摩擦材料(刹车片)中原材料的用法
刹车片原材料的组成

刹车片原材料的组成基材是刹车片的主体,它需要具有足够的强度和稳定性来承受来自刹车系统的力量和热量。
常见的刹车片基材材料包括钢、铸铁和铝。
这些材料具有良好的热传导性和机械强度,能够抵抗刹车系统产生的高温和高压。
衬片是安装在基材上的一层材料,可以提供增强刹车片性能的特殊功能。
衬片通常由金属材料制成,如钢、铜合金或铝合金。
这些金属材料具有良好的热传导性,能够迅速将刹车系统产生的热量导入基材,保持刹车片的稳定性。
摩擦材料是刹车片的关键组成部分,它能够和刹车盘产生摩擦力,将车辆的动能转化为热能,从而实现刹车的效果。
常见的刹车片摩擦材料有无机纤维(如石棉和陶瓷纤维)和有机材料(如橡胶和树脂)。
无机摩擦材料具有较高的摩擦系数和耐磨性,而有机摩擦材料则更加柔软,有助于提高刹车片的舒适性和制动性能。
粘结剂是将基材、衬片和摩擦材料粘结在一起的关键材料。
常见的粘结剂有无机粘结剂(如硬脂酸锌和硅酮)和有机粘结剂(如热塑性树脂和热固性树脂)。
粘结剂具有良好的粘结性能和热稳定性,能够确保刹车片在高温和高压的工作环境中保持稳定。
除了基材、衬片、摩擦材料和粘结剂,刹车片的制造过程中还需要考虑其他因素,如添加剂、填料和润滑剂。
添加剂能够改变刹车片的性能特点,如提高耐磨性、降低噪音和减小摩擦系数。
填料可以增加刹车片的密度和强度,提高制动效果。
润滑剂能够减少刹车片与刹车盘之间的摩擦,降低磨损和噪音。
总之,刹车片原材料的组成是多种多样的,各种材料的选择和组合取决于刹车系统的要求、制造工艺和性能需求,以确保刹车片在各种工作条件下都能稳定可靠地工作。
制作汽车刹车片的高分子材料解析
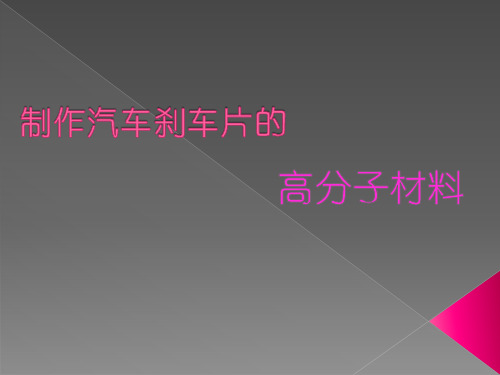
摩擦材料主要用于车辆和动力机械制动与传动,正从单一材 料向复合材料发展,其质量的好坏直接影响机器的可靠性和操 作人员的生命安全。随着科学技术的发展,人们对交通运输工 具和动力机械的速度、负荷和安全性要求越来越高。高速列车、 重载货车、轿车、赛车、摩托车等重载、高速行驶、制动频繁 的民用运载工具, 以及使用环境恶劣的装甲车、坦克、直升机等, 都对响应快、摩擦因数足够高而稳定、抗热衰减性能良好、质 量轻、寿命长和环境适应性强的高性能摩擦材料提出了迫切的 需求。20世纪90年代中期,C/C2SiC复合材料开始应用于摩擦 领域, 成为最新一代高性能制动材料而引起研究者的广泛关注和 重视,德、日等工业发达国家正逐步展开理论和应用研究。 C/C2SiC陶瓷制动材料具有密度低、耐磨性好、摩擦因数高、 制动平稳、抗腐蚀、抗氧化、耐高温、环境适应性强和寿命长 等优点,C/C2SiC陶瓷材料必将在高速高能载交通工具和工程 机械的摩擦机构上得到广泛应用,并且成本合理,所以该材料 在机械制动等领域有良好的应用前景。
C/C复合材料,即炭纤维增强炭基体复合材料。 自从1958年问世以来,由于其具有比重小(约为铁的 1/5)、强度高(抗拉强度>2GP)、热膨胀系数小、 耐高温等优点,在军工、航空、航天等方面取得了长 足的发展。其在民用领域方面的应用也日益扩大,很 多民用飞机(如波音系列:Boeing747、Boeing757 等,空客系列:A330、A340等)和高档赛车(Ferrari F2005、Renault R25、Toyota TF105等)已开始装备 C/C刹车副。目前国内中南大学、西北工业大学、中 科院金属所、航天集团第四院43所、621所等几家单位 的研究在国内居于领先水平。中南大学以博云新材料 股份有限公司为依托,C/C刹车副已全面实现产业化、 国产化[13-15]。由于C/C复合材料采用化学气相沉积 (CVD),液相浸渍炭化的生产工艺,生产周期较长, 因此成本较高,价格昂贵(一副C/C刹车盘价格高达 上万元),这也制约了其在更广阔领域特别是汽车领 域的应用。
摩擦材料

摩擦材料(盘式片、鼓式片、制动蹄)——指点行业运作迷津(一)摩擦材料的应用领域及重要性摩擦材料是用于运动中起传动、制动、减速、驻车等作用的功能配件,主要用于汽车、火车、飞机、摩托车、工程机械、船舶机械等的制动器、离合器中的刹车片、离合器面片、闸瓦(片)等,其中60%以上用于汽车工业。
汽车用制动器衬片俗称“刹车片”,按用途可分为两类:行车制动和驻车制动刹车片。
行车制动又分为盘式制动和鼓式制动刹车片。
汽车用制动刹车片在汽车工业中属于关键的安全件,汽车的制动和驻车都离不开它,刹车片质量的优劣直接关系到使用者的生命财产安全,摩擦材料质量性能的好坏,直接影响这整车、整机的使用效果,虽然在主机中所占成本较小,但功能和地位十分显赫。
(二)摩擦材料行业现状A—国外摩擦材料行业现状1897年,在英国,一个名叫Aerber Frood的人创造行的发明了摩擦材料,并成立了FERODO公司,从此奠定了摩擦材料的发展基石。
100多年的发展,现状国外发达国家的刹车片行业已经发展到了一个全新的高度,无论是在制动刹车片的生产设备、技术及工艺上,还是在产品的质量个管理等方面均处于世界绝对领先地位,刹车片的生产已经精细化、完美化,甚至于艺术品化。
最重要的,同时也是中国摩擦材料行业基本上很难做到的一点:发达国家的刹车片生产企业和整车汽车生产商对刹车片的开发是同步的,从刹车片的选定到出样品,要经过噪声检测、台架试验、匹配试验以及冬、夏季路试等反复测试,直到其性能均达到要求并稳定后,才批量生产。
目前,从世界范围来看,摩擦材料行业早已经品牌化、规模化、标准化。
对于先进的生产刹车片的技术工艺而言,国外大致分为三块:北美(半金属配方);欧洲(少金属配方)日本(NA——无石棉有机物配方)。
