乳化液配比要求及水质规定
乳化液化学检测与评价

乳化液化学检测与评价乳化液化学检测:浓度PH值电导率皂化值铁粉含量灰分含量氯离子含量酸值ESI( 稳定指数)细菌/真菌乳化液各项指标测试要求及参考值:1.浓度:控制范围(薄板:2.5 ﹪—3.5﹪)(厚板:1.5 ﹪—2.5﹪)适当的乳化液浓度,是保证工艺润滑及板面清洗基础。
浓度过高:可能导致轧制时过润滑,引起打滑,增大轧后板面的残油量,降低了板面的清洁度;浓度过低:可能导致轧制时欠润滑,引起热划伤,增大了铁粉的磨损。
浓度控制方法:按照油、水的比例同时补充。
2、PH值一般乳化液PH值在5.0– 8.0之间,波动范围0.2 – 0.5。
当PH值低于4.5或PH值高于9.0时有异常情况发生。
测量PH值作用:1)乳化液颗粒度分布同乳化液酸碱度有十分密切的关系。
通常,在PH值在5 – 8之间范围时,乳化液颗粒度是不变的。
2)当PH值低于4.5,颗粒度趋于增大,导致乳化液不稳定。
当PH 值在8 – 9之间,乳化液颗粒度趋于减小,导致冷轧过程中缺乏润滑性。
3)当PH值大于9.5以上,可能出现的相关现象,乳化液中脂/酯的颗粒度将趋于变小,而乳化液中碱性物质颗粒度趋于增大。
•当轧制乳化液PH值突然改变,伴随电导率改变,可能是被酸、盐、或碱性物质污染。
酸污染通常是由酸洗线带来。
盐污染可能来源:酸洗线,配液水质。
碱污染一般由于使用过清洗剂。
•细菌会引起PH值下降,而电导率不发生改变。
特别是停机不使用乳化液时经常发生。
受到细菌侵害的乳化液,会散发出难闻的气味来。
3、电导率•轧制乳化液电导率分布与铁有直接关系。
高铁含量容易和H+、OH-、 Cl-、 SO42-结合,同时较少同Ca2+、 Mg 2+、有机酸结合。
•在一般条件下,乳化液电导率每天最多增加20us/天,每天高于这个值被认为异常。
•控制范围<300us/cm电导率变化产生原因:1)电导率缓慢增加,PH值保持不变。
原因:配液水盐含量高。
2)电导率增加,PH值突然下跌原因:酸洗漂洗水污染。
乳化液管理规范样本

工作行为规范系列乳化液管理规范(标准、完整、实用、可修改)编号:FS-QG-80250乳化液管理规范Emulsion Management Specifications说明:为规范化、制度化和统一化作业行为,使人员管理工作有章可循,提高工作效率和责任感、归属感,特此编写。
1、总则第一条为规范我矿乳化液使用管理,确保液压支架乳化液配制、配比符合要求,结合目前乳化液使用情况,制定本办法。
2、管理职责第二条使用单位负责本单位乳化液配制和浓度配比,泵站及泵箱、过滤及自动补液装置和液压支架及管路等液压系统设备材料的保管、使用、保养、维修管理,乳化用水、乳化液的取样检验使用管理。
第三条技术科负责乳化液配比浓度的日常检查工作,如不符合规定处以综采队集体5000元罚款,包机人300元罚款。
第四条综采队负责本单位和液压支架使用期间乳化液配制和浓度配比,泵站及泵箱、过滤及自动补液装置和液压支架及管路等液压系统设备材料的保管、使用、保养、维修管理,乳化用水、乳化液的取样检验使用管理。
第五条供应部门负责乳化液的采购,并对每月乳化液消耗进行考核,负责取样检验、验收保管、配送及其质量管理,按煤业公司润滑管理办法执行。
第六条委托的油品检验单位负责乳化液的化验分析,按煤业公司设备润滑管理办法执行。
第七条乳化液的生产厂家负责乳化液与支架密封的相融性试验,负责乳化用水、乳化液的应用化验和配比,并负责产品应用全过程中每月一次的乳化液取样化验分析,化验结果同时报供应科、机电科备案。
3、乳化液的使用管理第八条乳化液的存贮温度必须符合规定,低温存贮的使用前一周应备用到井下升温,使用加注前必须先检查乳化液是否变质。
第九条乳化液的选用必须根据不同密封材料、水质和环境条件。
第十条乳化液用水必须达到清水配液用水要求:水质外观无色、无异味,无悬浮物和无机械杂质。
第十一条乳化液配比浓度必须符合要求:一般要求配比浓度达到3%-5%,不同水质必须根据乳化液制造厂化验配比要求进行配比,并使用制造厂配备的专用或允许使用通用的糖量仪按其折光系数进行检测。
2016新编乳化油配比

