蜡油加氢装置简介分解
蜡油加氢裂化装置设备操作规程
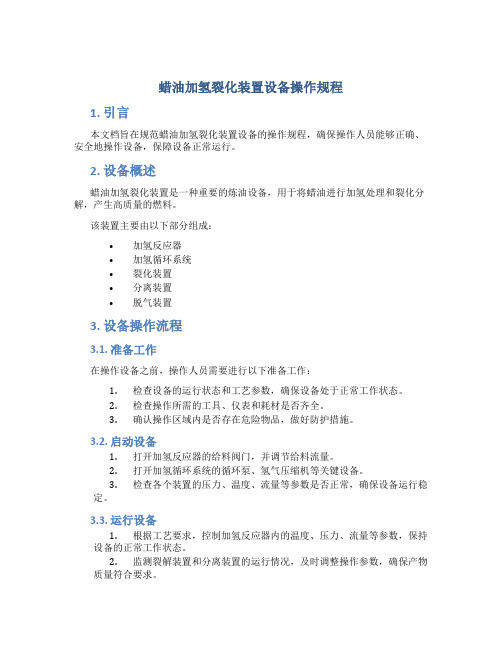
蜡油加氢裂化装置设备操作规程1. 引言本文档旨在规范蜡油加氢裂化装置设备的操作规程,确保操作人员能够正确、安全地操作设备,保障设备正常运行。
2. 设备概述蜡油加氢裂化装置是一种重要的炼油设备,用于将蜡油进行加氢处理和裂化分解,产生高质量的燃料。
该装置主要由以下部分组成:•加氢反应器•加氢循环系统•裂化装置•分离装置•脱气装置3. 设备操作流程3.1. 准备工作在操作设备之前,操作人员需要进行以下准备工作:1.检查设备的运行状态和工艺参数,确保设备处于正常工作状态。
2.检查操作所需的工具、仪表和耗材是否齐全。
3.确认操作区域内是否存在危险物品,做好防护措施。
3.2. 启动设备1.打开加氢反应器的给料阀门,并调节给料流量。
2.打开加氢循环系统的循环泵、氢气压缩机等关键设备。
3.检查各个装置的压力、温度、流量等参数是否正常,确保设备运行稳定。
3.3. 运行设备1.根据工艺要求,控制加氢反应器内的温度、压力、流量等参数,保持设备的正常工作状态。
2.监测裂解装置和分离装置的运行情况,及时调整操作参数,确保产物质量符合要求。
3.定期对设备进行巡视,并检查设备的运行状态和仪表的准确性。
4.注意设备周围的安全环境,及时排除可能存在的危险因素。
3.4. 停止设备1.逐步减少加氢反应器的给料流量,并关闭给料阀门。
2.停止加氢循环系统的循环泵、氢气压缩机等关键设备。
3.关闭各个装置的阀门,并排空介质。
4.对设备进行清理和维护,并记录设备停运情况。
4. 安全注意事项在操作蜡油加氢裂化装置时,操作人员需要严格遵守以下安全注意事项:•遵守操作规程和工艺要求,确保设备运行的稳定性和安全性。
•穿戴个人防护装备,包括安全帽、防护服、手套等。
•注意设备周围的危险区域,不要擅自进入。
•注意设备的运行参数和仪表的指示,及时发现异常情况并报告。
•禁止在设备周围吸烟或使用明火。
•熟悉并使用相应的应急设备和灭火器材。
5. 结束语通过遵守本操作规程,操作人员能够正确、安全地操作蜡油加氢裂化装置设备,并确保设备正常运行。
(完整word版)蜡油加氢工艺流程简介

蜡油加氢工艺流程简介一、反应部分自罐区来的混合蜡油经泵升压后先进行换热,再经自动反冲洗过滤器过滤后进入滤后原料缓冲罐,滤后原料油由反应进料泵抽除升压后,先于换热后的混氢混合,再与反应产物进行换热,换热后进入加热炉至要求温度,自上而下流经加氢精制反应器。
在反应器中,原料油和氢气在催化剂作用下,进行加氢脱硫、脱氮、烯烃饱和等精制反应。
从加氢精制反应器出来的反应产物与混氢原料换热后,进入热高分罐进行气液分离,热高分罐顶部出来的气相先与混氢换热后进入反应产物空冷器,冷却至50℃左右进入冷高分罐进行油、水、气三相分离。
为了防止加氢反应生成的硫化氢和氨在低温下生成铵盐,堵塞高压空冷器的管束,在空冷器前注入脱氧水。
冷高分罐顶部的气体经循环氢分液器分液后进入循环氢脱硫塔进行脱硫。
自富液再生装置来的贫胺液经泵升压后进入循环氢脱硫塔,与自塔顶部进入的循环氢进行逆向接触、反应,脱硫后的循环氢自塔顶进入循环氢压缩机入口分液罐,罐顶出来的循环氢经循环氢压缩机升压后,与经压缩后的新氢混合,返回到反应系统。
循环氢脱硫塔塔底出来的富液经闪蒸后自压至催化的富液再生装置进行再生。
从热高分罐底部出来的热高分油经减压后进入热低分罐,在热低分罐中再次进行气液分离,热低分罐顶部的气体经冷却后进入冷低分罐,热低分油自压进入脱丁烷塔。
冷高分罐及冷低分罐底部出来的含硫污水经减压后,自压送至污水汽提装置进行无害化处理。
冷低分油则在与产品柴油进行换热后,进入脱丁烷塔。
冷低分气自压送往催化装置吸收塔入口。
二、分馏部分冷、热低分油自压进入脱丁烷脱除含硫气体,塔下部设有汽提蒸汽,汽提所用的过热蒸汽来自加热炉对流段。
脱丁烷塔顶油气经冷凝冷却后进入脱丁烷塔顶回流罐,回流罐底部液体全部作为回流返回塔顶,回流罐顶的含硫气体自压送往焦化气压机的入口。
从塔底出来的脱丁烷塔底油经泵增压后,先与产品蜡油进行换热后,再经分馏塔进料加热炉升温至需要的温度后进入分馏塔。
分馏塔设有一个中段回流和一个侧线(柴油),塔下部设有汽提蒸汽,汽提所用的过热蒸汽来自加热炉对流段。
蜡油加氢装置用能分析及节能降耗

峰顶位置变化不大,所以在DS C分析中应尽量控制样品量在5~10mg,以保证测试结果的稳定。
通常我们在分析时选择称样量为7~9mg。
5惰性气体的影响。
将同一试样以同样的升降温程序,分别在有无通流动氮气保护的情况下测试,两者结果存在一定的差异,通氮气的情况下要比不通氮气时熔点要高一些。
这是因为在无氮气保护的情况下,聚酯切片容易被氧化,产生氧化放热峰,使熔融峰变大,而在氮气气氛下,无氧化峰。
因此应尽量选择惰性气体保护,特别是在二次升温的情况下。
6.其他方面的影响。
由于我们目前采用用刀片切的方式取样,所以样片底部切得是否平,以及是否将较平的面朝下放在铝坩埚中等等都很重要,因为如果样片与坩埚及加热炉内样品支持架接触不良,就会导致峰形不稳,从而导致结果出现偏差,影响结果的重复性和准确性。
三、结论1.熔点的确定方式不同,熔点值差别很大。
对于聚酯切片我们通常采用峰值作为熔点。
2.升温方式不同,熔点结果不同。
应根据需要选择合适的操作方式。
3.随着升温速率的升高,样品峰值温度会有所增加,通常选择10℃/min的升温速率。
4.称样量控制在7~9mg。
5.有无惰性气体保护,样品的熔点有差异,尽量选择通入惰性气体。
6制样片时,应尽量用刀片切平,并且保证让平的一面朝下放入铝坩埚中。
洛阳石化蜡油加氢处理装置设计年加工能力220万t,年开工时数8400h。
