丰田式管理制度培训课程
【培训课件】广汽丰田公司5S培训【秘密级】

05
总结与展望
5S推行成果回顾
5S推行活动自启动以来,已取得了显著的成果。通过在各个部门和生产线上实施 一系列有效的改善措施,工作环境和生产效率都得到了显著提升。
5S推行过程中,员工们的参与度和积极性高涨,这为活动的顺利推进起到了重要 作用。
通过5S推行,公司的整体形象得到了提升,员工的工作态度也变得更加严谨细致 。
根据实际情况制定 手册
在制定手册时,要结合企业的实 际情况,包括企业规模、行业特 点、员工素质等因素,制定符合 企业需求的5S管理手册。
加强培训和宣传
制定好手册后,要加强员工培训 和宣传,让员工充分了解5S管 理的意义和实施方法,提高员工 的意识和参与度。
建立监督机制
为了确保5S管理手册得到有效 执行,要建立完善的监督机制, 定期对现场管理进行检查和评估 ,及时发现问题并采取措施加以 改进。
5S管理有助于营造积极向上的工作 氛围,增强员工的归属感和责任感 。
5S管理手册的内容
整理(Sort)
将工作区域内的物品进 行分类,划分为需要和 不需要的,将不需要的 物品清除。
整顿( Straig…
将留下的物品进行标准 化、标识和定位存放, 以便在需要时快速找到 。
清扫(Scrub )
定期清扫工作区域,包 括机器设备、地面、墙 壁、桌面等,保持整洁 无尘。
持续推行5S的意义与价值
持续推行5S对于公司来说具有 重要的意义。首先,它能够提 高工作效率和产品质量,降低 生产成本。
其次,5S推行有助于提高员工 的工作满意度和归属感,增强 团队合作精神。
最后,5S能够为公司营造一个 更加整洁、安全、有序的生产 环境,树立良好的企业形象。
未来广汽丰田公司5S推行展望
丰田式管理制度培训课程
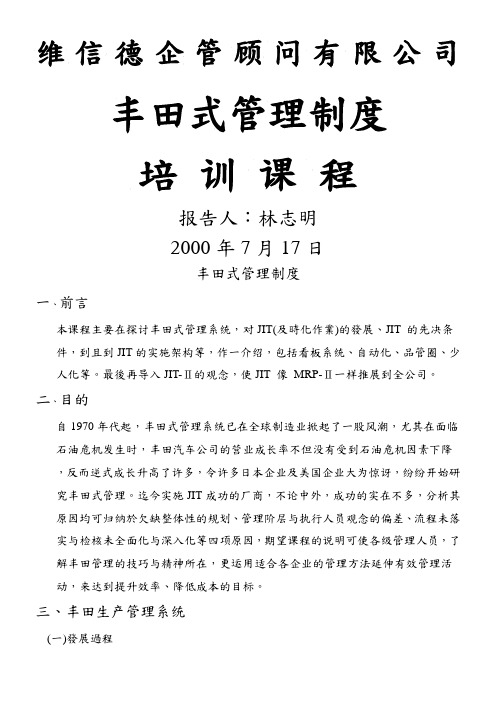
维信德企管顾问有限公司丰田式管理制度培训课程报告人:林志明2000年7月17日丰田式管理制度一、前言本课程主要在探讨丰田式管理系统,对JIT(及時化作業)的發展、JIT 的先决条件,到且到JIT的实施架构等,作一介绍,包括看板系统、自动化、品管圈、少人化等。
最後再导入JIT-Ⅱ的观念,使JIT 像MRP-Ⅱ一样推展到全公司。
二、目的自1970年代起,丰田式管理系统已在全球制造业掀起了一股风潮,尤其在面临石油危机发生时,丰田汽车公司的营业成长率不但没有受到石油危机因素下降,反而逆式成长升高了许多,令许多日本企业及美国企业大为惊讶,纷纷开始研究丰田式管理。
迄今实施JIT成功的厂商,不论中外,成功的实在不多,分析其原因均可归纳於欠缺整体性的规划、管理阶层与执行人员观念的偏差、流程未落实与检核未全面化与深入化等四项原因,期望课程的说明可使各级管理人员,了解丰田管理的技巧与精神所在,更运用适合各企业的管理方法延伸有效管理活动,来达到提升效率、降低成本的目标。
三、丰田生产管理系统(一)發展過程丰田生产系统是由丰田汽车公司前副社长----大野耐一先生( Mr.Taiich Ohno ) 历经30年的时间首创并推广的一种生产方式。
直到1973年第一次石油危机时,由於丰田汽车公司尚能在此种环境中获致庞大的利润,而引起日本工业界的注目。
此理論的基礎是集合了自動織機發明之王----豐田佐吉翁(豐田紡織廠) 及豐田汽車創始者豐田喜一郎的思想( Just In Time ),經過大野先生將之推行實施而成的学说。
(二)及時性生產JIT的定義丰田生产系统的基本理念是弹性地适应需求的变化,也就是在必要的时间,生产必要数量的产品。
丰田生产的最终目的是藉着成本的降低以创造利益,为了达此目标,就要排除浪费,如多余的库存、搬运‥等,以降低制造成本。
且藉着降库存而使各种问题显现,透过解决问题的改善活动及排除浪费的因素实施,而使制造成本降低,达到丰田管理的主要目标。
丰田精益生产管理培训课件

质量改进
对质量目标进行分解和制定实施措施.有质量审核计划,定期对体系、过程、产品进行内部审核确保体系运行有效性和适宜性.各类质量记录有专人收集保存、存档,对不良品、质量指标、用户抱怨、内外部故障成本等运用统计技术定期统计和分析,未达到标准有确实预防和分析纠正措施和评价
28
全员设备维护保养工作TPM
13
典型的工序看板
前工序部件1-3线出口位置POS.12-2
部件号A232-605C箱号:003箱内数量:100看板编号:2/5
使用工序总装1-3入口位置POS.12-8
14均衡Biblioteka 同步同节拍生产同步化节拍生产是按照生产工艺规定和物流顺序确定生产提前期条件下和产品总装配线保持同步地进行生产一个流的生产,前工序加工一结束即立即转到下一工序,尽量使工序间在制品接近于零一个流的生产,必须将设备的布局进行调正,不是按类型而是按工序形成相互衔接的生产线U形、T形等
17
过剩生产是最严重浪费
为什么会过剩是平衡生产和次废品需求,过剩生产说明由于人员和设备过多. 表面效率和实际效率 原来某工序生产100个,现通过努力增产到120个,表面效率得到提高,但实际祗需求或生产线工艺节拍100个,这就是浪费.实际效率没提高,所以整体效率重于个人效率
18
缩短作业切换时间
31
开展5S活动-现场管理基础
整理 停滞物的管理,是区分要与不要,不要的清除出现场.整顿 对整理后需要物品的整顿,重点是合理定置、方便使用.清扫 就是弄干净,核心是自已动手,创造一个优质、高效、安全、明快舒畅 它包含照明 的工作现场.清洁 坚持整理、整顿、清扫的结果就是清洁,它包括粉尘、噪音、有毒气体等环境要求.素养 就是行为规则,自觉执行制度、标准,不断地提高自身的修养.
