中国古代的钢铁渗碳和渗氮技术全解
纯铁及结构钢快速气体渗氮工艺及机理研究
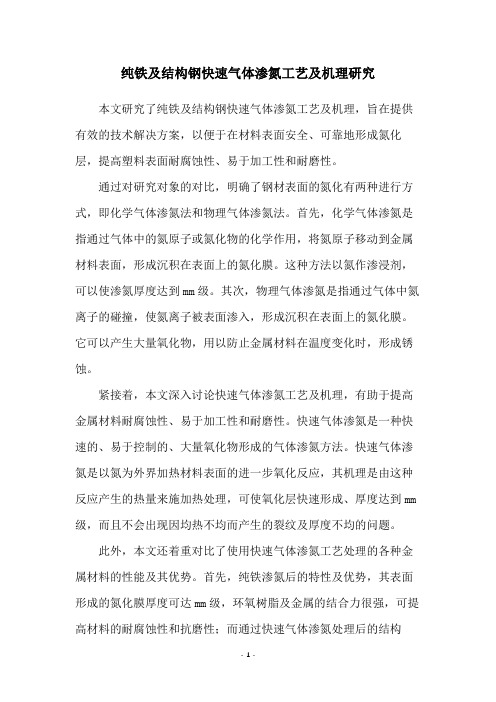
纯铁及结构钢快速气体渗氮工艺及机理研究本文研究了纯铁及结构钢快速气体渗氮工艺及机理,旨在提供有效的技术解决方案,以便于在材料表面安全、可靠地形成氮化层,提高塑料表面耐腐蚀性、易于加工性和耐磨性。
通过对研究对象的对比,明确了钢材表面的氮化有两种进行方式,即化学气体渗氮法和物理气体渗氮法。
首先,化学气体渗氮是指通过气体中的氮原子或氮化物的化学作用,将氮原子移动到金属材料表面,形成沉积在表面上的氮化膜。
这种方法以氮作渗浸剂,可以使渗氮厚度达到mm级。
其次,物理气体渗氮是指通过气体中氮离子的碰撞,使氮离子被表面渗入,形成沉积在表面上的氮化膜。
它可以产生大量氧化物,用以防止金属材料在温度变化时,形成锈蚀。
紧接着,本文深入讨论快速气体渗氮工艺及机理,有助于提高金属材料耐腐蚀性、易于加工性和耐磨性。
快速气体渗氮是一种快速的、易于控制的、大量氧化物形成的气体渗氮方法。
快速气体渗氮是以氮为外界加热材料表面的进一步氧化反应,其机理是由这种反应产生的热量来施加热处理,可使氧化层快速形成、厚度达到mm 级,而且不会出现因均热不均而产生的裂纹及厚度不均的问题。
此外,本文还着重对比了使用快速气体渗氮工艺处理的各种金属材料的性能及其优势。
首先,纯铁渗氮后的特性及优势,其表面形成的氮化膜厚度可达mm级,环氧树脂及金属的结合力很强,可提高材料的耐腐蚀性和抗磨性;而通过快速气体渗氮处理后的结构钢,其耐腐蚀性及抗磨性也得到了显著提升,而且可以更好地利用金属的热变形性能,具有较高的强度及硬度。
最后,研究表明,采用快速气体渗氮工艺处理的纯铁及结构钢,其表面氮化膜厚度可以达到mm级,可以有效提高材料耐腐蚀性、易于加工性和耐磨性。
综上所述,研究表明,快速气体渗氮工艺及机理可以有效提高纯铁及结构钢的耐腐蚀性、易于加工性和耐磨性,是一种高效、可靠地构建金属材料表面氮化层的有效方法。
未来期待研究人员继续深入研究,为金属材料表面氮化技术提供有力的技术支持与帮助。
钢的氮化及碳氮共渗讲解
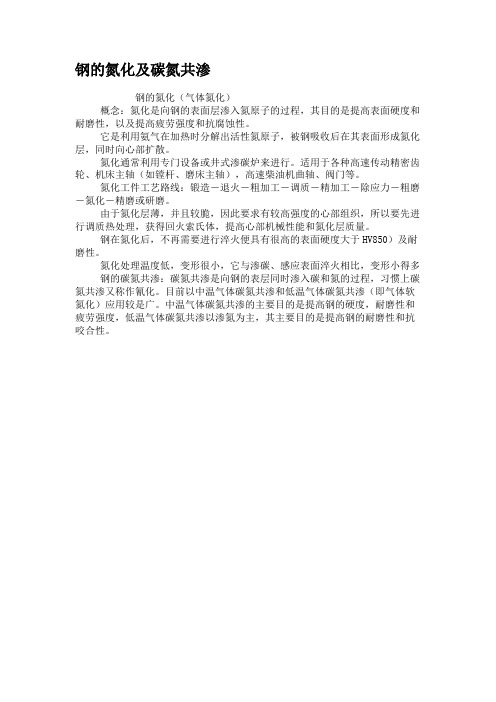
钢的氮化及碳氮共渗
钢的氮化(气体氮化)
概念:氮化是向钢的表面层渗入氮原子的过程,其目的是提高表面硬度和耐磨性,以及提高疲劳强度和抗腐蚀性。
它是利用氨气在加热时分解出活性氮原子,被钢吸收后在其表面形成氮化层,同时向心部扩散。
氮化通常利用专门设备或井式渗碳炉来进行。
适用于各种高速传动精密齿轮、机床主轴(如镗杆、磨床主轴),高速柴油机曲轴、阀门等。
氮化工件工艺路线:锻造-退火-粗加工-调质-精加工-除应力-粗磨-氮化-精磨或研磨。
由于氮化层薄,并且较脆,因此要求有较高强度的心部组织,所以要先进行调质热处理,获得回火索氏体,提高心部机械性能和氮化层质量。
钢在氮化后,不再需要进行淬火便具有很高的表面硬度大于HV850)及耐磨性。
氮化处理温度低,变形很小,它与渗碳、感应表面淬火相比,变形小得多钢的碳氮共渗:碳氮共渗是向钢的表层同时渗入碳和氮的过程,习惯上碳氮共渗又称作氰化。
目前以中温气体碳氮共渗和低温气体碳氮共渗(即气体软氮化)应用较是广。
中温气体碳氮共渗的主要目的是提高钢的硬度,耐磨性和疲劳强度,低温气体碳氮共渗以渗氮为主,其主要目的是提高钢的耐磨性和抗咬合性。
金属热处理-渗氮
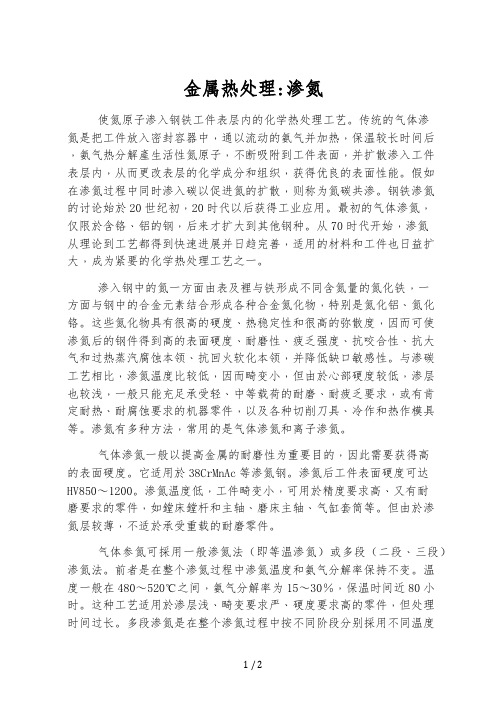
金属热处理:渗氮使氮原子渗入钢铁工件表层内的化学热处理工艺。
传统的气体渗氮是把工件放入密封容器中﹐通以流动的氨气并加热﹐保温较长时间后﹐氨气热分解產生活性氮原子﹐不断吸附到工件表面﹐并扩散渗入工件表层内﹐从而更改表层的化学成分和组织﹐获得优良的表面性能。
假如在渗氮过程中同时渗入碳以促进氮的扩散﹐则称为氮碳共渗。
钢铁渗氮的讨论始於20世纪初﹐20时代以后获得工业应用。
最初的气体渗氮﹐仅限於含铬﹑铝的钢﹐后来才扩大到其他钢种。
从70时代开始﹐渗氮从理论到工艺都得到快速进展并日趋完善﹐适用的材料和工件也日益扩大﹐成为紧要的化学热处理工艺之一。
渗入钢中的氮一方面由表及裡与铁形成不同含氮量的氮化铁﹐一方面与钢中的合金元素结合形成各种合金氮化物﹐特别是氮化铝﹑氮化铬。
这些氮化物具有很高的硬度﹑热稳定性和很高的弥散度﹐因而可使渗氮后的钢件得到高的表面硬度﹑耐磨性﹑疲乏强度﹑抗咬合性﹑抗大气和过热蒸汽腐蚀本领﹑抗回火软化本领﹐并降低缺口敏感性。
与渗碳工艺相比﹐渗氮温度比较低﹐因而畸变小﹐但由於心部硬度较低﹐渗层也较浅﹐一般只能充足承受轻﹑中等载荷的耐磨﹑耐疲乏要求﹐或有肯定耐热﹑耐腐蚀要求的机器零件﹐以及各种切削刀具﹑冷作和热作模具等。
渗氮有多种方法﹐常用的是气体渗氮和离子渗氮。
气体渗氮一般以提高金属的耐磨性为重要目的﹐因此需要获得高的表面硬度。
它适用於38CrMnAc等渗氮钢。
渗氮后工件表面硬度可达HV850~1200。
渗氮温度低﹐工件畸变小﹐可用於精度要求高﹑又有耐磨要求的零件﹐如鏜床鏜杆和主轴﹑磨床主轴﹑气缸套筒等。
但由於渗氮层较薄﹐不适於承受重载的耐磨零件。
