万吨蜡油加氢裂化装置开工技术总结汇报
加氢裂化车间个人工作总结
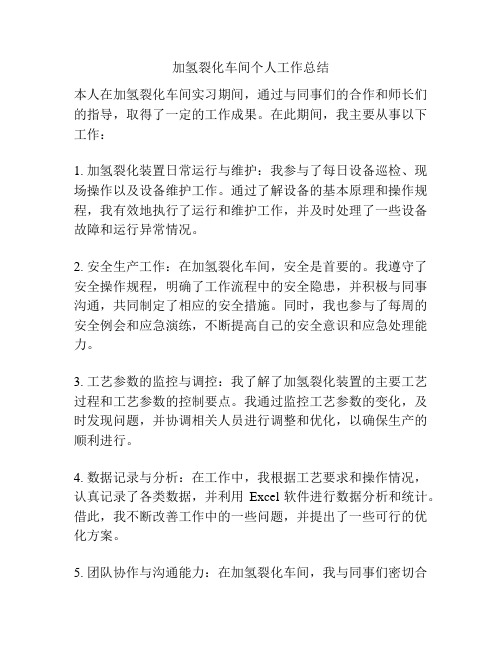
加氢裂化车间个人工作总结本人在加氢裂化车间实习期间,通过与同事们的合作和师长们的指导,取得了一定的工作成果。
在此期间,我主要从事以下工作:1. 加氢裂化装置日常运行与维护:我参与了每日设备巡检、现场操作以及设备维护工作。
通过了解设备的基本原理和操作规程,我有效地执行了运行和维护工作,并及时处理了一些设备故障和运行异常情况。
2. 安全生产工作:在加氢裂化车间,安全是首要的。
我遵守了安全操作规程,明确了工作流程中的安全隐患,并积极与同事沟通,共同制定了相应的安全措施。
同时,我也参与了每周的安全例会和应急演练,不断提高自己的安全意识和应急处理能力。
3. 工艺参数的监控与调控:我了解了加氢裂化装置的主要工艺过程和工艺参数的控制要点。
我通过监控工艺参数的变化,及时发现问题,并协调相关人员进行调整和优化,以确保生产的顺利进行。
4. 数据记录与分析:在工作中,我根据工艺要求和操作情况,认真记录了各类数据,并利用Excel软件进行数据分析和统计。
借此,我不断改善工作中的一些问题,并提出了一些可行的优化方案。
5. 团队协作与沟通能力:在加氢裂化车间,我与同事们密切合作,相互协助,共同完成了一系列工作任务。
在与他们的交流中,我学到了很多实际操作的技巧和经验,并且也积极与他们分享自己的心得和观点。
通过这段时间的实践与学习,我在加氢裂化车间的工作中逐渐提升了自己的专业能力和实践经验。
我学会了团队合作和沟通,提高了安全意识和应急处理能力。
我相信这些经验和收获将对我今后的工作起到积极的促进作用。
在未来的工作中,我将继续努力,不断提升自己的专业素养和实践能力,为加氢裂化车间的工作做出更大的贡献。
在加氢裂化车间的实习期间,我深入学习并参与了各种工作任务,获得了丰富的实践经验。
以下将对我在该车间的个人工作总结进行进一步描述。
首先,作为一个实习生,我非常重视日常工作的细节和规范操作。
我始终按照操作手册和安全操作规程进行工作,注重安全意识和工作质量。
装置开工工作总结

装置开工工作总结
在过去的一段时间里,我们团队一直在为新的装置开工工作而努力。
经过不懈
的努力和团队的协作,我们终于完成了这项任务。
在这个过程中,我们遇到了许多挑战,但也取得了许多成功。
现在,我想对我们的工作进行总结,以便我们能够更好地总结经验教训,为未来的工作做好准备。
首先,我们在规划阶段就遇到了很多问题。
我们需要考虑到装置的设计、材料
的采购、人员的安排等多个方面。
在这个阶段,我们遇到了很多困难,但通过团队的合作和沟通,我们最终找到了解决问题的方法。
我们学会了更加有效地分工合作,使得每个人都能够充分发挥自己的优势,从而提高了工作效率。
其次,在实施阶段,我们也遇到了很多挑战。
装置的制作需要精准的技术和耐
心的工作,而且还需要考虑到安全和环保等方面。
在这个阶段,我们不断进行试验和改进,最终成功地完成了装置的制作。
我们学会了在面对问题时不要轻易放弃,要不断尝试和改进,直到找到解决问题的方法。
最后,在验收阶段,我们也经历了一些波折。
由于装置的特殊性,我们需要进
行多次的测试和调整,以确保其能够正常运行。
在这个阶段,我们需要保持耐心和细心,不断进行检查和改进。
最终,我们成功地通过了验收,得到了领导和客户的认可。
总的来说,这次装置开工工作虽然充满了挑战,但我们团队最终取得了成功。
通过这次工作,我们学会了更加有效地合作,更加耐心地面对问题,更加细心地进行工作。
我相信,这些经验和教训将会对我们未来的工作产生积极的影响。
希望我们能够在未来的工作中继续保持团队精神和努力工作,为公司的发展做出更大的贡献。
燕山200万吨年加氢裂化装置开工总结

燕山200万吨年加氢裂化装置开工总结燕山200万吨/年加氢裂化装置开工总结1概述燕山200万吨/年加氢裂化装置设计加工进口原油的减压蜡油馏分和部分焦化蜡油,用于生产高质量的轻质油品和用作乙烯原料的尾油。
轻质产品包括作为车用汽油调和组分的轻石脑油,用于重整装置原料的高芳潜重石脑油,符合3号喷气燃料规格要求的煤油馏分,以及高十六烷值的清洁柴油馏分;尾油馏分是优质的乙烯原料,具有BMCI 值低、乙烯收率高的性质特点。
该装置的投产运行,将为燕山分公司在提高重油转化能力、生产清洁汽柴油以及优化乙烯原料等方面发挥重要作用。
本次开工的时间进度如下:2007年5月2日~11日进行催化剂装填;5月12日~15日氮气气密,5月15日~18日催化剂低温干燥;5月18日~28日氢气气密;5月29日~6月1日催化剂预硫化;6月16日催化剂钝化;6月18日切换新鲜VGO原料;6月20日操作调整基本到位,装置出合格产品。
2催化剂装填催化剂及瓷球的装填工作于5月2日始,至11日结束。
加氢裂化装置设两个反应器,分别为精制反应器R3101和裂化反应器R3102。
R3101分为三个催化剂床层,除一床层顶部装填部分保护催化剂RG-10B和RG-1外,其它床层装填精制催化剂RN-32。
R3101共装填RN-32精制催化剂288.9t,RG-10B保护剂5.7t,RG-1保护剂6.5t;裂化反应器R3102设四个催化剂床层,除四床层底部装填少量后精制催化剂RN-32(粗条)外,其余部分装填裂化催化剂RHC-1,R3102反应器共装填RHC-1裂化催化剂176.8t,RN-32(粗条)后精制催化剂21t。
两个反应器装填催化剂总量共498.9t。
精制催化剂装填堆比1.107 t/m3,裂化催化剂装填堆比为0.984 t/m3。
精制反应器R3101催化剂及瓷球实际装填情况列于表1。
裂化反应器R3102催化剂及瓷球实际装填情况列于表2。
3氮气气密催化剂装填结束后,于5月11日晚封反应器头盖,12日开始进行反应系统氮气置换、氮气气密。
金陵-卫建军-金陵分公司150万吨加氢裂化装置开工总结17

金陵分公司150万吨加氢裂化装置开工总结卫建军邢献杰(中国石化金陵分公司加氢裂化车间江苏南京210033)主题词加氢裂化FC-14催化剂硫化开工1 前言150万吨/年加氢裂化装置是“十五”金陵分公司1300万吨炼油改造项目的配套装置。