国外行业规范,想进入其市场,刹车片生产企业的设备、技术、工艺、产品的质量都应匹配,同时通过其市场的质量认证标准。
B—中国摩擦材料行业现状据不完全统计,我国国内现有摩擦材料生产企业超过600多家(若包括无生产许可证或小作坊式的,估计有800多家以上),销售产值约180亿人民币,其中70%产品为汽车用摩擦材料占30%,国外需求的摩擦材料占70%,产值前50各生产企业中,国外、合资、独资占30家。
刹车片 工艺流程

刹车片工艺流程刹车片工艺流程刹车片是车辆刹车系统中关键的零部件之一,起着重要的制动作用。
下面将介绍刹车片的工艺流程。
一、原材料准备刹车片的原材料主要包括金属基材、摩擦材料和粘接剂。
金属基材通常选择高性能的钢材,具有较高的抗疲劳和耐磨损性能。
摩擦材料通常为有机或无机材料,如石墨、碳化硅和玻璃纤维等,具有良好的摩擦阻力和热稳定性能。
粘接剂主要用于将金属基材和摩擦材料黏合在一起。
二、金属基材加工首先,对金属基材进行切割和车削加工,以得到符合规格要求的刹车片基础形状。
然后通过冲压和冲孔等工艺,将金属基材加工成具有孔洞和凹槽的形状。
三、摩擦材料制备摩擦材料主要是由摩擦粉末和粘接剂混合制成。
首先,将摩擦粉末进行筛选和混合,并根据配方将粘接剂逐渐加入混合物中。
混合均匀后,使用混合研磨机对材料进行细磨,以提高其表面平整度和颗粒度一致性。
四、压制成型将混合物放入压片机中,通过一定的压力进行压制成型。
压制成型过程中,需要控制好压力和温度,使得材料能够均匀且稳定地填充到金属基材的孔洞和凹槽中,并形成具有一定厚度和密度的刹车片。
五、硬化处理压制成型后的刹车片需要经过硬化处理,以增加其强度和硬度。
常用的硬化处理方法有热处理和化学处理。
热处理通常采用高温烘烤、淬火等工艺,以改变刹车片内部的晶体结构;化学处理则是通过浸泡在化学溶液中,使刹车片表面形成一层具有耐磨性和耐腐蚀性的保护膜。
六、精加工和检验经过硬化处理后,刹车片需要进行精加工和检验。
精加工包括平面研磨和光整等工艺,以提高刹车片的平整度和表面质量。
检验主要包括外观检查、尺寸检测和性能测试等,以确保刹车片符合质量要求。
七、包装和出厂经过精加工和检验后,刹车片可以进行包装,并入库等待出厂。
包装可以采用塑料薄膜或纸箱等方式,以保证刹车片的安全运输和存储。
通过以上工艺流程,刹车片得以制造出符合质量要求的零部件,其制动性能和可靠性得到保证。
刹车片工艺的优化和改进对提高刹车性能和延长使用寿命具有重要意义。
刹车片摩擦材料

刹车片摩擦材料刹车片是汽车、摩托车等车辆上不可或缺的零部件,它直接关系到车辆的安全性能。
而刹车片的摩擦材料则是决定刹车性能的关键因素之一。
在选择刹车片时,对于摩擦材料的了解是非常重要的。
本文将对刹车片摩擦材料进行详细介绍,希望能够帮助大家更好地了解刹车系统的工作原理和选购刹车片的相关知识。
刹车片的摩擦材料通常包括有机材料、半金属材料和全金属材料三种类型。
有机材料是最常见的刹车片摩擦材料,它主要由树脂、纤维和填料组成,具有制动效果好、噪音小、对刹车盘磨损小的优点。
然而,有机材料的耐磨性和耐高温性相对较差,容易产生刹车片退化和失效的情况。
半金属材料是有机材料与金属粉末混合而成,具有制动性能稳定、耐磨性好的特点,适用于大多数的汽车和摩托车。
全金属材料则是由金属粉末和树脂混合而成,具有耐高温、耐磨损的特点,适用于高速、高负荷的车辆。
在实际选购刹车片时,需要根据车辆的使用环境和个人驾驶习惯来选择合适的摩擦材料。
如果是在城市中较为平缓的道路上行驶,有机材料的刹车片是一个不错的选择,它可以提供平稳的制动效果和低噪音的驾驶体验。
而对于经常在山区、高速公路上行驶的车辆来说,半金属或全金属材料的刹车片则更适合,它们能够提供更稳定的制动性能和更长的使用寿命。
除了摩擦材料的选择外,刹车片的使用和保养也是非常重要的。
在日常行驶中,要避免急刹车和长时间连续制动,这样可以减少刹车片的磨损和提高其使用寿命。
另外,定期检查刹车片的磨损程度,及时更换磨损严重的刹车片,可以有效地保障行车安全。
总之,刹车片的摩擦材料是影响刹车性能的关键因素之一,正确选择适合自己车辆和行驶环境的摩擦材料对于行车安全至关重要。
希望通过本文的介绍,能够帮助大家更好地了解刹车片摩擦材料的相关知识,为正确选购和使用刹车片提供参考。
刹车片专业术语总结
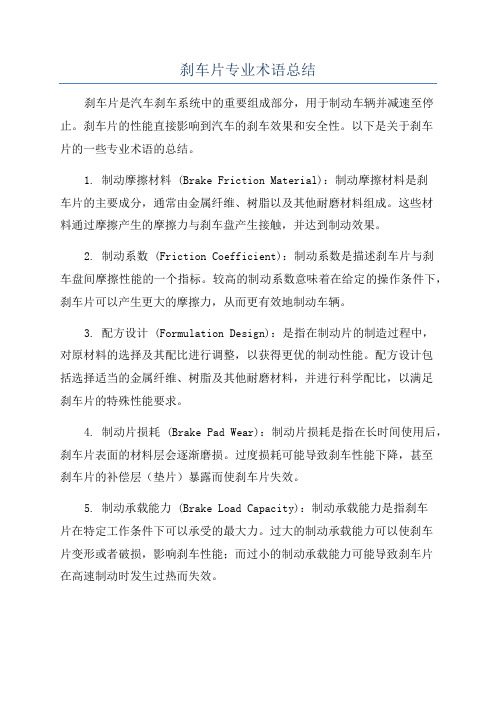
刹车片专业术语总结刹车片是汽车刹车系统中的重要组成部分,用于制动车辆并减速至停止。
刹车片的性能直接影响到汽车的刹车效果和安全性。
以下是关于刹车片的一些专业术语的总结。
1. 制动摩擦材料 (Brake Friction Material):制动摩擦材料是刹车片的主要成分,通常由金属纤维、树脂以及其他耐磨材料组成。
这些材料通过摩擦产生的摩擦力与刹车盘产生接触,并达到制动效果。
2. 制动系数 (Friction Coefficient):制动系数是描述刹车片与刹车盘间摩擦性能的一个指标。
较高的制动系数意味着在给定的操作条件下,刹车片可以产生更大的摩擦力,从而更有效地制动车辆。
3. 配方设计 (Formulation Design):是指在制动片的制造过程中,对原材料的选择及其配比进行调整,以获得更优的制动性能。
配方设计包括选择适当的金属纤维、树脂及其他耐磨材料,并进行科学配比,以满足刹车片的特殊性能要求。
4. 制动片损耗 (Brake Pad Wear):制动片损耗是指在长时间使用后,刹车片表面的材料层会逐渐磨损。
过度损耗可能导致刹车性能下降,甚至刹车片的补偿层(垫片)暴露而使刹车片失效。
5. 制动承载能力 (Brake Load Capacity):制动承载能力是指刹车片在特定工作条件下可以承受的最大力。
