精益生产工具(1)
精益生产12种工具

原则化工作
懂得要执行什么环节和懂得该环节运营正常,两者都是同等主要旳。 为了确保实现产品质量级别、一致性、有效性及效率,有必要采用写 成文件旳分环节流程或者原则作业程序(SOP)来降低错误和接触时 间。尽管原则化工作建立了明确要求工人和机器操作旳有用文档,原 则化工作在精益制造工具中是最不受到注重旳。这些明确要求旳操作 能帮助工人在制造流程中应用最佳实践。原则化工作同步还能为连续 改善打好基础,因为统计成文件形式旳流程更轻易加以分析与改善。 为了阐释原则化工作,SOP 应该采用图片、文字、表格、标志、色彩 及视觉指示器向不同旳工作组沟通一致旳直观旳信息。这种图形指示, 也被称为操作措施手册(OMS),解释特定生产线范围内根据事件顺 序(SOE)旳每个环节,还能设计并制作纸质或屏幕旳视觉工作指导。
另一项工具是模拟,它能帮助降低维护有关旳挥霍。经过支持模拟, 先进服务管理系统一般能根据生产计划安排维护并根据实际完毕旳生 产自动更新维护计划(电子链接设备本身旳运转时间仪到计划维护 上)。
全员生产维护 (TPM)
目旳是消除下列“六大”维护有关旳挥霍。 1. 设备停工 2. 安顿和调整 3. 小规模停工和闲置 4. 计划外旳停工 5. 因为机器错误制造不合格品所花旳时间 6. 开启期旳不合格品
订单被“推”向工厂车间及库存。
排序与混合模式生产
另一项精益工具是排序,或决定一条生产线上执行不同作业旳顺序, 以达成目旳(例如每日需要旳数量)。这也叫做混合模式生产,该模 式生产不同批量旳几种零件或产品,这些零件或产品旳量接近于当日 将销售旳相同旳产品组合。混合模式计划或排序决定组件旳制造和交 付,涉及那些由外部供给商提供旳组件。重申一下,目旳是根据每日 需求建立生产模式。这点对于汽车制造业极其主要,考虑到全球市场 上老到客户百分比越来越大,争取这些客户旳竞争驱使汽车业原始设 备制造商(OEM)提供有着越来越丰富特色和选择旳产品。从纯功能 旳角度来看,汽车和卡车正日益成为日用具,竞争性旳产品差别化主 要经过提供独特旳色彩、构造、风格及可选配置组合来实现,这么任 何一款车型都有上千种潜在组合。库存全部这些组合在成本上几乎无 法做到,而且查找是否生产了某种特定组合也要花诸多时间,这好比 海底捞针。另外,挑剔旳客户期望立即得到某种独特特色旳配置组合。 这些原因造成一种难题-怎样迅速又有利可图地交付定制成品车。
精益生产的十大工具

精益生产的十大工具精益生产的十大工具是精益生产方法中使用的工具和技术,旨在帮助企业提高生产效率、降低成本、提高质量。
精益生产是一套关于如何优化生产流程的方法论,其核心理念是通过消除浪费,实现更高效、更灵活的生产。
第一个工具是价值流图。
价值流图是将产品的生产流程可视化的工具,它可以帮助企业了解产品从原材料到最终交付的整个流程,从而找出生产中的浪费和瓶颈,并进行优化。
第二个工具是流程平衡。
流程平衡是通过平衡工作站之间的工作量,达到生产过程中的最佳效益。
通过优化工作站之间的工作分配,可以有效地降低等待时间,提高整体生产效率。
第三个工具是一体化生产系统。
一体化生产系统是通过整合产线上的各个工作站,实现生产过程的无缝衔接。
通过一体化生产系统,企业可以实现生产过程的整合和优化,提高生产效率。
第四个工具是短交付时间。
短交付时间是指将产品从订单到交付的时间尽量缩短。
通过缩短交付时间,可以提高客户满意度,同时也可以减少库存和浪费。
第五个工具是标准化工作。
标准化工作是指制定明确的工作标准和操作规范,确保每一项工作都能按照规定的要求进行。
通过标准化工作,可以提高产品质量和生产效率。
第六个工具是柔性生产。
柔性生产是指企业具备快速调整生产线的能力,以适应市场需求的变化。
通过柔性生产,企业可以更加灵活地应对市场变化,降低库存和生产成本。
第七个工具是持续改进。
持续改进是指企业不断地寻找改进的机会,并采取行动来实现持续的改变。
通过持续改进,企业可以不断提高生产效率和产品质量,保持竞争优势。
第八个工具是团队合作。
团队合作是指利用团队的力量,共同解决问题和实现目标。
通过团队合作,可以激发员工的创造力和合作精神,提高生产效率。
第九个工具是视觉管理。
视觉管理是指通过可视化的手段来传达信息和管理生产过程。
通过视觉管理,可以提高沟通效率,减少错误和浪费。
第十个工具是员工培训。
员工培训是指提供必要的培训和教育,使员工能够更好地理解和应用精益生产的方法。
精益生产十大工具

精益生产十大工具精益生产是一种旨在提高生产效率和减少浪费的管理方法。
它包含了许多工具和技术,旨在帮助组织更好地管理资源、提高产能和优化流程。
在这篇文章中,我将介绍精益生产的十大工具,以帮助读者更好地了解和应用这些工具。
1.5S法则:5S法则是一种用于组织工作环境和提高效率的方法。
它包括整理、整顿、清扫、标准化和自律五个步骤。
通过实施5S法则,组织可以改善工作环境,减少浪费和失误,并提高生产效率。
2.价值流图:价值流图是一种用于分析和改善生产流程的工具。
它可以帮助组织识别价值和非价值活动,并定位瓶颈和浪费。
通过分析价值流图,组织可以找到改进的机会,并优化流程以提高产出和客户满意度。
3.流程映射:流程映射是一种用于图形化表示和分析流程的工具。
它可以帮助组织识别和理解整个流程的各个步骤和关键决策点。
通过流程映射,组织可以更好地了解流程,并找出改进的机会。
4.持续改善:持续改善是精益生产的核心原则之一。
它强调从小改进开始,通过反复模拟和实验,逐步提高流程和产品的质量。
持续改进要求组织保持开放和灵活,不断追求更高的效率和产品质量。
5.单点故障:单点故障是指在生产过程中存在可能导致整个流程中断或崩溃的单一关键节点。
