生产节拍与产能分析表
产能分析(含OEE)模板
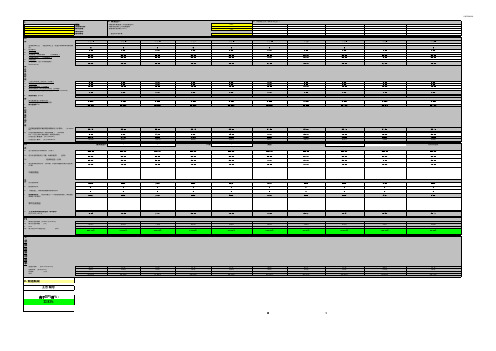
V. 总体设备利用率
设备可用率 [(N-O1-O2-P)/(N-O1)]
性能效率 [(M*Q)/(N-O1)]
合格率
[T/Q]
OEE
DSHEADRICEADTED
VI. 制造瓶颈
工艺 编号
5.03
60042 10007 1500 567.13%
97% 99% 99.97% 95.85%
10.26
37734 6289 1500 319.27%
C) 产能修改记录(例如按节拍生产)
工艺 6
1 1.00 16.00 90.00 0.00 6.00 87.00
0.00 0.00 10.00 0.00 1.00 99%
0.05% 99.95%
34.38 8.00 38681 6447 其他
960.00 90.00 0.00 10.00
6260 1 0
99%
0.60% 99.40%
33.40 20.00 15029 2505 例如试运转
960.00 90.00 20.00 10.00
2500 1 0
2499
30.47
14994 2499 1500 66.60%
97% 99% 99.96% 95.75%
99% 99% 99.98% 98.22%
工艺7
1.00 16.00 90.00 20.00 6.00 85.00
0.00 0.00 10.00 0.00 1.00 99%
0.05% 99.95%
33.58 25.00 12090 2015
960.00 90.00 20.00 10.00
2010 1 0
6259
25.00
37554 6259 1500 317.27%
冲压产能分析
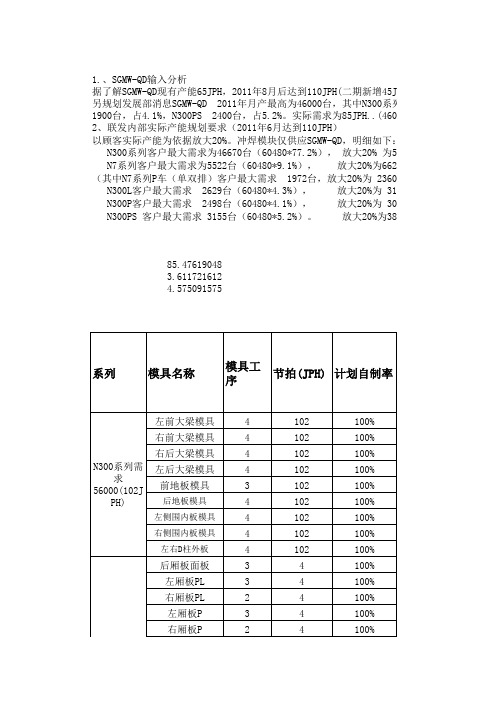
产能预测输 入---投资》
模具工序
月供产量 (件)
月需冲次 (产量*工
序数)
冲床21台 月供冲次
2011年是 否投资
备注
35
56000 1960000
52
2360 122720
28 25 39
3100 3000 3800
86800 75000 148200
21台*26 天
*17.875 小时*229 冲次/小时 =223498
85.47619048 3.611721612 4.575091575
模具投资细化
系列
模具名称
模具工 序
节拍(JPH) 计划自制率
左前大梁模具
4
102
100%
右前大梁模具
4
102
100%
右后大梁模具
4
102
100%
N300系列需 左后大梁模具
4
102
100%
求 56000(102J
前地板模具
3
102
P车需求 右后侧门外板PS
1
4
100%
2360台 左后侧门内板PS 5
4
100%
(4JPH) 右后侧门内板PS
5
4
100%
左厢板外板PS
4
4
100%
右厢板外板PS
4
4
100%
货车后板111P
5
4
100%
底板(PSL)
2
4
100%
底板(PL)
2
4
100%
底板(PS)
3
4
100%
左右后侧门
3
4
节拍产能分析验证报告

100%
0.005% 99.995%
49.27 40.00 11699 1950
B) 顾客生产
X 顾客需求量/星期(不包括售后件) Y 顾客/供应商的工作天数/星期 Z 顾客每天需求量(DPV)
售后件年需求量
工艺 2
工艺3
9500 5
1900 0
工艺 4
C) 产能修改记录(例如按节拍生产)
工艺 5
工艺 6
J 总计计划停机时间/星期(小时数) [(FxG+H+I)/60xAxD]
工艺 1 成型
1 2.00 12.00 60.00 10.00 6.00 130.00
60.00 0.00 0.00 0.00 0.00
K 设备可用性 [(E-J)/E]
预计合格率(%) 预计报废和返工零件百分比 对于相关工艺,请参见培训材料
IV. 产能计算
V 每周可运零件数 [E*3600*L/ (N*60/Q)] W 每天可运零件数 [V/Y]
Z DPV AA 高于/低于DPV的百分比
[W /Z]
V. 总体设备利用率
设备可用率 [(N-O1-O2-P)/(N-O1)]
性能效率 [(M*Q)/(N-O1)]
合格率
[T/Q]
OEE
DSHEDARICEADTED
120.00 0.00
10、
中断的原因
生产运转的零件量数据 Q 总计运转零件 R 拒收零件总计 S 下线后返工、再测试或着维修的零件总计 T 合格零件总计 (仅首次通过——不包括被拒收的、再1900 0 0
1900
U 工艺实际周期时间总计 (秒/零件)
[N x 60 / Q]
L 预计合格率 (%)
产能验证

产能规划和验证的目的
使用既定的生产工艺过程 按照规划的生产节拍 来生产合格的产品 满足顾客每周的生产需求
Produce the required VOLUME of QUALITY PARTS, In the planned OPERATING PATTERN, At the planned PRODUCTION RATE.
