特殊钢棒材的生产工艺技术探讨
棒线材轧制新工艺研究

棒线材轧制新工艺研究【摘要】为了适应市场经济的发展,我国的棒线材轧制技术已经不仅仅是要求产量上的提高,更在轧制的质量和成本的控制上有了更高的要求。
棒线材的轧制技术在不断发展,本文围绕棒线材轧制的新技术、新工艺展开研究,讨论新技术的发展和应用,以提高生产效率,获得更大的经济利益。
【关键词】棒线材;无头轧制技术;低温轧制技术;高精度轧制市场经济的飞速发展,钢铁工业也在不断的发展和进步,激烈的市场竞争使得棒线材轧制的生产制造从仅仅要求产量要满足市场需求,更在轧制的质量、精度上有更高的要求,同时还要充分考虑商品附加值的问题,从而获得更高的经济效益。
企业要在激烈的市场竞争中提高自身的市场竞争力,对棒线材轧制的生产设备和技术进行更新换代是十分必要的。
企业要勇于引进新设备,使用新技术和新工艺,这对加快企业的科技进步,提高生产效益具有重要意义。
1、线棒材轧制技术的发展20世纪中期,线棒材的生产发展迅速,其生产技术的发展方向是高速性和连续性。
以美国摩根公司的两辊水平式轧机和德国施曼公司的平、立交替轧机为代表。
在20世纪60年代,微张力精轧机的开发,和散卷冷却技术的产生促进了高速线材轧机的诞生。
现今轧制技术发展迅速,高精度轧制和低温轧制逐渐发展起来。
控冷技术的发展,使中高碳钢的力学性能不断的发展进步。
在线棒材轧制方面逐步将计算机控制应用其中,从而实现了高速高稳定的轧制。
日渐激烈的市场竞争对棒线材产品质量有了更高的要求,棒线材生产企业要提高自身的市场竞争力,就要在棒线材的生产进行全方面的革新,无论从生产设备上、生产技术还是生产工艺方面,都要进行更新和改进。
企业加大了设备投入和技术研发的力度,新的生产设备和生产技术应运而生。
棒线材的轧制从单方面的追求高产量逐渐向产品高产量、高质量和高产品附加值的方向发展。
面对新的经济形势,企业对棒线材的轧制,要保证其高精度,对产品的组织结构和表面质量都要满足性能的要求;面对市场日新月异的变化,随时能够对钢种及其规格的工艺进行更换;生产的产品覆盖范围广泛,技术上能够满足高附加值产品的开发需要;在生产效率和经济效益方面能够不断的开发新技术,满足不断发展的市场变化。
大规格TZM棒材锻造工艺研究

RE S EAR CH N 0 LAR G E l S ZE ’ ZM oD ’ RG l G I ’ R 0 PR0 CSS
LA G J g , I h n pn L a —pn J N i ja Z A G X n I N i X e g— ig ,IL i ig ,I G L — un , H N i n Z A ( .N r w s R sac ntueF rN n—fr u tlX n7 0 1 S aniC ia 1 o h et eerhIs tt o o t i er sMe , i 10 6,h a x, hn ) o a a
wa a y t rc s e s o c a k,fr i g ca k e sl xe d d x e so tr ltv o r t mp r t e,a d e e r d e h o gn r c a iy e t n e e tn i n a eai e lwe e e aur n v n p o uc d t e
形成 了明显 的纤维组织 。经过 110℃/ 0mn消除应力退火 , 5 3 i 棒材 的纵向抗拉强 度大于 7 0MP 屈服强度 大于 5 a,
6 0MP , 8 a延伸率大 于 2 %。在钼合金坯料单重大 , 5 要求锻造温度高 的情 况下 , 采用普通锻锤加 工人 工操 作难度大 、 效率低 。因此 , 于大规格棒材 , 对 在有条 件的情况下 , 用大吨位挤压机 的先挤 压 、 锻造 的方 式进行可 提高效率 , 采 再
rd + 0 m ) tem ca ia po et s f r ogn n ecr so dn irso i su t ew r s d o s( 8 m xL , eh ncl rpre t riga dt or p n igm cocpc t c r ee t — h i aef h e r u u
hrb500e带肋钢筋棒材及其生产 工艺

hrb500e带肋钢筋棒材及其生产工艺HRB500E带肋钢筋棒材是一种常用的建筑钢材,具有优异的力学性能和耐久性。
本文将介绍HRB500E带肋钢筋棒材的生产工艺及其特点。
一、HRB500E带肋钢筋棒材的生产工艺HRB500E带肋钢筋棒材主要通过以下几个步骤进行生产:1. 原材料准备:HRB500E带肋钢筋棒材的原材料是优质的碳素结构钢,通常采用轧钢厂提供的钢坯作为原材料。
钢坯经过预处理后,进入下一步的加工工艺。
2. 热轧加工:经过预处理的钢坯首先进入连铸机,通过连铸机将钢坯连续铸造成带有规定断面尺寸的钢坯。
然后将钢坯送入热轧机组,经过多道次的热轧,将钢坯轧制成带有纵向肋纹的钢筋棒材。
3. 冷却处理:热轧后的钢筋棒材需要经过冷却处理,以降低其温度并增强其力学性能。
冷却处理通常采用水冷方式,将热轧后的钢筋棒材浸入冷却水中进行快速冷却。
4. 调质处理:为了进一步提高钢筋棒材的强度和韧性,通常采用调质处理。
调质处理是通过加热和保温的方式,使钢筋棒材组织发生相变,得到细小的珠光体和贝氏体结构,从而提高其强度和韧性。
5. 表面处理:为了提高HRB500E带肋钢筋棒材的附着力和抗腐蚀性能,通常会对其表面进行处理。
常见的表面处理方法包括喷丸清理、酸洗处理、磷化处理等。
二、HRB500E带肋钢筋棒材的特点HRB500E带肋钢筋棒材具有以下几个特点:1. 高强度:HRB500E带肋钢筋棒材的强度远高于普通钢材,能够承受较大的拉力和压力。
这使得它在建筑结构中能够起到更好的支撑和抗震作用。
2. 良好的可焊性:HRB500E带肋钢筋棒材具有良好的可焊性,能够与其他钢材进行焊接,方便施工和连接。
3. 优异的韧性:HRB500E带肋钢筋棒材在受力时能够发生塑性变形,具有较好的韧性。
这使得它在抗震和抗风等极端环境下能够更好地保持结构的完整性和稳定性。
4. 良好的耐久性:HRB500E带肋钢筋棒材经过冷却处理和表面处理后,具有较好的耐腐蚀性能,能够在潮湿和腐蚀环境中长期使用。
异型钢管生产工艺

异型钢管生产工艺
嘿,朋友!咱今天来聊聊异型钢管生产工艺这事儿。
你知道吗?异型钢管就像是舞台上的独特舞者,总是能展现出与众
不同的风采。
它的生产工艺,那可是相当有讲究。
先说原材料的选择,这就好比是盖房子选基石,得精挑细选。
要是
原材料不行,后面的工艺再牛,也难出精品。
就像做饭,食材不新鲜,手艺再好也做不出美味佳肴,不是吗?
然后是模具设计,这可太关键啦!模具就像是给钢管定造型的魔法盒,尺寸、形状都得拿捏得死死的。
要是模具设计不合理,那生产出
来的钢管还能叫异型钢管吗?恐怕得成“四不像”喽!
接着是成型工艺。
这一步就像是给雕塑塑形,要精细、要准确。
有
的用冷拔,有的用热轧,就看需要什么样的效果。
这就好比画画,有
的喜欢水墨画的淡雅,有的喜欢油画的浓烈,得选对方法才能出好作品。
还有焊接工艺呢!焊缝的质量直接影响钢管的强度和密封性。
焊缝
处理不好,就像衣服上的破洞,既不美观又不实用。
在整个生产过程中,质量检测更是重中之重!这就好比是给学生考
试打分,一点儿都不能马虎。
要检测尺寸、表面质量、力学性能等等。
一个小瑕疵都可能让整个钢管掉价,你说是不是?