蜡油加氢处理装置以减压蜡油、焦化蜡油和脱沥青油的混合油为原料,采用抚顺石油化工研究院(FRIPP)开发的FFHT蜡油加氢处理工艺技术,加氢处理催化剂采用FRIPP的FF-18(保护剂为FZC系列保护剂)。
主要生产低硫含量的精制蜡油,为催化裂化装置提供优质的原料,同时副产少量石脑油和柴油,富氢气体经脱硫后去制氢装置做原料。
为了节约资源、节约能源和提高装置运行水平,加氢车间采取各种用能优化措施,挖潜增效,取得了一定的成绩。
一、装置工艺特点及设计能耗1.装置工艺特点。
采用热高压分离系统等工艺技术,在满足产品质量和工艺要求的前提下,尽量提高中、高温位热量的利用,以最大限度地回收热量,有效地减少反应流出物冷却负荷,达到降低装置能耗的目的。
蜡油介绍(20110301)
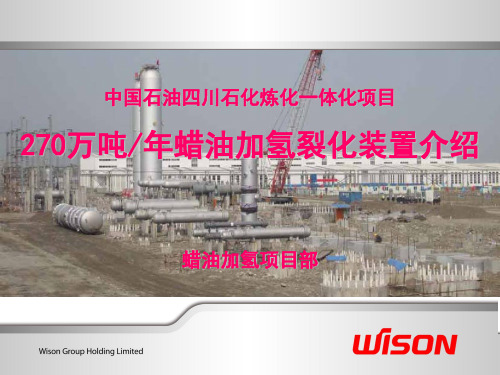
隔离液系统1台、注油器(3泵)1套
压缩机厂房32/5桥吊、反应框架15t电动葫芦
安装在C-2002内
Page : 3
装置涉及的设计专业
序
名称
图纸代号
序 8
名称 电气
图纸代号 1300#EE
1 2 3
工艺 热工 总图
13000PE 13000TM 13000GL
9
电信
13000TC
中国石油四川石化炼化一体化项目
270万吨/年蜡油加氢裂化装置介绍
蜡油加氢项目部
Page : 1
装置概况
装置规模:加工原料(减压蜡油)270万吨/年,生产轻重石脑油,航煤、准柴油、尾油、液化气、干气等产品。 年开工8400小时; 装置占地:110m(东西)*225m(南北)=2.475万平米 技术方案:专利商 UOP 采用双剂串联一次通过的加氢裂化工艺、反应部分采用炉后混氢方案(加热炉加热混合氢)、分馏 部分采用硫化氢汽提塔+常压塔出柴油和航煤方案。 装置组成:反应部分、分馏部分、公用工程部分、热工部分、机泵机组部分组成; 主要工程量:建筑物3座(4867m2)、有构架6个及主管廊1个(钢结构~2200t)、工艺设备302台(主要设备248台), 工艺管道~45km/1700t(高压管道~5km/550t),仪表设备~2500台、电气设备~200台。 装置特点:本装置设计压力和设计温度高,接触高危介质(H2、H2S)的特种设备及高压管道多,工艺设备及管道的 材质多、厚度大、重量大、安装及施工困难,装置布局紧凑,施工区域狭小。 装置最高设计/操作压力达 20.0/16.0 MPa、最高设计/操作温度达 513/488℃; 装置接触高温、高压、高危介质的反应器、塔器、容器、换热器、机泵、加热炉等特种设备45台,其 中,加氢裂化反应器的壳体重量931吨、壁厚228mm,为四川石化单台设备重量之最,4台压缩机出口 压力达15.46MPa、轴功率均在5000kw以上,16台高压空冷管束采用Inconel-Alloy825材质,12台高压 换热器有10台采用螺纹锁紧环式,最大单台重量~120t。 装置工艺管道涉及的材质有TP347、TP321、304、316、P11、P22、15CrMoG、A106、 20#、20G 、L245、 Q235B等,其中高压SHA类管道~6km/550t,重量占工艺管道总量的30%以上,是整个装置施工的重点和 难点,尤其是铬钼钢的焊接更是关键。 装置地下采取防渗措施,地管及地下构筑物施工困难;
蜡油加氢裂化装置柴油转化、减油增化方向研究

蜡油加氢裂化装置柴油转化、减油增化方向研究摘要:本文先是对蜡油加氢裂化装置概况及现状进行分析,其次蜡油加氢裂化装置柴油转化、减油增化的影响因素,最后提出蜡油加氢裂化装置柴油转化、减油增化的对策,促进企业可持续发展。
关键词:蜡油加氢;裂化装置;柴油转化;减油增化当前,为了促进企业可持续发展,很有必要探讨蜡油加氢裂化装置柴油转化、减油增化的措施,降低成本,提高企业发展效益。
1蜡油加氢裂化装置概况及现状某石化千万吨炼油项目的主体装置为蜡油加氢裂化装置,其将美国UOP企业的加氢裂化专利技术与工艺包引进。
通过分析,加氢裂化设计规模为每年210万吨,一年操作时间为8400h,装置操作弹性为60%~110%。
这一装置的主要反应部分在于合理利用炉前婚氢、单段全循环、热高分工艺流程,且还设置了循环氢脱硫塔,分馏系统主要使用的是四塔分离流程出柴油方案,即分馏塔、硫化氢脱硫塔、柴油汽提塔、航煤汽提塔[1]。
该装置使用的操作方法为单段全循环方法,最大程度地完成中间馏分忧的生产,将其当做整个企业的调和组分,将少量加氢裂化还未转化的油去重油催化裂化当做主要的原料,冷低分气脱硫之后可以去PSA装置完成氢气提纯,含硫干气到轻烃回收装置中。
当前,企业原始设计方案采用低硫原油为主要原料,完成最大量生产中间馏分柴油方案。
2016年企业为了降低生产加工总成本,将其换成加工高硫原料油,生产的是高效的石脑油,让装置柴汽比方案明显降低。
2018年之前,基本维持装置重石脑油在0.5~1.2ppm。
从2018年开始,维持硫含量在2.0~4.0ppm之间。
为了给下游重整更优的原料,被迫将加裂装置的石脑油通过石脑油加氢装置脱硫之后将其送到重整装置,最终导致企业加工总成本明显提高。
2蜡油加氢裂化装置柴油转化、减油增化的影响因素2.1反应器后精制剂超负荷运行最初的蜡油加氢裂化装置设计原材料为轻蜡油,反应器之内的催化剂装填级配更多以原始方案为基础,主要设计在于生产中间馏分油。
蜡油加氢装置简介

100万吨/年蜡油加氢装置装置简介中国石化股份有限公司上海高桥分公司炼油事业部2007年3月编制:何文全审核:严俊校对:周新娣目录第一章工艺简介一、概述中国石化股份有限公司上海高桥分公司炼油事业部是具有五十多年历史的加工低硫石蜡基中质原油的燃料——润滑油型炼油企业,根据中国石化股份有限公司原油油种变化和适应市场发展的需求,上海高桥分公司到2007年以后除了加工大庆原油、海洋原油等低硫原油外,将主要加工含硫2.0%左右的含硫含酸进口原油。
