支座压铸模具毕业设计
压铸模具 毕业设计

支座冲压工艺分析及模具毕业设计

毕业设计任(论文)务书填表时间: 20**年 03月 30日 (指导老师填表)指导老师签字: 教研室主任签字: 年 月 日学 生姓 名专业 机械制造 与自动化 班级 指导老师 课题 类型 工程设计题 目支座冲压工艺分析及模具设计研 究内 容 1.查阅有关冲压模具设计方面的资料,翻译相关英文文献。
2.对冲压制件进行结构和工艺性分析,选择合理的工艺及模具设计方案。
3.进行必要的参数计算,确定设计参数。
4.进行总体及零部件设计,绘制总装机零件图并撰写设计说明书。
课题要求、任务及数量(指图纸规格、张数等)1.培养学生综合运用知识的能力及绘图能力等。
2.查阅有关模具方面的资料,翻译不少于3000汉字的英文文献。
3.制定工艺及模具设计方案,绘制装配图、零件图。
要求结构合理,计算正确并完成三张零号图纸的工作量。
4.按照格式正确撰写设计说明书一份,不少于8000字进 度计 划 5-7周(4.9-4.20) 查阅资料,英文翻译,开题报告。
8-10周(4.23-5.4) 进行方案设计和工艺计算。
11-12周(4.30-5.21) 绘制总体装配图。
13-14周(5.28-6.4) 绘制零件图。
15-16周(6.11-6.18) 撰写设计说明书。
17周(6.25-6.27) 答辩主 要参 考文 献 [1] 卢险峰. 冲压工艺模具学 机械工业出版社,2006,4,第二版。
[2] 李学峰. 模具设计与制造实训 化学工业出版社,2005,1,第一版。
[3] 卢险峰. 中国模具设计大典 第三卷 机械工业出版社。
[4] 《模具设计与制造简明手册》 冯炳尧等 上海科学技术出版社。
支座冲压工艺分析及模具设计摘要本次设计了一套冲孔、落料的模具。
经过查阅资料,首先要对零件进行工艺分析,经过工艺分析和对比,采用冲孔落料工序,通过冲裁力、顶件力、卸料力等计算,确定压力机的型号。
再分析对冲压件加工的模具适用类型选择所需设计的模具。
压铸工艺与模具设计毕业论文

压铸工艺与模具设计毕业论文一、选题的依据及意义本课题来源于江铃汽车集团公司骨干企业,江铃汽车集团公司车厢饰件厂的全资子公司,江铃有色金属压铸厂。
该公司成立于2002年5月。
工厂总投入资金为四千万元人民币,自建立起就本着高起点,现代化的原则,工厂以生产铝合金压铸件及其加工为主,已为江铃汽车、奇瑞汽车及中华汽车配套生产变速器及发动机零部件,产品已出口欧洲,工厂还可生产路灯灯罩、电梯踏板、电机壳体等其它铝合金压铸件。
产品图如下所示:压力铸造是近代金属加工工艺中发展较快的一种少无切削的特种铸造方法。
它是将熔融金属在高压高速下充填铸型,并在高压下结晶凝固形成铸件的过程。
高压高速是压力铸造的主要特征。
常用的压力为数十兆帕,填充速度(浇口速度)约为16~80米/秒,金属液填充模具型腔的时间极短,约为0.01~0.2秒。
压力铸造特点如下:一、优点:(1)可以制造形状复杂、轮廓清晰、薄壁深腔的金属零件。
(2)压铸件的尺寸精度较高,可达IT11~IT13级,有时可达IT9级,表面粗糙度达Ra0.8~3.2um,有时达Ra0.4um,互换性好。
(3)材料利用率高。
(4)可以将其他材料的嵌件直接嵌铸在压铸件上。
(5)压铸件组织致密,具有较高的强度和硬度。
(6)可以实现自动化生产。
二、缺点:(1)由于高速充填,快速冷却,形腔中气体来不及排出,致使压铸件常有气孔及氧化夹杂物存在,从而降低了压铸件质量。
(2)压铸机和压铸模质量昂贵,不适合小批量生产。
(3)压铸件尺寸受到限制。
(4)压铸合金种类受到限制。
在此之上还发展出多种特殊压铸工艺,以解决压铸件的气孔和疏松问题。
迄今为止主要有真空压铸、充氧压铸、精速密压铸、半固态压铸等。
由于用这种方法生产产品具有生产效率高,工序简单,铸件公差等级较高,表面粗糙度好,机械强度大,可以省去大量的机械加工工序和设备,节约原材料等优点,且其缺点可以通过特殊压铸得到有效的克服,所以现已成为我国铸造业中的一个重要组成部分。
压铸模具毕业设计(论文)任务书

[4]陈金城,翟春泉.快速成长中的中国压铸机制造业[J].特种铸造及有色合金2010
[5] 许琳主 金属压铸工艺与模具设计 清华大学出版社 2006;
[6] 潘宪曾 成形工艺与现代模具设计丛书 电子工业出版社 2006
[7]徐平、王韶峰、基于Pro/E的数控加工技术研究与应用[J] 煤矿机械,2008
[8]王亦新,印飞,洪慎章.挤压铸造的应用与模具材料[J].机械工程材料,2000
[9] 晋兵营、欧阳凯伊 Pro/ENGINEER Wildfire中文版模具设计 电子共业出版社 2009
[10] 王立新 UGNX5.0模具设计案例实践 清华大学出版社 2008年
[11]崔向坡 《铸造技术》维普资讯网2009 第8期
3)查阅有关模具设计书查询
4)进行零件的建模到NC组件操作的全过程
5)进行其他零件的试行加工
6)对型腔的分析和画图
2、研究目标:
对铝合金端盖的模具设计进行加工,能掌握Pro/E软件的运用,并能熟练操作。在操作过程中能发现问题和解决问题。巩固所学的知识,熟悉有关资料,掌握设计方法,完成设计任务。
研究方法
[12] 李德群 《现代模具设计方法》 机械工业出版社 1998
[13]周永泰 我国冲压模具的现状与发展[J] 锻造与冲压 2005
[14]黄毅宏、李明辉 [模具制造工艺][M] 机械工业出版社 1999
[15]郑佳贤 冲压模具设计入门 机械工业出版社 2007
[16]许发樾 模具标准化与原型结构设计 机械工业出版社 2009
在设计过程中,可以充分利用图书馆和网络资源,了解和认识Pro/E软件三维建模的应用,并对零件的模具型腔进行分析,进行分模,分出动模、定模、等,掌握零件的装配,画出平面图和三维图。能完成整个加工过程。
机械课设 毕业论文 侧弯支座冲压模具及工艺设计

机械课设毕业论文侧弯支座冲压模具及工艺设计一、设计背景与意义侧弯支座是桥梁中常用的一种构配件,用于承受桥面荷载并传递到桥墩上,其作用十分重要。
然而,传统侧弯支座制作工艺复杂,成本高,且破坏率较高,容易导致桥梁的运行安全问题。
因此,研究一种新型的冲压成形工艺,加工出符合要求的侧弯支座成为了迫在眉睫的课题。
本文以侧弯支座为研究对象,结合机械制造和材料力学等知识,探讨了侧弯支座冲压模具及工艺设计的问题,旨在为侧弯支座的制造提供一种高效、经济、可靠的制造方法,为桥梁的运行安全保障做出贡献。
二、设计过程及设计方案1、材料选择侧弯支座对材料的选择要求非常高,必须满足强度高、抗疲劳性好、韧性好等特点。
根据实际应用情况及探测数据,本文选用Q345B钢板作为侧弯支座的材料。
2、模具设计本文的冲压模具采用固定式下压的方式进行成形,整个冲压过程分为以下几步:(1)将Q345B钢板切割成符合尺寸的工件。
(2)在冲压机上设置合适的模具,按照要求将工件固定在上模上,下模下压。
(3)通过机器进行成形加工,即对工件进行冲压成形。
模具部件:1)上模座板2)上模板3)下模板4)导向柱5)固定板6)挡料3、工艺设计(1)模具结构设计本模具采用固定式下压模具,上模和下模在压力的作用下合拢夹紧工件,使其进行成形冲压。
此种模具具有设计过程简单,操作简便,不易出现变形的优点。
(2)工艺分析为了减小冲压中工件的扭曲和翘曲,需要增加辅助冲压,从而保证产品成形要求。
工件冲压过程中应注意保证上、下模心一致,使成品在冲压过程中得到充分发挥,使产品在其设计寿命中具有稳定的性能。
(3)工艺参数通过在试验中反复调整,确定以下参数:1)冲头规格:Φ852)压力:40KN3)冲压时间:5s4)成形过程中保持上、下模心一致三、设计结果与分析经过一系列试验和工艺调整,成功制造出符合要求的侧弯支座产品,其性能稳定,强度高,耐疲劳性好,可靠性高,具有较强的抗震能力和抗水腐蚀能力。
支座铸造工艺毕业论文

支座铸造工艺毕业论文本文介绍了支座铸造工艺的相关背景和应用,详细阐述了支座铸造工艺流程和方法,探讨了支座铸造工艺中的材料选择和质量控制。
最后,提出了支座铸造工艺存在的问题和改进措施。
一、背景介绍支座是一种常见的机械零件,用于支撑设备或组件。
支座广泛应用于化工、制药、食品等行业,该领域的发展为支座铸造工艺的提升和创新提供了机会。
支座铸造工艺是通过铸造技术来生产该零件,其生产成本低、生产效率高,具有广泛的应用前景。
二、支座铸造工艺流程1.模具制备支座铸造的第一步是模具制备。
选择具有合适形状和尺寸的铸造模具,并将其涂抹上脱模剂,以便后续的模具脱模。
2.熔炼原材料将铸造材料,如铸铁、铸钢、铜、铝等材料,加入熔炉中进行熔炼,并添加合适的合金元素,以达到所需的材料化学成分。
3.铸造过程将熔融的金属注入模具中,然后静置,直到铸造材料凝固成型。
在铸造过程中,必须控制合金的温度、流动速度和氧化状态,以保证铸造质量。
4.去毛刺将成型支座从模具中取出,并进行去毛刺和砂型清洗。
5.表面处理进行表面处理,包括砂喷、抛光和涂漆等过程。
6.质量检验进行质量检验,以确保支座强度、硬度和尺寸精度符合设计要求。
三、材料选择和质量控制1.材料选择支座铸造工艺的材料选择将影响产品的性能和成本。
常见的支座材料有灰铸铁、球墨铸铁、铸钢、红铜和铝合金等。
根据具体应用场景,选择合适的支座材料,满足强度要求的同时尽可能降低成本。
2.质量控制支座铸造工艺的质量控制是确保支座产品性能和外观质量的关键。
对铸造温度、流速、浇注位置和氧化情况等参数进行严格控制,以确保产品成型质量。
此外,对于成型后的支座产品,进行温度处理、去毛刺和表面处理等工艺,以确保最终产品质量。
四、存在问题及改进措施1.存在问题支座铸造工艺存在生产效率低、产量不稳定、质量难以保证等问题。
2.改进措施为了缓解上述问题,可以采取以下改进措施:(1)优化生产流程,确保生产效率。
(2)引入智能化设备,提高产量稳定性。
毕设论文——铝支座精密成型及模具设计
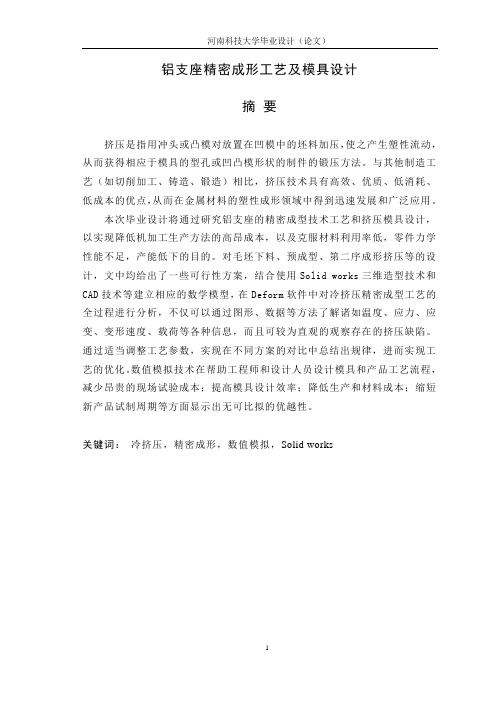
铝支座精密成形工艺及模具设计摘要挤压是指用冲头或凸模对放置在凹模中的坯料加压,使之产生塑性流动,从而获得相应于模具的型孔或凹凸模形状的制件的锻压方法。
与其他制造工艺(如切削加工、铸造、锻造)相比,挤压技术具有高效、优质、低消耗、低成本的优点,从而在金属材料的塑性成形领域中得到迅速发展和广泛应用。
本次毕业设计将通过研究铝支座的精密成型技术工艺和挤压模具设计,以实现降低机加工生产方法的高昂成本,以及克服材料利用率低,零件力学性能不足,产能低下的目的。
对毛坯下料、预成型、第二序成形挤压等的设计,文中均给出了一些可行性方案,结合使用Solid works三维造型技术和CAD技术等建立相应的数学模型,在Deform软件中对冷挤压精密成型工艺的全过程进行分析,不仅可以通过图形、数据等方法了解诸如温度、应力、应变、变形速度、载荷等各种信息,而且可较为直观的观察存在的挤压缺陷。
通过适当调整工艺参数,实现在不同方案的对比中总结出规律,进而实现工艺的优化。
