希望在中试阶段把产品质量问题解决掉,但中试的定位与运作也很困惑,发生质量与进度的冲突时,如何取舍与平衡,以前研发与制造的矛盾转化为研发与中试、中试与生产的矛盾,中试成了矛盾集散中心;4、市场的压力并不因中试的产生而减少,中试需要从哪些方面努力才能满足产品的质量、进度的要求?中试的业务是面向研发还是面向制造,还是兼而有之?5、量产后才发现产品可制造性差、成品率低、经常返工,影响发货;6、产品到了生产后还发生大量的设计变更;7、产品到了客户手中还冒出各种各样的问题以致要研发人员到处去“救火”。
本课程将基于多年的实践、长期的研发咨询积累,总结出一套理论与实践相结合的可操作的方法,配以大量实际案例,以指导研发/试产/制造部门主管如何高效的实现产品从样品走向量产。
【课程价值】1.了解业界公司在不同发展阶段的产品中试管理模式与实践2.掌握面向制造系统的产品设计(DFM)的方法与实施过程3.掌握面向生产测试的产品设计(DFT)的方法与实施过程4.掌握面向制造系统的新产品验证的过程与方法5.掌握在满足质量标准的前提下缩短产品试制周期的方法和技巧6.了解如何建立从样品到量产的管理机制【培训内容】一、案例研讨二、从样品到量产概述1、企业在追求什么:技术?样品?产品?商品?2、研发与制造的矛盾:1)制造系统如何面对研发的三无产品?2)研发如何面对制造系统越来越高的门槛?3、研发与制造矛盾的激化:中试的产生成为必然4、中试的定位与发展:1)研发(RD)、中试(D&P)、生产(P)的关系2)中试的使命是什么?3)中试如何定位?4)中试的发展问题:大而全?专业化分工?产品线划分与共享平台中试人员的发展定位:广度与深度问题5、中试的业务范围1)中试业务:新产品导入(NPI)2)承上:如何面向产品的研发?3)启下:如何面向产品的制造?4)桥梁:中试作为连接研发与制造的桥梁,独木桥还是阳关道?6、演练与问题讨论1)根据企业的实际情况,是否需要建立并发展中试的职能?三、新产品导入团队1、新产品导入团队的构成1)工艺工程2)设备工程3)测试工程4)工业工程5)产品验证6)试生产(计划、生产、质量)2、新产品导入团队的职责3、新产品导入团队与产品开发团队的关系1)开发模式的演变:串行变并行2)并行工程在产品开发中如何体现?3)新产品导入团队如何提前介入研发?为什么要提前介入?提前到什么时候介入?提前介入做什么?4)新产品导入团队的管理新产品导入团队与产品开发团队、职能部门的沟通新产品导入团队成员的汇报、考核和管理机制4、演练与问题讨论1)根据企业的实际情况,研讨建立新产品导入团队的时机四、面向制造系统的产品设计(DFM)1、如何在产品设计与开发过程中进行可制造性设计1)从制造的角度来看产品设计2)工艺人员介入产品开发过程的切入点:从立项就开始3)工艺管理的三个阶段:工艺设计、工艺调制与验证、工艺管制4)工艺设计:如何提出可制造性需求?需要哪些典型的工艺规范?可制造性需求如何落实到产品设计方案中?工艺设计与产品设计如何并行?产品工艺流程设计电装、整装、包装与物流的可制造性设计分析如何确保可制造性需求在产品开发中已被实现?工艺评审如何操作?什么时候考虑工装?如何在开发过程中同步输出工艺文件与生产操作指导文件5)工艺调制与验证工艺验证的时机工艺验证方案包括哪些内容?如何实施工艺验证?工艺验证报告的内容如何推动工艺验证的问题解决?研发人员如何配合新产品的工艺验证?制造外包模式下的工艺如何验证?6)工艺管制工艺管制的困惑:救火何时是尽头?工艺转产评审(标准、流程、责任)量产过程中的例行监控与异常管理2、演练与问题讨论1)分析学员企业的工艺管理工作做到什么程度?存在哪些差距?3、工艺管理平台建设1)谁负责工艺平台的建设?2)工艺委员会的产生:责任与运作模式3)如何进行工艺规划?4)基础工艺研究与应用5)支撑工艺管理平台的四大规范:品质规范设备规范工艺规范设计规划6)工艺管理部门如何推动DFM业务的开展?7)工艺体系的组织构成、发展与演变8)工艺人员的培养与技能提升4、演练与问题讨论1)分析学员企业的工艺平台建设工作做到什么程度?