数控车床对刀仪的用途与原理
数控机床“对刀”原理解析及应用
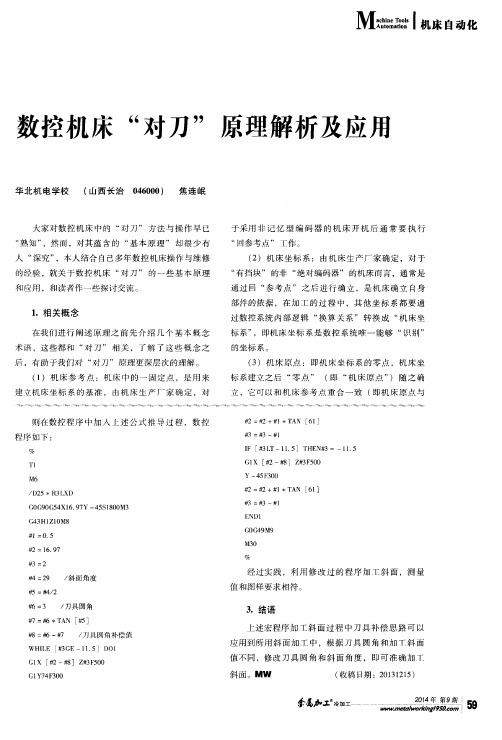
1 .相关概念
在我们 进行 阐述 原 理 之 前 先 介 绍 几 个 基 本 概 念
过数控 系 统 内部 逻 辑 “ 换 算 关 系 ”转 换 成 “ 机 床 坐 标系” ,即机床 坐 标 系 是 数控 系统 唯 一能 够 “ 识别”
的坐标 系 。
术语 ,这些 都 和 “ 对 刀 ” 相 关 ,了解 了这 些 概 念 之 后 ,有 助于 我们 对 “ 对 刀 ”原 理更 深层 次的理 解 。 ( 1 )机 床 参 考 点 :机 床 中 的一 固定 点 ,是 用 来 建立 机床 坐 标 系 的 基 准 , 由机 床 生 产 厂 家 确 定 ,对
% T I
M6
= 彝 2+ 样 I T A N[ 6 1 ] # 3 # 3 一 样 1
I F[ # 3 L T一1 1 . 5 ]T HE N # 3=一1 1 . 5 G1 X[ # 2一# 8 ]Z # 3 F 5 0 0
Y 一4 5 F 3 0 0
/ D 2 5 R 3 T X D
i n e T oo l s 上 vl A a c h
幻
I 机 床 自 动 化
数控机床 “ 对 刀" 原理解析及应用
华 北 机 电学 校 ( 山西 长 治 0 4 6 0 0 0 ) 焦 连 岷
大 家对 数控 机 床 中的 “ 对 刀 ” 方 法 与 操 作 早 已 “ 熟知” ,然 而 ,对 其蕴 含 的 “ 基 本原 理 ” 却 很 少 有 人 “ 深究” ,本人结 合 自己多 年数 控 机床 操作 与 维修 的经 验 ,就关 于 数 控机 床 “ 对 刀 ” 的一 些 基 本 原 理
联系 。
下面 以华 中世 纪 星数 控 车 床 为 例 ,通 过 不 同 的
数控车床对刀的原理及方法

数控车床对刀的原理及方法一、数控车床对刀的原理:对刀是数控加工中的主要操作和重要技能。
在一定条件下,对刀的精度可以决定零件的加工精度。
同时,对刀效事还直接影响数控加工效丰。
仅仅知道对刀方法是不够的。
还要知道数控系统的各种对刀设置方式,。
以及这些方式在加工程序中的调用方法,同时要知道各种对刀方式的优缺点。
使用条件等。
一股来说,数控加工零件的编程和加工是分开进行的。
数控编程员根据零件的设计图纸,速定一个方便编程的工件坐标系,工件坐标系-般与零件的工艺基准或设计基准重合。
在工件坐标系下进行零件加工程序的编制,对刀时,应使指刀位点与对刀点重合,所谓刀位点是指刀具的定位基准点,对于车刀来说,其刀位点是刀失。
对刀的目的是确定对刀点。
在机床坐标系中的绝对坐标值,测量刀具的刀位偏基值。
对刀点找正的准确度直接影响加工精度。
在实际加工工件时。
使用一把刀具一般不能满足工件的加工要求,通常要使用多把刀具进行加工。
在使用多把车刀加工时,在换刀位置不变的情况下,换刀后刀失点的几何位置将出现差异,这就要求不同的刀具在不同的起始位置开始加工时。
都能保证程序正常运行。
为了解决这个问题。
机床数控系統配备了刀具几何位置补能的功能,利用刀其几何位置补偿功能,只要事先把每把刀相对于某一预先选定的基准刀的位置偏差测量出来,输入到数控系统的刀具梦数补正栏指定组号里,在加工程序中利用T指令,即可在刀具轨述中自动补偿刀具位置偏差。
刀具位置值差的利量同样也需通过对刀操作来实现。
生产厂家在制造数控车床,必须建立位置测量,控制、显示的统基准点。
该基准点就是机床坐标系原点,也就是机床机械目零后所处的位置。
操作方法01数控车床对刀是车床加工技术中比较复杂的工艺之一,它的精度将会直接影响到所加工零部件的精度,所以不能马虎。
02数控车床对刀的基本原理就是将零件的坐标系与数控机床的坐标系整合起来,然后依据这个坐标系来确定对刀位置。
03目前数控车床大部分采用的是对刀器主动对刀,对刀器会自动向零件确定一个原点位置,这是十分方便快捷的对刀方法。
数控车床对刀仪的用途及原理(doc 8页)

的,只是按结构的复杂程度和操作的自动化水平分为低、中、高三档型号。
第一种,HPRA (High Precision Removable Arm) 型:这是一种结构较简单、价位低的型号,其特点是对刀仪的臂和基座之间是可分离的,使用时通过插拔机构把对刀仪臂安装至对刀仪基座上(图1)图1:HPRA型对刀仪的系统构成同时电器信号亦连通并进入可工作状态;用完后可将对刀臂从基座中拔出,放到合适的地方以保护精密的对刀臂和对刀传感器部分不受灰尘、碰撞的损坏。
第二种,HPPA (High Precision Pulldown Arm) 型:这是一种较实用、中等价位的型号。
其特点是对刀仪的臂和基座之间是可旋转联接、一体化的。
使用时由操作者将对刀仪臂从保护套中摆动拉出(图2)图2:HPPA型对刀仪的系统构成不用时由操作者作把对刀仪臂再摆动推回保护套中。
这一种对刀仪与上一种型号相比的优点是不必把对刀仪臂频繁地插上、拔出,避免了频繁插拔产生的磨损对对刀精度的影响及电信号传递的可靠性。
因对刀仪摆回后传感器部分进入到保护套中,也不必担心其在工作过程中受到损坏。
第三种,HPMA (High Precision Motorised Arm) 型:这是雷尼绍公司该系列产品中的高档型。
其特点是对刀仪的臂和基座之间是通过扭矩电机来实现对刀臂的摆出和摆回(图3),除提高了自动化程度外,更重要的是可把对刀臂的摆出、摆回通过M代码编制到加工程序中,在加工循环过程中即可方便地实现刀具磨损值的自动测量、补偿和刀具破损的监测。
图3:HPMA型对刀仪的系统构成2、对刀仪都能干哪些工作?(1)、可以快速、高效、精确地在±X、±Z及Y轴五个方向上进行刀具偏置值的测量和补偿,有效消除采用人工对刀易产生的对刀误差和效率低下的问题。
因为不管是采用何种切削刀具(外圆、端面、螺纹、切槽、镗孔还是车削中心上的铣、钻削动力刀具)进行工件型面车削或铣削时,所有参与切削刀具的刀尖点或刀具轴心线,都必须通过调整或补偿使其精确地位于工件坐标系的同一理论点或轴心线上。
数控车床对刀的原理与方法

数控车床对刀的原理与方法数控车床的刀具对刀是确保机床工作精度的关键步骤之一、对刀准确度影响着工件的加工精度和质量。
