安庆石化蜡油加氢装置开工过程及问题处理
制氢开工过程中难点分析及对策

制氢开工过程中难点分析及对策制氢装置为气体进料装置,所用的原料及产品气均为易燃易爆气体,且生产过程中工况比较苛刻,属高温中压型装置,开工过程中,存在以下控制难点,下面就分别阐述如下并给出相应对策以供参考:一、联动试车过程1、烘炉煮炉过程中蒸汽的配入制氢烘炉煮炉过程中,由于自产中压蒸汽不合格,不能配入系统,故须引管网3.5MPa 中压蒸汽配入转化炉进行升温,配入过程中,可能出现以下几种情况:①暖管不够造成中压蒸汽水击②暖管不够造成中压蒸汽冷凝水进入转化炉下集气管浸泡耐火浇注料层③由于系统已经建立氮气循环,如果操作不当,配入过猛过快容易造成蒸汽顶氮气的现象发生,造成压缩机出口憋压,破坏系统循环,严重影响以后工序的进行。
对策:对于第一、二种情况,比较简单,在配入蒸汽之前,一定要逐段暖管,暖管合格后方可将中压蒸汽向后引,同时放净管内存水,防止蒸汽冷凝水进入转化炉,即可避免,对于第三种情况则需派专人监督,操作过程种开关阀门一定要缓慢进行,同时将压缩机二返一阀门打自动,并设定合适的压力值,以防止出口憋压。
一旦发生上述的三种情况,应迅速关小中压蒸汽入装置阀门,待问题排除后方可再次引入中压蒸汽。
2、中压锅炉煮炉过程的控制中压锅炉煮炉过程中,由于自产蒸汽不合格,必须进行放空,同时要通过放空开度的大小来控制汽包的升压速度。
在不同的升压阶段可能会产生以下问题:①0~0.4MPa升压的过程中,汽包液位控制在最高可见液位,如果控制不当,将会造成高碱度的锅炉水冲入过热段中,造成过热段由于碱结晶堵塞过热段,严重影响锅炉的正常操作。
②各恒压阶段由于需要通过手阀手动控制汽包压力,存在控制准确度不足的问题,容易造成汽包压力的骤升骤降,造成汽包液位波动,破坏锅炉的正常操作。
③降压补水阶段,由于此时要大量排污,连排定排同时开启,容易造成汽包液位过低。
对策:对于第一、二种情况,要求操作过程中,升温、升压过程必须缓慢进行,由于过热蒸汽的压力和温度是对应的,控制汽包的升压速度就可以控制汽包的升温速度,所以,开关阀门的幅度一定要小,待压力稳定后再进行下一次开关阀门操作。
蜡油加氢操作规程(3篇)

第1篇一、操作前的准备1. 确保设备完好,检查各阀门、管道、仪表等无泄漏、堵塞现象。
2. 确认原料蜡油质量符合要求,检查原料罐液位、温度、压力等参数。
3. 检查氢气供应系统,确保氢气纯度、压力符合要求。
4. 检查反应器、分离器、冷却器等设备,确保正常运行。
5. 检查现场安全设施,如消防器材、报警装置等。
6. 确认操作人员熟悉操作规程,了解设备性能和安全隐患。
二、操作步骤1. 启动氢气供应系统,调节氢气流量,确保氢气纯度和压力稳定。
2. 打开原料油罐阀门,启动原料油泵,将蜡油送入反应器。
3. 调节反应器温度,使其保持在设定范围内。
4. 检查反应器进出口温度、压力等参数,确保反应器正常运行。
5. 检查分离器、冷却器等设备,确保其正常运行。
6. 检查氢气、蜡油、反应产物等物料流量,确保流量稳定。
7. 定期检查设备,发现异常情况及时处理。
8. 检查设备安全联锁,确保其正常工作。
9. 操作过程中,密切关注设备运行状态,发现异常情况立即停车检查。
三、操作注意事项1. 操作人员应穿戴好劳动保护用品,如防护服、防护眼镜、手套等。
2. 严禁在设备运行过程中进行检修、清洁等操作。
3. 操作过程中,严禁触摸高温、高压设备。
4. 严禁操作人员携带易燃、易爆物品进入操作区域。
5. 操作过程中,注意观察设备运行状态,发现异常情况立即停车处理。
6. 严格执行设备安全联锁,确保设备安全运行。
7. 操作过程中,注意观察反应器、分离器、冷却器等设备温度、压力、液位等参数,确保其稳定。
8. 操作过程中,注意观察氢气、蜡油、反应产物等物料流量,确保其稳定。
9. 定期对设备进行维护保养,确保设备正常运行。
四、操作后的处理1. 停车前,确保设备稳定运行,关闭相关阀门。
2. 停车后,对设备进行检查,确认无异常情况。
3. 关闭氢气供应系统,释放设备内残余压力。
4. 清理操作区域,确保现场整洁。
5. 记录操作过程中的各项参数,如温度、压力、流量等。
加氢裂化装置生产运行管理及事故处理

加氢裂化装置生产运行管理及事故处理一、引言加氢裂化装置是石油炼化工业中一种重要的生产设备,主要用于加氢裂化重油、轻油和渣油,通过裂化反应将其转化为高附加值的汽油、柴油和润滑油等产品。
加氢裂化装置在生产运行过程中,需要严格的管理措施来确保生产安全和产品质量。
同时,对于可能发生的事故情况,也需进行有效的事故处理措施,以减小事故对设备运行和人身安全的影响。
本文将对加氢裂化装置生产运行管理及事故处理进行详细的介绍,包括装置管理的准备工作、生产运行中的重点管理要点和灾难事故处理的应急措施。
二、装置管理准备工作1.人员培训加氢裂化装置操作人员需要接受专业的培训,了解装置的基本结构和原理,掌握操作技能,熟悉各种操作规程和安全操作规范。
同时,应定期进行培训和考核,提高操作人员的技能水平。