生产异型钢管可不是一件简单的事儿,每一个环节都得像绣花一样精细。
这就像一场精心编排的舞蹈,每个动作都要到位,才能呈现出完美的表演。
总之,异型钢管的生产工艺,那是一门高深的学问,需要技术、经验和细心的完美结合。
只有这样,才能生产出高质量、满足各种需求的异型钢管。
朋友,你说呢?。
棒材制作工艺

棒材制作工艺
棒材制作工艺是一种重要的金属加工工艺,旨在生产高质量、高强度的棒材。
制作工艺通常包括以下几个步骤:
1. 钢坯切割:将钢坯切割成适当长度,以便进一步加工。
2. 热处理:通过加热和冷却,调整钢材的组织和性能,提高钢材的强度和韧性。
3. 精密轧制:将热处理后的钢坯通过辊轧机进行轧制,使其逐渐变细,形成棒材的形状。
4. 拉拔:将精密轧制的棒材通过拉拔机进行拉拔,进一步提高棒材的强度和韧性。
5. 表面处理:通过抛光、喷砂等方法对棒材表面进行处理,提高其表面光洁度和美观度。
6. 检测:对制作出的棒材进行尺寸、质量、性能等方面的检测,确保其符合相关标准和要求。
以上就是棒材制作工艺的主要步骤,其中每个步骤都需要严格控制和精密操作,以确保制作出的棒材质量和性能优良。
- 1 -。
棒线材生产新工艺探究
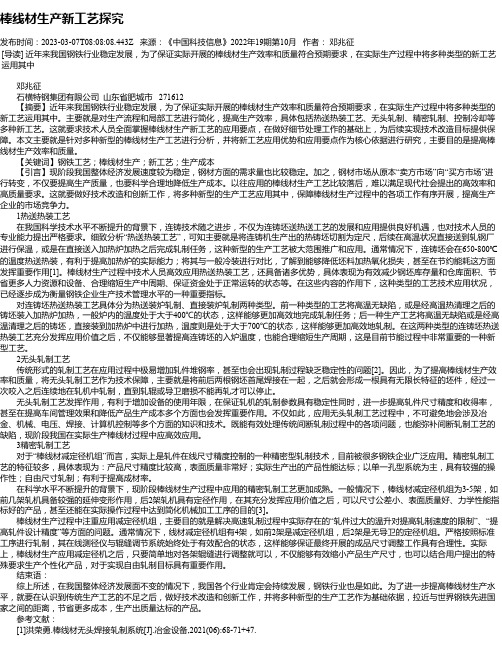
棒线材生产新工艺探究发布时间:2023-03-07T08:08:08.443Z 来源:《中国科技信息》2022年19期第10月作者:邓兆征[导读] 近年来我国钢铁行业稳定发展,为了保证实际开展的棒线材生产效率和质量符合预期要求,在实际生产过程中将多种类型的新工艺运用其中邓兆征石横特钢集团有限公司山东省肥城市 271612【摘要】近年来我国钢铁行业稳定发展,为了保证实际开展的棒线材生产效率和质量符合预期要求,在实际生产过程中将多种类型的新工艺运用其中。
主要就是对生产流程和局部工艺进行简化,提高生产效率,具体包括热送热装工艺、无头轧制、精密轧制、控制冷却等多种新工艺。
这就要求技术人员全面掌握棒线材生产新工艺的应用要点,在做好细节处理工作的基础上,为后续实现技术改造目标提供保障。
本文主要就是针对多种新型的棒线材生产工艺进行分析,并将新工艺应用优势和应用要点作为核心依据进行研究,主要目的是提高棒线材生产效率和质量。
【关键词】钢铁工艺;棒线材生产;新工艺;生产成本【引言】现阶段我国整体经济发展速度较为稳定,钢材方面的需求量也比较稳定。
加之,钢材市场从原本“卖方市场”向“买方市场”进行转变,不仅要提高生产质量,也要科学合理地降低生产成本。
以往应用的棒线材生产工艺比较落后,难以满足现代社会提出的高效率和高质量要求。
这就要做好技术改造和创新工作,将多种新型的生产工艺应用其中,保障棒线材生产过程中的各项工作有序开展,提高生产企业的市场竞争力。
1热送热装工艺在我国科学技术水平不断提升的背景下,连铸技术随之进步,不仅为连铸坯送热送工艺的发展和应用提供良好机遇,也对技术人员的专业能力提出严格要求。
细致分析“热送热装工艺”,可知主要就是将连铸机生产出的热铸坯切割为定尺,后续在高温状况直接送到轧钢厂进行保温,或是在直接送入加热炉加热之后完成轧制任务,这种新型的生产工艺被大范围推广和应用。
通常情况下,连铸坯会在650-800℃的温度热送热装,有利于提高加热炉的实际能力;将其与一般冷装进行对比,了解到能够降低坯料加热氧化损失,甚至在节约能耗这方面发挥重要作用[1]。
PC钢棒生产工艺技术若干问题探讨

Mn
0177 0182 0174 0175 0177 0157 0166 01647 0150 ~ 0180
P
01011 01008 01012 01021 01016 01012 01027 010164
S
产地
01004 日本 01003 日本 01006 日本 01015 韩国 01011 中国台湾
规模的稳定 ,生产厂家为了生存 ,必须降低生产成本 、 量 < 1%。韩国浦项公司和德国 SAARSTAHL AG公司
提高产品质量 ,而这些措施除了管理上的改进外 ,工艺 技术上的提高是首要考虑的途径 。目前国产 PC钢棒 存在的主要质量问题有以下几个方面 : PC钢棒抗延迟 断裂能力弱 ;力学性能不稳定 ,同一批甚至同一条 PC 钢棒的力学性能波动幅度大 ;平直度差 ;热镦性能差 , 表现为镦头开裂及镦头处的力学性能较母材降低过
式中 :σ012 —屈服强度 , M Pa; L —回归常数 , L = 1230 ~ 1270。
根据这些经验公式 ,可以得到控制 PC 钢力学性
能 、优化工艺参数的方法 。例如已知 0130% C、113%
M n、018% Si的原料在 k = 1、b = 1195、t1 = 950℃时 ,为
得到 1460M Pa的抗拉强度 ,根据 (3)式计算 t2 的值 :
factor ies( wt%)
试样序号
1 2 3 4 5 最小值 最大值 平均值
控制范围
C
0132 0128 0137 0130 0129 0134 0138 01358 0132 ~ 0140
Si
0126 1144 1180 1169 1170 0194 1106 11007 0190~ 1120
基于棒材生产中新工艺新技术的应用探讨

宽度 即为轧后 自由宽展宽度 , 没 有传统 孔型侧 壁的夹持 , 实
和控 制冷 却技术等 。 为 企业带来 了发 展。本文采用 “ 节能 、 减 现 自由宽展 。无孔 型轧 制技术 与传统 有孔 型轧制 技术 相比 , 排、 降本 、 增 效” 新 工艺 , 应用 到棒材生 产过程 中 , 无论棒 材 优 点如 下 : ( 1) 无 需对轧 辊开槽 , 轧辊辊 身硬度层 得到充 分 生产数量 、 规格 , 还是技术水平 以及产 品质量 , 都有 了很大 水 利 用 , 其耐 磨性好 , 有利 于提 高轧辊 使用 寿命 ; ( 2) 平辊 机