【培训课件】广汽丰田公司5S培训【秘密级】
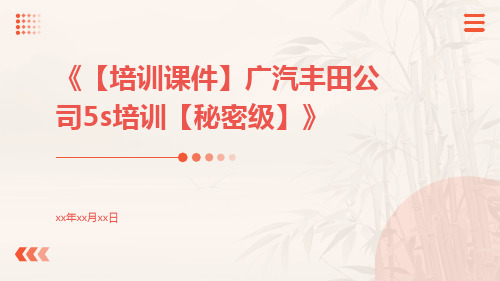
5S的发展
01
5S在实践中不断发展和完善,逐渐成为一种系统化的管理模式 。
02
5S的实践不仅提高了企业的生产效率和质量,还改善了员工的
工作环境和职业健康安全。
5S的实践还促进了企业文化的建设,提高了员工的归属感和凝
03
聚力。
02
5S推行目的和意义
5S推行目的
创建一个干净整洁、舒适安全的工作环境
5S的推行可以使得工厂和办公室等场所保持清洁、有序和安全,使得员工能够在舒适的环 境中工作,提高生产效率和工作质量。
提高工作效率和产品质量
通过5S的推行,可以提高工作效率和产品质量。这是因为5S可以帮助企业优化工作现场 的布局、提高物流的效率、减少浪费和不良品等,从而使得生产效率和质量得到提高。
提升企业形象
清扫实施难点及解决方案
清扫实施难点
员工对清扫态度不积极,清扫不彻底;缺乏有效的清扫工具和设备。
解决方案
加强员工清扫意识培训,提高积极性;引进先进的清扫工具和设备,提高效率和 质量。
清洁实施难点及解决方案
清洁实施难点
员工对清洁的定义理解不深刻,清洁标准执行不到位;检查 机制不健全。
解决方案
加强员工清洁定义培训,提高认识;建立完善的检查机制, 确保清洁标准的执行。
仅有利于员工个人的职业发展,也有助于企业的长远发展。
03
提升安全性和健康水平
5S的推行可以帮助企业提高安全性和健康水平。这是因为5S可以帮助
企业及时发现和解决潜在的安全隐患和健康问题,避免事故的发生。
5S与生产效率
优化生产现场布局
通过5S的推行,可以优化生产现场的布局和设计 ,使得生产流程更加合理、高效和顺畅,从而提 高生产效率。
丰田管理课程设计

丰田管理课程设计一、教学目标本课程旨在让学生了解和掌握丰田管理的基本理念、原则和实践方法。
通过学习,学生将能够:1.掌握丰田管理的基本理念,如“拉动生产”、“自动化”和“不断改善”。
2.理解丰田管理的五大原则,并能在实际工作中应用。
3.学习丰田生产系统的核心工具和技术,如看板系统、TWI和工作教导。
4.培养对丰田管理的认同感和实践热情,为未来的职业发展打下基础。
二、教学内容本课程的教学内容主要包括以下几个部分:1.丰田管理的基本理念:介绍丰田管理的起源、核心思想和核心价值观。
2.丰田管理的五大原则:详细讲解每个原则的含义和应用。
3.丰田生产系统:介绍TPS的组成部分,如看板系统、平准化生产、自动化等。
4.丰田管理的核心工具和技术:讲解TWI、工作教导、问题解决等工具和方法。
5.案例分析:分析实际案例,让学生更好地理解丰田管理的应用。
三、教学方法为了提高教学效果,本课程将采用多种教学方法,包括:1.讲授法:讲解丰田管理的基本理念、原则和工具。
2.案例分析法:分析实际案例,让学生更好地理解丰田管理的应用。
3.小组讨论法:分组讨论,促进学生之间的交流和思考。
4.角色扮演法:模拟实际工作场景,让学生亲身感受丰田管理的实践。
四、教学资源为了支持教学,我们将准备以下教学资源:1.教材:《丰田管理手册》和《丰田生产系统》。
2.参考书:提供相关的论文和书籍,供学生深入研究。
3.多媒体资料:播放丰田生产的视频资料,让学生更直观地了解丰田管理。
4.实验设备:提供模拟生产线和相关设备,让学生亲自动手实践。
五、教学评估为了全面评估学生的学习成果,我们将采用以下评估方式:1.平时表现:通过观察学生在课堂上的参与程度、提问和回答问题的情况,以及小组讨论的表现来评估。
2.作业:布置相关的练习和作业,评估学生对知识的理解和应用能力。
3.考试:进行期中和期末考试,测试学生对课程内容的掌握程度。
4.案例分析报告:学生需要提交案例分析报告,评估他们对实际案例的理解和分析能力。
丰田管理系统培训

丰田管理系统培训丰田管理系统是一套专门针对丰田公司的管理方法和工具,旨在提升组织运营效率和生产效益的培训课程。
该培训课程致力于培养学员对丰田管理系统的了解和应用能力,以及提供一种持续改进的管理模式。
培训目标:1. 了解丰田管理系统的基本原则和核心理念,如质量第一、零库存、持续改进等。
2. 学习制定和实施丰田管理方法,如标准化工作、价值流分析、5S管理等。
3. 培养学员对质量管理、生产流程优化、问题识别与解决等方面的能力。
4. 培养学员的团队协作和沟通能力,以及持续改进的思维方式。
培训内容:1. 丰田管理系统介绍:对丰田管理系统的起源、发展历程和核心原则进行介绍,激发学员对其的兴趣和认识。
