POCO技术手册_第10章
POCO C++库学习和分析 -- 异常、错误处理、调试
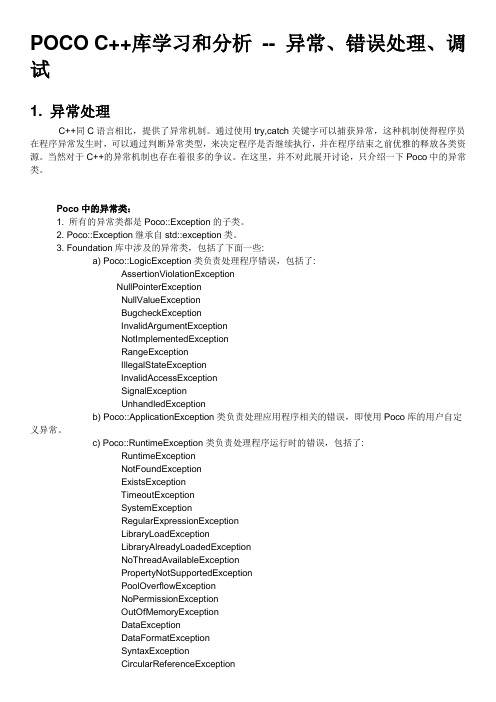
POCO C++库学习和分析-- 异常、错误处理、调试1. 异常处理C++同C语言相比,提供了异常机制。
通过使用try,catch关键字可以捕获异常,这种机制使得程序员在程序异常发生时,可以通过判断异常类型,来决定程序是否继续执行,并在程序结束之前优雅的释放各类资源。
当然对于C++的异常机制也存在着很多的争议。
在这里,并不对此展开讨论,只介绍一下Poco中的异常类。
Poco中的异常类:1. 所有的异常类都是Poco::Exception的子类。
2. Poco::Exception继承自std::exception类。
3. Foundation库中涉及的异常类,包括了下面一些:a) Poco::LogicException类负责处理程序错误,包括了:AssertionViolationExceptionNullPointerExceptionNullValueExceptionBugcheckExceptionInvalidArgumentExceptionNotImplementedExceptionRangeExceptionIllegalStateExceptionInvalidAccessExceptionSignalExceptionUnhandledExceptionb) Poco::ApplicationException类负责处理应用程序相关的错误,即使用Poco库的用户自定义异常。
c) Poco::RuntimeException类负责处理程序运行时的错误,包括了:RuntimeExceptionNotFoundExceptionExistsExceptionTimeoutExceptionSystemExceptionRegularExpressionExceptionLibraryLoadExceptionLibraryAlreadyLoadedExceptionNoThreadAvailableExceptionPropertyNotSupportedExceptionPoolOverflowExceptionNoPermissionExceptionOutOfMemoryExceptionDataExceptionDataFormatExceptionSyntaxExceptionCircularReferenceExceptionPathSyntaxExceptionIOExceptionProtocolExceptionFileExceptionFileExistsExceptionFileNotFoundExceptionPathNotFoundExceptionFileReadOnlyExceptionFileAccessDeniedExceptionCreateFileExceptionOpenFileExceptionWriteFileExceptionReadFileExceptionUnknownURISchemeException成员函数及数据定义:1. Poco::Exception包括了一个名字,这是一个静态的字符串,用来描述异常本身。
poco铂科手册

poco铂科手册【实用版】目录1.Poco 铂科手册概述2.手册的主要内容3.手册的使用方法和技巧4.Poco 铂科手册的优点和特点5.总结正文Poco 铂科手册是一款集各种实用功能于一身的在线工具书,为用户提供了丰富的信息资源。
它包含了许多实用工具,如词典、计算器、转换器等,方便用户在日常生活中快速查询和使用。
下面,我们来详细了解一下 Poco 铂科手册的主要内容、使用方法和技巧、优点和特点。
一、Poco 铂科手册概述Poco 铂科手册是一款面向广大用户的在线工具书,包含了各种实用工具和信息资源。
用户无需下载和安装任何软件,只需访问官网即可使用。
它旨在为用户提供方便、快捷、全面的信息服务,满足用户在生活、学习、工作中的各种需求。
二、手册的主要内容Poco 铂科手册主要包括以下几类实用工具:1.词典:提供了多种语言的词典查询服务,方便用户进行语言学习、翻译等工作。
2.计算器:包括各种计算器,如科学计算器、财务计算器等,满足用户在数学计算、财务分析等方面的需求。
3.转换器:支持多种单位转换,如长度、面积、体积、温度、货币等,方便用户进行各种换算。
4.其他实用工具:还包括一些生活实用工具,如菜谱、星座运势、心理测试等,丰富用户的日常生活。
三、手册的使用方法和技巧要使用 Poco 铂科手册,用户只需访问官网,即可看到各种工具的入口。
点击相应的工具,即可快速进行查询和使用。
为了提高使用效率,用户可以收藏自己喜欢的工具,方便下次直接访问。
此外,用户还可以通过搜索功能,快速找到自己需要的工具和信息。
四、Poco 铂科手册的优点和特点1.功能丰富:包含了各种实用工具和信息资源,满足用户在生活、学习、工作中的各种需求。
2.使用方便:无需下载和安装任何软件,只需访问官网即可使用,操作简单易懂。
3.更新及时:网站会定期更新工具和信息资源,确保用户使用的是最新、最准确的内容。
4.绿色环保:在线使用,无需下载,节省资源,降低环境污染。
poco铂科手册
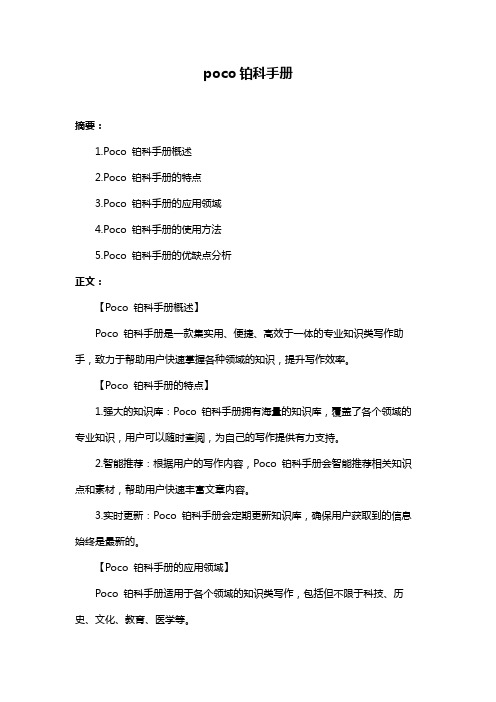
poco铂科手册摘要:1.Poco 铂科手册概述2.Poco 铂科手册的特点3.Poco 铂科手册的应用领域4.Poco 铂科手册的使用方法5.Poco 铂科手册的优缺点分析正文:【Poco 铂科手册概述】Poco 铂科手册是一款集实用、便捷、高效于一体的专业知识类写作助手,致力于帮助用户快速掌握各种领域的知识,提升写作效率。
【Poco 铂科手册的特点】1.强大的知识库:Poco 铂科手册拥有海量的知识库,覆盖了各个领域的专业知识,用户可以随时查阅,为自己的写作提供有力支持。
2.智能推荐:根据用户的写作内容,Poco 铂科手册会智能推荐相关知识点和素材,帮助用户快速丰富文章内容。
3.实时更新:Poco 铂科手册会定期更新知识库,确保用户获取到的信息始终是最新的。
【Poco 铂科手册的应用领域】Poco 铂科手册适用于各个领域的知识类写作,包括但不限于科技、历史、文化、教育、医学等。
【Poco 铂科手册的使用方法】1.下载并安装Poco 铂科手册软件。
2.打开软件,根据提示设置个人偏好和写作领域。
3.在写作过程中,如需查阅相关知识,可直接在软件中搜索,即可获取详细信息。
4.软件会根据用户的写作内容,智能推荐相关知识点和素材,用户可自行选择使用。
【Poco 铂科手册的优缺点分析】优点:1.强大的知识库,为用户提供丰富的写作素材。
2.智能推荐功能,节省用户查找资料的时间。
3.实时更新,确保用户获取到的信息始终是最新的。
缺点:1.需要用户自行下载安装,对电脑配置有一定要求。
2.软件使用过程中可能会出现卡顿现象,影响写作效率。
poco库使用手册

POCO库是一个强大的跨平台C++库,可用于编写多平台的网络应用程序。
该库支持多种平台,包括桌面端、服务端、移动端、物联网和嵌入式系统等。
使用POCO库可以带来许多优势。
首先,它支持跨平台,这意味着您编写的应用程序可以在多个平台上运行而无需修改代码。
其次,POCO库具有出色的性能表现,它经过优化以提供高效的内存管理和网络通信。
此外,POCO库还具有易于使用的API,使得开发人员可以轻松地集成到项目中。
POCO库的功能非常丰富,包括数据存储、网络编程、多线程处理、日志记录和XML 解析等。
这些功能可以帮助您快速构建功能强大的应用程序。
此外,POCO库还提供了灵活的模块化设计,使您可以根据需要仅包含所需的模块,从而减小应用程序的大小。
总之,POCO库是一个功能强大、易于使用且跨平台的C++库,非常适合开发人员构建多平台的网络应用程序。
使用POCO库可以加速开发过程,提高应用程序的性能和可靠性。
POCO技术手册_第9章
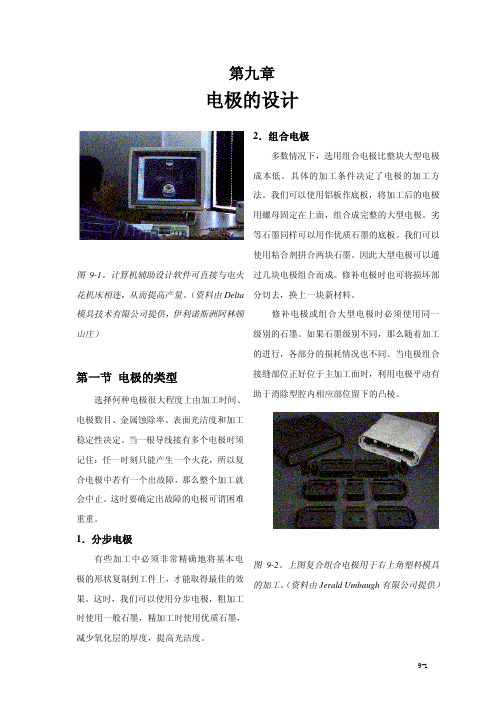
第九章电极的设计图9-1。
计算机辅助设计软件可直接与电火花机床相连,从而提高产量。
(资料由Delta 模具技术有限公司提供,伊利诺斯洲阿林顿山庄)第一节电极的类型选择何种电极很大程度上由加工时间、电极数目、金属蚀除率、表面光洁度和加工稳定性决定。
当一根导线接有多个电极时须记住:任一时刻只能产生一个火花,所以复合电极中若有一个出故障,那么整个加工就会中止。
这时要确定出故障的电极可谓困难重重。
1.分步电极有些加工中必须非常精确地将基本电极的形状复制到工件上,才能取得最佳的效果。
这时,我们可以使用分步电极,粗加工时使用一般石墨,精加工时使用优质石墨,减少氧化层的厚度,提高光洁度。
2.组合电极多数情况下,选用组合电极比整块大型电极成本低。
具体的加工条件决定了电极的加工方法。
我们可以使用铝板作底板,将加工后的电极用螺母固定在上面,组合成完整的大型电极。
劣等石墨同样可以用作优质石墨的底板。
我们可以使用粘合剂拼合两块石墨。
因此大型电极可以通过几块电极组合而成。
修补电极时也可将损坏部分切去,换上一块新材料。
修补电极或组合大型电极时必须使用同一级别的石墨。
如果石墨级别不同,那么随着加工的进行,各部分的损耗情况也不同。
当电极组合接缝部位正好位于主加工面时,利用电极平动有助于消除型腔内相应部位留下的凸棱。
图9-2。
上图复合组合电极用于右上角塑料模具的加工。
(资料由Jerald Umbaugh有限公司提供)3.局部电极现在数控电火花机床和自动换刀装置越来越多的使用局部电极,这使电极设计者能够为整个加工的不同部件选择最适合的材料和电极形状。
而选择的灵活性为电火花加工者开辟了崭新的世界,为用户带来了巨大的利润。
图9-3。
带自动换刀装置的电火花加工机床可以自动生产复合模具和模槽。
图9-4。
电脑辅助设计可从三位角度预览电极,使电火花加工者得以事先察觉可能的冲油问题。
(资料由CENTECH有限公司提供,伊利诺斯洲格伦维尤)第二节冲油设计首次看到加工成品的设计图时,您就得考虑冲油问题。
POCO技术手册_1前言
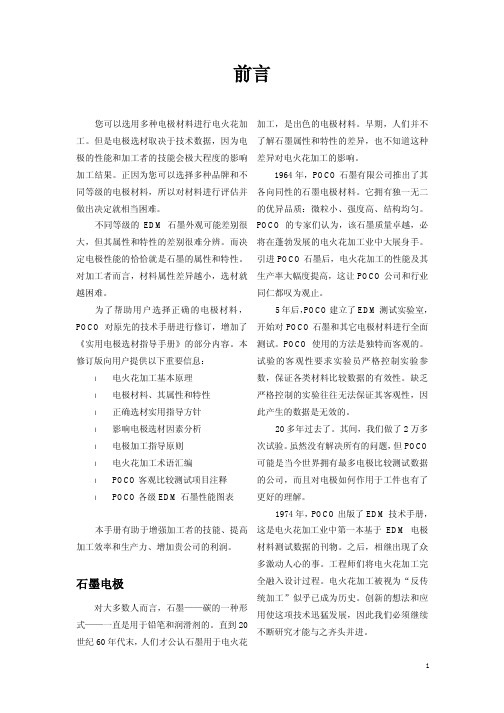
前言您可以选用多种电极材料进行电火花加工。
但是电极选材取决于技术数据,因为电极的性能和加工者的技能会极大程度的影响加工结果。
正因为您可以选择多种品牌和不同等级的电极材料,所以对材料进行评估并做出决定就相当困难。
不同等级的EDM石墨外观可能差别很大,但其属性和特性的差别很难分辨。
而决定电极性能的恰恰就是石墨的属性和特性。
对加工者而言,材料属性差异越小,选材就越困难。
为了帮助用户选择正确的电极材料,POCO对原先的技术手册进行修订,增加了《实用电极选材指导手册》的部分内容。
本修订版向用户提供以下重要信息:l电火花加工基本原理l电极材料、其属性和特性l正确选材实用指导方针l影响电极选材因素分析l电极加工指导原则l电火花加工术语汇编l POCO客观比较测试项目注释l POCO各级EDM石墨性能图表本手册有助于增强加工者的技能、提高加工效率和生产力、增加贵公司的利润。
石墨电极对大多数人而言,石墨——碳的一种形式——一直是用于铅笔和润滑剂的。