2.设备维护加氢裂化装置的设备维护工作至关重要,包括定期的设备检修、润滑和更换部件等。
定期维护可以预防设备故障和事故的发生,延长设备的使用寿命。
3.安全设施加氢裂化装置应配备完善的安全设施,包括防火、防爆、防静电等设施。
同时,应建立设备运行记录和管理制度,做好安全检查、隐患排查和事故记录等工作。
三、生产运行管理要点1.生产计划与排班根据市场需求和设备的运行情况,制定合理的生产计划,并做好排班工作。
生产计划应考虑装置的负荷运行状态,避免过高或过低的负荷对装置性能和安全产生影响。
2.储运系统管理加氢裂化装置的产品需要进行储存和运输,因此需要建立完善的储运系统管理。
包括储罐的清洁、检修和安全管理,管线的维护和防腐等。
3.原料控制与质量管理加氢裂化装置的原料控制和质量管理对于产品质量和装置运行稳定性有重要影响。
要严格控制原料的配比和质量,并定期进行原料的抽样检验,确保原料的稳定和质量。
4.装置运行监控加氢裂化装置的运行状态需要进行实时监控,通过监控系统对装置的各个参数进行监测和记录。
一旦发现异常情况,应及时报警并采取相应的措施进行处理。
安庆石化蜡油加氢装置开工过程及问题处理

化 剂 均 由石 科 院 开 发 , 国 石 化 催 化 剂 长 岭 分 公 司 生 产 。催 化 中 剂装填工作于 9月 1 7~2 1日完 成 , 填工作相 对 比较顺 利。本 装
次催化剂装填全采用普 通装填法 进行 , 主催化 剂 的物 性见表 1 , 装填数据见表 2 。
22Mt 蜡油加氢装置是 安庆 石化 8Mta . ・ a ・ 炼 油扩建 改 造工程的配套主体装 置之一 , 诣在 满足我 厂含硫 原油加 工适 应 性改造及油品质量升级 工程扩建 后急剧增加 的含硫 蜡油处 理量 的需求 , 即将新建的 3 ・ 为 Mta 催化裂化装 置提供新鲜 原料。 目 前装置 生产 的精制 蜡油 作为 现有 1 2Mta 催化 裂化装 置 和 . ・ 0 6Mt 催 化 裂 解 装 置 提 供 原 料 。装 置 采 用 冷 热 高 、 分 流 . ・ a 低 程, 增设循环氢脱硫 及低 分气脱硫 系统 流程 。装置 采用 北京 石 油 化 工 研 究 院 ( 称 石科 院 ) V T工 艺 技 术 进 行 设 计 , 用 R 简 R H 选 N 3 V型催化剂作 为主催 化剂 。装置 设计原 料 比例为 : 焦 化 2 m(
加氢(裂化)装置生产运行管理及事故处理

(三)正常生产过程中的工艺安全管理 3.操作安全事项
仪表
仪表线路投运前,应对所有仪表进行以下的检查:
•确认所有仪表能投入使用和性能符合要求。
•当在自动控制状态下运行时,改变给定值的过程应逐步进行,以防止剧 烈波动。 •在往调节阀逐步引入所要求的空气讯号前,确认所有自动控制器均处于 “手动”位置,以便在切往“自动”时,调节阀能处于正确位置。 •定期观察所有温度计、压力表和在调节阀上的空气压力讯号,并注意其 有否变化,如显示有变化时,则表明设备内可能有异常情况的迹象。 •有些联锁系统具有除了自动停的系统以外还有手动停系统,除非是在紧 急事故时,否则不得按动该手停按钮。
(三)正常生产过程中的工艺安全管理 3.操作安全事项 对下述操作规定,应视为对装置安全平稳操作所需的基本规则而加以遵守:
阀门
送气体或蒸汽的阀门,每一次开启1/10圈。仔细地观察阀门有无异常现
①应经常小心开启、关闭阀门。对输送液体的阀,每一次开启1/4圈;对输
象。如果一切正常,阀门需全开,将阀门全开后并回转一圈。
单一的或按一定比例混合的原料油进入装置,经与反应器流出物换热升 温,再与经加热炉升温的循环氢混合后进入加氢精制反应器,该反应器流出
物与循环油和经加热Байду номын сангаас升温的循环氢混合后进人加氢裂化反应器。裂化反应
器流出物与原料油、循环氢换热降温,并冷却到要求的温度进人高压分离器 (高分)。 高分顶部的循环氢经压缩、换热、加热升温后与原料油混合后进人反应 器。补充的氢气从装置外来,升压后进入反应系统。高分下部的液体油分水 后进入分馏部分,分割成<C4、轻石脑油、重石脑油、柴油以及塔底未转化 油。未转化油可排出装置,也可作为循环油返回反应器。
石蜡加氢精制装置扩能瓶颈问题分析和改进措施

石蜡加氢精制装置扩能瓶颈问题分析和改进措施摘要:石蜡制氢装置的原料将在一定的温度,压力和催化剂的存在下暴露于油的氢饱和度,脱水,脱氧和芳香碳氢化合物的转化以及其他反应。
为了将石蜡中的痕量物质转化为相应的去除成分,将致密的石蜡碳氢化合物转化为氢化芳香碳氢化合物,从而提高石蜡产品的色相和光学稳定性,去除异味,达到净化目的。
基于此,对石蜡加氢精制装置扩能瓶颈问题分析和改进措施进行研究,以供参考。
关键词:石蜡;加氢;瓶颈;扩能引言炼油厂石蜡脱氢装置于1993年建成投产,经过多次改造,目前装机容量为15万吨每年。
2020年2月,C-01B液压机在运行时由于高振动锁定而突然停止,操作员紧急启动备用机器。
