疲劳耐久测试与分析系统
耐久性和损伤容限分析软件MSC
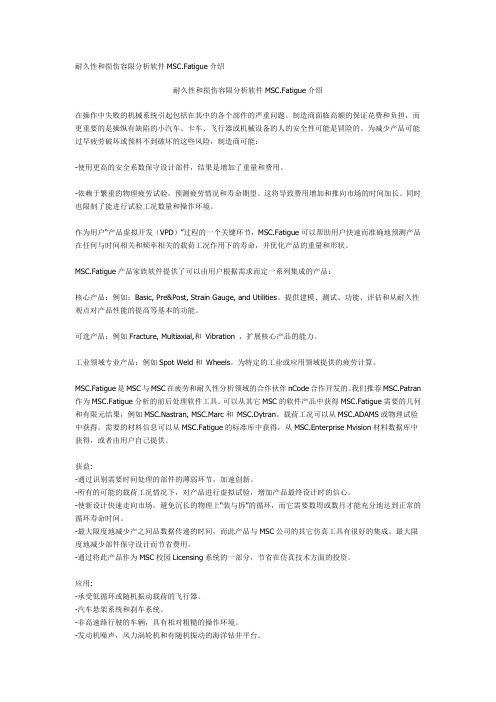
耐久性和损伤容限分析软件MSC.Fatigue介绍耐久性和损伤容限分析软件MSC.Fatigue介绍在操作中失败的机械系统引起包括在其中的各个部件的严重问题。
制造商面临高额的保证花费和负担,而更重要的是操纵有缺陷的小汽车、卡车、飞行器或机械设备的人的安全性可能是冒险的。
为减少产品可能过早疲劳破坏或预料不到破坏的这些风险,制造商可能:-使用更高的安全系数保守设计部件,结果是增加了重量和费用。
-依赖于繁重的物理疲劳试验,预测疲劳情况和寿命期望。
这将导致费用增加和推向市场的时间加长。
同时也限制了能进行试验工况数量和操作环境。
作为用户“产品虚拟开发(VPD)”过程的一个关键环节,MSC.Fatigue可以帮助用户快速而准确地预测产品在任何与时间相关和频率相关的载荷工况作用下的寿命,并优化产品的重量和形状。
MSC.Fatigue产品家族软件提供了可以由用户根据需求而定一系列集成的产品:核心产品:例如:Basic, Pre&Post, Strain Gauge, and Utilities。
提供建模、测试、功能、评估和从耐久性观点对产品性能的提高等基本的功能。
可选产品:例如Fracture, Multiaxial,和Vibration ,扩展核心产品的能力。
工业领域专业产品:例如Spot Weld和 Wheels。
为特定的工业或应用领域提供的疲劳计算。
MSC.Fatigue是MSC与MSC在疲劳和耐久性分析领域的合作伙伴nCode合作开发的。
我们推荐MSC.Patran 作为MSC.Fatigue分析的前后处理软件工具。
可以从其它MSC的软件产品中获得MSC.Fatigue需要的几何和有限元结果,例如MSC.Nastran, MSC.Marc和MSC.Dytran。
载荷工况可以从MSC.ADAMS或物理试验中获得。
需要的材料信息可以从MSC.Fatigue的标准库中获得,从MSC.EnterpriseMvision材料数据库中获得,或者由用户自己提供。
应用LMS测试系统进行整车道路模拟疲劳耐久试验载荷谱研究

应用LMS测试系统进行整车道路模拟疲劳耐久试验载荷谱研究1 前言道路模拟试验是一种室内试验技术,随着随机理论、控制技术和计算机的发展,整车道路模拟试验设备也日趋完善,是考察车辆道路可靠性试验的重要手段之一,且具有试验周期短、重复性和可控性好、不受天气限制等优点,能够满足各种波形再现振动试验,是汽车开发的一项重要技术[1]。
室内道路模拟试验的主要原理是:根据用户实际道路和试验场道路对车辆的等效损伤,选择合适的试验场路面,采集汽车轴头或者车身加速度等响应信号,将采集的信号进行编辑处理,获得合适的载荷谱原始信号;运用远程控制技术,将载荷谱原始响应信号作为期望信号,利用控制软件设置白噪声驱动信号,计算出台架的频率响应函数;由采集的原始信号,经过迭代,最终求出与路面激励等效的驱动信号;最后分析原始响应信号与试验台架得出的响应信号损伤比较,从而得到试验场道路最终循环次数,将驱动信号输入,进行整车疲劳耐久试验[2]。
近年来,对乘用车道路模拟强化坏路研究相对较少,且不同的设备的技术性能都有着较大的差别,试验准备要求较高,对于试验过程中的一些问题缺乏经验。
本文详细说明了试验准备的要求;应用LMS系统中的Xpress进行路谱的采集,并介绍运用Tecware编辑和处理原始信号的技巧方法及原则;并且在迭代完毕后对载荷谱原始信号与台架目标响应信号进行损伤对比,确定最终的试验循环次数。
2载荷谱的采集要进行台架试验首选要进行载荷谱的采集,实验台为四通道道路模拟试验台,因此需要采集汽车轴头位置处的加速度信号,以轴头对应的车身的侧位置作为过程辅助参考点,如图1、2所示:图1左前轴头加速度传感器安装位置图2车身加速度传感器安装位置传感器的安装原则是不论在车身还是在车轮上,传感器尽量布置在汽车的刚体位置,能够准确反映路面不平度;传感器的测量方向要尽量与车轮或车身的振动方向保持一致;确保传感器固定牢固,传感器及传感器走线不与车辆各部位产生干涉;对各传感器布置位置进行拍照,以便与台架试验时传感器保持一致[3]。
一套完整的疲劳分析设计试验管理系统nSoft

一套完整的疲劳分析设计试验管理系统nSoft林晓斌 博士林晓斌 摘要 介绍了nCode 国际有限公司发展的一套完整的疲劳分析系统nSo ft 。
该系统专门为解决工程系统的疲劳问题而设计,主要由数据分析、数据显示、疲劳分析软件以及其它一些专门软件组成。
可用在数据采集、疲劳设计分析以及实验室疲劳模拟等部门。
关键词 疲劳分析 动态数据处理 工程设计 实验室模拟中国图书资料分类法分类号 T P202收稿日期:1998—09—03 nSo ft 是一个“由工程师为工程师设计”的工程疲劳分析系统,它的功能覆盖了工程抗疲劳设计分析的3个主要领域,即数据采集、疲劳分析以及实验室模拟,并将它们紧密地结合在一起,见图1。
nSoft 集现代疲劳理论、数据信号分析处理和最新的计算机技术于一体,为工程界提供了全套功能强大的抗疲劳设计工具。
图1 工程抗疲劳设计分析中的几个主要步骤1 nSoft 系统简介nSo ft 是由许多独立模块组成的一个开放系统。
每一模块可在计算机操作环境下独立启动,模块之间的传递主要通过数据文件实现。
可处理的数据文件长度没有限制。
nSoft 也有一个独特的管理界面,它可以帮助用户设置操作环境,记录所执行的命令,启动各个模块,查阅在线操作手册,阅读疲劳背景知识电子文件等,nSo ft 配有功能强大的、nCode 自己发展的命令语言nCL ,使用nCL 可以使得繁琐重复的工作自动化,并允许用户进行二次开发,发展出自己所需要的模块。