数控车床的对刀一般采用刀具测量、感应式对刀、比较式对刀等方式。
下面将介绍数控车床对刀的原理和方法。
1.刀具测量:数控车床通常提供一个专门的测量装置,用来测量刀具的长度和半径。
通过刀具测量装置的读数,可以计算出刀具的几何参数,以便在数控系统中设置正确的刀具补偿值。
2.感应式对刀:数控车床使用感应式传感器,通过与刀具接触或靠近刀具来感应刀具的位置信息。
传感器可以测量到刀具的长度和半径,并将这些信息传递给数控系统。
3.比较式对刀:比较式对刀是通过测量工件上已加工的特征来确定刀具的位置。
例如,在数控车床上面加工一个规定尺寸的槽后,可以使用传感器测量槽的尺寸,然后根据预定的槽尺寸,调整刀具的位置。
根据数控车床对刀的原理,可以采用以下方法进行对刀:1.感应式对刀:数控车床上通常有一个专用的感应式对刀装置。
在对刀过程中,需要选取一把已知长度的刀具,并使用感应式传感器测量其长度。
将测量到的刀具长度输入数控系统,系统会自动计算并设置刀具长度补偿值。
然后,将正确长度的刀具安装到车刀刀架上,依次对各个刀具进行对刀。
2.刀具测量:刀具测量是比较常见的对刀方式。
使用专用的刀具测量设备可以测量刀具的长度和半径。
在对刀过程中,首先选取一把已知长度和半径的刀具,将其放入测量设备中测量。
然后,将测量到的数值输入数控系统,系统会自动计算出刀具的补偿值。
最后,将已校准好的刀具安装到车刀刀架上。
3.比较式对刀:在比较式对刀中,首先需要加工一个已知尺寸的特征,例如一条槽或一组孔。
然后,使用专用的测量仪器测量加工后的特征尺寸。
将测量到的尺寸和预定的尺寸进行比较,计算出相应的补偿值。
最后,根据计算结果调整刀具的位置。
除了上述方法外,还可以使用图形化的数控系统来辅助进行对刀。
通过在数控系统中显示工件轮廓的模拟图像,可以直观地观察刀具的位置与工件轮廓之间的关系,从而调整刀具的位置。
数控车床对刀仪的用途及原理

数控车床对刀仪的用途及原理
数控车床对刀仪是一款智能化的仪器设备,用于协助数控车床进行刀具的刀具长度和半径补偿校准,以保证机床精度和生产质量。
数控车床对刀仪的使用可以使机床开机调试更加方便快捷,并减少刀具加工过程中出现的误差,提高加工精度和效率。
数控车床对刀仪的原理是利用光电传感器捕捉机械臂差动运动时光柱划过光电头产生的信号,通过转换电路,将信号转化成电脉冲,并经由计算机处理,最终得出刀具的相对位置和偏差。
通过对刀具的长度、半径进行补偿校准,实现机床切削精度的保证。
下面对数控车床对刀仪的用途和功能进一步阐述:
1. 刀具长度校准功能:在机床加工过程中,由于刀具磨损、安装、更换等原因,刀具长度会发生变化,而数控车床对刀仪可以准确测量刀具的长度并补偿校准,确保加工精度和生产质量。
2. 刀具半径校准功能:刀具的半径也会随着使用而产生变化,如果不进行及时的补偿校准就会导致工件的尺寸和形状偏差,甚至影响到加工质量。
数控车床对刀仪可以快速测量刀具半径,进行调整和校准。
3. 刀具补偿计算:在数控加工中,刀具补偿是制造精度
的关键之一,数控车床对刀仪可以通过对刀具长度和半径的测量,计算出补偿量,以提高加工精度。
4. 制造过程中可追溯性的记录:数控车床对刀仪不仅能
够进行刀具长度和半径的检测和补偿,还能够记录下该过程的参数和数据,进行存档,以便之后进行质量追溯。
综上所述,数控车床对刀仪是一款非常重要的数控加工辅助设备,可通过快速测量刀具长度和半径进行刀具的自动补偿,从而提高加工精度,降低生产成本,达到优化生产效益的目的。
数控车床对刀的原理及方法

数控车床对刀的原理及方法数控车床对刀是指在进行数控加工前,通过调整工具与工件之间的相对位置,使其达到最佳的加工状态,从而确保加工精度和质量。
在进行数控车床对刀时,需要掌握一定的原理和方法。
一、数控车床对刀的原理:数控车床对刀是以工具为基准,通过调整工具与工件之间的相对位置,使其达到预定的加工要求。
数控车床对刀的原理包括工具长度补偿和半径补偿。
工具长度补偿:数控车床对刀时,要考虑工具长度的影响。
在机床的编程中,以工件参考点统一参考工具长度,通过编程输入工具长度补偿值,使操作者无需考虑具体工具长度,直接参照工件参考点与加工长度编程。
半径补偿:数控车床对刀时,还要考虑工具半径的影响。
在机床的编程中,通过编程输入刀具半径补偿值,使操作者无需考虑具体工具半径,直接参照工件轮廓绘制加工轮廓。
二、数控车床对刀的方法:1. 机械对刀法:数控车床对刀时,一般先采用机械对刀法进行初步调整。
具体步骤如下:(1) 选择合适的切削工具,将其装夹到主轴上;(2) 将工件装夹在工作台上,固定好;(3) 调整工具的位置,使其与工件接触;(4) 缓慢移动工具,观察工具与工件的接触情况;(5) 调整对刀量,使工具的刀尖与工件表面轻微接触;(6) 用毛刷或布将切屑清除干净;(7) 检查工具与工件的接触情况,如需调整,继续进行机械对刀。
2. 触发器对刀法:在数控车床上,一般配备有触发器对刀装置。
该装置可以根据工具与工件的相对位置变化,给出相应的触发信号。
具体步骤如下:(1) 在数控系统中,选择相应的对刀程序和参数;(2) 将工具装夹到主轴上;(3) 将工件装夹在工作台上,固定好;(4) 运行对刀程序,使切削工具逐渐接近工件;(5) 当工具与工件发生接触时,触发器将给出触发信号,停止继续靠近;(6) 根据触发信号调整工具位置,以使其与工件的接触减小到最小值;(7) 检查工具与工件的接触情况,如果需要调整,可再次进行触发器对刀。
3. 光电对刀法:光电对刀法是一种非接触式的对刀方法,通过使用光电开关检测刀具的位置与工件的位置关系,以确定最佳的对刀位置。
数控机床对刀的原理分析以及常用对刀方法

数控机床对刀的原理分析以及常用对刀方法进行数控加工时,数控程序所走的路径均是主轴上刀具的刀尖的运动轨迹。
刀具刀位点的运动轨迹自始至终需要在机床坐标系下进行精确控制,这是因为机床坐标系是机床唯一的基准。
编程人员在进行程序编制时不可能知道各种规格刀具的具体尺寸,为了简化编程,这就需要在进行程序编制时采用统一的基准,然后在使用刀具进行加工时,将刀具准确的长度和半径尺寸相对于该基准进行相应的偏置,从而得到刀具刀尖的准确位置。
所以对刀的目的就是确定刀具长度和半径值,从而在加工时确定刀尖在工件坐标系中的准确位置。
