微组装工艺流程
微组装技术简述及工艺流程及设备概述

微组装技术简述及工艺流程及设备概述微组装技术的工艺流程包括设计、加工、组装三个主要步骤。
首先,设计阶段需要对组装目标进行分析,并设计出符合要求的微零件。
其次是加工阶段,利用微加工技术对微零件进行精密加工,包括光刻、腐蚀、薄膜沉积等过程。
最后是组装阶段,通过微操作技术将微零件组装到目标物体上,包括自动化装配系统和微操作工具。
微组装技术的设备主要包括微加工设备和微操作设备。
微加工设备包括光刻设备、腐蚀设备、薄膜沉积设备等,用于对微零件进行精密加工。
微操作设备包括微操作工具、显微镜、自动化装配系统等,用于对微零件进行精确组装。
这些设备能够在微尺度上实现精密加工和组装,满足微组装技术的要求。
总的来说,微组装技术是一种十分重要的技术,在微纳米尺度上实现了精确加工和组装,为微纳米器件的制造提供了重要支持。
随着微加工技术和微操作技术的不断发展,微组装技术在未来将会有更加广泛的应用。
微组装技术是一种先进的制造技术,它在微纳米尺度上进行零部件的加工和组装,可以实现高效率、高精度和高灵活性的制造过程。
微组装技术在微电子、微机械、生物医学、光学等领域都有着广泛的应用前景。
本文将围绕微组装技术的设备概述、工艺流程和应用前景进行详细阐述。
首先,微组装技术的设备主要包括微加工设备和微操作设备。
微加工设备包括光刻设备、腐蚀设备和薄膜沉积设备等,用于对微零件进行精密加工。
光刻设备可以利用光刻胶对硅片进行图案化处理,形成微米尺度的光刻图案。
腐蚀设备可以将硅片进行精密腐蚀,实现微米尺度的结构加工。
薄膜沉积设备用于在硅片表面沉积金属膜或氧化物膜,形成微电子器件的电极或绝缘层。
这些设备可实现在微尺度上对材料的加工制备,为微组装技术提供了基础支持。
其次,微组装技术的微操作设备包括微操作工具、显微镜和自动化装配系统等,用于对微零件进行精确组装。
微操作工具是微组装过程中最基本的设备,它可以通过微操作手柄、微钳或微注射器等工具对微尺度零件进行操作。
微组装工艺

�路电成集片亿 081 要需约大国全年每在现 。币民人亿千几达将值产 年则�装封子电于用
2
后�主为壳外装封璃玻-属金型� eniltuO rotsisnarT� OT 的线引根三以代年 05 纪世 02 顿拉布 管体晶只一第 莱克肖 丁巴 。 史历的装封子电微创开�管体晶只一第明发室验实尔贝国美年 7491 程过展发、生产、一 展发的术技装封子电微 3.2.1 。术技装封� D3� 维 三的谓所是就这�展发向方 z 向上础基的装组维二在然 必装组子电�积面 的限有于对�上础基的 MCM 在�高 提断不的求要装组度密高等化型薄、化型轻、化型小 对域领等机算计、天航、空航在统系和机整子电于由 �装封� D2� 维二的现实内面平 yx 为均述所上以 。术技装组体立种一是这。的成构上板母的大更个一在 装插同共再卡插 或板插个各的装组级二由是�杂复大 庞加更术技装组�全更能功�高更度密装封级三 装封级三、四 。分部三术技 � ACD� 装安接直片芯和 � TMS� 术技装安面表 、 � THT� 术技装安孔通括包 。装封以 加独单再不般一级一这�外求要别特除。上板基他其或 BWP 到装安同一� BOC� 片芯 上板及件器元的型类种各、品产装封子电微种各级一上将是�装组是上际实装封级二 � BWP� 装封级二、三 。合组或件器元子电的能功用实有为成 之使�来起接连法方连互片芯种三述上用间脚引外的装封与区焊的片芯在�时同�来起装 封�合组的们他或料塑、瓷陶、属金� 料材的宜适用片芯 CI 个多或个一将是装封级一 � MCM、MCS� 装封级一、二 。连相然自属金线 布与区焊的片芯 CI 将�线布行 进一统再�后中层质介 IP 或板基到置埋片芯 CI 将先 �术技线布后� 术技连互片芯置埋� 4 。速迅展发�高都能性合综 BAT、BW 比。时省工省�成完次一均 �少多点凸论无 。小积面法方他其比积面装安的片芯 �短最线连互 以所 �度高的点凸是既度 长脚引的接焊连互为因 。术技 的连互接直区焊板基和区焊片芯将、下朝面片芯 术技 BCF� 3 。越优 BW 比能性合综 �种几带属金双和带层三、带层双、带层单有 BAT 。分部个几接焊线引外 的区焊板基与线引带载 的后最和接粘板基的后焊连互片芯-带载�接焊点凸片 芯与线引带 载�作制线引带载�成形点凸区焊片芯括包� ”梁桥“ 的区焊板基和区焊片芯接连是 BAT 术技 BAT� 2 。丝 lA�丝 uA -iS�丝 uA。要需接焊的巨艰和寸尺上以米微 07 足满 可高度强点焊 �便方活灵点特� � 焊球丝金� 焊声超 压热和焊声超、焊压热为分�术技连互的熟成最 术技 BW� 1 。 � 术技线布后� 术技连互片芯置埋及以� BCF� gnidnoB pihC pilF� 焊装倒和� BAT �gnidnoB detamotuA epaT � 焊动自带载、 � BW�gnidnoB eriW� 合键线引有要主 � 术技连互片芯、2 。务任项这成完的好很以可基脂树机有的力应低�可即固牢接粘板 基与片芯求要只 CI 寸尺大对�CI 寸尺小或管体晶于合适法方述前�法接粘脂树机有� 4 。便简作操�化固成完中箱烘的净干在可�化固行进间时 和度温的求要化固胶电导用采 �后接粘片芯�层化属金有具板基和面背片芯求要不
组装工艺流程

组装工艺流程组装工艺流程是指在产品制造过程中,将各个零部件按照一定的顺序和方法进行组装,最终形成成品的过程。
在制造行业中,组装工艺流程是非常重要的一环,它直接关系到产品的质量和生产效率。
下面我们将详细介绍一下组装工艺流程的具体步骤和注意事项。
首先,组装工艺流程的第一步是准备工作。
在进行组装之前,需要对所有的零部件进行清点和检查,确保所有零部件的数量和质量都是符合要求的。
同时,还需要准备好相应的工具和设备,以便于后续的组装作业顺利进行。
接下来是零部件的组装。
在进行组装时,需要根据产品的设计图纸和工艺要求,按照正确的顺序和方法进行组装。
在组装的过程中,要特别注意零部件之间的配合和连接,确保组装的准确性和稳固性。
另外,在组装的过程中还需要注意安全问题。
操作人员需要正确使用各种工具和设备,严格遵守操作规程,确保自身和他人的安全。
