宽厚板生产线工艺流程
宽厚板生产工艺设计

宽厚板生产工艺设计摘要本文对中厚板目前在我国的发展状况形式及中厚板轧制过程中的轧制规程、轧制方法及道次的确定进行阐述,并且对中厚板在轧制中的工艺、参数、设备,进行了进一步说明。
关键词:中厚板 ;轧钢工艺;轧钢设备Design of the production process of heavy plateAbstractIn this paper, plate current form of development in China and in the process of plate rolling schedule, rolling method and passes the determination to elaborate, and on the plate in the rolling process, parameters, equipment, further instructions.Key words: plate; steelrolling process; steelrolling equipment目录第1章绪论.......................................... 错误!未定义书签。
1.1国内中厚板生产简介................................... 错误!未定义书签。
1.2国外中厚板轧机的发展................................. 错误!未定义书签。
1.3中厚板生产的进步 (4)1.3.1生产技术方面的进步 (4)1.3.2装备方面的进步........................................................................... 错误!未定义书签。
1.4我国中厚板发展的不足................................. 错误!未定义书签。
宽厚板轧制工艺

展宽轧制有纵向展宽轧制、横向展宽轧制和角轧展宽 轧制三种。横向展宽轧制是目前厚板厂普遍使用的方
式。
2013-7-11 4
宽厚板轧制工艺
3)精轧(Final Rolling)阶段
精轧轧制的目的
质量控制
轧制延伸
通过板形控制、厚度控制、性能控制及表 面质量控制等手段生产出板厚精度高、同板差 小、平坦度好及具有良好的综合性能的钢板。
控轧轧制(TMR)
控制轧制手段
成份:Nb、V、Ti等碳氮化物生成元素是发挥控制轧制 效果的重要元素。 加热:采用通过低温加热,初期粒径变小,也是实现细
粒化的方法。
轧制:未再结晶区域的强压下,两相区的轧制是目前控 制轧制最有效的手段。
2013-7-11 13
宽厚板轧制工艺
控轧轧制(TMR)
单机架多块钢轧制工艺
11
宽厚板轧制工艺
控轧轧制(TMR)
第三阶段:(γ +α )两相区的 轧制(<Ar3) 如在两相共存区进一步轧制,
未相变的奥氏体晶粒更加伸长,
在晶粒内形成形变带。另一方面, 已经相变完成的铁素体晶粒中因
冷加工会形成位错密度高的亚晶
粒。其结果变成真正的晶粒细化。
2013-7-11
12
宽厚板轧制工艺
宽厚板轧制工艺
宽厚板轧制工艺
-轧线工艺
制作:胡贤磊
时间:2008年3月
2013-7-11
1
宽厚板轧制工艺
厚板轧制特点
厚板轧制的特点是尺寸规格繁多、轧制 中要求有展宽轧制。
厚板轧制过程一般分为以下三个阶段。
成形轧制、展宽轧制、精轧轧制
2013-7-11
2
宽厚板轧制工艺
宽厚板轧制工艺

4/9/2020
9
控轧轧制(TMR)
➢ 第一阶段:再结晶区轧制 (≥950℃) 经高温加热晶粒变粗的奥 氏体随着反复 轧制-再结晶 而逐步变细。再结晶及其以 后的晶粒成长是短时间发生 的,未见明显的微细化。在 再结晶温度领域的下限附近 的强化轧制,由于因轧制引 起的再结晶晶粒细化而使奥 氏体晶粒明显变化。
宽厚板轧制工艺
12
控轧轧制(TMR)
➢控制轧制手段
宽厚板轧制工艺
成份:Nb、V、Ti等碳氮化物生成元素是发挥控制轧制 效果的重要元素。
加热:采用通过低温加热,初期粒径变小,也是实现细 粒化的方法。
轧制:未再结晶区域的强压下,两相区的轧制是目前控 制轧制最有效的手段。
4/9/2020
13
控轧轧制(TMR)
宽厚板轧制工艺
宽厚板轧制工艺
-轧线工艺
制作:胡贤磊 时间:2008年3月
4/9/2020
1
宽厚板轧制工艺
厚板轧制特点
厚板轧制的特点是尺寸规格繁多、轧制 中要求有展宽轧制。
厚板轧制过程一般分为以下三个阶段。
成形轧制、展宽轧制、精轧轧制
4/9/2020
2
宽厚板轧制工艺
1) 成形轧制(Sizing Rolling)阶段
4/9/2020
5
厚板轧制过程示意图
宽厚板轧制工艺
4/9/2020
6
控轧控冷(TMCP) 技术
➢TMCP材特点:
宽厚板轧制工艺
强度、韧性、可焊性的统一;
降低成本、提高加工性能。
4/9/2020
7
控轧控冷(TMCP) 技术
宽厚板轧制工艺
➢控轧轧制(TMR)
固溶强化: 添加C,Mn,Si,Ni 等合金元素;
宽厚板工艺流程

宽厚板工艺流程宽厚板工艺流程宽厚板是一种广泛应用于建筑、电力、汽车和机械制造等行业的金属材料。
在其生产过程中,需要经历多个工艺流程来保证产品质量和性能。
首先,原材料准备是宽厚板生产的第一步。
通常使用的原材料包括钢坯和钢带。