直到20世纪60年代末,人们才公认石墨用于电火花加工,是出色的电极材料。
早期,人们并不了解石墨属性和特性的差异,也不知道这种差异对电火花加工的影响。
1964年,POCO石墨有限公司推出了其各向同性的石墨电极材料。
它拥有独一无二的优异品质:微粒小、强度高、结构均匀。
POCO的专家们认为,该石墨质量卓越,必将在蓬勃发展的电火花加工业中大展身手。
引进POCO石墨后,电火花加工的性能及其生产率大幅度提高,这让POCO公司和行业同仁都叹为观止。
5年后,POCO建立了EDM测试实验室,开始对POCO石墨和其它电极材料进行全面测试。
POCO使用的方法是独特而客观的。
试验的客观性要求实验员严格控制实验参数,保证各类材料比较数据的有效性。
缺乏严格控制的实验往往无法保证其客观性,因此产生的数据是无效的。
20多年过去了。
其间,我们做了2万多次试验。
虽然没有解决所有的问题,但POCO 可能是当今世界拥有最多电极比较测试数据的公司,而且对电极如何作用于工件也有了更好的理解。
POCO技术手册_第1章
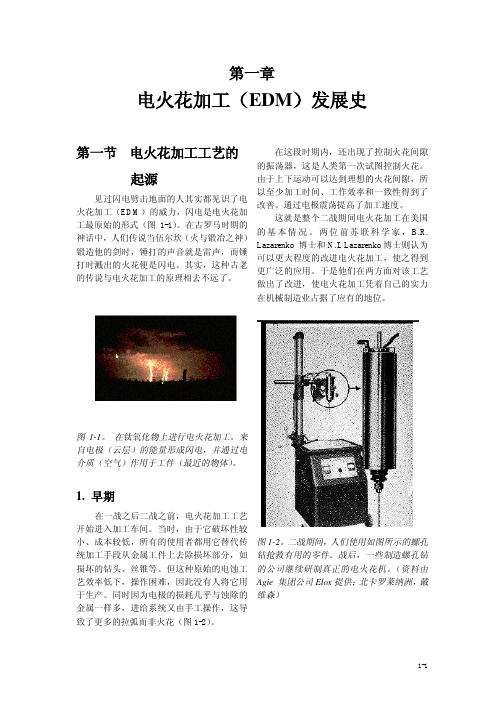
第一章电火花加工(EDM)发展史第一节电火花加工工艺的起源见过闪电劈击地面的人其实都见识了电火花加工(EDM)的威力,闪电是电火花加工最原始的形式(图1-1)。
在古罗马时期的神话中,人们传说当伍尔坎(火与锻冶之神)锻造他的剑时,锤打的声音就是雷声,而锤打时溅出的火花便是闪电。
其实,这种古老的传说与电火花加工的原理相去不远了。
图1-1。
在钛氧化物上进行电火花加工。
来自电极(云层)的能量形成闪电,并通过电介质(空气)作用于工件(最近的物体)。
1. 早期在一战之后二战之前,电火花加工工艺开始进入加工车间。
当时,由于它破坏性较小、成本较低,所有的使用者都用它替代传统加工手段从金属工件上去除损坏部分,如损坏的钻头、丝锥等。
但这种原始的电蚀工艺效率低下,操作困难,因此没有人将它用于生产。
同时因为电极的损耗几乎与蚀除的金属一样多,进给系统又由手工操作,这导致了更多的拉弧而非火花(图1-2)。
在这段时期内,还出现了控制火花间隙的振荡器,这是人类第一次试图控制火花。
由于上下运动可以达到理想的火花间隙,所以至少加工时间、工作效率和一致性得到了改善。
通过电极震荡提高了加工速度。
这就是整个二战期间电火花加工在美国的基本情况。
两位前苏联科学家,B.R. Lazarenko 博士和N.I. Lazarenko博士则认为可以更大程度的改进电火花加工,使之得到更广泛的应用。
于是他们在两方面对该工艺做出了改进,使电火花加工凭着自己的实力在机械制造业占据了应有的地位。
图1-2。
二战期间,人们使用如图所示的螺孔钻抢救有用的零件。
战后,一些制造螺孔钻的公司继续研制真正的电火花机。
(资料由Agie 集团公司Elox提供;北卡罗莱纳洲,戴维森)科学家们做出的第一项发明就是引进RC阻容张弛电路,从而对脉冲时间的控制提供了可靠的方式(图1-3)。
并由此发现了电极与工件之间的最佳距离,取得最大的切削速度。
而第二项改革是给电火花机增加一个简单的侍服控制电路,使它能够自动确定并保持设定的火花间隙。
POCO技术手册_第2章
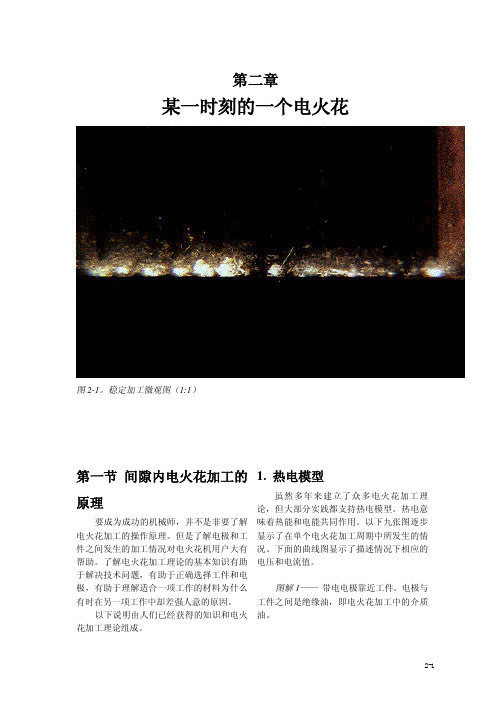
第二章某一时刻的一个电火花图2-1。
稳定加工微观图(1:1)第一节间隙内电火花加工的原理要成为成功的机械师,并不是非要了解电火花加工的操作原理。
但是了解电极和工件之间发生的加工情况对电火花机用户大有帮助。
了解电火花加工理论的基本知识有助于解决技术问题,有助于正确选择工件和电极,有助于理解适合一项工作的材料为什么有时在另一项工作中却差强人意的原因。
以下说明由人们已经获得的知识和电火花加工理论组成。
1. 热电模型虽然多年来建立了众多电火花加工理论,但大部分实践都支持热电模型。
热电意味着热能和电能共同作用。
以下九张图逐步显示了在单个电火花加工周期中所发生的情况。
下面的曲线图显示了描述情况下相应的电压和电流值。
图解1——带电电极靠近工件。
电极与工件之间是绝缘油,即电火花加工中的介质油。
尽管介质油是良好的绝缘物,但电压足够大时可以使它分解成带电离子,因此电流可以从电极间接传输到工件。
悬浮在介质油中的石墨微粒和金属微粒有助于电流的传导:这些微粒(带电导体)能够参与介质油的电离,直接携带电流;还可以促进介质油被电击穿。
如图最高点所示,当电极和工件表面的距离最小时,电场最强。
曲线图表明尽管电压不断增加,电流仍旧为零。
图解3——当介质油绝缘能力下降时,电流趋于稳定。
电压开始下降。
图解3图解4——随着电流的增加,热量快速积聚,电压继续下降。
热量使部分介质油、工件和电极气化,形成放电通道。
图解1图解2——随着电离(带电)粒子的增多,介质油的绝缘能力开始下降。
同时在电场最强的部分开始形成一条狭窄的通道。
电压达到峰点,但电流保持为零。
图解4图解2图解5——一个气泡试图向外膨胀,但由于离子受到强烈的电磁场作用,不断冲向放电通道。
这股冲力抑制了气泡的膨胀。
此时,电流不断增加,电压继续下降。
图解5图解6——当脉冲将近结束时,电流和电压都呈稳定状态,气泡中的热量和压力达到最大值,一些金属被熔蚀。
此刻,直接位于柱形放电通道下的金属层处于熔融状态,受到气泡的压力而原地不动。
poco铂科手册

Poco铂科手册一、Poco铂科简介在本节中,我们将介绍Poco铂科的背景和基本情况。
1.1 公司背景Poco铂科是一家创新科技公司,致力于提供高质量的移动设备和互联网服务。
公司成立于XXXX年,总部位于XXXXX,目前已经发展成为互联网行业的领军企业之一。
1.2 产品特点Poco铂科的产品以高性能和良好的用户体验而闻名,具有以下特点: - 强大的处理能力 - 先进的摄像技术 - 高清晰度的显示屏 - 长续航能力 - 精美的设计和制造工艺1.3 公司使命Poco铂科致力于为消费者提供创新、实用和高品质的移动设备和互联网服务,帮助用户畅享数字化生活。
二、Poco铂科手册概述本节中,我们将对Poco铂科手册的内容、目的和使用方法进行概述。
2.1 手册内容Poco铂科手册包含以下主要内容: 1. 产品介绍:详细介绍公司旗下的各类移动设备和相关配件。
2. 使用指南:提供详细的设备使用说明和技巧。
3. 常见问题:列出常见问题及解决方法,以帮助用户迅速解决设备使用中的疑难问题。
4. 售后服务:介绍售后服务政策和流程。
5. 客户支持:提供联系方式,方便用户与客户支持团队进行沟通和解决问题。
2.2 手册目的Poco铂科手册旨在为用户提供全面、详细、准确的产品信息和使用指导,帮助用户更好地了解和使用Poco铂科的产品。
2.3 手册使用方法用户在使用Poco铂科产品时,可以按照以下步骤使用手册: 1. 阅读产品介绍,了解Poco铂科产品的特点和功能。
2. 在使用设备过程中遇到问题时,查阅使用指南,按照说明操作或采取相应的解决方法。
3. 如遇到无法解决的问题,可查看常见问题,尝试寻找解决方案。
4. 如果问题依然无法解决,可联系客户支持团队,寻求专业的技术支持和解答。
5. 在购买Poco铂科产品后,如需售后服务,可参考手册中的售后服务政策和流程。
三、产品介绍本节中,我们将介绍Poco铂科的主要产品系列及其特点。
poco铂科手册
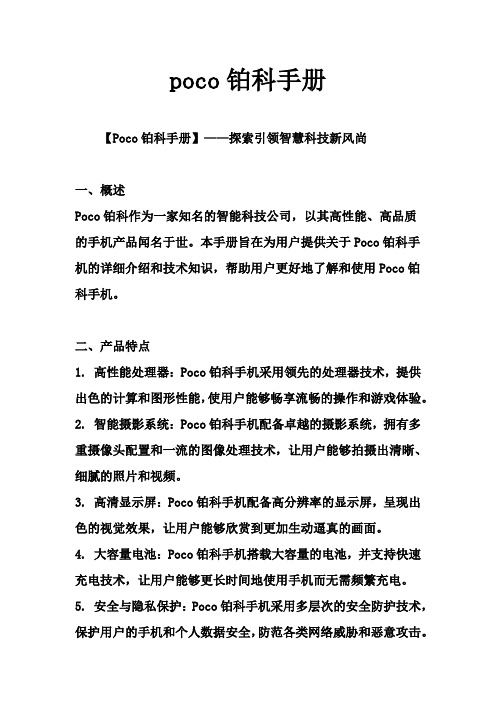
poco铂科手册【Poco铂科手册】——探索引领智慧科技新风尚一、概述Poco铂科作为一家知名的智能科技公司,以其高性能、高品质的手机产品闻名于世。
本手册旨在为用户提供关于Poco铂科手机的详细介绍和技术知识,帮助用户更好地了解和使用Poco铂科手机。
二、产品特点1. 高性能处理器:Poco铂科手机采用领先的处理器技术,提供出色的计算和图形性能,使用户能够畅享流畅的操作和游戏体验。
2. 智能摄影系统:Poco铂科手机配备卓越的摄影系统,拥有多重摄像头配置和一流的图像处理技术,让用户能够拍摄出清晰、细腻的照片和视频。
3. 高清显示屏:Poco铂科手机配备高分辨率的显示屏,呈现出色的视觉效果,让用户能够欣赏到更加生动逼真的画面。
4. 大容量电池:Poco铂科手机搭载大容量的电池,并支持快速充电技术,让用户能够更长时间地使用手机而无需频繁充电。
5. 安全与隐私保护:Poco铂科手机采用多层次的安全防护技术,保护用户的手机和个人数据安全,防范各类网络威胁和恶意攻击。
三、手机型号介绍1. Poco铂科 X系列:代表着Poco铂科的旗舰产品系列,拥有最高性能和最先进的技术配置,适合对手机性能要求较高的用户。
2. Poco铂科 M系列:注重出色的拍照能力和良好的续航表现,适合喜爱拍照和追求长续航时间的用户。
3. Poco铂科 C系列:以实惠的价格和全面的功能配置而闻名,适合初次接触Poco铂科手机的用户或预算较为有限的用户。
四、使用技巧与功能介绍1. 多任务处理:Poco铂科手机支持分屏多任务处理,使用户能够同时使用多个应用程序,提高工作效率。
2. 手势导航:Poco铂科手机支持全面屏手势导航,用户可以通过滑动屏幕完成返回、主页和最近任务等操作,简化操作流程。
3. 智能助手:Poco铂科手机搭载智能助手功能,能够提供个性化的服务和建议,帮助用户更好地管理生活和工作。
4. 游戏加速:Poco铂科手机通过软硬件优化,提供出色的游戏性能和流畅的游戏体验,支持游戏加速功能,减少卡顿和延迟。
poco断言用法 -回复
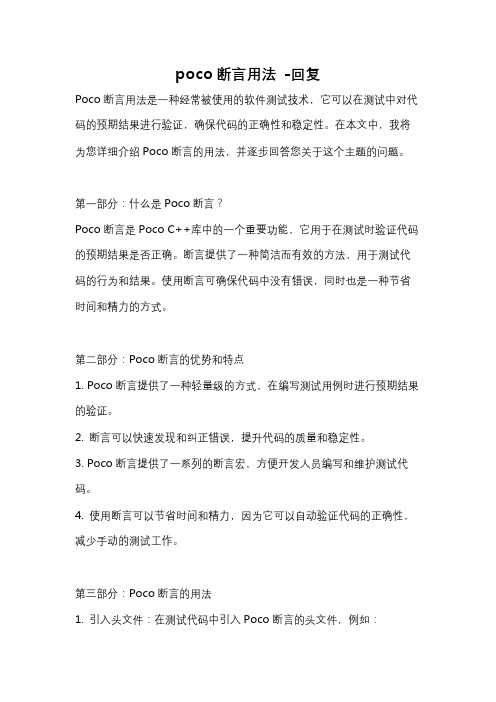
poco断言用法-回复Poco断言用法是一种经常被使用的软件测试技术,它可以在测试中对代码的预期结果进行验证,确保代码的正确性和稳定性。
在本文中,我将为您详细介绍Poco断言的用法,并逐步回答您关于这个主题的问题。
第一部分:什么是Poco断言?Poco断言是Poco C++库中的一个重要功能,它用于在测试时验证代码的预期结果是否正确。
断言提供了一种简洁而有效的方法,用于测试代码的行为和结果。
使用断言可确保代码中没有错误,同时也是一种节省时间和精力的方式。
第二部分:Poco断言的优势和特点1. Poco断言提供了一种轻量级的方式,在编写测试用例时进行预期结果的验证。
2. 断言可以快速发现和纠正错误,提升代码的质量和稳定性。
3. Poco断言提供了一系列的断言宏,方便开发人员编写和维护测试代码。
4. 使用断言可以节省时间和精力,因为它可以自动验证代码的正确性,减少手动的测试工作。
第三部分:Poco断言的用法1. 引入头文件:在测试代码中引入Poco断言的头文件,例如:cpp#include <Poco/Assert.h>2. 使用断言宏:Poco断言提供了多种断言宏,用于不同的测试场景。
以下是几个常用的断言宏的例子:- Poco_ASSERT(expr):断言一个表达式的值为真。
- Poco_ASSERT_EQUAL(x, y):断言两个值相等。
- Poco_ASSERT_NOT_EQUAL(x, y):断言两个值不相等。
- Poco_ASSERT_APPROXIMATELY_EQUAL(x, y, tolerance):断言两个浮点数的差值在给定的容差范围内。
