夹具设计实例模板
工装夹具设计实例100

工装夹具设计实例100一、背景工装夹具在工业生产中起到了至关重要的作用。
它们用于对零件、产品等进行定位、夹持、支撑等操作,以保证生产过程的精确性和效率。
本文介绍了一个工装夹具设计的实例,旨在展示设计过程和相关考虑因素。
二、需求分析根据客户需求,本次设计的夹具主要用于夹持电子产品的外殼。
夹具需要具备以下特点:1.稳定可靠:夹具需要能够牢固地夹持外壳,以防止其在加工过程中发生移动或变形。
2.精确度高:由于电子产品对尺寸和形状的要求较高,夹具需要保证制造出的外壳符合设计要求。
3.维护方便:夹具需要方便拆卸和更换零部件,以便在需要时进行维护和修理。
三、设计过程1. 认识产品在设计夹具之前,我们首先需要详细了解即将加工的电子产品外壳。
通过与客户沟通和参观样品,我们可以获得外壳的尺寸、形状、材料等信息,以便为夹具设计制定准确的要求。
2. 确定夹持方式根据产品外壳的形状和特点,我们需要确定最适合的夹持方式。
常见的夹持方式包括机械夹紧、真空吸附等。
在本例中,由于外壳的形状较规则,我们选择使用机械夹紧方式进行夹持。
3. 制定夹具结构根据选定的夹持方式,我们制定了夹具的结构框架,并选择了适当的材料。
结构框架需要具备足够的刚性和稳定性,以保证外壳加工过程中的精确度。
4. 设计夹具零部件在夹具结构框架的基础上,我们设计了各个零部件,并考虑了其功能和使用方式。
夹具零部件包括定位块、夹紧臂、调节螺母等。
这些零部件需要精确地配合,以确保夹具在使用过程中的可靠性和稳定性。
5. 制造与调试完成夹具的设计后,我们进行了制造和调试工作。
制造过程中,需要注意保证夹具各个零部件的精度和质量,以确保夹具能够正常工作。
调试过程中,我们对夹具进行了多次测试和优化,以保证其满足客户需求。
四、总结本文介绍了一个工装夹具设计的实例,重点阐述了设计过程和相关考虑因素。
通过对产品的认识、夹持方式的确定、夹具结构的制定、零部件的设计以及制造与调试的过程,我们成功地开发了一套满足客户需求的工装夹具。
专用夹具毕业设计论文案例
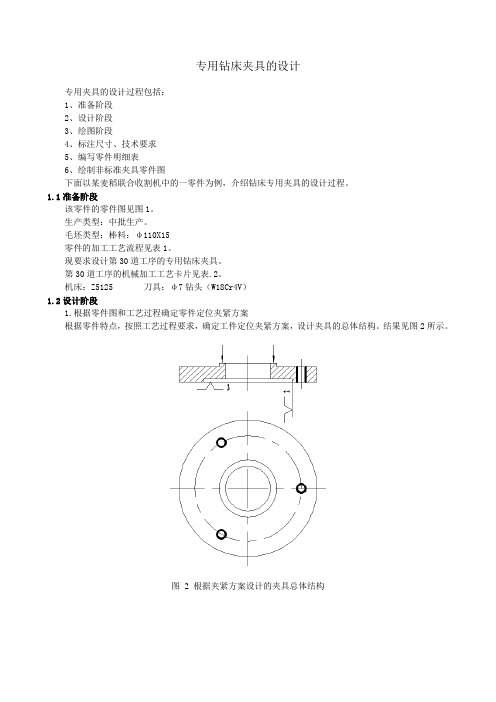
专用钻床夹具的设计专用夹具的设计过程包括:1、准备阶段2、设计阶段3、绘图阶段4、标注尺寸、技术要求5、编写零件明细表6、绘制非标准夹具零件图下面以某麦稻联合收割机中的一零件为例,介绍钻床专用夹具的设计过程。
1.1准备阶段该零件的零件图见图1。
生产类型:中批生产。
毛坯类型:棒料:φ110X15零件的加工工艺流程见表1。
现要求设计第30道工序的专用钻床夹具。
第30道工序的机械加工工艺卡片见表.2。
机床:Z5125 刀具:φ7钻头(W18Cr4V)1.2设计阶段1.根据零件图和工艺过程确定零件定位夹紧方案根据零件特点,按照工艺过程要求,确定工件定位夹紧方案,设计夹具的总体结构。
结果见图2所示。
图 2 根据夹紧方案设计的夹具总体结构图1 零件图表1 零件的加工工艺流程(续)表 2 第30道工序机械加工工艺卡片机械加工工序卡片产品型号零件图号4LG1-1.4-02产品名称零件名称轴承盖共页第页车间工序号工序名称材料牌号30 钳A3毛坯种类毛坯外形尺寸每毛坯可制件数每台件数棒料φ110X15 1 2设备名称设备型号设备编号同时加工件数Z5125 1夹具编号夹具名称切削液专用夹具ZYJJ-03 冷却液工位器具编号工位器具名称工序工时(分) 准终单件工步号工步内容工艺装备主轴转速切削速度进给量切削深度进给次数工步工时r/min m/min mm/r mm 机动辅助装夹钻头φ7(W18Cr4V)、专用夹具(ZYJJ-03)φ7塞规、游标卡尺(0~125:0.02)孔距综合量具(ZYLJ-01)1 钻3-φ7孔。
