生产线平衡的我秘笈(PPT 69页)
合集下载
怎样保持生产线平衡PPT课件
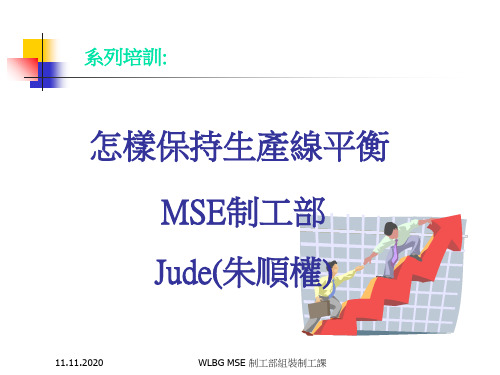
11.11.2020
(直通流程 1 )
(直通流程 2 )
WLBG MSE 制工部組裝制工課
相關的概念
概念8:高效率 1. 通常認為高效率就是:快速,簡單&大規模 2. 我們認為沒有浪費的時候才是高效率的
操作效率=實際產量/設定產能*100% 整體工廠效率(OPE)=平衡率*稼動率*操作效率
11.11.2020
WLBG MSE 制工部組裝制工課
相關的概念
概念9:改善 I. 同樣的投入更大的輸出; II. 不增值(無效)增值(有效)
?不增值?
等待 不良
庫存 移動
……
11.11.2020
WLBG MSE 制工部組裝制工課
例1: 減少移動與庫存提高效率
11.11.2020
WLBG MSE 制工部組裝制工課
T1
T3 T4 T5
S1 S2 S3 S4 S5 工站
單件標准時間 = T1+T2+T3+T4+T5 (流程中各工站所有動作標准時間之和)
11.11.2020
WLBG MSE 制工部組裝制工課
相關的概念
概念2:可供工時
可供工時=可供時間 *人數-借出工時 可供時間:上班時間內,為某產品生產而投入 的所有時間
上例中,若換線時間是15分鍾,則計劃停線工時為20人 *15min=300min=5H,則投入工時和稼動率為
60H-5H=55H 稼動率=55H/60H=92%
11.11.2020
WLBG MSE 制工部組裝制工課
相關的概念
概念4:設定產能 設定產能(H) =3600(S)/瓶頸時間(S) 設定產能(班)=投入時間/瓶頸時間(S)
系列培訓:
(直通流程 1 )
(直通流程 2 )
WLBG MSE 制工部組裝制工課
相關的概念
概念8:高效率 1. 通常認為高效率就是:快速,簡單&大規模 2. 我們認為沒有浪費的時候才是高效率的
操作效率=實際產量/設定產能*100% 整體工廠效率(OPE)=平衡率*稼動率*操作效率
11.11.2020
WLBG MSE 制工部組裝制工課
相關的概念
概念9:改善 I. 同樣的投入更大的輸出; II. 不增值(無效)增值(有效)
?不增值?
等待 不良
庫存 移動
……
11.11.2020
WLBG MSE 制工部組裝制工課
例1: 減少移動與庫存提高效率
11.11.2020
WLBG MSE 制工部組裝制工課
T1
T3 T4 T5
S1 S2 S3 S4 S5 工站
單件標准時間 = T1+T2+T3+T4+T5 (流程中各工站所有動作標准時間之和)
11.11.2020
WLBG MSE 制工部組裝制工課
相關的概念
概念2:可供工時
可供工時=可供時間 *人數-借出工時 可供時間:上班時間內,為某產品生產而投入 的所有時間
上例中,若換線時間是15分鍾,則計劃停線工時為20人 *15min=300min=5H,則投入工時和稼動率為
60H-5H=55H 稼動率=55H/60H=92%
11.11.2020
WLBG MSE 制工部組裝制工課
相關的概念
概念4:設定產能 設定產能(H) =3600(S)/瓶頸時間(S) 設定產能(班)=投入時間/瓶頸時間(S)
系列培訓:
生产线平衡分析.PPT
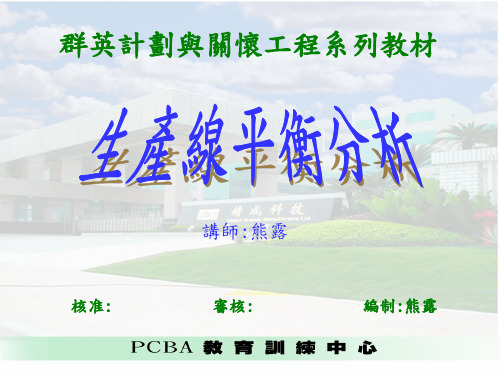
2.提高生產線平衡效率的意議 *提高作業員及設備工裝的工作效率; *減少單件產品的工時消耗,降低生產成本; *減少工序間的在制品,縮小其周轉場所; *可以縮短生產周期; *削除人員等待現象,提升員工士氣; *提升整體生產能力、生產效率和降低生 產現場的各種浪費; *可以穩定和提升產品品質.