nSo ft 配置的报告编辑工具,可让用户获得满意的报告格式,并且也能很方便地将nSoft 产生的图形及结果记录文件复制到一般的图文编辑软件里去。
n Soft 当前能在多种操作平台上工作,如DOS 、微软视窗95/NT 、UNIX (SGI 、SPARC 、HP 、IBM )、X 和MOT IF 。
另外,为了帮助用户进图2行疲劳分析,nSoft 还配有丰富的材料性能、应力强度因子和应力集中因子数据库。
混凝土结构疲劳性能测试与分析

混凝土结构疲劳性能测试与分析混凝土结构是现代建筑中应用最广泛的一种材料,具有较好的强度和耐久性。
但是,随着使用时间的延长和环境的变化,混凝土结构的疲劳性能也会逐渐降低,这对建筑物的结构安全和使用寿命带来了一定的威胁。
因此,进行混凝土结构疲劳性能测试与分析十分必要。
一、疲劳性能的定义和影响因素疲劳性能是指材料在交变载荷作用下的耐久性能。
混凝土结构在长期使用过程中,会受到交变载荷的作用,从而导致受力部位产生疲劳破坏,而产生的危害通常是逐渐积累的。
疲劳破坏是受到多种因素的影响,包括外部载荷的幅值、频率和周期等因素、混凝土的配合比、强度和含水率等因素、结构形式和材料连接方式等因素。
因此,对于不同的混凝土结构,其疲劳性能的测试和分析方法也有所不同。
二、混凝土结构疲劳性能测试方法目前,常见的混凝土结构疲劳性能测试方法主要包括静载试验、动载试验、试件制作和应力-应变监测等。
1. 静载试验:静载试验主要是通过施加一定的荷载,使试件产生不同的应变水平,从而对试件的疲劳性能进行评估。
该方法主要适用于规模较大的混凝土结构。
2. 动载试验:动载试验则是通过模拟实际使用条件下的载荷作用,对试件进行动态加载,从而研究混凝土结构的疲劳性能。
该方法主要适用于小尺寸试件的疲劳性能测试。
3. 试件制作:试件制作是通过制作混凝土构件模拟实际结构的特点和受力情况,进行疲劳性能测试。
该方法可以有效地模拟实际结构的受力情况,但试件尺寸可能会对结果产生一定的影响。
4. 应力-应变监测:该方法则是通过对试件的应变和应力进行实时监测,对混凝土结构的疲劳性能进行评估。
该方法可以比较准确地反映试件的疲劳性能,但需要一定的技术设备支持。
三、混凝土结构疲劳性能分析方法混凝土结构疲劳性能分析方法主要包括线性分析、非线性分析和疲劳寿命预测等。
1. 线性分析:线性分析主要是通过有限元方法对混凝土结构进行建模,分析其在交变载荷下的应力和应变变化情况,并预测其疲劳寿命。
ICE-flow汽车疲劳耐久性工程解决方案

ICE-flow汽车疲劳耐久性工程解决方案近年来,随着CAD/CAE 技术突飞猛进,靠实验室台架试验或试车场路试来评价或改进汽车耐久性的方法成本高、周期长,已经逐步被虚拟耐久性设计理念取代。
随着汽车行业内的竞争不断加剧,汽车制造商无不面临着如下情况:满足用户日益提高的安全性及可靠性要求的同时做到节省成本。
其中,汽车的疲劳耐久性设计就是必须面对的重要课题之一。
疲劳耐久性工程长期以来,汽车的耐久性主要靠实验室台架试验或试车场路试来评价或改进,这种设计思路成本高、周期长。
近一二十年来,CAD/CAE 技术突飞猛进,虚拟耐久性设计理念已经在一些著名的汽车公司得到了广泛应用。
一个完整的疲劳耐久性解决方案通常包括如下步骤(如图1):根据用户用途建立寿命设计目标;采集用户使用环境和试车场载荷数据;验证分析处理实测数据;创建零构件几何模型;求取零构件间所传递的载荷;获取材料的疲劳寿命性能;预估零构件的疲劳寿命;台架模拟试验;试车场耐久性试验。
图1 疲劳耐久性解决方案流程ICE-flow 的功能作为著名的疲劳耐久性技术服务公司之一的英国恩科(nCode)国际有限公司开发了一整套用于汽车耐久性设计、分析、试验及管理的硬件和软件工具——ICE-flow 系列产品。
包括:数据采集器Somat eDAQ、数据分析处理及实验疲劳软件GlyphWorks、CAE 疲劳分析软件DesignLife 和耐久性数据管理软件系统Library。
ICE-flow 集工程数据采集分析处理、疲劳寿命分析模拟、实验室台架加速和远程数据传递及管理于一身,是进行一体化抗疲劳设计必备的一个分析工具,也是进行异地协同设计的有效工具。
ICE-flow 系列产品如图2 所示,以下对各功能分别进行介绍。
图2 ICE- flow 系列产品。
高级疲劳耐久性分析和信号处理软件:FE-Safe介绍

高级疲劳耐久性分析和信号处理软件:FE-Safe 介绍ANSYS FE-SAFE 一直是多轴疲劳分析解决方案的领导者,算法先进,功能全面细致,是世界公认精度最高的疲劳分析软件。
ANSYS FE-SAFE 既支持基于疲劳试验测试应力和应变信号的疲劳分析技术,也支持基于有限元分析计算的疲劳仿真设计技术。
ANSYS FE-SAFE 具有完整的材料库、灵活多变的载荷谱定义方法、实用的疲劳信号采集与分析处理功能以及丰富先进的疲劳算法,完整的输出疲劳结果。
特色功能∙拥有基于应力应变测试信号的疲劳分析技术; ∙支持弹性、塑性,单轴、多轴的应力和局部应变全面疲劳算法; ∙丰富的材料疲劳数据库; ∙支持各种载荷输入文件格式,并对载荷信号进行分析处理; ∙概率疲劳计算载荷与材料服从某种概率分布时,在一定设计寿命下结构的生存概率; ∙可以构造复杂的疲劳载荷谱; ∙生成丰富的疲劳计算结果; ∙界面操作易学易用; ∙ CAE接口:Ansys, Nastran, Abaqus, I-deas, Hypermesh, Pro/E Mechanical。