过大的制动承载能力可以使刹车片变形或者破损,影响刹车性能;而过小的制动承载能力可能导致刹车片在高速制动时发生过热而失效。
6. 温度衰退 (Thermal Fade):温度衰退是指刹车片在高温状态下的制动性能下降。
高温会使刹车片中的树脂软化,使制动系数下降,从而降低了制动效果。
7. 刹车失灵 (Brake Failure):刹车失灵是指刹车系统在急刹车时无法产生足够的制动力,或者刹车力的响应时间过长。
刹车失灵可能是由于刹车片磨损、刹车盘变形、制动液泄漏等原因导致。
8. 刹车片去除率 (Pad Removal Rate):刹车片去除率是指刹车片在使用过程中磨损的速度,通常以毫米每千公里(mm/km)为单位。
刹车片生产流程

刹车片生产流程刹车片是汽车制动系统中重要的零部件之一,其主要功能是通过摩擦力减速并停止车辆。
下面我将介绍一下刹车片的生产流程。
刹车片的生产流程可以分为以下几个步骤:1. 原材料准备:首先需要准备刹车片的原材料,主要包括钢板、摩擦材料和胶合剂。
钢板是刹车片的骨架材料,而摩擦材料是刹车片与刹车盘接触时起到摩擦作用的部分。
胶合剂则用于将钢板与摩擦材料粘合在一起。
2. 材料切割:在刹车片生产过程中,首先需要将原材料进行切割。
先将钢板按照要求的规格和形状进行切割,保证其能够适应不同车辆的制动系统。
同时,摩擦材料也需要根据需要进行切割,确保其与钢板能够完全贴合。
3. 表面处理:在切割好的钢板上进行表面处理,以增加摩擦材料与钢板之间的粘合力。
常用的表面处理方法包括喷砂和酸洗,这些处理能够去除钢板表面的油污和氧化物,提供一个干净的表面给胶合剂粘合。
4. 胶合:在表面处理完成后,将胶合剂均匀地涂抹在摩擦材料和钢板的接触面上。
涂抹好胶合剂后,将两者进行叠放并施加一定的压力,使其紧密的粘合在一起。
这个过程通常是通过压机或热压机完成的,以确保胶合的均匀和牢固。
5. 切割整形:在刹车片完成胶合后,需要对其进行切割和整形。
切割的目的是将刹车片切割成符合要求的尺寸和形状,整形则是将切割好的刹车片进行修整和打磨,以提高其外观和质量。
6. 耐磨及附加处理:经过切割整形后的刹车片需要进行耐磨处理,以提高其摩擦性能和使用寿命。
同时,根据需要还可以对刹车片进行其他的附加处理,如防锈处理、降噪处理等,以提高刹车系统的整体性能。
7. 检测和质检:刹车片的生产过程中,每一道工序都需要经过严格的检测和质检。
常用的检测手段包括外观检查、尺寸检测和摩擦性能测试等,以确保每一片刹车片的质量符合标准和要求。
8. 包装和出厂:在刹车片生产完成后,需要进行包装和标识。
刹车片通常是以一片一片进行包装,并在包装上标注相关的信息,如刹车片型号、批次、生产日期等。
摩擦材料配方

摩擦材料配方
摩擦材料的配方因其用途和应用领域而有所不同。
以下是一些常见的摩擦材料配方:
1. 刹车片配方:
- 金属粉末(如铜、钢):提供摩擦性能和热传导性能。
- 碳纤维:增加摩擦系数和耐磨性。
- 树脂基体:提供强度和稳定性。
- 石墨或其他固体润滑剂:减少摩擦热和磨损。
- 硬化剂和填充剂:调整刹车片的硬度和摩擦性能。
2. 高温摩擦材料配方(用于摩擦离合器等高温环境):
- 陶瓷纤维:提供高温稳定性和耐磨性。
- 碳纤维:增加摩擦系数和耐磨性。
- 金属粉末(如铜、钢):提供高温摩擦性能和热传导性能。
- 有机或无机粘结剂:将材料粘结在一起,并提供强度。
- 硬化剂和填充剂:调整材料的硬度和摩擦性能。
3. 摩擦润滑材料配方(用于轴承等摩擦部件):
- 固体润滑剂(如石墨、二硫化钼):减少摩擦系数和磨损。
- 金属粉末(如铜、铝):提供摩擦性能和热传导性能。
- 基体材料(如聚合物或金属):提供强度和稳定性。
- 抗氧化剂和防腐剂:增加材料的耐久性和稳定性。
注意的是,不同的应用领域和特定要求可能需要不同的配方组合。
此外,具体的摩擦材料配方还受到专利保护,因此详细的配方可能无
法完全公开。
对于特定的摩擦材料需求,建议咨询专业的材料制造商或相关领域的专家以获取更准确的信息和建议。
刹车片组成结构

刹车片组成结构
刹车片是汽车刹车系统中非常重要的零部件之一,其组成结构较
为复杂。
以下将从多个步骤阐述刹车片的组成结构。
1. 基材层:刹车片基材主要是钢板或铸铁材质,可提供刹车片
机械强度。
基材层通常会在制造过程中先进行加工和打磨。
2. 摩擦材料层:刹车片的摩擦材料层是使用最为广泛的制动材
料层。
这一层主要由摩擦粉末、树脂、纤维和其他一些添加剂组成。
其中,摩擦粉末可以是金属粉末、碳化硅粉末和润滑剂等。
在摩擦制
动时,摩擦材料层将摩擦热量转移给刹车片基材。
这一层的厚度通常
在几毫米到十几毫米之间。
3. 胶合层:刹车片的胶合层主要起到粘合摩擦材料层和基材层
的作用。
该层通常使用有机胶水或无机硬化物胶水制成。
胶合层的良
好粘合质量对于提高刹车片的可靠性非常重要。
4. 钢片层:钢片层通常用于调整刹车片的整体硬度和厚度。
在
摩擦制动时,钢片层可以减少摩擦材料层和胶合层的变形。
5. 防噪层:防噪层也称为衬板层,主要用于减少刹车系统噪音
的产生。
该层通常使用铆钉固定于摩擦材料层上,并可以起到维护刹
车片美观、保护刹车盘的作用。
综上所述,刹车片的组成结构很复杂,由多个层组成。
这些层包
括基材层、摩擦材料层、胶合层、钢片层和防噪层。
一些实用的特殊
材料和技术通常也用于提高刹车体系的性能和制动效果。
在此提醒您,定期检查和更换车辆刹车系统的零部件,是保证驾驶安全的重要措施
之一。
刹车摩擦材料

刹车摩擦材料刹车摩擦材料是指用于制动系统的摩擦材料,它直接影响着汽车的刹车性能和安全性。
目前,常见的刹车摩擦材料主要包括有机材料、无机材料和半金属材料。