气体参氮可採用一般渗氮法(即等温渗氮)或多段(二段﹑三段)渗氮法。
前者是在整个渗氮过程中渗氮温度和氨气分解率保持不变。
温度一般在480~520℃之间﹐氨气分解率为15~30%﹐保温时间近80小时。
这种工艺适用於渗层浅﹑畸变要求严﹑硬度要求高的零件﹐但处理时间过长。
渗碳和渗氮的新概念及其实际运用
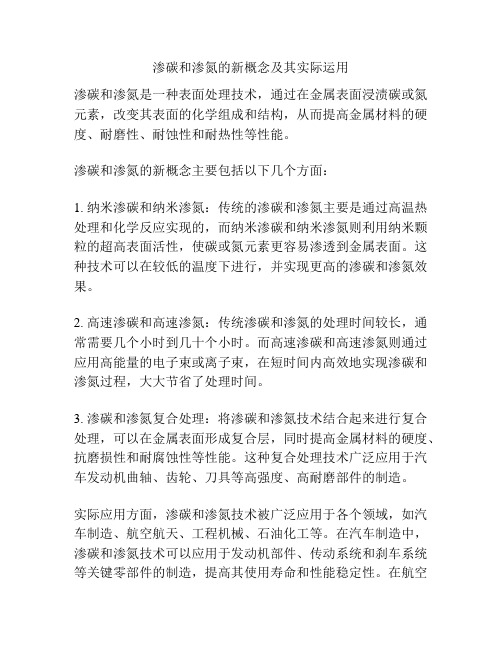
渗碳和渗氮的新概念及其实际运用
渗碳和渗氮是一种表面处理技术,通过在金属表面浸渍碳或氮元素,改变其表面的化学组成和结构,从而提高金属材料的硬度、耐磨性、耐蚀性和耐热性等性能。
渗碳和渗氮的新概念主要包括以下几个方面:
1. 纳米渗碳和纳米渗氮:传统的渗碳和渗氮主要是通过高温热处理和化学反应实现的,而纳米渗碳和纳米渗氮则利用纳米颗粒的超高表面活性,使碳或氮元素更容易渗透到金属表面。
这种技术可以在较低的温度下进行,并实现更高的渗碳和渗氮效果。
2. 高速渗碳和高速渗氮:传统渗碳和渗氮的处理时间较长,通常需要几个小时到几十个小时。
而高速渗碳和高速渗氮则通过应用高能量的电子束或离子束,在短时间内高效地实现渗碳和渗氮过程,大大节省了处理时间。
3. 渗碳和渗氮复合处理:将渗碳和渗氮技术结合起来进行复合处理,可以在金属表面形成复合层,同时提高金属材料的硬度、抗磨损性和耐腐蚀性等性能。
这种复合处理技术广泛应用于汽车发动机曲轴、齿轮、刀具等高强度、高耐磨部件的制造。
实际应用方面,渗碳和渗氮技术被广泛应用于各个领域,如汽车制造、航空航天、工程机械、石油化工等。
在汽车制造中,渗碳和渗氮技术可以应用于发动机部件、传动系统和刹车系统等关键零部件的制造,提高其使用寿命和性能稳定性。
在航空
航天领域,渗碳和渗氮技术可以应用于航空发动机涡轮叶片、导向叶片等高温部件的制造,提高其耐热性和耐腐蚀性。
总之,渗碳和渗氮的新概念和实际运用不断拓展着金属材料表面处理的领域,为各个行业提供了更高性能的金属材料解决方案。
中国古代灌钢法冶炼技术
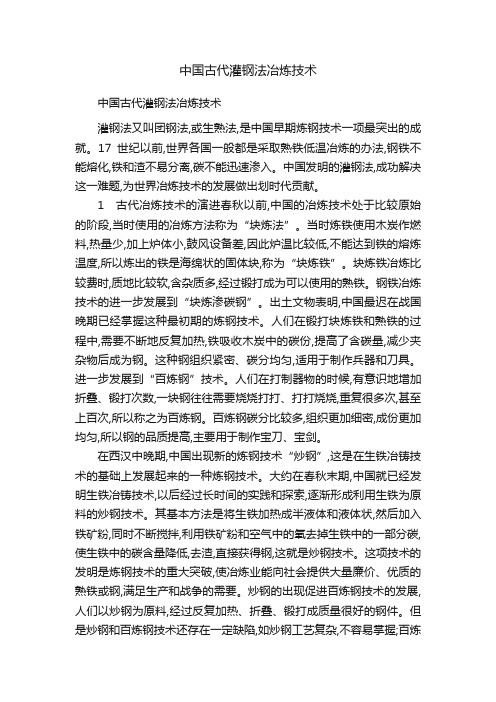
中国古代灌钢法冶炼技术中国古代灌钢法冶炼技术灌钢法又叫团钢法,或生熟法,是中国早期炼钢技术一项最突出的成就。
17世纪以前,世界各国一般都是采取熟铁低温冶炼的办法,钢铁不能熔化,铁和渣不易分离,碳不能迅速渗入。
中国发明的灌钢法,成功解决这一难题,为世界冶炼技术的发展做出划时代贡献。
1 古代冶炼技术的演进春秋以前,中国的冶炼技术处于比较原始的阶段,当时使用的冶炼方法称为“块炼法”。
当时炼铁使用木炭作燃料,热量少,加上炉体小,鼓风设备差,因此炉温比较低,不能达到铁的熔炼温度,所以炼出的铁是海绵状的固体块,称为“块炼铁”。
块炼铁冶炼比较费时,质地比较软,含杂质多,经过锻打成为可以使用的熟铁。
钢铁冶炼技术的进一步发展到“块炼渗碳钢”。
出土文物表明,中国最迟在战国晚期已经掌握这种最初期的炼钢技术。
人们在锻打块炼铁和熟铁的过程中,需要不断地反复加热,铁吸收木炭中的碳份,提高了含碳量,减少夹杂物后成为钢。
这种钢组织紧密、碳分均匀,适用于制作兵器和刀具。
进一步发展到“百炼钢”技术。
人们在打制器物的时候,有意识地增加折叠、锻打次数,一块钢往往需要烧烧打打、打打烧烧,重复很多次,甚至上百次,所以称之为百炼钢。
百炼钢碳分比较多,组织更加细密,成份更加均匀,所以钢的品质提高,主要用于制作宝刀、宝剑。
在西汉中晚期,中国出现新的炼钢技术“炒钢”,这是在生铁冶铸技术的基础上发展起来的一种炼钢技术。
大约在春秋末期,中国就已经发明生铁冶铸技术,以后经过长时间的实践和探索,逐渐形成利用生铁为原料的炒钢技术。
其基本方法是将生铁加热成半液体和液体状,然后加入铁矿粉,同时不断搅拌,利用铁矿粉和空气中的氧去掉生铁中的一部分碳,使生铁中的碳含量降低,去渣,直接获得钢,这就是炒钢技术。
这项技术的发明是炼钢技术的重大突破,使冶炼业能向社会提供大量廉价、优质的熟铁或钢,满足生产和战争的需要。
炒钢的出现促进百炼钢技术的发展,人们以炒钢为原料,经过反复加热、折叠、锻打成质量很好的钢件。
氮化与渗碳处理技术

氮化处理技术气体渗氮在1923年左右,由德国人Fry首度研究发展并加以工业化。
由於经本法处理的製品具有优异的耐磨性、耐疲劳性、耐蚀性及耐高温,其应用范围逐渐扩大。
例如钻头、螺丝攻、挤压模、压铸模、鍜压机用鍜造模、螺桿、连桿、曲轴、吸气及排气活门及齿轮凸轮等均有使用。
一、氮化用钢简介传统的合金钢料中之铝、铬、钒及鉬元素对渗氮甚有帮助。
这些元素在渗氮温度中,与初生态的氮原子接触时,就生成安定的氮化物。
尤其是鉬元素,不仅作為生成氮化物元素,亦作為降低在渗氮温度时所发生的脆性。
其他合金钢中的元素,如镍、铜、硅、锰等,对渗氮特性并无多大的帮助。
一般而言,如果钢料中含有一种或多种的氮化物生成元素,氮化后的效果比较良好。
其中铝是最强的氮化物元素,含有0.85~1.5%铝的渗氮结果最佳。
在含铬的铬钢而言,如果有足够的含量,亦可得到很好的效果。
但没有含合金的碳钢,因其生成的渗氮层很脆,容易剥落,不适合作為渗氮钢。
一般常用的渗氮钢有六种如下:(1)含铝元素的低合金钢(标準渗氮钢)(2)含铬元素的中碳低合金钢SAE 4100,4300,5100,6100,8600,8700,9800系。
