接插件电镀层变色原因及防变色措施(光亮剂的缺点)
电镀过程中镀层不良的描述、原因及对策

电镀过程中镀层不良的描述、原因及对策1、针孔。
针孔是由于镀件外表吸附着氢气,迟迟不开释。
使镀液无法亲润镀件外表,然后无法电析镀层。
跟着析氢点周围区域镀层厚度的添加,析氢点就构成了一个针孔。
特点是一个发亮的圆孔,有时还有一个向上的小尾巴"。
当镀液中短少湿润剂并且电流密度偏高时,容易构成针孔。
2、麻点。
麻点是由于受镀外表不洁净,有固体物质吸附,或许镀液中固体物质悬浮着,当在电场效果下到达工件外表后,吸附其上,而影响了电析,把这些固体物质嵌入在电镀层中,构成一个个小凸点(麻点)。
特点是上凸,没有发亮现象,没有固定形状。
总归是工件脏、镀液脏而构成。
3、气流条纹。
气流条纹是由于添加剂过量或阴极电流密度过高或络合剂过高而降低了阴极电流效率然后析氢量大。
假如当时镀液流动缓慢,阴极移动缓慢,氢气贴着工件外表上升的进程中影响了电析结晶的摆放,构成自下而上一条条气流条纹。
4、掩镀(露底)。
掩镀是由于是工件外表管脚部位的软性溢料没有除掉,无法在此处进行电析堆积镀层。
电镀后可见基材,故称露底(由于软溢料是半通明的或通明的树脂成份)。
5、镀层脆性。
在SMD电镀后切筋成形后,可见在管脚弯处有开裂现象。
当镍层与基体之间开裂,判定是镍层脆性。
当锡层与镍层之间开裂,判定是锡层脆性。
构成脆性的原因八成是添加剂,光亮剂过量,或许是镀液中无机、有机杂质太多构成。
6、气袋。
气袋的构成是由于工件的形状和积气条件而构成。
氢气积在"袋中"无法排到镀液液面。
氢气的存在阻挠了电析镀层。
使堆集氢气的部位无镀层。
在电镀时,只需留意工件的钩挂方向能够防止气袋现象。
如图示工件电镀时,当垂直于镀槽底钩挂时,不发生气袋。
当平行于槽底钩挂时,易发生气袋。
7、塑封黑体中心开"锡花”。
在黑体上有锡镀层,这是由于电子管在焊线时,金丝的向上抛物形太高,塑封时金丝显露在黑体外表,锡就镀在金丝上,像开了一朵花。
不是镀液问题。
8、"爬锡"。
电镀金层发黑的问题原因和解决方法

电镀金层发黑的问题原因和解决方法
由于各实际工厂的生产线,使用的设备、药水体系并不完全相同。
因此需要针对产品和实际情况进行针对性的分析和处理解决。
这里只是讲到三个一般常见的问题原因供大家参考。
1、电镀镍层的厚度控制。
说电镀金层的发黑问题,怎么会说到电镀镍层的厚度上了。
其实PCB电镀金层一般都很薄,反映在电镀金的表面问题有很多是由于电镀镍的表现不良而引起的。
一般电镀镍层偏薄会引起产品外观会有发白和发黑的现象。
因此这是工厂工程技术人员首选要检查的项目。
一般需要电镀到5UM左右的镍层厚度才足够。
2、电镀镍缸的药水状况
还是要说镍缸的事。
如果镍缸的药水长期得不到良好的保养,没有及时进行碳处理,那么电镀出来的镍层就会容易产生片状结晶,镀层的硬度增加、脆性增强。
严重的会产生发黑镀层的问题。
这是很多人容易忽略的控制重点。
也往往是产生问题的重要原因。
因此请认真检查工厂生产线的药水状况,进行比较分析,并且及时进行彻底的碳处理,从而恢复药水的活性和电镀溶液的干净。
3、金缸的控制
现在才说到金缸的控制。
一般如果只要保持良好的药水过滤和补充,金缸的受污染程度和稳定性比镍缸都会好一些。
但需要注意检查下面的几个方面是否良好:(1)金缸补充剂的添加是否足够和过量?(2)药水的PH值控制情况如何?(3)导电盐的情况如何?如果检查结果没有问题,再用AA机分析分析溶液里杂质的含量。
保证金缸的药水状态。
应该注意金缸过滤棉芯定期更换。
电镀加工出现问题的原因及解决办法
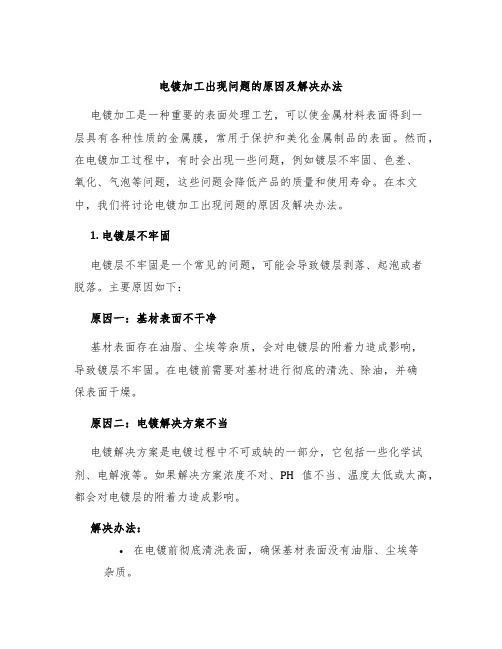
电镀加工出现问题的原因及解决办法电镀加工是一种重要的表面处理工艺,可以使金属材料表面得到一层具有各种性质的金属膜,常用于保护和美化金属制品的表面。
然而,在电镀加工过程中,有时会出现一些问题,例如镀层不牢固、色差、氧化、气泡等问题,这些问题会降低产品的质量和使用寿命。
在本文中,我们将讨论电镀加工出现问题的原因及解决办法。
1. 电镀层不牢固电镀层不牢固是一个常见的问题,可能会导致镀层剥落、起泡或者脱落。
主要原因如下:原因一:基材表面不干净基材表面存在油脂、尘埃等杂质,会对电镀层的附着力造成影响,导致镀层不牢固。
在电镀前需要对基材进行彻底的清洗、除油,并确保表面干燥。
原因二:电镀解决方案不当电镀解决方案是电镀过程中不可或缺的一部分,它包括一些化学试剂、电解液等。
如果解决方案浓度不对、PH值不当、温度太低或太高,都会对电镀层的附着力造成影响。
解决办法:•在电镀前彻底清洗表面,确保基材表面没有油脂、尘埃等杂质。
•在电镀解决方案中,加入一些添加剂,例如促进剂、增容剂等,来增强电镀层的附着力。
2. 镀层色差在电镀过程中,有时会出现镀层色差的问题,主要原因如下:原因一:电解液浓度不均电解液浓度的不均匀会导致镀层颜色不均匀。
例如,电解液中某些添加剂如果浓度过高或者过低,都可能导致镀层颜色的不同。
原因二:镀层表面存在缺陷镀层表面存在气泡、孔洞等缺陷也会导致镀层颜色不均匀。
解决办法:•定期检查电解液浓度,确保其均匀。
•彻底清洗基材的表面,确保表面无污染和缺陷。
3. 氧化问题氧化是电镀过程中另一个常见的问题,可以影响镀层的附着力和外观。
主要原因如下:原因一:电解液中的氧化物电解液中含有氧化物,而这些氧化物经常与电解液中的金属离子发生反应,从而导致镀层表面氧化。
原因二:镀层表面缺氧缺乏足够的电解气体氧分子也会导致金属离子表面氧化。
解决办法:•检查电解液中氧化物的含量,并确定其是否应该加入或减少。
•向电解液中添加抗氧化剂。
常见电镀不良原因及对策[1]
![常见电镀不良原因及对策[1]](https://img.taocdn.com/s3/m/c2a12aa4dd3383c4bb4cd2cb.png)