乳化油配比线切割工作液由专用乳化油与自来水配制而成,有条件采用蒸馏水或磁化水与乳化油配制效果更好,工作液配制的浓度取决于加工工件的厚度、材质及加工精度要求。
从工件厚度来看,厚度小于30mm的薄型工件,工作液浓度在1O%~15%之间;30~lOOmm的中厚型工件,浓度大约在5%~1O%之间;大于1OOmm的厚型工件,浓度大约在3%~5%之间。
从工件材质来看,易于蚀除的材料,如铜、铝等熔点和气化潜热低的材料,可以适当提高工作液浓度,以充分利用放电能量,提高加工效率,但同时也应选较大直径的电极丝进行切割,以利于排屑充分。
从加工精度来看,工作液浓度高,放电间隙小,工件表面粗糙度较好,但不利于排屑,易造成短路。
工作液浓度低时,工件表面粗糙度较差,但利于排屑。
总之,在配制线切割工作液时应根据实际加工的情况,综合考虑以上因素,在保证排屑顺利、加工稳定的前提下,尽量提高加工表面质量。
另外必需注意:在配制乳化液时,如果乳化油自身的流动性和乳化性能好,只要按一定比例将乳化油加入稀释水中,充分搅拌后即可达到乳化状态,得到均匀的乳化液。
但一定要将乳化油加入稀释水中。
如果反其道而行之,将稀释水加入乳化油中,在某些情况下(如温度较低),可能生成胶状物质,很难溶解开。
对于粘度大、甚至呈膏状的乳化油,需要将乳化油加热,或者先使用部分热水冲调,待其充分乳化后再用水稀释至所需浓度。
因为热水可以使乳化油的粘度降低,热水分子有较大的动能,而且热水的表面张力小,有利于乳化油的均匀分散。
如果乳化油自身的乳化性能不够好,应在乳化的初始阶段在不断搅拌下先向乳化油中缓慢地加入少量稀释水,待到乳化油已被充分乳化、变成均匀的乳化液后,再冲调大量的稀释水,并不断搅拌,直至达到所需配制的浓度。
这样做的目的是使其先形成油包水型(W/O)乳状液,在不断搅拌并继续加入稀释水的过程中,使其发生相转变,由W/O型转变为O/W型.这样做虽然费时、费事,但所得到的乳状液颗粒较均匀、细致,乳化液的稳定性较高,可以在一定程度上弥补乳化油本身乳化性能的欠缺。
乳化油的使用方法

技术服务——金属加工液上海田木润滑油有限公司
乳化油的使用方法
●调配及添加方法
1.可用工业自来水直接调配,先将自来水加入清洁的液箱或水桶中。
2.将准备好的乳化油慢慢倒入水中,边搅拌(或打循环)边加入浓
缩液至规定浓度,循环使用。
3.一定要将乳化油加入水中,而不可以把水加入乳化油中。
4.使用后请将桶盖锁紧,不可添加任何东西于乳化油中。
●配制浓度
1.轻切削或磨削:3—5%(兑水比例约1:20—1:30)
2.一般切削加工:5%(兑水比例约1:20)
3.中重负荷切削加工:7—10%(兑水比例约1:10—1:14)
4.建议夏季配置浓度应略高于规定浓度
●注意
1.切忌将乳化油与导轨油的抽油泵混用
2.乳化油必须正确调配和使用以确保其品质的稳定
3.补加水时最好补加相当比例的乳化油,以保持溶液浓度的稳定。
电液控制液压支架乳化液要求
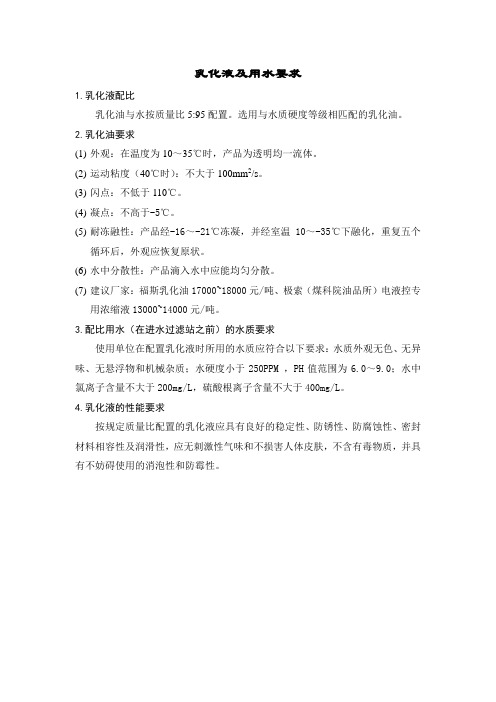
乳化液及用水要求
1.乳化液配比
乳化油与水按质量比5:95配置。
选用与水质硬度等级相匹配的乳化油。
2.乳化油要求
(1)外观:在温度为10~35℃时,产品为透明均一流体。
(2)运动粘度(40℃时):不大于100mm2/s。
(3)闪点:不低于110℃。
(4)凝点:不高于-5℃。
(5)耐冻融性:产品经-16~-21℃冻凝,并经室温10~-35℃下融化,重复五个
循环后,外观应恢复原状。
(6)水中分散性:产品滴入水中应能均匀分散。
(7)建议厂家:福斯乳化油17000~18000元/吨、极索(煤科院油品所)电液控专
用浓缩液13000~14000元/吨。
3.配比用水(在进水过滤站之前)的水质要求
使用单位在配置乳化液时所用的水质应符合以下要求:水质外观无色、无异味、无悬浮物和机械杂质;水硬度小于250PPM ,PH值范围为6.0~9.0;水中氯离子含量不大于200mg/L,硫酸根离子含量不大于400mg/L。
4.乳化液的性能要求
按规定质量比配置的乳化液应具有良好的稳定性、防锈性、防腐蚀性、密封材料相容性及润滑性,应无刺激性气味和不损害人体皮肤,不含有毒物质,并具有不妨碍使用的消泡性和防霉性。
配乳化液用水要求