数值模拟技术在帮助工程师和设计人员设计模具和产品工艺流程,减少昂贵的现场试验成本;提高模具设计效率;降低生产和材料成本;缩短新产品试制周期等方面显示出无可比拟的优越性。
关键词:冷挤压,精密成形,数值模拟,Solid worksAluminum Bearing Precision Forming Technology and DieDesignABSTRACTExtrusion punch or punch and refers to the use of the billet placed in die pressure, to produce plastic flow, which corresponds to the mold of hole or concave and convex shape of parts forging method. With other manufacturing processes, such as machining, casting, forging, extrusion technology has high efficiency, high-quality, low consumption, low cost advantages, thus in the field of plastic forming of metal material get rapid development and wide application.This graduation design will through the study of precision molding technology aluminum bearing process and extrusion die design, in order to achieve lower machining method is the high cost of production, and to overcome the low material utilization, insufficient mechanical properties, low capacity. The purpose of Under the blank material, preforming, second order design of extrusion forming, etc, are given in this paper some feasible solutions, combined with Solid works 3 d modelling technology and establish the corresponding mathematical model of CAD technology, in the Deform software to analyze the whole process of cold extrusion for precision molding process, not only can be through the graphics, data and other methods to understand, such as temperature, stress, strain, strain rate, load, etc all kinds of information, and can be more intuitive extrusion defects existing in the observation. By properly adjusting process parameters, implementation in different scheme comparison, summed up the regularity in achieving process optimization. Numerical simulation technology in helping engineers and designers to design mould and product process flow, reduce the cost of expensive field test; Improve the efficiency ofdie design; Reduce the production and the cost of materials; Shorten the new product trial production period, etc, show the incomparable superiority .KEY WORDS:cold extrusion,,precision forming,numerical simulation ,Solid works前言................................................... 第一章设计零件的工艺分析及方案选择.....................§ 1.1 任务零件...................................§ 1.2 任务零件的工艺分析及工艺参数的计算.........§ 1.3 任务零件方案初步选择 .......................§ 1.4 冷挤压力的计算 .............................§ 1.4.1冷挤压变形程度及许用变形程度..........§ 1.4.2冷挤压力的计算........................§ 1.5 坯料的前期处理 .............................§ 1.5.1下料..................................§ 1.5.2坯料的表面处理及润滑.................. 第二章任务零件的三维造型设计、模拟分析及设备选取..........§ 2.1凸、凹模的Solid works三维造型设计..........§ 2.1.1凸模的设计.................................§ 2.1.2凹模的设计.................................§ 2.2挤压过程的模拟分析 ..............................§ 2.2.1模拟前准备、前处理、后处理..............§ 2.2.2模拟结果分析 ..............................§ 2.3 液压机的选取..................................... 第三章铝支座冷挤压模具设计.............................§ 3.1 冷挤压模具装配简图及其工作原理 .............§ 3.2 模具设计要点 ...............................§ 3.2.1 凸模设计 ............................§ 3.2.2 组合凹模设计 ........................§ 3.2.3 预应力圈设计 ........................ 结论................................................... 参考文献................................................ 致谢...................................................挤压,特别是冷挤压,材料利用率高,材料的组织和机械性能得到改善,操作简单,生产率高,可制作长杆、深孔、薄壁、异型断面零件,是重要的少无切削加工工艺。
毕业设计说明书铸造工艺模具设计

目录1 绪论12 结构分析22.1立柱的结构分析和功用22.1.1立柱的功用22.1.2 立柱的结构分析22.2审图及校核23 工艺方案分析33.1 铸造工艺方案中浇注位置和分型面的确定原则33.1.1 浇注位置的确定原则33.1.2 分型面的确定原则33.2 工艺方案的分析和确定43.2.1 方案一:以立柱导轨背面为分模面(树脂砂造型)43.2.2 方案二:以立柱导轨的中心对称线为分模面(树脂砂造型)44 工艺参数54.1铸件最小铸出壁厚54.2 机械加工余量54.3 最小铸出孔和槽74.4 不铸出面74.5铸造收缩率74.6 冷铁放置计算84.7 分型负数的选择84.8 拔模斜度94.9铸件在砂箱冷却时间95 砂芯及砂型设计115.1 砂芯设计115.1.1 芯头设计115.1.2 排气设计115.1.3 分芯原则115.1.4 分芯方案125.2 外模设计126 浇冒口系统设计146.1 浇注系统的概述和作用146.2 浇注系统的组成及其各自作用146.3浇注系统的设计156.4出气孔设计186.4.1出气孔的作用及设置原则186.4.2出气孔的分类及尺寸197 砂箱的设计207.1 砂箱尺寸的确定20参考文献致附录1 绪论铸造业发展简介铸造是一种古老的制造方法,在我国可以追溯到6000年前。
随着工业技术的发展,铸大型铸件的质量直接影响着产品的质量,因此,铸造在机械制造业中占有重要的地位。
铸造技术的发展也很迅速,特别是19世纪末和20世纪上半叶,出现了很多的新的铸造方法,如低压铸造、瓷铸造、连续铸造等,在20世纪下半叶得到完善和实用化[2]。
由于现今对铸造质量、铸造精度、铸造成本和铸造自动化等要求的提高,铸造技术向着精密化、大型化、高质量、自动化和清洁化的方向发展,例如我国这几年在精密铸造技术、连续铸造技术、特种铸造技术、铸造自动化和铸造成型模拟技术等方面发展迅速。
中国铸造工艺装备同先进国家相比还有一定差距。
模具毕业设计135压铸模设计毕业设计

1 压铸工艺概论压力铸造是将熔融合金在高压、高速条件下充型,并在高压下冷却凝成形的精密铸造方法,简称比铸。
在压铸生产中,压铸合金、压铸模和压铸机是最基本的三大要素,而压铸生产就是将此三大要素加以组合、调整和正确实施的过程。
1.1 压铸生产过程和特点1.1.1 压铸生产过程压铸生产过程包括压铸模在压铸机上的安装与调整、对模具必要部位喷涂涂料、模具预热、安放镶嵌件、闭模、将熔融合金舀取倒入压室、压射(高压高速)成型、铸件冷却后脱模和压铸件清理等过程。
1.1.2压铸特点由于压铸时熔融合金在高压高速下充型,冷却速度快,因此有如下优点:1.压铸件尺寸精度高 压铸件尺寸精度一般可达IT11~IT13,最高可达IT9,表面粗糙度可达 3.2~0.4u R Ra m 。
因此,压铸件可不经机械加工或个别表面只需少量机械加工就可直接使用,既提高了金属利用率,又节省了机械加工工时。
2.压铸件组织致密、硬度和强度较高 由于熔融合金在压铸模内冷却迅速,同时又在高压下结晶,因此在压铸件上靠近表面的一层金属晶粒较细,组织致密,表面硬度和强度较高,但伸长率较低。