该装置由中国石化洛阳石油化工工程公司及金陵石化工程公司设计院共同设计,采用单段全循环加氢工艺,所用催化剂为抚顺石油化工研究院开发FF-16/FF-26加氢精制催化剂和FC-14单段加氢裂化催化剂,以沙特轻质蜡油和焦化蜡油的混合油为原料,生产航煤、柴油、液化气、轻石脑油和重石脑油。
该加氢裂化装置于2004年12月建成中交,2005年2月27日完成催化剂装填,3月21日开始进行催化剂预硫化,4月6日开始催化剂润湿和原料油切换,4月8日产品合格,装置一次投产成功。
2 催化剂装填金陵分公司150万吨/年加氢裂化装置催化剂装填于2005年2月23日开始,至2月27日结束,催化剂总装填量为267.02吨,其中FZC-100加氢保护剂1.78吨,FZC-102加氢保护剂2.55吨,FZC-103加氢保护剂3.99吨,FF-16加氢精制催化剂65.40吨,FF-26(φ3)加氢精制催化剂8.82吨,FF-26(φ1.2)加氢精制催化剂36.38吨,FF-14加氢裂化催化剂148.10吨。
各反应器具体装填情况见表1和表2。
表1 R1001催化剂装填表床层装填物装填高度/mm 体积/m3重量/kg 堆密度/kg.m-3一床层FZC-101 150 2.08 1777 854 FZC-102 450 6.23 2550 409FZC-103 600 8.31 3990 489FF-26粗条100 1.43 1140 797 FF-16 2615 36.22 28050 774 FF-26粗条170 2.35 1920 815Ф6瓷球55 0.76 1340 1759Ф13瓷球20 0.28 400 1444二床层Ф13瓷球80 0.80 1140 1425 FF-16 1400 18.00 14250 792FF-16 1871 27.30 23100 846FF-26 3149 39.19 36380 921 FF-26粗条200 2.38 1920 807Ф6瓷球80 1.09 1700 1560Ф13瓷球5600表2 R1002催化剂装填表床层装填物装填高度/mm 体积/m3重量/kg 堆密度/kg.m-3一床层Ф13瓷球100 1.36 2080 1529 FC-14 3860 53.46 47800 894Ф3瓷球80 1.10 1650 1500Ф6瓷球80 1.11 1200Ф13瓷球500二床层Ф13瓷球80 1.10 1720 1563 FC-14 3854 53.38 46600 873Ф3瓷球80 1.11 1660 1500Ф6瓷球80 1.11 1300Ф13瓷球400三床层Ф13瓷球80 1.01 1400 1386 FC-14 4524 60.03 53700 895 FF-26粗条306 4.24 3840 906Ф6瓷球100 2300Ф13瓷球6000表3 不同条件下反应器的径向温度分布一床层二床层三床层顶部中部底部顶部中部底部顶部中部底部硫化结束时的床层温度分布R1001床层温度分布(℃) 近端368.2 369.6 368.2 369.3 369.2中端368.1 369.3 368.3 369.5 369.4远端368.4 369.2 368.7 369.2 369.5R1002床层温度分布(℃) 近端369.1 366.9 366.5 367.8 367.2 365.2 365.1 364.3 365.2中端369.2 366.8 366.8 367.9 367.1 365.4 365.5 364.2 365.1远端369.3 367.1 366.7 367.5 367.4 365.2 365.5 364.5 365.4低负荷条件(反应进料110t/h)的床层温度分布R1001床层温度分布(℃) 近端353.8 361.4 361.5 367.6 375.0中端354.6 363.0 358.7 366.3 373.2远端354.9 361.4 361.1 367.0 373.6R1002床层温度分布(℃) 近端376.9 382.4 388.1 384.2 387.3 392.2 384.1 388.1 389.6中端379.4 380.5 386.4 384.6 387.3 389.5 385.1 386.3 389.4远端377.4 381.8 388.1 385.0 387.7 391.5 384.4 387.3 389.7高负荷条件(反应进料110t/h)的床层温度分布R1001床层温度分布(℃) 近端381.9 390.1 389.9 397.2 404.6中端381.6 390.8 389.0 397.7 404.4远端382.8 390.5 389.2 396.8 403.4R1002床层温度分布(℃) 近端404.5 409.3 412.4 406.8 408.9 415.2 406.0 410.7 412.4中端404.7 409.8 412.4 403.9 408.5 410.9 406.5 408.9 412.0远端404.5 409.3 413.6 407.6 407.2 415.8 405.2 409.5 411.7催化剂装填效果分析:(1)从3硫化结束时的床层温度分布可以看出,R1001、R1002各床层径向温差在0.1~0.5℃,说明反应器内因热电偶测量误差造成的床层径向温差很小,反应器内的热电偶是准确的。
加氢裂化车间个人工作总结
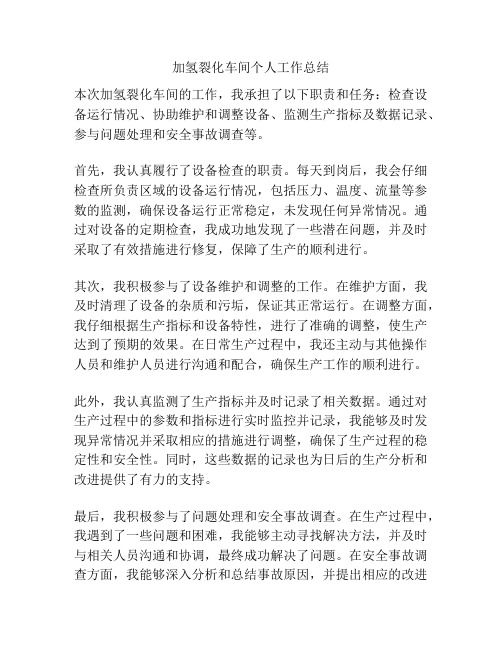
加氢裂化车间个人工作总结
本次加氢裂化车间的工作,我承担了以下职责和任务:检查设备运行情况、协助维护和调整设备、监测生产指标及数据记录、参与问题处理和安全事故调查等。
首先,我认真履行了设备检查的职责。
每天到岗后,我会仔细检查所负责区域的设备运行情况,包括压力、温度、流量等参数的监测,确保设备运行正常稳定,未发现任何异常情况。
通过对设备的定期检查,我成功地发现了一些潜在问题,并及时采取了有效措施进行修复,保障了生产的顺利进行。
其次,我积极参与了设备维护和调整的工作。
在维护方面,我及时清理了设备的杂质和污垢,保证其正常运行。
在调整方面,我仔细根据生产指标和设备特性,进行了准确的调整,使生产达到了预期的效果。
在日常生产过程中,我还主动与其他操作人员和维护人员进行沟通和配合,确保生产工作的顺利进行。
此外,我认真监测了生产指标并及时记录了相关数据。