配液时,使用水质(自来水或煤矿井下水)的硬度应不大于1500ppm,PH值应在6-8之间,氯离子含量不超过200mg/L,硫酸根离子含量不超过400 mg/L,自来水(或煤矿井下水)和原液按照95:5比例配制。
在配液时,按5%的质量比加入,然后倒入液箱内,稍加搅拌即可。
在使用过程中若有漏液损耗时,要及时补液;如发现大量析油、析皂或变质等异常现象,必须及时更换新液。
配制乳化液的水质要求:
1、水应为中性或接近中性。
2、水应为无色、透明、无味。
3、不能含有机械杂质和悬浮物,混浊泥水及海水不能用。
4、水的硬度愈低愈好,不能用硬度太高的水。
5、硫酸根离子、氯离子的含量要低,对金属防锈有利。
乳化液参数

乳化液参数哎,说起乳化液参数,这可真是个技术活儿,得仔细琢磨琢磨。
乳化液,那可是咱们工业制造里的宝贝,用得好,生产效率翻倍,用得不好,机器磨损、产品质量受影响。
今天,咱就来聊聊怎么根据乳化液的参数要求,来选对、用好乳化液。
一、乳化液基础参数得搞清首先啊,咱得明白乳化液的基础参数有哪些。
浓度,这个很重要,太浓了,机器负荷大,太稀了,润滑效果差。
粘度也得适中,太黏了,流动性不好,太稀了,附着性差。
还有PH值,酸碱度得平衡,不然对机器有腐蚀,对工人健康也不利。
1.1 浓度这事儿,咱得根据机器类型、工作环境来调整。
比如,精密机床,浓度稍微低点儿,保证润滑和冷却效果就行;重负荷设备,浓度得稍微高点,不然磨损大。
1.2 粘度嘛,也得根据实际情况来。
夏天温度高,粘度可以稍微低点儿,冬天温度低,粘度就得高点,保证乳化液在管道里能顺畅流动。
二、乳化液性能参数得了解除了基础参数,乳化液的性能参数也得心里有数。
比如,防锈性、抗氧化性、稳定性,这些都是关键。
防锈性不好,工件容易生锈;抗氧化性差,乳化液容易变质;稳定性不好,乳化液容易分层、沉淀。
2.1 防锈性这事儿,咱得根据工件材质来选择。
不锈钢工件,防锈性要求可以低点儿;铁质工件,防锈性就得高点。
2.2 抗氧化性,这个得根据工作环境来。
温度高、湿度大的环境,乳化液的抗氧化性得强,不然容易变质,影响使用效果。
2.3 稳定性,这个得靠质量好的乳化液来保证。
好的乳化液,不容易分层、沉淀,用起来更省心。
三、乳化液使用参数得掌握乳化液使用起来,也得注意一些参数。
比如,使用温度、使用压力、更换周期,这些都得心里有数。
3.1 使用温度,这个得根据乳化液的特性来。
有的乳化液耐高温,有的不耐高温,得根据说明书来操作。
3.2 使用压力,也得根据实际情况来调整。
压力太大,乳化液容易变质;压力太小,润滑效果差。
四、总结乳化液参数,看起来复杂,其实只要掌握了基础参数、性能参数和使用参数,用起来也就不难了。
乳化液配制的基本程序(doc 12页)

乳化液配制的基本程序(doc 12页)目录一、化液配制准备和配制条件;二、乳化液配制加油,加水计算方法;三、乳化液配制程序;四、乳化液管理人员日常操作;五、乳化液临时调控指标;六、乳化液应用相关数据检测和收集;七、其它;八、附录5)关闭污油箱与净油箱的排液阀门,打开油箱与净油箱的连通阀门。
6)将清洗剂溶液(冷轧油相同时可不加清洗剂)加入到系统中,加入量以能使系统循环为准,并加热到400C。
启动循环泵和供液泵(包括加热泵)循环清洗整个系统。
准备站清洗视情况而定。
7)将系统排空再次用新水按条款1.4进行清洗并排放。
8)加自来水同时加热到400C再次运行1小时后排空,配液系统视情况决定。
乳化液配制加油,加水计算方法系统加油1、油桶加热方式,(侍定)2、根据需求计算加油加水量,第一次充填量如下:a、第一次配制目标浓度为2.0%,主要用于系统简单压下调试;如果道次压下量需要达到30%以上时,可先将浓度提高至3.0%;b、第一次配制乳化液总体积为100m3。
c、所需总油量为100m3*2.0%=2m3,每桶为200L/185kg,合计需要10桶。
3、准备站总体积为3 m3,可用液位为2.5m3,按浓度15%进行预配,需要加入2500×15%=375kg,约2桶;因此,每次在准备站中加入2桶轧制油,配制过程如下:a、在箱中加入水2.2m3后,开动搅拌和加热;b、加入2桶轧制油完毕后搅拌15-20分钟;c、开动送液泵,向乳化液箱送液;d、重复上述过程5次,直完成所需加油量;系统加水1、初次配液,在开始加水时,检查系统排放阀门已经关闭;并记录开始时间和温度;2、由乳化液箱配置的脱盐水管路向系统加水乳化液配制程序1、 在系统中注入脱盐水,其总量约为正常量的60-70%(约60m 3)2、 打开净油箱和污油箱中的机械搅拌;3、 打开系统小循环(乳化液箱-加热泵-加热-净油箱);4、 打开加热器,开始加热升温;控制温度为35-450C ;5、 从准备站中加入预配液,直至完成所需加油量6、 乳化液取样测定浓度,同时将系统温度升至所需温度( 约为500C );7、 如果所测浓度高于设定浓度,向系统中补水,直至达到或低于设定浓度;8、 根据测定浓度,向净油箱内加入15%高浓度乳化液,达到所需浓度;9、在日常生产过程中,须要加油时,可按同样方式操作;注:按乳化液系统总体积约为100m 3计算,每次从配液箱加入1m 3浓度为15%的乳化液,系统浓度可提高约0.15%,可以据此计算所需的预配液。
乳化液配比要求及水质规定