对刀仪演示视频(时长1分10秒,建议wifi下观看)一、对刀的原理和对刀中出现的问题1、刀位点刀位点是刀具上的一个基准点,刀位点相对运动的轨迹即加工路线,也称编程轨迹。
2、对刀和对刀点对刀是指操作员在启动数控程序之前,通过一定的测量手段,使刀位点与对刀点重合。
可以用对刀仪对刀,其操作比较简单,测量数据也比较准确。
还可以在数控机床上定位好夹具和安装好零件之后,使用量块、塞尺、千分表等,利用数控机床上的坐标对刀。
对于操作者来说,确定对刀点将是非常重要的,会直接影响零件的加工精度和程序控制的准确性。
在批生产过程中,更要考虑到对刀点的重复精度,操作者有必要加深对数控设备的了解,掌握更多的对刀技巧。
(1)对刀点的选择原则在机床上容易找正,在加工中便于检查,编程时便于计算,而且对刀误差小。
对刀点可以选择零件上的某个点(如零件的定位孔中心),也可以选择零件外的某一点(如夹具或机床上的某一点),但必须与零件的定位基准有一定的坐标关系。
提高对刀的准确性和精度,即便零件要求精度不高或者程序要求不严格,所选对刀部位的加工精度也应高于其他位置的加工精度。
选择接触面大、容易监测、加工过程稳定的部位作为对刀点。
对刀点尽可能与设计基准或工艺基准统一,避免由于尺寸换算导致对刀精度甚至加工精度降低,增加数控程序或零件数控加工的难度。
关于对刀仪的使用
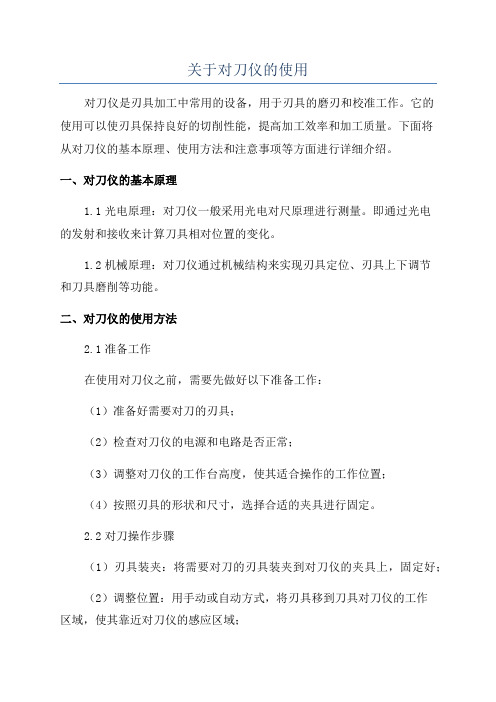
关于对刀仪的使用对刀仪是刃具加工中常用的设备,用于刃具的磨刃和校准工作。
它的使用可以使刃具保持良好的切削性能,提高加工效率和加工质量。
下面将从对刀仪的基本原理、使用方法和注意事项等方面进行详细介绍。
一、对刀仪的基本原理1.1光电原理:对刀仪一般采用光电对尺原理进行测量。
即通过光电的发射和接收来计算刀具相对位置的变化。
1.2机械原理:对刀仪通过机械结构来实现刃具定位、刃具上下调节和刀具磨削等功能。
二、对刀仪的使用方法2.1准备工作在使用对刀仪之前,需要先做好以下准备工作:(1)准备好需要对刀的刃具;(2)检查对刀仪的电源和电路是否正常;(3)调整对刀仪的工作台高度,使其适合操作的工作位置;(4)按照刃具的形状和尺寸,选择合适的夹具进行固定。
2.2对刀操作步骤(1)刃具装夹:将需要对刀的刃具装夹到对刀仪的夹具上,固定好;(2)调整位置:用手动或自动方式,将刃具移到刀具对刀仪的工作区域,使其靠近对刀仪的感应区域;(3)校准刃具:触发对刀仪开始工作,刃具会自动校准至最佳位置,并进行刀具磨削;(4)检查刃具:磨刃完成后,需要检查刃具刀口的状态是否符合要求,刀刃是否锋利;(5)收尾工作:将刃具从夹具上取下,进行清理和保养。
三、对刀仪的注意事项3.1安全操作:对刀仪是一种高速旋转的设备,所以在使用时要格外注意安全,不要将手指等物体靠近其中的运动部件。
3.2选对夹具:夹具不仅要保持稳定,而且还要适合刃具的形状和尺寸,以免在固定过程中对刃具造成损伤。
3.3定期校准:对刀仪的精度会随着使用时间的增长而下降,所以需要定期进行校准,以保证刃具加工的精度和质量。
3.4注意磨损:刃具在使用过程中会不可避免地产生磨损,尤其是刃具的切削部分。
所以,在使用对刀仪之前要对刃具进行必要的修整和磨削工作,以延长其使用寿命。
3.5增加润滑:在对刀仪的工作过程中,刃具和夹具之间的摩擦会产生热量,如果没有做好润滑工作,可能会导致刃具和夹具的损坏。
数控车床的对刀方法
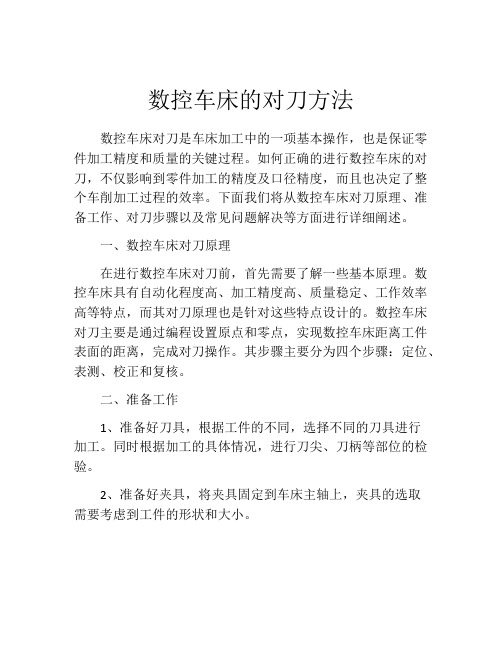
数控车床的对刀方法数控车床对刀是车床加工中的一项基本操作,也是保证零件加工精度和质量的关键过程。
如何正确的进行数控车床的对刀,不仅影响到零件加工的精度及口径精度,而且也决定了整个车削加工过程的效率。
下面我们将从数控车床对刀原理、准备工作、对刀步骤以及常见问题解决等方面进行详细阐述。
一、数控车床对刀原理在进行数控车床对刀前,首先需要了解一些基本原理。
数控车床具有自动化程度高、加工精度高、质量稳定、工作效率高等特点,而其对刀原理也是针对这些特点设计的。
数控车床对刀主要是通过编程设置原点和零点,实现数控车床距离工件表面的距离,完成对刀操作。
其步骤主要分为四个步骤:定位、表测、校正和复核。
二、准备工作1、准备好刀具,根据工件的不同,选择不同的刀具进行加工。
同时根据加工的具体情况,进行刀尖、刀柄等部位的检验。
2、准备好夹具,将夹具固定到车床主轴上,夹具的选取需要考虑到工件的形状和大小。
3、安装好测头,并对其进行校准。
测头的精度直接影响到加工精度,所以在安装测头之前,一定要检查好测头的精度和准确程度,确保其可靠性。
4、指定好原点及零点,原点具有特殊的意义,指的是机床的固定点,所有的测量都是以这个点为基础,而零点则是指刀具离工件表面的距离,即数控车床进行加工时,刀具和工件距离的最小值。
三、对刀步骤1、定位:将夹具握紧工件,确定工件的位置。
这一步是整个对刀过程中十分关键的一步,需要运用专业工具进行定位。
定位具体方法根据工件形状的不同而有所不同。
2、表测:按照正常的夹法夹紧刀具,车床主轴旋转。
将手摇车床主轴进给轮旋转到零位,然后将测头放置到工件表面上,将表头调至位于车床主轴的刀尖、刀柄之中。
这一步是对加工的精度评估,通过测头测量,求出实际加工距离与预设距离之间的距离差值(误差),用于进行下一步的校准。
3、校正:通过调整测头,调整刀尖的位置,使其与实际加工距离相等。
具体方法为:根据表测数据,通过对刀偏差进行计算,并将测量值进行调节,使零点与对刀偏差精确重合。
数控机床对刀仪的使用说明
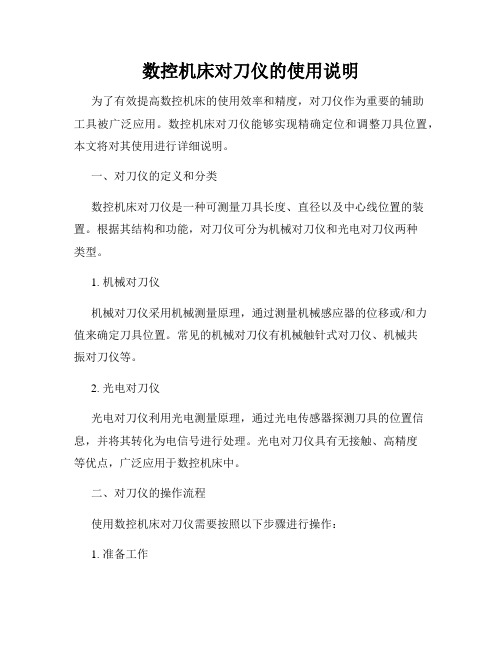
数控机床对刀仪的使用说明为了有效提高数控机床的使用效率和精度,对刀仪作为重要的辅助工具被广泛应用。
数控机床对刀仪能够实现精确定位和调整刀具位置,本文将对其使用进行详细说明。
一、对刀仪的定义和分类数控机床对刀仪是一种可测量刀具长度、直径以及中心线位置的装置。
根据其结构和功能,对刀仪可分为机械对刀仪和光电对刀仪两种类型。
1. 机械对刀仪机械对刀仪采用机械测量原理,通过测量机械感应器的位移或/和力值来确定刀具位置。
常见的机械对刀仪有机械触针式对刀仪、机械共振对刀仪等。
2. 光电对刀仪光电对刀仪利用光电测量原理,通过光电传感器探测刀具的位置信息,并将其转化为电信号进行处理。