通过对生产过程中的参数和指标进行实时监控并记录,我能够及时发现异常情况并采取相应的措施进行调整,确保了生产过程的稳定性和安全性。
同时,这些数据的记录也为日后的生产分析和改进提供了有力的支持。
最后,我积极参与了问题处理和安全事故调查。
在生产过程中,我遇到了一些问题和困难,我能够主动寻找解决方法,并及时与相关人员沟通和协调,最终成功解决了问题。
在安全事故调查方面,我能够深入分析和总结事故原因,并提出相应的改进
措施,确保类似事故不再发生。
通过这次加氢裂化车间的工作,我更加深入地理解了设备运行和生产管理的重要性。
在今后的工作中,我将进一步提升自己的技术能力和业务素质,更好地履行自己的职责,为车间的发展和生产效益做出更大的贡献。
加氢装置开工个人工作总结
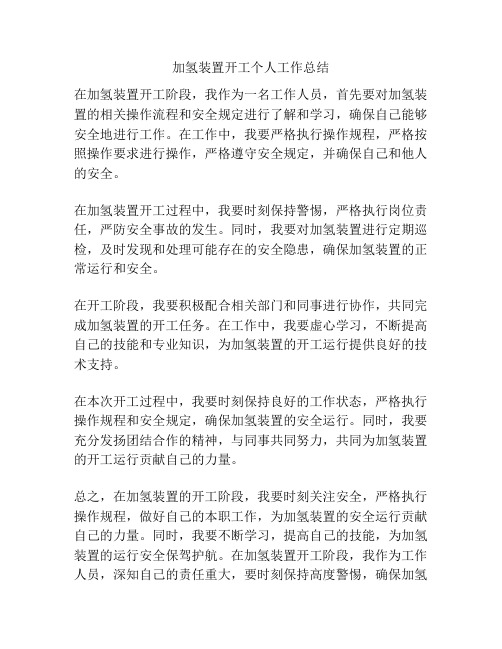
加氢装置开工个人工作总结在加氢装置开工阶段,我作为一名工作人员,首先要对加氢装置的相关操作流程和安全规定进行了解和学习,确保自己能够安全地进行工作。
在工作中,我要严格执行操作规程,严格按照操作要求进行操作,严格遵守安全规定,并确保自己和他人的安全。
在加氢装置开工过程中,我要时刻保持警惕,严格执行岗位责任,严防安全事故的发生。
同时,我要对加氢装置进行定期巡检,及时发现和处理可能存在的安全隐患,确保加氢装置的正常运行和安全。
在开工阶段,我要积极配合相关部门和同事进行协作,共同完成加氢装置的开工任务。
在工作中,我要虚心学习,不断提高自己的技能和专业知识,为加氢装置的开工运行提供良好的技术支持。
在本次开工过程中,我要时刻保持良好的工作状态,严格执行操作规程和安全规定,确保加氢装置的安全运行。
同时,我要充分发扬团结合作的精神,与同事共同努力,共同为加氢装置的开工运行贡献自己的力量。
总之,在加氢装置的开工阶段,我要时刻关注安全,严格执行操作规程,做好自己的本职工作,为加氢装置的安全运行贡献自己的力量。
同时,我要不断学习,提高自己的技能,为加氢装置的运行安全保驾护航。
在加氢装置开工阶段,我作为工作人员,深知自己的责任重大,要时刻保持高度警惕,确保加氢装置的安全运行。
在工作中,我要严格按照操作规程进行操作,确保操作步骤的准确性和规范性。
同时,我要认真履行岗位职责,积极主动地发现和处理可能存在的问题,确保加氢装置的运行安全稳定。
为了保证加氢装置的运行状态,我要进行定期巡检和维护工作,及时发现和解决可能存在的故障和问题。
在开工阶段,特别要注意加氢装置的相关设备和管道是否存在泄漏、腐蚀等现象,及时进行维修和更换,确保设备的正常运行。
在加氢装置开工的过程中,我要密切配合相关部门和同事进行协作,共同努力完成加氢装置的开工任务。
在工作中,我要主动沟通,及时交流工作进展和问题,确保工作的顺利进行。
同时,我也要尊重和支持同事,发挥团队合作精神,共同为加氢装置的开工运行贡献自己的力量。
加氢裂化装置技术改造及开工总结

425. 83 t,其中保护剂 23. 47 t,精制剂 224. 7 t,裂 化剂 159. 26 t,后精制剂 18. 4 t,具体装填情况见 表 1。
催化剂
精制反应器第一床层 KG-55 KF-542-9R KG9-5R KFR-22-3Q KF-648-3Q KF-848-1. 3Q UF-210( 库存剂) KF-648-3Q
2 催化剂干燥 绝大数加氢催化剂都以氧化铝或含硅氧化铝
作为载体,属多孔物质,吸水性很强,一般吸水量 可达 1% ~ 3% ,最高可达 5% 以上。催化剂含水 有如下危害: 当潮湿的催化剂与热的油气接触升 温时,其中所含水迅速汽化,导致催化剂孔道内水 汽压力急剧上升,容易引起催化剂骨架结构被挤 压崩塌[1]。
2018 年 6 月 22 日,反应系统采用 4. 0 MPa 氮气进行催化剂干燥,反应器入口温度 120 ℃ ,由 于受加氢精制催化剂 UF-210 配方限制,进入反应 器床层的开工油温度只能低于 140 ℃ ,当 UF-210 全部润湿以后,床层温度可以升至 200 ℃ 。整个 催化剂干燥过程为 48 h,冷高分界位切水 4 次,大 约 3. 0 t,为催化剂装填总量的 0. 7% ,催化剂干燥 趋势见图 1。
加氢裂化装置技术改造及开工总结
童 军,黎臣麟,武宝平,姚 峰,公为军
( 中国石油四川石化有限责任公司,四川省成都市 611930)
摘要: 为了提高重石脑油与喷气燃料收率,并将柴油组分切入尾油,进一步降低柴汽比,增产优质乙烯原料,中 国石油四川石化有限责任公司对 2. 70 Mt / a 加氢裂化装置进行技术改造,采用中国石油化工股份有限公司石油化 工科学研究院开发的多产化工原料和喷气燃料的加氢裂化技术并配套加氢精制剂 RN-410、加氢裂化催化剂 RHC210 与 RHC-220 组合,产品质量得到明显改善,重石脑油芳烃潜含量达到 60% ; 喷气燃料烟点达到30. 5 mm,比上周 期初期喷气燃料烟点高 5 mm,喷气燃料收率达到 35% ,在当前转化率下就达到了设计值; 尾油BMCI为 11. 45,比上 周期初期降低 3 个单位,因尾油中含有 50% 以上的柴油组分,降低了尾油立方平均沸点,导致尾油 BMCI 偏高,当前 密度下,如果尾油 10% 点切到 320 ℃ ,尾油 BMCI 可降到 8. 3 左右。
蜡油加氢装置技术分析报告

关于在技术人员中开展装置分析工作的通知各部门:充分了解和掌握自己分管装置的技术实情是技术人员管理、优化装置技术工作的基础。
为透彻分析装置的技术现状、进一步寻找与国内外同类装置之间的差距,学习先进理念和先进技术,启迪管理思路,更好地营造学习技术的氛围。
经研究,决定在技术人员中开展装置分析工作。
一、对象:已转正上岗的装置工艺员、设备员(包括后备)以及公用工程作业区和储运部技术员(包括后备)。
二、要求:1.年底前,技术人员完成对自己分管装置的详细技术分析报告。
内容包括本装置在工艺、设备、能耗、产品质量、管理等方面的现状,与国内同类装置之间的比对,查找存在的差距,改进需落实的具体措施等。
2.有条件的,可到国内同类装置进行外出调研,带去问题或疑惑,带回体会与启发。
3.年终事业部举行技术分析报告演示交流,表彰优秀报告。
三、时间安排:1.7月份布置工作、宣传工作开展的意义。