3. 举例使用断言宏:以下是一个使用Poco断言进行测试的示例:cppvoid testCalculateArea(){Rectangle rect(5, 10);Poco_ASSERT_EQUAL(rect.calculateArea(), 50);}在上面的示例中,我们定义了一个测试用例testCalculateArea,使用Poco_ASSERT_EQUAL断言宏验证矩形的面积是否等于50。
poco铂科手册
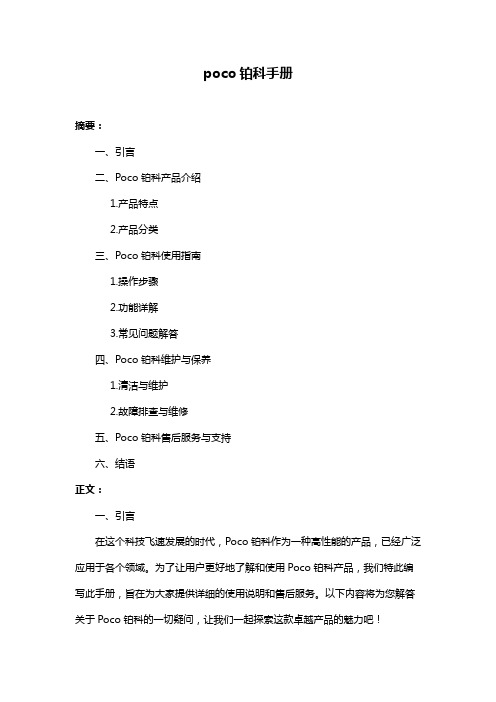
poco铂科手册摘要:一、引言二、Poco铂科产品介绍1.产品特点2.产品分类三、Poco铂科使用指南1.操作步骤2.功能详解3.常见问题解答四、Poco铂科维护与保养1.清洁与维护2.故障排查与维修五、Poco铂科售后服务与支持六、结语正文:一、引言在这个科技飞速发展的时代,Poco铂科作为一种高性能的产品,已经广泛应用于各个领域。
为了让用户更好地了解和使用Poco铂科产品,我们特此编写此手册,旨在为大家提供详细的使用说明和售后服务。
以下内容将为您解答关于Poco铂科的一切疑问,让我们一起探索这款卓越产品的魅力吧!二、Poco铂科产品介绍1.产品特点Poco铂科产品以其出色的性能、精湛的工艺和人性化的设计脱颖而出。
它具有以下特点:(1)高效能:Poco铂科采用高性能材料,确保产品在各种环境下都能稳定运行,大大提高了工作效率。
(2)高精度:Poco铂科产品具有高精度,可在细小范围内精确控制,满足各类需求。
(3)耐用性:Poco铂科产品在设计时充分考虑了耐用性,采用优质材料,确保长时间使用不磨损。
(4)易于操作:Poco铂科产品操作简便,即使是初学者也能快速上手。
2.产品分类Poco铂科产品线丰富,主要包括以下几类:(1)Poco铂科主机系列:适用于各种场景的主机产品。
(2)Poco铂科配件系列:为用户提供丰富的配件选择,提高使用体验。
(3)Poco铂科周边系列:包括各种实用工具和辅助设备,方便用户日常使用。
三、Poco铂科使用指南1.操作步骤Poco铂科产品操作简单,只需遵循以下步骤即可:(1)准备工作:确保设备连接稳定,电源充足。
(2)开机启动:按下开机键,等待设备启动。
(3)设置与应用:根据需求进行相关设置,如参数调整、模式选择等。
(4)操作执行:按照实际需求执行相应操作,如加工、测量等。
2.功能详解Poco铂科产品功能丰富,以下为您介绍几个主要功能:(1)智能控制:Poco铂科具备智能控制功能,可自动调整参数,确保设备稳定运行。
POCO技术手册_第3章
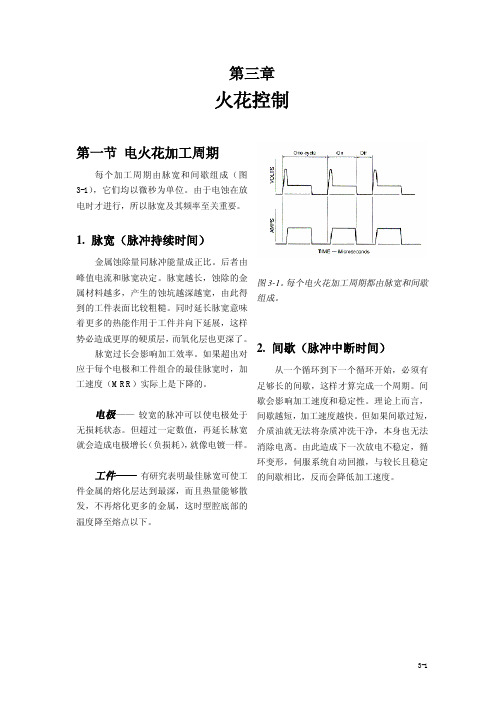
第三章火花控制第一节电火花加工周期每个加工周期由脉宽和间歇组成(图3-1),它们均以微秒为单位。
由于电蚀在放电时才进行,所以脉宽及其频率至关重要。
1. 脉宽(脉冲持续时间)金属蚀除量同脉冲能量成正比。
后者由峰值电流和脉宽决定。
脉宽越长,蚀除的金属材料越多,产生的蚀坑越深越宽,由此得到的工件表面比较粗糙。
同时延长脉宽意味着更多的热能作用于工件并向下延展,这样势必造成更厚的硬质层,而氧化层也更深了。
脉宽过长会影响加工效率。
如果超出对应于每个电极和工件组合的最佳脉宽时,加工速度(MRR)实际上是下降的。
电极——较宽的脉冲可以使电极处于无损耗状态。
但超过一定数值,再延长脉宽就会造成电极增长(负损耗),就像电镀一样。
工件——有研究表明最佳脉宽可使工件金属的熔化层达到最深,而且热量能够散发,不再熔化更多的金属,这时型腔底部的温度降至熔点以下。
图3-1。
每个电火花加工周期都由脉宽和间歇组成。
2. 间歇(脉冲中断时间)从一个循环到下一个循环开始,必须有足够长的间歇,这样才算完成一个周期。
间歇会影响加工速度和稳定性。
理论上而言,间歇越短,加工速度越快。
但如果间歇过短,介质油就无法将杂质冲洗干净,本身也无法消除电离。
由此造成下一次放电不稳定,循环变形,伺服系统自动回撤,与较长且稳定的间歇相比,反而会降低加工速度。
3. 能量电火花的能量由电流强度、电压和脉宽三者共同决定。
电流——在脉冲持续时间内,电流从零一直上升到设定值,即电流峰值(图3-2)。
电压——电流产生之前,放电间隙内的电压不断增加直到介质油中形成电离通道(图3-2)。
一旦电流产生,电压便很快下降,并稳定在预设的工作间隙电压。
该值决定了电极端面同工件之间放电间隙的宽度。
电压值越高,放电间隙越宽,冲油条件就越好,加工也比较稳定。
但是,使用石墨作为电极时,高电压会增加电极的损耗。
4. 极性极性是指电极的极性,它决定了电流的方向。
电极极性正负皆可。
根据不同的加工情况,有时改变极性可以改善加工效果。
POCO X3 NFC设备用户手册说明书
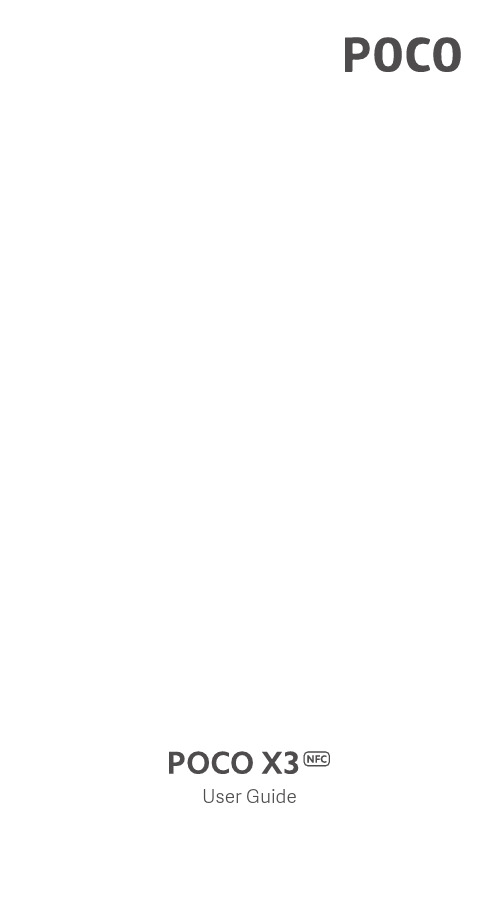
User GuideVolume ButtonsPowerButtonThank you for choosingLong press the power button to turn on the device.Follow the on-screen instructions to configure the device.For more information, visit our official website:/global/service/userguideMIUI (for POCO)POCO X3 NFC comes pre-installed with MIUI (for POCO), our customized Android-based OS which provides frequent updates and user-friendly features based on suggestions from over 200 million active users worldwide. For more information, please visit SIM Card Tray:Nano-SIM Nano-SIM Nano-SIM Micro SDAbout Dual SIM:• Dual 4G SIM is offered by select telecom operators and may not be available in all regions.• Supports dual nano-SIM cards. When using both SIM card slots, either card can be set as the primary card.• VoLTE is only supported by telecom operators in certain regions.• System may be automatically updated for optimal network performance. For details, please refer to the system version in use on the device.• Please do not insert non-standard SIM cards into the SIM card slot. They may damage the SIM card slot.• WARNING: Do not disassemble this device.WEEESpecial precautions must be taken to safely dispose of thisproduct. This marking indicates that this product may not bediscarded with other household waste in the EU.To prevent harm to the environment or human health frominappropriate waste disposal, and to promote sustainable reuse of material resources, please recycle responsibly.To safely recycle your device, please use return and collection systems or contact the retailer where the device was originally purchased.To view our Environmental Declaration, please refer to the following link: /en/about/environmentCAUTIONRISK OF EXPLOSION IF BATTERY IS REPLACED BY AN INCORRECT TYPE. DISPOSE OF USED BATTERIES ACCORDING TO INSTRUCTIONS.To prevent possible hearing damage, do not listen at high volumelevels for long periods.Additional safety information and precautions can be accessed at the following link: /en/certificationImportant Safety InformationRead all safety information below before using your device:• Use of unauthorized cables, power adapters, or batteries can cause fire, explosion, or pose other risks.• Use only authorized accessories which are compatible with your device.• This device’s operating temperature range is 0°C to 40°C. Using this device in an environment outside of this temperature range may damage the device.• If your device is provided with a built-in battery, to avoid damaging the battery or the device, do not attempt to replace the battery yourself.• Charge this device only with the included or authorized cable and power adapter. Using other adapters may cause fire, electric shock, and damage the device and the adapter.