在对氢气压缩机进行维修时,发现曲轴箱中的连接杆断裂。
1石蜡加氢精制催化剂的开发石蜡制氢过程中的反应条件相对较温和,为了达到芳香族碳氢化合物的深度解吸、解吸和饱和的目的,催化剂必须具有较高的制氢性能。
在精炼过程中,不需要牵引反应,以避免产品中的油含量增加。
根据石蜡反应的特性,为了提高催化剂的性能,满足工业应用的要求,催化剂应充分利用新型载体材料的孔隙率、孔隙率和高强度,克服传统载体的缺点,提高催化剂的加氢性能和对劣质原料的适应性。
同时,根据石油蜡的加氢特性,优化活性成分体系,添加适当的助剂来调节表面酸,以提高催化剂的活性、选择性和稳定性。
2原因分析2.1 原材料质量恶化统计数据显示,假设白土未被石蜡活化,与前一个周期相比,本周期生产了超过3个非尿素精炼蜡油,产量为2,556吨。
石蜡的原料含有一定量的金属、浓缩的芳香族碳氢化合物、硫、氮化合物等。
上述物质的含量通常会随着原料干燥的增加而增加一倍。
在进入水力发电厂之前,不使用白底制备循环原料,原料中含有的极化合物和微小杂质不能有效过滤,直接在水力反应器中产生,并在催化剂表面和床位上吸附和沉积,从而形成第一层和上层分布板。
同时,随着床层自由度的降低,也将导致流量和物质分布的恶化,沟渠流动,干燥区域的出现,甚至床层的混合,内部元素的变形。
蜡油加氢裂化装置检修开工总结-2014
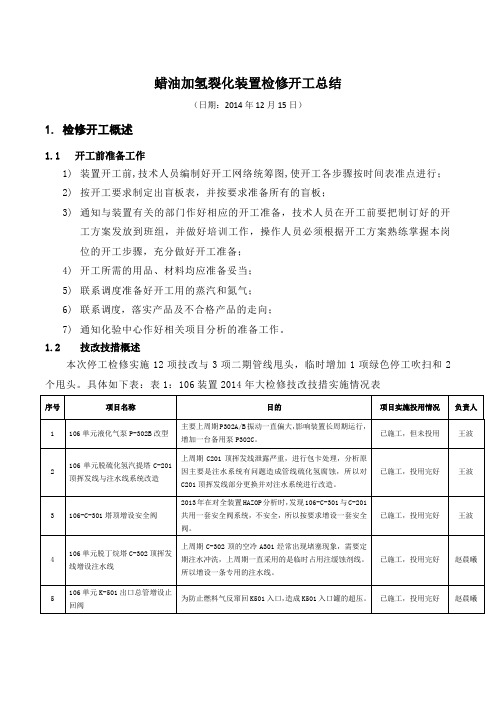
蜡油加氢裂化装置检修开工总结(日期:2014年12月15日)1.检修开工概述1.1开工前准备工作1)装置开工前,技术人员编制好开工网络统筹图,使开工各步骤按时间表准点进行;2)按开工要求制定出盲板表,并按要求准备所有的盲板;3)通知与装置有关的部门作好相应的开工准备,技术人员在开工前要把制订好的开工方案发放到班组,并做好培训工作,操作人员必须根据开工方案熟练掌握本岗位的开工步骤,充分做好开工准备;4)开工所需的用品、材料均应准备妥当;5)联系调度准备好开工用的蒸汽和氮气;6)联系调度,落实产品及不合格产品的走向;7)通知化验中心作好相关项目分析的准备工作。
1.2技改技措概述本次停工检修实施12项技改与3项二期管线甩头,临时增加1项绿色停工吹扫和2个甩头。
具体如下表:表1:106装置2014年大检修技改技措实施情况表1.3装置开工计划及总体安排106单元2014年停工检修在10月13日0点开始,10月22日交付检修,检修在12月24 日结束,12月25日检修交付生产,装置开始进入开工阶段,装置开工计划15天,5天是三查四定、机组试机、装置吹扫气密准备时间,10天正式开工时间,装置计划是在12月10日生产正常。
总体安排如下表:表2:106单元开工节点安排表2.开工方案的执行与变更情况本次装置开工过程严格按照开工方案来消项操作,由于本次大检修的技改项目较多,针对这些技改项目编写了对应的投用方案和消项卡。
本次开工时间较长用时15天,比2011年检修开工增加了3-4天时间。
本次开工气密工作和油运工作做得时间较长。
方案较大变更主要有以下几个方面:(1)反应系统N2气密,原方案是要求做到10.0MPa,实际只做到8.0MPA,因为受K101出口温度影响,在氮气工况只能承受到8.0MPa,以后开工方案中反应系统N2气密最高压力修改为8.0 MPa。
(2)根据shell催化剂专家建议预硫化末期要在330度恒温4小时,然后升温到345度就结束预硫化,根据当时反应催化剂床层温度情况,预硫化末期床层温度在240度恒温6小时后就结束预硫化,没有按方案升温至350度恒温4小时。
蜡油加氢工艺装置工艺优化开工总结
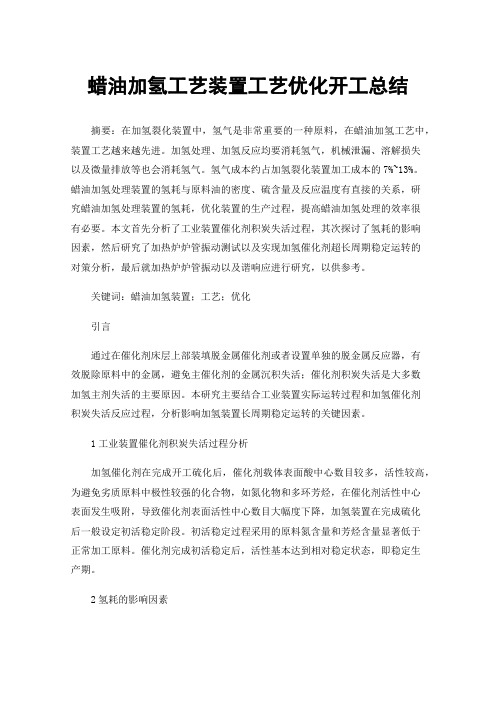
蜡油加氢工艺装置工艺优化开工总结摘要:在加氢裂化装置中,氢气是非常重要的一种原料,在蜡油加氢工艺中,装置工艺越来越先进。
加氢处理、加氢反应均要消耗氢气,机械泄漏、溶解损失以及微量排放等也会消耗氢气。
氢气成本约占加氢裂化装置加工成本的7%~13%。
蜡油加氢处理装置的氢耗与原料油的密度、硫含量及反应温度有直接的关系,研究蜡油加氢处理装置的氢耗,优化装置的生产过程,提高蜡油加氢处理的效率很有必要。
本文首先分析了工业装置催化剂积炭失活过程,其次探讨了氢耗的影响因素,然后研究了加热炉炉管振动测试以及实现加氢催化剂超长周期稳定运转的对策分析,最后就加热炉炉管振动以及谐响应进行研究,以供参考。
关键词:蜡油加氢装置;工艺;优化引言通过在催化剂床层上部装填脱金属催化剂或者设置单独的脱金属反应器,有效脱除原料中的金属,避免主催化剂的金属沉积失活;催化剂积炭失活是大多数加氢主剂失活的主要原因。
本研究主要结合工业装置实际运转过程和加氢催化剂积炭失活反应过程,分析影响加氢装置长周期稳定运转的关键因素。
1工业装置催化剂积炭失活过程分析加氢催化剂在完成开工硫化后,催化剂载体表面酸中心数目较多,活性较高,为避免劣质原料中极性较强的化合物,如氮化物和多环芳烃,在催化剂活性中心表面发生吸附,导致催化剂表面活性中心数目大幅度下降,加氢装置在完成硫化后一般设定初活稳定阶段。