同时,还需要注意防止零部件的损坏或丢失,避免对整个组装工艺流程造成影响。
完成组装后,需要进行产品的检测和调试。
通过对组装好的产品进行各项性能和功能的检测,确保产品的质量和性能符合要求。
同时,还需要对产品进行调试,确保各项功能正常运行。
最后,是产品的包装和出厂。
在产品通过检测和调试后,需要进行包装作业,将产品包装好,以防止在运输和使用过程中受到损坏。
最终,产品将会出厂,交付给客户使用。
总的来说,组装工艺流程是一个非常重要的环节,它直接关系到产品的质量和生产效率。
只有严格按照工艺要求进行操作,确保每一个步骤都正确无误,才能最终保证产品的质量和性能。
希望以上内容对您有所帮助,谢谢阅读。
微组装技术简述及工艺流程及设备
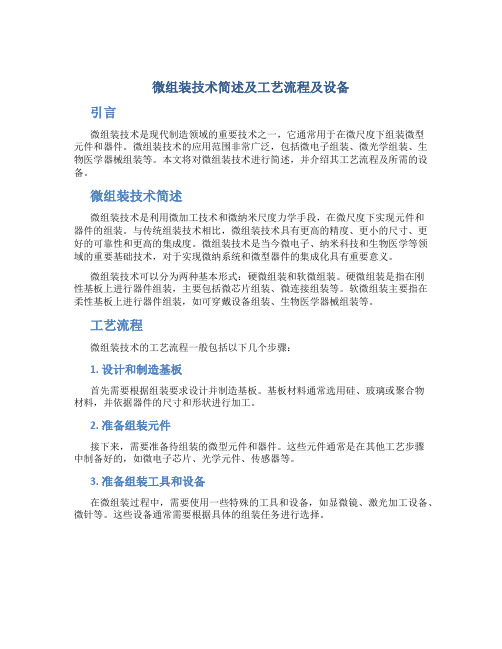
微组装技术简述及工艺流程及设备引言微组装技术是现代制造领域的重要技术之一,它通常用于在微尺度下组装微型元件和器件。
微组装技术的应用范围非常广泛,包括微电子组装、微光学组装、生物医学器械组装等。
本文将对微组装技术进行简述,并介绍其工艺流程及所需的设备。
微组装技术简述微组装技术是利用微加工技术和微纳米尺度力学手段,在微尺度下实现元件和器件的组装。
与传统组装技术相比,微组装技术具有更高的精度、更小的尺寸、更好的可靠性和更高的集成度。
微组装技术是当今微电子、纳米科技和生物医学等领域的重要基础技术,对于实现微纳系统和微型器件的集成化具有重要意义。
微组装技术可以分为两种基本形式:硬微组装和软微组装。
硬微组装是指在刚性基板上进行器件组装,主要包括微芯片组装、微连接组装等。
软微组装主要指在柔性基板上进行器件组装,如可穿戴设备组装、生物医学器械组装等。
工艺流程微组装技术的工艺流程一般包括以下几个步骤:1. 设计和制造基板首先需要根据组装要求设计并制造基板。
基板材料通常选用硅、玻璃或聚合物材料,并依据器件的尺寸和形状进行加工。
2. 准备组装元件接下来,需要准备待组装的微型元件和器件。
这些元件通常是在其他工艺步骤中制备好的,如微电子芯片、光学元件、传感器等。
3. 准备组装工具和设备在微组装过程中,需要使用一些特殊的工具和设备,如显微镜、激光加工设备、微针等。
这些设备通常需要根据具体的组装任务进行选择。
4. 进行组装操作组装操作是微组装技术的核心步骤。
根据组装要求,将待组装的元件定位到基板上,并使用适当的力或温度进行粘合或焊接。
组装过程需要在洁净的环境中进行,以避免灰尘或杂质对器件性能的影响。
5. 测试和质量控制完成组装后,需要对组装好的器件进行测试和质量控制。
这包括检查组装位置的准确性、元件之间的连接可靠性以及器件的功能性能等。
设备微组装技术需要使用一系列特殊的设备来完成组装任务。
下面列举一些常用的微组装设备:1.显微镜:用于精确定位待组装的微元件,可采用光学显微镜或电子显微镜等。
微组装技术简述及工艺流程及设备概述
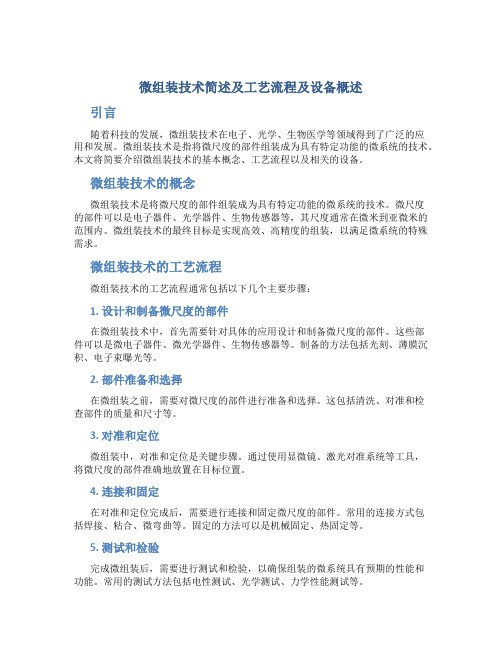
微组装技术简述及工艺流程及设备概述引言随着科技的发展,微组装技术在电子、光学、生物医学等领域得到了广泛的应用和发展。
微组装技术是指将微尺度的部件组装成为具有特定功能的微系统的技术。
本文将简要介绍微组装技术的基本概念、工艺流程以及相关的设备。
微组装技术的概念微组装技术是将微尺度的部件组装成为具有特定功能的微系统的技术。
微尺度的部件可以是电子器件、光学器件、生物传感器等,其尺度通常在微米到亚微米的范围内。
微组装技术的最终目标是实现高效、高精度的组装,以满足微系统的特殊需求。
微组装技术的工艺流程微组装技术的工艺流程通常包括以下几个主要步骤:1. 设计和制备微尺度的部件在微组装技术中,首先需要针对具体的应用设计和制备微尺度的部件。
这些部件可以是微电子器件、微光学器件、生物传感器等。
制备的方法包括光刻、薄膜沉积、电子束曝光等。
2. 部件准备和选择在微组装之前,需要对微尺度的部件进行准备和选择。
这包括清洗、对准和检查部件的质量和尺寸等。
3. 对准和定位微组装中,对准和定位是关键步骤。
通过使用显微镜、激光对准系统等工具,将微尺度的部件准确地放置在目标位置。
4. 连接和固定在对准和定位完成后,需要进行连接和固定微尺度的部件。
常用的连接方式包括焊接、粘合、微弯曲等。
固定的方法可以是机械固定、热固定等。
5. 测试和检验完成微组装后,需要进行测试和检验,以确保组装的微系统具有预期的性能和功能。
常用的测试方法包括电性测试、光学测试、力学性能测试等。
微组装技术的设备概述显微镜显微镜是微组装中常用的设备之一。
它能够提供高分辨率的图像,帮助操作人员对微尺度的部件进行准确定位和对准。
常见的显微镜类型包括光学显微镜、扫描电子显微镜等。
激光对准系统激光对准系统是一种用于微组装中的精准定位工具。
通过发射激光光束,检测和测量部件的位置和角度,从而实现高精度的对准。
焊接设备微组装中的焊接设备用于将微尺度的部件连接在一起。
常见的焊接方法包括激光焊接、红外焊接等。
微组装技术简述及工艺流程及设备概述.pptx

4) 易于实现多功能。MCM可将模拟电路、数 字电路、光电器件、微波器件、传感器以及 其片式元器件等多种功能的元器件组装在一 起,通过高密度互连构成具有多种功能微电 子部件、子系统或系统。Hughes Reserch laboratory 采用三维多芯片组件技术开发 的计算机系统就是MCM实现系统级组件的 典型实例。
3.类型和特点——
通常可按MCM所用高密度多层布线基板的结构 和工艺,将MCM分为以下几个类型。
1)叠层型MCM(MCM-L,其中L为“叠层”的 英文词“Laminate”的第一个字母)也称为L 型多芯片组件,系采用高密度多层印制电路板 构成的多芯片组件,其特点是生产成本低,制 造工艺较为成熟,但布线密度不够高,其组装 效率和性能较低,主要应用于30MHz和100个 焊点/英寸2以下的产品以及应用环境不太严酷 的消费类电子产品和个人计算机等民用领域。
3)淀积型MCM(MCM-D,其中D是“淀积”的英 文名Deposition 的第一个字母),系采用高密度 薄膜多层布线基板构成的多芯片组件。其主要特 点是布线密度和组装效率高,具有良好的传输特 性、频率特性和稳定性.
