3.6.1压铸模流分析基本操作流程
压铸模流分析讲义
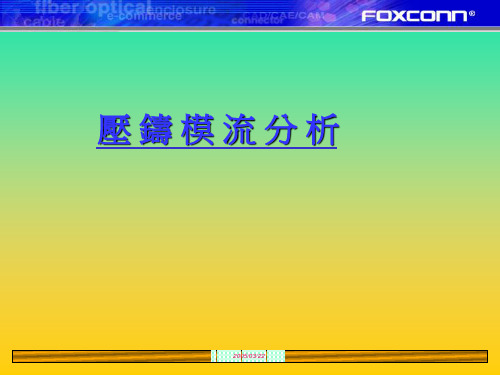
3.這是模擬充填過程的結果
2005/03/22
4.這是模擬澆口充填速度的結果圖
2005/03/22
5.這是模擬凝固時間的結果圖
2005/03/22
6.這是模擬凝固過程的結果
2005/03/22
7.這是模擬熱結點的結果圖
2005/03/22
考試
2005/03/22
2005/03/22
選擇產品的材質:AZ91D
2005/03/22
選擇產品的材質:AZ91D
2005/03/22
設定計算該產品的幾何資料
2005/03/22
設定計算壓鑄該產品所需的的 壓鑄機資料
2005/03/22
調整幾何參數, 由PQ2圖判斷幾 何參數是否正確?
2005/03/22
所有參數設定好後,開始計算.
2005/03/22
計算結束後,最後可以看到以下結果.
1.氣壓圖 2.充填時間圖 3.充填過程圖 4.充填速度圖 5.凝固時間圖 6.凝固過程圖 7.熱節點圖 ......
2005/03/22
1.這是一張模擬充填100%時的氣壓結果圖
2005/03/22
2.這是一張模擬充填時間的結果圖
2005/03/22
2005/03/22
壓鑄模流分析功能介紹
湯液於模具中流動狀態之模擬觀摩與充填過程的變化; 壓鑄制程條件參數之最佳化; 壓鑄件傳熱,凝固熱流分析; 模具結構應力分析;
冷卻系統布置分析;
澆流道設計與Βιβλιοθήκη 流井設計之參考; 模具熱傳與離型劑噴涂效益分析; 模穴中湯流速度觀測;
2005/03/22
壓鑄之特性
壓鑄具有生產性高,尺寸精度優良、后加 工量少,鑄件表面平滑,機械強度高,可鑄薄壁 鑄件等優良特點.但由于熔湯高速射入模穴, 易卷入空氣,故使鑄件內常含有氣孔及充填不 良等,所以壓鑄模成型方案至關重要,在壓鑄 模具的開發階段,人們一直在致力于預先驗證 模具設計方案的可行性,以確保製造出高品質 的壓鑄模具,壓鑄模流分析軟件(MAGMA)的應 用,為我們提供了捷徑.
压铸模具开发流程

压铸模具开发流程
1. 设计与概念阶段
- 与客户就产品要求进行沟通和确认
- 定义产品的功能和性能参数
- 进行产品的外观设计和结构设计
2. 模具设计阶段
- 根据产品设计进行模具结构设计
- 选择合适的模具钢材料
- 设计浇口、冷却系统、顶出系统等模具功能部件 - 进行模流分析和应力分析,优化模具设计
3. 模具制造阶段
- 加工模具零件
- 装配和调试模具
- 进行模具试模和优化改进
- 对模具进行热处理和机加工
4. 模具试生产阶段
- 安装模具在压铸机上
- 调试压铸工艺参数
- 生产小批量试制品
- 对产品进行检测和评估,并对模具进行修改完善
5. 量产阶段
- 正式投产
- 持续监控产品质量和模具状态
- 定期对模具进行维护保养
- 根据需求对模具进行改造或更新
在整个压铸模具开发过程中,需要密切关注客户需求,严格执行质量控制,确保模具的精度和性能,以满足产品的功能和质量要求。
同时,也要注重成本控制和工艺优化,提高模具的使用寿命和生产效率。
压铸模流分析分析报告

压铸模流分析分析报告目录压铸模流分析分析报告 (1)引言 (1)背景介绍 (1)目的和意义 (2)压铸模流分析概述 (3)压铸模流分析的定义 (3)压铸模流分析的作用 (4)压铸模流分析的方法 (4)压铸模流分析的关键步骤 (5)模型建立 (5)材料参数设定 (6)网格划分 (7)求解器选择 (8)结果分析 (9)压铸模流分析的应用案例 (10)案例一:汽车零部件压铸模流分析 (10)案例二:电子产品外壳压铸模流分析 (11)案例三:家电产品压铸模流分析 (12)压铸模流分析的优势和局限性 (13)优势 (13)局限性 (14)结论 (14)对压铸模流分析的总结 (14)对未来研究的展望 (15)引言背景介绍压铸模流分析是一种重要的工程分析方法,用于评估和优化压铸模具的设计和制造过程。
随着工业技术的不断发展和进步,压铸模流分析在压铸行业中的应用越来越广泛。
通过模拟和分析压铸过程中的流动、凝固和收缩等关键参数,可以帮助工程师们更好地理解和控制压铸过程,提高产品质量和生产效率。
压铸是一种常用的金属成型工艺,广泛应用于汽车、航空航天、电子、家电等行业。