在选择刹车摩擦材料时,需要考虑摩擦性能、耐磨性能、热稳定性、环保性以及成本等因素。
有机材料是指以有机高分子材料为基础的刹车摩擦材料,主要包括有机树脂、纤维和填料等。
有机材料具有摩擦性能好、制动时噪音小、对刹车盘磨损小等优点,但耐热性和耐磨性相对较差。
因此,有机材料通常用于小型车辆和低速车辆的制动系统中。
无机材料是指以无机非金属材料为主要成分的刹车摩擦材料,主要包括氧化物、硼化物、碳化物等。
无机材料具有耐热性和耐磨性好的特点,适用于高速、高负荷的制动系统,如卡车、赛车等。
半金属材料是指以金属粉末为基础,添加少量有机树脂和无机材料的刹车摩擦材料。
半金属材料综合了有机材料和无机材料的优点,具有良好的摩擦性能、耐磨性能和耐热性能,适用于大多数中高档车辆的制动系统。
除了以上几种常见的刹车摩擦材料外,还有一些新型材料在研发和应用中,如陶瓷复合材料、碳纤维复合材料等。
这些新型材料具有高温稳定性好、耐磨性能好、重量轻等优点,但成本较高。
在选择刹车摩擦材料时,需要根据车辆类型、使用环境、制动性能要求等因素进行综合考虑。
同时,还需要注意刹车摩擦材料的更换周期,及时更换磨损严重的刹车摩擦材料,以确保车辆的刹车性能和安全性。
总的来说,刹车摩擦材料是制动系统中至关重要的一部分,选择合适的刹车摩擦材料对于车辆的刹车性能和安全性具有重要影响。
随着科技的发展和材料的不断创新,相信未来会有更多更优秀的刹车摩擦材料出现,为汽车制动系统的性能提升提供更多可能。
摩擦材料的用途
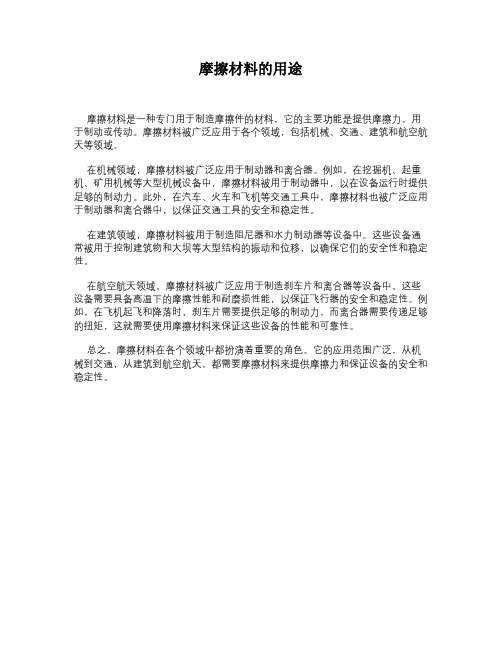
摩擦材料的用途
摩擦材料是一种专门用于制造摩擦件的材料,它的主要功能是提供摩擦力,用于制动或传动。
摩擦材料被广泛应用于各个领域,包括机械、交通、建筑和航空航天等领域。
在机械领域,摩擦材料被广泛应用于制动器和离合器。
例如,在挖掘机、起重机、矿用机械等大型机械设备中,摩擦材料被用于制动器中,以在设备运行时提供足够的制动力。
此外,在汽车、火车和飞机等交通工具中,摩擦材料也被广泛应用于制动器和离合器中,以保证交通工具的安全和稳定性。
在建筑领域,摩擦材料被用于制造阻尼器和水力制动器等设备中。
这些设备通常被用于控制建筑物和大坝等大型结构的振动和位移,以确保它们的安全性和稳定性。
在航空航天领域,摩擦材料被广泛应用于制造刹车片和离合器等设备中。
这些设备需要具备高温下的摩擦性能和耐磨损性能,以保证飞行器的安全和稳定性。
例如,在飞机起飞和降落时,刹车片需要提供足够的制动力,而离合器需要传递足够的扭矩,这就需要使用摩擦材料来保证这些设备的性能和可靠性。
总之,摩擦材料在各个领域中都扮演着重要的角色。
它的应用范围广泛,从机械到交通,从建筑到航空航天,都需要摩擦材料来提供摩擦力和保证设备的安全和稳定性。
解析汽车刹车片中的陶瓷基摩擦材料
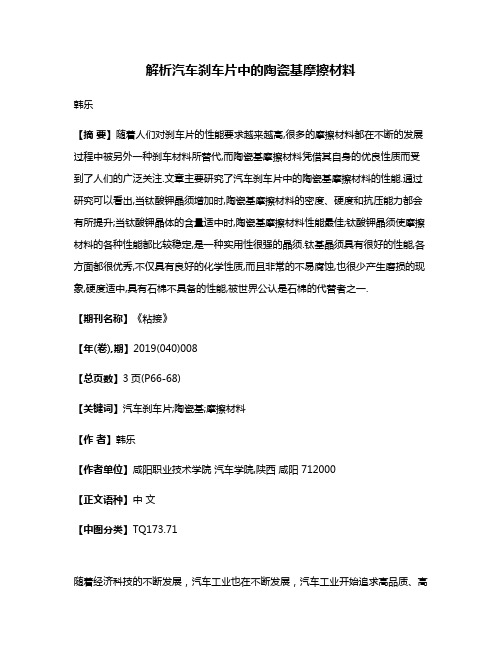
解析汽车刹车片中的陶瓷基摩擦材料韩乐【摘要】随着人们对刹车片的性能要求越来越高,很多的摩擦材料都在不断的发展过程中被另外一种刹车材料所替代,而陶瓷基摩擦材料凭借其自身的优良性质而受到了人们的广泛关注.文章主要研究了汽车刹车片中的陶瓷基摩擦材料的性能.通过研究可以看出,当钛酸钾晶须增加时,陶瓷基摩擦材料的密度、硬度和抗压能力都会有所提升;当钛酸钾晶体的含量适中时,陶瓷基摩擦材料性能最佳;钛酸钾晶须使摩擦材料的各种性能都比较稳定,是一种实用性很强的晶须.钛基晶须具有很好的性能,各方面都很优秀,不仅具有良好的化学性质,而且非常的不易腐蚀,也很少产生磨损的现象,硬度适中,具有石棉不具备的性能,被世界公认是石棉的代替者之一.【期刊名称】《粘接》【年(卷),期】2019(040)008【总页数】3页(P66-68)【关键词】汽车刹车片;陶瓷基;摩擦材料【作者】韩乐【作者单位】咸阳职业技术学院汽车学院,陕西咸阳 712000【正文语种】中文【中图分类】TQ173.71随着经济科技的不断发展,汽车工业也在不断发展,汽车工业开始追求高品质、高质量的汽车,也对汽车的制动系统和速度要求更高。
摩擦材料的选择影响到汽车的安全性能,速度、驾驶人员的安全等,是汽车制动系统中的一项非常重要的组分。
在汽车制造过程中,要选择性能好、较稳定、磨损率较低、摩擦系数高、使用时间较长的摩擦材料。
摩擦材料包括增强材料、基体材料、摩擦改性剂等,其中最重要的就是增强材料,这种材料不仅影响着汽车的性能,而且对于摩擦片的性能也有重要的影响。
石棉本来是一种各方面很优秀的材料,但是石棉对人体健康伤害很大,石棉中含有大量致癌物,长期使用会对人体和环境造成很大伤害。
之后,国外专门研究了石棉的性能,并取得了很大成就。
1 摩擦材料试样的准备增强材料、粘合材料等其他填充材料共同组成了汽车刹车片中的陶瓷基摩擦材料。
其中粘合材料起重要作用,粘合剂的作用就是将各种材料、纤维均匀的粘合在一起,之后经过加热、加压等一系列加工,形成结构细密,性能较好的陶瓷基摩擦材料。
刹车片配料工艺流程

刹车片配料工艺流程一、原料准备。
咱先说这原料啊,那可都是有讲究的。
就像做菜得先准备食材一样,做刹车片得把各种原料都找齐喽。
有石棉纤维,这就像盖房子的钢筋一样,给刹车片提供一定的强度呢。
还有树脂,它就像是胶水,能把其他的原料都黏合在一起,让整个刹车片团结起来,不至于散架。
另外,像铜丝啊,这也是很重要的成分,它能增强刹车片的导热性能,让刹车的时候产生的热量能更快地散出去。
这原料啊,得保证质量好,要是质量不行,那做出来的刹车片可就没法用喽。
二、称重配比。
原料准备好之后呢,就到了称重配比这个环节啦。