3.可生产薄壁、形状复杂和轮廓清晰的铸件 锌合金压铸件最小壁厚可为0.3mm ,铸孔孔径最小值可达0.7mm ,螺纹的最小螺距能达0.75mm 。
同时,也可以压铸清晰的文字、图案和符号等。
4.可采用镶铸法简化装配和制造工艺 将事先准备好的与浇注金属不同材料零件,放入压铸模中规定部位,压铸后零件被固定在压铸件中,这种压铸方法称为镶铸法(又称嵌铸法)。
它既可满足特定部位的使用要求,又可简化装配和制造工艺。
5.生产效率高,易实现机械化和自动化生产 —般冷压室压铸机每小时可压铸75~80次,热压室压铸机平均每小时可压铸370~870次,当采用“一模多腔”时,产量还可以成倍增加。
尤其是压铸过程是在压铸机上实现的,故易实现生产过程的机械化和自动化。
尽管压铸生产有上述优点,但也存在以下缺点:1.压铸件易出现气孔和缩松由于充型时间短,金属液在压铸模内凝固速度快,因此,型腔中的气体很难完全排出,补缩也困难,致使铸件容易产生气孔和缩松,铸件壁越厚越严重,故压铸件壁厚一般在4.5~6mm以下。
本科毕业设计-支撑架压铸模cad设计及cae成型仿真

安徽建筑工业学院毕业设计(论文)专业机械设计制造及其自动化班级08机械一班学生姓名王涛学号08210010113课题支撑架压铸模三维CAD设计及CAE成型仿真指导教师赵茂俞2012年6 月1 日支撑架压铸模CAD设计及CAE成型仿真中文摘要首先,分析支撑架压铸件的结构工艺,提出几种不同的压铸工艺方案,计算环形浇口尺寸、弯销尺寸、充填速度、温度、压实压力等工艺参数,完成压铸模结构设计。
然后,确定模具分型面和浇注系统,借助PRO/E三维软件,对支撑架零件三维造型,解决模具的结构设计。
在此基础上,应用CAE软件PROCAST 仿真支撑架充填、凝固过程,优化压铸模具结构设计。
再次,绘制模具装配图、零件工程图,同时校核模具关键零件的强度。
最终表明该模具结构合理,制造工艺良好,工作稳定可靠。
关键词:压铸模;环形浇口;弯销;分型面;Pro/E;CAESupport frame Die-Casting Mould CAD / CAEABSTRACTIn this thesis, firstly, the structures of the Support frame die-casting were analyzed. The structure of die casting die was designed through the analysis of various process planning and the calculations of technological parameters of ring gate, bent pin, speed, temperature, pressure, etc. Secondly, the mold parting surface and gating system must be determined. By using 3D PRO/E software, the die-casting model and the mould structure had been drawn. On the basis, the design of die-casting mould structure was optimized through the application of CAE software PROCAST simulating the pressure filling and solidification course. Then, the Mold assembly drawings, parts drawings were drawn and the key parts intensity was checked. Finally, the conclusions show that the mold structure is reasonable, stable, reliable and the mould has good manufacturing processes.Keywords: Die-casting mould;ring gate;bent pin;mould surface;Pro/E;CAE目录第一章前言 --------------------------------------------------------------------------------------------------------------------------- 01.1 课题的提出----------------------------------------------------------------------------------------------------------------- 01.2 国内外压铸研究的现状------------------------------------------------------------------------------------------------- 01.2.1国外压力铸造业的现状------------------------------------------------------------------------------------------ 01.2.2国内压力铸造业的现状------------------------------------------------------------------------------------------ 01.3设计的内容和目标--------------------------------------------------------------------------------------------------------- 11.3.2.重点需要研究的问题------------------------------------------------------------------------------------------- 31.3.3.完成任务可能思路和方案 ------------------------------------------------------------------------------------ 31.3.4.设计的目标 ------------------------------------------------------------------------------------------------------- 3 第二章支撑架压铸件的结构工艺性分析 -------------------------------------------------------------------------------------- 42.2压铸合金的化学成分和性能 -------------------------------------------------------------------------------------------- 42.2压铸件的尺寸精度--------------------------------------------------------------------------------------------------------- 42.2.1.影响压铸件的精度的主要因素 ------------------------------------------------------------------------------ 42.2.2.压铸件的轮廓性尺寸------------------------------------------------------------------------------------------- 5压铸件的轮廓性尺寸 ---------------------------------------------------------------------------------------------------- 52.3 压铸件的形位公差 -------------------------------------------------------------------------------------------------------- 62.4 壁厚--------------------------------------------------------------------------------------------------------------------------- 72.5 铸造圆角半径 -------------------------------------------------------------------------------------------------------------- 72.6 脱模斜度 -------------------------------------------------------------------------------------------------------------------- 72.7 压铸件的表面质量 -------------------------------------------------------------------------------------------------------- 72.8 加工余量 -------------------------------------------------------------------------------------------------------------------- 7 第三章金属压铸件压铸工艺------------------------------------------------------------------------------------------------------ 93.1 压力参数 -------------------------------------------------------------------------------------------------------------------- 93.2 速度参数 -------------------------------------------------------------------------------------------------------------------103.3 时间参数 -------------------------------------------------------------------------------------------------------------------103.3.1.