(3)热作模具钢(含约5%之铬)SAE H11 (SKD – 61)H12,H13(4)肥粒铁及麻田散铁系不锈钢SAE 400系(5)奥斯田铁系不锈钢SAE 300系(6)析出硬化型不锈钢17 - 4PH,17 – 7PH,A – 286等含铝的标準渗氮钢,在氮化后虽可得到很高的硬度及高耐磨的表层,但其硬化层亦很脆。
相反的,含铬的低合金钢硬度较低,但硬化层即比较有韧性,其表面亦有相当的耐磨性及耐束心性。
因此选用材料时,宜注意材料之特徵,充分利用其优点,俾符合零件之功能。
至於工具钢如H11(SKD61)D2(SKD – 11),即有高表面硬度及高心部强度。
二、氮化处理技术:调质后的零件,在渗氮处理前须澈底清洗乾净,兹将包括清洗的渗氮工作程序分述如下:(1)渗氮前的零件表面清洗大部分零件,可以使用气体去油法去油后立刻渗氮。
钢的渗碳和渗氮
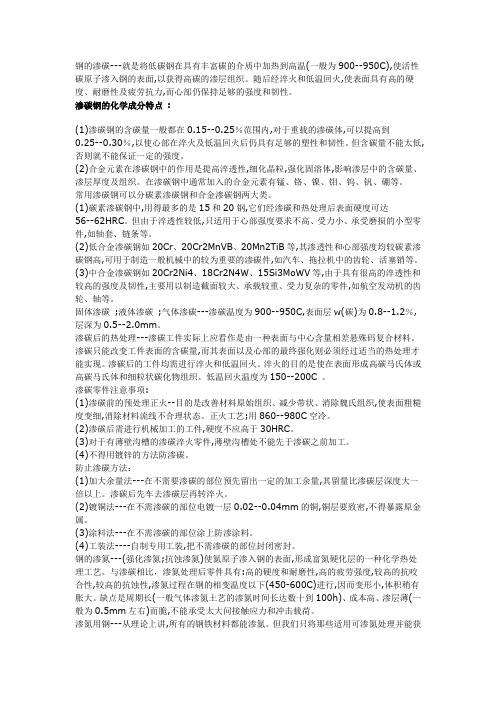
钢的渗碳---就是将低碳钢在具有丰富碳的介质中加热到高温(一般为900--950C),使活性碳原子渗入钢的表面,以获得高碳的渗层组织。
随后经淬火和低温回火,使表面具有高的硬度、耐磨性及疲劳抗力,而心部仍保持足够的强度和韧性。
渗碳钢的化学成分特点:(1)渗碳钢的含碳量一般都在0.15--0.25%范围内,对于重载的渗碳体,可以提高到0.25--0.30%,以使心部在淬火及低温回火后仍具有足够的塑性和韧性。
但含碳量不能太低,否则就不能保证一定的强度。
(2)合金元素在渗碳钢中的作用是提高淬透性,细化晶粒,强化固溶体,影响渗层中的含碳量、渗层厚度及组织。
在渗碳钢中通常加入的合金元素有锰、铬、镍、钼、钨、钒、硼等。
常用渗碳钢可以分碳素渗碳钢和合金渗碳钢两大类。
(1)碳素渗碳钢中,用得最多的是15和20钢,它们经渗碳和热处理后表面硬度可达56--62HRC。
但由于淬透性较低,只适用于心部强度要求不高、受力小、承受磨损的小型零件,如轴套、链条等。
(2)低合金渗碳钢如20Cr、20Cr2MnVB、20Mn2TiB等,其渗透性和心部强度均较碳素渗碳钢高,可用于制造一般机械中的较为重要的渗碳件,如汽车、拖拉机中的齿轮、活塞销等。
(3)中合金渗碳钢如20Cr2Ni4、18Cr2N4W、15Si3MoWV等,由于具有很高的淬透性和较高的强度及韧性,主要用以制造截面较大、承载较重、受力复杂的零件,如航空发动机的齿轮、轴等。
固体渗碳;液体渗碳;气体渗碳---渗碳温度为900--950C,表面层w(碳)为0.8--1.2%,层深为0.5--2.0mm。
渗碳后的热处理---渗碳工件实际上应看作是由一种表面与中心含量相差悬殊码复合材料。
渗碳只能改变工件表面的含碳量,而其表面以及心部的最终强化则必须经过适当的热处理才能实现。
渗碳后的工件均需进行淬火和低温回火。
淬火的目的是使在表面形成高碳马氏体或高碳马氏体和细粒状碳化物组织。
低温回火温度为150--200C 。
渗碳渗氮作用及氮碳共渗及碳氮共渗区别

渗碳:是对金属表面办理的一种,采用渗碳的多为低碳钢或低合金钢,详尽方法是将工件置入拥有活性渗碳介质中,加热到900--950摄氏度的单相奥氏体区 ,保温足够时间后,使渗碳介质中分解出的活性碳原子浸透钢件表层,从而获得表层高碳 ,心部仍保持原有成分. 相似的还有低温渗氮办理。
这是金属资料常有的一种热办理工艺,它能够使渗过碳的工件表面获得很高的硬度,提高其耐磨程度。
渗碳是指派碳原子浸透到钢表面层的过程。
也是使低碳钢的工件拥有高碳钢的表面层,再经过淬火和低温回火,使工件的表面层拥有高硬度和耐磨性,而工件的中心部分依旧保持着低碳钢的韧性和塑性。
渗碳工件的资料一般为低碳钢或低碳合金钢 (含碳量小于%)。
渗碳后﹐钢件表面的化学成分可凑近高碳钢。
工件渗碳后还要经过淬火﹐以获得高的表面硬度﹑高的耐磨性和疲倦强度﹐并保持心部有低碳钢淬火后的强韧性﹐使工件能承受冲击载荷。
渗碳工艺广泛用于飞机﹑汽车和拖拉机等的机械零件﹐如齿轮﹑轴﹑凸轮轴等。
渗碳零件的资料一般采用低碳钢或低碳合金钢(含碳量小於%)。
渗碳后必定进行淬火才能充分发挥渗碳的有利作用。
工件渗碳淬火后的表层显微组织主要为高硬度的马氏体加上节余奥氏体和少量碳化物﹐心部组织为韧性好的低碳马氏体或含有非马氏体的组织﹐但应防范出现铁素体。
一般渗碳层深度范围为~毫米﹐深度渗碳时可达2毫米或更深。
表面硬度可达 HRC58~63﹐心部硬度为 HRC30~42。
渗碳淬火后﹐工件表面产生压缩内应力﹐对提高工件的疲倦强度有利。
所以渗碳被广泛用以提高零件强度﹑冲击韧性和耐磨性﹐借以延长零件的使用寿命。
按含碳介质的不同样﹐渗碳可分为固体渗碳﹑液体渗碳﹑气体渗碳和碳氮共渗;渗氮,是在必然温度下必然介质中使氮原子浸透工件表层的化学热办理工艺。
常有有液体渗氮、气体渗氮、离子渗氮。
传统的气体渗氮是把工件放入密封容器中,通以流动的氨气并加热,保温较长时间后,氨气热分解产生活性氮原子,不断吸附到工件表面,并扩散浸透工件表层内,从而改变表层的化学成分和组织,获得优异的表面性能。
渗碳工艺的中国专利分析

渗碳工艺的中国专利分析渗碳工艺是一种常用的表面处理方法,目的是提高钢铁的硬度和耐磨性。
