第四章 化学气相沉积
化学气相沉积法的原理和材料制备

化学气相沉积法的原理和材料制备化学气相沉积法(Chemical Vapor Deposition,简称CVD)是一种常用于材料制备的技术方法。
它利用气体化学反应,在高温下生成固态材料,并将其沉积在基底表面上形成薄膜或纳米结构。
CVD方法广泛应用于半导体、纳米材料、涂层等领域,并在电子、光学、能源等产业中发挥重要作用。
CVD的原理是利用气体在高温下分解反应,生成高纯度材料。
首先,将所需材料的前体化合物(一种或多种)以气体形式引入反应室。
然后,通过加热反应室使其达到适宜的温度,并在此温度下维持一定时间。
在高温下,前体分子会分解为活性物种(如原子、离子或自由基),这些活性物种与基底表面发生反应,生成所需材料的沉积物。
反应过程中,通常还会加入载气(如氢气)以稀释和传递反应物质。
CVD方法提供了一种有效的材料制备手段,其优势在于能够实现高纯度、均匀性好的材料生长,并且可以控制沉积速率和沉积形貌。
其适用范围广泛,不仅可以制备块体材料,也可以制备薄膜、纳米颗粒等纳米结构材料。
此外,CVD还可以在不同的温度下进行,因此能够适应多种材料的生长需求。
CVD方法主要分为热分解CVD、化学气相沉积CVD和物理气相沉积CVD等几种类型。
在热分解CVD中,通过加热气体源使之分解,产生所需材料的沉积物。
这种方法常用于制备碳纳米管、金属纳米线等纳米结构材料。
在化学气相沉积CVD中,主要利用气体的化学反应生成沉积物。
通过选用合适的前体化合物及反应条件,可以实现对材料成分和结构的控制。
物理气相沉积CVD则是通过物理过程实现材料的沉积,如物理吸附或辐射捕捉。
CVD方法可以制备多种材料,例如二氧化硅、氮化硅、氮化铝、碳化硅等。
其中,二氧化硅是一种广泛应用于微电子器件中的重要材料。
通过CVD方法可以在硅基底上沉积高纯度、均匀性好的二氧化硅薄膜,用于制备晶体管、电容器等器件。
同样,氮化硅和氮化铝等氮化物材料也可以通过CVD方法制备,用于制备高能效LED、功率器件等光电子器件。
化学气相沉积

集成电路芯片工艺化学气相沉积(CVD)化学汽相淀积(CVD)化学汽相淀积是指通过气态物质的化学反应在衬底上淀积一层薄膜材料的过程。
CVD膜的结构可以是单晶、多晶或非晶态,淀积单晶硅薄膜的CVD过程通常被称为外延。
CVD技术具有淀积温度低、薄膜成分和厚度易于控制、均匀性和重复性好、台阶覆盖优良、适用范围广、设备简单等一系列优点。
利用CVD方这几乎可以淀积集成电路工艺中所需要的各种薄膜,例如掺杂或不掺杂的SiO:、多晶硅、非晶硅、氮化硅、金属(钨、钼)等。
一:化学气相沉积方法常用的CVD方法主要有三种:常压化学汽相淀积(APCVD)、低压化学汽相淀积(LPCVIi~)和等离子增强化学汽相淀积(PECVD).APCVD反应器的结构与氧化炉类似,如图1-1所示,该系统中的压强约为一个大气压,因此被称为常压CVD。
气相外延单晶硅所采用的方法就是APCVD。
图1-1APCVD反应器的结构示意图,LPCVD反应器的结构如图1-2所示,石英管采用三温区管状炉加热,气体由一端引入,另一端抽出,半导体晶片垂直插在石英舟上。
由于石英管壁靠近炉管,温度很高,因此也称它为热壁CVD装置,这与利用射频加热的冷壁反应器如卧式外延炉不同.这种反应器的最大特点就是薄膜厚度的均匀性非常好、装片量大,一炉可以加工几百片,但淀积速度较慢.它与APCVD的最大区别是压强由原来的1X10SPa降低到1X102Pa左右。
图1-2LPCVD反应器的结构示意图图1-3平行板型PECVD反应器的结构示意图PECVD是一种能量增强的CVD方法,这是因为在通常CVD系统中热能的基础上又增加了等离子体的能量.图1-3给出了平行板型等离子体增强CVD反应器,反应室由两块平行的金属电极板组成,射频电压施加在上电极上,下电极接地。
射频电压使平板电极之间的气体发生等离子放电。
工作气体由位于下电极附近的进气口进入,并流过放电区。
半导体片放在下电极上,并被加热到100—400;C左右.这种反应器的最大优点是淀积温度低。
化学气相沉积法
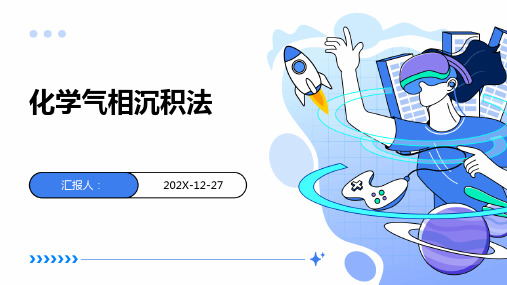
时间与速率
要点一
总结词
时间和沉积速率在化学气相沉积过程中具有重要影响,它 们决定了薄膜的厚度和均匀性。
要点二
详细描述
时间和沉积速率决定了化学气相沉积过程中气体分子在反 应器中的停留时间和沉积时间。较长的停留时间和较慢的 沉积速率有利于气体分子充分反应和形成高质量的薄膜。 然而,过长的停留时间和过慢的沉积速率可能导致副反应 或降低沉积速率。因此,选择合适的时间和沉积速率是实 现均匀、高质量薄膜的关键。
05
化学气相沉积法优 缺点
优点
适用性广
涂层性能优良
化学气相沉积法适用于各种材料表面改性 和涂层制备,如金属、陶瓷、玻璃等。
通过控制化学气相沉积的条件,可以制备 出具有高硬度、高耐磨性、高抗氧化性的 涂层。
环保
高效
化学气相沉积法使用的原料在高温下分解 ,不会对环境造成污染。
化学气相沉积法具有较高的沉积速率,可 实现快速涂层制备。
应用领域
半导体产业
用于制造集成电路、微 电子器件和光电子器件
等。
陶瓷工业
制备高性能陶瓷材料, 如氧化铝、氮化硅等。
金属表面处理
在金属表面形成耐磨、 防腐、装饰等功能的涂
层。
其他领域