填充时间------------------------------------------------------------------------------------------------------------ 113.3.2.持压时间------------------------------------------------------------------------------------------------------------ 113.3.3.留模时间------------------------------------------------------------------------------------------------------------ 113.4 温度参数 ------------------------------------------------------------------------------------------------------------------- 113.4.1.浇注温度------------------------------------------------------------------------------------------------------------ 113.4.2模具温度------------------------------------------------------------------------------------------------------------123.5 成型收缩率 ----------------------------------------------------------------------------------------------------------------123.5.1.压铸件的收缩率的影响因素 --------------------------------------------------------------------------------123.5.2.铝合金的计算收缩率------------------------------------------------------------------------------------------133.6 液态铝合金的密度 -------------------------------------------------------------------------------------------------------133.7 压铸用涂料 ----------------------------------------------------------------------------------------------------------------133.7.1.压铸涂料的作用------------------------------------------------------------------------------------------------133.7.2.对涂料的要求 ---------------------------------------------------------------------------------------------------133.8 压铸件的后处理 ----------------------------------------------------------------------------------------------------------143.8.1.压铸件的清理 -----------------------------------------------------------------------------------------------------143.8.2.压铸件浸渗处理------------------------------------------------------------------------------------------------143.8.3.压铸件的表面处理---------------------------------------------------------------------------------------------143.8.4.压铸件的热处理------------------------------------------------------------------------------------------------143.8.5.压铸件的整形处理 -----------------------------------------------------------------------------------------------15 第四章铸件基本参数的计算与压铸机的选用-------------------------------------------------------------------------------164.1 压铸机的种类和特点----------------------------------------------------------------------------------------------------164.1.1.热室压铸机---------------------------------------------------------------------------------------------------------164.1.2.卧式冷压室压铸机 -----------------------------------------------------------------------------------------------164.1.3.立式冷压室压铸机 ----------------------------------------------------------------------------------------------174.1.4.全立式冷压室压铸机 --------------------------------------------------------------------------------------------174.1.5.本次设计压铸机种类选用--------------------------------------------------------------------------------------174.2 确定型腔数目及布置形式----------------------------------------------------------------------------------------------174.3 确定压实压力 -------------------------------------------------------------------------------------------------------------174.4 压铸机锁模力的确定----------------------------------------------------------------------------------------------------184.5 计算胀型力 -----------------------------------------------------------------------------------------------------------194.6 核定投影面积 -------------------------------------------------------------------------------------------------------------204.7 初步选定压铸机 ----------------------------------------------------------------------------------------------------------20 第五章压铸模分型面的设计-----------------------------------------------------------------------------------------------------22 第六章浇注系统和溢流、排气系统的设计----------------------------------------------------------------------------------236.1 浇注系统的分类 ----------------------------------------------------------------------------------------------------------236.2 内浇口的设计 -------------------------------------------------------------------------------------------------------------256.3 直浇道的设计 -------------------------------------------------------------------------------------------------------------266.4 横浇道的设计 -------------------------------------------------------------------------------------------------------------286.5 溢流槽的设计 -------------------------------------------------------------------------------------------------------------296.3 排气槽的设计 -------------------------------------------------------------------------------------------------------------316.4 