存在哪些差距?如何改进?五、面向生产测试的产品设计(DFT)1、基于产品生命周期全流程的测试策略1)研发测试(Alpha)、试验局测试(Beta)、生产测试2.研发测试(Alpha)与BETA测试1)测试人员介入产品开发过程的时机(提可测试性需求的时机)2)可测试性需求需要考虑的内容(示例)3)单元测试、模块测试、系统集成测试、专业化测试、BETA测试的重点分析4)产品开发过程中测试业务流程分析5)企业在不同的发展阶段如何开展测试的相关工作(短平快的项目测试工作如何开展)3、面向生产测试业务的产品设计与开发1)生产测试业务流程分析2)典型的部品测试、整机测试方法介绍3)开发专门的生产测试工装的条件分析4)生产测试工装的开发管理5)在产品开发过程中如何实施面向生产测试的产品设计?如何提出可测试性需求?可测试性需求如何落实到产品设计方案中?研发面对众多的需求如何取舍?可测试性需求的优先级分析如何在产品开发过程中同步开发生产测试工装?如何在产品开发过程中同步输出生产测试所需的操作指导文件?如何进行测试工装的验证?如何推动测试验证问题的解决?6)如何推动可测试性设计(DFT)业务的开展7)如何进行测试平台的建设?4、演练与问题讨论1)分析学员企业的DFT工作做到什么程度?存在哪些差距?如何改进?六、产品试制验证管理1、影响产品试制周期的因素分析2、研发人员对试制准备提供的支持3、试制团队的构成、职责与定位(设置试制部门的时机与优缺点分析)4、试制人员介入产品开发过程的时机1)如何进行试制准备(准备要素示例)5、面向制造系统的验证1)研发人员如何在试制过程中进行产品设计的优化2)制造系统的验证策略与计划3)制造系统的验证方案4)如何实施制造系统的验证:工艺验证(工艺流程、工艺路线、单板工艺、整机工艺、包装工艺、物流工艺)工装验证(装配工装、测试工装、生产设备)结构验证产品数据验证(BOM验证、制造文档验证)产品试制验证(质量、效率、成本)5)批次验证报告,验证多少批才合适?6)如何推动验证问题的解决?6、转产评审1)研发人员如何支持新产品的转产工作2)转产评审的评审组织如何构成?3)评审标准是什么?4)如何判定是否转产?5)评审流程与运作机制7、产品转产后的管理1)新产品的试制效果评价2)新产品的质量目标达成情况3)工程变更管理4)缺陷与问题管理5)质量审计8、演练与问题讨论1)分析学员企业的产品试制验证过程,分析差距,提出改进建议。
从样品到量产产品中试管理
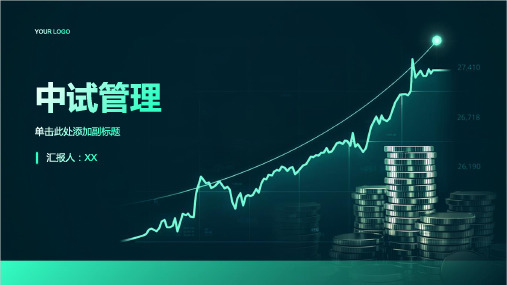
中试管理的新理念和新模式
智能化中试管理:利用大数据、人工智能等技术提升中试效率和质量
敏捷中试管理:快速响应市场需求,实现产品快速迭代和优化
开放式中试管理:加强与外部合作伙伴的协作,共同推进产品研发和 创新 定制化中试管理:满足个性化需求,提高产品的针对性和市场竞争 力
中试管理与数字化技术的结合
中批量阶段
定义:中批量阶段是指产品从样品验证阶段过渡到规模化生产阶段的过程。
目的:验证产品的可重复性和可扩展性,确保规模化生产时产品的稳定性和可靠性。
关键要素:生产工艺、设备、检测方法等需要经过验证和确认,确保符合规模化生产的要求。
意义:中批量阶段是产品从研发走向市场的关键环节,对于产品的成功上市和商业化具有重要意 义。
单击添加标题
中试管理流程
中试管理与企业 发展的关系
中试管理概述
中试管理中的关 键要素
中试管理的未来 发展
中试管理的定义和重要性
中试管理是指在产品正式投产前的试验阶段所进行的管理,旨在确保 产品的可生产性和工艺的可行性。
中试管理对于企业来说至关重要,它能够降低产品上市的风险,提 高生产效率,确保产品质量,并缩短产品上市时间。
中试管理是产品 创新的重要环节, 为产品创新提供 支持和保障。
中试管理通过试 验和验证,确保 产品创新的可行 性和可靠性,降 低创新风险。
中试管理过程中, 可以发现和解决 产品创新中的问 题和瓶颈,提升 产品创新的效率 和成功率。
中试管理能够促 进跨部门协作和 资源整合,推动 产品创新的全面 实现和市场应用。