在航空航天、能源、环 保等领域也有广泛应用
。
02
化学气相沉积法分 类
热化学气相沉积法
原理
在较高的温度下,使气态的化 学反应剂与固态表面接触,通 过气相反应生成固态沉积物。
缺点
高温要求
化学气相沉积法需要在高温下进行,这可能会对 基材产生热损伤或变形。
操作难度大
化学气相沉积法需要精确控制反应条件,操作难 度较大。
ABCD
设备成本高
第四章CVD工艺优质获奖课件

CVD反应是指反应物为气体而生成物之一为固体旳
化学反应。
CVD完全不同于物理气相沉积(PVD)
一、化学气相沉积旳基本原理
☞化学气相沉积旳基本原理
➢ CVD
CVD法实际上很早就有应用,用于材料精制、装
饰涂层、耐氧化涂层、耐腐蚀涂层等。
在电子学方面PVD法用于制作半导体电极等。
CVD法一开始用于硅、锗精制上,随即用于适合
➢ CVD法制备薄膜过程描述
(1)反应气体向基片表面扩散;
(2)反应气体吸附于基片表面;
(3)在基片表面发生化学反应;
(4)在基片表面产生旳气相副产物脱离表面,向空间扩
散或被抽气系统抽走;
(5)基片表面留下不挥发旳固相反应产物——薄膜。
CVD基本原理涉及:反应化学、热力学、动力学、输
运过程、薄膜成核与生长、反应器工程等学科领域。
化学气相沉积工艺(CVD)
一、化学气相沉积旳基本原理
二、化学气相沉积旳特点
三、CVD措施简介
一、化学气相沉积旳基本原理
☞化学气相沉积旳基本原理
➢化学气相沉积旳定义
化学气相沉积是利用气态物质经过化学反应在基片
表面形成固态薄膜旳一种成膜技术。
化学气相沉积(CVD)
——Chemical Vapor Deposition
外延生长法制作旳材料上。
表面保护膜一开始只限于氧化膜、氮化膜等,之
后添加了由Ⅲ、Ⅴ族元素构成旳新旳氧化膜,近来还
开发了金属膜、硅化物膜等。
以上这些薄膜旳CVD制备法为人们所注意。CVD
法制备旳多晶硅膜在器件上得到广泛应用,这是CVD
法最有效旳应用场合。
一、化学气相沉积旳基本原理
☞化学气相沉积旳基本原理
化学气相沉积法PPT课件

CVD法是一种化学反应法,应用非常广泛,可制备多种物 质的薄膜,如单晶、多晶或非晶态无机薄膜,金刚石薄膜, 高Tc超导薄膜、透明导电薄膜以及某些敏感功能的薄膜。
2020/10/13
3
化学气相沉积薄膜的特点:
• 由于CVD法是利用各种气体反应来组成薄膜,所以可 以任意控制薄膜的组成,从而制得许多新的膜材。
化学气相沉积法
2020/10/13
姓名:尤凤霞 08材成
1
• 一.化学气相沉积的概念 • 二.化学气相沉积薄模的特点 • 三.化学气相沉积的分类 • 四.化学气相沉积的基本工艺流程 • 五.化学气相沉积的工艺方法
2020/10/13
2
ห้องสมุดไป่ตู้ 化学气相沉积的概念:
化学气相沉积(英文:Chemical Vapor Deposition,简称 CVD)是通过气相物质的化学反应的基材表面上沉积固态薄 膜的一种工艺方法。是一种用来产生纯度高、性能好的固 态材料的化学技术。各种化学反应,如分解、化合、还原、 置换等都可以用来沉积于基片的固体薄膜,而反应多余物 (气体)可以从反应室排出。
1.气溶胶辅助气相沉积 (AACVD):使用液体/气体的气溶胶的 前驱物成长在基底上,成长速非常快。此种技术适合使用 非挥发的前驱物。
2.直接液体注入化学气相沉积 (DLICVD):使用液体 (液体或固 体溶解在合适的溶液中) 形式的前驱物。
等离子技术分类
20203/1.0/微13 波等离子辅助化学气相沉积, (MPCVD)
6
4.等离子增强化学气相沉积 (PlECVD):利用等离 子增加前驱物的反应速率。PECVD技术允在低 温的环境下成长,这是半导体制造中广泛使用 PECVD的最重要原因。
化学气相沉积
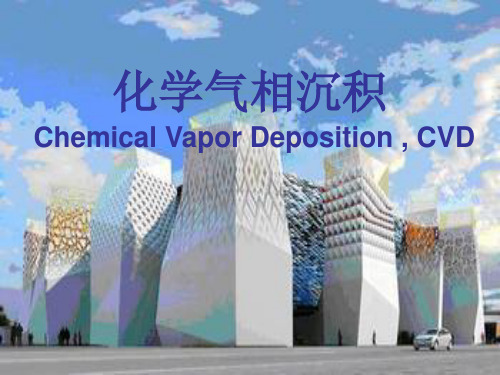
化学气相沉积作为一种非常有效的材料表 面改性方法,具有十分广阔的发展应用前景。 随着工业生产要求的不断提高, CVD 的工艺 及设备得到不断改进, 现已获得了更多新的 膜层, 并大大提高了膜层的性能和质量,它 对于提高材料的使用寿命、改善材料的性 能、节省材料的用量等方面起到了重要的 作用,下一步将向着沉积温度更低、有害生 成物更少、规模更大等方向发展。随着各 个应用领域要求的不断提高, 对化学气相沉 积的研究也将进一步深化,CVD 技术的发展 和应用也将跨上一个新的台阶。
2、CVD过程 反应气体向基体表面扩散
反应气体吸附于基体表面
在基体表面上产生的气相副产物脱离表面
留下的反应产物形成覆层
3、CVD几种典型化学反应
1)热分解
SiH4 >500℃ Si + 2H2 (在900-1000℃成膜) CH3SiCl3 1400℃ SiC + 3HCl
2)还原
WF6 +3H2 SiCl4 + 2Zn WF6 + 3 Si 2 W + 6HF (氢还原) Si + 2ZnCl2 (金属还原) SiF4 (基体材料还原) W+3 2
反应沉积成膜 反应沉积成膜
3、PCVD的特点
成膜温度低
沉积速率高 膜层结合力高
膜层质量好 能进行根据热力学规律难以发生的反应
4、PCVD与CVD装置结构相近, 只是需要增加能产生等离子体 的反应器。用于激发CVD反应 的等离子体有: 直流等离子体 射频等离子体 微波等离子体 脉冲等离子体
