浅谈压力容器制造的常见缺陷及处理
压力容器制造常见问题与解决方法
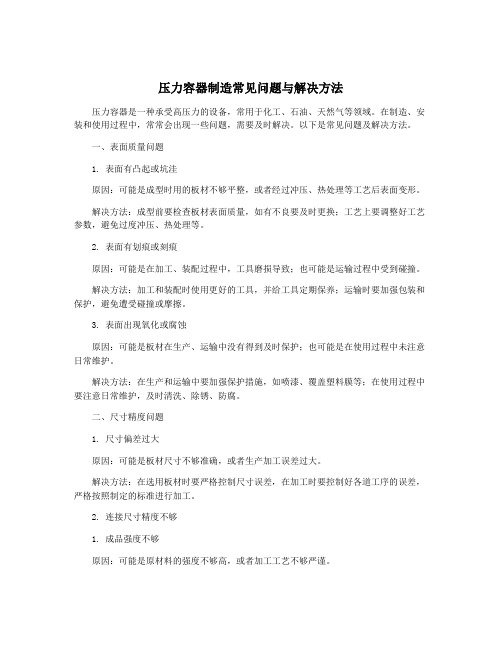
压力容器制造常见问题与解决方法压力容器是一种承受高压力的设备,常用于化工、石油、天然气等领域。
在制造、安装和使用过程中,常常会出现一些问题,需要及时解决。
以下是常见问题及解决方法。
一、表面质量问题1. 表面有凸起或坑洼原因:可能是成型时用的板材不够平整,或者经过冲压、热处理等工艺后表面变形。
解决方法:成型前要检查板材表面质量,如有不良要及时更换;工艺上要调整好工艺参数,避免过度冲压、热处理等。
2. 表面有划痕或刻痕原因:可能是在加工、装配过程中,工具磨损导致;也可能是运输过程中受到碰撞。
解决方法:加工和装配时使用更好的工具,并给工具定期保养;运输时要加强包装和保护,避免遭受碰撞或摩擦。
3. 表面出现氧化或腐蚀原因:可能是板材在生产、运输中没有得到及时保护;也可能是在使用过程中未注意日常维护。
解决方法:在生产和运输中要加强保护措施,如喷漆、覆盖塑料膜等;在使用过程中要注意日常维护,及时清洗、除锈、防腐。
二、尺寸精度问题1. 尺寸偏差过大原因:可能是板材尺寸不够准确,或者生产加工误差过大。
解决方法:在选用板材时要严格控制尺寸误差,在加工时要控制好各道工序的误差,严格按照制定的标准进行加工。
2. 连接尺寸精度不够1. 成品强度不够原因:可能是原材料的强度不够高,或者加工工艺不够严谨。
解决方法:在选用原材料时,要选择优质材料,保证强度要求;在加工工艺中,要精确控制温度、压力等参数,严格按照标准进行加工。
2. 成品韧性不足四、安全问题1. 泄漏原因:可能是制造过程中没有严格检查质量,或者使用过程中没有注意日常维护。
解决方法:在制造时要严格按照标准和规范进行生产,严格检查各项质量指标,确保无泄漏隐患;在使用过程中要注重日常维护,及时发现和排除泄漏隐患。
2. 爆炸解决方法:在制造过程中要严格按照标准加强质量控制,确保结构安全可靠;在使用过程中要按照规范操作,避免产生危险。
压力容器制造常见问题与解决方法

压力容器制造常见问题与解决方法在每个行业中,压力容器都是必不可少的设备之一。
因为压力容器承载着高压气体或液体,所以其制造需要非常高的技术和责任心。
然而,即使在高度的技术要求、严格的检查和测试下,压力容器生产中难免会遇到一些常见的问题。
下面我们将介绍一些常见问题及其解决方法。
1. 压力容器的内部缺陷压力容器的内部缺陷包括气孔、缩孔、裂纹和夹杂等问题。
其中,气孔和缩孔是由于金属在凝固过程中受到空气的影响所产生的;而裂纹和夹杂则可能是由于过度的应力或金属粘附所引起的。
解决方法:对于气孔和缩孔等小的内部缺陷,可以采用后加工的方法进行修复。
对于较大的缺陷,可以采用修补焊接等方法进行处理。
但对于严重的裂纹和夹杂等问题,建议重新制造。
2. 四边焊缝区域的开裂压力容器的四边焊缝是容易产生问题的一个区域。
开裂问题通常是由于制造过程中的焊接不当、造成应力和温度变化引起的。
开裂问题会导致高压气体和液体泄漏,从而影响设备和环境的安全。
解决方法:在焊接过程中,需要采取恰当的焊接技术和工艺,例如提高预热温度、降低焊接速度和控制焊接质量等。
对于已经出现的开裂问题,可以通过补焊、加强结构和调整焊缝形状等方法进行修复。
3. 污染和腐蚀在高压气体和液体环境下运行的压力容器,长期暴露于该环境中会导致污染和腐蚀问题。
同时,错误的使用、维护和清洗方法也可能会导致此类问题的发生。
解决方法:相应的材料和涂层可以延长容器的使用寿命。
同时,定期的设备检查和维护也是避免污染和腐蚀问题的重要措施。
如果发现容器已经存在腐蚀或污染,需要及时修复或更换。
4. 节点设计的失误节点是压力容器中连接部分的结构设计。
不良的节点设计或结构松散,容器出现摆动、松动甚至崩裂等问题。
节点出现失误可能是由于设计不当、操作错误或材料疲劳等原因引起的。
解决方法:基于质量和容量的考虑,需要从安全的角度进行节点设计。
重要的是,需要确保连接部分不会松动、移动或变形,这需要通过适当的材料选择、强度计算和安全测试等方面实现。
压力容器制造常见问题与解决方法

压力容器制造常见问题与解决方法压力容器是一种用于储存或传输气体或液体的设备,通常用于工业领域。
制造压力容器需要严格遵循相关的标准和技术要求,以确保其安全可靠。
压力容器制造过程中也存在一些常见问题,本文将针对这些问题进行介绍并提出解决方法。
一、常见问题1.材料选择问题制造压力容器的材料选择是至关重要的,不合适的材料选择可能导致容器在使用过程中出现安全隐患。
常见的材料选择问题包括材料的抗压强度不足、耐腐蚀性能不佳等。
2.焊接质量问题焊接是压力容器制造过程中关键的环节,焊接质量直接影响到容器的使用寿命和安全性。
常见的焊接质量问题包括焊缝裂纹、焊接温度过高等。
3.设计问题压力容器的设计对其安全性和稳定性有着重要影响,不合理的设计可能导致容器在使用过程中出现问题。
常见的设计问题包括结构设计不合理、受力分布不均匀等。
4.工艺控制问题压力容器制造需要严格的工艺控制,包括材料预处理、成型工艺、热处理等环节。
工艺控制不到位可能导致容器出现质量问题。
5.检验测试问题压力容器的检验测试是其质量保障的重要环节,不合格的检验测试可能导致容器在使用过程中出现问题。
常见的检验测试问题包括检测设备不足、检测标准不规范等。
二、解决方法在材料选择上,应根据压力容器的工作压力、使用环境等因素选择合适的材料,确保其具有足够的抗压强度和耐腐蚀性能。
为了确保焊接质量,应严格按照相关标准和规范进行焊接操作,采用适当的焊接工艺参数,保证焊缝的质量。
对焊接工艺进行严格监控和检验,确保焊接质量符合要求。
在压力容器的设计过程中,应遵循相关的设计规范,按照受力分析结果进行合理的结构设计,确保受力分布均匀,提高容器的稳定性和安全性。