这就好比咱们做饭得按照食谱上的比例放调料一样,做刹车片每个原料放多少那都是有严格要求的。
比如说石棉纤维放多少克,树脂又得放多少克,这可不能乱了套。
工人师傅们就得像特别细心的大厨一样,精确地称出每一种原料的重量。
要是哪一种原料放多了或者放少了,那这刹车片的性能可就会受到影响。
就像做菜盐放多了咸得没法吃,盐放少了没味一样,刹车片的配比不对,可能就刹不住车或者磨损得特别快,那可就危险啦。
三、混合搅拌。
称好重量的原料呢,就一股脑地都被放进一个大搅拌机里啦。
这个搅拌机就像一个超级大的搅拌碗,开始疯狂地搅拌这些原料。
在搅拌的时候啊,这些原料就开始充分地混合在一起,树脂就开始发挥它黏合的作用啦。
就像我们搅面糊一样,要搅得均匀,不能有疙瘩。
在这个过程中呢,搅拌机轰隆隆地响着,原料们就在里面欢快地翻滚着,混合着。
这一搅拌啊,得保证每个角落都搅拌到,这样才能让原料们完美地融合在一起,就像一个团结的大家庭一样。
四、成型加工。
混合好的原料接下来就到了成型加工这一步。
这时候就像是把揉好的面团做成馒头的形状一样。
原料会被放进特定的模具里,然后通过压力机给它施加一定的压力,让它变成刹车片的形状。
这个压力得刚刚好,压力小了,刹车片的密度不够,强度就不行;压力大了呢,又可能会把原料压坏了。
在这个过程中,工人师傅们得时刻盯着,就像照顾自己的小宝贝一样,小心翼翼地确保每一个刹车片都能成型得完美无缺。
刹车片制作工艺

刹车片制作工艺刹车片是汽车制动系统中的重要组成部分,其制作工艺直接影响着车辆的制动性能和安全性。
本文将介绍刹车片的制作工艺,包括原材料的选择、制作流程和质量控制等方面。
一、原材料的选择刹车片的主要原材料是摩擦材料,常用的有有机材料、半金属材料和陶瓷材料等。
有机材料是指使用有机纤维和树脂作为基体,添加摩擦剂和填料制成的刹车片。
半金属材料是指在有机材料基础上添加金属颗粒,提高刹车片的热导性和耐磨性。
陶瓷材料是指使用陶瓷纤维和陶瓷颗粒作为基体,具有优异的高温性能和耐磨性。
二、制作流程1. 原材料准备:根据刹车片的要求选择合适的摩擦材料,并进行粉碎、筛分等处理,确保材料的均匀性和粒度合适。
2. 配方调配:根据刹车片的性能要求,确定合适的配方比例,将摩擦材料、粘结剂和填料等按一定比例混合搅拌。
3. 压制成型:将调配好的混合料放入刹车片模具中,经过高压压制成型,使其具有一定的形状和密度。
4. 烘干处理:将成型后的刹车片放入烘干室中进行烘干处理,去除水分,提高刹车片的强度和稳定性。
5. 研磨加工:对烘干后的刹车片进行研磨加工,使其表面光滑平整,提高摩擦效果和制动性能。
6. 表面处理:根据需要,对刹车片进行表面处理,如喷涂防锈漆、涂覆摩擦剂等,增加使用寿命和稳定性。
7. 质量检测:对制作好的刹车片进行严格的质量检测,包括外观检查、尺寸测量、摩擦性能测试等,确保产品符合标准要求。
8. 包装存储:将合格的刹车片进行包装,标明产品型号、规格和生产日期等信息,进行存储和销售。
三、质量控制刹车片作为汽车制动系统的重要组成部分,其质量直接关系到行车安全。
因此,在刹车片的制作过程中,需要严格控制质量,确保产品的性能稳定和可靠性。
主要包括以下几个方面:1. 原材料的选择要合理,确保摩擦材料的品质和稳定性。
2. 制作工艺要规范,严格按照流程进行操作,确保每个环节的质量。
3. 质量检测要全面,对刹车片的外观、尺寸、摩擦性能等进行严格检测,确保产品符合标准要求。
刹车片制作工艺流程

刹车片制作工艺流程一、原材料准备。
做刹车片得先把原材料找齐咯。
这里面有好多东西呢,像摩擦材料就是超级重要的一部分。
这摩擦材料啊,一般是由一些纤维呀,树脂之类的组成。
纤维就像是刹车片的小骨架,让它有一定的强度。
有石棉纤维,不过现在因为石棉对健康不太好,很多都改用陶瓷纤维之类的啦。
还有树脂呢,就像是胶水一样,把各种材料黏合在一起。
另外,还得有一些填充料,像铁粉之类的,这些填充料能让刹车片的性能更好哦。
二、混合材料。
把这些原材料都准备好了之后,就开始混合它们啦。
这就像是在做一个超级特别的大杂烩。
要把那些纤维、树脂、填充料按照一定的比例放在一起搅拌。
这个比例可是很有讲究的呢,如果哪个材料放多了或者放少了,那做出来的刹车片可能就不好用啦。
搅拌的时候,就看着那些不同的材料在机器里欢快地打转,逐渐变成了一种均匀的混合物,就像一群小伙伴手拉手,团结在一起啦。
三、成型。
混合好的材料就可以开始成型啦。
这个过程有点像捏泥巴,不过是用专门的模具来捏。
把混合好的材料放到模具里,然后用很大的压力把它压成刹车片的形状。
这个压力得刚刚好,压力小了,刹车片可能就不够紧实,容易坏掉。
压力大了呢,又可能会让刹车片有一些小问题。
在这个过程中,要特别小心,就像照顾一个小宝贝一样,因为这个形状一旦定下来,可就很难改啦。
四、热处理。
成型后的刹车片还得经过热处理呢。
这就像是给刹车片做一个SPA。
把刹车片放到专门的炉子里,给它加热到一定的温度,然后再让它慢慢冷却。
这个热处理的过程能让刹车片的内部结构变得更稳定,性能也会更好。
就好像是经过锻炼之后,身体变得更强壮了一样。
五、加工与打磨。
热处理完了之后,刹车片还得进行加工和打磨。
要把它的边缘处理得光滑圆润,就像给它修修边幅一样。
打磨也是很重要的一步呢,要把刹车片的表面打磨得平整光滑,这样在使用的时候,它才能和刹车盘更好地贴合。
这就像是给刹车片穿上了一件精致的衣服,让它能够在刹车系统里优雅地工作。
六、质量检测。
制动器摩擦片材料介绍
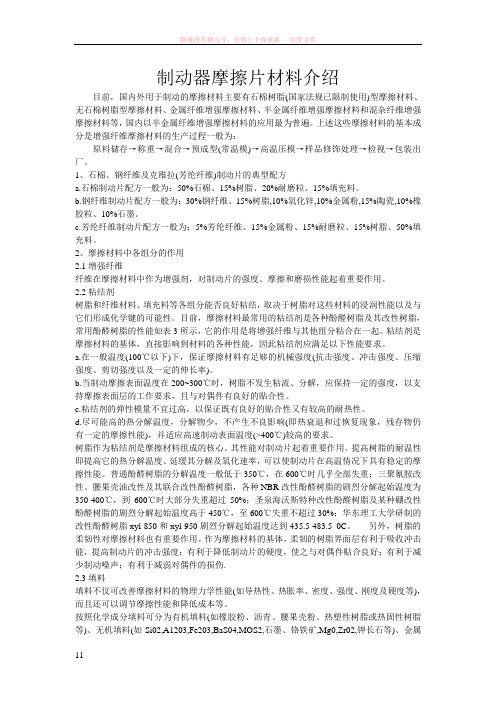
制动器摩擦片材料介绍目前,国内外用于制动的摩擦材料主要有石棉树脂(国家法规已限制使用)型摩擦材料、无石棉树脂型摩擦材料、金属纤维增强摩擦材料、半金属纤维增强摩擦材料和混杂纤维增强摩擦材料等,国内以半金属纤维增强摩擦材料的应用最为普遍。
