汽车曲轴的软氮化技术
生产四种曲轴强化工艺的介绍
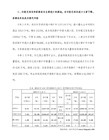
表面滚压强化是一种无屑光整加工方法。它是在常温状态下,利用高硬度材料(如淬火钢、硬质合金以及红宝石等)制成的工具对被加工零件表面施加一定的压力,使表面层金属产生塑性变形,产生表层残余压应力的一种强化方法。
圆角滚压强化是一种特殊的表面滚压强化。它是在曲轴的轴颈与主轴颈、曲柄与连杆之间的圆角上应力状态,使之形成合理分布的压应力状态的一种特殊的表面强化方法。
气体软氯化后的氮化层具有残余应力,且氮原子的渗入阻碍了位错运动,防止了疲劳裂纹的产生和扩散,使疲劳强度得以提高。
气体软氮化后的曲轴表层的白亮层化学性能极为稳定,使曲轴具有良好的耐腐蚀性能。
曲轴氮化与其他热处理工艺相比,具有投资小、劳动强度低、质量可靠稳定、抗疲劳强度较高等特点,氮化能提高曲轴疲劳强度的20%—60%。
复合强化
复合强化就是应用多种强化工艺对曲轴进行强化处理,例如曲轴圆角滚压加轴颈淬火等。据国外资料介绍,球墨铸铁曲轴采用圆角滚压工艺与离子氮化结合使用进行复合强化,可使整条曲轴的抗疲劳强度提高130%以上。可见曲轴进行滚压强化是提高曲轴疲劳强度的主要途径,使之广泛地运用于曲轴加工是必然的趋势。但在国内,仅仅有少数厂家进行这方面的实践。不过,也有一些厂家在这方面的研究有了一定的成果,如东风汽车集团公司工艺研究所的“曲轴圆角滚压强化与滚压校直技术研究开发及应用”解决了国内企业花巨资引进国外技术的问题。东风汽车公司工艺研究所冯美斌、李满良等人在滚压强化和复合强化方面申请了两项国家专利,一项是2002年申请的“一种发动机球铁曲轴的强化工艺”,该工艺采用氮化后进行圆角滚压的复合强化工艺,经这种复合强化工艺处理的球铁曲轴,其弯曲疲劳极限已接近圆角感应淬火的锻钢曲轴的水平,解决了单纯采用氮化或圆角滚压工艺已难以满足发动机对曲轴的可靠性要求的问题;另一项是2003年申请的“一种曲轴滚压强化工艺”,克服了曲轴半精磨后滚压再进行精磨,会将滚压强化层磨去、会显着降低疲劳强度的传统观念。
曲轴氮化变形的分析
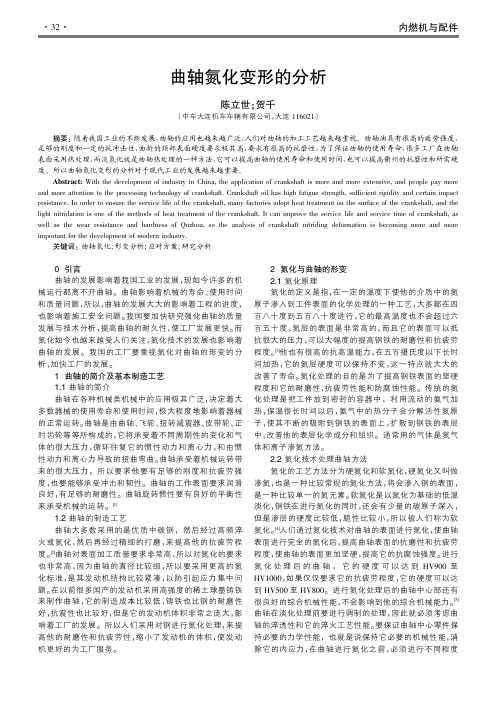
0引言曲轴的发展影响着我国工业的发展,现如今许多的机械运行都离不开曲轴。
曲轴影响着机械的寿命、使用时间和质量问题,所以,曲轴的发展大大的影响着工程的进度,也影响着施工安全问题。
我国要加快研究强化曲轴的质量发展与技术分析,提高曲轴的耐久性,使工厂发展更快。
而氮化如今也越来越受人们关注,氮化技术的发展也影响着曲轴的发展。
我国的工厂要重视氮化对曲轴的形变的分析,加快工厂的发展。
1曲轴的简介及基本制造工艺1.1曲轴的简介曲轴在各种机械类机械中的应用极其广泛,决定着大多数器械的使用寿命和使用时间,极大程度地影响着器械的正常运转。
曲轴是由曲轴、飞轮、扭转减震器、皮带轮、正时齿轮等等所构成的,它将承受着不同周期性的变化和气体的很大压力,循环往复它的惯性动力和离心力,和由惯性动力和离心力导致的扭曲弯曲。
曲轴承受着机械运转带来的很大压力,所以要求他要有足够的刚度和抗疲劳强度,也要能够承受冲击和韧性。
曲轴的工作表面要求润滑良好,有足够的耐磨性。
曲轴旋转惯性要有良好的平衡性来承受机械的运转。
[1]1.2曲轴的制造工艺曲轴大多数采用的是优质中碳钢,然后经过高频淬火或氮化,然后再经过精细的打磨,来提高他的抗疲劳程度。