2.8、9月份创造条件外出调研。
3.11月底前完成分析报告。
4.12月底前组织审阅报告、演示交流、表彰优秀报告。
望各部门接到通知后,组织广泛宣传,切实推进装置分析工作。
部门行政主要领导要创造条件,扶持技术人员落实这项工作;充分利用事业部专业技术小组资源,帮助联系落实外出调研单位,确保这项工作有序开展。
注:1、装置分析报告提纲见附件一、附件二。
2、公用工程、储运部装置分析报告提纲参考附件一、附件二。
炼油事业部2007年7月27日附件二:2#汽柴油加氢装置技术分析报告(设备)1.装置概况上海高桥分公司到2007年以后除了加工大庆原油、海洋原油等低硫原油外,将主要加工含硫2.0%左右的含硫含酸进口原油。
由于常减压生产的减压蜡油和延迟焦化装置生产的焦化蜡油中含有较多的不饱和烃及硫、氮等有害的非烃化合物,这些产品无法达到催化裂化装置的要求。
为此,必须对焦化蜡油和减压蜡油进行加氢精制。
上海高桥分公司炼油事业部进行原油适应性改造时,将原100万吨/年柴油加氢精制装置改造为100万吨/年蜡油加氢装置,主要是为了催化裂化装置降低原料的硫含量和酸度服务。
万吨加氢裂化装置开工总结

数量 1
7 1
2
1
生产厂家 中国第一重型机械(集团) 有限责任公司 兰州石化机械厂 沈阳鼓风机厂 杭州汽轮机股份有限公司 德国NEA公司 南阳防爆集团有限公司
德国FLOWSERVE公司
1 德国FLOWSERVE公司 佳木斯电机
2 加拿大David Brown泵业
1 美国Ronningen-Petter Filters
独山子石化
反应器直径为4000mm,对装填工作要求较高,采取 固定料斗内催化剂量、固定料斗后进行标高测量、人工 下反应器检查、随时计算装填密度等方法,严格规范装 填作业;由于密相装填器的不稳定性和异常故障,影响 了催化剂的装填速度,但经过20天的工作,顺利完成催 化剂装填工作。从实际装填数据分析,各类催化剂的装 填量、装填密度与理论值相比误差均在0.8%以内,很好 地完成了催化剂装填工作。
独山子石化
200万吨/年加氢裂化装置 开工总结
花小兵
独山子石化
一、概述
独山子石化
1、装置主要设计特点 1.1反应部分采用一次通过流程,一台反应器,热壁结构,设 五个床层。精制催化剂选用UF210STARS,裂化剂选用含少量分 子筛的无定形硅铝复合型DHC-32LT催化剂,无后精制催化剂; 开工催化剂采用湿法硫化。 1.2采用热高分工艺,提高反应流出物的热能利用率,避免稠 环芳烃在冷却器中沉积和堵塞。一台原料泵设置热高分液力 透平驱动,降低能耗,节省操作费用。 1.3采用炉后混油流程,加热炉只加热循环氢,避免反应油气 两相炉内分配不均匀和原料油结焦,还可以降低系统压力降。 1.4 原料油采用美国RP自动反冲洗过滤器,滤去>25um的固体 杂质。
独山子石化
1.5 催化剂采用密相装填、内构件采用UOP公司专利技术, 有利于减小反应器的径向温差,消除局部过热现象,提高 催化剂的利用率。 1.6 每个裂化床层底部均设置22支多点热电偶,外表面反 应器设置器壁监控热电偶80支,这些热电偶均一选一参与 装置2.1MPa/min 紧急泄压联锁。 1.7 循环氢加热炉支路流量控制采用了经典的支路平衡控 制;加热炉出口温度控制采用交叉限幅控制,反应压力采 用三返一、高选控制。 1.8 采用汽提塔工艺,保证塔底物流不含硫化氢,避免后 续设备的腐蚀;产品分馏塔设侧线柴油汽提塔,设置重柴、 轻柴两个循环回流回收热量。
蜡油加氢裂化装置检修开工总结-2014
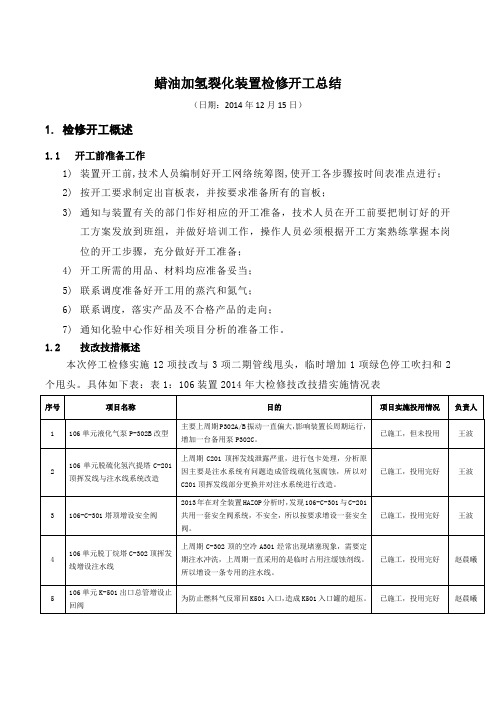
蜡油加氢裂化装置检修开工总结(日期:2014年12月15日)1.检修开工概述1.1开工前准备工作1)装置开工前,技术人员编制好开工网络统筹图,使开工各步骤按时间表准点进行;2)按开工要求制定出盲板表,并按要求准备所有的盲板;3)通知与装置有关的部门作好相应的开工准备,技术人员在开工前要把制订好的开工方案发放到班组,并做好培训工作,操作人员必须根据开工方案熟练掌握本岗位的开工步骤,充分做好开工准备;4)开工所需的用品、材料均应准备妥当;5)联系调度准备好开工用的蒸汽和氮气;6)联系调度,落实产品及不合格产品的走向;7)通知化验中心作好相关项目分析的准备工作。
1.2技改技措概述本次停工检修实施12项技改与3项二期管线甩头,临时增加1项绿色停工吹扫和2个甩头。
具体如下表:表1:106装置2014年大检修技改技措实施情况表1.3装置开工计划及总体安排106单元2014年停工检修在10月13日0点开始,10月22日交付检修,检修在12月24 日结束,12月25日检修交付生产,装置开始进入开工阶段,装置开工计划15天,5天是三查四定、机组试机、装置吹扫气密准备时间,10天正式开工时间,装置计划是在12月10日生产正常。
总体安排如下表:表2:106单元开工节点安排表2.开工方案的执行与变更情况本次装置开工过程严格按照开工方案来消项操作,由于本次大检修的技改项目较多,针对这些技改项目编写了对应的投用方案和消项卡。
本次开工时间较长用时15天,比2011年检修开工增加了3-4天时间。
本次开工气密工作和油运工作做得时间较长。
方案较大变更主要有以下几个方面:(1)反应系统N2气密,原方案是要求做到10.0MPa,实际只做到8.0MPA,因为受K101出口温度影响,在氮气工况只能承受到8.0MPa,以后开工方案中反应系统N2气密最高压力修改为8.0 MPa。
(2)根据shell催化剂专家建议预硫化末期要在330度恒温4小时,然后升温到345度就结束预硫化,根据当时反应催化剂床层温度情况,预硫化末期床层温度在240度恒温6小时后就结束预硫化,没有按方案升温至350度恒温4小时。
蜡油加氢工艺装置工艺优化开工总结
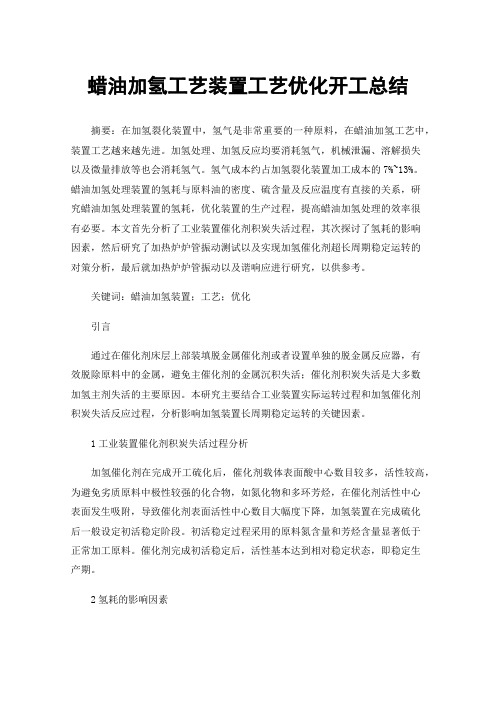
蜡油加氢工艺装置工艺优化开工总结摘要:在加氢裂化装置中,氢气是非常重要的一种原料,在蜡油加氢工艺中,装置工艺越来越先进。
加氢处理、加氢反应均要消耗氢气,机械泄漏、溶解损失以及微量排放等也会消耗氢气。
氢气成本约占加氢裂化装置加工成本的7%~13%。
蜡油加氢处理装置的氢耗与原料油的密度、硫含量及反应温度有直接的关系,研究蜡油加氢处理装置的氢耗,优化装置的生产过程,提高蜡油加氢处理的效率很有必要。
