大变位齿轮变位系数的可视化
齿轮变位系数计算公式
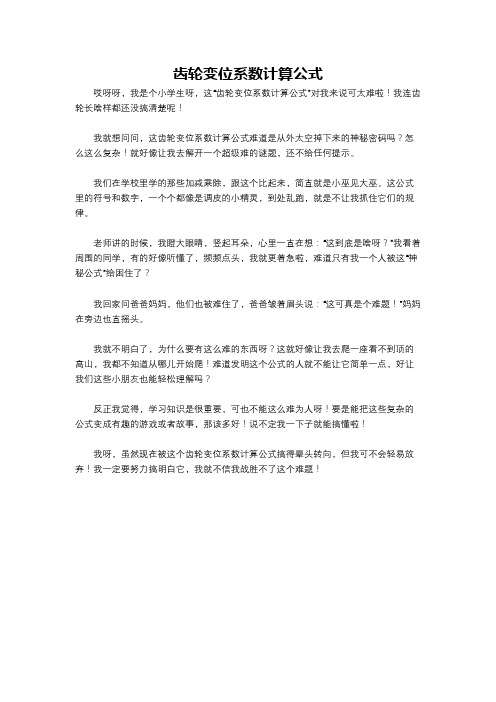
齿轮变位系数计算公式
哎呀呀,我是个小学生呀,这“齿轮变位系数计算公式”对我来说可太难啦!我连齿轮长啥样都还没搞清楚呢!
我就想问问,这齿轮变位系数计算公式难道是从外太空掉下来的神秘密码吗?怎么这么复杂!就好像让我去解开一个超级难的谜题,还不给任何提示。
我们在学校里学的那些加减乘除,跟这个比起来,简直就是小巫见大巫。
这公式里的符号和数字,一个个都像是调皮的小精灵,到处乱跑,就是不让我抓住它们的规律。
老师讲的时候,我瞪大眼睛,竖起耳朵,心里一直在想:“这到底是啥呀?”我看着周围的同学,有的好像听懂了,频频点头,我就更着急啦,难道只有我一个人被这“神秘公式”给困住了?
我回家问爸爸妈妈,他们也被难住了,爸爸皱着眉头说:“这可真是个难题!”妈妈在旁边也直摇头。
我就不明白了,为什么要有这么难的东西呀?这就好像让我去爬一座看不到顶的高山,我都不知道从哪儿开始爬!难道发明这个公式的人就不能让它简单一点,好让我们这些小朋友也能轻松理解吗?
反正我觉得,学习知识是很重要,可也不能这么难为人呀!要是能把这些复杂的公式变成有趣的游戏或者故事,那该多好!说不定我一下子就能搞懂啦!
我呀,虽然现在被这个齿轮变位系数计算公式搞得晕头转向,但我可不会轻易放弃!我一定要努力搞明白它,我就不信我战胜不了这个难题!。
基于AutoLISP的齿轮变位系数的选择
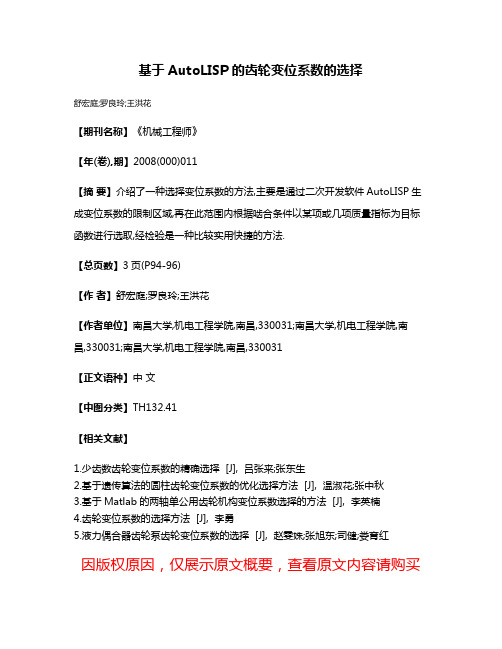
基于AutoLISP的齿轮变位系数的选择
舒宏庭;罗良玲;王洪花
【期刊名称】《机械工程师》
【年(卷),期】2008(000)011
【摘要】介绍了一种选择变位系数的方法,主要是通过二次开发软件AutoLISP生成变位系数的限制区域,再在此范围内根据啮合条件以某项或几项质量指标为目标函数进行选取,经检验是一种比较实用快捷的方法.
【总页数】3页(P94-96)
【作者】舒宏庭;罗良玲;王洪花
【作者单位】南昌大学,机电工程学院,南昌,330031;南昌大学,机电工程学院,南昌,330031;南昌大学,机电工程学院,南昌,330031
【正文语种】中文
【中图分类】TH132.41
【相关文献】
1.少齿数齿轮变位系数的精确选择 [J], 吕张来;张东生
2.基于遗传算法的圆柱齿轮变位系数的优化选择方法 [J], 温淑花;张中秋
3.基于Matlab的两轴单公用齿轮机构变位系数选择的方法 [J], 李英楠
4.齿轮变位系数的选择方法 [J], 李勇
5.液力偶合器齿轮泵齿轮变位系数的选择 [J], 赵雯姝;张旭东;司健;娄育红
因版权原因,仅展示原文概要,查看原文内容请购买。
齿轮变位系数 -回复
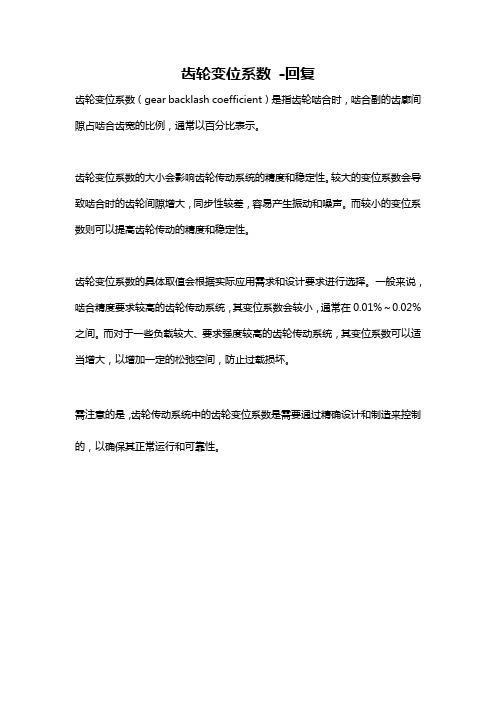
齿轮变位系数-回复
齿轮变位系数(gear backlash coefficient)是指齿轮啮合时,啮合副的齿廓间隙占啮合齿宽的比例,通常以百分比表示。
齿轮变位系数的大小会影响齿轮传动系统的精度和稳定性。
较大的变位系数会导致啮合时的齿轮间隙增大,同步性较差,容易产生振动和噪声。
而较小的变位系数则可以提高齿轮传动的精度和稳定性。
齿轮变位系数的具体取值会根据实际应用需求和设计要求进行选择。
一般来说,啮合精度要求较高的齿轮传动系统,其变位系数会较小,通常在0.01%~0.02%之间。
而对于一些负载较大、要求强度较高的齿轮传动系统,其变位系数可以适当增大,以增加一定的松弛空间,防止过载损坏。
需注意的是,齿轮传动系统中的齿轮变位系数是需要通过精确设计和制造来控制的,以确保其正常运行和可靠性。
渐开线齿轮变位系数选择的新方法
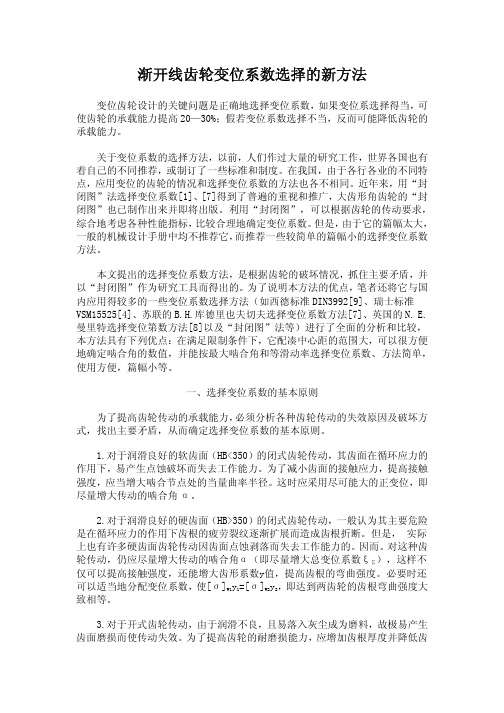
曲线),在该曲线上选取位变系数时,齿轮的最大滑动率是相等的。
从公式(10)还可以看出,η'=η"曲线的基本斜率主要取决于齿数比u的大 小,当然,曲线的具体形状还与齿数Z2、Z1有关。
图 8 为Z1=17,而Z2不同(即u不同)时的η'=η"曲线。可以看出,各曲线的
图2
在图 3 中,曲线组Ⅱ中的每一条曲线即为Z1一定时(如Z1=12,13,……等), 对于不同的Z2所得到的ξ∑B──Z∑变化曲线。而曲线组Ⅰ为ε=1 的曲线与 η'=η"曲线的交点所得的总变位系数ξ∑──Z∑曲线。
图3
从图 3 中可以看出,当小齿轮数Z1一定时,ξ∑B随Z∑的增加而增加,而当Z∑ 一定时,随小齿轮齿数Z1的增大,ξ∑B也不断增大。
渐开线齿轮变位系数选择的新方法
变位齿轮设计的关键问题是正确地选择变位系数,如果变位系选择得当,可 使齿轮的承载能力提高 20—30%;假若变位系数选择不当,反而可能降低齿轮的 承载能力。
关于变位系数的选择方法,以前,人们作过大量的研究工作,世界各国也有 着自己的不同推荐,或制订了一些标准和制度。在我国,由于各行各业的不同特 点,应用变位的齿轮的情况和选择变位系数的方法也各不相同。近年来,用“封 闭图”法选择变位系数[1]、[7]得到了普遍的重视和推广,大齿形角齿轮的“封 闭图”也已制作出来并即将出版。利用“封闭图”,可以根据齿轮的传动要求, 综合地考虑各种性能指标,比较合理地确定变位系数。但是,由于它的篇幅太大, 一般的机械设计手册中均不推荐它,而推荐一些较简单的篇幅小的选择变位系数 方法。
齿轮变位系数

齿轮变位系数
齿轮变位系数是指外部齿轮和轴之间的变位比,也称为齿轮比。
它代表着两个齿轮之间的转动方向和转速之差。
变位系数是决定输入输出轴的转子比。
变位系数表示内外轴的速度,由此可以判断出轴的机械效率,同时也可以确定发动机的转速比。
在设计时,变位系数是非常重要的一个参数,它可以提高机械设计的灵活性和方便性。
齿轮变位系数的计算非常重要,它是确定某个轴的转速比的核心要素。
通常可以通过试验确定变位系数。
通过观察不同转速下的变位系数,我们可以预测出车轮比率。
另外,还可以利用有限元分析法求解更高精度的变位系数。
在实际应用中,变位系数具有很重要的作用,它可以提高发动机的效率,减少能源损失,同时还能够改善整个机械系统的可靠性。
一般来说,齿轮变位系数越大,则驱动效率越高,能量损失也越小。
但是,如果变位系数过大,也可能导致整体性能下降,所以在实际应用中,要根据实际情况选择合适的变位系数。
齿轮变位系数是一个复杂的概念,它不仅关系到机械效率,也关系到整体性能。
因此,在选取变位系数时,要仔细考虑多方面的影响因素,以便可以获得最佳的齿轮系数,从而获得高效的机械性能。
另外,在齿轮变位系数设计中,还需要考虑其它因素,如轴承承受的负载情况、齿轮的摩擦情况以及齿轮的强度情况等。
齿轮变位系数的设计要求考虑这些因素,以便可以有效地减少能源损失,达到最佳的发动机性能。
总之,齿轮变位系数是设计发动机转速比的重要参数,它可以改善发动机效率,减少能源损失,而且还能提高整体机械性能。