通过识别和消除单点故障,组织可以提高生产线的稳定性和可靠性,并降低因故障引起的停产和成本。
6.稳定性:稳定性是指生产流程的可靠性和一致性。
通过确保设备和工艺的稳定性,组织可以减少因工艺变异而导致的浪费和不良品,提高生产效率和质量。
7.柔性制造:柔性制造是指组织能够快速适应市场需求变化,并在不降低质量和效率的情况下生产不同类型的产品。
通过实施柔性制造,组织可以更好地利用资源、减少库存和满足客户需求。
8.精细化:精细化是指组织对生产过程中每一个环节和细节进行深入分析和控制。
通过精细化,组织可以更好地了解产品和生产线的性能,并找到改进的机会,以提高生产效率和质量。
9.标准化:标准化是指通过制定和执行标准,确保生产过程和产品的一致性和质量。
精益生产十大工具

精益生产的十大工具------施增虎一、精益生产的起源精益生产:不多不少,不迟不早,刚刚好,以最少的投入来满足顾客的需求,企业获得最大的回报,投入里面包括人力、物力、设备、时间、场地,通过你的加工、生产、制造变成了成品,成品质量要好,数量要准确,供货要及时,价格要具有竞争力。
生产资源投入5M:人员manpower,机器machine,材料materials,方法methods,测量measuremant.成品输出SQDCM:安全safety,质量quality,成本cost,交期delivery,士气morale.精益5大原则:寻找价值;认识价值流;让作业流动起来;按客户的需求拉动生产;持续生产,尽善尽美。
-丰田生产方式与精益生产-丰田生产方式产生背景及发展-精益生产的新发展二、精益生产两大支柱-核心理论:消除八大浪费,降低成本-两大支柱:准时化和自动化三、精益生产要领的应用精益案例:一、通用加工工厂从濒临破产到精益生产美国第一工厂。
二、从求医进程看医院办理四、杜绝浪费消除成本(一)精益生产的思想基础:消除浪费浪费:一切不为顾客创造价值但却消耗资源活动或行为。
区分增值活动与非增值活动增值活动:将原料或信息转换,改变形状,第一次来满足客户的需求;浪费:目前是不能取消的动作叫浪费增值的三个条件:改变形状或形态,第一次做对不返工,客户付钱。
五、杜绝浪费消除成本(二)七种浪费:过量生产浪费,纠正缺陷浪费,多余工序浪费,过渡库存浪费,物料运输浪费,多余动作浪费,等候时间浪费去除过量生产浪费技巧:小批量生产(或单件流),拉动式生产,均衡计划。
去除纠正缺陷浪费技巧:供应商质量保证,防错,减少变差,在线检验去除多余工序浪费技巧:对比现有工艺和顾客需求,产品设计改进,六、杜绝浪费消除成本(三)去除过渡库存浪费技巧:小批量生产,均衡计划,拉动系统,提升设备可利用率和一次合格率,及时处理过期物料,小批量采购,及时生产,缩小仓库面积。
精益生产管理的十大工具

精益生产管理的十大工具精益生产管理是一种通过优化生产过程,减少浪费和提高效率的方法。
在精益生产管理中,有许多工具和技术可用于帮助企业实现这些目标。
以下是精益生产管理的十大工具。
1. 价值流图:价值流图是一种可视化工具,用于展示产品或服务在整个价值流中的流动,包括所有的价值和非价值活动。
通过使用价值流图,企业可以识别出浪费和瓶颈,并制定改进计划。
2. 5S:5S是一个用于组织和维护工作场所的系统。
它包括整理、整顿、清扫、标准化和维持的步骤。
通过实施5S,企业可以改善工作环境,减少浪费和提高工作效率。
3. 高效供应链管理:高效供应链管理是通过优化供应链中的物流和信息流来降低成本和提高响应速度。
它包括减少库存、改善交付时间和优化供应链合作伙伴关系等方面。
4. 物料需求计划:物料需求计划是一种用于确定需要多少原材料和零部件的工具。
通过正确计划物料需求,企业可以避免库存积压和缺货的问题。
5. 单点作业:单点作业是一种通过减少从一台机器到另一台机器的传送时间来减少生产周期的方法。
这可以通过重新布局设备、改进工艺流程和优化工作站来实现。
6. 柔性生产:柔性生产是一种能够快速适应市场需求和变化的生产方式。
它包括灵活的工作组织、多功能的设备和高度培训的员工。
7. 持续改进:持续改进是一种通过不断寻找和消除浪费、改进工艺和提高质量来提升生产效率的方法。
它可以通过实施PDCA循环(计划、执行、检查、行动)和员工参与来实现。
8. 产能平衡:产能平衡是一种通过平衡生产线上的工作负荷来避免瓶颈和过度生产的方法。
这可以通过调整生产节奏、提高设备利用率和优化工艺来实现。
9. 供应商合作:供应商合作是一种与供应商建立长期合作关系,并与其共同努力改进质量、交付和成本的方法。
这可以通过共享信息、共同制定目标和进行持续改进活动来实现。
10. 质量管理工具:质量管理工具是一系列用于识别和解决质量问题的方法和技术。
其中包括流程图、因果图、直方图、散点图等。
精益生产培训之十大工具
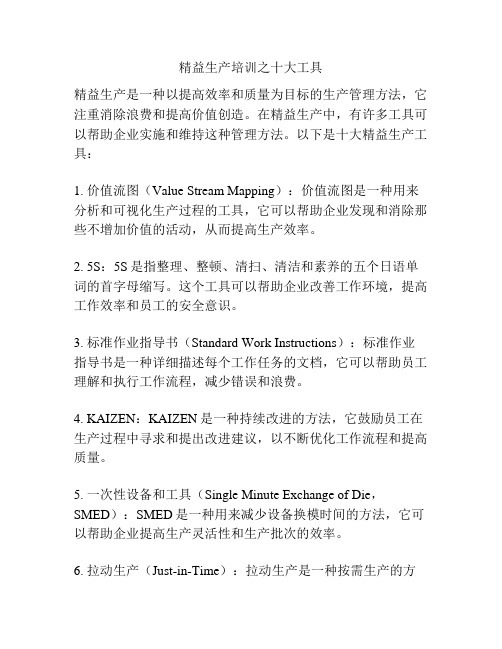
精益生产培训之十大工具精益生产是一种以提高效率和质量为目标的生产管理方法,它注重消除浪费和提高价值创造。
在精益生产中,有许多工具可以帮助企业实施和维持这种管理方法。
以下是十大精益生产工具:1. 价值流图(Value Stream Mapping):价值流图是一种用来分析和可视化生产过程的工具,它可以帮助企业发现和消除那些不增加价值的活动,从而提高生产效率。
2. 5S:5S是指整理、整顿、清扫、清洁和素养的五个日语单词的首字母缩写。
这个工具可以帮助企业改善工作环境,提高工作效率和员工的安全意识。
3. 标准作业指导书(Standard Work Instructions):标准作业指导书是一种详细描述每个工作任务的文档,它可以帮助员工理解和执行工作流程,减少错误和浪费。