预测可能出现的压铸缺陷及处理方法------------------------------------------------------------------------------31 第七章压铸模抽芯机构的设计 -------------------------------------------------------------------------------------------------327.1常用抽芯机构的类型----------------------------------------------------------------------------------------------------327.2抽芯力和抽芯距的确定-------------------------------------------------------------------------------------------------327.2.1影响抽芯力的因素 -----------------------------------------------------------------------------------------------337.2.2抽芯力的估算 -----------------------------------------------------------------------------------------------------337.3.1弯销的设计---------------------------------------------------------------------------------------------------------36 第八章模架与成形零件的设计 -------------------------------------------------------------------------------------------------418.1 模架的设计 ----------------------------------------------------------------------------------------------------------------418.2 成形零件的结构设计----------------------------------------------------------------------------------------------------418.3 加热与冷却系统的设计-------------------------------------------------------------------------------------------------478.4 推出机构的设计 ----------------------------------------------------------------------------------------------------------498.5 复位机构的设计 ----------------------------------------------------------------------------------------------------------50 第九章模具的总体结构设计-----------------------------------------------------------------------------------------------------519.1 压铸模的技术要求 -------------------------------------------------------------------------------------------------------519.2 压铸模外形和安装部位的技术要求 ---------------------------------------------------------------------------------51 第十章校核模具与压铸机的相关尺寸 ----------------------------------------------------------------------------------------5510.1 锁模力的校核------------------------------------------------------------------------------------------------------------5510.2 铸件最大投影面积校核 -----------------------------------------------------------------------------------------------5510.3 压室容量校核------------------------------------------------------------------------------------------------------------5510.4 模具尺寸的的校核 -----------------------------------------------------------------------------------------------------569.5 压实压力的校核 ----------------------------------------------------------------------------------------------------------5610.6 开模行程的校核---------------------------------------------------------------------------------------------------------56 第十一章压铸CAE数值模拟分析---------------------------------------------------------------------------------------------5711.1 概述 ------------------------------------------------------------------------------------------------------------------------5711.2 模拟分析过程------------------------------------------------------------------------------------------------------------5711.3 结果分析------------------------------------------------------------------------------------------------------------------65 第十二章结论 -----------------------------------------------------------------------------------------------------------------------69 参考文献 -------------------------------------------------------------------------------------------------------------------------------71 致谢---------------------------------------------------------------------------------------------------------------------------------72 附录一科技文献翻译 --------------------------------------------------------------------------------------------------------------73 附录二毕业设计任务书--------------------------------------------------------------------------------------------------------- 100第一章前言1.1 课题的提出压力铸造是近代金属加工工艺中,发展较快的一种先进的铸造方法。
毕业论文(设计)隔震橡胶支座模具设计

毕业设计任务书1.设计的主要任务及目标主要任务:审查隔震橡胶支座,了解生产量及产品所用胶种。
确定模具结构,要确定模具结构形式,腔数和分型面,考虑好模块间定位,余胶槽和启模槽。
确定收缩率。
计算型腔尺寸。
确定模具外形尺寸。
确定模具精度。
模具材料的选择及热处理。
模具的整体分析。
目标:设计一个符合规定性能要求的隔震橡胶支座模具。
2.设计的基本要求和内容设计图纸齐全;毕业设计说明书一份;答辩PPT。
3.主要参考文献[1]陈良辉.《模具工程技术手册》[M].北京:机械工业出版社,2002[2]张秀英.《橡胶模具方法与实例》[M].北京:化学工业出版社,2003:46-110[3]模具使用技术丛书编委会.《橡胶模具设计应用实例》[M].北京:机械工业出版社,2003[4]刘小年.《机械制图》[M].北京:高等教育出版社,20074.进度安排隔震橡胶支座模具设计摘要:面对拥有巨大破坏力的地震灾害,我们不能任其祸害。
在建筑物基础层与底层间安装叠层隔震橡胶支座是一种被实践证明了的有效的减震技术。
隔震这种抗震方式比单纯强化结构本身及主要承重构件更体现以柔克刚。
支座代替上部结构承受地震强烈的位移动力,以此来隔离或耗散地震的能量,避免或减少地震能量向上部结构传输,此时上部建筑结构的反应相当于不隔震情况下的1/4~1/8。
对隔震橡胶支座性能提高的追求促进着隔震橡胶支座模具设计的不断优化。
在支座生产工厂的实习经验和认知积累能够保证该设计结果的一定的实用性。
针对有效直径600的支座,本文对余胶槽,启模口,硫化收缩率,型腔尺寸等模具设计所含内容进行了设计。
为Ⅰ型支座设计了普通型和铅芯型的两种类型的模具。