[2]曲轴对表面加工质量要求非常高,所以对氮化的要求也非常高,因为曲轴的直径比较细,所以要采用更高的氮化标准,是其发动机结构比较紧凑,以防引起应力集中问题。
在以前很多国产的发动机采用高强度的稀土球墨铸铁来制作曲轴,它的制造成本比较低,铸铁也比钢的耐磨性好,抗震性也比较好,但是它的发动机体积非常之庞大,影响着工厂的发展。
所以人们采用对钢进行氮化处理,来提高他的耐磨性和抗疲劳性,缩小了发动机的体积,使发动机更好的为工厂服务。
2氮化与曲轴的形变2.1氮化原理氮化的定义是指,在一定的温度下使他的介质中的氮原子渗入到工件表面的化学处理的一种工艺,大多都在四百八十度到五百八十度进行,它的最高温度也不会超过六百五十度,氮层的表面是非常高的,而且它的表面可以抵抗很大的压力,可以大幅度的提高钢铁的耐磨性和抗疲劳程度。
曲轴的氮化强化处理方式
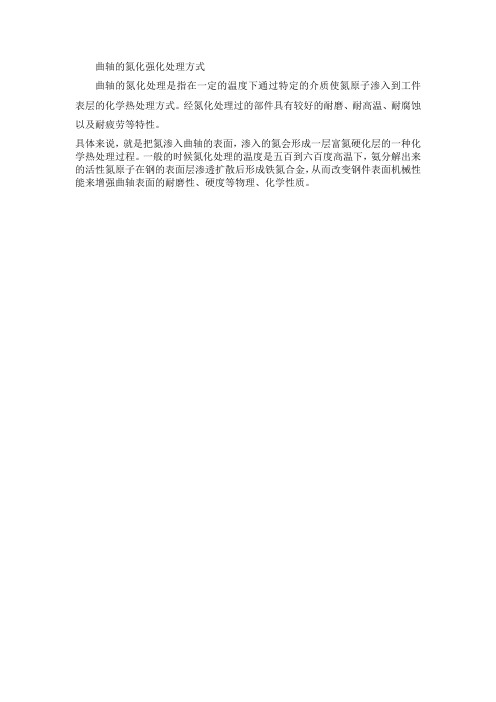
曲轴的氮化强化处理方式
曲轴的氮化处理是指在一定的温度下通过特定的介质使氮原子渗入到工件表层的化学热处理方式。
经氮化处理过的部件具有较好的耐磨、耐高温、耐腐蚀以及耐疲劳等特性。
具体来说,就是把氮渗入曲轴的表面,渗入的氮会形成一层富氮硬化层的一种化学热处理过程。
一般的时候氮化处理的温度是五百到六百度高温下,氨分解出来的活性氮原子在钢的表面层渗透扩散后形成铁氮合金,从而改变钢件表面机械性能来增强曲轴表面的耐磨性、硬度等物理、化学性质。
球墨铸铁曲轴的气体软氮化

作者: 方涛平;方彩娟;孙建章
作者机构: 长沙水电师院;济南职业大学;济南职业大学
出版物刊名: 长沙理工大学学报:社会科学版
页码: 77-83页
主题词: 气体软氮化;催渗;软氮化层
摘要:柴油机的珠墨铸铁曲轴系重要零件,气体软氮化应用到球墨铸铁领域还是一种新工艺,而且比中频淬火效果好,提高了曲轴的抗疲劳和抗磨损的能力。
本文对气体软氮化的基本原理、设备、工艺参数的选择和催渗方法进行了探讨,对软氮化后曲轴的尺寸形状误差、光洁度和机械性能的提高等进行了较详细的试验、分析和比较,结果,经气体软氮化后的曲轴不但尺寸形站误差符合图纸要求外,而且抛去轻微氧化层后光洁度还略有提高,曲轴安全系数由1.3~1.6提高到1.70~1.77,并且一般不再发生疲劳断(?),使用寿命比原来寿命增加3.32倍以上。
热处理和表面强化处理技术

4、热处理和表面强化处理技术曲轴的热处理关键技术是表面强化处理。
球墨铸铁曲轴一般均采用正火处理,为表面处理做好组织准备,表面强化处理一般采用感应淬火或氮化工艺。
锻钢曲轴则采用轴颈与圆角淬火工艺。
引进的设备有AEG全自动曲轴淬火机床、EMA淬火机床等。
据国外资料介绍,球墨铸铁曲轴采用圆角滚压工艺与离子氮化结合使用进行复合强化,可使整条曲轴的抗疲劳强度提高130%以上。
国内部分厂家近几年也进行了这方面的实践,取得了良好的效果。
曲轴圆角滚压加工方面,德国赫根塞特(HEGENSCHEIDT-MFD AUTOMATIC)生产的机床应用了变压力滚压和矫正专利技术,是比较好的圆角滚压设备,但价格昂贵。
目前国内在这方面的研究也有了一定的成果,东风汽车有限公司工艺研究所的“曲轴圆角滚压强化与滚压校直技术研究开发及应用”解决了国内企业化巨资引进国外技术的问题,该课题获得了原国家机械工业局科技进步二等奖。
曲轴制造技术的发展趋势1、铸造技术(1)熔炼对于高牌号铸铁的熔化,将采用大容量中频炉进行熔炼或变频中频炉熔炼,并采用直读光谱仪检测铁水成分。
球墨铸铁处理采用转包,研制新品种球化剂,采用随流孕育、型内孕育及复合孕育等先进孕育方法。