这些原材料需要经过检验和筛选,以确保其符合生产标准和要求。
接下来是钢坯预处理。
钢坯通常需要经过切割、破碎和清洗等处理工艺,以去除表面氧化物、气孔和杂质,并为后续的加工做好准备。
然后是热轧工艺。
热轧是宽厚板生产的核心工艺之一。
在这个过程中,钢坯经过预热和热轧机械压制,在高温下经过多次加热和轧制,最终形成所需的宽厚板。
热轧工艺可以改变钢材的结构和性能,提高其机械强度和塑性。
紧接着是冷轧工艺。
冷轧是在宽厚板热轧之后的一个重要工艺。
在这个过程中,宽厚板通过冷轧机进行冷压,以进一步提高板材的表面精度和尺寸稳定性。
冷轧工艺可以提高宽厚板的表面质量,使其适用于更高要求的应用领域。
然后是退火处理。
退火是一种热处理工艺,将宽厚板加热到一定温度并保持一段时间,然后缓慢冷却。
退火可以改变宽厚板的组织结构,提高其机械强度和塑性,并减轻因冷加工导致的内应力和组织不均匀问题。
最后是表面处理工艺。
宽厚板通常需要进行涂层、喷漆或镀锌等表面处理,以提高其耐腐蚀性和装饰性。
这些工艺可以保护宽厚板的表面,延长其使用寿命。
综上所述,宽厚板的工艺流程包括原材料准备、钢坯预处理、热轧、冷轧、退火处理和表面处理等多个环节。
每个工艺环节都有各自的目的和要求,必须严格按照工艺流程进行执行,以保证宽厚板的质量和性能。
只有通过科学合理的工艺流程,才能生产出符合市场需求的高质量宽厚板产品。
莱钢4300mm宽厚板生产线工艺技术特点
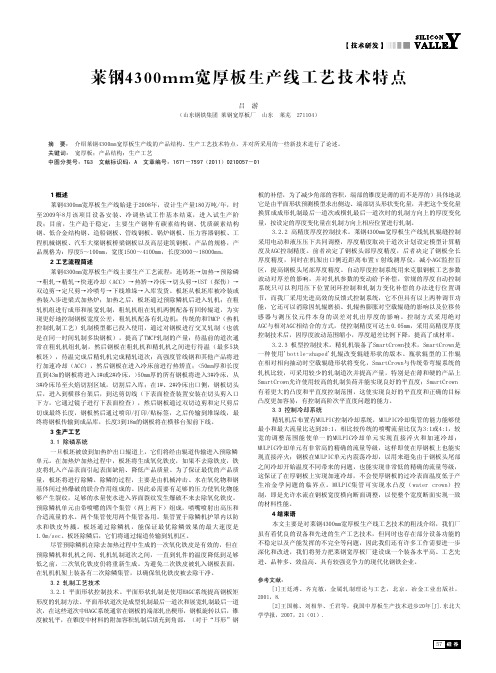
莱钢4300mm宽厚板生产线工艺技术特点吕游(山东钢铁集团 莱钢宽厚板厂山东莱芜 271104)摘 要:介绍莱钢4300mm宽厚板生产线的产品结构、生产工艺技术特点,并对所采用的一些新技术进行了论述。
关键词:宽厚板;产品结构;生产工艺中图分类号:TG3 文献标识码:A 文章编号:1671-7597(2011)0210057-011 概述板的补偿,为了减少角部的容积,端部的锥度是薄的而不是厚的)具体地说它是由平面形状预测模型求出侧边、端部切头形状变化量,并把这个变化量莱钢4300mm宽厚板生产线始建于2008年,设计生产量180万吨/年,时换算成成形轧制最后一道次或横轧最后一道次时的轧制方向上的厚度变化至2009年8月该项目设备安装、冷调热试工作基本结束,进入试生产阶量,按设定的厚度变化量在轧制方向上相应位置进行轧制。
段;目前,生产趋于稳定,主要生产钢种有碳素结构钢、优质碳素结构3.2.2 高精度厚度控制技术。
莱钢4300mm宽厚板生产线轧机辊缝控制钢、低合金结构钢、造船钢板、管线钢板、锅炉钢板、压力容器钢板、工采用电动和液压压下共同调整,厚度精度取决于道次计划设定模型计算精程机械钢板、汽车大梁钢板桥梁钢板以及高层建筑钢板,产品的规格,产度及AGC控制精度。
前者决定了钢板头部厚度精度,后者决定了钢板全长品规格为:厚度5~100mm,宽度1500~4100mm,长度3000~18000mm。
厚度精度,同时在机架出口侧近距离布置γ射线测厚仪,减小AGC监控盲2 工艺流程简述区,提高钢板头尾部厚度精度。
自动厚度控制系统用来克服钢板工艺参数莱钢4300mm宽厚板生产线主要生产工艺流程:连铸坯→加热→预除磷波动对厚差的影响,并对轧机参数的变动给予补偿,常规的厚度自动控制→粗轧→精轧→快速冷却(ACC)→热矫→冷床→切头剪→UST(探伤)→系统只可以利用压下位置闭环控制和轧制力变化补偿的办法进行位置调双边剪→定尺剪→冷喷号→下线堆垛→入库发货。
厚板工艺流程

厚板工艺流程
厚板工艺流程主要包括以下步骤:
1. 板材切割:根据设计要求将原始的金属板材切割成所需的形状和尺寸。
常用的切割方法有火焰切割、等离子切割、激光切割等。
切割完成后,板材需要进行校平和清理的处理,以确保下一步工艺的顺利进行。
2. 预弯处理:通过预弯操作,将板材的边缘折弯成所需的角度。
这一步骤主要是通过专用的边缘卷辊进行,使板材在弯角处加强性能,并为下一步的成型做好准备。
3. 成型轧制:消除板坯表面的影响和提高宽度控制的精度,沿板坯长度方向或斜向进行1~4道轧制,把坯料轧至所要求的厚度。
4. 展宽轧制:为达到轧制成品规格所要求的宽度,板坯转90°、沿板宽方向轧制。
5. 精轧:展宽轧制后再转90°,转回原坯料长度方向,轧制到成品板厚度。
6. 探伤检测:根据钢板质量要求,用超声波进行不同深度的探伤,对焊管用板的四个板边要全面进行探伤。
7. 涂层处理:如果需要防锈,可使用抛丸涂层法。
抛丸去除氧化铁皮后,再涂层防锈,涂层后应快干。
8. 其他处理:根据成品交货状态的不同,可能需要进行热处理、抛丸或涂漆等处理。
请注意,厚板的生产工艺流程根据每个厂的生产线布置情况、车间内物流的走向以及其主要产品品种和交货状态的不同而具有其各自的特点。
如需了解更多信息,建议咨询专业人士。
厚板生产工艺

–
矫直速度是根据钢板的矫直温度、厚度及强度性能等因素确定的,速度范 围为0.8~2.0m/sec(通过最大2.5 m/sec),在使用快速冷却设备时, 须与快速冷却同步。 矫直压下量主要取决于钢板的矫直温度,一般在1.0~5.0mm的范围内选 取。
厚度大于80~250mm的钢板从矫直机中空过
–
–
冷却
轧后加速冷却(ACC)