关键词:隔震橡胶支座,模具,实用性,有效直径,Ⅰ型The Mold Design of Seismic Isolation Rubber BearingsAbstract:Faced with the enormity of the earthquake disaster, we can't let it scourge.Thatstacked seismic isolation rubber bearings isInstalled between the base layer and the bottom of buildings is a proven and effective technique.Isolating is a better waywhich embodys softness than simply strengthening the structure itself and the main load-bearing components.Bearings replace upper structures subject to seismic strong motivationthus isolating or dissipating earthquake energy and avoiding or reducing the energy transferred to the superstructure.The pursuit of performance improvement of seismic isolation rubber bearings promote continuous optimization of its moulddesign .Internship experience in the factory which produce thisrubber bearing and the accumulation of knowledge can ensure the certain utility of the design result.For effective diameter 600mm,this paperdescripesandinterpretates residual glue groove,restart of die mouth, cavity dimensions and other mold design contents.For type Ⅰ, two molds of general and lead bearing are designed.Key words:stacked seismic isolation rubber bearings,molds,utility,effective diameter,typeⅠ目录1前言 (1)2 隔震橡胶支座审查 (3)2.1隔震橡胶支座简介 (3)2.2制品信息 (3)数据信息 (3)胶种选择 (4)胶粘剂 (5)嵌件 (5)生产阶段 (6)2.3关于生产量 (8)3模具结构的确定 (10)3.1模具结构形式和腔数的确定 (10)模具结构形式的确定 (10)模具腔数的确定 (10)3.2分型面的确定 (10)3.3模具的定位 (10)3.4余胶槽和启模槽 (12)3.4.1余胶槽 (12)启模槽 (13)4 收缩率的确定 (15)4.1模压制品收缩率的影响因素 (15)4.2橡胶模压硫化收缩率的确定 (15)5 型腔尺寸的计算 (16)5.1型腔尺寸的计算和相关因素考虑 (16)5.2型腔尺寸公差的确定 (17)6 模具外形尺寸的确定 (18)6.1中模的壁厚 (18)6.2模具的高度 (20)7 模具精度要求 (22)7.1形位公差确定 (22)7.2模具的表面粗糙度 (22)8 手柄 (24)9 模具材料的选择及热处理 (25)10 模具的整体分析 (27)10.1硫化工艺的可行性 (27)10.2机械加工的可行性和经济性分析 (27)结论.............................................................................错误!未定义书签。
支座压铸模具设计任务书

2)掌握压铸模的运用及各部件的设计依据。
3)论文要求思路清晰,重点突出,图文并茂,举例恰当。
4)认真查阅资料,收集的数据资料要求具体、真实、详细。
5)论文字数要求6000字以上。
附件三:
紫琅职业技术学院
毕业设计任务书
系部名称
机电工程系
专业班级
模具设计与制造 模具3091
学生姓名
吴骏
指导教师姓名
程洋
论文题目
支座压铸模具设计
毕业设计的目的
1、撰写毕业论文是在校大学生最后一次知识的全面检验,是对学生基本知识、基本理论和基本技能掌握与提高程度的一次总测试。
2、通过撰写毕业设计让学生不断了解的压铸模设计过程,并针对目前压铸模具的发展趋势从而分析模具的设计走向。
2012年4月下旬—5月下旬定稿并提交毕业设计相关资料,准备答辩
2012年6月2日—6月3日答辩
6)认真对待毕业设计撰写,内容要有自己的观点。
7)独立完成毕业设计。
毕业设计进度安排
2011年11月中旬—12月上旬依照任务书阅读文献,收集资料准备草案
2011年12月上旬—12月中旬确定方案,编写设计开题报告,并交老师审核
2011年12月中旬—2012年3月中旬完成初稿,交老师审核。
2012年3月中旬—4月下旬完成二稿,交老师审核
(完整版)压铸模毕业课程设计(薄壁壳体压铸工艺与压铸模具设计)

井冈山大学压铸模课程设计说明书题目薄壁壳体压铸工艺与压铸型设计院(部):机电工程学院专业:材料成型班级:姓名:学号:指导教师:完成日期:目录摘要............................................................................................................................................. . (Ⅲ)1前言1.1选题背景和意义 (1)1.2 压铸相关文献综述 (1)△)+a…………………………………(5-3)型芯尺寸计算见公式(5-4):Y-a=(Y0+KY0+n△)-a ……………………………….(5-4)Y0——铸件的公称尺寸;n ——补偿和磨损系数。
取n=0.7;△——铸件偏差;a ——模具成型部分的制造偏差;5.3 镶块、型芯、模板的设计5.3.1 镶块的设计镶块的壁厚尺寸确定:据铸件形状和尺寸大小来确定。
结合铸件的结构特点,根据参考文献[16]《压铸模设计手册》中表6-22镶块壁厚尺寸推荐值,所设计的镶块材料用3Gr2W8V,定模镶块的结构形式及尺寸如图5.1所示。
动模镶块的结构形式及尺寸如图5-1所示。
材料:3Cr2W8V热处理:HRC50~55图5.1动模镶块如(图5.31)所示,具体尺寸如下:(单位:mm)图5.2镶块尺寸5.3.2型芯的设计型芯作用:用来形成鋳件在开模方向或不在开模方向孔或凹位,形状和尺寸按产品要求。
结合铸件的结构特点,根据参考文献[16]《压铸模设计手册》中表6-25圆型芯尺寸推荐值,型芯的成形段直径为45mm。
型芯的具体尺寸见图5-3。
材料:3Cr2w8v热处理:HRC43~4图5.3型芯如(图5.3.2)所示,具体尺寸如下:(单位:mm)图5.4型芯尺寸5.3.3 动、定模板的设计动模是压铸模的另一个重要组成部分, 动模是和定模形成压铸模成型部分的另一个整体,它一般固定在压铸机中板上,随中板作并合运动,与定模分开合拢。
压铸模具设计毕业设计说明书
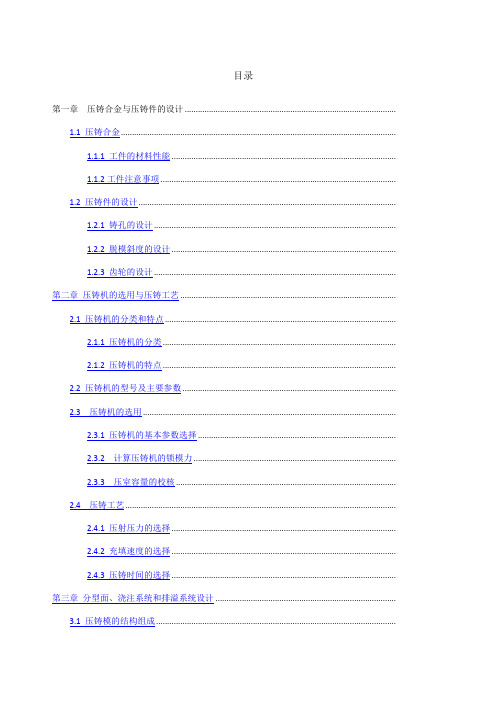
目录第一章压铸合金与压铸件的设计 ................................................................................................1.1 压铸合金 .............................................................................................................................1.1.1 工件的材料性能 ......................................................................................................1.1.2工件注意事项 ...........................................................................................................1.2 压铸件的设计 .....................................................................................................................1.2.1 铸孔的设计 ..............................................................................................................1.2.2 脱模斜度的设计 ......................................................................................................1.2.3 齿轮的设计 .............................................................................................................. 