315 6.92 手动进给 3.5 12 去毛刺。
设计(日期)校对(日期)审核(日期)标准化(日期)会签(日期)标记处数更改文件号签字日期标记处数更改件号签字日期2.定位方案设计(1)在本设计方案中,工序尺寸为φ85±0.27、φ71.00+,工序基准为孔的中心线。
要满足加工要求理论应限制的自由度为:。
夹具设计实例-模板
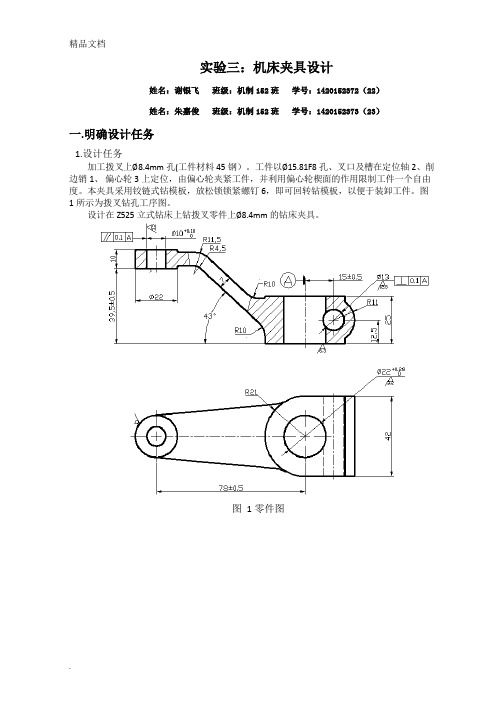
实验三:机床夹具设计姓名:谢银飞班级:机制152班学号:1420152372(22)姓名:朱嘉俊班级:机制152班学号:1420152373(23)一.明确设计任务1.设计任务加工拨叉上8.4mm孔(工件材料45钢)。
工件以15.81F8孔、叉口及槽在定位轴2、削边销1、偏心轮3上定位,由偏心轮夹紧工件,并利用偏心轮楔面的作用限制工件一个自由度。
本夹具采用铰链式钻模板,放松锁锁紧螺钉6,即可回转钻模板,以便于装卸工件。
图1所示为拨叉钻孔工序图。
设计在Z525立式钻床上钻拨叉零件上8.4mm的钻床夹具。
图 1 零件图图 2 三维实体图2.杠杆臂加工工艺分析(1)加工要求加工φ10 和φ13 两孔;孔距为78±0.5;U型槽对称轴线与8.4轴线的水平尺寸为3.1±0.1mm,垂直尺寸为12.5 两孔垂直;8.4对15.81F8轴线平行度公差为0.2;φ13对φ22 轴线垂直度公差为0.1。
Φ10 孔Ra 值为3.2,Φ13 孔Ra 值为12.5。
(2)加工工艺由于该工序中两个孔的位置关系为相互垂直,且不在同一个平面里,要钻完一个孔后翻转90°再钻削另一个孔,因此要设计成翻转式钻夹具。
分析零件图可知,该拔叉的叉角两端面厚度薄于连接的表面,但减少了加工面,使用淬火处理提供局部的接触硬度。
叉角两端面面积相对较大,可防止加工过程中钻头钻偏,保证孔的加工精度,及孔与叉角两端面的垂直度。
其它表面加工精度较低,通过铣削、钻床的粗加工就可达到加工要求;而主要工作表面虽然加工精度相对较高,但也可以在正常的生产条件下,采用较经济的方法保质保量地加工出来,可见该零件工艺性好。
二.定位方案与定位元件1.夹具设计要求已知工件材料为45钢,毛坯为模锻件,所用机床为Z525型立式钻床,大批生产规模。
试为该工序设计一钻床夹具。
2、夹具的设计方案分析:①孔8.4mm为自由尺寸,可一次钻削保证。
该孔在轴线方向的设计基准距离槽mm的对称中心线为 3.1mm±0.1mm;在径向方向的设计基准是孔15.81F8的中心线,其对称度要求为0.2mm,该尺寸精度可以通过钻模保证。
机床夹具设计步骤和实例
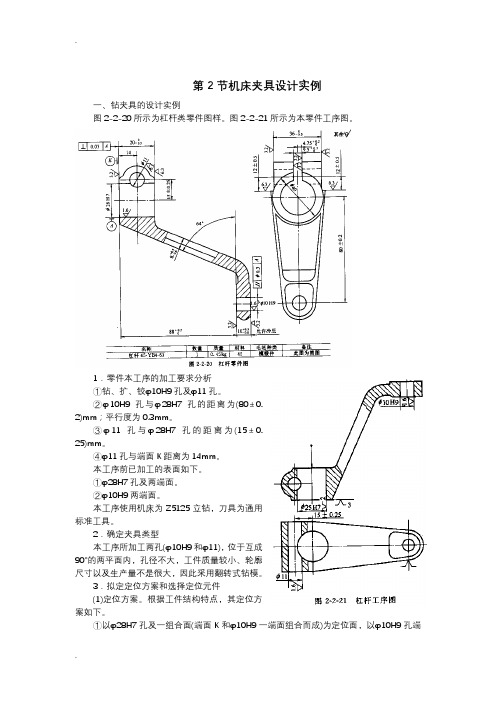
第2节机床夹具设计实例一、钻夹具的设计实例图2-2-20所示为杠杆类零件图样。
图2-2-21所示为本零件工序图。
1.零件本工序的加工要求分析①钻、扩、铰φ10H9孔及φ11孔。
②φ10H9孔与φ28H7孔的距离为(80±0.2)mm;平行度为0.3mm。
③φ11孔与φ28H7孔的距离为(15±0.25)mm。
④φ11孔与端面K距离为14mm。
本工序前已加工的表面如下。
①φ28H7孔及两端面。
②φ10H9两端面。
本工序使用机床为Z5125立钻,刀具为通用标准工具。