在压铸过程中,液态金属被注入到模具中,经过凝固和冷却后形成所需的零件或产品。
然而,由于压铸过程中涉及到复杂的流动和凝固现象,模具设计和制造过程中存在许多挑战和难题。
在传统的压铸模具设计中,通常需要通过试模和试产的方式来验证模具的可行性和性能。
这种方法不仅费时费力,而且成本高昂。
而压铸模流分析则可以在模具制造之前,通过计算机模拟和分析来预测和评估模具的性能。
通过模拟压铸过程中的流动、凝固和收缩等关键参数,可以帮助工程师们更好地理解和控制压铸过程,提高产品质量和生产效率。
压铸模流分析的核心是数值模拟方法,通过建立数学模型和计算流体力学(CFD)方法来模拟和分析压铸过程中的流动和凝固现象。
通过对模具结构、材料和工艺参数等进行优化,可以提高产品的成型质量和生产效率。
压铸模具模流分析报告解析
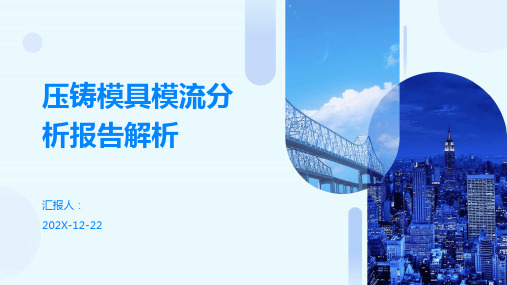
热处理可以改善模具材料的力学性能和耐热性,提高模具的使用寿命。报告中 应分析热处理工艺是否合理,是否达到预期的力学性能和使用寿命等。
模具制造工艺分析
粗加工工艺
粗加工是模具制造的第一道工序,其工艺直接影响到后续的精加工和装配。报告 中应分析粗加工工艺是否合理,是否能够保证模具零件的精度和表面质量等。
压铸模具模流分析将与多个领域进行交 叉融合,如机械、材料、电子等,形成 跨行业的合作模式,共同推动压铸模具 技术的发展。
VS
多元化应用
压铸模具模流分析不仅应用于汽车、摩托 车等制造领域,还将拓展到航空航天、新 能源等领域,实现多元化应用。
绿色环保和可持续发展要求
环保材料应用
随着环保意识的提高,压铸模具将更多地采 用环保材料,如可回收材料、生物降解材料 等,降低对环境的影响。
智能化和自动化程度提高
智能化技术应用
随着人工智能、大数据等技术的不断发展,压铸模具模流分析将更加智能化,实现自动 化数据收集、处理和分析,提高分析效率和准确性。
自动化生产流程
通过引入自动化设备和系统,实现压铸模具生产流程的自动化,减少人工干预,提高生 产效率和产品质量。
多领域交叉融合发展
跨行业合作
提高产品质量
通过优化模具设计和调整工艺参数,提高产 品质量和稳定性。
降低生产成本
通过减少废品率、提高生产效率等手段,降 低生产成本。
缩短产品研发周期
通过模流分析,可以更快地确定模具设计方 案和工艺参数,缩短产品研发周期。
03
CATALOGUE
压铸模具模流分析报告解析
模具结构分析
模具类型
分析报告中应包含模具类型的详细描述,例如单分型面模 具、多分型面模具等。
moldflow6.1中文教程第3 章Moldflow6.1 分析流程介绍
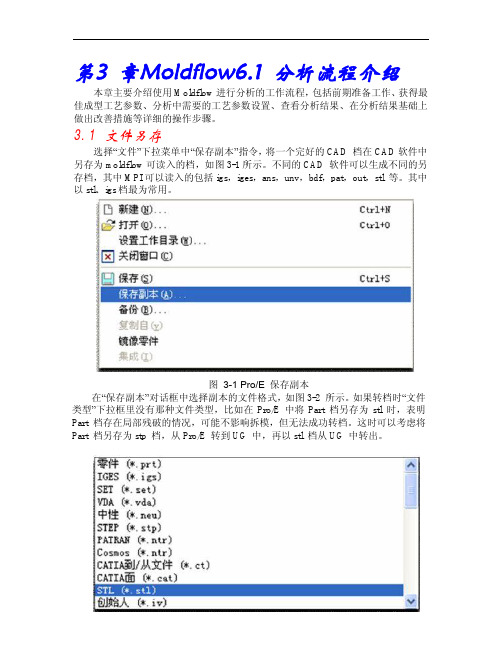
第3 章Moldflow6.1 分析流程介绍本章主要介绍使用Moldflow进行分析的工作流程,包括前期准备工作、获得最佳成型工艺参数、分析中需要的工艺参数设置、查看分析结果、在分析结果基础上做出改善措施等详细的操作步骤。
3.1 文件另存选择“文件”下拉菜单中“保存副本”指令,将一个完好的CAD 档在CAD软件中另存为moldflow可读入的档,如图3-1所示。
不同的CAD 软件可以生成不同的另存档,其中MPI可以读入的包括igs,iges,ans,unv,bdf,pat,out,stl 等。
其中以stl、igs档最为常用。
图3-1 Pro/E 保存副本在“保存副本”对话框中选择副本的文件格式,如图3-2 所示。
如果转档时“文件类型”下拉框里没有那种文件类型,比如在Pro/E 中将Part 档另存为stl 时,表明Part 档存在局部残破的情况,可能不影响拆模,但无法成功转档。
这时可以考虑将Part 档另存为stp 档,从Pro/E 转到UG 中,再以stl 档从UG 中转出。
图3-2 Pro/E 选择副本的文件格式3.2 另存文件格式对网格划分的影响转档时不同文件格式对moldflow 中网格划分有不同的影响:1. 另存为stl。
在Pro/E 中以Part 档为源档转出的情况最多,其优点为在精度控制得当的情况下,显示成功转出后的stl 档不会丢失源档的特征。
缺点是对源档点、线、面的完好性要求高,必须是完好无损的源档才能以STL 档转出。
2. 另存为igs 档。