本文首先分析了工业装置催化剂积炭失活过程,其次探讨了氢耗的影响因素,然后研究了加热炉炉管振动测试以及实现加氢催化剂超长周期稳定运转的对策分析,最后就加热炉炉管振动以及谐响应进行研究,以供参考。
关键词:蜡油加氢装置;工艺;优化引言通过在催化剂床层上部装填脱金属催化剂或者设置单独的脱金属反应器,有效脱除原料中的金属,避免主催化剂的金属沉积失活;催化剂积炭失活是大多数加氢主剂失活的主要原因。
本研究主要结合工业装置实际运转过程和加氢催化剂积炭失活反应过程,分析影响加氢装置长周期稳定运转的关键因素。
1工业装置催化剂积炭失活过程分析加氢催化剂在完成开工硫化后,催化剂载体表面酸中心数目较多,活性较高,为避免劣质原料中极性较强的化合物,如氮化物和多环芳烃,在催化剂活性中心表面发生吸附,导致催化剂表面活性中心数目大幅度下降,加氢装置在完成硫化后一般设定初活稳定阶段。
初活稳定过程采用的原料氮含量和芳烃含量显著低于正常加工原料。
催化剂完成初活稳定后,活性基本达到相对稳定状态,即稳定生产期。
2氢耗的影响因素(1)溶解损失。
氢气在循环过程中,有一部分会溶解在热高压分离器(简称热高分)和冷高压分离器(简称冷高分)的液相中,称之为溶解损失。
相关研究文献指出,热高分温度180℃和240℃是2个拐点。
180℃左右,循环氢的体积分数最低,温度高于180℃后,随着温度的升高,循环氢的体积分数逐渐增加;温度超过240℃后,循环氢体积分数的增加趋势变缓。
蜡油加氢装置工业运行总结
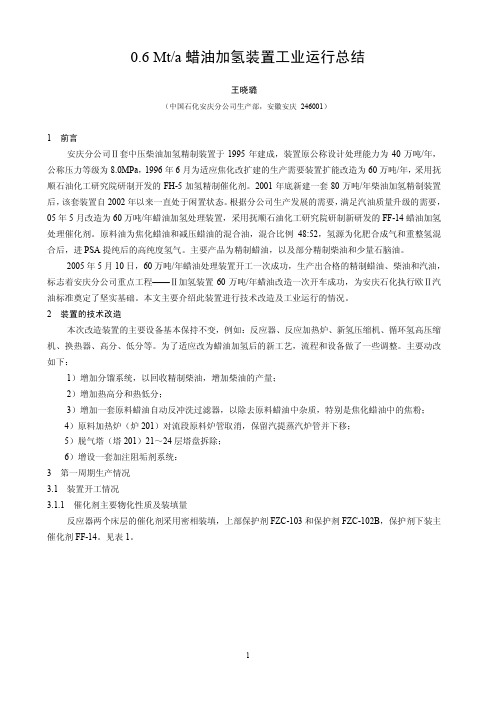
0.6 Mt/a蜡油加氢装置工业运行总结王晓璐(中国石化安庆分公司生产部,安徽安庆246001)1 前言安庆分公司Ⅱ套中压柴油加氢精制装置于1995年建成,装置原公称设计处理能力为40万吨/年,公称压力等级为8.0MPa,1996年6月为适应焦化改扩建的生产需要装置扩能改造为60万吨/年,采用抚顺石油化工研究院研制开发的FH-5加氢精制催化剂。
2001年底新建一套80万吨/年柴油加氢精制装置后,该套装置自2002年以来一直处于闲置状态。
根据分公司生产发展的需要,满足汽油质量升级的需要,05年5月改造为60万吨/年蜡油加氢处理装置,采用抚顺石油化工研究院研制新研发的FF-14蜡油加氢处理催化剂。
原料油为焦化蜡油和减压蜡油的混合油,混合比例48:52,氢源为化肥合成气和重整氢混合后,进PSA提纯后的高纯度氢气。
主要产品为精制蜡油,以及部分精制柴油和少量石脑油。
2005年5月10日,60万吨/年蜡油处理装置开工一次成功,生产出合格的精制蜡油、柴油和汽油,标志着安庆分公司重点工程——Ⅱ加氢装置60万吨/年蜡油改造一次开车成功,为安庆石化执行欧Ⅱ汽油标准奠定了坚实基础。
本文主要介绍此装置进行技术改造及工业运行的情况。
2 装置的技术改造本次改造装置的主要设备基本保持不变,例如:反应器、反应加热炉、新氢压缩机、循环氢高压缩机、换热器、高分、低分等。
为了适应改为蜡油加氢后的新工艺,流程和设备做了一些调整。
主要动改如下:1)增加分馏系统,以回收精制柴油,增加柴油的产量;2)增加热高分和热低分;3)增加一套原料蜡油自动反冲洗过滤器,以除去原料蜡油中杂质,特别是焦化蜡油中的焦粉;4)原料加热炉(炉201)对流段原料炉管取消,保留汽提蒸汽炉管并下移;5)脱气塔(塔201)21~24层塔盘拆除;6)增设一套加注阻垢剂系统:3 第一周期生产情况3.1 装置开工情况3.1.1 催化剂主要物化性质及装填量反应器两个床层的催化剂采用密相装填,上部保护剂FZC-103和保护剂FZC-102B,保护剂下装主催化剂FF-14。
两段全循环加氢裂化装置修复开工总结
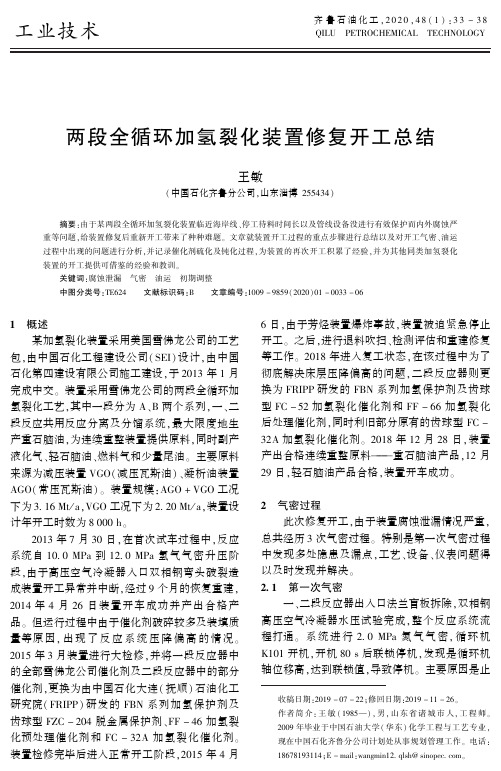
过程中出现的问题进行分析ꎬ并记录催化剂硫化及钝化过程ꎬ为装置的再次开工积累了经验ꎬ并为其他同类加氢裂化
装置的开工提供可借鉴的经验和教训ꎮ
关键词:腐蚀泄漏 气密 油运 初期调整
中图分类号:TE624 文献标识码:B 文章编号:1009 - 9859(2020)01 - 0033 - 06
2 气密过程
AGO( 常压瓦斯油) ꎮ 装置规模:AGO + VGO 工况
计年开工时数为 8 000 hꎮ
2013 年 7 月 30 日ꎬ在首次试车过程中ꎬ反应
系统自 10 0 MPa 到 12 0 MPa 氢气气密升 压 阶
段ꎬ由于高压空气冷凝器入口双相钢弯头破裂造
此次修复开工ꎬ由于装置腐蚀泄漏情况严重ꎬ
型 FC - 52 加氢裂化催化剂和 FF - 66 加氢裂化
32A 加氢裂化催化剂ꎮ 2018 年 12 月 28 日ꎬ装置
产出合格连续重整原料———重石脑油产品ꎬ12 月
来源为减压装置 VGO( 减压瓦斯油) 、凝析油装置
29 日ꎬ轻石脑油产品合格ꎬ装置开车成功ꎮ
下为 3 16 Mt / aꎬVGO 工况下为 2 20 Mt / aꎬ装置设
12 0 MPa、13 6 MPa 等级ꎮ 在向 13 6 MPa 等级升
表 PI266 引压管崩出ꎬ现场紧急处理ꎬ停止升压ꎮ
兰均为人 工ꎬ 未 使 用 液 压 扳 手) ꎬ 系 统 充 压 过 程
防喘振线进入法兰密封面中ꎮ 发现泄漏再次紧固
完成中交ꎮ 装置采用雪佛龙公司的两段全循环加
换为 FRIPP 研发的 FBN 系列加氢保护剂及齿球
催化裂化操作工开工总结
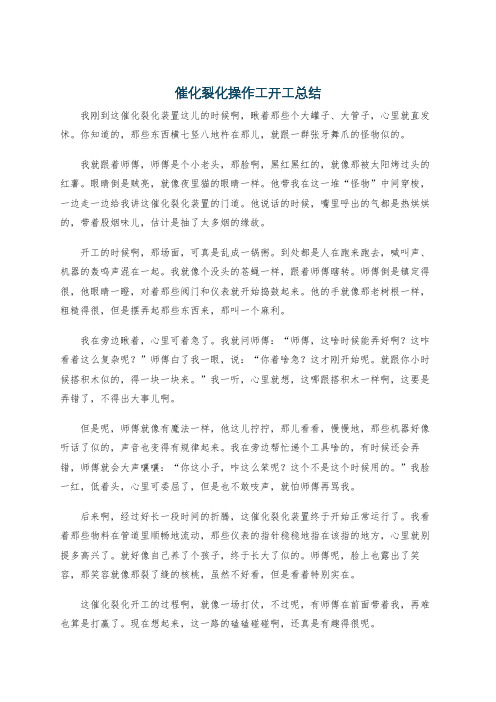
催化裂化操作工开工总结我刚到这催化裂化装置这儿的时候啊,瞅着那些个大罐子、大管子,心里就直发怵。
你知道的,那些东西横七竖八地杵在那儿,就跟一群张牙舞爪的怪物似的。
我就跟着师傅,师傅是个小老头,那脸啊,黑红黑红的,就像那被太阳烤过头的红薯。
眼睛倒是贼亮,就像夜里猫的眼睛一样。
他带我在这一堆“怪物”中间穿梭,一边走一边给我讲这催化裂化装置的门道。
他说话的时候,嘴里呼出的气都是热烘烘的,带着股烟味儿,估计是抽了太多烟的缘故。
开工的时候啊,那场面,可真是乱成一锅粥。
到处都是人在跑来跑去,喊叫声、机器的轰鸣声混在一起。
我就像个没头的苍蝇一样,跟着师傅瞎转。
师傅倒是镇定得很,他眼睛一瞪,对着那些阀门和仪表就开始捣鼓起来。