经济性分析是指在满足产品性能和安全要求的前提下,通过优化设计、降低成本、提高生产效率 等手段,实现经济效益的最大化。
中试管理中的经济性分析需要考虑产品的全生命周期成本,包括研发、生产、销售、维护等方面 的成本。
★产品中试管理-从样品到量产
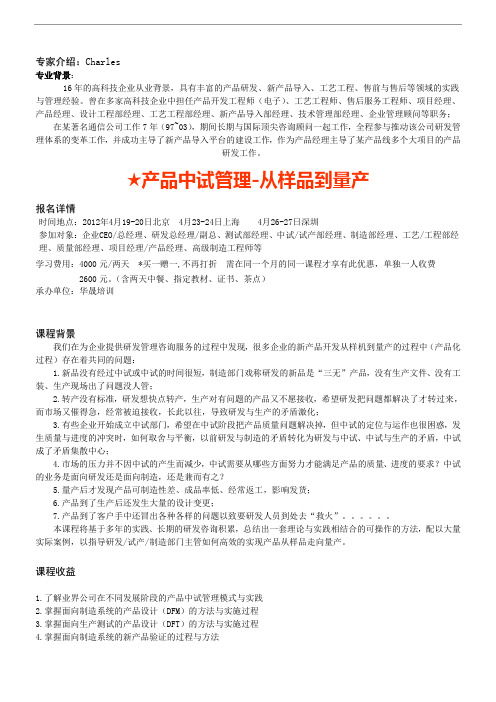
专家介绍:Charles专业背景:16年的高科技企业从业背景,具有丰富的产品研发、新产品导入、工艺工程、售前与售后等领域的实践与管理经验。
曾在多家高科技企业中担任产品开发工程师(电子)、工艺工程师、售后服务工程师、项目经理、产品经理、设计工程部经理、工艺工程部经理、新产品导入部经理、技术管理部经理、企业管理顾问等职务;在某著名通信公司工作7年(97~03),期间长期与国际顶尖咨询顾问一起工作,全程参与推动该公司研发管理体系的变革工作,并成功主导了新产品导入平台的建设工作,作为产品经理主导了某产品线多个大项目的产品研发工作。
★产品中试管理-从样品到量产报名详情时间地点:2012年4月19-20日北京 4月23-24日上海 4月26-27日深圳参加对象:企业CEO/总经理、研发总经理/副总、测试部经理、中试/试产部经理、制造部经理、工艺/工程部经理、质量部经理、项目经理/产品经理、高级制造工程师等学习费用:4000元/两天 *买一赠一,不再打折需在同一个月的同一课程才享有此优惠,单独一人收费2600元。
(含两天中餐、指定教材、证书、茶点)承办单位:华晟培训课程背景我们在为企业提供研发管理咨询服务的过程中发现,很多企业的新产品开发从样机到量产的过程中(产品化过程)存在着共同的问题:1.新品没有经过中试或中试的时间很短,制造部门戏称研发的新品是“三无”产品,没有生产文件、没有工装、生产现场出了问题没人管;2.转产没有标准,研发想快点转产,生产对有问题的产品又不愿接收,希望研发把问题都解决了才转过来,而市场又催得急,经常被迫接收,长此以往,导致研发与生产的矛盾激化;3.有些企业开始成立中试部门,希望在中试阶段把产品质量问题解决掉,但中试的定位与运作也很困惑,发生质量与进度的冲突时,如何取舍与平衡,以前研发与制造的矛盾转化为研发与中试、中试与生产的矛盾,中试成了矛盾集散中心;4.市场的压力并不因中试的产生而减少,中试需要从哪些方面努力才能满足产品的质量、进度的要求?中试的业务是面向研发还是面向制造,还是兼而有之?5.量产后才发现产品可制造性差、成品率低、经常返工,影响发货;6.产品到了生产后还发生大量的设计变更;7.产品到了客户手中还冒出各种各样的问题以致要研发人员到处去“救火”。
产品中试管理——从样品到量产-最新

产品中试管理——从样品到量产2012年4月19-20日北京 | 2012年4月23-24日上海 | 2012年4月26-27日深圳我们在为企业提供研发管理咨询服务的过程中发现,很多企业的新产品开发从样机到量产的过程中(产品化过程)存在着共同的问题:1、新品没有经过中试或中试的时间很短,制造部门戏称研发的新品是“三无”产品,没有生产文件、没有工装、生产现场出了问题没人管;2、转产没有标准,研发想快点转产,生产对有问题的产品又不愿接收,希望研发把问题都解决了才转过来,而市场又催得急,经常被迫接收,长此以往,导致研发与生产的矛盾激化;3、有些企业开始成立中试部门,希望在中试阶段把产品质量问题解决掉,但中试的定位与运作也很困惑,发生质量与进度的冲突时,如何取舍与平衡,以前研发与制造的矛盾转化为研发与中试、中试与生产的矛盾,中试成了矛盾集散中心;4、市场的压力并不因中试的产生而减少,中试需要从哪些方面努力才能满足产品的质量、进度的要求?中试的业务是面向研发还是面向制造,还是兼而有之?5、量产后才发现产品可制造性差、成品率低、经常返工,影响发货;6、产品到了生产后还发生大量的设计变更;7、产品到了客户手中还冒出各种各样的问题以致要研发人员到处去“救火”。