第二節
群英計劃與關懷工程系列教材
講師:熊露
核准: 核准:
審核: 審核:
編制: 編制:熊露
第一節 木桶定律與生產線平衡 一、何為木桶定律 1.木桶定律 一只木桶盛水多少,並不取決於桶壁上最高的那 塊木板,而恰恰取決於桶壁上最短的那塊木板,這一規 律我們稱之為“木桶定律”. 2.木桶定律的三個推論 (1)只有桶壁上的所有木板都足夠高,木桶才能盛 滿水. (2)所有木板高出最低木板的部分都是沒有意義 的,而且高出越多,浪費就越大. (3)提高木桶容量最有效的辦法就是設法加高最 低木板的高度
2.平衡改善的實施步驟 第一步:明確改善目的與對象. *是不是因為生產量變動(增產或減產)而進行的改善? *是否為了提高生產率、減少作業員? *改善對象是一條生產線、某段工序還是整個流程? 第二步:了解、分析生產現狀及相關人員的工作狀況. 如各工位或工序的良品率有多高?人員出勤狀況、產品 加工的難易度、品質事故的發生點等. 第三步:了解產品工藝流程並分解各工程的作業要素. 根據工作分析圖了解加工作業內容,依據作業拆分原則 拆分各工程的作業要素. 第四步:對各作業要素進行時間觀測. 第五步:對觀測記錄的結果進行處理,得出各作業要素的標準 時間,在進行數據處理應注意如下兩點: *剔除異常值、排除各種影響作業的因素,最后制定 出各作業要素的標準時間;
例如:一條有5個工序的生產線(如下圖所示),第3個工 序是最緩慢的工序,作業時間為30秒,如果不是“一個流”生 產, 那麼第1道工序要比第3道工序快17%,第2道工序要比第3道工 序快33%左右.換句話說,每當前兩個工序生產5個產品后第3 道工序就會有一個在制品堆積,一個小時后就會堆積20多個 產品,而后2道工序的人卻在等待.整個陰影部分都是平衡損 失,如果將第3工序的部分作業內容調整給第2工序后,那麼, 生產線的平衡損失時間得到減少,同時整體產能可以提升17%.
生产线平衡分析课件
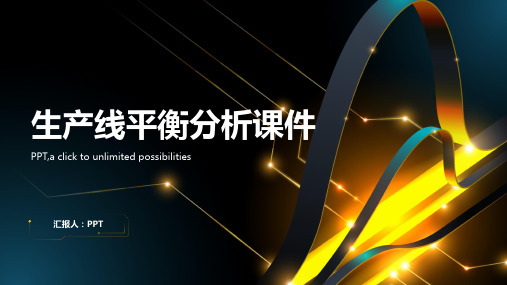
生产线平衡分析课件
PPT,a click to unlimited possibilities
汇报人:PPT
目录
01 添 加 目 录 项 标 题 03 生 产 线 平 衡 分 析 方 法 05 生 产 线 平 衡 优 化 策 略 07 生 产 线 平 衡 案 例 分 析
02 生 产 线 平 衡 概 述 04 生 产 线 平 衡 评 价 指 标 06 生 产 线 平 衡 实 施 步 骤
平衡率指标
定义:平衡率指标是指生产线各工 序时间与瓶颈工序时间的比值
意义:平衡率指标用于衡量生产线 平衡程度,即生产线各工序时间分 布的均匀程度
添加标题
添加标题
添加标题
添加标题
计算方法:平衡率 = (各工序时间 总和 / 瓶颈工序时间) × 100%
改善方向:通过调整生产线各工序 的作业时间,降低瓶颈工序时间, 提高平衡率指标,以实现生产效率 的提升
确定需要收集的数 据和信息类型
确定数据和信息来 源
制定收集计划和时 间表
确保数据和信息的 准确性和完整性
进行分析和评估
确定生产线的瓶颈工序 分析生产线的平衡状况 制定平衡改善方案 实施平衡改善方案并进行评估
制定改进措施并实施
根据分析结果,制定针对性的改进措施 确定改进措施的优先级和实施顺序 制定详细的实施计划和时间表 确保改进措施得到有效执行和监控
明确分析目标:确定生产 线平衡的目标和范围
收集数据:收集生产线上 的相关数据,包括设备、 人员、时间等
流程图绘制:根据收集的 数据绘制流程图,展示生 产线的运行过程
平衡点确定:根据流程图 确定生产线上的平衡点, 即瓶颈工序
平衡方法选择:根据平衡 点选择合适的平衡方法, 如调整设备、优化流程等
PPT,a click to unlimited possibilities
汇报人:PPT
目录
01 添 加 目 录 项 标 题 03 生 产 线 平 衡 分 析 方 法 05 生 产 线 平 衡 优 化 策 略 07 生 产 线 平 衡 案 例 分 析