广州有道科技培训中心 h t t p ://w w w .020f e a .c o m客户价值∙基于有限元分析的疲劳技术,实现了产品设计-CAE 仿真-疲劳设计-重设计的现代设计研发流程,使疲劳设计更加高效快速和经济实用; ∙自带信号分析处理技术使信号去假存真,并进一步提取信号的幅频特性、提取峰值序列、雨流矩阵、PSD 等,可以直接用于疲劳分析; ∙材料库提供了丰富的材料,每种材料都有缺省疲劳算法自动用于疲劳计算,便于本地化和用户化,内置Netscape link 访问国际国内发布的各种疲劳测试报告和相关数据; ∙ ANSYS 作为世界先进的CAE 分析程序,其强大的结构-热-流体-电磁耦合场分析能力,为Fe-safe 提供多种单场或耦合场载荷工况的FEA 结果,确保疲劳计算代表真实工程载荷工况;∙ 疲劳算法能同时考虑各种疲劳影响因素,多轴疲劳算法全球领先,速度快精度高。
疲劳耐久测试系统疲劳损伤谱(FDS)功能
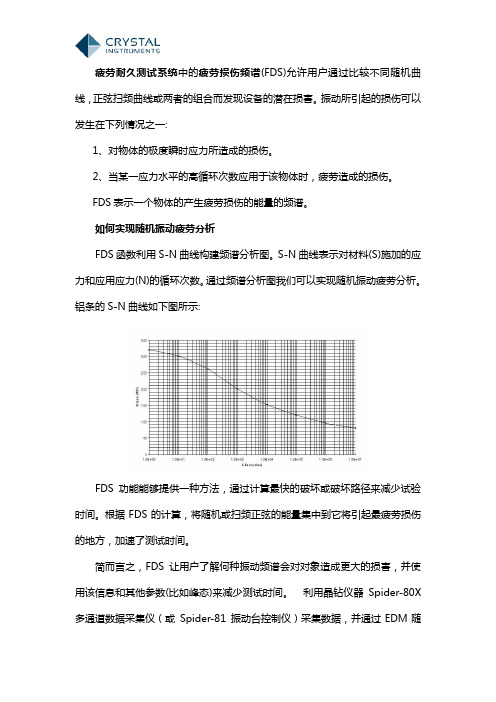
疲劳耐久测试系统中的疲劳损伤频谱(FDS)允许用户通过比较不同随机曲线,正弦扫频曲线或两者的组合而发现设备的潜在损害。
振动所引起的损伤可以发生在下列情况之一:1、对物体的极度瞬时应力所造成的损伤。
2、当某一应力水平的高循环次数应用于该物体时,疲劳造成的损伤。
FDS表示一个物体的产生疲劳损伤的能量的频谱。
如何实现随机振动疲劳分析FDS函数利用S-N曲线构建频谱分析图。
S-N曲线表示对材料(S)施加的应力和应用应力(N)的循环次数。
通过频谱分析图我们可以实现随机振动疲劳分析。
铝条的S-N曲线如下图所示:FDS功能能够提供一种方法,通过计算最快的破坏或破坏路径来减少试验时间。
根据FDS的计算,将随机或扫频正弦的能量集中到它将引起最疲劳损伤的地方,加速了测试时间。
简而言之,FDS让用户了解何种振动频谱会对对象造成更大的损害,并使用该信息和其他参数(比如峰态)来减少测试时间。
利用晶钻仪器Spider-80X 多通道数据采集仪(或Spider-81 振动台控制仪)采集数据,并通过EDM随机测试功能生成疲劳损伤谱,下图是20Hz-40Hz的4g峰值的正弦曲线的疲劳损伤谱:通过这些具体的测试,在较高的频率域内随机频谱造成的疲劳损伤大于正弦扫频曲线。
然而,在低频范围内,疲劳损伤是相似的。
当然,结果取决于测试对象的特性(比如S-N曲线的斜率)和配置文件的水平和频率范围。
这将提供一种方法来比较和研究具有相对相同级别的目标谱是否适合于运行特定的测试。
在许多测试中,目标是通过失效对象来估计对象的目标生命。
通过进行FDS分析,可以显著降低扩展测试的时间(例如,进行40小时的测试取代400小时的测试),以达到同样的目标,即试件失效。
对于一个昂贵而复杂的测试对象,如卫星,完全破坏是不需要的。
因此,利用FDS分析,可以减小应力的持续时间和强度,以观察长期振动试验中可能出现的松动部分。
杭州锐达数字技术有限公司是美国晶钻仪器公司中国总代理,负责产品销售、技术支持与产品维护,是机械状态监测、振动噪声测试、动态信号分析、动态数据采集、应力应变测试等领域的供应商,提供手持一体化动态信号分析系统、多通道动态数据采集系统、振动控制系统、多轴振动控制系统、三综合试验系统和远程状态监测系统等。
ANSYS FE_SAFE简介
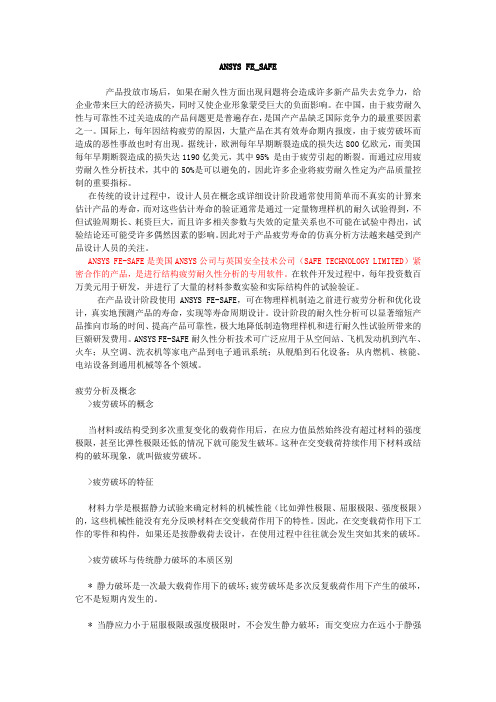
ANSYS FE_SAFE产品投放市场后,如果在耐久性方面出现问题将会造成许多新产品失去竞争力,给企业带来巨大的经济损失,同时又使企业形象蒙受巨大的负面影响。
在中国,由于疲劳耐久性与可靠性不过关造成的产品问题更是普遍存在,是国产产品缺乏国际竞争力的最重要因素之一。
国际上,每年因结构疲劳的原因,大量产品在其有效寿命期内报废,由于疲劳破坏而造成的恶性事故也时有出现。
据统计,欧洲每年早期断裂造成的损失达800亿欧元,而美国每年早期断裂造成的损失达1190亿美元,其中95% 是由于疲劳引起的断裂。
而通过应用疲劳耐久性分析技术,其中的50%是可以避免的,因此许多企业将疲劳耐久性定为产品质量控制的重要指标。
在传统的设计过程中,设计人员在概念或详细设计阶段通常使用简单而不真实的计算来估计产品的寿命,而对这些估计寿命的验证通常是通过一定量物理样机的耐久试验得到,不但试验周期长、耗资巨大,而且许多相关参数与失效的定量关系也不可能在试验中得出,试验结论还可能受许多偶然因素的影响。
因此对于产品疲劳寿命的仿真分析方法越来越受到产品设计人员的关注。
ANSYS FE-SAFE是美国ANSYS公司与英国安全技术公司(SAFE TECHNOLOGY LIMITED)紧密合作的产品,是进行结构疲劳耐久性分析的专用软件。
在软件开发过程中,每年投资数百万美元用于研发,并进行了大量的材料参数实验和实际结构件的试验验证。
在产品设计阶段使用ANSYS FE-SAFE,可在物理样机制造之前进行疲劳分析和优化设计,真实地预测产品的寿命,实现等寿命周期设计。
设计阶段的耐久性分析可以显著缩短产品推向市场的时间、提高产品可靠性,极大地降低制造物理样机和进行耐久性试验所带来的巨额研发费用。
ANSYS FE-SAFE耐久性分析技术可广泛应用于从空间站、飞机发动机到汽车、火车;从空调、洗衣机等家电产品到电子通讯系统;从舰船到石化设备;从内燃机、核能、电站设备到通用机械等各个领域。
207-应用CAE方法构建虚拟疲劳耐久性试验台
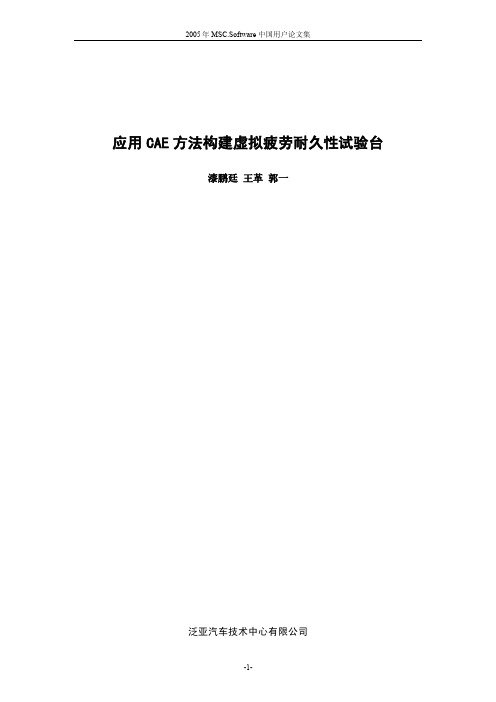