直流等离子体法(DCPCVD)
2、PCVD的成膜步骤 等离子体产生 等离子体产生
辉光放电的压力较低,加 速了等离子体的质量 输送和扩散
化学气相沉积法ppt课件

优点:可以在热敏感的基体上进行沉积;
缺点:沉积速率低,晶体缺陷密度高,膜中杂质 多。
原料输送要求:把欲沉积膜层的一种或几种组分 以金属烷基化合物的形式输送到反应区,其他 的组分可以氢化物的形式输送。
精选ppt
(A)CVD的原理
CVD的机理是复杂的,那是由于反应气体中不同 化学物质之间的化学反应和向基片的析出是同 时发生的缘故。
基本过程:通过赋予原料气体以不同的能量使其 产生各种化学反应,在基片上析出非挥发性的 反应产物。
图3.14表示从TiCl4+CH4+H2的混合气体析出 TiC过程的模式图。如图所示,在CVD中的析出 过程可以理解如下:
精选ppt
7
⑥绕镀性好:可在复杂形状的基体上及颗粒材 料上沉积。
⑦气流条件:层流,在基体表面形成厚的边界 层。
⑧沉积层结构:柱状晶,不耐弯曲。通过各种 技术对化学反应进行气相扰动,可以得到细晶 粒的等轴沉积层。
⑨应用广泛:可以形成多种金属、合金、陶瓷和 化合物沉积层
精选ppt
8
(2)CVD的方法
LCVD技术的优点:沉积过程中不直接加热整块 基板,可按需要进行沉积,空间选择性好,甚 至可使薄膜生成限制在基板的任意微区内;避 免杂质的迁移和来自基板的自掺杂;沉积速度
比2
(D)超声波化学气相沉积(UWCVD)
定义:是利用超声波作为CVD过程中能源的一种 新工艺。
①常压CVD法; ②低压CVD法; ③热CVD法; ④等离子CVD法; ⑤间隙CVD法; ⑥激光CVD法; ⑦超声CVD法等。
精选ppt
14
(C)CVD的流程与装置
化学气相沉积解读
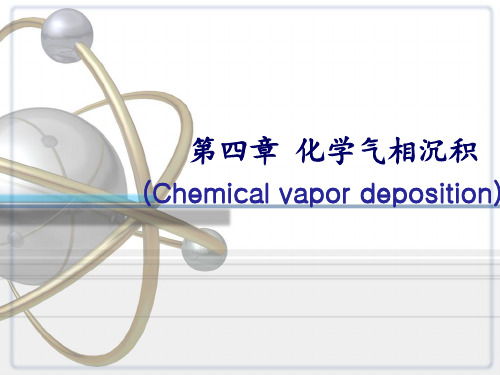
由上图分析可知: 高温:扩散控制 低温:表面反应控制 反应导致的沉积速率为:
其中 N0 为表面原子密度。 沉积速率随温度的变化规律取决于Ks,D,δ 等随温度的变化情况。 因此,一般而言,化学反应或化学气相沉积的速度将随温度的升 高而加快。 但有时并非如此,化学气相沉积的速率随温度的升高 出现先升高后降低的情况。 这是什么原因呢?
第四章 化学气相沉积
(Chemical vapor deposition)
•
•
4.4 薄膜生长动力学 4.5 化学气相沉积装置
4.4 薄膜生长动力学
在CVD过程中,薄膜生长过程取决于气体与衬底间界面
的相互作用,具体过程如下: 1. 反应气体扩散通过界面 层 2. 气体分子在薄膜或衬底 表面的吸附 3. 原子表面的扩散、反应 和溶入薄膜晶格之中 4. 反应产物扩散离开衬底 表面并通过界面层
此式表明:Si的沉积速度将随着距离的增加呈指数 趋势下降,即反应物将随着距离的增加逐渐贫化。
•
轴向生长速率的均匀性:
•
扩散速度小于气流速度
•
沉积速率随距离的增加呈指数下降! 倾斜基片使薄膜生长的均匀性得以改善 ;
提高气体流速v和装置的尺寸b 调整装置内温度分布,影响扩散系数D的分布
因此,提高沉积均匀性可以采取如下措施:
我们用CVD方法共同的典型式子来说明: 设这一反应正向进行时为放热反应,则
aA( g ) bB( g ) cC (s) dD( g )
ΔH<0, U0<U
上式描述的正向和逆向反应速率如下页图a所示,均随 温度上升而提高。同时,正向反应的激活能低于逆向反应 的激活能。而净反应速率应是正反向反应速率之差,而他 随温度升高时会出现一个最大值。因此温度持续升高将会 导致逆反应速度超过正向的,薄膜的沉积过程变为薄膜的 刻蚀过程。
第四章化学气相沉积

设在生长中的薄膜表面形成了界面层,其厚度为,cg和cs分别为 反应物的原始浓度和其在衬底表面的浓度,则
扩散至衬底表面的反应物的通量为: 衬底表面消耗的反应物通量与Cs成正比
平衡时两个通量相等,得
F1 hg (Cg Cs )
F2 ksCs
F1 F2
Cs
Cg 1 ks
hg
hg为气相质量输运系数,Ks为表面化学反应速率常数
4. 氧化反应 利用氧气作为氧化剂促进反应:
SiH4(g) + O2 = SiO2(s) + H2O(g) (450℃) Si(C2H5O)4 + 8O2 = SiO2 + 10H2O + 8CO2
(Si(C2H5O)4是正硅酸乙酯 简称TEOS)
SiCl4 + O2 = SiO2 + 2Cl2 GeCl4 + O2 = GeO2 + 2Cl2
1) 反应物的
质量传输 气体传送
2) 薄膜先驱 物反应
3) 气体分 子扩散
4) 先驱物 的吸附
CVD 反应室
副产物
7) 副产物的解吸附作用
8) 副产物去除
排气
5) 先驱物扩散 到衬底中
6) 表面反应
连续膜
衬底
第四章 化学气相沉积----4.2 化学气相沉积
二、CVD动力学分析 1、CVD模型(Grove模型)
薄膜的生长过程取决于气体与衬底间界面的相互作用, 可能涉及以下几个步骤: (1)反应气体从入口区域流动到衬底表面的淀积区域 (2)气相反应导致膜先驱物(组成膜最初的原子或分
子)和副产物的形成 (3)膜先驱物附着在衬底表面
第四章 化学气相沉积----4.2 化学气相沉积
化学气相沉积原理
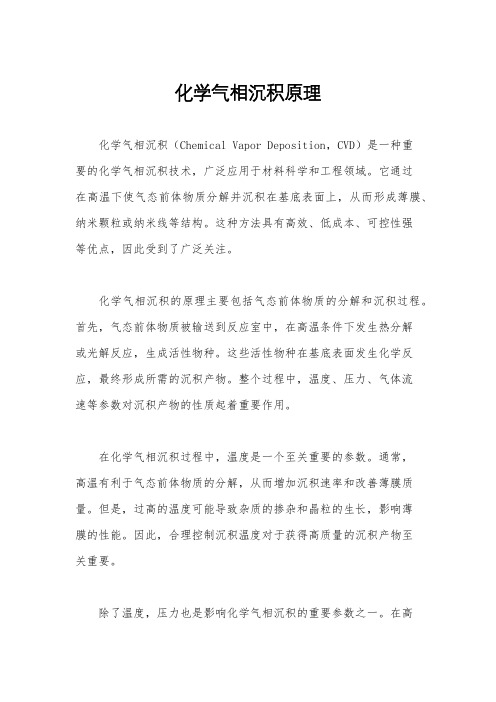