4. KAIZEN:KAIZEN是一种持续改进的方法,它鼓励员工在生产过程中寻求和提出改进建议,以不断优化工作流程和提高质量。
5. 一次性设备和工具(Single Minute Exchange of Die,SMED):SMED是一种用来减少设备换模时间的方法,它可以帮助企业提高生产灵活性和生产批次的效率。
6. 拉动生产(Just-in-Time):拉动生产是一种按需生产的方法,它可以帮助企业减少库存和生产浪费,并且能够更好地满足顾客需求。
7. 故障模式与影响分析(Failure Mode and Effects Analysis,FMEA):FMEA是一种用来分析和评估潜在故障模式和其影响的方法,它可以帮助企业识别潜在风险,并采取措施进行预防和改进。
8. 委托管理(Gemba Walk):委托管理是一种通过实地走访生产现场来了解问题和挑战的方法,它可以帮助管理层与现场员工保持沟通,并及时解决问题。
9. PDCA循环:PDCA循环是指计划、实施、检查和行动的四个步骤,它是一种持续改进的管理方法,可以帮助企业不断优化工作流程和提高绩效。
精益生产常用工具
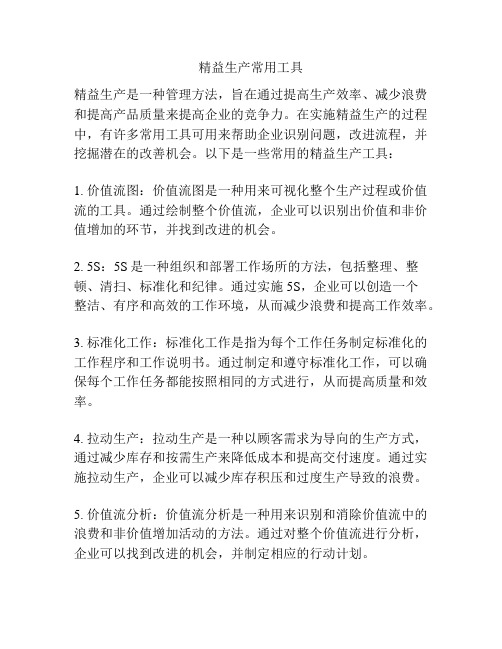
精益生产常用工具精益生产是一种管理方法,旨在通过提高生产效率、减少浪费和提高产品质量来提高企业的竞争力。
在实施精益生产的过程中,有许多常用工具可用来帮助企业识别问题,改进流程,并挖掘潜在的改善机会。
以下是一些常用的精益生产工具:1. 价值流图:价值流图是一种用来可视化整个生产过程或价值流的工具。
通过绘制整个价值流,企业可以识别出价值和非价值增加的环节,并找到改进的机会。
2. 5S:5S是一种组织和部署工作场所的方法,包括整理、整顿、清扫、标准化和纪律。
通过实施5S,企业可以创造一个整洁、有序和高效的工作环境,从而减少浪费和提高工作效率。
3. 标准化工作:标准化工作是指为每个工作任务制定标准化的工作程序和工作说明书。
通过制定和遵守标准化工作,可以确保每个工作任务都能按照相同的方式进行,从而提高质量和效率。
4. 拉动生产:拉动生产是一种以顾客需求为导向的生产方式,通过减少库存和按需生产来降低成本和提高交付速度。
通过实施拉动生产,企业可以减少库存积压和过度生产导致的浪费。
5. 价值流分析:价值流分析是一种用来识别和消除价值流中的浪费和非价值增加活动的方法。
通过对整个价值流进行分析,企业可以找到改进的机会,并制定相应的行动计划。
6. 周期时间分析:周期时间分析是一种用来测量和分析整个生产过程或价值流的时间的方法。
通过测量各个环节的时间,并分析其比例和关系,企业可以找到时间浪费和瓶颈,并采取相应的改进措施。
7. 柔性生产:柔性生产是一种以快速响应市场需求为导向的生产方式,通过灵活地调整生产线和生产能力,以适应需求的变化。
通过实施柔性生产,企业可以降低库存、提高交付速度和灵活性。
8. 产能平衡:产能平衡是指在不同工序间平衡产能,以避免过剩和瓶颈的发生,从而提高效率和质量。
通过进行产能平衡,企业可以合理安排生产能力,以满足顾客需求并避免资源浪费。
综上所述,以上提到的工具是精益生产中常用的工具,通过使用这些工具,企业可以识别问题,改进流程,并发现潜在的改善机会,从而提高生产效率和产品质量,降低成本,提高竞争力。
精益生产十大工具
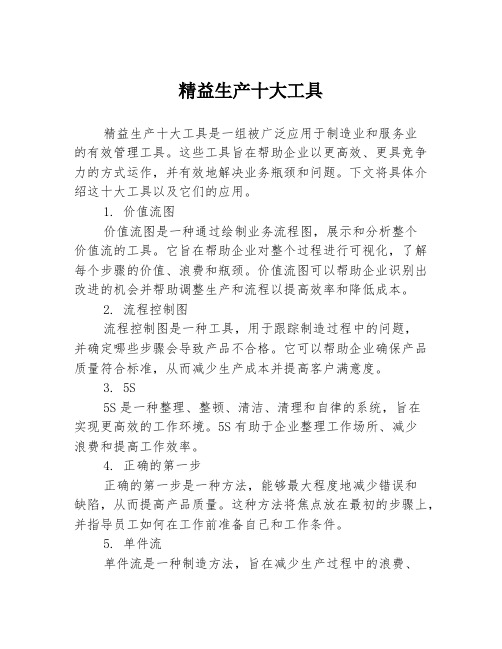
精益生产十大工具精益生产十大工具是一组被广泛应用于制造业和服务业的有效管理工具。
这些工具旨在帮助企业以更高效、更具竞争力的方式运作,并有效地解决业务瓶颈和问题。
下文将具体介绍这十大工具以及它们的应用。
1. 价值流图价值流图是一种通过绘制业务流程图,展示和分析整个价值流的工具。
它旨在帮助企业对整个过程进行可视化,了解每个步骤的价值、浪费和瓶颈。
价值流图可以帮助企业识别出改进的机会并帮助调整生产和流程以提高效率和降低成本。
2. 流程控制图流程控制图是一种工具,用于跟踪制造过程中的问题,并确定哪些步骤会导致产品不合格。
它可以帮助企业确保产品质量符合标准,从而减少生产成本并提高客户满意度。
3. 5S5S是一种整理、整顿、清洁、清理和自律的系统,旨在实现更高效的工作环境。
5S有助于企业整理工作场所、减少浪费和提高工作效率。
4. 正确的第一步正确的第一步是一种方法,能够最大程度地减少错误和缺陷,从而提高产品质量。
这种方法将焦点放在最初的步骤上,并指导员工如何在工作前准备自己和工作条件。
5. 单件流单件流是一种制造方法,旨在减少生产过程中的浪费、减少库存和减少制造时间。
它可以帮助企业以更高效的方式生产各种产品,并根据客户的需求提供服务。
6. 智能制造智能制造是一种制造技术,旨在将传统的制造过程与先进的计算机技术结合起来,以实现更高效、更可靠且更精确的生产。
智能制造的目标是提高质量、降低成本并增强企业的竞争力。
7. 按需制造按需制造是一种生产模式,在该模式下,生产和服务是根据客户需求实时产生的。
按需制造可以大大减少库存,避免过剩的库存和减少过时产品,从而提高效率和降低成本。
8. JidokaJidoka是一种制造方法,旨在通过自动化控制制造过程和机器上的检测,实现实时可视化生产过程。
Jidoka可帮助企业有效地识别和纠正制造过程中的错误,并最大限度地减少损失和产品缺陷。
9. KaizenKaizen是一种改进方法,旨在不断优化生产过程。
精益生产的十大工具
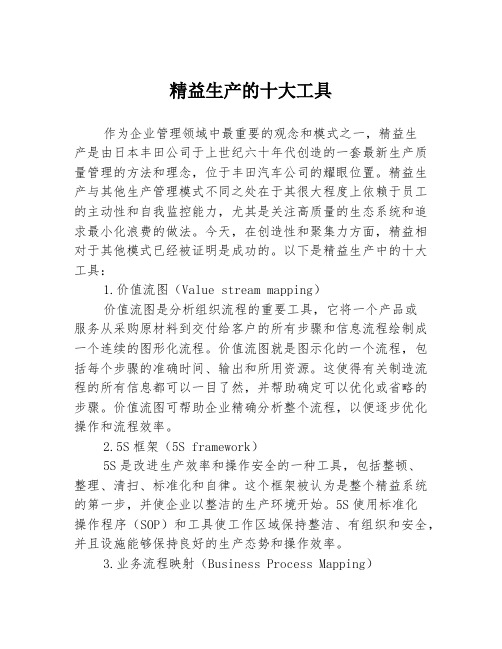
精益生产的十大工具作为企业管理领域中最重要的观念和模式之一,精益生产是由日本丰田公司于上世纪六十年代创造的一套最新生产质量管理的方法和理念,位于丰田汽车公司的耀眼位置。