OEE简化后的公式为:
OEE OEE
OEE=
总良品数(GPP) 最大可能产品数
=
总良品数(GPP) x净理 想节拍时间(NICT) 净可用时间(NAT)
19
课程内容提要
产能验证简介 什么是OEE? 产能验证要求 产能验证表格Section A:所需OEE 产能验证表格Section B:展示OEE
暂停机损失
利用水平
减速损失
利用水平
生产过程次品损失
质量水平
14
OEE的构成
OEE的计算方法
OEE
总良品数(GPP) x净理 想节拍时间(NICT) 净可用时间(NAT)
可用水平
操作时间 净可用时间(NAT)
利用水平
净理想节拍时间(NICT) 操作时间/生产零件总数
质量水平
总良品数(GPP) 生产零件总数
福特使用基于OEE的工具来判断产能计划是否有效 OEE数据的收集是Q1现场评审(Q1 MSA)要求的一部分
9
产能验证要求
展示OEE vs. 所需OEE
产能验证要求: 所需OEE <100% 所需OEE能够满足所有 自身的潜在损失 总的共线分配率 ≤100% 展示OEE ≥所需OEE
什么是OEE?
10
装配
凸轮
产能分析表说明.ppt
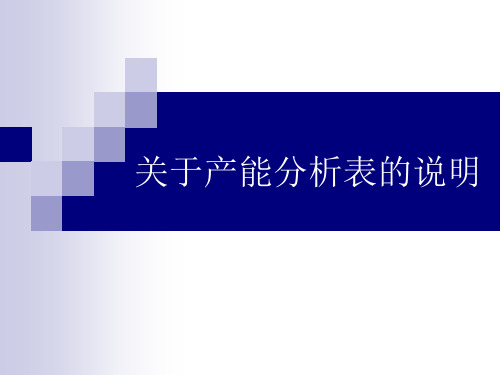
• 7、Although the world is full of suffering, it is full also of the overcoming of it.----Hellen Keller, American writer虽然世界多苦难,但是苦难总是能战胜的。20.8.520.8.520.8.5。2020年8月5日星期三二 〇二〇年八月五日
所以,产能分析表是指针对生产能力进行分 析的图表,它包含了投入人员,产出成品数 量,工时及节拍时间等参数
作用
1、根据产能分析表中所提供的工时对供应 商进行报价
2、根据所设定的目标产能预估产品的完成 日期及安排生产排程
3、根据工时确定每个工位的工作内容及投 入的人数及设备数量
4、评估每个工位的负荷,以便保证产线平 衡
• 3、Patience is bitter, but its fruit is sweet. (Jean Jacques Rousseau , French thinker)忍耐是痛苦的,但它的果实是甜蜜的。11:038.5.202011:038.5.202011:0311:03:108.5.202011:038.5.2020
• 10、Life is measured by thought and action, not by time. ——Lubbock 衡量生命的尺度是思想和行为,而不是时间。8.5.20208.5.202011:0311:0311:03:1011:03:10
• 11、To make a lasting marriage we have to overcome self-centeredness.要使婚姻长久,就需克服自我中心意识。Wednesday, August 5, 2020August 20Wednesday, August 5, 20208/5/2020
冲压产能分析计算公式
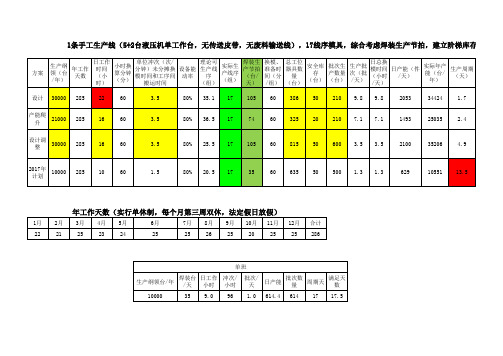
生产纲 年工作 领(台 天数 /年) 30000 285 日工作 单位冲次(次/ 理论可 焊装生 换模、 总工位 小时换 实际生 安全库 批次生 生产批 时间 分钟)未分摊换 设备能 生产线 产节拍 准备时 器具数 算分钟 产线序 存 产数量 次(批 (小 模时间和工序间 动率 序 (台/ 间(分 量 (分) (组) (台) (台) /天) 时) 搬运时间 (组) 天) /组) (台) 22 60 3.5 80% 35.1 17 105 60 386 50 210 9.8 日总换 实际年产 模时间 日产能(件 生产周期 能(台/ (小时 /天) (天) 年) /天) 9.8 2053 34424 1.7
80%
20.5
17
35
60
635
50
500
1.3
1.3
629
10551
13.5
年工作天数(实行单休制,每个月第三周双休,法定假日放假)
1月 22 2月 21 3月 25 4月 23 5月 24 6月 25 7月 25 8月 26 9月 25 10月 20 11月 25 12月 25 合计 286