02 生 产 线 平 衡 概 述 04 生 产 线 平 衡 评 价 指 标 06 生 产 线 平 衡 实 施 步 骤
平衡率指标
定义:平衡率指标是指生产线各工 序时间与瓶颈工序时间的比值
意义:平衡率指标用于衡量生产线 平衡程度,即生产线各工序时间分 布的均匀程度
添加标题
添加标题
添加标题
添加标题
计算方法:平衡率 = (各工序时间 总和 / 瓶颈工序时间) × 100%
改善方向:通过调整生产线各工序 的作业时间,降低瓶颈工序时间, 提高平衡率指标,以实现生产效率 的提升
确定需要收集的数 据和信息类型
确定数据和信息来 源
制定收集计划和时 间表
确保数据和信息的 准确性和完整性
进行分析和评估
确定生产线的瓶颈工序 分析生产线的平衡状况 制定平衡改善方案 实施平衡改善方案并进行评估
制定改进措施并实施
根据分析结果,制定针对性的改进措施 确定改进措施的优先级和实施顺序 制定详细的实施计划和时间表 确保改进措施得到有效执行和监控
明确分析目标:确定生产 线平衡的目标和范围
收集数据:收集生产线上 的相关数据,包括设备、 人员、时间等
流程图绘制:根据收集的 数据绘制流程图,展示生 产线的运行过程
平衡点确定:根据流程图 确定生产线上的平衡点, 即瓶颈工序
平衡方法选择:根据平衡 点选择合适的平衡方法, 如调整设备、优化流程等
生产线平衡分析与改善(最全面的IE分析,生产线平衡)ppt课件

0.1
0.2 0.5 1.0 2.0 5.0 ≥10
<1.0 100 50 20 10 5 2 1
1.0~2.0 50 20 20 10 5 2 1
2.0~5.0 20 20 10 5 2 2 1
5.0~10 10 10 5 2 2 1 1
13
三、流水生产线平衡的设计方法
3、 单品种流水线平衡方法 ● 案例:生产线平衡分析案例(直流式流程序为例)
10 A
工序1
工序2 11 B
工序3 12 E
C5
4 D
工序4 3
F
11 H
7
工序6
G
3 I
工序5 34
五、生产线平衡的其它案例
装配流水线平衡的方法很多,这里介绍一种简便而又能取得 满意效果的方法——阶位法。 阶位法的工作步骤如下
① 作图表示装配工艺过程中各作业元素的先后关系,并标 明每项作业元素的时间。 ② 从作业元素先后关系图找出每项作业元素的后续作业 元素,计算它们的时间总和,即每项作业元素的阶位值。 ③ 按阶位值的大小,由大到小,将作业元素排队,制成 作业元素阶位表。 ④ 从阶位值最高的作业元素开始,向工作地分配作业要 素。每分配一项作业元素,计算一次在节拍时间内的剩余 时间。若剩余时间足够安排另一项作业元素,从阶位表中 找出阶位值次高的作业元素分给该工作地。若剩余时间不 够安排其它作业元素,就向下一个工作地分配,直到全部 作业要素都被安排入工作地为止。
比较B、C两个工作站,将可发现B工作站的产能为C工作站的 2.69倍,B、C两个工作站将积压大量的半成品。若以传统追求 各工作站提升效率的方式进行管理,B工作站的效率提升,只会 恶化B、C站的半成品积压的浪费,而无助于整体产量的提高 (假设B工作站经训练生产效率达100%,则B工作站每小时产量 将达702.35个,产量为C工作站的3.36倍)。
生产线平衡的秘籍

必要重新安排。 (三)虽然使用批量生产,因生产量增加,有必
要改用生产线化。 (四)现在实施生产线生产,由于产品一部分变
更,修正工程分析必要。 (五)工序间的负荷不平衡,要改善生产线,其
工程分析的顺序或重点会改变其编排。
16
3、生产线工程分析及编排要点
(A)装配顺序的考量。 (B)时间的分析。 (C)主生产线和副生产线串联。 (D)必要条件的分析:
9
SDCA 与 PDCA
PD AC
現有 水準
PD AC
SD AC
SD AC
具體落實的方法:QC Story
SD AC
期望 水準
S:標準化程序,SOP (P:Plan計劃)
D:Do執行 C:Check檢查 A:Action行動
‧維持:(Standardization)DCA 依標準SOP而DCA