[
…
基于棒材生产 中新工艺新技术的应用探讨
张 国琪
( 江 苏 申特钢 铁 有 限公 司 , 江苏 常』 、 I ' 1 2 1 3 3 0 0 )
摘要 : 随 着 钢铁 行 业 不断 发展 ,市场 竞 争加 剧 , 钢 铁 企 业 纷纷 应 用 新 技 术 、 新工艺, 增 强 自身竞 争 力 。 本 文仅 对 棒 材 生
Di sc u ss i on on Appl i c a t i on of Ne w T e ch nol og y an d Ne w T ec hn ol o gy Ba s e d on Bar Pr od uc t i on
ZHANG Gu o - q i
着重解 决以 下四个 问题 ’ : ( 1) 放弃切 分轧制 , 通 过提高 终 轧速 度来提高 其生产 能力 ; ( 2) 解 决好棒材 高速轧 制 中存 在 的振动 , 轴承发热轧辊磨损及主电机动 态速 降等 问题 ; ( 3) 实 现棒 材轧制过程 的控 轧控冷 ,提高其机 械性能 ; ( 4) 解决 好 小规格棒材高速上冷床的问题 。因此 , 棒材生产也吸收许多新 技术新工艺 , 如 : 切分轧制技术 、 无孔型轧 制技 术 、 控 制轧 制
特殊钢棒线材扎制工艺技术的发展
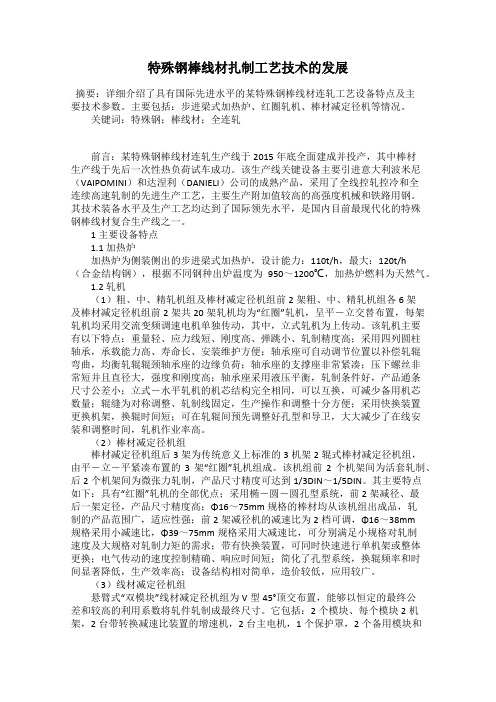
特殊钢棒线材扎制工艺技术的发展摘要:详细介绍了具有国际先进水平的某特殊钢棒线材连轧工艺设备特点及主要技术参数。
主要包括:步进梁式加热炉、红圈轧机、棒材减定径机等情况。
关键词:特殊钢;棒线材;全连轧前言:某特殊钢棒线材连轧生产线于2015年底全面建成并投产,其中棒材生产线于先后一次性热负荷试车成功。
该生产线关键设备主要引进意大利波米尼(VAIPOMINI)和达涅利(DANIELI)公司的成熟产品,采用了全线控轧控冷和全连续高速轧制的先进生产工艺,主要生产附加值较高的高强度机械和铁路用钢。
其技术装备水平及生产工艺均达到了国际领先水平,是国内目前最现代化的特殊钢棒线材复合生产线之一。
1 主要设备特点1.1 加热炉加热炉为侧装侧出的步进梁式加热炉,设计能力:110t/h,最大:120t/h(合金结构钢),根据不同钢种出炉温度为950~1200℃,加热炉燃料为天然气。
1.2 轧机(1)粗、中、精轧机组及棒材减定径机组前2架粗、中、精轧机组各6架及棒材减定径机组前2架共20架轧机均为“红圈”轧机,呈平-立交替布置,每架轧机均采用交流变频调速电机单独传动,其中,立式轧机为上传动。
该轧机主要有以下特点:重量轻、应力线短、刚度高、弹跳小、轧制精度高;采用四列圆柱轴承,承载能力高、寿命长、安装维护方便;轴承座可自动调节位置以补偿轧辊弯曲,均衡轧辊辊颈轴承座的边缘负荷;轴承座的支撑座非常紧凑;压下螺丝非常短并且直径大,强度和刚度高;轴承座采用液压平衡,轧制条件好,产品通条尺寸公差小;立式-水平轧机的机芯结构完全相同,可以互换,可减少备用机芯数量;辊缝为对称调整、轧制线固定,生产操作和调整十分方便;采用快换装置更换机架,换辊时间短;可在轧辊间预先调整好孔型和导卫,大大减少了在线安装和调整时间,轧机作业率高。
(2)棒材减定径机组棒材减定径机组后3架为传统意义上标准的3机架2辊式棒材减定径机组,由平-立-平紧凑布置的3架“红圈”轧机组成。
H13钢连轧棒材轧制工艺研究
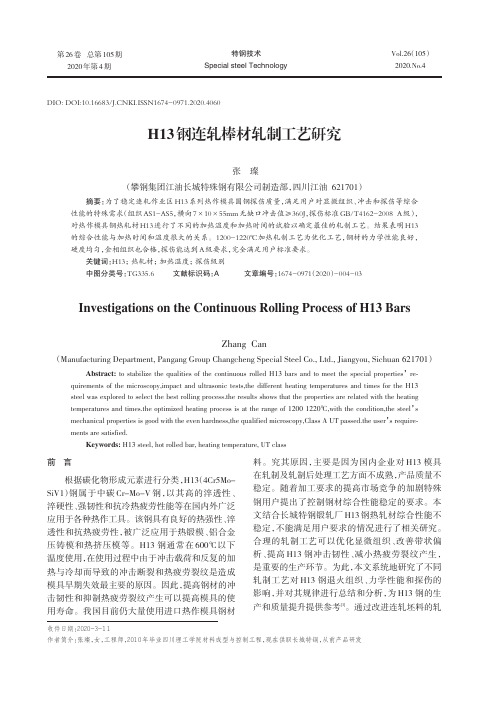
DIO:DOI:10.16683/KI.ISSN1674-0971.2020.4060前言根据碳化物形成元素进行分类,H13(4Cr5Mo-SiV1)钢属于中碳Cr-Mo-V 钢,以其高的淬透性、淬硬性、强韧性和抗冷热疲劳性能等在国内外广泛应用于各种热作工具。
该钢具有良好的热强性、淬透性和抗热疲劳性,被广泛应用于热锻模、铝合金压铸模和热挤压模等。
H13钢通常在600℃以下温度使用,在使用过程中由于冲击载荷和反复的加热与冷却而导致的冲击断裂和热疲劳裂纹是造成模具早期失效最主要的原因。
因此,提高钢材的冲击韧性和抑制热疲劳裂纹产生可以提高模具的使用寿命。
我国目前仍大量使用进口热作模具钢材料。
究其原因,主要是因为国内企业对H13模具在轧制及轧制后处理工艺方面不成熟,产品质量不稳定。
随着加工要求的提高市场竞争的加剧特殊钢用户提出了控制钢材综合性能稳定的要求。
本文结合长城特钢锻轧厂H13钢热轧材综合性能不稳定,不能满足用户要求的情况进行了相关研究。
合理的轧制工艺可以优化显微组织、改善带状偏析、提高H13钢冲击韧性、减小热疲劳裂纹产生,是重要的生产环节。
为此,本文系统地研究了不同轧制工艺对H13钢退火组织、力学性能和探伤的影响,并对其规律进行总结和分析,为H13钢的生产和质量提升提供参考[1]。
通过改进连轧坯料的轧H13钢连轧棒材轧制工艺研究张璨(攀钢集团江油长城特殊钢有限公司制造部,四川江油621701)摘要:为了稳定连轧作业区H13系列热作模具圆钢探伤质量,满足用户对显微组织、冲击和探伤等综合性能的特殊需求(组织AS1-AS5,横向7×10×55mm 无缺口冲击值≥360J,探伤标准GB/T4162-2008A 级),对热作模具钢热轧材H13进行了不同的加热温度和加热时间的试验以确定最佳的轧制工艺。
结果表明H13的综合性能与加热时间和温度很大的关系。
1200-1220℃加热轧制工艺为优化工艺,钢材的力学性能良好,硬度均匀,金相组织也合格,探伤能达到A 级要求,完全满足用户标准要求。
棒材生产工艺流程
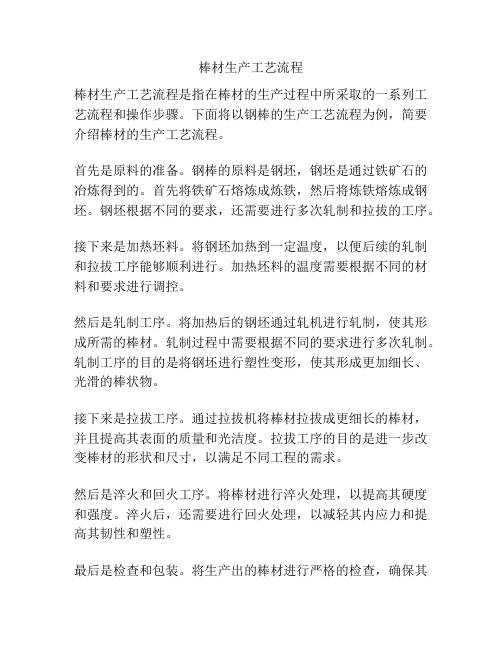
棒材生产工艺流程
棒材生产工艺流程是指在棒材的生产过程中所采取的一系列工艺流程和操作步骤。