第二章压铸机的选用与压铸工艺 ..................................................................................................2.1 压铸机的分类和特点 .........................................................................................................2.1.1 压铸机的分类 ..........................................................................................................2.1.2 压铸机的特点 ..........................................................................................................2.2 压铸机的型号及主要参数 .................................................................................................2.3 压铸机的选用 ...................................................................................................................2.3.1 压铸机的基本参数选择 ..........................................................................................2.3.2 计算压铸机的锁模力 ............................................................................................2.3.3 压室容量的校核 ....................................................................................................2.4 压铸工艺 ...........................................................................................................................2.4.1 压射压力的选择 ......................................................................................................2.4.2 充填速度的选择 ......................................................................................................2.4.3 压铸时间的选择 ...................................................................................................... 第三章分型面、浇注系统和排溢系统设计 ..................................................................................3.1 压铸模的结构组成 .............................................................................................................3.2 分型面的设计 .....................................................................................................................3.2.1 分型面的类型 ..........................................................................................................3.2.2 分型面的选择原则 ..................................................................................................3.2.3 浇注系统设计 ..........................................................................................................3.2.4 溢流与排气系统的设计 ..........................................................................................第四章成型零件与模架设计 ..........................................................................................................4.1成型零件的结构设计 ..........................................................................................................4.2 成型零件的成型尺寸的计算 .............................................................................................4.3 模架的设计 .........................................................................................................................4.4 加热与冷却系统设计(该模具不采用加热冷却系统,略) .........................................第五章抽芯结构设计 ......................................................................................................................参考文献 ............................................................................................................................................附录(翻译) ...................................................................................................................摘要随着我国与国际接轨脚步的不断加快,市场竞争的日益加剧,,人们开始越来越认识到产品食量、成本和新产品的开发能力的重要性。
压铸模设计说明书

湘潭大学毕业设计说明书题目:压铸件模具设计学院:机械工程学院专业:材料成型及控制工程学号:姓名:指导教师:完成日期: 2015.3。
16目录一。
设计前准备工作 (1)1。
压铸工艺分析: (1)2.零件初步分析 (1)3.初步确定设计方案: (1)二。
压铸件工艺分析 (2)1.压铸合金工艺分析: (2)2.压铸件工艺分析: (2)3.分型面的选择: (2)三.浇注系统和排溢系统的设计 (3)1.浇注系统的设计: (3)2。
溢流排气系统的设计: (3)四。
压铸机的选择 (4)1.压铸机的种类和特点 (4)2。
选定压射比压 (5)3.确定型腔数目及布置形式 (5)4。
确定模具分型面上铸件的总投影面积 (6)5.计算锁模力: (6)五。
压铸模的结构设计 (7)1。
成型零件设计 (7)2。
结构零件设计 (10)3、各零件采用材料要求 (15)4、螺钉选用 (16)六、压铸模的整体结构 (16)1、压铸模的技术要求 (16)2、压铸模外形和安装部位的技术要求 (17)七、校核模具与压铸机的有关尺寸 (18)1、锁模力的校核 (18)2、铸件最大投影面积校核 (18)3、压室容量校核 (18)4、模具厚度的校核 (18)5、开模行程的校核 (18)八、参考文献: (19)一。
设计前准备工作1。
压铸工艺分析:压力铸造是将液态或半液态的金属,在高压作用下,以高的速度填充压铸模的型腔,并在压力作用下快速凝固而获得铸件的一种方法。
高压力和高速度是压铸时熔融合金充填成型过程的两大特点,也是压铸与其它铸造方法最根本的区别所在。
压铸件尺寸精度和表面粗糙度较好,铸件轮廓清晰,有致密的表层,比内层有更好的机械性能,内部存在气孔和缩孔缺陷。
2。
零件初步分析零件为对称圆筒型零件,截面为工字形,中心开有一小孔。
壁厚为5mm,属于薄壁零件。
型腔深度约为97。
5mm,属于深腔。
零件图如下所示:图1—1 零件图3。
初步确定设计方案:1)压铸合金此铸件的材料为YZCuZn40Pb:此材料属于铅黄铜合金,具有加工性能较好,成本较低等优点,多用于化工、造船的零件和耐磨的零件。
方形支架体压铸模具设计(机械CAD图纸)

前言在现代工业发展的进程中,模具的地位及其重要性日益被人们所认识。
模具工业作为进入富裕社会的原动力之一,正推动着整个工业技术向前迈进!模具就是“高效益”,模具就是“现代化”之深刻含意,也正在为人们所理解和掌握。
金属压铸成型所用的模具称为压铸模,是用于成型金属压铸件的模具,它是型腔模中的一种类型。
随着机械工业,尤其是汽车、摩托车工业、航空工业和仪器仪表工业的发展,金属压铸件的需求量越来越大,精度等质量要求也愈来愈高,这就要求压铸模具的开发、设计与制造的水平也必须越来越高。
据资料表明,各类模具占模具总量的比例大致如下:冲压模、塑料模约各占35%~40%;压铸模约占10%~15%;粉末冶金模、陶瓷模、玻璃模等其他模具约占10%左右,压铸模在各类模具的应用中占有“老三”的位置。
随着我国经济与国际的接轨,汽车工业、摩托车工业和航空工业的飞速发展,压铸件的应用大有快速上升的趋势。
压铸的应用在世界范围内的情况是:汽车部件约占70%;摩托车部件约占10%;农业机械约占8%;电讯电器约占7%;其他约占5%。
以上实际统计的数字表明,压铸成型工业在基础工业中的地位和对国民经济的影响显得日益重要。
对于一个模具专业的毕业生来说,对压铸模的设计已经有了一个大概的了解。
此次毕业设计,培养了我综合运用多学科理论、知识和技能,以解决较复杂的工程实际问题的能力,主要包括设计、实验研究方案的分析论证,原理综述,方案方法的拟定及依据材料的确定等。
它培养了我树立正确的设计思想,勇于实践、勇于探索和开拓创新的精神,掌握现代设计方法,适应社会对人才培养的需要。
毕业设计这一教学环节使我独立承担实际任务的全面训练,通过独立完成毕业设计任务的全过程,培养了我的实践工作能力。
另外,本次毕业设计还必须具备一定的计算机应用的能力,在毕业设计过程中都应结合毕业设计课题利用计算机编制相应的工程计算、分析和优化的程序,同时还具备必要的计算机绘图能力,如利用AutoCAD 2007软件进行二维图的绘制。
- 1、下载文档前请自行甄别文档内容的完整性,平台不提供额外的编辑、内容补充、找答案等附加服务。
- 2、"仅部分预览"的文档,不可在线预览部分如存在完整性等问题,可反馈申请退款(可完整预览的文档不适用该条件!)。
- 3、如文档侵犯您的权益,请联系客服反馈,我们会尽快为您处理(人工客服工作时间:9:00-18:30)。
压力铸造是目前成型有色金属铸件的重要成型工艺方法,压铸的工艺特点是铸件的强度和精度较高,形状较为复杂且铸件壁较薄,而且生产力极高。