精益生产与其他生产管理模式不同之处在于其很大程度上依赖于员工的主动性和自我监控能力,尤其是关注高质量的生态系统和追求最小化浪费的做法。
今天,在创造性和聚集力方面,精益相对于其他模式已经被证明是成功的。
以下是精益生产中的十大工具:1.价值流图(Value stream mapping)价值流图是分析组织流程的重要工具,它将一个产品或服务从采购原材料到交付给客户的所有步骤和信息流程绘制成一个连续的图形化流程。
价值流图就是图示化的一个流程,包括每个步骤的准确时间、输出和所用资源。
这使得有关制造流程的所有信息都可以一目了然,并帮助确定可以优化或省略的步骤。
价值流图可帮助企业精确分析整个流程,以便逐步优化操作和流程效率。
2.5S框架(5S framework)5S是改进生产效率和操作安全的一种工具,包括整顿、整理、清扫、标准化和自律。
这个框架被认为是整个精益系统的第一步,并使企业以整洁的生产环境开始。
5S使用标准化操作程序(SOP)和工具使工作区域保持整洁、有组织和安全,并且设施能够保持良好的生产态势和操作效率。
3.业务流程映射(Business Process Mapping)业务流程映射也被称为过程绘图,是企业中获得一些方案和改善的关键步骤。
此工具小组可以使用符号和图形描述企业中任何类型的业务流程和相关信息。
这可以揭示在过程中发生的问题、浪费、冗余和延迟,因此有助于消除不必要的步骤、改善流程的质量和效率。
4.一次流程变更(Single Piece Flow)这是一种最小化生产时间的原则,可以通过同一物品的生产技术一步步生产出多个物品。
使用一次流程变更工具,可以有效地降低制造成本,并使产品变得更加高效和可追溯,提高产品的核心竞争力。
5.生产平衡(Production Levelling)生产平衡是实现精益生产中的关键工具,可以帮助企业产生一个稳定的、平均的生产率水平。
实施精益生产时有哪些管理工具精益生产工具介绍

实施精益生产时有哪些管理工具精益生产工具介绍精益生产是一种优化生产流程的管理方法,通过消除浪费和提高效率来提升生产质量和降低成本。
在实施精益生产的过程中,有许多管理工具可以帮助企业识别问题、优化流程和提升绩效。
以下是一些常用的精益生产工具的介绍:1.价值流图:价值流图是一种用于分析和改进价值流的工具。
它是一种以图表方式展示物料和信息在整个生产过程中流动情况的方法。
通过绘制价值流图,企业可以清晰地了解从原材料进入到产品交付的整个过程,并识别出其中的浪费环节和瓶颈。
2.5S法:5S法是一种用于提高工作环境和工作效率的管理工具。
它包括整理、整顿、清理、清扫和素养五个步骤,通过对工作场所进行有序排列、标识化管理和定期清洁,可以提高工作效率、减少浪费和避免事故发生。
3.业务过程再造:业务过程再造是一种重新设计和优化业务流程的方法。
通过彻底改变现有的业务流程,消除冗余环节和不必要的手续,企业可以提高生产效率、缩短交付时间和降低成本。
4.产能平衡:产能平衡是一种用于平衡生产能力和需求的方法。
通过分析和评估企业的产能和订单情况,以及对需求的预测,企业可以制定合理的生产计划,避免因生产能力不足或过剩而导致的浪费或延误。
5.供应链管理:供应链管理是一种用于优化供应链运作的方法。
通过对供应商、生产商和分销商之间的信息流和物流进行协调和优化,企业可以提高物料采购、生产调度和产品交付的效率。
6.KANBAN系统:KANBAN是一种用于控制生产流程的物料和信息管理系统。
它通过设立KANBAN卡片或信号来指导生产和供应链运作,以确保按需生产和物料补给,避免产能浪费和库存积压。
7.故障模式与影响分析(FMEA):FMEA是一种用于分析和预防故障的方法。
通过对产品和生产过程中可能发生的故障模式和其影响进行评估,企业可以提前采取措施来防止故障发生,并最大限度地减少故障对生产和产品质量的影响。
8. Kaizen活动:Kaizen是一种持续改进的管理方法。
精益生产管理的十大工具和实施步骤
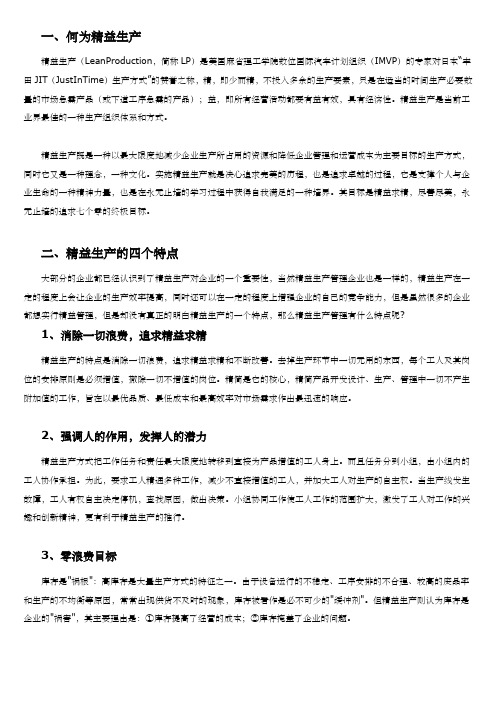
一、何为精益生产精益生产(LeanProduction,简称LP)是美国麻省理工学院数位国际汽车计划组织(IMVP)的专家对日本“丰田JIT(JustInTime)生产方式”的赞誉之称,精,即少而精,不投入多余的生产要素,只是在适当的时间生产必要数量的市场急需产品(或下道工序急需的产品);益,即所有经营活动都要有益有效,具有经济性。
精益生产是当前工业界最佳的一种生产组织体系和方式。
精益生产既是一种以最大限度地减少企业生产所占用的资源和降低企业管理和运营成本为主要目标的生产方式,同时它又是一种理念,一种文化。
实施精益生产就是决心追求完美的历程,也是追求卓越的过程,它是支撑个人与企业生命的一种精神力量,也是在永无止境的学习过程中获得自我满足的一种境界。
其目标是精益求精,尽善尽美,永无止境的追求七个零的终极目标。
二、精益生产的四个特点大部分的企业都已经认识到了精益生产对企业的一个重要性,当然精益生产管理企业也是一样的,精益生产在一定的程度上会让企业的生产效率提高,同时还可以在一定的程度上增强企业的自己的竞争能力,但是虽然很多的企业都想实行精益管理,但是却没有真正的明白精益生产的一个特点,那么精益生产管理有什么特点呢?1、消除一切浪费,追求精益求精精益生产的特点是消除一切浪费,追求精益求精和不断改善。
去掉生产环节中一切无用的东西,每个工人及其岗位的安排原则是必须增值,撤除一切不增值的岗位。
精简是它的核心,精简产品开发设计、生产、管理中一切不产生附加值的工作,旨在以最优品质、最低成本和最高效率对市场需求作出最迅速的响应。
2、强调人的作用,发挥人的潜力精益生产方式把工作任务和责任最大限度地转移到直接为产品增值的工人身上。