乳化液配比要求及水质规定
签发:
关于乳化液配比浓度的补充规定
各采掘、安撤单位:
由于我矿工作面乳化液配置用水硫酸根离子含量较高,水质酸性强,具有较强的腐蚀性,为保证支架液压管件良好的润滑保护,从即日起,工作面乳化液配比浓度必须达到1.5—2.2%,公司检查时必须达到4%,一经发现乳化液配比达不到规定要求者,一律给予挂黄牌处理,并根据综机油脂管理规定,对相关责任者进行经济处罚。
各单位必须严格按照要求配制乳化液,加强液压支架和液压管路管理,制定严厉的工作措施,杜绝“跑、冒、滴、漏”现象,保证乳化液配比合格,并把乳化液配比合格作为交接班重要内容。
综采管理办公室
2012年1月6日
关于乳化液配制用水和配比要求的说明济宁二号煤矿使用的乳化油为ME20-5型乳化油,配比要求达到1.5—2.2%,要求乳化液配置用水是中性或偏碱性,PH值在6—9之间,硫酸根离子含量≤400毫克/升。
经从15301工作面、9301工作面和2308工作面抽取水样化验,其硫酸根离子含量分别达到612.8毫克/升、964.8毫克/升和564.2毫克/升,硫酸根离子含量均超标。
综机管理中心提出水与乳化油的配制质量比不得低于5%的要求。
(1)中性水溶液,pH=-lgaH+=-lg10-7=7
(2)酸性水溶液,Ph<7,pH值越小,表示酸性越强;
(3)碱性水溶液,Ph>7,pH值越大,表示碱性越强。
综采管理办公室
2012年1月6日。
3T乳化液处理方案要点

3T/H乳化液处理设备设计方案工程有限公司二00九年八月目录一、工程概况 (2)二、设计依据 (3)三、设计范围及原则 (3)四、设备施工范围 (3)五、工艺流程说明 (4)六、设计参数 (5)七、电器控制 (14)八、二次污染与防治 (15)九、主要设备及材料表 (15)十、运行成本分析 (17)十一、工程的施工安装、调试及基本管理 (18)十二、操作管理人员的培训及建议 (19)十三、公司简介 (19)一、工程概况1、污水水量:乳化液总量Q=3m3/h设计乳化液处理装置的处理水量Q=3m3/h。
2、进出水水质:(参考)(1)、进水水质BOD5:≤4000mg/LCOD Cr:≤9000mg/L油类:≤150 mg/LPH: 8∽10(2)、出水水质BOD5:≤300mg/LCOD Cr:≤500mg/LSS:≤400mg/L油类:≤20mg/LPH: 6∽93、出水标准乳化液处理装置出水水质达到《污水综合排放标准》(GB8978-1996)中的三级排放标准。
二、设计依据本工程设计方案的编制,主要技术依据如下:1、用户提供的水量、水质等有关资料以及小试的相关资料。
2、《污水综合排放标准》(GB8978-96);3、《给水排水设计手册》;4、《乳化液处理工艺》;5、《室外排水设计规范》GBJ14-876、《水处理设备制造技术条件》JB/T2932-19997、《钢制焊接常压容器技术条件》JB2880-818、《通用电器设备配电设计规范》(GB50055-93);9、《水处理设备油漆、包装技术条件》ZBJ98003-8710、我公司所完成同类工程所取得的实际经验和实际工程参数。
三、设计范围及原则1、工程设计范围为处理装置进水口至排放口为止,包括工艺设计、设备设计及电器控制设计等。
2、处理设备采用成熟、可靠、稳定的处理工艺,出水水质达到相关标准。
3、处理设备的构件经济合理,投资省、占地少,运行费用低。
液压支架乳化液配比浓度标准