应用CAE方法构建虚拟疲劳耐久性试验台漆鹏廷王革郭一泛亚汽车技术中心有限公司应用CAE方法构建虚拟疲劳耐久性试验台Durability Test on Visual Test RigUsing CAE Method漆鹏廷王革郭一(泛亚汽车技术中心有限公司)摘要:后桥在道路试验中,发生局部开裂现象. 由于道路试验和台架试验花费的时间都比较长,不利于多种方案的比较. 为此如果应用CAE方法构建一个虚拟台架试验台, 在虚拟台架上再现真实台架上裂纹开裂过程,将有利于快速高效地解决问题. 这也可以为以后在做台架试验前, 应用CAE分析的方法, 考核哪一种试验方法能再现道路上的裂纹. 同时, 这也可在设计阶段对车架进行耐久性考核提供手段. 本次分析应用FE-Fatigue软件成功构建一个虚拟台架试验台, 进行改进方案的虚拟验证, 最终帮助解决开裂问题.Abstract: Rear axle cracked in proving ground. Proving ground and real rig test are disadvantage on every improvement case validation because much time will be spent onit. If using CAE method, this problem could be solved. In this analysis, an imitation of a real test rig is built using CAE tools. On visual rig, test is performed, and key areas that easily fail ed can be founded.关键词: 后桥, 道路试验, 台架试验, 疲劳耐久性, 裂纹Key words: Rear Axle, Proving Ground, Rig Test, Durability, Crack1 概述某款车型的后桥在道路试验过程中裂纹发生开裂. 由于道路试验和台架试验花费的时间都比较长,不利于多种方案的比较. 而且目前有多种常用的台架试验,哪一种更能反映在道路试验的破坏过程,这需要很强的经验知识才能作出一定的判断,而且容易产生错误. 但如果用CAE方法构建一个虚拟台架, 在这个虚拟台架上进行疲劳耐久性试验, 这不仅可以快速高效地进行方案比较, 而且可以帮助选择一个正确的台架试验方式. 它还能在设计阶段, 在没有物理样件的情况下, 进行台架试验,找到结构设计的薄弱环节, 为结构设计提供帮助.2 物理试验本次试验是在实际解决问题的基础上, 选择做了一个标准的台架试验. 在试验的过程中, 提取相关的数据, 用于校核虚拟试验台.2.1 试验简介试验中,固定所有与车身相连接的点,主要有:横拉杆与车身连接点,左右摇臂与车身连接的点, 左右减振弹簧与车身连接的点,左右阻尼弹簧与车身连接的点. 在左轮心施加1g 的向上静止载荷, 在右轮心施加2g的向上循环载荷. 同时输出左右减振弹簧和左右阻尼弹簧的反力, 用于校核后面的分析结果.2.2 试验结果通过上面的试验主要得到三方面的结果: 试验开裂次数, 裂纹开裂位置(见图1). 左右减振弹簧和左右阻尼弹簧载荷曲线(见图2).图1 开裂位置图2 约束反力输出结果3 CAE 虚拟试验根据以上的物理台架试验,在其他CAE 软件和FE-Fatigue 软件平台上构建如图4所示的CAE 虚拟台架. 约束所有的与车身相连接的点. 在左轮心施加1g 的向上静止载荷, 在右轮心施加2g 的向上瞬态循环载荷. 同时输出左右减振弹簧和左右阻尼弹簧的反力.3.1加载步骤Step1.约束车身固定点Step2.在左轮心施加1g 的向上静止载荷 Step3.在右轮心施加2g 的向上瞬态载荷LoadLoadLeft Spring Back Right Spring Left Damper Right Damper3.2 输出瞬态动力学分析结果关键区域的应力,位移和时间关系.左右减振弹簧和左右阻尼弹簧的反力与时间关系3.3 分析结果验证通过与测试结果的比较,校核分析结果的可信度,见图3.通过比较可以看出CAE 输出的载荷曲线与实测的载荷曲线比较一致.图3 输出的载荷曲线与实测的载荷曲线4 疲劳耐久性分析MSC.Software 公司的FE-Fatigue 软件提供了强大的疲劳耐久性分析的工具包,里面还包含众多的材料数据库, 这些都是能够获得可信的工程分析结果, 所要求的必须的前提条件. 同时, 输出的后处理结果丰富多样, 而且直观可视,有助于及时准确地发现问题,解决问题.这些都是作者选择应用FE-Fatigue 软件来完成本次分析任务的原因.4.1 材料的选择在FE-Fatigue 中施加循环载荷,选择疲劳材料特性:SAE1008_91_HR, E:2.07E5, YieldStrength:253Mpa.4.2 分析类型选择E-N 分析类型Right Spring Back Left Spring BackForce(N) Time(s)Force(N)Time(s)4.3 分析结果运行FE-Fatigue,得到如图4所示的关键危险点.得到最小寿命循环次数。
疲劳试验及其分析方法的研究与应用

疲劳试验及其分析方法的研究与应用近年来,汽车、飞机、机械等领域的发展极大地促进了人类的经济和社会进步,然而,这些高精密机械的使用却不可避免地带来了一系列涉及工程安全和健康的问题。
其中之一就是疲劳损伤。
事实上,所有材料都会经历疲劳,而重复载荷、弯曲、扭曲和震动通常是导致零件损坏的原因,进而导致事故发生。
因此,疲劳性分析变得至关重要,研究整个系统的耐久性,为工程师提供预测和防止各种疲劳现象的方法。
本文将重点介绍疲劳试验及其分析方法的研究与应用。
一、疲劳基础疲劳是由于物体在反复受到应力的作用下,经过一定次数的加载后发生异常损伤和断裂,在实际生产过程中给机械设备带来很大危害。