随着工业化的不断发展,渗碳工艺在各个行业中得到了广泛应用。
在中国,相关的渗碳技术也得到了长期的研究和实践。
本文将对中国专利中的渗碳相关技术进行简要分析。
一、渗碳原理渗碳又称渗碳硬化,是一种将碳源掺入合金材料表面,以提高其硬度、磨损和耐腐蚀性的加工工艺。
渗碳工艺主要是利用钢铁在高温条件下吸附碳的特性,通过控制温度、时间和碳源,使钢铁材料表面的碳含量得到相应的提高。
常见的渗碳方式有气体渗碳和固体渗碳两种。
气体渗碳主要是将加热的钢料放在含有高浓度碳的气体中,使其表面吸收碳元素。
固体渗碳则是将钢材浸泡在含有碳化物的固体混合物中,使碳元素向钢铁表面扩散。
1、CN107739084A 渗碳液凝胶及其制备方法及应用该专利涉及一种渗碳液凝胶及其制备方法及应用。
所述液凝胶包括醋酸纤维素、黏土、甲基纤维素、蔗糖乙酸酯、甘油、聚乙二醇等组分。
该渗碳液凝胶在制备时不仅能够保证渗碳效果的同时,还具有降低渗碳过程中残碳率和表面轻微氧化的优点。
该专利适用于钢铁、金属、非金属等材料中的渗碳处理,对于提高被渗碳材料的硬度和耐磨性等性能有显著效果。
该专利公开了一种新型环氧氨基树脂渗碳液及其制备方法。
该液体由烷基酰胺、环氧氨基树脂、淀粉、异氰酸酯、固化剂等组分组成。
所述渗碳液在渗碳过程中可以缩短渗碳时间和温度,同时也能提高被渗碳材料的硬度和耐磨性。
该专利涉及一种渗碳涂层材料及其制备方法,所述涂层材料由钨酸酐、粉末钢、氧化物、微量元素等组分组成。
所述渗碳涂层材料具有渗碳效果显著、渗碳层与底材结合紧密、硬度高等优点,适用于在各种材料表面制备高级别渗碳层的操作。
三、结论通过对中国专利中的渗碳相关技术进行分析,可以看出,中国在渗碳技术领域的研究和发展取得了不俗的成绩。
不仅涉及到渗碳材料的组分和性质的研究,还涵盖了渗碳方法和渗碳涂层等领域的创新和优化。
这些技术的出现和应用不仅为渗碳行业的发展提供了新的思路和途径,而且也对其他相关行业的应用产生了较大的推动作用。
渗碳

渗碳:是对金属表面处理的一种,采用渗碳的多为低碳钢或低合金钢,具体方法是将工件置入具有活性渗碳介质中,加热到900--950摄氏度的单相奥氏体区,保温足够时间后,使渗碳介质中分解出的活性碳原子渗入钢件表层,从而获得表层高碳,心部仍保持原有成分. 相似的还有低温渗氮处理。
这是金属材料常见的一种热处理工艺,它可以使渗过碳的工件表面获得很高的硬度,提高其耐磨程度。
渗碳(carburizing/carburization)渗碳是指使碳原子渗入到钢表面层的过程。
也是使低碳钢的工件具有高碳钢的表面层,再经过淬火和低温回火,使工件的表面层具有高硬度和耐磨性,而工件的中心部分仍然保持着低碳钢的韧性和塑性。
渗碳工件的材料一般为低碳钢或低碳合金钢(含碳量小于0.25%)。
渗碳后﹐钢件表面的化学成分可接近高碳钢。
工件渗碳后还要经过淬火﹐以得到高的表面硬度﹑高的耐磨性和疲劳强度﹐并保持心部有低碳钢淬火后的强韧性﹐使工件能承受冲击载荷。
渗碳工艺广泛用于飞机﹑汽车和拖拉机等的机械零件﹐如齿轮﹑轴﹑凸轮轴等。
渗碳工艺在中国可以上溯到2000年以前。
最早是用固体渗碳介质渗碳。
液体和气体渗碳是在20世纪出现并得到广泛应用的。
美国在20年代开始采用转筒炉进行气体渗碳。
30年代﹐连续式气体渗碳炉开始在工业上应用。
60年代高温(960~1100℃)气体渗碳得到发展。
至70年代﹐出现了真空渗碳和离子渗碳。
原理渗碳与其他化学热处理一样﹐也包含3个基本过程。
①分解渗碳介质的分解产生活性碳原子。
②吸附活性碳原子被钢件表面吸收后即溶到表层奥氏体中﹐使奥氏体中含碳量增加。
③扩散表面含碳量增加便与心部含碳量出现浓度差﹐表面的碳遂向内部扩散。
碳在钢中的扩散速度主要取决于温度﹐同时与工件中被渗元素内外浓度差和钢中合金元素含量有关。
渗碳零件的材料一般选用低碳钢或低碳合金钢(含碳量小於0.25%)。
渗碳后必须进行淬火才能充分发挥渗碳的有利作用。
工件渗碳淬火后的表层显微组织主要为高硬度的马氏体加上残余奥氏体和少量碳化物﹐心部组织为韧性好的低碳马氏体或含有非马氏体的组织﹐但应避免出现铁素体。
金属热处理,渗碳,渗氮,发黑发蓝等处理

金属热处理,渗碳,渗氮,发黑发蓝等处理金属热处理,渗碳,渗氮,发黑发蓝等处理金属热处理:1.金属热处理是将金属工件放在一定的介质中加热到适宜的温度,并在此温度中保持一定时间后,又以不同速度冷却,通过改变金属材料表面或内部的组织结构来控制其性能的一种工艺。
2.金属热处理是机械制造中的重要工艺之一,与其他加工工艺相比,热处理一般不改变工件的形状和整体的化学成分,而是通过改变工件内部的显微组织,或改变工件表面的化学成分,赋予或改善工件的使用性能。
其特点是改善工件的内在质量,而这一般不是肉眼所能看到的。
3.钢铁的热处理是金属热处理的主要内容。
另外,铝、铜、镁、钛等及其合金也都可以通过热处理改变其力学、物理和化学性能,以获得不同的使用性能。
4.热处理工艺一般包括加热、保温、冷却三个过程,有时只有加热和冷却两个过程。
这些过程互相衔接,不可间断。
5.加热是热处理的重要工序之一。
金属热处理的加热方法很多,最早是采用木炭和煤作为热源,进而应用液体和气体燃料。
电的应用使加热易于控制,且无环境污染。