熔化过程的各参数实现微机控制和屏幕显示。
(2)造型消失模铸造将得到发展和推广。
在砂型铸造中,无箱射压造型和挤压造型将受到重视并继续在新建厂或改建厂中推广应用。
原有的高压造型线将继续使用,其中部分关键元件将得到改进,实现自动组芯和下芯。
2、锻造技术以热模锻压力机、电液锤为主机的自动线是锻造曲轴生产的发展方向,这些生产线将普遍采用精密剪切下料、辊锻(楔横轧)制坯、中频感应加热、精整液压机精压等先进工艺,同时配有机械手、输送带、带回转台的换模装置等辅机,形成柔性制造系统(FMS)。
通过FMS可自动更换工件和模具以及自动进行参数调节,在工作过程中不断测量。
显示和记录锻件厚度和最大压力等数据并与定值比较,选择最佳变形量以获得优质产品。
球墨铸铁曲轴的离子氮化工艺

组织游离的 铁素体不大于5 %,以便控制变形量 在要求的范围内。 氮化 设备采用P Ⅱ脉 冲电源等离子体 氮化 N 炉 ,无需对芯孔 、配重孔 、斜油孔等 进行堵 塞防
护 ,但氮 化 前状 态 很 重要 ,要 求其 洁 净 、 干燥 ,无
锈 ,无残 留 铁 屑 。
4 0 型 曲轴 放 外 固 。 因 起 辉 面 积 大 ,相 对 温 度 l5 高 ,靠 近 炉壁 ,散 热快 ;无 内孔 四缸 曲轴 ( 朝柴 如
电 气柜 控 制 两 台设 备 ,当一 台设 备 保温 结 束 ,立 刻
启动另一台设备 ,既节省了空 间,也提高 了效率 。 设备价格低廉 。 ( )离子氮化工件表面 质量好 ,易抛光 ,产 6
能 高 ,温 度 低 ,变形 量 比 气 体氮 化 小 ,工 艺过 程 易
球墨铸铁曲轴的离子氮化工艺
滨 州海得 曲轴有 限责任公 司 ( 山东 2 6 0 ) 李 永真 5 6 0 滨州 职业学 院 ( 山东 2 6 2 ) 郭婷婷 5 6 4 赵 向方
曲轴是 内燃 机 中最重要 的零 件之 一 ,它与 气 缸 、活塞、连杆等组成发动机的动力源装置 ,并 由 曲轴向外输 出功率。曲轴工作时承受反复 弯曲和扭
2 3 区/ 9 0 、 、4 ℃ 3
硬度H RC
3 4 ~ 3 4 ~ 3 5 ~ 3 6 ~ 3 6 ~ 3 6 ~
火 脆性 ,因此 在 高温 回火 时 常采 用 快 速风 冷 的 方式
3 6
3 6
3 7
3 8
3 8
3 9
进行冷却。回火工艺为 :50 8  ̄ 7 ~50C保温9 mi , 0 n 回火硬度3 ~3 H C,回火组织是保 留马 氏体位向 3 9R
氮化处理优化技术在机械零部件制造中的应用分析
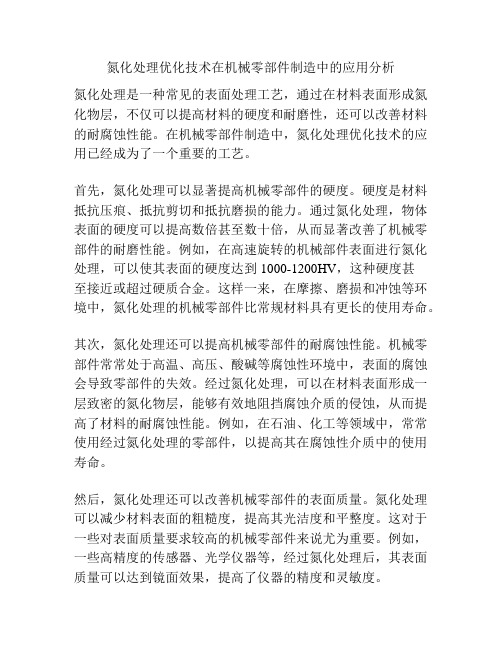
氮化处理优化技术在机械零部件制造中的应用分析氮化处理是一种常见的表面处理工艺,通过在材料表面形成氮化物层,不仅可以提高材料的硬度和耐磨性,还可以改善材料的耐腐蚀性能。
在机械零部件制造中,氮化处理优化技术的应用已经成为了一个重要的工艺。
首先,氮化处理可以显著提高机械零部件的硬度。
硬度是材料抵抗压痕、抵抗剪切和抵抗磨损的能力。
通过氮化处理,物体表面的硬度可以提高数倍甚至数十倍,从而显著改善了机械零部件的耐磨性能。
例如,在高速旋转的机械部件表面进行氮化处理,可以使其表面的硬度达到1000-1200HV,这种硬度甚至接近或超过硬质合金。
这样一来,在摩擦、磨损和冲蚀等环境中,氮化处理的机械零部件比常规材料具有更长的使用寿命。
其次,氮化处理还可以提高机械零部件的耐腐蚀性能。
机械零部件常常处于高温、高压、酸碱等腐蚀性环境中,表面的腐蚀会导致零部件的失效。