微组装技术简述
张经国 1404
Байду номын сангаас
一.微组装技术内涵及其与电子组装技术的关系 1.内涵——微组装技术(micropackging technology) 是微电子组装技术(microelectronic packging technology)的简称,是新一代高级的电子组装技 术。它是通过微焊互连和微封装工艺技术,将高 集成度的IC器件及其他元器件组装在高密度多层 基板上,构成高密度、高可靠、高性能、多功能 的立体结构微电子产品的综合性高技术,是一种 高级的混合微电子技术。
微组装工艺流程

微组装工艺流程基板的准备分为电路软基板(RT/DUroid5880)的准备和陶瓷基板(AL2O3)的准备。
电路软基板要求操作者戴指套,将电路软基板放在干净的中性滤纸上,按图纸用手术刀切割电路板边框线和去除工艺线。
要求电路软基板的图形符合图纸要求,表面平整,没有翘曲,外形尺寸比图纸小 0。
1 ㎜~0.2 ㎜,切面平整。
工艺线的去除切地,切口断面与代线平面垂直,手指不允许不戴指套接触镀金层,以免造成氧化.陶瓷基板的准备,要求用细金刚砂纸打磨陶瓷基板,使边缘整齐,无毛刺、无短路,然后用纯净水洗净。
基板清洗基板的清洗,通过超声清洗进行。
超声清洗是利用超声波在清洗液中的辐射,使液体震动产生数万计的微小气泡,这些气泡在超声波的纵向传播形成的负压区产生、生长,而在正压区闭合,在这种空化效应的过程中,微小气泡闭合时可以产生超过 1000 个大气压的瞬间高压,连续不断的瞬间高压冲击物体表面,使物体表面和微小缝隙中的污垢迅速剥落。
因此,超声波清洗对物体表面具有一定损伤性,经过多次实验(此实验未记录实验数据),确定合理的超声功率、去离子水用量以及清洗液的高度和清洗时间.具体清洗流程及参数设置如下:打开超声清洗机,功率调至100 瓦,加入去离子水,液面高度为 60 ㎜~80 ㎜之间。
将电路软基板或陶瓷基板放入瓷盒中,倒入 HT1 清洗液,液面略高基板上表面 3 ㎜~5 ㎜,然后将整个瓷盒放入超声清洗机的支架上(水面低于清洗液 2 ㎜~3 ㎜),清洗时间为Xmin~Xmin。
将95%乙醇倒入瓷盒,液面略高于基板上表面 3 ㎜~5 ㎜,然后将整个瓷盒放入超声清洗机的支架上(水面低于清洗液 2 ㎜~3 ㎜),清洗时间为Xmin~Xmin。
将清洗完毕的基板放入 X℃±3℃的烘箱中烘 0.5h 后,放入氮气保护柜。
通过上述多次实验后确定的清洗工序,清洗完成后的基板表面无油污、杂质等残留物.腔体的准备和清洗腔体的准备主要是用手术刀打净毛刺,再用洗耳球打磨毛刺形成的杂质。
微组装技术简述及工艺流程及设备课件
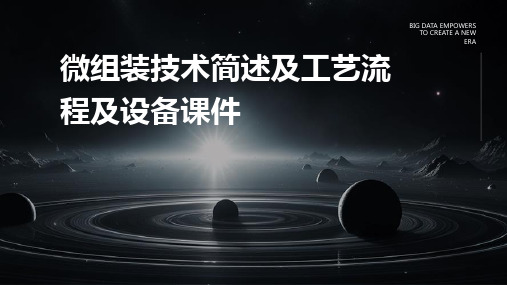
精度控制问题
精度控制问题
微组装技术要求零件的精度非常高,如何确保每个组件的精确位置和尺寸是微组装过程中的一大挑战 。
解决方案
采用高精度的设备和工艺,如激光加工、纳米压印等,同时加强质量检测,对不合格的零件进行修复 或替换。
生产效率问题
生产效率问题
微组装技术的复杂性和高精度要求使 得生产效率相对较低。
ERA
定义及特点
微组装技术定义 高密度组装 高可靠性 高灵活性
微组装技术是一种将微电子器件(如芯片、MEMS等)通过物 理、化学或电学方法组装到基板上,形成复杂电路和系统的技
术。
微组装技术可以实现高密度组装,将多个微电子器件组装到有 限的基板面积内,提高了电路和系统的集成度。
由于微组装技术采用可靠的物理、化学或电学方法进行连接和 固定,因此可以保证组装后的电路和系统具有高可靠性。
05
案例分析
BIG DATA EMPOWERS TO CREATE A NEW
ERA
案例一:某公司微组装生产线
总结词
高效、自动化、定制化
主要设备
自动拾取机、微型焊接机、芯片贴装机、烘箱、 显微镜等。
详细描述
该公司的微组装生产线采用了先进的自动化设备 和精细的工艺流程,实现了高效的生产。同时, 公司根据客户需求进行定制化生产,满足客户多 样化的需求。
技术参数
引线键合机的主要技术参数包括 金属线的直径、键合压力、加热 温度和键合速度等,这些参数需 要根据不同的芯片和基板材料进 行调整。
芯片封接机
设备功能
芯片封接机主要用于将芯片、引线和基板等部件密封在一起,以保 护电气连接不受环境影响。
工作原理
芯片封接机采用热压、超声波焊接或环氧树脂密封等技术,将芯片 、引线和基板等部件密封在环氧树脂或其他密封材料中。
微组装工艺设计流程

微组装工艺流程基板的准备分为电路软基板(RT/DUroid5880)的准备和陶瓷基板(AL2O3)的准备。
电路软基板要求操作者戴指套,将电路软基板放在干净的中性滤纸上,按图纸用手术刀切割电路板边框线和去除工艺线。
要求电路软基板的图形符合图纸要求,表面平整,没有翘曲,外形尺寸比图纸小 0.1 ㎜~0.2 ㎜,切面平整。
工艺线的去除切地,切口断面与代线平面垂直,手指不允许不戴指套接触镀金层,以免造成氧化。
陶瓷基板的准备,要求用细金刚砂纸打磨陶瓷基板,使边缘整齐,无毛刺、无短路,然后用纯净水洗净。
基板清洗基板的清洗,通过超声清洗进行。
超声清洗是利用超声波在清洗液中的辐射,使液体震动产生数万计的微小气泡,这些气泡在超声波的纵向传播形成的负压区产生、生长,而在正压区闭合,在这种空化效应的过程中,微小气泡闭合时可以产生超过 1000 个大气压的瞬间高压,连续不断的瞬间高压冲击物体表面,使物体表面和微小缝隙中的污垢迅速剥落。
因此,超声波清洗对物体表面具有一定损伤性,经过多次实验(此实验未记录实验数据),确定合理的超声功率、去离子水用量以及清洗液的高度和清洗时间。
具体清洗流程及参数设置如下:打开超声清洗机,功率调至 100 瓦,加入去离子水,液面高度为 60 ㎜~80 ㎜之间。
将电路软基板或陶瓷基板放入瓷盒中,倒入 HT1 清洗液,液面略高基板上表面 3 ㎜~5 ㎜,然后将整个瓷盒放入超声清洗机的支架上(水面低于清洗液 2 ㎜~3 ㎜),清洗时间为 Xmin~Xmin。