由于常减压生产的减压蜡油和延迟焦化装置生产的焦化蜡油中含有较多的不饱和烃及硫、氮等有害的非烃化合物,这些产品无法达到催化裂化装置的要求。
为了使二次加工的蜡油达到催化裂化装置的要求,必须对焦化蜡油和减压蜡油进行加氢精制,因此上海高桥分公司炼油事业部进行原油适应性改造时,将原100万吨/年柴油加氢精制装置改造为100万吨/年蜡油加氢装置。
本装置的建设主要是为了催化裂化装置降低原料的硫含量和酸度服务。
本装置由中国石化集团上海工程有限公司设计,基础设计于2005年6月份完成,2005年8月份进行了基础设计审查,工程建设总投资2638.73万元,其中工程费用2448.74万元。
2006年7月降蜡油含硫量由原设计2.44%提高至3.28%,工程建设总概算增加820.8万元。
二、装置概况及特点1.装置规模及组成蜡油加氢精制装置技术改造原料处理能力为100万吨/年,年开工时数8400小时。
本装置为连续生产过程。
主要产品为蜡油、柴油、汽油。
本装置由反应部分、循环氢脱硫部分、氢压机部分(包括新氢压缩机、循氢压缩机)、加热炉部分及公用工程部分等组成。
2.生产方案混合原料经过滤后进入缓冲罐,用泵升压,经换热、混氢,再经换热进入加热炉,加热至350℃后进反应器进行加氢,反应产物经换热后进热高分进行气液分离,气相进一步冷却,进冷高分进行气液分离,气相进新增的循环氢脱硫塔脱硫后作为循环氢与新氢混合,组成混合氢循环使用;液相减压后至热低分,热低分的液相至催化裂化装置。
石蜡加氢精制装置简介和重点部位及设备

石蜡加氢精制装置简介和重点部位及设备一、装置简介(一)装置发展及类型1.装置发展石蜡精制工艺有白土精制、渗透精制、硫酸精制和加氢精制四种类型,其中白土精制和渗透精制都不容易脱净蜡中的稠环芳烃,难以生产对于纯度要求很高的食品工业用蜡:而硫酸精制方法的主要缺点是产品产率低,劳动条件恶劣,有大量的废渣产生,污染环境。
无论在生产成本上,产品产率和质量及环境保护上,石蜡加氢精制均比其他精制工艺有明显的优越性。
因此,在国外主要炼油厂中,石蜡加氢精制己逐步代替其他精制工艺。
1957年加拿大萨尼亚炼油厂首先宣布用钼钻铝催化剂加氢精制生产白石蜡,由于该工艺对蜡中稠环芳烃组分有很好的加氢转化能力,容易制取食品级纯度商品蜡而进一步为人们重视;其后催化重整工艺的兴起,为炼油厂提供了廉价的氢气来源,尤为石蜡加氢精制装置的建设创造了有利条件。
1962年一套处理量为1.5X104t/a、10.OMPa的石蜡和凡士林加氢精制装置在西德汉堡建成。
1963年美国大西洋公司费城炼油厂建成日处理量300t /a的石蜡加氢精制装置,代替原来的石蜡硫酸和渗透精制工艺。
我国从20世纪70年代初正式开始研究石蜡加氢精制催化剂和工艺,1979年11月大庆石化总厂首次采用5053催化剂进行处理量6X104t/a的低压石蜡加氢装置开工投产。
1981年10月石油工业部对481—2B催化剂及中压石蜡加氢精制工艺组织技术鉴定,本工艺先后在东方红炼油厂(现中石化燕山分公司炼油厂)、抚顺石油一厂、荆门炼油厂、大连石油七厂、茂名炼油厂实现工业化。
1983年11月第一套采用石蜡加氢专用催化剂处理量为6X104t/a的石蜡加氢装置在东方红炼油厂投产,1984年另两套石蜡加氢装置在抚顺石油一厂和荆门炼油厂投产,1986年又两套石蜡加氢装置在大连石油七厂和茂名炼油厂相继投产。
2.装置的主要类型20世纪60年代以来国外陆续发展的蜡加氢精制工艺有十多种,可归纳为五种类型见表2—85。
蜡油加氢装置技术分析报告

关于在技术人员中开展装置分析工作的通知各部门:充分了解和掌握自己分管装置的技术实情是技术人员管理、优化装置技术工作的基础。
为透彻分析装置的技术现状、进一步寻找与国内外同类装置之间的差距,学习先进理念和先进技术,启迪管理思路,更好地营造学习技术的氛围。
经研究,决定在技术人员中开展装置分析工作。
一、对象:已转正上岗的装置工艺员、设备员(包括后备)以及公用工程作业区和储运部技术员(包括后备)。
二、要求:1.年底前,技术人员完成对自己分管装置的详细技术分析报告。
内容包括本装置在工艺、设备、能耗、产品质量、管理等方面的现状,与国内同类装置之间的比对,查找存在的差距,改进需落实的具体措施等。
2.有条件的,可到国内同类装置进行外出调研,带去问题或疑惑,带回体会与启发。
3.年终事业部举行技术分析报告演示交流,表彰优秀报告。
三、时间安排:1.7月份布置工作、宣传工作开展的意义。
2.8、9月份创造条件外出调研。
3.11月底前完成分析报告。
4.12月底前组织审阅报告、演示交流、表彰优秀报告。
望各部门接到通知后,组织广泛宣传,切实推进装置分析工作。
部门行政主要领导要创造条件,扶持技术人员落实这项工作;充分利用事业部专业技术小组资源,帮助联系落实外出调研单位,确保这项工作有序开展。
注:1、装置分析报告提纲见附件一、附件二。
2、公用工程、储运部装置分析报告提纲参考附件一、附件二。
炼油事业部2007年7月27日附件二:2#汽柴油加氢装置技术分析报告(设备)1.装置概况上海高桥分公司到2007年以后除了加工大庆原油、海洋原油等低硫原油外,将主要加工含硫2.0%左右的含硫含酸进口原油。
由于常减压生产的减压蜡油和延迟焦化装置生产的焦化蜡油中含有较多的不饱和烃及硫、氮等有害的非烃化合物,这些产品无法达到催化裂化装置的要求。
为此,必须对焦化蜡油和减压蜡油进行加氢精制。