2. 质量第一:学习如何确保产品和服务的质量,了解质量管理的重要性以及如何通过质量改进来提高企业竞争力。
3. 价值流分析:学习如何通过价值流分析来优化生产流程,降低浪费并提高生产效率。
4. 5S管理:学习如何通过整理、整顿、清洁、清扫和纪律来创建一个高效的工作环境。
5. 持续改进:学习如何通过PDCA循环(计划、执行、检查、行动)和A3报告来解决问题并实现持续改进。
6. 团队协作和沟通:培养学员的团队合作和沟通能力,以促进各部门之间的合作和信息流通。
7. 实施丰田管理系统的关键因素:学习在实施丰田管理系统中需要注意的关键因素和挑战,并分享成功案例和经验。
培训方法:1. 理论讲解:通过讲座、案例分析等方式,向学员介绍丰田管理系统的基本原则和工具。
2. 实践演练:通过实地参观和模拟操作,让学员亲身体验丰田管理系统的实际应用。
3. 小组讨论和分享:组织学员进行小组讨论和分享,以促进彼此之间的学习和交流。
4. 案例分析:通过分析实际案例,让学员学会如何应用丰田管理系统解决实际问题。
5. 辅导和指导:提供个别辅导和指导,帮助学员在实施丰田管理系统时克服困难和挑战。
通过丰田管理系统培训,学员可以深入了解丰田公司的管理理念和方法,并将其应用于自己的工作中,提升工作效率和质量,进一步促进企业的持续改进和发展。
丰田管理培训课件

丰田管理培训课件丰田管理培训课件丰田管理培训课件1、丰田的变化点管理流程:来自于日本资料,从人、机、料、法四方面进行,由组长、班长(线外、脱产,系他们日常工作的一部分)负责识别、记录、结案。
其中主要是人的变化,丰田分为两类,一类是新进员工,由老员工或者班长、组长旁边帮忙,保证量产生产节拍,一般在3个月内进行观察,并针对员工技能提交培训要求,由铸造部安排培训计划。
另一类是其他岗位支援员工,不可让其担当组内核心作业岗位。
2、丰田的三本柱:标准作业:作业组合票、标准作业票、山积票、作业要领书自主保全:设备点检表、定期保全、定量保全、预发保全、突发保全型管理:热芯盒、金属造型模具的保全3、丰田的'自主保全:现场从5S为主,从最基本的跑、冒、滴、漏开始,谁操作设备谁负责,首先是班、组长必须有发现的能力并能够解决,告诉自己的属下:气管漏气就是不对的,要么自己解决要么寻求上级解决;4、丰田的安全意识:班组长必须建立安全意识,非常清楚自己所属范围的危险隐患是那些;班组长在调动新老员工或者其他本部门支援员工劳动岗位的时候必须向其讲解安全隐患;员工在不熟知自己马上要操作的内容时可以拒绝上岗,反向给班组长压力、动力; 多人合作,必须建立指挥人原则,具体就是谁听谁的;5、以下是模具保全组长闫嘉宾、赵忠华、邢少飞现场针对模具保全的实习内容:A. 保全分为(由于是铸铝铸造,与我们有些差异)热芯盒保全区:金属型模具,安装制芯机上,上下分型;B. 模具维修管理流程模具组自己建立维修台账,维修记录保全10个月;模具组每付芯盒建立问题点联络书及其作业履历卡,将在库模具状态描述完毕,随同模具一同发往现场,待生产结束,生产现场若有问题及时填写问题点联络书,要求维修。
确保问题点发生后便于追溯责任方,并依此增强模具库人员的服务意识;模具维修完毕后,维修后检验书填写完毕,现场汇同模具库确认后,确认存档;C. 模具日常管理流程外形尺寸:技术员参与,氩弧焊堆焊,机加工铣型,延长模型寿命(一次延长3万模),后续进行试生产,切断验证尺寸、试机组装验证机械性能;寿命管理:现场每日生产数据统计(设备程序可以调出数据作为证据),每月进行汇总,现场可视化标出;备品备件:摸索出使用寿命,在未出故障前提下进行更换;模具清理:玻璃、树脂球(减轻磨损用玻璃粉及其树脂粉);安全管理:明确模具库每一位员工可以使用的设备,定人定岗,严禁外部使用; 要人计划:模具库优先挑选员工,遴选最稳定的员工到核心岗位上去;部门递交三票分析瓶颈工序,以提交用人计划;模具预热:高压直接用铝水试浇注缸体(5~6件)来加热模具(称之为可打件)热芯盒使用Φ12mm~14mm的加热管,数量多布,3mm厚铜片并联,机台加热,升温快;模具保存:分区域进行管理,三种设备,三个区域划分;根据沟通结合我们目前的在库模具量,建议我们可以进行按照品种、或者生产数量、或者易损情况进行针对的重点保全和一般保全;(当然,丰田产品单一,产量大,可以使用大规模的维修设备,进行固定化标准化模式的维修和管理,且不轻易装卸模具,这一点对比参照我们的量产生产任务的产品有参考意义)。