2.确定夹具类型本工序所加工两孔(φ10H9和φ11),位于互成90°的两平面内,孔径不大,工件质量较小、轮廓尺寸以及生产量不是很大,因此采用翻转式钻模。
3.拟定定位方案和选择定位元件(1)定位方案。
根据工件结构特点,其定位方案如下。
①以φ28H7孔及一组合面(端面K 和φ10H9一端面组合而成)为定位面,以φ10H9孔端外缘毛坯面一侧为防转定位面,限制六个自由度。
这一定位方案,由于尺寸885.00+mm 公差大,定位不可靠,会引起较大的定位误差。
如图2-2-22(a)所示。
②以孔φ28H7孔及端面K 定位,以φ11孔外缘毛坯一侧为防转定位面,限制工件六个自由度。
为增加刚性,在φ10H9的端面增设一辅助支承,如图2-2-22 (b)所示。
比较上述两种定位方案,初步确定选用图2-2-22(b)所示的方案。
(2)选择定位元件。
①选择带台阶面的定位销,作为以φ28H7孔及其端面的定位元件,如图2-2-23所示。
定位副配合取6728g H φ。
②选择可调支承钉为φ11孔外缘毛坯一侧防转定位面的定位元件,如图2-2-24(a)所考虑结构简单,现选用图2-2-24(a)所示结构。
(3)定位误差计算①加工φ10H9孔时孔距尺寸(80±0.2)mm的定位误差计算。
由于基准重合,故ΔB=0。
基准位移误差为定位孔(φ38021.00+mm)与定位销(φ38007.0002.0--mm)的最大间隙,故ΔY =(0.021+0. 007+0.013)mm =0.041rnm 。
铣床夹具设计示例.doc

铣床夹具设计示例.doc一、设计要求:本设计的铣床夹具主要用于加工复杂形状的工件,要求夹具具有良好的稳定性和紧固力,能够保证被加工工件的精度和表面质量。
二、设计思路:本设计采用了双定位、单锁紧的夹具方式,夹持工件后,通过两侧的定位模板来保证工件的定位精度,然后通过中央的锁紧螺杆来锁定工件,实现夹持效果。
同时,在夹持面和定位面上布置有多个压板,可调节压紧力度,保证工件夹持牢固。
三、设计方案:1、夹具主体结构:夹具主体结构采用铝合金材料精密加工而成,整体强度高、重量轻、耐腐蚀性好。
主体上下各自开有一个槽口,用于安装定位模板和压板。
中央开有一个中空结构,用于安装锁紧螺杆。
2、定位模板:定位模板采用SUS316L不锈钢材料定制而成,精度高、硬度大、耐磨性好。
定位模板的两端分别安装在夹具槽口中,保证固定位置不变。
定位模板的中间部分,开有一个适应工件形状的凹槽,可与工件配合定位。
3、压板:压板采用特殊的弹簧夹持结构,可自由调节压紧力度。
压板上开有多个V形槽,可适应不同尺寸的工件。
在夹击面和定位面上均安装了多个压板,保证夹持稳固。
4、锁紧螺杆:锁紧螺杆采用优质合金钢材料制成,结构简单,耐用性好。
其头部装有手柄,方便操作。
锁紧螺杆的螺杆体与夹具中空结构配合,旋紧后可通过摩擦力夹紧工件。
四、设计效果:本设计的铣床夹具具有以下优点:2、制造精度高、耐用性好。
夹具主体采用铝合金材料,定位模板采用不锈钢材料,压板采用弹簧夹持结构,整个夹具结构紧凑、牢固,制造精度高、耐用性好。
3、适用范围广。
本设计的铣床夹具可以适应各种形状的工件加工,并且可根据工件尺寸自由调整夹击力度,具有极高的适用性。
五、总结:本设计的铣床夹具通过双定位、单锁紧的夹紧方式,保证了工件的稳定性和精度,同时通过弹簧夹持结构可以自由调节夹持力度,适应各种形状的工件。
整个夹具结构紧凑、制造精度高,可靠性强。
该夹具在实际使用中具有较好的效果,可以为工件的精密加工提供良好的保障。
