挤压模具设计思考题
模具制造工艺思考题答案
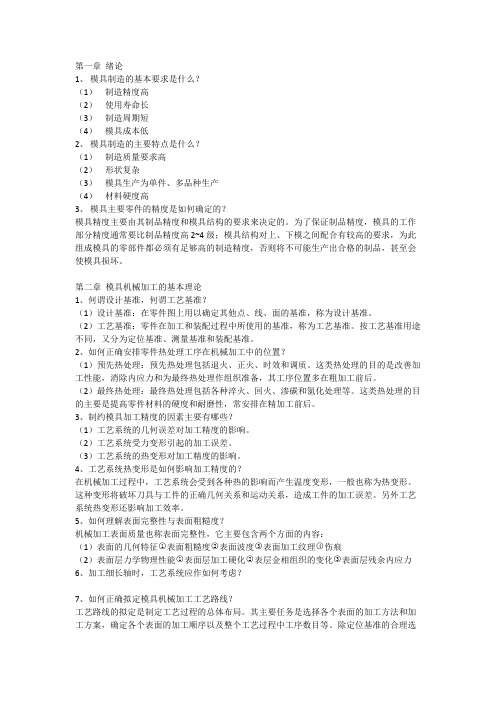
第一章绪论1、模具制造的基本要求是什么?(1)制造精度高(2)使用寿命长(3)制造周期短(4)模具成本低2、模具制造的主要特点是什么?(1)制造质量要求高(2)形状复杂(3)模具生产为单件、多品种生产(4)材料硬度高3、模具主要零件的精度是如何确定的?模具精度主要由其制品精度和模具结构的要求来决定的。
为了保证制品精度,模具的工作部分精度通常要比制品精度高2~4级;模具结构对上、下模之间配合有较高的要求,为此组成模具的零部件都必须有足够高的制造精度,否则将不可能生产出合格的制品,甚至会使模具损坏。
第二章模具机械加工的基本理论1、何谓设计基准,何谓工艺基准?(1)设计基准:在零件图上用以确定其他点、线、面的基准,称为设计基准。
(2)工艺基准:零件在加工和装配过程中所使用的基准,称为工艺基准。
按工艺基准用途不同,又分为定位基准、测量基准和装配基准。
2、如何正确安排零件热处理工序在机械加工中的位置?(1)预先热处理:预先热处理包括退火、正火、时效和调质。
这类热处理的目的是改善加工性能,消除内应力和为最终热处理作组织准备,其工序位置多在粗加工前后。
(2)最终热处理:最终热处理包括各种淬火、回火、渗碳和氮化处理等。
这类热处理的目的主要是提高零件材料的硬度和耐磨性,常安排在精加工前后。
3、制约模具加工精度的因素主要有哪些?(1)工艺系统的几何误差对加工精度的影响。
(2)工艺系统受力变形引起的加工误差。
(3)工艺系统的热变形对加工精度的影响。
4、工艺系统热变形是如何影响加工精度的?在机械加工过程中,工艺系统会受到各种热的影响而产生温度变形,一般也称为热变形。
这种变形将破坏刀具与工件的正确几何关系和运动关系,造成工件的加工误差。
另外工艺系统热变形还影响加工效率。
5、如何理解表面完整性与表面粗糙度?机械加工表面质量也称表面完整性,它主要包含两个方面的内容:○1○2○3○4(1)表面的几何特征表面粗糙度表面波度表面加工纹理伤痕○1○2○3(2)表面层力学物理性能表面层加工硬化表层金相组织的变化表面层残余内应力6、加工细长轴时,工艺系统应作如何考虑?7、如何正确拟定模具机械加工工艺路线?工艺路线的拟定是制定工艺过程的总体布局。
安徽工业大学材料成型专业课《挤压模具设计》复习题part1
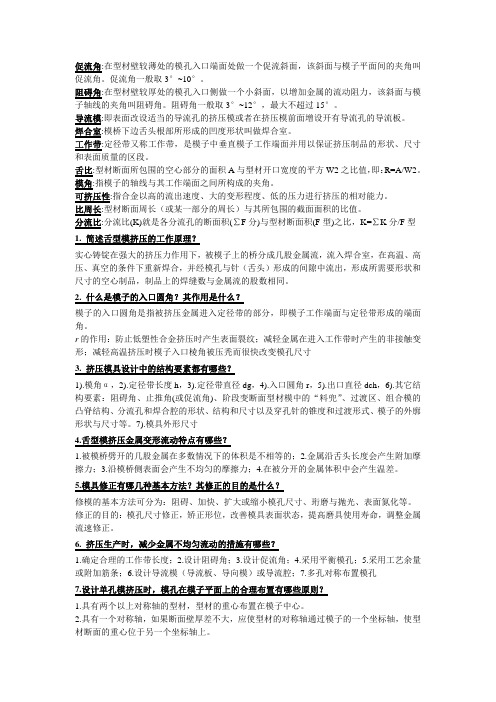
促流角:在型材壁较薄处的模孔入口端面处做一个促流斜面,该斜面与模子平面间的夹角叫促流角。
促流角一般取3°~10°。
阻碍角:在型材壁较厚处的模孔入口侧做一个小斜面,以增加金属的流动阻力,该斜面与模子轴线的夹角叫阻碍角。
阻碍角一般取3°~12°,最大不超过15°。
导流模:即表面改设适当的导流孔的挤压模或者在挤压模前面增设开有导流孔的导流板。
焊合室:模桥下边舌头根部所形成的凹度形状叫做焊合室。
工作带:定径带又称工作带,是模子中垂直模子工作端面并用以保证挤压制品的形状、尺寸和表面质量的区段。
舌比:型材断面所包围的空心部分的面积A与型材开口宽度的平方W2之比值,即:R=A/W2。
模角:指模子的轴线与其工作端面之间所构成的夹角。
可挤压性:指合金以高的流出速度、大的变形程度、低的压力进行挤压的相对能力。
比周长:型材断面周长(或某一部分的周长)与其所包围的截面面积的比值。
分流比:分流比(K)就是各分流孔的断面积(∑F分)与型材断面积(F型)之比,K=∑K分/F型1. 简述舌型模挤压的工作原理?实心铸锭在强大的挤压力作用下,被模子上的桥分成几股金属流,流入焊合室,在高温、高压、真空的条件下重新焊合,并经模孔与针(舌头)形成的间隙中流出,形成所需要形状和尺寸的空心制品,制品上的焊缝数与金属流的股数相同。
2. 什么是模子的入口圆角?其作用是什么?模子的入口圆角是指被挤压金属进入定径带的部分,即模子工作端面与定径带形成的端面角。
r的作用:防止低塑性合金挤压时产生表面裂纹;减轻金属在进入工作带时产生的非接触变形;减轻高温挤压时模子入口棱角被压秃而很快改变模孔尺寸3. 挤压模具设计中的结构要素都有哪些?1).模角α,2).定径带长度h,3).定径带直径dg,4).入口圆角r,5).出口直径dch,6).其它结构要素:阻碍角、止推角(或促流角)、阶段变断面型材模中的“料兜”、过渡区、组合模的凸脊结构、分流孔和焊合腔的形状、结构和尺寸以及穿孔针的锥度和过渡形式、模子的外廓形状与尺寸等。
冷挤压工艺及模具设计试题.doc
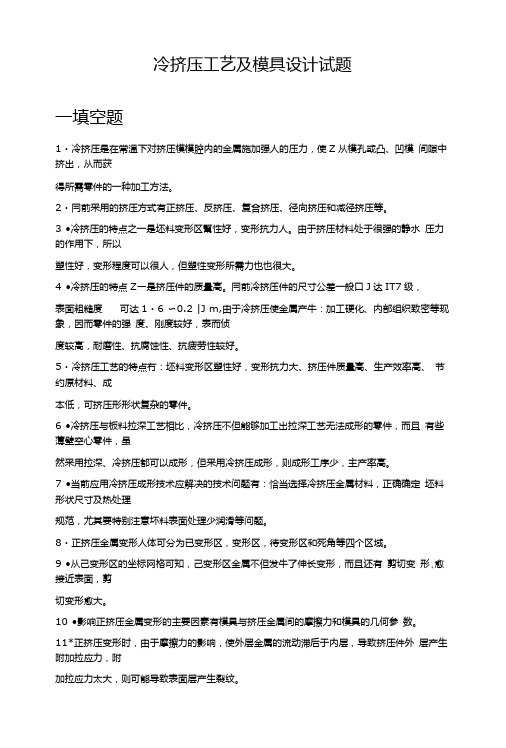
冷挤压工艺及模具设计试题一填空题1・冷挤压是在常温下对挤压模模腔内的金属施加强人的压力,使Z从模孔或凸、凹模间隙中挤出,从而获得所需零件的一种加工方法。
2・冃前采用的挤压方式有正挤压、反挤压、复合挤压、径向挤压和减径挤压等。
3•冷挤压的特点之一是坯料变形区幫性好,变形抗力人。
由于挤压材料处于很强的静水压力的作用下,所以塑性好,变形程度可以很人,但塑性变形所需力也也很大。
4•冷挤压的特点Z—是挤压件的质量高。
冃前冷挤压件的尺寸公差一般口J达IT7级,表面粗糙度可达1・6 〜0.2 |J m,由于冷挤压使金属产牛:加工硬化、内部组织致密等现象,因而零件的强度、刚度较好,表而侦度较高,耐磨性、抗腐蚀性、抗疲劳性较好。
5・冷挤压工艺的特点冇:坯料变形区塑性好,变形抗力大、挤压件质量高、生产效率高、节约原材料、成本低,可挤压形形状复杂的零件。
6•冷挤压与板料拉深工艺相比,冷挤压不但能够加工出拉深工艺无法成形的零件,而且有些薄壁空心零件,虽然采用拉深、冷挤压都可以成形,但采用冷挤压成形,则成形工序少,主产率高。