初活稳定过程采用的原料氮含量和芳烃含量显著低于正常加工原料。
催化剂完成初活稳定后,活性基本达到相对稳定状态,即稳定生产期。
2氢耗的影响因素(1)溶解损失。
氢气在循环过程中,有一部分会溶解在热高压分离器(简称热高分)和冷高压分离器(简称冷高分)的液相中,称之为溶解损失。
相关研究文献指出,热高分温度180℃和240℃是2个拐点。
180℃左右,循环氢的体积分数最低,温度高于180℃后,随着温度的升高,循环氢的体积分数逐渐增加;温度超过240℃后,循环氢体积分数的增加趋势变缓。
制氢装置开工难点分析及对策
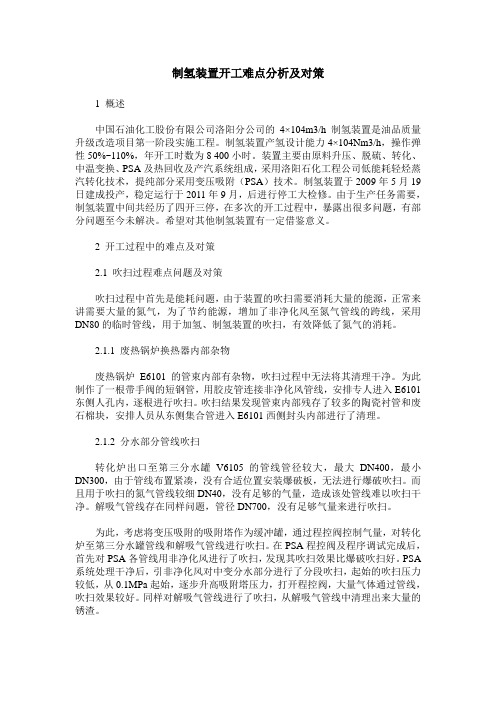
制氢装置开工难点分析及对策1 概述中国石油化工股份有限公司洛阳分公司的4×104m3/h制氢装置是油品质量升级改造项目第一阶段实施工程。
制氢装置产氢设计能力4×104Nm3/h,操作弹性50%~110%,年开工时数为8 400小时。
装置主要由原料升压、脱硫、转化、中温变换、PSA及热回收及产汽系统组成,采用洛阳石化工程公司低能耗轻烃蒸汽转化技术,提纯部分采用变压吸附(PSA)技术。
制氢装置于2009年5月19日建成投产,稳定运行于2011年9月,后进行停工大检修。
由于生产任务需要,制氢装置中间共经历了四开三停,在多次的开工过程中,暴露出很多问题,有部分问题至今未解决。
希望对其他制氢装置有一定借鉴意义。
2 开工过程中的难点及对策2.1 吹扫过程难点问题及对策吹扫过程中首先是能耗问题,由于装置的吹扫需要消耗大量的能源,正常来讲需要大量的氮气,为了节约能源,增加了非净化风至氮气管线的跨线,采用DN80的临时管线,用于加氢、制氢装置的吹扫,有效降低了氮气的消耗。
2.1.1 废热锅炉换热器内部杂物废热锅炉E6101的管束内部有杂物,吹扫过程中无法将其清理干净。
为此制作了一根带手阀的短钢管,用胶皮管连接非净化风管线,安排专人进入E6101东侧人孔内,逐根进行吹扫。
吹扫结果发现管束内部残存了较多的陶瓷衬管和废石棉块,安排人员从东侧集合管进入E6101西侧封头内部进行了清理。
2.1.2 分水部分管线吹扫转化炉出口至第三分水罐V6105的管线管径较大,最大DN400,最小DN300,由于管线布置紧凑,没有合适位置安装爆破板,无法进行爆破吹扫。
而且用于吹扫的氮气管线较细DN40,没有足够的气量,造成该处管线难以吹扫干净。
解吸气管线存在同样问题,管径DN700,没有足够气量来进行吹扫。
为此,考虑将变压吸附的吸附塔作为缓冲罐,通过程控阀控制气量,对转化炉至第三分水罐管线和解吸气管线进行吹扫。
在PSA程控阀及程序调试完成后,首先对PSA各管线用非净化风进行了吹扫,发现其吹扫效果比爆破吹扫好。
蜡油加氢装置工业运行总结
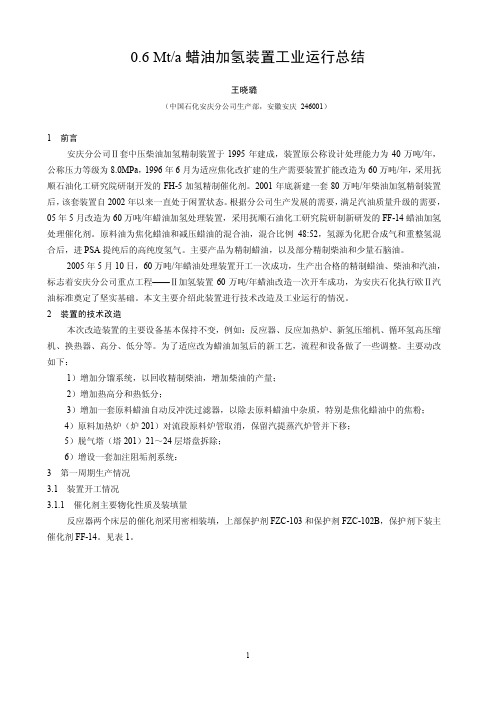
0.6 Mt/a蜡油加氢装置工业运行总结王晓璐(中国石化安庆分公司生产部,安徽安庆246001)1 前言安庆分公司Ⅱ套中压柴油加氢精制装置于1995年建成,装置原公称设计处理能力为40万吨/年,公称压力等级为8.0MPa,1996年6月为适应焦化改扩建的生产需要装置扩能改造为60万吨/年,采用抚顺石油化工研究院研制开发的FH-5加氢精制催化剂。
2001年底新建一套80万吨/年柴油加氢精制装置后,该套装置自2002年以来一直处于闲置状态。
根据分公司生产发展的需要,满足汽油质量升级的需要,05年5月改造为60万吨/年蜡油加氢处理装置,采用抚顺石油化工研究院研制新研发的FF-14蜡油加氢处理催化剂。
原料油为焦化蜡油和减压蜡油的混合油,混合比例48:52,氢源为化肥合成气和重整氢混合后,进PSA提纯后的高纯度氢气。
主要产品为精制蜡油,以及部分精制柴油和少量石脑油。
2005年5月10日,60万吨/年蜡油处理装置开工一次成功,生产出合格的精制蜡油、柴油和汽油,标志着安庆分公司重点工程——Ⅱ加氢装置60万吨/年蜡油改造一次开车成功,为安庆石化执行欧Ⅱ汽油标准奠定了坚实基础。
本文主要介绍此装置进行技术改造及工业运行的情况。
2 装置的技术改造本次改造装置的主要设备基本保持不变,例如:反应器、反应加热炉、新氢压缩机、循环氢高压缩机、换热器、高分、低分等。
为了适应改为蜡油加氢后的新工艺,流程和设备做了一些调整。
主要动改如下:1)增加分馏系统,以回收精制柴油,增加柴油的产量;2)增加热高分和热低分;3)增加一套原料蜡油自动反冲洗过滤器,以除去原料蜡油中杂质,特别是焦化蜡油中的焦粉;4)原料加热炉(炉201)对流段原料炉管取消,保留汽提蒸汽炉管并下移;5)脱气塔(塔201)21~24层塔盘拆除;6)增设一套加注阻垢剂系统:3 第一周期生产情况3.1 装置开工情况3.1.1 催化剂主要物化性质及装填量反应器两个床层的催化剂采用密相装填,上部保护剂FZC-103和保护剂FZC-102B,保护剂下装主催化剂FF-14。
石蜡加氢精制装置说明与危险因素防范措施