本课程将基于多年的实践、长期的研发咨询积累,总结出一套理论与实践相结合的可操作的方法,配以大量实际案例,以指导研发/试产/制造部门主管如何高效的实现产品从样品走向量产。
培训方式:案例分享、实务分析、互动讨论、项目模拟、培训游戏培训收益1、了解业界公司在不同发展阶段的产品中试管理模式与实践2、掌握面向制造系统的产品设计(DFM)的方法与实施过程3、掌握面向生产测试的产品设计(DFT)的方法与实施过程4、掌握面向制造系统的新产品验证的过程与方法5、掌握在满足质量标准的前提下缩短产品试制周期的方法和技巧6、了解如何建立从样品到量产的管理机制课程内容一、案例研讨二、从样品到量产概述1、企业在追求什么:技术?样品?产品?商品?2、研发与制造的矛盾:1)制造系统如何面对研发的三无产品?2)研发如何面对制造系统越来越高的门槛?3、研发与制造矛盾的激化:中试的产生成为必然4、中试的定位与发展:1)研发(RD)中试(D&P)生产(P)的关系2)中试的使命是什么?3)中试如何定位?4)中试的发展问题:◇大而全?◇专业化分工?◇产品线划分与共享平台◇中试人员的发展定位:广度与深度问题5、中试的业务范围1)中试业务:新产品导入(NPI)2)承上:如何面向产品的研发?3)启下:如何面向产品的制造?4)桥梁:中试作为连接研发与制造的桥梁,独木桥还是阳关道?6、演练与问题讨论1)根据企业的实际情况,是否需要建立并发展中试的职能?三、新产品导入团队1、新产品导入团队的构成1)工艺工程2)设备工程3)测试工程4)工业工程5)产品验证6)试生产(计划、生产、质量)2、新产品导入团队的职责3、新产品导入团队与产品开发团队的关系1)开发模式的演变:串行变并行2)并行工程在产品开发中如何体现?3)新产品导入团队如何提前介入研发?◇为什么要提前介入?◇提前到什么时候介入?◇提前介入做什么?4)新产品导入团队的管理◇新产品导入团队与产品开发团队、职能部门的沟通◇新产品导入团队成员的汇报、考核和管理机制4、演练与问题讨论1)根据企业的实际情况,研讨建立新产品导入团队的时机四、面向制造系统的产品设计(DFM)1、如何在产品设计与开发过程中进行可制造性设计1)从制造的角度来看产品设计2)工艺人员介入产品开发过程的切入点:从立项就开始3)工艺管理的三个阶段:工艺设计、工艺调制与验证、工艺管制4)工艺设计:◇如何提出可制造性需求?◇需要哪些典型的工艺规范?◇可制造性需求如何落实到产品设计方案中?◇工艺设计与产品设计如何并行?◇产品工艺流程设计◇电装、整装、包装与物流的可制造性设计分析◇如何确保可制造性需求在产品开发中已被实现?◇工艺评审如何操作?◇什么时候考虑工装?◇如何在开发过程中同步输出工艺文件与生产操作指导文件5)工艺调制与验证◇工艺验证的时机◇工艺验证方案包括哪些内容?◇如何实施工艺验证?◇工艺验证报告的内容◇如何推动工艺验证的问题解决?◇研发人员如何配合新产品的工艺验证?◇制造外包模式下的工艺如何验证?6)工艺管制◇工艺管制的困惑:救火何时是尽头?◇工艺转产评审(标准、流程、责任)◇量产过程中的例行监控与异常管理2、演练与问题讨论1)分析学员企业的工艺管理工作做到什么程度?存在哪些差距?3、工艺管理平台建设1)谁负责工艺平台的建设?2)工艺委员会的产生:责任与运作模式3)如何进行工艺规划?4)基础工艺研究与应用5)支撑工艺管理平台的四大规范:◇品质规范◇设备规范◇工艺规范◇设计规划6)工艺管理部门如何推动DFM业务的开展?7)工艺体系的组织构成、发展与演变8)工艺人员的培养与技能提升4、演练与问题讨论1)分析学员企业的工艺平台建设工作做到什么程度?存在哪些差距?如何改进?五、面向生产测试的产品设计(DFT)1、基于产品生命周期全流程的测试策略1)研发测试(Alpha)试验局测试(Beta)生产测试2、研发测试(Alpha)与BETA测试1)测试人员介入产品开发过程的时机(提可测试性需求的时机)2)可测试性需求需要考虑的内容(示例)3)单元测试、模块测试、系统集成测试、专业化测试、BETA测试的重点分析4)产品开发过程中测试业务流程分析5)企业在不同的发展阶段如何开展测试的相关工作(短平快的项目测试工作如何开展)3、面向生产测试业务的产品设计与开发1)生产测试业务流程分析2)典型的部品测试、整机测试方法介绍3)开发专门的生产测试工装的条件分析4)生产测试工装的开发管理5)在产品开发过程中如何实施面向生产测试的产品设计?