优点是网格匹配率较stl 高一些,缺点是在源档残破的情况下也能转出,但由于无提示信息,转档过程中一旦出现重叠或缺失的特征,不仅增加网格的缺陷,细小的特征还会因无意识丢失而很难被发现,造成分析失误增加。
对于某些重要的细小特征的遗失,有时要等到去查看那里的缩水或其他成型问题时才会被发现,耽搁了宝贵的时间。
所以一定要慎用igs档。
3.3 编辑输出模型的精度图3-3 “输出副本文件”Pro/E 对话框确定副本文件格式后弹出“输出副本文件”对话框,如图3-3 所示。
压铸模具的制作流程与浇排系统设计

压铸模具的制作流程与浇排系统设计压铸模具的制作流程与浇排系统设计压铸是有色金属成型的一个重要方法之一。
压铸件的质量好坏80%取决于压铸模具。
制作好压铸模具是产品开发的关键所在。
在压铸过程中,由于型腔内的金属液流动状态不同,可能产生冷隔、花纹、气孔、偏析等不良现象。
所以控制型腔内的金属液流动状态是相当必要的,而控制型腔内的金属液流动状态,关键在于压铸模具浇排系统的设计。
1 压铸模具的制作流程上述流程是压铸模具制作的大致流程,但并非一成不变。
应在整个制作过程中前后协调,不断反馈与调整各阶段的信息,根据分析结果,修改设计方案,以期取得实效。
笔者从事压铸模具开发多年,就模具制作流程中的相关注意事项总结如下,供同行参考。
(1)要对客户来图应进行检证根据压铸工艺的特性结合有色金属的牌号,先进行毛坯方案设计,然后开始模具设计。
对有些不符合压铸工艺的结构,应及时与客户沟通,在征求客户同意的基础上再行修改。
日本三大著名摩托车品牌的研发部门都是在开发之初就重点把握图面检证这一关,这样可避免开发损失、减少开发时间。
压铸模具的设计与有色金属的牌号有关。
特别是ADC6(JIS标准)铝合金,其浇排系统结构及其拔模斜度与普通铝合金有所不同,应根据其流动性差、压铸温度较高等特点适当应对。
日本在高强度的零件上已大量应用ADC6铝合金,而国内应用的较少。
ADC6铝合金压铸模具常见的问题有:模具寿命短;脱模阻力大,易变形、拉模,工件顶出易产生裂纹;流动性差,易产生花纹、冷隔;模具突出部位易产生裂纹等,在设计过程中应提前应对。
(2)做好模具的检测在模具检测阶段,不应单纯检测模具尺寸,更重要的是应检测压铸产品质量。
压铸产品质量检测可分外观检测、内部品质检测及机械性能检测。
检测的数据应符合压铸产品的合格率要求、内部品质标准及机械性能指标。
(3)做好试模试模阶段是验证模具的.关键阶段,通常初次试模后还要进行修模,修模时针对不良项目逐二进行改善,直至符合客户要求。
模流分析流程
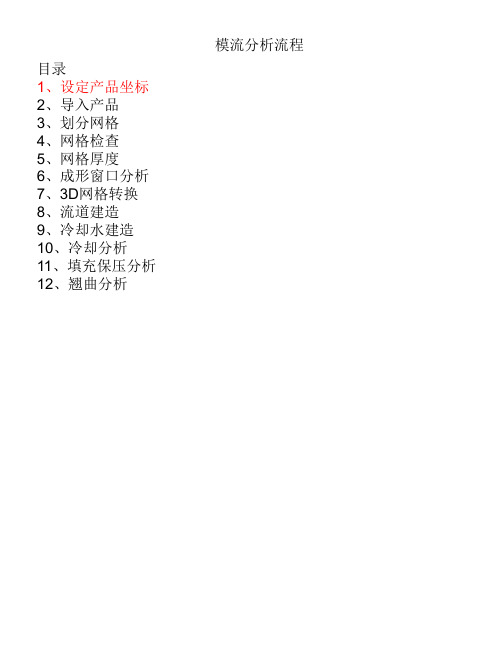
模流分析流程 5、网格厚度
模流分析流程 目录 1、设定产品坐标 2、导入产品 3、划分网格 4、网格检查 5、网格厚度 6、成形窗口分析 7、3D网格转换 8、流道建造 9、冷却水建造 10、冷却分析 11、填充保压分析 12、翘曲分析
模流分析流程 6、成形窗口分析
选择成形窗口分析序列。
模流分析流程 1)质量
模流分析流程 目录 1、设定产品坐标 2、导入产品 3、划分网格 4、网格检查 5、网格厚度 6、成形窗口分析 7、3D网格转换 8、流道建造 9、冷却水建造 10、冷却分析 11、填充保压分析 12、翘曲分析
模流分析流程 2、导入产品
网格划分先要作成”双层面“,修 正后视情况转成3d网格。
模流分析流程 目录 1、设定产品坐标 2、导入产品 3、划分网格 4、网格检查 5、网格厚度 6、成形窗口分析 7、3D网格转换 8、流道建造 9、冷却水建造 10、冷却分析 11、填充保压分析 12、翘曲分析
模流分析流程 12、翘曲分析 1)参数设定 定好射出、保压条件后,就可以进行翘曲分析了。 一般选择小变形项。
2)分析结果
指定模温和料温后,根据 成形质量确定注射时间。
2)区域图
模流分析流程 目录 1、设定产品坐标 2、导入产品 3、划分网格 4、网格检查 5、网格厚度 6、成形窗口分析 7、3D网格转换 8、流道建造 9、冷却水建造 10、冷却分析 11、填充保压分析 12、翘曲分析
模流分析流程 7、3D网格转换
模流分析流程 目录 1、设定产品坐标 2、导入产品 3、划分网格 4、网格检查 5、网格厚度 6、成形窗口分析 7、3D网格转换 8、流道建造 9、冷却水建造 10、冷却分析 11、填充保压分析 12、翘曲分析