上海高桥分公司炼油事业部进行原油适应性改造时,将原100万吨/年柴油加氢精制装置改造为100万吨/年蜡油加氢装置,主要是为了催化裂化装置降低原料的硫含量和酸度服务。
分析蜡油加氢裂化装置低负荷生产问题及对策

分析蜡油加氢裂化装置低负荷生产问题及对策摘要:加氢裂化装置在低负荷加工条件下运行,对装置内设备使用提出了更高的要求,但装置本周期已连续运行2年半,综合考虑安全生产和装置经济效益指标,决定采取“小进料量,低转化率,大空速,高循环比”生产方案,通过连续2个月的运行分析,对装置在低负荷操作过程中部分参数进行优化调整,保证设备参数均在设计流速、温度、压差条件下运行。
关键词:加氢裂化;低负荷;优化转化率中国石油长庆石化公司120×104t/a加氢裂化装置由洛阳工程设计院设计,以本公司的重柴油和减压蜡油为原料,采用全循环流程操作时,最大限度生产航煤及柴油(多产中油方案),同时副产液化气、轻石脑油、重石脑油,此流程为该装置的主方案;采用一次通过流程操作时,在生产中间馏分油的同时,生产尾油,为乙烯项目提供裂解原料。
加氢裂化装置设计操作弹性为60-110%,本周由于常减压装置进行降量操作,蜡油产量降低至2000吨/天,为确保加氢裂化装置正常生产运行,同步降低加工量,维持58%加工负荷连续运行2个月,并成功在58%负荷操作条件下平稳运行。
1、加氢裂化装置概况该加氢裂化装置为2.0Mt/a高压加氢裂化装置,由中国石化工程建设公司参与设计,并于2007年成功投料开车。
该装置主要由四部分组成,分别是反应部分、分馏部分、吸收稳定部分及脱硫部分组成,其中反应部分采用的是目前国内外已经应用较为成熟的炉前混氢流程,操作更加简便,传热效率更加高效,流程也得到了良好的优化。
分馏部分通过设置硫化氢汽提塔,并采用分馏塔进料,常压塔与加热炉出柴油的方案,在分馏塔中,还设置了两个中段回流,从而使得热量得到了较好的回收,有利于整体装置能耗降低。
吸收稳定部分在吸收方案选择上,采用的是重石脑油作为吸收剂的方案,从而使得干气中的液化气得到很好的回收,有效避免了轻石脑油与液化气出现更大的损失;最后对于脱硫部分来说,在脱硫剂选择上,选择的是N-甲基二乙醇胺,进行低分气与液化气的脱硫方案。
(完整ppt)290万加氢裂化装置简介

初期 0.7973
172/187 194/201 209/222
237 <5 <1 55 -54 27
末期 0.7992
国标
172/188 194/201 209/222
237 <5 <1 55 -54 25
不大于2000
不低于38 不高于-47 不小于25
保证值
2000 max 38 min -47 max 25 min
290万吨/年加氢裂 化装置简介
中国石油华北石化公司
目录
• 一、装置概述 • 二、原料及主要产品性质 • 三、工艺技术方案 • 四、关键设备选型 • 五、仪表控制
中国石油华北石化公司
目录
• 六、能耗及物料平衡 • 七、平面布置 • 八、工艺流程简图 • 九、设备图片
中国石油华北石化公司
一、装置概述
中国石油华北石化公司
工艺技术方案
• 紧急泄放系统方案 为确保催化剂、高压设备及操作人员的安 全,设置2.1MPa/min和0.7MPa/min两个 紧急泄压系统
中国石油华北石化公司
工艺技术方案
• 反应部分共设置了两个循环氢加热炉和两 个加氢裂化反应器(并联使用),原料油 自高压进料泵出口分为两路,经换热后分 别与从两个循环氢加热炉出口来的循环氢 气混合,进入加氢裂化反应器,反应器生 成物经换热后合并进入热高压分离器进行 气液分离。
轻石脑油主要技术指标
产品 密度(20℃),g/cm3
初期 0.6413
末期 0.6418
硫,μg/g 氮,μg/g
<0.5
<0.5
<0.5
<0.5
保证值 10 Max
中国石油华北石化公司
新建蜡油加氢装置与柴油加氢装置共用氢气系统运行总结

新建蜡油加氢装置与柴油加氢装置共用氢气系统运行总结摘要:蜡油加氢是一类加氢(Hydrotreating),是指这些加氢过程通过加氢反应,原油的分子大小不发生变化,或者只有不到10%的分子变小。
蜡油加氢装置主要用减压蜡油(VGO)和蒸发装置的碳氢化合物(CGO)作为原料,通过加氢处理,去除原料中的硫和部分去除氮化物、氧化物和金属杂质。
同时,也有反应,如油和芳香族饱和度。
通过加氢可以达到以下效果:改善产品的性能,催化汽油的硫含量可以降低到小于0.015%(质量分数)。
奥林含量低于35%(体积百分比);催化柴油的密度和硫含量大大降低;Hexadhan值增加近10个单位;满足环保要求,大大减少催化裂化气体中的SOx和NOx。
它有利于提高中间蒸发器的产量,氢化过程的副产量约为低硫柴油的8%~12%,是一种优质柴油混合组分;与此同时,汽油和液化天然气的硫含量分别下降了61.1%。
64.7%和增加汽油和柴油的产量,并减少了催化干气的碳产量。
在当今油品质量和环保要求越来越严格的情况下,催化裂化原料必须加氢,否则难以满足质量和环保要求。
因此,蜡油加氢装置得到了迅速发展。
关键词:蜡油加氢装置;柴油加氢装置;共用氢气系统;运行总结引言蜡油加氢是炼油工业生产中最重要的环节之一,其中氢的消耗量与炼油企业的生产成本有关,因此,为了降低投入成本,提高行业竞争力,炼油企业应做好蜡油加氢处理研究,优化相关加工工艺。
1蜡油加氢装置介绍某公司在产品质量升级改造项目中,为了充分利用剩余的重整氢资源、最大限度改善蜡油性质,根据产品质量升级改造规划,在现有的柴油加氢装置内新建了蜡油加氢装置。
装置原料为焦化蜡油和直馏蜡油,其中焦化蜡油占比55.1%,直馏蜡油占比44.9%。
装置生产的加氢蜡油全部送至催化裂化(催化)装置作为进料的一部分,可以改善催化装置的进料性质以及产品分布。
装置所需氢气由柴油加氢装置供给,与柴油加氢装置共用氢气系统,两套装置同开同停。