◇如何提出可测试性需求?◇可测试性需求如何落实到产品设计方案中?◇研发面对众多的需求如何取舍?可测试性需求的优先级分析◇如何在产品开发过程中同步开发生产测试工装?◇如何在产品开发过程中同步输出生产测试所需的操作指导文件?◇如何进行测试工装的验证?◇如何推动测试验证问题的解决?6)如何推动可测试性设计(DFT)业务的开展7)如何进行测试平台的建设?4、演练与问题讨论1)分析学员企业的DFT工作做到什么程度?存在哪些差距?如何改进?六、产品试制验证管理1、影响产品试制周期的因素分析2、研发人员对试制准备提供的支持3、试制团队的构成、职责与定位(设置试制部门的时机与优缺点分析)4、试制人员介入产品开发过程的时机1)如何进行试制准备(准备要素示例)5、面向制造系统的验证1)研发人员如何在试制过程中进行产品设计的优化2)制造系统的验证策略与计划3)制造系统的验证方案4)如何实施制造系统的验证:◇工艺验证(工艺流程、工艺路线、单板工艺、整机工艺、包装工艺、物流工艺)◇工装验证(装配工装、测试工装、生产设备)◇结构验证◇产品数据验证(BOM验证、制造文档验证)◇产品试制验证(质量、效率、成本)5)批次验证报告,验证多少批才合适?6)如何推动验证问题的解决?6、转产评审1)研发人员如何支持新产品的转产工作2)转产评审的评审组织如何构成?3)评审标准是什么?4)如何判定是否转产?5)评审流程与运作机制7、产品转产后的管理1)新产品的试制效果评价2)新产品的质量目标达成情况3)工程变更管理4)缺陷与问题管理5)质量审计8、演练与问题讨论1)分析学员企业的产品试制验证过程,分析差距,提出改进建议。
产品中试管理从样品到量产

产品中试管理——从样品到量产●课程背景我们在为企业提供研发管理咨询服务的过程中发现,很多企业的新产品开发从样机到量产的过程中(产品化过程)存在着共同的问题:1、新品没有经过中试或中试的时间很短,制造部门戏称研发的新品是“三无”产品,没有生产文件、没有工装、生产现场出了问题没人管;2、转产没有标准,研发想快点转产,生产对有问题的产品又不愿接收,希望研发把问题都解决了才转过来,而市场又催得急,经常被迫接收,长此以往,导致研发与生产的矛盾激化;3、有些企业开始成立中试部门,希望在中试阶段把产品质量问题解决掉,但中试的定位与运作也很困惑,发生质量与进度的冲突时,如何取舍与平衡,以前研发与制造的矛盾转化为研发与中试、中试与生产的矛盾,中试成了矛盾集散中心;4、市场的压力并不因中试的产生而减少,中试需要从哪些方面努力才能满足产品的质量、进度的要求?中试的业务是面向研发还是面向制造,还是兼而有之?5、量产后才发现产品可制造性差、成品率低、经常返工,影响发货;6、产品到了生产后还发生大量的设计变更;7、产品到了客户手中还冒出各种各样的问题以致要研发人员到处去“救火”。
本课程将基于多年的实践、长期的研发咨询积累,总结出一套理论与实践相结合的可操作的方法,配以大量实际案例,以指导研发/试产/制造部门主管如何高效的实现产品从样品走向量产。
●培训方式:案例分享、实务分析、互动讨论、项目模拟、培训游戏●培训收益1、了解业界公司在不同发展阶段的产品中试管理模式与实践2、掌握面向制造系统的产品设计(DFM)的方法与实施过程3、掌握面向生产测试的产品设计(DFT)的方法与实施过程4、掌握面向制造系统的新产品验证的过程与方法5、掌握在满足质量标准的前提下缩短产品试制周期的方法和技巧6、了解如何建立从样品到量产的管理机制●课程内容一、案例研讨二、从样品到量产概述1、企业在追求什么:技术?样品?产品?商品?2、研发与制造的矛盾:1)制造系统如何面对研发的三无产品?2)研发如何面对制造系统越来越高的门槛?3、研发与制造矛盾的激化:中试的产生成为必然4、中试的定位与发展:1)研发(RD)中试(D&P)生产(P)的关系2)中试的使命是什么?3)中试如何定位?4)中试的发展问题:◇大而全?