在四辊精轧机和热矫直机之间布置有一套钢板加速冷却系统。 对于那些要求进一步提高强度或改善焊接性能和低温韧性的产品,以及那些要求抗氢致 裂纹(HIC)或抗硫化物应力腐蚀(SSCC)的产品,在完成控制轧制后即进入ACC装置进行加 速冷却。 根据不同的产品要求,这套冷却系统分为两部分:高压喷水冷却系统(DQ)、加速冷却系 统(ACC)。一旦两套冷却系统同时使用,就有可能采用两个不同的冷却速率对钢板进行冷 却,从而使钢板在厚度方向上的机械性能保持一致。但大多数情况下,一般只采用其中的 某一系统对钢板进行冷却。 加速冷却钢板的厚度一般在10~12mm以上。钢板在成品轧制的最后一个道次抛钢后, 由辊道运送,按照给定的速度直接进入ACC装置。钢板通过ACC装置时,上、下两面同时 喷水进行加速冷却,使钢板的温度由约700~800℃(即奥氏体区或双相区)快速下降至约 400~650℃。 根据成品钢板的不同长度,通过ACC装置冷却时可以采用两种方式:当长度26m时,钢 板可进行摆动冷却;当长度26m时,采用直通式冷却。钢板通过ACC装置的速度约0.5~ 2.5m/sec,考虑在上、下两面喷冷的同时,还有侧喷以清除板面的汽化层。 厚度在25mm以上的钢板,通过ACC装置的速度约在0.5~1.2m/sec之间;对厚度小于 25mm的钢板,通过速度最高可达2.5m/sec。 对其它控轧钢板,以及那些含碳量或合金含量较高的结构钢、工具钢等轧后不宜喷水降 温的钢板,在通过ACC装置时,不予喷水。
济钢4300mm宽厚板生产线工艺及设备特点
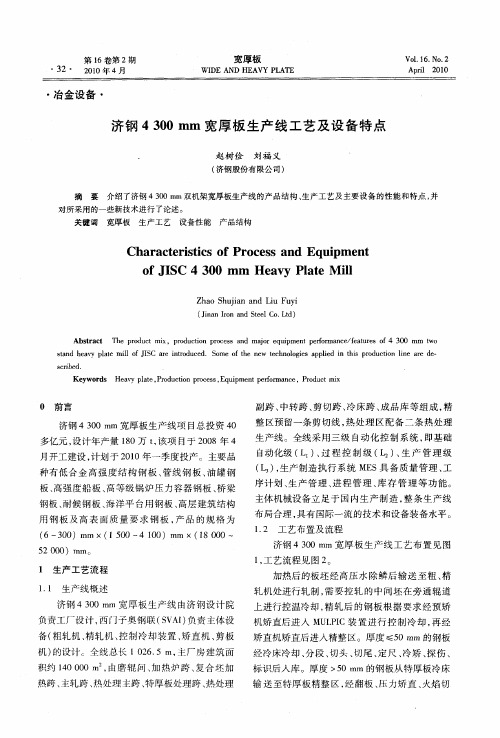
第 2期
赵树俭等 : 济钢430m m宽厚板生产线工艺及设备特点 0
。 3・ 3
1 步进式加热炉 ;2 台车式加热炉; 3 高压水除鳞系统 ; 4 四辊粗轧机 ;5 旁通辊道装置 ;-1 精轧机 ; 一 一 一 - - 6  ̄
7 预矫机 ; 8轧后 控制冷却装置 ; 9 热矫直机 ; 1一 一 一 一 O 步进 式 冷 床 ; l一 头 剪 ; 1 一 边 剪 ;3 超 声 波 探 伤 装 置 1切 2双 1一 1 定 尺 剪 ; l 一冷 矫 机 ; 1 一 平 机 ; 1一自动 火 焰切 割 机 ; 1一 4一 5 6压 7 8 厚板 缓 冷坑 ; 1一 段 剪 2 一 刃 机 ; 9分 O抛 2 一 底 热 处 理 炉 ; 2 一自动 火 焰 切 割 机 ; 2 一 火 机 ; 2一 直 机 ; 2一 床 ; 2 一 样 剪 ; 2 一 库 1辊 2 3淬 4矫 5冷 6取 7板
矫 直机矫 直后进入 精整 区。厚度 ≤5 / 的钢板 0FT f/ /
经冷床 冷却 、 分段 、 切头 、 尾 、 尺 、 切 定 冷矫 、 伤 、 探
标 识后入 库 。厚度 > 0m 的钢板从 特厚板冷 床 5 m 输 送 至特厚 板精整 区 , 经翻板 、 力矫 直 、 压 火焰切
( 济钢股份有限公)
摘
要
介绍了济钢 430m 0 m双机架宽厚板生产线 的产 品结构 、 生产 工艺及主要设 备的性能和特点 , 并
生 产工 艺 设备 性 能 产 品结 构
对所 采 用 的 一些 新 技 术进 行 了论 述 。 关 键 词 宽厚 板
Ch r c e itc fPr c s n u p e t a a t rs is o o e s a d Eq i m n
厚板生产工艺

时效炉
用途:对淬火厚板进行加热到一定温度, 保温一定时间后,使固溶于铝基体中强 化相析出,达到弥散强化作用 30吨时效炉温度范围:80-250 ℃,料垛 尺寸:1400×2500×10000mm 50吨时效炉温度范围:80-280 ℃,料垛 尺寸:1400×4000×16000mm
典型合金时效参数
热轧线工艺控制关键
铸锭加热温度 厚板尺寸精度控制 板材不平度控制
三、精整线(中厚板) 精整线(中厚板)
主要设备及参数
辊底式淬火炉
用途:对板材加热到一定温度、保温一定 时间后快速冷却,使板材强化相固溶到铝基 体中,形成过饱和固溶体 产品规格:6-200×1000-3500 ×600013500mm 固溶温度:465-550 ℃ 淬火方式:喷淋式
目 录 一、厚板生产流程图 二、热轧线 三、精整线(中厚板) 精整线(中厚板)
一、厚板生产流程图
铸锭
铣面
加热
热轧
包铝
剪切
可强化
不可强化
矫直
退火
淬火
矫直
退火
锯切
矫直
拉伸板
淬火板
锯切
矫直
包装
锯切
预拉伸
矫直
包装
锯切
包装
时效
锯切
包装
锯切
包装
包装
二、热轧线
主要设备及参数
加热炉
作用:对铸锭加热,使铸锭温度达到最佳 热塑性区间,提高热轧生产效率。 6台链式双膛炉,炉膛尺寸 568×3140×21800mm,可装铸锭400×11201620×1085-4000mm; 1台推进式加热炉可装铸锭规格370600×980-1700×2300-5000mm, 炉气温度650℃,加热温度范围350-550 ℃
厚板生产工艺

轧后加速冷却(ACC)