光电对刀仪具有无接触、高精度等优点,广泛应用于数控机床中。
二、对刀仪的操作流程使用数控机床对刀仪需要按照以下步骤进行操作:1. 准备工作首先,确保对刀仪与数控机床正确连接,并确认连接稳固可靠。
其次,检查刀具是否安装正确,刀具应牢固固定在刀柄上,无松动现象。
2. 设置测量模式根据实际需要,选择对刀仪的测量模式。
常见的测量模式有刀长度测量、刀具半径测量和刀具边角测量等,根据不同的模式选择相应功能。
3. 启动机床和对刀仪打开数控机床和对刀仪的电源开关,并等待系统启动完成。
确保数控机床和对刀仪的通信正常。
4. 定位刀具和刀柄使用机械手或手动操作,将刀具和刀柄准确安装到数控机床的刀库中。
确保刀具和刀柄的编号与程序中一致。
5. 进行对刀操作按照数控机床的操作界面提示,选择对刀功能,并按要求操作。
对刀过程中,对刀仪将会自动测量刀具的位置信息,并将测量结果传输给数控机床进行相应调整。
6. 验证刀具位置对刀完成后,使用测量工具(如游标卡尺或三坐标测量机)验证刀具位置的准确性。
如果发现误差较大,应重新进行对刀操作。
三、对刀仪的注意事项在使用数控机床对刀仪时,需要注意以下事项,以确保操作的准确性和安全性:1. 定期校准对刀仪作为精密测量设备,需要定期进行校准,以保证测量的准确性。
数控铣床的对刀原理及对刀方法

数控铣床的对刀原理及对刀方法数控铣床是一种由数控设备控制的铣床,它通过控制系统精确地控制刀具在工件上的运动,从而实现对工件的加工。
对刀是数控铣床加工程序中的首要步骤,它决定了刀具与工件之间的相对位置,直接影响到加工结果的准确性和质量。
对刀原理:数控铣床的对刀原理主要是通过探针测量工件和刀具的相对位置,以确定刀具与工件表面之间的距离,从而确定刀具的切削深度和位置。
常用的对刀原理有一次性对刀和分次对刀两种。
一次性对刀原理:一次性对刀是在数控铣床上使用专用的对刀仪器进行的,它包括一个探针和一个数显表。
首先用手动操作将刀具移动到离工件表面一定距离的位置,并将数显表的指针归零。
然后将探针轻轻触碰工件表面,此时数显表的读数就是刀具与工件的相对位置。
根据需要调整刀具的位置,使得数显表的读数达到所需的数值,完成对刀。
分次对刀原理:分次对刀是在定位基准上进行的,基准有工件表面、加工基准台等。
首先将刀具装夹到铣床刀柄上,并用手动操作将刀具轻轻接触工件或基准台的表面。
然后通过微调螺杆来调整刀具的位置,直到刀具与工件或基准台之间的距离满足要求,完成对刀。
对刀方法:数控铣床的对刀方法根据具体情况有多种选择,下面介绍一些常用的方法。
1.轴线对刀法:将铣刀轴线与工件轴线重合,然后调整刀具的加工深度和侧向位置,使得刀具能够正常切削工件。
2.检测刀具圆心位置:将刀具移动到工件上方,通过探针检测刀具圆心位置。
然后根据检测结果调整刀具的位置,使得刀具与工件圆心的距离满足要求。
3.检测刀具的倾角:将刀具沿着X、Y轴移动到工件上方,并通过探针检测刀具的倾角。
然后根据检测结果调整刀具的位置,使得刀具与工件的倾角满足要求。
自动对刀仪工作原理

自动对刀仪工作原理自动对刀仪是一种用于快速精确地对准机床工具的装备。
自动对刀仪通常被使用在CNC车床、铣床和磨床等机床中。
在实际应用中,自动对刀仪的工作方式相对简单,主要依靠光电传感器进行测量和反馈。
以下将对自动对刀仪的工作原理进行详细介绍,以帮助读者深入了解这一机械设备。
一、自动对刀仪的组成部分为了更好地理解自动对刀仪的工作原理,先对其组成部分进行简单介绍。
1.测量头:测量头是自动对刀仪的核心部件,用于与工具或工件接触,并测量该位置。
在接触过程中,测量头会根据工作原理进行操作,识别出工具或工件的位置。
2.传感器:传感器是自动对刀仪的另一核心部件,用于检测和传输测量头测量到的数据。
一般而言,自动对刀仪会配备至少一个光电传感器。
3.控制器:控制器是自动对刀仪的“大脑”。
传感器采集的测量数据会被传输到控制器,控制器则对数据进行分析处理,并根据结果发出对测量头的指令。
4.指示器:指示器是自动对刀仪的辅助部件之一,用于显示测量结果。
一般而言,指示器会显示出两个数值,分别代表当前与工具或工件的距离和生成工具长度的位置。
二、自动对刀仪的工作原理自动对刀仪的工作原理可以大致分为以下几个步骤:1.工具首先要进行夹持,然后人员需要在自动对刀仪上输入所需信息,如测量方式、工具类型、工作台坐标等。
2.运行自动对刀仪程序,此时控制器将采集到的传感器信号进行分析,并根据分析结果进行调整。
在此过程中,控制器会自动调整测量头的位置,使其更贴近工具或工件。
3.测量完成后,自动对刀仪会通过指示器显示测量结果。
这些结果可以是从工具末端测量到工作台的距离,或是工具长度的实际位置。
如果结果需要校准,自动对刀仪将自动进行调整,直到准确为止。
4.一旦校准完毕,自动对刀仪就会以相同的方式使用,将测量值传递给CNC控制器,用于生成程序。
三、自动对刀仪的优点和局限性自动对刀仪的优点显而易见,最大优点便是可以快速精确地定位工具或工件。
因此,自动对刀仪可以显著减少设置时间,并提高加工效率和几何精度。
对刀仪的工作原理、操作规程及维护维修注意事项

对刀仪工作原理、操作规程及维护维修注意事项在工件的加工过程中,工件装卸、刀具调整等辅助时间,占加工周期中相当大的比例,其中刀具的调整既费时费力,又不易准确,最后还需要试切。
统计资料表明,一个工件的加工,纯机动时间大约只占总时间的55%,装夹和对刀等辅助时间占45%。
因此,对刀仪便显示出极大的优越性。
目录工作原理对刀精度操作规程对刀仪工作原理对刀仪的核心部件是由一个高精度的开关(测头),一个高硬度、高耐磨的硬质合金四面体(对刀探针)和一个信号传输接口器组成(其他件略)。
四面体探针是用于与刀具进行接触,并通过安装在其下的挠性支撑杆,把力传至高精度开关;开关所发出的通、断信号,通过信号传输接口器,传输到数控系统中进行刀具方向识别、运算、补偿、存取等。
数控机床的工作原理决定,当机床返回各自运动轴的机械参考点后,建立起来的是机床坐标系。
该参考点一旦建立,相对机床零点而言,在机床坐标系各轴上的各个运动方向就有了数值上的实际意义。