机床夹具设计(实例)
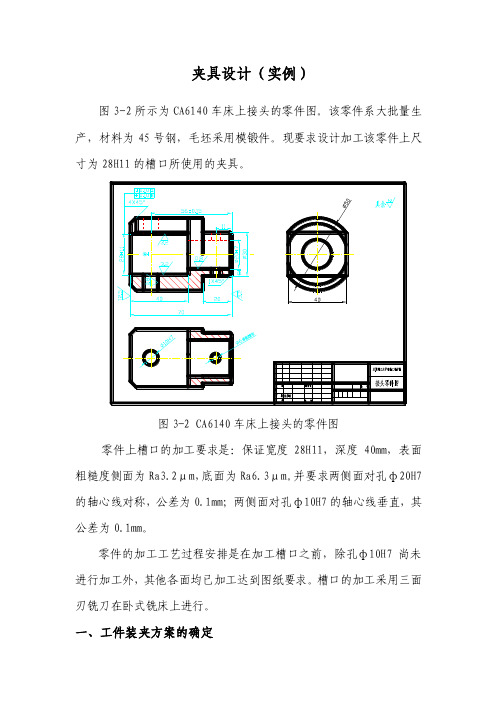
夹具设计(实例)图3-2所示为CA6140车床上接头的零件图。
该零件系大批量生产,材料为45号钢,毛坯采用模锻件。
现要求设计加工该零件上尺寸为28H11的槽口所使用的夹具。
图3-2 CA6140车床上接头的零件图零件上槽口的加工要求是:保证宽度28H11,深度40mm,表面粗糙度侧面为Ra3.2μm,底面为Ra6.3μm。
并要求两侧面对孔ф20H7的轴心线对称,公差为0.1mm;两侧面对孔ф10H7的轴心线垂直,其公差为0.1mm。
零件的加工工艺过程安排是在加工槽口之前,除孔ф10H7尚未进行加工外,其他各面均已加工达到图纸要求。
槽口的加工采用三面刃铣刀在卧式铣床上进行。
一、工件装夹方案的确定工件装夹方案的确定,首先应考虑满足加工要求。
槽口两侧面之间的宽度28H11取决于铣刀的宽度,与夹具无关,而深度40mm则由调整刀具相对夹具的位置保证。
两侧面对孔ф10H7轴心线的垂直度要求,因该孔尚未进行加工,故可在后面该孔加工工序中保证。
为此,考虑定位方案,主要应满足两侧面与孔ф20H7轴心线的对称度要求。
根据基准重合的原则,应选孔ф20H7的轴心线为第一定位基准。
由于要保证一定的加工深度,故工件沿高度方向的不定度也应限制。
此外,从零件的工作性能要求可知,需要加工的两侧面应与已加工过的两外侧面互成90度,因此在工作定位时还必须限制绕孔ф20H7的轴心线的不定度。
故工件的定位基准的选择如图3.3所示,除孔ф20H7(限制沿x,y轴和绕x,y轴的不定度)之外,还应以一端面(限制沿z轴的不定度)和一外侧面(限制绕z轴的不定度)进行定位,共限制六个不定度,属于完全定位。
工件定位方案的确定除了考虑加工要求外,还应结合定位元件的结构及夹紧方案实现的可能性而予以最后确定。
对接头这个零件,铣槽口工序的夹紧力方向,不外乎是沿径向或沿轴向两种。
如采用如图 3.4(a)所示的沿径向夹紧的方案,由于ф20H7孔的轴心线是定位基准,故必须采用定心夹紧机构,XYZX以实现夹紧力方向作用于主要定位基面。
铣床夹具设计经典案例
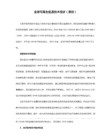
工件加工精度分析
定位误差ΔD:
–由于本设计加工时,定位基准和加工基准都 是中心轴,因此基准不重合误差为零 . –所以定位误差来自于基准位移误差,其计算 公式为:
孔:Φ12H8 ES=+27μm EI=0μm 轴:Ф12g6 es=-6μm ei=es-IT6=-17μm
ε= Xmax = (27 + 17)= 44μm
第二部分 铣床夹具设计实例分析
研究原始资料,明确设计任务
工件为一水泵叶轮, 要求设计一副铣床夹 具,用在卧式铣床上 加工两条互成90°的 十字槽,如图所示: 工件三维结构图
定位方案的确定
确定要限制的自由度
–根据加工工序的尺寸 , 形状和位置精度要求,工件 定位时需完全限制六个方向的自由度: 沿X,Y,Z方向 的水平运动以及轴向转动。
装配三维结构图夹紧配置分度机构的设计分度装置的确定该工件选用一个立轴式回转分度装置一般这样的分度采用棘轮的比较普遍但是由于该工件的定位夹紧机构尺寸较大采用棘轮的化比较不方便因此应改用分度盘加定位销的分度方案具体如下
铣床夹具设计经 典案例
二、 直线进给铣夹具
• 图8-69为单件加工铣夹具。在卧式铣 床上加工分离叉4的两个内側面。工 件以锥头顶销2和柱头定位销5及右支 座6的端面在孔中定位限制5个自由度; 工件背面靠在支承板上,形成完全定 位。拧紧螺母夹紧工件。