• After charging is complete, disconnect the adapter from both the device and the power outlet. Do not charge the device for more than 12 hours.• The battery must be recycled or disposed of separately from household waste. Mishandling the battery may cause fire or explosion. Dispose ofor recycle the device, its battery, and accessories according to your local regulations.• Do not disassemble, hit, crush, or burn the battery. If the battery appears deformed or damaged, stop using it immediately.-Do not short circuit the battery, as this may cause overheating, burns,or other injury.-Do not place the battery in a high-temperature environment.-Overheating may cause explosion.-Do not disassemble, hit, or crush the battery, as this may cause thebattery to leak, overheat, or explode.-Do not burn the battery, as this may cause fire or explosion.-If the battery appears deformed or damaged, stop using it immediately.• User shall not remove or alter the battery. Removal or repair of the battery shall only be done by an authorized repair center of the manufacturer.• Keep your device dry.• Do not try to repair the device yourself. If any part of the device does not work properly, contact Mi customer support or bring your device to an authorized repair center.• Connect other devices according to their instruction manuals. Do not connect incompatible devices to this device.• For AC/DC adapters, the socket-outlet shall be installed near the equipment and shall be easily accessible.Safety Precautions• Observe all applicable laws and rules restricting use of mobile phones in specific situations and environments.• Do not use your phone at petrol stations or in any explosive atmosphere or potentially explosive environment, including fueling areas, below decks on boats, fuel or chemical transfer or storage facilities, or areas where the air may contain chemicals or particles such as grain, dust, or metal powders. Obey all posted signs to turn off wireless devices such as your phone or other radio equipment. Turn off your mobile phone or wireless device when in a blasting area or in areas requiring “two-way radios” or “electronic devices” to be turned off to prevent potential hazards.• Do not use your phone in hospital operating rooms, emergency rooms,or intensive care units. Always comply with all rules and regulationsof hospitals and health centers. If you have a medical device, please consult your doctor and the device manufacturer to determine whether your phone may interfere with the device’s operation. To avoid potential interference with a pacemaker, always maintain a minimum distance of 15 cm between your mobile phone and the pacemaker. This can be done by using your phone on the ear opposite to your pacemaker and not carrying your phone in a breast pocket. To avoid interference with medical equipment, do not use your phone near hearing aids, cochlear implants, or other similar devices.• Observe all aircraft safety regulations and turn off your phone on board aircraft when required.• When driving a vehicle, use your phone in accordance with relevant traffic laws and regulations.• To avoid being struck by lightning, do not use your phone outdoors during thunderstorms.• Do not use your phone to make calls while it is charging.• Do not use your phone in places with high humidity, such as bathrooms. Doing so may result in electric shock, injury, fire, and charger damage.Security StatementPlease update your phone’s operating system using the built-in software update feature, or visit any of our authorized service outlets. Updating software through other means may damage the device or result in data loss, security issues, and other risks.EU RegulationsRED Declaration of ConformityXiaomi Communications Co., Ltd. hereby declares that this GSM / GPRS / EDGE / UMTS / LTE Digital Mobile Phone with Bluetooth and Wi-FiM2007J20CG is in compliance with the essential requirements and other relevant provisions of the RE Directive 2014/53/EU. The full text of the EU declaration of conformity is available at the following internet address: /en/certificationRF Exposure Information (SAR)This device is in compliance with Specific Absorption Rate (SAR) limits for general population/uncontrolled exposure (Localized 10-gram SAR for head and trunk, limit: 2.0W/kg) specified in Council Recommendation 1999/519/EC, ICNIRP Guidelines, and RED (Directive 2014/53/EU).During SAR testing, this device was set to transmit at its highest certified power level in all tested frequency bands and placed in positions that simulate RF exposure during use against the head with no separation and near the body with a separation of 5 mm.SAR compliance for body operation is based on a separation distance of 5 mm between the unit and the human body. This device should be carried at least 5 mm away from the body to ensure RF exposure level is