因此,在进行耐久性设计过程中,必须进行疲劳强度试验。
通过对构件的疲劳破坏试验分析,可以获得相应的材料、零件等物理学性质,并且能够在逐渐确定其受力下,量化分析其疲劳威胁度,以找到有效的解决方案,提高机械设备的耐久性。
二、疲劳试验方法为更好的分析疲劳效应,需要对本质的疲劳特性进行测试,并在进行疲劳寿命分析时,将这些测试中积累的数据加以利用和处理。
目前,常见的疲劳试验方法主要有6种:载荷控制疲劳试验、应变控制疲劳试验、力量降低疲劳试验、一定应力幅疲劳试验、弛豫疲劳试验和复合式疲劳试验。
您可以根据具体需要选择不同的试验方法,在其基础上结合系统化、定量地分析和处理数据,得到更具有实际意义的结果。
三、疲劳分析方法尽管疲劳试验是对材料性质的重要评估,但对于机械结构的安全性而言,疲劳分析却是更为重要的。
采用现代计算机-辅助分析技术,先将载荷历史数据转化成应力-时间/应变-时间曲线,再对其进行计算与分析,可以计算出疲劳寿命及其他性能指标。
在此基础上,结合因素分析、分类分析、回归分析等方法,以全面地预测疲劳损伤。
四、疲劳试验的应用疲劳试验不仅可以应用于机械设备 fatigue testing,而且在其他领域发挥重要作用。
例如,在汽车和气体轮机制造商中,疲劳试验可用于确保主要部件(如油泵)有足够的工作寿命;涉及到机械基础的交通运输装置,如铁路车辆和飞机,疲劳试验可以全面评估其长期安全管理的有效性;而在纺织品、食品工业和医疗工业等行业中,疲劳测试也是非常有用的。
疲劳测试和分析(理论与实践)张开桂

疲劳试验测试分析(理论与实践) 李永利、卓·帕恩、理查德·伯克希尔·哈撒韦、马克·E·巴基巴特沃斯海涅曼出版社2005第二阶段疲劳裂纹第一阶段疲劳裂纹(稳定的滑移带)图2.1 疲劳过程:承受循环拉伸载荷薄板.在工程应用中,通常将零件在裂纹成核和短裂纹扩展期间的寿命长度称为裂纹萌生期,而花费在长裂纹扩展的寿命被称为裂纹扩展期。
通常对从产生到扩展的过渡时期无法做出确切的定义。
然而,对于钢材裂纹起始阶段的裂纹尺寸a0,大约为钢材的几个晶粒大小。
这种裂纹尺寸通常在0.1至1毫米的范围内。
初始裂纹的大小可以通过线弹性断裂力学的方法对光滑试样进行估计(1998):(2.2.1)或者为切口试样切口尖端半径的0.1至0.2倍(道林,1998年),或者为彼得森钢材经验材料的两倍(彼得森,1959年)(2.2.2)其中S u是材料的极限拉伸强度,S e是疲劳极限的应力范围,K th为R=-1时临界强度因子的范围。
通常情况下,钢制零件的裂纹萌生阶段占据疲劳寿命的大部分,特别是在高频循环疲劳的状态下(约为>10,000次)。
在低频循环疲劳状态下(约<10,000次循环)的大部分疲劳寿命用于裂纹扩展。
一旦裂纹形成或发生完全失效,就可以检查到疲劳失效的表面。
弯曲或轴向疲劳失效一般留下类似海滩的层状条纹痕迹。
这些痕迹的名称来自断裂表面的形状特征,如图2.2所示。
裂纹核点位于外壳的中心,并且裂缝从该点开始传播,通常是在径向方向辐射扩展,留下一个半椭圆形的图案。
在一些情况下,痕迹的大小和位置可指明裂纹扩展开始或结束不同阶段。
在类似海滩斑纹的层状条纹上,如图2.2所示的条纹类似于树的横截面的年轮。
这些条纹代表了在一个加载周期内裂纹的扩张范围。
每一层条纹都有一个加载周期相对应。
在出现失效的情况下,会有一个最后的切变裂痕,它是材料在失效之前的最后承受载荷的区域。
这个裂痕的大小取决于加载的类型,材料和其他条件。
车辆疲劳耐久性分析、试验与优化关键技术
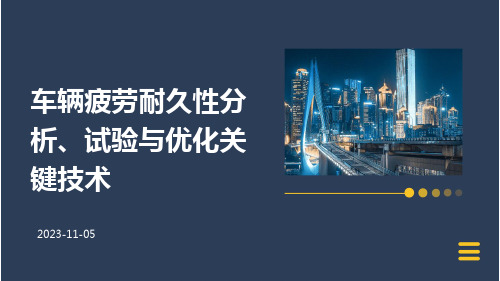
喷涂技术
喷涂技术可以提高车辆的外观质量和耐腐蚀性,如电泳涂装、静电喷涂等技术在车辆制造车辆疲劳耐久性研究展望
1
深入研究车辆疲劳损伤机理
2
3
深入研究金属材料疲劳裂纹萌生和扩展机理,包括微裂纹、界面裂纹等特殊疲劳损伤机理。
试验过程
01
安装样品
将选择的样品按照规定的安装方式安装在试验台上,确保安装牢固、稳定。
02
预处理样品
在试验开始前,对样品进行必要的预处理,如表面处理、涂层等,以消除样品本身对试验结果的影响。
数据整理
对试验过程中记录的数据进行整理,提取与疲劳耐久性相关的数据,如应力、应变、循环次数等。
数据统计
对提取的数据进行统计和分析,计算相应的指标和参数,如疲劳寿命、应力幅等。
优化设计
对新设计的发动机支架进行疲劳试验,并与原车型进行对比评估,以确保优化后的支架疲劳性能得到提升。
验证与评估
A
B
C
D
整体结构分析
利用三维扫描技术获取重型卡车的整体结构模型,进行详细的应力、应变分析。
优化设计
根据预测结果,对重型卡车的整体结构进行优化设计,如改变车身形状、增加支撑结构等。
验证与评估
针对不同使用工况和环境条件,进行疲劳寿命预测模型的修正和优化,提高预测的准确性和可靠性。
01
03
02
研究新型高强度材料和先进制造技术,以提高车辆结构和零部件的抗疲劳性能。
发展车辆疲劳耐久性设计方法和优化策略,包括优化零部件的几何形状、受力分析和优化布局等。
探索基于健康监测和无损检测的车辆疲劳损伤监测与评估技术,及时发现和修复潜在损伤,延长车辆使用寿命。
MSC车辆动态与疲劳耐久测试系统

MSC 有两座工厂,从事不同业务: 位于 Milford, Michigan,是一个 10,200 平方英尺的技术中心。
该中心的主要业务有:电子和机械设计、计算机辅助设计、有限元分
析和仪器设备的技术支持。 位于 Charlevoix, Michigan 的 30,000 平方英尺的厂房专门负
转向系的方向盘、转向轴、拉杆、球 铰链 车身各种受力部件,如门铰链,滑移门支 架,锁扣,换挡杆,车窗夹力等