7•当前应用冷挤压成形技术应解决的技术问题有:恰当选择冷挤压金属材料,正确确定坯料形状尺寸及热处理规范,尤其要特别注意坏料表面处理少润滑等问题。
8・正挤压金属变形人体可分为已变形区,变形区,待变形区和死角等四个区域。
9•从己变形区的坐标网格可知,己变形区金属不但发牛了伸长变形,而且还有剪切变形,愈接近表面,剪切变形愈大。
10•影响正挤压金属变形的主要因素有模具与挤压金属间的摩擦力和模具的几何参数。
11*正挤压变形时,由于摩擦力的影响,使外层金属的流动滞后于内层,导致挤压件外层产生附加拉应力,附加拉应力太大,则可能导致表面层产生裂纹。
12•冷挤压变形程度的表示形式断面收缩率、挤压比和对数挤压比等三种,其中最常用的是断面收缩率。
13•冷挤压极限变形程度实际上是指在模具强度允许的条件下,保持模具具有一定寿命的一次挤压变形程度。
冷冲压模具设计习题集(1)
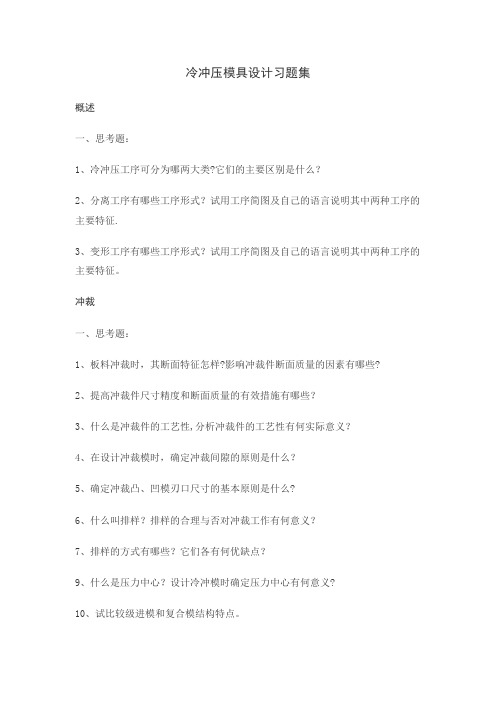
冷冲压模具设计习题集概述一、思考题:1、冷冲压工序可分为哪两大类?它们的主要区别是什么?2、分离工序有哪些工序形式?试用工序简图及自己的语言说明其中两种工序的主要特征.3、变形工序有哪些工序形式?试用工序简图及自己的语言说明其中两种工序的主要特征。
冲裁一、思考题:1、板料冲裁时,其断面特征怎样?影响冲裁件断面质量的因素有哪些?2、提高冲裁件尺寸精度和断面质量的有效措施有哪些?3、什么是冲裁件的工艺性,分析冲裁件的工艺性有何实际意义?4、在设计冲裁模时,确定冲裁间隙的原则是什么?5、确定冲裁凸、凹模刃口尺寸的基本原则是什么?6、什么叫排样?排样的合理与否对冲裁工作有何意义?7、排样的方式有哪些?它们各有何优缺点?9、什么是压力中心?设计冷冲模时确定压力中心有何意义?10、试比较级进模和复合模结构特点。
11、冲裁凸模的基本固定方式有哪几种?12、怎么提高凸模的强度和刚度?13、设计定位零件时应注意什么?14、级进模中使用定距侧刃有什么优点?怎样设计定距侧刃?15、级进模中使用导正销的作用是什么?怎样设计导正销?16、弹性卸料与刚性卸料各有什么特点.二、计算题:1、某厂生产变压器硅钢片零件如图下图所示,试计算落料凹、凸模刃口尺寸及制造公差。
2、计算下图所示零件用的模具的刃口尺寸,并确定制造公差。
材料厚度t=0.8mm,材料:08F。
3、设计冲制下图所示零件的凹模。
4、计算冲裁下图所示零件的凸、凹模刃口尺寸及公差。
5、试确定下图所示零件的合理排样方法,并计算其条料宽度和材料利用率.6、试根据下图所示的凹模简图画出冲裁件形状及冲裁时的排样图。
7、试根据下图所示的凹模简图画出冲裁件形状及冲裁时的排样图.8、如下图所示零件,材料为40钢,板厚为6mm,请确定落料凹、凸模尺寸及制造公差.9、如下图所示零件,材料为10钢,料厚2mm,采用配作法加工,求凸、凹模刃口尺寸及公差。
10、请计算下图所示零件落料冲孔复合模的冲裁力、推件力、卸料力,确定压力机吨位。
模具设计复习思考题含答案

2021级<<模具设计>>课程复习思考题2021.11.151.塑料注射模主要由哪几局部所组成?构造特点及开合模动作过程?P47-48答:塑料注射模主要组成局部:〔1〕成型零部件:定、动模局部中组成的零件。
〔由凸模〔或型芯〕、凹模〔型腔板〕、镶件等组成,合模时构成型腔,用于填充塑料熔体,它决定塑件的形状与尺寸。
如动模板1,定模板2,型芯7〕〔2〕浇注系统:熔融塑料从注塑机喷嘴进入模具型腔所流经的通道,它由主流道、分流道、浇口与冷料穴组成。
〔3〕导向机构:为定模及动模之间的导向机构与推出机构的导向机构两类。
〔前者是保证动模与定模在合模时准确对合,以保证塑件形状与尺寸准确度,如导柱8与导套9;后者是保证推出过程中推出板顺畅而设置的,如推板导柱16、推板导套17。
〕〔4〕脱模机构:又称推出机构。
〔常见的有推杆推出机构、推板推出机构与推管推出机构等。
图1中推板13、推杆固定板14、拉料杆15、推杆18与复位杆19组成推杆推出机构。
〕〔5〕侧向分型及抽芯机构当塑件侧向有凹凸形状的孔或凸台时,就需要有侧向型芯来成型。
使侧向型芯移动的机构称为侧向分型抽芯机构。
〔6〕加热与冷却系统为满足注射工艺对模具的温度要求,必须对模具温度进展控制,所以模具常常设有冷却系统或在模具内部或四周安装加热元件。
冷却系统一般在模具上开设冷却水道,如冷却水道3。
〔7〕排气系统在注射成型过程中,为将型腔内的空气排出,常常需要开设排气系统,通常是在分型面上开设假设干条沟槽,或利用模具的推杆或型芯及模板之间的配合间隙进展排气。
小型塑件的排气量不大,可直接利用分型面排气,而不必另设排气槽。
〔8〕其他零部件用来固定、支承成型零部件或起定位与限位作用的零部件等。
〔如动模板垫板,定模底板,支撑柱,定位圈,螺钉,销钉,吊环等。
〕2.按总体构造来分类,塑料注射模有哪几种类型?能简述这些类型的模具构造、特点,并能区分模具的类型及其工作过程〔或原理〕。
挤压工艺课后答案资料

挤压工艺及模具习题库1. 反挤压进入稳定挤压状态时,可将坯料的变形情况分为几个区域?反挤压进入稳定阶段,坯料的变形情况可分为以下几个区域:已变形区、变形区、过渡区、死区、待变形区。
2.三向应力为何可以提高被挤压材料的塑形?三向应力之所以可以提高被挤压材料的塑形,归纳起来主要原因是:第一:三向压应力状态能遏制晶间相对移动,阻止晶间变形。
第二:三向压应力状态有利于消除由于塑性变形所引起的各种破坏。
第三:三向压应力状态能使金属内某些夹杂物的危害程度大为降低。
第四:三向压应力状态可以抵消或减小由于不均匀变形而引起的附加应力,从而减轻了附加应力所造成的破坏作用。