单班 生产纲领台/年 10000 焊装台 日工作 冲次/ /天 小时 小时 35 9.0 96 批次/ 批次数 满足天 日产能 周期天 天 量 数 1.0 614.4 614 17 17.5
模具,综合考虑焊装生产节拍,建立阶梯库存,循环生产。
一周期满 足焊装生 产时间 (天) 2.0
备注 三班,阶梯库存105、 210台。每天按批次生 产数量循环生产。 双班,阶梯库存74、 148、222台,每天按 批次生产数量循环生产 。 双班,阶梯库存105、 210、315、420、525 、630台,每天按批次 生产数量循环生产。 双班,根据生产周期、 生产顺序和批次生产数 量做好初始库存,然后 循环生产即可。
精益生产评价表
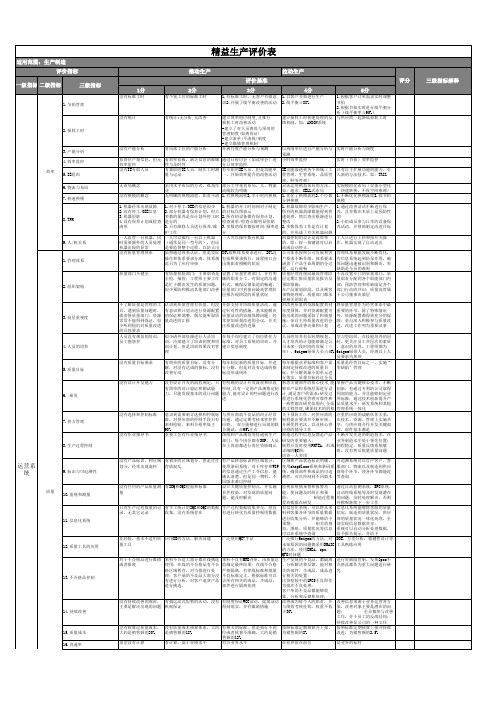
量与记录
一,开始效率提升的改善活动 程管理、生管系统、品质管 入新的方法技术。如:TRIZ
理、财务管理)
无布局概念
采用水平布局的方式,孤岛作 部分工序垂直布局,人、物流 灵活运用精益布局的方法。 实现模组化布局(设备小型化
业
动线较为明确
如:超市、CELL式布局
、快速转换,不收空间束缚)
没有换模的概念
部;预防管理和零缺陷是各个
很少预防和推动其他部门改善 质量部门可直接向最高管理阶 在产品策划阶段,以及顾客 部门行动的共识;质量高管属
层报告现阶段的质量状况
事物处理时,质量部门都承 于公司董事决策层
担相关的职责
不了解质量是管理的工 认识到质量管理有价值,但没 开始支持并协助质量活动,通 对改善质量的资源配置列到 将质量管理作为经营体系中最
进行挑选。
部件进行隔离处理
为批次不良处理;
客户单的不良品都能够收
集,分析和反馈和处理;
没有持续改善的规范, 有搞运动式短暂的活动,没有 有制度保证WCC活动,提案活动 改善成为每个人的职责,并 改善信息来源于业务运营各方
主要是解决出现的问题 机制保证
得到落实,并有激励措施
与绩效考核挂钩,权重不低 面,改善对象主要是潜在的问
质量 10.监视和测量
11.信息化系统
12.质量工具的应用
13.不合格品控制
14.持续改善
15.质量成本 16.直通率
精益生产评价表
推动生产
拉动生产
评价基准
评分
1分
2分
3分
4分
5分
没有标准工时
有个别工位的标准工时
1.有标准工时,无客户节拍意 1.以客户节拍进行生产
APQP生产系统产能估计表

最小量(件 /日))
最大量 (件/ 日))
实际合格产 月份产能
实际产量 量(件/ (26天/
(件/日) 日)
月)
1 2 3 4
5
6 7 9 10 11 12 13 14 15 16 17 18 19 20 备注:
下料 调质 钻镗孔 车外圆 钻铰孔倒
角 铣平面 清洗防锈
外协 外协 内制 内制
内制
内制 内制
数控车床 数控车床
台钻
铣床 清洗机
1
1
480
450
0.4 2.00% 1125
2
2
960
900
0.6 2.00% 1500
1125 1500
1102 1470
28665 19110
2
2
960
900
0.3 2.00% 3000
3000
2940 76440
1
1
480
450
0.3 2.00% 1500
1500
1470 38220
1
1
480
450
0.01
480பைடு நூலகம்00
480000 480000 480000
1470 8820
编号:ZD-APQP-1-9 零件名称: ****** 零件号:***********
生产系统
生产系统产能分析表
产能分析
日期: 填写 者:
在途、库存
按节拍生产运行结果
序号
工序名称 工序性质 设备名称 设备型号 设备数量
班/天
分钟/天 (分)
可利用时 间/天
生产节拍 (分)
(分)
进行按节拍
【精品】Run-at-Rate节拍生产(FORD)汇总

Required Input
Trained Supplier Production Operators
Supplier must show verification that the required operators have been trained on new / revised tooling, equipment and process.