‧改善:I(Improvement)DCA 依改善之計劃而DCA
步骤4 准备改善作业的进行 步骤5 藉着5S及目视管理不断改善“个别作业准备”的目 8
維持/改善/創新 三階段
高階主管 中階主管 基層員工
維持
創新 改善
維持(Maintenance): ‧遵守作業標準
改善(Improvement): ‧改良改善
創新(Innovation,Break-Through): ‧結構性改善 ‧滿足客戶潛在需求
搬运设备选定
生产线布置设计
工厂 布置原则
稼动时间 预测不良率等
输送带上 的产品间隔 生产线速度
产品特性 作业特性
7
缩短准备时间方法
步骤1 对准备作业分析,把内部作业准备和外部作业准备 区分开来。
步骤2 分开外部作业准备,尽可能进行外部作业准备,缩 短机械停待的时间。
要改用生产线化。 (四)现在实施生产线生产,由于产品一部分变
更,修正工程分析必要。 (五)工序间的负荷不平衡,要改善生产线,其
工程分析的顺序或重点会改变其编排。
16
3、生产线工程分析及编排要点
(A)装配顺序的考量。 (B)时间的分析。 (C)主生产线和副生产线串联。 (D)必要条件的分析:
9
SDCA 与 PDCA
PD AC
現有 水準
PD AC
SD AC
SD AC
具體落實的方法:QC Story
SD AC
期望 水準
S:標準化程序,SOP (P:Plan計劃)
D:Do執行 C:Check檢查 A:Action行動
‧維持:(Standardization)DCA 依標準SOP而DCA
‧改善:I(Improvement)DCA 依改善之計劃而DCA
步骤4 准备改善作业的进行 步骤5 藉着5S及目视管理不断改善“个别作业准备”的目 8
維持/改善/創新 三階段
高階主管 中階主管 基層員工
維持
創新 改善
維持(Maintenance): ‧遵守作業標準
改善(Improvement): ‧改良改善
創新(Innovation,Break-Through): ‧結構性改善 ‧滿足客戶潛在需求
搬运设备选定
生产线布置设计
工厂 布置原则
稼动时间 预测不良率等
输送带上 的产品间隔 生产线速度
产品特性 作业特性
7
缩短准备时间方法
步骤1 对准备作业分析,把内部作业准备和外部作业准备 区分开来。
步骤2 分开外部作业准备,尽可能进行外部作业准备,缩 短机械停待的时间。
生产线平衡培训课程PPT课件

第13页/共48页
二. 生产线平衡分析方法
• 案例计算
第14页/共48页
二. 生产线平衡分析方法
• 案例
第15页/共48页
二. 生产线平衡分析方法
6. 生产线平衡分析方法
第16页/共48页
二. 生产线平衡分析方法
7. 改善瓶颈岗位
第17页/共48页
二. 生产线平衡分析方法
• 改善四大原则
• 较少动作次数
改善前生产线平衡率=(18+16+24+37+45+16)/(37*7)*100%=60.2%
• 改善前生产线各工位平衡图
第42页/共48页
四. 线平衡经典案例分享
2. 改善前分析
第43页/共48页
四. 线平衡经典案例分享
பைடு நூலகம்3. 改善前后对比
第44页/共48页
四. 线平衡经典案例分享
3. 改善前后对比
B值得最优值为“1”
第29页/共48页
三. B值、F值的定义和计算
2. 一个流成产 One world、One dream One piece、One flow
• One piece flow是指单件进行生产,即人工每次只加工一件产品或部件,理想状态下,任何操作工位 间和工作内的多余的WIP为零。
• 例1:缩短生产节拍 • 提升生产速度,维持人手不变。
第20页/共48页
二. 生产线平衡分析方法
• 例2:减少人手(1) • 减少人员,维持生产速度不变
第21页/共48页
二. 生产线平衡分析方法
• 例3:减少人手(2) • 降低线体速度,减少生产产量
第22页/共48页
二. 生产线平衡分析方法
二. 生产线平衡分析方法
• 案例计算
第14页/共48页
二. 生产线平衡分析方法
• 案例
第15页/共48页