经过氮化处理,可以在材料表面形成一层致密的氮化物层,能够有效地阻挡腐蚀介质的侵蚀,从而提高了材料的耐腐蚀性能。
例如,在石油、化工等领域中,常常使用经过氮化处理的零部件,以提高其在腐蚀性介质中的使用寿命。
然后,氮化处理还可以改善机械零部件的表面质量。
氮化处理可以减少材料表面的粗糙度,提高其光洁度和平整度。
这对于一些对表面质量要求较高的机械零部件来说尤为重要。
例如,一些高精度的传感器、光学仪器等,经过氮化处理后,其表面质量可以达到镜面效果,提高了仪器的精度和灵敏度。
最后,氮化处理优化技术还可以改善机械零部件的工作性能。
氮化处理可以在材料表面形成氮化物层,这种层具有较高的化学稳定性和热稳定性,可以提高零部件在高温、高压、高速等工作条件下的稳定性和可靠性。
例如,在汽车发动机中,使用经过氮化处理的曲轴、凸轮轴等重要零部件,可以提高其在高温高压环境下的工作性能,降低零部件失效和损坏的风险。
综上所述,氮化处理优化技术在机械零部件制造中的应用是非常广泛的,可以提高零部件的硬度和耐磨性,改善耐腐蚀性能,优化表面质量,提升工作性能,从而提高机械零部件的使用寿命和可靠性。
关于曲轴氮化规定
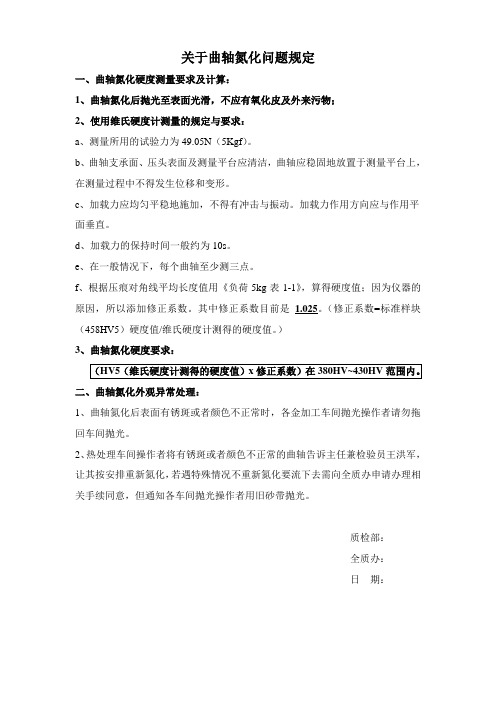
关于曲轴氮化问题规定
一、曲轴氮化硬度测量要求及计算:
1、曲轴氮化后抛光至表面光滑,不应有氧化皮及外来污物;
2、使用维氏硬度计测量的规定与要求:
a、测量所用的试验力为49.05N(5Kgf)。
b、曲轴支承面、压头表面及测量平台应清洁,曲轴应稳固地放置于测量平台上,在测量过程中不得发生位移和变形。
c、加载力应均匀平稳地施加,不得有冲击与振动。
加载力作用方向应与作用平面垂直。
d、加载力的保持时间一般约为10s。
e、在一般情况下,每个曲轴至少测三点。
f、根据压痕对角线平均长度值用《负荷5kg表1-1》,算得硬度值;因为仪器的原因,所以添加修正系数。
其中修正系数目前是 1.025。
(修正系数=标准样块(458HV5)硬度值/维氏硬度计测得的硬度值。
)
3、曲轴氮化硬度要求:
二、曲轴氮化外观异常处理:
1、曲轴氮化后表面有锈斑或者颜色不正常时,各金加工车间抛光操作者请勿拖回车间抛光。
2、热处理车间操作者将有锈斑或者颜色不正常的曲轴告诉主任兼检验员王洪军,让其按安排重新氮化,若遇特殊情况不重新氮化要流下去需向全质办申请办理相关手续同意,但通知各车间抛光操作者用旧砂带抛光。
质检部:
全质办:
日期:。
汽车发动机钢曲轴气氮化试验
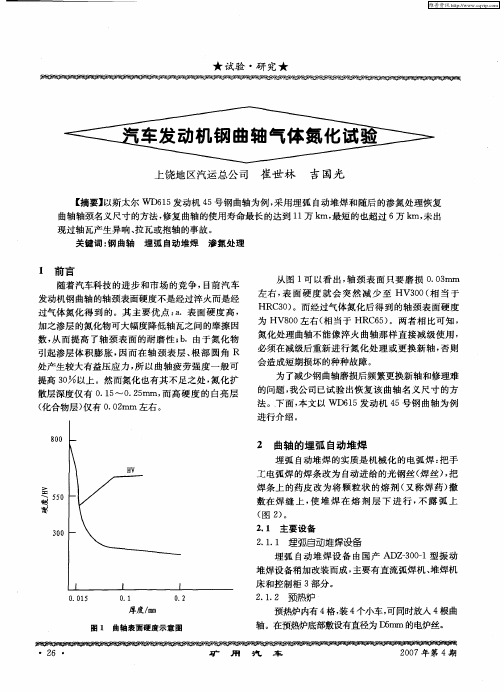
过气体氮化得 到的。其主要优点 ..表面硬度高 , a
加之 渗层 的氮化 物可 大 幅度降 低轴 瓦之 间的摩擦 因 数 , 而 提 高 了轴 颈表 面 的耐 磨性 ;.由于氮 化 物 从 b 引起 渗层体 积 膨 胀 , 而 在 轴 颈 表 层 、 部 圆角 R 因 根 处 产生较 大 有益压 应 力 , 以 曲轴疲 劳强 度 一 般 可 所 提 高 3 以上 。然 而氮化 也有 其 不 足之 处 , 化 扩 0 氮 散 层深度 仅 有 0 1 ~ 02 mm, 高硬 度 的 白亮 层 。5 。 5 而 ( 化合 物层 ) 仅有 00mm 左右 。 .2
2 2 4 3 钻 通油 孔 。 . ..
2 2 埋 弧 自动堆 焊工 艺 .
2 2 4 4 车 削 和磨削 曲轴 轴颈 。先 车削 主轴 颈 , . .. 然
2 2 1 堆焊 前准备 ..