将 95%乙醇倒入瓷盒,液面略高于基板上表面 3 ㎜~5 ㎜,然后将整个瓷盒放入超声清洗机的支架上(水面低于清洗液 2 ㎜~3 ㎜),清洗时间为 Xmin~Xmin。
将清洗完毕的基板放入 X℃±3℃的烘箱中烘 0.5h 后,放入氮气保护柜。
通过上述多次实验后确定的清洗工序,清洗完成后的基板表面无油污、杂质等残留物。
腔体的准备和清洗腔体的准备主要是用手术刀打净毛刺,再用洗耳球打磨毛刺形成的杂质。
微组装技术简述及工艺流程及设备
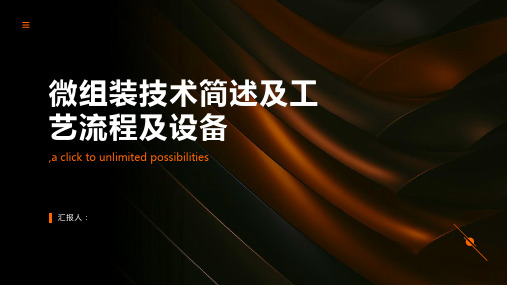
感谢您的观看
汇报人:
添加标题
添加标题
添加标题
自动化程度高:微组装技术采用自 动化设备,提高生产效率和质量稳 定性
环保性:微组装技术采用环保材料 和工艺,减少对环境的影响
微组装技术的应用领域
生物医学领域:如生物芯片、 微流体、微针等
光学领域:如微光学器件、 微光学系统等
航空航天领域:如微型卫星、 微型飞行器等
电子行业:如集成电路、传 感器、微机电系统等
微组装技术是一种将微小部 件组装成复杂结构的技术
微组装技术广泛应用于电子、 通信、医疗等领域
微组装技术可以提高产品的 性能和可靠性,降低成本和
能耗
微组装技术的特点
精度高:微组装技术可以实现纳米 级别的精度,满足高精度要求
灵活性强:微组装技术可以适应多 种材料和工艺要求,满足不同产品 的需求
添加标题
微组装技术简述及工 艺流程及设备
,a click to unlimited possibilities
汇报人:
目录 /目录
01
点击此处添加 目录标题
02
微组装技术简 述
03
微组装工艺流 程
04
微组装设备
05
微组装技术发 展趋势
01 添加章节标题
02 微组装技术简述
微组装技术的定义
微组装技术包电路板封装 在一起,保护芯片和电路板
免受外界环境的影响
测试:对封装好的芯片进行 电气性能测试,确保其性能
符合要求
微组装工艺流程需要精确控 制,以保证产品的质量和可
靠性。
检测与调试
检测方法:光学显微镜、电子显微镜、X射线衍射等 调试步骤:调整参数、优化工艺、验证结果等 调试工具:自动化测试设备、软件工具等 调试目标:提高产品质量、降低生产成本、提高生产效率等
微组装技术简述及工艺流程及设备
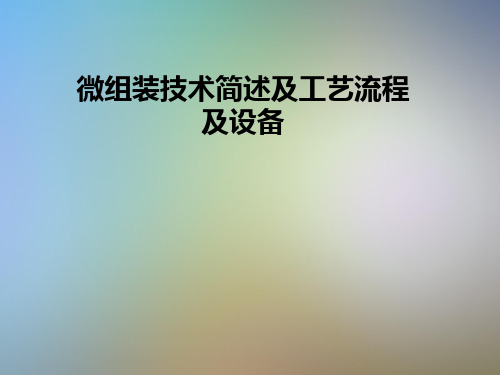
2.优点——MCM技术有以下主要优点。
1)使电路组装更加高密度化,进一步实现整机 的小型化和轻量化。与同样功能的SMT组装 电路相比,通常MCM的重量可减轻 80%~90%,其尺寸减小70~80%。在军事应 用领域,MCM的小型化和轻量化效果更为明 显,采用MCM技术可使导弹体积缩小90%以 上,重量可减轻80%以上。卫星微波通信系 统中采用MCM技术制作的T/R组件,其体积 仅为原来的1/10~1/20。
3)淀积型MCM(MCM-D,其中D是“淀积”的英 文名Deposition 的第一个字母),系采用高密度 薄膜多层布线基板构成的多芯片组件。其主要特 点是布线密度和组装效率高,具有良好的传输特 性、频率特性和稳定性.
4)混合型MCM-H(MCM-C/D和MCM-L/D,其中 英文字母C、D、L的含义与上述相同),系采用 高密度混合型多层基板构成的多芯片组件。这是 一种高级类型的多芯片组件,具有最佳的性能/价 格比、组装密度高、噪声和布线延迟均比其它类 型MCM小等特点。这是由于混合多层基板结合了 不同的多层基板工艺技术,发挥了各自长处的缘 故。特别适用于巨型、高速计算机系统、高速数 字通信系统、高速信号处理系统以及笔记本型计 算机子系统。
2)厚膜陶瓷型MCM(MCM-C,其中C是“陶瓷 ”的英文名Ceramic的第一个字母),系采用 高密度厚膜多层布线基板或高密度共烧陶瓷 多层基板构成的多芯片组件。其主要特点是 布线密度较高,制造成本适中,能耐受较恶 劣的使用环境,其可靠性较高,特别是采用 低温共烧陶瓷多层基板构成的MCM-C,还 易于在多层基板中埋置元器件,进一步缩小 体积,构成多功能微电子组件。MCM-C主 要应用于30~50MHz的高可靠中高档产品。 包括汽车电子及中高档计算机和数字通信领 域。
微组装基本工艺流程
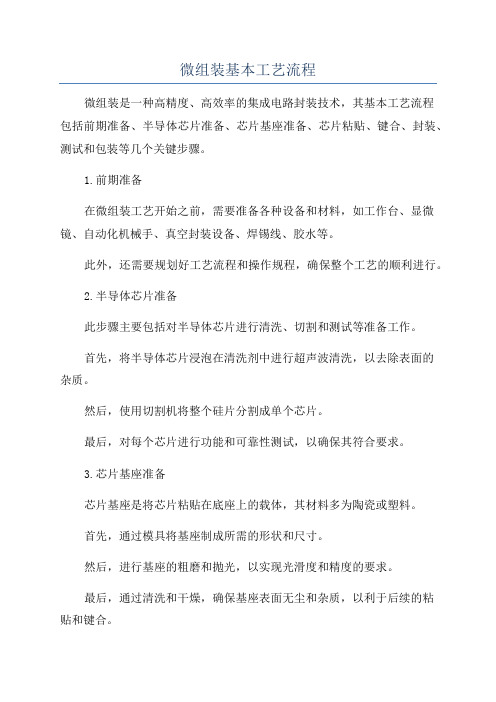
微组装基本工艺流程微组装是一种高精度、高效率的集成电路封装技术,其基本工艺流程包括前期准备、半导体芯片准备、芯片基座准备、芯片粘贴、键合、封装、测试和包装等几个关键步骤。
1.前期准备在微组装工艺开始之前,需要准备各种设备和材料,如工作台、显微镜、自动化机械手、真空封装设备、焊锡线、胶水等。
此外,还需要规划好工艺流程和操作规程,确保整个工艺的顺利进行。
2.半导体芯片准备此步骤主要包括对半导体芯片进行清洗、切割和测试等准备工作。
首先,将半导体芯片浸泡在清洗剂中进行超声波清洗,以去除表面的杂质。
然后,使用切割机将整个硅片分割成单个芯片。
最后,对每个芯片进行功能和可靠性测试,以确保其符合要求。
3.芯片基座准备芯片基座是将芯片粘贴在底座上的载体,其材料多为陶瓷或塑料。
首先,通过模具将基座制成所需的形状和尺寸。
然后,进行基座的粗磨和抛光,以实现光滑度和精度的要求。
最后,通过清洗和干燥,确保基座表面无尘和杂质,以利于后续的粘贴和键合。
4.芯片粘贴在芯片基座的定位平台上,使用显微镜和自动化机械手将芯片粘贴在基座上。
首先,将一定量的导热胶敷在基座上。
然后,使用自动化机械手将芯片从芯片库位中取出并粘贴在基座上。
最后,通过压力和温度控制,确保芯片与基座粘结牢固。
5.键合键合是将芯片上的金线连接到基座上的引脚。
首先,通过焊锡线将引脚与基座连接起来,形成临时的电气连接。
然后,使用焊线绑扎机或激光焊接机器进行金线的键合。
最后,用显微镜检验键合点的质量,确保键合的牢固度和电气连接的可靠性。
6.封装封装是将粘贴在基座上的芯片封装在外壳中,以保护芯片并提供所需的引脚。
首先,通过接触式或非接触式方法将封装材料涂布在基座上。
然后,在暴露的引脚上焊接封装材料,形成引脚的支撑和保护。