◇专业化分工?◇产品线划分与共享平台◇中试人员的发展定位:广度与深度问题5、中试的业务范围1)中试业务:新产品导入(NPI)2)承上:如何面向产品的研发?3)启下:如何面向产品的制造?4)桥梁:中试作为连接研发与制造的桥梁,独木桥还是阳关道?6、演练与问题讨论1)根据企业的实际情况,是否需要建立并发展中试的职能?三、新产品导入团队1、新产品导入团队的构成1)工艺工程2)设备工程3)测试工程4)工业工程5)产品验证6)试生产(计划、生产、质量)2、新产品导入团队的职责3、新产品导入团队与产品开发团队的关系1)开发模式的演变:串行变并行2)并行工程在产品开发中如何体现?3)新产品导入团队如何提前介入研发?◇为什么要提前介入?◇提前到什么时候介入?◇提前介入做什么?4)新产品导入团队的管理◇新产品导入团队与产品开发团队、职能部门的沟通◇新产品导入团队成员的汇报、考核和管理机制4、演练与问题讨论1)根据企业的实际情况,研讨建立新产品导入团队的时机四、面向制造系统的产品设计(DFM)1、如何在产品设计与开发过程中进行可制造性设计1)从制造的角度来看产品设计2)工艺人员介入产品开发过程的切入点:从立项就开始3)工艺管理的三个阶段:工艺设计、工艺调制与验证、工艺管制4)工艺设计:◇如何提出可制造性需求?◇需要哪些典型的工艺规范?◇可制造性需求如何落实到产品设计方案中?◇工艺设计与产品设计如何并行?◇产品工艺流程设计◇电装、整装、包装与物流的可制造性设计分析◇如何确保可制造性需求在产品开发中已被实现?◇工艺评审如何操作?◇什么时候考虑工装?◇如何在开发过程中同步输出工艺文件与生产操作指导文件5)工艺调制与验证◇工艺验证的时机◇工艺验证方案包括哪些内容?◇如何实施工艺验证?◇工艺验证报告的内容◇如何推动工艺验证的问题解决?◇研发人员如何配合新产品的工艺验证?◇制造外包模式下的工艺如何验证?6)工艺管制◇工艺管制的困惑:救火何时是尽头?◇工艺转产评审(标准、流程、责任)◇量产过程中的例行监控与异常管理2、演练与问题讨论1)分析学员企业的工艺管理工作做到什么程度?存在哪些差距?3、工艺管理平台建设1)谁负责工艺平台的建设?2)工艺委员会的产生:责任与运作模式3)如何进行工艺规划?4)基础工艺研究与应用5)支撑工艺管理平台的四大规范:◇品质规范◇设备规范◇工艺规范◇设计规划6)工艺管理部门如何推动DFM业务的开展?7)工艺体系的组织构成、发展与演变8)工艺人员的培养与技能提升4、演练与问题讨论1)分析学员企业的工艺平台建设工作做到什么程度?存在哪些差距?如何改进?五、面向生产测试的产品设计(DFT)1、基于产品生命周期全流程的测试策略1)研发测试(Alpha)试验局测试(Beta)生产测试2、研发测试(Alpha)与BETA测试1)测试人员介入产品开发过程的时机(提可测试性需求的时机)2)可测试性需求需要考虑的内容(示例)3)单元测试、模块测试、系统集成测试、专业化测试、BETA测试的重点分析4)产品开发过程中测试业务流程分析5)企业在不同的发展阶段如何开展测试的相关工作(短平快的项目测试工作如何开展)3、面向生产测试业务的产品设计与开发1)生产测试业务流程分析2)典型的部品测试、整机测试方法介绍3)开发专门的生产测试工装的条件分析4)生产测试工装的开发管理5)在产品开发过程中如何实施面向生产测试的产品设计?◇如何提出可测试性需求?◇可测试性需求如何落实到产品设计方案中?◇研发面对众多的需求如何取舍?可测试性需求的优先级分析◇如何在产品开发过程中同步开发生产测试工装?◇如何在产品开发过程中同步输出生产测试所需的操作指导文件?◇如何进行测试工装的验证?◇如何推动测试验证问题的解决?6)如何推动可测试性设计(DFT)业务的开展7)如何进行测试平台的建设?4、演练与问题讨论1)分析学员企业的DFT工作做到什么程度?存在哪些差距?如何改进?