在压力容器的检验测试过程中,应使用合格的检测设备和符合标准的检测方法,确保检验测试的准确性和可靠性。
压力容器筒体卷制质量缺陷分析及对策

压力容器筒体卷制质量缺陷分析及对策前言随着工业的不断发展,压力容器在工业生产中发挥着越来越大的作用。
而对于压力容器筒体的卷制质量缺陷问题,一直是生产中值得关注和解决的问题。
本文将对压力容器筒体卷制质量缺陷问题进行分析,并提出一些对策。
压力容器筒体卷制质量缺陷的原因压力容器筒体卷制的质量缺陷问题主要是由以下几方面原因所导致:材料原因材料的选用是影响压力容器筒体卷制质量的重要因素。
材料的质量及其物理化学性能直接影响到卷制后成品的质量。
一些材料中含有的杂质、疵点、氧化物等,在卷制时会产生卷制质量的缺陷。
设备因素由于设备的制造工艺和工艺水平等差异,也会引起不同程度的卷制质量缺陷。
因此,压力容器筒体卷制设备的选购和制造工艺的优化,对卷制质量具有重要的影响。
工艺因素卷制工艺是影响塞筒卷制质量的另一个因素。
卷制工艺过程中,材料的卷制速度、压力、温度等参数的控制方式、卷筒焊缝的处理方法等都会影响卷制质量。
而一些不当的卷制工艺,往往会导致卷制质量的缺陷。
压力容器筒体卷制质量缺陷分析对于压力容器筒体卷制质量缺陷问题,常见的有以下几种:1. 卷筒表面有裂纹卷筒表面常常出现裂纹的问题。
这主要是由于卷制过程中,卷筒钢板的弯曲受力过大,导致钢板表面产生了一定程度的破裂。
2. 卷筒表面出现气泡卷筒表面出现气泡是由于卷制时未能将含气的空气排出。
由于没有排气,气泡被卡在铁板内部,形成了气泡的问题。
3. 焊缝未打磨因为卷筒是由多个钢板焊接而成的,焊缝的处理对于卷制质量具有重要的影响。
如果卷制后的焊缝未能及时清理和打磨,就会留下大量的杂质和毛刺,从而影响焊接质量。
4. 波纹形变严重卷制过程中,如果钢板的卷制弯曲角度过大,就会造成卷筒的波纹形变过大的问题。
这个问题不仅影响到产品的外观质量,还会影响到产品的使用寿命。
压力容器筒体卷制质量缺陷对策针对以上分析的问题,提出以下对策:1. 选择优质的钢材选择合适的钢材是防止卷筒钢板卷制质量缺陷的关键。
压力容器制造常见问题与解决方法

压力容器制造常见问题与解决方法【摘要】本文主要介绍了压力容器制造过程中常见的问题及解决方法。
材料选择不当可能导致压力容器的性能下降甚至发生安全事故。
焊接质量不合格也是一个常见问题,需要加强焊接质量管理。
设计参数计算错误和表面处理不到位也会影响压力容器的质量。
检测手段不完善可能导致隐藏的问题无法及时发现。
为了解决这些问题,需要加强材料选择与焊接质量管理,提高设计参数计算和表面处理的准确性,以及完善检测手段和质量保障体系。
通过这些措施,可以提高压力容器的制造质量,确保其安全可靠性。
【关键词】压力容器、制造、常见问题、材料选择、焊接质量、设计参数、表面处理、检测手段、解决方法、管理、准确性、质量保障、体系。
1. 引言1.1 压力容器制造常见问题与解决方法压力容器是一种用于储存或传输气体、液体或蒸汽的设备,广泛应用于化工、石油、制药等行业。
在压力容器的制造过程中,常常会出现一些问题,如材料选择不当、焊接质量不合格、设计参数计算错误、表面处理不到位以及检测手段不完善等。
材料选择不当可能导致压力容器在使用过程中出现强度不足或耐腐蚀性能不佳的问题,进而影响设备的安全性和使用寿命。
解决这一问题的关键在于加强材料选择与焊接质量管理,确保选用符合要求的材料,并进行严格的材料检验和焊接监控。
焊接质量不合格可能会导致焊缝处出现裂纹、气孔等缺陷,从而降低压力容器的承压能力和安全性。
要解决这一问题,需要加强焊接工艺控制,提高焊工技术水平,确保焊接质量符合要求。
设计参数计算错误可能导致压力容器在工作过程中出现超压或不稳定等问题,危及设备和人员安全。
要解决这一问题,需要提高设计人员的专业水平,加强设计参数计算的准确性和可靠性。
检测手段不完善可能导致压力容器内部缺陷难以发现,从而影响设备的安全性。
要解决这一问题,需要完善检测手段和质量保障体系,确保对压力容器进行全面、准确的检测。
要提高压力容器制造的质量和安全性,需要加强材料选择与焊接质量管理,提高设计参数计算和表面处理的准确性,完善检测手段和质量保障体系。
浅谈压力容器制造的常见缺陷及处理

浅谈压力容器制造的常见缺陷及处理摘要:压力容器是工业生产中经常使用的器件,在对压力容器进行制造时,不仅要遵循严格的设计要求,更重要的是排除制造过程中压力容器的缺陷影响。
常见的缺陷主要体现在容器的计划环节、制作过程中以及安装方面,本文针对压力容器的制造过程进行研究,探讨一下制造过程中常见的缺陷以及缺陷处理的有效措施。
关键词:压力容器;常见缺陷;处理我国各行各业,压力容器的使用非常普遍,例如:餐饮行业、生物制药行业、石油化工行业等等,随着压力容器的使用越来越频繁,不同样式、不同规模的压力容器逐渐问世,压力容器在制作过程中的缺陷也随之而来,缺陷的存在直接关系到压力容器在使用上的效果,因此需对制造过程中的缺陷进行处理,一方面提高压力容器的制造效率;另一方面提高压力容器的使用效益。
1.压力容器简介市场上压力容器的产品是多种多样的,为满足不同行业客户的需求,提升了压力容器的制造规模,由于行业需求的不同,促使压力容器的形态、结构朝向多样化的方向发展。
压力容器制造的过程中,涉及到多种规范性的标准,而且制造过程中对标准需要严格遵循。
制造过程中,受到多方条件影响,例如:真空、高温等,压力容器在使用上常接触不稳定的物质,因此安全因素是压力容器制造过程中必须考虑的内容,由此,必须对制造过程中出现的缺陷进行控制,采取有效的措施处理,保障压力容器的标准性。
2.压力容器制造缺陷压力容器的缺陷[1]是贯穿在整体制造过程中的,主要是围绕压力容器的使用材料、焊接工艺以及加工过程产生的,对此进行以下分析:2.1.材料使用不得当压力容器在制造时,对材料的选择是非常严格的,材料稍微不得当即会引起制造缺陷,因此在材料选择时,需重点考虑材料的性能,高性能的材料在压力容器制造过程中发挥着关键作用,但是材料是受多方面因素影响的,例如:温度、湿度等等,导致材料的稳定性发生变化,导致制造过程中,压力容器出现缺陷。