他的手就像那老树根一样,粗糙得很,但是摆弄起那些东西来,那叫一个麻利。
我在旁边瞅着,心里可着急了。
我就问师傅:“师傅,这啥时候能弄好啊?这咋看着这么复杂呢?”师傅白了我一眼,说:“你着啥急?这才刚开始呢。
就跟你小时候搭积木似的,得一块一块来。
”我一听,心里就想,这哪跟搭积木一样啊,这要是弄错了,不得出大事儿啊。
但是呢,师傅就像有魔法一样,他这儿拧拧,那儿看看,慢慢地,那些机器好像听话了似的,声音也变得有规律起来。
我在旁边帮忙递个工具啥的,有时候还会弄错,师傅就会大声嚷嚷:“你这小子,咋这么笨呢?这个不是这个时候用的。
”我脸一红,低着头,心里可委屈了,但是也不敢吱声,就怕师傅再骂我。
后来啊,经过好长一段时间的折腾,这催化裂化装置终于开始正常运行了。
我看着那些物料在管道里顺畅地流动,那些仪表的指针稳稳地指在该指的地方,心里就别提多高兴了。
就好像自己养了个孩子,终于长大了似的。
师傅呢,脸上也露出了笑容,那笑容就像那裂了缝的核桃,虽然不好看,但是看着特别实在。
这催化裂化开工的过程啊,就像一场打仗,不过呢,有师傅在前面带着我,再难也算是打赢了。
现在想起来,这一路的磕磕碰碰啊,还真是有趣得很呢。
加氢裂化车间年度总结(3篇)

第1篇一、前言过去的一年,我国加氢裂化行业在政策支持、市场需求和技术创新等多重因素推动下,取得了显著的成绩。
本年度,我车间紧紧围绕公司战略目标,紧密围绕安全生产、技术改造、节能减排等方面,全面推进各项工作,现将年度总结如下:一、安全生产1. 严格落实安全生产责任制,强化安全生产教育培训,提高员工安全意识。
2. 加强设备管理,定期进行设备维护保养,确保设备安全稳定运行。
3. 深入开展隐患排查治理,及时消除安全隐患,确保生产安全。
4. 严格执行操作规程,加强现场管理,降低事故发生率。
二、技术改造1. 优化生产工艺,提高装置运行效率。
2. 引进先进技术,提升装置产能。
3. 推进节能减排,降低生产成本。
4. 加强技术创新,提高产品质量。
三、节能减排1. 优化能源结构,提高能源利用率。
2. 加强废水、废气处理,减少污染物排放。
3. 推广清洁生产技术,降低污染物排放。
4. 强化节能减排宣传教育,提高全员节能减排意识。
四、团队建设1. 加强人才培养,提高员工综合素质。
2. 深化内部交流,促进知识共享。
3. 增强团队凝聚力,激发员工积极性。
4. 举办各类活动,丰富员工业余生活。
五、市场拓展1. 深入挖掘市场潜力,拓展销售渠道。
2. 加强与客户沟通,提高客户满意度。
3. 优化产品结构,提升市场竞争力。
4. 积极参与行业交流,提升品牌知名度。
六、展望未来新的一年,我车间将继续秉承“安全第一、质量至上、创新驱动、绿色发展”的理念,紧紧围绕公司战略目标,不断提升安全生产、技术改造、节能减排等方面的水平,为公司发展贡献力量。
1. 深化安全生产管理,确保生产安全稳定运行。
2. 加快技术改造步伐,提升装置产能和效率。
3. 持续推进节能减排,降低生产成本。
4. 加强团队建设,提高员工综合素质。
5. 拓展市场,提升品牌知名度。
总之,我车间将以更加饱满的热情、更加务实的作风,为实现公司战略目标而努力奋斗。
第2篇一、前言2021年,加氢裂化车间在公司领导的正确指导下,紧紧围绕安全生产、技术进步、节能减排等中心工作,以技术创新为动力,以安全生产为前提,以经济效益为目标,全体员工团结一心,顽强拼搏,圆满完成了全年各项工作任务。
270万吨_年蜡油加氢裂化装置开工总结
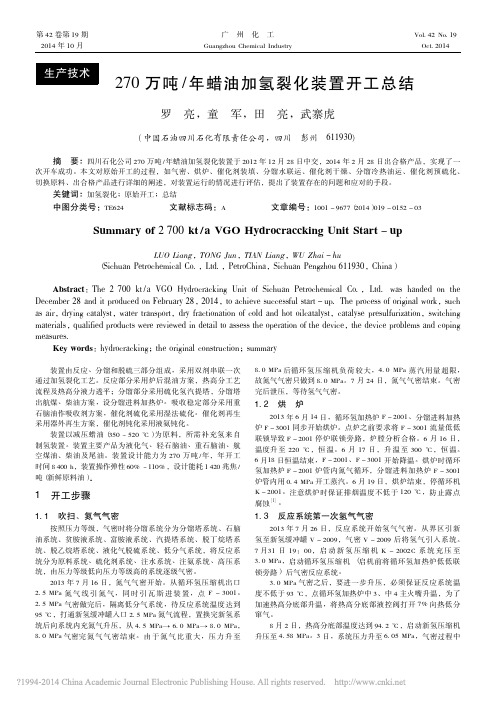
2013 年 7 月 26 日,反应系统开始氢气气密 。 从界区引新 氢至新氢缓冲罐 V - 2009 ,气密 V - 2009 后将氢气引入系统。 7 月31 日 19 : 00 ,启 动 新 氢 压 缩 机 K - 2002C 系 统 充 压 至 3. 0 MPa,启动循环氢压缩机 ( 启机前将循环氢加热炉低低联 锁旁路) 后气密反应系统。 3. 0 MPa 气密之后,要进一步升压,必须保证反应系统温 度不低于 93 ℃ ,点循环氢加热炉中 3 、中 4 主火嘴升温,为了 加速热高分底部升温,将热高分底部液控阀打开 7% 向热低分 窜气。 8 月 2 日,热高分底部温度达到 94. 2 ℃ ,启动新氢压缩机 升压至 4. 58 MPa。3 日,系统压力升至 6. 05 MPa,气密过程中
装置由反应、分馏和脱硫三部分组成,采用双剂串联一次 通过加氢裂化工艺。反应部分采用炉后混油方案,热高分工艺 流程及热高分液力透平; 分馏部分采用硫化氢汽提塔,分馏塔 出航煤、柴油方案,设分馏进料加热炉。 吸收稳定部分采用重 石脑油作吸收剂方案,催化剂硫化采用湿法硫化 。 催化剂再生 采用器外再生方案,催化剂钝化采用液氨钝化 。 装置以减压蜡油( 350 ~ 520 ℃ ) 为原料,所需补充氢来自 制氢装置。装置主要产品为液化气 、 轻石脑油、 重石脑油、 航 空煤油、柴油及尾油。 装置设计能力为 270 万吨 / 年,年开工 时间 8 400 h,装置操作弹性 60% ~ 110% ,设计能耗 1 420 兆焦 / 吨( 新鲜原料油) 。 8. 0 MPa 后循环氢压缩机负荷较大,4. 0 MPa 蒸汽用量超限, 故氮气气密只做到 8. 0 MPa。7 月 24 日,氮气气密结束。 气密 完后泄压,等待氢气气密。
广 州 化 工 Guangzhou Chemical Industry
蜡油加氢装置技术分析报告

关于在技术人员中开展装置分析工作的通知各部门:充分了解和掌握自己分管装置的技术实情是技术人员管理、优化装置技术工作的基础。
为透彻分析装置的技术现状、进一步寻找与国内外同类装置之间的差距,学习先进理念和先进技术,启迪管理思路,更好地营造学习技术的氛围。
经研究,决定在技术人员中开展装置分析工作。
一、对象:已转正上岗的装置工艺员、设备员(包括后备)以及公用工程作业区和储运部技术员(包括后备)。
二、要求:1.年底前,技术人员完成对自己分管装置的详细技术分析报告。
内容包括本装置在工艺、设备、能耗、产品质量、管理等方面的现状,与国内同类装置之间的比对,查找存在的差距,改进需落实的具体措施等。
2.有条件的,可到国内同类装置进行外出调研,带去问题或疑惑,带回体会与启发。