后车 削连 杆 轴 颈 ( 颈 堆 焊 后 的加 工 余 量 为 2 5 轴 .~ 3 mm, 削 时要 注 意 留 出 0 6 .rm 的磨 削量 ) 车 . ~0 8 a , 在车 削结 束后 再磨 削 曲轴轴 颈 。
大 时偏 置量 应大 ) 。 2 2 3 埋 弧自动 堆 焊工艺 .. 2 2 3 1 当轴 颈 中部 向两边 圆角 堆焊 , 圆角堆 焊 . . . 在 结束 后 将 电弧拉 离 圆 角 , 起 焊 和停 焊 均 处 在轴 颈 使 应力 较 小 的部位 。 2 23 2 一 次 堆 焊 层 厚 度 为 3 5 ... ~ mm。当轴 颈 需 要 堆焊 2 ~3次 时 , 以连续 堆 焊 , 每次 堆焊 后 , 可 但 均 应使 堆 焊层表 面平整 。
预 热炉 内有 4 , 4 格 装 个小车 , 同时放人 4 曲 可 根
曲轴的离子氮化工艺现状
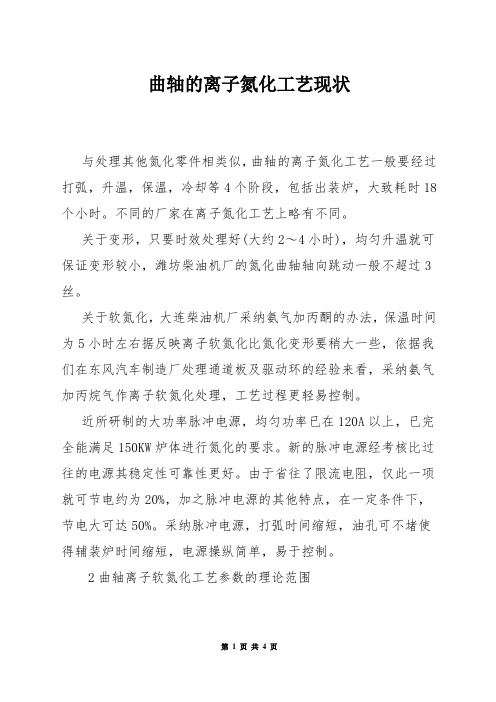
曲轴的离子氮化工艺现状与处理其他氮化零件相类似,曲轴的离子氮化工艺一般要经过打弧,升温,保温,冷却等4个阶段,包括出装炉,大致耗时18个小时。
不同的厂家在离子氮化工艺上略有不同。
关于变形,只要时效处理好(大约2~4小时),均匀升温就可保证变形较小,潍坊柴油机厂的氮化曲轴轴向跳动一般不超过3丝。
关于软氮化,大连柴油机厂采纳氨气加丙酮的办法,保温时间为5小时左右据反映离子软氮化比氮化变形要稍大一些,依据我们在东风汽车制造厂处理通道板及驱动环的经验来看,采纳氨气加丙烷气作离子软氮化处理,工艺过程更轻易控制。
近所研制的大功率脉冲电源,均匀功率已在120A以上,已完全能满足150KW炉体进行氮化的要求。
新的脉冲电源经考核比过往的电源其稳定性可靠性更好。
由于省往了限流电阻,仅此一项就可节电约为20%,加之脉冲电源的其他特点,在一定条件下,节电大可达50%。
采纳脉冲电源,打弧时间缩短,油孔可不堵使得辅装炉时间缩短,电源操纵简单,易于控制。
2曲轴离子软氮化工艺参数的理论范围就曲轴等离子体氮化技术而言,大多数厂家采纳了离子软氮化技术,其工艺参数的制定一般应遵循以下几项原则:1. 氮化温度的选择范围等离子体氮化就是利用真空辉光放电的方法把氮渗透金属表面形成FeN 的一种化学热处理方法。
在铁氮相图中,580℃为同素异晶转变点,低于580℃其组织为铁,高于580℃其组织转变为铁。
通常,进步处理温度有助于氮化物的形成和获得较深的渗层(在相同时间内),这是由于扩散系数与温度的指数变化成正比。
但是,由于在铁中氮的扩散系数仅为铁中的1/4 ,当处理温度高于580℃时,渗层的增长反而减慢,因此,离子氮化的控制温度范围为520℃至580℃。
2. 软氮化温度的选择范围关于碳钢或铸铁或低合金钢,人们常采纳离子软氮化(低温碳、氮共渗)技术。
就大量的施行说明:氮化层的硬度和渗层与温度、时间、浓度有极值关系。
通常在氨气与丙酮之比为10:1,温度在560℃至580℃,时间在3至4小时之间,获得的硬度和渗层。
雪佛莱曲轴离子氮化工艺
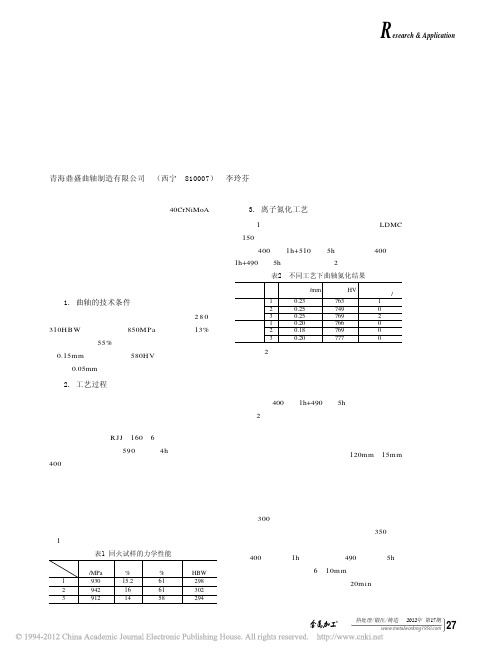
27esearch & ApplicationR研究与应用汽车零部件制造技术专题雪佛莱曲轴离子氮化工艺青海鼎盛曲轴制造有限公司 (西宁 810007) 李玲芬我公司生产的雪佛莱曲轴材质为40CrNiMoA ,毛坯经过调质处理,具有良好的力学性能和一定的心部硬度。
成品采用辉光离子氮化处理,具有以下优点:①表面硬度高,耐磨性好。
②表层有较高的残留压应力,显著提高疲劳强度。
③变形小,且规律性强。
④渗氮层组织容易控制,脆性小。
⑤渗氮速度快,节约能源,没有污染。