3.什么是挤压变形的附加应力?它是如何形成的?在塑形变形过程中,变形金属内部除了存在着与外力相应的基本应力以外,还由于物体内各层的不均匀变形受到变形体整体性的限制,而引起变形金属内部各部分自相平衡的应力,称为附加应力。
产生原因:1,变形金属与模具之间存在着摩擦力。
2各部分金属流动阻力不一致。
3变形金属的组织结构不均匀。
4模具工作部分的形状与尺寸不合理。
4.根据正挤压实心件的坐标网格,分析实心件正挤压的金属流动特点。
实心件正挤压的金属流动特点:坯料除了受凹模工作表面的接触摩擦影响外,还受到芯棒表面接触摩擦的影响,因而坯料上的横向坐标线向后弯曲,不再有产生超前流动的中心区域,这说明正挤压空心件的金属流动比正挤压实心件均匀一些。
在进入稳定流动时,剧烈变形区也是集中在凹模锥孔附近高度很小的范围之内,金属在进入变形区以前或离开变形区以后几乎不发生塑性变形,仅作刚性平移。
5.什么是残余应力?附加应力和残余应力有何危害性?当外力取消以后,附加应力并不消失而残留在变形体内部,成为残余应力。
附加应力和残余应力的危害:第一:缩短挤压件的使用寿命;第二:引起挤压件尺寸及形状的变化;第三:降低金属的耐蚀性。
6. 分析正挤压、反挤压缩孔产生的原因。
缩孔是指变形过程中变形体一些部位上产生较大的空洞或凹坑的缺陷。
05 压缩成型模具设计——习题答案

第五章塑料压缩模设计——习题答案一、填空题1.溢式压缩模无_加料室_,凸模、凹模无配合部分,完全靠__导柱__定位,这种模具不适用于_压缩率_高的塑料,不宜成型__薄壁__或_壁厚均匀性要求很高_的塑件。
2.半溢式压缩模的加料腔与型腔分界处有一__溢料槽_,过剩的原料可通过_配合间隙_或在凸模上开设专门的_溢料槽_排出。
3.半溢式压缩模应用力较广,适用于成型_流动性较好_塑料及形状复杂、带有小型嵌件的塑件,不适于压制以_布片_或_长纤维_作填料的塑料。
4.不溢式压缩模适于压制_形状复杂_、_薄壁_、_长流程_、_深形塑件_塑件,也适于压制特别小、_压制流动性差_、_单位比压_高、_比容大_的塑料。
用它压制棉布、玻璃布或长纤维填充的塑料是可行的。
5.热固性塑料模压成型的设备常为_压力机_。
6.压制塑件所需的总成型压力F压应满足F压=p·A·n,式中A为每一型腔的_水平投影_面积,其值取决于压缩模的结构形式,对于溢式和不溢式压缩模,等于塑件最大_轮廓的水平投影_面轵,对于半溢式压缩模,等于加料腔的_水平投影_面积。
7.设计压缩模时要校核压机的闭合高度与压缩模的闭合高度,对于固定式压缩模应满足不等式_hmax≤Hmax-h凸-h塑-(10~20)mm及hmin≥Hmin+(10~15)mm_的条件。
8.压缩模设计时应考虑塑件在模具内的加压方向,确定加压方向时应考虑_有利于压力传递_、_便于加料_、_便于安装和固定嵌件_、_保证凸模强度_、_应便于塑料流动_、_长型芯应位于施压方向_、_保证重要尺寸的精度_。
9.不溢式和半溢式压缩模中的引导环,其作用是导正凸模进入凹模,引导环—般设在__凹模__上部,长度值应保证_塑粉达到熔融_时,凸模已进入__配合__环。
10.不溢式和半溢式压缩模还需有配合环,它是凸模与凹模的配合部位,其配合间隙以_不产生溢料和不擦伤模壁_为原则,单边间隙取0.025~0.075mm,也可采用_H8/f7_或_H9/f9_配合。
浅谈挤压模具设计中的要点及常见问题
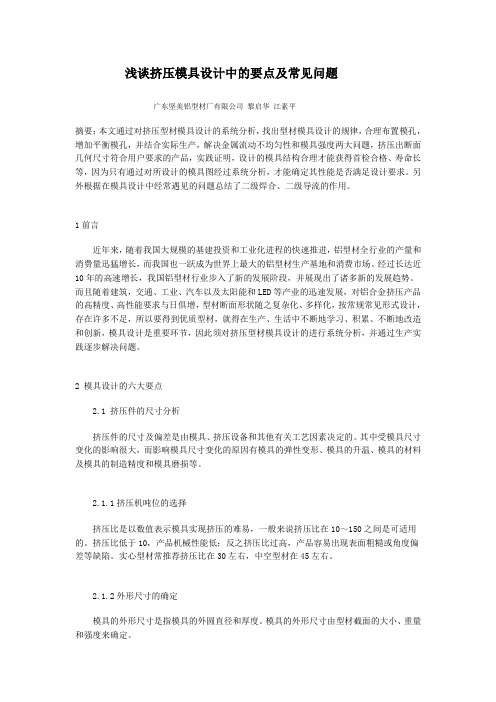
浅谈挤压模具设计中的要点及常见问题广东坚美铝型材厂有限公司黎启华江素平摘要:本文通过对挤压型材模具设计的系统分析,找出型材模具设计的规律,合理布置模孔,增加平衡模孔,并结合实际生产,解决金属流动不均匀性和模具强度两大问题,挤压出断面几何尺寸符合用户要求的产品,实践证明,设计的模具结构合理才能获得首检合格、寿命长等,因为只有通过对所设计的模具图经过系统分析,才能确定其性能是否满足设计要求。
另外根据在模具设计中经常遇见的问题总结了二级焊合、二级导流的作用。
1前言近年来,随着我国大规模的基建投资和工业化进程的快速推进,铝型材全行业的产量和消费量迅猛增长,而我国也一跃成为世界上最大的铝型材生产基地和消费市场。
经过长达近10年的高速增长,我国铝型材行业步入了新的发展阶段,并展现出了诸多新的发展趋势。
而且随着建筑,交通、工业、汽车以及太阳能和LED等产业的迅速发展,对铝合金挤压产品的高精度、高性能要求与日俱增,型材断面形状随之复杂化、多样化,按常规常见形式设计,存在许多不足,所以要得到优质型材,就得在生产、生活中不断地学习、积累、不断地改造和创新,模具设计是重要环节,因此须对挤压型材模具设计的进行系统分析,并通过生产实践逐步解决问题。
2 模具设计的六大要点2.1 挤压件的尺寸分析挤压件的尺寸及偏差是由模具、挤压设备和其他有关工艺因素决定的。
其中受模具尺寸变化的影响很大,而影响模具尺寸变化的原因有模具的弹性变形、模具的升温、模具的材料及模具的制造精度和模具磨损等。
2.1.1挤压机吨位的选择挤压比是以数值表示模具实现挤压的难易,一般来说挤压比在10~150之间是可适用的。
挤压比低于10,产品机械性能低;反之挤压比过高,产品容易出现表面粗糙或角度偏差等缺陷。
实心型材常推荐挤压比在30左右,中空型材在45左右。
2.1.2外形尺寸的确定模具的外形尺寸是指模具的外圆直径和厚度。
模具的外形尺寸由型材截面的大小、重量和强度来确定。
挤压工艺课后答案图文稿

挤压工艺课后答案集团文件版本号:(M928-T898-M248-WU2669-I2896-DQ586-M1988)挤压工艺及模具习题库1. 反挤压进入稳定挤压状态时,可将坯料的变形情况分为几个区域?反挤压进入稳定阶段,坯料的变形情况可分为以下几个区域:已变形区、变形区、过渡区、死区、待变形区。