蜡油加氢装置氢耗影响因素分析及降耗措施
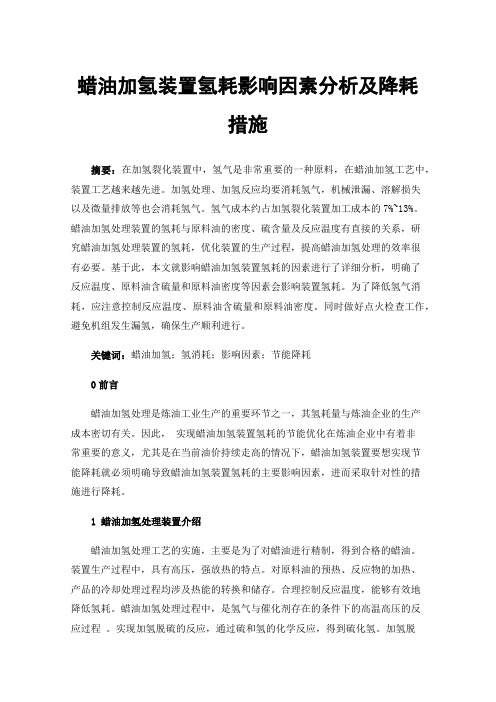
蜡油加氢装置氢耗影响因素分析及降耗措施摘要:在加氢裂化装置中,氢气是非常重要的一种原料,在蜡油加氢工艺中,装置工艺越来越先进。
加氢处理、加氢反应均要消耗氢气,机械泄漏、溶解损失以及微量排放等也会消耗氢气。
氢气成本约占加氢裂化装置加工成本的7%~13%。
蜡油加氢处理装置的氢耗与原料油的密度、硫含量及反应温度有直接的关系,研究蜡油加氢处理装置的氢耗,优化装置的生产过程,提高蜡油加氢处理的效率很有必要。
基于此,本文就影响蜡油加氢装置氢耗的因素进行了详细分析,明确了反应温度、原料油含硫量和原料油密度等因素会影响装置氢耗。
为了降低氢气消耗,应注意控制反应温度、原料油含硫量和原料油密度。
同时做好点火检查工作,避免机组发生漏氢,确保生产顺利进行。
关键词:蜡油加氢;氢消耗;影响因素;节能降耗0前言蜡油加氢处理是炼油工业生产的重要环节之一,其氢耗量与炼油企业的生产成本密切有关。
因此,实现蜡油加氢装置氢耗的节能优化在炼油企业中有着非常重要的意义,尤其是在当前油价持续走高的情况下,蜡油加氢装置要想实现节能降耗就必须明确导致蜡油加氢装置氢耗的主要影响因素,进而采取针对性的措施进行降耗。
1 蜡油加氢处理装置介绍蜡油加氢处理工艺的实施,主要是为了对蜡油进行精制,得到合格的蜡油。
装置生产过程中,具有高压,强放热的特点。
对原料油的预热、反应物的加热、产品的冷却处理过程均涉及热能的转换和储存。
合理控制反应温度,能够有效地降低氢耗。
蜡油加氢处理过程中,是氢气与催化剂存在的条件下的高温高压的反应过程。
实现加氢脱硫的反应,通过硫和氢的化学反应,得到硫化氢。
加氢脱氮反应以及加氢脱氧的反应,通过氢气的消耗,使原料油中的杂质硫、氮和过多的氧消耗掉,实质是对原料油的一个提纯的过程。
2蜡油加氢装置氢耗影响因素影响蜡油加氢能耗的原因有很多,根据生产实践,蜡油加氢装置的氢耗受反应温度、食用油含硫量和食用油密度的影响。
因此,在满足生产要求的基础上,做好这些参数的研究工作,掌握其影响规律,优化这些参数,并将其控制在合理范围内,以降低氢耗,更好地实现生产和经济目标。
石蜡加氢精制装置说明与危险因素防范措施

石蜡加氢精制装置说明与危险因素防范措施石蜡加氢精制装置是一种用于将黄蜡或石蜡通过加氢处理转化为白蜡的一种工业设备。
这种设备将石蜡加热至一定温度后与氢气反应,通过饱和烃的裂解与合成反应,将石蜡中的不饱和化合物去除,从而得到更纯净的白蜡产品。
然而,在进行石蜡加氢精制过程中,也存在一些危险因素需要引起注意,并采取相应的防范措施来保证设备操作的安全。
下面将对石蜡加氢精制装置的危险因素和防范措施进行详细说明。
1.高温和高压:石蜡加氢精制过程需要高温和高压环境,而高温和高压环境下容易引发爆炸和火灾等危险。
因此,需要严格控制加热温度和操作压力,确保设备的安全运行。
同时,需要定期检查和维护设备的阀门、管道和容器,确保其能够承受高温和高压环境的要求。
2.氢气泄漏:石蜡加氢精制过程需要使用氢气,而氢气是一种易燃易爆的气体,一旦泄漏可能引发火灾和爆炸。
因此,需要在装置中设置可靠的气体泄漏报警装置,并定期检查其是否正常工作。
同时,需要定期对氢气系统进行检查和维护,确保气体管道的完整性,避免泄漏的发生。
3.工作环境污染:石蜡加氢精制过程中会产生一些有害气体和污染物,如硫化氢、二甲苯等。
这些物质对人体健康有一定的危害。
因此,需要在装置周围设置通风系统和排气装置,确保工作环境的良好通风。
同时,操作人员需要佩戴防护装备,如防毒面具、防护手套和防护眼镜等,避免有害物质的直接接触。
4.废水和废气处理:石蜡加氢精制过程会产生大量的废水和废气。
这些废水和废气中含有一些有害物质,需要进行处理,以避免对环境造成污染。
因此,需要在装置中设置废水处理和废气处理系统,并定期进行检查和维护,确保其正常工作。
综上所述,石蜡加氢精制装置的操作过程中需要注意防范各种危险因素,以保证设备操作的安全。
通过控制加热温度和操作压力、设置气体泄漏报警装置、保持良好的通风环境、佩戴防护装备和进行废水和废气的处理等措施,可以有效减少事故的发生,保障人员的身体健康和环境的安全。
蜡油加氢装置简介

蜡油加氢装置简介 Document serial number【KKGB-LBS98YT-BS8CB-BSUT-BST108】100万吨/年蜡油加氢装置装置简介中国石化股份有限公司上海高桥分公司炼油事业部2007年3月编制:何文全审核:严俊校对:周新娣目录第一章工艺简介一、概述中国石化股份有限公司上海高桥分公司炼油事业部是具有五十多年历史的加工低硫石蜡基中质原油的燃料——润滑油型炼油企业,根据中国石化股份有限公司原油油种变化和适应市场发展的需求,上海高桥分公司到2007年以后除了加工大庆原油、海洋原油等低硫原油外,将主要加工含硫2.0%左右的含硫含酸进口原油。
由于常减压生产的减压蜡油和延迟焦化装置生产的焦化蜡油中含有较多的不饱和烃及硫、氮等有害的非烃化合物,这些产品无法达到催化裂化装置的要求。
为了使二次加工的蜡油达到催化裂化装置的要求,必须对焦化蜡油和减压蜡油进行加氢精制,因此上海高桥分公司炼油事业部进行原油适应性改造时,将原100万吨/年柴油加氢精制装置改造为100万吨/年蜡油加氢装置。
本装置的建设主要是为了催化裂化装置降低原料的硫含量和酸度服务。
本装置由中国石化集团上海工程有限公司设计,基础设计于2005年6月份完成,2005年8月份进行了基础设计审查,工程建设总投资2638.73万元,其中工程费用2448.74万元。