上述这些摩擦材料的基本成分是增强纤维摩擦材料的生产过程一般为:原料储存→称重→混合→预成型(常温模)→高温压模→样品修饰处理→检视→包装出厂。
1、石棉、钢纤维及克维拉(芳纶纤维)制动片的典型配方a.石棉制动片配方一般为:50%石棉、15%树脂、20%耐磨粒、15%填充料。
b.钢纤维制动片配方一般为:30%钢纤维、15%树脂,10%氧化锌,10%金属粉,15%陶瓷,10%橡胶粒、10%石墨。
c.芳纶纤维制动片配方一般为:5%芳纶纤维、15%金属粉、15%耐磨粒、15%树脂、50%填充料。
2、摩擦材料中各组分的作用2.1增强纤维纤维在摩擦材料中作为增强剂,对制动片的强度、摩擦和磨损性能起着重要作用。
2.2粘结剂树脂和纤维材料、填充料等各组分能否良好粘结,取决于树脂对这些材料的浸润性能以及与它们形成化学键的可能性。
目前,摩擦材料最常用的粘结剂是各种酚醛树脂及其改性树脂,常用酚醛树脂的性能如表3所示,它的作用是将增强纤维与其他组分粘合在一起。
粘结剂是摩擦材料的基体,直接影响到材料的各种性能,因此粘结剂应满足以下性能要求。
a.在一般温度(100℃以下)下,保证摩擦材料有足够的机械强度(抗击强度、冲击强度、压缩强度、剪切强度以及一定的伸长率)。
b.当制动摩擦表面温度在200~300℃时,树脂不发生粘流、分解,应保持一定的强度,以支持摩擦表面层的工作要求,且与对偶件有良好的贴合性。
c.粘结剂的弹性模量不宜过高,以保证既有良好的贴合性又有较高的耐热性。
d.尽可能高的热分解温度,分解物少,不产生不良影响(即热衰退和过恢复现象,残存物仍有一定的摩擦性能),并适应高速制动表面温度(>400℃)较高的要求。
刹车片原材料和制作工艺
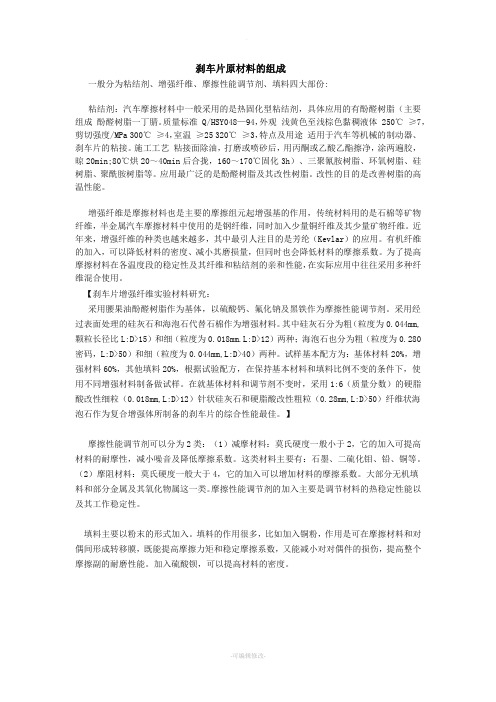
刹车片原材料的组成一般分为粘结剂、增强纤维、摩擦性能调节剂、填料四大部份:粘结剂:汽车摩擦材料中一般采用的是热固化型粘结剂,具体应用的有酚醛树脂(主要组成酚醛树脂一丁腈。
质量标准Q/HSY048—94,外观浅黄色至浅棕色黏稠液体250℃≥7,剪切强度/MPa 300℃≥4,室温≥25 320℃≥3,特点及用途适用于汽车等机械的制动器、刹车片的粘接。
施工工艺粘接面除油,打磨或喷砂后,用丙酮或乙酸乙酯擦净,涂两遍胶,晾20min;80℃烘20~40min后合拢,160~170℃固化3h)、三聚氰胺树脂、环氧树脂、硅树脂、聚酰胺树脂等。
应用最广泛的是酚醛树脂及其改性树脂。
改性的目的是改善树脂的高温性能。
增强纤维是摩擦材料也是主要的摩擦组元起增强基的作用,传统材料用的是石棉等矿物纤维,半金属汽车摩擦材料中使用的是钢纤维,同时加入少量铜纤维及其少量矿物纤维。
近年来,增强纤维的种类也越来越多,其中最引人注目的是芳纶(Kevlar)的应用。
有机纤维的加入,可以降低材料的密度、减小其磨损量,但同时也会降低材料的摩擦系数。
为了提高摩擦材料在各温度段的稳定性及其纤维和粘结剂的亲和性能,在实际应用中往往采用多种纤维混合使用。
【刹车片增强纤维实验材料研究:采用腰果油酚醛树脂作为基体,以硫酸钙、氟化钠及黑铁作为摩擦性能调节剂。
采用经过表面处理的硅灰石和海泡石代替石棉作为增强材料。
其中硅灰石分为粗(粒度为0.044mm,颗粒长径比L:D>15)和细(粒度为0.018mm.L:D>12)两种;海泡石也分为粗(粒度为0.280密码,L:D>50)和细(粒度为0.044mm,L:D>40)两种。
试样基本配方为:基体材料20%,增强材料60%,其他填料20%,根据试验配方,在保持基本材料和填料比例不变的条件下,使用不同增强材料制备做试样。
在就基体材料和调节剂不变时,采用1:6(质量分数)的硬脂酸改性细粒(0.018mm,L:D>12)针状硅灰石和硬脂酸改性粗粒(0.28mm,L:D>50)纤维状海泡石作为复合增强体所制备的刹车片的综合性能最佳。
摩擦片芯块
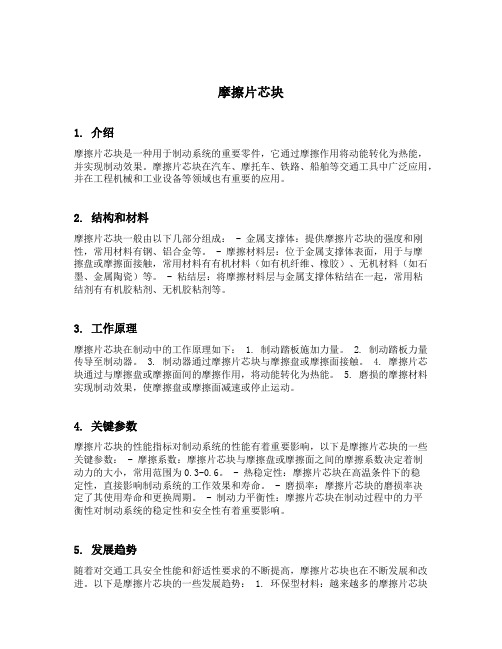
摩擦片芯块1. 介绍摩擦片芯块是一种用于制动系统的重要零件,它通过摩擦作用将动能转化为热能,并实现制动效果。
摩擦片芯块在汽车、摩托车、铁路、船舶等交通工具中广泛应用,并在工程机械和工业设备等领域也有重要的应用。
2. 结构和材料摩擦片芯块一般由以下几部分组成: - 金属支撑体:提供摩擦片芯块的强度和刚性,常用材料有钢、铝合金等。
- 摩擦材料层:位于金属支撑体表面,用于与摩擦盘或摩擦面接触,常用材料有有机材料(如有机纤维、橡胶)、无机材料(如石墨、金属陶瓷)等。
- 粘结层:将摩擦材料层与金属支撑体粘结在一起,常用粘结剂有有机胶粘剂、无机胶粘剂等。
3. 工作原理摩擦片芯块在制动中的工作原理如下: 1. 制动踏板施加力量。
2. 制动踏板力量传导至制动器。
3. 制动器通过摩擦片芯块与摩擦盘或摩擦面接触。
4. 摩擦片芯块通过与摩擦盘或摩擦面间的摩擦作用,将动能转化为热能。
5. 磨损的摩擦材料实现制动效果,使摩擦盘或摩擦面减速或停止运动。
4. 关键参数摩擦片芯块的性能指标对制动系统的性能有着重要影响,以下是摩擦片芯块的一些关键参数: - 摩擦系数:摩擦片芯块与摩擦盘或摩擦面之间的摩擦系数决定着制动力的大小,常用范围为0.3-0.6。
- 热稳定性:摩擦片芯块在高温条件下的稳定性,直接影响制动系统的工作效果和寿命。
- 磨损率:摩擦片芯块的磨损率决定了其使用寿命和更换周期。
- 制动力平衡性:摩擦片芯块在制动过程中的力平衡性对制动系统的稳定性和安全性有着重要影响。
5. 发展趋势随着对交通工具安全性能和舒适性要求的不断提高,摩擦片芯块也在不断发展和改进。