二. 生产线平衡分析方法
6. 生产线平衡分析方法
第16页/共48页
二. 生产线平衡分析方法
7. 改善瓶颈岗位
第17页/共48页
二. 生产线平衡分析方法
• 改善四大原则
• 较少动作次数
改善前生产线平衡率=(18+16+24+37+45+16)/(37*7)*100%=60.2%
• 改善前生产线各工位平衡图
第42页/共48页
四. 线平衡经典案例分享
2. 改善前分析
第43页/共48页
四. 线平衡经典案例分享
பைடு நூலகம்3. 改善前后对比
第44页/共48页
四. 线平衡经典案例分享
3. 改善前后对比
B值得最优值为“1”
第29页/共48页
三. B值、F值的定义和计算
2. 一个流成产 One world、One dream One piece、One flow
• One piece flow是指单件进行生产,即人工每次只加工一件产品或部件,理想状态下,任何操作工位 间和工作内的多余的WIP为零。
• 例1:缩短生产节拍 • 提升生产速度,维持人手不变。
第20页/共48页
二. 生产线平衡分析方法
• 例2:减少人手(1) • 减少人员,维持生产速度不变
第21页/共48页
二. 生产线平衡分析方法
• 例3:减少人手(2) • 降低线体速度,减少生产产量
第22页/共48页
二. 生产线平衡分析方法
生产线平衡培训资料(国内版本)PPT课件
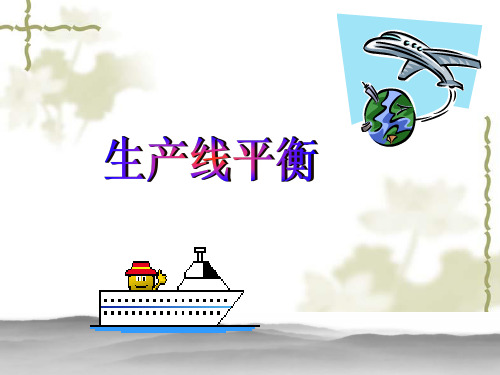
概念4:设定产能
设定产能(H) =3600(S)/瓶颈时间(S)
设定产能(班)=投入时间/瓶颈时间(S)
思考:1)为什么设定产能(班) =投入工時/总工时
总工时=瓶颈时间*作业人数
2)总工时 VS 单件标准时间
最费时的作业决定了 整体效率(产能)?
总工时应大于单件标 准时间?
概念5:实际产量
实际产量是可供时间内所产出的良品数
概念9:改善
相关的概念
I. 同样的投入更大的输出;
II. 不增值(无效)增值(有效)
?不增值?
等待 不良
库存 移动
……
例1: 减少移动与库存提高效率
例2: 减少无效动作提高效率
2020/11/24
10
概念10:多能工
2020/11/24
11
平衡的手法
工时测量 山积表 程序改善 损失分析 作业条件改善 打破平衡
概念8:高效率
1. 通常认为高效率就是:快速,简单和规模
2. 我们认为没有浪费的時候才是高效率的
操作效率=实际产量/设定产能×100%
整体工厂效率(OPE)=平衡率*利用率×操作效率
(直通流程 2 )
设计者责 任
管理者责 任
操作者责 任
2020/11/24 整体人(员 O 的 P∑ in E 总 直 总 )工 接 序 效 生 × 满 标 产 足 准 率 勤 人 客 工 工 员 户 时 时 投 X 需 1入 要 0 % 总 的 09考 良量 5次为宜; ❖ 量测人员应站在作业员斜后面1米以外, 以能看清楚全部操作动作为准则; 测试中不能打扰作业员的正常操作,和 引起作业员的紧张;
时间测量流程
作业內容
测试中判断作业员的速度水平,并作
- 1、下载文档前请自行甄别文档内容的完整性,平台不提供额外的编辑、内容补充、找答案等附加服务。
- 2、"仅部分预览"的文档,不可在线预览部分如存在完整性等问题,可反馈申请退款(可完整预览的文档不适用该条件!)。
- 3、如文档侵犯您的权益,请联系客服反馈,我们会尽快为您处理(人工客服工作时间:9:00-18:30)。
第二次浪费 生产过多浪费
多余折旧费用 多余的保养费用 多余的利息费用 多余的劳务费用
第三次浪费 库存过剩的浪费
第四次浪费 ①多余的仓库 ②多余的搬运人员 ③多余的搬运设备 ④多余的库存管理人员、
维持品质人员
制造成本增加
4
3. 总结降低成本示意图
降 低 变 动 费
降 低 成 本
降低单价
最佳的采购
最佳的规格等级、 原材料配比等
生产线平衡 (工程分割结合)
所要工程数
所要作业人员
人员编成
全面工厂 布置计划
生产计划 规制时间推算