石蜡加氢精制装置说明与危险因素防范措施石蜡加氢精制装置是一种用于将黄蜡或石蜡通过加氢处理转化为白蜡的一种工业设备。
这种设备将石蜡加热至一定温度后与氢气反应,通过饱和烃的裂解与合成反应,将石蜡中的不饱和化合物去除,从而得到更纯净的白蜡产品。
然而,在进行石蜡加氢精制过程中,也存在一些危险因素需要引起注意,并采取相应的防范措施来保证设备操作的安全。
下面将对石蜡加氢精制装置的危险因素和防范措施进行详细说明。
1.高温和高压:石蜡加氢精制过程需要高温和高压环境,而高温和高压环境下容易引发爆炸和火灾等危险。
因此,需要严格控制加热温度和操作压力,确保设备的安全运行。
同时,需要定期检查和维护设备的阀门、管道和容器,确保其能够承受高温和高压环境的要求。
2.氢气泄漏:石蜡加氢精制过程需要使用氢气,而氢气是一种易燃易爆的气体,一旦泄漏可能引发火灾和爆炸。
因此,需要在装置中设置可靠的气体泄漏报警装置,并定期检查其是否正常工作。
同时,需要定期对氢气系统进行检查和维护,确保气体管道的完整性,避免泄漏的发生。
3.工作环境污染:石蜡加氢精制过程中会产生一些有害气体和污染物,如硫化氢、二甲苯等。
这些物质对人体健康有一定的危害。
因此,需要在装置周围设置通风系统和排气装置,确保工作环境的良好通风。
同时,操作人员需要佩戴防护装备,如防毒面具、防护手套和防护眼镜等,避免有害物质的直接接触。
4.废水和废气处理:石蜡加氢精制过程会产生大量的废水和废气。
这些废水和废气中含有一些有害物质,需要进行处理,以避免对环境造成污染。
因此,需要在装置中设置废水处理和废气处理系统,并定期进行检查和维护,确保其正常工作。
综上所述,石蜡加氢精制装置的操作过程中需要注意防范各种危险因素,以保证设备操作的安全。
通过控制加热温度和操作压力、设置气体泄漏报警装置、保持良好的通风环境、佩戴防护装备和进行废水和废气的处理等措施,可以有效减少事故的发生,保障人员的身体健康和环境的安全。
蜡油加氢装置循环氢脱硫系统问题分析及对策
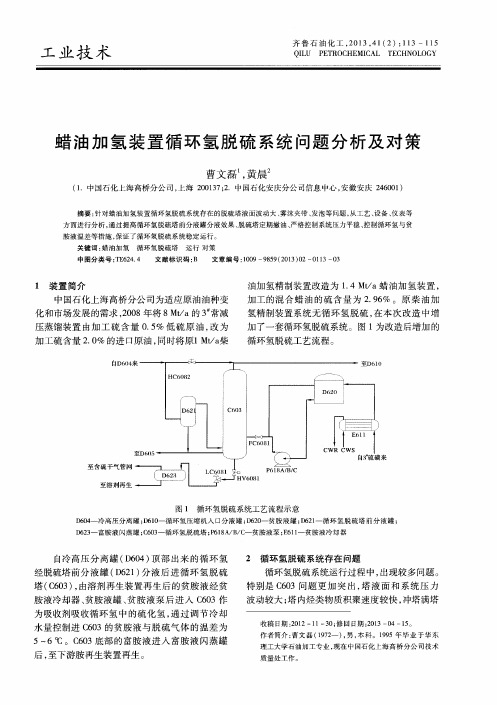
中图分类号 : T E 6 2 4 . 4
文献标识码 : B
1 装 置 简介
油 加氢精 制 装置 改造 为 1 . 4 M t / a蜡 油加 氢 装 置 ,
加 工 的混 合 蜡 油 的硫 含 量 为 2 . 9 6 % 。原 柴 油 加
中 国石化 上海 高桥 分公 司为适应 原 油油 种 变 化 和 市场 发展 的需 求 , 2 0 0 8年将 8 Mt / a的 3 常减 压 蒸馏 装 置 由加 工 硫 含 量 0 . 5 %低硫原 油 , 改 为 加 工硫 含量 2 . 0 % 的进 口原 油 , 同 时将原 1 Mt / a 柴
曹文磊 , 黄晨
( 1 .中国石化上海 高桥 分公司 , 上海 2 0 0 1 3 7; 2 .中国石化安庆分公 司信息 中心 , 安徽安庆 2 4 6 0 0 1 )
摘要 : 针对蜡油加氢装置循环氢脱硫 系统存 在的脱硫塔液 面波动 大 、 雾 沫夹带 、 发泡等 问题 , 从工艺 、 设备 、 仪表等
工 业 技 术
齐 Q I 鲁 L U 石 油 P E 化 T R 工 O C , H 2 E 0 M 1 3 I C , A 4 L 1 ( 2 T E ) C : H 1 1 N 3 O L — O 1 G 1 Y 5
蜡 油 加 氢 装 置循 环 氢 脱 硫 系统 问题 分 析 及 对 策
L D 6 0 8 6 、 沉筒 液面 计 L C 6 0 8 1和 现 场 液 面 计 , 这3 个 测点 为塔 的 同一 开 孑 L 。 由于 L D 6 0 8 6引 出 管 线
比较 细 长 , 导致 测 量 值 不 能及 时反 映 , 在 L C 6 0 8 1 液面发生波动 时, L D 6 0 8 6指 示 延 迟 不 能 作 为 参 考 。 只能 到 C 6 0 3塔 上 与 现 场 液 面 计 进 行 核 对 , 影 响操作 及 时调 整 。 同 时 , 3个 液 面计 测 点 开孔
加氢制氢装置操作问题及解决方案 (2)解析
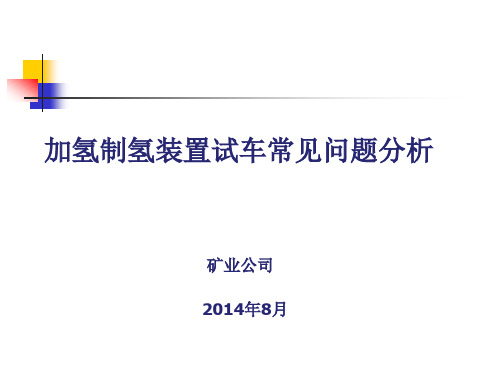
矿业公司 2014年8月
主要内容:
一、制氢装置工艺 二、制氢装置试车程序 三、制氢装置常见问题分析 四、加氢装置工艺 五、加氢装置试车程序 六、加氢装置常见问题分析
一、制氢工艺
主要 工艺路线
1、催化转化(烃类蒸汽转化) 2、部分氧化(煤汽化 、重油) 3、化工附产 (重整、甲醇、乙烯、) 4、氨、甲醇裂解 5、电解水
转化催化剂
操作中出现的问题——炉管过热
● 催化剂热老化——催化剂Ni表面烧结,引起催化剂的活性 逐渐损失 ◎转化炉原料不连续,瞬间中只有蒸汽存在下,由于 没有吸热,顶部温度比操作温度高100℃以上,再长时间 导致催化剂钝化!! ◎转化炉过热也会加快催化剂的热老化,即使短时 间温度聚升也会引起催化剂Ni表面的损失,缩短数月催化 剂使用寿命!