最后,通过温度和压力控制,将封装材料固化,并保证封装的完整性和可靠性。
7.测试封装完成后,在专用的测试设备中对封装的芯片进行成品测试。
测试项目包括芯片的性能、功耗、温度等。
微组装技术简述及工艺流程及设备ppt

微组装技术在未来面临的挑战和机遇
微组装技术的经济效益和社会效益
THANKS
感谢观看
将显卡插入主板上的PCI-E插槽中,确保插槽与显卡的金手指对应。
安装显卡
工业控制系统中的微组装工艺流程
总结与展望
05
微组装技术的成果与经验总结
微组装技术发展的历史和现状
微组装技术的工艺流程和设备
微组装技术在各个领域的应用成果
微组装技术的设计原则和方法
微组装技术的应用前景与展望
微组装技术在未来的应用前景
贴装后需要进行焊接和检测,以确保芯片与电路基板之间的可靠连接。
Байду номын сангаас
03
焊接完成后需要进行检测,以发现是否存在虚焊、漏焊等缺陷。
引脚焊接工艺
01
引脚焊接是将芯片引脚与电路基板上的导线焊接在一起的过程,常用的焊接方法有热压焊、超声波焊、激光焊等。
02
焊接过程中需要控制温度、时间和压力等参数,以确保焊接质量和可靠性。
贴片机
包括自动焊接机和热压焊接机等,用于将芯片引脚与基板引脚焊接牢固;
引脚焊接设备
包括视觉检测设备和电检测设备等,用于检测芯片和元器的位置、贴装质量等。
检测设备
芯片贴装设备的种类与原理
芯片贴装设备的技术参数
芯片贴装设备的选用
芯片贴装设备
引脚焊接设备
引脚焊接设备的种类与原理
根据焊接原理的不同,引脚焊接设备可分为热压焊接机、超声波焊接机、激光焊接机等几种类型;
xx年xx月xx日
微组装技术简述及工艺流程及设备ppt
CATALOGUE
目录
微组装技术简介微组装工艺流程微组装设备及选用微组装技术的应用案例总结与展望
微组装技术简述及工艺流程及设备教材

NASA采用厚膜混合集成技术研制了导弹制导计算机 的运算组件。其中采用了2.88in见方的厚膜多层布线基板, 组装了5个大规模半导体集成电路芯片,12个中规模半导 体集成电路芯片(TTL),6个片式电容和6个片式电阻, 629根键合互连丝。 采用厚膜集成技术制作厚膜混合集成DC∕DC变换器是 厚膜混合电路的一大类产品。其产品功率范围达1W~120 W,电流最大20A ,输出路数从单路到三路,开关频率 300kHz~550kHz,国内120W DC∕DC变换器产品的功率密 度达78W∕in3,输出电压15V ,输出电流8A,效率85 % , 纹波<100 mV 。电性能与INTERPOINT同类产品相同, 功率密度高于INTERPOINT同类产品(后者为66.3 W∕in3)。 还可制作高压输出(160V~900V)的厚膜混合集成 DC∕DC变换器.
3.类型和特点——
通常可按 MCM 所用高密度多层布线基板的结构 和工艺,将MCM分为以下几个类型。 1)叠层型MCM(MCM-L,其中L为“叠层”的 英文词“Laminate”的第一个字母)也称为L 型多芯片组件,系采用高密度多层印制电路板 构成的多芯片组件,其特点是生产成本低,制 造工艺较为成熟,但布线密度不够高,其组装 效率和性能较低,主要应用于30MHz和100个 焊点/英寸2以下的产品以及应用环境不太严酷 的消费类电子产品和个人计算机等民用领域。
八。薄膜混合电路定义及其应用特点
1.定义——采用物理汽相淀积(PVD,蒸发、溅射
和离子镀等)或化学汽相淀积(CVD)工艺 以及湿刻(光刻)或干刻(等离子刻蚀等)
图形形成技术,在基板上形成薄膜元件和布
线,然后组装微型元器件(多为芯片和片式 元器件)构成具有一定功能的微电路。 区分是“薄膜”还是“厚膜”,主要按工艺技术分,而 非主要按其膜厚度(虽然厚度有区别,GJB548中提到, 薄膜厚度通常小于5微米)
微组装工艺流程培训
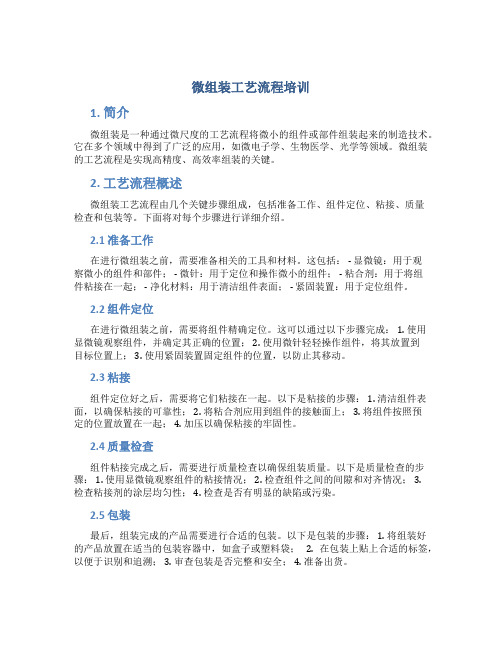
微组装工艺流程培训1. 简介微组装是一种通过微尺度的工艺流程将微小的组件或部件组装起来的制造技术。
它在多个领域中得到了广泛的应用,如微电子学、生物医学、光学等领域。
微组装的工艺流程是实现高精度、高效率组装的关键。
2. 工艺流程概述微组装工艺流程由几个关键步骤组成,包括准备工作、组件定位、粘接、质量检查和包装等。
下面将对每个步骤进行详细介绍。
2.1 准备工作在进行微组装之前,需要准备相关的工具和材料。
这包括: - 显微镜:用于观察微小的组件和部件; - 微针:用于定位和操作微小的组件; - 粘合剂:用于将组件粘接在一起; - 净化材料:用于清洁组件表面; - 紧固装置:用于定位组件。
2.2 组件定位在进行微组装之前,需要将组件精确定位。
这可以通过以下步骤完成: 1. 使用显微镜观察组件,并确定其正确的位置; 2. 使用微针轻轻操作组件,将其放置到目标位置上; 3. 使用紧固装置固定组件的位置,以防止其移动。
2.3 粘接组件定位好之后,需要将它们粘接在一起。
以下是粘接的步骤: 1. 清洁组件表面,以确保粘接的可靠性; 2. 将粘合剂应用到组件的接触面上; 3. 将组件按照预定的位置放置在一起; 4. 加压以确保粘接的牢固性。
2.4 质量检查组件粘接完成之后,需要进行质量检查以确保组装质量。
以下是质量检查的步骤: 1. 使用显微镜观察组件的粘接情况; 2. 检查组件之间的间隙和对齐情况; 3.检查粘接剂的涂层均匀性; 4. 检查是否有明显的缺陷或污染。
2.5 包装最后,组装完成的产品需要进行合适的包装。
以下是包装的步骤: 1. 将组装好的产品放置在适当的包装容器中,如盒子或塑料袋; 2. 在包装上贴上合适的标签,以便于识别和追溯; 3. 审查包装是否完整和安全; 4. 准备出货。
3. 注意事项在进行微组装工艺流程培训时,需要注意以下事项: - 操作时需要戴手套和眼镜,以保护自己的安全; - 需要保持工作环境整洁和干净,以确保组件的质量; - 注意组件的存储和运输,避免损坏和污染。
微组装工艺流程

微组装工艺流程基板的准备分为电路软基板(RT/DUroid5880 )的准备和陶瓷基板(AL2O3)的准备。