常見電鍍不良原因及對策一鍍層品質不良的發生多半為電鍍條件,電鍍設備或電鍍藥水的異常,及人為疏忽所致.通常在現場發生不良時比較容易找出原因克服,但電鍍後經過一段時間才發生不良就比較棘手.然而日後與環境中的酸氣,氧氣,水分等接觸,加速氧化腐蝕作用也是必須注意的.以下將對電鍍不良的發生原因及改善的對策加以探討說明.1.表面粗糙:指不平整,不光亮的表面,通常成粗白狀(1)可能發生的原因: (2)改善對策:1.素材表面嚴重粗糙,鍍層無法覆蓋平整. 1.若為素材嚴重粗糙,立即停產並通知客戶.2.金屬傳動輪表面粗糙,且壓合過緊,以至於壓傷. 2.若傳動輪粗糙,可換備用品使用並檢查壓合緊度.3.電流密度稍微偏高,部分表面不亮粗糙(尚未燒焦) 3.計算電流密度是否操作過高,若是應降低電流4.浴溫過低,一般鍍鎳才會發生) 4.待清晰度回升再開機,或降低電流,並立即檢查溫控系統.5.PH值過高或過低,一般鍍鎳或鍍金(過低不會)皆會發生. 5.立即調整PH至標準範圍.6.前處理藥液腐蝕底材. 6.查核前處理藥劑,稀釋藥劑或更換藥劑2.沾附異物:指端子表面附著之污物.(1)可能發生的原因: (2)改善對策:1.水洗不乾淨或水質不良(如有微菌). 1.清洗水槽並更換新水.2.佔到收料系統之機械油污. 2.將有油污處做以遮蔽.3.素材帶有類似膠狀物,於前處理流程無法去除. 3.須先以溶劑浸泡處理.4.收料時落地沾到泥土污物. 4.避免落地,若已沾附泥土可用吹氣清潔,浸透量很多時,建議重新清洗一次.5.錫鉛結晶物沾附 5.立即去除結晶物.6刷鍍羊毛?纖維絲 6.更換羊毛?並檢查接觸壓力.7.紙帶溶解纖維絲. 7.清槽.8.皮帶脫落屑. 8.更換皮帶.3.密著性不良:指鍍層有剝落.起皮,起泡等現象.(1)可能發生的原因: (2).改善對策:1.前處理不良,如剝鎳. 1.加強前處理.2.陰極接觸不良放電,如剝鎳,鎳剝金,鎳剝錫鉛. 2.檢查陰極是否接觸不良,適時調整.3.鍍液受到嚴重污染. 3.更換藥水4.產速太慢,底層再次氧化,如鎳層在金槽氧化(或金還原),剝錫鉛. 4,電鍍前須再次活化.5.水洗不乾淨. 5.更換新水,必要時清洗水槽.6.素材氧化嚴重,如氧化斑,熱處理後氧化膜. 6.必須先做除銹及去氧化膜處理,一般使用化學拋光或電解拋光.7.停機化學置換反應造成. 7.必免停機或剪除不良品8,操作電壓太高,陰極導電頭及鍍件發熱,造成鍍層氧化. 8.降低操作電壓或檢查導線接觸狀況9,底層電鍍不良(如燒焦),造成下一層剝落. 9.改善底層電鍍品質.10.嚴重.燒焦所形成剝落10.參考NO12處理對策.4.露銅:可清楚看見銅色或黃黑色於低電流處(凹槽處)(1)可能發生原因: (2)改善對策:1.前處理不良,油脂,氧化物.異物尚未除去,鍍層無法析出. 1.加強前處理或降低產速2.操作電流密度太低,導致低電流區,鍍層無法析出. 2.重新計算電鍍條件.3鎳光澤劑過量,導致低電流區,鍍層無法析出 3.處理藥水,去除過多光澤劑或更新.4.嚴重刮傷造成露銅. 4.檢查電鍍流程,(查參考NO5)5.未鍍到. 5.調整電流位置.5刮傷:指水平線條狀,一般在錫鉛鍍層比較容易發生.(1)可能發生的原因: (2)改善對策:1.素材本身在沖壓時,及造成刮傷. 1.停止生產,待與客戶聯繫.2.被電鍍設備中的金屬製具刮傷,如陰極頭,烤箱定位器,導輪等. 2.檢查電鍍流程,適時調整設備和制具.3.被電鍍結晶物刮傷. 3.停止生產,立即去除結晶物.6.變形(刮歪):指端子形狀已經偏離原有尺寸或位置.(1)可能發生的原因: (2)改善對策:1.素材本身在沖壓時,或運輸時,即造成變形. 1.停止生產,待與客戶聯繫.2.被電鍍設備,制具刮歪(如吹氣.定位器,振蕩器,槽口,回轉輪) 2.檢查電鍍流程,適時調整設備和制具.3.盤子過小或捲繞不良,導致出入料時刮歪 3.停止生產,適時調整盤子4.傳動輪轉歪, 4.修正傳動輪或變更傳動方式.7壓傷:指不規則形狀之凹洞可能發生的原因:改善對策:1)本身在沖床加工時,已經壓傷,鍍層無法覆蓋平整2)傳動輪鬆動或故障不良,造成壓合時傷到1)停止生產,待與客戶聯2)檢查傳動機構,或更換備品8白霧:指鍍層表面卡一層雲霧狀,不光亮但平整可能發生的原因:1)前處理不良2)鍍液受污染3)錫鉛層愛到酸腐蝕,如停機時受到錫鉛液腐蝕4)錫鉛藥水溫度過高5)錫鉛電流密度過低6)光澤劑不足7)傳致力輪髒污8)錫鉛電久進,產生泡沫附著造成改善對策:1)加強前處理2)更換藥水並提純污染液3)避免停機,若無法避免時,剪除不良4)立即檢查溫控系統,並重新設定溫度5)提高電流密度6)補足不澤劑傳動輪7)清潔傳動輪8)立即去除泡沫9針孔:指成群、細小圓洞狀(似被鍾紮狀)可能發生的原因:改善對策:1.操作的電流密度太 1.降低電流密度2.電鍍溶液表面張力過大,濕潤劑不足。
电镀不良之原因与对策

電鍍不良之原因與對策鍍層品質不良的發生多半為電鍍條件、電鍍設備或電鍍藥水的異常.及人為疏忽所致。
通常在現場發生不良時比較容易找出原因克服.但電鍍後經過一段時間才發生不良就比較棘手.然而日後與環境中的酸氣、氧氣、水分等接觸.加速氧化腐蝕作用也是必須注意的。
以下對電鍍不良的發生原因及改善的對策加以探討說明。
鍍層檢驗在電鍍業界的鍍層檢驗.一般包括外觀檢查、膜厚測試、附著能力測試、抗腐蝕能力測試、抗老化能力測試等。
1.外觀檢查:一般廠家在檢查外觀比較多使用目視法.較嚴格則會使用4倍或10倍放大鏡檢查(在許多國際標準規範也是如此.如ASTM)。
建議作業人員先用目視法檢查.一旦看到有疑慮的外觀時.再使用放大鏡觀察。
而技術人員則建議必須以50~100倍來檢查(倍數越高.外觀瑕疵越多).甚至分析原因時還得借助200倍以上的顯微鏡。
在電鍍層的外觀判定標準.一般並無一定的規範.都需要由買賣雙方協議。
當然表面完全沒有瑕疵最好.但這是高難度.不過一般人們對色澤均勻這個定義比較能達成共識.因此匯整以下經常發生的一些外觀異常.供參考:(1)色澤不均.深淺色.異色(如變黑.發紅.發黃.白霧等)(2)光澤度不均勻.明亮度不一.暗淡粗糙(3)沾附異物(如水分.毛屑.土灰.油污.結晶物.纖維等)(4)不平滑.有凹洞.針孔.顆粒物等(5)壓傷.刮傷.磨痕.刮歪等各種變形現象及鍍件受損情形(6)電鍍位置不齊.不足.過多.過寬等(7)裸露底層金屬現象(8)有起泡.剝落.掉金屬屑等2.膜厚測試:鍍層膜厚測試方法有顯微鏡測試法、電解測試法、X 光螢光測試法、β射線測試法、渦流測試法、滴下測試法等。