3.年终事业部举行技术分析报告演示交流,表彰优秀报告。
三、时间安排:1.7月份布置工作、宣传工作开展的意义。
2.8、9月份创造条件外出调研。
3.11月底前完成分析报告。
4.12月底前组织审阅报告、演示交流、表彰优秀报告。
望各部门接到通知后,组织广泛宣传,切实推进装置分析工作。
部门行政主要领导要创造条件,扶持技术人员落实这项工作;充分利用事业部专业技术小组资源,帮助联系落实外出调研单位,确保这项工作有序开展。
注:1、装置分析报告提纲见附件一、附件二。
2、公用工程、储运部装置分析报告提纲参考附件一、附件二。
炼油事业部2007年7月27日附件二:2#汽柴油加氢装置技术分析报告(设备)1.装置概况上海高桥分公司到2007年以后除了加工大庆原油、海洋原油等低硫原油外,将主要加工含硫2.0%左右的含硫含酸进口原油。
由于常减压生产的减压蜡油和延迟焦化装置生产的焦化蜡油中含有较多的不饱和烃及硫、氮等有害的非烃化合物,这些产品无法达到催化裂化装置的要求。
为此,必须对焦化蜡油和减压蜡油进行加氢精制。
上海高桥分公司炼油事业部进行原油适应性改造时,将原100万吨/年柴油加氢精制装置改造为100万吨/年蜡油加氢装置,主要是为了催化裂化装置降低原料的硫含量和酸度服务。
泉州加氢裂化开工总结

广东石化
2.1 实习过程
4月16日开始对室内DCS流程、SIS、ESD的学习 和熟悉,结合现场学习与其他装置不同的流程和 设备,重点学习循环氢脱硫系统、石脑油脱硫系 统的流程系统、系统压力控制的调节。学习了开 工收油流程、长、短循环流程。 开工收油流程: 开工柴油 聚结器 原料虑前罐 原料升压泵 热低分 汽提塔 闪蒸罐 分馏塔 冷低分
序 试车内容 号
起始时间
1
2 3
设备水压试验
单机试运
2014年4月12 日
2014年4月20 日
2014年5月10 日
2014年5月15 日 2014年5月15 日 2014年5月15 日 2014年5月15 日
28天
25天 30天
高压换热器E111A/B内漏
多台机泵振动大
堵管束, 换垫片
拆检并返 厂
3
新氢压 缩机A/B
压缩比过大 三个逐级返回 线设计过小, 且无跨线
4
反应注 水泵A/B
贫胺液A 泵
机封泄漏
机封本身问题
更换新机封
5
日本嘉利
联锁停机
仪表信号不准,处仪表问题仪表
广东石化 2重要设备出现的问题
序号 6 设备名称 预闪蒸罐底B泵 厂家 开工中出现的问题 振动大 原因 解决方案 管线应力大, 减少管线应 泵本体缺陷 力 反厂修理 机泵本身有 缺陷 A3根管束漏 B垫片 • 2014年4月1日加氢裂化装置对循环水管线进行冲洗, 配合全厂进行循环水系统预膜处理。 循环机,新氢机, 原料泵,贫胺泵等润滑油系统跑 油完毕,4月3开始对原料泵和循环油泵电机进行单机试 运,4月11日对循氢机润滑油泵联锁进行测试,在机组 联锁等条件满足的情况下4月17日开始对汽轮机试机,5 月7日循氢机空负荷试机,试机结束后安装正式密封, 在汽轮机试运中发现汽轮机震动大,转速在500转/秒, 1500转/秒时的振动都较高曲线,初次判断是热应力过 大,处理后未出现好转,后判断叶轮局部不圆,轴可能 有磁化点,后返厂处理转子回装后振动正常。在装循氢 机入口过滤器时施工人员将方向装反,操作工及时发现 重新回装。
- 1、下载文档前请自行甄别文档内容的完整性,平台不提供额外的编辑、内容补充、找答案等附加服务。
- 2、"仅部分预览"的文档,不可在线预览部分如存在完整性等问题,可反馈申请退款(可完整预览的文档不适用该条件!)。
- 3、如文档侵犯您的权益,请联系客服反馈,我们会尽快为您处理(人工客服工作时间:9:00-18:30)。
TE12710D TE12710F TE12710H
大有关,同时与催化剂的完全干燥也
TE12710I TE12712A TE12712C
TE12710J TE12712B TE12712D
有关系。
160
TE12712E TE12712G
TE12712F TE12712H
TE12712I
TE12712J
9
蜡油加氢裂化装置开工总结
10
装置开工
催化剂装填 干燥
① 催化剂装填 ② 催化剂干燥
催化剂预硫化 切换原料
① 催化剂预湿 ② 催化剂预硫化 ③ 切换原料
装置初期运行状况
① 原料情况和主要操作参数 ② 开工期间物料平衡 ③ 产品质量情况
小结
11
催化剂装填 干燥
本装置反应器分成相同的两系列(R101A/B),每个反应器均设六个床层。 反应器内装三种类型的催化剂,分别为:加氢保护催化剂、精制催化剂、裂 化催化剂。
24
密度 kg/m3 残炭 %(m/m) 硫含量 %(m/m) 氮含量 ppm 粘度 mm2/s
初馏点 ℃ 5% ℃ 10% ℃ 20% ℃ 30% ℃ 40% ℃ 50% ℃ 60% ℃ 70% ℃ 80% ℃ 90% ℃ 95% ℃
终馏点 ℃
原料性质
减二线 916.7 0.03
268.8 323.2 329.2 348.4
升温过程中,1至6床层的温升分别为:12、10、8、4、5、6℃,表 明从300℃向350℃升温的过程中,催化剂床层温度得到了很好控制。
22
催化剂预硫化 切换原料
催化剂设计注硫量:93t,实际注硫量:101.85t,其中,绝大部分是由催化剂完成 硫化态反应所消耗,另一部分则由下列几部分损耗构成,它们分别为:废氢排放带走H2S ;系统预硫化结束后在高压系统以H2S形式存在而滞留在系统中的硫;系统泄漏损耗;高 分含硫污水排放带走溶解的硫以及其他损失。催化剂的上硫量占总硫的94.5%。
2001年04月 开始预可研 2002年04月 开始可行性研究 2004年08月 可研报告得到国家批复 2004年11月 总公司成立炼油项目
领导小组及管理项目组 2005年03月 完成总体设计 2005年08月 基础设计开始 2005年11月 总公司批准总体设计 2005年12月 开工奠基
开工柴油穿过催化剂床层,历时2小时48分。 预湿完成后,42%设计负荷运行4h后提进料至
400t/h,开始全量循环预湿2h。
17
催化剂预硫化 切换原料
催化剂预硫化工艺条件: 反应器入口温度:175℃ 反应器进料量:250t/h (两列) 系统压力:5.0MPa 循环机转速:7000rpm 循环氢流量:508260.8Nm3/h