对于安装了对刀仪的机床,对刀仪传感器距机床坐标系零点的各方向实际坐标值是一个固定值,需要通过参数设定的方法来精确确定,才能满足使用,否则数控系统将无法在机床坐标系和对刀仪固定坐标之间进行相互位置的数据换算。
当机床建立了“机床坐标系”和“对刀仪固定坐标”后(不同规格的对刀仪应设置不同的固定坐标值),对刀仪的工作原理如下:1.机床各直线运动轴返回各自的机械参考点之后,机床坐标系和对刀仪固定坐标之间的相对位置关系就建立起了具体的数值。
2.不论是使用自动编程控制,还是手动控制方式操作对刀仪,当移动刀具沿所选定的某个轴,使刀尖(或动力回转刀具的外径)靠向且触动对刀仪上四面探针的对应平面,并通过挠性支撑杆摆动触发了高精度开关传感器后,开关会立即通知系统锁定该进给轴的3)、将X轴量表测头调至接触测试棒,使量表指针向顺时针方向接触第一个0的位置;4)、将X轴显示数据设定为测试棒半径之数字,即完成归“0”;2、确定测试棒的归“0”的动作:1)、将刀具装入主轴,并锁紧螺帽固定之;2)、旋转主轴,使刀具之刀尖接触到X轴测头,让量表指针转至第一个“0”的位置;3)、在显示器上设定刀具所需之尺寸,X轴输入刀具半径值,此时即完成刀具预调值;4)、取下刀具时,请以逆时针方向松脱主固定螺帽;对刀仪(M70/M700)操作使用注意事项及维护维修事项立式加工中心机采用美德龙系列(T24E/F)对刀仪,对刀重复精度0.003mm以内。
数控机床对刀的原理和方法之我见
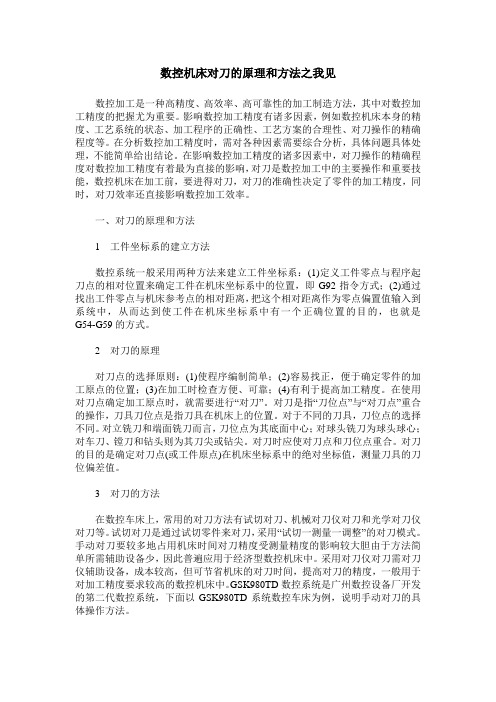
数控机床对刀的原理和方法之我见数控加工是一种高精度、高效率、高可靠性的加工制造方法,其中对数控加工精度的把握尤为重要。
影响数控加工精度有诸多因素,例如数控机床本身的精度、工艺系统的状态、加工程序的正确性、工艺方案的合理性、对刀操作的精确程度等。
在分析数控加工精度时,需对各种因素需要综合分析,具体问题具体处理,不能简单给出结论。
在影响数控加工精度的诸多因素中,对刀操作的精确程度对数控加工精度有着最为直接的影响,对刀是数控加工中的主要操作和重要技能,数控机床在加工前,要进得对刀,对刀的准确性决定了零件的加工精度,同时,对刀效率还直接影响数控加工效率。
一、对刀的原理和方法1工件坐标系的建立方法数控系统一般采用两种方法来建立工件坐标系:(1)定义工件零点与程序起刀点的相对位置来确定工件在机床坐标系中的位置,即G92指令方式;(2)通过找出工件零点与机床参考点的相对距离,把这个相对距离作为零点偏置值输入到系统中,从而达到使工件在机床坐标系中有一个正确位置的目的,也就是G54-G59的方式。
2对刀的原理对刀点的选择原则:(1)使程序编制简单;(2)容易找正,便于确定零件的加工原点的位置;(3)在加工时检查方便、可靠;(4)有利于提高加工精度。
在使用对刀点确定加工原点时,就需要进行“对刀”。
对刀是指“刀位点”与“对刀点”重合的操作,刀具刀位点是指刀具在机床上的位置。
对于不同的刀具,刀位点的选择不同。
对立铣刀和端面铣刀而言,刀位点为其底面中心;对球头铣刀为球头球心;对车刀、镗刀和钻头则为其刀尖或钻尖。
对刀时应使对刀点和刀位点重合。
对刀的目的是确定对刀点(或工件原点)在机床坐标系中的绝对坐标值,测量刀具的刀位偏差值。
3对刀的方法在数控车床上,常用的对刀方法有试切对刀、机械对刀仪对刀和光学对刀仪对刀等。
试切对刀是通过试切零件来对刀,采用“试切一测量一调整”的对刀模式。
手动对刀要较多地占用机床时间对刀精度受测量精度的影响较大胆由于方法简单所需辅助设备少,因此普遍应用于经济型数控机床中。
对刀仪使用
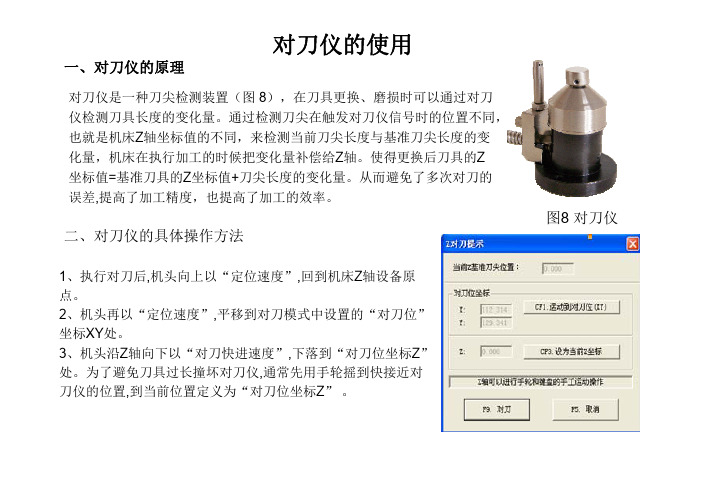
对刀仪的使用一、对刀仪的原理对刀仪是一种刀尖检测装置(图8),在刀具更换、磨损时可以通过对刀仪检测刀具长度的变化量。
通过检测刀尖在触发对刀仪信号时的位置不同,也就是机床Z轴坐标值的不同,来检测当前刀尖长度与基准刀尖长度的变轴坐标值的不同来检测当前刀尖长度与基准刀尖长度的变化量,机床在执行加工的时候把变化量补偿给Z轴。
使得更换后刀具的Z坐标值=基准刀具的Z坐标值+刀尖长度的变化量。
从而避免了多次对刀的误差,提高了加工精度,也提高了加工的效率。
提高了加精度也提高了加的效率图8 对刀仪二、对刀仪的具体操作方法1、执行对刀后,机头向上以“定位速度”,回到机床Z轴设备原点。
2、机头再以“定位速度”,平移到对刀模式中设置的“对刀位”坐标XY处。
3、机头沿Z轴向下以“对刀快进速度”,下落到“对刀位坐标Z”处。
为了避免刀具过长撞坏对刀仪,通常先用手轮摇到快接近对刀仪的位置,到当前位置定义为“对刀位坐标Z”。
1、定义工件z轴坐标(即工件的零平面)2、按A(对刀快捷键)——CF1(运动到对刀位)3、摇手轮Z轴运动到对刀仪表面(不要碰触到对刀仪)按CF1设置当前坐标(即对摇手轮刀仪慢下距离的位置)4、按F9(对刀)5、对刀完成后按F1(定义对刀基准)6、试切加工——加工直至第一把刀具加工结束7、换上第二把刀具按A(对刀快捷键)——CF1(运动到对刀位)8、摇手轮Z轴运动到对刀仪表面(不要碰触到对刀仪)按CF1设置当前坐标(即对刀仪慢下距离的位置)9F9、按(对刀)10、对刀完成后按F5(修正刀具长度补偿)(每把刀具装的长度不同,需要通过对刀仪计算两把刀具的高度差使第二把刀具刀尖也在零平面上)11、换上第三把刀,步骤重复7、8、9、10 以此类推换上第三把刀步骤重复104、机头以系统设置的慢下速度向下移动,在“对刀慢下距离”范围内寻找对刀仪信号,若在该范围内没有接收到对刀仪信号,则系统认为对刀失败。
当接收到对刀仪信号后,机头向上以“定位速度”,回到机床Z轴设备原点,同时弹出“对刀结束”对话框,供用户选择。
数控车床机内对刀仪的常见功能和优势

数控车床机内对刀仪的常见功能和优势在应用数控车床进行生产制造产品零件的工艺过程中,影响零件质量的因素很多,如数控机床精度、工件材料、工件热处理、加工工艺、冷却液、刀具等等诸多因素。
其中,刀具参数的准确设置,一直以来却很少被大家所关心和重视,今天来介绍一下数控车床专用对刀仪常见功能优势。
1.刀具长度/直径的自动测量和参数更新:刀具在转动时进行长度/直径的动态测量,测量参数包含了车床主轴的端向跳动/径向跳动误差,从而得到了刀具在高速加工时的“动态”的偏置值;同时,可以随时进行刀具参数的自动测量,从而极大消除了由于机床热变形引起的刀具参数的“改变”;测量结果自动更新到相应刀具的参数表中,完全避免人为对刀和参数输入带来的潜在风险。