2.2.焊接工艺不到位焊接是压力容器制造过程中的主要工艺,焊接过程中会造成极大的影响,导致压力容器的部件发生缺陷,例如:焊接的纵向选取与横向选取,两者均为压力容器制造过程中不可缺少的工艺,但是两种焊接工艺在使用的过程中均会对压力容器造成不同程度的影响。
压力容器制造常见问题与解决方法

压力容器制造常见问题与解决方法压力容器是一种用于储存或传递气体、液体或蒸汽等物质的装置,通常用于工业生产和其他领域。
在制造和使用过程中,压力容器面临着一系列的问题,如泄漏、腐蚀、变形等,这些问题可能会对设备的安全性和稳定性造成影响。
了解压力容器制造中常见的问题以及对应的解决方法是非常重要的。
本文将从材料选择、制造工艺、质量检测等方面介绍压力容器制造中常见问题,并提出相应的解决方法。
一、材料选择1. 问题:材料选择不当导致压力容器腐蚀解决方法:在压力容器制造过程中,材料选择是至关重要的一环。
首先需要考虑容器所处的工作环境及介质的性质,选择适合的材料,如不锈钢、碳钢等,以提高耐腐蚀性能。
要对所选材料进行严格的质量检测,确保其符合技术标准和工艺要求。
二、制造工艺2. 问题:焊接质量不合格导致压力容器泄漏解决方法:焊接是压力容器制造中至关重要的工艺环节,焊接质量直接关系到容器的安全性和稳定性。
在焊接过程中,需要严格控制焊接参数,如焊接电流、电压、焊接速度等,确保焊缝的牢固性和密封性。
还需采用合适的焊接工艺,如气体保护焊、电弧焊等,以减少气孔、夹渣等焊接缺陷的产生。
3. 问题:压力容器变形严重解决方法:压力容器在制造过程中,可能会因为材料变形或者加工误差等原因而导致变形。
为了解决这一问题,首先需要对容器的设计参数进行合理选取,尽量减少材料的应力集中,提高容器的稳定性。
需要在制造过程中严格控制加工质量,减少加工误差的出现。
还可以采用热处理等工艺手段,对变形的压力容器进行修复。
三、质量检测4. 问题:质量检测不到位导致隐患解决方法:质量检测是保证压力容器安全性和稳定性的重要手段。
在制造过程中需要加强对材料、焊接接头、容器结构等关键部位的质量检测。
对于焊接接头,可以采用X射线探伤、超声波检测等无损检测技术进行检测,确保焊缝的质量和密封性。
对于容器结构,可以进行压力测试、泄漏测试等工艺检测,以排除隐患。
压力容器制造过程中常见问题的解决方法主要包括合理选择材料、严格控制制造工艺、加强质量检测等环节。
浅谈压力容器设计中的常见问题及对策

浅谈压力容器设计中的常见问题及对策压力容器是工业生产中常见的设备,用于加工、储存和输送各种气体、液体和粉末。
它们承受着高压、高温或低温等复杂的工作环境,因此在设计和制造过程中要特别注意安全性和可靠性。
在压力容器设计中常常会遇到一些问题,下面就让我们来浅谈一下这些常见问题及对策。
一、焊接质量问题焊接是压力容器制造过程中最关键的环节之一,焊接质量直接影响着容器的安全性和可靠性。
常见的焊接质量问题包括焊接缺陷、焊接接头设计不合理和焊接接头处的应力集中等。
为了解决这些问题,首先应该加强焊工的技术培训,提高他们的焊接水平和质量意识;其次要严格控制焊接工艺参数,确保焊接质量符合标准要求;最后要设计合理的焊接接头结构,减少应力集中并提高接头的疲劳寿命。
二、材料选择和损伤问题压力容器的材料选择直接关系到其抗压性能和耐腐蚀性能。
选择不当或材料损伤都会导致容器失效。
为了避免这些问题,首先应该在设计阶段就对材料进行严格筛选和检测,确保材料符合要求;其次要加强对材料的管理和保养,及时发现并处理材料损伤问题;最后要严格按照材料的使用规范来设计和制造压力容器,确保其安全性和可靠性。
三、安全阀和压力表问题安全阀和压力表是压力容器的重要保护装置,它们直接关系到容器的安全运行。
常见的问题包括安全阀和压力表的选择不当、安装位置不合理和维护不及时等。
为了解决这些问题,首先应该对安全阀和压力表的性能和使用要求有清楚的了解,确保其选择和安装符合标准要求;其次要加强对安全阀和压力表的维护保养,及时发现并处理问题;最后要加强对安全阀和压力表的使用管理,确保其在容器运行过程中起到应有的作用。
四、设备结构设计问题压力容器的结构设计直接关系到其承压性能和使用寿命。
常见的结构设计问题包括受力分析不合理、结构尺寸设计不合理和支撑方式选择不当等。
为了解决这些问题,首先应该加强对设备结构设计的理论研究和实践经验总结,确保设计合理性;其次要加强对设备结构的计算分析,确保其受力性能符合要求;最后要结合实际情况对设备结构进行合理优化,确保容器的安全运行。
压力容器设计制造的问题及解决对策

压力容器设计制造的问题及解决对策压力容器是一种常见的工艺设备,在化工、医药、食品等行业都有广泛应用。
随着工业发展的迅猛,压力容器的设计制造也面临着一些问题和挑战。
本文将探讨压力容器设计制造中存在的问题,并提出相应的解决对策。
一、设计问题1.材料选择不当。
压力容器的制造材料通常是金属材料,而不同的工作条件对压力容器材料的性能要求也不同。
选材不当可能导致容器在工作过程中出现失效或事故。
解决对策:对于不同工作条件下的压力容器,应根据具体情况选择合适的材料,并对材料进行充分的测试和验证,确保其符合设计要求。
2.设计强度不够。
在使用压力容器的过程中,可能会受到内部或外部的压力,如果设计强度不够,就会存在安全隐患。
解决对策:在设计压力容器时,必须充分考虑各种工作条件下的压力情况,进行强度计算和模拟分析,确保设计的容器具有足够的强度和稳定性。
3.焊接质量不合格。
焊接是压力容器制造中不可或缺的工艺,焊接质量直接影响到容器的使用性能和安全性。
解决对策:在焊接过程中,必须严格按照相关规范和标准进行操作,保证焊接质量符合要求。