丰田式管理规定培训课程
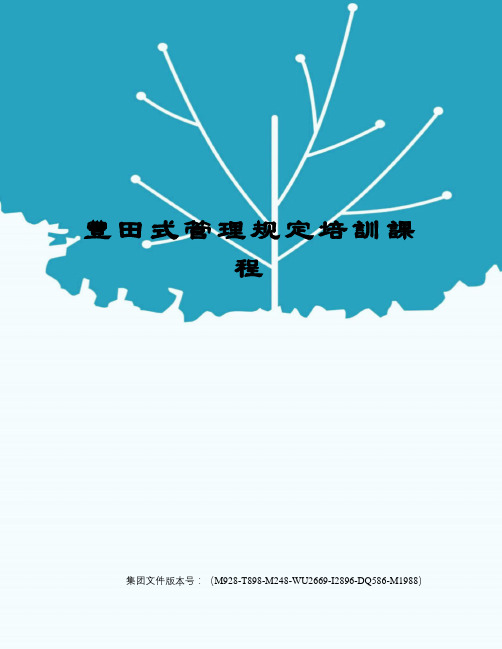
豐田式管理规定培訓課程集团文件版本号:(M928-T898-M248-WU2669-I2896-DQ586-M1988)维信德企管顾问有限公司丰田式管理制度培训课程报告人:林志明2000年7月17日丰田式管理制度一、前言本课程主要在探讨丰田式管理系统,对JIT(及时化作业)的发展、JIT 的先决条件,到且到JIT的实施架构等,作一介绍,包括看板系统、自动化、品管圈、少人化等。
最後再导入JIT-Ⅱ的观念,使JIT 像 MRP-Ⅱ一样推展到全公司。
二、目的自1970年代起,丰田式管理系统已在全球制造业掀起了一股风潮,尤其在面临石油危机发生时,丰田汽车公司的营业成长率不但没有受到石油危机因素下降,反而逆式成长升高了许多,令许多日本企业及美国企业大为惊讶,纷纷开始研究丰田式管理。
迄今实施JIT成功的厂商,不论中外,成功的实在不多,分析其原因均可归纳於欠缺整体性的规划、管理阶层与执行人员观念的偏差、流程未落实与检核未全面化与深入化等四项原因,期望课程的说明可使各级管理人员,了解丰田管理的技巧与精神所在,更运用适合各企业的管理方法延伸有效管理活动,来达到提升效率、降低成本的目标。
三、丰田生产管理系统(一)发展过程丰田生产系统是由丰田汽车公司前副社长----大野耐一先生( Mr.Taiich Ohno )历经30年的时间首创并推广的一种生产方式。
直到1973年第一次石油危机时,由於丰田汽车公司尚能在此种环境中获致庞大的利润,而引起日本工业界的注目。
此理论的基础是集合了自动织机发明之王----丰田佐吉翁(丰田纺织厂)及丰田汽车创始者丰田喜一郎的思想( Just In Time ),经过大野先生将之推行实施而成的学说。
(二)及时性生产JIT的定义丰田生产系统的基本理念是弹性地适应需求的变化,也就是在必要的时间,生产必要数量的产品。
丰田生产的最终目的是藉着成本的降低以创造利益,为了达此目标,就要排除浪费,如多余的库存、搬运‥等,以降低制造成本。
精益管理方法—丰田式改善培训课件
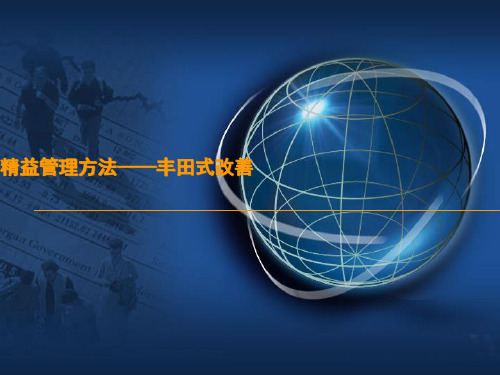
6. 彻底地思考和执行
再三思考、怀着“决不放弃”的强大 意志和坚忍不拔的精神,将工作进行 到最后
7. 速度・时机
迅速对应客户需求,贯彻实施对策。
如果对策的实施尚需要一定时间,可采取适当措施, 以免错失良机
8. 诚实・正直(实事求是)
进阶篇
在处理新业务或范围广的业务、或制定方 针时所需要的工作的“经验技巧”
丰田工作方法的开发背景
海外
随着丰田汽车事业的国际化, 为使其价值观可视化,制定了 《Toyota way 2001》
日本
针对年轻员工工作能力低下,从 2000年开始加强丰田工作方法的 培训
尽管“Toyota way”目前已在全世界 的事业体中广为人知。 但仍然有很多员工,甚至是管理层 都不知道如何才算真正实践了 Toyota Way
问题发生在哪个环节?
问题发生的环节
为什么一定要确定 问题发生的环节呢?
是为了有效率地 分析真因。
Step 2.分解问题
Process 3. “现地现...
理想状态
差距=问题
现状
对所承担的业务怀有高度的问题意识
要点 1) 自己工作的基本功要扎实; 2) 明确自己工作的目的; 3) 站在客户角度考虑问题; 4) 对变化敏感; 5) 了解竞争对手水平 。
…etc.
摒弃“有问题是坏事”的意识
• 丰田并不认为“有问题”是件坏事。
有划痕的车辆
不好的切入点
好的切入点
1班
2班
底盘
前装
轿车
箱车
后装
Step 2.分解问题
Process 2.确定自身要着手解决的问题
管理人员培训丰田的问题解决课件

①把握对策的相关者
②筛选对策 ③决定实施对策
(3)寻求共识
(4)制定明确具体的实施计划
通过逻辑树整理出对策
从效果、成本、风险的角度对比筛选最优方案
(方案运营巩固阶段的风险及遵纪守法视点
统合相关人员及部门,取得共识,制定行管动理人计员划培训-丰田的问题解决
33
问题解决的8大步骤
P
3.设定目标
4.把握真因
5.制定对策
D
6.贯彻实施对策
C
7.评价结果和过程
A
8.巩固成果
管理人员培训-丰田的问题解决
28
Step 5. 制定对策
How? (如何解决)
根本原因
能否消除?
对策 对策 对策 对策 对策 对策 对策
风险? 固有观念框架
本职工作的框架
相关人员?