产品的尺寸 作业性其他 工程间隔 生产线长度
搬运设备选定
Байду номын сангаас
生产线布置设计
工厂 布置原则
稼动时间 预测不良率等
输送带上 的产品间隔 生产线速度
产品特性 作业特性
7
缩短准备时间方法
步骤1 对准备作业分析,把内部作业准备和外部作业准备 区分开来。
使各作业员的工 作范围能弹性的
扩大或缩小
「省人化」 减少各制程的作
业人数
连结U型生产线 的机械配置
多功能作业员 工作轮调
修正标准操作 流程
制程的改善
改善作业
机器的改善 (自动化) 13
改善活动的框架图
生产力的提高
作业人员的削减 (省人化)
标准操作 流程表的修正
人性尊重 作业员提高士气
作业标准化
现场改善的活动
制造工程部门 生产技术、安排、作业指导书
采购
外购、外发、计划, 库存管理
制造部门 小日程管理/作业指导 进度/在制/工具/品质管理
质量管理 成本管理
6
5、装配生产线安排流程
图面
试作
出勤率其他
支援人员 间接人员
场区空间分析
•作业空间 •保管空间
装配顺序的决定
时间分析
主线、副线区分 编成条件分析
•优先顺位 •作业位置 •设备
作业员在一周期时间 内可操作许多机器
调查故障,或者是 异常的根本原因
仅供给「良品」
人力操作和机器 作业可以分离
「指示灯」点亮
必要的数量或者 是作业完成,机 器会自动停止
故障被发觉之后, 机器会自动停止
自动化=偏差(异常)发觉后机器会自动停止
12
「省人化」的过程
「少人化」 为适应需要品的变动,对各制程作业人数作弹性变化
最低库存 确保库存最低量, 没有无用或多余 东西
个别工序的改善
让每个人都成为多 能高手,提高个人 的改善意识和技巧
基础的改善
运用5S,现 时现地现物管 理,清除浪费
成本降低的整体 实现
通过VA/VE及流
程改善做最佳組
合
3
2. 造成成本高涨的因果图
第一次浪费 ① 设备过剩 ② 库存过剩 ③ 人员过剩
a.优先顺序位分析 b.作业位置分析 c.设备限制分析 (E)生产线平衡(Line Balance)
17
生產線平衡
1.測定標準工時 2.決定不平衡率(N.B)-----目標為 5% 以下 中国最大的资料库下载
S
机械设备故障和不良的排除 和
目视管理
减
自动化
少
批次大小最优化
浪
提高作业人员技能 日程计划和进度的管理
费
5
4. 生产管理的全貌
营销业务 客户讯息往来 确认订单
预测订单情况 销售计划
产品负责人 订单、出货管理
研发设计部门 研发设计 技术资料整理
生产管理部门
大日程计划
材料计划
产能负荷计划
中日程计划
发行作业指示书
步骤2 分开外部作业准备,尽可能进行外部作业准备,缩 短机械停待的时间。
步骤3 改善内部作业准备,缩短准备的时间。 工具的改善 确定下一个要加工零部件的摆放位置 确定加工完毕零部件的摆放位置 改善零部件的装卸方法 减少调整作业 对于模具、夹具之高度,可进行标准化
步骤4 准备改善作业的进行 步骤5 藉着5S及目视管理不断改善“个别作业准备”的目 8
小集团活动
人的作业改善 机器的改善(自动化) 材料消耗品使用上的改善 QCC 提案
制度
改善的动机
看板制度
14
二. 工程分析及编排要点
1、工程分析
所谓的工程分析就是依照工程顺序为 了达成生产效果,把设备和人配置在连续 生产线的作业区域内所安排的设计。
15
2、工程分析的必要性
(一)投入新产品的大量生产。 (二)虽然是生产线生产,但经常更换形式,有
SD AC
SD AC
具體落實的方法:QC Story
SD AC
期望 水準
S:標準化程序,SOP (P:Plan計劃)
D:Do執行 C:Check檢查 A:Action行動
‧維持:(Standardization)DCA 依標準SOP而DCA
‧改善:I(Improvement)DCA 依改善之計劃而DCA
1. 正确生产管理工厂改善图
良好生产性保全
保护我们的设备, 实现设备的良好运 行
品质管理及保证
改善质量,提供 质量保证
车间之间的协调
以满足顾客为目标, 以“下一道工序是 客户”的认知,推 动车间之间的协调