镁铝合金铸件压铸过程的模流分析
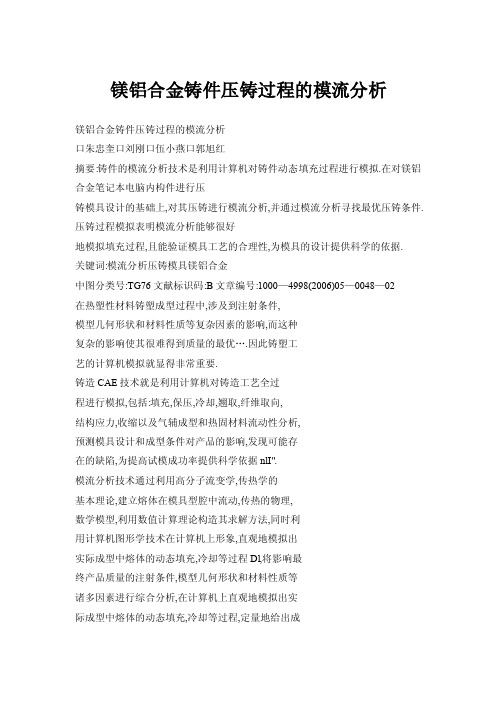
镁铝合金铸件压铸过程的模流分析镁铝合金铸件压铸过程的模流分析口朱忠奎口刘刚口伍小燕口郭旭红摘要:铸件的模流分析技术是利用计算机对铸件动态填充过程进行模拟.在对镁铝合金笔记本电脑内构件进行压铸模具设计的基础上,对其压铸进行模流分析,并通过模流分析寻找最优压铸条件.压铸过程模拟表明模流分析能够很好地模拟填充过程,且能验证模具工艺的合理性,为模具的设计提供科学的依据.关键词:模流分析压铸模具镁铝合金中图分类号:TG76文献标识码:B文章编号:1000—4998(2006)05—0048—02在热塑性材料铸塑成型过程中,涉及到注射条件,模型几何形状和材料性质等复杂因素的影响,而这种复杂的影响使其很难得到质量的最优….因此铸塑工艺的计算机模拟就显得非常重要.铸造CAE技术就是利用计算机对铸造工艺全过程进行模拟,包括:填充,保压,冷却,翘取,纤维取向,结构应力,收缩以及气辅成型和热固材料流动性分析,预测模具设计和成型条件对产品的影响,发现可能存在的缺陷,为提高试模成功率提供科学依据nlI".模流分析技术通过利用高分子流变学,传热学的基本理论,建立熔体在模具型腔中流动,传热的物理,数学模型,利用数值计算理论构造其求解方法,同时利用计算机图形学技术在计算机上形象,直观地模拟出实际成型中熔体的动态填充,冷却等过程Dl,将影响最终产品质量的注射条件,模型几何形状和材料性质等诸多因素进行综合分析,在计算机上直观地模拟出实际成型中熔体的动态填充,冷却等过程,定量地给出成型过程中的状态参数.模流分析技术可以在模具制造之前,在计算机上对模具设计方案进行分析和模拟,预测设计中潜在的缺陷,为设计人员修改设计提供科学的依据l【o本文对镁铝合金笔记本电脑内构件的压铸模具进行模流分析,仿真试验表明模流分析能够很好地模拟填充过程,验证铸件结构的工艺合理性,或者发现模具设计中存在的工艺问题,为压铸模具的参数设计和合理改进提供科学的依据.皿镁铝合金构件的模流分析(1)铗铝合金构件的设计镁铝合金构件为一笔记本电脑的内构件,材料为AZ91D,其三维造型如图1 所示.首先针对这个构件进行模具设计,充填时间与浇口速度参数的设计,射出条件的计算,流道设计,排气槽和溢流槽的设计,推杆导柱的设计,分型面的设计. 7006/$(2)铸件的模流分析注射流动过程中的工艺参数主要有填充时间,流动前沿温度,流动终止温度,流动压力,剪切速率,剪切应力,气泡及熔接痕的位置等. 预测保压阶段型腔内熔体的压力,温度,密度,剪切应力等的变化,可为合理确定保压压力,保压时间,浇口尺寸,注射温度等提供科学依据.模流分析软件MoldFlow可以在计算机上对整个铸塑过程进行模拟分析,包括填充,保压,冷却,翘曲等分析,使模具在设计阶段就找出未来产品可能出现的缺陷,提高一次试模的成功率.运用MoldFlow软件,可以给出注射流动过程中的主要参数,从而确定最佳的铸塑过程,完成这个工作主要包括3步:设计零件造型; 设计模具;根据模流分析确定最佳铸塑过程.在应用MoldFlow进行模流分析时,首先定义相关材质,传热系数,制程条件来满足镁铝合金在热室压铸机充填凝固现象.针对镁铝合金(AZ91D)笔记本电脑内构件,进行模流分析时需要设定模拟参数,包括注汤温度,压铸模具钢材(SKD61)的平均温度,水道中热煤油的温度,热煤油与模具钢之间的传热系数等.热煤油与模具钢之间的传热系数1000W/(m:K),改变注汤温度,从50o~620℃变化,步长为20℃;改变压铸模具钢材平均温度,从180~240℃变化;改变水道中热煤油的温度,从16~32℃变化,步长为4℃.针对注汤温度和煤油温度的所有组合,进行模拟填充,记录填充时间.结果表明,当注汤温度定ff~J560℃,压铸模具平均温度#J220℃,热煤油的温度#J22℃时,模拟填充时间最短,为0.507s.图2表示了内构件在最优的压铸条件下模拟填充10%,50%,80%与100%时的填充结果.根据模流分析,可以得到在最优的压铸条件下填充比例和填充压力与填充时间的关系(见图3).图3表明完成铸塑过程所需的最大铸塑压力以及完成铸塑所需的时间.