高温变换 SK-201-2 325-500 ℃ 中温变换 LK-811 200-350 ℃ 低温变换 LK-821-2 185-275 ℃
操作中出现的问题 硫催化剂中毒 有较高的抗氯、 硅中毒能力。
1、深冷:投资大、能耗高、开停车慢、 可获 得多产品。
2、膜分离:投资小、操作简便、纯度低、 压损大。
传统 10-2-4 PSA 时序表
1 2 3 4 5 6 7 8 9 10 11 12 13 14 15 16 17 18 19 20 A A A A E1D E2D E3D E4D PP1 PP2 PP3 D P3 P2 P1 E4R E3R E2R E1R FR E1R FR A A A A E1D E2D E3D E4D PP1 PP2 PP3 D P3 P2 P1 E4R E3R E2R E3R E2R E1R FR A A A A E1D E2D E3D E4D PP1 PP2 PP3 D P3 P2 P1 E4R P1 E4R E3R E2R E1R FR A A A A E1D E2D E3D E4D PP1 PP2 PP3 D P3 P2 P3 P2 P1 E4R E3R E2R E1R FR A A A A E1D E2D E3D E4D PP1 PP2 PP3 D PP3 D P3 P2 P1 E4R E3R E2R E1R FR A A A A E1D E2D E3D E4D PP1 PP2 PP1 PP2 PP3 D P3 P2 P1 E4R E3R E2R E1R FR A A A A E1D E2D E3D E4D E3D E4D PP1 PP2 PP3 D P3 P2 P1 E4R E3R E2R E1R FR A A A A E1D E2D E1D E2D E3D E4D PP1 PP2 PP3 D P3 P2 P1 E4R E3R E2R E1R FR A A A A A A E1D E2D E3D E4D PP1 PP2 PP3 D P3 P2 P1 E4R E3R E2R E1R FR A A
加氢裂化装置事故处理后的开工方案

加氢裂化装置事故处理后的开工方案事故处理过程中,有两种可能情况:一种是维持循环氢压缩机运转;另一种是循环氢压缩机停转。
所以下面的开工操作也按两种情况来说明。
(一)、当维持循环气循环时的开工1、反应器降温按降温规定,将反应器温度降至300℃。
2、反应器升温当温度稳定后,提高反应器温度约300~325℃。
3、分馏部分由循环操作转入准备进料。
4、进原料油。
⑴启动泵1401-P-101 、1401-P-102,向反应系统进料。
⑵进油2小时内往反应系统注水。
⑶以110t/h的进料量向反应系统进油。
注意观察反应器床层吸附热温波。
⑷待全装置平稳后,再将处理量提至规定值。
注意提量要少提、勤提,每次提量后,要待系统平稳后再进行。
5、根据停工时的进料量和总平均床层温度,确定开工后所需的总的床层平均温度。
调整各参数,转入正常操作。
(二)当停止循环氢循环时的开工1、分馏部分原来在循环,则继续循环操作,如处于氮气密封,则向系统加重柴油和石脑油,然后加压系统并进行热循环。
2、启动循环氢压缩机1401-K-102,并建立循环氢循环。
3、加热炉1401-F-101点火。
4、提高反应器入口温度到300~325℃。
6、启动新氢压缩机1401-K-101,(当反应器所有各点的表面温度超过93℃时,1401-R-101入口压力才可超过4.125MPa)提高系统压力至操作压力。
在升压的时候,密切观察温度,假如催化剂温度突然上升,使用冷氢使温度处于控制条件下并继续以较低的速度加压。
假如不能控制,则降低压力并继续以最大循环气流量进行循环。
如果温度还没控制住而循环压缩机又不得不停止,则继续泄压至温度不再上升为止。
如果温度又回升,则继续以最大流量用单程补充氢冷却。
一旦温度稳定,就以更慢的速度提高压力。
7、进原料油,调整各参数,转入正常操作。
石蜡加氢精制装置开工方案

石蜡加氢精制装置开工方案加氢精制装置开工方案一、开工说明依据厂物料平衡、节能降耗、降低加工成本等综合考虑后安排决定,15万吨/年石蜡加氢精制装置进行开工。
三、开工注意事项及风险评估开工注意事项1、开工过程要严格按照开工网络和规程进行,严禁乱排乱放,污油必须及时处理干净,否则严禁施工动火。
2、设备、管线的吹扫、置换必须严格按照规程进行,不留死角,按管理区域进行分工、责任,保证开工引油的安全。
3、拆盲板严格按照盲板表进行、专人负责,做好各项拆盲板的记录,保证不漏拆一块盲板,同时要求施工单位拆盲板的工作人员要固定,本着谁装的盲板、谁拆除的原则,防止遗漏。
4、装置内的下水井、地漏必须认真用石棉布封堵好,上面盖上黄土并有记录,每天还需对此进行认真地检查,及时整改不符合要求的下水井、地漏。
5、进入开工施工现场的人员必须按要求着装,戴好安全帽,高处作业系好安全带。
6、夜间要有足够的照明,临时电线必须绝缘良好,不破皮,移动照明要有铁网罩保护。
7、各种施工机具必须安全可靠,发现失灵要立即消除,严禁迁就使用,避免发生意外。
8、开工引油时,严禁大量排入污水管道,油水混合物退到装置外罐区或装置内污油罐。
9、气密过程中,发现泄漏要及时处理,要泄压后再进行处理,严禁带压操作,以免发生意外。
10、气密前,关闭系统所有安全阀的保护阀,待气密合格后再打开。
11、高压临氢系统气密时,低压临氢系统放空阀应打开,防止串压、超压。
12、严格控制升降压速度,一般升降压速度不大于1.0MPa/h,以防催化剂破损。
13、系统气密结束后,做好记录,相关人员共同确定并签字。
14、加热炉点火时,对流室通入过热蒸汽经消音器排空,同时E-203、E-202通冷却水。
15、250℃恒温时,对高压临氢系统各设备进行热紧。
16、当反应器开始升压时,在操作温度升至135℃以前,操作压力不得超过2.18MPa,同理当反应器降压时,操作压力降至2.18MPa 以前,其操作温度必须维持在135℃以上。
安徽 余春文--蜡油加氢开工过程及问题处理

蜡油加氢装置开工过程及问题处理余春文李继炳袁德明中国石化股份有限公司安庆分公司安徽安庆246001摘要:着重介绍了蜡油加氢装置反应系统的主要开工步骤,以及在开工过程中出现的主要问题及解决方法,为装置的一次试车成功提供了保障,同时优化了催化、裂解装置的原料性质,改善了全厂生产汽柴油生产方案。