利用这些热源可以直接加热,也可以通过熔融的盐或金属,以至浮动粒子进行间接加热。
6.金属加热时,工件暴露在空气中,常常发生氧化、脱碳(即钢铁零件表面碳含量降低),这对于热处理后零件的表面性能有很不利的影响。
金属通常应在可控气氛或保护气氛中、熔融盐中和真空中加热,也可用涂料或包装方法进行保护加热。
7.加热温度是热处理工艺的重要工艺参数之一,选择和控制加热温度,是保证热处理质量的主要问题。
加热温度随被处理的金属材料和热处理的目的不同而异,但一般都是加热到相变温度以上,以获得高温组织。
另外转变需要一定的时间,因此当金属工件表面达到要求的加热温度时,还须在此温度保持一定时间,使内外温度一致,使显微组织转变完全,这段时间称为保温时间。
采用高能密度加热和表面热处理时,加热速度极快,一般就没有保温时间,而化学热处理的保温时间往往较长。
8.冷却也是热处理工艺过程中不可缺少的步骤,冷却方法因工艺不同而不同,主要是控制冷却速度。
热处理知识——渗碳和渗氮
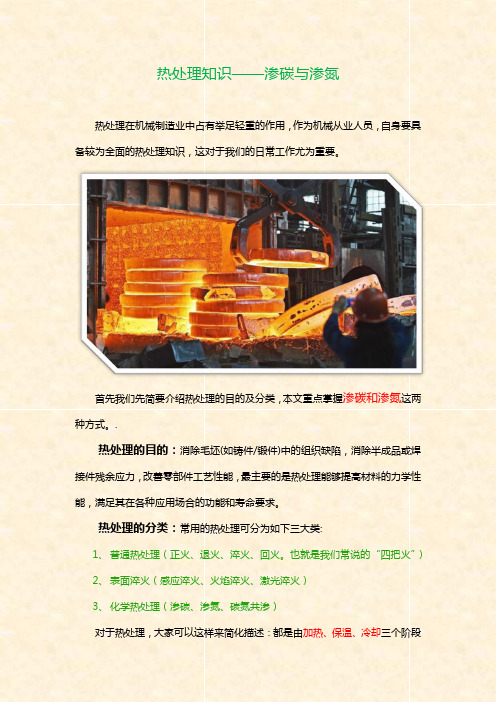
热处理知识——渗碳与渗氮热处理在机械制造业中占有举足轻重的作用,作为机械从业人员,自身要具备较为全面的热处理知识,这对于我们的日常工作尤为重要。
首先我们先简要介绍热处理的目的及分类,本文重点掌握渗碳和渗氮这两种方式。
.热处理的目的:消除毛坯(如铸件/锻件)中的组织缺陷,消除半成品或焊接件残余应力,改善零部件工艺性能,最主要的是热处理能够提高材料的力学性能,满足其在各种应用场合的功能和寿命要求。
热处理的分类:常用的热处理可分为如下三大类:1、普通热处理(正火、退火、淬火、回火。
也就是我们常说的“四把火”)2、表面淬火(感应淬火、火焰淬火、激光淬火)3、化学热处理(渗碳、渗氮、碳氮共渗)对于热处理,大家可以这样来简化描述:都是由加热、保温、冷却三个阶段组成。
不同热处理方法区别就在于这三个阶段,加热方式,加热温度或者加热的速度不同;保温方式,保温环境或者保温时间不同等;冷却的速度及冷却的环境不同等。
进入正文,主要介绍渗碳和渗氮渗碳定义:把零部件置于渗碳介质中,加热到单相奥氏体区,保温一定时间,使碳原子渗入钢表层的化学热处理工艺。
目的:使零件表面具有高硬度、耐磨及疲劳极限,心部具有较高的强度和韧性。
常用钢种:含碳量0.1%-0.25%的碳钢或合金(即低碳钢和低碳合金钢)渗碳方法:常用的气体渗碳法:工件置于密闭的加热炉中,滴入煤油、丙酮、甲苯等在高温(900-950°C)下分解出CO、CO2、CH4等,气体再分解出活性碳原子,随后活性碳原子溶于高温奥氏体中,随着时间进行,碳原子逐渐向内扩散,深度主要取决于保温时间,可大约按0.2mm/h的速度近似计算。
关键技术点:1)表面含碳量最好在0.85%-1.05%内,若含碳量过低,淬火、低温回火后得到的回火马氏体,含碳量较低,硬度低,耐磨性差。
2)在一定的渗碳层深度范围内,随渗碳层深度的增加,疲劳极限、抗弯强度及耐磨性都将增加,但渗碳层深度超过一定限度后,疲劳极限反随着渗碳层深度的增加而降低。
渗氮、渗碳工艺与操作过程

渗氮、渗碳工艺与操作过程一渗碳工艺(气体渗碳——煤油):渗碳钢的碳含量一般在0.12%~0.25%之间,其所含主要合金元素一般是铬、锰、镍、钼、钨、钛等。
○1把炉温升到800℃左右,断开电源打开炉盖,放入装好工件的工装,关闭炉盖升温到930℃左右。
在升温过程中,打开风扇及煤油阀门,以每分钟160滴的速度滴入炉内,进行排气,同时打开试样孔和排气管并点燃排气火焰。
排气时间一般为60~80分钟(保证温度到渗碳温度还要排气30分钟左右);○2当火焰为鸡蛋黄颜色时开始强渗了,此时要加大煤油的滴量,按每分钟180~200滴。
在强渗时就可用放入试棒(含碳量少的材料,尺寸Ф8×100mm),关闭试样孔,炉压保持在6~10格——渗层深炉压取高值。
渗碳速度一般按0.15~0.2mm/h来计算,如要渗层深度为0.8~1.2mm,则强渗时间为6小时,提前在强渗设定时间结束前半小时,取出试棒,观察渗层深度(试棒渗层深度一般为工件的一半,这边渗层深度靠操作工的肉眼加经验判断),深度够在强渗结束就可以开始扩散,否则增加强渗时间;○3扩散期温度不变,减少煤油滴量,按每分钟100滴,一般扩散时间为60~90分钟,作用是均匀工件表层的碳溶度;○4扩散期结束开始降温,此时断开加热器,降温到810℃左右,并在此温度保温10~20分钟。
降温期减少煤油滴量,按每分钟60滴。
保温结束时断开加热器,关闭风扇,打开炉盖,用行车吊起工装,垂直进入温度为50~70℃的油中冷却,冷却时上下左右轻轻摇动工装,一般冷却时间为10~20分钟左右,吊起工装时也要注意工件出油的温度。
○5冷却好的工件要在半个小时之内(防止工件开裂)进行低温回火,温度一般在160~190℃(由硬度要求而定),保温时间2小时左右出炉空冷。
在渗碳过程中要随时注意火焰形状,正常的火焰是:火焰呈金黄色,无力不熄灭(断续熄灭,说明水气高了),火苗无黑焰和火星,火苗长100~150mm;若火苗出现火星,说明炉内炭黑过度;火苗过长、尖端外缘呈亮白色,说明渗碳剂供量过多;火苗短、外缘呈浅蓝色并有透明,说明渗碳剂供量不足或炉子漏气。
古人打铁时怎么渗碳??