液压支架乳化液配比浓度标准英文回答:The concentration standard for the emulsion ratio of the hydraulic support is an important factor in ensuring the proper functioning of the hydraulic system. The emulsion ratio refers to the proportion of oil to water in the emulsion. It is crucial to maintain the right concentration to ensure optimal performance and prevent any potential issues.The concentration standard for the emulsion ratio is typically expressed as a percentage. The specific concentration may vary depending on the specific requirements of the hydraulic system and the manufacturer's recommendations. However, a common standard is to maintain an emulsion ratio of around 5% to 10%.To achieve the desired concentration, it is important to carefully mix the oil and water in the correctproportions. This can be done using specialized equipmentor through manual mixing. The mixing process should be thorough to ensure a homogeneous emulsion.Regular monitoring and testing of the emulsion concentration is essential to ensure that it remains within the desired range. This can be done using various methods, such as using a refractometer or conducting laboratory tests. If the concentration deviates from the standard, adjustments should be made to restore the proper ratio.中文回答:液压支架乳化液配比浓度标准是确保液压系统正常运行的重要因素。
乳化液配制的基本程序
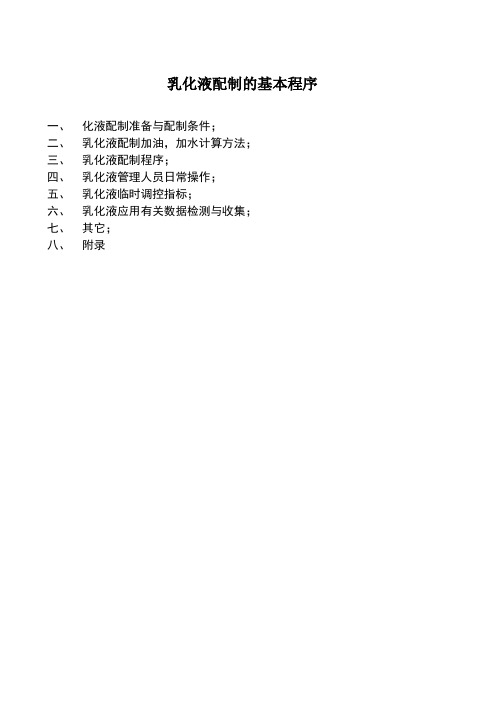
乳化液配制的基本程序一、化液配制准备与配制条件;二、乳化液配制加油,加水计算方法;三、乳化液配制程序;四、乳化液管理人员日常操作;五、乳化液临时调控指标;六、乳化液应用有关数据检测与收集;七、其它;八、附录乳化液配制准备与配制条件在乳化液配制前,需首先进行如下准备工作1、乳化液系统及输送设备经确认正常;a、系统的大循环(净液箱-加热泵-加热-喷嘴排-收集箱-磁分离器-污油箱)已测试正常;b、系统旁路循环(净液箱-加热泵-加热-净油箱)经测试正常,搅拌正常,以保证乳化液在配制后,长期不应用时保持状态。
2、系统排空第一次配液前应完成必要的清洗工作后,并通过乳化液供方与我方共同确认,内容为:a、基本无可见杂质与残余涂油;b、无大量清洗水残留(小于总体积的1%或者1m3);c、乳化液系统已经用去离子水至少冲洗过一次,以减少杂质离子对乳化液的首次污染;d、制时水后已确认去离子水符合要求,及管道系统完成清洗,在管出口处取样检测;3、加热系统经测试正常,保证乳化液配制后在长期不使用时能保持温度400C以上,以防止细菌生长;4、原油加热系统经检查运行正常,保证油桶内油品能够加热至可流淌状态;5、检查轧制油的名称、批号,确保使用所需轧制油;注:乳化液系统清箱操作如下1)通知废乳化液处理站准备接收废乳化液。
2)关闭所有系统泵,(包含供液泵、循环过滤泵、循环加热泵、搅拌器、带式的、撇油机、磁分离器)3)打开污油箱与净油箱的排液阀门。
4)系统排空后,用高压水清洗下列部位。
污油箱、净油箱(包含加热器)、配液槽、磁分离器、平床过滤器、主轧机及收集池与喷嘴排。
5)关闭污油箱与净油箱的排液阀门,打开油箱与净油箱的连通阀门。
6)将清洗剂溶液(冷轧油相同时可不加清洗剂)加入到系统中,加入量以能使系统循环为准,并加热到400C。
启动循环泵与供液泵(包含加热泵)循环清洗整个系统。
准备站清洗视情况而定。
7)将系统排空再次用新水按条款1.4进行清洗并排放。
食品添加剂—第四章 乳化液的制备