Phase 0 包含的Phase PPAP要素
1 – Design Records 2 – Engineering Change Documents 3 – Customer Engineering Approval 4 – Design FMEA 5 – Process Flow Diagrams 6 – Process FMEA 7 – Control Plan 8 – Measurement System Analysis Studies 16 – Checking Aids 17 – Customer-Specific Requirements Capacity Analysis Report
发布的设计
※ 1.已经获得CAF采购的订单,记录订单号。
※ 2.RSMS/IMDS已经注册成功,获得注册成功的Screen Print 及MDS报告。
※ 3.已经获得福特发布的图纸,并且和采购订单一致,记录零件 号和国内工程变更等级/日期。
※ 4.已经获得子零件的图纸并内部已发布。出示正式的BOM表。
Required Input
Quantity of parts required as defined by customer (default 300 consecutive parts)
Supplier must perform a production run on intended production machinery utilizing a minimum of 1 tool, and facilities with intended operators at the intended production rate. The approving authority may deviate from the 300 piece (e.g., instrument panel produced in Just-in-Time plant, wiring hardness assembly)
生产人员配置生产节拍预测分析统计表

合计
10
155/19
440
40
17.6件
17
439分钟
DPF生产人员配置/生产节拍预测分析统计
组件名称 一、燃烧室组件 工序名称 1-1筒体焊接 加工设备 氩弧焊机 气保焊机 氩弧焊机 氩弧焊机 焊接专机 气保焊机 气保焊机 氩弧焊机 人工 氩弧焊机 气保焊机 人工 气保焊机 氩弧焊机 气保焊机 气保焊机 气保焊机 气保焊机 气保焊机 气保焊机 气保焊机 焊接专机 焊接专机 气保焊机 灌装机 气保焊机 人工 气保焊机 人工 人工 人工 人工 人工 人工/检具 人工/检具 人工 人工 1人 2人 2人 1人 人员配置 加工数据 ⊿2¢76 ⊿3L60 ⊿2¢6 ⊿2¢76 ⊿3¢76 ⊿2¢243 ⊿5¢266 ¢20 ¢266 ⊿2¢243 1人 o5¢266 ¢20 ¢63.5/¢76 139*134 ¢63.5/¢76 1人 ¢76 ¢76 ¢76 节拍 单件生产 (分钟) 合计时间 10 2 3 4 3 5 2 3 5 5 5 5 2 3 5 5 4 5 4 3 4 5 5 5 5 2 3 8 3 5 10 5 5 5 5 10分钟 10分钟 26分钟 25分钟 22分钟 顾客需求 工作时 休息/其他 间(分 每天最大产能 每天最 时间 生产时间 钟) 大需求 440 440 440 440 440 440 440 440 440 440 440 440 440 440 440 440 440 440 440 440 440 440 440 440 440 440 440 440 440 440 440 440 440 440 440 440 440 40 40 40 40 40 40 40 40 40 40 40 40 40 40 40 40 40 40 40 40 40 40 40 40 40 40 40 40 40 40 40 40 40 40 40 40 40 44件 44件 16.9件 20件 17 17 17 17 17 17 17 17 17 17 17 17 17 17 17 17 17 17 17 17 17 17 17 17 17 17 17 17 17 17 17 17 17 17 17 17 17 170分钟 检具/量具 439分钟 气动扳手 装配工装 331分钟 备注 18MM/min(1M) 83mm/min(5M)
自动化生产流水线节拍、设备利用率计算

自动化生产流水线节拍、设备利用率计算引言概述:自动化生产流水线是一种高效率、高产能的生产模式,通过合理安排生产流程和优化设备利用率,可以实现生产效率的最大化。
本文将介绍自动化生产流水线节拍的概念和计算方法,以及设备利用率的计算方式。
一、自动化生产流水线节拍1.1 节拍的定义自动化生产流水线的节拍是指完成一个产品的生产所需的时间,通常以单位时间内生产的产品数量来衡量。