下面将以钢棒的生产工艺流程为例,简要介绍棒材的生产工艺流程。
首先是原料的准备。
钢棒的原料是钢坯,钢坯是通过铁矿石的冶炼得到的。
首先将铁矿石熔炼成炼铁,然后将炼铁熔炼成钢坯。
钢坯根据不同的要求,还需要进行多次轧制和拉拔的工序。
接下来是加热坯料。
将钢坯加热到一定温度,以便后续的轧制和拉拔工序能够顺利进行。
加热坯料的温度需要根据不同的材料和要求进行调控。
然后是轧制工序。
将加热后的钢坯通过轧机进行轧制,使其形成所需的棒材。
轧制过程中需要根据不同的要求进行多次轧制。
轧制工序的目的是将钢坯进行塑性变形,使其形成更加细长、光滑的棒状物。
接下来是拉拔工序。
通过拉拔机将棒材拉拔成更细长的棒材,并且提高其表面的质量和光洁度。
拉拔工序的目的是进一步改变棒材的形状和尺寸,以满足不同工程的需求。
然后是淬火和回火工序。
将棒材进行淬火处理,以提高其硬度和强度。
淬火后,还需要进行回火处理,以减轻其内应力和提高其韧性和塑性。
最后是检查和包装。
将生产出的棒材进行严格的检查,确保其
质量符合要求。
合格的棒材经过质检后,还需要进行包装,以便于运输和储存。
综上所述,棒材生产工艺流程包括原料的准备、加热坯料、轧制、拉拔、淬火和回火、检查和包装等一系列工序。
每个工序都有其特定的目的和要求,通过这些工序的处理,最终得到质量合格的棒材。
论西宁特钢棒材轧制工艺和设备选择

论西宁特钢棒材轧制工艺和设备选择通过对西宁特钢的轧制工艺和设备选择进行了阐述,使读者对合金钢棒材生产工艺和设备选择有一定了解。
标签:合金钢棒材;合金钢生产工艺;工艺设计中图分类号:TB文献标识码:A文章编号:16723198(2012)130186011工艺布置方案的选择对于热轧棒材来说工艺布置方案主要分为连轧(中间一般设置脱头区)和半连轧布置。
1.1半连轧布置方式一般为一架二辊可逆轧机+连轧机(6架或者8架)布置。
二辊轧机一般带机前机后翻钢和推床,连轧机一般为平/立布置,或者也有立/平布置。
采用立/平布置主要考虑为来料为矩形坯时不必翻钢。
1.2连轧布置方式一般为粗轧机组(4架或者6架轧机,一般优选4架轧机)、第一中轧机组、第二中轧机组、精轧机组、减定径机组布置。
2坯料的选择合金钢棒材生产坯料主要选用为锻坯、轧坯、连铸坯、钢锭、电轧锭。
坯料选择主要根据钢种、压缩比等要求。
2.1钢种对坯料的要求锻、轧坯:(莱氏体及马氏体)、高工、合工(冷模具)、不锈(马氏体、双相钢)。
连铸坯:碳结、合结、(碳工)、弹簧、轴承(圈)、不锈(奥氏作、铁素体)。
钢锭(或电渣):轴承(珠)、合金模具(莱氏体及马氏体)。
2.2压缩比对坯料的要求压缩比大小对轧材产品影响方面主要包括:中心疏松、疲劳性质、表面质量。
连铸坯最小断面应根据钢种的最小压缩比和生产的产品的最大断面来选择,如果产品规格范围比较大,连铸坯可多选用几个断面规格。
2.3坯料断面形状选择对轴承钢优选矩形坯,对中心疏松有利,但是对轧钢孔形设计不利。
其它钢种主要以有利孔型设计为主以及连铸过程中尽可能减少疏松的断面为主。
3轧线工艺设备选择3.1轧机的选择(1)平均延伸系数和轧制道次。
轧制道次在选择过程中主要受到压缩比和平均延伸系数的限制,根据压缩比最大的轧件计算平均延伸系数,根据计算出的平均延伸系数来选择轧机数量。
其它压缩比较小的在设计轧制道次的过程中也需要考虑品均延伸系数。
棒材轧钢工艺介绍

a
10
➢ 思考题: ➢ 1、轧制时采用切分轧制的优缺点有哪些? ➢ 2、为什么圆钢轧制时不采用切分轧制?
a
11
三、棒材多线切分生产工艺分析
➢ 切分轧制生产具有高产、低耗的特点,其中 多线切分对提高产量、降低主机电耗的效果更为 显著,但是由于多线切分时条形的不对称性,获 得各线之间均匀的条形成为切分生产过程中的一 个难点,尤其在对产品精度要求较高的情况下(如 在钢筋生产过程中要求负偏差接近国标下限时), 多线切分各线之间的不均匀性更是成为生产过程 中的一大障碍。
a
图5 新工艺设计原理图
18
➢ 因此,在这个道次中,即使三个单元之间切分 得不太均匀,也可以由后面第13道次进行二次切 分来补救。
➢ 通过了第11道和第12道的轧件,进入第13道时 的条形基本上是宽度合适、不均匀变型已经基本 消化的条形,这样的条形再经过第13道次的二次 预切分和第14道次对宽度的进一步整理,进入第 15道时其条型宽度及形状已与 孔 型完全匹配,而 第15道 孔 型的轮廓与第13道是基本相似的,所以 第15道次已经基本属于均匀变型的轧制过程了, 即可以把第14道次孔型的宽度设计得与第15道次 的宽度接近。这样 孔 型本身对条型就有较好的扶 持作用,这样就解决了第15道预切分超负荷的问 题。
图4 第14到16道孔型示意图
a
13
➢ 在此工艺中,第15道次孔型的任务是在 平板条形上切出凹凸截面花生型条形,属 于严重不均匀变型状态,本道次轧制时宽 展量很大。因此,第14道次条形宽度须明 显小于第15道孔型。同时,第15道孔型本 身对轧件缺少对中扶持的能力,这是造成 多线切分各线之间不均匀性的主要原因。
➢ (3)切分道次切分楔磨损严重,换槽频繁,同时切分
高速棒材的轧制工艺及优势
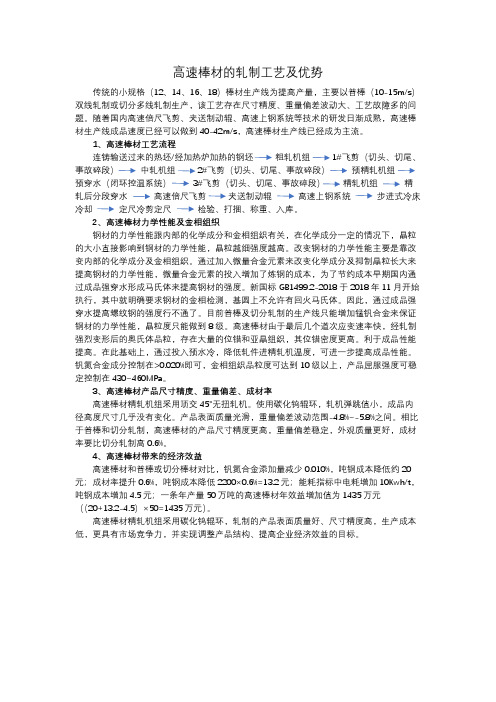
高速棒材的轧制工艺及优势传统的小规格(12、14、16、18)棒材生产线为提高产量,主要以普棒(10-15m/s)双线轧制或切分多线轧制生产,该工艺存在尺寸精度、重量偏差波动大、工艺故障多的问题。
随着国内高速倍尺飞剪、夹送制动辊、高速上钢系统等技术的研发日渐成熟,高速棒材生产线成品速度已经可以做到40-42m/s,高速棒材生产线已经成为主流。