在四辊精轧机和热矫直机之间布置有一套钢板加速冷却系统。 对于那些要求进一步提高强度或改善焊接性能和低温韧性的产品,以及那些要求抗氢致 裂纹(HIC)或抗硫化物应力腐蚀(SSCC)的产品,在完成控制轧制后即进入ACC装置进行加 速冷却。 根据不同的产品要求,这套冷却系统分为两部分:高压喷水冷却系统(DQ)、加速冷却系 统(ACC)。一旦两套冷却系统同时使用,就有可能采用两个不同的冷却速率对钢板进行冷 却,从而使钢板在厚度方向上的机械性能保持一致。但大多数情况下,一般只采用其中的 某一系统对钢板进行冷却。 加速冷却钢板的厚度一般在10~12mm以上。钢板在成品轧制的最后一个道次抛钢后, 由辊道运送,按照给定的速度直接进入ACC装置。钢板通过ACC装置时,上、下两面同时 喷水进行加速冷却,使钢板的温度由约700~800℃(即奥氏体区或双相区)快速下降至约 400~650℃。 根据成品钢板的不同长度,通过ACC装置冷却时可以采用两种方式:当长度26m时,钢 板可进行摆动冷却;当长度26m时,采用直通式冷却。钢板通过ACC装置的速度约0.5~ 2.5m/sec,考虑在上、下两面喷冷的同时,还有侧喷以清除板面的汽化层。 厚度在25mm以上的钢板,通过ACC装置的速度约在0.5~1.2m/sec之间;对厚度小于 25mm的钢板,通过速度最高可达2.5m/sec。 对其它控轧钢板,以及那些含碳量或合金含量较高的结构钢、工具钢等轧后不宜喷水降 温的钢板,在通过ACC装置时,不予喷水。
轧制
在轧机前后(粗、精)设置有转钢辊道和推床。 一般情况下,普通热轧、控制轧制过程都包含成形轧制、展宽轧制和延长轧 制三个基本阶段。 送达轧机处的板坯,将根据不同的钢种和成品规格,有以下两种轧制工艺: 普通热轧 对一般用途的普通碳素钢、中高碳钢、部分合金结构钢以及成品厚度在 80~100mm以上的各类钢板,均采用普通轧制工艺。 控制轧制 对于成品厚度在5~80mm的造船板、锅炉板、容器板、管线板、各类高强 结构板及部分海洋石油平台板等低碳低微合金钢,屈服强度级别约在 500MPa左右及以下者,采用控制轧制工艺生产。
宽厚板材热处理调质生产线的制作方法
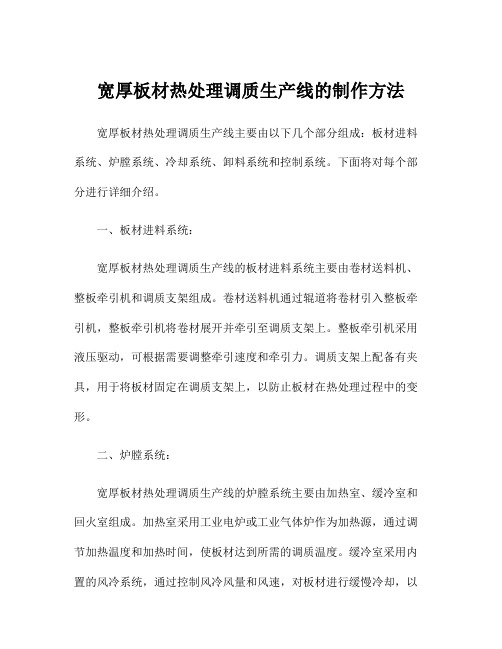
宽厚板材热处理调质生产线的制作方法宽厚板材热处理调质生产线主要由以下几个部分组成:板材进料系统、炉膛系统、冷却系统、卸料系统和控制系统。
下面将对每个部分进行详细介绍。
一、板材进料系统:宽厚板材热处理调质生产线的板材进料系统主要由卷材送料机、整板牵引机和调质支架组成。
卷材送料机通过辊道将卷材引入整板牵引机,整板牵引机将卷材展开并牵引至调质支架上。
整板牵引机采用液压驱动,可根据需要调整牵引速度和牵引力。
调质支架上配备有夹具,用于将板材固定在调质支架上,以防止板材在热处理过程中的变形。
二、炉膛系统:宽厚板材热处理调质生产线的炉膛系统主要由加热室、缓冷室和回火室组成。
加热室采用工业电炉或工业气体炉作为加热源,通过调节加热温度和加热时间,使板材达到所需的调质温度。
缓冷室采用内置的风冷系统,通过控制风冷风量和风速,对板材进行缓慢冷却,以消除内部应力,提高材料的韧性。
回火室则用于对调质后的材料进行回火处理,回复材料的硬度和强度。
三、冷却系统:宽厚板材热处理调质生产线的冷却系统主要包括水冷却系统和风冷却系统。
水冷却系统将通过喷水或浸水的方式对板材进行冷却,以快速降低板材温度,提高材料的硬度。
风冷却系统通过喷射冷却气体,如氮气或氧气,对板材进行冷却。
冷却系统可根据板材的不同要求进行调整,以获得理想的硬度和强度。
四、卸料系统:宽厚板材热处理调质生产线的卸料系统主要包括卸料架和卷材收料机。
在热处理完成后,调质支架上的板材将通过液压卸料架从调质支架上卸下,并由卷材收料机将板材收集起来。
卸料系统采用液压驱动,具有稳定的卸载效果和高效的工作效率。
五、控制系统:宽厚板材热处理调质生产线的控制系统主要由PLC控制器和人机界面组成。
PLC控制器负责控制整个生产线的运行,根据设定的参数控制各个部分的工作状态,如板材进料速度、加热温度、冷却风量等。
人机界面则提供对生产线的监控和操作,操作员可以通过触摸屏设定参数、监测生产状态和故障诊断。
宽厚板生产工艺

②常化炉: 常化炉主要对钢板进行常化处理,和少部分的回火处 理。常化处理能改善钢板内部质量,细化晶粒、均匀组 织,常作为调质或者回火前的预处理。回火处理主要消 除钢板内应力,降低钢板的脆性,提高钢板的韧性。常 化炉主要由上料辊道、辊底式常化炉、出料辊道三部分 组成。
入炉钢板温度:≤50℃;最高炉温:1000℃。 正火处理钢板温度:max.950℃; 回火处理钢板温度:max.730℃。 年处理量25万吨,其中正火钢板23万吨/年;高温回 火钢板2万吨/年。 辐射管加热、自身预热式烧嘴,脉冲控制 。
热矫直机 主体设备包括九辊矫直机,辅助装置包括、入口 推床、辊道。 最大开口度:200mm 最大矫直力:24000kN 矫直速度: 0 - 60/150 m/min
热分切剪: 最大通过厚度120mm,温度≥550℃时剪切钢板的 最大厚度为40mm,常温最大剪切厚度25mm。
最大剪切力:4500kN 长度:上1、2号冷床冷却钢板剪前最长740000mm,剪 后20000~420000mm;
一、粗轧 主体设备包括四辊可逆粗轧机和附着式的立辊, 辅助装置包括高压水除鳞箱、辊道、机架辊、推床等。
高压水除鳞
喷嘴压力:16~18 Mpa 系统压力: 20 Mpa 管数:上、下各2排 水量:约440 m3/h
带立辊轧机的四辊可逆式粗轧机: 立辊轧机: 型式:附着式,上传动 位置:四辊粗轧机入口,与四辊粗轧机中心距4100mm 轧辊规格:Φ900/825×400 mm 轧辊开口度:1300~3800 mm
一座VD炉,双处理工位,年处理能力100万吨
RH炉: RH功能: 1)脱碳 2)脱氢 3)脱氮 4)脱氧 5)去除钢水中夹杂。 设计参数:设计公称容量120吨 一座RH炉,单处理位,双待机位,设计年处理能力60 万吨。