化学气相沉积原理化学气相沉积(Chemical Vapor Deposition,CVD)是一种重要的化学气相沉积技术,广泛应用于材料科学和工程领域。
它通过在高温下使气态前体物质分解并沉积在基底表面上,从而形成薄膜、纳米颗粒或纳米线等结构。
这种方法具有高效、低成本、可控性强等优点,因此受到了广泛关注。
化学气相沉积的原理主要包括气态前体物质的分解和沉积过程。
首先,气态前体物质被输送到反应室中,在高温条件下发生热分解或光解反应,生成活性物种。
这些活性物种在基底表面发生化学反应,最终形成所需的沉积产物。
整个过程中,温度、压力、气体流速等参数对沉积产物的性质起着重要作用。
在化学气相沉积过程中,温度是一个至关重要的参数。
通常,高温有利于气态前体物质的分解,从而增加沉积速率和改善薄膜质量。
但是,过高的温度可能导致杂质的掺杂和晶粒的生长,影响薄膜的性能。
因此,合理控制沉积温度对于获得高质量的沉积产物至关重要。
除了温度,压力也是影响化学气相沉积的重要参数之一。
在高压条件下,气态前体物质的浓度增加,有利于沉积速率的提高。
但是,过高的压力可能导致气体的对流扩散受到限制,从而影响沉积产物的均匀性和致密性。
因此,合理控制沉积压力对于获得均匀致密的沉积产物至关重要。
此外,气体流速和反应时间等参数也对化学气相沉积过程起着重要作用。
合理控制这些参数,可以实现沉积产物的精确控制和优化,从而满足不同应用领域的需求。
总的来说,化学气相沉积技术具有很高的灵活性和可控性,可以制备多种材料和结构。
通过合理控制反应条件和参数,可以实现对沉积产物性质的精确调控,满足不同应用领域的需求。
因此,化学气相沉积技术在材料科学和工程领域具有广阔的应用前景。
材料合成与制备 第4章 CVD合成

沉积温度对氧化锌纳米材料形貌的影响
纳米氧化锌是重要的紫外发光材料,其在紫、蓝、绿光发光二极管 和激光器以及紫外探测器等方面显示了巨大的应用潜力,对于提高 光记录密度和光信息的存取速度将起到非常重要的作用。以氧化锌 粉为原料,采用化学气相沉积方法,在无需使用催化剂的情况下, 通过调控沉积温度分别得到了棒状、线状和螺旋状等形状各异的氧 化锌纳米材料。
化学气相沉积法制备GaN薄膜
GaN微纳米材料,由于其具有热产生率低、抗辐射、击穿电压高、电 子饱和漂移速度大和介电常数小的优点,已被广泛应用在高频、高温、高压 电子器件领域、发光二级管(LED) 、半导体激光器(LD)和太阳能电池等方面。
硅基底的CVD扩磷工艺
单晶硅的主要用途是用作半导体材料、利用太阳能光伏发电和供热等。 掺杂后的单晶硅可用于薄膜衬底材料、超大规模集成电路及太阳能电池。
Si基底CVD扩磷工艺如下: (1)向高温炉中通入氩气,当高温炉中的气压与外界气压相同时,气 体将高温炉门顶开,关闭气体。 (2)将清洗好的硅基底放在瓷舟上,该位置为高温炉第1温区。将红 磷装满2个瓷舟,关闭炉门。 (3)用氩气清洗气路和高温炉腔体3遍,关闭氩气,打开机器泵开始 抽真空。 (4)抽真空30 min后,打开升温系统开始升温,升温时间为2 h。 (5)当温度升到扩磷温度(1050/1150℃)时,通过高温热扩散运动向 硅基底扩磷。 (6)当达到实验时间后,通入氩气,当高温炉内温度降到室温后将样 品取出待检测。
第四章 化学气相沉积
一、化学气相沉积法的概念
第四章--薄膜的化学气相沉积

压力梯度驱动的扩散过程使得该组元得以不 断到达衬底表面。
降低压力(提高扩散系数Di)将有利于提高气体 的扩散通量,加快化学反应进行的速度。
低压CVD就是利用这一原理,即采用了降低沉 积室压力的办法,加快气体组分的扩散和促 进化学反应的进行。
27
(四)表面吸附及表面化学反应
气体组分在扩散至薄膜表面后,还要经 过表面吸附、表面扩散、表面反应、反 应产物脱附等多个过程,才能完成薄膜 的沉积过程。
30
对CVD过程来说,尤其是当衬底温度 很低或者衬底表面已经被吸附分子 覆盖的情况下,Sc的数值可能很小; 而在气相与固相处于平衡下,Sc=0。
31
假设从物理吸附向化学吸附的转化过程为一 个一级反应,速率为
Rr krns krns0 (4- 54), 式中,kr为相应过程的速度常;数 ns、ns0分别为表面物理吸附子分的面密度 以及吸附分子可以占位据置的面密度。
20
二级反应 A+B=C+D (4-42) A、B两组元参加的正反应过程反应速率等于
R
knAnB
k
pApB (kT)2
(443)
式中, pA、pB为气体组A元 、B的分压; nA、nB为组元体密度
同样,两个组元A的分子参与的过程也属于二 级反应,这时,反应速率为
RknA2k(kp2A T )2 (4-44)
21
反应速度常数
k
k0e
E
RT,其
中K0系
数,
E为 反 应 过 程 的 激 活 能
图4.10示意性地画 出了化学反应从状 态1至状态2的自由 能变化曲线
22
反应总速率应正比于
Rk0n1e-RG*T-k0-n2e-G*RTG (4-47) G*和G*+G相 当 于 正 向 和 逆的向激反活应能 k0、k0-分 别 是 正 反 方 向速反度应常的数 的 系
第4章薄膜的化学气相沉积
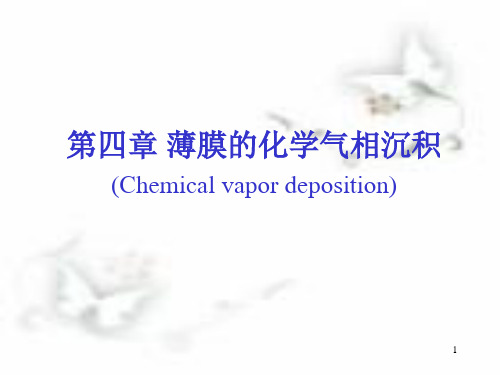
一、化学反应的自由能变化