正确的变位系数的设计可以有效地提高机械系统的性能,以及发动机的效率。
齿轮变位系数计算公式
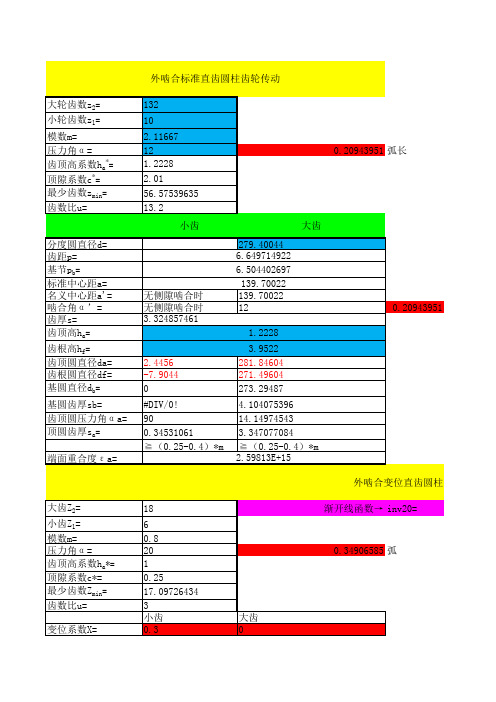
齿顶高ha=
0.664884418
齿根高hf=
0.76
齿顶圆直径da=
6.129768836
齿根圆直径df=
3.28
基圆直径db=
4.51052458
齿距p=
基圆齿距pb=
齿厚s=
1.431342774
基圆齿厚sb=
1.412247101
齿顶圆压力角αa= 42.62181966
顶圆齿厚sa=
端面重合度εa=
#NUM!
校验干涉
应满足
渐开线干涉
1
≧
小齿轮过渡曲线干涉
≧
由表2-11查 #NUM!
外啮合标准斜齿(人字齿)圆柱齿轮传动
大轮齿数z2=
9
小轮齿数z1=
9
法向模数mn=
1.5
法向压力角αn=
30
螺旋角β=
25
端面模数mt=
1.655066878
端面压力角αt=
32.49858487
法向齿顶高系数han*= 1 法向顶隙系数cn*= 0.25
1.743355127
1.622393438
27.87834641
0.295868875
直齿外齿轮
公法线长度
公法线长度的计算 Wk=
标准齿轮 9.70116265
直齿外齿轮 斜齿外齿轮
跨测齿数 公法线长度 跨测齿厚
k= Wkn= k=
5.055555556
直齿外齿轮
公法线长度 跨测齿数
齿顶高hae1= 齿根高hfe1= 全齿高he1= 齿顶圆直径dae1= 分度圆直径de1= 齿根角Øf1= 齿顶角Øa1= 顶锥角δa1= 根锥角δf1= Ak1=
(完整版)变位齿轮的计算方法
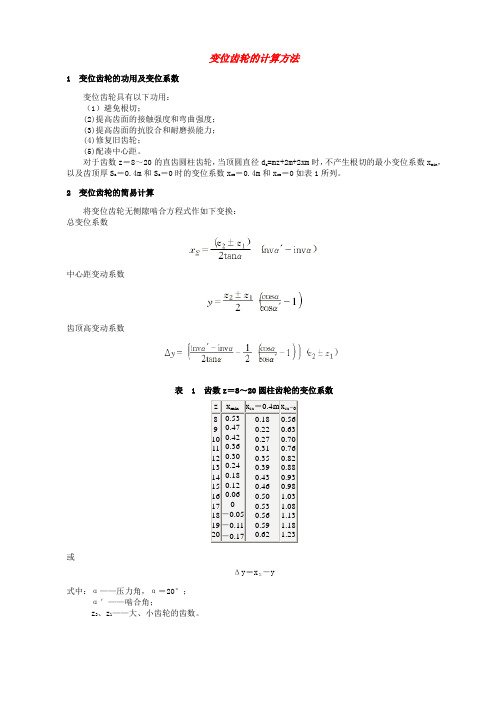
Wk=Wk*m+0.684xm
式中:Wk*——某齿数齿轮跨测k齿时,模数m=1的公法线长度。
表 2 变位齿轮的yz、xz、Δyz和啮合角α′(α=2ห้องสมุดไป่ตู้°)
α′
(分)
19°
20°
21°
yz
xz
Δyz
yz
xz
Δyz
yz
xz
Δyz
0
1
2
3
4
5
6
7
8
9
-0.00616
606
596
0.00107
118
129
139
150
161
172
183
194
205
0.00001
001
001
001
001
001
001
001
002
002
0.00768
779
790
802
813
825
836
847
859
870
0.00789
801
814
825
837
850
862
874
886
898
0.00022
023
023
024
236
246
257
268
279
290
301
312
0.00216
227
238
249
260
271
282
293
304
315
0.00002
002
002
003
003
直齿圆柱齿轮变位系数、公法线长度、齿厚、最小法向侧隙的计算

外啮合直齿圆柱齿轮变位系数、公法线长度、齿厚、最小法向侧隙的计算1,直齿圆柱齿轮变位系数计算:Case1:a,此处例子仅计算用齿条型刀具加工时的情况(插齿刀加工见相关手册公式):小结:由此可知本例选取的齿数在不变位的情况也不会产生根切现象。
b,根据下图选择大小齿轮的变位系数和x∑。
本例在P6-P7区间取值。
即齿根及齿面承载能力较高区,进行选择。
因大小齿轮的齿数和为18+19=37。
所以本例选择的变位系数和x∑=0.8。
本例我们的两个齿轮在工作时属于减速运动,所以按减速运动的变位系数分配线图,进行2个齿轮的变位系数的选择。
先按(z1+z1)/2=18.5,作为横坐标,做一条垂线(图中蓝色的线),再按x∑/2=0.4,作为纵坐标,做一条水平线(图中橙色的线),接着沿着L线的趋势,穿过上面2条线的交点做一条射线(图中红色的线)最后按大小齿轮的齿数做相应的垂线(图中紫色的线),即得到需要的各自变位系数。
最后我们选择的变位系数即为:小齿轮x1=0.42,大齿轮x2=0.38。
【基本保障其和与之前x ∑一致,即可】。
c,验算变位后的齿顶厚度:注:一般要求齿顶厚Sa≥0.25m;对于表面淬火的齿轮要求Sa≥0.4m下表中的da的计算见后面的计算表格中的计算公式(因为当齿轮变位后,齿顶圆的计算和未变位齿轮的计算稍有差别-涉及到变位系数和中心距变位系数。
)。
分度圆直径db mm 73.8 77.9齿轮的齿顶圆直径da mm 83.027 86.799齿轮的齿顶压力角αa °27.27 26.17中间值invα0.0215 0.0215中间值invαa 0.0587 0.0347齿顶厚Sα 5.77 7.47判断值0.25m 1.025 1.025判断值0.4m 1.64 1.64小结:计算发现变位后的齿轮齿顶厚满足设计需求。
根据上面确定的变位系数,计算齿轮的中心距变位系数和节圆直径、齿根圆直径、齿顶圆直径。
超大模数变位齿轮-齿条传动瞬态热弹流润滑
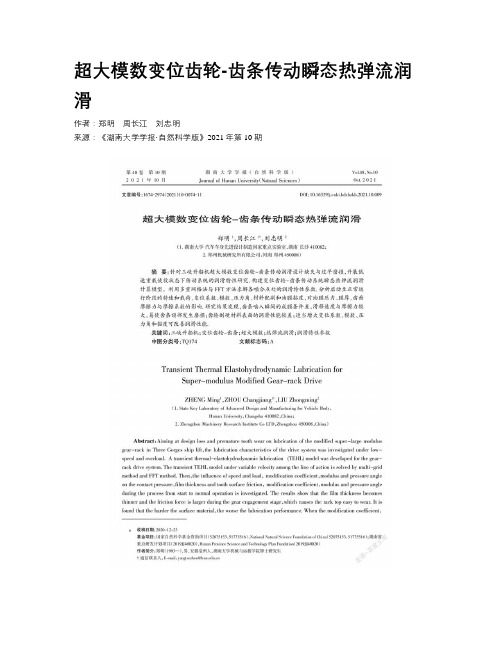
超大模数变位齿轮-齿条传动瞬态热弹流润滑作者:郑明周长江刘忠明来源:《湖南大学学报·自然科学版》2021年第10期摘要:针对三峡升船机超大模数变位齿轮-齿条传动润滑设计缺失与过早磨损,开展低速重载使役状态下传动系统的润滑特性研究. 构建变位齿轮-齿条传动系统瞬态热弹流润滑计算模型,利用多重网格法与FFT方法求解各啮合点处的润滑特性参数. 分析启动至正常运行阶段的转速和载荷、变位系数、模数、压力角、材料配副和油膜黏度,对油膜压力、膜厚、齿面摩擦力与摩擦系数的影响. 研究结果发现,齿条啮入瞬间的成膜条件差,滑移速度与摩擦力较大,易使齿条顶部发生磨损;齿轮副硬材料表面的润滑性能较差;适当增大变位系数、模数、压力角和黏度可改善润滑性能.关键词:三峡升船机;变位齿轮-齿条;超大模数;热弹流润滑;润滑特性参数中图分类号:TQ174 文献标志码:ATransient Thermal Elastohydrodynamic Lubrication forSuper-modulus Modified Gear-rack DriveZHENG Ming ZHOU Changjiang LIU Zhongming(1. State Key Laboratory of Advanced Design and Manufacturing for Vehicle Body,Hunan University,Changsha 410082,China;2. Zhengzhou Machinery Research Institute Co LTD,Zhengzhou 450008,China)Abstract:Aiming at design loss and premature tooth wear on lubrication of the modified super-large modulus gear-rack in Three Gorges