2.三向应力为何可以提高被挤压材料的塑形?三向应力之所以可以提高被挤压材料的塑形,归纳起来主要原因是:第一:三向压应力状态能遏制晶间相对移动,阻止晶间变形。
第二:三向压应力状态有利于消除由于塑性变形所引起的各种破坏。
第三:三向压应力状态能使金属内某些夹杂物的危害程度大为降低。
第四:三向压应力状态可以抵消或减小由于不均匀变形而引起的附加应力,从而减轻了附加应力所造成的破坏作用。
3.什么是挤压变形的附加应力它是如何形成的在塑形变形过程中,变形金属内部除了存在着与外力相应的基本应力以外,还由于物体内各层的不均匀变形受到变形体整体性的限制,而引起变形金属内部各部分自相平衡的应力,称为附加应力。
产生原因:1,变形金属与模具之间存在着摩擦力。
2各部分金属流动阻力不一致。
3变形金属的组织结构不均匀。
4模具工作部分的形状与尺寸不合理。
4.根据正挤压实心件的坐标网格,分析实心件正挤压的金属流动特点。
实心件正挤压的金属流动特点:坯料除了受凹模工作表面的接触摩擦影响外,还受到芯棒表面接触摩擦的影响,因而坯料上的横向坐标线向后弯曲,不再有产生超前流动的中心区域,这说明正挤压空心件的金属流动比正挤压实心件均匀一些。
在进入稳定流动时,剧烈变形区也是集中在凹模锥孔附近高度很小的范围之内,金属在进入变形区以前或离开变形区以后几乎不发生塑性变形,仅作刚性平移。
5.什么是残余应力附加应力和残余应力有何危害性当外力取消以后,附加应力并不消失而残留在变形体内部,成为残余应力。
附加应力和残余应力的危害:第一:缩短挤压件的使用寿命;第二:引起挤压件尺寸及形状的变化;第三:降低金属的耐蚀性。
模具设计制造专业答辩思考题

答辩思考题一.带有抽芯滑块机构的模具:1.斜导柱与斜楔之间的角度有何关系?为何?答:一般斜楔角度应大于斜导柱角度2°~3°。
因开模时,斜楔与斜导柱随定模同时运动,而斜楔角度大于2°~3°,使斜滑块在运动前有一定的微距,保证了斜滑块能作水平向外运动;同理,闭模时能保证斜滑块作水平向内运动。
否则斜滑块作水平运动受到干涉。
2.斜导柱与斜楔各有何作用?答:斜导柱是抽芯机构的动力源,带动斜滑块向内或向外运动,而斜楔是确保抽芯机构最终到位并锁住斜滑块。
3.对于带有抽芯滑块机构的模具,其模架选用有何特殊要求?答:首先模架的导柱要倒装;其次模架导柱高度必须大于斜导柱高度;使模架先起到导向作用,再使斜导柱起导向作用,从而确保抽芯滑块机构运动的稳定性。
4.当抽芯滑块机构与顶出机构发生干涉时,一般采用何种办法来避免干涉?答:采用预复位机构(常用:弹性、钢性、液压等机构)。
5.叙说抽芯滑块机构模具运动的工作原理答:开模时,斜导柱在定模的作用下带动斜滑块作水平向外运动,完成抽芯动作,然后通过注射机的活塞杆推动顶针顶出塑件。
闭模时,定模推动复位杆使预复位机构先运动,同时斜导柱带动斜滑块作水平向内运动,完成入芯运作,最终闭模的同时斜楔锁住斜滑块,完成一次周期运动。
6. 计算抽芯距时,主要涉及到那个零件、哪些数据?答:斜导柱。
斜导柱的长度、角度、直径。
斜导柱的直径取决于所承受的弯曲应力、抽拔力、长度、角度等。
斜导柱的长度、角度取决于抽芯距。
7. 理论抽芯距与实际抽芯距是否一致?答:不一致。
一般实际抽芯距大于理论抽芯距2~5㎜。
若实际抽芯距与理论抽芯距一致,那就不能保证侧抽芯每次均能理想的脱离塑件(加工误差、装配误差等),从而造成塑件撕裂。
所以,实际抽芯距要大于理论抽芯距2~5㎜。
8. 怎样将斜滑块稳定于规定的位置?答:因⑴. 当斜导柱脱离斜滑块顺间,斜滑块还有运动惯性。
⑵.当斜导柱脱离斜滑块后,斜滑块靠自重会垂直下落脱离模具。
《模具设计与制造》思考题与答案

《模基础》自测题一、名词解释:1.冷冲压:2.变形工序:3.冲裁:4.排样:5.冲裁间隙:6.弯曲:7.拉深:8.校平:9.特种加工:10.模具装配:二、填充题:1.冷冲压是塑性加工的基本方法之一,它是利用安装在压力机上的模具,在对板料施加压力使其,从而获得具有一定形状、尺寸和精度的零件的一种压力加工方法。
因为它主要用于加工板料零件,所以也称。
2.是实现冷冲压加工中必不可少的工艺装备,没有先进的,先进的冲压工艺就无法实现。
3.冷冲压用材料大部分是各种规格的、和。
4.选择冷冲压设备的类型主要根据所要完成的冲压工艺的性质、、冲压件的几何尺寸和。
5.冲裁变形过程大致分为三个阶段,分别是阶段、阶段和阶段。
6.冲裁时搭边,会造成材料的浪费,搭边,则起不到搭边应有的作用。
7.冲压力是、、推料力和顶料力的总称。
8.设计冲裁模的刃口尺寸时,落料模应以为设计基准,再按间隙值确定尺寸;冲孔模应以为设计基准,再按间隙值确定尺寸。
9.模具设计时,要尽可能减小和消除回弹常用的方法有和。
10.为了保证拉深件的质量,在拉深过程中选择合适的,以减少模具与工件之间的,使拉深过程正常进行。
11.决定拉深工序次数的原则是既要使材料的应力不超过材料的,又要充分利用材料的塑性,使之达到最大可能的变形程度,通常以表示拉深的变形程度。
12.凸、凹模的圆角半径,尤其是凹模的圆角半径对拉深工作影响很大。
凹模圆角半径,易使拉深件表面划伤或产生断裂;圆角半径,由于悬空面积增大,使压边面积减小,易起内皱。
13.冷挤压是在条件下,利用模具在压力机上对金属以一定的速度施加的压力,使金属产生塑性变形,从而获得所需形状和尺寸的零件。
14.塑料是以相对分子量较高的为主要成分,加入其它添加剂,可在一定温度和压力下塑化成型的合成材料。
15.塑料按照热性能分为塑料和塑料两类。