1、高速棒材工艺流程连铸输送过来的热坯/经加热炉加热的钢坯 粗轧机组 1#飞剪(切头、切尾、事故碎段) 中轧机组 2#飞剪(切头、切尾、事故碎段) 预精轧机组预穿水(闭环控温系统) 3#飞剪(切头、切尾、事故碎段) 精轧机组 精轧后分段穿水 高速倍尺飞剪 夹送制动辊 高速上钢系统 步进式冷床冷却 定尺冷剪定尺 检验、打捆、称重、入库。
2、高速棒材力学性能及金相组织钢材的力学性能跟内部的化学成分和金相组织有关,在化学成分一定的情况下,晶粒的大小直接影响到钢材的力学性能,晶粒越细强度越高。
改变钢材的力学性能主要是靠改变内部的化学成分及金相组织。
通过加入微量合金元素来改变化学成分及抑制晶粒长大来提高钢材的力学性能,微量合金元素的投入增加了炼钢的成本,为了节约成本早期国内通过成品强穿水形成马氏体来提高钢材的强度。
新国标GB1499.2-2018于2018年11月开始执行,其中就明确要求钢材的金相检测,基圆上不允许有回火马氏体。
因此,通过成品强穿水提高螺纹钢的强度行不通了。
目前普棒及切分轧制的生产线只能增加锰钒合金来保证钢材的力学性能,晶粒度只能做到8级。
高速棒材由于最后几个道次应变速率快,经轧制强烈变形后的奥氏体品粒,存在大量的位错和亚晶组织,其位错密度更高。
利于成品性能提高。
在此基础上,通过投入预水冷,降低轧件进精轧机温度,可进一步提高成品性能。
钒氮合金成分控制在>0.020%即可,金相组织品粒度可达到10级以上,产品屈服强度可稳定控制在430~460MPa。
特种钢的制备与性能研究
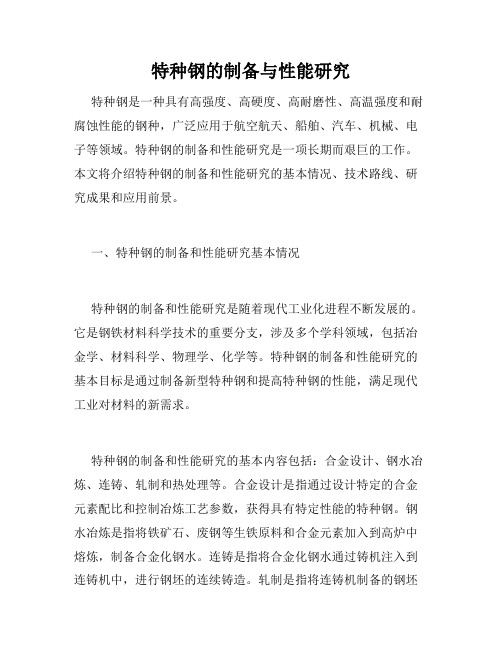
特种钢的制备与性能研究特种钢是一种具有高强度、高硬度、高耐磨性、高温强度和耐腐蚀性能的钢种,广泛应用于航空航天、船舶、汽车、机械、电子等领域。
特种钢的制备和性能研究是一项长期而艰巨的工作。
本文将介绍特种钢的制备和性能研究的基本情况、技术路线、研究成果和应用前景。
一、特种钢的制备和性能研究基本情况特种钢的制备和性能研究是随着现代工业化进程不断发展的。
它是钢铁材料科学技术的重要分支,涉及多个学科领域,包括冶金学、材料科学、物理学、化学等。
特种钢的制备和性能研究的基本目标是通过制备新型特种钢和提高特种钢的性能,满足现代工业对材料的新需求。
特种钢的制备和性能研究的基本内容包括:合金设计、钢水冶炼、连铸、轧制和热处理等。
合金设计是指通过设计特定的合金元素配比和控制冶炼工艺参数,获得具有特定性能的特种钢。
钢水冶炼是指将铁矿石、废钢等生铁原料和合金元素加入到高炉中熔炼,制备合金化钢水。
连铸是指将合金化钢水通过铸机注入到连铸机中,进行钢坯的连续铸造。
轧制是指将连铸机制备的钢坯通过热轧机进行加工成具有特定厚度和宽度的特种钢板。
热处理是指通过将特种钢板加热和冷却处理的方法,改善特种钢的性能和组织结构。
二、特种钢的制备和性能研究技术路线特种钢的制备和性能研究技术路线包括:合金设计、钢水冶炼、连铸、轧制和热处理等。
其中合金设计是特种钢制备和性能研究的关键。
钢铁行业通过对新型合金配比的研究和冶炼工艺的改进,可以大大提高特种钢的力学性能和耐腐蚀性能。
合金设计要考虑特种钢所需的性能指标,并根据这些指标筛选合适的元素进行配比,最终制备出适用于特定应用场合的特种钢。
例如,航空航天领域需要的特种钢要求强度高、韧性好、耐腐蚀性好,因此需要加入具有高强度、高韧性和耐腐蚀性能的特殊合金元素。
钢水冶炼是实现特种钢制备和性能研究的关键环节。
冶炼工艺要根据特种钢所需的合金元素调整配比和控制炉温、氧化还原等参数,以确保合金元素在钢铁中充分溶解和均匀分布。
几种棒线材生产的新工艺

国内高速线材生产已有近30年历史,产量从几十万t发展到超过5000万t,最大轧制速度从10m/s提高到120m/s以上,尺寸精度的控制从±0.30mm进步到±0.10mm,强度波动范围从±50MPa减小到±10MPa。
近些年国内外又出现了许多新的线材生产工艺及技术。
棒线材生产新工艺和新技术主要分两类:一是通过微合金化强化或工艺强化机理,提高棒线材强度或塑性,如碳纳米管技术、超细晶钢生产技术、超快冷工艺、线材在线盐浴处理工艺等;二是通过流程简化和局部工艺优化,提高生产节奏,降低生产成本,如连铸连轧工艺、热装热送工艺、无头轧制技术和超短流程工艺等。
下面简要介绍其中的添加碳纳米管提高强度技术、超细晶钢生产技术、控制网碳析出的超快冷工艺、盐浴控冷工艺和条材短流程工艺等几种最新工艺和技术。
纳米材料又称为超微颗粒材料,由纳米粒子组成。
在炼钢的出钢过程或精炼过程,加入压制后附有一定钝化层的碳纳米管(可防止其被高温氧化,并提高了碳纳米管的收得率)。
经充分搅拌后,碳纳米管均匀分布在钢基中,既起到弥散强化的作用,还可在轧制过程中阻止奥氏体晶粒长大,进而达到细晶强化的目的。
现取得良好的应用效果,添加微量碳纳米管后制成的线材强度平均提高30~50MPa。
影响碳纳米管广泛应用的最大制约因素在于其制造成本高,但随着其制造技术的提高,可预见添加纳米碳纤维管提高钢的强度在未来必定会普遍应用。
纳米微粒还可用来作催化剂。
冶炼过程中,催化剂作用主要是控制反应时间、提高反应效率和反应速度。
我国目前所生产的低碳钢,铁素体晶粒度一般为ASTMNo.8~9级,即晶粒尺寸相当于14~20μm,根据Hall-Petch公式,现在大量生产的碳素结构钢,只要把晶粒细化到小于5μm,其强度就可以由200MPa提高到400MPa以上。
对低合金钢晶粒细化至2μm左右,强度可提高到800MPa以上。
因此,实现晶粒超细化非常重要,而关键是探索细化的理论和工艺技术。
轧钢棒线材生产新技术探析

轧钢棒线材生产新技术探析摘要:本文阐述了传统轧制工艺的缺点与无头轧制工艺的优点,并对无头轧制工艺及棒线材轧制技术的发展进行了分析与探讨,以供同仁参考。