ship lift,the lubrication characteristics of the drive system was investigated under low-speed and overload. A transient thermal-elastohydrodynamic lubrication (TEHL) model was developed for the gear-rack drive system. The transient TEHL model under variable velocity among the line of action is solved by multi-grid method and FFT method. Then,the influence of speed and load, modification coefficient,modulus and pressure angle on the contact pressure,film thickness and tooth surface friction, modification coefficient,modulus and pressure angle during the process from start to normal operation is investigated. The results show that the film thickness becomes thinner and the friction force is larger during the gear engagement stage,which causes the rack top easy to wear. It is found that the harder the surface material,the worse the lubrication performance. When the modification coefficient,modulus,pressure angle and viscosity are increased,the lubricating property can be improved.Key words:Three Gorges ship lift;modified gear-rack;super-large modulus;thermal-elastohydrodynamic lubrication;lubricating property parameters三峽升船机作为规模最大和技术难度最高的升船机[1],由4组超大模数的开式齿轮-齿条机构驱动. 齿条设计寿命为35年,总载荷循环周次可达4.22 × 105次,抬升重量达3000 t级,加工精度高,更换困难,是升船机的关键部件. 升船机机组低速重载传动易引起齿轮-齿条啮合润滑不良,致使齿面出现磨损与胶合. 德国Wollhofen调研报告显示,开式齿轮传动损坏18.2%因润滑不良发生严重磨损或胶合而失效[2]. 因此,有必要对升船机齿轮-齿条传动的润滑状态进行研究,并通过参数分析优化润滑性能.根据Stribeck曲线齿轮润滑状态可分为全膜润滑、混合润滑、边界润滑三种[3]. 基于Reynolds方程和线接触动压润滑理论,Martin[4]对直齿轮齿面的润滑状态进行研究,引入刚体与等黏度假设得出重载下的膜厚过薄. Grubin[5]引入表面弹性变形与变黏度流体,结合Hertz接触模型提出弹流润滑理论(EHL),得到较为准确的线接触平均膜厚经验公式. 润滑方程的复杂性与非线性使得求解难度极大,Dowson等[6]基于逆解法求出线接触润滑模型的完全数值解. 随着摩擦学理论与试验方法的快速发展,数值求解的效率与稳定性已不能满足应用,直接迭代法将表面弹性变形方程、膜厚方程、黏度与密度方程和Reynolds方程联立求解,进行循环迭代,最终收敛到数值解. 对于高速重载等严苛工况,其求解稳定性与效率不佳,Lubrecht[7]将多重网格法引入润滑方程的求解,极大地提高了求解效率与收敛稳定性.上述求解基于等温与牛顿流体假设,与润滑油的实际承载情况差别较大. 杨沛然等[8]导出润滑力学中关于非牛顿流体介质的普遍Reynolds方程,通过定义广义牛顿黏度,适用于多种流变模型. 现代弹流润滑模型求解中,考虑非牛顿、热效应与时变性的影响,对于求解真实表面下混合润滑参数的难度愈来愈大. Hu等[9]提出统一Reynolds方程求解混合润滑模型,Liu等[10]和王文中等[11]分别采用DC-FFT方法求解润滑表面的弹性变形,极大地提高了膜厚方程求解效率. 王优强等[12]考虑瞬态效应与热效应,分析直齿轮线接触下的瞬态热弹流润滑性能,讨论轮齿间油膜的厚度、压力与温度场的变化规律. 王文中等[13]对渐开线斜齿轮非稳态弹流润滑进行分析,发现等主动轮齿根附近和节点位置润滑状态较差. 徐彩红[14]采用等温下的时变弹流润滑模型研究载荷突变对齿轮-齿条传动中的润滑性能影响,发现啮入点为危险点;袁玉鹏等[15]利用油膜厚度准则研究低速重载、频繁换向下的开式齿轮-齿条润滑状态.综上所述,弹流润滑机理的研究日益成熟,但超大模数变位齿轮-齿条啮合传动中的润滑状态及其失效预测仍有待完善. 作为超大模数齿轮-齿条传动机构,其模数62.667 mm,齿宽810 mm,单节长4705 mm,采用分节式設计安装,材料为18CrNiMo7-6,齿面加工处理为5级精度,齿轮-齿条采用正变位传动(x = 0.5). 针对三峡升船机齿条性能评定试验装置启动至正常运行阶段的转速和载荷等10种工况参数,分别讨论变位系数、模数与压力角等几何参数,材料配副、油膜黏度等材料参数对油膜厚度、接触圧力及摩擦系数的影响,基于膜厚比与Stribeck曲线判定油膜润滑状态.1 变位齿轮-齿条润滑模型正变位齿轮可提高齿根抗弯强度,增大齿面接触强度和提高齿面耐磨损能力. 研究变位齿轮的润滑性能,以便合理设计润滑方式及优选润滑参数及性能评估. 对于变位齿轮,正变位时,齿廓变厚,齿顶圆、分度圆与齿根圆直径变大;负变位时,齿廓变薄,齿顶圆、分度圆与齿根圆直径变小,如图1(a)所示. 齿条齿形保持不变,对应于不同变位齿轮相啮合的齿条,其齿廓的厚薄不同. 升船机齿轮-齿条传动机构相比齿轮传动,其变位工况下的啮合角大小恒为压力角α,其啮合原理见图1(b). 实际啮合线长B1B2位于理论啮合线上,且啮合点沿oz轴方向移动;由齿轮的齿根与齿条的齿顶先啮入(B1点),直至齿轮的齿顶与齿条齿根处啮出(B2点).2 热弹流润滑控制方程2.1 通用Reynolds方程2.2 油膜厚度方程2.3 润滑油黏度方程2.4 润滑油密度方程2.5 载荷平衡方程2.6 温度场方程3 计算流程与参数3.1 润滑参数计算流程3.2 材料与工况参数4 结果分析与讨论4.1 载荷与转速影响当第10时刻转速达到额定转速时,即工况为表1中的组11,其油膜压力沿啮合线的变化和各特征点中心膜厚的分布见图7. 