乳化液的后处理 高压均质
经过上述乳化设备乳化后的乳化液, 其粒径的大小以及粒子分布对于一些要求 比较高的乳化液是不够的,还必须对乳化 液进行高压均质。
高压均质可以使分散相粒子变得非常 小,使乳化液均匀、细腻。
均质后脂肪球直径
有足够的蛋白质和乳化剂
均质后脂肪球直径变小,其表面积增加, 同时也增加脂肪球表面的蛋白质及乳化剂的吸 附量,使脂肪密度增大,上浮能力变小,即球 径越小,乳化液越稳定。
如乳化液黏度高了,提高乳化剂的HLB值 可以降低其黏度,反之亦然。
5.2 乳化液的制备方法
相的准备
油相的准备 水相的准备
间歇式乳化法
相的乳化
连续式乳化法 乳化液的后处理
乳化液的稳定
油相的准备
5.2.1 相的准备
油相中存在有低熔 点固态成分时
需要把油相混合物加热到超过低熔点 固态成分熔点的2~4℃。
冰淇淋 部分冻结的泡沫,其中空气占40~50% 的体积。
由分散并成群的脂肪球(大多数是固体) 所构成的乳化液 由分散的冰晶构成的悬浮液 多糖凝胶 糖和蛋白质的浓溶液及空气泡
乳化剂在现代冰淇淋中的作用
真溶液 糖类及可溶性的盐
分子运动特性,产生较高的渗透压
复 杂
胶体 蛋白质、胶体磷酸盐及稳定剂
O/W
W/O
调整乳化剂的配比,使大体符合最佳 HLB值,以避开相转变点。
5.1.3 调整
目的 是乳化剂试配工作中最后进行的完善工作
•调整乳化剂的比例,使用量适合全液相。
•3.2调整pH值
根据食品原料的实际情况, 在乳化液中加入香料、色素和防 腐剂,并根据产品的要求在指定
•3.3调黏度
的水硬度范围内进行。
关于对利用井下采煤水配制乳化液的几点思考

摘要:众所周知,随着我国井下采煤所需要的液压系统的标准变得越来越高,为了安全起见,我们所使用的液压支架大多采用水包油型的乳化液。
本文首先对于乳化液的基本概念进行了简要的介绍,然后给出了几点有关于井下采煤水配制乳化液的思考,有利于乳化液的配制。
关键词:井下水乳化液配制随着我们国家采煤自动化所具有的程度的不断提高以及液压支架的使用次数的不断提升,井下采煤所需要的液压系统具有越来越高的标准。
以前我们采用的液压系统所具有的工作压力一般都低于每平方厘米70千克,然而,目前绝大多数的液压系统的工作压力都在每平方厘米200至300之间。
在如此高的工作压力之下,液压油从破裂的油管所喷设出来的状态主要为雾状,如果其遇到300-400℃之间的热表面就容易引起火灾,因此,为了安全起见,我们现在所使用的液压支架大多利用水包油型的乳化液。
1乳化液的基本概念所谓的乳化液主要是指由两种彼此互不相溶的液体构成,例如水与油,如果其中有一个液体变成小液滴形态,并且较为均匀地扩散到剩下的另一个液体里面,进而呈现出乳状的外观,我们则称其为乳化液。
所谓的水包油型的乳化液则是指将油分散于水里面,油作为内相,水则作为外相,其表示形式为O/W。
一般情况下,水包油型的乳化液具有如下特点:经济性、安全性、防锈性以及润滑性等,因此,人们大多将其放在井下的液压支架中进行使用。
一开始我们在配制乳化液的过程中所需要用到的水属于中低硬水,就是说该水的硬度需要低于28DH°,然而,随着我国人口的不断增加以及生活生产用水的不断提高,在乳化液配制过程中用到的软水面临着匮乏的现象,因此,为了解决用水问题,我们需要研究怎样利用井下特高硬度的水来配制乳化液。
2利用井下采煤水配制乳化液2.1乳化油的主要组成我们知道,油与水属于无法相溶的两种液体,并且这两种液体的密度具有很大的差别,所以利用机械方法无法形成比较稳定的乳化液,如果需要将其组成较为稳定的水包油型的乳化液,我们需要利用表面活性剂,即乳化剂,与此同时,我们还需要具备润滑、防锈、消泡以及防霉特性的添加剂。
关于乳化切削液的配制方法