管理人员培训-丰田的问题解决
管理人员培训-丰田的问题解决
12
Step 2. 分解问题
1.将问题分层次,具体化
例)分析“未完成销售任务”的问题的切入点
销售好的车
销售不好的车
轿车
SUV
两厢车
面包车
A店 B店 C店 D店
不好的切入点
好的切入点
管理人员培训-丰田的问题解决
13
Step 2. 分解问题
2. 决定优先顺序,选定要着手解决的问题
14
Step 2. 分解问题
3. 现地现物观察流程,明确问题点
▪▪▪
▪▪▪
问题 问题
问题
▪▪
问题
综合考虑,判断优先顺序
问题点
观察过程,明确问题点
对于”要着手解决的问题”,顺着时间轴,
丰田4S管理培训教材

提高信任感和满意度
异常减少 品质提高 满意度提高
对策
寻找解决对策
TOYOTAL&F
“发现浪费”→“改善” 可以发现浪费的组织架构 4S
这一循环不断往复。
平均化生产
后续工序
标准作业
T P S 的 2 根 支 柱
Just/in/time 仅对“需要的产品”、“在必要的时间”、生产和搬运“必要 的量”。
TOYOTAL&F
制定4S日历
TOYOTAL&F
1. 丰田的生产方式和4S
2. 4S的实践
3. 维持4S的关键,另外一个S“教育”
TOYOTA L&F
检查你的公司的“教育”度 □①把不需要的物品扔掉后,会马上发生大量堆积。 □②工具使用完毕后,丢在那里不管。 □③物品不是什么时候不见了 □④钻头和美工刀的放置方法会影响其锋利程度 □⑤材料和零部件的堆积易发生倾倒 □⑥厕所肮脏 □⑦机械和设备沾满油污和粉尘,乌黑一片。 □⑧无论怎么劝说,都不戴安全帽和防护眼镜 □⑨作业场所和通道上布满烟屁股和垃圾 □⑩无法打招呼
在制造业中,只有“加工”是具有附加价值的作业=正式作业 只有正式作业才能得到回报。
TOYOTAL&F
所谓浪费:所有不能提高附加价值的工作。 浪费的种类 7种浪费
最严重的浪费 ①制造过剩 (会诱发其它浪费的 产生) ②拿在手里 ③搬运 ④加工过程自身存在的 浪费 ⑤库存 ⑥动作 ⑦不合格产品/修理
子啊丰田公司,在生产中, 把 ,在物流过程中把 定位为“最严重的浪费”。
自动化(带人字部的自动化) 发生异常时停止、人和机械的分离、在工序中控制质量
TOYOTAL&F
4S是基本中的基本,是进行改善最为重要的基础工作。
丰田管理方式与问题解决八步法-培训手册
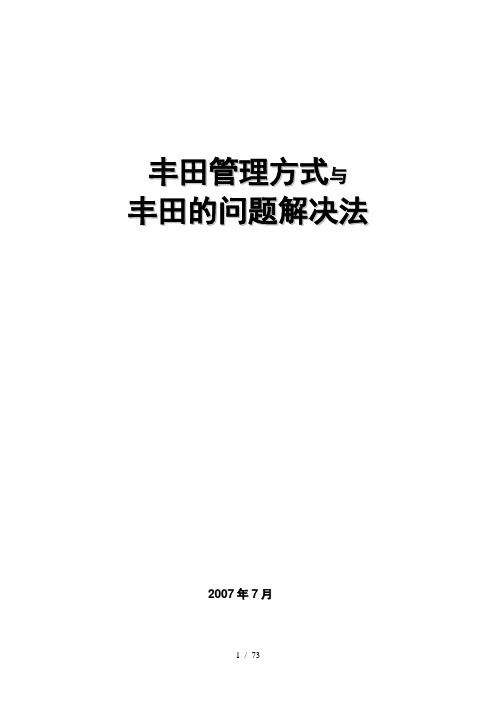
丰田管理方式与丰田的问题解决法2007年7月目录“丰田管理方式”发表和丰田问体解决法产生的背景丰田人共同的经营理念和价值观:丰田管理方式 Toyota Way2001社长X富士夫在致辞提出:“Toyota Way”随环境的变化而变动,作为丰田的强项将不断发展下去; 在不断思索的过程中,理解丰田管理方式,发展和完善丰田管理方式的内容.丰田的基本理念丰田的基本理念---表明自己想向客户、股东、员工、商业伙伴和社会提供一种什么样的价值。
[ TOYOTA WAY 2001 ]从如何将 [丰田的基本理念]运用到企业的实际活动中去的角度出发,揭示了作为丰田的员工应该拥有什么样的价值观,应该采取怎样的行动姿态。
对于丰田组织来说,培养人们的自觉意识,维持健全而有活力的经营活动,是实现 [丰田的基本理念]的基本支柱。
丰田的基本理念--------Added Value员工的自觉意识健全而有活力的经营活动全体丰田员工共同的追求:❑永不满足于现状,追求更高的附加值,并为此而发挥智慧❑尊重所有的关系户,将员工的发展与企业的成果联系起来丰田管理方式 Toyota Way2001挑战---面向梦想的实现,发挥想象力,充满勇气和创造力去挑战改善---- 时刻前进,追求革新,坚持不懈地改善现地现物---通过现地现物看清事物的本质,迅速果断地统一意见,并全力付诸实施尊重--- 尊重他人, 努力做到诚实待人,相互理解,互相负责团队合作---培养人材, 机遇共享, 最大限度地发挥团队以及团队中每一个人的力量1.什么是丰田的问题解决法?丰田管理方式要求每个员工:1.永不满足于现状,追求更高的附加值,并为此而发挥智慧2.尊重所有的关系户,将员工的发展与企业的成果联系起来丰田工作方式—人人都带着“TOYOTA WAY”的价值观去工作,是每一个丰田人都应该掌握的工作.实践的方法。
Plan(计划) Do(实施) Check(评价) Action(巩固,改善)2. 日常工作中的10个基本意识丰田问题解决法的重要性❑客户至上在为本部门或公司推展工作时,应始终将客户利益放在第一位.❑经常自问自答为什么?不要将当前的手段混淆为目的.常常自问:“真正的目的是什么?”❑当事者意识只有认识到自己是当事者,才能理解自己工作的使命和价值,产生自豪感.才会思考“我想要做什么?”, “我一定要达成这个!”❑可视化❑根据现场和事实判断将问题用一目了然的方式显现,使之在相关人员之间共享,促进新的发现. 对其他如信息,计划,对情况的认识,意见等需要共享的信息,也应当进行可视化处理.不要想当然,以无拘无束之心,看待事物的真实方面.不将臆测与事实相混淆.❑彻底地思考和执行再三思考,怀着“决不放弃”的强大意志和坚忍不拔的精神,将工作进行到最后.