安钢宽厚板工艺要求

安钢宽厚板工艺要求一、宽厚板生产工艺流程:炼钢区工艺路线:高炉铁水→转炉兑铁水(倒罐站)→铁水预处理→转炉炼钢→炉外精炼(LF、VD、RH)→连铸(模铸)→板坯。
轧钢区工艺路线:板坯加热→高压水除鳞→粗轧(带立辊)→精轧→ACC→热矫直→热分切→冷床冷却→A、B。
其中A(小于等于50mm厚)→上下表面检查(翻板)→切边→定尺、取样→标志→收集入半成品库→性能检验→探伤→入库;抛丸→热处理(正火、回火、淬火)→冷床冷却→表面检查(翻板)→定尺、取样→收集入半成品库→性能检验→探伤→入库。
B(大于50mm厚)→标志→火焰切边、取样→收集入半成品库→性能检验→探伤→入库。
抛丸→热处理(正火、回火、淬火)→冷床冷却→表面检查(翻板)→定尺、取样→收集入半成品库→性能检验→探伤→入库。
二、生产线工艺装备1、炼钢区:工艺装备:铁水预处理二座180吨转炉(带副枪系统)包括小方坯需要三座180t LF钢包炉一套180t VD真空脱气装置(或RH);一套180t RH装置一套直结晶器连续弯曲连续矫直弧形板坯连铸机一套直结晶器连续弯曲连续矫直弧形板方坯连铸机关键技术:转炉采用简单高效无污染的喷吹镁粒脱硫工艺(铁水脱硫)。
采用惰性气体搅拌熔池的顶底复吹工艺,加强熔池搅拌,抑制喷溅,缩短吹炼时间,提高金属收得率和氧气利用率,提高转炉脱磷效率。
采用两级自动化控制系统,实现炼钢过程的自动化控制。
采用副枪技术,提高冶炼终点目标命中率,缩短冶炼周期,提高转炉生产能力。
精炼双钢包车式的LF和双工位VD装置精炼形式双钢包车式的LF和双工位RH装置精炼形式先进的冶金模型(180t LF和VD设备工艺操作模型;合金加料最佳化模型;能量输入优化模型;炉渣模型;真空脱[C]脱[O]计算模型等)氩气自动连接连铸直弧型多点弯曲多点矫直型连铸软压下二冷采用气雾冷却在线调宽2、轧钢区:主要工艺装备:三座步进式加热炉四辊可逆式粗轧机(带立辊轧机)、精轧机各一架加速冷却ACC机组一台热矫直机三个冷床(两座42mX64m薄板,一座21mX30m厚板)在线超声波探伤装置双边剪两台(滚切式、圆盘剪)滚切式横剪三台自动标志机4台热处理线:抛丸机组无氧化辊底式常化炉无氧化辊底式淬火炉辊压式淬火机明火辊底式回火炉关键技术:轧制线全程采用二级自动控制轧制。
4300宽厚板车间工艺设计

学生毕业设计(论文)原创性声明本人以信誉声明:所呈交的毕业设计(论文)是在导师的指导下进行的设计(研究)工作及取得的成果,设计(论文)中引用他(她)人的文献、数据、图件、资料均已明确标注出,论文中的结论和结果为本人独立完成,不包含他人成果及为获得重庆科技学院或其它教育机构的学位或证书而使用其材料。
与我一同工作的同志对本设计(研究)所做的任何贡献均已在论文中作了明确的说明并表示了谢意。
毕业设计(论文)作者(签字):年月日摘要近年来,随着我国经济的快速发展,对宽厚板的需求量越来越大,并且对宽厚板的质量、强度、板形以及厚度的要求也越来越高。
这使得宽厚板行业迅猛发展,生产技术得以进一步成熟。
本设计主要介绍了宽厚板从原料到成品的整个生产过程,粗轧5个道次,精轧5个道次;粗轧采用三角形速度图,精轧采用梯形速度图,开轧温度1200℃,横轧开轧温度1150℃,精轧开轧温度1000℃,使产品的强韧性和力学性能有很大提高。
在基本的轧制工艺设计基础上,本设计重点描述了板形控制工艺在宽厚板生产中的应用。
本设计所采取的液压弯辊配合HCW轧机的板形控制技术,明显改善了宽厚板产品的浪形、瓢曲、侧弯等板形问题,使得产品的组织更加均匀,晶粒更加细化,从而获得了良好的力学性能和工艺性能。
并且液压弯辊技术和工作辊横移式HCW轧机技术较容易在现有传统四辊轧机上改造,具有很强的适用性。
关键词:宽厚板车间工艺板形控制液压弯辊 HCW轧机ABSTRACTIn recent years, along with the rapid economic development of our country, heavy plate to the growing demand, and to the quality of the heavy plate, strength and plate shape and thickness of the demand is higher and higher. This situation make heavy plate industry rapid development, production technology be further mature.This design is mainly introduced the heavy plate from raw materials to finished products of the whole production process. In this design, rough rolling 5 passes and finish rolling 5 passes, rough rolling with the triangle velocity diagram and finish rolling with trapezoid, initial rolling temperature is 1200℃,cross rolling initial rolling temperature is 