关键词:棒线钢材;轧制技术;生产工艺一、前言近年来,随着我国经济建设的不断发展,我国各行业技术以及综合的竞争能力也在不断的增强,轧钢的发展也取得了比较辉煌的进步,其在轧钢的制造工艺以及生产线的成套装备技术方面都取得了比较显著的进展。
下面就对传统轧制工艺的缺点与无头轧制工艺的优点进行阐述,并对无头轧制工艺及棒线材轧制技术的发展进行了分析与探讨,以供同仁参考。
二、传统轧制工艺的缺点与无头轧制工艺的优点(1)传统轧制工艺的缺点。
传统轧制工艺是间歇加工,生产率较低,加工过程冲击与作业载荷大,设备的使用寿命短,维修率比较高,系统的稳定性较差,轧制过程轧件两端与中间部位受力不同,造成两端与中间尺寸不同,加工质量也受到一定的影响。
(2)无头轧制工艺的优点。
无头轧制是匀速连续轧制,不是间歇加工,因而生产效率较高,加工时载荷恒定并且冲击很少,设备的使用寿命长,维修率低,而且产品的质量较好,系统的稳定性较高,产品的长度没有限制,需要时根据购货方的需求进行切割,成品率高。
三、无头轧制工艺系统的主要组成无头轧制系统与传统轧制系统的最大区别是无头轧制系统有以下几个装置,送进装置、除鳞装置、焊接装置、去毛装置、摆动辊、保湿装置、焊机液压站和去毛刺液压站(见图1)四、棒线材无头轧制技术分析(1)钢坯除鳞。
因为轧制钢坯的预热温度要求较高,所以钢坯和附近环境内的氧气能够互相作用,容易在其表面形成一层较厚的氧化铁皮。
钢坯除鳞即是在钢坯进行焊接之前,消除其头部与尾部1.5m范围内,表面1mm左右的氧化铁皮。
现阶段在采用无头轧制生产工艺的钢坯除鳞装置一般都选择动态除鳞技术,由于钢坯表层的氧化铁皮清除相对较慢,若选择静态除磷技术不但会降低其温度,提高钢坯尖角破裂的概率,同时还可能会降低轧线的工作效率。
PC钢棒的生产工艺及其产品性能

PC钢棒的生产工艺及其产品性能范玫光孙本荣( 轧钢工程事业部 )摘要:PC钢棒是高档次预应力钢材的新品种,本文介绍了该产品性能特点及发展趋势,针对产品的原料、生产、热处理工艺、标准及其发展提出了观点。
关键词:PC钢棒新品种发展1、前言从1994年在广东国产PC钢棒生产线的顺利投产到我国YB/T111-1997预应力混凝土用钢棒标准的发布,我国管桩用PC钢棒的生产得到了很大的发展,尤其是近几年来在原料盘条的选择、生产工艺的优化、产品性能的稳定方面积累了不少的经验。
本文从调整PC钢棒生产工艺入手,总结出原料盘条的化学成分,钢棒的淬火温度、回火温度,冷却方式,水冷方式和张拉力对其性能的影响,并且获得了良好的效果。
为我公司建设更加完善的PC钢棒生产设备建立了坚实的基础。
2、试验用钢和试验方法试验用钢的化学成分如表1,盘条为国产高速线材轧机生产的无扭热轧盘条。
表1 试验用钢的化学成分试验在由我公司转让的国内某厂PC钢棒生产线上进行,高线盘条经机械除锈后,经螺旋模变形20%形成螺旋槽,然后进入热处理生产线,进行矫直、中频与超音频感应加热、水冷淬火、中频感应加热、水冷、剪断和松卷收线。
试样在每盘产品的头、尾部取样,进行了拉伸试验金相检验和松弛试验。
3、试验结果与分析3.1、淬火加热温度对力学性能的影响试验用钢属于低中碳硅锰低合金钢,从稳态热处理的角度来看,使钢棒实现奥氏体化的加热温度应该为840~860℃,然而本生产线采用感应加热方式,其特点是加热速度快,加热时间短,钢棒表面透热深度小,所以要求其加热温度应比稳态热处理时的淬火加热温度要高。
本试验选择的温度范围为880~960℃,试验结果见表2。
从表2可以看出,随着淬火温度的提高,钢棒的抗拉强度和屈服强度都有所提高,当淬火温度从880℃提高到960℃时,各试验用钢的屈服强度增幅大于抗拉强度的增幅。
而伸长率随着淬火温度的提高都有所下降。
这一结果反映出了钢中添加了微量的合金元素V会随着淬火加热温度的提高,使其固溶到奥氏体中的量有所增加,在随后的冷却相变过程中会以弥散的V(C、N)形式折出,起到弥散强化的作用,4#钢虽然没有微量的V加入,但是添加了微量的B,B同样也起到了强化钢棒的作用。
特殊钢棒线材生产技术的进步
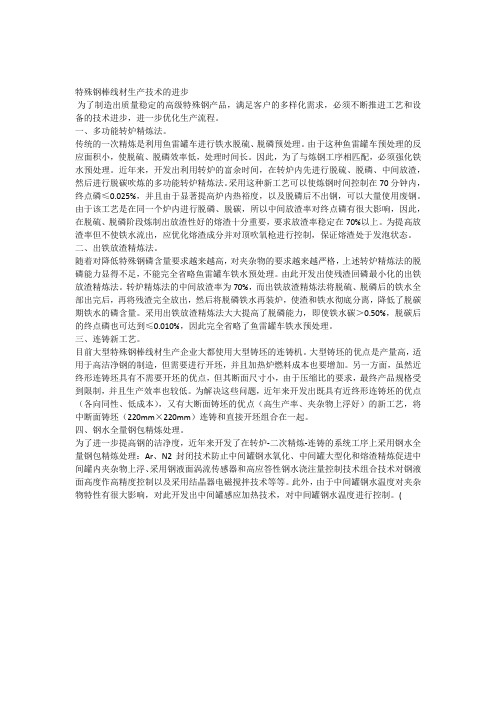
特殊钢棒线材生产技术的进步为了制造出质量稳定的高级特殊钢产品,满足客户的多样化需求,必须不断推进工艺和设备的技术进步,进一步优化生产流程。
一、多功能转炉精炼法。
传统的一次精炼是利用鱼雷罐车进行铁水脱硫、脱磷预处理。
由于这种鱼雷罐车预处理的反应面积小,使脱硫、脱磷效率低,处理时间长。
因此,为了与炼钢工序相匹配,必须强化铁水预处理。
近年来,开发出利用转炉的富余时间,在转炉内先进行脱硫、脱磷、中间放渣,然后进行脱碳吹炼的多功能转炉精炼法。
采用这种新工艺可以使炼钢时间控制在70分钟内,终点磷≤0.025%,并且由于显著提高炉内热裕度,以及脱磷后不出钢,可以大量使用废钢。
由于该工艺是在同一个炉内进行脱磷、脱碳,所以中间放渣率对终点磷有很大影响,因此,在脱硫、脱磷阶段炼制出放渣性好的熔渣十分重要,要求放渣率稳定在70%以上。
为提高放渣率但不使铁水流出,应优化熔渣成分并对顶吹氧枪进行控制,保证熔渣处于发泡状态。
二、出铁放渣精炼法。
随着对降低特殊钢磷含量要求越来越高,对夹杂物的要求越来越严格,上述转炉精炼法的脱磷能力显得不足,不能完全省略鱼雷罐车铁水预处理。
由此开发出使残渣回磷最小化的出铁放渣精炼法。
转炉精炼法的中间放渣率为70%,而出铁放渣精炼法将脱硫、脱磷后的铁水全部出完后,再将残渣完全放出,然后将脱磷铁水再装炉,使渣和铁水彻底分离,降低了脱碳期铁水的磷含量。
采用出铁放渣精炼法大大提高了脱磷能力,即使铁水碳>0.50%,脱碳后的终点磷也可达到≤0.010%,因此完全省略了鱼雷罐车铁水预处理。
三、连铸新工艺。
目前大型特殊钢棒线材生产企业大都使用大型铸坯的连铸机。