❑速度.时机迅速对应客户需求,贯彻实施对策.如果对策的实施尚需要一定时间,可先采取适当措施,避免错失良机❑诚实.正直(用理所应当的方式去做理应去做的事) 坚定地执行每一道工序(不任意跳过).虚心听取别人的意见.对自己的行为负起责任.❑实现彻底地沟通❑全员参与诚心诚意,与客户和相关人员沟通,直到他们给予理解并能够主动积极提供协助.动员一切可动员的力量,引领团队及相关人员,集思广益,以达到效果和效率的最大化.3. 什么是丰田的“问题” ?丰田的“问题”……..如何发现“问题”….要发现问题, 需要经常保持高度的问题意识, 不断审视自己的工作.永远不满足自己工作的现状,常常思考: “这样真的行吗?能不能做得更好?”如何保持高度的问题意识❖自己工作的基本功要扎实❖要站在客户的角度考虑问题❖对变化敏感❖把握时代的动向❖了解竞争对手的状况水平………………………大野耐一: 没有问题才是最大的问题保持高度的问题意识小K随意打开电视,电视里正在播放一个介绍某酒店为提高房客满意度而展开改善活动的节目。
丰田5S管理制度
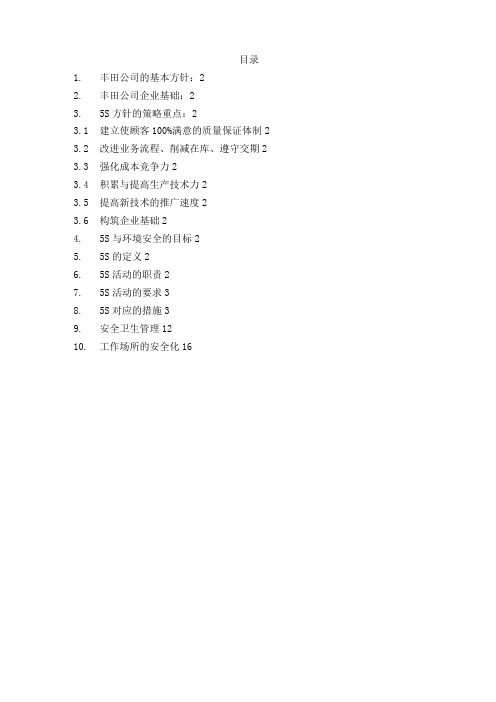
目录1.丰田公司的基本方针:22.丰田公司企业基础:23.5S方针的策略重点:23.1建立使顾客100%满意的质量保证体制2 3.2改进业务流程、削减在库、遵守交期2 3.3强化成本竞争力23.4积累与提高生产技术力23.5提高新技术的推广速度23.6构筑企业基础24.5S与环境安全的目标25.5S的定义26.5S活动的职责27.5S活动的要求38.5S对应的措施39.安全卫生管理1210.工作场所的安全化161.丰田公司的基本方针:提供顾客100%满意的服务,创建员工100%满意的公司。
2.丰田公司企业基础:危机管理体制,人才培养,环境安全以及5S的推行3.5S方针的策略重点:3.1建立使顾客100%满意的质量保证体制3.2改进业务流程、削减在库、遵守交期3.3强化成本竞争力3.4积累与提高生产技术力3.5提高新技术的推广速度3.6构筑企业基础4.5S与环境安全的目标4.1提高生产性4.2提高服务水平和维修产品质量4.3提高速度4.4提高人员素质4.5提高安全性5.5S的定义5.1整理:工作现场,区别要与不要的东西,只保留有用的东西,撤除不需要的东西;5.2整顿:把要用的东西,按规定位置摆放整齐,并做好标识进行管理;5.3清扫:将不需要的东西清除掉,保持工作现场无垃圾,无污秽状态;5.4清洁:维持以上整理、整顿、清扫后的局面,使工作人员觉得整洁卫生;5.5修养:通过进行上述4S的活动,让每个员工都自觉遵守各项规章制度,养成良好的工作习惯,做到“以厂为家、以厂为荣”的地步。
6.5S活动的职责6.1办公室负责组织整个公司的5S及安全卫生的检查6.2各部门负责按5S管理要求对本部门的5S及安全卫生进行检查6.3责任部门负责对5S及安全卫生检查中发现的问题进行改进5S 活动的要求良好的仪表及礼仪:统一规范的着装要求,良好的坐姿、站姿,电话礼仪,整洁、明亮、大方、舒适的接待环境单一整洁的办公室:台面整洁,文具单一化管理,公用设施责任人标识生产工具管理:单一化管理现场管理:分区划线,员工工作井然有序,工作环境清洁明亮工作速度和效率:最佳的速度和零不良率空间效率:对现场分区划线,对各场地的利用率予于分析,增加有限空间的利用价值严明的小组督导:上班前经理、班组长对员工进行检查督导,工作过程中,对发现的问题及时开展小组督导,下班前对全天的工作进行总结工作评估:自我评估与综合考核评价相结合5S 对应的措施整理的措施1清除不用物品的措施 a)进行整理,首先要根据情况,分清什么需要,什么不需要。
- 1、下载文档前请自行甄别文档内容的完整性,平台不提供额外的编辑、内容补充、找答案等附加服务。
- 2、"仅部分预览"的文档,不可在线预览部分如存在完整性等问题,可反馈申请退款(可完整预览的文档不适用该条件!)。
- 3、如文档侵犯您的权益,请联系客服反馈,我们会尽快为您处理(人工客服工作时间:9:00-18:30)。
維信德企管顧問有限公司豐田式管理制度培訓課程報告人:林志明2000年7月17日豐田式管理制度一、前言本課程主要在探討豐田式管理系統,對JIT(及時化作業)的發展、JIT 的先決條件,到且到JIT的實施架構等,作一介紹,包括看板系統、自動化、品管圈、少人化等。
最後再導入JIT-Ⅱ的觀念,使JIT 像 MRP-Ⅱ一樣推展到全公司。
二、目的自1970年代起,豐田式管理系統已在全球製造業掀起了一股風潮,尤其在面臨石油危機發生時,豐田汽車公司的營業成長率不但沒有受到石油危機因素下降,反而逆式成長升高了許多,令許多日本企業及美國企業大為驚訝,紛紛開始研究豐田式管理。
迄今實施JIT成功的廠商,不論中外,成功的實在不多,分析其原因均可歸納於欠缺整體性的規劃、管理階層與執行人員觀念的偏差、流程未落實與檢核未全面化與深入化等四項原因,期望課程的說明可使各級管理人員,瞭解豐田管理的技巧與精神所在,更運用適合各企業的管理方法延伸有效管理活動,來達到提升效率、降低成本的目標。