compliant or lower than the reported level. When attaching the device near the body, a belt clip or holster should be used which does not contain metallic components and allows a separation of at least 5 mm to be maintained between the device and the body. RF exposure compliance was not tested or certified with any accessory containing metal worn on the body, and use of such an accessory should be avoided.Certification Information (Highest SAR)SAR 10 g limit: 2.0 W/Kg,SAR Value: Head: 0.558 W/Kg, Body: 0.986 W/Kg (5 mm distance).Legal InformationThis device may be operated in all member states of the EU.Observe national and local regulations where the device is used.This device is restricted to indoor use only when operating in the 5150 to 5350 MHz frequency range in the following countries:Restrictions in the 2.4 GHz band:Norway: This subsection does not apply for the geographical area within a radius of 20 km from the centre of Ny-Ålesund.Receiver Category 2Ensure the power adapter used meets the requirements of Clause 6.4.5 in IEC/EN 62368-1 and has been tested and approved according to national or local standards.Frequency Bands and PowerThis mobile phone offers the following frequency bands in EU areas only and maximum radio-frequency power:GSM 900: 35 dBmGSM 1800: 32 dBmUMTS band 1/8: 25 dBmLTE band 1/3/7/8/20/28/38/40: 25.7 dBmBluetooth: 20 dBmWi-Fi 2.4 GHz band: 20 dBmWi-Fi 5 GHz: 5150 to 5250MHz: 20 dBm, 5250 to 5350 MHz: 20 dBm,5470 to 5725 MHz: 20 dBm, 5725 to 5825 MHz: 14 dBmNFC: 13.56 MHz < -24.131 dBuA/m at 10mFCC RegulationsThis mobile phone complies with part 15 of the FCC Rules. Operation is subject to the following two conditions: (1) This device may not cause harmful interference, and (2) this device must accept any interference r eceived, including interference that may cause undesired operation.This mobile phone has been tested and found to comply with the limits for a Class B digital device, pursuant to Part 15 of the FCC Rules.These limits are designed to provide reasonable protection against harmful interference in a residential installation.This equipment generates, uses and can radiate radio frequency energy and, if not installed and used in accordance with the instructions, may cause harmful interference to radio communications.However, there is no guarantee that interference will not occur in a particular installation. If this equipment does cause harmful interference to radio or television reception, which can be determined by turning the equipment off and on, the user is encouraged to try to correct the interference by one or more of the following measures:-Reorient or relocate the receiving antenna.-Increase the separation between the equipment and receiver.-Connect the equipment into an outlet on a circuit different from that to which the receiver is connected.-Consult the dealer or an experienced radio/TV technician for help.RF Exposure Information (SAR)This device meets the government’s requirements for exposure to radio waves. This device is designed and manufactured not to exceed the emission limits for exposure to radio frequency (RF) energy. The exposure standardfor wireless devices employs a unit of measurement k nown as Specific Absorption Rate, or SAR.The SAR limit set by the FCC is 1.6 W/Kg. For body-worn operation, this device has been tested and meets the FCC RF exposure guidelines for use with an accessory that contains no metal and positions the device a minimum of 1.0 cm from the body. RF exposure compliance with any body-worn accessory that contains metal was not tested and certified, and use of such body-worn accessory should be avoided. Any accessory used with this device forbody-worn operation must keep the device a minimum of 1.0 cm away from the body.FCC NoteChanges or modifications not expressly approved by the party responsible for compliance could void the user’s authority to operate the equipment.E-labelThis device has an electronic label for certification information.To access it, please go to Settings > About phone > Certification, or open Settings and type “Certification” into the search bar.Model: M2007J20CG2007 indicates that this product will be launched after 202007. AdapterManufacturer: Xiaomi Communications Co.,Ltd.address: #019, 9th Floor, Building 6, 33 Xi’erqi Middle Road, Haidian District, Beijing, ChinaModel: MDY-11-EYInput Voltage: 100-240V~Input Frequency: 50/60HzOutput Voltage: 5.0V/9.0V/12.0V/20.0V/11.0VOutput Current: 3.0A/3.0A/2.25A/1.35A/3.0A MaxOutput power: 15.0W/27.0W/27.0W/27.0W/33.0W MaxAverage active efficiency: ≥82.0%DisclaimerThis user guide is published by Xiaomi or its local affiliated company. Improvements and changes to this user guide necessitated by typographical errors, inaccuracies of current information, or improvements to programs and/or equipment, may be made by Xiaomi at any time and without notice. Such changes will, however, be incorporated into new online editions of the user guide (please see details at /global/service/userguide). All illustrations are for illustration purposes only and may not accurately depict the actual device.This smartphone is designed withCorning® Gorilla® Glass 5.Manufacturer: Xiaomi Communications Co., Ltd.Manufacturer postal address:#019, 9th Floor, Building 6, 33 Xi’erqi Middle Road,Haidian District, Beijing, China, 100085M2007J20CGBrand: POCO Model:© Xiaomi Inc. All rights reserved.。