关键词:蜡油加氢反应系统开工步骤问题方法前言2.2 Mt/a蜡油加氢装置是安庆石化8 Mt/a炼油扩建改造工程的配套主体装置之一,诣在满足公司含硫原油加工适应性改造及油品质量升级工程扩建后急剧增加的含硫蜡油处理量的需求,为即将新建的3 Mt/a催化裂化装置提供新鲜原料。
目前装置生产的精制蜡油作为现有1.2 Mt/a催化裂化装置和0.6 Mt/a催化裂解装置提供原料。
装置采用冷热高、低分流程,增设循环氢脱硫及低分气脱硫系统流程。
装置采用北京石油化工研究院(简称石科院)RVHT工艺技术进行设计,选用RN-32V 型催化剂作为主催化剂。
装置设计原料比例为:m(焦化蜡油):m(热直馏蜡油):m(冷直馏蜡油)=15.8:75.9:8.5。
生产硫含量1 200 μg/g以下,氮含量900 μg/g以下的催化裂化原料,副产少量柴油及石脑油。
装置于2009年7月28日高标准中交,10月17日一次试车成功,生产出硫含量低于1 000μg/g的合格产品,大大改善了催化裂化装置的原料性质,满足未来市场对低硫柴油供运的需求,优化了公司生产汽柴油加工方案。
1 装置开工主要步骤装置建成后,进入开工的起步阶段,各项工作稳步推进,除反应系统外,其余系统进行水冲洗、水联运。
针对公司氮气少的现状及降低开工成本,反应系统引入中压风(1.6 MPa)进行吹扫及气密,合格后引氮气置换,充压气密至反应系统的操作压力(11.04 MPa)。
1.1 催化剂装填装置用于加氢脱硫和脱氮的主催化剂为RMS-1和RN-32V催化剂,为减缓反应器顶部因沥青质、残炭等结焦前驱物遇热生焦造成主催化剂结焦,减少金属在主剂床层的沉积和尽可能促进沥青质解聚。
- 1、下载文档前请自行甄别文档内容的完整性,平台不提供额外的编辑、内容补充、找答案等附加服务。
- 2、"仅部分预览"的文档,不可在线预览部分如存在完整性等问题,可反馈申请退款(可完整预览的文档不适用该条件!)。
- 3、如文档侵犯您的权益,请联系客服反馈,我们会尽快为您处理(人工客服工作时间:9:00-18:30)。
安庆石化蜡油加氢装置开工过程及问题处理余春文,李继炳,袁德明(中国石化股份有限公司安庆分公司,安徽 安庆 246001)摘 要:着重介绍了蜡油加氢装置反应系统的主要开工步骤,以及在开工过程中出现的主要问题及解决方法,为装置的一次试车成功提供了保障,同时优化了催化、裂解装置的原料性质,改善了全厂生产汽柴油生产方案。
关键词:蜡油加氢;反应系统;开工步骤;问题;方法The Starti ng Process and Proble m s Solvi ng ofW ax O ilH ydrogenation Unit of Anqi ng Petroche m icalYU Chun -w en,LI J i -bing,YUAN D e -m ing (Anqing Co m pany ,SI N OPEC ,Anhu iAnq i n g 246001,Ch i n a)Abst ract :The w ax o il hydrogenation un it reacto r syste m of the m ajor starti n g step wasm ai n ly focused on .M any m a i nproble m s i n the starting step and the m easures w ere introduced .It prov ided a guarantee for the first starting process suc ceeded .The ra w m aterials of the catalytic unit and cracked un itw ere opti m ized .And the production progra m of the gaso li n e and d iese l opti o ns w as i m proved.K ey w ords :w ax o il hydrogenati o n ;reactor syste m ;startling steps ;prob le m ;m ethod作者简介:余春文(1966-),男,工程师,现从事炼油技术管理工作。
通讯作者:袁德明。
2.2M t a -1蜡油加氢装置是安庆石化8M t a -1炼油扩建改造工程的配套主体装置之一,诣在满足我厂含硫原油加工适应性改造及油品质量升级工程扩建后急剧增加的含硫蜡油处理量的需求,为即将新建的3M t a -1催化裂化装置提供新鲜原料。
目前装置生产的精制蜡油作为现有1.2M t a -1催化裂化装置和0.6M t a -1催化裂解装置提供原料。
装置采用冷热高、低分流程,增设循环氢脱硫及低分气脱硫系统流程。
装置采用北京石油化工研究院(简称石科院)RVHT 工艺技术进行设计,选用RN -32V 型催化剂作为主催化剂。
装置设计原料比例为:m (焦化蜡油):m (热直馏蜡油):m (冷直馏蜡油)=15.8 75.9 8.5。
生产硫含量1200 g g -1以下,氮含量900 g g -1以下的催化裂化原料,副产少量柴油及石脑油。
装置于2009年7月28日高标准中交,10月17日一次试车成功,生产出硫含量低于1000 g g -1的合格产品,大大改善了我厂催化裂化装置的原料性质,满足未来市场对低硫柴油供运的需求,优化了全厂生产汽柴油加工方案。
1 装置开工主要步骤装置建成后,进入开工的起步阶段,各项工作稳步推进,除反应系统外,其余系统进行水冲洗、水联运。
针对我厂氮气少的现状及降低开工成本,反应系统引入中压风(1 6M Pa)进行吹扫及气密,合格后引氮气置换,充压气密至反应系统的操作压力11 04M Pa 。
1.1 催化剂装填装置用于加氢脱硫和脱氮的主催化剂为RM S -1和RN -32V 催化剂,为减缓反应器顶部因沥青质、残炭等结焦前驱物遇热生焦造成主催化剂结焦,减少金属在主剂床层的沉积和尽可能促进沥青质的解聚。
在反应器上床层顶部依次装填RG -10系列保护剂,保护剂下装填部分大孔径RD M -2脱金属剂,针对我厂原料的沥青质含量偏高的特点,装填RG -10序列保护剂可有效降低进入主催化剂物流中金属、残炭和沥青质含量,减缓主催化剂的聚炭速率,延长装置运转周期(设计3年)。