电路软基板要求操作者戴指套,将电路软基板放在干净的中性滤纸上,按图纸用手术刀切割电路板边框线和去除工艺线。
要求电路软基板的图形符合图纸要求,表面平整,没有翘曲,外形尺寸比图纸小0.1 ㎜~ 0.2 ㎜,切面平整。
工艺线的去除切地,切口断面与代线平面垂直,手指不允许不戴指套接触镀金层,以免造成氧化。
陶瓷基板的准备,要求用细金刚砂纸打磨陶瓷基板,使边缘整齐,无毛刺、无短路,然后用纯净水洗净。
基板清洗基板的清洗,通过超声清洗进行。
超声清洗是利用超声波在清洗液中的辐射,使液体震动产生数万计的微小气泡,这些气泡在超声波的纵向传播形成的负压区产生、生长,而在正压区闭合,在这种空化效应的过程中,微小气泡闭合时可以产生超过 1000 个大气压的瞬间高压,连续不断的瞬间高压冲击物体表面,使物体表面和微小缝隙中的污垢迅速剥落。
因此,超声波清洗对物体表面具有一定损伤性,经过多次实验(此实验未记录实验数据),确定合理的超声功率、去离子水用量以及清洗液的高度和清洗时间。
具体清洗流程及参数设置如下:打开超声清洗机,功率调至 100 瓦,加入去离子水,液面高度为60㎜~ 80 ㎜之间。
将电路软基板或陶瓷基板放入瓷盒中,倒入 HT1 清洗液,液面略高基板上表面 3 ㎜~ 5 ㎜,然后将整个瓷盒放入超声清洗机的支架上(水面低于清洗液 2 ㎜~ 3 ㎜),清洗时间为 Xmin ~ Xmin 。
将 95% 乙醇倒入瓷盒,液面略高于基板上表面 3 ㎜~ 5 ㎜,然后将整个瓷盒放入超声清洗机的支架上(水面低于清洗液 2 ㎜~3㎜),清洗时间为 Xmin ~ Xmin 。
将清洗完毕的基板放入 X℃±3℃的烘箱中烘 0.5h后,放入氮气保护柜。
通过上述多次实验后确定的清洗工序,清洗完成后的基板表面无油污、杂质等残留物。
腔体的准备和清洗腔体的准备主要是用手术刀打净毛刺,再用洗耳球打磨毛刺形成的杂质。
组装工艺流程
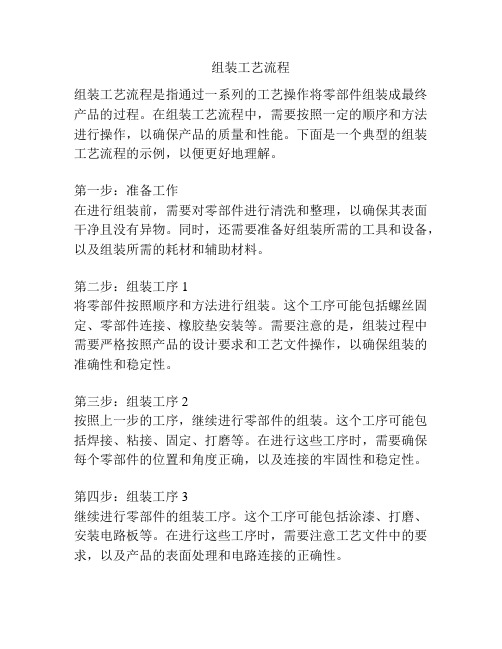
组装工艺流程组装工艺流程是指通过一系列的工艺操作将零部件组装成最终产品的过程。
在组装工艺流程中,需要按照一定的顺序和方法进行操作,以确保产品的质量和性能。
下面是一个典型的组装工艺流程的示例,以便更好地理解。
第一步:准备工作在进行组装前,需要对零部件进行清洗和整理,以确保其表面干净且没有异物。
同时,还需要准备好组装所需的工具和设备,以及组装所需的耗材和辅助材料。
第二步:组装工序1将零部件按照顺序和方法进行组装。
这个工序可能包括螺丝固定、零部件连接、橡胶垫安装等。
需要注意的是,组装过程中需要严格按照产品的设计要求和工艺文件操作,以确保组装的准确性和稳定性。
第三步:组装工序2按照上一步的工序,继续进行零部件的组装。
这个工序可能包括焊接、粘接、固定、打磨等。
在进行这些工序时,需要确保每个零部件的位置和角度正确,以及连接的牢固性和稳定性。
第四步:组装工序3继续进行零部件的组装工序。
这个工序可能包括涂漆、打磨、安装电路板等。
在进行这些工序时,需要注意工艺文件中的要求,以及产品的表面处理和电路连接的正确性。
第五步:组装工序4继续进行零部件的组装工序。
这个工序可能包括调试、检测、包装等。
在进行这些工序时,需要进行各项功能和性能的测试,以确保产品的正常运行和外观的完好。
第六步:完成工作当产品组装完成后,需要进行最后一次的检验和检测。
确保产品符合质量标准和设计要求。
同时,还需要对产品进行包装和标识,以便后续的运输和销售。
上述的组装工艺流程只是一个示例,不同的产品可能具有不同的组装工艺流程。
在实际的生产中,还需要考虑到产品的特点、工艺装备、生产线布局等因素,来确定最佳的组装工艺流程。
同时,还需要根据实际情况进行不断的改进和优化,以提高产品质量和生产效率。
微组装工艺流程

微组装工艺流程
《微组装工艺流程》
微组装是一种先进的制造技术,它能够将微小尺寸的部件组装成整体产品。
微组装工艺流程是实现微组装的关键,它涉及到材料选择、加工工艺、装配流程等多个方面。
首先,微组装工艺流程的第一步是材料选择。
由于微组装部件通常非常小且精密,因此材料的选择非常重要。
要选择能够满足微组装要求的材料,例如具有良好的机械性能和化学稳定性的材料。
其次,加工工艺是微组装的关键环节之一。
微组装部件通常需要进行微细加工,因此需要采用高精度的加工设备和工艺。
例如,激光加工、电子束加工等技术可以用于微组装部件的加工。
接下来,装配流程是微组装工艺流程中不可或缺的一环。
微组装部件通常需要进行精密的装配,包括对部件的定位、对接和固定。
因此,需要采用高精度的装配设备和技术,确保微组装部件的装配质量和稳定性。
此外,质量控制也是微组装工艺流程中非常重要的一环。
由于微组装部件通常非常小且精密,因此对质量的要求也非常高。
需要采用严格的质量控制手段,确保微组装产品的质量和稳定性。
总的来说,微组装工艺流程是一个复杂而严谨的过程,涉及到
材料选择、加工工艺、装配流程和质量控制等多个方面。
只有严格按照工艺流程进行操作,才能够确保微组装产品的质量和稳定性。
组装工艺流程

组装工艺流程1. 零件准备:首先需要准备好所有需要组装的零件、部件或原材料,确保其质量完好,数量齐全。
2. 清洁处理:对于需要进行组装的表面,要进行清洁处理,以确保组装过程中不会受到污染或影响质量。
3. 组装定位:根据设计图纸或工艺要求,将各个零件、部件或原材料进行定位,确保其位置和方向正确。
4. 固定连接:采用焊接、螺栓连接、胶粘、焊接等方法,将各个部件进行固定连接,确保整体结构牢固。
5. 调试检测:完成组装后,进行整体的调试和检测,确保各个部件的功能正常,没有质量问题。
6. 补充配套:根据需要,对组装好的产品进行配套,如加装外壳、镀层等。
7. 包装出厂:最后对成品进行包装,做好防潮、防损等措施,以确保产品在运输和储存过程中不受损坏。
以上是一般性的组装工艺流程,具体的流程和步骤还需要根据实际产品的特点和要求进行调整和完善。