1、化学反应的自由能判定式 对于一个化学反应总可以表达为: aA+bB=cC 自由能变化:△G=cGc-aGA-bGB 其中a、b、c分别为反应物和产物的mol数 Gi—是每mol i物质的自由能。 i=A,B, C 0 对于每种反应物:Gi Gi RT ln ai
①+② ×3,得到 总反应为:
1 CO 2 ( g ) CO( g ) O 2 ( g ) 2
②
△G0 =195.5kJ/mol
2YCl3 ( g ) 3CO2 ( g ) Y2O3 (s) 3CO( g ) 3Cl2 ( g )
此时, G0 195.5 3 248.7 337.8KJ / mol
27
这一自由能变化决定了反应将过于趋向于向左进行。 d)再用YBr3代替YCl3
2YBr3 g 3CO2 g Y2O3 s 3CO g 3Br2 g
此时:△G 0 = -450.8+337.8= -113 kJ/mol
•与此相对应的平衡条件要求:当系统的总压力为 0.2MPa时,YBr3的分压为1 kPa。
24
二、化学反应路线与自由能变化
1、单晶与多晶的生长条件
根据晶体的形核生长理论:要满足晶体的生长 条件,就需要新相形成自由能△G<0。
对于单晶:引入一个生长核心(△ G <0),同时要抑制其它的
晶核形成,确保单晶生长条件,就要△ G在数值上接近 于0 。显然在满足这一条件的情况下,应有相当数量的 反应物与反应产物处于一种平衡共存的状态 。
(450℃)
另外,还可以利用
SiCl 4( g ) 2H 2( g ) O 2( g ) SiO 2(s) 4HCl ( g ) (1500℃)
化学气相沉积技术在半导体工业中的应用

化学气相沉积技术在半导体工业中的应用第一章:引言化学气相沉积技术(Chemical Vapor Deposition, CVD)是在气相条件下通过化学反应在固体表面上沉积出薄膜的一种重要技术。
近年来,随着半导体工业的不断发展,CVD技术在半导体工业中得到了广泛应用。
本文将重点介绍CVD技术在半导体工业中的应用。
第二章:CVD技术的原理与分类2.1 CVD技术的原理CVD技术是一种化学反应技术,其基本原理是将气态反应物在一定条件下传输到反应室中,与基板表面上的化学物种反应,从而在基板表面上形成所需薄膜。
传统的CVD技术基于热解原理,即通过加热反应室使反应物分解并在基板表面上沉积形成薄膜。
而PLD、ALD等技术则是基于激光或等离子体等方式进行反应,由于反应条件不同,CVD技术也可以被分类为热CVD、光化学CVD、等离子体CVD、水热CVD等类型。
2.2 CVD技术的分类根据CVD技术反应物输送方式的不同,CVD技术也可以被分类为低压CVD、大气压CVD、微波CVD等类型。
其中低压CVD是指反应室内的气压低于1 kPa,主要用于制备高质量、低缺陷密度的薄膜。
大气压CVD则适用于磁性材料、非晶材料等的生长,并且由于反应室气压较大,CVD技术成本也相对较低。
而微波CVD则利用微波能量带动激励原子在反应室中进行反应,制备薄膜速度较快,且具有良好的均匀性。
第三章:CVD技术在半导体工业中的应用3.1 CVD技术在薄膜制备中的应用CVD技术在半导体工业中最为广泛的应用就是在制备各类薄膜方面。
例如CVD技术可以制备二氧化硅(SiO2)和氮化硅(Si3N4)等常用的绝缘层膜,这些薄膜被广泛应用于振荡器、电容器、光缆等领域。
此外,CVD技术也可以制备氧化铝(Al2O3)等陶瓷材料,用于高温氧化抑制、阻挡金属杂质、光学涂层等领域。
3.2 CVD技术在半导体器件制备中的应用除了薄膜制备,CVD技术在半导体器件的制备中也扮演着重要的角色。
第4章化学气相沉积

4.2 化学气相沉积原理
对流传热 对流是流体通过自身各部的宏观流动实现热量传递的过程,它主要是借着流 体的流动而产生。 依不同的流体流动方式,对流可以区分为强制对流及自然对流两种。 强制对流是当流体因内部的“压力梯度”而形成的流动所产生的;自然对流 则是来自流体因温度或浓度所产生的密度差所导致的。 单位面积的能量对流=Ecov=hc(Ts1- Ts2) 其中:hc为“对流热传系数”
19
4.2 化学气相沉积原理
二、化学气相沉积法原理
CVD工艺并不希望反 应气体以湍流的形式 流动,因为湍流会扬 起反应室内的微粒或 微尘,使沉积薄膜的 品质受到影响
2、CVD技术的热动力学原理
输送现象:
动量传递
以“雷诺数”作为流体以何 种方式进行流动的评估依据:
Re
d v
流速与流向均 平顺者称为 “层流”;
850~9000 C
3SiCl4 N2 4H 2 SiN4 12HCl 3SiH 4 4 NH3 SiN4 12H 2
7500 C
11
4.2 化学气相沉积原理
化学输运反应:
把所需要沉积的物质作为源物质,使之与适当的气体介质发生反应并形成一 种气态化合物。这种气态化合物经化学迁移或物理载带而输运到与源区温度 不同的沉积区,再发生逆向反应生成源物质而沉积出来。这样的沉积过程称 为化学输运反应沉积。也有些原料物质本身不容易发生分解,而需添加另一 种物质(称为输运剂)来促进输运中间气态产物的生成。
10
325~4750 C
300~5000 C
4500 C
1150~12000 C
4.2 化学气相沉积原理
化学合成反应:
化学气相沉积技术
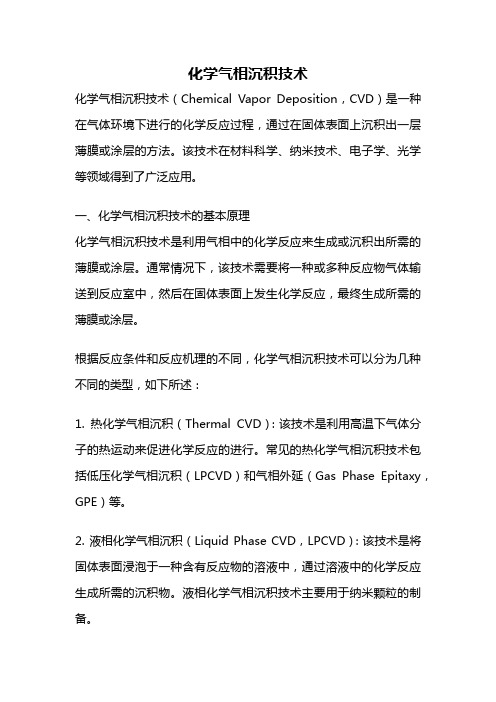