用“生产管 理”改善和 改变工厂, 完成做强做 大的目标
保证及缩短交期 创建-灵活及可 目视管理的工厂
必要重新安排。 (三)虽然使用批量生产,因生产量增加,有必
要改用生产线化。 (四)现在实施生产线生产,由于产品一部分变
更,修正工程分析必要。 (五)工序间的负荷不平衡,要改善生产线,其
工程分析的顺序或重点会改变其编排。
16
3、生产线工程分析及编排要点
(A)装配顺序的考量。 (B)时间的分析。 (C)主生产线和副生产线串联。 (D)必要条件的分析:
外协价格的降低
提高良品 率材料利
用率
降低不良率 降低损耗
消除库存
压
缩
提高生产效
固
率、速度、 改善设备开工率、
定
灵活性
改变生产方式
费
减少支出
合理的采购战略 批量的改善
VA/VE 生产技术的改善 制造工艺的改善
外协批量改善 简化生产的设计
易于生产的设计
设计更改的最优化
工序布局的改善 工具、夹具改善
5
加工条件最优化
‧創新
10
如何判定生产合理化?
设备的自动化程度不是判定的基准 库存品的高低才是判定的基准
库存高,生产合理化程度低 库存低,生产合理化程度高
降低库存才能达到合理化
11
如何达成「自动化」的目的
适应可能的生产
降低成本
品质保证 人性的尊重
及时生产的达成 作业人数的削减
改善活动(更正活动)
仅供给必要的数量
維持/改善/創新 三階段
高階主管 中階主管 基層員工
維持
創新 改善
維持(Maintenance): ‧遵守作業標準
改善(Improvement): ‧改良改善
創新(Innovation,Break-Through): ‧結構性改善 ‧滿足客戶潛在需求
9
SDCA 与 PDCA
PD AC
現有 水準
PD AC
多余折旧费用 多余的保养费用 多余的利息费用 多余的劳务费用
第三次浪费 库存过剩的浪费
第四次浪费 ①多余的仓库 ②多余的搬运人员 ③多余的搬运设备 ④多余的库存管理人员、
维持品质人员
制造成本增加
4
3. 总结降低成本示意图
降 低 变 动 费
降 低 成 本
降低单价
最佳的采购
最佳的规格等级、 原材料配比等
生产线平衡 (工程分割结合)
所要工程数
所要作业人员
人员编成
全面工厂 布置计划
生产计划 规制时间推算
产品的尺寸 作业性其他 工程间隔 生产线长度
搬运设备选定
Байду номын сангаас
生产线布置设计
工厂 布置原则
稼动时间 预测不良率等
输送带上 的产品间隔 生产线速度
产品特性 作业特性
7
缩短准备时间方法
步骤1 对准备作业分析,把内部作业准备和外部作业准备 区分开来。
使各作业员的工 作范围能弹性的
扩大或缩小
「省人化」 减少各制程的作
业人数
连结U型生产线 的机械配置
多功能作业员 工作轮调
修正标准操作 流程
制程的改善
改善作业
机器的改善 (自动化) 13
改善活动的框架图
生产力的提高
作业人员的削减 (省人化)
标准操作 流程表的修正
人性尊重 作业员提高士气
作业标准化
现场改善的活动
制造工程部门 生产技术、安排、作业指导书
采购
外购、外发、计划, 库存管理
制造部门 小日程管理/作业指导 进度/在制/工具/品质管理
质量管理 成本管理
6
5、装配生产线安排流程
图面
试作
出勤率其他
支援人员 间接人员
场区空间分析
•作业空间 •保管空间
装配顺序的决定
时间分析
主线、副线区分 编成条件分析
•优先顺位 •作业位置 •设备
作业员在一周期时间 内可操作许多机器
调查故障,或者是 异常的根本原因
仅供给「良品」
人力操作和机器 作业可以分离
「指示灯」点亮
必要的数量或者 是作业完成,机 器会自动停止
故障被发觉之后, 机器会自动停止
自动化=偏差(异常)发觉后机器会自动停止
12
「省人化」的过程
「少人化」 为适应需要品的变动,对各制程作业人数作弹性变化
最低库存 确保库存最低量, 没有无用或多余 东西
个别工序的改善
让每个人都成为多 能高手,提高个人 的改善意识和技巧
基础的改善
运用5S,现 时现地现物管 理,清除浪费