大型铸坯的优点是产量高,适用于高洁净钢的制造,但需要进行开坯,并且加热炉燃料成本也要增加。
另一方面,虽然近终形连铸坯具有不需要开坯的优点,但其断面尺寸小,由于压缩比的要求,最终产品规格受到限制,并且生产效率也较低。
为解决这些问题,近年来开发出既具有近终形连铸坯的优点(各向同性、低成本),又有大断面铸坯的优点(高生产率、夹杂物上浮好)的新工艺,将中断面铸坯(220mm×220mm)连铸和直接开坯组合在一起。
赛钢棒 加工工艺
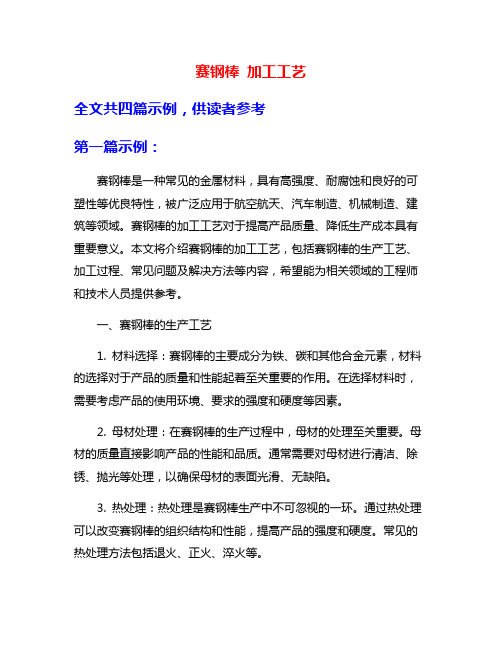
赛钢棒加工工艺全文共四篇示例,供读者参考第一篇示例:赛钢棒是一种常见的金属材料,具有高强度、耐腐蚀和良好的可塑性等优良特性,被广泛应用于航空航天、汽车制造、机械制造、建筑等领域。
赛钢棒的加工工艺对于提高产品质量、降低生产成本具有重要意义。
本文将介绍赛钢棒的加工工艺,包括赛钢棒的生产工艺、加工过程、常见问题及解决方法等内容,希望能为相关领域的工程师和技术人员提供参考。
一、赛钢棒的生产工艺1. 材料选择:赛钢棒的主要成分为铁、碳和其他合金元素,材料的选择对于产品的质量和性能起着至关重要的作用。
在选择材料时,需要考虑产品的使用环境、要求的强度和硬度等因素。
2. 母材处理:在赛钢棒的生产过程中,母材的处理至关重要。
母材的质量直接影响产品的性能和品质。
通常需要对母材进行清洁、除锈、抛光等处理,以确保母材的表面光滑、无缺陷。
3. 热处理:热处理是赛钢棒生产中不可忽视的一环。
通过热处理可以改变赛钢棒的组织结构和性能,提高产品的强度和硬度。
常见的热处理方法包括退火、正火、淬火等。
4. 成型加工:成型加工是赛钢棒生产的关键环节。
通过冷拉、热轧、锻造等方法,将母材加工成所需形状和尺寸的赛钢棒。
成型加工需要根据产品的要求选择合适的加工方法和工艺参数。
5. 表面处理:赛钢棒的表面处理包括镀锌、喷涂、抛光等,可以提高产品的耐腐蚀性和美观度。
表面处理需要考虑产品的使用环境和要求,选择合适的处理方法和工艺。
二、赛钢棒的加工过程1. 切割:在赛钢棒的加工过程中,常见的第一步是切割。
切割主要是将赛钢棒切割成所需长度,通常采用锯床、切割机等设备进行切割。
2. 粗加工:粗加工是赛钢棒的主要加工步骤之一,包括车削、铣削、钻孔等。
粗加工的目的是将赛钢棒加工成初步形状,为后续精加工做准备。
3. 精加工:精加工是对赛钢棒进行细致加工的过程,包括磨削、抛光、磨床等。
精加工可以提高产品的表面光滑度和精度,确保产品的质量。
4. 调质处理:赛钢棒在加工过程中可能因受热变形而产生应力,需要进行调质处理。
- 1、下载文档前请自行甄别文档内容的完整性,平台不提供额外的编辑、内容补充、找答案等附加服务。
- 2、"仅部分预览"的文档,不可在线预览部分如存在完整性等问题,可反馈申请退款(可完整预览的文档不适用该条件!)。
- 3、如文档侵犯您的权益,请联系客服反馈,我们会尽快为您处理(人工客服工作时间:9:00-18:30)。
特殊钢棒材生产工艺技术探讨
河北钢铁集团
石家庄钢铁有限责任公司
2014.10
二、特殊钢棒材主要应用领域及产品特点、
发展趋势
特殊钢主要应用领域
□民用:包括汽车、机械、铁路、能源、矿山、船舶、环保等行业。
□军工:航空、航天、舰船、兵器、核工业等行业
特殊钢产品特点
满足不同服役条件下钢材的特殊性能要求,和普通钢相比特殊钢往往要求钢材具有更高的洁净度、组织成分的均匀性以及优良的表面质量和尺寸精度。
四、关键工艺技术
1、转炉冶炼工序
铁水废钢钢水合金料烤窑合金料出钢氩气搅拌顶底复吹转炉精确挡渣
转炉冶炼工序示意图
关键工艺技术问题
□原辅料理化指标、放射性检测问题
□原辅料中含有的B、Ni等元素对淬
透性影响问题
□铁前吃低价料降成本,带来铁水中
P、Ti等元素含量高,冶炼难度增加
问题
□合金含量增加,合金烘烤问题突出
□纯净度要求提高,出钢下渣污染钢
水问题
四、关键工艺技术
严把入炉原料关:
□需严格控制铁水中的残余元素Cr、Ni、Cu、Sn、As等含量,保证钢材使用性能和质量的稳定性,轴承钢还需控铁水Ti含量。
□高品质特殊钢铁水的P、S必须严格控制在一定范围
□入厂废钢及其它原辅料理化指标及放射性检测
□合金烘烤:入炉合金料须经进行烘烤,控制钢中H及O含量
□监控合金等原辅料中对钢材性能有影响的元素含量
□炉子大小:
大炉子比小炉子生产过程的稳定性好,对特殊钢的窄成份控制、窄淬透性控制、纯净钢的生产更稳定;但特钢品种多、批量小,小炉子对市场的适应性更强,企业应根据自身情况和市场状况进行选择
□转炉冶炼工艺
顶底复吹转炉采用底吹气搅拌,配合顶吹氧枪搅拌,提高冶炼过程反应动力学条件,吹炼终点C、P、S等元素的均匀性要优于顶吹转炉
□挡渣出钢:挡渣锥、挡渣球、滑板挡渣等出钢几种方式中,滑板挡渣的效果相对要好
□炉后扒渣设施:扒掉钢包顶渣,重新造渣,对低Ti、低氧、低P 等高洁净钢的生产更有优势
2、LF炉精炼工序
钢水
氮气搅拌氩气搅拌
窄成分控制
特殊精炼渣料合金料称量微正压炉盖LF精炼示意图
优转特LF精炼关键技术问题
□高均质化要求对窄成份、窄淬透性控制要求提高□钢中夹杂物的有效去除问题
□S、N等特殊元素控制问题
□含硫钢低氧含量与高硫含量的冶金矛盾问题
□与钢水接触的所有原辅料理化等指标与特钢相适应要求
2、LF炉精炼工序
□脱氧:采用铝脱氧更为广泛
□造渣:采用多种特殊渣料,针对不同钢种特性,造不同碱度渣系,基本上以高碱度渣系为主,同时注意保证冶炼过程炉渣性能的稳定性,促进钢水的窄成分控制及洁净度提高
□吹氩搅拌技术:针对精炼升温过程、加合金调成分、软吹氩去夹杂等不同过程的冶金任务,需建立不同流量供氩制度,确保钢水搅拌均匀和夹杂物的有效去除
窄成分控制
□要求准确计量:原辅料、合金料、钢水量