同时图3还显示了铸塑过程中铸塑完成比机械制造44卷第501期(a)模拟填充过程10%●图1零件的三维造型(b)模拟填充过程50%(c)模拟填充过程80%(d)模拟填充过程100%▲图2压铸填充过程模拟结果基本与铸塑时间成线性关系.铸塑压力在铸塑过程中随铸塑时间的增加而增加,这说明在铸塑过程中必须将注射压力保持一段时间,否则不能完成铸塑填充.通过图2和图3,以及对该内构件的模流分析给出的评估方案,得到如下结论:①该内构件的铸塑能够在适当的压力,较短的时间下完成铸塑填充;②注汤温度560℃较低.可以保证铸件定型时间;③压铸模具平均温度为220℃.水道中热煤油的温度为22℃的选择是比较理想的,也是在实践中比较容易实现的;④模流分析没有发现模具设计中存在潜在的严重的压铸结构工艺缺陷.说明铸件的结构基本合理.目结论\丑填充时间/ms▲图3铸塑压力和填充比例与时间的关系毫\出野基于CAE的模流分析能够形象直观地模拟填充过程,根据模拟填充寻找最优压铸条件;同时还可以根据模流分析的结果得到压铸过程中的铸塑压力和铸塑完成比随时间的变化曲线.基于模流分析的填充过程模拟能够发现模具设计中的工艺缺陷,有效地验证模具设计的合理性.为模具的设计提供可靠建议.参考文献1郭广思.注塑成型技术【M】.机械工业出版社,20022唐忠民.注塑模流分析技术现状与Moldex3D软件应用【J】_ CAD/CAM与制造业信息化.2003(1)3张春吉,唐跃.CAD/CAE在塑料模具设计中的应用【J】.塑料科技,20o4(1)4李红林.贺华波,费春华,刘军,孙保寿.模流分析CAE技术在塑料模具设计和制造中的应用【J】.电加工与模具,2003(4)5欧长劲,郑子军.胡如夫.气辅注射成型工艺参数CAE模拟分析【J】.电加工与模具,2005(3)△(编辑方也)作者单位:苏州大学机电工程学院邮政编码:江苏?215021收稿日期:2oo5~12月贝加莱APC620@~ControlEngineering中文版2005年度产品大奖目前,ControlEngineering中文版将2005年度产品大奖授予了贝加莱工业自动化公司,其得奖的产品是新一代工业PC——APC620.贝加莱新一代工业Pc——APc620省去了Pc组件接线,线路板稳定安装,摒弃旋转组件后的大容量内存(compaetFlash)的使用以及强健的机械结构形成了最佳的系统故障保护.APC620结构紧凑,节省了配电柜中的空间,所有接线和接口都分布于模块的顶部.不会因突出的接头而增加安装尺寸.同时.APC620不配备风扇,所有需冷却组件都机械制造44卷第501期分布于主板上,每个APC620均集成一个连接AutomationPanel或显示器的接口,与面板的连接可采用DVI,SDL或ThinClint方式.APC620共有三种安装类型,分别带1个,2个或5个PCI插槽.其余的组件也具有高度的模块化特性,基础系统中通常包括一个CompaetFlash插槽.另外可以增加一个CompactFlash 插槽或一个硬盘,还可以为其它驱动最多增加两个插槽.比如CD.ROM,DVD.ROM/CD.RW,软盘或硬盘设备等.模块化的插入技术让用户轻易地在不同驱动之问切换.(施红芳)2006/5回。
压铸工艺及操作规程(3篇)

第1篇一、压铸工艺概述压铸是一种将金属熔体在高压下注入到铸模中,冷却凝固后得到所需的铸件的金属成型方法。
压铸工艺具有生产效率高、尺寸精度好、表面光洁度高等优点,广泛应用于汽车、家电、电子等行业。
二、压铸工艺流程1. 铝合金熔炼:将铝锭或铝合金锭放入熔炼炉中,通过加热熔化成铝液。
2. 模具准备:根据产品图纸制作或选用合适的模具,并对模具进行预热。
3. 铝液准备:将熔化的铝液过滤、除气、去除杂质,使其达到压铸要求。
4. 压射成型:将铝液注入到预热的模具中,在高压下使铝液充满模具型腔。
5. 冷却凝固:铝液在模具中冷却凝固,形成铸件。
6. 取件:将铸件从模具中取出。
7. 清理:对铸件进行去毛刺、抛光等表面处理。
8. 检验:对铸件进行尺寸、表面质量、机械性能等检验。
三、压铸操作规程1. 安全操作:操作者必须穿戴好劳保用品,如工作服、手套、眼镜等,确保人身安全。
2. 设备检查:开机前,检查设备是否正常运行,如油压、冷却系统、控制系统等。
3. 模具准备:根据产品图纸制作或选用合适的模具,并对模具进行预热。