铣床专用夹具的设计特点和要求
由于铣削过程不是连续切削,极易产生铣削 振动。铣削的加工余量一般较大,铣削力也 较大,且方向是变化的,因此设计时要注意:
• 夹具要有足够的刚度和强度; • 夹具要有足够的夹紧力,夹紧装置自锁性要好 • 夹紧力应作用再工件刚度较大的部位上,且作用 点和施力方向要恰当; • 夹具的重心应尽量低,高度与宽度之比应不大于 1~1.25; • 要有足够的排屑空间。切削和冷却液能顺利排除, 必要时可设计排屑孔。
机械工装夹具设计资料【范本模板】

图3.1 异形杠杆简图图图图 3.2 车床夹具图3.3 盖板简图图 3.4 钻床夹具1 钻模板2 钻套3 压板4 圆柱销5 夹具体6 挡销7 菱形销图 3.6 固定支承钉—图3.8 可调支承图 3.9 可调支承的应用(a ) (b) (c)图 3.10 自位支承图3.16 圆柱心轴图3.16 小锥度心轴图3.19 圆锥销组合定位(a ) (b) (c)图 3.20 定位套图 3.21半园定位(a) (b) (c) (d)图 3.22 固定V 形块结构形式图3.26 基准位移误差φ400-0.0380-0.110-0.2450O O 1图 3.31 v 形块上定位铣斜面图 3.32 夹紧机构的组成1-压板;2-连杆;3-活塞推杆;4-气缸;5-活塞;6-配气阀图 3.35 夹紧力作用点靠近加工表面图 3.40 斜楔夹紧机构1-夹具体; 2-斜楔; 3-工件(d)图 3.37 快速螺旋夹紧机构1工件 2 压板 3 T形槽用螺母图 3.40 典型螺旋压板夹紧机构图 3.41 偏心夹紧机构图3.42圆偏心及其弧形楔展开图图3.48 单件联动夹紧机构1-工件;2-浮动压板;3-活塞杆;5-摇臂;4、6-摆动压块;7-螺母图3.49 多件联动夹紧机构图3.44 螺旋式定心夹紧机构图 3.45 杠杆式三爪自定心卡盘图3.46机动楔式夹爪自动定心机构图 3.47 弹性心轴及弹簧夹头1-夹具体;2-弹簧筒夹;3-锥套;4-螺母;5-心轴图 3.54 膜片卡盘定心夹紧机构1 夹具体2 薄壁套筒3 液性塑料4 柱塞5 螺钉6 限位螺钉图3.56液性塑料定心夹紧机构图 3.49波纹套心轴图 3.58 固定钻模1 夹具体2 平面支承3 削边销4 圆柱销5 快速夹紧螺母6 特殊快换钻套图 3.59 回转式钻模1 钻模板2夹具体3手柄4、8 螺母5 把手6 对定销7 圆柱销9开口垫圈10衬套11 钻套12 螺钉(a) (b)图3.60 翻转式钻模1 夹具体2 定位件3削扁开口垫圈 4 螺杆5 手轮6对定销7沉头螺钉图 3.61 盖板式钻模1 盖板2 圆柱销3 削边销4 支承钉5 把手图 3.62滑柱式钻模1-导向滑柱;2-齿条滑柱3夹具体4钻模板;5齿轮轴;6手柄;7套环(a)(b) (c)图 3.63 标准钻套1-钻套; 2-衬套 3 钻模板; 4-螺钉图 3.64.特殊钻套(e)(a) (b) (c)图3.65 三种钻模板图3.66 悬挂式钻模板1-多轴传动头;2-弹簧;3-导柱;4-钻模板;5 -螺钉;6-导套图 3.67 铁垫块铣直角多件联动铣床夹具1-定向键 ;2-对刀块;3 -夹具体; 4、8-压板 ;5-螺母; 6-定位块; 7-螺栓; 9-支钉; 10-浮动杠杆图3.68 杠杆零件的料仓式铣床夹具图3.69多工位铣削杠杆端面夹具1-锯齿支钉;2,3,4-挡销; 5-压板; 6-螺母; 7- 压板支承螺钉; 8-对刀块图3.71 