□脱氧效果要好:高碱度渣系、白渣时间控制、在脱氧良好的情况下微调合金
□保证足够的软吹氩时间:尽量在精炼前、中期调好成分,精炼末期不再加入合金,保证足够的软吹时间,促进化学成分和温度的均匀性□增S、增N工艺:喂丝技术的应用
□取样的代表性:为窄成份控制提供保证
□在线建立快速分析及数据共享系统
钢水
氩气搅拌
全程监控控制溢渣过称合金料
计算丝线喂入量
真空脱气
定氢仪
定H 喂线镇静处理3、真空脱气处理工序
合金含量高、规格大的特殊钢须经真
空脱H处理,防止棒材出现白点、内裂
等缺陷,常采用RH、VD等脱气手段。
须具有足够的真空处理能力和达到相
应的处理效果
Heraeus
定氢仪
真空脱气
□在真空处理方式上
VD炉真空脱气相比下投资成本低,但处理时间长、处理过程钢渣混合,夹杂物不能充分上浮,影响纯净度;
RH投资高、但处理时间短、效率高,且真空精炼过程钢水与渣子不混合,比VD炉更利于提高钢水纯净度。
□一般特殊钢采用VD炉就够用了,高纯净的钢建议采用RH 炉
□钙处理:对夹杂物进行变性处理、改善连铸可浇性,但在高纯净度钢生产过程中,精炼效果和钢水可浇性有保证前提下,部分高纯净钢不能进行钙处理(二次氧化)
□喂线工艺:某些须加S、Al、N等元素的特殊钢,在真空处理后须调成份,为准确控制成份需经喂线处理,适用于低氧高S、高Al、含N等系列钢的生产。
□软吹氩技术
控制流量,保持足够长软吹氩时间,促进钢中夹杂物碰撞、上浮、吸附。
4、连铸工序
铸坯
钢水结晶器中间包氩气隔绝空气
长水口保护
大包下渣检测氩气排空
吸渣剂、覆盖剂保护结晶器液位自动控制
浸入式水口电磁搅拌动态二
冷配水自动助燃切割缓冷坑末端电磁搅拌连续测温
连铸生产常遇到的工艺技术问题
□连铸坯均质性控制问题
□纯净度控制:钢包下渣、中间包下渣污染钢水问题□保护浇注效果不好
□连铸坯表面质量控制难题
□连铸坯解决内裂(白点)问题
洁净度控制
□在精炼效果良好前提下,一般钢种采用大包下渣检测设备即可满足夹杂物要求,对夹杂物零缺陷要求的高纯净度钢必须增加其它手段,如大包剩钢操作
□非稳态坯、正常坯的分开管理(头坯、尾坯、正常坯的分类管理)
□全程保护浇注技术(密封+吹氩)
□水口选型:中间包整体水口保护效果好于分体式水口
□结晶器液位自动控制系统,减少液面
波动,液面波动大的坯子需隔离
□中间包冶金技术:水模试验和数值模
拟,优化中包流场,减少死区
□建立不同钢种的保护渣体系
□保持适当的钢水静置时间,促进钢中
夹杂物上浮
□采用高端耐火材料
大包下渣检测示意图
均质性控制
□适当的过热度控制(建议应用中间包加热技术)
□连铸浇钢恒拉速操作(优于拉速随过热度变的拉速控制)
□采用结晶器电磁搅拌+末端电磁搅拌,优化参数减轻偏析
□大方坯轻压下技术
□二冷气水雾化
□采用结晶器液位自动控制系统,保证稳态浇注,减少液面波动带来的卷渣
□轧钢:采用蓄热式加热炉,优化连铸坯加热使偏析元素充分扩散(加热温度、加热时间)
□中间包钢水加热技术:感应加热技术、等离子加热技术(新日铁),感应加热装置应用较为普遍,利于提高铸坯组织的均质性□轻压下技术:大方坯可有效改善凝固末端组织,小方坯应用不好将坯子压扁
□内部裂纹控制:
考虑合适的二次冷却方式、连铸坯缓冷等
□表面质量控制方面:
连铸坯考虑合适的二次冷却速度、合适的保护渣体系、合适的过热度、拉速控制等,连铸坯、钢材的修磨等
5、轧制工艺技术
□加热制度:采用蓄热式加热炉,轴承钢加热时间长与弹簧钢表面脱碳问题矛盾,轴承钢可考虑两个加热炉
□尺寸精度控制问题(孔型设计、轧机及轧辊选择、活套控制、KOCKS轧机、减定径机组、设备管理等)
□表面质量控制问题(折叠、耳子、棒材表面麻点、划伤等,滚动代替滑动、检查)
□内裂(白点):钢材缓冷,缓冷坑、缓冷房
□CrMo钢等硬度要求钢种冷床快进控制问
□特殊钢种温升速率控制问题
□高表面质量要求钢材:采用钢坯火焰清理+KOKS轧机高精度轧制
□控轧控冷技术:棒材适用于小规格
五、效果及体会
□窄成分控制效果(16MnCr5)
轿车齿轮用钢16MnCr5成品C、Mn、
Cr窄成分控制效果:C控制范围达到
±0.01%,Mn和Cr达到±0.02%,
2012年比2009的成份分布范围更窄
□窄淬透性控制效果
图28 日本本田对石钢SCM420H端淬评价石钢SCM420H
(20CrMoH)齿轮钢的淬透带宽控制在29-32HRC的窄范围内,完全达到了日本本田轿车用钢要求水平。
石钢材日本材
石钢20CrMoH材带状
组织0~1.5级,平均
为1.0级,而日本材
带状0~1.0级,带状
组织与日本材相当
左图为日本本田汽车对石钢SCM420H金相组织和带状组织的评价,带状组织完全满足本田要求
□带状组织控制效果
日本NSK对比分析日本材与石钢材洁净度
石钢S48C、SCr420微观洁净度、宏观洁净度均满足日本NSK轿车用钢规范要求,实现向NSK轿车零部件生产厂(大众汽车)稳定供钢。
宏观洁净度对比
微观洁净度对比
□尺寸精度控制效果
◎热轧材尺寸公差控制到±0.2mm以内,不圆度控制在0.2mm以内,而国内其它特钢厂尺寸公差一般控制±0.35mm内(GB/T 702的2组)◎银亮材直径公差≤IT10,不圆度≤直径公差的50%,表面粗糙度≤3.2μm
返回Ф13.2mm圆钢尺寸精度图53 Ф13.2mm圆钢不圆度
几点体会:
□普钢向特钢转型质量意识是前提、管理是根本、设备是保证,人才是关键(包括技术人才、岗位操作人员)
□建立“零缺陷”的质量管控体系
□要注意工序流程优化、匹配问题
□一切以客户为中心开展各项工作,提升市场服务意识
□技术营销、生产技术销售一体化是与用户联系的纽带
□用户的所有要求都不过分,用户的要求是我们持续进步的动力源泉
谢谢!
欢迎各位专家批评指正!。