压铸模具是压力铸造的生产关键,压铸模具的质量决定着压铸件的质量和精度,而且模具设计直接影响着模具的质量和寿命。
因此,模具设计是模具技术进步关键,也是模具发展的重要因素。
根据零件的结构和尺寸设计了完整的模具。
设计内容主要包括:浇注系统设计,成型零件设计,抽芯机构设计,推出机构设计及模体结构设计。
根据铸件的形状特点,零件尺寸及精度,选定了合适是我压铸机,通过准确的计算并查阅设计手册,确定了成型零件以及模体是我尺寸及精度,在材料的选取及热处理要求上也做了详细说明,并在结合理论的基础上,借助于计算机辅助软件绘制了各部分零件及装配体的立体图和工程图,以保障模具的加工制造。
关键词:压力铸造,压铸模具,模具设计前言 (1)摘要 (I)目录 (I)1、压铸件的工艺分析 (1)1.1对压铸件的结构分析 (3)1.2压铸件材料的分析 (3)2、设备型号及其相关参数 (3)3、分析模具结构 (4)3.1浇注系统的设计 (4)3.2溢流槽和排气槽的设计 (4)3.3分型面的设计 (4)3.4型腔和型芯尺寸的确定 (4)3.5导柱与导套 (5)3.6推杆的结构设计 (5)3.7模具的冷却 (5)4、压铸工艺参数的选择 (5)4.1压射比压 (5)4.2压铸温度 (5)4.3压铸模温度 (5)4.4保压时间 (6)4.5留模时间 (6)4.6压射速度 (6)5、涂料的种类 (7)5.1压铸涂料 (7)6、型芯与型腔的选材 (7)7、校核 (7)8、零件图和装配图 (7)致谢 (11)参考文献 (12)结论 (13)前言国内外模具发展现状现代模具工业有“不衰亡工业”之称。
世界模具市场总体上供不应求,市场需求量维持在600亿至650亿美元,同时,我国的模具产业也迎来了新一轮的发展机遇。
近几年,我国模具产业总产值保持13%的年增长率中国模具行业发展现状:目前,中国17000多个模具生产厂点,从业人数约50多万。
1999年中国模具工业总产值已达245亿元人民币。
工业总产值中企业自产自用的约占三分之二,作为商品销售的约占三分之一。
在模具工业的总产值中,冲压模具约占50%,塑料模具约占33%,压铸模具约占6%,其它各类模具约占11%。
在中国,人们已经越来越认识到模具在制造中的重要基础地位,认识到模具技术水平的高低,已成为衡量一个国家制造业水平高低的重要标志,并在很大程度上决定着产品质量、效益和新产品的开发能力。
许多模具企业十分重视技术发展,加大了用于技术进步的投资力度,将技术进步视为企业发展的重要动力。
此外,许多研究机构和大专院校开展模具技术的研究和开发。
虽然中国模具工业在过去十多年中取得了令人瞩目的发展,但许多方面与工业发达国家相比仍有较大的差距。
例如,精密加工设备在模具加工设备中的比重还比较低,CAD/CAE/CAM技术的普及率不高,许多先进的模具技术应用还不够广泛等等。
特别在大型、精密、复杂和长寿命模具技术上存在明显差距,这些类型模具的生产能力也不能满足国内需求,因而需要大量从国外进口。
模具工艺发展过程及发展方向我国模具标准化工作起步较晚,模具标准生产、销售、推广和应用工作也比较落后。
因此,模具标准件品种规格少、供应不及时、配件性等问题长期存在。
从模具标准件使用覆盖率一直较低。
近年来虽然由于外资企业的介入,比例已有较大提高,但总的来说还很低。
据初步估计,目前这一比例大致为40%--产各种工业产品和民用产品的重要工艺装备,模具已发展成为一门产业。
20世纪80年代以来,中国模具工业的发展十分迅速。
近20年来,产值以每年15%左右的迅速增长。
2000年我国模具工业总产值已达280亿元人民币。
在冷冲模具方面,代表当代模具技术水平的汽车覆盖件模具,我国东风汽车公司模具厂、第一汽车厂模具中心等都能制造。
他们在CAD/CAM/CAE冲压件质量及模具性能方面,均以达到或接近国际先进水平,多工位连续模和多功能模具是我国重点发展的精密、高校模具品种。
目前,国内以可制造具有自动冲切、叠压、计数、分组、转子铁心扭斜和安全保等功能的铁心精密自动叠压多功能模具。
生产电动机定、转子双回转叠片的硬质合金连续模的步距精度可的2微米。
寿命达到1亿次以上。
用于生产集成电路引线匡架20—30工位生产电子枪零件的硬质合金连续模和生产空调器散热片的连续模也已经达到较高水平。
中国模具行业发展前景1999年中国大陆制造工业对模具的总市场需求量约为330亿元,今后几年仍将以每年10%以上的速度增长。
对于大型、精密、复杂、长寿命模具需求的增长将远超高速增长,特别是汽车覆盖件模具、塑料模具和压铸模具的发展。
家用电器,如彩电、冰箱、洗衣机、空调等,在国内的市场很大。
目前,我国的彩电的年产量已超过3200万台,电冰箱、洗衣机和空调的年产量均超过了1000万台。
家用电过每年10%的增幅。
汽车、摩托车行业的发展将器行业的发展对模具的需求量也将会很大。
其他发展较快的行业,如电子、通讯和建筑材料等行业对模具的需求,都将对中国模具工业和技术的发展产生巨大的推动作用。
近年来,中国模具市场对精密、大型、复杂型、长寿命模具的需求量有所增长,预计到2010年,国内模具市场需求量将在1,200亿元人民币左右。
综合媒体2008年6月4日报道,中国模具协会企业年报显示:近年来,中国模具市场对精密、大型、复杂型、长寿命模具的需求量有所增长,预计到2010年,国内模具市场需求量将在1,200亿元人民币左右。
现在国内相当多的模具企业普及了计算机绘图,应用各种CAD软件进行模具设计。
而从事模具技术研究的机构和院校已达30余家。
在模具CAD/CAE/CAM技术、冷冲模和精冲模CAD软件、模具的电加工和数控加工技术、快速成型技形(RP)和快速制模技术、新型模具材料等方面都取得了长足的进步和显著的成果。
1、压铸件的工艺分析1.1对压铸件的结构分析a、壁厚均为2mm,材料是YZAlSi12,制品无异形孔,零件不太复杂,所以此制品壁厚为安全壁厚。
b、零件外侧有个5mm的不通圆孔,深度为12.5mm经查表(铸孔最小孔径和孔径与深度的关系)可知此孔深度和孔径是合理的。
c、模斜度:因此制品为铝合金可知:配合面的最小出模斜度外表面为10'内表面为15',非配合面的最小出模斜度外表面15'内表面45'1.2压铸件材料的分析此材料为YZAlSi12合金代号是YL102 化学成份:硅Si :10.0~13.0 ,铜Cu :≤0.6,镁Mg:≤0.05,锌Zn:≤0.3,锰Mn:≤0.6,铁Fe:0.000~1.200 ,铝Al :余量,力学性能:抗拉强度σb (MPa):≥220 伸长率δ5 (%):≥2 硬度:≥60(5/250/30)HB特性及适用范围:不可热处理强化,该合金的铸造性能优良,无热裂及疏松倾向,气密性较高。
其密度小,耐蚀性好,可在受大气海水腐蚀的环境中使用,可承受工业气氛的环境中浓硝酸过氧化氢等的腐蚀作用;焊接性能也好。
但该合金的力学性能低,耐热性和切削加工性差。
2、设备型号及其相关参数F主=1.3A1p=21.1*104NF分=A芯ptanα=148NF锁=K(F主+F分)=27.6*104N铸件的最大投影面积S=125*26+25π-36π=32.23cm2铸件的体积V=16.68cm3铸件质量m=45g纵上所述可选:卧室冷压压铸机J116相关参数:锁模力/(104N)63开模力/(104N)7压射力/(104N)5——9压室直径/(mm)30压射比压/(105 Pa)705——1270压室内最大合金容量/Kg 0.25铸件最大投影面积/(cm2)42压射冲头回程力/(104N)2——5压射冲头最大行程/(mm)260压射冲头伸出定模距离/(mm)60模具最大尺寸(长*宽)/mm*mm 360*450模板最大间距/(mm)570模板最小间距/(mm)250合模行程/(mm)320压室偏心距/(mm)60管路工作压力/(105 Pa)100工作循环次数/(次/h)150——1803、分析模具结构3.1浇注系统的设计A、直浇道的设计a根据铸件质量为45g ,选择喷嘴导入口直径为8mb处于浇口套部分直浇道的直径,应比喷嘴部分的直浇道的直径每边大1mm。
c直浇道与横浇道连接处要圆弧过渡,其半径取R10,以使金属液流动顺畅。
B、横浇道的设计a横浇道的截面积应从直浇道到内浇口保持均匀或逐渐缩小,不允许有突然的扩大或缩小现象,以免产生涡流。
b横浇道应平直,不能设计成曲面,以免产生包气或流态不稳。
c横浇道应具有一定的厚度和长度,若横浇道过薄,则热量损失大,若过厚,则冷却速度慢,影响生产率,增大金属消耗;保持一定长度是为了对金属液起到稳流和导的作用向。
d横浇道的截面积不能小于内浇口的截面积。
3.2溢流槽和排气槽的设计a溢流槽因此压铸件简似一方盖是从上顶面进料,为排除金属液流前头的气体、冷污金属液所以溢流槽设计在内浇口两侧和压铸件两侧(金属液最先冲击的部分)尺寸:溢流口的宽度为10mm,溢流口半径为8mm溢流口长度为3mm溢流口厚度为0.7mmb排气槽在分型面上布置排气槽;利用型芯和推杆间隙布置排气槽尺寸:排气槽深度0.1mm,在离开型腔20---30mm后,可将深度增大为0.3mm,以提高排气效果3.3分型面的设计此模具的分型面设计在压铸件的下底面,这样便于开模后留在动模;能确保制品的外观质量;使加工、修配、更换都很方便,降低模具制造的难度,从而降低模具的制造成本。
3.4型腔和型芯尺寸的确定型腔尺寸计算公式D'=(D+0.6%D-0.7Δ)+Δ/5精度为CT5H'=(H+0.6%H-0.7Δ)+Δ/5135-0.62D1=(135+135*0.6%-0.7*0.62)+0.62/5= 135.38+0.12φ16-0.38D2=(16+16*0.6%-0.7*0.38)+0.38/5=15.83+0.08+0.08φ15-0.38D3=(15+15*0.6%-0.7*0.38)+0.38/5=14.82+0.0816-0.38H1=(16+16*0.6%-0.7*0.38)+0.38/5=15.83+0.0831 -0.38H2=(31+31*0.6%-0.7*0.46)+0.46/5=30.86+0.09型芯尺寸计算公式d'=(d+0.6%d+0.7Δ)-Δ精度为CT5h'=(h+0.6%h+0.7Δ)-Δ131+0.62d1=(131+131*0.6%+0.7*0.62)-0.62/5=132.22-0.12φ12+0.38d2=(12+12*0.6%+0.7*0.38)-0.38/5=12.34-0.08φ11+0.38d3=(11+11*0.6%+0.7*0.38) -0.38/5 =11.33-0.08φ5+0.32d4=(5+5*0.6%+0.7*0.32) -0.38/5=5.30-0.0814 +0.38h1=(14+14*0.6%+0.7*0.38) -0.38/5=14.35-0.0829+0.46h2=(29+29*0.6%+0.7*0.46) -0.46/5=29.50-0.09中心距尺寸计算公式L'=(L+0.6%L)±Δ/555±0.25 L=(55+0.6%*55) ±0.5/5=55.33±0.13.5导柱与导套导柱与导套是标准件。