其中A为啮入点,B为节点,C为HPSTC点,D为LPSTC 点,E为啮出点. 油膜压力变化趋势可由齿面载荷谱和Hertz接触半宽b简单分析. 由于齿条的曲率半径恒定,齿轮-齿条啮合过程中综合曲率半径R较齿轮-齿条啮合时增加更快,使得相同载荷谱下的接触半宽b较大,进而影响油膜承载区域内润滑参数的变化,b和R的变化趋势见图8. 由此可见,啮合过程中膜厚分布均出现颈缩现象,且膜厚由啮入至啮出逐渐增加,与直齿轮瞬态热弹流润滑[12]不同点是A到B过程中油膜压力逐渐降低,且C到D至E的过程中油膜压力降低的趋势更明显,这与接触半宽b的变化相一致.4.2 几何参数影响变位系数会改变齿轮-齿条传动中重合度大小,轮齿正变位会缩短啮合线长度,进而改变载荷沿啮合线的分布,对啮合传动的润滑性能产生影响. 图9(a)和(b)所示,随着变位系数增加,齿条顶部会较晚进入啮合,各特征点的油膜压力均有所降低,对应的中心膜厚逐渐增大,进而提高轮齿承载能力. 随着变位系数增加,齿面摩擦力的变化趋于缓和,啮入阶段摩擦力显著降低,这将有效减弱切向啮入冲击,节点至变位后的单齿啮合区摩擦力反向增大,啮出阶段的摩擦力则变化不大. 从图9(c)和(d)发现,增大变位系数可相对降低啮入时刻和单双齿交替啮合时刻的切向冲击.降低,且单双齿交替啮合处的压力突变减小,中心膜厚显著增加,齿面摩擦力与摩擦系数变化趋于缓和,可有效减弱轮齿啮合过程中的法向与切向冲击. 故增大模数可有效提高轮齿的承载能力,并改善润滑相关参数的分布.对于部分重载齿轮传动,标准压力角20°的轮齿已经满足不了行业需求,而压力角变化会对齿轮润滑性能与承载能力产生影响. 压力角增大会减小轮齿啮合过程的重合度,但增大压力角会同时增大等效曲率半径R与卷吸速度,这有利于油膜压力的降低与膜厚的增加,与图11(a)中心膜厚变化趋势一致. 轮齿压力角增大,使得半径R增加,进而增大接触半宽,这使得在单齿与双齿啮合区域的油膜压力显著降低(见图11). 同时因膜厚增加使得剪应变率相应减小,从而降低摩擦力,有效改善齿轮-齿条啮合冲击.上述求解基于等温与牛顿流体假设,与润滑油的实际承载情况差别较大. 杨沛然等[8]导出润滑力学中关于非牛顿流体介质的普遍Reynolds方程,通过定义广义牛顿黏度,适用于多种流变模型. 现代弹流润滑模型求解中,考虑非牛顿、热效应与时变性的影响,对于求解真实表面下混合润滑参数的难度愈来愈大. Hu等[9]提出统一Reynolds方程求解混合润滑模型,Liu等[10]和王文中等[11]分别采用DC-FFT方法求解润滑表面的弹性变形,极大地提高了膜厚方程求解效率. 王优强等[12]考虑瞬态效应与热效应,分析直齿轮线接触下的瞬态热弹流润滑性能,讨论轮齿间油膜的厚度、压力与温度场的变化规律. 王文中等[13]对渐开线斜齿轮非稳态弹流润滑进行分析,发现等主动轮齿根附近和节点位置润滑状态较差. 徐彩红[14]采用等温下的时变弹流润滑模型研究载荷突变对齿轮-齿条传动中的润滑性能影响,发现啮入点为危险点;袁玉鹏等[15]利用油膜厚度准则研究低速重载、频繁换向下的开式齿轮-齿条润滑状态.综上所述,弹流润滑机理的研究日益成熟,但超大模数变位齿轮-齿条啮合传动中的润滑状态及其失效预测仍有待完善. 作为超大模数齿轮-齿条传动机构,其模数62.667 mm,齿宽810 mm,单节长4705 mm,采用分节式设计安装,材料为18CrNiMo7-6,齿面加工处理为5级精度,齿轮-齿条采用正变位传动(x = 0.5). 针对三峡升船机齿条性能评定试验装置启动至正常运行阶段的转速和载荷等10种工况参数,分别讨论变位系数、模数与压力角等几何参数,材料配副、油膜黏度等材料参数对油膜厚度、接触圧力及摩擦系数的影响,基于膜厚比与Stribeck曲线判定油膜润滑状态.1 变位齿轮-齿条润滑模型正变位齿轮可提高齿根抗弯强度,增大齿面接触强度和提高齿面耐磨损能力. 研究变位齿轮的润滑性能,以便合理设计润滑方式及优选润滑参数及性能评估. 对于变位齿轮,正变位时,齿廓变厚,齿顶圆、分度圆与齿根圆直径变大;负变位时,齿廓变薄,齿顶圆、分度圆与齿根圆直径变小,如圖1(a)所示. 齿条齿形保持不变,对应于不同变位齿轮相啮合的齿条,其齿廓的厚薄不同. 升船机齿轮-齿条传动机构相比齿轮传动,其变位工况下的啮合角大小恒为压力角α,其啮合原理见图1(b). 实际啮合线长B1B2位于理论啮合线上,且啮合点沿oz轴方向移动;由齿轮的齿根与齿条的齿顶先啮入(B1点),直至齿轮的齿顶与齿条齿根处啮出(B2点).2 热弹流润滑控制方程2.1 通用Reynolds方程2.2 油膜厚度方程2.3 润滑油黏度方程2.4 润滑油密度方程2.5 载荷平衡方程2.6 温度场方程3 计算流程与参数3.1 润滑参数计算流程3.2 材料与工况参数4 结果分析与讨论4.1 载荷与转速影响当第10时刻转速达到额定转速时,即工况为表1中的组11,其油膜压力沿啮合线的变化和各特征点中心膜厚的分布见图7. 其中A为啮入点,B为节点,C为HPSTC点,D为LPSTC 点,E为啮出点. 油膜压力变化趋势可由齿面载荷谱和Hertz接触半宽b简单分析. 由于齿条的曲率半径恒定,齿轮-齿条啮合过程中综合曲率半径R较齿轮-齿条啮合时增加更快,使得相同载荷谱下的接触半宽b较大,进而影响油膜承载区域内润滑参数的变化,b和R的变化趋势见图8. 由此可见,啮合过程中膜厚分布均出现颈缩现象,且膜厚由啮入至啮出逐渐增加,与直齿轮瞬态热弹流润滑[12]不同点是A到B过程中油膜压力逐渐降低,且C到D至E的过程中油膜压力降低的趋势更明显,这与接触半宽b的变化相一致.4.2 几何参数影响变位系数会改变齿轮-齿条传动中重合度大小,轮齿正变位会缩短啮合线长度,进而改变载荷沿啮合线的分布,对啮合传动的润滑性能产生影响. 图9(a)和(b)所示,随着变位系数增加,齿条顶部会较晚进入啮合,各特征点的油膜压力均有所降低,对应的中心膜厚逐渐增大,进而提高轮齿承载能力. 随着变位系数增加,齿面摩擦力的变化趋于缓和,啮入阶段摩擦力显著降低,这将有效减弱切向啮入冲击,节点至变位后的单齿啮合区摩擦力反向增大,啮出阶段的摩擦力则变化不大. 从图9(c)和(d)发现,增大变位系数可相对降低啮入时刻和单双齿交替啮合时刻的切向冲击.降低,且单双齿交替啮合处的压力突变减小,中心膜厚显著增加,齿面摩擦力与摩擦系数变化趋于缓和,可有效减弱轮齿啮合过程中的法向与切向冲击. 故增大模数可有效提高轮齿的承载能力,并改善润滑相关参数的分布.对于部分重载齿轮传动,标准压力角20°的轮齿已经满足不了行业需求,而压力角变化会对齿轮润滑性能与承载能力产生影响. 压力角增大会减小轮齿啮合过程的重合度,但增大压力角会同时增大等效曲率半径R与卷吸速度,这有利于油膜压力的降低与膜厚的增加,与图11(a)中心膜厚变化趋势一致. 轮齿压力角增大,使得半径R增加,进而增大接触半宽,这使得在单齿与双齿啮合区域的油膜压力显著降低(见图11). 