靠模铣床夹具图3.72 定向键图3.73 对刀装置图3.74 标准对刀块图 3.76 铣床夹具体与耳座图 3.77 车床尾座孔镗模1-支架;2 -镗套; 3、4-定位板;5、8-压板; 6-夹紧螺钉; 7-可调支承钉; 9-镗模底座; 10- 镗刀杆;11 浮动接头图 3.78 镗曲轴轴承孔金刚镗床夹具1、3 -V形块; 2-浮动压块; 4-弹簧;5-活塞; 6-活塞杆; 7-转动叉形块; 8、9 -浮动压板(a)(b) (c)图 3.80 常用的回转式镗套图 3.81 内滚式滚动镗套图3.82 回转镗套的引刀槽及尖头键(a)(b) (c)图3.83 单支承导向镗孔示意图(a)(b)图 3.84 双支承导向镗孔示意图图 3.85 确定让刀量示意图图 3.86 镗杆前端导引部分结构(e)图 3.87 浮动接头1-镗杆;2-接头体;3-外套;4-拨动销图3.88 飞球保持架工序图及心轴夹具图 3.89 喷油嘴壳体尾部法兰端面的车床夹具1-拉杆;2-弹簧;3-套筒;4-斜块;5-压板;6-支承板;7-圆柱销;8-菱形销图 3.90阀体四孔偏心回转分度车床夹具图 3.91 开合螺母中心孔的角铁式车床夹具1、11-螺栓; 2-压板; 3-摆动V形块; 4-过渡盘; 5-夹具体; 6-平衡块; 7-盖板; 8、10-固定、活动支承板; 9-活动菱形销图 3.92 十字槽轮零件精车圆弧工序简图图3.93 花盘式车床夹具1、3、4-定位套;2-定位销图 3.94 车床夹具与机床主轴的连接图3.95 加工偏心件的通用可调夹具图 3.96 铣两端面成组夹具1-组合气缸;2-双向压板;3-基体;4-快卸垫板;5-可换V形块;6-传动杆;7-压板;8-螺钉图 3.100 自动线上的机床固定夹具及随行夹具1-活动定位销;2-钩形压板;3-随行夹具;4-输送支承;5-定位支承板;6-润滑液压泵;7-杠杆;8-液压缸图3.101 数控镗铣床夹具1、2-步进电机;3、4、8、9-支承;5-丝杠;6-小滑板;7-大滑板10-钩形压板3.5.2 专用夹具的设计示例拨杆零件如图3。
- 1、下载文档前请自行甄别文档内容的完整性,平台不提供额外的编辑、内容补充、找答案等附加服务。
- 2、"仅部分预览"的文档,不可在线预览部分如存在完整性等问题,可反馈申请退款(可完整预览的文档不适用该条件!)。
- 3、如文档侵犯您的权益,请联系客服反馈,我们会尽快为您处理(人工客服工作时间:9:00-18:30)。
实验三:机床夹具设计
姓名:谢银飞班级:机制152班学号:1420152372(22)
姓名:朱嘉俊班级:机制152班学号:1420152373(23)
一.明确设计任务
1.设计任务
加工拨叉上8.4mm孔(工件材料45钢)。
工件以∅15.81F8孔、叉口及槽在定位轴2、削边销1、偏心轮3上定位,由偏心轮夹紧工件,并利用偏心轮楔面的作用限制工件一个自由度。
本夹具采用铰链式钻模板,放松锁锁紧螺钉6,即可回转钻模板,以便于装卸工件。
图1所示为拨叉钻孔工序图。
设计在Z525立式钻床上钻拨叉零件上∅8.4mm的钻床夹具。
图 1 零件图
图 2 三维实体图
2.杠杆臂加工工艺分析
(1)加工要求
加工φ10 和φ13 两孔;孔距为78±0.5;U型槽对称轴线与8.4轴线的水平尺寸为3.1±0.1mm,垂直尺寸为12.5 两孔垂直;8.4对∅15.81F8轴线平行度公差为0.2;φ13对φ22 轴线垂直度公差为0.1。
Φ10 孔Ra 值为
3.2,Φ13 孔Ra 值为12.5。