16.在塑件脱模过程中为了避免擦伤和拉毛,塑件上于脱模方向的表面一般应具有合理的。
17.注射机一般由、合模部分、和四个部分组成。
最新挤压工艺及模具习题库参考答案

挤压工艺及模具习题库参考答案1.答:反挤压进入稳定阶段,坯料的变形情况可分为以下几个区域:已变形区、变形区、过渡区、死区、待变形区。
2.答:三向应力之所以可以提高被挤压材料的塑形,归纳起来主要原因是:第一:三向压应力状态能遏制晶间相对移动,阻止晶间变形。
第二:三向压应力状态有利于消除由于塑性变形所引起的各种破坏。
第三:三向压应力状态能使金属内某些夹杂物的危害程度大为降低。
第四:三向压应力状态可以抵消获减小由于不均匀变形而引起的附加应力,从而减轻了附加应力所造成的破坏作用。
3.答:在塑形变形过程中,变形金属内部除了存在着与外力相应的基本应力以外,还由于物体内各层的不均匀变形受到变形体整体性的限制,而引起变形金属内部各部分自相平衡的应力,称为附加应力。
4.答:实心件正挤压的金属流动特点:坯料除了受凹模工作表面的接触摩擦影响外,还受到芯棒表面接触摩擦的影响,因而坯料上的横向坐标线向后弯曲,不再有产生超前流动的中心区域,这说明正挤压空心件的金属流动比正挤压实心件均匀一些。
在进入稳定流动时,剧烈变形区也是集中在凹模锥孔附近高度很小的范围之内,金属在进入变形区以前或离开变形区以后几乎不发生塑性变形,仅作刚性平移。
5.答:附加应力不是由外力引起的,而是为了自身得到平衡引起的。
因此,当外力取消以后,附加应力并不消失而残留在变形体内部,成为残余应力。
附加应力和残余应力的危害:第一:缩短挤压件的使用寿命;第二:引起挤压件尺寸及形状的变化;第三:降低金属的耐蚀性。
6.答:缩孔是指变形过程中变形体一些部位上产生较大的空洞或凹坑的缺陷。
当正挤压进行到待变形区厚度较小时、甚至只有变形区而无待变形区时,会产生缩孔。
筒形件反挤压时进行到待变形区厚度较小,甚至当坯料底厚小于壁厚时仍继续反挤,则会因材料不足以形成较厚的壁部而产生角部缩孔缺陷。
7.答:挤压对金属组织和力学性能的影响有:挤压时,在强烈的三向应力作用下金属晶粒被破碎,原来较大的晶粒挤压后变成为等轴细晶粒组织,因而提高了强度。
模具设计与快速成型1、冲裁思考题

冲裁思考题1 .影响金属塑性和变形抗力的因素有哪些?2 .除了冲压性能外, 对冷冲压材料还有哪些要求?3 .请说明标号为88521308887082-------GB HF GB B 钢板的含义。
4 .请说明标号为88521308887082-----GB HF GB B -- 钢板的含义。
5.什么是金属的塑性?什么是 塑性变形?6.比较开式压力机与闭式压力机各有什么特点?7.在压力机上 模具如何安装?8.按材料的分离形式不同,冲裁一般可以分为哪两的类?它们的主要区别是什么?9.板料冲裁时,其断面特征怎样?影响冲裁件断面质量的因素有哪些?10.什么是冲裁间隙?冲裁间隙对冲裁有哪些影响?11.确定冲裁凸模、凹模刃口尺寸的基本原则是什么?12.什么叫材料的利用率?在冲裁工作中如何提高材料的利用率?13.排样的方式有哪些?它们各有何优缺点?14.什么叫搭边?搭边的作用有哪些?搭边值的大小与哪些因素有关?15.什么叫冲裁力?冲裁力的大小与哪些因素有关?16.在冲裁工作中降低冲裁力有何实际意义?降低冲裁力的方法有哪些?17.什么是卸料力、推件力和顶件力,怎样确定这些力的大小?18.冲裁时,怎样确定冲压设备的公称压力?19.冷冲模的基本类型有哪些?20.冲模一般由哪些部分组成?各部分的作用是什么?21.单工序模有哪几种类型?各有什么特点?22.试比较级进模和复合模的结构特点。
23.冲裁凸模的基本固定方式有哪几种?24.挡料销的作用是什么?常用的挡料销有哪些结构形式?25.级进模中使用定距侧刃有什么优点?26.级进模中使用导正销的作用是什么?27.弹性卸料与刚性卸料各有什么特点?28.冲裁模的卸料方式有哪几种?各有何特点?。
挤压模具设计思考题

挤压模具设计思考题挤压模具设计思考题1、基本概念平模、锥模、正锥模、倒锥模、舌比、比周长、阻碍角、促流角、分流比、宽展量、宽展变形率、比压正锥模:操作时顺着挤压方向装入模支承内,其锥角一般为1°30′~4°。
倒锥模:操作时逆着挤压方向装入模支承内,其锥角一般取6°。
舌比:包围的空间面积与开口宽度平方的比值。
比周长:型材断面周长(或某一部分的周长)与其所包围的截面面积的比值。
阻碍角:在型材壁较厚处的模孔入口侧做一个小斜面,以增加金属的流动阻力,该斜面与模子轴线的夹角叫阻碍角。
促流角:在型材壁较薄处的模孔入口端面处做一个促流斜面,该斜面与模子平面间的夹角叫促流角。
分流比:各分流孔的断面积(∑F分)与型材断面积(F型)之比。
宽展量△B :铸锭经宽展变形以后的最大宽度B2与挤压筒直径D1之差。
宽展变形率δB:δB =(B2-B1)/B1×100% ,B2 、B1——宽展模出、入口宽度。
2、从模具的整体结构上可将挤压模具分成那几类,各自的主要用途是什么?答:按模具结构形式可分为:整体模、拆卸模、组合模、专用模具。
整体模:模子是由一块钢材加工制造。
广泛用于挤压铝合金型、棒、管材。
拆卸模:由数块拼装组成一整体模子。
用于生产阶段变断面型材。
模子是由大头和小头两部分构成。
而这两部分又分别由多块组装而成。
.挤压模具设计思考题组合模:用于生产内径较小的管材、各种断面形状的空心型材。
专用模具——如水冷模、宽展模等等。
3、根据模孔压缩区的形状,可将挤压模具分那几种?最常用的是什么模子,主要用于挤压什么产品?答:平模、锥形模、平锥模、流线形模和双锥模等;平模:挤压铝合金型材、棒材,镍合金、铜合金管、棒材。
锥模:挤压铝合金管材,高温合金钨、钼、锆等。