2.刀具磨损/破损的自动监控:在实际生产过程中,当刀具磨损或者破损(折断)时,操作者很难及时发现并纠正(尤其是直径较小的钻头类刀具),从而造成更多后续刀具的损失甚至工件的报废。
使用机内对刀仪可以在刀具加工完毕后放回刀库前,自动对刀具长度进行一次测量,若发生正常磨损时可以自动将磨损数值更新到刀损参数中,若发生超长磨损可以当作刀具破损(折断)从而选择更换新刀进行下一个工件的加工或者自动停机报警提示操作者进行刀具更换。
这样,提高了产品质量并降低刀具损耗或废品率。
3.数控车床热变形的自动补偿:机床进行生产加工时,随着周围环境温度的变化以及工作负荷的变化,机床的热变形随时都在发生进而带动刀具发生变化,其结果就是车间内同一台数控车床在早/中/晚不同时段加工出产品的尺寸精度发生很大的波动。
使用机内对刀仪后,可以在加工前或者加工过程中随时对刀具参数进行自动测量和更新,每次测量都是在当前机床热变形的状态下进行的刀具设置,从而极大的降低了由于机床热变形引入的误差。
4.轮廓的测量和监控:在特殊的加工中,如成型刀,使用机外对刀仪进行刀具轮廓的测量和刀具状态判断是费时而复杂的工作,同时对操作者的对刀技巧也有很高的要求。
数控车床的对刀原理
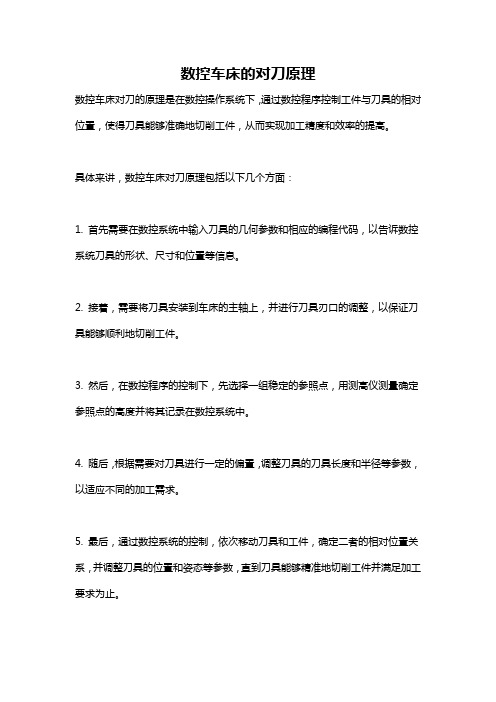
数控车床的对刀原理
数控车床对刀的原理是在数控操作系统下,通过数控程序控制工件与刀具的相对位置,使得刀具能够准确地切削工件,从而实现加工精度和效率的提高。
具体来讲,数控车床对刀原理包括以下几个方面:
1. 首先需要在数控系统中输入刀具的几何参数和相应的编程代码,以告诉数控系统刀具的形状、尺寸和位置等信息。
2. 接着,需要将刀具安装到车床的主轴上,并进行刀具刃口的调整,以保证刀具能够顺利地切削工件。
3. 然后,在数控程序的控制下,先选择一组稳定的参照点,用测高仪测量确定参照点的高度并将其记录在数控系统中。
4. 随后,根据需要对刀具进行一定的偏置,调整刀具的刀具长度和半径等参数,以适应不同的加工需求。
5. 最后,通过数控系统的控制,依次移动刀具和工件,确定二者的相对位置关系,并调整刀具的位置和姿态等参数,直到刀具能够精准地切削工件并满足加工要求为止。
综上所述,数控车床对刀的原理是通过数控程序控制刀具和工件的相对位置,利用各种测量和偏置手段,实现对刀具精度的调整和工件加工的高效性,从而提高数控加工的生产效率和加工质量。
数控车床对刀仪设备工艺原理

数控车床对刀仪设备工艺原理摘要数控车床对刀仪作为一种重要的加工设备,主要用于对刀和调整加工中心的位置。
本文将介绍数控车床对刀仪的工艺原理,包括对刀仪的结构、原理、调整方法等方面。
概述数控车床对刀仪是一种用于对平面和立面的工具进行调整的设备,其主要作用是调整机床切削中心的位置,以保证切削在正确的位置进行。
对刀仪一般由两部分组成,一部分是直线度检查系统,用于检查X、Y方向上的垂直度和平行度,另一部分是圆度检查系统,用于检查Z方向上的圆度。
同时,对刀仪还具有数据存储功能,能够存储多组测量数据,在加工过程中随时进行刀具的调整。
结构数控车床对刀仪的结构较为复杂,主要由控制器、检测头、电子尺、检测棒等组件组成。
其中,控制器主要负责对检测头和电子尺进行控制,收集检测信息并显示出来。
检测头是对刀仪的核心部件,主要用于检测工件的平面度和圆度。
电子尺则用于精确定位检测头,从而获得更为准确的检测数据。
检测棒则用于辅助定位,能够提高对刀的精度。
原理数控车床对刀仪的工作原理是基于非接触式的激光测量原理。
当检测头对准工件时,会发出激光信号,该激光信号将被工件反射回来后被检测头接收到。
通过分析反射信号和原始信号的差异,对刀仪就能够精确的测量工件的尺寸和形状,并根据检测结果调整切削中心的位置。
此外,对刀仪还能够自动进行光斑的自动修正,以提高检测精度。
调整方法数控车床对刀仪的调整方法比较简单,一般可分为以下几个步骤:1.确认工件的切削中心位置;2.将工艺清单中的切削中心位置输入数控车床对刀仪;3.安装检测头,并对准工件;4.开始测量并保存数据;5.根据数据调整工具长度和位置;6.再次检查调整结果是否符合要求。
需要注意的是,在进行调整时,应根据实际情况进行细致的调整。
此外,为了确保对刀仪的使用效果,还需定期对其进行保养和维修。
结论数控车床对刀仪作为一种重要的加工设备,是保证加工品质和效率的关键工具。
其工艺原理主要基于激光测量原理,具有良好的测量精度和自动修正功能。
雷尼绍数控车床对刀仪的用途及设置

雷尼绍数控车床对刀仪的用途及设置雷尼绍数控车床对刀仪是一种用于数控车床上的加工设备。
它可以帮助加工人员在加工过程中快速精准地定位工件和刀具,提高加工效率和加工质量。
本文将详细介绍雷尼绍数控车床对刀仪的用途及设置方法。
一、雷尼绍数控车床对刀仪的用途1.快速定位工件在数控车床加工过程中,加工人员需要将工件准确定位到加工平台上,并将刀具对准工件进行加工。
使用雷尼绍数控车床对刀仪可以使这个过程更加轻松快捷。
只需要将对刀仪放在工件上,通过调整对刀仪的位置和刀具的高度,就可以准确地定位工件和刀具。
2.节省加工时间在传统的加工方式中,加工人员需要通过手动试刀或者使用其他设备进行对刀调整。
这个过程比较费时费力,并且很难达到完美的对刀效果。
而使用雷尼绍数控车床对刀仪可以节省大量的对刀时间,提高加工效率。
3.保证加工质量对刀的准确性对整个加工过程的质量和精度有着非常重要的影响。
使用雷尼绍数控车床对刀仪可以精准地调整刀具位置和高度,保证了加工质量和加工精度。
二、雷尼绍数控车床对刀仪的设置方法1.连接对刀仪首先需要将对刀仪安装到数控车床上,并且与控制系统进行连接。
连接成功后,我们可以开始进行对刀调整。
2.选择对刀方式雷尼绍数控车床对刀仪有两种对刀方式,分别是机械式对刀和光电式对刀。
机械式对刀需要使用刀具和工件进行接触,而光电式对刀则是通过激光进行测量。
根据不同的加工需求选择合适的对刀方式。
3.调整对刀仪位置将对刀仪移动到要加工的工件附近,调整位置使其与工件紧密贴合。
注意不要碰到工件,否则会影响对刀的准确性。