1. 曲轴的技术条件雪佛莱曲轴毛坯调质处理后硬度为280~310HBW ,抗拉强度≥850MPa ,伸长率≥13%,断面收缩率≥55%;成品氮化处理后氮化层深度≥0.15mm ,表面硬度≥580HV ,各主轴颈径向圆跳动≤0.05mm 。
2. 工艺过程曲轴加工工艺流程为:锻造(正火态)→调质→粗加工→去应力回火→校直→去应力回火→抛丸→精加工→氮化→抛光、检验、入库。
去应力回火在RJJ -160-6井式炉中进行,竖直放置,可放两层,590℃保温4h 后随炉冷却至400℃以下,然后出炉空冷。
氮化前去除应力工序对减小氮化变形起着十分重要的作用,能消除锻造、调质及机加工造成的大部分内应力,如果回火后变形超差,校直后再次按原工艺回火可消除校直造成的应力,直到变形量合格为止。
曲轴回火后截取试样做拉伸试验,检测结果如表1所示,各项指均标符合技术要求。
表1 回火试样的力学性能项目编号抗拉强度/MPa 伸长率(%)断面收缩率(%)基体硬度HBW 193015.26129829421661302391214582943. 离子氮化工艺(1)氮化工艺方案的确定 曲轴氮化在LDMC -150氮化炉中进行,初步定了两种工艺方案:工艺一为400℃×1h+510℃×5h ;工艺二为400℃×1h+490℃×5h 。
氮化效果如表2所示。
氮化曲轴工艺流程加工工艺
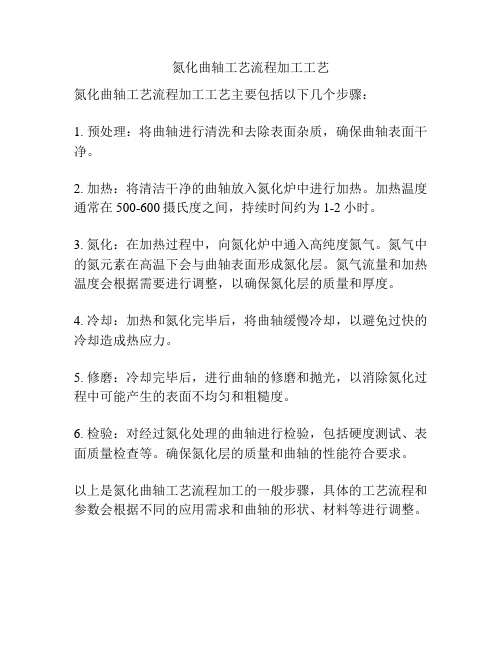
氮化曲轴工艺流程加工工艺
氮化曲轴工艺流程加工工艺主要包括以下几个步骤:
1. 预处理:将曲轴进行清洗和去除表面杂质,确保曲轴表面干净。
2. 加热:将清洁干净的曲轴放入氮化炉中进行加热。
加热温度通常在500-600摄氏度之间,持续时间约为1-2小时。
3. 氮化:在加热过程中,向氮化炉中通入高纯度氮气。
氮气中的氮元素在高温下会与曲轴表面形成氮化层。
氮气流量和加热温度会根据需要进行调整,以确保氮化层的质量和厚度。
4. 冷却:加热和氮化完毕后,将曲轴缓慢冷却,以避免过快的冷却造成热应力。
5. 修磨:冷却完毕后,进行曲轴的修磨和抛光,以消除氮化过程中可能产生的表面不均匀和粗糙度。
6. 检验:对经过氮化处理的曲轴进行检验,包括硬度测试、表面质量检查等。
确保氮化层的质量和曲轴的性能符合要求。
以上是氮化曲轴工艺流程加工的一般步骤,具体的工艺流程和参数会根据不同的应用需求和曲轴的形状、材料等进行调整。
曲轴加工工艺
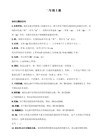
(2) 造型
气流冲击造型工艺明显优于粘土砂型工艺,可获得高精度的曲轴铸件,该工艺制作的砂型具有无反弹变形量等特点,这对于多拐曲轴尤为重要。目前,国内已有一些曲轴生产厂家从德国、意大利、西班牙等国引进气流冲击造型工艺,不过,引进整条生产线的只有极少数厂家,如文登天润曲轴有限公司引进了德国KW铸造生产线。
(1) 熔炼
高温低硫纯净铁水的获得是生产高质量球墨铸铁的关键。国内主要是以冲天炉为主的生产设备,铁水未进行预脱硫处理;其次是高纯生铁少、焦炭质量差。目前已采用双联外加预脱硫的熔炼方法,采用冲天炉熔化铁水,经炉外脱硫,然后在感应电炉中升温并调整成分。目前,在国内铁水成分的检测已普遍采用真空直读光谱仪来进行。
曲轴制造技术/工艺的进展
1、球墨铸铁曲轴毛坯铸造技术
球墨铸铁曲轴的生产继QT800-2、QT900-2等几种牌号后,广西玉柴等经过攻关已能稳定生产QT800-6牌号的曲轴,为曲轴“以铁代钢”奠定了基础。
(1) 熔炼
高温低硫纯净铁水的获得是生产高质量球墨铸铁的关键。国内主要是以冲天炉为主的生产设备,铁水未进行预脱硫处理;其次是高纯生铁少、焦炭质量差。目前已采用双联外加预脱硫的熔炼方法,采用冲天炉熔化铁水,经炉外脱硫,然后在感应电炉中升温并调整成分。目前,在国内铁水成分的检测已普遍采用真空直读光谱仪来进行。