SoMachine Basic中文培训手册
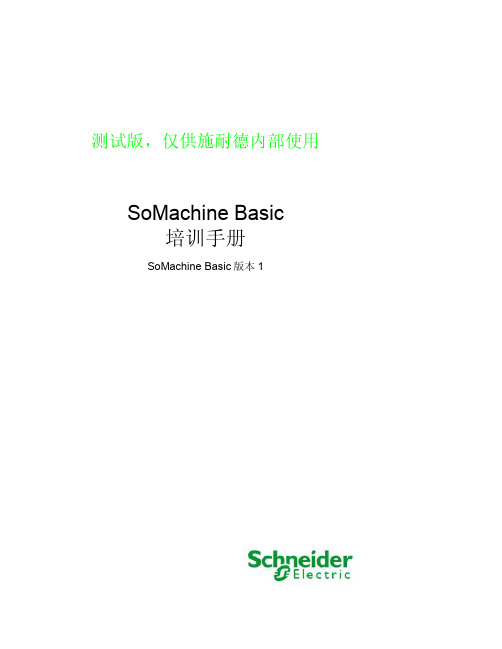
viii
SoMachine Basic 版本 1
2013 年 9 月
课程开始前(续)
启动和测试
在施行本培训时,在电气控制和自动化设备的设计和安装后、使用前,必须由符 合资格的人员对应用和相关功能性安全系统执行一项启动测试,以核实设备的正 确运行。重要的是,要安排执行此项测试,并留出足够的时间以执行完全和合格 的测试。
注意:
与作业点保护相关的互锁和安全措施的协调不在本培训文档的实例和建议实施措 施范围内。
有时候可能会错误调试设备,也许会造成不满意或不安全的操作。总是使用制造 商指示作为功能性调试的指南。可以进行该类调试的人员必须熟悉设备制造商指 示以及与该电气设备一同使用的机械装置。
x
SoMachine Basic 版本 1
有效性注意事项
当前的手册适用于负责所述产品实施、操作和维护的合资格技术人员。它包含合理使用产品所需了解的信息。
关于我们
施耐德电气的教学设计小组成员具有教育学、教育课程开发的三级资格,也是经验丰富的教员。目前,该小组正在从事一系列多 语言、多软件环境的施耐德电气课程的开发和教学。
作者
Richard Irons
符合资格的人员指的是具备电气设备的构建和操作,以及安装方面的相关技能和 知识,并已接受安全培训,能够识别并规避相关危险的人员。
iv
SoMachine Basic 版本 1
2013 年 9 月
课程开始前
本培训手册 的范围
本培训手册是对授权培训的一项补充。为了正确使用软件,学员应同时参考产品 提供的文档,如帮助文件、用户指南或知识库。
SoMachine Basic
手册 第 1 次发布
Poco入门介绍
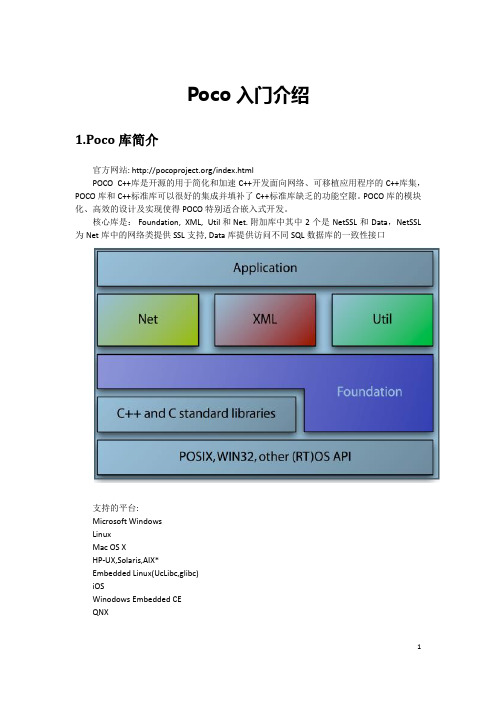
Poco入门介绍1.Poco库简介官方网站: /index.htmlPOCO C++库是开源的用于简化和加速C++开发面向网络、可移植应用程序的C++库集,POCO库和C++标准库可以很好的集成并填补了C++标准库缺乏的功能空隙。
POCO库的模块化、高效的设计及实现使得POCO特别适合嵌入式开发。
核心库是: Foundation, XML, Util 和 Net. 附加库中其中2个是NetSSL和Data,NetSSL 为Net库中的网络类提供SSL支持, Data库提供访问不同SQL数据库的一致性接口支持的平台:Microsoft WindowsLinuxMac OS XHP-UX,Solaris,AIX*Embedded Linux(UcLibc,glibc)iOSWinodows Embedded CEQNX2.常用功能点> Any and DynamicAny classes> Cache framework> Cryptography (cryptographic hashes, encryption based on OpenSSL)> Date and Time classes> Events (signal/slot mechanism) and notifications framework> FTP client for transferring files> Filesystem classes for platform-independent path manipulation,directory listing and globing > HTML form handling> HTTP server and client (also secure), C++ Server Page Compiler> Logging framework> Multithreading: basic threads and synchronization and advanced facilities (thread pool, active objects, work queues, etc.)> POP3 client for receiving mail> Platform Abstraction: write once, compile and run on multiple platforms> Processes and IPC> Reactor framework> Regular expressions (based on PCRE)> SMTP client for sending mail> SQL database access (SQLite, MySQL, ODBC)> SSL/TLS support based on OpenSSL> Shared library and class loading>Smart pointers and memory management (buffer, pool)> Sockets and raw sockets> Stream classes for Base64 and HexBinary encoding/decoding, compression (zlib), line ending conversion, reading/writing tomemory, etc> String formatting and string utilities> TCP server framework (multithreaded)> Text encodings and conversions> Tuples> URI handling> UTF-8 and Unicode support> UUID handling and generation> XML parsing (SAX2 and DOM) and XML generation> Zip file manipulation2.编译安装2.1 windows下的编译安装2.1.1 Visual Studio 2008 下的编译安装---省略演示2.1.2 Eclipse 下的编译安装---演示为主1.安装MinGW+msys cygwin2.安装eclipse3.设置eclipse编译工具链2.2 unix/linux平台下的编译安装主要步骤如下:1.2.3.HelloWorld 开发自己的第一个应用3.1构建自己的工程a.创建工程目录hellWorldb.创建目录include src 目录helloWorld/include/srcMakefilec. 创建hellWorld.cpp文件3.2编写Makefile警告:Objects,target,target_version,target_libs变量最末尾一定不能有空格,否则编译会出现异常3.3 编译Gmake shared_release3.4 运行3.5 调试4.核心模块介绍4.1.跨平台编译包编译脚本目录$POCO_BASE/build常见的修改:POCO_BASE 定义poco代码目录OSARCH_64BITS =1 定义64位编译模式SRCDIR = src makefile与.cpp的位置INCDIR = include .h文件夹LIBDIR = lib lib文件夹BINDIR = bin bin文件夹OBJDIR = obj/$(OSNAME)/$(OSARCH)DEPDIR = .dep/$(OSNAME)/$(OSARCH)LIBPATH = $(POCO_BUILD)/$(LIBDIR)BINPATH = $(POCO_BUILD)/$(COMPONENT)/$(BINDIR) -->建议改为$(BINDIR)OBJPATH = $(POCO_BUILD)/$(COMPONENT)/$(OBJDIR)-->可以不用管)$(OBJDIR)DEPPATH = $(POCO_BUILD)/$(COMPONENT)/$(DEPDIR)-->依赖文件目录)$(DEPDIR)系统自带的编译指令:all: $(DEFAULT_TARGET)all_static: static_debug static_releaseall_shared: shared_debug shared_releaseall_debug: static_debug shared_debugall_release: static_release shared_release自定义编译指令:CFLAGS += -gCXXFLAGS += -gPOCO_FLAGS +=COMMONFLAGS = -DPOCO_BUILD_HOST=$(HOSTNAME) $(POCO_FLAGS)添加额外的头文件路径:POCO_ADD_INCLUDE += $(ORACLE_HOME)/precomp/public $(ORACLE_HOME)/rdbms/public $(ORACLE_HOME)/rdbms/demoPOCO_ADD_LIBRARY +=$(ORACLE_HOME)/$(OraLib)添加额外的链接库非POCO编译出来的库SYSLIBS +=-locci -lclntsh编译方式:gmake shared_releasegmake shared_debuggmake static_releasegmake static_debuggmake all_releasegmake all_debuggmake all4.2.Foundation库4.2.1 core 模块a.Platform abstraction1.统一了各个平台的数据类型比如long ,int ,long long 等,参考types.h2.平台的big-endian和little-endian 参考ByteOrder.h3.平台类型相关信息platform.hb. Memory Management1.智能指针(smart pointer)和共享指针(shared pointer) 参考AutoPtr.h,SharedPtr.h2.据以引用计数器的垃圾回收机制AtomicCounter.h,refCountedObject.h3.单件类(singleton objects) SingletonHolder.hc.String Utilities字符串的比较(大小写转换,大小写无关转换,去除空白符号,字符转换和连接,分拆),参考String.h,StringTokenizer.hd.Error Handling1. 断言类,类似assert,主要使用宏断言,比如poco_asert(myPtr);参考Bugcheck.h2.异常类, 了解Poco::exception结构,使用POCO_DECLARE_EXCEPTION宏,参考Exception.h4.2.2.streamspass4.2.3.Threadingpass4.2.4.DateTimea.Timestamp 微秒级精度,对gettimeofday()封装,参考Timestamp.hb.Stopwatch 计时器,参考Stopwatch.hc.DateTime 日历时间,参考DateTime.hd.日历时间的格式转换DateTimeFormat,DateTimeFormatter,DateTimeParser 等e.日历时区Timezonef.本地时间LocalDateTime4.2.5 FileSystem与平台无关的文件,目录的操作类。