同时因膜厚增加使得剪应变率相应减小,从而降低摩擦力,有效改善齿轮-齿条啮合冲击.上述求解基于等温与牛顿流体假设,与润滑油的实际承载情况差别较大. 杨沛然等[8]导出润滑力学中关于非牛顿流体介质的普遍Reynolds方程,通过定义广义牛顿黏度,适用于多种流变模型. 现代弹流润滑模型求解中,考虑非牛顿、热效应与时变性的影响,对于求解真实表面下混合润滑参数的难度愈来愈大. Hu等[9]提出统一Reynolds方程求解混合润滑模型,Liu等[10]和王文中等[11]分别采用DC-FFT方法求解润滑表面的弹性变形,极大地提高了膜厚方程求解效率. 王优强等[12]考虑瞬态效应与热效应,分析直齿轮线接触下的瞬态热弹流润滑性能,讨论轮齿间油膜的厚度、压力与温度场的变化规律. 王文中等[13]对渐开线斜齿轮非稳态弹流润滑进行分析,发现等主动轮齿根附近和节点位置润滑状态较差. 徐彩红[14]采用等温下的时变弹流润滑模型研究载荷突变对齿轮-齿条传动中的润滑性能影响,发现啮入点为危险点;袁玉鹏等[15]利用油膜厚度准则研究低速重载、频繁换向下的开式齿轮-齿条润滑状态.综上所述,弹流润滑机理的研究日益成熟,但超大模数变位齿轮-齿条啮合传动中的润滑状态及其失效预测仍有待完善. 作为超大模数齿轮-齿条传动机构,其模数62.667 mm,齿宽810 mm,单节长4705 mm,采用分节式设计安装,材料为18CrNiMo7-6,齿面加工处理为5级精度,齿轮-齿条采用正变位传动(x = 0.5). 针对三峡升船机齿条性能评定试验装置启动至正常运行阶段的转速和载荷等10种工况参数,分别讨论变位系数、模数与压力角等几何参数,材料配副、油膜黏度等材料参数对油膜厚度、接触圧力及摩擦系数的影响,基于膜厚比与Stribeck曲线判定油膜润滑状态.1 变位齿轮-齿条润滑模型正变位齿轮可提高齿根抗弯强度,增大齿面接触强度和提高齿面耐磨损能力. 研究变位齿轮的润滑性能,以便合理设计润滑方式及优选润滑参数及性能评估. 对于变位齿轮,正变位时,齿廓变厚,齿顶圆、分度圆与齿根圆直径变大;负变位时,齿廓变薄,齿顶圆、分度圆与齿根圆直径变小,如图1(a)所示. 齿条齿形保持不变,对应于不同变位齿轮相啮合的齿条,其齿廓的厚薄不同. 升船机齿轮-齿条传动机构相比齿轮传动,其变位工况下的啮合角大小恒为压力角α,其啮合原理见图1(b). 实际啮合线长B1B2位于理论啮合线上,且啮合点沿oz轴方向移动;由齿轮的齿根与齿条的齿顶先啮入(B1点),直至齿轮的齿顶与齿条齿根处啮出(B2点).2 热弹流润滑控制方程2.1 通用Reynolds方程2.2 油膜厚度方程2.3 润滑油黏度方程2.4 润滑油密度方程2.5 载荷平衡方程2.6 温度场方程3 计算流程与参数3.1 润滑参数计算流程3.2 材料与工况参数4 结果分析与讨论4.1 载荷与转速影响当第10时刻转速达到额定转速时,即工况为表1中的組11,其油膜压力沿啮合线的变化和各特征点中心膜厚的分布见图7. 其中A为啮入点,B为节点,C为HPSTC点,D为LPSTC 点,E为啮出点. 油膜压力变化趋势可由齿面载荷谱和Hertz接触半宽b简单分析. 由于齿条的曲率半径恒定,齿轮-齿条啮合过程中综合曲率半径R较齿轮-齿条啮合时增加更快,使得相同载荷谱下的接触半宽b较大,进而影响油膜承载区域内润滑参数的变化,b和R的变化趋势见图8. 由此可见,啮合过程中膜厚分布均出现颈缩现象,且膜厚由啮入至啮出逐渐增加,与直齿轮瞬态热弹流润滑[12]不同点是A到B过程中油膜压力逐渐降低,且C到D至E的过程中油膜压力降低的趋势更明显,这与接触半宽b的变化相一致.4.2 几何参数影响变位系数会改变齿轮-齿条传动中重合度大小,轮齿正变位会缩短啮合线长度,进而改变载荷沿啮合线的分布,对啮合传动的润滑性能产生影响. 图9(a)和(b)所示,随着变位系数增加,齿条顶部会较晚进入啮合,各特征点的油膜压力均有所降低,对应的中心膜厚逐渐增大,进而提高轮齿承载能力. 随着变位系数增加,齿面摩擦力的变化趋于缓和,啮入阶段摩擦力显著降低,这将有效减弱切向啮入冲击,节点至变位后的单齿啮合区摩擦力反向增大,啮出阶段的摩擦力则变化不大. 从图9(c)和(d)发现,增大变位系数可相对降低啮入时刻和单双齿交替啮合时刻的切向冲击.降低,且单双齿交替啮合处的压力突变减小,中心膜厚显著增加,齿面摩擦力与摩擦系数变化趋于缓和,可有效减弱轮齿啮合过程中的法向与切向冲击. 故增大模数可有效提高轮齿的承载能力,并改善润滑相关参数的分布.对于部分重载齿轮传动,标准压力角20°的轮齿已经满足不了行业需求,而压力角变化会对齿轮润滑性能与承载能力产生影响. 压力角增大会减小轮齿啮合过程的重合度,但增大压力角会同时增大等效曲率半径R与卷吸速度,这有利于油膜压力的降低与膜厚的增加,与图11(a)中心膜厚变化趋势一致. 轮齿压力角增大,使得半径R增加,进而增大接触半宽,这使得在单齿与双齿啮合区域的油膜压力显著降低(见图11). 同时因膜厚增加使得剪应变率相应减小,从而降低摩擦力,有效改善齿轮-齿条啮合冲击.。
变位齿轮详解(精品)

a a ym
a″
ym (x1 x2 )m ym
(X1+ X2)m a′ ym
y x1 x2 y
O2
O2
△y为齿顶降低系数 ,
其值恒大于零。
h (2ha* c* y)m
ha (ha* X y)m
hf (ha* c* x)m 变位齿轮齿高比标准齿轮少 ym
2 无侧隙啮合方程
O1
xmtgα
a
b
rb
xm
s’ 分度圆 基圆
刀具节线 刀具分度线
ab c
P 设计:潘存云
S=πm/2
N1 α B2
xm
α
c
h* a
m
xm xm
xmtg
xm
h* a
m
xm
N
p
xm
正变位齿轮 x>0
标准齿轮 x=0
负变位齿轮 x<0
ha hf
z 17 正变位提高强度
凑中心距
• 变位后
s m 2xmtg
2
e m 2xmtg
2
1。变位齿轮的加工方法,模 数,压力角,分度圆,基圆都 与标准齿轮一样。
2。几何尺寸有所变化。
3。中心距一般不是两分度圆 半径之和,除非它们分别等值 正,负变化。
a=m(z1+z2)/2
a, a=m(z1+z2)/2
齿条与齿的切点变化, 齿间出现侧隙
x1 m
c* m c* m
好的传动形式
4)两轮齿数不受 Z1 Z2 2Zmin 的限制。
5)正传动的重叠系数有所下降。
O
r1 r1
O
1rb1
B2 N1
r1
齿轮变位系数

齿轮变位系数、侧隙选择
z1=10z2=60m=0.35
安装中心距12.3
材料为pa66
那么变位系数选择
侧隙的控制方法
侧隙根据经验选取
如果中心距为12.3
那么需要0.145的总变位系数
建议你小齿轮采用0.2变位
大齿轮采用-0.055变位
此时小齿轮齿顶稍有变尖
但可以满足0.1齿顶园角(线切割单变偏置)
1>按照常规,总变位0.145027。
按DIN 3992合理分配小齿x1≈0.28 x2 = 0.145027-x1= -0.134473 .