以下是摩擦片芯块的一些发展趋势: 1. 环保型材料:越来越多的摩擦片芯块采用环保型有机材料,减少对环境的污染。
2. 高温稳定性:提高摩擦片芯块在高温条件下的稳定性,以满足更高要求的制动性能。
3. 低磨损率:减少摩擦片芯块的磨损,延长使用寿命,减少更换频率。
- 1、下载文档前请自行甄别文档内容的完整性,平台不提供额外的编辑、内容补充、找答案等附加服务。
- 2、"仅部分预览"的文档,不可在线预览部分如存在完整性等问题,可反馈申请退款(可完整预览的文档不适用该条件!)。
- 3、如文档侵犯您的权益,请联系客服反馈,我们会尽快为您处理(人工客服工作时间:9:00-18:30)。
摩擦材料(刹车片)中原材料的用法?;摩擦材料;一、概论;摩擦材料是一种应用在动力机械上,依靠摩擦作用来执;(刹车片)和离合器面片(离合器片);它最主要的功能是通过摩擦来吸收或传递动力;机动车辆能够安全可靠地工作;摩擦性能调节剂三大类组成及其它配合剂构成,经一系;摩擦系数和耐磨损性能,同时具有一定的耐热性和机械;被广泛应用在汽车、火车、飞机、石油钻机等各类工程--------------------------------------------------------------------------------摩擦材料(刹车片)中原材料的用法摩擦材料一、概论摩擦材料是一种应用在动力机械上,依靠摩擦作用来执行制动和传动功能的部件材料。
它主要包括制动器衬片(刹车片)和离合器面片(离合器片)。
刹车片用于制动,离合器片用于传动。
任何机械设备与运动的各种车辆都必须要有制动或传动装置。
摩擦材料是这种制动或传动装置上的关键性部件。
它最主要的功能是通过摩擦来吸收或传递动力。
如离合器片传递动力,制动片吸收动能。
它们使机械设备与各种机动车辆能够安全可靠地工作。
所以说摩擦材料是一种应用广泛又甚关键地材料。
摩擦材料是一种高分子三元复合材料,是物理与化学复合体。
它是由高分子粘结剂(树脂与橡胶)、增强纤维和摩擦性能调节剂三大类组成及其它配合剂构成,经一系列生产加工而制成的制品。
摩擦材料的特点是具有良好的摩擦系数和耐磨损性能,同时具有一定的耐热性和机械强度,能满足车辆或机械的传动与制动的性能要求。
它们被广泛应用在汽车、火车、飞机、石油钻机等各类工程机械设备上。
民用品如自行车、洗衣机等作为动力的传递或制动减速用不可缺少的材料。
二、摩擦材料发展简史自世界上出现动力机械和机动车辆后,在其传动和制动机构中就使用摩擦片。
初期的摩擦片系用棉花、棉布、皮革等作为基材,如:将棉花纤维或其织品浸渍橡胶浆液后,进行加工成型制成刹车片或刹车带。
其缺点:耐热性较差,当摩擦面温度超过120℃后,棉花和棉布会逐渐焦化甚至燃烧。
随着车辆速度和载重的增加,其制动温度也相应提高,这类摩擦材料已经不能满足使用要求。
人们开始寻求耐热性好的、新的摩擦材料类型,石棉摩擦材料由此诞生。
石棉是一种天然的矿物纤维,它具有较高的耐热性和机械强度,还具有较长的纤维长度、很好的散热性,柔软性和浸渍性也很好,可以进行纺织加工制成石棉布或石棉带并浸渍粘结剂。
石棉短纤维和其布、带织品都可以作为摩擦材料的基材。
更由于其具有较低的价格(性价比),所以很快就取代了棉花与棉布而成为摩擦材料中的主要基材料。
1905年石棉刹车带开始被应用,其制品的摩擦性能和使用寿命、耐热性和机械强度均有较大的提高。
1918年开始,人们用石棉短纤维与沥青混合制成模压刹车片。
20世纪20年代初酚醛树脂开始工业化应用,由于其耐热性明显高于橡胶,所以很快就取代了橡胶,而成为摩擦材料中主要的粘结剂材料。
由于酚醛树脂与其他的各种耐热型的合成树脂相比价格较低,故从那时起,石棉-酚醛型摩擦材料被世界各国广泛使用至今。
20世纪60年代,人们逐渐认识到石棉对人体健康有一定的危险性。
在开采或生产过程中,微细的石棉纤维易飞扬在空气中被人吸入肺部,长期间处于这种环境下的人们比较容易患上石棉肺一类的疾病。
因此人们开始寻求能取代石棉的其它纤维材料来制造摩擦材料,即无石棉摩擦材料或非石棉摩擦材料。
20世纪70年代,以钢纤维为主要代替材料的半金属材料在国外被首先采用。
80年代-90年代初,半金属摩擦材料已占据了整个汽车用盘式片领域。
20世纪90年代后期以来,NAO(少金属)摩擦材料在欧洲的出现是一个发展的趋势。
无石棉,采用两种或两种以上纤维(以无机纤维为主,并有少量有机纤维)只含少量钢纤维、铁粉。
NAO(少金属)型摩擦材料有助于克服半金属型摩擦材料固有的高比重、易生锈、易产生制动噪音、伤对偶(盘、鼓)及导热系数过大等缺陷。
目前,NAO(少金属)型摩擦材料已得到广泛应用,取代半金属型摩擦材料。
2004年开始,随汽车工业飞速发展,人们对制动性能要求越来越高,开始研发陶瓷型摩擦材料。
陶瓷型摩擦材料主要以无机纤维和几种有机纤维混杂组成,无石棉,无金属。
其特点为:1. 无石棉符合环保要求;2. 无金属和多孔性材料的使用可降低制品密度,有利于减少损伤制动盘(鼓)和产生制动噪音的粘度。
3. 摩擦材料不生锈,不腐蚀;4. 磨耗低,粉尘少(轮毂)。
三、摩擦材料分类在大多数情况下,摩擦材料都是同各种金属对偶起摩擦的。
一般公认,在干摩擦条件下,同对偶摩擦系数大于0.2的材料,称为摩擦材料。
材料按其摩擦特性分为低摩擦系数材料和高摩擦系数材料。
低摩擦系数材料又称减摩材料或润滑材料,其作用是减少机械运动中的动力损耗,降低机械部件磨损,延长使用寿命。
高摩擦系数材料又称摩阻材料(称为摩擦材料)。
1.按工作功能分可分为传动与制动两大类摩擦材料。
如传动作用的离合器片,系通过离合器总成中离合器摩擦面片的贴合与分离将发动机产生的动力传递到驱动轮上,使车辆开始行走。