2006年7月降蜡油含硫量由原设计2.44%提高至3.28%,工程建设总概算增加820.8万元。
二、装置概况及特点1.装置规模及组成蜡油加氢精制装置技术改造原料处理能力为100万吨/年,年开工时数8400小时。
本装置为连续生产过程。
主要产品为蜡油、柴油、汽油。
本装置由反应部分、循环氢脱硫部分、氢压机部分(包括新氢压缩机、循氢压缩机)、加热炉部分及公用工程部分等组成。
2.生产方案混合原料经过滤后进入缓冲罐,用泵升压,经换热、混氢,再经换热进入加热炉,加热至350℃后进反应器进行加氢,反应产物经换热后进热高分进行气液分离,气相进一步冷却,进冷高分进行气液分离,气相进新增的循环氢脱硫塔脱硫后作为循环氢与新氢混合,组成混合氢循环使用;液相减压后至热低分,热低分的液相至催化裂化装置。
03蜡油加氢裂化装置

3蜡油加氢裂化装置预评价报告3.1装置概况根据总加工流程安排,需建设一套220×104t/a加氢裂化装置。
加工原料为苏丹混合原油的减压蜡油,所用氢气由PSA装置提供。
采用一段全循环流程,最大限度生产中间馏分油,作为全厂产品调合组份。
少量的加氢裂化尾油去重油催化裂化作为原料,冷低分气脱硫后去PSA装置进行氢气提浓,含硫气体和不稳定石脑油至轻烃回收装置。
3.1.1装置名称中国石油天然气股份有限公司广西石化分公司蜡油加氢裂化装置。
3.1.2装置规模及设计能力装置规模为220×104t/a,实际加工量为219.78×104t/a。
年操作时数8400小时。
3.1.3原料及产品3.1.3.1原料来源装置加工原料油为常减压蒸馏装置的减一、减二和减三线蜡油219.78×104t/a。
3.1.3.2产品及去向产品品种及去向见表3.1-1。
装置产品:石脑油、航煤、柴油和尾油。
副产品:冷低分气脱硫后去PSA氢提浓装置,汽提塔顶气至轻烃回收装置。
产品品种及去向见表3.1-1。
3.1.3.3物料平衡装置物料平衡见表3.1-2。
3.1.4公用工程消耗3.1.4.1水用量水用量见表3.1-3。
3.1.4.2电用量电用量见表3.1-4。
3.1.4.3蒸汽用量装置蒸汽用量见表 3.1-5。
3.1.4.4燃料用量燃料用量见表3.1-6。
3.1.4.5压缩空气用量压缩空气用量见表 3.1-7。
3.1.4.6氮气用量装置氮气用量见表 3.1-8。
3.1.5装置的平面布置占地面积:180×90=16200 m2。
压缩机厂房分两层布置,房内设置桥式吊车。
装置的所有管桥及构架均采用钢结构。
装置内留有足够的吊装检修用场地,以满足大型吊车接近与回旋。
反应构架上方设置单轨电动吊车与手动葫芦,大型泵的上方设置有检修用手动葫芦或检修吊梁,以方便检修与维护。
管桥成组合式布置,仪表电缆、电气电缆拟以槽盒的形式布置在管桥最上层,便于检修和维护,同时节省地下空间,所有设备与建、构筑物均沿管桥两侧布置;管桥下设置泵房。
蜡油介绍

2.66
7.18
102.66
277.18
1.89
5.10
1.02
2.75
4.76
12.85
8.63
23.30
25.67
69.31
19.97
53.92
10.57
28.54
30.15
81.41
102.66
277.18
Page : 9
装置工艺组成
反应部分,设备、管道、仪表编号130-X-2XXX(高压部分) 分馏部分,设备、管道、仪表编号 130-X-3XXX 公用工程部分,设备、管道、仪表编号 130-X-4XXX 热工部分,设备、管道、仪表编号 130-X-5XXX 机泵机组部分,管道、仪表编号X-6XXX(厂商部分)
压力达15.46MPa、轴功率均在5000kw以上,16台高压空冷管束采用Inconel-Alloy825材质,12台高压
换热器有10台采用螺纹锁紧环式,最大单台重量~120t。 装置工艺管道涉及的材质有TP347、TP321、304、316、P11、P22、15CrMoG、A106、 20#、20G 、L245、 Q235B等,其中高压SHA类管道~6km/550t,重量占工艺管道总量的30%以上,是整个装置施工的重点和 难点,尤其是铬钼钢的焊接更是关键。 装置地下采取防渗措施,地管及地下构筑物施工困难;
蜡油加氢装置简介
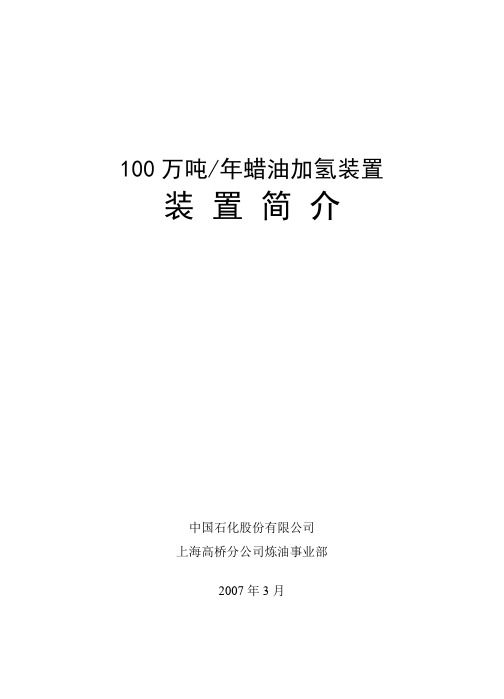
100万吨/年蜡油加氢装置装置简介中国石化股份有限公司上海高桥分公司炼油事业部2007年3月编制:何文全审核:严俊校对:周新娣目录第一章工艺简介 (1)一、概述 (1)二、装置概况及特点 (1)三、原材料及产品性质 (2)四、生产工序 (4)五、装置的生产原理 (5)六、工艺流程说明 (5)七、加工方案 (6)八、自动控制部分 (10)九、装置内外关系 (11)第二章设备简介 (13)一、加热炉 (13)二、氢压机 (13)三、非定型设备 (13)四、设备一览表 (15)五、设备简图 (20)第一章工艺简介一、概述中国石化股份有限公司上海高桥分公司炼油事业部是具有五十多年历史的加工低硫石蜡基中质原油的燃料——润滑油型炼油企业,根据中国石化股份有限公司原油油种变化和适应市场发展的需求,上海高桥分公司到2007年以后除了加工大庆原油、海洋原油等低硫原油外,将主要加工含硫2.0%左右的含硫含酸进口原油。
由于常减压生产的减压蜡油和延迟焦化装置生产的焦化蜡油中含有较多的不饱和烃及硫、氮等有害的非烃化合物,这些产品无法达到催化裂化装置的要求。
为了使二次加工的蜡油达到催化裂化装置的要求,必须对焦化蜡油和减压蜡油进行加氢精制,因此上海高桥分公司炼油事业部进行原油适应性改造时,将原100万吨/年柴油加氢精制装置改造为100万吨/年蜡油加氢装置。
本装置的建设主要是为了催化裂化装置降低原料的硫含量和酸度服务。