对焊接接头进行全面的检测和检验,确保质量合格。
二、制造问题1.工艺方面存在缺陷。
在压力容器的制造过程中,可能会出现工艺方面的不足,例如工艺流程不合理、设备不足等问题,影响容器的制造质量。
解决对策:在制造过程中,应充分合理规划工艺流程,确保每个环节都符合相关标准和要求。
对关键工艺环节进行监控和控制,及时发现和解决问题。
2.质量管理不到位。
如果在压力容器的制造过程中质量管理不到位,就很容易出现质量问题,导致产品的安全性和可靠性受到影响。
解决对策:建立完善的质量管理体系,对每个制造环节进行严格的控制和管理,确保产品质量满足设计要求。
三、技术问题1.缺乏相关技术人才。
压力容器的设计制造需要丰富的工程经验和专业知识,缺乏相关技术人才会影响产品质量和生产效率。
解决对策:加强人才培养和引进工作,培养一批具有丰富经验和专业知识的技术人才,确保能够满足压力容器设计制造的需求。
浅谈压力容器制造过程中存在的问题及相应解决措施
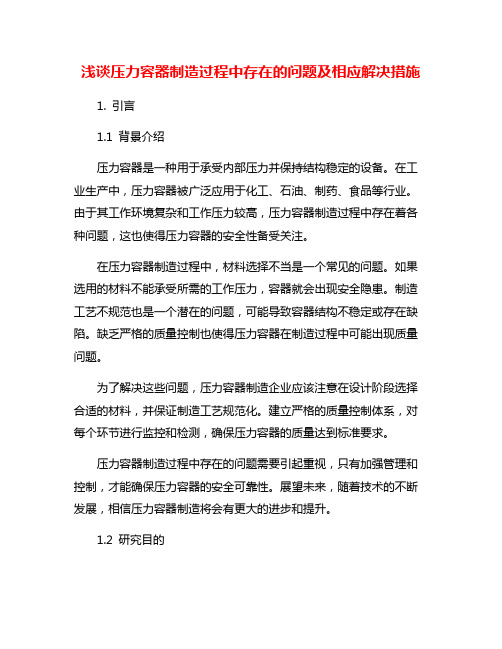
浅谈压力容器制造过程中存在的问题及相应解决措施1. 引言1.1 背景介绍压力容器是一种用于承受内部压力并保持结构稳定的设备。
在工业生产中,压力容器被广泛应用于化工、石油、制药、食品等行业。
由于其工作环境复杂和工作压力较高,压力容器制造过程中存在着各种问题,这也使得压力容器的安全性备受关注。
在压力容器制造过程中,材料选择不当是一个常见的问题。
如果选用的材料不能承受所需的工作压力,容器就会出现安全隐患。
制造工艺不规范也是一个潜在的问题,可能导致容器结构不稳定或存在缺陷。
缺乏严格的质量控制也使得压力容器在制造过程中可能出现质量问题。
为了解决这些问题,压力容器制造企业应该注意在设计阶段选择合适的材料,并保证制造工艺规范化。
建立严格的质量控制体系,对每个环节进行监控和检测,确保压力容器的质量达到标准要求。
压力容器制造过程中存在的问题需要引起重视,只有加强管理和控制,才能确保压力容器的安全可靠性。
展望未来,随着技术的不断发展,相信压力容器制造将会有更大的进步和提升。
1.2 研究目的研究目的是为了深入探讨压力容器制造过程中存在的问题及相应解决措施,通过对材料选择不当、制造工艺不规范、缺乏严格质量控制等方面进行分析和总结,为压力容器制造行业提供一些具体的改进建议和指导意见。
通过本研究,希望能够促进压力容器制造工艺的不断完善和提升,确保压力容器的安全性和可靠性,保障人民生命财产安全,推动我国压力容器制造行业的健康发展。
2. 正文2.1 压力容器制造过程中存在的问题在压力容器制造过程中,存在着诸多问题需要引起重视和解决。
材料选择不当是一个常见的问题。
由于一些厂家为了降低成本,使用劣质材料或者不符合标准的材料进行制造,导致容器的使用寿命大大缩短,甚至存在安全隐患。
制造工艺不规范也是一个常见问题。
一些制造企业为了赶工期或者降低成本,忽略了制造工艺的严谨和规范性,造成了制造过程中的各种质量问题,影响了容器的使用效果和安全性。
压力容器制造中常见问题及分析
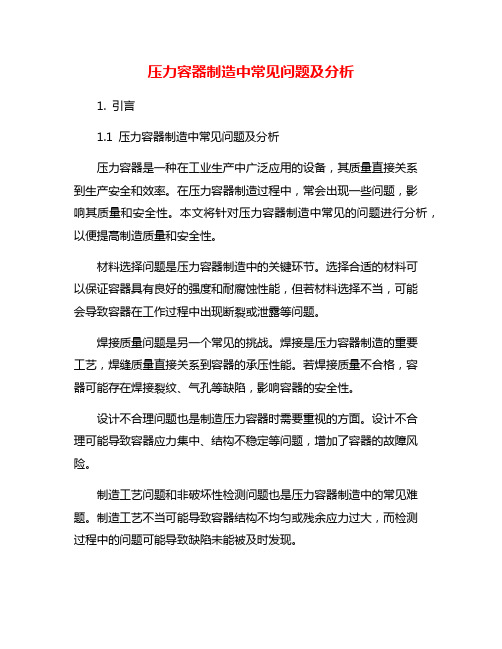
压力容器制造中常见问题及分析1. 引言1.1 压力容器制造中常见问题及分析压力容器是一种在工业生产中广泛应用的设备,其质量直接关系到生产安全和效率。
在压力容器制造过程中,常会出现一些问题,影响其质量和安全性。
本文将针对压力容器制造中常见的问题进行分析,以便提高制造质量和安全性。
材料选择问题是压力容器制造中的关键环节。
选择合适的材料可以保证容器具有良好的强度和耐腐蚀性能,但若材料选择不当,可能会导致容器在工作过程中出现断裂或泄露等问题。
焊接质量问题是另一个常见的挑战。
焊接是压力容器制造的重要工艺,焊缝质量直接关系到容器的承压性能。
若焊接质量不合格,容器可能存在焊接裂纹、气孔等缺陷,影响容器的安全性。
设计不合理问题也是制造压力容器时需要重视的方面。
设计不合理可能导致容器应力集中、结构不稳定等问题,增加了容器的故障风险。
制造工艺问题和非破坏性检测问题也是压力容器制造中的常见难题。
制造工艺不当可能导致容器结构不均匀或残余应力过大,而检测过程中的问题可能导致缺陷未能被及时发现。
压力容器制造中存在诸多潜在问题,需要加强质量管理措施、持续改进制造工艺和技术,以及强化员工培训和素质提升,以确保压力容器的质量和安全性,促进工业生产的可持续发展。
2. 正文2.1 材料选择问题材料选择问题是压力容器制造中一个至关重要的环节。
在材料选择过程中,需要考虑到压力容器的工作环境、工作压力、温度范围、介质性质等多方面因素。
一旦选用不当的材料,可能导致压力容器在工作过程中出现严重问题,甚至引发事故。
材料的机械性能是材料选择的关键因素之一。
压力容器在工作时需要承受较大的压力,因此材料的抗拉强度、屈服强度、抗压强度等机械性能必须符合标准要求。
材料的耐热性、耐腐蚀性、抗疲劳性等性能也需要被充分考虑。
材料的焊接性能也是十分重要的。
压力容器通常需要通过焊接工艺进行组装,因此选用的材料必须具备良好的焊接性能,能够确保焊接接头的质量和可靠性。
压力容器常见的缺陷及措施

5.2压力容器常见的缺陷及措施在用压力容器常见缺陷就其存在部位可分为表面缺陷和埋藏缺陷两类,都对压力容器的安全性能构成潜在威胁,以下对其中的焊接所造成的缺陷分别进行讨论。
1、表面缺陷(1)表面裂纹裂纹是在用压力容器的重点检验项目。
现场检验时优先使用磁粉探伤技术,它能快速、准确和直观地发现表面裂纹,是目前检验表面缺陷最为灵敏可靠的手段。
表面裂纹危害性极大,一旦发现应认真分析其产生原因,采取适当的措施(如打磨和挖补等) 予以彻底消除。
从断裂力学观点而言,表面裂纹也存在允许尺寸,但考虑到内表面裂纹与储存介质直接接触,外表面裂纹与大气接触,因此易促使裂纹的扩展,危害极大,故对表面裂纹一律采取打磨消除的措施。