节拍的快慢直接影响到生产效率和产能。
1.2 节拍的计算方法节拍的计算方法可以根据生产流水线的具体情况进行调整,但通常可以使用以下公式进行计算:节拍 = 生产时间 / 生产数量其中,生产时间指的是从开始生产到完成生产所经过的时间,生产数量是指在这段时间内生产的产品数量。
1.3 节拍的优化方法为了提高自动化生产流水线的节拍,可以采取以下优化方法:- 优化生产流程,减少生产环节和不必要的等待时间。
- 提高设备的运行速度和稳定性,减少设备故障和停机时间。
- 合理安排生产计划,避免生产过程中的阻塞和等待。
二、设备利用率的计算2.1 设备利用率的定义设备利用率是指设备在生产过程中实际运行的时间与总运行时间之间的比率,反映了设备的利用效率。
2.2 设备利用率的计算方法设备利用率的计算方法可以使用以下公式:设备利用率 = 实际运行时间 / 总运行时间其中,实际运行时间是设备在生产过程中真正处于运行状态的时间,总运行时间是指设备在生产过程中应该运行的总时间。
2.3 设备利用率的优化方法为了提高设备利用率,可以采取以下优化方法:- 减少设备故障和停机时间,提高设备的可靠性和稳定性。
- 合理安排设备维护计划,减少维护时间对生产的影响。
- 优化生产计划,避免设备的空闲和闲置。
三、自动化生产流水线节拍与设备利用率的关系3.1 节拍与设备利用率的影响关系节拍和设备利用率是相互关联的,节拍的快慢直接影响到设备的利用率。
如果节拍过慢,会导致设备的空闲和闲置,从而降低设备利用率;如果节拍过快,可能会导致设备的超负荷运行,增加设备故障的风险。
标准工时模板
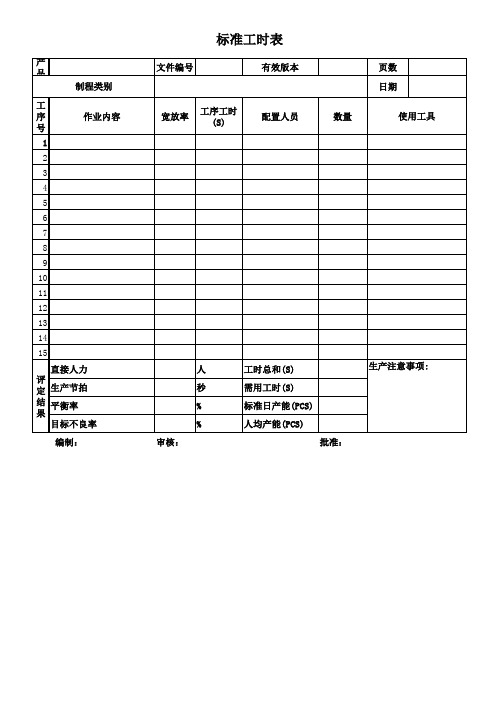
需用工时s标准日产能pcs人均产能pcs产能负荷分析表工位名称所属制程名称分析时段工位代号代号产能分析正常班可稼动天数说明可稼动设备每班人数每日班次设备产能时间人产能时间加班可加班时间设备可加班时间人力可加班时间合计产能时间负荷分析制造命令标准工时负荷工时累计负荷分析分析对策
标准工时表
产品规格 制程类别 工 序 号 1 2 3 4 5 6 7 8 9 10 11 12 13 14 15 直接人力 评 定 生产节拍 结 平衡率 果 目标不良率 编制: 审核: 人 秒 % % 工时总和(S) 需用工时(S) 标准日产能(PCS) 人均产能(PCS) 批准: 生产注意事项: 作业内容 宽放率 工序工时 (S) 配置人员 数量 文件编号 有效版本 页数 日期 使用工具
产品产能验证分析报告

每班净 生产时 间(DF-G)
每周净 分配到 生产时 该产品 间(H× 时间比 B×C) 率
每周用 于该产 品的净 生产时 间(K×
L)
(L )
(M)
(N)
(O)
(P)
生
产 节 拍 (秒 /
模腔 数 (个)
每周理
良品 论生产
率 H(%)
数量(K ×3600 ÷L×M
×N)
客户 的每 周需 求 (件)
零件号码:
序号
工序名称
×××产品产能验证分析报告
零件名称:
车型
供应商名称
编号:
(A) 生产线
(B)
(C )
(D)
(E) (F)
单条线
每周 工作 天数
每天 班数
每班工作小 时
每周工 作时间 (B×C×
D)
每班平 均计划 停机时 间(小
时)
(G)
单条线 每班平 均非计 划停机 损失时 间(小 时)
(H) (I) (J) (K)
台)
备注:供方必须以每道工序产能盈余提升到15%为最终目标。
编制:
核准:
瓶颈工位
#N/A 产能是否满足需求
ቤተ መጻሕፍቲ ባይዱ
瓶颈工位的产能赢余 0.00% 不满足
品产能验证分析报告
编号:
(Q) 产能盈余 (N-O)/O
0.00% 不满足
产能分析生产计划产能均衡

产能分析生产计划产能均衡引言在现代制造业中,产能分析和生产计划是关键的组织和管理工具。
通过对企业的产能进行全面分析,并制定合理的生产计划,可以实现产能的均衡,提高生产效率和降低成本。
本文将从产能分析的概念和方法、生产计划的制定和产能均衡的实现等方面进行探讨。
产能分析产能分析是指通过对企业现有资源的评估和利用程度的分析,判断企业是否具备完成所需产量的能力。
产能分析可以从多个维度进行,包括设备产能、人力资源、原材料供应等。
以下是一些常用的产能分析方法:1. 设备产能分析设备产能是企业生产的基础,通过对设备的技术参数、工作时间、工作效率等指标进行分析,可以评估设备的产能。
常用的设备产能分析方法包括:•设备利用率分析:计算设备的实际产出与理论产能的比值,评估设备的利用程度。
•设备损失分析:分析设备的故障停机时间、维护时间等损失因素,评估设备的稳定性和可靠性。
•设备改善分析:通过改进设备的工艺流程、工作方式等,提高设备产能。
2. 人力资源分析人力资源是企业生产的重要组成部分,通过对人力资源的数量、技能水平等进行分析,可以评估人力资源的产能。