1150,finish rolling initial rolling temperature is 1000,which makes the product of strong toughness and mechanical performance has improved a lot. In the basic rolling technology based on design, the design mainly describe the shape control technology in the heavy plate of the application of the production. The design of the hydraulic bending roll system with HCW mill of the shape control technology, can significantly improve the thick plate waves of product form, gourd ladle song and lateral bending plate shape etc, make the product structure is more uniform and more refined grains, and obtain a good mechanical properties and process performance. And hydraulic technology and work roll bending roll lateral movement type HCW mill technology are more prone to the existing traditional four roll rolling mill in transformation, and has a strong suitability.Keywords: Heavy Plate; Workshop Process; Shape Control; hydraulic bending roll; HCW rolling mill目录摘要 (I)ABSTRACT........................................................... I I 目录.............................................................. I II 1绪论.. (1)1.1 国外研究现状分析 (1)1.1.1 工艺方面 (2)1.1.2 设备方面 (2)1.2 我国中厚板产品生产现状 (4)1.3 本课题的目的意义 (5)1.4 本课题的主要内容 (6)2产品方案 (7)2.1 产品大纲 (7)2.2 金属平衡表 (9)2.3 典型产品 (9)2.4 生产方案 (9)3 工艺流程 (11)3.1 原料准备 (11)3.1.1 原料加热 (12)3.1.2 高压水除鳞 (12)3.2 轧制 (12)3.2.1 粗轧 (12)3.2.2 精轧 (12)3.3 冷却 (13)3.3.1 轧制过程中的轧件冷却 (13)3.3.2 轧后钢板的加速冷却 (13)3.3.3 成品钢板的冷却 (13)3.4 矫直、剪切和表面处理 (13)3.4.1 矫直 (13)3.4.2 剪切 (13)3.4.3 表面清理 (14)3.5 热处理 (14)3.6 表面标识 (14)4 主辅设备选型 (15)4.1 主要设备选型 (15)4.1.1 粗轧机 (16)4.1.2 立辊轧机 (16)4.1.3 精轧机 (16)4.2 辅助设备选型 (16)4.2.1 加热炉 (16)4.2.2 高压水除鳞系统 (17)4.2.3 轧后加速冷却系统(ACC) (17)4.2.4 热矫直机 (18)4.2.5 冷床 (18)4.2.6 剪切机构 (18)5 典型产品工艺设计 (19)5.1 典型产品原料尺寸及成品尺寸 (19)5.2 轧制道次确定及压下量分配 (19)5.3 轧制各工艺参数的计算 (20)5.3.1 轧制速度制度的确定 (20)5.3.2 轧制延续时间的确定 (20)5.3.3 轧制温度的确定 (21)5.3.4 计算各道次轧制压力 (22)5.3.5 计算传动力矩 (25)5.4 工艺参数校核 (28)5.4.1 电机负荷校核 (28)5.4.2 轧辊强度校核 (29)6 板形控制 (31)6.1 板形的概念 (31)6.2 常见板形缺陷及其原因 (31)6.3 板形控制基本原理 (32)6.4 本设计板形控制方法 (32)6.4.1 HCW轧机分析 (33)6.4.2 液压弯辊技术分析 (33)6.5板形控制效果 (34)6.5.1直观效果 (34)6.5.2显微组织效果 (34)6.5.3力学性能效果 (35)7 年产量计算 (36)7.1 轧制图表 (36)7.2 年产量计算 (36)7.2.1 典型产品实际小时产量 (36)7.2.2 轧机平均小时产量 (36)7.2.3 车间年产量 (37)8 车间平面布置与立面尺寸 (38)8.1 车间平面布置的原则 (38)8.2 金属流程线的确定 (38)8.3 主要设备间距的确定 (38)8.3.1 加热炉及其前后设备间距 (39)8.3.2 轧机及其前后设备间距 (39)总结 (40)参考文献 (41)致谢 (42)1绪论中厚钢板大约有200年的生产历史,它是国家现代化不可或缺的一项钢材品种,被广泛应用于大直径输送管、压力容器、桥梁、锅炉、海洋平台、坦克装甲、各类战舰、车辆、机器结构、建筑构件等领域。