本装置由中国石化集团上海工程有限公司设计,基础设计于2005年6月份完成,2005年8月份进行了基础设计审查,工程建设总投资2638.73万元,其中工程费用2448.74万元。
2006年7月降蜡油含硫量由原设计2.44%提高至3.28%,工程建设总概算增加820.8万元。
二、装置概况及特点1.装置规模及组成蜡油加氢精制装置技术改造原料处理能力为100万吨/年,年开工时数8400小时。
本装置为连续生产过程。
主要产品为蜡油、柴油、汽油。
- 1、下载文档前请自行甄别文档内容的完整性,平台不提供额外的编辑、内容补充、找答案等附加服务。
- 2、"仅部分预览"的文档,不可在线预览部分如存在完整性等问题,可反馈申请退款(可完整预览的文档不适用该条件!)。
- 3、如文档侵犯您的权益,请联系客服反馈,我们会尽快为您处理(人工客服工作时间:9:00-18:30)。
100万吨/年蜡油加氢装置装置简介中国石化股份有限公司上海高桥分公司炼油事业部2007年3月编制:何文全审核:严俊校对:周新娣目录第一章工艺简介 (1)一、概述 (1)二、装置概况及特点 (1)三、原材料及产品性质 (2)四、生产工序 (4)五、装置的生产原理 (5)六、工艺流程说明 (5)七、加工方案 (6)八、自动控制部分 (10)九、装置内外关系 (11)第二章设备简介 (13)一、加热炉 (13)二、氢压机 (13)三、非定型设备 (13)四、设备一览表 (15)五、设备简图 (20)第一章工艺简介一、概述中国石化股份有限公司上海高桥分公司炼油事业部是具有五十多年历史的加工低硫石蜡基中质原油的燃料——润滑油型炼油企业,根据中国石化股份有限公司原油油种变化和适应市场发展的需求,上海高桥分公司到2007年以后除了加工大庆原油、海洋原油等低硫原油外,将主要加工含硫2.0%左右的含硫含酸进口原油。
由于常减压生产的减压蜡油和延迟焦化装置生产的焦化蜡油中含有较多的不饱和烃及硫、氮等有害的非烃化合物,这些产品无法达到催化裂化装置的要求。
为了使二次加工的蜡油达到催化裂化装置的要求,必须对焦化蜡油和减压蜡油进行加氢精制,因此上海高桥分公司炼油事业部进行原油适应性改造时,将原100万吨/年柴油加氢精制装置改造为100万吨/年蜡油加氢装置。
本装置的建设主要是为了催化裂化装置降低原料的硫含量和酸度服务。
本装置由中国石化集团上海工程有限公司设计,基础设计于2005年6月份完成,2005年8月份进行了基础设计审查,工程建设总投资2638.73万元,其中工程费用2448.74万元。
2006年7月降蜡油含硫量由原设计2.44%提高至3.28%,工程建设总概算增加820.8万元。
二、装置概况及特点1.装置规模及组成蜡油加氢精制装置技术改造原料处理能力为100万吨/年,年开工时数8400小时。
本装置为连续生产过程。
主要产品为蜡油、柴油、汽油。
本装置由反应部分、循环氢脱硫部分、氢压机部分(包括新氢压缩机、循氢压缩机)、加热炉部分及公用工程部分等组成。
2.生产方案混合原料经过滤后进入缓冲罐,用泵升压,经换热、混氢,再经换热进入加热炉,加热至350℃后进反应器进行加氢,反应产物经换热后进热高分进行气液分离,气相进一步冷却,进冷高分进行气液分离,气相进新增的循环氢脱硫塔脱硫后作为循环氢与新氢混合,组成混合氢循环使用;液相减压后至热低分,热低分的液相至催化裂化装置。
热低分气相经冷凝冷却至冷低分,冷低分的液相至汽柴油加氢装置。
3.装置平面布置在总体布置,节约用地的基础上,根据生产流程、防火、防爆、安全、卫生、环境保护、施工、检修等要求,结合场地自然条件,紧凑、合理地布置。
力求工艺流程合理,物料流线短,并充分依托、利用现有设施和资源,节约建设投资,同时满足生产、操作、节能、有利管理的要求。
本装置建东有#3常减压蒸馏装置,建南是常减压装置的原料罐区,建西是延迟焦化装置,建北与催化重整装置组成联合装置,加热炉、氢压机、控制室等集中布置,功能分区,保留6米宽的消防、检修通道,达到节约用地、节能、安全、紧凑的要求。
防火间距符合规范。
4.工艺技术特点⑴为避免原料油与空气接触氧化产生聚合物,减轻高温部位的结焦,故在原料油缓冲罐的罐顶采用了燃料气保护。
⑵原料油经预热后与氢气在换热器前混合,这样可提高换热器的换热效率,减少进料加热炉炉管结焦。
⑶在热高分顶出口空冷器上游设置注水设施,避免铵盐析出堵塞管线和设备。
⑷循环氢系统增加脱硫塔,进行脱除硫化氢。
⑸在反应部分的流程设计中,考虑了催化剂预硫化设施。
预硫化采用液相预硫化方法,预硫化油为直馏煤油,硫化剂为二甲基二硫。
催化剂再生按器外再生考虑。
⑹分馏部分采用单塔汽提流程,即从反应油气中分离出来的液相反应生成油先进入脱硫化氢塔,用过热蒸汽汽提方法将硫化氢脱除,然后至催化装置热进料或者冷却后去罐区。
脱硫化氢塔脱除的含硫化氢干气自压至制氢装置或干气脱硫装置。
⑺本装置的最主要工艺特点就是采用了热高分流程。
热高分流程能充分地利用热能,降低能耗,它主要是将反应生成物经热高压分离器及热低压分离器分离后,大部分的液相物料不必经过冷却后再换热的过程,而直接由分离器压至分馏部分,这样使热量得到了最有效的利用。
三、原材料及产品性质1.原料本装置的原料为焦化蜡油和减压蜡油的混合原料。
本装置的补充氢由80万吨/年连续重整装置提供,其组成详见表32. 产品本装置的主要产品为汽油、柴油和蜡油。
3. 辅助材料性质⑴催化剂及保护剂的物化性质⑵二甲基二硫市售工业标准⑶苯甲酸胺市售工业标准⑷直馏煤油四、生产工序本装置的生产工序分为反应、分离和循环氢脱硫三部分。
1.反应工序混合原料自装置外来,在原料油缓冲罐液面控制下,通过原料油过滤器进入原料缓冲罐。