措施:有关文件规定,如表面裂纹打磨深度≤7 %的设计厚度,且>3mm 时,可不补焊。
但为了减少应力集中,要求磨削部位光滑并过渡圆滑。
如果超出上述规定,则必须采取严格的补焊措施予以修复。
(2)焊缝咬边焊缝咬边为几何不连续与应力集中部位,容易诱发裂纹。
对于容器的焊缝咬边,都应打磨消除或打磨后补焊;对于其它容器,当其表面焊缝咬边深度≤0. 5mm ,连续长度≤100mm ,且焊缝两侧咬边总长不超过该焊缝长度的10 %时,可不作处理。
如超过上述范围,则应打磨消除或打磨后补焊。
2、埋藏缺陷常见的埋藏缺陷主要有裂纹、未焊透、未熔合、气孔和夹渣等。
这些缺陷多为制造时留下的,其中处理的重点为埋藏裂纹。
壁厚< 8mm 的钢制容器一般采用X 射线探伤,可直接准确地反映缺陷类型和大小。
随着板厚的增加,X 射线能量衰减增大,探伤灵敏度降低,因此当检测壁厚> 8mm 的钢制容器时,一般采用超声波探伤。
超声波穿透能力很强,对厚板中缺陷的探伤灵敏度较高且检测速度快。
(1)埋藏裂纹不与腐蚀介质接触,相对于表面裂纹而言,所受的应力较小,危害性也较小。
但在使用过程中,尤其是在交变载荷或频繁间歇操作时,有可能产生裂纹扩展至表面或穿透,产生破坏,因此对埋藏裂纹的处理要重视,一旦发现必须采取严格的措施予以挖补修复。
压力容器制造常见问题与解决方法

压力容器制造常见问题与解决方法
压力容器是一种重要的设备,常用于各种工业领域,如石油化工、电力、食品加工、制药等。
在使用过程中,压力容器制造常见问题可能会影响设备的安全性和可靠性。
以下将就压力容器制造常见问题及解决方法进行探讨。
一、常见问题
1. 材料选择不当
压力容器的材料选择关系到其使用环境和耐压性能。
在材料选择不当时,会导致压力容器的承压能力不足,引发安全隐患。
2. 制造工艺缺陷
压力容器的制造工艺质量是影响设备安全的重要因素。
若制造工艺存在缺陷,如焊接质量不良、成形工艺不当等,容易导致设备在使用中出现问题。
3. 设计不合理
压力容器设计不合理可能会导致设备结构强度不足或受力不均,影响设备的安全运行。
4. 焊接裂纹
焊接是压力容器制造过程中不可或缺的工艺,而焊接裂纹是较常见的焊接质量问题之一,严重时会导致设备失效。
5. 腐蚀和磨损
压力容器在使用中可能会受到介质腐蚀和磨损,若未能正确预防和处理,则会影响设备的寿命和安全性。
二、解决方法
1. 材料选择
在压力容器的制造过程中,应选择符合国家标准和行业要求的耐压材料,严格按照设计要求进行材料选择,确保设备的耐压性能。
2. 完善的制造工艺
在压力容器的制造过程中,应严格按照相关工艺标准进行操作,确保设备制造过程中无质量缺陷。
3. 合理设计
在压力容器的设计阶段,应充分考虑设备的受力情况和使用环境,确保设计方案合理可靠,提高设备的安全性。
4. 焊接质量控制
在焊接过程中,应严格按照相关标准进行操作,确保焊缝质量良好,避免出现焊接裂纹等问题。
压力容器制造中常见问题及分析

压力容器制造中常见问题及分析压力容器是承受内外压力,用于贮存或输送液体、气体或气体逸出产物的设备。
由于其工作环境的特殊性,压力容器制造中常见一些问题,下面将对这些问题进行分析。
1. 裂纹问题:压力容器因为长期受力,容易在焊接或制造过程中出现裂纹。
造成裂纹的原因可能是材料质量不合格、焊接工艺不当或应力集中等。
解决这个问题的方法是经过严格的质量控制,选择合适的材料和焊接工艺,并对容器结构进行适当的优化设计。
2. 腐蚀问题:由于压力容器通常用于存储或输送腐蚀性介质,容器壁会受到腐蚀的影响。
这种腐蚀可能会导致容器壁变薄或出现孔洞,从而降低容器的强度和密封性。
解决这个问题的方法是选择抗腐蚀性能好的材料,并在容器壁表面进行防腐处理。
3. 渗漏问题:压力容器的密封性是其工作的关键。
渗漏问题可能是由于焊接不牢固、密封材料老化或安装不当等原因造成的。
解决这个问题的方法是加强焊接质量控制,定期检查密封材料的状态,并进行必要的维修和更换。
4. 事故暴露问题:压力容器在使用过程中,可能会受到外部冲击、高温、高压等因素的影响,从而导致事故。
这种事故暴露问题可能是由于设计不合理、材料或制造工艺问题造成的。
解决这个问题的方法是对容器进行严格的设计和制造标准要求,并在使用前进行必要的检测和试验。
5. 疲劳问题:压力容器在长期使用过程中,由于受到交变载荷的作用,容器结构容易产生疲劳损伤。
这种疲劳问题可能是由于容器结构设计不合理、材料强度不足或工作条件超过容器耐受能力造成的。
解决这个问题的方法是对容器结构进行合理的设计和优化,并选择高强度材料进行制造。
压力容器设计制造常见缺陷及应对措施
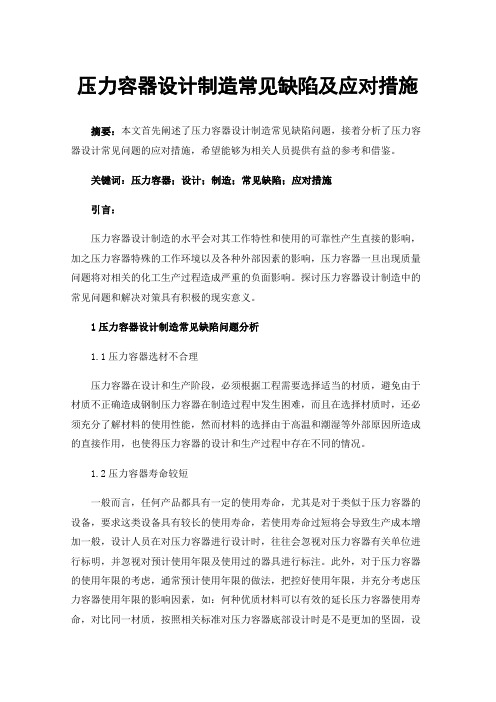
压力容器设计制造常见缺陷及应对措施摘要:本文首先阐述了压力容器设计制造常见缺陷问题,接着分析了压力容器设计常见问题的应对措施,希望能够为相关人员提供有益的参考和借鉴。
关键词:压力容器;设计;制造;常见缺陷;应对措施引言:压力容器设计制造的水平会对其工作特性和使用的可靠性产生直接的影响,加之压力容器特殊的工作环境以及各种外部因素的影响,压力容器一旦出现质量问题将对相关的化工生产过程造成严重的负面影响。
探讨压力容器设计制造中的常见问题和解决对策具有积极的现实意义。
1压力容器设计制造常见缺陷问题分析1.1压力容器选材不合理压力容器在设计和生产阶段,必须根据工程需要选择适当的材质,避免由于材质不正确造成钢制压力容器在制造过程中发生困难,而且在选择材质时,还必须充分了解材料的使用性能,然而材料的选择由于高温和潮湿等外部原因所造成的直接作用,也使得压力容器的设计和生产过程中存在不同的情况。
1.2压力容器寿命较短一般而言,任何产品都具有一定的使用寿命,尤其是对于类似于压力容器的设备,要求这类设备具有较长的使用寿命,若使用寿命过短将会导致生产成本增加一般,设计人员在对压力容器进行设计时,往往会忽视对压力容器有关单位进行标明,并忽视对预计使用年限及使用过的器具进行标注。