其中以顯微鏡測試法最為正確.不過需要時間、設備、技術等支援.不適合檢驗用.一般用來做分析研究之用。
現在大部分都使用X光螢光測試法.因為準確度高.速度快(幾十秒)。
目前業界使用X-RAY 螢光膜厚儀的廠牌有德國的FISCHER、美國的CMI、日本的SEIKO.其測試原理與方法大同小異.但由於廠牌不同.多少會有少許誤差.只要使用標準片作好檢量線.作好定位工作.作好底材修正.即可將誤差降低到最小。
接插件电镀层变色原因及防变色措施(光亮剂的缺点)
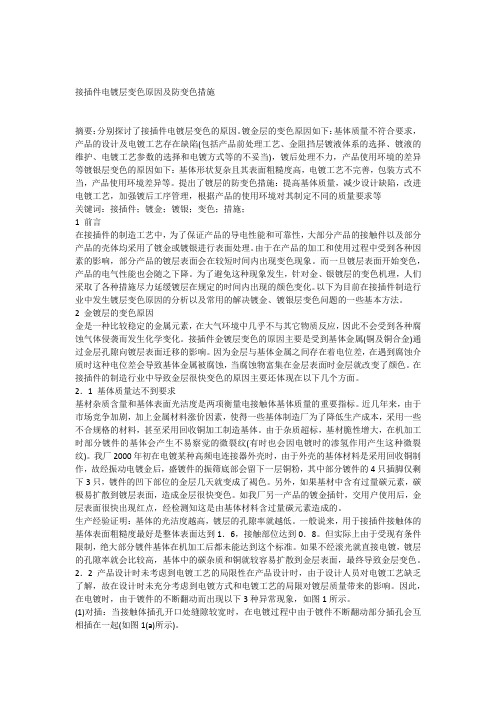
接插件电镀层变色原因及防变色措施摘要:分别探讨了接插件电镀层变色的原因。
镀金层的变色原因如下:基体质量不符合要求,产品的设计及电镀工艺存在缺陷(包括产品前处理工艺、金阻挡层镀液体系的选择、镀液的维护、电镀工艺参数的选择和电镀方式等的不妥当),镀后处理不力,产品使用环境的差异等镀银层变色的原因如下:基体形状复杂且其表面粗糙度高,电镀工艺不完善,包装方式不当,产品使用环境差异等。
提出了镀层的防变色措施:提高基体质量,减少设计缺陷,改进电镀工艺,加强镀后工序管理,根据产品的使用环境对其制定不同的质量要求等关键词:接插件;镀金;镀银;变色;措施;1 前言在接插件的制造工艺中,为了保证产品的导电性能和可靠性,大部分产品的接触件以及部分产品的壳体均采用了镀金或镀银进行表面处理。
由于在产品的加工和使用过程中受到各种因素的影响,部分产品的镀层表面会在较短时间内出现变色现象。
而一旦镀层表面开始变色,产品的电气性能也会随之下降。
为了避免这种现象发生,针对金、银镀层的变色机理,人们采取了各种措施尽力延缓镀层在规定的时间内出现的颜色变化。
以下为目前在接插件制造行业中发生镀层变色原因的分析以及常用的解决镀金、镀银层变色问题的一些基本方法。
2 金镀层的变色原因金是一种比较稳定的金属元素,在大气环境中几乎不与其它物质反应,因此不会受到各种腐蚀气体侵袭而发生化学变化。
接插件金镀层变色的原因主要是受到基体金属(铜及铜合金)通过金层孔隙向镀层表面迁移的影响。
因为金层与基体金属之间存在着电位差,在遇到腐蚀介质时这种电位差会导致基体金属被腐蚀,当腐蚀物富集在金层表面时金层就改变了颜色。
在接插件的制造行业中导致金层很快变色的原因主要还体现在以下几个方面。
2.1 基体质量达不到要求基材杂质含量和基体表面光洁度是两项衡量电接触体基体质量的重要指标。
近几年来,由于市场竞争加剧,加上金属材料涨价因素,使得一些基体制造厂为了降低生产成本,采用一些不合规格的材料,甚至采用回收铜加工制造基体。
镀层发黄的原因分析及处理方法
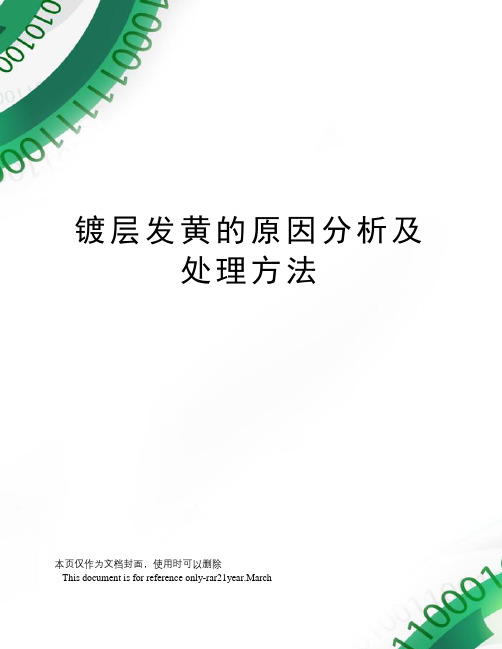
镀层发黄的原因分析及处理方法本页仅作为文档封面,使用时可以删除This document is for reference only-rar21year.March镀层发黄的原因分析及处理方法1.镀层中,金属之间结合会有空隙,当然这个用肉眼很难看得见,空隙之间会残留有镀槽中的药水和添加剂,而药水大多分为酸性和碱性,所电镀产品暴露在空气中,会随着气温的变化产生一些物理性质,热胀冷缩。
致使其内部残留药水和添加剂外吐,而所电镀附着上的锡层,极易被这些物质所腐蚀。
造成表面氧化,产生镀层发黄。
2.后处理不充分,电镀过程中,附着在产品表面上的药水,必须经过水洗之后,清除表面大部分药水,再以弱碱对其表面所残留少量药水进行中和处理,以确保其表面清洁,这样对以后的存贮有很大的帮助。
在中和的过程中,会对所电镀的锡层进行封孔处理,防止过多的药水进入电镀层中。
所以说,水洗越充分对电镀层越好。
采用超声波进行水洗其效果会更好。
3.产品的烘干,水也是一种氧化剂。
虽然反应缓慢,但是长时间的腐蚀也是会造成镀层发黄。
所以在后处理的过程中,要将水吹干,并在烘干的时候注意温度的控制。
4.导电不良,在电镀过程中,对导电的要求很严格,不可以产生间断性的导电效果,这样会给产品的表面造成不规则的电镀黄斑,导电不良也可以造成整个表面发黄,发黑的一种现象。
这种不良的情况可以从现场上看出来,只要针对其的导电进行这方面的改善便可以得到改善。
5.四价锡的附着,在电镀的过程中,槽中的药水会电解,产品表面产生高温,二价锡离子会部分被氧化成四价锡离子,四价锡离子不溶于水,会使电镀浴混浊,电镀产品在电镀的过程中,如果水洗不充分,其会沾染在产品上面,形成一种泥状的固态现象。
造成产品外观显黄色。
6.添加剂过量,添加剂在药水中含量偏高,这种情况在电镀的过程中不易看出来,它大大缩短了电镀产品的保质期。
添加剂都是一些有机物质,有机物质的化学性质极为不稳定。
7.镀浴中有锌杂质污染,这种可能性不会很大,有可能的话是某些素材上是锌的合金。
电镀不良之原因分析及防范措施精编WORD版
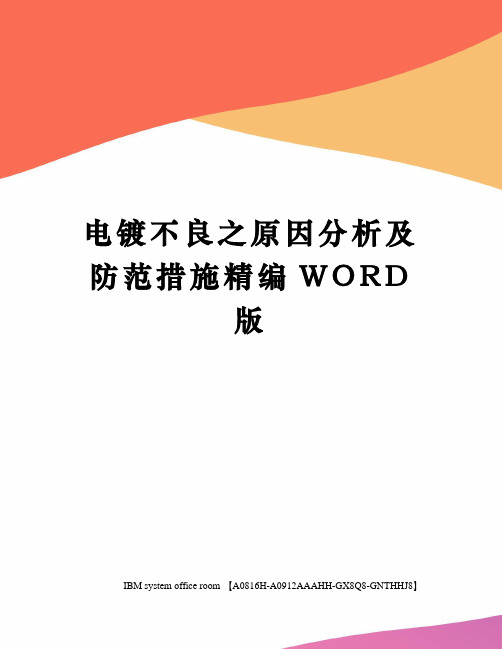
电镀不良之原因分析及防范措施:
不良状况
可能发生的原因
防范措施
备注
1.氧化、生锈
a.素材表面粗糙,孔粗细度较大,形成电位差,缩短保质期,产生氧化点;
b.端子表面压伤,电镀时形成低电流区,压伤抗氧化能力较低;
c.端子後处理不良,表面残留酸性物。
a.素材冲压成型时,须做到表面光滑,不能有压伤伤痕等;
(指端子形状已经偏离原有尺寸)
a.素材本身冲床或运输时,即造成形;
b.被电镀设备、治具刮歪(如吹氯、定位器、警报器、槽口);
c.盘子过小或卷绕不良,导致出入时伤到。
a.停止生产,退回给客户;
b.检查电镀流程,适时调整设备及治具;
c.停止生产,退回给客户或适时调整盘子。
11.重熔
(指镀层表面有如山丘平原状<似起泡,但密着良好>,只有锡铅镀层会发生)
d.镀镍不良:
1.电流布不均或电压过高;
2.镍槽主要成份及泽剂含量过高;
3.镍槽污染;
4.镍槽内线材位置未於槽中。
e.镍金不良;
1.金槽电压过高(24.5v);
2.金槽内线材位置未於槽中。
a.检查;
1.测485-E含後调整;
2.依操作手册检查;
3.检查後调整;
b.测PH,SP,GR值,不良更换;
1.检查导轮清洁,端子电刷接触情形,不良更换;
2.风压及风量不正常。
b.水洗不良
a.