成本降低的整体 实现
通过VA/VE及流
程改善做最佳組
合
3
2. 造成成本高涨的因果图
第一次浪费 ① 设备过剩 ② 库存过剩 ③ 人员过剩
a.优先顺序位分析 b.作业位置分析 c.设备限制分析 (E)生产线平衡(Line Balance)
17
生產線平衡
1.測定標準工時 2.決定不平衡率(N.B)-----目標為 5% 以下 中国最大的资料库下载
S
机械设备故障和不良的排除 和
目视管理
减
自动化
少
批次大小最优化
浪
提高作业人员技能 日程计划和进度的管理
费
5
4. 生产管理的全貌
营销业务 客户讯息往来 确认订单
预测订单情况 销售计划
产品负责人 订单、出货管理
研发设计部门 研发设计 技术资料整理
生产管理部门
大日程计划
材料计划
产能负荷计划
中日程计划
发行作业指示书
步骤2 分开外部作业准备,尽可能进行外部作业准备,缩 短机械停待的时间。
步骤3 改善内部作业准备,缩短准备的时间。 工具的改善 确定下一个要加工零部件的摆放位置 确定加工完毕零部件的摆放位置 改善零部件的装卸方法 减少调整作业 对于模具、夹具之高度,可进行标准化
步骤4 准备改善作业的进行 步骤5 藉着5S及目视管理不断改善“个别作业准备”的目 8
小集团活动
人的作业改善 机器的改善(自动化) 材料消耗品使用上的改善 QCC 提案
制度
改善的动机
看板制度
14
二. 工程分析及编排要点
1、工程分析
所谓的工程分析就是依照工程顺序为 了达成生产效果,把设备和人配置在连续 生产线的作业区域内所安排的设计。
15
2、工程分析的必要性
(一)投入新产品的大量生产。 (二)虽然是生产线生产,但经常更换形式,有
SD AC
SD AC
具體落實的方法:QC Story
SD AC
期望 水準
S:標準化程序,SOP (P:Plan計劃)
D:Do執行 C:Check檢查 A:Action行動
‧維持:(Standardization)DCA 依標準SOP而DCA
‧改善:I(Improvement)DCA 依改善之計劃而DCA
1. 正确生产管理工厂改善图
良好生产性保全
保护我们的设备, 实现设备的良好运 行
品质管理及保证
改善质量,提供 质量保证
车间之间的协调
以满足顾客为目标, 以“下一道工序是 客户”的认知,推 动车间之间的协调
用“生产管 理”改善和 改变工厂, 完成做强做 大的目标
保证及缩短交期 创建-灵活及可 目视管理的工厂
必要重新安排。 (三)虽然使用批量生产,因生产量增加,有必
要改用生产线化。 (四)现在实施生产线生产,由于产品一部分变
更,修正工程分析必要。 (五)工序间的负荷不平衡,要改善生产线,其
工程分析的顺序或重点会改变其编排。
16
3、生产线工程分析及编排要点
(A)装配顺序的考量。 (B)时间的分析。 (C)主生产线和副生产线串联。 (D)必要条件的分析:
外协价格的降低
提高良品 率材料利
用率
降低不良率 降低损耗
消除库存
压
缩
提高生产效
固
率、速度、 改善设备开工率、
定
灵活性
改变生产方式
费
减少支出
合理的采购战略 批量的改善
VA/VE 生产技术的改善 制造工艺的改善
外协批量改善 简化生产的设计
易于生产的设计
设计更改的最优化
工序布局的改善 工具、夹具改善
5
加工条件最优化
‧創新
10
如何判定生产合理化?
设备的自动化程度不是判定的基准 库存品的高低才是判定的基准
库存高,生产合理化程度低 库存低,生产合理化程度高
降低库存才能达到合理化
11
如何达成「自动化」的目的
适应可能的生产
降低成本
品质保证 人性的尊重
及时生产的达成 作业人数的削减
改善活动(更正活动)
仅供给必要的数量
維持/改善/創新 三階段
高階主管 中階主管 基層員工
維持
創新 改善
維持(Maintenance): ‧遵守作業標準
改善(Improvement): ‧改良改善
創新(Innovation,Break-Through): ‧結構性改善 ‧滿足客戶潛在需求
9
SDCA 与 PDCA
PD AC
現有 水準
PD AC