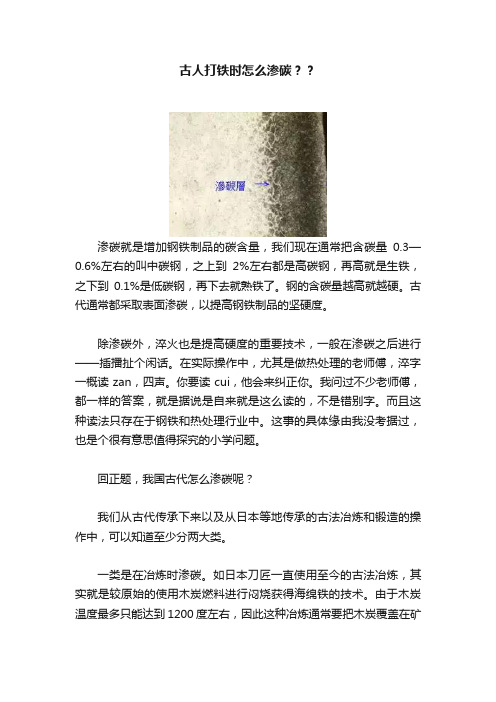
古人打铁时怎么渗碳??渗碳就是增加钢铁制品的碳含量,我们现在通常把含碳量0.3—0.6%左右的叫中碳钢,之上到2%左右都是高碳钢,再高就是生铁,之下到0.1%是低碳钢,再下去就熟铁了。
钢的含碳量越高就越硬。
古代通常都采取表面渗碳,以提高钢铁制品的坚硬度。
除渗碳外,淬火也是提高硬度的重要技术,一般在渗碳之后进行——插播扯个闲话。
在实际操作中,尤其是做热处理的老师傅,淬字一概读zan,四声。
你要读cui,他会来纠正你。
我问过不少老师傅,都一样的答案,就是据说是自来就是这么读的,不是错别字。
而且这种读法只存在于钢铁和热处理行业中。
这事的具体缘由我没考据过,也是个很有意思值得探究的小学问题。
回正题,我国古代怎么渗碳呢?我们从古代传承下来以及从日本等地传承的古法冶炼和锻造的操作中,可以知道至少分两大类。
一类是在冶炼时渗碳。
如日本刀匠一直使用至今的古法冶炼,其实就是较原始的使用木炭燃料进行闷烧获得海绵铁的技术。
由于木炭温度最多只能达到1200度左右,因此这种冶炼通常要把木炭覆盖在矿石上连续烧好几天。
而燃烧是会让钢铁失碳的,但覆盖木炭进行闷烧这种手段,使得一些未燃烧的一氧化碳经过反应,最终成了渗碳过程,部分地局部地补充了含碳量。
但也由于这种冶炼方式的原因,得到的海绵铁成品成分非常复杂,还有不少有害杂质,各部位含碳量当然更不一样。
所以铁匠们会把成品海绵铁砸开,然后凭经验挑出含碳量接近的部分归类,在分别用于不同的用途。
这是最原始也最常见的冶炼渗碳技术之一。
还有一类是在冶炼得到成品钢铁后,在锻造过程中进行渗碳。
这个过程中的手段就多了,我说的非常有意思的事情也出现在这个阶段。
手段之一,是对制品进行固体渗碳。
如日本刀制造时,在折叠锻打钢铁时,会在工件外包裹纸张和草木灰及泥浆等进行锻打,这是一种渗碳手法。
纸张草木灰都是渗入剂,泥浆则是分散剂,可防止碳渗入物黏结不匀、以及帮助析出炭黑。
我国明代《天工开物》里记载的制针方法,也是固体渗碳,但和日本刀制造过程中的渗碳技术比,这是属于非常(gao)高(da)端(shang)的外热式箱体渗碳技术,科技树的高度不可同日而语。
司母戊鼎中合金钢的详细内容介绍细化到奥氏体渗碳体
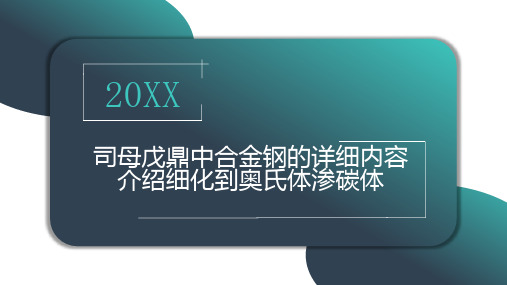
本文将详细介绍司母戊鼎中合 金钢的成分、组织及性能,并
阐述奥氏体渗碳体的作用
2
司母戊鼎的合金
成分
司母戊鼎的合金成分
司母戊鼎的主要成分是铜、锡、 铅,并含有少量的铁、镍、铝、
硅等元素
这种合金成分的配比,使得鼎的 硬度、韧性、耐腐蚀性等性能达 到了理想的平衡
3
奥氏体渗碳体
奥氏体渗碳体
在司母戊鼎的合金钢中,奥氏体渗碳体起到了关键作
1用
奥氏体是一种碳溶解在面心立方点阵金属中的固溶体,
2
具有高塑性和低硬度
渗碳体则是合金中的一种硬脆相,具有良好的耐磨性
3
和耐腐蚀性
奥氏体渗碳体
奥氏体渗碳体的形成
在司母戊鼎的制造过程中,工匠们通过精 湛的技艺和精确的合金成分配比,使得鼎 的基体金属在冷却过程中部分地转化为奥 氏体组织。同时,由于碳元素的偏析作用 ,部分奥氏体组织进一步转化为渗碳体, 从而形成了奥氏体渗碳体复合组织
司母戊鼎的制造工艺与性能优化
表面处理与防护
为了提高司母戊鼎的耐腐蚀性和 观赏性,工匠们对其表面进行了 精细的处理。如使用蜂蜡、沥青 等材料进行封护,有效地延缓了 青铜器的腐蚀进程。同时,通过 对鼎表面进行抛光处理,使其呈 现出亮丽的光泽
5
结论
r
xxxxx
结论
司母戊鼎作为中国古代青铜文化的 瑰宝,其精湛的制造工艺和卓越的 性能体现了古代人们对合金钢的运 用能力
20XX
司母戊鼎中合金钢的详细内容 介绍细化到奥氏体渗碳体
-
1
引言
2
目录
3
CONTENTS
司母戊鼎的合金成分 奥氏体渗碳体
4
司母戊鼎的制造工艺与性能优化
渗碳工艺的中国专利分析
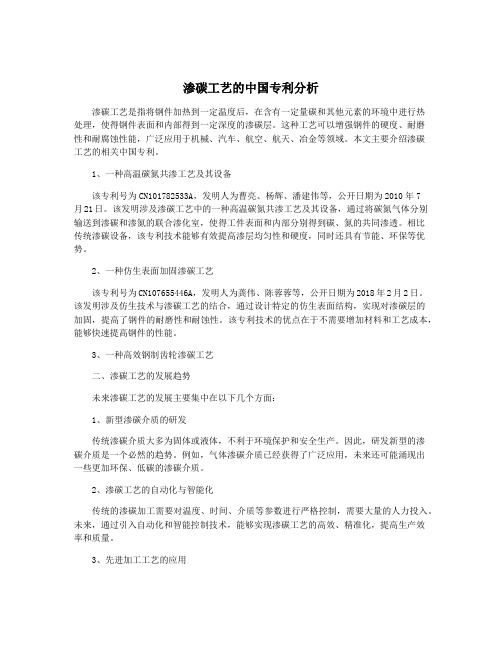
渗碳工艺的中国专利分析渗碳工艺是指将钢件加热到一定温度后,在含有一定量碳和其他元素的环境中进行热处理,使得钢件表面和内部得到一定深度的渗碳层。
这种工艺可以增强钢件的硬度、耐磨性和耐腐蚀性能,广泛应用于机械、汽车、航空、航天、冶金等领域。
本文主要介绍渗碳工艺的相关中国专利。
1、一种高温碳氮共渗工艺及其设备该专利号为CN101782533A,发明人为曹亮、杨辉、潘建伟等,公开日期为2010年7月21日。
该发明涉及渗碳工艺中的一种高温碳氮共渗工艺及其设备,通过将碳氮气体分别输送到渗碳和渗氮的联合渗化室,使得工件表面和内部分别得到碳、氮的共同渗透。
相比传统渗碳设备,该专利技术能够有效提高渗层均匀性和硬度,同时还具有节能、环保等优势。
2、一种仿生表面加固渗碳工艺该专利号为CN107655446A,发明人为龚伟、陈蓉蓉等,公开日期为2018年2月2日。
该发明涉及仿生技术与渗碳工艺的结合,通过设计特定的仿生表面结构,实现对渗碳层的加固,提高了钢件的耐磨性和耐蚀性。
该专利技术的优点在于不需要增加材料和工艺成本,能够快速提高钢件的性能。
3、一种高效钢制齿轮渗碳工艺二、渗碳工艺的发展趋势未来渗碳工艺的发展主要集中在以下几个方面:1、新型渗碳介质的研发传统渗碳介质大多为固体或液体,不利于环境保护和安全生产。
因此,研发新型的渗碳介质是一个必然的趋势。
例如,气体渗碳介质已经获得了广泛应用,未来还可能涌现出一些更加环保、低碳的渗碳介质。
2、渗碳工艺的自动化与智能化传统的渗碳加工需要对温度、时间、介质等参数进行严格控制,需要大量的人力投入。