4、分流模、舌型模都是用于挤压空心制品的,他们各自的优缺点是什么,适用于挤压什么产品?答:桥模(舌形模):所需的挤压力较小,焊合室中延伸系数大,主要用于挤压硬合金空心型材。
铝型材挤压模具考题

铝型材挤压模具设计思考题1、基本概念平模、锥模、正锥模、倒锥模、舌比、比周长、宽厚比、阻碍角、促流角、挤压比、分流比、宽展量、宽展角、比压2.模具工作带的作用是什么?确定工作带长度的原则是什么?3.挤压模具设计时,为什么要设计入口圆角?4.在50MN挤压机直径为360mm的挤压筒上,挤压直径为40mm棒材,合理的挤压比范围为10~15,模孔数目为多少合适?5. 不等壁型材模设计时,如何确定不同壁厚处的模孔工作带长度?6.在型材模具设计时,如何平衡模孔不同部位金属的流动速度?7.在槽形型材模具设计时,为什么型材模孔的角度应增大1°~2°,设计成91°~92°,而且型材底部的模孔尺寸应适当扩大0.1~0.8mm?8.分流模主要由那几部分构成,焊合室的主要作用是什么?。
9.型材模孔设计时,模孔尺寸要比型材的名义尺寸大一些,这是为什么?10.分流模设计中,为什么要将模孔置于分流桥下面?如果模孔不能完全被桥遮蔽,工作带尺寸如何确定?11.分流模设计时,模芯为什么要伸出模孔工作带一定长度?12.焊合室的大小、形状对挤压制品的质量有何影响?13.焊合室高度对制品的焊合质量有何影响?14.一般来说,焊合室高度越大,制品的焊合质量越好,但易造成制品偏心,这是为什么?15.挤压模具设计中为什么要设计“空刀”,空刀尺寸大小对产品质量和模具寿命有何影响?16.宽展模挤压的基本原理是什么?17.导流模挤压的基本原理是什么?18.模具优化设计的意义是什么?模具优化设计的基本方法是什么?19.采用平模挤压生产普通实心型材时,如果出现弯曲、扭拧等缺陷,可采用那些修模方法以消除这些缺陷?20.采用分流模挤压空心型材时,如果出现弯曲、扭拧等缺陷,可采用那些修模方法以消除这些缺陷?21.当型材尺寸出现超负偏差,或超正偏差时,如何修模?。
压铸模具设计复习思考题

压铸模具设计复习思考题Modified by JACK on the afternoon of December 26, 2020压铸模具设计复习思考题2011-12-9一、名词概念-掌握1、压铸:是一种将熔融状态或半熔融状态的金属浇入压铸机的压室,在高压力的作用下,以极高的速度充填在压铸模的型腔内,并在高压下使熔融或半熔融的金属冷却凝固成行而获得铸件的高效益、高效率的精密铸造方法。
P1,L2~L42、脱模斜度:为了便于压铸件从压铸模中脱出及防止划伤铸件表面,铸件上所有与模具运动方向(即脱模方向)平行的孔壁和外壁表面均需设计成一定的表面倾斜度。
P24,L2~L33、嵌件:压铸件内镶入金属或非金属制件,与压铸件形成牢靠不可分开的整体,此镶入的制件为嵌件。
P27,L1~L24、压铸工艺:是把压铸合金压铸模和压铸机这3个压铸生产要素有机组合和运用是过程。
P32,L15、压射力:指压射冲头作用于(压室中)金属液上的力。
P32 L16、压射速度:即压室内压射冲头推动金属液的移动速度(又称冲头速度)7、内浇口速度:是指金属液通过内浇口时的线速度(又称充填速度)。
P37 L18、合金浇注温度:是指金属液从压室进入型腔的平均温度,因测量不便,通常以保温炉内的温度表示。
一般高于合金液相线20~30℃。
P38 L19、模具温度:压铸模生产前应预热到一定温度,在生产过程中要始终保持在一定的温度范围内,这一温度范围即为~。
P40 L2~L3 与浇注温度有何关系?模具温度应为三分之一的金属液浇注温度。
(式3-9)10、10、充填时间:金属液自开始进入模具型腔直至充满型腔所需的时间。
P44 L111、增压建压时间:是指金属液充满型腔的瞬时开始,至达到预定增压压力所需的时间,也就是比压由压射比压上升到增压比压所需的时间。
P45 图3-6下,L112、持压时间:从金属液充满型腔到内浇口完全凝固,冲头压力作用在金属液上所持续的时间。
07 挤出成型模具设计——习题答案
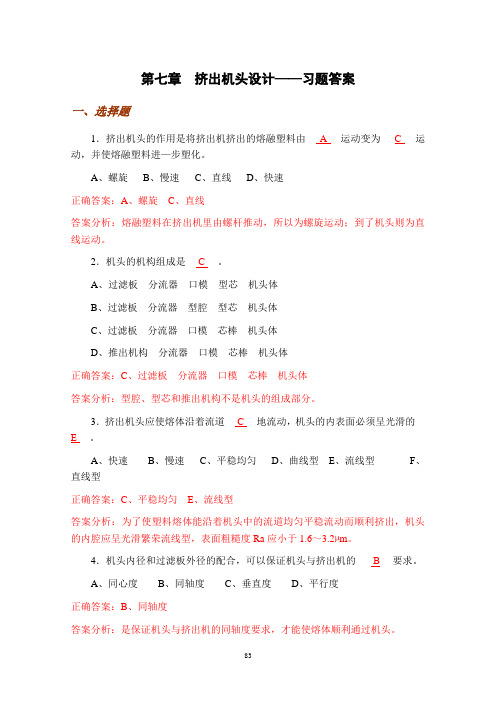
第七章挤出机头设计——习题答案一、选择题1.挤出机头的作用是将挤出机挤出的熔融塑料由__A __运动变为__ C __运动,并使熔融塑料进—步塑化。
A、螺旋B、慢速C、直线D、快速正确答案:A、螺旋C、直线答案分析:熔融塑料在挤出机里由螺杆推动,所以为螺旋运动;到了机头则为直线运动。
2.机头的机构组成是__ C __。
A、过滤板分流器口模型芯机头体B、过滤板分流器型腔型芯机头体C、过滤板分流器口模芯棒机头体D、推出机构分流器口模芯棒机头体正确答案:C、过滤板分流器口模芯棒机头体答案分析:型腔、型芯和推出机构不是机头的组成部分。
3.挤出机头应使熔体沿着流道__ C __地流动,机头的内表面必须呈光滑的__ E __。
A、快速B、慢速C、平稳均匀D、曲线型E、流线型F、直线型正确答案:C、平稳均匀E、流线型答案分析:为了使塑料熔体能沿着机头中的流道均匀平稳流动而顺利挤出,机头的内腔应呈光滑繁荣流线型,表面粗糙度Ra应小于1.6~3.2µm。
4.机头内径和过滤板外径的配合,可以保证机头与挤出机的___ B __要求。
A、同心度B、同轴度C、垂直度D、平行度正确答案:B、同轴度答案分析:是保证机头与挤出机的同轴度要求,才能使熔体顺利通过机头。
5.口模主要成型塑件的__ B __表面,口模的主要尺寸为口模的__ D __尺寸和定型段的长度尺寸。
A、内部B、外部C、外径D、内径正确答案:B、外部D、内径答案分析:由口模的内径尺寸来成型管材塑件的外部表面。