4. 铝液准备:将熔化的铝液过滤、除气、去除杂质,使其达到压铸要求。
5. 压射成型:将铝液注入到预热的模具中,在高压下使铝液充满模具型腔。
6. 冷却凝固:铝液在模具中冷却凝固,形成铸件。
7. 取件:将铸件从模具中取出。
8. 清理:对铸件进行去毛刺、抛光等表面处理。
9. 检验:对铸件进行尺寸、表面质量、机械性能等检验。
10. 设备维护:定期对设备进行保养、检修,确保设备正常运行。
四、注意事项1. 铝液温度:铝液温度应控制在合适的范围内,过高或过低都会影响铸件质量。
2. 压射压力:压射压力应根据产品材质、厚度等因素进行调整,确保铸件成型质量。
3. 模具预热:模具预热温度应控制在合适的范围内,过高或过低都会影响铸件质量。
4. 铝液过滤:铝液过滤可有效去除杂质,提高铸件质量。
5. 模具维护:定期对模具进行检查、清洗、维护,确保模具使用寿命。
压铸的工艺流程
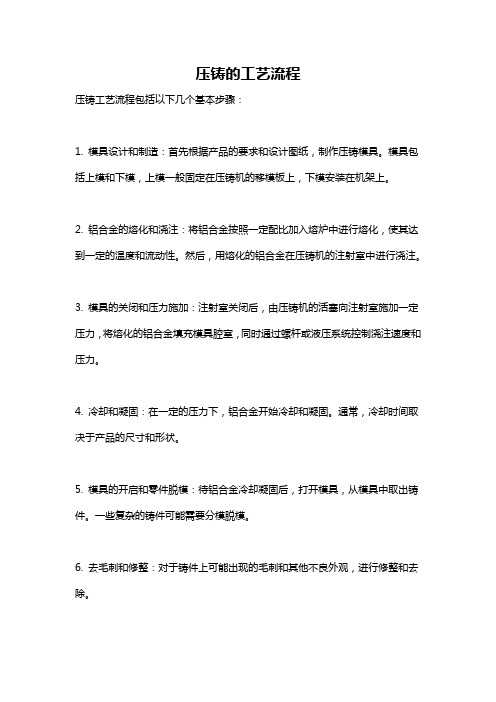
压铸的工艺流程
压铸工艺流程包括以下几个基本步骤:
1. 模具设计和制造:首先根据产品的要求和设计图纸,制作压铸模具。
模具包括上模和下模,上模一般固定在压铸机的移模板上,下模安装在机架上。
2. 铝合金的熔化和浇注:将铝合金按照一定配比加入熔炉中进行熔化,使其达到一定的温度和流动性。
然后,用熔化的铝合金在压铸机的注射室中进行浇注。
3. 模具的关闭和压力施加:注射室关闭后,由压铸机的活塞向注射室施加一定压力,将熔化的铝合金填充模具腔室,同时通过螺杆或液压系统控制浇注速度和压力。
4. 冷却和凝固:在一定的压力下,铝合金开始冷却和凝固。
通常,冷却时间取决于产品的尺寸和形状。
5. 模具的开启和零件脱模:待铝合金冷却凝固后,打开模具,从模具中取出铸件。
一些复杂的铸件可能需要分模脱模。
6. 去毛刺和修整:对于铸件上可能出现的毛刺和其他不良外观,进行修整和去除。
7. 表面处理和后处理:对于一些需要特殊表面处理的铸件,如电镀、喷涂等,进行相应的后处理工序。
8. 检查和质量控制:对铸件进行检查和测量,进行质量控制,确保产品的质量符合要求。
经过以上步骤,压铸工艺流程完成。
最终的铸件可用于各种应用,如汽车零部件、通信设备、家电等。
压铸操作流程

压铸操作流程压铸机操作规范1.机床启动;2.启动机床前,必须全面检查机床确保机床处于正常状态;3.手动润滑后再开机;4.点动启动机床并观察机床运转情况,如有异常立即停机;5.机床启动后,应开冷却水,以防油温升高;6.机床发生故障或报警信号响起,应立即查看原因后报修,严禁机床带病工作;压铸操作工艺流程模具安装→调试→清理预热模具→喷刷涂料→合模→涂料准备→涂料配制→压铸→冷却与凝固→开模→顶出铸件→质量检验→成品→废品→合金溶化一、模具安装模具安装前,压铸工必须全面了解模具结构状况,包括:1.模具有无抽芯;动模抽芯,还是静模抽芯;润滑抽芯,还是液压抽芯。
2.是否需要安装复位拉杆。
3.浇口套大小,熔杯大小,结合尺寸是否一致。
4.是否中心浇口。
5.顶棒位置、大小、长短是否合适。
二、操作规范1.根据模具情况更换熔杯冲头,必要时调节压射升降机构。
2.检查动静模板,确保表面无异物、无高点。
3.正确安装吊具,在确保安全的情况下起吊,并确保模具进入机床前无摇动,以免撞伤机床。
4.根据模具情况,正确安装模具。
特别注意,带有液压抽芯的模具,必须将机床相对应抽芯状态调到“选择”并且抽芯在动模的,要调到“锁模前”抽芯。
5.压紧模具,接好油管及冷却水管完成模具安装。
三、模具调试1.调节机床开档选择合适的锁模力。
2.调节压射跟出行程,检查冲头冷却水,确保无泄漏。
四、压铸生产1.压铸生产前,对模具型腔、顶杆、复位杆、导柱、导套、型芯、滑道等全面刷油。
2.在冷模状态下,在工艺无特殊规定情况下应将机床二快和增压关闭。
3.根据零件重量,合理选择浇注量进行试压,并相应调节,确保料饼厚度。
4.模具在冷模的状态下,多刷油少喷涂,模具热起来按正常喷涂料。
5.模具到了正常温度后,将二快和增压打开,按正常程序生产。
6.生产的首件产品,必须进行全面的检查,做好记录,并保留由检验员检验。