体 目 标
清洁化
生产过程清洁化:低排放(污水零排放,废气排放达环境空气二级标准)
低消耗
生产产品清洁化:所产油品质量全部达到欧Ⅲ、欧Ⅳ标准
:
三 化 信息化 一 高
一个平台:企业综合信息平台 两个网络:DCS控制网、生产信息管理网 三个层面:PCS、MES、ERP
“1-2-3”
高价值 产品附加值高
5
XX炼油项目历程
裂化段 WABT
系统压力, MPa(g)
2
DMDS 累计注入量 10^4 kg
0
0
0
10
20
30
40
50
60
70
具体硫化过程:
运行时间, h (从进油开始计)
反应器温度至175℃(不允许超过200℃),系统压力5.0~5.5MPa,开始注硫。 起始注入量为1700~1800kg/h。以15℃/h速度升温至220℃恒温。增加DMDS注入量至3500kg/h。 13小时23分后H2S穿透催化剂床层,同时降低DMDS注入量至1000~1200kg/h,硫化过程中保证H2S浓度
23
装置初期运行状况
经过初期调整,4月23日13时30分所有产品合格(从预湿到产品合格共用时4天22 小时)。主要操作参数如下: 反应器进料:250t/h (50~60%设计负荷) 系统压力:13.53MPa 循环氢量:613918Nm3/h 催化剂床层平均温度:364℃
2009年4月28日19:30分切换减三线蜡油35t/h,装置处理量为310t/h(65%设计负荷 ),催化剂床层平均温度升至381℃,后续逐渐调整CGO的掺炼比例。
反应部分采用炉后混油方案,反应产物分离流程采用热高分流程,并且设 置液力透平,回收冷高分油的能量。
针对尾油产品收率低的特点,专利商采用了一次通过流程,装置的单程转 化率达到88%。
分馏部分采用双塔汽提流程,设置分馏塔进料加热炉。吸收稳定部分为吸 收脱吸,采用单塔流程,以混合石脑油作为吸收剂。
大于5000ppm。通过计量硫化氢穿透床层前大约注硫35t。
19
催化剂预硫化 切换原料
H2S含量 /ppm vol DMDS 注入量, kg/h
14000 12000 10000
8000 6000 4000 2000
0 0
4000
H2S含量 /ppm
3500
DMDS注入量 / kg/h
3000
2500
400万吨/年蜡油加氢裂化装置 开工技术总结汇报
XX炼油公司
1
主要内容
XX炼油项目概况
主
要
400万吨/年蜡油加氢裂化装置概况
内
容
装置开工技术总结
装置标定结果
2
XX炼油项目概况
XX炼油项目:
CNOOC投资建设的第一座特大型炼厂 设计100%加工海洋低硫高含酸环烷基重质原油 加工规模为1200万吨/年 常减压蒸馏、加氢裂化、延迟焦化、连续重整与PX等16套主要生产装置 配套原油和成品油码头、储罐及公用工程设施等 主要产品为汽油、航煤、柴油、苯、对二甲苯、液化气、丙烯15大类1150多万吨石化产品
催化剂于150℃干燥脱水4h,然后升温至180 ℃恒温16小时,但高分未 见有水脱出,因此又升温至200℃,仍未见有水脱出。
15
催化剂预硫化 切换原料
本装置催化剂采用湿法硫化方案,以二甲基二硫醚(DMDS)为硫化剂,硫化 终温为350℃。以直馏柴油作为硫化油,在硫化过程中逐步切换减压蜡油。
催化剂预湿条件:
3
XX炼油项目概况
总体目标:
“差异化、清洁化、信息化和高价值”的炼油厂
最主要特点
燃料-化工型特大型炼厂 主要装置采用单系列配置 技术先进,16套主生产装置,11套专利其中8套主装置引进国外工艺包
4
XX炼油项目概况
建设目标:具有国际竞争力的精品炼厂
具
差异化 原料差异、规模差异和产品差异
367.4 376.2 388.2
416.4 430.2 454.6 478.8
减三线 937.3 0.21
294.3 403.7 422.7 437.6 445.2 453.8 459.2 466.9 477 488.3 507.6 522 533.5
焦化蜡油 953.2 0.16 0.417 5640 77.21 293 354.8 377.6 400.4
425 433.4 441.2
混合原料 917 0.14 0.20 1320
干燥时系统压力:4.0MPa
14
干燥温度 / ℃
催化剂干燥
250
200
150
100
设计干燥曲线
第一床层入口温度
50
第六床层出口温度
0 0 4 8 12 16 20 24 28 32 36 40 44 48 52 56 60 64 68 干燥时间 / h
150~200℃干燥时 间56小时。
干燥过程:
6
400万吨/年蜡油加氢裂化装置
7
400万吨/年蜡油加氢裂化装置概况
处理能力400×104 MTA 国内首套引进SHELL工艺包 Criterion Catalysts & Technologies 的催化剂 装置设计原料为减二线蜡油、减三线蜡油和焦化蜡油的混合原料(混合
比例为49.08:30.92:20) 主要生产轻、重石脑油、航煤、柴油和加氢尾油产品
加氢裂化反应器切线高度38.27米、内径4.4米,催化剂装填量708840kg,预计 装填时间10天,而实际装填时间只用了不到9天时间。
此次催化剂装填,所有到货催化剂全部按计划装填完毕,实际装填数据与原 定催化剂装填方案基本吻合。
12
催化剂装填 干燥
13
催化剂干燥
干燥介质:氮气
氮气纯度为99.6%,氧含量为0.03%,氢加烃含量小于0.01%。
TE12702D
TE12702E
TE12702F
TE12704A
TE12704B
220
TE12704C
TE12704D
但催化剂床层温度远没有超过预湿最
TE12704E
TE12704F
TE12706A TE12706C
TE12706B TE12706D
高温度240℃的限制条件,因此,对
TE12706E
TE12706F
200
TE12708A TE12708C
TE12708B TE12708D
催化剂的活性没有任何负面影响。
TE12708E
TE12708F
TE12708G
TE12708H
TE12708I
TE12708J
TE12710A
TE12710B
催化剂床层出现较大温升与预湿量较
180
TE12710C TE12710E TE12710G
21