未来,通过引入自动化和智能控制技术,能够实现渗碳工艺的高效、精准化,提高生产效率和质量。
3、先进加工工艺的应用随着激光加工、电化学加工、等离子喷涂等先进加工技术的不断发展,未来有可能在渗碳工艺中应用这些技术,实现对渗层的定制加工,使得渗碳工艺的应用更加高效和精准。
- 1、下载文档前请自行甄别文档内容的完整性,平台不提供额外的编辑、内容补充、找答案等附加服务。
- 2、"仅部分预览"的文档,不可在线预览部分如存在完整性等问题,可反馈申请退款(可完整预览的文档不适用该条件!)。
- 3、如文档侵犯您的权益,请联系客服反馈,我们会尽快为您处理(人工客服工作时间:9:00-18:30)。
中国古代的钢铁渗碳和渗氮技术我国是最古老的文明古国之一,在金属热处理技术发展史上,我国古代先民做出过杰出的贡献,取得了许多伟大的成就。
在化学热处理方面,我国先民依靠自己的聪明才智,发展了多种工艺,包括渗碳、渗氮、碳氮共渗等。
这些技术的发展,推动了我国古代金属材料的应用和对材料的表面改性,形成了具有特色的古代热处理技术。
本文在文献史料和考古成果综合分析的基础上,力图反映我国古代钢铁渗碳和渗氮技术状况,并提出一些分析见解,以求同行较全面准确地认识古代化学热处理的发展历程。
限于热处理考古属交叉领域,不当之处在所难免,望予以指正。
1 钢铁渗碳技术1.1 固体渗碳固体渗碳是将工件埋入固体渗碳物质中进行处理的工艺,它是最古老的热处理技术之一。
从公元前18世纪一直到18世纪,固体渗碳都是西方钢铁增碳的主流手段。
因此在国外产生了多种不同的固体渗碳工艺,大体可分为灼烧法、焖熬法和层叠法。
其渗碳工艺水平相当高,甚至在17世纪以后还开发出固体渗碳专用的窑炉和箱式炉。
我国古代除了拥有传统的灼烧法固体渗碳方法以外,古文献中还描述了焖熬法固体渗碳方法。
1.1.1 灼烧法固体渗碳一般认为人工冶铁的发源地是两河流域北部、土耳其及其附近地区。
该地有很多的铁矿,而铜矿又较少。
在靠近土耳其的Changar Ba zar镇出土的匕首柄,其年代可定为公元前2700年以前。
而根据报道,在Gizeh的大金字塔内遗存一块铁板,使人工冶炼金属铁板的年代提前到公元前2761年以前。
这些人工冶铁器件是将铁矿石还原后经锻接的产物。
人工冶铁的初级产品是海绵铁,它是由铁矿石在约1200℃的木炭火的温度下还原出来的,海绵铁是杂质含量很高的松散、柔软的金属块,其杂质主要有未还原的氧化铁、铁橄榄石、木炭粉等,为了用它制作器物,只有将其反复加热锻打、去渣、聚块、分散杂质后,才能获得可以造型的熟铁,这种熟铁通常被称为块炼铁。
海绵铁的加热往往是在灼热的木炭中进行,其时铁被埋在木炭之间,在铁的作用下,未完全燃烧的一氧化碳发生分解,分解的活性碳形成高的碳势,铁在碳势气氛中,自然而然地被渗碳。
这种不自觉的固体渗碳可以认为基本是与块炼铁同时出现的,可以说这是金属化学热处理的开端。
对中国冶铁术的起源年代有很大的争议,迄今为止,我国发掘的年代最久远的块炼铁制品可能是新疆哈密三堡焉不拉克墓地出土的公元前1300年的弧背直刃刀。
我国出土的较早的铁器还有和静察吾乎沟口一号墓地中出土的公元前1000年左右的铁器残片和河南三门峡市上村岭虢国西周晚期墓葬中发掘出土的公元前9至8世纪的铜茎玉柄铁剑等。
也就是说在我国不自觉地应用固体渗碳工艺可能始于公元前1300年以前,一般早期的块炼铁产品的含碳量都很低,渗层很浅,有的铁器甚至测不出碳的存在。
从不自觉地应用固体渗碳过渡到固体渗碳的诞生,从利用炭火外焰的加热功能到利用炭火内焰的渗碳功能,可能经历了相当长的一段时间。
当人们意识到在灼热的木炭中在不同情况下氧化的程度和硬化的效果不同,人们逐渐考虑如何改变加热方式,最简单的办法是将工件埋入炭火深处,尽管降低了工件加热的速度,却使工件容易在不完全燃烧的含碳气氛中获得一定的增碳效果,直到最后依靠添加渗碳物质和调整鼓风条件,使工件获得较高的含碳量,从而发展成为有意识的固体渗碳,这一方法在国外制铁业的发源地大约出现于公元前1800年以前。
公元前12世纪的腓力斯铁剑的含碳量从0到0.8%C不等。
埃及的公元前10世纪的斧头,心部含碳为零,刃部的含碳量达0.9%。
而从考古发掘的含碳块炼铁器物来看,中国古代有意识的渗碳大约始于春秋时期,其年代大约在公元前7至前6世纪,出土的器物中的碳很容易被测出。
我国出土的块炼铁实物不多,考古证实在春秋晚期墓葬中已经出现中碳的块炼铁渗碳钢。
如对湖南长沙杨家山出土的春秋晚期钢剑的分析表明,其含碳量为0.5%左右,属块炼铁渗碳钢制品,其年代为公元前6世纪左右。
对燕下都的战国剑、满城西汉墓的刘胜佩剑等制品进行了较为详细的分析,表明它们的心部均为低碳钢,表层均为中高碳钢,在组织中还有很多的未经还原和熔解的FeO和2FeO·Si ,这都是典型的块炼铁渗碳钢制O2品。
1.1.2 焖熬法固体渗碳焖熬法固体渗碳可能是从灼烧法固体渗碳发展而来的,采用灼烧法要获得理想的渗碳效果,必须将工件深埋于火炭之中,尽量减少渗碳气氛的流失,因而出现了焖熬法固体渗碳工艺。
采用焖熬法可降低高碳势气氛的氧化和流失,从而使铁件具有更高的含碳量。
国外考古发现,在印度很早就有采用坩埚进行渗碳的方法,是将熟铁和木炭混合装入坩埚,封闭起来后加热。
这种采用坩埚的焖熬法固体渗碳在欧洲流行了很长的时期,成为中世纪国外制钢的主要手段之一。
中国古代开始采用焖熬法固体渗碳年代尚无从知晓,看来采用的是完全不同的方法。
明代宋应星的《天工开物》中记载了一种焖熬法固体渗碳技术,写道:“凡针,先锤铁为细条。
用铁尺一根,锥成线眼,抽过条铁成线,逐寸剪断成针。
先其末成颖,用小槌敲扁其本,刚锥穿鼻,复其外。