六、产品试制验证管理1、影响产品试制周期的因素分析2、研发人员对试制准备提供的支持3、试制团队的构成、职责与定位(设置试制部门的时机与优缺点分析)4、试制人员介入产品开发过程的时机1)如何进行试制准备(准备要素示例)5、面向制造系统的验证1)研发人员如何在试制过程中进行产品设计的优化2)制造系统的验证策略与计划3)制造系统的验证方案4)如何实施制造系统的验证:◇工艺验证(工艺流程、工艺路线、单板工艺、整机工艺、包装工艺、物流工艺)◇工装验证(装配工装、测试工装、生产设备)◇结构验证◇产品数据验证(BOM验证、制造文档验证)◇产品试制验证(质量、效率、成本)5)批次验证报告,验证多少批才合适?6)如何推动验证问题的解决?6、转产评审1)研发人员如何支持新产品的转产工作2)转产评审的评审组织如何构成?3)评审标准是什么?4)如何判定是否转产?5)评审流程与运作机制7、产品转产后的管理1)新产品的试制效果评价2)新产品的质量目标达成情况3)工程变更管理4)缺陷与问题管理5)质量审计8、演练与问题讨论1)分析学员企业的产品试制验证过程,分析差距,提出改进建议。
产品中试管理从样品到量产

■ 研发管理培训经验:
曾为中国空间技术研究院、南瑞科技、TCL集团、长虹集团、OPPO、同方威 视、宝钢集团、中国移动、大唐电信、上海电信、陕鼓集团、科达通信、中 电集团、威创科技、和记奥普泰、国人通信、京信科技、天碁科技、格林威 尔、兴大豪科技、星星集团、山特电子、富港电子、宇龙通信、聚光科技、 绿盟科技、天津内燃机研究所、中集集团、高斯贝尔、星网锐捷、特变电工、 思源电器、美的集团、海尔集团、海信集团、普天集团、福建敏讯、国光电 子、苏州金龙、宇通重工、雷沃重汽、上汽五凌、东风汽车、威科姆、同洲 电子、科立讯、新北洋、光迅科技、沈阳机床、瑞斯康达、佳讯飞鸿、浪潮 集团、威胜电子、京城控股、联想集团、迈瑞医疗、华大电子、上海华虹、 联芯科技、旋极科技、畅通科技、长城软件、九院、天地奔牛、阳天电子、 清华机械、方正集团、研祥智能、烟台万华、东方电子、东方通信、美菱、 科大讯飞、万峰石材、万家乐、泛仕达、远光软件、优特等近500家企业 提供了专业的研发管理培训。
3
三、新产品导入团队
1、新产品导入团队的构成 1)工艺工程 2)设备工程 3)测试工程 4)工业工程 5)产品验证 6)试生产(计划、生产、质量) 2、新产品导入团队的职责 3、新产品导入团队与产品开发团队的关系 1)开发模式的演变:串行变并行 2)并行工程在产品开发中如何体现? 3)新产品导入团队如何提前介入研发? ◇ 为什么要提前介入? ◇ 提前到什么时候介入? ◇ 提前介入做什么? 4)新产品导入团队的管理 ◇ 新产品导入团队与产品开发团队、职能部门的沟通 ◇ 新产品导入团队成员的汇报、考核和管理机制 4、演练与问题讨论 1)根据企业的实际情况,研讨建立新产品导入团队的时机
9
1
● 培训方式:案例分享、实务分析、互动讨论、项目模拟、培训游戏 ● 培训收益 1、了解业界公司在不同发展阶段的产品中试管理模式与实践 2、掌握面向制造系统的产品设计(DFM)的方法与实施过程 3、掌握面向生产测试的产品设计(DFT)的方法与实施过程 4、掌握面向制造系统的新产品验证的过程与方法 5、掌握在满足质量标准的前提下缩短产品试制周期的方法和技巧 6、了解如何建立从样品到量产的管理机制
- 1、下载文档前请自行甄别文档内容的完整性,平台不提供额外的编辑、内容补充、找答案等附加服务。
- 2、"仅部分预览"的文档,不可在线预览部分如存在完整性等问题,可反馈申请退款(可完整预览的文档不适用该条件!)。
- 3、如文档侵犯您的权益,请联系客服反馈,我们会尽快为您处理(人工客服工作时间:9:00-18:30)。
2020/12/10
5
Байду номын сангаас
新产品导入团队