6.分流器的作用是对塑料熔体进行__ D __,进一步__ C __。
A、分流B、成型C、加热和塑化D、分层减薄正确答案:D、分层减薄C、加热和塑化答案分析:塑料熔体经过过滤网后,经过分流初步形成管状(原为实心),即分层减薄;由于机头上有加热器,所以塑料被进一步加热和塑化。
7.管材的拉伸比是指__ D __在成型区的环隙截面积与管材截面积之比。
A、分流器和分流器支架B、机头体和芯棒C、定径套D、口模和芯棒正确答案:D、口模和芯棒答案分析:管材的拉伸比是口模和芯棒的环隙截面积与管材成型后的截面积之比拉伸比。
- 1、下载文档前请自行甄别文档内容的完整性,平台不提供额外的编辑、内容补充、找答案等附加服务。
- 2、"仅部分预览"的文档,不可在线预览部分如存在完整性等问题,可反馈申请退款(可完整预览的文档不适用该条件!)。
- 3、如文档侵犯您的权益,请联系客服反馈,我们会尽快为您处理(人工客服工作时间:9:00-18:30)。
挤压模具设计思考题1、基本概念平模、锥模、正锥模、倒锥模、舌比、比周长、阻碍角、促流角、分流比、宽展量、宽展变形率、比压正锥模:操作时顺着挤压方向装入模支承内,其锥角一般为1°30´~4°。
倒锥模:操作时逆着挤压方向装入模支承内,其锥角一般取6°。
舌比:包围的空间面积与开口宽度平方的比值。
比周长:型材断面周长(或某一部分的周长)与其所包围的截面面积的比值。
阻碍角:在型材壁较厚处的模孔入口侧做一个小斜面,以增加金属的流动阻力,该斜面与模子轴线的夹角叫阻碍角。
促流角:在型材壁较薄处的模孔入口端面处做一个促流斜面,该斜面与模子平面间的夹角叫促流角。
分流比:各分流孔的断面积(∑F分)与型材断面积(F型)之比。
宽展量△B :铸锭经宽展变形以后的最大宽度B2与挤压筒直径D1之差。
宽展变形率δB:δB =(B2-B1)/B1×100% ,B2 、B1——宽展模出、入口宽度。
2、从模具的整体结构上可将挤压模具分成那几类,各自的主要用途是什么?答:按模具结构形式可分为:整体模、拆卸模、组合模、专用模具。
整体模:模子是由一块钢材加工制造。
广泛用于挤压铝合金型、棒、管材。
拆卸模:由数块拼装组成一整体模子。
用于生产阶段变断面型材。
模子是由大头和小头两部分构成。
而这两部分又分别由多块组装而成。
组合模:用于生产内径较小的管材、各种断面形状的空心型材。
专用模具——如水冷模、宽展模等等。
3、根据模孔压缩区的形状,可将挤压模具分那几种?最常用的是什么模子,主要用于挤压什么产品?答:平模、锥形模、平锥模、流线形模和双锥模等;平模:挤压铝合金型材、棒材,镍合金、铜合金管、棒材。
锥模:挤压铝合金管材,高温合金钨、钼、锆等。
4、分流模、舌型模都是用于挤压空心制品的,他们各自的优缺点是什么,适用于挤压什么产品?答:桥模(舌形模):所需的挤压力较小,焊合室中延伸系数大,主要用于挤压硬合金空心型材。
但挤压残料较多。
平面分流模:多用于挤压变形抗力低、焊合性能好的软合金空心型材。
残料较少。
5、平模和锥模各自有什么优缺点,适合挤压什么样的产品,为什么?答:平模:α=90°。
挤压时,可以,形成较大的死区,从而获得优良的制品表面。
但是,倘若死区发生断裂时,则会在制品表面发生起皮或分层。
挤压力较大,特别在较高温度和高强度的合金是,模孔会因塑性变形而变小。
应用:挤压铝合金型材、棒材,镍合金、铜合金管、棒材。
锥模:当α=45~60°时,挤压力最小;当α=45~50°时,死区很小,甚至消失。
应用:挤压有色金属时通常选择α=60~65°。
挤压铝合金管材,高温合金钨、钼、锆等。
6、为下列铝合金挤压产品选择较合适的挤压模具:无缝圆管材、棒材、直角型材、舌比较小的半空心型材(普通平面模)、纯铝空心型材、2A11硬铝合金空心型材(舌型模)、宽度等于挤压筒直径的排材(宽展模)7、锥模设计时,如何选择模角?答:锥模:当α=45~60°时,挤压力最小;当α=45~50°时,死区很小,甚至消失。
挤压有色金属时通常选择α=60~65°。
8、模具工作带的作用是什么?确定工作带长度的原则是什么?答:工作带的作用:稳定制品尺寸,保证制品表面质量。
工作带长度的确定原则:A、工作带的最小长度,应按照挤压时能保证制品断面尺寸的稳定性和工作带的耐磨性来确定。
一般最短1.5~3mm。
B、工作带的最大长度,是按照挤压时金属与工作带的最大有效接触长度来确定。
铝合金一般最长不超过15~20mm。
9、挤压模具设计时,为什么要设计入口圆角?答:模孔入口圆角半径r的作用:防止低塑性合金挤压时产生表面裂纹;减轻金属在进入工作带时产生的非接触变形;减轻高温挤压时模子入口棱角被压秃而很快改变模孔尺寸。
10、在什么情况下要设计多孔模,多孔模设计时如何合理布置模孔?答:挤压直径较小的棒材、简单断面的小规格型材、线坯等时,为提高挤压机生产效率,避免挤压比过大引起挤压力过高或挤不动等,造成锭坯过短,成品率太低等,采用多孔模挤压。
布置:a、模孔布置在距模子中心一定距离同心圆上,且各孔之间的距离相等;b、孔与孔间、模孔边部距筒壁间应保持一定距离(见表5-2)。
同心圆直径D与挤压筒直径D0有如下关系:D=D0/[a-0.1(n-2)]11、在50MN挤压机直径为360mm的挤压筒上,挤压直径为40mm棒材,合理的挤压比范围为10~15,模孔数目为多少合适?答:12、单孔型材模设计时,如何合理布置模孔?答:单孔挤压时的模孔布置(1)具有两个以上对称轴的型材,型材的重心布置在模子中心。
(2)具有一个对称轴,如果断面壁厚差不大,应使型材的对称轴通过模子的一个坐标轴,使型材断面的重心位于另一个坐标轴上。
(3)对于非对称的型材和壁厚差别很大的型材,将型材重心相对模子中心偏移一定距离,且将金属不易流动的壁薄部位靠近模子中心,尽量使金属在变形时的单位静压力相等。