本装置设一台反应器,反应器分三个催化剂床层,保护剂下装填RD M -2脱金属;二床层和三床层主要装填主催化剂RN -32V 。
所有催化剂均由石科院开发,中国石化催化剂长岭分公司生产。
催化剂装填工作于9月17~21日完成,装填工作相对比较顺利。
本次催化剂装填全采用普通装填法进行,主催化剂的物性见表1,装填数据见表2。
表1 主催化剂主要物化性质项目数据尺寸/w t % 1.3化学组成/w%WO 23.0M oO 3 2.3N i O2.3孔体积/(m L g -1) 0.24比表面积/(m 2 g -1) 150堆密度/(g c m-3)~0.95压碎强度/(N mm -1)18表2 反应器催化剂装填数据床层理论装填量实际装填量堆比装填物质高度/mm体积/m3高度/mm体积/m3重量/t g/c m3一床层料面到梁底25016013RG-102503.14240 3.012.50.8293 6RG-10A93011.6884010.555.40.5118 3.5RG-10B140017.58136017.089.60.5620 2.2RD M-2309238.84307038.5619.80.5135 3mm瓷球1001.26100 1.261.656mm瓷球1001.26100 1.261.525冷氢箱内构件二床层料面到梁底2502006mm瓷球1001.26100 1.261.752.2RD M-26808.5484010.555.20.4928 1.3RM S-1166520.91175021.98140.6369 1.3RN-32V563270.74527066.1966.030.9975 3mm瓷球1001.26100 1.261.6756mm瓷球1001.26100 1.261.5冷氢箱内构件三床层料面到梁底2501606mm瓷球1001.26100 1.261.7751.3RN-32V9789122.309690121.70121.971.0022 3mm瓷球1501502.86mm瓷球1501502.513mm瓷球高于收集器200高于收集器2004.75由表2可见:RG-10/RG-10A/RG-10B催化剂的装填堆比分别为0.82、0 51、0 56t/m3,RRD M-2催化剂在一床层的装填堆比为0 51t/m3,RN-32V在二床层和三床层的平均装填堆比约为1 00t/m3。
RN-32V催化剂在二、三床层的装填堆比相当,表明催化剂的装填过程较为均匀一致。
各催化剂实际装填堆比和理论值基本吻合,开工后径向温差小于3!,表明催化剂的装填过程控制较为理想。
1 2 催化剂干燥加氢催化剂具有吸水性,在运输、装填过程中吸收空气中的水分。
易使催化剂的机械强度降低,使其易破碎。
装置在9月24日开始催化剂干燥,26日结束,干燥用时43h,其中160!恒温阶段为20h。
干燥期间反应器入口压力为2 12~2 85M Pa(理论2 5M P a),循环气量111000~131000Nm3/h,气剂比为400v/v 左右。
此次干燥采用冷高分V6105初始垫水到界位一定高度,然后干燥,根据玻璃板高度计算干燥出水量,由于循环氢量较低,发现床层温度穿透速度缓慢,干燥期间,反应器下床层底部温度未达到150!,干燥结束,催化剂脱水不明显。
理论干燥曲线及实际干燥曲线见图1。
1 3 系统气密及紧急泄压试验1 3 1 反应系统气密催化剂干燥结束后,10月3日,系统引氮气置换,充压至15M Pa气密,合格后,撤压至微正压,4日引氢气,开新氢机气密升压至4 0M Pa检漏,处理。
图1 催化剂干燥曲线装置初次运行后再次开工,12Cr2M o1R(H)、12Cr2M o1锻材料在低温条件下回火脆化和氢脆破坏设备,在开工升压过程中,在设备温度不大于93!时,12C r2M o1R(H)、12Cr2M o1锻材料的设备应力应严格限制不大于20%设备材料的屈服极限,具体压力限制要求见表3[1]。
由于反应器使用的材质在高压下需要一定的温度,因此继续氢气升压前,要求点炉F6101升温,同时开循环机,温度控制在93!~120!,系统升压至8 0M P a,检查无漏点。
1 32 紧急泄压试验表3 开工升压时的压力限制设备名称部位限制压力/M Pa加氢反应器全部∀4 817热高压分离器全部∀4 83反应流出物/混合进料换热器(3台)管、壳程∀5 84为考察全厂火炬排放系统能力,进行一次事故状态的实际演练。
10月9日,进行8 0M Pa 紧急泄压实验,此次泄压准备充足,泄压时联锁按预期动作,火炬系统无明显位移,孔板经设计院核算能满足要求。
实验数据见表4。
实验结果表明:(1)8.0M P a 条件下,系统管网能承受目前的泄压速度,并未对火炬系统造成太大的冲击;(2)相关联锁动作正常;(3)经设计院核算,在系统压力达到11.0M P a 时,目前的孔板能够满足0 7M Pa /m i n 泄压要求,无需扩孔。
紧急泄压结束后,系统继续升压至11.0M Pa 进行气密。
表4 紧急泄压实验数据泄压时间/s 0153045607590105120135150165180系统压力/M Pa 7 987 917 857 787 727.667.67.537.487.427.367.37.24泄压速度/(M Pa/m i n)00.280.240.280.240.240.240.280.200.240.240.240.24反应器压降/M Pa1.4 催化剂预硫化催化剂硫化采用湿法硫化,具体操作过程按石科院提供的方案执行。
硫化剂用DM DS ,硫化油用常一线油。
10月12日系统引油后升至8.0M P a 、进油量提至1601t /h ,循环氢量控制在150000Nm 3/h 左右。
开始注硫化剂并升温,初始注硫量720kg /h 。
由于循环氢压缩机干气密封自增压系统问题(进出口差压小造成密封气压力小),床层停止升温并停止注硫。
经石科院确认,反应系统5.0M Pa 左右硫化。
主要操作条件为:系统(冷高分)压力:5.13M P;硫化油进料量:160t/h 循环氢量:110000~140000Nm 3/h ;反应器压降:0.15M P a 。
由于硫化阶段系统压力只有5.0M P a ,造成硫化剂分解产生甲烷占系统中气体比例较高,导致循环氢纯度下降。