宽厚板生产工艺流程

宽厚板生产工艺流程朋友!今天来跟您唠唠宽厚板生产这档子事儿。
您知道不,我在这行都混了 20 多年啦!咱先说说这原料准备吧,那可真是个基础活儿。
得把那些矿石啥的弄来,挑挑拣拣,可不能有啥杂质混进去。
这就好比做饭,食材不好,做出来的能好吃吗?说到加热这步,哇塞,那温度高得吓人!我记得有一回,我不小心靠太近了,差点没给我烤焦喽!加热得均匀,不然这板子就废啦。
然后就是轧制,这可是个技术活。
就像揉面团,得把它揉得恰到好处,薄厚均匀。
我刚开始学的时候,老是掌握不好力度,唉,被师傅骂了不知道多少回。
不过后来呀,我慢慢就上手了,嘿嘿。
还有啊,这冷却也有讲究。
太快太慢都不行,我记得好像有一次,冷却速度没控制好,那板子的质量就不咋地,被领导狠狠批了一顿,当时那个惨哟!哦,对了!这中间的检测环节可不能少。
得像给病人做体检似的,一点小毛病都不能放过。
咱再回过头来说说加热,这里面的学问可大着呢。
温度、时间,都得拿捏得死死的。
我跟您说,这要是弄错了,那可就全完啦!嗯……还有啥来着?哦,对!这最后的精整,那得细致入微,就跟给新娘子化妆一样,得漂漂亮亮的才能出厂。
我这说得有点乱,您可别嫌弃哈。
我这脑子有时候就爱犯糊涂。
您说要是突然停电了可咋办?这可真是个让人头疼的假设情况。
我刚开始干这行的时候,觉得这工艺可难了,差点就打退堂鼓。
不过后来坚持下来,发现也没那么可怕,就是得多琢磨多练习。
您要是有啥不懂的,随时问我,咱一起探讨探讨。
这行啊,变化也挺快的,新的技术不断出来,我这老家伙有时候都跟不上喽!就先说这么多吧,剩下的您自个儿琢磨琢磨,说不定能有新发现呢!。
宽厚板生产线工艺流程

02
原料准备与处理
原料选择与验收
总结词:确保质量
详细描述:根据生产需求和规格,选择合适质量和规格的原料,并进行严格的验 收,确保原料的质量符合生产标准。
原料的储存与运
宽厚板生产工艺的发展历程
传统工艺阶段
传统的宽厚板生产工艺主要采用氧气顶吹转炉、平炉和连 续浇铸技术,该阶段的生产技术相对落后,产品质量和品 种有限。
优化升级阶段
随着科技的进步和市场需求的变化,宽厚板生产工艺不断 优化升级,出现了连铸连轧、炉卷轧机等先进技术,提高 了生产效率和产品质量。
绿色环保阶段
涂装
在表面涂装防腐、防锈涂料,以提高宽厚板的耐腐蚀性能和外观 质量。
表面质量检测
通过专业设备对表面进行质量检测,确保表面质量符合要求。
热处理
1 2
加热
将宽厚板加热至所需的温度,以实现材料的相变 和硬化。
保温
保持一定时间,使材料充分吸收热量并完成相变。
3
冷却
将材料快速冷却,以获得所需的机械性能和显微 组织。
精整与切割
矫直
通过矫直机对宽厚板进行矫直,消除内应力,提高平整度。
切割
根据需求对宽厚板进行切割,以获得不同规格和形状的产品。
修磨
对边缘进行修磨,使其平滑并去除毛刺,提高安全性和美观度。
06
宽厚板的质量检测与控制
外观检测
总结词
通过目视或机器视觉系统对外观进行检测,确保表面无缺陷 、颜色一致。
详细描述
总结词
保持原料品质
详细描述
合理规划原料的储存和运输,确保原料在储存和运输过程中不受损坏,保持其 品质和性能。
3800mm宽厚板轧机生产线 技 术 规 格 书
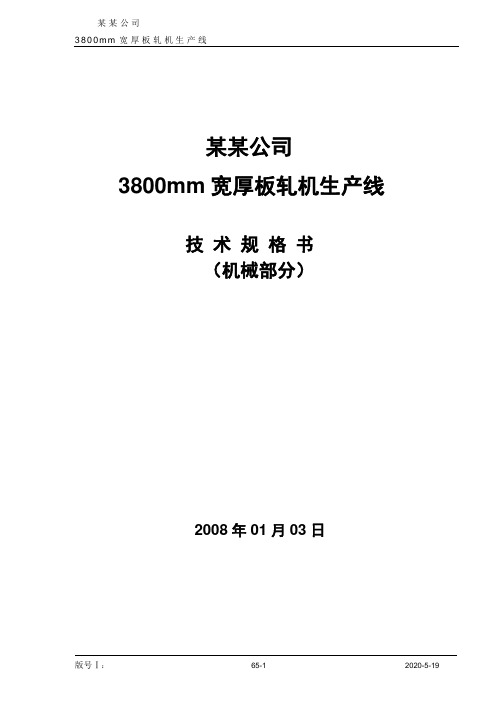
某某公司3800m m宽厚板轧机生产线某某公司3800mm宽厚板轧机生产线技术规格书(机械部分)2008年01月03日目录一、原料与产品二、工艺流程简图三、装机水平四、设备及技术参数一、原料与产品1、坯料规格:(100%连铸坯)坯料厚度:170mm 200mm 230mm坯料宽度:1450~2300 mm坯料长度:2500~3600 mm坯料重量(max):15 t2、钢种:碳素结构钢、优质碳素结构钢、低合金高强度结构钢、造船板、管线钢、工程机械用钢板、建筑结构用钢、桥梁板、压力容器板、锅炉板等。
3、轧制板规格:轧制板厚度:6~100 mm轧制板宽度(max):1500~3650 mm(不切边)轧制板长度(max):~50000 mm4、产品规格:钢板厚度:6~100 mm钢板宽度:1450~3600mm钢板长度:6000~24000 mm钢板重量(max):~14.8 t5、生产规模:年生产各种规格钢板::140万吨轧机作业时间:7400小时/年二、装机水平1、采用三点高压水除鳞以提高板材表面质量2、R四辊轧机采用电动APC+液压AGC,F四辊轧机采用电动APC+液压AGC。
压下系统中装测压仪、位移传感器用以进行压力、位置信号反馈、F四辊轧机后设测厚仪,配合液压AGC实现板厚控制。
R、F轧机带有工作辊弯辊。
3、R、F工作辊轴承采用四列短圆柱滚子轴承,R/F轧机支承辊轴承采用动压油膜轴承。
工作辊采用高铬铸钢轧辊(球墨铸铁轧辊、半钢轧辊),支承辊采用整体合金锻钢轧辊。
轧机前后上部设除尘罩。
4、F轧机后设控冷装置,实现控轧、控冷(TMCP)。
5、采用十一辊厚板热矫直机。
6、采用滚盘式冷床。
7、剪切线采用激光划线、磁力对中、液压分体夹送辊、滚切式双边剪切机组。
采用液压分体夹送辊、自动测长滚切式横切剪机组。