1.检查後调整;
2.检查送风机滤纲及各风嘴,管路有无漏气,不良清洁调整;
b. 检查D4、D5槽之水质、水洗步骤,热水洗温度及水质,不良更换。
7.密着不良
(指镀层有剥落、脱皮、起泡等现象)
接插件镀金、镀银层变色原因及防变色措施

接插件镀金、镀银层变色原因及防变色措施摘要:分别探讨了接插件镀金和镀银层变色的原因。
镀金层的变色原因如下:基体质量不符合要求,产品的设计及电镀工艺存在缺陷(包括产品前处理工艺、金阻挡层镀液体系的选择、镀液的维护、电镀工艺参数的选择和电镀方式等的不妥当),镀后处理不力,产品使用环境的差异等镀银层变色的原因如下:基体形状复杂且其表面粗糙度高,电镀工艺不完善,包装方式不当,产品使用环境差异等。
提出了镀层的防变色措施:提高基体质量,减少设计缺陷,改进电镀工艺,加强镀后工序管理,根据产品的使用环境对其制定不同的质量要求等关键词:接插件;镀金;镀银;变色;措施;1 前言在接插件的制造工艺中,为了保证产品的导电性能和可靠性,大部分产品的接触件以及部分产品的壳体均采用了镀金或镀银进行表面处理。
由于在产品的加工和使用过程中受到各种因素的影响,部分产品的镀层表面会在较短时间内出现变色现象。
而一旦镀层表面开始变色,产品的电气性能也会随之下降。
为了避免这种现象发生,针对金、银镀层的变色机理,人们采取了各种措施尽力延缓镀层在规定的时间内出现的颜色变化。
以下为目前在接插件制造行业中发生镀层变色原因的分析以及常用的解决镀金、镀银层变色问题的一些基本方法。
2 金镀层的变色原因金是一种比较稳定的金属元素,在大气环境中几乎不与其它物质反应,因此不会受到各种腐蚀气体侵袭而发生化学变化。
接插件金镀层变色的原因主要是受到基体金属(铜及铜合金)通过金层孔隙向镀层表面迁移的影响。
因为金层与基体金属之间存在着电位差,在遇到腐蚀介质时这种电位差会导致基体金属被腐蚀,当腐蚀物富集在金层表面时金层就改变了颜色。
在接插件的制造行业中导致金层很快变色的原因主要还体现在以下几个方面。
2.1 基体质量达不到要求基材杂质含量和基体表面光洁度是两项衡量电接触体基体质量的重要指标。
近几年来,由于市场竞争加剧,加上金属材料涨价因素,使得一些基体制造厂为了降低生产成本,采用一些不合规格的材料,甚至采用回收铜加工制造基体。
镀金镀银件变色原因及对策

接插件镀金、镀银层变色原因及防变色措施镀金层的变色原因如下:基体质量不符合要求,产品的设计及电镀工艺存在缺陷(包括产品前处理工艺、金阻挡层镀液体系的选择、镀液的维护、电镀工艺参数的选择和电镀方式等的不妥当),镀后处理不力,产品使用环境的差异等镀银层变色的原因如下:基体形状复杂且其表面粗糙度高,电镀工艺不完善,包装方式不当,产品使用环境差异等。
1 前言在接插件的制造工艺中,为了保证产品的导电性能和可靠性,大部分产品的接触件以及部分产品的壳体均采用了镀金或镀银进行表面处理。
由于在产品的加工和使用过程中受到各种因素的影响,部分产品的镀层表面会在较短时间内出现变色现象。
而一旦镀层表面开始变色,产品的电气性能也会随之下降。
为了避免这种现象发生,针对金、银镀层的变色机理,人们采取了各种措施尽力延缓镀层在规定的时间内出现的颜色变化。
以下为目前在接插件制造行业中发生镀层变色原因的分析以及常用的解决镀金、镀银层变色问题的一些基本方法。
2 金镀层的变色原因金是一种比较稳定的金属元素,在大气环境中几乎不与其它物质反应,因此不会受到各种腐蚀气体侵袭而发生化学变化。
接插件金镀层变色的原因主要是受到基体金属(铜及铜合金)通过金层孔隙向镀层表面迁移的影响。
因为金层与基体金属之间存在着电位差,在遇到腐蚀介质时这种电位差会导致基体金属被腐蚀,当腐蚀物富集在金层表面时金层就改变了颜色。
在接插件的制造行业中导致金层很快变色的原因主要还体现在以下几个方面。
2.1 基体质量达不到要求基材杂质含量和基体表面光洁度是两项衡量电接触体基体质量的重要指标。
近几年来,由于市场竞争加剧,加上金属材料涨价因素,使得一些基体制造厂为了降低生产成本,采用一些不合规格的材料,甚至采用回收铜加工制造基体。
由于杂质超标,基材脆性增大,在机加工时部分镀件的基体会产生不易察觉的微裂纹(有时也会因电镀时的渗氢作用产生这种微裂纹)。
我厂2000年初在电镀某种高频电连接器外壳时,由于外壳的基体材料是采用回收铜制作,故经振动电镀金后,盛镀件的振筛底部会留下一层铜粉,其中部分镀件的4只插脚仅剩下3只,镀件的凹下部位的金层几天就变成了褐色。
电镀不良原因分析及解决方案

镀层呈青绿色
镀层呈灰黑色 镀层色泽发白
镀层色泽不均 镀层粗糙
成因及对策 (1)镀液中铜含量偏高。应在镀液中添加适量锌盐。 (2)阴极电流密度偏低。应适当提高。 (3)镀液温度偏高。应适当降低。 (4)镀液的pH值偏高。应使用碳酸氢钠调整镀液的pH值。 (5)镀液中游离氰化物含量偏低。应补充适量氰化物。 (1)镀液中二价锌离子浓度过高。应补充适量铜盐。 (2)镀液温度偏低。应适当提高。 (3)镀液中游离氰化物含量偏高。应补充适量铜盐。 (1)镀液中游离氰化物含量偏高。应补充适量铜盐。 (2)镀液中有砷等杂质污染。应在大电流密度下进行电解处理。 (1)电流密度偏高。应适当降低。 (2)镀液中二价锌离子浓度太高。应补充适量铜盐。 (3)镀液温度偏低。应适当提高。 (4)镀液中游离氰化物或氨水过多。应补充适量铜盐。 (1)镀液中游离氰化物含量偏低。应补充适量氰化物。 (2)镀液中氨水添加不足。应适当补充。 (1)镀液中氰化物含量偏低。应补充适量氰化物。 (2)阳极不清洁。应清洗阳极。 (3)镀液中杂质太多。应使用活性碳滤出杂质。
镀银产品的变色原因与防护

镀银产品的变色原因与防护凡铜镀银,磷铜镀银包括铁基材镀银之产品,如果处置不当的话,从电镀之日算起,存放大约50天以后就会出现表面变质之现象!所表现的特征和产生的原因以及预防措施如下:一、变质现象的三个特征:1、表面有暗黑点;2、局部变暗黑色;3、整体变暗黑色。
二、起因:镀层变质的起因十分复杂,涉及到销售、计划、采购、中转、IQC、组装、储存环境、储存方法、包装物选用、包装方法以及作业流程与管理。
1、电镀工艺不当!由于电镀工艺未达到规定之要求而引起的磷、铜被氧化呈暗黑点的现象!注意是黑点!不是变色!具体细节如下:a、镀银前表面清洗不干净;b、配方或操作工艺不规范;c、在烘烤过程中有杂物沾上;d、镀层太薄.2、储存环境不良!银遇空气会氧化!如果储存环境长期潮湿和空气中带酸碱性,所用之包装存在漏气;或者该类产品与其它物品混放在一起,那么肯定会造成镀银层氧化整体变色现象。