组装工艺流程是制造行业中非常重要的一部分,它直接影响着产品的质量、成本和生产效率。
随着技术的不断进步和工艺的改进,组装工艺流程也在不断地完善和优化,以适应市场的需求和产品的创新。
在实际的生产中,组装工艺流程通常会根据产品的特点和生产规模而进行调整。
比如在汽车制造过程中,组装工艺流程就需要考虑到车身结构、车内配置、电子系统等诸多方面的因素,因此其工艺流程相对复杂。
而一些简单的家居产品组装,则可能更加注重流程的简化和效率的提高。
除了根据产品特点进行定制化的工艺流程外,制定良好的标准化流程也是非常重要的。
标准化的组装工艺流程可以提高生产效率,降低成本,确保产品质量,并且有利于员工的操作培训和技能培养。
对于大规模生产的产品而言,标准化流程更是必不可少的管理手段。
在组装工艺流程中,对原材料和零部件的采购也至关重要。
只有在质量合格、规格齐全的基础上,才能确保组装过程的顺利进行。
因此,良好的供应链管理对于组装工艺流程的顺利进行具有重要的意义。
实现供应链和生产流程的有效衔接,有助于减少库存压力、提高生产效率和增加整个价值链的竞争力。
- 1、下载文档前请自行甄别文档内容的完整性,平台不提供额外的编辑、内容补充、找答案等附加服务。
- 2、"仅部分预览"的文档,不可在线预览部分如存在完整性等问题,可反馈申请退款(可完整预览的文档不适用该条件!)。
- 3、如文档侵犯您的权益,请联系客服反馈,我们会尽快为您处理(人工客服工作时间:9:00-18:30)。
微组装工艺流程基板的准备分为电路软基板(RT/DUroid5880 )的准备和陶瓷基板(AL2O3)的准备。
电路软基板要求操作者戴指套,将电路软基板放在干净的中性滤纸上,按图纸用手术刀切割电路板边框线和去除工艺线。
要求电路软基板的图形符合图纸要求,表面平整,没有翘曲,外形尺寸比图纸小伽〜mm,切面平整。
工艺线的去除切地,切口断面与代线平面垂直,手指不允许不戴指套接触镀金层,以免造成氧化。
陶瓷基板的准备,要求用细金刚砂纸打磨陶瓷基板,使边缘整齐, 无毛刺、无短路,然后用纯净水洗净。
基板清洗基板的清洗,通过超声清洗进行。
超声清洗是利用超声波在清洗液中的辐射, 使液体震动产生数万计的微小气泡,这些气泡在超声波的纵向传播形成的负压区产生、生长,而在正压区闭合,在这种空化效应的过程中,微小气泡闭合时可以产生超过1000 个大气压的瞬间高压,连续不断的瞬间高压冲击物体表面,使物体表面和微小缝隙中的污垢迅速剥落。
因此,超声波清洗对物体表面具有一定损伤性, 经过多次实验(此实验未记录实验数据),确定合理的超声功率、去离子水用量以及清洗液的高度和清洗时间。
具体清洗流程及参数设置如下:打开超声清洗机,功率调至100瓦,加入去离子水,液面高度为60 mm〜80 mm之间。
将电路软基板或陶瓷基板放入瓷盒中,倒入HT1清洗液,液面略高基板上表面 3 mm〜5 mm,然后将整个瓷盒放入超声清洗机的支架上(水面低于清洗液 2 mm〜3 mm),清洗时间为Xmin〜Xmin。
将95%乙醇倒入瓷盒,液面略高于基板上表面 3 mm〜5 mm,然后将整个瓷盒放入超声清洗机的支架上(水面低于清洗液 2 mm〜3 mm),清洗时间为Xmin〜Xmin。
将清洗完毕的基板放入X C±3C的烘箱中烘后,放入氮气保护柜。
通过上述多次实验后确定的清洗工序,清洗完成后的基板表面无油污、杂质等残留物。
腔体的准备和清洗腔体的准备主要是用手术刀打净毛刺,再用洗耳球打磨毛刺形成的杂质。
腔体的清洗使用超声波清洗机,具体清洗流程及参数设置如下:打开超声清洗机,功率调至100瓦,倒入HT1清洗液,液面高度为60 mm〜80 mm之间,将腔体放入超声清洗机清洗液中,液面略高腔体上表面 3 mm〜5 m,且液面高度不得超过80 m,清洗时间为Xmin〜Xmin。
将95%乙醇倒入超声波清洗机中,液面高度为60 mm〜80 mm之间,将腔体放入超声清洗机清洗液中,液面略高腔体上表面 3 m〜5 m,且液面高度不得超过80 mm,清洗时间为Xmin〜Xmin。
将清洗完毕的基板放入X C±3C的烘箱中烘后,放入氮气保护柜。
通过上述多次实验后确定的清洗工序,清洗完成后的腔体表面无油污、杂质等残留物。
焊料/ 导电胶的准备焊料,主要使用锡铅合金锡箔焊料(Pb37Sn63),用镊子将焊料展平,接着用铅笔将压块形状画上,然后用剪刀沿画痕剪成压块形状。
要求锡铅合金锡箔焊料必须平展,不能有褶皱,压块大小和焊料一致,不允许未戴指套直接触摸焊料。
焊料的清洗使用超声波清洗机,具体清洗流程及参数设置如下:打开超声清洗机,功率调至100 瓦,加入去离子水,液面高度为60 mm〜80 mm之间。
将锡铅合金锡箔焊料放入瓷盒中,将95%乙醇清洗液放入瓷盒,液面略高焊料上表面 3 mm〜5 mm,然后将整个瓷盒放入超声清洗机的支架上(水面低于清洗液 2 mm〜3 mm),清洗时间为Xmi n〜Xmin。
将清洗完毕的焊料放入X ± 3C的烘箱中烘4min〜10min后,放入氮气保护柜。
导电胶,主要使用H20E导电银胶,导电胶不用时应放入0 C〜5C的冰箱内保存。
使用时从冰箱取出后,在室温下放置15min ,恢复至室温后,用钨针拌15min 使各成份混合均匀,挑出少许搅拌好的导电胶放入小坩埚中,再搅拌15〜20min以去气(若没有适当去气,空气会陷入固化的粘接剂中,在粘接层中产生空洞,这些空洞会降低电导率和热导率甚至降低粘接强度)。
装夹的过程是将焊料/ 导电胶放入腔体内,并装好基片,用专用夹具固定。
此步工序主要需要注意焊料/ 导电胶必须涂覆均匀、平整、不能有折叠角或褶皱。
另外导电胶在涂覆时,厚度不能超过m。
焊料烧结/ 导电胶固化用锡铅合金锡箔焊料装夹好的产品放入已达到设定温度的烧结炉上进行烘烤,温度根据焊料的融化温度设定,时间以温度降低又重新升至设定温度保持1min〜5min 后结束。
锡铅合金锡箔焊料温度为183 C,烘烤温度约200 C〜220Co用导电胶装夹好的产品放入已达到设定温度的烧结炉上进行烘烤,固化时间和温度以导电胶厂家提供数据为依据,H20E 导电胶温度为120 C,时间X小时。