国外的曲轴砂带抛光机可同时抛光主轴颈、连杆轴颈、圆角、轴肩及止推面。其结构均采用对夹式,每个轴颈上用4片垫块(中凹型)压紧砂带;垫块和砂带宜根据工件材质和硬度选择;机床上的卷带机能保证每个轴颈都有一段新砂带(长度可调)参加工作;抛光的方式以超精加工的原理进行。其效率和效果都远远优于油石。
对于球铁曲轴的抛光与磨削,由于球铁内的铁素体磨削后会形成突起毛刺,所以应使轴的磨削转向与工作转向相反,抛光转向与工作转向相同。这样才能在抛光中有效地去除毛刺,避免工作时刮伤轴瓦。(end)本类相关文章
软氮化工艺

软氮化1.适用范围:本资料是对提高汽车用结构钢,铸铁件的性能进行软氮化处理。
但是本资料不涉及原来氮化钢的氮化处理。
注1.标准中{}内的单位、数值是由原来单位换算而得到。
供标注时参考。
注2.资料中〈〉中的事项为国外记载的内容。
2.术语含义:资料所说软氮化就是钢及铸铁件在400~650℃盐浴,或气体环境中表面形成几μ至几十μ的碳、氮化合物及0.1~1.0mm深氮素层的处理方法。
备注:1.急冷就是防止提高疲劳强度的铁氮化物析出(γ. Fe7N)。
2.慢冷就是空冷(炉冷),空冷后水冷或空冷后油冷。
特别是对于变形有要求的工件,一定要慢冷却。
3.软氮化处理有以下几种:1)经过允许,使用氰盐或氰酸盐为主体的盐浴软氮化法2)气体中的软氮化法3)低压气体状态下进行放电离子软氮化4)英国某公司特定在表面化合物层上得到氧化膜的高温软氮化法(通称专用氮化),对氰化物氮化、气体氮化、离子氮化后的强化性能没有差异。
根据需要可以选定3种中的一种。
专用氮化的处理方法以提高耐磨、耐腐蚀性为主,对于提高抗疲劳的情况应确认其必要性。
表示方法氰化物氮化用“T”、气体氮化用“G”、离子氮化用“I”、对专用氮化处理的涂蜡件用“W”表示,不涂蜡的用“X”表示,如同ATSH5205G-AT的样子表示。
因为这种蜡处理有腐蚀性,可以让其浸泡在不溶于水的碱性脂肪酸盐、白色的有机溶液中。
4.指定项目:软氮化的指定项目见表2。
注〈1〉专用氮化处理的场合及有要求的场合可以个别指定氧化膜、渗透层、致密层、残余奥氏体层。
备注:1. 根据工件的性质可以从项目中指定一个或多个项目。
2.对于离子氮化、软氮化部位有特殊要求的场合应同有关部门协商。
5.扩散层深度5.1扩散层深及疲劳强度软氮化处理可以提高疲劳强度,化合物以下的氮扩散层硬度增加,并产生残余压应力。
1/4但,在处理的目的是提高疲劳强度的场合,须按图纸要求达到扩散层深。
5.2 扩散层深的测定方法5.2.1显微组织试验方法把试片在300~350℃的温度加热并保温1小时(时效处理),使扩散层中的固溶氮作为 γ4N 析出。
WD618曲轴气体软氮化试验
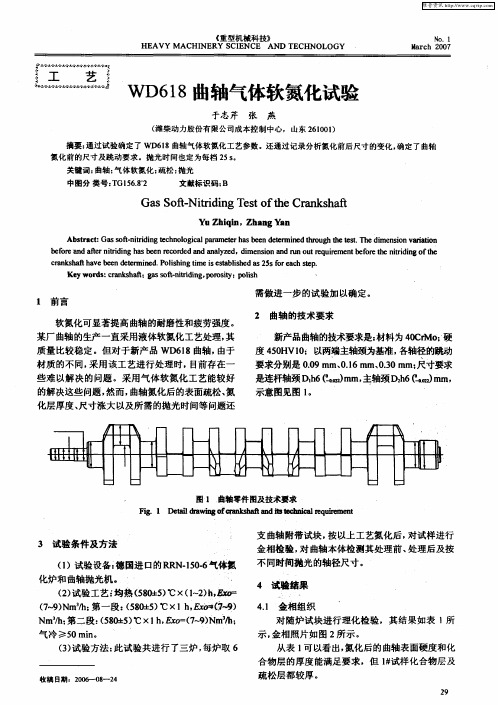
毳 I
.
_ - 一
_ _ — —
t
_ 一
- ● 一
r
黎 .
、
_] T 盯
I 8 l
幽
I . _ L
,
图 l 曲轴零件 图及 技术 要求 F吕 l ea a n o aa k d adi tc ncl u c n - D tid wig f n  ̄ t n t  ̄h i  ̄q i me t lr s a r
Nm3 : / 第二段 :5 o 5 ℃ Xl , x = 7 9 Nm'  ̄ h ( 8 士 ) h E o ( ̄ ) / h
r
金相检验, 曲轴本体检测其处理前 、 对 处理后及按 不 同时伺抛光的轴径尺寸 。
4 试 验 结果
一
_
41 金 相 组织 .