选择较大侧隙,例如GB2363-90 的 d , 也可以按照材料特性自己定义。
2>不需要拉大中心距。
3>小齿轮虽然存在一些根切,对啮合没有太大影响。
进啮点处0.0059 没有渐开线。
齿厚按照-0.03 考虑,用0.15 线丝切割模具型腔,还可以走丝不干涉。
4>PA66 按照 1.35% 考虑收缩,也可以按实际修改。
【本文来源】皇家小铺(/)【原文地址】/post/20090412434.html。
变位齿轮的计算方法

变位齿轮的计算方法1 变位齿轮的功用及变位系数变位齿轮具有以下功用:(1)避免根切;(2)提高齿面的接触强度和弯曲强度;(3)提高齿面的抗胶合和耐磨损能力;(4)修复旧齿轮;(5)配凑中心距。
对于齿数z=8~20的直齿圆柱齿轮,当顶圆直径d a=mz+2m+2xm时,不产生根切的最小变位系数x min,以及齿顶厚S a=0。
4m和S a=0时的变位系数x sa=0.4m和x sa=0如表1所列。
2 变位齿轮的简易计算将变位齿轮无侧隙啮合方程式作如下变换:总变位系数中心距变动系数齿顶高变动系数表 1 齿数z=8~20圆柱齿轮的变位系数z x min x sa=0.4m x sa=08 910111213141516171819 200。
53 0.47 0。
42 0.36 0。
30 0.24 0.18 0。
12 0.06 0-0。
05 -0.11 -0。
170.180.220。
270.310.350。
390。
430.460.500。
530.560.590。
620.560.630。
700。
760.820。
880。
930.981。
031。
081.131。
181.23或Δy=xΣ-y式中:α-—压力角,α=20°;α′--啮合角;z2、z1——大、小齿轮的齿数。
将上述三式分别除以,则得:由上述公式可以看出,当齿形角α一定时,x z、y z和Δy z均只为啮合角α′的函数。
在设计计算时,只要已知x z、y z、Δy z和α′四个参数中的任一参数,即可由变位齿轮的x z、y z、Δy z和啮合角α′的数值表(表2)中,查出其他三个参数,再进行下列计算。
一般齿轮手册上均列有此数值表。
式中正号用于外啮合,负号用于内啮合。
3 计算实例例1:已知一对外啮合变位直齿轮,齿数z1=18,z2=32,压力角α=20°,啮合角α′=22°18′,试确定总变位系数xΣ、中心距变动系数y及齿顶高变动系数Δy。
变位系数与螺旋角变化对齿轮性能影响的研究

作者简介:黄超群(1981-),女,湖南邵东人,助教,硕士研究生,研究方向:汽车结构分析。
收稿日期:2009-06-15;修回日期:2009-09-290%引%言在齿轮结构参数中,变位系数和螺旋角的改变对斜齿轮啮合性能有很大的影响[1-5],变位系数直接影响齿轮传动系统的性能;而对于斜齿轮,螺旋角的大小也直接影响齿轮系统的啮合传动性能。
本文利用有限元显式动力学分析方法对变位系数和螺旋角大小的变化对齿轮系统的瞬态性能的影响进行了分析,为改善齿轮系统的动态性能提供参考。
1显式动力学分析显式动力学的核心是将时间变量进行离散。
假设在时间t 有一个时间增量△t ,在t 时刻的加速度定义为:{at }=[M ]-1{Ft ext ]-Ft int}.%%%%其中F extt 是施加的外部体积力分量;F intt 是相关单元应变引起的内部力矢量。
同时F intt =∑{%Ω乙B T σnd Ω+Fhg }+Fcontact %%%.Fhg 为沙漏阻力,Fcontact 为接触力。
由加速度的中心差分法,可得t+△t /2时刻的速度和位移:{Vt+△t /2}={Vt-△t /2}+{at }△tt %%;{ut+△t }={ut }+{Vt+△t /2}△tt+△t /2;△tt+△t /2=0.5(△tt+△tt+△t)%。
从而实现在初始几何形状{X0}上由增加位移增量来改变几何形状:{x t+△t }={x 0}+{ut+△t }%.%2%斜齿轮有限元模型的建立本文利用UG 建立三维几何模型,斜齿轮副中主动齿轮、被动齿轮的齿数分别为40和26,齿宽分别为19.7mm ,21.5mm ,变位系数分别为0.12,0.245,法向模量为2,压力角为16°,中心距为79.4mm ,分度圆螺旋角β=33°,其有限元模型见图1,该齿轮副的设计材料为20CrM n T i 。
在主动齿轮轴上施加一角速,同时在输出齿轮轴上施加转矩。
变为系数理论计算与图表查看
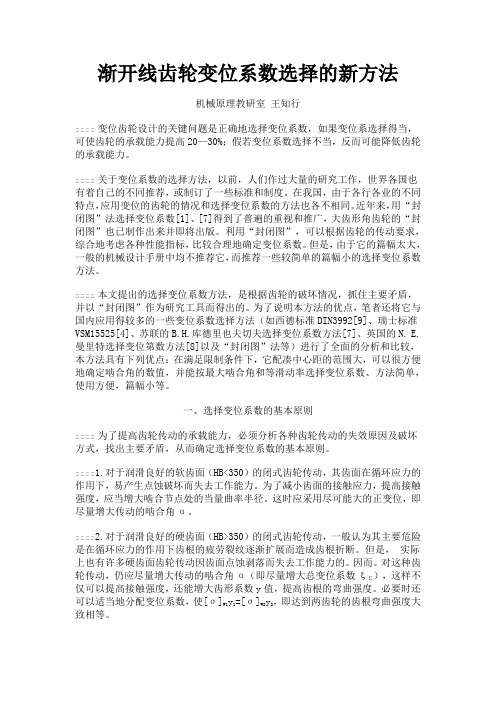
渐开线齿轮变位系数选择的新方法机械原理教研室王知行zzzz变位齿轮设计的关键问题是正确地选择变位系数,如果变位系选择得当,可使齿轮的承载能力提高20—30%;假若变位系数选择不当,反而可能降低齿轮的承载能力。
zzzz关于变位系数的选择方法,以前,人们作过大量的研究工作,世界各国也有着自己的不同推荐,或制订了一些标准和制度。
在我国,由于各行各业的不同特点,应用变位的齿轮的情况和选择变位系数的方法也各不相同。
近年来,用“封闭图”法选择变位系数[1]、[7]得到了普遍的重视和推广,大齿形角齿轮的“封闭图”也已制作出来并即将出版。
利用“封闭图”,可以根据齿轮的传动要求,综合地考虑各种性能指标,比较合理地确定变位系数。
但是,由于它的篇幅太大,一般的机械设计手册中均不推荐它,而推荐一些较简单的篇幅小的选择变位系数方法。
zzzz本文提出的选择变位系数方法,是根据齿轮的破坏情况,抓住主要矛盾,并以“封闭图”作为研究工具而得出的。
为了说明本方法的优点,笔者还将它与国内应用得较多的一些变位系数选择方法(如西德标准DIN3992[9]、瑞士标准VSM15525[4]、苏联的B.H.库德里也夫切夫选择变位系数方法[7]、英国的N. E.曼里特选择变位第数方法[8]以及“封闭图”法等)进行了全面的分析和比较,本方法具有下列优点:在满足限制条件下,它配凑中心距的范围大,可以很方便地确定啮合角的数值,并能按最大啮合角和等滑动率选择变位系数、方法简单,使用方便,篇幅小等。
一、选择变位系数的基本原则zzzz为了提高齿轮传动的承载能力,必须分析各种齿轮传动的失效原因及破坏方式,找出主要矛盾,从而确定选择变位系数的基本原则。
zzzz1.对于润滑良好的软齿面(HB<350)的闭式齿轮传动,其齿面在循环应力的作用下,易产生点蚀破坏而失去工作能力。
为了减小齿面的接触应力,提高接触强度,应当增大啮合节点处的当量曲率半径。
这时应采用尽可能大的正变位,即尽量增大传动的啮合角α。
变位齿轮参数及计算
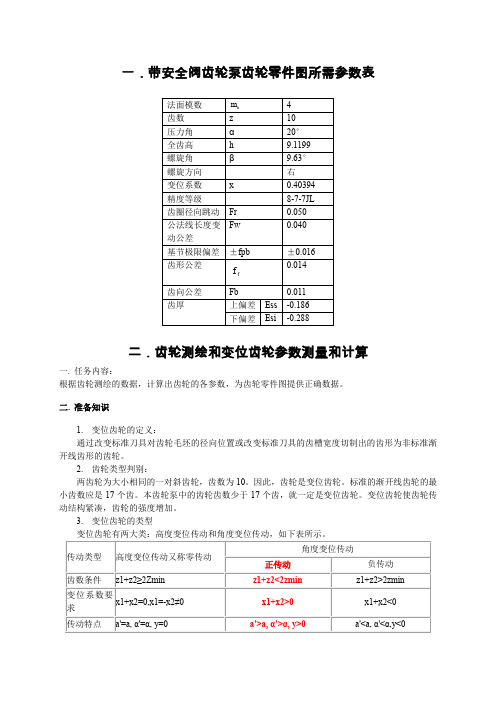
一.带安全阀齿轮泵齿轮零件图所需参数表法面模数nm 4齿数z 10压力角α20°全齿高h 9.1199螺旋角β9.63°螺旋方向右变位系数x 0.40394精度等级8-7-7JL齿圈径向跳动Fr 0.050公法线长度变动公差Fw 0.040基节极限偏差±fpb ±0.016齿形公差ff0.014齿向公差Fb 0.011齿厚上偏差Ess -0.186下偏差Esi -0.288二.齿轮测绘和变位齿轮参数测量和计算一.任务内容:根据齿轮测绘的数据,计算出齿轮的各参数,为齿轮零件图提供正确数据。
二.准备知识1.变位齿轮的定义:通过改变标准刀具对齿轮毛坯的径向位置或改变标准刀具的齿槽宽度切制出的齿形为非标准渐开线齿形的齿轮。
2.齿轮类型判别:两齿轮为大小相同的一对斜齿轮,齿数为10。
因此,齿轮是变位齿轮。
标准的渐开线齿轮的最小齿数应是17个齿。
本齿轮泵中的齿轮齿数少于17个齿,就一定是变位齿轮。
变位齿轮使齿轮传动结构紧凑,齿轮的强度增加。
3.变位齿轮的类型变位齿轮有两大类:高度变位传动和角度变位传动,如下表所示。
传动类型高度变位传动又称零传动角度变位传动正传动负传动齿数条件z1+z2≥2Zmin z1+z2<2zmin z1+z2>2zmin 变位系数要求x1+x2=0,x1=-x2≠0x1+x2>0 x1+x2<0 传动特点a'=a, α'=α, y=0 a'>a, α'>α, y>0 a'<a, α'<α,y<0主要优点小齿轮取正变位,允许z1<zmin ,减小传动尺寸。