旋转部件测试相关的仪器,滑环及遥测机
MSC 车辆动态与疲劳耐久测试传感器分类
MSC 车辆动态与疲劳耐久测试传感器简介
MSC 为汽车的各种系统提供测试传感器。这些系统为: 发动机系、传动系、行驶系、制动系、转向系、车身。其中 行驶系还包括悬架、车架、车轮等子系统。主要测试参数为 这些部件及系统的扭矩、应变、力、转速、温度。主要部分 如上图所示。
于对传动轴本体的改动极小,该类传感器所能承受的各种最大应力及 扭矩与原来一致。
除了传动轴之外,MSC 同样也提供万向节测试传感器。
驱动轴扭矩测试系统
半轴传感器 不同车型的半轴长短不一。我们能对所有长度及使用空间的半轴
系统提供扭矩传感器。我们提供的半轴传感器,直接由原车上的传动 轴改装而成。由于对传动轴本体的改动极小,该类传感器所能承受的 各种最大应力及扭矩与原来一致。信号传输的介质为管状滑环或轴端滑 环。
变速器输入轴扭矩传感器(可长时高速在油中工作)
9
车轮
车轮
轮胎
轮胎
制动器, 轴承, 油封 皮带轮
轮胎
制动器, 轴承, 油封
轮胎
变速器
TP:皮带轮扭矩 TC:曲轴扭矩 TF:柔性板或离合器扭矩 TT:各种齿轮及轴的扭矩 TD:传动轴扭矩 TA:驱动桥或半轴 TW:车轮扭矩
LMS在零部件疲劳耐久性试验评价中的应用

LMS在零部件疲劳耐久性试验评价中的应用彭辉何荣国胡文伟上海大众汽车有限公司,上海,201805摘要本文介绍了LMS Tecware和FALANCS LifeStat软件在零部件(以轿车支承座为例)疲劳耐久性试验评价中的应用。
提出了制定试验规范的一般方法,可供在其它零部件疲劳试验评价中参考。
关键词LMS Tecware FALANCS LifeStat 疲劳耐久性试验评价 试验规范Fatigue life evaluation of the automotive partsusing LMSPeng Hui He Rongguo Hu WenweiShanghai Volkswagen,shanghai,201805Abstract This paper introduces the application of LMS Tecware and FALANCS LifeStat to fatigue life evaluation of the automotive parts (here for example:bracket). It can also extract the general method to set up the test standard for fatigue life evaluation of other parts.Key Words LMS Tecware FALANCS LifeStat fatigue life evaluation test standard1导言某轿车支承座是后桥和车身间的一个冲压连接件(见图1),一直采用进口材料生产。
为了提高国产化率,降低成本,供应商拟采用国产材料生产,这就需要进行合理的疲劳耐久性试验评价。
由于没有针对该车型支承座的试验规范,需要根据实际使用载荷情况,制定试验规范,作为试验评价的依据。
LMS Tecware 和FALANCS LifeStat可以协助完成疲劳耐久性试验评价。
汽车排气系统局部疲劳耐久性试验仿真分析

汽车排气系统局部疲劳耐久性试验仿真分析汽车排气系统是关键的发动机零部件,它负责将废气从发动机中排出。
同时,排气系统庞大的设计,包括排气管、消声器、吸气管等部分。
因此,汽车排气系统表现出良好的疲劳耐久性是必不可少的。
为了保证汽车排气系统的疲劳耐久性,研究人员最近进行了一项试验仿真分析。
在这篇文章中,我们将简要介绍该研究的目的和结果。
研究目的汽车排气系统的疲劳耐久性与排气管、消声器、吸气管等部分有关,这些部分在长时间使用中容易发生疲劳断裂。
因此,研究团队开发了一种试验仿真模型,以模拟汽车排气系统在工作过程中的实际使用情况。
他们的目标是通过分析模型得出新的设计指导方针,以满足汽车排气系统的疲劳耐久性标准。
试验设计研究人员使用有限元方法来模拟汽车排气系统的耐久性。
他们设计了一个模型,包括了汽车的发动机和排气系统,模型使用了500000个单元,每个单元尺寸约为2毫米。
这个模型可以模拟排气系统的疲劳过程,并预测其使用寿命和压力受力情况。
试验流程在试验中,研究人员向模型中输入压力和温度数据,以模拟排气系统在工作时的真实情况。
然后,他们根据不同的载荷条件,通过数值方法计算得到了排气系统在使用过程中的应力和变形情况。
结果分析通过试验,研究者发现最容易发生疲劳断裂的区域集中在排气管与消声器连接点、消声器与吸气管连接点等重要部位。
根据评估,路上反复行驶会再次摩擦并引起底部生锈,钢桶管内腐蚀和外部碰撞等因素也是当前排气系统容易疲劳的主要原因。
研究者还发现,加大零粉和碱性物质对中空铁管表面的腐蚀也会影响其耐久性。
研究者推荐在设计阶段应考虑强度增加的措施来提高汽车排气系统的疲劳耐久性。
本文介绍了一项研究,通过试验仿真分析汽车排气系统在工作过程中的实际情况,研究者运用有限元素方法,通过输入压力和温度数据,以模拟排气系统在工作时的真实情况,最终推荐在设计过程中考虑强度增加的措施,以提高汽车排气系统的疲劳耐久性。
该研究对汽车排气系统的设计和生产具有指导意义,可以指导汽车生产厂家改进其设计和制造工艺,提高汽车的性能和质量。
FeSafe

轮毂疲劳寿命
排气管热疲劳
(A) 热应力循环 (B)热应力分布 (C) 不考虑高温蠕变疲劳寿命 (D) 考虑高温蠕变疲劳寿命 结论:高温蠕变效应使C与D疲劳位置和寿命完全不同
内燃机活塞高温蠕变疲劳
FE-SAFE