’
对 随炉 试块 进行 理化 检 验 ,其 结果 如表 l 所
新产品曲轴的技术要求是: 材料为 4 CMo 硬 0r : 度 4 0 : 以两端主轴颈为基准 , 5HV1 0 各轴径 的跳动
要求分别是 00 .9mm、 . 03 m; 寸要求 01 mm、.0r 尺 6 a 是连杆轴颈 DI mm, 颈 D 6 , mm, hC 6 主轴 h
l 前言
需 做进 一步 的试 验加 以确 定 。 2 曲轴 的 技术要 求
软氮化可显著提高曲轴 的耐磨性和疲劳强度。 某厂曲轴 的生产一直采用液体软氮化工艺处理, 其 质量 比较 稳定 。但 对于 新产 品 WD 1 6 8曲轴 , 由于
材质 的不 同 , 用 该工 艺进 行 处理 时 , 采 目前 存在 一
示, 金相 照 片如 图 2所 示 。
气冷 ≥5 n 0mi。
- 1、下载文档前请自行甄别文档内容的完整性,平台不提供额外的编辑、内容补充、找答案等附加服务。
- 2、"仅部分预览"的文档,不可在线预览部分如存在完整性等问题,可反馈申请退款(可完整预览的文档不适用该条件!)。
- 3、如文档侵犯您的权益,请联系客服反馈,我们会尽快为您处理(人工客服工作时间:9:00-18:30)。
汽车曲轴的软氮化技术
为提高曲轴的疲劳强度,许多曲轴生产厂采用了气体软氮化技术(气体软氮化是一种由液体软氮化发展起来的、化学热处理工艺,其实质是以渗氮为主的低温碳氮共渗。
它的特点是处理温度低、时间短,工件变形小,质量稳定,不受钢种限制,能显著提高零件的耐磨性、疲劳强度、抗咬合、抗擦伤等性能,同时还能解决液体软氮化中的毒性问题,避免了公害,因而劳动条件好。
此外,设备和操作都简单,容易推广。
其基本原理是气体软氮化的原理是在530°~580℃的气氛中产生2CO →[C]+CO_2(渗碳)及2NH3→2[N]+3H_2(氮化)反应,使钢铁表面形成氮化物或碳
氮化物。
),其中采用这项技术以山东曲轴总厂、潍坊柴油机厂、重汽集团复强动力公司等为典型代表。
仅山东曲轴总厂,就拥有连续软氮化生产设备及5-2
型气体软氮化设备近10多台。
而重汽集团复强动力公司设备能力达到技术国内最先进、功率最大、装炉量最多,同时比同行业设备更具有节能环保效应。
目前,国内生产曲轴所采用的典型材料为45钢和42CrMoTi。
曲轴气体软氮化与处理其他软氮化零件相类似,其氮化工艺过程一般要经过前清洗、升温、保温、冷却、后清洗等5个阶段,包括出装炉。
不同的厂家在气体软氮化工艺上略有不同。
1.前清洗工艺
待处理零件装炉前应通过清洗使零件表面清洁无油,目前采用的主要清洗方法主要有下列方式:高温蒸汽加清洗剂洗涤然后加高温蒸汽漂洗涤、自动清洗机清洗、汽油擦洗。
清洗的好坏将直接影响曲轴的处理质量和延长处理周期。
如果曲轴表面脏,处理后的曲轴表面附着很多碳黑,既影响产品外观又影响产品质量。
经改进清洗工艺后,处理质量大大提高。
据实际经验来看,表面清洁易形成连续的厚度较为均匀的化合物层,反之则不易形成连续和厚度均匀的化合物层。
而在气体软氮化时化合物层对硬度、耐磨及抗疲劳性能有较大贡献。
本文的第三种方式是在生产条件不具备时的变通方法,仅适用于小规模清洗。
2.预氧化工艺
为保证零件性能的综合要求,在气体软氮化之前一般还需要进行预先热处理,气体软氮化的预热温度一般取400~490℃,保温1h左右,去除工件表面油污、
油脂,并在表面形成一层氧化物,使(合金)氮化物缓慢形成,使深层更加均匀。
根据零件易变形程度,选择适当的升温速度并应在预先热处理使组织充分均匀化。
3.软氮化工艺
气体软氮化工艺参数一般为:平均升温速度100℃/h;保温温度为540~570℃;保温时间为3~4h。
(1)软氮化温度的选择范围及控制
对于碳钢或铸铁或低合金钢,人们常采用气体软氮化(低温碳、氮共渗)技术。
就大量的实践表明:氮化层的硬度和渗层与温度、时间、浓度有极值关系。
在铁氮碳三元相图中,同素异晶转变点略有降低,其等温截面大约降至575℃。
当温度高于575℃时,随着温度的升高,渗层和硬度迅速下降,高于600℃时,渗层几乎完全消失。
为使有较好的碳、氮共渗效果,气体软氮化的控制温度一般取570℃(高于三元共析点)。
表层中形成含氮奥氏体,快冷时形成含氮马氏体,使表面形成高硬度,所以软氮化易采用快冷。
软氮化前期(约3h)属强渗阶段,在表层形成高氮势相ε,提高渗速,而后进入扩散阶段,降低表面氮含量,减小脆性。
(2)软氮化工艺气体比例流量
强渗时NH3、CO2、N2时的比例一般为55:5:40,通气量一般为炉堂体积的1.5~2倍。
适当提高NH3含量,可以提高渗层;适当提高CO2含量,可以提高
工件表面硬度(若采用HV10测量,则对表面硬度影响的因素是氮前基体硬度,扩散层深度,白亮层硬度。
45钢要求氮前基体硬度应>200HBW)。
扩散时NH3、CO2、N2时的比例一般为40:5:55,通气量一般为炉堂体积的1~1.5倍。
炉内氢含量:强渗区氢含量10%~18%以上(新炉氢含量偏低);扩散区氢含量8%~13%以上(新炉氢含量偏低)。
烘炉工艺:每次新起炉装工件之前应进行空渗,空渗时间6~12h,氢含量达到10%以上。
新炉子连续使用一段时间(3个月)后,应进行空渗。
温度600℃保温12h以上,只通少量氮气,维持炉压即可(240~300Pa)获得最佳的硬度和渗层。
4.软氮化后冷却工艺
为使曲轴有较好的碳、氮共渗效果,气体软氮化的控制温度一般取570℃(高于三元共析点)表层中形成含氮奥氏体,氮化后快冷时形成含氮马氏体,使表面迅速形成高硬度,所以软氮化易采用快冷。
某设备厂商连续软氮化冷却采用油冷却,其设备采用完全自动控制,由推料机构直接从氮化炉体内推到油冷升降台上,自动降到油槽冷却。
冷却采用双搅拌冷却,一般快搅取:5~6min,1300r/min。
慢搅取:10min左右,750r/min。
淋油取5min左右。
冷却后一般曲轴都会大小
产生变形,关于变形只要时效处理好(2~4h),均匀升温就可保证变形较小,潍坊柴油机厂的氮化曲轴轴向跳动控制方面做的就比较好。
5.氮化后清洗工艺
处理后零件应通过清洗使零件表面清洁无油,目前采用的主要清洗方法主要有下列方式:高温蒸汽加清洗剂洗涤然后加高温蒸汽漂洗涤;自动清洗机清洗;汽油擦洗。