关于乳化切削液的配制方法
在我们平常的金属加工切削液中,使用乳化切削液的广大厂商对乳化切削液的配制方法可能还了解的不是很明白,那么现在东莞美科石油化工公司为大家分享一下乳化切削液的配制方法。
乳化切削液是由乳化油用水稀释而成的一款切削液。
乳化油是由基础油、乳化剂、防锈剂、油性剂、极压剂、防腐杀菌剂登组成。
乳化切削液的组成比较复杂,因此对配制要求比较严格。
1.乳化切削液配制的水质很重要,水的流动性极好,具有较大的比热容和很强的溶解和分散能力,所以在我们选用水来配制时,我们需要选择优质的自来水进行配制。
乳化油的常规溶解法
2.如果乳化油自身是具有流动性和乳化性能较好的,那么将乳化油加入稀释水中,按照一定的比例,充分搅拌均匀即可。
在乳化切削液配制的乳化液时,要注意,一定要将乳化液加入水中;如果相反,将悉数的水加入到乳化油中,在一定的情况下,温度低时)可能生成胶状物质,很难溶解开来。
3.加热溶解法在使用稀释过程中,对于粘度大以及呈现膏状的乳化油,须将乳化油加热,或先使用部分热水冲调,待充分乳化后,再用冷水稀释所需要的浓度。
用热水可使乳化液的浓度降低,有利于乳化油的均匀分布。
4.相转变溶解法如果乳化油自身的溶化性能不够好,应在乳化的交刃
初始阶段不断的搅拌。
先向乳化油中缓慢地添加一些少量的稀释水,并不断地搅拌,直至达到所需要配置的浓度。
切削液的使用
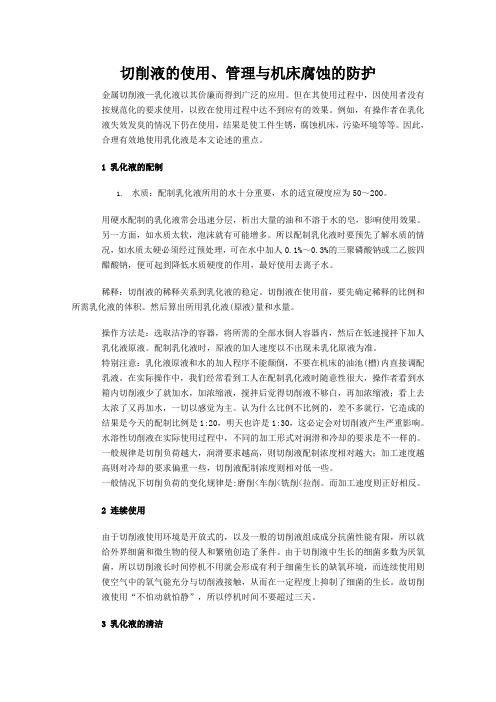
切削液的使用、管理与机床腐蚀的防护金属切削液—乳化液以其价廉而得到广泛的应用。
但在其使用过程中,因使用者没有按规范化的要求使用,以致在使用过程中达不到应有的效果。
例如,有操作者在乳化液失效发臭的情况下仍在使用,结果是使工件生锈,腐蚀机床,污染环境等等。
因此,合理有效地使用乳化液是本文论述的重点。
1 乳化液的配制1.水质:配制乳化液所用的水十分重要,水的适宜硬度应为50~200。
用硬水配制的乳化液常会迅速分层,析出大量的油和不溶于水的皂,影响使用效果。
另一方面,如水质太软,泡沫就有可能增多。
所以配制乳化液时要预先了解水质的情况,如水质太硬必须经过预处理,可在水中加人0.1%~0.3%的三聚磷酸钠或二乙胺四醋酸钠,便可起到降低水质硬度的作用,最好使用去离子水。
稀释:切削液的稀释关系到乳化液的稳定。
切削液在使用前,要先确定稀释的比例和所需乳化液的体积。
然后算出所用乳化液(原液)量和水量。
操作方法是:选取洁净的容器,将所需的全部水倒人容器内,然后在低速搅拌下加人乳化液原液。
配制乳化液时,原液的加人速度以不出现未乳化原液为准。
特别注意:乳化液原液和水的加人程序不能颠倒,不要在机床的油池(槽)内直接调配乳液。
在实际操作中,我们经常看到工人在配制乳化液时随意性很大,操作者看到水箱内切削液少了就加水,加浓缩液,搅拌后觉得切削液不够白,再加浓缩液;看上去太浓了又再加水,一切以感觉为主。
认为什么比例不比例的,差不多就行,它造成的结果是今天的配制比例是1:20,明天也许是1:30,这必定会对切削液产生严重影响。
水溶性切削液在实际使用过程中,不同的加工形式对涧滑和冷却的要求是不一样的。
一般规律是切削负荷越大,润滑要求越高,则切削液配制浓度相对越大;加工速度越高则对冷却的要求偏重一些,切削液配制浓度则相对低一些。
一般情况下切削负荷的变化规律是:磨削<车削<铣削<拉削。
而加工速度则正好相反。
2 连续使用由于切削液使用环境是开放式的,以及一般的切削液组成成分抗菌性能有限,所以就给外界细菌和微生物的侵人和繁殖创造了条件。
乳化油配比

乳化油配比线切割工作液由专用乳化油与自来水配制而成,有条件采用蒸馏水或磁化水与乳化油配制效果更好,工作液配制的浓度取决于加工工件的厚度、材质及加工精度要求。
从工件厚度来看,厚度小于30mm的薄型工件,工作液浓度在1O%~15%之间;30~lOOmm的中厚型工件,浓度大约在5%~1O%之间;大于1OOmm的厚型工件,浓度大约在3%~5%之间。
从工件材质来看,易于蚀除的材料,如铜、铝等熔点和气化潜热低的材料,可以适当提高工作液浓度,以充分利用放电能量,提高加工效率,但同时也应选较大直径的电极丝进行切割,以利于排屑充分。
从加工精度来看,工作液浓度高,放电间隙小,工件表面粗糙度较好,但不利于排屑,易造成短路。
工作液浓度低时,工件表面粗糙度较差,但利于排屑。
总之,在配制线切割工作液时应根据实际加工的情况,综合考虑以上因素,在保证排屑顺利、加工稳定的前提下,尽量提高加工表面质量。
另外必需注意:在配制乳化液时,如果乳化油自身的流动性和乳化性能好,只要按一定比例将乳化油加入稀释水中,充分搅拌后即可达到乳化状态,得到均匀的乳化液。
但一定要将乳化油加入稀释水中。
如果反其道而行之,将稀释水加入乳化油中,在某些情况下(如温度较低),可能生成胶状物质,很难溶解开。
对于粘度大、甚至呈膏状的乳化油,需要将乳化油加热,或者先使用部分热水冲调,待其充分乳化后再用水稀释至所需浓度。
因为热水可以使乳化油的粘度降低,热水分子有较大的动能,而且热水的表面张力小,有利于乳化油的均匀分散。
如果乳化油自身的乳化性能不够好,应在乳化的初始阶段在不断搅拌下先向乳化油中缓慢地加入少量稀释水,待到乳化油已被充分乳化、变成均匀的乳化液后,再冲调大量的稀释水,并不断搅拌,直至达到所需配制的浓度。
这样做的目的是使其先形成油包水型(W/O)乳状液,在不断搅拌并继续加入稀释水的过程中,使其发生相转变,由W/O型转变为O/W型.这样做虽然费时、费事,但所得到的乳状液颗粒较均匀、细致,乳化液的稳定性较高,可以在一定程度上弥补乳化油本身乳化性能的欠缺。
铝热轧乳化液配液用水及影响因素