4.调整刀具高度将刀具按照需要插入刀杆,然后将刀杆插入可调高度的杆座中。
使用对刀仪的调节装置,调整刀具的高度使其与工件接触,然后调整到合适的位置。
5.校准参数将调节好的刀具高度输入数控系统中。
然后进行参数校准,检测参数是否正确。
如果参数正确,可以开始进行加工操作。
通过以上步骤,我们可以轻松地完成对刀操作,并且可以保证加工的精度和质量。
广州数控车床对刀原理
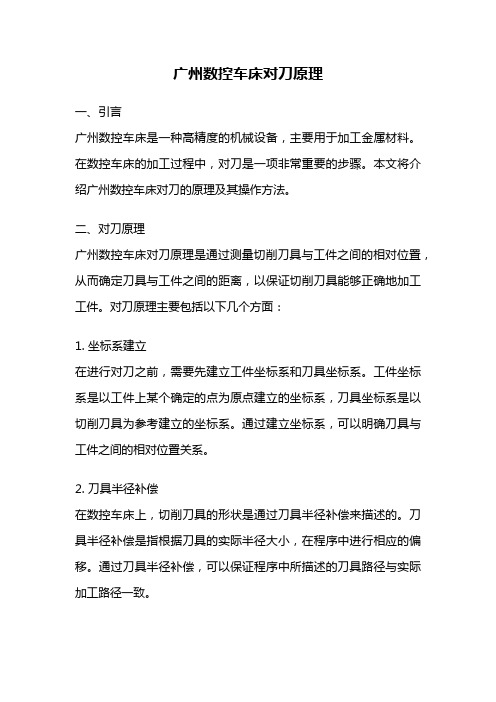
广州数控车床对刀原理一、引言广州数控车床是一种高精度的机械设备,主要用于加工金属材料。
在数控车床的加工过程中,对刀是一项非常重要的步骤。
本文将介绍广州数控车床对刀的原理及其操作方法。
二、对刀原理广州数控车床对刀原理是通过测量切削刀具与工件之间的相对位置,从而确定刀具与工件之间的距离,以保证切削刀具能够正确地加工工件。
对刀原理主要包括以下几个方面:1. 坐标系建立在进行对刀之前,需要先建立工件坐标系和刀具坐标系。
工件坐标系是以工件上某个确定的点为原点建立的坐标系,刀具坐标系是以切削刀具为参考建立的坐标系。
通过建立坐标系,可以明确刀具与工件之间的相对位置关系。
2. 刀具半径补偿在数控车床上,切削刀具的形状是通过刀具半径补偿来描述的。
刀具半径补偿是指根据刀具的实际半径大小,在程序中进行相应的偏移。
通过刀具半径补偿,可以保证程序中所描述的刀具路径与实际加工路径一致。
3. 刀具长度补偿切削刀具的长度也是需要进行补偿的。
在进行对刀时,需要准确测量切削刀具的长度,然后在程序中进行相应的补偿。
通过刀具长度补偿,可以确保刀具与工件之间的距离准确无误。
4. 对刀工具的选择在进行对刀时,需要选择合适的对刀工具。
对刀工具一般包括刀具测量仪、刀具夹具等。
刀具测量仪可以用来测量切削刀具的长度和半径,刀具夹具可以用来固定切削刀具。
三、对刀操作方法广州数控车床对刀的具体操作方法如下:1. 安装刀具测量仪需要将刀具测量仪安装到数控车床上。
刀具测量仪一般固定在车床的主轴上,可以通过测量刀具的长度和半径来进行对刀。
2. 安装刀具将需要进行对刀的切削刀具安装到刀具夹具上,并夹紧刀具夹具。
确保切削刀具的位置准确无误。
3. 校准刀具测量仪打开数控车床的控制系统,选择对刀功能。
通过刀具测量仪的测量功能,测量刀具的长度和半径,并输入到数控车床的控制系统中。
4. 进行对刀根据数控车床的操作界面,选择对刀功能,并按照提示进行操作。
数控车床会自动调整刀具的位置,直到刀具与工件之间的距离准确无误。
- 1、下载文档前请自行甄别文档内容的完整性,平台不提供额外的编辑、内容补充、找答案等附加服务。
- 2、"仅部分预览"的文档,不可在线预览部分如存在完整性等问题,可反馈申请退款(可完整预览的文档不适用该条件!)。
- 3、如文档侵犯您的权益,请联系客服反馈,我们会尽快为您处理(人工客服工作时间:9:00-18:30)。
英国“雷尼绍”(RENISHAW)车床对刀仪的用途及原理济南一机床集团有限公司李军摘要:文中着重介绍了英国“雷尼绍”公司数控车床用对刀仪的种类、用途以及简要的工作原理,同时也简要介绍了在数控车床上采用对刀仪对提高加工精度及加工效率的意义。
关键词:对刀仪种类及用途工作原理作为机械加工业中用量最大的数控车床,近些年来随国内经济的高速发展已迅速得到普及。
今天,一个企业内拥有几十台甚至上百台数控车床早已不是什么稀罕事了。
但众所周知,使用数控车床的目地是提高工件的加工质量和效率。
可是使用过数控车床的人都知道,在一个工件的加工过程中,工件的装卸、刀具的调整等辅助时间占用了加工周期中相当大的比例,其中的刀具调整更是既麻烦、又费力。
统计资料证明,实现一个工件的加工,纯机动时间大约要占总时间的55%,装、夹和对刀等辅助时间却占到45%,这实在不是一个小数。
老话讲磨刀不误砍柴工,但在现代社会中,时间就是金钱,效率就是生命。
要多砍柴就必须向磨刀要效益,对时间进行分秒必争。
那么,在提高对刀效率方面我们还有什么好办法吗?实践证明,通过在数控车床上增设对刀仪装置即是一种向“磨刀”要时间的好方法。
以下,结合英国雷尼绍公司的对刀仪装置,谈谈它在构成、用途及简要工作原理等方面的知识:1、雷尼绍公司有哪几种对刀仪装置?目前在雷尼绍车床对刀仪系列产品中共有三种型号,其对刀的原理是一样的,只是按结构的复杂程度和操作的自动化水平分为低、中、高三档型号。
第一种,HPRA (H igh P recision R emovable A rm) 型:这是一种结构较简单、价位低的型号,其特点是对刀仪的臂和基座之间是可分离的,使用时通过插拔机构把对刀仪臂安装至对刀仪基座上(图1)图1:HPRA型对刀仪的系统构成同时电器信号亦连通并进入可工作状态;用完后可将对刀臂从基座中拔出,放到合适的地方以保护精密的对刀臂和对刀传感器部分不受灰尘、碰撞的损坏。
第二种,HPPA (H igh P recision P ulldown A rm) 型:这是一种较实用、中等价位的型号。
其特点是对刀仪的臂和基座之间是可旋转联接、一体化的。
使用时由操作者将对刀仪臂从保护套中摆动拉出(图2)图2:HPPA型对刀仪的系统构成不用时由操作者作把对刀仪臂再摆动推回保护套中。
这一种对刀仪与上一种型号相比的优点是不必把对刀仪臂频繁地插上、拔出,避免了频繁插拔产生的磨损对对刀精度的影响及电信号传递的可靠性。
因对刀仪摆回后传感器部分进入到保护套中,也不必担心其在工作过程中受到损坏。
第三种,HPMA (H igh P recision M otorised A rm) 型:这是雷尼绍公司该系列产品中的高档型。
其特点是对刀仪的臂和基座之间是通过扭矩电机来实现对刀臂的摆出和摆回(图3),除提高了自动化程度外,更重要的是可把对刀臂的摆出、摆回通过M代码编制到加工程序中,在加工循环过程中即可方便地实现刀具磨损值的自动测量、补偿和刀具破损的监测。
图3:HPMA型对刀仪的系统构成2、对刀仪都能干哪些工作?(1)、可以快速、高效、精确地在±X、±Z及Y轴五个方向上进行刀具偏置值的测量和补偿,有效消除采用人工对刀易产生的对刀误差和效率低下的问题。
因为不管是采用何种切削刀具(外圆、端面、螺纹、切槽、镗孔还是车削中心上的铣、钻削动力刀具)进行工件型面车削或铣削时,所有参与切削刀具的刀尖点或刀具轴心线,都必须通过调整或补偿使其精确地位于工件坐标系的同一理论点或轴心线上。