而且任务分到小组,由小组内的工人协作承担。
为此,要求工人精通多种工作,减少不直接增值的工人,并加大工人对生产的自主权。
当生产线发生故障,工人有权自主决定停机,查找原因,做出决策。
小组协同工作使工人工作的范围扩大,激发了工人对工作的兴趣和创新精神,更有利于精益生产的推行。
精益生产管理的十大工具和实施步骤

精益生产管理的十大工具和实施步骤一、价值流分析(Value Stream Mapping):价值流分析是了解和改进产品或服务的价值流程的方法。
通过绘制价值流地图,可以清楚地看到从原料到最终交付的整个价值流程,以及其中存在的浪费和瓶颈。
通过分析和改进价值流程,可以实现生产过程的优化。
二、5S整理法:5S整理法是一种是一种工作环境整理和管理方法。
通过整理、整顿、清扫、标准化和维护这五个步骤,可以创造一个整洁、有序、高效的工作环境,提高工作效率和质量。
三、流程改进活动(Kaizen):Kaizen是一种小创新的方法,通过持续改善工作流程,减少或消除浪费,提高效率和质量。
它鼓励员工提出改进建议,并通过小规模试验和迭代改进的方式,不断优化工作流程。
四、单点教导法(One-Piece Flow):单点教导法是一种用来实现流程连续化和缩短生产周期的方法。
通过将生产任务拆分为较小的单元,并且一个接一个地完成,可以减少库存和等待时间,提高生产效率和质量。
五、标准化工作(Standardized Work):标准化工作是一种明确工作内容和作业要求的方法。
通过对工作流程进行详细的规范和记录,包括工作步骤、所需时间和所需材料等,可以确保工作一致性和质量,减少浪费和错误。
六、自动化(Automation):自动化是一种利用机械装置和技术来替代人力的方法。
通过引入自动化设备和技术,可以实现生产过程的标准化和高度自动化,提高生产效率和稳定性。
七、质量管控(Quality Control):质量管控是一种确保产品或服务质量的方法。
通过建立质量控制流程和标准,进行检验和测试,可以及时发现和纠正质量问题,保证产品或服务的一致性和可靠性。
八、产能平衡(Capacity Balancing):产能平衡是一种调整生产线中各个工位和机器的产能,以适应需求变化的方法。
通过平衡各个工位和机器的产能,可以避免瓶颈和浪费,提高整个生产线的效率。
九、持续改进(Continuous Improvement):持续改进是一种通过不断寻找和解决问题,优化工作流程和提高效率的方法。
精益生产的12种工具

精益生产的12种工具引言精益生产是一种重视提高效率、减少浪费的管理方法,通过减少无价值的活动和资源的浪费来提高生产效率。
其目标是通过对价值流程的优化,实现更高质量、更快速的生产,并以客户需求为导向。
为了达到这一目标,精益生产借鉴了许多工具和技术。
本文将介绍精益生产的12种常用工具,以帮助读者理解和应用这种管理方法。
1. 价值流图 (Value Stream Mapping)价值流图是一种绘制价值流程的工具,通过详细描述和可视化企业内部和供应链中的物流、信息流和价值流程,以帮助发现和改进潜在的浪费和瓶颈。
它能够帮助团队识别增值和非增值活动,从而优化生产流程。
2. 5S方法5S方法是一种通过创建整洁、有序的工作环境来提高工作效率的工具。
它包括以下五个步骤:整理(Seiri)、整顿(Seiton)、清扫(Seiso)、标准化(Seiketsu)和维持(Shitsuke)。
通过实施5S方法,团队可以更好地组织工作区域,提高人员工作效率。
3. 连续流 (Continuous Flow)连续流是一种生产模式,旨在通过减少库存和生产周期时间来提高生产效率。
它通过将生产过程分解为一系列连续的步骤,并确保每个步骤都能够连续进行,以实现高效的生产。
4. 快速换模 (Quick Changeover)快速换模是一种减少生产更换模具所需时间的工具。
通过分析和优化更换模具的步骤,团队可以减少停机时间,并提高生产效率。
5. 一次性流程 (One-Piece Flow)一次性流程是一种将生产过程分解为一系列单个产品的工具,以减少库存和减缩生产周期。
通过实现一次性流程,团队可以实现零库存生产,并提高响应速度。
6. 标准化工作 (Standardized Work)标准化工作是一种确保员工按照最佳实践执行工作的工具。
通过定义和记录标准化工作流程,团队可以提高工作质量和一致性,并避免浪费和错误发生。
7. 产线平衡 (Line Balancing)产线平衡是一种通过合理分配工作任务和资源来确保生产线上各工作站之间的负载均衡的工具。
精益生产的十大工具[].doc
![精益生产的十大工具[].doc](https://img.taocdn.com/s3/m/6b5039b10740be1e640e9a01.png)
精益生产的十大工具[1]1精益生产的十大工具1、准时化生产(JIT)准时生产方式是起源于日本丰田汽车公司,其基本思想是“只在需要的时候,按需要的量生产所需的产品”。
这种生产方式的核心是追求一种无库存的生产系统,或使库存达到最小的生产系统。
2、单件流JIT是精益生产的终极目标,它是通过不断消除浪费、降低库存、减少不良、缩短制造周期时间等具体要求来实现的。
单件流是帮助我们达到这一目标的关键手法之一。
3、看板管理(Kanban)看板是可以作为交流厂内生产管理信息的手段。
看板卡片包含相当多的信息并且可以反复使用。
常用的看板有两种:生产看板和运送看板。
4、零库存管理工厂的库存管理是供应链的一环,也是最基本的一环。
就制造业而言,加强库存管理,可缩短并逐步消除原材料、半成品、成品的滞留时间,减少无效作业和等待时间,防止缺货,提高客户对“质量、成本、交期”三大要素的满意度。