OP10说明书
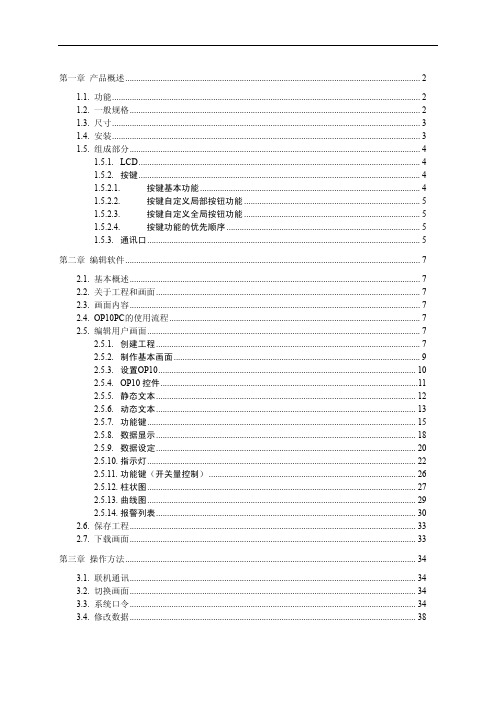
第一章 产品概述 (2)1.1. 功能 (2)1.2. 一般规格 (2)1.3. 尺寸 (3)1.4. 安装 (3)1.5. 组成部分 (4)1.5.1. LCD (4)1.5.2. 按键 (4)1.5.2.1. 按键基本功能 (4)1.5.2.2. 按键自定义局部按钮功能 (5)1.5.2.3. 按键自定义全局按钮功能 (5)1.5.2.4. 按键功能的优先顺序 (5)1.5.3. 通讯口 (5)第二章 编辑软件 (7)2.1. 基本概述 (7)2.2. 关于工程和画面 (7)2.3. 画面内容 (7)2.4. OP10PC的使用流程 (7)2.5. 编辑用户画面 (7)2.5.1. 创建工程 (7)2.5.2. 制作基本画面 (9)2.5.3. 设置OP10 (10)2.5.4. OP10控件 (11)2.5.5. 静态文本 (12)2.5.6. 动态文本 (13)2.5.7. 功能键 (15)2.5.8. 数据显示 (18)2.5.9. 数据设定 (20)2.5.10. 指示灯 (22)2.5.11. 功能键(开关量控制) (26)2.5.12. 柱状图 (27)2.5.13. 曲线图 (29)2.5.14. 报警列表 (30)2.6. 保存工程 (33)2.7. 下载画面 (33)第三章 操作方法 (34)3.1. 联机通讯 (34)3.2. 切换画面 (34)3.3. 系统口令 (34)3.4. 修改数据 (38)第四章通信 (40)4.1. 通讯口 (40)4.2. 通信连接 (40)4.2.1. 下载用户程序 (40)4.2.2. 与TP03 PG口以RS-422方式连接 (41)4.2.3. 与TP03 485口连接 (41)4.2.4. 与EV300 连接 (41)4.2.5. 与SV300 连接 (42)第一章 产品概述1.1.功能OP10是一个小型的人机界面,主要与各类PLC(或带通信口的智能控制器)配合使用,以文字或指示灯等形式监视、修改PLC内部寄存器或继电器的数值及状态,从而使操作人员能够自如地控制机器设备。
PRODOK中文入门手册
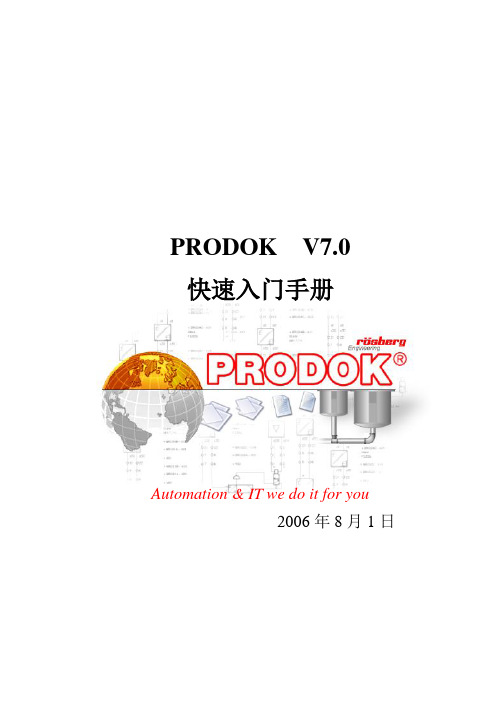
PRODOK V7.0快速入门手册Automation & IT we do it for you2006年8月1日目录1 光盘内容介绍 (1)2软件安装 (2)2.1硬件要求 (2)2.2软件要求 (2)2.3安装指导 (2)2.4 版本更新 (5)2.5硬件加密“狗” (5)2.5.1作用简介 (5)2.5.2安装方法 (6)2.6帮助信息 (7)3用户管理 (7)3.1作用简介 (7)3.2用户管理 (8)4工程创建 (9)4.1项目管理 (9)4.1.1项目窗口展示 (9)4.1.2控件功能 (9)4.2主数据模块 (10)4.2.1功能简介 (10)4.2.2主数据设置 (10)4.2.3 主数据编辑 (11)4.3初步设计 (18)4.3.1设计简介 (18)4.3.2初步设计 (19)4.4逻辑图 (23)4.4.1功能简介 (23)4.4.2设计步骤 (23)4.5详细设计 (27)4.5.1功能简介 (27)4.5.2资源管理 (27)4.5.3模块连线 (29)4.5.4图纸生成 (30)5文档管理 (32)5.1功能简介 (32)5.2 创建文档 (32)5.3 打印文档 (33)5.4 文档时间追踪功能 (34)5.5 网页浏览功能 (37)6结束语 (39)1 光盘内容介绍PRODOK软件必须在有硬件加密“狗”的情况下才能正常运行,因此我们制作了一张示例光盘。
通过该光盘,我们把系统的安装,基本使用方法均用FLASH 形式演示。
内容包括:1.系统安装2.用户管理3.主数据编辑4.初步设计5.详细设计6.逻辑图建立7.文档管理PRODOK不仅可以对工程项目进行新建与改造,还具有非常强大的文档管理功能,因此可以满足对项目维护的需求。
接下来我们将较为详细的向您介绍我们软件的安装及基本使用方法。
2软件安装2.1硬件要求2.2软件要求Windows 2000 NT4/Windows XP Sp2以上版本Visual Foxpro 6.0以上版本Auto CAD 2000 以上版本与Windows相兼容的网络2.3安装指导在满足上述软硬件要求的前提下我们可以遵循以下步骤进行系统的安装:1.将安装光盘插入光驱中。
PetaPoco参考手册
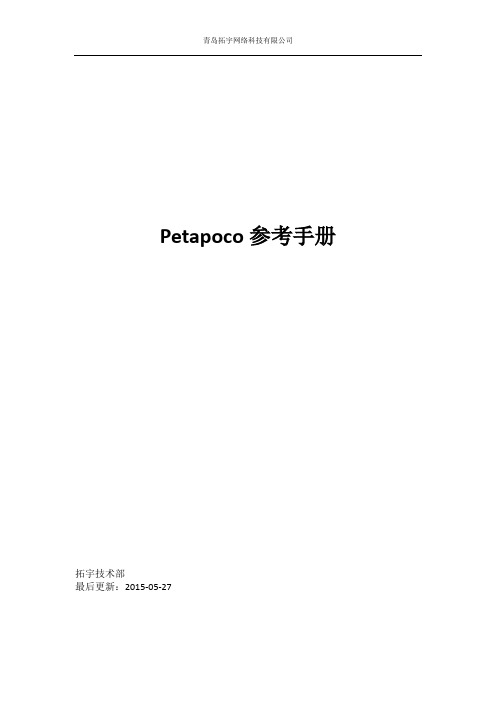
Petapoco参考手册拓宇技术部最后更新:2015-05-27目录1.Petapoco介绍 (3)1.1 Petapoco是干什么的? (3)1.2 Petapoco的特色 (3)1.3 Petapoco官网及下载地址 (3)2.Petapoco引用 (3)2.1 使用NuGet方法 (3)2.2 使用手动添加方法 (5)3.Petapoco使用 (6)3.1 添加数据库连接 (6)3.2 创建实体 (6)3.3 DataBase的调用 (6)4.Petapoco基本操作 (7)4.1 添加 (7)4.2 删除 (7)4.3 修改 (7)4.4 查询单条 (8)4.5 查询全部 (8)5.Petapoco扩展操作 (8)5.1 分页 (8)5.2 增删改简化 (9)5.3 查询扩展属性 (10)5.4 不带查询的指令Execute (11)5.5 Fetch和Query的区别 (11)5.6 FirstOrDefault (12)5.7 ExecuteScalar 查询数量 (13)1.P etapoco介绍1.1 Petapoco是干什么的?PetaPoco是一款适用于.Net 和Mono的微小、快速、单文件的微型ORM。
1.2 Petapoco的特色●微小,没有依赖项,单个的C#文件可以方便的添加到任何项目中●支持动态的扩展●支持对象和数据库表之间的关系●支持T4模版生成poco类(T4模版定义的是生成类的模版,用于自动生成代码)●使用sql语句进行查询1.3 Petapoco官网及下载地址官网:/petapoco/下载地址:https:///toptensoftware/petapoco2.P etapoco引用2.1使用NuGet方法右键引用点击管理NuGet程序包在联机下搜索Petapoco并安装安装完成后在Model中会生成Petapoco类(Petapoco的核心)2.2 使用手动添加方法在官网下载最新的Petapoco在项目中添加现有项,位置如下图3.P etapoco使用3.1 添加数据库连接在web.config中添加数据库连接3.2 创建实体在Model中创建实体3.3 DataBase的调用4.P etapoco基本操作4.1添加4.2删除4.3修改4.4查询单条4.5 查询全部5.Petapoco扩展操作5.1 分页分页方法使用的是Petapoco里的Page类型在视图中也有一点不同Page类型不能直接使用foreach,需要把page类型转为list,如下图Model.Items翻页只需要把页数的参数(Model.CurrentPage)返回到控制器中分页显示的数目是参数(Model.ItemsPerPage)5.2 增删改简化之前说的增删改的参数需要表名主键实体我们在model中加上一些信息TableName和PromaryKey 表名和主键这里需要引用Petapoco这时只需要一个实体的参数,删除和修改也是如此5.3 查询扩展属性查询时可以使用Sql.Append(“”)直接写查询语句,与Sql中相同使用Sql.Select时,例如Where Inner Join Order By使用方法如下图5.4 不带查询的指令Execute使用Execute方法,直接使用Sql语句,但是不能使用查询5.5 Fetch和Query的区别Fetch返回的是List类型Fetch也可以用作分页(不过是List类型)参数和Page相同,页码和每页显示数量Query返回的是IEnumerable类型5.6 FirstOrDefault获取条件下的第一条数据5.7 ExecuteScalar 查询数量查询时需要注意Select count(*),ExecuteScalar可直接查询数量。
第9章 进阶技术
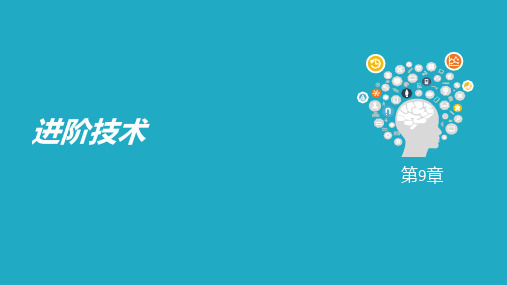
2021/10/19
第9章 进阶技术
8
手势检测
注意点
➢ 有返回值的手势事件方法的结果都会返回到View的onTouchEvent方法中,会影响View的事 件分发
➢ onDown()方法应返回true,否则就只能触发onDown()和onLongPress()事件,其他的手势时间 都不能触发,因为影响了事件的分发过程
第9章 进阶技术
18
Jetpack的优势
轻松管理应用程序的生命周期 构建可观察的数据对象,以便在基础数据库更改时通知视图 存储在应用程序转换中未销毁的UI数据,界面重建后恢复数据 轻松实现SQLite数据库 系统自动调度后台任务的执行,优化性能
2021/10/19
第9章 进阶技术
19
Jetpack的构成
保存到文件 ➢ 调用GestureLibrary对象的recognize()方法进行手势识别
案例:D0901_Gesture
2021/10/19
第9章 进阶技术
11
9.2 传感器开发
传感器简介
传感器:用来探测外界信号、物理条件或化学组成的物理设备,它能将探测 的信息传输给其它设备或部件
Android支持的传感器包括:
2021/10/19
第9章 进阶技术
13
使用传感器
涉及的类
➢ SensorManager类:传感器管理类,提供访问传感器列表、注册或注销传感器的事件监听、 获取方位信息等方法,通过getSystemService()方法获取它的实例对象