MCAE-SAFE-P09
info@
■ Fe-safe/TMF™ 热-机械疲劳分析模块
● 考虑变化的温度和应力对结构的影响,提供快速精确的疲劳寿命分析 ● 可以考虑应变率和瞬态温度对循环应力-应变响应的影响 ● 可以考虑瞬态温度对应变-寿命曲线的影响 ● 可以考虑在每个循环中的应力和温度的相位关系的影响 ● 体积应力松弛 ● 可以考虑应变老化对疲劳强度的影响
应力-应变滞后环
Turbolife应用实例
■ Fe-safe/Rotate™ 旋转机械疲劳分析模块
● 利用结构的循环对称性提高了旋转部件的疲劳分析效率 ● 疲劳分析时间缩短:自动产生一系列不同旋转角度上的应力结果 ● 有限元计算时间缩短:一次静力计算可以用来定义一个循环的疲劳载荷谱 ● 有限元计算结果文件更小:求解规模降低 ● 想要旋转角度增量小于模型对称角,则需要额外的有限元求解 ● 支持完整模型、一半模型和奇、偶对称的扇区模型
济南分公司 电话:86-31-86072996 传真:86-31-85180808
基于结构应力法的焊接疲劳求解技术
焊接疲劳寿命计算实例
FE-SAFE
FE-SAFE
高级疲劳耐久性分析和信号处理软件
■ Fe-safe/Turbolife™ 涡轮机械疲劳分析模块
● 与ANSYS等主流FEA软件的直接接口 ● 由弹性有限元计算结果来计算应力及温度的时间历程 ● 支持多轴塑性松弛准则,用来估计实际的应力和应变 ● 蠕变损伤、疲劳损伤的评估以及蠕变疲劳的计算 ● 综合考虑蠕变机理对疲劳寿命的影响 ● 多种计算参量的输出与图形化显示
ES-TEST:MTS 多轴向耐久疲劳试验机操作说明
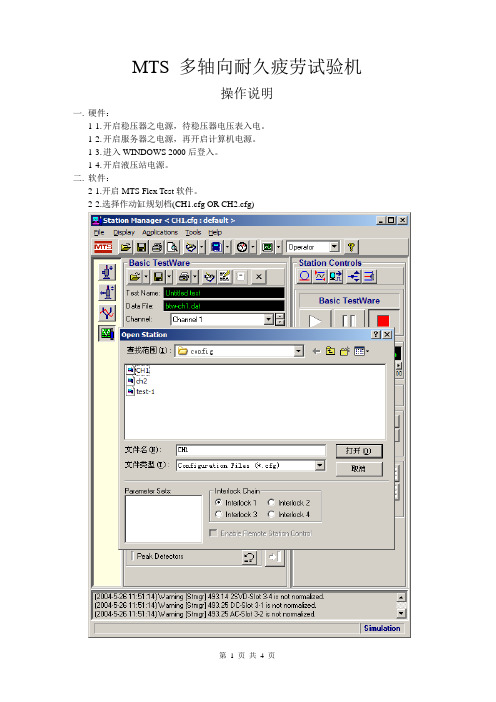
MTS 多轴向耐久疲劳试验机
操作说明
一.硬件:
1-1.开启稳压器之电源,待稳压器电压表入电。
1-2.开启服务器之电源,再开启计算机电源。
1-3.进入WINDOWS 2000后登入。
1-4.开启液压站电源。
二.软件:
2-1.开启MTS Flex Test软件。
2-2.选择作动缸规划档(CH1.cfg OR CH2.cfg)
2-3.进入测试软件后选择Basic Test Ware输入试验参数。
如:施力大小F=10.0kgf,频率=5.0Hz等
三.按规范要求安装好试验治具,并将工件按指定方式安装完毕。
四.作动缸调整与归位
4-1.于Station Control中设定极限侦测(Detectors)并启动。
4-2.将液压站冷却水开辟打开。
4-3.使用软件控制将HPU开启(顺序须由左至右)。
4-4.再将下方HSM1 OR HSM2依顺序开启。
4-5.开启Manual Controls可调整作动缸位置(配合手动控制台),并将治具与作动缸连接。
4-6.完全装设后将力量与位移归零如右
4-7.待一切就蓄后开始测试
核准:审核:作成:。
- 1、下载文档前请自行甄别文档内容的完整性,平台不提供额外的编辑、内容补充、找答案等附加服务。
- 2、"仅部分预览"的文档,不可在线预览部分如存在完整性等问题,可反馈申请退款(可完整预览的文档不适用该条件!)。
- 3、如文档侵犯您的权益,请联系客服反馈,我们会尽快为您处理(人工客服工作时间:9:00-18:30)。
Besides effective load data cleaning and validation, LMS TecWare Load Data Processing focuses on monitoring and comparison of essential loading portions from a durability perspective. With the built-in reduction methods (rainflow counting, range pair, time-at-level, spectral analysis, statistical methods….) and dedicated visualization tools, users can quickly overlay and correlate the durability impact of different road surfaces or different design variants. This helps users in selecting representative loading scenarios for further Test or CAE based Durability engineering.
2
LMS International info@lms.be
LMS TecWare and LMS TWR
Faster, easier, better multi-axial control...