5、全面生产维护(TPM)以全员参与的方式,创建设计优良的设备系统,提高现有设备的利用率,实现安全性和高质量,防止故障发生,从而使企业达到降低成本和全面生产效率的提高。
6、运用价值流图来识别浪费生产过程中到处充斥着惊人的浪费现象,价值流图(ValueStreamMapping)是实施精益系统、消除过程浪费的基础与关键点。
7、生产线平衡设计由于流水线布局不合理导致生产工人无谓地移动,从而降低生产效率;由于动作安排不合理、工艺路线不合理,导致工人三番五次地拿起或放下工件。
8、拉系统与补充拉系统所谓拉动生产是以看板管理为手段,采用“取料制”即后道工序根据“市场”需要进行生产,对本工序在制品短缺的量从前道工序取相同的在制品量,从而形成全过程的拉动控制系统,绝不多生产一件产品。
JIT需要以拉动生产为基础,而拉系统操作是精益生产的典型特征。
精益追求的零库存,主要通过拉系统的作业方式实现的。
9、降低设置时间(SetupReduction)为了使停线等待浪费减为最少,缩短设置时间的过程就是逐步去除和减少所有的非增值作业,并将其转变为非停线时间完成的过程。
精益生产管理十大工具

精益生产管理十大工具在现代制造业中,精益生产管理是一种重要的管理思想,旨在提高生产效率、降低成本、提高产品质量。
为了实现这一目标,精益生产管理应用了各种工具和技术。
以下是精益生产管理中最常用的十大工具:价值流映射价值流映射是一种识别和消除生产过程中浪费的工具。
通过绘制价值流图,生产管理者可以清晰地看到价值创造的流程,并找出其中的浪费,进而采取措施进行改善。
小批量生产采用小批量生产可以减少库存、降低生产成本,并提高生产效率。
通过减少生产周期,企业可以更加灵活地响应市场需求。
标准化工作制定和遵守标准化工作流程可以确保生产过程稳定、高效。
员工们在遵循标准操作流程的情况下工作,有助于减少产生的错误和浪费。
5S整理法5S整理法是一种工厂管理方法,通过整顿、清扫、清洁、清理、素养的五个步骤,使工作环境整洁有序,提高工作效率。
建议箱建议箱是鼓励员工提出改进建议的工具。
通过员工的参与,可以发现生产过程中存在的问题和改进的机会,从而不断优化生产流程。
好的团队沟通有效的团队沟通是实现精益生产管理的重要前提。
通过团队沟通,可以加强团队协作,促进信息共享,提高生产效率。
周生产会议定期召开周生产会议可以及时跟踪生产进度,识别问题并制定解决方案。
通过会议记录和持续改进,可以提高生产计划的准确性。
一体化生产计划一体化生产计划是整合市场需求、生产能力、物流等因素的生产计划模式。
通过一体化计划,企业可以优化资源配置,提高生产效率。
质量控制质量控制是确保产品质量符合标准的一系列措施。
通过质量控制,可以降低次品率,提高产品质量,增强企业竞争力。
持续改进持续改进是精益生产管理的核心理念。
通过不断地发现问题、分析原因、提出改进建议并实施改进措施,企业可以不断提高生产效率和产品质量。
以上就是精益生产管理中最常用的十大工具。
通过合理应用这些工具,企业可以不断优化生产流程,提高生产效率,降低成本,实现持续增长。
精益生产工具

精益生产工具精益生产是一种管理和生产方法,旨在通过最大化价值、降低浪费和提高效率来改进生产过程。
在精益生产中,有许多工具和技术可以帮助企业实现这些目标。
在本文中,我们将介绍一些常用的精益生产工具,并解释它们如何在实践中应用。
1. 价值流图价值流图是一种流程图,用于表示产品或服务的价值流动路径。
它标识了价值创造和浪费的点,并帮助识别改进的机会。
通过绘制和分析价值流图,企业可以更好地了解生产过程中的瓶颈、延误和浪费,并采取相应的改善措施。
2. 5S5S 是一种组织和管理方法,旨在创造整洁、有序和高效的工作环境。
它包括以下五个步骤:整理(Sort)、整顿(Set in order)、清洁(Shine)、标准化(Standardize)和维护(Sustain)。
通过实施5S,企业可以提高生产环境的可视性、安全性和效率。
3. 单片流单片流是一种生产方法,通过一次只生产一个产品,以最大程度地减少库存和等待时间。
单片流可以避免生产过剩,并提高产品交付的速度和质量。
它需要高度的协调和协作,但可以显著提高生产效率。
4. 精益生产零库存精益生产零库存是一种管理方法,旨在通过减少库存来降低成本和浪费。
它要求企业根据实际需求进行生产,并且只在必要时才从供应链中获取所需的原材料和零部件。
这种方法可以减少库存积压、降低仓储成本,并提高生产效率。
5. 业绩看板业绩看板是一种用于跟踪和可视化生产绩效的工具。
通过在工作区展示指标和数据,业绩看板可以帮助员工了解工作进展、问题和改进机会。
它还可以促进团队沟通和合作,激励员工参与精益生产活动。
6. 持续改进持续改进是精益生产的核心原则之一。
它鼓励企业不断寻求改进的机会,并通过小步骤和小改变来逐渐实现进步。
持续改进可以通过定期的团队会议、员工建议和问题解决活动来实施,以保持精益生产的持久性和稳定性。
总结:精益生产工具是实现精益生产方法的关键要素。
它们可以帮助企业发现并消除生产过程中的浪费和瓶颈,提高效率和质量。
精益生产十大工具
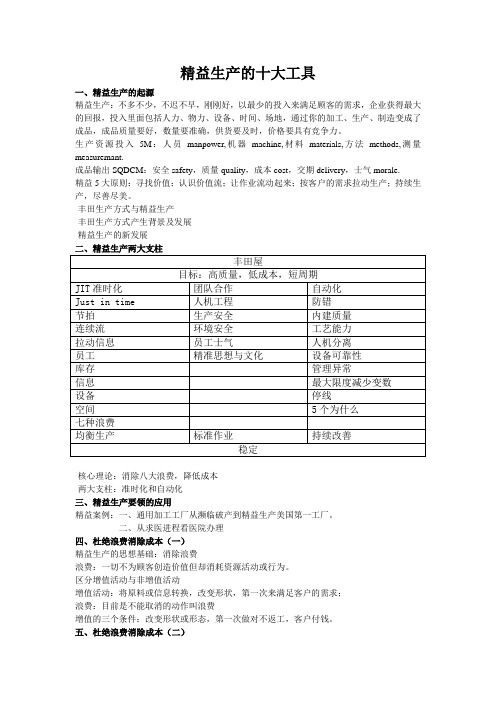
精益生产的十大工具一、精益生产的起源精益生产:不多不少,不迟不早,刚刚好,以最少的投入来满足顾客的需求,企业获得最大的回报,投入里面包括人力、物力、设备、时间、场地,通过你的加工、生产、制造变成了成品,成品质量要好,数量要准确,供货要及时,价格要具有竞争力。
生产资源投入5M:人员manpower,机器machine,材料materials,方法methods,测量measuremant.成品输出SQDCM:安全safety,质量quality,成本cost,交期delivery,士气morale.精益5大原则:寻找价值;认识价值流;让作业流动起来;按客户的需求拉动生产;持续生产,尽善尽美。