(2)加工工艺由于该工序中两个孔的位置关系为相互垂直,且不在同一个平面里,要钻完
一个孔后翻转90°再钻削另一个孔,因此要设计成翻转式钻夹具。
分析零件图可知,该拔叉的叉角两端面厚度薄于连接的表面,但减少了加工面,使用淬火处理提供局部的接触硬度。
叉角两端面面积相对较大,可防止加工过程中钻头钻偏,保证孔的加工精度,及孔与叉角两端面的垂直度。
其它表面加工精度较低,通过铣削、钻床的粗加工就可达到加工要求;而主要工作表面虽然加工精度相对较高,但也可以在正常的生产条件下,采用较经济的方法保质保量地加工出来,可见该零件工艺性好。
二.定位方案与定位元件
1.夹具设计要求
已知工件材料为45钢,毛坯为模锻件,所用机床为Z525型立式钻床,大批生产规模。
试为该工序设计一钻床夹具。
2、夹具的设计方案
分析:
①孔∅8.4mm为自由尺寸,可一次钻削保证。
该孔在轴线方向的设计基准距
离槽mm的对称中心线为 3.1mm±0.1mm;在径向方向的设计基准是孔∅15.81F8的中心线,其对称度要求为0.2mm,该尺寸精度可以通过钻模保证。
②孔:15.81F8、槽mm和拨叉槽口mm是已完成的尺寸,钻孔∅8.4mm。
③立钻Z525的最大钻孔直径为∅25mm,主轴端面到工作台面的最大距离H 为700mm,工作台面尺寸为375mm×500mm,其空间尺寸完全能够满足夹具的布置和加工范围的要求。
④本工序为单一的孔加工,夹具可采用固定式。
方案设计:
1、定位基准的选择:为了保证孔∅8.4mm对基准孔∅15.8F8垂直并对该孔中心线的对称度符合要求,应当限制工件X的平移、Y轴旋转、Z轴旋转,三个自由度;为保证孔∅8.4处于拨叉的对称面内且不发生扭斜,应当限制Y轴旋转自由度;
根据零件的构造,最容易想到的是以Φ22mm 的孔为定位基准,这样可以避免基准不重合误差,同时可以限定四个自由度;用Φ22 孔口端面(底面)
限定零件的上下移动的自由度;用φ10 孔附近圆柱表面限定零件沿Φ22 中心线转动的自由度就可以实现完全定位。
φ10 孔附近为悬壁梁结构,加工时容易变形,在φ10 孔口端面(底面)设辅助支承,用来增加零件的刚性。
图 3 零件定位示意图
2.定位元件的选择:
定位销:插入Φ22 的孔,用来限制X,Y 方向的移动和转动,共四个自由度。
定位元件为非标准元件。
用定位销的小端面(相当于一个支承钉)与Φ22 孔口端面支靠限定Z 方向的移动自由度。
定位元件为非标准元件。
可调支承钉:限定Z 方向的转动。
定位元件为标准元件。
用一辅助支承来提高工件的安装刚度和定位的稳定性。
定位元件为非标准元
件。
图 4 定位方案
三.夹紧方案的确定
根据零件的定位方案,采用锁紧螺母和开口垫圈来实现快速锁紧夹紧机构,它与一个加工面位置靠近,增加了刚性,零件夹紧变形也小,但对于另一个加工面较远,为提高刚性,故采用辅助定位元件来固定,该设计采用了螺旋辅助支承。
图 5 夹紧方案
四.夹具结构设计
1.定位装置
(1)销轴
图 6 销轴
(2)可调支承钉
可调支承钉在GB JB/T 8026.1-1999(六角头支承)中选取M8×40-S。
图7 可调支撑钉
2.夹紧装置
(1)夹紧
选用M10 螺纹以满足强度要求。
(2)开口垫圈
图8 夹紧方案
3.辅助装置
(1)钻模板类型选择
根据工件和夹具体的结构,选用固定式钻模板。
固定式钻模板虽然有时装卸工件不便,但它结构简单、制造方便、定位精度
高。
图9 辅助装置
3.辅助装置
夹具设计实例-模板
(1)钻套从国家标
准中选用。