化学气相沉积技术化学气相沉积技术(Chemical Vapor Deposition,CVD)是一种在气体环境下进行的化学反应过程,通过在固体表面上沉积出一层薄膜或涂层的方法。
该技术在材料科学、纳米技术、电子学、光学等领域得到了广泛应用。
一、化学气相沉积技术的基本原理化学气相沉积技术是利用气相中的化学反应来生成或沉积出所需的薄膜或涂层。
通常情况下,该技术需要将一种或多种反应物气体输送到反应室中,然后在固体表面上发生化学反应,最终生成所需的薄膜或涂层。
根据反应条件和反应机理的不同,化学气相沉积技术可以分为几种不同的类型,如下所述:1. 热化学气相沉积(Thermal CVD):该技术是利用高温下气体分子的热运动来促进化学反应的进行。
常见的热化学气相沉积技术包括低压化学气相沉积(LPCVD)和气相外延(Gas Phase Epitaxy,GPE)等。
2. 液相化学气相沉积(Liquid Phase CVD,LPCVD):该技术是将固体表面浸泡于一种含有反应物的溶液中,通过溶液中的化学反应生成所需的沉积物。
液相化学气相沉积技术主要用于纳米颗粒的制备。
3. 辅助化学气相沉积(Assisted CVD):该技术是在化学气相沉积的过程中引入外部能量或辅助剂来促进反应的进行。
常见的辅助化学气相沉积技术包括等离子体增强化学气相沉积(Plasma Enhanced CVD,PECVD)和光辅助化学气相沉积(Photo-Assisted CVD)等。
三、化学气相沉积技术的应用领域化学气相沉积技术在材料科学、纳米技术、电子学、光学等领域有着广泛的应用。
下面列举几个常见的应用领域:1. 半导体器件制造:化学气相沉积技术可以用于制备半导体材料的薄膜,如硅、氮化硅等。
这些薄膜可以作为半导体器件的绝缘层、隔离层或介质层。
2. 硬质涂层:化学气相沉积技术可以用于制备硬质涂层,如碳化硅、氮化硼等。
这些硬质涂层具有优异的耐磨损性和高温稳定性,广泛应用于刀具、模具等领域。
化学气相沉积
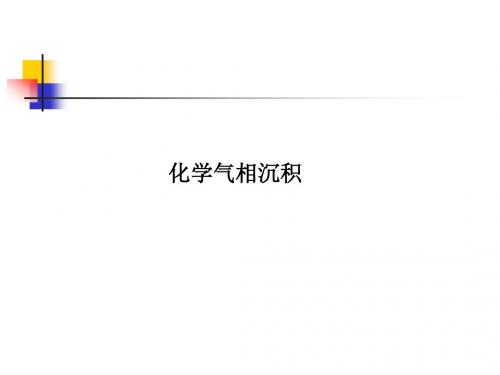
三、化学输运反应
140 ~ 240C
一、热解反应
单氨络合物已用于热解制备氮化物。
GaCl 3 NH3 GaN+3HCl
800~900C
AlCl3 NH3 AlN+3HCl
800~900C
B3 N3 H6 3BN 3H2
9001100
二、化学合成反应
两种或多种气态反应物在一热衬底上相互反应,这类反应称为化 学合成反应。
化学气相沉积合成实例 1.制备纳米级氧化物、碳化物、氮化物超细粉
A(g) + B(g) → C(s) + D(g)↑
典型的气相合成反应有: 3SiH4(g)+4NH3(g) → Si3N4(s)+12H2(g)↑ 3SiCl4(g)+4NH3(g) → Si3N4(s)+12HCl(g)↑ 2SiH4(g)+C2H4(g) → 2SiC(s)+6H2(g)↑ BCl(g)+3/2H2(g) → B(s)+3HCl(g)↑
~1200C SiCl 4 2H 2 1150 Si +4HCl
475 SiH4 2O2 325 SiO2 2H 2O 1250C TiCl4 N2 H 2 1200 2TiN 8HCl
C Al2 (CH3 )6 12O2 450 Al2O3 9H2O
第四章 化学气相沉积讲解

设在生长中的薄膜表面形成了界面层,其厚度为,cg和cs分别为 反应物的原始浓度和其在衬底表面的浓度,则
扩散至衬底表面的反应物的通量为: 衬底表面消耗的反应物通量与Cs成正比
平衡时两个通量相等,得
F1 hg (Cg Cs )
F2 ksCs
F1 F2
Cs
Cg 1 ks
hg
hg为气相质量输运系数,Ks为表面化学反应速率常数
第四章 化学气相沉积----4.2 化学气相沉积
1. 歧化反应
大多数歧化反应,源区只有在高温下才能生成可进行歧化反 应的中间产物,源区的反应器壁也要处于高温下,以避免在 反应器上进行沉积,如生成SiI2中间产物需要1150℃:
Si(s) + 2I2(g) → SiI4 (g) SiI4 (g) + Si(s) → 2SiI2 (g) 衬底区生成硅外延层的歧化反应只需900℃:
第四章 化学气相沉积----4.2 化学气相沉积
3. 热解反应 某些元素的氢化物和金属有机化合物高温下不稳
定,发生分解,产物可沉积为薄膜,反应是不可逆的。 如:
SiH4(g) = Si(s) + 2H2(g) Ni(CO)4(g) = Ni(s) + 4CO(g)
TiI(g) = Ti(s) + 2I 多晶硅沉积的生长温度可低至600℃;单晶硅则需850。 当需要低温工艺时,硅烷可作为理想的硅源来使用。
4. 氧化反应 利用氧气作为氧化剂促进反应:
SiH4(g) + O2 = SiO2(s) + H2O(g) (450℃) Si(C2H5O)4 + 8O2 = SiO2 + 10H2O + 8CO2
(Si(C2H5O)4是正硅酸乙酯 简称TEOS)
化学气相沉积技术

produce the desired deposit. Frequently, volatile by-products are also
produced, which are removed by gas flow through the reaction chamber.