1.新产品导入团队的构成 1)工艺工程 2)设备工程 3)测试工程 4)工业工程 5)产品验证 6)试生产(计划、生产、质量) 2.新产品导入团队的职责 3.新产品导入团队与产品开发团队的关系 1)开发模式的演变:串行变并行 2)并行工程在产品开发中如何体现? 3)扣扣贰叁壹贰贰贰陆伍伍叁 4)新产品导入团队如何提前介入研发? a 为什么要提前介入? b 提前到什么时候介入? c 提前介入做什么? 4).新产品导入团队的管理 a 新产品导入团队与产品开发团队、职能部门的沟通 b 新产品导入团队成员的汇报、考核和管理机制 4.演练与问题讨论 1)根据企业的实际情况,研讨建立新产品导入团队的时机
2020/12/10
6
面向制造系统的产品设计(DFM) 1.如何在产品设计与开发过程中进行可制造性设计 1)从制造的角度来看产品设计 2)工艺人员介入产品开发过程的切入点:从立项就开始 3)工艺管理的三个阶段:工艺设计、工艺调制与验证、工艺管制 4)工艺设计: a 如何提出可制造性需求? b 需要哪些典型的工艺规范? c 可制造性需求如何落实到产品设计方案中? d工艺设计与产品设计如何并行? e 产品工艺流程设计 f 电装、整装、包装与物流的可制造性设计分析 g 如何确保可制造性需求在产品开发中已被实现? h 工艺评审如何操作? i 什么时候考虑工装? j 如何在开发过程中同步输出工艺文件与生产操作指导文件
3.掌握面向生产测试的产品设计(DFT)的方法 与实施过程
4.掌握面向制造系统的新产品验证的过程与方法
5.掌握在满足质量标准的前提下缩短产品试制周 期的方法和技巧
6.了解如何建立从样品到量产的管理机制
2020/12/10
4
从样品到量产概述
1.企业在追求什么:技术?样品?产品?商品? 2.研发与制造的矛盾: 1)制造系统如何面对研发的三无产品? 2)研发如何面对制造系统越来越高的门槛? 3.研发与制造矛盾的激化:中试的产生成为必然 4.中试的定位与发展: 1)研发(RD)、中试(D&P)、生产(P)的关系 2)中试的使命是什么? 3)中试如何定位? 4)中试的发展问题: a 大而全? b 专业化分工? c 产品线划分与共享平台 d 中试人员的发展定位:广度与深度问题 5.中试的业务范围 1)中试业务:新产品导入(NPI) 2)承上:如何面向产品的研发? 3)启下:如何面向产品的制造? 4)桥梁:中试作为连接研发与制造的桥梁,独木桥还是阳关道? 6.演练与问题讨论 1).根据企业的实际情况,是否需要建立并发展中试的职能?
将基于多年的实践、长期的研发咨询积累,总结 出一套理论与实践相结合的可操作的方法,配以 大量实际案例,以指导研发/试产/制造部门主管如 何高效的实现产品从样品走向量产。课程收益
2020/12/10
3
1.了解业界公司在不同发展阶段的产品中试管理 模式与实践
2.掌握面向制造系统的产品设计(DFM)的方法 与实施过程
2020/12/10
7
PPT教学课件
谢谢观看
Thank You For Watching
2020/12/10
8
产品中试管理-从样品到量产
2020/12/10
1
我们在为企业提供研发管理咨询服务的过程中发 现,很多企业的新产品开发从样机到量产的过程 中(产品化过程)存在着共同的问题: 1.新品没有经过中试或中试的时间很短,制造部 门戏称研发的新品是“三无”产品,没有生产文 件、没有工装、生产现场出了问题没人管; 2.转产没有标准,研发想快点转产,生产对有问 题的产品又不愿接收,希望研发把问题都解决了 才转过来,而市场又催得急,经常被迫接收,长 此以往,导致研发与生产的矛盾激化; 3.有些企业开始成立中试部门,希望在中试阶段 把产品质量问题解决掉,但中试的定位与运作也 很困惑,发生质量与进度的冲突时,如何取舍与 平衡,以前研发与制造的矛盾转化为研发与中试、 中试与生产的矛盾,中试成了矛盾集散中心;
2020/12/10
2
4.市场的压力并不因中试的产生而减少,中试需 要从哪些方面努力才能满足产品的质量、进度的 要求?中试的业务是面向研发还是面向制造,还 是兼而有之? 5.量产后才发现产品可制造性差、成品率低、经 常返工,影响发货; 6.产品到了生产后还发生大量的设计变更; 7.产品到了客户手中还冒出各种各样的问题以致 要研发人员到处去“救火”。。。。。。