➢ Sensor类:传感器类,提供访问传感器技术参数的方法,包括名称、类型、版本以及供应 商等
基本原理
- 1、下载文档前请自行甄别文档内容的完整性,平台不提供额外的编辑、内容补充、找答案等附加服务。
- 2、"仅部分预览"的文档,不可在线预览部分如存在完整性等问题,可反馈申请退款(可完整预览的文档不适用该条件!)。
- 3、如文档侵犯您的权益,请联系客服反馈,我们会尽快为您处理(人工客服工作时间:9:00-18:30)。
第十章电极的加工第一节传统加工法人们可用通用设备加工石墨,但必须提供相应的除尘设备,控制石墨加工造成的污染。
您可以根据加工规模和类型使用多种有效的除尘系统和方法。
如果没有除尘设备,就无法进行石墨加工。
不同等级石墨的密度、强度、挠曲强度和抗压强度均不同,这些属性会影响其本身的可加工性和刀具所受的压力及其磨损。
通常在特定的加工情况下,电极的尺寸和形状将决定使用石墨的品牌和等级。
只有使用数控电火花机床对优质石墨进行加工才能得到高精度的电极。
1.通用加工准则加工石墨应使用标准的加工方法, 包括保持刀具的刚度,尽量使用刀具的副后角和正前角进行切削,确保刀具的锋利,降低刀具所受的压力等。
不同的加工情况要求的操作参数可能与下列通用准则稍有出入。
2.锯削用此方法进行加工时应使用转速为2100- 3100平方英尺/分钟的标准碳钢锯条。
锯齿分布为每英寸10个。
首先调整进给量,以免锯齿超负荷或锯条被卡住。
调整动力最恰当的方法就是不断增加进给量,直到每次完成切削时,锯条在锯穿石墨的刹那产生轻微的加速为止。
不同的锯条使用的进给量和调整量都不同,所以即使在相似的设备上进行加工,也必须经过试验才能确定进给量。
您还得降低锯臂,使之同工件之间保持6mm的最大间隙,从而确保锯条的刚度。
材料导板的各个部位应保持一定的刚度,以防石墨移动、锯条弯曲、降低加工精度、损坏锯条。
3.车削相对于一般的石墨,用高强度石墨加工长棒和圆柱可用转速较高的车削进行加工。
由于大型圆柱加工时不会发生偏移,所以可以用于深度切削。
切削深度为25mm的特殊刀具可以加工直径为100mm、长1000mm的圆柱。
加工时应降低进给速度,粗加工为0.13mm/转,精加工为0.025-0.076mm/转。
加工深度与表面光洁度有非同寻常的关系。
车削石墨时,切削深度为0.38-0.50mm 的加工比深度仅为0.13mm的最终的表面光洁度好,这是因为石墨被切削时,不像金属以塑性流变的方式切开,而是碎裂,也因此,加工石墨时无需另开断屑槽。
过大的压力会使石墨加工部位在未完成切削之前崩掉,因此加工中不能使用方鼻形的刀具,而应使用20度锐角的斜角刀具。
通常进行车削加工时,我们建议您使用优质的碳化钨硬质合金刀具或金刚石刀具,用正前角加工,前角半径为0.40~0.80mm。
工装支持——与其他石墨相比,高强度石墨可以装夹得更紧些,因为它们能产生更大的刀具压力,但也不宜夹得过紧。
可能的话,使用弹簧夹固定石墨。
这样可以减少换件时间,降低加工成本。
加工时应按常规方法适当调整活顶尖,以防材料在顶尖上自由转动。
同时应避免活顶尖过载。
石墨加工中不能使用死顶尖,因其磨损很快。
可以使用托架,但一定要用活转子。
固定的铜尖会在石墨上刻出凹痕。
您必须调整转子的压力,使石墨始终处于中心位置旋转。
转子不得过载。
加工石墨时不宜使用跟刀架。
4.铣削为了避免加工时刀具颤动,须调整好镶条,固定住加工材料,并降低工具进给率。
刀具的崩刃和磨损是立铣时经常碰到的问题。
摩擦会产生过大的压力,刀具经常因此而崩刃。
由于刀具的磨损无法避免,所以我们必须经常检查并更换刀具。
优质品牌的端面铣削刀具如强生、Basset、Wendt-Sonis 等比较耐损耗。
铣刀脱离工件时总会造成石墨崩块。
为了防止崩块,您应该使用锋利的刀具,正前角和低进给速度进行加工。
这样有助于减轻刀具应力,减少石墨的碎裂。
另一个有效避免石墨崩块的方法是先在铣削末端出口处铣掉一部分,然后再从头铣削。
图10-1。
我们可以利用石墨加工出高精度的电极。
(资料由航空技术有限公司提供,康奈提格洲,克伦威尔)加工深度和刀具负载直接取决于设备功率、刚性及装夹方法。
刀具颤动或装夹不牢固会造成机床超载,损坏工件。
如果可以保持适当的刀具刚度,使用恰当的装夹方法,您的机床会在工件材料受损前停止工作。
以下图表(图10-2和图10-3)阐明了进给率、每分钟转数和铣刀直径之间的关系。
图10-2。
加工石墨中推荐加工速度。
图10-3。
石墨加工中推荐刀具负荷。
5.攻丝对石墨进行通孔攻丝应使用常规丝锥,无需切削液。
我们可以使用多种方法在石墨上攻出盲孔。
用底锥加工盲孔易使丝扣破碎,而使用标准丝锥就可减少这种情况。
或者您也可以使用标准丝锥先加工到尽量深,然后再用底锥完成攻丝。
6.钻孔选择、设计刀具时必须考虑钻孔的数目和尺寸。
小钻削量加工——可使用高速钢钻头进行为数不多的钻孔。
由于石墨对高速钢钻头顶端和刀刃处磨损很严重,所以应该检查钻头的使用状况。
而且由于刀具的磨损,随后加工的钻孔形状会发生改变,内壁无法保持垂直。
大钻削量加工——加工直径超过1.60mm的大孔时应该使用优质的硬质合金钻头,因为它耐磨损,可以减少维修和换刀次数。
尽管此类钻头使用寿命比高速钢钻头长,但当直径小于4.20mm时,硬质合金钻头很易碎。
所以加工小孔时还是应该使用高速钢钻头。
图10-4。
在石墨上进行钻孔加工时,工作台始终保持设定的距离。
主轴被包裹着,有助于收集石墨粉尘。
金刚石钻头(PCD)的使用寿命最长。
但加工直径小于6.3mm的孔时,钻头表面的金刚石会脱离基体。
这是由于杂质堵塞在钻孔中,摩擦生热引起的。
深孔加工——多数深孔(深度大于直径3倍)加工面临的问题是杂质难以清除。
杂质的积聚、高转速和低进给率都会增加摩擦,从而聚集热能损坏钻头。
为了防止刀具的损坏,可在钻头上开一个环形啄槽,快速引出大量粉尘。
高速麻花钻头由于其表面有许多凹槽,所以能够最大程度的避免这个问题。
在实际加工中,可以使用有中心冷却孔的钻头,通过注入压缩空气将钻孔底部的杂质带出。
直径小于0.80mm的钻头,进给速度应为0.038~0.050mm/转,直径为0.80~3.175mm 的钻头,进给速度应为0.025~0.076mm/转,更粗的钻头进给速度为0.050~0.127mm/转。
转速由钻头直径和材料决定。
空心钻——空心钻孔时应使用金刚石涂层的刀具,如Diachrome和诺顿等品牌。
利用压强为40-80psi的压缩空气清除空心钻内部的杂质,外部的尘屑由真空吸尘罩收集。
采用手动进给时,应将初始值设在125转/分钟,然后慢慢增加,直到刀具能够稳定加工为止。
然后应该提高加工速度,根据中心孔的大小,达到500-600转/分钟。
枪孔钻——要在石墨上加工出光滑、高精度的孔,可以使用枪孔钻。
与金属不同,石墨加工时不会大片脱落,以致堵塞枪孔或凹槽。
石墨掉落的微粒直径一般在0.025~0.25mm之间,在压缩空气的作用下很容易清除。
使用压缩空气时,钻孔工作部位应放置集尘装置。
7.拉削标准的拉床是为加工金属设计的。
对石墨而言,拉刀齿负重过大,而在拉床退出石墨的时候,过大的压力会造成石墨从根部断裂。
所以,尽可能使用单齿键槽铣刀代替拉刀加工石墨。
在必须使用拉床加工的情况下,在加工面上应留有足够的余量,以便拉削结束后再加工拉削留下的边缘,通常余量为2.50~3.80mm足矣。
键槽铣削——加工石墨使用单齿键槽铣刀能够获得理想的效果。
为提高加工质量,应选用较低的进给(0.025~0.10mm/行程),并使用锋利的硬质合金刀具。
高速钢刀具可用于短行程的加工,但也很快会变钝,变钝的刀具会造成石墨的碎裂。
并且在刀具退出石墨时造成崩块。
即使进给很小,刀具退出石墨时仍然会产生轻微的崩块。
如果使用高进给率或较钝的刀具,会造成石墨严重的崩块。
8.磨削平面磨削——标准的平面磨床可以加工石墨,但必须保持磨轮的锋利。
最常用的磨轮是绿砂轮,主要组成部分为60碳化硅颗粒。
常用的有诺顿、Carborundum、Cincinnati,或相同品质的砂轮。
使用时将转速设为5300-6000表面英尺/分钟,不要超过生产厂家标签上规定的转速。
总之,重复性高的工作应该使用金刚石磨轮,因为它可以保持原先的尖角和加工精度。
尽管同碳化硅刀具相比,它价格昂贵,加工速度慢,但是它无需经常修补。
粗磨时每行程进给0.127~0.254mm,精磨时每行程进给0.025~0.076mm,横向进刀均为每分钟1422mm。
应避免进刀量过大而使粉尘来不及清除。
清除石墨粉尘最好的方法是将强力真空吸尘罩置于磨轮的前面,并在磨轮的后面吹进压缩空气。
平面磨削的光洁度一般在0.45~0.8μmR a之间。
要得到更好的表面光洁度可以通过改善无火花磨削、使用细砂磨轮等常规方法实现。
通常我们很难加工出小于0.2μmR a 的表面光洁度。
此时唯有研磨可以达到要求。
薄片磨削——加工厚度小于0.25mm的薄片,应先用带锯切下厚度约1mm石墨片,然后进行磨削。
通常我们使用真空吸盘固定薄片。
加工时,首先磨削薄片的一面,去除粗糙面。
然后将薄片翻转,进行精加工。
不断的磨削,直到薄片符合加工的要求。
记住,使用的石墨结构越紧密,强度越高,加工出的成品越薄。
因此,粒径为1μm、挠曲强度为17,000psi的特微石墨远比粒径为20μm、挠曲强度为6,500psi的精细石墨加工效果好。
无心磨削——尽管通常石墨的加工都是在干燥的环境下进行,以免遭到污染,但有时却无法做到这一点。
如果没有冷却液及时带走热量,无心磨削时产生的热能足以损坏磨轮。
图10-5。
吸尘装置应嵌入磨轮的防护罩内。
这里使用真空吸盘固定住工件。
使用热固树脂粘接的碳化硅磨轮进行加工时,横向进刀量设定为每分钟4950mm,可以达到1.6μm R a甚至更好的表面光洁度。
由于高强度的石墨可以承受更大的压力,所以一个边长为8mm的方料可以一次磨到直径为0.6mm的圆棒。
更大的尺寸须在磨削前先加工成八棱形棒料。
无心磨削的精度很高,POCO石墨棒的标准公差可达到0.005mm。
轧辊磨削加工效果一样出色,适用于大批量加工形状复杂的小圆零件。
9.装夹POCO高强度石墨由于挠曲强度高,所以比其他石墨装夹后更牢固。
但装夹过紧也会造成石墨像钢或铝一样发生弯曲。
在柔和的压力下,石墨棒也可以像金属一样产生永久性弯曲变形,尽管其变形不会有金属那么大。
我们可以使用多种装夹方法固定石墨。
最简单的莫过于标准压板,偶尔还使用螺栓和定位梢。
如今还有众多组合装夹系统,可以简化加快工件的装夹工序。
图10-6。
典型刀具系统。
(图片由3R美国系统有限公司提供;新泽西洲,费尔菲尔德)为了取得更好的加工精度,您应该在加工电极和电火花加工时使用同一套装夹系统,这样可以最大限度地减少误差。
如果电极较薄或比较脆弱,您应该在夹具中刻出特定的凹穴,以此固定电极。
真空装夹——如果进行五面加工,那么就得使用真空装夹固定电极。
使用真空装夹能够减少一种或几种工装。
POCO公司经常使用真空吸盘固定工件,进行表面磨削。
动力装夹——气动或液压动力装夹非常适用于大型电极的加工,因为这样可以减少固定各个部分所需的时间。
用液压动力装夹时,必须控制压力,以免压碎石墨。
使用气动系统装夹时,应使用气阀控制活塞,不要猛烈撞击夹具和工件。