速加热晶圆。只对基底加热,而不是气体或腔壁。可以减少不必要的气
相反应,以免产生不必要的粒子。
气相外延 (Vapor phase epitaxy, VPE)
……
34
化学气相沉积的特点
优点:
1)既可制作金属薄膜,又可制作多组分合金薄膜,且成分控制准确;
2)可在复杂形状基片上沉积薄膜,绕射性能好;
3)一些反应可在常压或低真空进行,不需要昂贵的真空设备;
超高真空CVD (Ultrahigh vacuum CVD, UHVCVD):
在非常低压环境下的CVD。大多低于10-6 Pa (约为10-8 torr)。大部
分现今的CVD制程都是使用LPCVD或UHVCVD。
30
化学气相沉积的种类
以气相的特性分类:
气溶胶辅助CVD (Aerosol assisted CVD, AACVD):
层位于最初表面以上。
8
SiO2薄膜的热氧化法制备
Oxidation technology
大多数热氧化在加热炉中进行,温
度800到1200℃。将基片放在石英
支架(石英舟)里,一个加热炉同
时可以处理一批基片。
水平炉和垂直炉
- 1、下载文档前请自行甄别文档内容的完整性,平台不提供额外的编辑、内容补充、找答案等附加服务。
- 2、"仅部分预览"的文档,不可在线预览部分如存在完整性等问题,可反馈申请退款(可完整预览的文档不适用该条件!)。
- 3、如文档侵犯您的权益,请联系客服反馈,我们会尽快为您处理(人工客服工作时间:9:00-18:30)。
设在生长中的薄膜表面形成了界面层,其厚度为,cg和cs分别为 反应物的原始浓度和其在衬底表面的浓度,则
扩散至衬底表面的反应物的通量为: 衬底表面消耗的反应物通量与Cs成正比
平衡时两个通量相等,得
F1 hg (Cg Cs )
F2 ksCs
F1 F2
Cs
Cg 1 ks
hg
hg为气相质量输运系数,Ks为表面化学反应速率常数
硅CVD外延生长三个基本热化学类型: 歧化反应、还原反应、热解反应
1. 歧化反应 包含二价卤化物的分解:
2SiX2(g) ↔ Si(s) + SiX4(g) 低温时,反应向右进行;高温时,反应向左进行。
➢ 大多数的闭管反应都是利用歧化反应,将单晶硅衬底放在沉 积区,沉积固态硅就可以获得单晶外延薄膜。
热能:热CVD ,热丝CVD 光能:激光诱导CVD;紫外光诱导CVD 电磁场:等离子体增强CVD
第四章 化学气相沉积----4.1 概述
一、CVD原理及特点 优点:
➢ 可准确控制薄膜的组分及掺杂水平; ➢ 可在形状复杂的基片上沉积薄膜; ➢ 系统不需要昂贵的真空设备; ➢ 高沉积温度会大幅度改善晶体的结晶完整性; ➢ 可利用某些材料在熔点或蒸发时分解的特点而得到其他
第四章 化学气相沉积----4.2 化学气相沉积
3. 热解反应 主要优点是能够在低温下实现外延生长;热
解反应不可逆,不存在卤化物的气相腐蚀作 用,因而对衬底的腐蚀不严重,对异质外延 生长尤为有利。 主要问题是气态反应物的纯度、成本和安全 使用等。
第四章 化学气相沉积----4.2 化学气相沉积
二、CVD动力学分析 掌握CVD反应室中的流体动力学是相当重
要的,因为它关系到反应剂输运(转移)到衬 底表面的速度,也关系到反应室中气体的温度 分布,温度分布对于薄膜淀积速率以及薄膜的 均匀性都有着重要的影响。
二、CVD动力学分析---1、CVD模型(Grove模型)
薄膜的生长过程取决于气体与衬底间界面的相互作用,可能涉及的 步骤如下:
方法无法得到的材料; ➢ 沉积过程可以在大尺寸基片或多基片上进行。
第四章 化学气相沉积----4.1 概述
一、CVD原理及特点 缺点:
➢ CVD外延层容易形成自掺杂; ➢ 化学反应需要高温; ➢ 反应气体会与基片或设备发生化学反应; ➢ 设备较为复杂,需要控制变量多。
第四章 化学气相沉积----4.1 概述
质量输运控制的CVD 质量输运过程是通过气体扩散完成的,扩散速
度与气体的扩散系数和边界层内的浓度梯度有关。 质量输运速率控制的薄膜沉积速率与主气流速
度的平方根成正比,增加气流速度可以提高薄膜沉 积速率,当气流速率大到一定程度时,薄膜的沉积 速率达到一稳定值不再变化。沉积速率转变为由表 面反应速度控制
目前,制备半导体单晶外延薄膜的最主要方法是化学气相沉 积(chemical vapor deposition,简称CVD)。
第四章 化学气相沉积----4.1 概述
一、CVD原理及特点
CVD(chemical vapor deposition)是利用汽态的先驱反应物, 通过原子分子间化学反应的途径生成固态薄膜的技术。 特点: ✓ 需要使用汽态的物质作为反应物质 ✓ 源物质要经过化学汽相反应生成所需要的材料 ✓ 需要相对较高的气体压力环境 ✓ 通常需要热,电磁场或光等的作用,促使化学反应的进行。
第四章 化学气相沉积----4.2 化学气相沉积
5. 化合反应 只要所需物质的先驱物可以气态存在并具有反应
活性,就可利用化学反应沉积其化合物。 如:
SiCl4(g) + CH4(g) = SiC(s) + 4HCl(g) (1400℃) 3SiH4 + 4NH3 = Si3N4 + 12H2 BCl3 + NH3 = BN + HCl
✓ 当H2以鼓泡的形式通过液体时,由于蒸发作用使液体冷却。 冷却使液体蒸气压降低,并减小硅源气体对氢气的体积比。 根据理想气体状态方程n=PV/RT,维持硅源气体的蒸发速率, 便可保持硅源气体与载气恒定的体积比。