(2)钻模板
图10 钻模板1
图11 钻模板2
(2)钻套的选择
由于孔φ10mm 和φ13mm 一次钻孔就可达到要求,因此采用固定式钻套。
(查手册确定型号)
Φ10mm 选无肩
Φ13mm选有肩
图12 钻模4 夹具体选用铸
造夹具体。
图13 夹具体五.绘制夹具总图
图14 夹具三维实体图
六. 夹具装配图上的尺寸、公差及技术要求的标注最大轮廓尺寸(长、
宽、高):180、140、141影响工件定位精度的尺寸:φ22e8、影响导向的尺寸及公差:Φ10G7、
Φ13F7(公差带查表确定)
影响夹具精度的尺寸及公差(公差按零件公差的1/2 至1/5):78±0.15、15±0.15、12.5±0.05、相对于基准F 的垂直度Φ0.05、相对于基准F 的垂直度Φ0.03、相对于基准E 的垂直度Φ0.05
其它重要尺寸和公差:Φ18H7/r6、Φ22H7/n6 以及定位销与夹具体的配合尺寸(图中遗漏,应补上)
需标注的技术要求:见装配图
七.工件加工精度分析定
位误差:
两孔的直径尺寸基本上由钻头尺寸保证,没有定位误差。
尺寸78±0.5、15±0.5 平行度公差和垂直度公差的工序基准和定位基准重合,基准不重合误差为ΔB= 0;
尺寸78±0.5、15±0.5 和平行度公差和垂直度公差存在基准位移误差,其大小等于定位轴与φ22 孔之间的最大配合间隙ΔY=Xmax=0.28+0.033+0.04=0.353 尺寸78±0.5、15±0.5 和平行度公差和垂直度公差的定位误差分别为ΔD= ΔB+ ΔY=0.353
尺寸12.5 的基准位移误差和基准不重合误差都为0,所以定位误差为0
工件加工精度分析对刀误
差ΔT:
因加工孔处工件较薄,可不考虑钻头的偏差。
钻套导向孔尺寸为φ10F7 和φ13F7;钻头尺寸为φ10-0.036 和φ13 -0.036;各尺寸的对刀误差为:ΔT=
(0.028+0.036)mm=0.064mm
安装误差ΔA:
ΔA=0
夹具误差ΔJ:
78±0.5 的夹具误差为:0.3
15±0.5 的夹具误差为:0.3
12.5 的夹具误差为:0.1
平行度0.1 的夹具误差为:0.05
垂直度 0.1 的夹具误差为:0.05 加工方法误差 ΔG :
各尺寸的加工方法误差各取相应尺寸的 1/3 78±0.5 的加工方法误差为:1/3=0.33 15±0.5 的加工方法误差为: 1/3=0.33 12.5 的加工方法误差为:0.27/3=0.09 平行度 0.1 加工方法误差的为:0.03 垂直度 0.1 加工方法误差的为:0.03 钻模在钻孔时的加工精度计算
表 1 钻模加工精度计算表
78±0.5 15±0.5
12.5±0.13
平行度 0.1
垂直度 0.1
夹具精度储备 J C 1- 0.45=0.55 1- 0.45=0.55 0.27- 0.15=0.12 0.1- 0.09=0.01 0.1- 0.09=0.01
(0.27)
定位误差ΔD
0.0353
0.0353
0.0353
0.0353 对刀误差ΔT
0.064
0.064
0.064
0.064
0.064
安装误差ΔA
0 夹具误差ΔJ
0.3
0.3
0.1
0.05
0.05
加工方法误差ΔG
0.33
0.33
0.09
0.03
0.03
加工总误差ΣΔ
0.45
0.45
0.15
0.09
0.09
附件:图纸列表
序号图号图纸名称备注1ZJJ-00 钻模夹具装配图装配图A1 2ZJJ 加工件零件图A4 3ZJJ-01 零件图
4ZJJ-02 零件图。