制动作用的刹车片(分为盘式与鼓式刹车片),系通过车辆制动机构将刹车片紧贴在制动盘(鼓)上,使行走中的车辆减速或停下来。
2.按产品形状分可分为刹车片(盘式片、鼓式片)、刹车带、闸瓦、离合器片、异性摩擦片。
盘式片呈平面状,鼓式片呈弧形。
闸瓦(火车闸瓦、石油钻机)为弧形产品,但比普通弧形刹车片要厚的多,25~30mm范围。
刹车带常用于农机和工程机械上,属软质摩擦材料。
离合器片一般为圆环形状制品。
异性摩擦片多用于各种工程机械方面,如摩擦压力机,电葫芦等。
3.按产品材质分可分为石棉摩擦材料、无石棉摩擦材料两大类。
A、石棉摩擦材料分为以下几类:a、石棉纤维摩擦材料,又称为石棉绒质摩擦材料。
生产:各种刹车片、离合器片、火车合成闸瓦、石棉绒质橡胶带等。
b、石棉线质摩擦材料。
生产:缠绕型离合器片、短切石棉线段摩擦材料等。
c、石棉布质摩擦材料。
生产:制造层压类钻机闸瓦、刹车带、离合器面片等。
d、石棉编织摩擦材料。
生产:制造油浸或树脂浸刹车带。
石油钻机闸瓦等。
B、无石棉摩擦材料分为以下几类:a、半金属摩擦材料。
应用于轿车和重型汽车的盘式刹车片。
其材质配方组成中通常含有30%~50%左右的铁质金属物(如钢纤维、还原铁粉、泡沫铁粉)。
半金属摩擦材料因此而得名。
是最早取代石棉而发展起来的一种无石棉材料。
其特点:耐热性好,单位面积吸收功率高,导热系数大,能适用于汽车在高速、重负荷运行时的制动工况要求。
但其存在制动噪音大、边角脆裂等缺点。
b、NAO摩擦材料。
从广义上是指非石棉-非钢纤维型摩擦材料,但现盘式片也含有少量的钢纤维。
NAO摩擦材料中的基材料在大多数情况下为两种或两种以上纤维(以无机纤维,并有少量有机纤维)混合物。
因此NAO摩擦材料是非石棉混合纤维摩擦材料。
通常刹车片为短切纤维型摩擦块,离合器片为连续纤维型摩擦片。
c、粉末冶金摩擦材料。
又称烧结摩擦材料,系将铁基、铜基粉状物料经混合、压型,并在在高温下烧结而成。
适用于较高温度下的制动与传动工况条件。
如:飞机、载重汽车、重型工程机械的制动与传动。
优点:使用寿命长;缺点:制品价格高,制动噪音大,重而脆性大,对偶磨损大。
d、碳纤维摩擦材料。
系用碳纤维为增强材料制成的一类摩擦材料。
碳纤维具有高模量、导热好、耐热等特点。
碳纤维摩擦材料是各种类型摩擦材料中性能最好的一种。
碳纤维摩擦片的单位面积吸收功率高及比重轻,特别适合生产飞机刹车片,国外有些高档轿车的刹车片也使用。
因其价格昂贵,故其应用范围受到限制,产量较少。
在碳纤维摩擦材料组分中,除了碳纤维外,还使用石墨,碳的化合物。
组分中的有机粘结剂也要经过碳化处理,故碳纤维摩擦材料也称为碳——碳摩擦材料或碳基摩擦材;四、摩擦材料的技术要求;摩擦材料是车辆与机械的离合器总成和制动器中的关键;要求:;1.适宜而稳定的摩擦系数;摩擦系数是评价任何一种摩擦材料的一个最重要的性能;一个常数,而是受温度、压力、摩擦速度或表面状态及;数应具有理想的冷摩擦系数和可以控制的温度衰退;擦系数发生变化;温度是影响摩擦系数的重要因素;数开始下降--------------------------------------------------------------------------------碳纤维摩擦材料也称为碳——碳摩擦材料或碳基摩擦材料。
四、摩擦材料的技术要求摩擦材料是车辆与机械的离合器总成和制动器中的关键安全零件,在传动和制动过程中,主要应满足以下技术要求:1.适宜而稳定的摩擦系数。
摩擦系数是评价任何一种摩擦材料的一个最重要的性能指标,关系着摩擦片执行传动和制动功能的好坏。
它不是一个常数,而是受温度、压力、摩擦速度或表面状态及周围介质因素等影响而发生变化的一个数。
理想的摩擦系数应具有理想的冷摩擦系数和可以控制的温度衰退。
由于摩擦产生热量,增高了工作温度,导致了摩擦材料的摩擦系数发生变化。
温度是影响摩擦系数的重要因素。
摩擦材料在摩擦过程中,由于温度的迅速升高,一般温度达200℃以上,摩擦系数开始下降。
当温度达到树脂和橡胶分解温度范围后,产生摩擦系数的骤然降低,这种现象称为“热衰退”。
严重的“热衰退”会导致制动效能变差和恶化。
在实际应用中会降低摩擦力,从而降低了制动作用,这很危险也是必须要避免的。
在摩擦材料中加入高温摩擦调节剂填料,是减少和克服“热衰退”的有效手段。
经过“热衰退”的摩擦片,当温度逐渐降低时摩擦系数会逐渐恢复至原来的正常情况,但也有时会出现摩擦系数恢复得高于原来正常的摩擦系数而恢复过头,对这种摩擦系数恢复过头我们称之为“过恢复”。
摩擦系数通常随温度增加而降低,但过多的降低也是不能忽视。
我国汽车制动器衬片台架试验标准中就有制动力矩、速度稳定性要求。
(QC/T 239-1997 货车、客车制动器性能要求;QC/T 582-1999 轿车制动器性能要求;T564-1999 轿车制动器台架试验方法;QC/T 479-1999 货车、客车制动器台架试验方法),因此当车辆行驶速度加快时,要防止制动效能的下降因素。
摩擦材料表面沾水时,摩擦系数也会下降,当表面的水膜消除恢复至干燥状态后,摩擦系数就会恢复正常,称之为“涉水恢复性”。
摩擦材料表面沾有油污时,摩擦系数显著下降,但应保持一定的摩擦力,使其仍有一定的制动效能。
2.良好的耐磨性。
摩擦材料的耐磨性是其使用寿命的反映,也是衡量摩擦材料耐用程度的重要技术经济指标。
耐磨性越好,表示它的使用寿命越长。
但是摩擦材料在工作过程中的磨损,主要是由摩擦接触表面产生的剪切力造成的。
工作温度是影响磨损量的重要因素。
当材料表面温度达到有机粘结剂的热分解温度范围时,有机粘结剂如橡胶、树脂产生分解、碳化和失重现象。