常用的人力资源分析方法包括:•人力资源需求分析:根据生产计划和工作流程,评估所需人力资源的数量和技能水平。
•人力资源供应分析:评估现有人力资源的数量和技能水平,判断是否能够满足生产需求。
•人力资源培训分析:通过培训和提升员工的技能水平,提高人力资源的产能。
3. 原材料供应分析原材料供应是企业生产的基础,通过对原材料供应的稳定性、供货能力等进行分析,可以评估原材料的供应产能。
常用的原材料供应分析方法包括:•供应商评估分析:评估供应商的信誉度、交货能力等因素,判断供应商是否能够满足生产需求。
•原材料库存分析:评估原材料库存的安全库存和经济批量,确保充足的原材料供应。
生产计划制定生产计划是根据产能分析结果,制定合理的生产安排,确保生产过程的顺利进行。
生产计划制定需要考虑以下几个因素:1. 产能需求根据市场需求和产品特性,确定所需产能数量和时间周期。
产能分析报告(含附属全套EXCEL表)
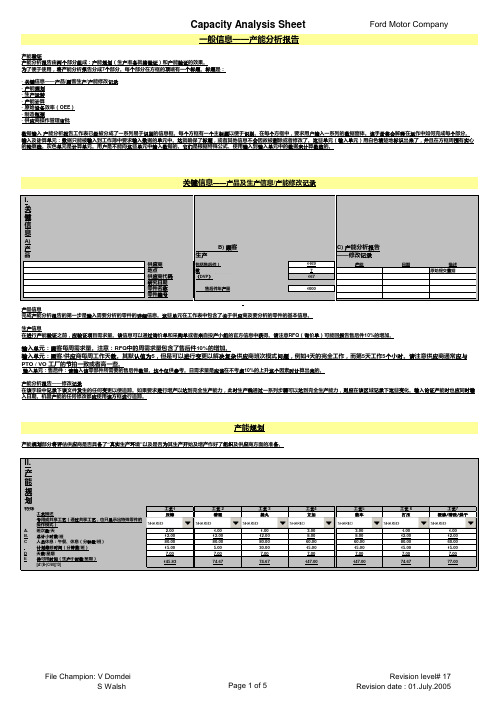
数据输入 产能分析报告工作表已经被分成了一系列易于识别的信息框。每个方框有一个主标题以便于识别。在每个方框中,要求用户输入一系列的数据窗体。该手册将会解释在运作中如何完成每个部分。 输入及计算单元:数据只能被输入到工作簿中要求输入数据的单元中。这就确保了标题,或者其他信息不会因故被删除或者修改了。这些单元(输入单元)用白色清楚地标识出来了,并且在方框周围有实心 的轮廓线。灰色单元是计算单元。用户是不能向这些单元中输入数据的。它们是根据特殊公式、使用输入到输入单元中的数据来计算数值的。
·计算单元:设备可用性会使用先前的数据自动计算得出。 设备可用性=(总计计划生产时间-停机时间)/总计计划生产时间
预计 合格 预计报废件和返工件的百分比
L 预计合格率(%)
1.50% 98.50%
0.50% 99.50%
0.50% 99.50%
0.50% 99.50%
0.60% 99.40%
·输入单元:预计报废率-输入该机器的损失值。注意:该工作表不记录相关工艺的报废率损失。为了计算相关工艺的输出,该报废率应乘上先前工艺的报废率。
·计算单元:正好满足顾客需求量所需的周期时间-仅供参考,工作表显示了正好满足顾客需求量的周期时间,是根据计划操作模式、预计停机时间及合格率计算得到的。这是用来与计划周期时间进行对比的 。 ·计算单元:每星期计划生产量和每天的计划生产量。这是为了与每星期或每天的顾客需求量进行对比的。
生产运转
在进行按节拍生产(阶段0)或者产能验证(阶段3)之前,供应商和顾客应就下列关键参数达成一致:要生产的零件数量、需测量的特性的选择、工艺设定、对涉及到的人员的审核、数据分析及报告。 生产运转的意图是为了确定供应商是否可以按照生产输入和速度生产出合格的零件。在生产运转计算中没有直接来自产能规划图的数据。
04-001生产节拍与产能分析表

90 100
110
120 130
齿圈加工节拍时间表
设备名称及型号 卷圆机LCYJ40
锯床G5230 对焊机
UNC-125-Y 刨渣机 BZ-500 井式炉
R03-180-90 压力机
YD61-500/YJ32-500 压力机 JL500T
CK-36P数控
CK-36P数控
超声波水浸探伤机 PCUGO02
DQ-T1122A
滚齿机Y3150E
工序名称 卷圆 切断
焊接、去渣
焊接、去渣
正火处理
平面整形
内孔整形
精车内孔、端面 并倒角
精车端面、外圆 并倒角
超声波水浸探伤 及外观检查
打印标识及生产 批号“HT×××
××××” 滚齿并去毛刺
淬火机床
HRZP-200 磁粉探伤机 CJW-
6000
齿圈高频淬火、 回火,磁力探伤
磁粉探伤
单件加工时间
10″ 12″ 20″ 12″ 16″ 20″ 20″ 35″ 35″ 35″
8″ 3′56″
48″
30″Βιβλιοθήκη 备注含上、下 件时间和 程序时 间,但不 包括换刀
时间
冲压产能分析计算公式

方案
生产纲 领(台 /年)
年工作 天数
日工作 时间 (小 时)
小时换 算分钟 (分)
单位冲次(次/ 分钟)未分摊换 模时间和工序间
搬运时间
设备能 动率
理论可 生产线
序 (组)
实际生 产线序 (组)
2.9
双产班数,量阶循梯环库生存产74。、 148、222台,每天按 批次生产数量循环生产 双班,阶梯。库存105、
阶梯库存:根据生产顺序安排,在第1天生产的备1 天量的库存,第2天生产的备2天量的库存,第3天 生产的备3天量的库存……直到一个周期完成所有 制件的生产,然后继续按照生产顺序循环生产。
10000
285
10
60
1.5
80% 20.5 17
35
60 635 50 500 1.3 1.3
629
10551 13.5
年工作天数(实行单休制,每个月第三周双休,法定假日放假)
1月 2月 3月 4月 5月
6月
7月 8月 9月 10月 11月 12月 合计
22
21
25
23
24
25
25
26