第四章 化学气相沉积----4.2 化学气相沉积
2. 还原反应
✓ 优点:能在整个沉淀区实现比较均匀的外延生长;可 控制反应平衡移动;可利用反应可逆性在外延生长之 前对衬底进行原位气相腐蚀;在深而窄的沟槽内进行 平面化的外延沉积。
反应导致的沉积速率 G F kshg Cg N1 ks hg N1
N1表示形成单位体积的薄膜所需原子个数
结论: 反应气体没有稀释时,沉积速率与反应剂浓度Cg
成正比。
多数CVD中,反应剂先被惰性气体稀释,Cg=YCT
Y是反应剂的摩尔百分比,CT单位体积中反应剂和惰性气体分 子的总数,
则薄膜的生长速度:
薄膜的沉积速率由表面反应速率控制
在hg<<ks时,
G hgCTY N1
薄膜的沉积速率由质量输运速率控制
• 表面反应速率控制的CVD 薄膜的沉积速率是由表面反应速率控制的,
衬底的温度对沉积速率有较大影响,因为表面化 学反应对温度的变化非常敏感。
当温度升高时,反应速率增加,薄膜的沉积 速率加快。当温度升高到一定程度时,由于反应 速度的加快,输运到表面的反应剂的数量低于表 面反应所需的数量,这时沉积速率转为由质量输 运控制,反应速度不再随温度变化而变化。
SiHCl3(g) + H2(g) ↔ Si(s) + 3HCl(g) 2SiHCl3(g) ↔ Si(s) + SiCl4(g) + 2HCl(g)
第四章 化学气相沉积----4.2 化学气相沉积
2. 还原反应
✓ SiCl4和SiHCl3常温下都是液体,氢气作载体,由鼓泡法携带 到反应室。容器的温度和压力决定于硅源气体与载气H2的体 积比,要想维持稳定的生长速率,体积比必须保持恒定,使 用SiCl4和SiHCl3所带来的问题是要维持一个恒定的温度。
4. 氧化反应 利用氧气作为氧化剂促进反应:
SiH4(g) + O2 = SiO2(s) + H2O(g) (450℃) Si(C2H5O)4 + 8O2 = SiO2 + 10H2O + 8CO2
(Si(C2H5O)4是正硅酸乙酯 简称TEOS)
SiCl4 + O2 = SiO2 + 2Cl2 GeCl4 + O2 = GeO2 + 2Cl2
第四章 化学气相沉积
第四章 化学气相沉积----4.1 概述
所谓外延生长,就是在一定条件下在单晶基片上生长一层单 晶薄膜的过程,所生长的单晶薄膜称为外延层。
20世纪60年代初在硅单晶薄膜研究基础上出现,已可实现各 种半导体薄膜一定条件的外延生长。
气相外延生长是最早应用于半导体领域的较成熟的外延生长 技术,促进了半导体材料和器件质量及性能提高。
2SiI2 (g) → Si(s) + SiI4 (g)
第四章 化学气相沉积----4.2 化学气相沉积
1. 歧化反应
根本性的缺点
要求气流流速低,暴露给输运气体的源表面积 大;反应效率低,源利用率不高;系统沾污可能性 大;在闭管系统内的生长过程中引入掺杂剂较困难。
未能广泛应用在工业生产中
第四章 化学气相沉积----4.2 化学气相沉积
第四章 化学气相沉积----4.2 化学气相沉积
二、CVD动力学分析 应用气相外延制备外延片的质量和数量都与
生长机理密切相关,因此了解气相外延生长动力 学的基本过程和规律对外延工艺的选择、反应器 的设计都具有重要意义。以开管系统为例对其过 程进行讨论。
第四章 化学气相沉积----4.2 化学气相沉积
G F kshg CTY N1 ks hg N1
结论:
当反应剂稀释时,沉积速率与气相中反应剂的 摩尔百分比Y成正比。
G F kshg CTY N1 ks hg N1
结论: 在Cg或Y为常数时,薄膜沉积速率将由ks和hg中
较小的一个决 定:
结论: 在ks<<hg时,
G ksCTY N1
致膜淀积和副产物的生成 (7)气态副产物和未反应的反应剂扩散离开衬底表面 (8)副产物排出反应室(进入主气流区被排除系统)
第四章 化学气相沉积----4.2 化学气相沉积
二、CVD动力学分析 1、CVD模型(Grove模型)
CVD过程主要受两步工艺过程控制: (1)气相输运过程; (2)表面化学反应过程。
2. 还原反应 ✓ 用还原剂还原含有欲沉积物质的化合物(大多数是卤
化物)。 ✓ 吸热反应,高温下进行,可采用简单的冷壁单温区。 ✓ 可逆反应。
第四章 化学气相沉积----4.2 化学气相沉积
2. 还原反应 最典型的是H2(还原剂和载气)还原卤化物。对
于硅的外延,卤化物一般采用SiCl4或SiHCl3,如: SiCl4(g) + 2H2(g) ↔ Si(s) + 4HCl(g) (1150-1300℃)
薄膜的生长过程取决于气体与衬底间界面的相互作用, 可能涉及以下几个步骤: (1)反应气体从入口区域流动到衬底表面的淀积区域 (2)气相反应导致膜先驱物(组成膜最初的原子或分
子)和副产物的形成 (3)膜先驱物附着在衬底表面
第四章 化学气相沉积----4.2 化学气相沉积
二、CVD动力学分析 1、CVD模型(Grove模型) (4)膜先驱物粘附在衬底表面 (5)膜先驱物向膜生长区域的表面扩散 (6)吸附原子(或分子)在衬底表面发生化学反应导
第四章 化学气相沉积----4.2 化学气相沉积
二、CVD动力学分析 1、CVD模型(Grove模型)
1966年Grove建立了一个简单的CVD模型。认为控制 薄膜沉积速率的两个主要因素是: (1)反应剂在边界层中的输运过程。 (2)反应剂在衬底表面上的化学反应过程。