3、管控不当!采购、领用无计划,没做到按需采购,按产领用;中途检验、中转库、专用库多次拆包;半成品及成品以后的包装漏气与存放时间过长也会造成整体变色现象;4、装配时用手直接接触镀层会造成表面局部变暗黑色现象。
三、预防措施:1、计划部下达生产计划时应考虑50天以内的周转用量。
2、品质部(IQC)要建立一套镀银产品来料检测标准,要重点检测镀层厚度,颜色偏差,色牢度测试或耐盐雾测试等,事先要与供应商签订能确保镀银产品品质要求的相关测试项目,配足测试仪器,不定时地对来料进行测试检验。
不符标准的坚决不放行!3、镀银产品的储存仓库应分独立区域,不得与其它物料混放,并保证长期干燥且无带酸碱性的气源,要避免阳光直射!进出人员少且严格控制。
采用铁皮箱以后如其它管控没跟上也无法解决变色现象。
当然有了铁皮箱再在其它方面也管控好就更能确保不变色了!4、镀银产品的包装应用无毒的聚氯乙烯尼龙袋,必须热封封口!内装干燥剂!包装采用小量包装,一般以日产量为宜。
5、镀银产品按需且不拆包领用!领用做到先进先出!6、进入车间以后的镀银产品的管控应与仓库相同,工作场地必须确保干燥和避开带酸碱性气源,戴手套作业,尽量不做半成品,减少接触空气时间应采用流水作业直止成品为止,成品后的包装应用热封口!7、成品应在50天以内销售!做到先进先出!。
Why?电镀后的产品过段时间出现了变色和斑点

Why?电镀后的产品过段时间出现了变色和斑点展开全文平台上有朋友联系到我们“跪”求帮忙解决一个头疼的大问题:每年都时不时会发生,镀好好的产品放仓库过段时间出现了变色和斑点,有时候是我们也检查过并且客户也进行了检查了没问题的产品,出货到下一个客户手上就又有发现变色和斑点!其实不论是做卫浴,汽配,首饰,还是普通装饰件,很多人都会碰到这个问题,以我们乐将团队的现场经验,要解决这个问题要先从简单的入手,而不是动不动就去调整工艺,大处理镀液。
一.首先是解决包装材料,运输,储存方法1. 因为包装的楞纸板纸浆和包装材料工艺纸含硫化钠而导致的变色和斑点。
通常,大家都会将电镀后的产品放入托盘中,将产品置于顶部和底部的纸板隔板之间,并最后放入纸箱封存放入仓库。
这是一种常规包装操作,没什么特别的问题,但是,当添加某种因素时,会发生变色和斑点。
案例1:由于包装材料的长期储存而导致的腐蚀斑点部分变色的放大照片当你使用了含硫化钠的瓦楞纸板纸浆和包装材料工艺纸,含硫量为5至26 ppm。
这时我们的电镀产品,特别是没有喷光油保护的产品在纸板上密封数周或更长时间后,就会产生硫化气体,这种气体会使电镀表面被硫化而发生变色。
当然这种含硫气体的产生不仅来自纸板,它还来自皮革,胶水,塑料和粘合剂成型时附着的产品。
2.由于包装内部产生的冷凝水而导致的变色斑点案例2:由于冷凝和腐蚀而发生污渍变色斑点露水凝结点的放大图片在梅雨季,白天温度升至30°C,夜间温度降至接近20°C。
另外,夏天,在30℃以上运输,或保存。
当从炎热的高温环境下转移到有空调仓库中,在这样的凉爽环境下,包装内部会发生冷凝。
当温度从30℃的温度和80%的湿度降至20℃时,每1m 3空间会释放6.6g的水出来。
并且水会自然地粘附在电镀产品上。
这种冷凝水溶解表面上的隐形污垢,并融入空气中的污垢之后,它将被浓缩并干燥,这将最终成为斑点出现在产品的表面上。
另外,如果时间过久这种结露期间同时还在发生壳体1的情况,则会出现集中腐蚀而产生变色斑点。
电镀不良之原因分析及防范措施
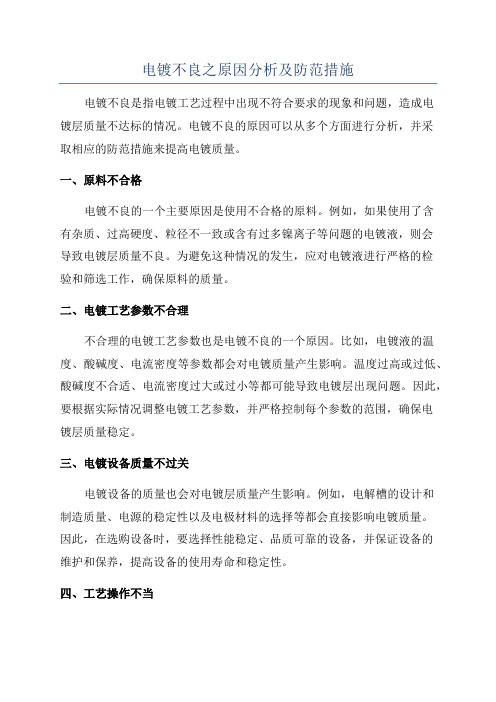
电镀不良之原因分析及防范措施电镀不良是指电镀工艺过程中出现不符合要求的现象和问题,造成电镀层质量不达标的情况。
电镀不良的原因可以从多个方面进行分析,并采取相应的防范措施来提高电镀质量。
一、原料不合格电镀不良的一个主要原因是使用不合格的原料。
例如,如果使用了含有杂质、过高硬度、粒径不一致或含有过多镍离子等问题的电镀液,则会导致电镀层质量不良。
为避免这种情况的发生,应对电镀液进行严格的检验和筛选工作,确保原料的质量。
二、电镀工艺参数不合理不合理的电镀工艺参数也是电镀不良的一个原因。
比如,电镀液的温度、酸碱度、电流密度等参数都会对电镀质量产生影响。
温度过高或过低、酸碱度不合适、电流密度过大或过小等都可能导致电镀层出现问题。
因此,要根据实际情况调整电镀工艺参数,并严格控制每个参数的范围,确保电镀层质量稳定。
三、电镀设备质量不过关电镀设备的质量也会对电镀层质量产生影响。
例如,电解槽的设计和制造质量、电源的稳定性以及电极材料的选择等都会直接影响电镀质量。
因此,在选购设备时,要选择性能稳定、品质可靠的设备,并保证设备的维护和保养,提高设备的使用寿命和稳定性。
四、工艺操作不当不正确的工艺操作也是电镀不良的一个常见原因。
例如,电镀工艺操作的速度太快或太慢,工件的浸泡时间控制不准确等都可能导致电镀层质量不良。
因此,操作人员在进行电镀工艺操作时要严格按照程序进行,并且进行必要的培训和技术指导,提高工艺操作的准确性和稳定性。
综上所述,电镀不良的原因可以从原料、工艺参数、设备质量和工艺操作等多个方面进行分析。
为了防范电镀不良的发生,可以采取以下措施:1.选用优质的原料,并进行严格检验和筛选;2.根据实际情况调整电镀工艺参数,并进行严格的控制;3.选购品质可靠的设备,并保证设备的维护和保养;4.进行工艺操作前进行必要的培训和技术指导,确保操作的准确性和稳定性;5.建立完善的质量控制体系,对电镀过程进行监控和检测,及时处理不良产品;6.加强与供应商的合作,建立长期稳定的合作关系,确保原料和设备质量的稳定性。
镀金颜色不正常原因详解
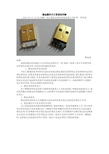
镀金颜色不正常原因详解
2016-04-12 12:50来源:内江洛伯尔材料科技有限公司作者:研发部
镀金连接器
接插件镀金层的颜色与正常的金层颜色不一致,或同一配套产品中不同零件的金层颜色出现差异,出现这种问题的原因是:
1、镀金原材料杂质影响
当加入镀液的化学材料带进的杂质超过镀金液的忍受程度后会很快影响金层的颜色和亮度.如果是有机杂质影响会出现金层发暗和发花的现象,郝尔槽试片检查发暗和发花位置不固定.若是金属杂质干扰则会造成电流密度有效范围变窄,郝尔槽试验显示是试片电流密度低端不亮或是高端镀不亮低端镀不上.反映到镀件上是镀层发红甚至发黑,其孔内的颜色变化较明显。
2、镀金电流密度过大
由于镀槽零件的总面积计算错误其数值大于实际表面积,使镀金电流量过大,或是采用振动电镀金时其振幅过小,这样槽中全部或部分镀件金镀层结晶粗糙,目视金层发红。
3、镀金液老化
镀金液使用时间太长则镀液中杂质过度积累必然会造成金层颜色不正常.