7.在正常生产过程中,压铸工要根据压铸工艺要求,正确控制并及时调整如下要素:①喷涂②料温控制③模温控制④料饼厚度控制⑤分型面清洗⑥滑动部位润滑8.在正常生产过程中,要按要求检查铸件质量,如有异常,及时停止生产做好修理或更换模具工作。
压铸工艺流程
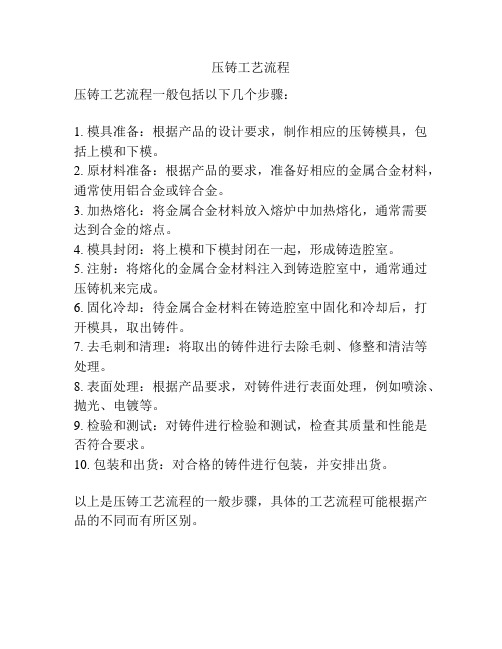
压铸工艺流程
压铸工艺流程一般包括以下几个步骤:
1. 模具准备:根据产品的设计要求,制作相应的压铸模具,包括上模和下模。
2. 原材料准备:根据产品的要求,准备好相应的金属合金材料,通常使用铝合金或锌合金。
3. 加热熔化:将金属合金材料放入熔炉中加热熔化,通常需要达到合金的熔点。
4. 模具封闭:将上模和下模封闭在一起,形成铸造腔室。
5. 注射:将熔化的金属合金材料注入到铸造腔室中,通常通过压铸机来完成。
6. 固化冷却:待金属合金材料在铸造腔室中固化和冷却后,打开模具,取出铸件。
7. 去毛刺和清理:将取出的铸件进行去除毛刺、修整和清洁等处理。
8. 表面处理:根据产品要求,对铸件进行表面处理,例如喷涂、抛光、电镀等。
9. 检验和测试:对铸件进行检验和测试,检查其质量和性能是否符合要求。
10. 包装和出货:对合格的铸件进行包装,并安排出货。
以上是压铸工艺流程的一般步骤,具体的工艺流程可能根据产品的不同而有所区别。
压铸开模流程-概述说明以及解释

压铸开模流程-概述说明以及解释1.引言1.1 概述压铸是一种常见的金属加工方法,它通过将熔化的金属注入到模具中,使其迅速冷却凝固成型。
在压铸过程中,开模是一个关键步骤,它决定了最终产品的质量和精度。
开模流程包括了一系列准备工作和步骤,以确保金属能够成功注入到模具中,并在冷却过程中顺利脱模。
本文将详细介绍压铸开模的流程和步骤。
在压铸开模前的准备工作中,首先需要对模具进行检查和保养,确保其完好无损、表面光洁,并做好必要的润滑处理。
同时,还需准备好一些辅助工具,如起重设备、钳工工具以及安全措施等,以确保开模过程的安全和顺利进行。
压铸开模的流程步骤主要包括以下几个方面:首先是将模具安装在压铸机上,并进行必要的调整和校正,确保模具在封闭状态下能够正常运行。
接下来,将金属材料熔化并装入到压铸机的注射系统中,通过控制系统对注射过程进行精确控制。
当金属注射完成后,需要等待一定的时间,以确保金属在模具中充分冷却凝固。
最后,通过开启压铸机的顶出模系统,将成型品从模具中取出,并进行必要的后续处理和检验。
通过以上步骤,我们可以看出压铸开模流程对于最终产品的质量和精度至关重要。
只有通过科学的流程和严格的操作,才能够得到符合要求的产品。
因此,在实际操作中,需要工程师和技术人员具备一定的技术水平和经验,并严格按照相关标准和要求进行操作,以确保产品的质量和稳定性。
1.2 文章结构文章结构部分的内容可以包括以下内容:文章结构的设计是为了使读者更好地理解和掌握压铸开模流程。
本文将按照以下方式组织内容:引言、正文和结论。
在引言部分,首先概述了压铸开模流程的背景和重要性。
接着介绍了本文的结构和目的,以引导读者对整篇文章的内容有一个整体的了解。
正文部分将分为两个主要部分。
首先,会详细介绍压铸开模前的准备工作。
这些准备工作包括:准备开模设备和工具、检查模具和压铸机的状态、准备原材料以及安全措施等。
这一部分的内容将帮助读者了解开模前的必要步骤和注意事项。
压铸模流分析讲义

压铸模流分析讲义模具流动性分析是压铸模流分析的关键环节。
通过模具流动性分析,可以预测模具填充过程中可能出现的缺陷,如短流、冷隔、气孔等,并针对性地进行模具设计和优化。
模具流动性分析通常使用计算流体力学(CFD)方法来模拟设备中的铝液流动,通过计算和显示铝液在模腔中的压力、速度、温度和液面高度等参数的分布情况,以评估模具的填充性能。
此外,模具流动性分析还可以进一步分析铝液在填充过程中的温度场、应力场和凝固形态等,以预测可能导致缺陷的原因和位置。
压铸模具设计优化是通过模具流动性分析的结果对模具的结构和形状进行调整,以提高模具的填充性能和铸件质量。
在模具设计优化中,常用的方法包括增加给铝液的进场路线,减小液态金属在流动过程中的变形和浊流等。
例如,可以通过设计合理的浇口和浇注系统,使铝液能够均匀流动并避免在模腔中产生气隙,从而减少模具填充过程中的缺陷。
此外,在模具设计优化中还可以采用一些先进的材料和涂层技术,以提高模具的耐磨性和导热性,从而进一步降低模具的使用成本。