此外,对于压力容器的使用年限的考虑,通常预计使用年限的做法,把控好使用年限,并充分考虑压力容器使用年限的影响因素,如:何种优质材料可以有效的延长压力容器使用寿命,对比同一材质,按照相关标准对压力容器底部设计时是不是更加的坚固,设计方案不同在一定程度上会影响压力容器质量,然而,这些方面设计并没有引起重视。
1.3压力容器制造中容器变形问题致使压力容器出现变形的影响因素有很多,主要包括以下几点:第一,在压力容器罐体的制造焊接过程中,压力容器焊接接头容易发生变形现象,并且在操作运行过程中,也很容易产生瞬间高温的现象,从而导致了压力容器罐体材料屈服强度降低,罐体变形的情况。
压力容器设计制造常见缺陷及应对措施
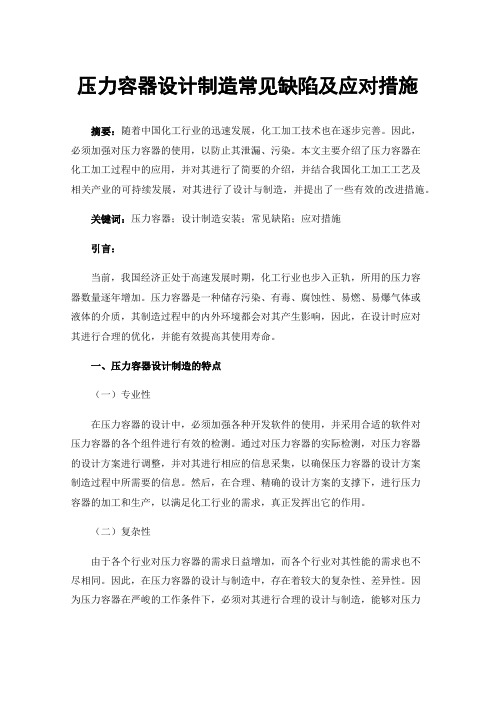
压力容器设计制造常见缺陷及应对措施摘要:随着中国化工行业的迅速发展,化工加工技术也在逐步完善。
因此,必须加强对压力容器的使用,以防止其泄漏、污染。
本文主要介绍了压力容器在化工加工过程中的应用,并对其进行了简要的介绍,并结合我国化工加工工艺及相关产业的可持续发展,对其进行了设计与制造,并提出了一些有效的改进措施。
关键词:压力容器;设计制造安装;常见缺陷;应对措施引言:当前,我国经济正处于高速发展时期,化工行业也步入正轨,所用的压力容器数量逐年增加。
压力容器是一种储存污染、有毒、腐蚀性、易燃、易爆气体或液体的介质,其制造过程中的内外环境都会对其产生影响,因此,在设计时应对其进行合理的优化,并能有效提高其使用寿命。
一、压力容器设计制造的特点(一)专业性在压力容器的设计中,必须加强各种开发软件的使用,并采用合适的软件对压力容器的各个组件进行有效的检测。
通过对压力容器的实际检测,对压力容器的设计方案进行调整,并对其进行相应的信息采集,以确保压力容器的设计方案制造过程中所需要的信息。
然后,在合理、精确的设计方案的支撑下,进行压力容器的加工和生产,以满足化工行业的需求,真正发挥出它的作用。
(二)复杂性由于各个行业对压力容器的需求日益增加,而各个行业对其性能的需求也不尽相同。
因此,在压力容器的设计与制造中,存在着较大的复杂性、差异性。
因为压力容器在严峻的工作条件下,必须对其进行合理的设计与制造,能够对压力容器进行有效的控制,以及在压力容器的多样化、复杂的特性下,对其进行合理的制造[1]。
(三)适应性化工行业对压力容器的性能提出了更高的要求,既要满足不同气体储运和化学生产的需要,又要对其进行优化调整,确保其适用性,满足气体储罐的设计、制造、储藏的适应性。
因此,在设计和制造过程中,必须对现有的压力容器进行改造,以提高压力容器的设计和制造工艺,缩短压力容器制造工艺与使用要求的差距,促进其健康发展。
二、压力容器设计制造常见的缺陷(一)法兰数值不够准确法兰是压力容器的关键部件,其法兰尺寸的精确与否直接关系到设备的优化设计。
压力容器制造常见问题与解决方法
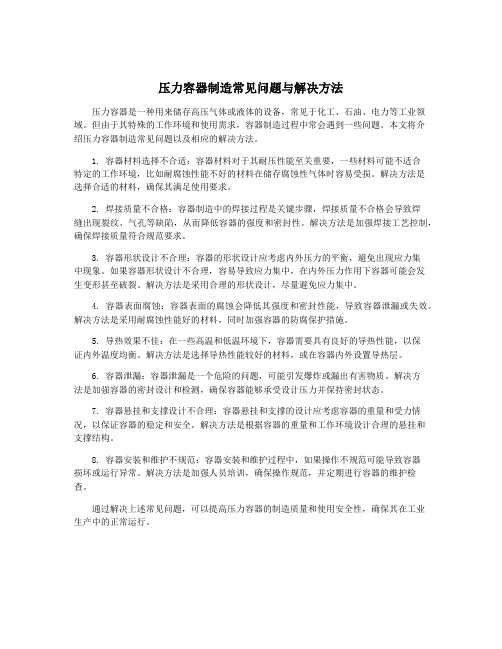
压力容器制造常见问题与解决方法压力容器是一种用来储存高压气体或液体的设备,常见于化工、石油、电力等工业领域。
但由于其特殊的工作环境和使用需求,容器制造过程中常会遇到一些问题。
本文将介绍压力容器制造常见问题以及相应的解决方法。
1. 容器材料选择不合适:容器材料对于其耐压性能至关重要,一些材料可能不适合特定的工作环境,比如耐腐蚀性能不好的材料在储存腐蚀性气体时容易受损。
解决方法是选择合适的材料,确保其满足使用要求。
2. 焊接质量不合格:容器制造中的焊接过程是关键步骤,焊接质量不合格会导致焊缝出现裂纹、气孔等缺陷,从而降低容器的强度和密封性。
解决方法是加强焊接工艺控制,确保焊接质量符合规范要求。
3. 容器形状设计不合理:容器的形状设计应考虑内外压力的平衡,避免出现应力集中现象。
如果容器形状设计不合理,容易导致应力集中,在内外压力作用下容器可能会发生变形甚至破裂。
解决方法是采用合理的形状设计,尽量避免应力集中。
4. 容器表面腐蚀:容器表面的腐蚀会降低其强度和密封性能,导致容器泄漏或失效。
解决方法是采用耐腐蚀性能好的材料,同时加强容器的防腐保护措施。
5. 导热效果不佳:在一些高温和低温环境下,容器需要具有良好的导热性能,以保证内外温度均衡。
解决方法是选择导热性能较好的材料,或在容器内外设置导热层。
6. 容器泄漏:容器泄漏是一个危险的问题,可能引发爆炸或漏出有害物质。
解决方法是加强容器的密封设计和检测,确保容器能够承受设计压力并保持密封状态。
7. 容器悬挂和支撑设计不合理:容器悬挂和支撑的设计应考虑容器的重量和受力情况,以保证容器的稳定和安全。
解决方法是根据容器的重量和工作环境设计合理的悬挂和支撑结构。
8. 容器安装和维护不规范:容器安装和维护过程中,如果操作不规范可能导致容器损坏或运行异常。
解决方法是加强人员培训,确保操作规范,并定期进行容器的维护检查。
通过解决上述常见问题,可以提高压力容器的制造质量和使用安全性,确保其在工业生产中的正常运行。
压力容器制造常见问题与解决方法

压力容器制造常见问题与解决方法压力容器是一种容器,可以容纳高压气体或液体,用于贮存、运输或处理。
在压力容器制造过程中,常见一些问题需要及时解决,以确保容器的安全和可靠性。
本文将介绍常见的压力容器制造问题及解决方法。
一、焊接问题1. 问题:焊接中出现气孔、裂纹等质量问题。
解决方法:首先要对焊接材料进行质量检查,确保焊材的质量符合要求;其次要对焊工进行严格的培训和考核,确保焊接工艺的正确性;要对焊接设备进行定期维护,确保设备的稳定性。
2. 问题:焊接变形严重,影响容器的整体结构。
解决方法:在焊接过程中,要控制好焊接参数,避免过大的焊接温度和速度;采用适当的预热和冷却措施,帮助减轻焊接变形。