三、豐田生產管理系統(一)發展過程豐田生產系統是由豐田汽車公司前副社長----大野耐一先生( Mr.Taiich Ohno )歷經30年的時間首創並推廣的一種生產方式。
直到1973年第一次石油危機時,由於豐田汽車公司尚能在此種環境中獲致龐大的利潤,而引起日本工業界的注目。
此理論的基礎是集合了自動織機發明之王----豐田佐吉翁(豐田紡織廠)及豐田汽車創始者豐田喜一郎的思想( Just In Time ),經過大野先生將之推行實施而成的學說。
(二)及時性生產JIT的定義豐田生產系統的基本理念是彈性地適應需求的變化,也就是在必要的時間,生產必要數量的產品。
豐田生產的最終目的是藉著成本的降低以創造利益,為了達此目標,就要排除浪費,如多餘的庫存、搬運‥等,以降低製造成本。
且藉著降庫存而使各種問題顯現,透過解決問題的改善活動及排除浪費的因素實施,而使製造成本降低,達到豐田管理的主要目標。
除了主要目標外,還有三個次要目標 :1.能適應每月每日的需要變動,兼顧數量與種類的數量管理。
2.每項工程都能提供後面工程良好的品質保證。
3.為達成降低成本,利用人力資源時,也必須提高對人性的尊重目的。
(三)及時性生產JIT的主要架構生產線的一貫流程,與對市場的數量及種類的需求變化,是藉著「及時化」及「自動化」來完成。
1.及時化( Just in time ) : 必要的物品,必要的時候,生產必要的份量。
2.自動化 : 能自動檢出製程上異常現象的裝備,且自動停止裝置的機械。
這二個可說是豐田生產的二大支柱。
同樣重要的概念還包括了下列兩項 :1.適應需求變化而對作業員人數作理性調整的「少人化」。
2.透過作業員的提案改善活動的「品管圈」。
為了實現這4個概念,豐田公司採用下列幾個方法 :1.使用「看板制度」以達成及時生產。
2.採行生產、平穩化的方法以適應需求變化。
3.縮短整備時間以減少生產前置期。
4.實施「操作標準化」以達成生產線的平衡。
5.注意機器設備之安排及運用「多能工」以期能保有增減作業人數之彈性。
6.藉著進行小組「改善活動」和,提案制度,以削減作業人數和提高作業員士氣。
7.藉「目視控制」制度以實現「自動化」概念「功能管理制度」以推進全公司的品質管理。
(四)排除浪費豐田生產方式可以稱為徹底排除浪費的方式。
製造現場通常視浪費為「增加成本負擔之要素」,因此若不重視浪費的問題,將會發生很多不必要的麻煩。
◆常見的浪費有下列七種形式 :1.修改不良品的浪費。
2.生產過剩的浪費,生產過剩將導致增設機器設備、材料預支、多餘操作員金錢的損失、倉庫擴大等,百害而無一利。
3.加工的浪費,自己認為最好的方式或工作,其實包含了浪費。
4.搬運的浪費。
5.庫存的浪費。
6.動作的浪費 : 製造過程中,假如人手、設備、機器之操作而產生找不到物品,不良品等時,這些都是浪費的主因。
7.等待的浪費:機器還在加工,後面的人沒有工作,空手等待稱為等待的浪費。
◆改善浪費的順序 :l.表格標準作業 : 正確記錄,對於日常作業要求必定按照事實寫出來。
2.發現浪費 : 根據步驟 1的確實記錄與標準作業做比較找出問題點。
3.改善 : 針對浪費的地方找出解決之道(五) 看板制度(Kanban)看板制度是對各製程的生產量進行控制的一種資訊系統。
這種生產管理,可稱為及時生產,但看板制度並不等於豐田生產體系。
1.看板種類(1)常用的看板有二種 : 取用看板及生產訂購看板,取用看板是記載後製程應該向前製程領取的零組件種類和數量。
生產訂購看板又被稱為生產看板,則記載前製程必須生產或訂購的零組件的種類和數量(2)供應商看板 : 向零件供應商提取零取件。
供應商看板則一律使用條碼。
(3)信號看板 : 用來載明壓鑄機,或是鍛造工程等批量生產。
2.看板功能(1)避免生產過剩的浪費。
(2)索取情報、生產指示情報。
(3)目視的管理、道具。
(4)改善的道具一看板太多反而沒有效果。
3.看板的使用技術(1)後工程的運貨人員,要將必要領取的數量與貨櫃,裝在叉式起重機或台車上,而搬到前工程的倉庫 (零件倉庫) A。
(2)後工程的搬運工,於倉庫A領取零件之後,須拿開裝載貨架內的零件生產指示看板,放入已領取的地方。
(3)搬運人員,於自己所拿開的每一張生產指示看板後,要再掛上一張領取看板(4)在後工程作業一開始時,領取看板放置在收容領取看板的地方。
(5)前工程裏,在一定時間或生產一定數量的零件時,從看板領取處搜集而來的生產指示看板,須按倉庫拿走的順序,將這些生產指示看板放在其收容處才行。
(6)按照放在收容處的生產指示看板順序,來生產零件。
(7)進行加工零件時,這些零件與其看板,要成對的移動。
(8)在此工程中,每完成零件加工後,其零件的生產指示看板須放置倉庫,讓後工程的搬運工隨時領走。
4.達成看板的五個原則:(1)後製程祇有在必要的時候,向前製程領取必要數量的必要零組件。
(2)前製程應該只生產足夠的量,以補充被後製程提取的零件。
(3)不良品決不送往後製程。
(4)看板的使用數目應儘量減少。
(5)應該使用看板以適應小幅度的需求變動。
5.違反看板規則的影響(1)看板會發生狀況(2)易產生不良品(3)增加看板數量(4)庫存增加(5)不易發現問題點(6)不需改善以上的不良結果產生,對於Just In Time實施上的搬運無法運作,當然對生產現場之活性化沒有幫助。