三.设备及技术参数1 炉区设备(略)2. R粗轧区设备2.1高压水除鳞机用途:除去板坯表面加热过程中产生的一次氧化铁皮。
宽厚板轧制规程设计

宽厚板轧制规程设计本规程旨在规定宽厚板轧制过程中的生产流程、工艺参数、设备使用及技术要求等方面的规定,以确保生产质量和安全生产。
一、生产流程1.投料:按照工艺要求将原材料运输至生产现场并投入料斗中。
2.预热:将原材料加热至合适的温度,以便后续加工。
3.轧制:将预热后的原材料通过轧机进行轧制,并根据要求进行多次轧制,直至达到所需厚度和规格。
4.切割:将轧制完成的板材进行切割,使其符合用户要求的尺寸和形状。
5.质检:对切割完成的板材进行严格的质量检测,确保其符合相关标准和用户要求。
6.包装:将质检合格的板材进行包装,并标注相关信息。
7.出库:将包装好的板材运输至仓库,并进行入库管理。
二、工艺参数1.预热温度:根据原材料种类和要求确定预热温度,确保其能够满足轧制要求。
2.轧制厚度:根据用户要求和标准规定确定轧制厚度,确保生产出的板材符合相关标准和用户要求。
3.轧制速度:根据轧制要求和轧机性能确定轧制速度,确保生产效率和生产质量。
4.切割长度:根据用户要求和标准规定确定切割长度,确保生产出的板材符合相关标准和用户要求。
三、设备使用1.轧机:选用性能稳定、操作简单的轧机设备,并进行定期维护和保养,确保其正常运转和生产质量。
2.切割机:选用性能稳定、切割精度高的切割机设备,并进行定期维护和保养,确保其正常运转和生产质量。
3.质检设备:选用符合标准要求的质检设备,并进行定期校准和维护,确保其准确性和可靠性。
四、技术要求1.严格执行生产流程和工艺参数,确保生产质量和安全生产。
2.人员必须按照操作规程进行作业,并进行必要的安全防护措施,确保人身安全和生产设备的正常运转。
3.定期进行设备维护和保养,确保设备的正常运转和生产质量。
4.对生产过程中发现的问题及时处理和纠正,确保生产质量和生产效率。
- 1、下载文档前请自行甄别文档内容的完整性,平台不提供额外的编辑、内容补充、找答案等附加服务。
- 2、"仅部分预览"的文档,不可在线预览部分如存在完整性等问题,可反馈申请退款(可完整预览的文档不适用该条件!)。
- 3、如文档侵犯您的权益,请联系客服反馈,我们会尽快为您处理(人工客服工作时间:9:00-18:30)。
轧钢车间职工培训
1 2020/7/30
主要培训内容 一 介绍生产线工艺流程 二 轧钢车间工作范围 三 车间各工种职责介绍
2 2020/7/30
工艺流程介绍
工艺流程 车间布置图() 产品介绍
3 2020/7/30
关键特点: • 高效的板坯除鳞设备,可根据板坯厚度不同进行调整 • 粗轧机进出口侧的旋转辊道将用于产品宽度的展宽。 • 采用控制轧制和热机轧制工艺生产高性能的钢板(如管线钢板、高强度船板和 优质结构钢板)。 • 液压自动厚度控制 (AGC) 缸具有高精度和快速动态响应特性,该缸的特性能 够进行平面形状轧制。。 • VAI 平面形状轧制和AGC 系统,与VAI 的2 级模型相结合能保证成材率和钢 板的矩形化最优。 • VAI 的2 级模型通过保证精确预报宽展和实现正确宽度的轧边道次计算来使成 材率最优。2 级模型也能计算头尾需要的短行程和需要的钢板板体的修正。 • 实现绝对辊缝控制、头尾短行程控制和板身修正控制的VAI 技术控制系统 (TCS)。 • 提高凸度和平直度控制、提高产量和轧宽轧薄能力的VAI SmartCrown 系 统。 • 钢板平直度控制的工作辊弯辊系统 (WRB)。 • 使用电动机械宽度调整和短行程液压缸进行立辊辊缝调整的轧边机,轧边机附 着在粗轧机机座上,具有保证钢板头尾宽度最优的高速短行程能力。VAI 有很 多液压轧边机的参考。 • 绝对的立辊辊缝测量, VAI自动化技术不需要轧边机的测压元件并且使宽度公 差更好。
在1#剪切线,一台机械滚切式双切边剪达到切边最小化、切边 质量和成品宽度精确、剪切厚度最大到50mm的水平。
将来建造第二条剪切线后,生产能力达到180万吨。
机械定尺剪具有为精确定尺的和保证整条剪切线高产能的剪切 速度而采用的较高剪切力设计。
钢板的标志和打印通过高性能设备的联合操作进行。
钢板堆垛装置去进行成品钢板的预堆垛,以便转移到成品发货 区。
10 2020/7/30
11 2020/7/30
总结
回顾所学的内容 指出应用所学内容的方法 要求得到培训反馈信息
12 202ቤተ መጻሕፍቲ ባይዱ/7/30
其他信息
其他培训活动 列出相关的书籍、文章及电子文档 顾问服务及其他资源
13 2020/7/30
5 2020/7/30
MULPIC 加速钢板冷却系统提供了高可控性的、精确的加速冷 却能力。这个系统的特点是具有非常高的流量调节比,允许广 泛厚度范围的钢板的控制冷却和工艺需要。这个系统也设计了 直接淬火(DQ)功能。
热矫直机具有覆盖很大厚度和宽度范围的矫直能力的技术水平。
2个主冷床和第三个厚板冷床允许全部范围的钢板进行有效冷却, 同时为下游工序提供了缓冲能力。
冷矫直机能够为有特殊的高精度要求的最终用户提高钢板的平 直度。
整条生产线的工艺仪表和仪器为VAI的自动化系统提供需要的 数据,以控制和优化完善钢板的生产。
6 2020/7/30
连铸坯规格
7 2020/7/30
产品尺寸
8 2020/7/30
9 2020/7/30
二 轧钢车间工作范围
三个区域-轧钢,精整,生产准备 各区域具体分工,职工职责 各区域间的衔接联系