清理、检验在显微镜下用手术到清理多余的焊料/导电胶。
如焊料/导电胶有多余溢出造成短路而又无法清理时,需报废。
清理完毕的产品按腔体的清洗工艺进行清洗并烘干。
检验的标准按照工艺要求进行,不合格的报废。
芯片粘接工艺芯片的焊接是指半导体芯片与载体(封装壳体或基片)形成牢固的、传导性或绝缘性连接的方法。
焊接层除了为器件提供机械连接和电连接外,还须为器件提供良好的散热通道。
芯片粘接工艺是通过环氧树脂导电胶粘接来形成焊接层。
芯片粘接工艺是采用环氧树脂导电胶(掺杂金或银的环氧树脂)在芯片和载体之间形成互连和形成电和热的良导体。
环氧树脂是稳定的线性聚合物,在加入固化剂后,环氧基打开形成羟基并交链,从而由线性聚合物交链成网状结构而固化成热固性塑料。
其过程由液体或粘稠液-凝胶化 -固体。
固化的条件主要由固化剂种类的选择来决定。
而其中掺杂的金属含量决定了其导电、导热性能的好坏。
芯片共晶工艺芯片的焊接是指半导体芯片与载体(封装壳体或基片)形成牢固的、传导性或绝缘性连接的方法。
焊接层除了为器件提供机械连接和电连接外,还需为器件提供良好的散热通道。
芯工共晶工艺是通过金属合金焊料来形成焊接层。
共晶是指在相对较低的温度下共晶焊料发生共晶物熔合的现象,共晶合金直接从固态变到液态,而不经过塑性阶段。
其熔化温度称共晶温度。
芯片共晶主要指金硅、金锗、金锡等共晶焊接。
金的熔点为1063 C,硅的熔点为1414 C,但金硅合金的熔点远低于单质的金和硅。
从二元系相图中可以看到,含有31%的硅原子和69%的金原子的Au-Si共熔体共晶点温度为370 C。
这个共晶点是选择合适的焊接温度和对焊接深度进行控制的主要依据。
金硅共晶焊接法就是芯片在一定的压力下(附以摩擦或超声),当温度高于共晶温度时,金硅合金融化成液态的Au-Si 共熔体。
冷却后,当温度低于共晶温度时,共熔体由液相变为以晶粒形式互相结合的机械混合物——金硅共熔晶体而全部凝固,从而形成了牢固的欧姆接触焊接面。
金属合金焊接还包括“软焊料”焊接(如95Pb/5Sn ,5In/ ),由于其机械强度相对较小,在半导体器件芯片焊接中不太常用。
影响芯片共晶的关键因素共晶焊料的特性a)比纯组元熔点低,简化了熔化工艺。
b)共晶合金比纯金属有更好的流动性,在凝固中可防止阻碍液体流动的枝晶形成,从而改善了铸造性能。
c)恒温转变(无凝固温度范围)减少了铸造缺陷,如偏聚和缩孔。
d)共晶凝固可获得多种形态的显微组织,尤其是规则排列的层状或杆状共晶组织,可成为优异性能的原位复合材料。
共晶焊料的选用焊料是共晶焊接非常关键的因素。
有多种合金可以作为焊料,如Au Ge 、Au Sn、Au Si 、Snln、Sn Ag、Sn Bi 等,各种焊料因其各自的特性适于不同的应用场合。
如:含银的焊料Ag Sn ,易于与镀层含银的端面接合,含金、含铟的合金焊料易于与镀层含金的端面接合。
根据被焊件的热容量大小,一般共晶炉设定的焊接温度要高于焊料合金的共晶温度30〜50C。
芯片能耐受的温度与焊料的共晶温度也是进行共晶时应当关注的问题。
如果焊料的共晶温度过高,就会影响芯片材料的物理化学性质,使芯片失效。
因此焊料的选用要考虑镀层的成份与被焊件的耐受温度。
此外,如焊料存放时间过长,会使其表面的氧化层过厚,因焊接过程中没有人工干预,氧化层是很难去除的,焊料熔化后留下的氧化膜会在焊后形成空洞。
在焊接过程中向炉腔内充入少量氢气,可以起到还原部分氧化物的作用,但最好是使用新焊料,使氧化程度降到最低。
温度控制工艺曲线参数的确立共晶时的热损耗,热应力,湿度,颗粒以及冲击或振动是影响焊接效果关键因素。
热损伤会影响薄膜器件的性能。
湿度过高可能引起粘连,磨损,附着现象。
无效的热部件会影响热的传导。
共晶时最常见的问题是基座的温度低于共晶温度。
在这种情况下,焊料仍能熔化,但没有足够的温度来扩散芯片背面的镀金层,而操作者容易误认为焊料熔化就是共晶了。
另一方面,用过长的时间来加热基座会导致电路金属的损坏,可见共晶时温度和时间的控制是十分重要的。
由于以上原因,温度曲线的设置是共晶好坏的重要因素。
由于共晶时需要的温度较高,特别是用Au Ge 焊料共晶,对基板及薄膜电路的耐高温特性提出了要求。
要求电路能承受400 C的高温,在该温度下,电阻及导电性能不能有改变。
因此共晶的一个关键因素是温度,它不是单纯的到达某个定值温度,而是要经过一个温度曲线变化的过程,在温度变化中,还要具备处理任何随机事件的能力,如抽真空、充气、排气等事件。
这些都是共晶炉设备具备的功能。
多芯片共晶的温度控制与单芯片共晶不同。
多芯片共晶时会出现芯片材料不同,共晶焊料不同,因此共晶温度不同的情况。
这时需要采用阶梯共晶的方法。
一般先对温度高的共晶焊料共晶,再共晶温度低的。
共晶炉控制系统可以设定多条温度曲线,每条温度曲线可以设定9 段,通过链接的方式可扩展到81 段,在温度曲线运行过程中可增加充气、抽真空、排气等工艺步骤。
芯片载体的选择芯片载体的导电性能,导热性能以及CTE,是选用的参考标准。
另外载体镀层厚度同样直接影响共晶焊接的强度,镀层太薄会造成焊料不能充分浸润,而导致形成空洞、焊接不牢,甚至掉片。
镀层太厚成本太高。
载体粗糙度及清洗载体表面不同的粗糙度对共晶效果有一定影响。
载体镀金层表面的洁净度对焊接的质量影响也大,表面的无机物、有机污物,氧化物等都会造成共晶焊层的空洞,从而影响共晶质量。
工艺参数的设定共晶参数除了温度控制工艺曲线以外,在不使用共晶炉,而采用共晶贴片机时,还需对温度、时间、气氛、摩擦速度、摩擦行程、摩擦时间、不同芯片大小、焊料大小、共晶台温度设置等参数通过多次实验来确定合适范围。
空洞率的控制空洞的多少直接关系到芯片的散热、可靠性的高低,是共晶工艺首要需要解决的问题。
它和焊料、温度、环境洁净度、材质、时间等多个因素都有关。
只有通过实验,优化工艺参数来控制空洞率。
金丝键合工艺金丝键合指使用金属丝(金线等),利用热压或超声能源,完成微电子器件中固电路内部互连接线的连接,即芯片与电路或引线框架之间的连接。