Reproducing time histories on multi-axial test rigs remains a special art in many organizations. Very often, the drive file generation process takes too long. All too often, engineering intuition and years of experience are required to gain control of the rig. Invariably, little use is made of the valuable data that are generated... LMS/IST RS Time Waveform Replication provides the most advanced and flexible control features on the market today. Some modules incorporate new technologies that help slash the time required to reproduce measured or synthesized drive signals. Work that previously took a week is now often finished in a day. Others show what is happening during the process - the quality of the system model, rainflow counting and range pair diagrams, structural FRFs, time histories and error displays... All will turn an intuitive art into a faster, safer and more effective simulation process.
LMS International info@lms.be
ቤተ መጻሕፍቲ ባይዱ
LMS TecWare and LMS TWR
LMS TecWare Load Data Processing
A critical factor in successful durability engineering is gaining a precise understanding of the loads that your product will undergo during its lifetime. The use of unreliable load scenarios for Test or CAE based durability engineering inherently implies invalid fatigue performance prediction.
LMS/IST RS TWR allows the comparison of target and measured road profiles and the updating of rig control signals to be executed fully automatically.
3
LMS TecWare Load Data Processing has all the standards, hooks and connections to import data from any source: vast amounts of field load data collected after a day out on the proving ground; or predicted load data synthesized using multi-body simulations. If you are processing field load data, it is more than likely that your data will need to be cleaned and validated. LMS TecWare contains a set of tools which help you edit, manipulate and validate your data in every way.
LMS Solutions Guide
LMS TecWare and LMS TWR
LMS TecWare and LMS TWR
LMS TecWare and LMS TWR
Accelerating Test-based Durability Engineering
Executing extensive field tests to validate the durability performance of mechanical designs is very expensive and time-consuming. This pressures automotive OEMs and suppliers to efficiently reproduce equivalent laboratory tests. LMS TecWare and LMS TWR offer a robust solution that integrates and automates the physical durability testing workflow, from load data processing over test schedule optimization up to drive file generation for test rig campaigns. This complements the IST solution for test rig setup, control and data management, and durability test execution, to result in the complete and integrated Durability Alliance software suite for environmental durability simulation.