4、硬金镀层中合金含量发生变化
为了提高接插件的硬度和耐磨程度,接插件镀金一般采用镀硬金工艺.其中使用较多的是金钴合金和金镍合金.当镀液中的钴和镍的含量发生变化时会引起金镀层颜色改变.若是镀液中钴含量过高金层颜色会偏红;若是镀液中这镍含量过高金属颜色会变浅;若是镀液中这种变化过大而同一配套产品的不同零件又不在同一槽镀金时,这样就会出现提供给用户的同一批次产品金层颜色不相同的现象。
电镀件产生色差原因是怎样的

电镀件产生色差原因是怎样的电镀件是指通过电镀工艺,在金属基材表面形成一层金属膜的零部件。
它被广泛应用于汽车、电子、家电等领域中。
但在实际生产中,会出现电镀件产生色差的情况,为了更好地了解这个问题,本文将深入探讨其产生色差的原因。
电镀件色差的表现形式电镀件产生色差的表现形式有很多种,比如:•金属色不均匀:电镀件在不同部位出现的金属色存在明显差异;•颜色异常:电镀件的金属色出现异常,比如某一部位呈现棕色、黑色等;•金属色发蓝:电镀件金属色很浓,且呈现出一定的蓝色调;•发黑:电镀件表面出现小黑点,导致出现黑色的斑点。
以上几种表现形式都与电镀件产生色差有关。
电镀件产生色差的原因电解液成分不稳定电解液是电镀非常重要的一部分。
如果电解液成分不稳定,电镀件表面的镀层就会无法均匀地附着在基材上。
这样会导致金属色不均匀,出现色差。
电解液温度不稳定电解液温度不稳定也是产生电镀件色差的一个重要因素。
如果电解液的温度过高或者过低,均会导致电镀层产生质量问题。
因此,在镀电之前,需要对电解液的温度进行调整,以确保电镀的质量。
基材表面处理不当基材表面处理不当也是一个常见的问题。
如果基材表面没有做好处理,会导致沉积不均。
镀层在基材上的附着力不够,易发生剥离或者其他类似的问题。
电极质量差电极的质量也是影响电镀质量的一个因素。
如果使用的电极电气特性差,就会导致电流传递不均匀,进而导致出现色差的问题。
如何避免电镀件产生色差为了避免电镀件产生色差,我们需要采取一些预防措施:•电解液需稳定:针对电解液成分不稳定的问题,我们可以选择优质的电解液,并通过科学合理的管理方法来控制电解液的稳定性。
•严格控制电解液的温度:电解液的温度需要控制在适宜的范围内,应该根据实际情况进行调整。
•加强基材表面处理:对于基材表面处理不当的问题,我们需要注意加强基材的表面处理,保证基材表面的质量。
•使用优质的电极:使用优质的电极可以有效提高电镀质量,这样会减少出现色差的概率。
电镀产生问题原因及对策
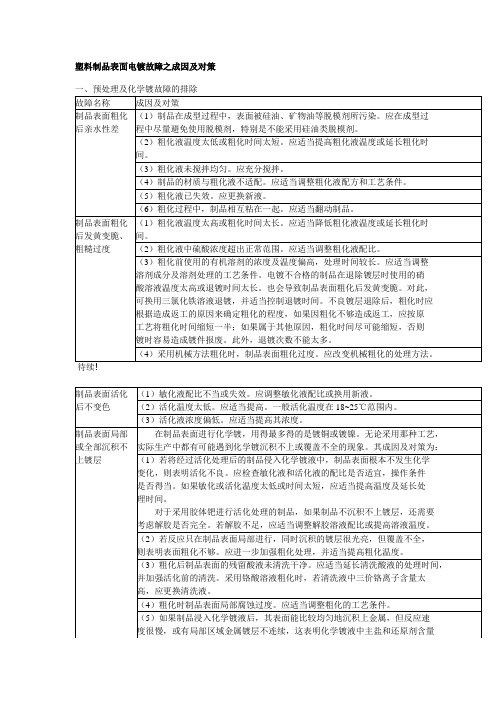
塑料制品表面电镀故障之成因及对策完二、电镀故障的排除的方法来检查镀层的热稳定性能。
在试验中选用得高低温度范围和循环次数,是根据制品的使用条件和环境确定的。
如汽车上使用的零件,在进行冷热循环试验时,先将镀件放入85℃的烘箱中保温1h,取出后在室温中放置15min,然后再放入40℃条件下1h,最后再在室温中放置15min。
如此循环4次,如果镀层表面状态和结合力均无变化则为合格所谓剥离试验,是在制品电镀的样片上切取1!2cm宽的镀层,橇起一头,用垂直于基体的力拉镀层,并测定剥离镀层时所需的力,其单位为kg/cm。
一般剥离在0.45kg/cm以上则为合格。
由于制品成型条件对镀层结合力影响的因素相当复杂,处理较为困难,尚未完待续完!完四、光亮硫酸盐铜常见故障的排除五、焦磷酸盐闪镀铜常见故障的排除完八、氰化镀铜合金故障的排除完完十一、ABS制品表面电镀故障的排除一、ABS制品表面酸性镀铜故障的排除复杂形状塑料大件电镀麻点产生的原因及对策董兴华摘要从工艺试验和实际生产方面找出了复杂形状塑料大件电镀产生麻点的主要原因,分析了产生麻点的各种因素,提出了减少麻点产生的办法和消除对策。
关键词塑料件电镀麻点对策新研制的电熨斗,有空心手柄、商标凸耳、大平面面积的侧身、散热窗、大穴内空、螺孔、凹槽、盲孔、通孔、非镀绝缘等部位,上壳为ABS塑料,形状复杂,受镀面积10 dm2。
常规塑料件电镀的工艺弊病很多,分析如下:1 麻点产生之因麻点的产生,主要来源于:(1)基材缺陷;(2)镀液;(3)工艺;(4)挂勾。
1.1 基材缺陷基材产生的麻点由模具精度和成型工艺及操作等造成,分布无规则。
轻微的缺陷孔,可通过电镀的填平将其减轻。
稍轻的缺陷孔,可机械抛磨后进行电镀。
严重的缺陷孔,视用户要求酌情处理。
1.2 镀液及其相关性(1)镀液性能差。
镀液成分含量改变,如酸铜中CuSO4过低,氯离子过高,光亮剂失调(S类光亮剂),表面活性剂过少。
(2)镀液污染。
常见电镀缺陷和原因分析

常见电镀缺陷和原因分析电镀缺陷是指在电镀过程中(包括准备工作和电镀工艺)出现的不良现象或问题。
下面我将介绍一些常见的电镀缺陷以及可能的原因分析。
1. 镀层不均匀:电镀层在部分区域厚度不均匀或出现斑点、斑纹等现象。
可能的原因包括:- 温度控制不准确:电镀液的温度不稳定、过高或过低,导致镀液在镀件表面的分布不均匀。
- 电镀液流动不均匀:电镀液在镀件上的流动速度不同,导致电流分布不均,进而影响镀层的均匀性。
- 镀液成分不稳定:电镀液中的添加剂、盐类等成分浓度不稳定,导致镀层的形成不均匀。
2. 黑斑或黄斑:镀层表面出现黑色或黄色的斑点。
可能的原因包括:- 杂质污染:电镀液中的杂质(如氧化物、铁离子等)进入镀液中,被还原到镀层表面形成斑点。
- 温度控制不当:电镀液的温度过高,导致镀层表面出现黄色或黑色反应物。
- 电流密度不均匀:镀件表面的电流密度不均匀,导致镀层表面出现黑斑或黄斑。
3. 镀层剥落:镀层与基材之间出现脱落现象。
可能的原因包括:- 镀液准备不当:电镀液的配方和浓度不正确,导致镀液附着力不足。
- 清洗不彻底:镀件在电镀前未进行彻底的清洗,导致表面存在杂质或脱脂剂,影响镀液与基材的结合。
- 电镀时间过短:电镀时间不足,镀层与基材之间的结合力不强,易剥离。
4. 镀层起泡:镀层表面出现气泡现象。
可能的原因包括:- 水分污染:电镀液中存在水分,经电解反应后生成氢气,导致镀液中产生气泡。
- 剧烈搅拌:电镀液在搅拌过程中引入大量气体,导致镀液中产生气泡。
- 电流密度不均匀:镀件表面的电流密度分布不均匀,导致一些区域出现过高的电流密度,进而引发气泡。
5. 镀层色差:镀层表面出现色差现象,包括颜色不均匀、色泽深浅不一等。
可能的原因包括:- 镀液浓度不均:电镀液中添加剂或盐类的浓度不均匀,导致镀层颜色不均匀。
- 电镀液PH值不稳定:电镀液中PH值变化较大,会影响镀层的色泽。
- 镀液渗染:电镀液渗透到基材中,与基材反应产生色差。
金手指镀金质量问题及措施

金手指镀金质量问题及措施1前言在接插件电镀中,由于接触对有着较高的电气性能要求,镀金工艺在接插件电镀中占有明显重要的地位.目前除部分的带料接插件采用选择性电镀金工艺外,其余大量的针孔散件的孔内镀金仍采用滚镀和振动镀来进行.近几年,接插件体积发展到越来越小型化,其针孔散件的孔内镀金质量问题日趋突出,用户对金层的质量要求也越来越高,一些用户对金层的外观质量甚至达到了十分挑剔的程度.为了保证接插件镀金层质量结合力这几类常见质量问题总是提高接插件镀金质量的关键.下面就这些质量问题产生的原因进行逐一分板提供大家探讨.2镀金层质量问题的产生原因2.1金层颜色不正常接插件镀金层的颜色与正常的金层颜色不一致,或同一配套产品中不同零件的金层颜色出现差异,出现这种问题的原因是:2.1.1镀金原材料杂质影响当加入镀液的化学材料带进的杂质超过镀金液的忍受程度后会很快影响金层的颜色和亮度.如果是有机杂质影响会出现金层发暗和发花的现象,郝尔槽试片检查发暗和发花位置不固定.若是金属杂质干扰则会造成电流密度有效范围变窄,郝尔槽试验显示是试片电流密度低端不亮或是高端镀不亮低端镀不上.