-丰田生产方式与精益生产-丰田生产方式产生背景及发展-精益生产的新发展-核心理论:消除八大浪费,降低成本-两大支柱:准时化和自动化三、精益生产要领的应用精益案例:一、通用加工工厂从濒临破产到精益生产美国第一工厂。
二、从求医进程看医院办理四、杜绝浪费消除成本(一)精益生产的思想基础:消除浪费浪费:一切不为顾客创造价值但却消耗资源活动或行为。
区分增值活动与非增值活动增值活动:将原料或信息转换,改变形状,第一次来满足客户的需求;浪费:目前是不能取消的动作叫浪费增值的三个条件:改变形状或形态,第一次做对不返工,客户付钱。
五、杜绝浪费消除成本(二)七种浪费:过量生产浪费,纠正缺陷浪费,多余工序浪费,过渡库存浪费,物料运输浪费,多余动作浪费,等候时间浪费去除过量生产浪费技巧:小批量生产(或单件流),拉动式生产,均衡计划。
去除纠正缺陷浪费技巧:供应商质量保证,防错,减少变差,在线检验去除多余工序浪费技巧:对比现有工艺和顾客需求,产品设计改进,六、杜绝浪费消除成本(三)去除过渡库存浪费技巧:小批量生产,均衡计划,拉动系统,提升设备可利用率和一次合格率,及时处理过期物料,小批量采购,及时生产,缩小仓库面积。
去除物料运输浪费技巧:预设搬运路线/频繁送料,小转运箱/配套,拉动系统,改进工厂布局,单件流。
- 1、下载文档前请自行甄别文档内容的完整性,平台不提供额外的编辑、内容补充、找答案等附加服务。
- 2、"仅部分预览"的文档,不可在线预览部分如存在完整性等问题,可反馈申请退款(可完整预览的文档不适用该条件!)。
- 3、如文档侵犯您的权益,请联系客服反馈,我们会尽快为您处理(人工客服工作时间:9:00-18:30)。
Check, Do, Verify
Check - The previous operators work. Do - Your work. Verify - That you did your work correctly.
Process
Building Quality into the Process 2 ways to perform SPF
精益生产工具(1)
2020/11/30
精益生产工具(1)
Batch
Building Quality into the Process Single Piece Flow
Single Piece Flow
From: The Toyota Production System
Sample Inspect catches Defect too Late • When you Finally Find a Defect
Ref Material Presentation training for explanation on Supermarket definition and use
精益生产工具(1)
Pull Production Methodology & Sequence
Legend
8 Parts
7 6
5
10 9
process of any problem. - an obligation to stop the process until any
problem has been resolved.
Single piece or one piece flow is a means to primarily build Quality into the process. This is achieved by establishing a takt Time, developing std work, and swip. The premise is that an Operator can only work on one piece at a time, and performs a Quick quality check on the CTQs of the process before moving The part to the following process. If a defect is detected, Jidoka Is enacted…the line is stopped, and immediate action is taken To remediate the situation and take countermeasures to prevent reoccurence
1. Takt time 2. Std work
Flow: work (process) that is done in conjunction with or simultaneous to transportation
精益生产工具(1)
One Piece Flow
• The production is organized into a synchronous chain where each person has a balanced amount of work relative to his/her supplier and customer in the chain.
flaw in 100 parts. The next person checks your work and can catch 1/100 so that’s 1/10,000. Then that person Verifies their work and can catch 1/100. That’s 1/1,000,000 errors that can get through.