提高了小齿轮齿根强度,减小了小齿轮齿面磨损,可成对替换标准齿轮。
传动机构更加紧凑,提高了抗弯强度和接触强度,提高了耐磨性能,可满足a'>a 的中心距要求。
重合度略有提高,满足a'<a 的中心距要求。
基于SolidWorks的变位齿轮参数化设计
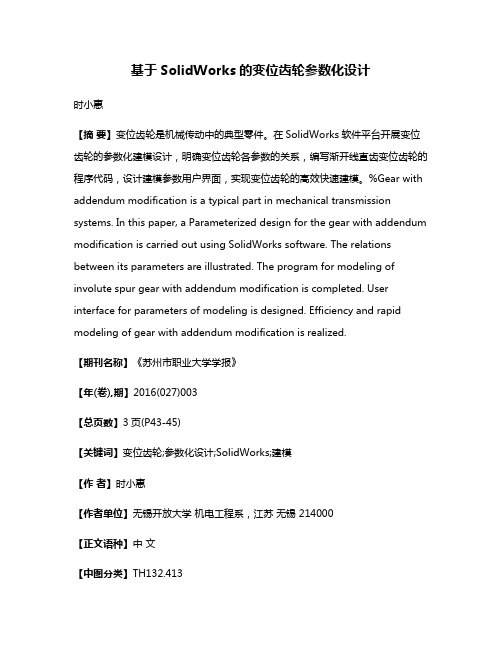
基于SolidWorks的变位齿轮参数化设计时小惠【摘要】变位齿轮是机械传动中的典型零件。
在SolidWorks软件平台开展变位齿轮的参数化建模设计,明确变位齿轮各参数的关系,编写渐开线直齿变位齿轮的程序代码,设计建模参数用户界面,实现变位齿轮的高效快速建模。
%Gear with addendum modification is a typical part in mechanical transmission systems. In this paper, a Parameterized design for the gear with addendum modification is carried out using SolidWorks software. The relations between its parameters are illustrated. The program for modeling of involute spur gear with addendum modification is completed. User interface for parameters of modeling is designed. Efficiency and rapid modeling of gear with addendum modification is realized.【期刊名称】《苏州市职业大学学报》【年(卷),期】2016(027)003【总页数】3页(P43-45)【关键词】变位齿轮;参数化设计;SolidWorks;建模【作者】时小惠【作者单位】无锡开放大学机电工程系,江苏无锡 214000【正文语种】中文【中图分类】TH132.413齿轮是机械传动系统中能提供连续平稳传动的常见零件.为了改善高速小齿轮强度、调整齿轮啮合传动中心距或避免小齿数齿轮加工时的根切现象,通常会将齿轮做变位处理,即加工齿轮时改变标准刀具对齿轮毛坯的径向位置或改变标准刀具的齿槽宽切制出齿形,形成变位齿轮.由于变位齿轮不是标准齿轮,其变位系数等参数通常因设计或加工要求的不同而不同,这就使得其相应的三维建模较标准齿轮更复杂.为简化设计过程,缩短建模时间,参数化设计是一个有效途径.也正因如此,近年来基于Pro/E[1]、CATIA[2],以及SolidWorks[3-4]等三维建模软件二次开发技术的参数化建模和设计获得了较快的发展.本文基于参数化设计的理念,利用SolidWorks三维建模软件平台,以变位直齿齿轮为建模对象,利用软件VBA功能编写二次开发程序,制作参数化建模界面,完成三维模型快速构建,可有效缩短设计周期,提高设计效率.由加工齿轮的不根切条件可得最小变位系数为式中:ha*为齿顶高系数;zmin为用标准齿条形刀具切削标准齿轮的最少齿数;z为齿轮的当前齿数.当齿轮的齿数z<zmin时,xmin为正值,为了避免发生根切,该齿轮应采用正变位,其变位系数x≥xmin;反之,当z>zmin时,xmin为负值,说明该齿轮在满足x≥xmin的前提下采用负变位也不会发生根切.由于变位齿轮模数m、齿数z、压力角α(本文取20°)和变位系数x预先确定,因此变位齿轮特征参数可以采用以上4个参数确定,并有以下公式:式中:D为齿轮分度圆直径;Db为基圆直径;Da为齿顶圆直径;Df为齿根圆直径;s为变位齿轮分度圆上的齿厚;e为分度圆上的齿槽宽;m为变位齿轮模数;z为齿数;α为压力角.在二次开发变位齿轮的时候,确定齿轮齿廓渐开线和齿轮的齿根圆之间的过渡关系是关键[5-7].齿轮轮齿截面图见图1.当齿根圆直径大于基圆直径时,需要采用过渡曲线连接齿廓渐开线与齿根圆,使齿轮轮廓线平滑.本文采用圆弧方式过渡,圆弧半径r0取值0.38 m.编写程序代码时,可通过比较z和的大小来判断齿根圆直径Df是否大于基圆直径Db.当时,Df>Db;反之,Df<Db.绘制过渡圆弧AB部分时,采用下列程序代码:Dim skSegment As ObjectSet skSegment = Part.SketchManager.CreateArc(x2 / 1000,0.001 * (y2 - 5),0,0.001 * x3,0.001 * (y3 - 5),0,0.001 * x0,0.001 * (y0 - 5),0,1)Part.SetPickModePart.ClearSelection2 Trueboolstatus = Part.Extension.SelectByID2("Arc1","SKETCHSEGMENT",0,0,0,True,0,Nothing,0)Part.Extension.MoveOrCopy False,1,False,0,0,0,0,0.001 * 5,0 Part.ClearSelection2 True渐开线部分利用渐开线上的各个控制点经点描后生成的近齿廓渐开线,采用以下程序代码实现:Part.SetPickModeDim pointArray As VariantDim points() As DoubleReDim points(0 To n) As Double...pointArray = pointsSet skSegment = Part.SketchManager.CreateSpline((pointArray))Part.ClearSelection2 True中间部分插入的是点的坐标,将点的三维坐标(编号从0到n)赋值给point (),完成近齿廓渐开线各个控制点的绘制.齿轮外轮廓采用插入圆弧的方式绘制,其程序代码如下:Set skSegment = Part.SketchManager.CreateArc(0#,0#,0#,0.001 * 0.5 * Db * (Cos(u) + u * Sin(u)),0.001 * 0.5 * Db * (Sin(u) - u * Cos (u)),0#,0.001 * x11,0.001 * y11,0#,1)Part.SetPickModePart.ClearSelection2 True其余圆弧插入的方式类似,再经过拉伸、阵列等操作完成齿轮的三维建模.在SolidWorks自带的VBA中插入用户界面,提供模数m、齿数z、压力角α和变位系数x四个关键参数的输入功能,其界面设计如图2所示[8-9].将齿轮的参数在窗体的指定位置输入,点击生成模型即可完成变位齿轮的建模.图3是输入一组参数后的模型效果图.以变位齿轮为对象,在SolidWorks平台上进行了参数化三维建模,完成了包括齿根过渡圆弧、齿廓关键部位的程序编写和建模界面设计,实现了变位齿轮的高效快速建模,为齿轮及其他典型机械零件的参数化设计提供了思路.【相关文献】[1]毕舟,吴成智. 基于Pro/E二次开发的渐开线变位齿轮精确建模[J]. 新技术新工艺,2014(6):57-61.[2]顾勇,高一知. 基于CATIA 的渐开线变位齿轮参数化建模与二次开发[J]. 机械,2009,36(S1):60-62.[3]孙付春,蒋家旺,魏勇,等. 基于SolidWorks API的全摆线齿轮参数化设计[J]. 成都大学学报(自然科学版),2012,31(4):382-384.[4]高红英. 基于SolidWorks 的变位齿轮的分析与设计[J]. 工程图学学报,2007,28(4):141-144.[5]施雄泉. 园柱齿轮传动最少齿数的分析[J]. 苏州市职业大学学报,2014,25(1):38-40. [6]喻久港. 基于SolidWorks利用VB编程绘制渐开线齿轮[J]. 机械工程与自动化,2012(1):63-64.[7]鲁春艳. 基于UG 的齿轮齿条式转向器的虚拟设计与分析[J]. 苏州市职业大学学报,2009,20(1):20-23.[8]杨晓蕾,吴淑芳. 基于Archard磨损理论的螺旋伞齿轮精锻成形模具磨损分析[J]. 长春大学学报(自然科学版),2014,24(4):451-454.[9]侯红玲. 斜齿轮及斜齿变位齿轮的参数化建模[J]. 机械设计与制造,2015(8):214-217.。