二、材料问题1. 问题:材料质量不达标。
解决方法:严格按照国家标准选用合格的压力容器材料,杜绝使用劣质材料;同时对材料进行严格的检测,确保其质量符合要求。
2. 问题:材料强度不足。
解决方法:选用合适的材料和厚度,确保容器的强度符合设计要求;在制造过程中要进行严格的材料控制和检测,确保材料的强度符合要求。
三、设计问题1. 问题:容器设计不合理,存在安全隐患。
解决方法:在设计容器时,要充分考虑到使用环境和使用条件,确保容器的设计符合国家标准和要求;在设计过程中要充分考虑到压力容器的可靠性和安全性,保证容器在使用过程中不会出现问题。
四、制造问题1. 问题:制造工艺不合理,影响容器的整体质量。
解决方法:在制造过程中,要严格按照国家标准和要求进行操作,确保制造工艺的正确性;要对制造设备进行定期维护和保养,确保设备的稳定性。
2. 问题:制造中出现操作失误。
解决方法:对制造人员进行严格的培训和考核,确保他们能够熟练掌握操作技能;要建立严格的质量管理体系,确保每一个制造工序都能够得到有效的监控和管理。
五、检测问题1. 问题:检测设备不足,无法对容器进行全面的检测。
解决方法:建立完善的检测体系,确保每一道工序都能够得到有效的检测和监控;对检测设备进行定期维护和保养,确保设备的稳定性。
压力容器制造中常见问题及分析
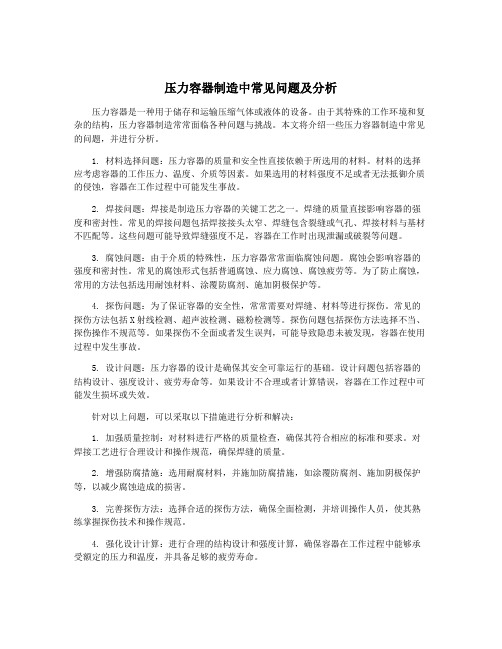
压力容器制造中常见问题及分析压力容器是一种用于储存和运输压缩气体或液体的设备。
由于其特殊的工作环境和复杂的结构,压力容器制造常常面临各种问题与挑战。
本文将介绍一些压力容器制造中常见的问题,并进行分析。
1. 材料选择问题:压力容器的质量和安全性直接依赖于所选用的材料。
材料的选择应考虑容器的工作压力、温度、介质等因素。
如果选用的材料强度不足或者无法抵御介质的侵蚀,容器在工作过程中可能发生事故。
2. 焊接问题:焊接是制造压力容器的关键工艺之一。
焊缝的质量直接影响容器的强度和密封性。
常见的焊接问题包括焊接接头太窄、焊缝包含裂缝或气孔、焊接材料与基材不匹配等。
这些问题可能导致焊缝强度不足,容器在工作时出现泄漏或破裂等问题。
3. 腐蚀问题:由于介质的特殊性,压力容器常常面临腐蚀问题。
腐蚀会影响容器的强度和密封性。
常见的腐蚀形式包括普通腐蚀、应力腐蚀、腐蚀疲劳等。
为了防止腐蚀,常用的方法包括选用耐蚀材料、涂覆防腐剂、施加阴极保护等。
4. 探伤问题:为了保证容器的安全性,常常需要对焊缝、材料等进行探伤。
常见的探伤方法包括X射线检测、超声波检测、磁粉检测等。
探伤问题包括探伤方法选择不当、探伤操作不规范等。
如果探伤不全面或者发生误判,可能导致隐患未被发现,容器在使用过程中发生事故。
5. 设计问题:压力容器的设计是确保其安全可靠运行的基础。
设计问题包括容器的结构设计、强度设计、疲劳寿命等。
如果设计不合理或者计算错误,容器在工作过程中可能发生损坏或失效。
针对以上问题,可以采取以下措施进行分析和解决:1. 加强质量控制:对材料进行严格的质量检查,确保其符合相应的标准和要求。
对焊接工艺进行合理设计和操作规范,确保焊缝的质量。
2. 增强防腐措施:选用耐腐材料,并施加防腐措施,如涂覆防腐剂、施加阴极保护等,以减少腐蚀造成的损害。
3. 完善探伤方法:选择合适的探伤方法,确保全面检测,并培训操作人员,使其熟练掌握探伤技术和操作规范。
压力容器制造常见问题与解决方法

压力容器制造常见问题与解决方法压力容器是一种用于存储或运输液体或气体的设备,因为工作环境的特殊性,压力容器制造过程中可能会出现一些常见问题。
这些问题可能会影响到压力容器的性能和安全性。
了解这些常见问题以及解决方法对于压力容器制造业是非常重要的。
1.焊接问题焊接是压力容器制造中最重要的工艺之一。
焊接质量的好坏直接影响到压力容器的安全性和使用寿命。
常见的焊接问题包括焊接温度过高导致焊缝金属变脆、焊接过程中气孔、夹渣等缺陷等。
解决方法包括严格控制焊接温度,采用合适的焊接材料,加强对焊缝的检测和清洁。
2.材料问题压力容器的材料对于其性能和安全性起着关键作用。
常见的材料问题包括材料选用不当导致耐压性能不足、材料质量不合格等。
解决方法包括选择合适的材料,加强对材料的质量检测和控制。
3.设计问题压力容器的设计是其安全性的基础。
常见的设计问题包括设计参数不合理导致应力集中、结构强度不足、疲劳寿命不足等。
解决方法包括加强设计参数的分析和计算,采用合理的设计方法和工艺。
4.工艺问题压力容器的制造过程中涉及到多种工艺,包括成形、焊接、热处理等。
常见的工艺问题包括成形尺寸不准确、热处理温度不合适等。
解决方法包括加强对工艺流程的控制和管理,严格按照工艺要求进行操作。
5.质量检测问题质量检测是压力容器制造中不可或缺的环节。
常见的质量检测问题包括检测设备不准确、检测标准不合理等。
解决方法包括加强对检测设备的维护和校准,建立合理的检测标准和流程。
压力容器制造中的常见问题虽然多种多样,但通过加强对生产工艺的管理、加强对材料和质量的控制、加强对设计和检测的认真解决这些问题并不是不可能做到。
在加强制度管理的基础上,压力容器制造企业可以确保产品质量和安全性,为用户提供更加可靠的压力容器产品。
- 1、下载文档前请自行甄别文档内容的完整性,平台不提供额外的编辑、内容补充、找答案等附加服务。
- 2、"仅部分预览"的文档,不可在线预览部分如存在完整性等问题,可反馈申请退款(可完整预览的文档不适用该条件!)。
- 3、如文档侵犯您的权益,请联系客服反馈,我们会尽快为您处理(人工客服工作时间:9:00-18:30)。
浅谈压力容器制造的常见缺陷及处理
摘要:压力容器是工业生产中经常使用的器件,在对压力容器进行制造时,不仅要遵循严格的设计要求,更重要的是排除制造过程中压力容器的缺陷影响。