(六) 自動化豐田的自動化牽涉到品質管制,因為它使不良品無法通過生產線,並且它也有降低成本,具有因應彈性的生產及對人性更進一層的重要等等的效果。
2.達成自動化的具體技術 :(1)發生異常的時候,停止生產線所使用的特殊設計法。
A.接觸式的安全系統B.整體式的安全系統C.行動步驟式的安全系統(2)使作業員習於「自動化」生產的技術A.防止盲目操作裝置:關閉型式、警示式B.防呆裝置(3)監視生產及當異常發生的時候,加以修正的手段。
A.視覺控制:標準操作表、看板、數字顯示板和貯存處及倉庫的顯示板。
3.自動化前必要的注意事項(1)定期更換機器的配件(2)定期檢查品質(3)定期補給機油(4)定期除去粉屑等等(5)防止異常停止再發生。
以上的維護作業,需靠各維修人員定期並加以注意維修,使有好的設備,才能製造優良的產品。
(七)及時生產「及時化」就是在必要的時間,把必要的東西 (產品) 送到需要的地方。
要實現及時化,必須完成下列三項準備:1.生產平準化2.作業標準化3.製程設計。
而看板的任務,則是作為情報傳遞的資訊系統。
◆生產平準化所謂生產平準化就是每一個單位製程時間,不管在數量或種類方面都處於平均化的狀態。
平準化生產的優缺點:1.優點:(1)零件的使用量會安定化。
(2)各工程以及承包企業的生產負荷量會安定化。
(3)可降低製品或工程進行間半製品的庫存量。
(4)依據小批量的生產與搬運,單位製品的平均生產佔用時間,可以縮減。
2.缺點:(1)由於各製品的種類大不相同,反而需要有事前的訓練,但實際上其作業的情形,常有延誤或零件裝置錯誤的現象。
(2)必須具備能適用各種製品作業的夾具和製造系統。
如:彈性製造系統(FMS)、群組技術(GT)。
(3)對於前工程作業,需要以小批量且頻繁的領料,而為要縮短庫存與佔用時間,有必要縮短調換機件的時間。
(4)當市場需要有大幅度變動時,就會有生產量難以配合的情形。
◆作業標準化使生產現場有提高生產效率的依據,有管理者管理自己的過程的基礎,便是標準作業。
標準作業由下列三個因素所成立。
1.週期時間 : 指一件物品必須以多少時間來裝配或製造公式為:一天必需數量 = 一個月的必需數量 / 實際工作日數週期時間 = 實際工作時間 / 一天的必需數量2.作業順序 : 是指作業人員在加工物品時,由材料至製品的次序變化過程。
3.在製品標準存量 : 乃指作業過程內最低需要量的半成品,也包括裝在機器上的在內。
◆製程設計1.把單功能作業員變成多功能作業員。
如 : 一人多機、工作輪調、U型生產線2.縮短特定製品的生產時間。
3.排除各製程間不必要的庫存。
4.多功能作業員觀念,減少所需的作業員人數。
5.參與工廠整體生產體系的籌劃,因而對自己的工作更為滿意。
6.每個作業員能從事團隊合作而彼此互相協助。
(八)品管圈( QCC )是指為了解決作業現場存在的問題,而由作業員組成的小團體,自發性並且繼續不斷地研讀品質管理的觀念和技術。
其最終目標是要增進作業員的責任感,提供作業員達成生產目標的方法,並使得作業員的技能得以提高成長。
其研究範圍包括品質管制、成本降低、設備保養、工廠安全、產業公害等。
三、JIT執行步驟(一)豐田生產方式的特徵1.和經營直接有關的公司IE活動:(1)生產計劃予以平準化(2)生產批量愈小愈佳(3)徹底做到必需的物料,在必需時才製造必要的數量2.更重視事實的科學態度(1)反覆的問 5 次「why」(2)使問題一目了然(3)使解決問題的目的明朗化(4)即使只有一個不良品,也要想出對策3.能切身實踐的工數減低活動(1)從作業的改善設備改善(2)工數與人數、省力化與省人化(3)所謂的檢查就是反省4.「經濟性」為一切的判斷基準(1)設備的稼動率,視生產需要量而定(2)有餘力就練習調換機件(3)生產現場才是主角(4)重視應變能力(二) JIT製造的先決條件1.使生產排程穩定2.使工廠集中3.製造中心的生產產能增加4.改善生產品質5.培養多能工6.透過預防保養,以減少設備故障(三) 改革程序 :1.意識改革一教育訓練2.現場改善之基礎: 5S5S---整理、整頓、清掃、清潔、紀律3.JIT的縱面改革生產現狀分析--- P、Q分析、標準流程、 U型生產線、平準化、標準作業4.橫面推展,由一個部門,推展到全公司(四) JIT 成功的七個步驟l. Educatin and leadership 教育和領導力2. Company assessment of JIT elements 實行 JIT 的評估3. Implementation plan 執行 JIT 的計劃4.Pilot implementation 政策執行5. Small group improvement orgamization 小團體的改善組織6. performance evaluation 績效評估7. Company wide transition and internalization 小組擴大實施,不斷轉變和內部化四、JIT-ⅡJIT-Ⅱ? 什麼是JIT-Ⅱ? 它與JIT 有什麼關係 ?我們可說JIT 的目的是要降低成本,達到零庫存或減少庫存的生產方法。