25
20
25
25 286
单班
生产纲领台/年
焊装台 /天
日工作 小时
冲次/ 小时
批次/ 天
日产能
批次数 量
周期天
满足天 数
10000
35 9.0 96 1.0 614.4 614 17 17.5
模具,综合考虑焊装生产节拍,建立阶梯库存,循环生产。
APQP新产品设计开发全套表格模板(含部分范本)
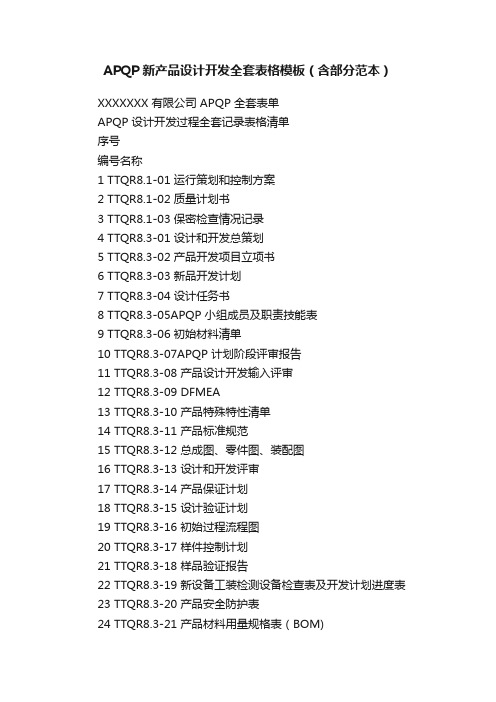
APQP新产品设计开发全套表格模板(含部分范本)XXXXXXX 有限公司 APQP 全套表单APQP 设计开发过程全套记录表格清单序号编号名称1 TTQR8.1-01 运行策划和控制方案2 TTQR8.1-02 质量计划书3 TTQR8.1-03 保密检查情况记录4 TTQR8.3-01 设计和开发总策划5 TTQR8.3-02 产品开发项目立项书6 TTQR8.3-03 新品开发计划7 TTQR8.3-04 设计任务书8 TTQR8.3-05APQP 小组成员及职责技能表9 TTQR8.3-06 初始材料清单10 TTQR8.3-07APQP 计划阶段评审报告11 TTQR8.3-08 产品设计开发输入评审12 TTQR8.3-09 DFMEA13 TTQR8.3-10 产品特殊特性清单14 TTQR8.3-11 产品标准规范15 TTQR8.3-12 总成图、零件图、装配图16 TTQR8.3-13 设计和开发评审17 TTQR8.3-14 产品保证计划18 TTQR8.3-15 设计验证计划19 TTQR8.3-16 初始过程流程图20 TTQR8.3-17 样件控制计划21 TTQR8.3-18 样品验证报告22 TTQR8.3-19 新设备工装检测设备检查表及开发计划进度表23 TTQR8.3-20 产品安全防护表24 TTQR8.3-21 产品材料用量规格表(BOM)25 TTQR8.3-22 工程规范审查确认26 TTQR8.3-23 产品防错一览表27 TTQR8.3-24 可制造性和装配性设计28 TTQR8.3-25 模具配置申请表29 TTQR8.3-26 模具设计任务书30 TTQR8.3-27 模具制造报价单31 TTQR8.3-28 模具供方评定表32 TTQR8.3-29 模具加工合同33 TTQR8.3-30 模具跟踪评审验收记录34 TTQR8.3-31 设计和开发验证记录35 TTQR8.3-32 小组可行性承诺36 TTQR8.3-33 产品设计和开发输出评审XXXXXXX 有限公司 APQP 全套表单序号编号名称37 TTQR8.3-34 APQP 产品设计阶段评审报告38 TTQR8.3-35 产品/过程质量体系评审39 TTQR8.3-36 过程设计和开发输入评审40 TTQR8.3-37 产品特性重要度分级表41 TTQR8.3-38 产品和过程特殊特性清单42 TTQR8.3-39 特性矩阵图43 TTQR8.3-40 过程流程图44 TTQR8.3-41 车间平面定置管理图及检查表45 TTQR8.3-42 PFMEA 表46 TTQR8.3-43 试生产控制计划47 TTQR8.3-44 生产设备清单48 TTQR8.3-45 检测设备清单49 TTQR8.3-46 工艺规范及评审报告50 TTQR8.3-47 过程作业指导书51 TTQR8.3-48 测量系统分析计划52 TTQR8.3-49 初始过程能力研究计划53 TTQR8.3-50 包装作业指导书(包装规范)54 TTQR8.3-51 OTS 样件全尺寸报告55 TTQR8.3-52 OTS 样件材质试验结果56 TTQR8.3-53 OTS 样件性能试验结果57 TTQR8.3-54 过程设计开发输出评审58 TTQR8.3-55 APQP 设计阶段评审报告59 TTQR8.3-56 试生产计划60 TTQR8.3-57 试生产准备检查表(确认设备、工装、人员)61 TTQR8.3-58 试过程工艺参数检测记录62 TTQR8.3-59 试生产验证测试报告63 TTQR8.3-60 试生产总结报告64 TTQR8.3-61 节拍产能分析报告65 TTQR8.3-62 初始过程能力研究报告66 TTQR8.3-63 生产控制计划67 TTQR8.3-64 设计开发确认表68 TTQR8.3-65 零件提交保证书69 TTQR8.3-66 产品质量策划总结和认定70 TTQR8.3-67 APQP 试生产阶段评审报告71 TTQR8.3-68 工程变更申请单72 TTQR8.3-69 工程变更通知单73 TTQR8.3-70 嵌入式软件开发评估表XXXXXXX 有限公司 APQP 全套表单嵌入式软件开发评估表项目名称:一、推进流程应用工作量TQR8.3-70NO.