(4)壁厚差不太大,但断面较复杂的型材,将型材断面外接圆的圆心布置在模子中心。
对于挤压比很大,金属流动困难或流动很不均匀的某些型材,可采用平衡模孔或增加工艺余量的方法。
13、多孔型材模设计时,如何合理布置模孔?答:多孔挤压时的模孔布置:挤压多孔型材时,模孔布置必须遵守中心对称原则,可以不遵守轴对称原则。
配置模孔时,型材断面上薄壁部分应向着模子的中心;对称性较好、壁厚差不大的型材,模孔的重心应均布在以模子重心为圆心的圆周上。
为了保证模子强度,多孔型材模的模孔之间也应保持一定距离。
为了保证制品的质量,模孔边缘与挤压筒壁之间的距离不能太小,避免制品边缘出现成层缺陷。
14、多孔模设计时,为什么模孔既不能过于靠近边缘(挤压筒壁),也不能过于靠近模子中心位置?答:因为会降低模子的强度和导致死区流动,从而恶化制品表面质量出现起皮和分层等缺陷。
15、多孔模设计时,为什么通常不在模子中心位置布置模孔?答:模孔离模子中间的距离不同,金属流动速度有差异的现象,越靠近模子中心的金属越容易流动。
在制品表面的内侧出现裂纹。
16、不等壁型材模设计时,如何确定不同壁厚处的模孔工作带长度?答:当型材断面较复杂,仅依靠合理布置模孔难以消除金属流动不均时,可采用不等长工作带。
即:型材断面壁厚处的工作带长度大于壁薄处。
也就是说比周长小的部分工作带长度大于比周长大的部分。
17、在型材模具设计时,如何平衡模孔不同部位金属的流动速度?答:(1)合理布置模孔(2)确定合理的工作带长度(3)设计阻碍角或促流角(4)采用平衡模孔(5)附加筋条(6)设计导流模或导流腔18、在槽形型材模具设计时,为什么型材模孔的角度应增大1°~2°,设计成91°~92°,而且型材底部的模孔尺寸应适当扩大0.1~0.8mm?答:在挤压时模子受压力后要产生弹性弯曲变形,会导致金属不能与工作带全部接触,因此对于易发生并口的角材,设计时模孔角度应增大1°~2°;对于易发生扩口的槽形型材,设计时角度应减小1°~2°。
19、分流模主要由那几部分构成,焊合室的主要作用是什么?答:平面分流组合模一般是由阳模(上模),阴模(下模),定位销,联结螺钉四部分组成。
焊合室是把分流孔流出来的金属汇集在一起重新焊合起来形成以模芯为中心的整体坯料,由于金属不断聚集,静压力不断增大,直至挤出模孔。
20、型材模孔设计时,模孔尺寸要比型材的名义尺寸大一些,这是为什么?答:因为考虑到型材和模子的冷却收缩;工作带在载荷作用下的畸变;由于不均变形引起的拉缩变形;因金属在流入模孔时不能急转弯而引起的非接触变形;型材在拉伸矫直时的断面尺寸收缩。
同时,还注意到在型材拉伸矫直时,无论在长度上,还是在断面上,各部分的变化是不同的。
21、分流模设计中,为什么要将模孔置于分流桥下面?如果模孔不能完全被桥遮蔽,工作带尺寸如何确定?答:从增大分流比、降低挤压力来考虑,分流桥宽度B应选择得小些,但从改善金属流动均匀性来考虑,模孔最好受到分流桥的遮蔽,则B应选择得宽些。
处于分流桥底下的模孔由于金属流进困难,作为模腔工作带长度的最短处,此处工作带的长度可取型材壁厚的两倍。
壁厚较厚或金属容易流动和供料较充分的地方,工作带长度可适当加长。
暴露在分流孔中的工作带长度,可取桥下的2倍。
22、分流比大小对于挤压制品的焊合质量有何影响?为什么?答:分流比K的大小直接影响到挤压阻力的大小,制品成型和焊合质量。
K值越大,越有利于金属流动与焊合,也可减少挤压力。
因此,在模具强度允许的范围内,应尽可能选取较大的K值。
在一般情况下,生产空心型材时,取K=10~30;生产管材时,取K=8~15。
23、分流模设计时,模芯为什么要伸出模孔工作带一定长度?答:模芯的长度宜短,稍伸出定径带即可。
过长易使管子偏心;过短则易形成椭圆。
对于小挤压机模芯可伸出模子定径带1 ~ 3㎜;对于大吨位挤压机可伸出10 ~ 12㎜。
24、焊合室的大小、形状对挤压制品的质量有何影响?答:圆形焊合室:在两分流孔之间会产生—个十分明显的死区,不仅增大挤压阻力,而且会影响焊缝质量。
蝶形焊合室:有利于消除这种死区,提高焊缝质量。
25、焊合室高度对制品的焊合质量有何影响?答:焊合室高度:焊合腔的容积越大,焊合腔的截面积与制品断面之比越大,则焊合腔所建立起来的静水压力就越大;焊合室越深,金属在焊合腔中停留的时间也越长,因而,焊接的质量就越高,可能采用的挤压速度也就越大。
焊合室太浅时,由于摩擦力太小,不能建立起足够的反压力,使焊合压力不足,导致焊合不良。
同时,还限制了挤压速度的提高。
太深时,会影响模芯的稳定性,易出现空心制品壁厚不均匀现象。
同时分离残料后,积存金属过多,会降低成品率,影响制品质量。
26、一般来说,焊合室高度越大,制品的焊合质量越好,但易造成制品偏心,这是为什么?答:焊合室越深,金属在焊合腔中停留的时间也越长,因而,焊接的质量就越高,可能采用的挤压速度也就越大。
太深时,会影响模芯的稳定性,易出现空心制品壁厚不均匀现象。
同时分离残料后,积存金属过多,会降低成品率,影响制品质量。
27、挤压模具设计中为什么要设计“空刀”,空刀尺寸大小对产品质量和模具寿命有何影响?答:影响:空刀量过大,定径带的支承减弱,在冲击载荷和闷车的情况下可能把定径带压坏;空刀量过小,易划伤制品表面。
28、宽展模挤压的基本原理是什么?答:宽展挤压原理:在圆挤压筒的前端增加一个宽展模,使圆锭产生预变形,厚度变薄,宽度逐渐增加到大于圆挤压筒直径,然后再从模孔中流出的挤压过程。
29、导流模挤压的基本原理是什么?答:原理:铸锭镦粗后,先通过导流模产生预变形,金属进行第一次分配,形成与型材断面相似的坯料,然后进行第二次变形,挤出型材。