自原料缓冲罐出来的原料油经原料泵升压后,在流量控制下,经换热器换热后与混合氢混合,经反应流出物/混合进料换热器换热后进入反应进料加热炉加热至反应所需温度后进入加氢精制反应器,在反应器内进行加氢反应,主要是脱除其中的有机硫、氮、氧化物,以及烯烃饱和,以提高汽柴油的质量。
反应产物进入产物分离器,经气液相分离,气相经氢气循环机作为循环氢,液相则进入分馏系统。
2.分离工序分离工序是将加氢反应后的生成油中的H2S、NH3、H2O脱除,以保证产品中杂质含量合格。
反应生成油(柴油蜡油混合组分)从热低分D603进入脱硫化氢塔,塔底用过热蒸汽汽提,以达到脱除杂质的目的。
热低分的汽柴油组分直接进柴油加氢装置。
3.循环氢脱硫工序自D-604顶部出来的冷高分气(循环氢)经脱硫塔前分离器(D-621)分液后进循环氢脱硫塔(C-603),由溶剂再生装置再生后的贫胺液经贫胺液水冷器(E-611)、贫胺液罐(D-620)、贫胺液泵(P-618/A.B)后进入C-603作为吸收剂吸收循环氢中的硫化氢,通过调节冷却水量控制进C-603的贫胺液与脱硫气体的温差为5℃。
C-603底部的富胺液回加氢裂化胺再生装置再生。
五、装置的生产原理焦化蜡油和减压蜡油在一定的温度、压力下,借助于催化剂进行加氢脱金属、脱硫、脱氮、烯烃和芳烃饱和、部分转化等反应,同时对含硫量较高的循环氢进行脱硫。
从而使精制蜡油符合催化裂化装置进料的要求。
加氢精制经过几十年的发展,工艺技术水平有了很大提高,并趋于成熟。
FF-14催化剂是针对蜡油而开发的加氢精制催化剂,它具有孔结构合理、酸性适中等特点,中型加氢装置评价结果表明:FF-14催化剂在保持高加氢脱氮活性的同时,催化剂的加氢脱硫活性明显高于参比剂,可以提高蜡油加氢精制装置脱硫能力,并且不降低脱氮和芳烃饱和能力。
故本次设计采用FF-14催化剂。
本次蜡油加氢精制装置技术改造,利旧原汽柴油加氢精制装置,工艺流程仍采用热高分流程,新增循环氢脱硫系统,停开分馏塔C602。
六、工艺流程说明温度80℃的减压蜡油和焦化蜡油在罐区用泵送入装置后按一定比例混合,通过原料油过滤器(FL-601/A.B)除去原料中大于25微米的颗粒后,进入原料油缓冲罐(D-601),该罐顶用燃料气进行气封,以达到隔绝空气、防止油品氧化之目的。
然后用进料泵(P-601/A.B)将混合蜡油从D-601抽出升压后,经原料油/精制蜡油换热器(E-604/A.B)换热后与混合氢混合,该混合进料经反应流出物/混合进料换热器(E-601/A~C)换热后进入反应进料加热炉(F-601),加热至350︒C(末期375℃)后进入加氢精制反应器(R-601)。
由R-601出来的反应物经E-601/A~C与混合进料换热温度降至220︒C后,进热高压分离器(D-602)。
热高分气体经热高分气/混合氢换热器(E-602)、热高分气空冷器(A-601/A~D)、热高分气冷却器(E-603)冷至45︒C后进入冷高压分离器(D-604) 进行油、气、水三相分离。
为防止热高分气在冷却过程中析出铵盐,堵塞管路和设备,通过除盐水泵(P-602/A~C)抽取除盐水罐(D-611)的除盐水,注入A-601前。
自D-604顶部出来的冷高分气(循环氢)经脱硫塔前分离器(D-621)分液后进循环氢脱硫塔(C-603),由加氢裂化胺再生装置后的贫胺液经贫胺液水冷器(E-611)、贫胺液罐(D-620)、贫胺液泵(P-618/A.B)后进入C-603作为吸收剂吸收循环氢中的硫化氢,通过调节冷却水量控制进C-603的贫胺液与脱硫气体的温差为5︒C。
C-603底部的富胺液回加氢裂化胺再生装置再生。
脱硫后的循环氢经循环氢压缩机入口分液罐(D-610)分液、循环氢压缩机(K-602)升压后,与来自新氢压缩机(K-601/A.B)出口的新氢混合成为混合氢循环使用。
D-604的油相经液控阀降压后进入冷低压分离器(D-605)。
D-602的热高分油经液控阀降压后,进入热低压分离器(D-603),D-603气相经热低分气冷却器(E-605)冷却到45︒C后与冷高分油混合进入冷低压分离器(D-605)。
D-603底部的热低分油(精制蜡油)进入脱硫化氢塔,塔底用过热蒸汽汽提,以达到脱除杂质的目的。
C601底油与原料油在E-604/A.B换热至160︒C后作为热出料至催化裂化装置。
停工时精制蜡油通过精制蜡油空冷器A-604/A~D冷却至90︒C去罐区。
D-605的冷低分油(汽柴油),去柴油加氢精制装置。
停工时去罐区。
D-604 、D-605底部排出的含硫污水自压至酸性水处理装置。
D-605顶部的含硫气体,自压至140万吨/年加氢裂化装置脱硫塔。
D-610排放的废氢自压至火炬管网。
压力为1.9~2.0MPa的补充氢由连续重整装置来,经新氢压缩机入口分液罐(D-608)分液后,再经新氢压缩机(K-601/A.B)升压后与K-602出口的循氢混合成为混合氢。
七、加工方案1.物料平衡4.消耗指标5.辅助材料及消耗6.主要操作条件⒎操作条件的影响7.1 加氢反应器影响加氢转化催化剂活性因素甚多,不同使用条件如温度、压力、空速、H2/油,将直接影响原料中有机硫的转化率,故选择合适的操作条件对有机硫加氢转化活性极为重要。
①反应温度有机硫加氢转化反应是放热反应,因此从热力学角度看,降低温度有利于转化反应,温度越低,有机硫的平衡浓度愈低,但因为加氢转化反应的平衡常数较大,因此从提高反应速度着想,反应应在较高温度下进行。
因此操作温度一般为280~370℃。
如400℃就有可能产生聚合结焦副反应(尤其对C7以上重质烃最重要)。
当温度超过430℃时可能发生析炭反应,放出的大量热使催化剂床层飞温,损坏催化剂和设备。
因此,反应温度应严格控制,特别是对含烯烃较多或碳氧化物含量较高的原料,反应起始温度不要控制的过高。