反映到镀件上是镀层发红甚至发黑,其孔内的颜色变化较明显.2.1.1镀金电流密度过大由于镀槽零件的总面积计算错误其数值大于实际表面积,使镀金电流量过大,或是采用振动电镀金时其振幅过小,这样槽中全部或部分镀件金镀层结晶粗糙,目视金层发红.2.1.3镀金液老化镀金液使用时间太长则镀液中杂质过度积累必然会造成金层颜色不正常.2.1.4硬金镀层中合金含量发生变化为了提高接插件的硬度和耐磨程度,接插件镀金一般采用镀硬金工艺.其中使用较多的是金钴合金和金镍合金.当镀液中的钴和镍的含量发生变化时会引起金镀层颜色改变.若是镀液中钴含量过高金层颜色会偏红;若是镀液中这镍含量过高金属颜色会变浅;若是镀液中这种变化过大而同一配套产品的不同零件又不在同一槽镀金时,这样就会出现提供给用户的同一批次产品金层颜色不相同的现象.2.2孔内镀不上金接插件的插针或插孔镀金工序完成后镀件外表面厚度达到或超过规定厚度值时,其焊线孔或插孔的内孔镀层很薄甚至无金层.2.2.1镀金时镀件互相对插为了保证接插件的插孔在插孔在插拔使用时具有一定弹性,在产品设计时大多数种类的插孔都有是在口部设计一道劈槽.在电镀过程中镀件不断翻动部份插孔就在开口处互相插在一起致使对插部位电力线互相屏敝造成孔内电镀困难.2.2.2镀金时镀件首尾相接有些种类的接插件其插针在设计时其针杆的外径尺寸略小于焊线孔的孔径尺寸,在电镀过程中部份插针就会形成首尾相接造成焊线孔内镀不进金.(见图示)以上两种现象在振动镀金时较容易发生.2.2.3盲孔部位浓度较大超过电镀工艺深镀能力由于在插孔的劈槽底部距孔底还有一段距离,这段距离客观上形成了一段盲孔.同样在插针和插孔的焊线孔里也有这样一段盲孔,它是提供导线焊接时的导向作用.当这些孔的孔径较小(往往低于1毫米甚至低于0.5毫米)而盲孔浓度超过孔径时镀液很难流进孔内,流进孔内的镀液又很难流出,所以孔内的金层质量很难保证.2.2.4镀金阳极面积太小当接插件体积较小时相对来说单槽镀件的总表面积就较大,这样在镀小型针孔件时如果单槽镀件较多.原来的阳极面积就显得不够.特别是当铂钛网使用时间过长铂损耗太多时,阳极的有效面积就会减少,这样就会影响镀金的深镀能力,镀件的孔内就会镀不进.2.3镀层结合力差在镀后检验接插件的镀层结合力时,有时会遇到部份插针的针端前部在折弯时或针孔件的焊线孔在压扁时镀层有起皮现象,有时在高温(2001小时)检测试验发现金层有极细小的鼓泡现象发生.2.3.1镀前处理不彻底对于小型针孔件来说,如果在机加工序完毕后不能立即采用三氯乙烯超声波除油清洗,那么接下来的常规镀前处理很难将孔内干涸的油污除净,这样孔内的镀层结合力就会大大降低.2.3.2基体镀前活化不完全在接插件基体材料中大量使用各类铜合金,这些铜合金中的铁铅锡铍等微量金属在一般的活化液中很难使其活化,如果不采用对应的酸将其活化,在进行电镀时,这些金属的氧化物跟镀层很难结合,于是就造成了镀层高温起泡的现象.2.2.3镀液浓度偏低在使用氨磺酸镍镀液镀镍时,当镍含量低于工艺范围时,小型针孔件的孔内镀层质量要受到影响.如果是预镀液的金含量过低,那么在镀金时孔内就有可能镀不上金,当镀件进入加厚金镀液时,孔内五金层的镀件孔内的镍层已钝化其结果是孔内的金层结合力自然就差.2.3.4细长状插针电镀时未降低电流密度在镀细长形状插针时,如果按通常使用遥电流密度电镀时,针尖部位的镀层会比针杆上厚许多,在放大镜下观察针尖有时会旦火柴头形状.(见图3)其头颈部的镀层即插针前端顶部靠后一点部位的金镀层检验结合力就不合格.这种现象在振动镀金时易出现.2.3.5振动镀金振频调整不正确采用振动电镀镀接插件时,如果在镀镍时振动频率调整不正确镀件跳动太快,易开成双层镍对镀层结合力影响甚大.3解决质量问题的方法3.1从产品设计开始消除影响电镀质量的因素首先在接插件进行产品设计时就要考虑到对电镀工序可能带来的影响,尽量避免因设计考虑不当给电镀质量留下隐患.3.1.1对一字形开口的插孔,采用在劈槽时先从口部边缘向口部中央斜向45度角开口,然后再顺着口部中央垂直向下进行.若是十字形开口的插孔,可以先将插孔收口使劈槽口部的链宽度小于插孔壁厚度,这样就可减少和避免镀金时产生插孔互相对插现象.(见图4)3.1.2设计时插针的针杆尺寸应始终略大于焊线孔孔尺寸或是延长焊线孔铣弧长度避免电镀时插针首尾相接.3.1.3在盲孔部位的底部设计一横向通孔使电镀时镀液能在孔内顺利出入.(见图5)3.2采用科学的电镀工艺管理方法3.2.1加强对电镀质量控制,特别是对金盐的质量要重点关注.对使用的每一批金盐除了必须经过常规的理化检验外均要取样作郝尔槽试验,试验认定合格后再用于镀槽.郝尔槽试验方法:取样品中金盐十二克,加入柠檬酸钾100克配制成1升镀液,加温至50℃调整PH5.4-5.8作]郝尔槽试验.正常结果为250毫升郝尔槽试验样片在0.SA电流电镀1分钟时光亮范围应在靠电流密度低端二分之一以上面积,整块试片上应是均匀的金黄色,否则应判定金盐不能正常使用.3.2.2对每槽镀件的数量、表面积、总电流量在电镀前进行计算并作好记录,以便在出现质量问题后查找原因。
- 1、下载文档前请自行甄别文档内容的完整性,平台不提供额外的编辑、内容补充、找答案等附加服务。
- 2、"仅部分预览"的文档,不可在线预览部分如存在完整性等问题,可反馈申请退款(可完整预览的文档不适用该条件!)。
- 3、如文档侵犯您的权益,请联系客服反馈,我们会尽快为您处理(人工客服工作时间:9:00-18:30)。
接插件电镀层变色原因及防变色措施摘要:分别探讨了接插件电镀层变色的原因。
镀金层的变色原因如下:基体质量不符合要求,产品的设计及电镀工艺存在缺陷(包括产品前处理工艺、金阻挡层镀液体系的选择、镀液的维护、电镀工艺参数的选择和电镀方式等的不妥当),镀后处理不力,产品使用环境的差异等镀银层变色的原因如下:基体形状复杂且其表面粗糙度高,电镀工艺不完善,包装方式不当,产品使用环境差异等。
提出了镀层的防变色措施:提高基体质量,减少设计缺陷,改进电镀工艺,加强镀后工序管理,根据产品的使用环境对其制定不同的质量要求等关键词:接插件;镀金;镀银;变色;措施;1 前言在接插件的制造工艺中,为了保证产品的导电性能和可靠性,大部分产品的接触件以及部分产品的壳体均采用了镀金或镀银进行表面处理。
由于在产品的加工和使用过程中受到各种因素的影响,部分产品的镀层表面会在较短时间内出现变色现象。
而一旦镀层表面开始变色,产品的电气性能也会随之下降。
为了避免这种现象发生,针对金、银镀层的变色机理,人们采取了各种措施尽力延缓镀层在规定的时间内出现的颜色变化。
以下为目前在接插件制造行业中发生镀层变色原因的分析以及常用的解决镀金、镀银层变色问题的一些基本方法。
2 金镀层的变色原因金是一种比较稳定的金属元素,在大气环境中几乎不与其它物质反应,因此不会受到各种腐蚀气体侵袭而发生化学变化。
接插件金镀层变色的原因主要是受到基体金属(铜及铜合金)通过金层孔隙向镀层表面迁移的影响。
因为金层与基体金属之间存在着电位差,在遇到腐蚀介质时这种电位差会导致基体金属被腐蚀,当腐蚀物富集在金层表面时金层就改变了颜色。
在接插件的制造行业中导致金层很快变色的原因主要还体现在以下几个方面。
2.1 基体质量达不到要求基材杂质含量和基体表面光洁度是两项衡量电接触体基体质量的重要指标。
近几年来,由于市场竞争加剧,加上金属材料涨价因素,使得一些基体制造厂为了降低生产成本,采用一些不合规格的材料,甚至采用回收铜加工制造基体。
由于杂质超标,基材脆性增大,在机加工时部分镀件的基体会产生不易察觉的微裂纹(有时也会因电镀时的渗氢作用产生这种微裂纹)。
我厂2000年初在电镀某种高频电连接器外壳时,由于外壳的基体材料是采用回收铜制作,故经振动电镀金后,盛镀件的振筛底部会留下一层铜粉,其中部分镀件的4只插脚仅剩下3只,镀件的凹下部位的金层几天就变成了褐色。
另外,如果基材中含有过量碳元素,碳极易扩散到镀层表面,造成金层很快变色。
如我厂另一产品的镀金插针,交用户使用后,金层表面很快出现红点,经检测知这是由基体材料含过量碳元素造成的。
生产经验证明:基体的光洁度越高,镀层的孔隙率就越低。