模具热平衡控制是压铸模流分析的另一个重要方面。
在压铸模具的填充过程中,由于铝液的高温和高压作用,模具会受到严重的热应力,从而导致模具的变形和损坏。
为了解决这个问题,可以通过模具热平衡控制来降低模具的温度梯度和热应力。
模具热平衡控制的主要方法包括采用合理的冷却系统和冷却通道,以提高模具的散热能力和温度均匀性。
此外,还可以采用一些热障涂层和陶瓷材料,以提高模具的抗高温性能和热传导性能。
总之,压铸模流分析是一项非常重要的模具设计和优化技术。
通过模具流动性分析、压铸模具设计优化和模具热平衡控制,可以预测和减少压铸模具制造过程中的缺陷和损坏,提高铸件的质量和生产效率。
随着计算机仿真技术的不断进步,压铸模流分析将在压铸模具制造中发挥越来越重要的作用。
压铸模流分析分析报告

压铸模流分析分析报告
一、模具结构分析
通过对模具结构进行分析,可以确定模具的开合方式、浇注系统设计以及冷却系统设置等方面的参数。
在模具结构设计方面,需要考虑到金属充填的流态,避免产生二次气孔和翻砂现象,同时还需要保证金属的充填速度和压力等因素。
二、模具温度分析
模具温度对于铸件的质量有很大的影响,过高或过低的模具温度都会导致铸件出现缺陷。
通过模流分析可以对模具温度进行分析,可以帮助优化冷却系统的设计,保证模具表面均匀的温度分布,以提高铸件的质量。
三、金属流动分析
金属充填过程是压铸过程中的关键环节,通过模流分析可以模拟和分析金属在模具中的流动情况。
可以通过分析金属流动速度、充填时间和充填压力等参数,对模具结构和浇注系统进行优化设计,以提高铸件的充填性能。
四、缺陷分析
通过模流分析,可以模拟和分析金属在模具中的凝固过程,进而预测铸件中可能出现的缺陷情况,如气孔、缩孔、翻砂等。
通过这些分析可以提前发现潜在的缺陷问题,从而对模具结构和工艺进行改进,以提高铸件的质量。
五、优化建议
根据分析结果,可以得出针对模具结构和工艺的优化建议,以提高铸件的质量和生产效率。
建议可能包括改善浇注系统设计、调整模具温度、优化冷却系统设置等方面。
综上所述,压铸模流分析分析报告是对压铸模具结构、温度、金属流动和缺陷等方面进行模拟和分析,并给出相应的优化建议。
通过该分析可以提高铸件的质量,减少缺陷的产生,优化生产过程,提高生产效率。
压铸机操作规程

压铸机操作规程一、前言压铸是一种高效率、高质量的金属成形方法,广泛应用于汽车、航空、电子等行业。
而压铸机是压铸工艺的核心设备。
为了确保生产的正常进行,保障压铸机安全运行,制定一份严格的压铸机操作规程非常必要。
二、压铸机的基本组成1.机身:压铸机主体结构,包括四柱式压铸机和C型压铸机;2.锁模机构:负责开合模板,实现模具的锁紧和脱模;3.注射机构:将金属材料加热并注入模具中;4.液压系统:控制压铸机的各项动作,如开合模、注射、顶出等;5.电气控制系统:控制压铸机电机、油泵等各部件的运转。
三、压铸机操作规程(一)操作前的准备工作1.检查压铸机电气设备是否正常;2.检查液压系统及油位是否正常;3.检查锁模机构及注射机构是否紧固;4.检查在压铸过程中所需要的工具是否齐全,并放置在工具台上方便使用;5.确认模具、护板、浇口、温控器正常。
(二)开机测试1.首先将压铸机开机,从80℃升至160℃,持续5分钟;2.将柱塞退回到顶部,再打开油路;3.检查油泵、电机工作是否正常;4.关闭所有电机进入待机状态。
(三)模具装卸1.在装卸模具时,必须关闭压铸机的电源;2.在拆卸模具时必须确认柱塞前推到底部位置;3.在安装模具时,必须先将模具平面清洁干净;4.装夹模具前,必须将模具提升到位,并将螺钉螺母旋紧;5.模具安装完毕后,必须进行试运转,确认操作是否正常。
(四)调整操作参数1.首先将设定好的温度值输入温控器,预热模具;2.需要调整压铸机操作参数时,必须确保压铸机处于空车状态;3.调整操作参数时,必须停车操作;4.操作人员调整参数时必须牢记每一项操作的参数值。
(五)压铸生产操作1.将模具装好并调整好所有参数后,可进行压铸生产操作;2.压铸时,应根据供应商要求注入合适的金属材料;3.待材料熔化到一定程度后,启动压力控制设备;4.压力控制设备工作后,观察生产情况,及时停车进行调整。
一旦出现异常停车,确认异常原因后再投入生产;5.完成生产后,关闭机器并将模具拆卸下来。