对动力型回转刀具,除要测量并补偿刀具长度方向上的偏置值外,同时还要测量和补偿刀具直径方向上的偏置值(刀具以轴心线分界的两个半径的偏置值)。
否则机床也无法加工出尺寸正确的工件来。
安装、调整、或更换新刀具后,要使刀架上每把刀具的刀尖点或刀具的轴心线都准确地与机床坐标系零点(对数控车床而言,X轴机床坐标系的零点与主轴中心线重合;Z轴在主轴头前端发蓝的立面上)保持一个精准的固定值是不可能的,这是因刀具安装、调整、磨损后必然会产生的误差造成,或是更换刀具后新刀具与旧刀具位置之间所产生的安装偏差值造成。
所谓刀具偏置值就是指的这种误差值(图4)。
图4:四个坐标方向上的刀具的偏置值在没有安装对刀仪的机床上,每把刀具的偏置值是通过对每把刀具都进行仔细的试切削,然后通过对试切削后的工件尺寸进行测量、计算、补偿(手工对刀)才可完成,肯定费时费力,稍不小心还会报废工件。
当更换刀具后,这项工作还要重新进行。
因而对刀实际上是占用机床辅助时间最长的工作内容之一。
在使用了对刀仪的机床上,因对刀后能够自动设置好刀具对工件坐标系的偏置值,从而自动建立起工件坐标系,在这种情况下加工程序中就无需再用“G50指令”来建立工件坐标系了。
(2)、可以对加工过程中的刀具磨损、破损进行自动监测、补偿和报警。
刀具在切削过程中会产生磨损,当这种磨损值达到一定程度后就应及时补偿,否则会影响工件尺寸的加工稳定性。
在没有安装对刀仪的机床上完成磨损值的补偿是很麻烦的,需要频频的停下机床对工件的尺寸进行手工测量、还要将得到的磨损值人工敲到系统中去修改刀补参数。
而当安装了对刀仪后,解决这个问题就方便简单的多了,特别是机床安装的是HPPA型或HPMA型后则更为方便。
前者,只要根据刀具的磨损规律,干完一定数量的工件后停下机床,用对刀仪再进行一遍对刀的过程即可;后者,只要在程序中人为设定完成多少个加工循环后执行一次自动对刀,既可完成刀具的偏置补偿工作。
对于刀具破损报警或对刀具磨损到一定程度后进行强制更换,其原理也是一样,根据刀具允许的磨损量,人为设定一个“门槛值”,一旦对刀仪监测到的误差超过门槛值,即可认为刀具已破损或超过了允许的磨损值,则机床自动报警停机,然后强制进行刀具的更换。
(3)、当机床因热变型造成滚珠丝杠伸长后,也可对由此而引起的刀具偏置值变动量进行补偿,以确保工件尺寸的稳定。
机床在工作循环过程中,由于机床直线运动产生的摩擦是以热量的形式体现出来,另还有一个不可忽视的热源是切削下来的铁屑向机床的热传导。
这些因素的客观存在都会导致机床的变形特别是丝杠的热伸长,反映出来的现象是刀尖的位置要发生变化,其结果是工件的尺寸精度一定会随这种热变形同步变化。
如果在机床上安装了对刀仪装置,上述问题也可迎刃而解,无非是把这种由热变形产生的刀尖位置变化视为刀具的磨损值罢了,通过用对刀仪来测量及补偿这种新产生的刀具偏置值即可解决。
3、对刀仪的简要工作原理雷尼绍对刀仪的核心构件是由一个高精度的开关(传感器)、一个高硬度高耐磨性的硬质合金四面体(对刀探针)和一个信号传输接口器组成(其它构件略)。
四面体探针是用于与刀具进行接触并通过安装在其下的绕性支撑杆把力向高精度开关传递;开关所发出的通、断信号通过信号传输接口器传输到数控系统中去进行刀具方向识别、运算、补偿、存取等。
不管是刀具偏置值还是磨损值还是热变形引起的刀尖位置变动值,实质上都可归结为刀具初始偏置值与刀具经工作一段时间后的实际偏置值之间的变动量。
数控机床的工作原理决定,当机床返回各自运动轴的机械参考点后,建立起来的是机床坐标系。
该参考点一旦建立,相对机床零点而言,在机床坐标系数轴上的各运动方向就有了数值上的实际意义。
一般情况下此时只要在机床坐标系的基础上通过编程,建立起G50工件坐标系就可以进行实际加工了(仅使用机床坐标系十分不便于加工程序的编制)。
但仅此对于安装了对刀仪的机床还不行,还必须要通过参数设定的方法来精确确定对刀仪传感器距机床坐标系零点的各方向实际坐标固定值才能满足使用(图5),否则数控系统将无法在机床坐标系和对刀仪固定坐标之间进行相互位置的数据换算。
图5:对刀仪的坐标系当我们在机床上建立起来了“机床坐标系”和“对刀仪固定坐标”后(不同规格的对刀仪应设置不同的固定坐标值),有以下对刀仪的简要工作原理描述:(1)、机床各直线运动轴返回各自的机械参考点之后,机床坐标系和对刀仪固定坐标之间的相对位置关系就建立起了具体的数值。
(2)不论是使用自动编程控制还是手动控制方式操作多刀仪,当移动所选定的某个轴的刀具并使刀尖(或动力回转刀具的外径)触动、靠向对刀仪上四面探针的对应平面并探针通过绕性支撑杆摆动触发了高精度开关传感器后,开关会立即通知系统锁定该进给轴的运动。
因为数控系统是把这一信号作为高级信号来处理,所以动作的控制会极为迅速、准确。
(3)由于数控机床直线进给轴上均安装有进行位置环反馈的脉冲编码器,数控系统中也有记忆该进给轴实际位置的计数器,此时系统只要读出该轴停止的准确位置,通过机床、对刀仪两者之间相对关系的自动换算,即可确定该轴刀具刀尖(或直径)的初始刀具偏置值了。
换一个角度说,如把它放到机床坐标系中来衡量,即相当于确定了机床参考点距机床坐标系零点的距离与该刀具测量点距机床坐标系零点的距离及两者之间的实际偏差值。
(4)不论是工件切削后产生的刀具磨损、还是滚珠丝杠热伸长后出现的刀尖变动量,只要再进行一次对刀的作业,数控系统就会自动把测得的该把刀具的新刀具偏置量与该把刀具的初始刀具偏置量进行比较计算,并将需要进行补偿的δ误差值自动补偿进刀补存储区中去。
当然,如果换了新的一把刀具,再对其重新进行对刀,所获得的偏置值就应该是该刀具新的初始刀具偏置值了。
附:雷尼绍对刀仪能达到怎样的对刀精度?根据实际应用情况及有关资料证明,雷尼绍对刀仪能达到以下精度:15"以下卡盘(含15")的中小规格数控车床,使用雷尼绍对刀仪能达到的对刀重复精度为:±5um 。
18"以上卡盘(含18")的大规格数控车床,使用雷尼绍对刀仪能达到的对刀重复精度为:±8um 。
在以上篇幅中,只是将雷尼绍对刀仪装置的构成、用途及简单的工作原理进行了简要介绍。
受篇幅所限,有关对刀仪安装后的调试、参数设置及使用方法、注意事项等,不在此赘述。
(完)。