一般说来,用于接插件接触体的基体表面粗糙度最好是整体表面达到1.6,接触部位达到0.8。
但实际上由于受现有条件限制,绝大部分镀件基体在机加工后都未能达到这个标准。
如果不经滚光就直接电镀,镀层的孔隙率就会比较高,基体中的碳杂质和铜就较容易扩散到金层表面,最终导致金层变色。
2.2 产品设计时未考虑到电镀工艺的局限性在产品设计时,由于设计人员对电镀工艺缺乏了解,故在设计时未充分考虑到电镀方式和电镀工艺的局限对镀层质量带来的影响。
因此,在电镀时,由于镀件的不断翻动而出现以下3种异常现象,如图1所示。
(1)对插:当接触体插孔开口处缝隙较宽时,在电镀过程中由于镀件不断翻动部分插孔会互相插在一起(如图1(a)所示)。
(2)首尾相接:插针在设计时针杆的外径尺寸略小于焊线孔的孔径尺寸,在电镀过程中部份插针就会形成首尾相接,如图1(b)所示。
(3)孔内镀不上:当镀件孔径小于1 mm时,如果孔底未设计工艺通孔,电镀时由于气泡堵塞住.,D-fL,孔内镀上金十分困难。
以上几种现象都会给镀层带来变色的隐患。
2.3 电镀工艺缺陷对镀层质量的影响由于电镀工艺不完善造成金层变色的因素主要有以下方面。
2.3.1 镀前处理工艺不当对于黄铜件来说,不正确的镀前处理会使基体质量明显下降,最终影响到镀层质量。
最常见的是因酸洗过量造成基体粗糙,化学除油时间过长造成基体严重脱锌等。
2.3.2 金阻挡层镀液体系选择不正确作为接触体金镀层的阻挡层,应符合镀层致密度高、应力低和不向金层表面扩散等条件。
若选择带光亮剂的镍镀层作为金的阻挡层,在产品使用过程中,会因为镍层的脆性而产生微裂纹从而丧失阻挡作用。
同时夹杂在镀层中的光亮剂也是镀层变色的主要因素。
如果是以铜或者银作为金层的阻挡层,那么由于铜或银的快速向上扩散,金层也将很快改变颜色。
我厂在上个世纪80年代中期,曾经采用锡镍合金镀层作为接触体金镀层的阻挡层,由于镀层中锡的扩散作用,使得产品在半年的时问内其金层表面就由金黄色变为浅黄色,最终完全变成银白色。
2.3.3 镀液维护工作较差在接插件的电镀过程中,如果镀液维护工作没做好,将会给镀层质量带来灾难性的后果。
当不小心将金属杂质带人镀液,那么造成的结果是镀液分散能力下降,电流效率降低,甚至出现金镀层发花、发黑的现象。
如果是采用振动电镀设备镀金,而被选用的振筛口部内边缘没有加焊塑料焊条(新买出厂的振筛壁是光滑的,须自己加焊条),在振幅过大时在离心力作用下会有镀件翻出振筛掉人镀槽。
同时如果在镀细长插针时选用了壁上带有滤网的振筛,一旦有插针刺人滤网孔,镀件马上会拥挤成一堆,使部分镀件掉落到镀槽中。
这些落人镀槽中的镀件若未及时捞出,会在镀液的作用下慢慢溶解使镀液受到污染。
值得注意的是:如果电镀时是使用换相脉冲电镀电源,若反向电流的大小或反向时间的长短设定不正确,同样会有因镀件溶解而污染镀液的现象发生。
2.3.4 电镀工艺参数不正确在镀阻挡层时,如果施镀的电流密度过低(镀件总面积计算错误),在规定的时间内镀层厚度就达不到要求。
同样,在镀镍时若镀液pH调得过低或低于工艺下限,镍层会沉积得太慢而达不到规定的厚度,其阻挡作用也会下降。
2.3.5 电镀方式不妥对一些单件体形较长或单件体积较重的镀件,若采用的电镀方式不正确,将会使镀件的镀层均匀性变差,或因镀件互相撞击而直接影响到镀层的质量,最终造成金层局部很快变色。
正确的做法是:将这些镀件分别采用滚镀、挂镀和振动镀作比较,若是挂镀效果好,就不要强调提高生产效率勉强采用滚镀和振动镀。
实践证明:不能采用滚镀和振动镀的镀件若勉强采用滚镀和振动镀,那么容易造成镀件缺损或互相缠绕。
2.4 镀后工序对合格镀层的影响。
首先,镀件镀后清洗不净是金层变色的主要因素之一:其次,镀后切边、铆装、印字和封胶后的高温烘烤以及装配工人的手汗污染都将会使金层变色。
2.5 产品使用环境差异镀金元件在高温、高湿环境使用时,基底金属的扩散作用会进行得很快,金层变色的时间会大大提前前几年我厂同一种产品在北方地用户使用时,一年以上金层都不会变色,而在交付深圳用户使用时,平时3个月、夏季一个月就有变色现象发生。
3 银镀层的变色原因银跟金的性质明显不同。
由于银的化学性质比较活泼,在大气环境中对含硫气体极为敏感,很容易与硫反应生成黑色硫化银。
在光的催化作用下,银的变色反应速度会加快。
其变色过程为:生成黄点一形成黄斑一黄斑变黑一整个镀层表面呈棕褐色。
在接插件的制造和使用过程中,以下几种因素会导致银层很快变色。
3.1 基体形状复杂或表面粗糙度较高当镀银件呈不规则的几何曲面或带有滚花和螺纹时,在滚花和螺纹部位或镀件台阶、转角处,这些部位极易粘附灰尘和水分。
在受到含硫气体侵袭时,这些部位的银层将很快变色。
同样,基体粗糙度高,镀层的致密度也就低,镀层还会受到基体金属杂质扩散的影响。
所以在同一环境,光洁度差的镀件银层变色速度就比光洁度高的镀件快。
3.2 电镀工艺不完善对于接触体中的黄铜件镀银,如果在镀银工序前未采用镀镍作阻挡层,银层会因基体中的金属杂质快速向表面渗透使银层很快变色。
另外,目前应用较多的光亮镀银工艺,其光亮剂多为含硫有机物。
当光亮剂质量变坏时,银层先天就存在变色的隐患。
同时,使用光亮镀银工艺会使银的电阻率增加。
目前在接插件制造行业,已有人指出:射频连接器的内外导体镀银时,采用加入光亮剂的镀银工艺,会对产品的导电性能和耐环境性产生较大影响。
如我厂在上个世纪80年代以前一直是采用无光亮剂氰化镀银,以镀后化学浸亮和滚光来提高银层表面光洁度。
后来采用光亮镀银工艺,在使用初期,就发现新的镀银件比老的镀银件变色快。
用户怀疑银层变色快是电镀工序偷工减料导致银层减薄造成的,其实是光亮剂的原因。
3.3 包装方式不妥在镀银件镀后包装时,若包装方式不妥也会引起银层较快变色。
我厂早先对镀银件采用牛皮纸包装,由于纸易吸潮,改为塑料袋包装热压封口。
但是当装配序拆开包装后,发现靠近封口处的部分镀件银层已开始变色,后来采用蜡纸包装放干燥器储存,镀银件变色现象立即减少。
3.4 产品使用环境差异接插件镀银由于使用环境不同,变色影响程度相差较大。
据调查,在我国镀银层的变色速度夏天南方比北方快,其原因是高温环境加快了变色反应速度;而在冬天镀银层的变色速度却是北方比南方快,其原因是冬天北方地区使用烧煤集中供暖,空气中含硫量较大所引起4 镀层防变色措施4.1 提高基体质量提高基体质量是解决镀层变色的基础工作。
特别是防止金层变色,抓好基体质量往往能收到事半功倍的效果。
台湾接插件行业中宏海公司的经验表明,使用进口铜带(光洁度高、杂质含量少),提高模具质量(减少压痕和毛刺)能使接触体镀层抗变色能力大大提高。
在我国一些制造出口家具的工厂,其高档家具最早采用镀仿金工艺,后来发展成采用在基材上电镀多层镍后罩薄金工艺,现已发展为采用不锈钢制作基材经抛光后闪镀金工艺,并解决了镀金变色问题。
由此可见要解决金层变色问题,提高基体质量是关键。
4.2 减少设计缺陷在产品设计定型前认真进行工艺评审。
对于牵涉到镀金和镀银的产品在通过电镀工艺试验,认定无设计缺陷后才允许批量生产。
4.3 改进电镀工艺对于基体材料为黄铜件的镀金镀银产品,在电镀镍阻挡层前增加镀铜打底工艺,这样对减少镀层孔隙、增强镀层防变色效果特别明显。
在电镀过程中,要十分重视镀金中间层工艺的改进,要努力寻求最佳的镀金中间层。
目前,在接插件电镀工艺中,采用氨磺酸镍体系镀镍是比较合理的镀金中间层工艺,但是镍层厚度一定要保证。
采用震动电镀时,镍层厚度下限为3 m;若采用滚镀或挂镀,镍层厚度下限还应适当提高。
对于带料选择性电镀,由于受生产场的限制不可能将镀镍槽作得较长,同时为了兼顾其它工序处理时间,也不可能将走带速度控制得太慢。
在镍层厚度不能充分保障时,町采用镀金后浸防变色剂进行封孔处理。
对于镀银件,目前防变色效果较好的方法是:镀银后化学钝化或电化学钝化然后再浸防银变色剂。
这里需注意的是,选择浸防银变色剂要预先考虑对接触体其它性能指标例如接触电阻和插拔力等指标的影响。