齿轮的变位系数

齿轮的变位系数变位系数x是径向变位系数,加工标准齿轮时,齿条形刀具中线与齿轮分度圆相切。
加工变位齿轮时齿条形刀具中线与齿轮分度圆相切位置偏移距离xm,外移x为正,内移x为负。
除了圆锥齿轮有时采用切向变位xt外,圆柱齿轮一般只采用径向变位。
变位系数x的选择不仅仅是为了凑中心距,而主要是为了提高强度和改善传动质量。
变位齿轮的主要功用如下:(1)减小齿轮传动的结构尺寸,减轻重量 在传动比一定的条件下,可使小齿轮齿数zl<zmin,从而使传动的结构尺寸减小,减轻机构重量。
(2)避免根切,提高齿根的弯曲强度 当小齿轮齿数z1<zmin时,可以利用正变位避免根切,提高齿根的弯曲强度。
x≥xmin=(Z-Zmin)/Zmin,对α=20o时,Zmin=17。
(3)提高齿面的接触强度 采用啮合角α’>α的正传动时,由于齿廓曲率半径增大,故可以提高齿面的接触强度。
(4)提高齿面的抗胶合耐磨损能力 采用啮合角α’>α的正传动,并适当分配变位系数xl、x2,使两齿轮的最大滑动率相等时,既可降低齿面接触应力,又可降低齿面间的滑动率以提高齿轮的抗胶合和耐磨损能力。
(5)配凑中心距 当齿数z1、z2不变的情况下,啮合角α’不同,可以得到不同的中心距,以达到配凑中心距的目的。
(6)修复被磨损的旧齿轮 齿轮传动中,小齿轮磨损较重,大齿轮磨损较轻,可以利用负变位把大齿轮齿面磨损部分切去再使用,重配一个正变位小齿轮,这就节约了修配时需要的材料与加工费用。
选择变位系数的基本原则(1)润滑条件良好的闭式齿轮传动 当齿轮表面的硬度不高时(HBS<350),即对于齿面未经渗碳、渗氮、表面淬火等硬化处理的齿轮,齿面疲劳点蚀或剥伤为其主要的失效形式,这时应选择尽可能大的总变位系数x,即尽量增大啮合角,以便增大啮合节点处齿廓的综合曲率半径,减少接触应力,提高接触强度与疲劳寿命。
当轮齿表面硬度较高时(HBS>350),常因齿根疲劳裂纹的扩展造成轮齿折断而使传动失效,这时,选择变位系数应使齿轮的齿根弯曲强度尽量增大,并尽量使相啮合的两齿轮具有相近的弯曲强度。
机械设计基础_第4章_变位齿轮
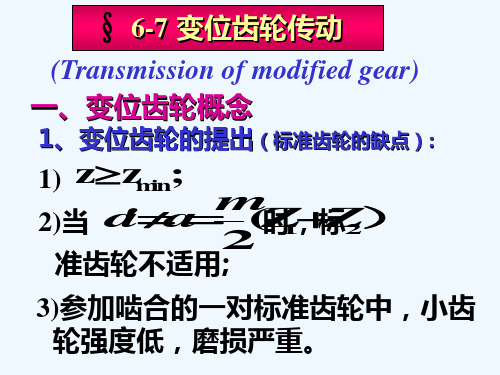
(1)、分度圆齿厚s与齿间e
r
O
ab
xm
sm2xmtg
2
rb
c
em2xmtg
xm
B
xm
N
ab
Pc
ham
2
(2)、齿根高
h
与
f
齿顶高h a
hf (hac*)mxm
在 保 证 齿 全 高 不 变 时 : h a h a m x m
x1x20,且 x1x20
aa(rr),
齿数xx21条xx件12m m:iinnhhaa((Z ZZ Zm mm m iinniinnZ Z12))两 则 式 Z 相 1 加Z , 2设 h2 aZ m 1in
优点:减小机构的尺寸,改善磨损情况; 提高小齿轮强度,提高承载能力。
解: ∵ s'
m 2xmtg
2
s'
19.52162 2x216tg20
x20.482
x 1 x 20 .4 8 2
计算尺寸,校核 sa1 ?
解:1)确定传动类型
m
4 .2 5
a 2 (Z 1 Z 2 )2(1 3 4 4 ) 1 2 1 .1 2 5
∵ a a , 可 采 用 等 移 距 变 位 齿 轮 传 动 。
2)选择变位系数,计算参数
1713
小齿轮正变位: x1x1m in 17 0.235 大齿轮负变位: x 2 x 1 0 .2 3 5
k in(vk)
θ
二、变位齿轮传动
1、正确啮合条件与连续传动条件同 标准齿轮传动。
即 : m 1m 2m ,12; [].
- 1、下载文档前请自行甄别文档内容的完整性,平台不提供额外的编辑、内容补充、找答案等附加服务。
- 2、"仅部分预览"的文档,不可在线预览部分如存在完整性等问题,可反馈申请退款(可完整预览的文档不适用该条件!)。
- 3、如文档侵犯您的权益,请联系客服反馈,我们会尽快为您处理(人工客服工作时间:9:00-18:30)。
[1]Radouane Akrache1 - Jian Lu.Integrated Design for Fatigue Life Estimation of Structures
[2]江旭昌.大变位齿轮.北京:中闭建材工业出版社.2001.
[3]朱景梓.渐开线齿轮变位系数的选择(修订本).北京:人民教育出版社,1982.
大变位齿轮变位系数的可视化
湖南文理学院芙蓉学院
本科生毕业设计任务书
设计题目
大变位齿轮变位系数的可视化设计
学生姓名
专业班级
学号
指导教师
教研室(或外聘单位)
机械设计教研室
起止Байду номын сангаас间
2015年3月2日----2015年5月22日
毕业设计任务、目的与基本要求:
1 毕业设计的任务
研究大变位齿轮变位系数选择的原理,研究齿轮大变位系数选择的封闭图软件,完成设计任务。
[7]薛定宇,陈阳泉.控制数学问题的MATLAB求解[M].北京:清华大学出版社,2007
[8]薛定宇,陈阳泉.基于MATLAB/Simulink的系统仿真技术与应用(第2版)[M].北京:清华大学出版社,2011
[98]薛定宇.高等应用数学问题的MATLAB求解(第2版)[M].北京:清华大学出版社,2008
2 毕业设计的目的
综合已学知识,提高学生外语水平、专业水平、计算机水平、综合能力、创新开发研究能力以及与严谨的工作作风。
3 毕业设计的要求
(1)查阅资料,撰写开题报告,掌握软件开发的基本步骤,将参考文献1译成中文,并打印;
(2)研究齿轮大变位系数选择的封闭图的各种约束条件,利用封闭图的原理,采用计算机可视化技术,通过建立变位系数设计数学模型,设计者可根据需要的齿数组合将其封闭图显示在屏幕上,并能将变位系数与各项性能指标之间的关系直观地显示出来。设计者可根据期望的各项性能指标来调整变位系数,直到满意为止, 以MATLAB软件研究大变位系数选择的封闭图可视化设计软件
(3)将完整的各种文件、说明书、软件使用说明书与软件平台等刻成光盘一张,按学院规定的格式撰写并打印设计说明书与附件,说明书字数不少于1.5万字;
(4)除给定参考文献外查《机械传动》、《机械设计》、《矿山机械》等专业期刊与MATLAB图书,文献不小于12篇(至少英文二篇)。
注意:资料格式采用2015版。
[4]武丽梅,刘岩松.大变位齿轮变位系数的可视化设计[J].机械设计与制造,2003,3:66-67
[5]侯克青徐荣张伟侯晓晨.齿轮变位系数选择的封闭图软件研发[J].机械传动,2013,37(12):90-92
[6]马翠龙.用于选取齿轮变位系数的电子封闭图的研究[D]华中农业大学,2007-06-01
⑤毕业设计主要工作阶段:
学习软件基本知识与课题有关专题部分2015年3月29日-5月22日。
⑥毕业设计答辩阶段:答辩时间:2015年5月22
课
题
申
报
与
审
查
指导教师(签名):2014年11月30日
教研室主任(签名):2014年11月30日
系主任(签名):2014年11月30日
[10]薛定宇.控制系统计算机辅助设计—MATLAB语言与应用(第3版)[M].北京:清华大学出版社,2012
毕业设计进度安排:
①毕业设计准备、资料查找阶段:2015年3月2日前
②毕业调研阶段:2015年3月2日至2015年3月15日
③毕业设计开题报告阶段:2015年3月15日-29日
④毕业设计中期检查:2014年4月12日