# Lots of
Total Manual & Travel Time
Standard Work-in-Process
Operator
Man/Travel Time
27 - avg lot = 6
Turns
Takt/Rate Time
100/Day
DPU's
The next process is the customer … never send defects !
Check, Do, Verify
精益生产工具(1)
One Piece Flow
Your customer is the next step in the process. Give to your customer, exactly what they need ( 1 item), exactly when they need it, done perfect every time.
• As one person finishes their element, so do all. Work is then moved down the line synchronously.
• Every person is empowered to stop the production process if a reject is spotted.
Inspect
Process
Inspect
Transport
The next process is the customer … never send defects ! 精益生产工具(1)
Check, Do, Verify
Gets you into Parts Per Million qualityWhen you verify your work, you catch 1
Supplier
Supermarket
Material Information Empty container Full container 1 Sequence / Timing
3
4
Cell or Chaku-Chaku line
2
1
Assembly Line
精益生产工具(1)
JIT Jidoka
Tenants of 1 pcs Flow
• Do Not Make Defects • Do Not Pass Along Defects • Do Not Accept Defect
Quality, Quality, Quality…Defects are the Worst Kind of Waste
Average by total volume
Average by
model
In general, the more fluctuations you in the production flow, the more muda you
end up having. That is because the capacity and capability of a line tends to be set
精益生产工具(1)
Leveled Production
roducts that can be sold
lowering the peaks among the daily production volumes
HEIJUNKA
as much as possible and making the production flow smooth and unflucuating.
Production Line Cell 6
Part Number All Parts
Part Name
All Tubes
Operator
Orbital Weld
Flex
Weld
End Finish
Weld
End Finish
Torch Braze
Mech. Clean
Mech. Clean
Mark
GEMS Global Production System
g ACTION WORKOUT
New / Rev Organization
Tubing
Area
CFM Cell
Page 1 of 1
Supervisor
Fern Bissonnette
Date 2nd Qtr. ‘01
Standard Work Sheet
• You only have one • You know where it occurred • You Can find/Resolve the Root Cause immediately
The next process is the customer … never send defects !
Hydro Test
Outside Cell FPI X-Ray EDM
Weld
End Finish
Scope of Operations
From: Raw material To: Finished Goods
Quality Check
Safety Precaution
Standard Work-in-Process
Check, Do, Verify
Every Customer in a Process has:
- a right to expect perfect material - an obligation to inspect the material before use. - an obligation to inform the previous step in the
Transportation is integrated into the production process via human conveyance e.g., Chaku-Chaku