序号阶段1 项目准备2 系统配置3 流程调研4 设定流程5 模拟调试6 管理员培训7 用户培训8 系统启用工作内容现有系统配置情况检查系统相关模块的基本数据情况检查制定实施阶段计划,约定每个阶段的时长,准确划分各阶段时间节点预定培训实施期间培训日期安排建立相关组织结构, 建立相关角色调整全局配置项建立权限分配方案落实需要上线的流程列表,这些流程主要包括:党委发文流程、纪委发文流程、公司发文流程、部门发文流程(报告、函、请示、通知)、公司收文流程,以及:用印申请流程、出差申请流程、会议管理流程等培训流程图的标准画法收集流程图,交流流程信息、修改流程图、流程图定稿建立流程,谁提交,谁批准,谁执行建立流程表单,及相应说明, 建立流程处理签建立存档管理,配置相关归档目录建立权限管理对所有流程进行模拟测试,特别是各个重要公文流程,必须进行遍历测试根据模拟测试发现的情况,对流程设置进行检讨和调整对流程管理员进行培训,使其掌握流程异常情况处理、流程微调技巧根据项目实际整理培训资料落实培训人员、场地、时间安排三场用户培训,需用户积极配合协调建立起与系统运行相适应的管理规章制度发布正式启用系统的通知系统检查与实施补充问题收集、反馈、调整阶段评估验证9 项目收尾项目回顾、权限收回总评XXXXXXX 有限公司 APQP 全套表单二、新功能开发流程序号 1 2 3 4 5 67阶段工作内容需求调研、分析需求确认了解用户业务,获取用户对功能、性能等方面的需求用户方、开发方对需求进行审核确认这些功能包括:安全认证、电子印章、规章制度管理、业务整合总体设计系统初步设计总体设计评审详细设计详细设计评审用户方、开发方对总体设计审核确认对系统功能、操作界面、处理逻辑、数据库、代码体系等进行详细设计开发组对详细设计方案审核确认编写程序、单元测试系统管理(设置,备份还原)操作人员管理及权限管理编程、单元测试安全认证电子印章规章制度管理业务整合(初步)业务整合(深入)8集成测试系统集成测试、系统测试,编程与测试可以交叉进行到用户现场安装调试开发好的系 9 安装调试统,并与用户一起试走业务流程,对系统进行功能确认测试10系统初始化将系统初始化;准备业务基础数据并录入系统;11 用户培训对用户操作人员、系统管理人员进行详细培训12项目跟踪与总结系统 bug 控制,操作指导合计阶段评估验证XXXXXXX 有限公司 APQP 全套表单设计评审报告产品名称:研制单位:产品负责人:拟制日期:XXXXXXX 有限公司 APQP 全套表单设计评审申请表部门评审项目名称评审日期设计所 XXXxx 年 xx 月 xx 日产品研发工程师产品内部代号评审地点技术中心三楼会议室一、建议参加评审单位及人员设计所:模具中心:工艺技术部:技术管理部:品质中心:检测中心:企划部:车载事业部:营销中心:物流部:财务部:设备部:其它:二、申请评审内容三、室主任审批意见四、总工程师审批意见XXXXXXX 有限公司 APQP 全套表单提供评审的文件、资料清单序号1 2 3 4 5 6 7 8 9 10文件资料名称产品立项书新品开发计划产品设计任务书初始材料清单初始过程流程图初始特殊特性清单产品三维草图DFMEA 试验计划其它(如:顾客要求)编审人或资料来源营销中心企划部研发工程师研发工程师研发工程师研发工程师研发工程师研发工程师研发工程师备注评审意见汇总及问题解决措施一、评审意见汇总(请研发工程师根据评审意见表上所列各项建议和意见进行汇总,未列入的评审意见视为不采纳)==由于设计评审意见太过随意,此处对其进行汇总,未列入里头的意见视为不采纳XXXXXXX 有限公司 APQP 全套表单二、存在问题及解决措施一览表序号问题内容1 2 3 4 5 6 7 8 9 10 11 12 13 14 15 16措施建议要求完成追踪负责人日期结论XXXXXXX 有限公司 APQP 全套表单评审结果1、评审结论:2、研制单位意见:评审组组长:3、主管领导复审决定:主管:签字:年月日年月日年月日XXXXXXX 有限公司 APQP 全套表单评审组名单姓名职务/职称XXX 设计室主任高工XXX 工艺技术部经理高工XXX 模具副主任工程师单位设计所工艺技术部模具中心签名是否有评审意见是否√√√备注:未提交《设计评审意见表》视为“同意该产品的所有设计”XXXXXXX 有限公司 APQP 全套表单附件 1设计评审意见表评审项目名称产品内部代号序号存在问题描述评审日期措施建议评审者/单位:XXXXXXX 有限公司 APQP 全套表单产品开发项目立项书项目名称: (例如:XXXXX) 项目类别: (例如:汽车继电器)XXXXXXX 有限公司 APQP 全套表单项目来源及概况项目名称项目来源申请部门申请人承办部门承办人一、市场调研与分析、顾客输入(公司决策的会议纪要等文件或销售人员市场调查、出差报告可作为附件): 1. 开发背景(基于何种目的):2. 市场需求情况(产品的年预计需求量、主要针对怎样的客户或市场等):3. 特定的客户需求(希望的目标价格、开发进度等):4.市场竞争情况:5.竞争对手样品、样本、安全认证或专利等资料的提供(可作为附件)。