然后入釜,慢火炒熬。
炒后以土末松木火矢、豆豉三物罨盖,下用火蒸。
”可知当时的渗碳是在釜中进行的,采用釜外供热方式,固体渗碳剂中松木火矢是一种木炭,同书有说明火矢是木材经“不闭穴火”所获产物,是主要的渗入剂;豆豉也是含碳物质是辅助渗入剂;土末是分散剂,对防止含碳物质的相互黏结和炭黑的析出有一定的作用。
这与当今的装箱固体渗碳方法如出一辙。
它们的加热方式已不同于传统的内热式,而采用的是外热式。
外热式与内热式比较,有明显的优点,主要是碳势高、碳源稳定、渗碳均匀。
在近代这种焖熬法固体渗碳方法还被华中和华北地区的工匠采用,所用的“釜”是铁锅,制备的钢被称为“焖钢”。
1·2 液体渗碳液体渗碳与固体渗碳比较,有渗速快、渗层厚度均匀和产品质量稳定等的优点。
中国古人独创了以熔融生铁为渗碳剂的液体渗碳方法,极大地推进了我国古代的钢铁制造业。
据《吴越春秋·阖闾内传》所载,铸剑师干将制剑时,遇到“金铁之精不销沦流”,乃“断发剪爪,投入炉中,使童女童男三百人鼓橐装炭,金铁乃濡。
遂以成剑,阳曰干将,阴曰莫耶,阳作龟文,阴作漫理。
”杨宽认为这是一种以海绵铁为原料的固体渗碳制钢之术。
根据描述的“三百人鼓橐装炭”的情况看,更像是液体渗碳,可以认为干将在制剑时,将块炼铁的剑坯埋入以铁碎末和含碳物质为主的渗剂中加热,渗剂中的铁达到一定含碳量后,“金铁乃濡”,这时铁碎末和铁坯表面与含碳物质反应而熔化,“濡”指的是铁坯未完全熔化。
受当时的加热温度所限,通过三百人鼓橐装炭,有可能使炼炉的炉内温度达到铁碳合金熔点的下限1148℃,从而使块炼铁的剑坯获得渗碳效果。
从此看来,《吴越春秋》描绘的事件极有可能是液体渗碳的开端。
液体渗碳显然是在当时的金属加工工艺方面取得的一项突破性的进展,无怪乎先人的著作对此重笔称赞。
而此前,工匠运用的技术是未出现熔化的渗碳剂的固体渗碳方法。
根据文献分析,干将制剑事件大约是出现在公元前6世纪。
中国古代工匠主要通过3种方法获得含碳很低的铁与钢,一是块炼铁,二是退火脱碳钢,三是炒钢。
他们称含碳很低的铁为熟铁,熟铁性软,为使其坚硬,中国古人发明了以熔融生铁为渗碳剂的液体渗碳方法。
有关生铁与熟铁杂炼的记载很多。
《北史》:“怀文造宿铁刀,其法烧生铁精,以重柔铤,数宿则成刚”。
《重修政和经史正们类备用本草》中引南朝陶弘景语:“钢铁是杂炼生柔作刀镰者”。
苏颂《本草图经》:“以生柔相杂合,用以作刀剑锋刃者为钢铁”。
明代宋应星在《锤锻》篇中提及,锄用“熟铁锻成,熔化生铁淋口,入水淬健,即成刚劲”。
可以看出,该处理方法是将锄具在熔化生铁中渗碳,最终使得其表面成为高碳钢,经淬火后得到马氏体而强化。
这是典型的采用液体渗碳对锄具进行表面处理的工艺,实际上成为一种制钢的方法,制取的钢被称为灌钢,是我国古代钢铁技术的一项独创性的成就。
宋应星对此工艺描述得很详细,在《五金》篇中指出,将“熟铁打成薄片”,生铁安置其上,“火力到时,生钢(铁)先化,渗淋熟铁之中,两情投合。
”关于灌钢,较早见于公元3世纪西晋张协的《七命》:“乃炼乃烁,万辟千灌。
”其中“辟”是折叠,“灌”是渗入。
这一工艺被李约瑟称为“合炼法”,英文是“co-fusion”,史密斯则认为这一工艺用“灌注法(perfusion)”来表达更贴切,“perfusion”刚好有“灌”、“渗”之意。
采用熔融生铁作为渗碳剂的用于小农具生产的“灌注法”在前些年还在使用,有时这种方法也被误称为“擦生法”,从工件与生铁的作用时间和后续处理的情况来看。
“擦生法”应属固体渗碳+加工的复合热处理范畴。
国内外尚未见对液态生铁渗碳进行详细研究的报导,实验表明液态生铁的渗速相当快,因而在近代的中国这一工艺仍被广为采用。
当然,以熔融生铁作为渗剂要比现在用熔融盐液作为渗剂的渗碳方法难得多,主要是加热慢、温度高、渗剂消耗大,而且更重要的是要将温度控制在共晶线和液相线之间,但对于不知渗碳原理的古代工匠来说,能想到这一方法真可谓匠心独具,也使我国古代的渗碳技术遥遥领先。
国外液体渗碳技术是近代才发展起来的,波斯人从19世纪方才考虑以生铁取代木炭为渗碳剂的坩埚法渗碳方法。
在西方工业国大规模应用气体渗碳方法以前,将熟铁块埋在熔融生铁之下进行渗碳反复处理仍是主要的方法。
1.3 固-液渗碳固-液渗碳不同于固体或液体渗碳,它是以固态物质为骨架或载体、液态物质为渗剂的渗碳方式。
最常见的固—液渗碳工艺是膏体法渗碳,是将含碳物质混和于粘性物质中,形成膏体,涂于工件表面,在后续的加热处理中,碳渗入工件表面。
为了要在涂膏中获得液相,一般在膏体中都要添加盐类,盐在600~900℃经常呈熔融态。
中世纪的欧洲常用毛发、蹄角灰和盐作为膏体的主要填料进行渗碳。
我国古代文献中多次提及膏体法渗碳。
《便民图篡》提及:“羊角、乱发俱煅灰,细研,水调,涂刀口,烧红,磨之。
”羊角、乱发经煅烧后主要成分为氧化钙、碳酸钙和未充分燃烧的生物角质,这些物质含碳。
其中氧化钙、碳酸钙主要是被用作为载体,而未充分燃烧的生物角质为含碳渗入剂。
明代《物理小识》“器用类·淬刀法”中干脆用未经煅烧的生物角质为含碳渗入剂:“一以羊角,乱发为末,调傅刀口,不必蟾酥而自然灰埋也。
”其中羊角、乱发是主要的含碳物质,它们含碳量高于其灰;“蟾酥”为癞蛤蟆皮下的汁液,是生物油脂,油脂不仅可做黏结剂,也可做渗碳剂;“自然灰”主要成分是碳酸钠,看来此工艺开始时的关键是以蟾酥为添加剂,以后发展成以自然灰为重要添加剂的工艺。
这两种添加剂都是很必要的,自然灰的应用是一个明显的进展,不仅因为自然灰来源相对广泛,更重要的是因为碳酸钠具有明显的碳原子的催渗效果。
现在液体化学热处理常用碳酸钠作为渗碳促进剂,在膏体中亦有其催渗效果。