常见的缺陷主要体现在容器的计划环节、制作过程中以及安装方面,本文针对压力容器的制造过程进行研究,探讨一下制造过程中常见的缺陷以及缺陷处理的有效措施。
关键词:压力容器;常见缺陷;处理
我国各行各业,压力容器的使用非常普遍,例如:餐饮行业、生物制药行业、石油化工行业等等,随着压力容器的使用越来越频繁,不同样式、不同规模的压力容器逐渐问世,压力容器在制作过程中的缺陷也随之而来,缺陷的存在直接关系到压力容器在使用上的效果,因此需对制造过程中的缺陷进行处理,一方面提高压力容器的制造效率;另一方面提高压力容器的使用效益。
1.压力容器简介
市场上压力容器的产品是多种多样的,为满足不同行业客户的需求,提升了压力容器的制造规模,由于行业需求的不同,促使压力容器的形态、结构朝向多样化的方向发展。
压力容器制造的过程中,涉及到多种规范性的标准,而且制造过程中对标准需要严格遵循。
制造过程中,受到多方条件影响,例如:真空、高温等,压力容器在使用上常接触不稳定的物质,因此安全因素是压力容器制造过程中必须考虑的内容,由此,必须对制造过程中出现的缺陷进行控制,采取有效的措施处理,保障压力容器的标准性。
2.压力容器制造缺陷
压力容器的缺陷[1]是贯穿在整体制造过程中的,主要是围绕压力容器的使用材料、焊接工艺以及加工过程产生的,对此进行以下分析:
2.1.材料使用不得当
压力容器在制造时,对材料的选择是非常严格的,材料稍微不得当即会引起制造缺陷,因此在材料选择时,需重点考虑材料的性能,高性能的材料在压力容器制造过程中发挥着关键作用,但是材料是受多方面因素影响的,例如:温度、湿度等等,导致材料的稳定性发生变化,导致制造过程中,压力容器出现缺陷。
2.2.焊接工艺不到位
焊接是压力容器制造过程中的主要工艺,焊接过程中会造成极大的影响,导
致压力容器的部件发生缺陷,例如:焊接的纵向选取与横向选取,两者均为压力容器制造过程中不可缺少的工艺,但是两种焊接工艺在使用的过程中均会对压力容器造成不同程度的影响。
2.3.加工过程不合理
压力容器在加工的过程中,涉及到尺寸测量、定型操作,由于操作人员技术不规范或者是在加工过程中出现不合理的操作,造成压力容器缺陷,压力容器制造过程中,过多的采取人工操作,降低了加工过程的合理性,而且在制造过程中,由于受加工过程不合理因素的影响,很容易造成压力容器变形。
3.制造缺陷的处理措施
针对压力容器在制造过程中出现的缺陷,进行有效的研究、分析,为有效控制压力容器缺陷的出现,提出具体的处理措施,如下:
3.1.材料的标准化选取
压力容器制造材料的选取首先要符合国家对材料的规定,同时结合制造行业的要求,保障制造材料的达标性。
如果制造过程中,遇到难以采购的材料,需要利用其他材料替代时,必须以书面申请的方式递交报告,相关设计人员、制造人员确保材料无缺陷[2]影响的情况下,对其进行审批,同时,不论是原始制造材料还是替换的材料,必须按照相关的行业原则标准使用。
制造过程中,根据材料的特性,结合制造的实际过程,实行材料各方面性能的检测,降低材料特性对压力容器的影响。
3.2.合理布置焊接工艺
为避免压力容器中的焊接工艺[3]出现过度重叠或细微裂缝的情况,在进行焊接时,需着重考虑横向与纵向的关系,严格把控十字焊接的工艺,如果焊接工艺布置不合理,极有可能造成焊接缝隙的重叠情况,此现象虽然无法避免,但是可以将其不合理的工艺控制在可接受范围内,首先在部分压力容器制造的环节中,尽量避免十字焊接工艺的出现,降低焊接缝隙重叠出现的频率,例如:拼版环节、筒体的尺寸设计和组装环节;其次在进行焊接工艺选取时,应根据压力容器受力的具体情况,对其进行系统的分析,选择合适的焊接工艺,一方面提高压力容器制造的效益;另一方面最大化的控制焊接对压力容器制造的影响;最后是考虑压力容器的强度和性能,合理布置焊接工艺。
3.3.加工过程中影响因素的分析
压力容器的制造过程中,分析影响因素,避免操作上的失误。
首先在压力容器制造过程中,综合考虑工艺过程以及技术上的规定,严格按照相关的规定进行加工,利用严格的样板、模具对压力容器的制造进行约束和控制,防止压力容器在制造的过程中,或者是制造完成后发生形变;其次考虑成型压力容器的回弹量,
回弹量是制造模具的一项影响因素,压力容器同样具备热胀冷缩[4]的物理特性,压力容器在热加工、冷处理后容易收缩,以壳体为例,在制造时,为避免热涨冷缩造成的变形,可使用定位卡模具,选取大直径、薄厚度的加工工具,必要时可对其采取一定程度的支撑,有效防止接头处出现错位的现象;最后是引进校对自动化技术,利用自动化技术对参数的校对进行控制,避免人为校对造成的偏差,提高压力容器下料的利用率。
综上所述,压力容器制造过程中对缺陷的控制是一项细致、系统的工作,不仅需要提升工作人员的操作水平,而且还需要提高工作人员缺陷处理的意识,同时结合现代信息技术,将压力容器制造的缺陷控制在可使用的范围内。
4.结束语
提高压力容器制造过程中对缺陷的重视度,提出有效的处理措施,提高压力容器的合格率,同时保障压力容器制造过程的质量。
针对压力容器制造的每一项环节,充分做好缺陷处理的工作,促使压力容器在制造过程中,体现高水平的设计工艺,通过对制造工艺不断的修整、改善,降低缺陷对压力容器制造的影响力度。
参考文献:
[1] 姜静,张赞.压力容器制造中的问题及对策探讨[J].现代商贸工业,2011(22).
[2] 郝永臣.压力容器制造过程中常见缺陷问题分析[J].现代商贸工业,2010(21).
[3] 张惠娟,纳杰.压力容器制造应考虑的缺陷问题[J].有色金属设计,2012(01).
[4] 付卫宾.探讨压力容器设计中的热处理问题[J].中国石油和化工标准与质量,2012(03).
1989年毕业于江苏电大机械工艺及设备专业。
1989年就职于盐城新光集团,机械工程师,主要从事煤矿机械的设计与制造,2000年就职江苏岭南发酵设备有限公司,主要从事发酵设备、压力容器的设计及制造工艺。