铝热轧乳化液配液用水及影响因素铝板带轧制包括以生产中厚板及铝卷为主的铝板带热轧和以生产铝板带、箔轧为主的冷轧。
所用的铝轧制工艺润滑剂主要有热轧铝板用乳化液、冷轧铝板用轧制油、铝箔用轧制油、冷轧铝板用油水分施技术等。
铝热轧用乳化液由热轧油及水调配而成,乳化液的浓度通常在2——10%的范围,其中水相大约占乳化液90——98%的比例,因此,铝热轧乳化液中的水对铝热轧的生产及板带质量起到非常重要的作用。
本文将对铝热轧乳化液配液用水及相关影响因素进行简要论述。
一、水及相关水的分类水(H₂O)是由氢、氧两种元素组成的无机物,在常温常压下为无色无味的透明液体。
水可分为:硬水(天然水)、软水和去离子水等。
硬水是含有钙离子(Ca2+)和镁离子(Mg2+)及其它能溶于水的离子的水。
软水是仅去除了硬水中钙、镁离子的水。
去离子水则是指通过离子交换装置将水中的阴、阳离子全部去除的水。
根据水的硬度可以将水分类为:一般可采用硬度、电导率来衡量水的纯度。
水的硬度就是水中钙、镁离子的总浓度,而电导率为水中离子导电能力的大小。
天然水:除了含有Ca2+,Mg2+离子外,还包含有其它一些离子,这些离子对水质有各自不同的影响。
软水(钠离子交换水):水经过钠离子软化除去水中的Ca2+,Mg2+。
该水的特点:所得水的硬度减低,但pH不变;水中阴、阳离子的总量基本不变,Na+的含量会明显增加,电导率基本不变;由于再生剂为NaCl,所以钠离子软化水中,氯离子(Cl-)含量要高于原水中的氯离子含量。
去离子水:由于去除了所有溶在水中的离子,所以水的硬度和电导率均有大幅的降低,利于生产使用。
电导率反映了水中阳离子和阴离子的量,离子含量越高,水的电导率越大,水的纯度越低。
例如:某天然水的硬度和电导率一定,那么所制软化水的硬度会大大降低,电导率却基本不变,所制去离子水的硬度和电导率均会大大的降低,一般情况下,去离子水的硬度基本接近0,而电导率也会在3uS/cm以下。
乳化液配比操作规程

乳化液配比工操作规程一.上岗条件第1条:必须经过专业技术培训,考试合格取得合格证后,持证上岗方准操作:第2条:应熟知操作反渗透水处理成套设备的结构、性能、工作原理、技术特征,能独立操作。
第3条:实习作业人员操作应经主管部门批准并指定专人指导监护。
第4条:作业人员应身体健康,应无妨碍本职工作的病症。
二.安全规定第1条:每班安排两人值班,一正一副。
操作时,副值班操作,正值班监护。
上岗按规定穿好劳保用品。
第2条:上班前严禁饮酒,班中严禁睡觉与吸烟,不做与本职工作无关的事情。
严格执行交接班制度和工种岗位责任制,坚守工作岗位,遵守本操作规程、《煤矿安全规程》及有关规定。
第3条:检修设备或处理故障时,严格执行“停电挂牌制度”,设专人监护并制定有效的安全措施。
第4条:经常检查维护反渗透水处理系统各种计量装置,阀门和安全装置等,保证灵活可靠,每天要对全部设备的外表进行一次擦洗。
第5条:精滤器和保安滤器进水水压压差升高至0.15MPa时需要更换滤芯;炭滤器内的活性炭每半年检测一次炭滤器出水中余氯的含量,并与原水中余氯含量比较,若进出水中余氯含量无明显差异,则表明活性炭已失效,需更换;当钛棒过滤器进水水压压差达0.15MPa 时,应对钛棒滤芯进行清洗。
第6条:当出现标准化产水量降低10%以上、标准化脱盐率增加5%以上、进水和浓水之间的标准化压差上升了15%的情况中任意一项时,需要清洗膜元件。
当准备清洗液时,应确保在循环进入膜元件前,所有的化学品得到很好的溶解和混合。
在清洗液循环期间,清洗液温度不能超过35摄氏度。
第7条:掌握电气设备防、灭火知识,能正确使用灭火器材。
第8条:坚守本职岗位,爱岗敬业。
三.操作准备第1条:按规定检查RO水生产线、饮用水生产线、乳化液生产线成套设备状况,确保无重大缺陷和不安全因素。
第2条:根据交接班情况,重点检查存在问题的处理情况,达到各项保护齐全有效,所有阀门开关位置正确、压力表、流量计完好。